塑料制品的设计原则
塑料制品绿色设计评价导则
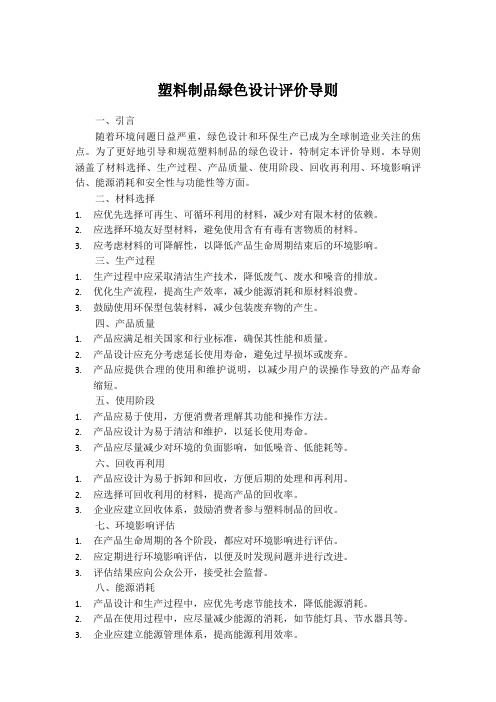
塑料制品绿色设计评价导则一、引言随着环境问题日益严重,绿色设计和环保生产已成为全球制造业关注的焦点。
为了更好地引导和规范塑料制品的绿色设计,特制定本评价导则。
本导则涵盖了材料选择、生产过程、产品质量、使用阶段、回收再利用、环境影响评估、能源消耗和安全性与功能性等方面。
二、材料选择1.应优先选择可再生、可循环利用的材料,减少对有限木材的依赖。
2.应选择环境友好型材料,避免使用含有有毒有害物质的材料。
3.应考虑材料的可降解性,以降低产品生命周期结束后的环境影响。
三、生产过程1.生产过程中应采取清洁生产技术,降低废气、废水和噪音的排放。
2.优化生产流程,提高生产效率,减少能源消耗和原材料浪费。
3.鼓励使用环保型包装材料,减少包装废弃物的产生。
四、产品质量1.产品应满足相关国家和行业标准,确保其性能和质量。
2.产品设计应充分考虑延长使用寿命,避免过早损坏或废弃。
3.产品应提供合理的使用和维护说明,以减少用户的误操作导致的产品寿命缩短。
五、使用阶段1.产品应易于使用,方便消费者理解其功能和操作方法。
2.产品应设计为易于清洁和维护,以延长使用寿命。
3.产品应尽量减少对环境的负面影响,如低噪音、低能耗等。
六、回收再利用1.产品应设计为易于拆卸和回收,方便后期的处理和再利用。
2.应选择可回收利用的材料,提高产品的回收率。
3.企业应建立回收体系,鼓励消费者参与塑料制品的回收。
七、环境影响评估1.在产品生命周期的各个阶段,都应对环境影响进行评估。
2.应定期进行环境影响评估,以便及时发现问题并进行改进。
3.评估结果应向公众公开,接受社会监督。
八、能源消耗1.产品设计和生产过程中,应优先考虑节能技术,降低能源消耗。
2.产品在使用过程中,应尽量减少能源的消耗,如节能灯具、节水器具等。
3.企业应建立能源管理体系,提高能源利用效率。
九、安全性与功能性1.产品应符合相关国家和行业安全标准,确保产品的安全性。
2.产品应具备良好的功能性,满足用户的需求。
塑料制品分析模具结构

塑料制品分析模具结构引言塑料制品在现代工业生产中占据着重要地位,而模具作为塑料制品生产的关键工具,其结构设计对于产品质量和生产效率有着直接影响。
本文将从塑料制品分析模具结构的角度出发,探讨模具结构的种类和设计原则。
1. 模具结构的种类1.1 单腔模具单腔模具是最简单的一种模具结构,适用于生产单一塑料制品。
其结构简单直接,易于制造和维护,成本相对较低。
然而,由于单腔模具每次只能生产一件产品,效率较低,适用于小批量生产。
1.2 多腔模具多腔模具是在一个模具中设置多个腔室,可以同时生产多个产品。
多腔模具的生产效率较高,适用于大批量生产。
然而,多腔模具的结构复杂,制造和维护难度较大,成本较高。
1.3 滑动模具滑动模具是指在模具中设置滑动块或滑动模块,用以实现产品中的倒角、凹槽等复杂结构。
滑动模具可以增加产品的设计灵活性和功能多样性,但同时增加了模具结构的复杂性和制造难度。
1.4 套模模具套模模具是指在一个模具中设置多个附加模块,用以实现产品中的套模结构,如套芯、套筒等。
套模模具可以实现产品的空心结构、腔体内壁的形状复杂性,但制造和维护难度较大。
2. 模具结构的设计原则2.1 结构简洁性模具结构应尽量简洁,减少额外的复杂部件和连接点。
简洁的结构有利于提高模具的制造和维护效率,并降低生产成本。
2.2 刚性和稳定性模具结构应设计成具有足够的刚性和稳定性,能够承受生产过程中的各种力和压力。
刚性和稳定性的不足会导致模具在生产过程中产生变形或破损,影响产品质量。
2.3 分模和脱模方便性模具结构应设计成易于分模和脱模的形式,以提高生产效率和降低脱模过程中的损耗。
合理的分模和脱模方式可以减少模具的损坏风险。
2.4 可靠性和耐久性模具结构应设计成可靠和耐久的形式,能够经受长时间高强度的生产使用。
可靠和耐久的模具结构可以减少维护和更换的频率,提高生产效率。
2.5 维护和保养便利性模具结构应设计成方便进行维护和保养的形式,以延长模具的使用寿命并降低维护成本。
塑料制品的结构设计规范
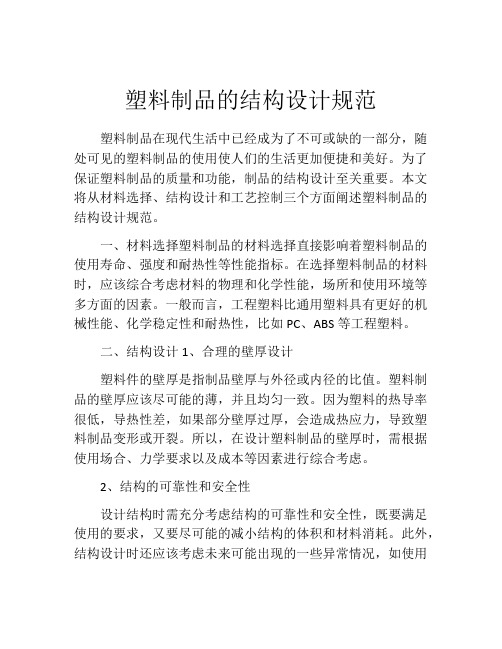
塑料制品的结构设计规范塑料制品在现代生活中已经成为了不可或缺的一部分,随处可见的塑料制品的使用使人们的生活更加便捷和美好。
为了保证塑料制品的质量和功能,制品的结构设计至关重要。
本文将从材料选择、结构设计和工艺控制三个方面阐述塑料制品的结构设计规范。
一、材料选择塑料制品的材料选择直接影响着塑料制品的使用寿命、强度和耐热性等性能指标。
在选择塑料制品的材料时,应该综合考虑材料的物理和化学性能,场所和使用环境等多方面的因素。
一般而言,工程塑料比通用塑料具有更好的机械性能、化学稳定性和耐热性,比如PC、ABS等工程塑料。
二、结构设计1、合理的壁厚设计塑料件的壁厚是指制品壁厚与外径或内径的比值。
塑料制品的壁厚应该尽可能的薄,并且均匀一致。
因为塑料的热导率很低,导热性差,如果部分壁厚过厚,会造成热应力,导致塑料制品变形或开裂。
所以,在设计塑料制品的壁厚时,需根据使用场合、力学要求以及成本等因素进行综合考虑。
2、结构的可靠性和安全性设计结构时需充分考虑结构的可靠性和安全性,既要满足使用的要求,又要尽可能的减小结构的体积和材料消耗。
此外,结构设计时还应该考虑未来可能出现的一些异常情况,如使用环境的变化、超负荷的物理作用和力学应力等因素都应该在结构设计中进行考虑。
三、工艺控制优秀的结构设计标准是塑料制品质量保证的前提,但良好的生产工艺过程也是确保质量的关键。
生产过程中应该选择先进的生产工艺技术,如模具设计、注塑机选型和注射参数的调控等。
此外,应该做好产品的标准化、精细化生产和检验工作,以确保产品品质达到标准。
综上所述,塑料制品的结构设计对产品质量至关重要,必须遵循一定的规范和标准进行设计和制造。
同时,在生产过程中也需要遵循简单、精细、标准化、自动化和人性化原则。
一旦遇到质量问题,企业应该采取积极有效的措施,及时处理,以免造成不必要的损失和影响公司声誉。
模具设计原理及考虑

制件设计的一般考虑工程塑料制品大部分是用注射成型方法加工而成的,制件的设计必须在满足使用要求和符合塑料本身的特性前提下,尽可能简化结构和模具、节省材料、便于成型。
制件设计中应分别考虑如下因素:一、制件的形状应尽量简单、便于成型。
在保证使用要求前提下,力求简单、便于脱模,尽量避免或减少抽芯机构,如采用下图例中(b)的结构,不仅可大大简化模具结构,便于成型,且能提高生产效率。
二、制件的壁厚确定应合理。
塑料制件的壁厚取决于塑件的使用要求,太薄会造成制品的强度和刚度不足,受力后容易产生翘曲变形,成型时流动阻力大,大型复杂的制品就难以充满型腔。
反之,壁厚过大,不但浪费材料,而且加长成型周期,降低生产率,还容易产生气泡、缩孔、翘曲等疵病。
因此制件设计时确定制件壁厚应注意以下几点:1.在满足使用要求的前提下,尽量减小壁厚;2.制件的各部位壁厚尽量均匀,以减小内应力和变形;3.承受紧固力部位必须保证压缩强度;4.避免过厚部位产生缩孔和凹陷;5.成型顶出时能承受冲击力的冲击。
国外的一些常用塑料的推荐壁厚如下表:三、必须设置必要的脱模斜度为确保制件成型时能顺利脱模,设计时必须在脱模方向设置脱模斜度,其大小与塑料性能、制件的收缩率和几何形状有关,对于工程塑料的结构件来说,一般应在保证顺利脱模的前提下,尽量减小脱模斜度。
下表为根据不同材料而推荐的脱模斜度:具体确定脱模斜度时应考虑以下几点:1.对于收缩率大的塑料制件应选用较大的脱模斜度;2.对于大尺寸制件或尺寸精度要求高的制件应采用较小的脱模斜度;3.制件壁厚较厚时,成型收缩增大,因此脱模斜度应取大;4.对于增强塑料脱模斜度宜取大;5.含自润滑剂等易脱模塑料可取小;6.一般情况下脱模斜度不包括在制件公差范围内。
四.强度和刚度不足可考虑设计加强筋为满足制件的使用所需的强度和刚度单用增加壁厚的办法,往往是不合理的,不仅大幅增加了制件的重量,而且易产生缩孔、凹痕等疵病,在制件设计时应考虑设置加强筋,这样能满意地解决这些问题,它能提高制件的强度、防止和避免塑料的变形和翘曲。
塑料制品设计原则
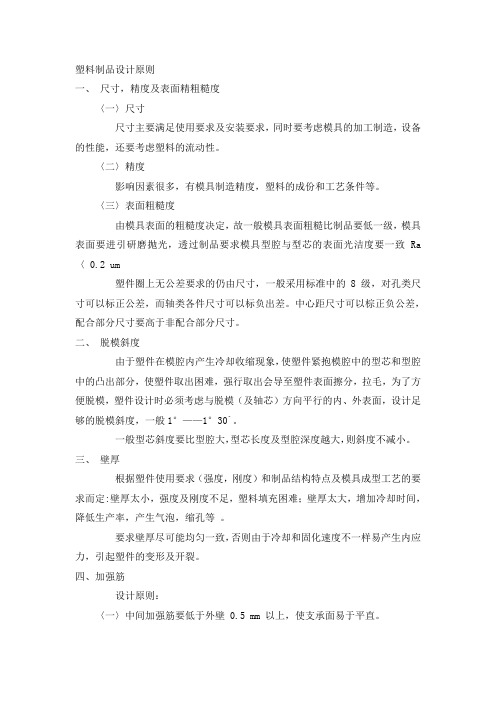
塑料制品设计原则一、尺寸,精度及表面精粗糙度〈一〉尺寸尺寸主要满足使用要求及安装要求,同时要考虑模具的加工制造,设备的性能,还要考虑塑料的流动性。
〈二〉精度影响因素很多,有模具制造精度,塑料的成份和工艺条件等。
〈三〉表面粗糙度由模具表面的粗糙度决定,故一般模具表面粗糙比制品要低一级,模具表面要进引研磨抛光,透过制品要求模具型腔与型芯的表面光洁度要一致 Ra 〈 0.2 um塑件圈上无公差要求的仍由尺寸,一般采用标准中的8 级,对孔类尺寸可以标正公差,而轴类各件尺寸可以标负出差。
中心距尺寸可以棕正负公差,配合部分尺寸要高于非配合部分尺寸。
二、脱模斜度由于塑件在模腔内产生冷却收缩现象,使塑件紧抱模腔中的型芯和型腔中的凸出部分,使塑件取出困难,强行取出会导至塑件表面擦分,拉毛,为了方便脱模,塑件设计时必须考虑与脱模(及轴芯)方向平行的内、外表面,设计足够的脱模斜度,一般1°——1°30`。
一般型芯斜度要比型腔大,型芯长度及型腔深度越大,则斜度不减小。
三、壁厚根据塑件使用要求(强度,刚度)和制品结构特点及模具成型工艺的要求而定:壁厚太小,强度及刚度不足,塑料填充困难;壁厚太大,增加冷却时间,降低生产率,产生气泡,缩孔等。
要求壁厚尽可能均匀一致,否则由于冷却和固化速度不一样易产生内应力,引起塑件的变形及开裂。
四、加强筋设计原则:〈一〉中间加强筋要低于外壁 0.5 mm 以上,使支承面易于平直。
〈二〉应避免或减小塑料的局部聚积。
〈三〉筋的排例要顺着在型腔内的流动方向。
五、支承面塑件一般不以整个平面作为支承面,而取而代之以边框,底脚作支承面。
六、圆角要求塑件防有转角处都要以圆角(圆弧)过渡,因尖角容易应力集中。
塑件有圆角,有利于塑料的流动充模及塑件的顶出,塑件的外观好,有利于模具的强度及寿命。
七、孔(槽)塑件的孔三种成型加工方法:(1)模型直接模塑出来。
(2)模塑成盲孔再钻孔通。
(3)塑件成型后再钻孔。
塑料艺术品设计理念是什么

塑料艺术品设计理念是什么
塑料艺术品设计是一门独特而富有创意的艺术形式,它将废弃的塑料制品转化
为令人惊叹的艺术品。
在这个设计理念中,塑料被重新赋予了生命和价值,不再是简单的废弃物,而是成为了艺术家们创作的媒介。
首先,塑料艺术品设计理念强调环保和可持续发展。
随着塑料制品在我们日常
生活中的广泛使用,废弃的塑料制品也越来越多。
通过将这些废弃的塑料制品转化为艺术品,不仅可以减少对环境的污染,还可以提醒人们关注环境保护和可持续发展的重要性。
其次,塑料艺术品设计理念注重创新和想象力。
塑料是一种具有多种形状和颜
色的材料,艺术家们可以利用这些特性创作出各种独特的作品。
他们可以将废弃的塑料瓶、袋子、玩具等重新组合,创造出富有想象力和创意的艺术品,从而给人们带来全新的艺术体验。
最后,塑料艺术品设计理念强调艺术与生活的结合。
通过将废弃的塑料制品转
化为艺术品,艺术家们不仅为这些废弃物赋予了新的生命,还让人们重新审视日常生活中的物品。
这些艺术品可以成为人们生活中的装饰品,提醒人们环保的重要性,同时也为人们的生活增添了美感和艺术氛围。
总的来说,塑料艺术品设计理念是一种注重环保、创新和生活融合的艺术形式。
通过这种设计理念,我们可以看到艺术家们对环境保护的关注,对创新和想象力的追求,以及对艺术与生活结合的探索。
希望未来能有更多的人关注和支持塑料艺术品设计,让这种独特的艺术形式得到更好的发展和传播。
塑料件的设计规范
注塑件设计的一般原则:a.充分考虑塑料件的成型工艺性,如流动性:b.塑料件的形状在保证使用要求的前提下,应有利于充模,排气,补缩,同时能适应高效冷却硬化;c.塑料设计应考虑成型模具的总体结构,特别是抽芯与脱出制品的复杂程度,同时应充分考虑到模具零件的形状及制造工艺,以便使制品具有较好的经济性;d.塑料件设计主要内容是零件的形状、尺寸、壁厚、孔、圆角、加强筋、螺纹、嵌件、表面粗糙度的设计。
4.2.1壁厚塑料件壁厚设计与零件尺寸大小、几何形状和塑料性质有关。
塑料件的壁厚决定于塑料件的使用要求,即强度、结构、尺寸稳定性以及装配等各项要求,壁厚应尽可能均匀,避免太薄,否则会引起零件变形,产品壁厚一般2~4mm。
小制品可取偏小值,大制品应取偏大值。
4.2.1.1塑料件相邻两壁厚应尽量相等,若需要有差别时,相邻的壁厚比应满足以下要求:t :t1≤1.5 ~24.2.1.2塑料凸肩H与壁厚t之间关系如图4.2-2中,图a中H>t,则造成塑料件的厚度不均匀,应改图b所示,H≤t可使塑料件壁厚不均匀程度减少。
4.2.2过渡圆角为了避免应力集中,提高强度和便于脱模,零件的各面连接处应设计过渡圆角。
零件结构无特殊要求时,在两面折弯处应有圆角过渡,一般半径不小于0.5~1mm,R≥t。
4.2.2.1内外圆角半径零件内外表面的拐角处设计圆角时,应保证零件壁厚均匀一致,图中以R为内圆角半径,R1为外圆角半径,t为零件的壁厚.4.2.3加强筋为了确保零件的强度和刚度,而又不使零件的壁厚过大,避免零件变形,可在零件的适当部位设置加强筋。
4.2.3.2设计加强筋时,应使中间筋低于外壁0.5~1mm,以减少支承面积,达到平直要求。
4.2.4孔的设计孔的周壁厚会影响到孔壁的强度。
孔口与塑件边缘间距离a不应小于孔径,并不小于零件壁厚t的0.25倍。
孔口间的距离b不宜小于孔径0.75倍,并不小于3mm。
4.2.4.1 孔的周壁厚H和突起部分的壁厚c和高度h、h与c之比不能超过3,如图内螺纹直径不能小于2mm,外螺纹直径不能小于4mm.螺距不小与0.5mm.螺纹的拧合长度一般不大于螺纹直径的1.5倍,为了防止塑料螺纹的第一扣牙崩裂,并保证拧入,必须在螺纹的始端和末端留有0.2~0.8mm的圆柱形.并注意:塑料件螺纹不能有退刀槽,否则无法脱模。
塑料制品的设计(强行脱模、表面质量)
塑胶制品结构的设计
一.制品结构工艺设计的原则:
1.在保证制品性能和使用要求的情况下,尽量选用价廉、且成型性能好的塑料;
2.力求使制品结构简单,避免侧向凹凸结构,使模具结构简单,易于制造;(内侧凹凸结构有两种情况可不用内行位:碰穿和强行脱模)
•注:关于强行脱模:
1)当侧向凹凸较浅且允许有圆角时,可强行脱模;
2)可强行脱模的塑料有PE、PP、POM和PVC等;
三、制品的表面质量:
1、包括制造质量:型腔省模抛光,一般模具型腔粗糙度为
Ra0.02—1.25um,制品的粗糙度比模具型腔粗糙度低1-2级。
2、注塑质量:水花,蛇纹,熔接痕,顶白变形,黑斑,披锋、
凹痕等。
3、烤柒质量:
4、电镀质量:
5、丝印质量:
6、拉丝质量:
7、抛光质量:
8、汤金质量
9、贴纸质量
10、贴片
四.塑料制品的常见结构设计:
1.脱模斜度:
1).不同塑料的脱模斜度不同,在不影响产品性能的情况下,脱模斜度尽量取较大值;
2).脱模斜度不包括在公差范围之内;
3).晒纹脱模斜度应取较大值,
一般为3°~9°;
4).硬质塑料比软质塑料的脱模斜度大,收缩率大的塑料比收缩率小的脱模斜度大;
5)、制品高度越高,孔越深,为保证精度要求,脱模斜度宜取小一点;
6)、制品形状复杂难脱模时,脱模斜度要大一些;
7)、前模脱模斜度大于后模脱模斜度;
8)、配合精度要求越高,脱模斜度要越小;
9)、壁厚大的制品,脱模斜度可取较大值;机械性能强塑料,自润滑性塑料,脱模斜度可取小一些。
塑料制品的设计
塑料制品的設計塑料制品的設計不僅要滿足使用要求﹐而且要符合塑料的成型工藝特點﹐并且進可能使模具結構簡化。
這樣﹐可使成型工藝穩定﹐保証塑料制品地質量﹐又可使生產成本降低。
塑料制品的設計必須考慮以下因素﹕1.塑料的性能塑撩制品的設計與塑料的物理力學性能和工藝性能有密切關系。
2.成型方法塑料制品的設計要求視成型方法而異。
3.模具結溝和制造工藝性塑料制品的設計應有利于模具結溝的簡化和制造。
塑料制品設計的主要內容包括塑料制品的几何形狀﹑尺寸精度和表面質量。
一﹑塑料制品的几何形狀塑料制品的几何形狀包括形狀﹑壁厚﹑脫模斜度﹑加強脛﹑支撐面﹑圓角﹑孔﹑螺紋﹑嵌件等。
(一)形狀塑料制品應盡量避免側壁凹槽或與制品脫模方向垂直的孔﹐這樣可避免采用瓣合分型或側軸芯等復雜的模具結溝和使分型面上留下飛邊。
為改進前的塑料制品結溝﹐需采用側軸芯或瓣合分型凹模結溝﹔為經改進后的塑料制品的結溝﹐可采用整體式凹模(或凸模)結溝。
這樣使模具結溝得以簡化。
塑料制品的形狀還要有利于提高制品的強度和剛度。
如將塑料制品設計成球面或帶凸緣形狀。
(二)壁厚塑料制品的壁厚主要決定于塑料制品的使用條件。
但壁厚的大小對塑料成型影響很大﹐因此必須合理選擇。
壁厚過小則成型時流動阻力大﹐對大型復雜塑料制品就難以充滿型腔﹐而且不能保証塑料制品的強度和剛度﹔壁厚過大則浪費原料﹐增加塑料制品的成本﹐而且會增加成型時間和冷卻時間﹐降低生產率﹐還容易產生氣泡﹑縮孔等缺陷。
壁厚大小主要與塑料品種﹑塑料制品大小及成型工藝條件等因素有關。
對于熱固性塑料﹐壁厚一般取1.6~2.5mm,大型塑件取3.2~8mm,熱固性塑料制品的壁厚推荐值可參見表2-3.對與熱塑性塑料﹐薄壁塑料制品易于成型﹐但壁厚一般不小于0.6~0.9mm﹐常選取4~6mm。
熱塑性塑料制品的最小壁厚和常用壁厚推荐值見表2-4.表2—3 熱固性塑料制品的壁厚推荐值表2—4 熱塑性塑料制品的最小壁厚和常用壁厚推荐值(mm)塑料制品的壁厚一般應力求均勻﹐否則會因固化或冷卻速度不同而引起收縮不均勻﹐產生內應力﹐導致塑料制品產生翹曲變形或縮孔。
塑料制品的设计规范
的充模流动阻力。如图3-13 ⑵应避免或减少塑料的局部集中,
以防止产生凹陷和气泡。如图3-14 ⑶加强筋以设计矮一些多一些为好。 ⑷筋与筋的间隔距离应大于塑件的
壁厚。
PPT文档演模板
塑料制品的设计规范
3.4.5 增加刚性减少变形的其他措施
将薄壳状的塑件设计为球面, 拱曲面等, 可 以有效地增加刚性、减少变形。
PPT文档演模板
塑料制品的设计规范
3.4.3 加强筋及其它增强结构
为了提高塑件的强度和防止塑件翘曲变形, 常设计加强筋,如图筋的设置位置应沿塑料 充模流向,降低充模流动阻力. 见图3-12
加强筋的正确形状和尺寸比例如图3-15 所示。
PPT文档演模板
塑料制品的设计规范
3.4.4 加强筋的主要形式
PPT文档演模板
塑料制品的设计规范
3.2 尺寸精度与表面质量
3.2.1 尺寸精度 3.2.2 尺寸精度的确定 3.2.3 表面质量
PPT文档演模板
塑料制品的设计规范
3.2 尺寸精度与表面质量
3.2.1 尺寸精度 1、塑件尺寸概念
塑件尺寸——塑件的总体尺寸。 2.塑料制品总体尺寸受限制的主要 因素:
PPT文档演模板
塑料制品的设计规范
3.2 尺寸精度与表面质量
3.2.2 尺寸精度的确定
表3—1是模塑件尺寸公差国家标 准(GB/T 14486-1993), 表 3—2是常用塑料材料的公差等级选 用。
将表3—1和表3—2结合起来使
用, 先查表3—2, 根据模塑件的材料
品种及用要求选定塑件的尺寸精度
图3—6 可强制脱模的浅侧凹结构
a)(A-B)×100%/B≤5% b) (A-B)×100%/C≤5%
- 1、下载文档前请自行甄别文档内容的完整性,平台不提供额外的编辑、内容补充、找答案等附加服务。
- 2、"仅部分预览"的文档,不可在线预览部分如存在完整性等问题,可反馈申请退款(可完整预览的文档不适用该条件!)。
- 3、如文档侵犯您的权益,请联系客服反馈,我们会尽快为您处理(人工客服工作时间:9:00-18:30)。
第一部份塑料制品的设计原则塑料制件主要是根据使用要求进行设计,在满足使用要求的前提下,塑件形状应尽可能地做到简化模具结构,符合成型工艺特点。
设计塑件时必须考虑以下几方面的因素。
(1)塑件的物理机械性能,如强度、刚性、韧性弹性、吸水性以及对应的敏感性。
(2)塑料的成型工艺性,如流动性。
(3)塑件形状应有利于充模流动、排气、补缩。
(4)塑件在成型后收缩情况及各向收缩差异。
(5)模具的总体结构,特别是抽芯与脱出塑件的复杂程度。
(6)模具零件的形状及其制造工艺。
塑件设计的主要内容包括塑料的形状尺寸、精度表面光洁度、壁厚、斜度、以及塑件的加强筋、支承面、孔、圆角、螺纹、嵌件等的设置。
一、塑件的尺寸和精度受塑料流动性和壁厚的影响影响精度的因素:1、模具制造精度2、塑料收缩率的波动3、模具尺寸的磨损4、工艺条件的变化5、脱模斜度制品公差留有修模余地孔类取(+)号、轴取(-)号中心距取(+、-)号二、表面光洁度制品光洁度比模具光洁度低一级,透明产品的阴阳模光洁度一致。
三、形状须有利于脱模,使模具结构简单。
四、脱模斜度,〆:0.5 1.5°硬脆性塑料脱模斜度大,收缩力大的塑件斜度大、壁厚的斜度大、有皮纹,4°6°亚光,不同的皮纹、1°6°(有纹样对照)若斜度不妨碍制品的使用,则可将斜度值取得大一些。
五、塑件壁厚及其均匀性塑料制件的壁厚对塑件的质量影响很大,壁厚过小时成型时流动阻力大,大型复杂制品就难以充满型腔。
(壁厚应尽可能一致)否则因冷却固化速度不同。
塑料壁厚的最大尺寸应满足以下有几方面的要求:1、足够的强度和刚度。
2、脱模时能经受脱模机构的冲击与震动。
3、装配时能承受紧固力。
热塑性塑料:制品壁厚增加一倍,冷却时间将增加四倍,使生产效率大大降低。
另外也影响产品质量,如易产生充气泡,缩孔,翘曲等缺陷。
热塑性塑料易于成型薄壁制件,能达至0.25mm,但一般不宜小于0.6-0.9mm,常取2-4毫米。
六、加强筋与其它防止变形的结构设计:加强筋的主要作用是增加制品强度和避免翘曲变形。
布置加强筋时,应避免或减少塑料局部集中,否则会产生缩孔、气泡。
加强筋不应设计得过厚,否则在其对应的壁上产生凹陷,加强筋必须有足够的强度,加强筋不宜设计得过高。
采用反边、内凹、球面可加强刚度。
七、支承面可采用凸边、底脚。
加强筋与支承面有高度差。
1、圆角R>壁厚R/A=0.3-0.5 R/A≮0.25圆角可避免塑件应力集中和模板应力集中.同时圆角可大大地改善塑料的充模特性。
即使采用可R0.5mm的圆角就能使塑件的强度大为增加。
塑件设计成圆角,使模具型腔对应部位亦呈圆角,这增加了模具的坚固性,塑件的外圆角对应着型腔的内圆角,它使模具在淬火或使用时不致因而应力集中而开裂.(但是在塑件的某些部位如分型面、型芯与型腔配合处等不便作成圆角而只能采用尖角.九、孔的设计:塑件上常见的孔有通孔、盲孔、形状复杂的孔,螺纹孔等。
孔之间与边壁之间均应有足够的距离。
孔柱的直径和孔与边壁最小厚度之间的关系:孔柱的高度(深度)不宜过大。
孔柱直径也不宜过小。
十、螺纹设计(略)a 直接成型b先成型直孔、再加工(自攻螺纹)C放入螺纹钳件。
十一、嵌件设计(略)1 、嵌件设计的作用:增加局部强度,硬度、塑件尺寸的稳定性,提高精度等,以及满足其它多种要求。
缺点:采用嵌件一般会增加塑件成本,使模具结构复杂,而且向模具中安装嵌件会降低塑件的生产效率。
嵌件周围有一定的塑料层厚度.十二、标记、符号、文字(略)第二部份塑料注射成型模具:一、注射模具典型结构:(一)成型零部件型腔是直接成型塑料制件的部分。
(二)浇注系统指主流道、分流道、浇口、冷料#等。
(三)导向部分导向柱、导向孔、为保持证准确对中而设。
(四)分型抽芯机构(五)顶出装置(六)冷却加热系统(七)排气系统二、注射成型模具分类按总体结构分(一)单分型面模具(二)双分型面注射模具(三板式)(三)带有活动镶件的注射模具(四)分型抽芯注射模(五)无流道注射模具三、模具与注射机的关系(一)注射机有关参数的校核1、最大注射量2、注射压力的校核3、锁模力的校核P锁≥P腔P腔=Q.FQ:塑料在模内的单位压力kg/cm2,F:制品+浇注系统在分型面上的投影面积,cm2。
4、模具与注射机安装模具部分相关尺寸的校核。
(1)喷嘴头的球面半径;R=R+1 3mm(2)定位圈尺寸;Ф100-(3)机台的模具闭合高度与模厚的关系;(4)机台拉杆间距与模具外形尺寸关系;(5)模具脚安装孔尺寸与机台安装孔尺寸的关系;(6)注射机顶出装置与模具顶出机构的关系;5、注射机开模行程与模具的关系。
(1)注射机开模行程与模厚无关的(液压机械联合用的锁模机构)最大开模行程由连杆机构的最大冲程决定。
①对单分型的模具S≥H1+H2+5-10mmS=制品脱模所需的开模行程H1-脱模距H2-制品加浇注系统的高度。
②、对双分型面模具S≥H1+H2+a+5-10mm.2、注射机开模行程与模厚有关的(全液压或锁模机构)①对单分型面模具SK≥Hm+H1+H2+5-10mmSK-开模行程Hm-模厚②对双分型面模具SK=Hm+H1+H2+a+5-10mm四、浇注系统设计(一)、浇注系统及其设计原则:1、浇注系统浇注系统是指模具中从注射机喷嘴开始到型腔为止的塑料流动通道。
可分为普通流道浇注系统和无流道浇注系统两大类型。
2、浇注系统的设计原则:(一)塑料熔体的流动特性①剪切速率提高,表现粘度下降。
②温度升高、表现粘度下降。
③压力增加、粘度增加。
设计原则①充模时尽量减少流道阻力、提高剪切速率。
②保压时应保证注射压力传递到型腔的各部分(避免熔接痕)。
③控制好浇口的适时封闭,降低制品的内应力。
④在满足成型的条件下,应取最小体积。
(二)普通浇注系统:1、普通浇注系统的组成。
由主流道、分流道、浇口、冷料#几部分组成。
2、普通浇注系统的设计:(1)主流道、(尽量取短值、减少压力损失)①主流道锥角〆2-4°短取大值〆太小,阻力、比表面积大比表面积=————〆太小、易造成涡流(由空气阴力造成)使制品带有气泡。
②小端直径О=О1+0.5-1mm(3)光洁度▽8▽(4)长度一般不大于60mm(5)浇口套(2)分流道①断面形状a圆形(此表面积小、表面积与体积之比)b椭圆形、C梯形、dV形、eU半圆形、f矩形②布置形式a平衡式(同时注满、同时保压)b非平衡式(4)冷塑和拉料杆的设计①设置冷料#的作用:除去料流中的前锋冷料而设置。
②冷料#和拉料杆的形式。
2、常用浇口的形式:(1)侧浇口(边缘浇口)从侧面进料。
(2)扇形浇口(用于长条形的制品)(3)平缝式浇口(4)圆环形浇口(中心浇口)(5)轮辐式浇口(6)爪浇口(7)直接浇口①结构简单、加工方便。
②浇注射系统程短转折少、注射压力少传递好。
③对深腔制品有利于排气。
④进料一致制品质量均匀。
⑤浇口去除后,制品上留下较大的浇口痕迹,影响制品的外观。
⑥浇口附近容易产生缩孔或应力开裂。
(8)菱形浇口(点浇口、针浇口)特点:①进料口小,制品外观质量好;②便于生产过程自动化;③注射压力少损耗大;④对薄壁制品、浇口周围内应力大。
浇口经验数据:PE取0.7 PS/0.5-1 ABS/0.8-1.4(9)潜伏式浇口(10)护耳式浇口1、横浇口设计(略)2、浇注系统进料部位的选择选择的原则:(1)避免熔体破裂现象在制品上留下缺陷(使剪切应力小于熔体强度)(2)应有利于塑料熔体的流动,排气和补料;(3)应考虑定向方位对制件性能的影响;(4)减少熔痕,增加熔接牢度;(5)应防止料流将型芯或嵌件挤压变形;(6)应考虑模内压力与锁模力相平衡。
考虑流动比流动比三、无流道浇注系统1、特点:(1)物料利用率高(2)减少工序节约劳力(3)可缩短生产周期(4)可采用低压注射(5)有利于生产自动化2、采用无流道模具进行成型的树脂应具有的特性。
(1)对温度敏感(否则对堵塞浇口)(2)对压力敏感(3)导热系数高(4)热变形温度(5)比热小A、PE、B、PP、PS、C、ABS、PC。
B、POM、PVC。
五、模具分型面的确定1、分型面及其形成:(1)分型面——分开模具,取出塑件的面;(2)分型面的形成;①水平分型面②阶梯分型面③斜分型面④异型分型面分型面是否得当,对制件质量、操作难易、模具制造都有很大影响。
2、确定模具分型面的基本原则。
①尽量采用开模方向垂直的分型面;②分型面应尽量简单,避免采用复杂形状;③分型面应设在塑件断面轮廓最大的地方;④分型面必须使塑件在开模时留在动模内;⑤分型面不应影响尺寸精度;⑥分型面不应影响塑件的外观。
因为分型面不可避免地要在制件上留下溢料痕迹,或拼合缝的痕迹,故分型面最好不选在制品光亮平滑的外表面或带圆弧的转角处。
⑦分型面应有利于带侧孔塑件抽芯。
(二)排气槽的设计(略)四、成型零部件的设计一、成型零件部件的结构设计1、镶件原则;①镶嵌部分的形状尽量简单;②镶件必须牢固可靠;③镶嵌配合的间隙必须与制品的脱模方向平衡;④尽量避免镶拼痕迹残留在制品表面;⑤镶块不宜过多;⑥尽量减少拼接面长度。
六、合模导向机构一、合模导向机构的作用:1、起定位作用;2、防止模具闭合时对位不准而发生碰撞;3、合模后使型腔保持正确形状;4、抵消注射时的侧向力。
七、塑件脱模机构(一)脱模机构的组成及分类:1、组成(1)推出元件(推杆、推管、推板、推块)(2)复位元件(回程杆、弹簧)(3)导向元件(4)传动元件2、分类(1)按驱动方式分1、手动2、机动3、液动(顶出油缸)(2)按结构分1、简单脱模机构;2、双脱模机构;3、顺序脱模机构;4、二级脱模机构;5、浇注系统脱模机构;6、带螺纹塑件的脱模机构(二)简单脱模机构1、推杆脱模机构(顶杆、顶针)2、推杆脱模机构3、推板脱模机构(1)使用场合薄壁制品、壳体4、简单脱模机构的其它元件复位元件:(1)回程杆(2)弹簧(3)导向元件七、侧向分型与抽芯机构:八、注射模具温度调节系统:(1)冷却系统(2)加热系统。