蒸发器的工艺计算+最终版1
多效蒸发计算实例
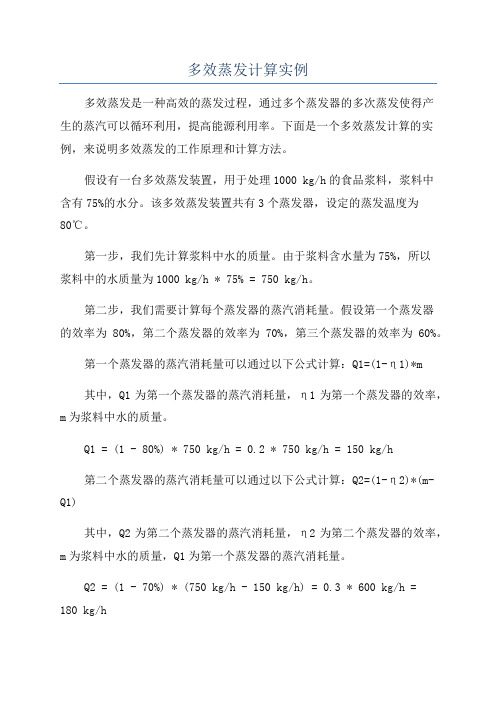
多效蒸发计算实例多效蒸发是一种高效的蒸发过程,通过多个蒸发器的多次蒸发使得产生的蒸汽可以循环利用,提高能源利用率。
下面是一个多效蒸发计算的实例,来说明多效蒸发的工作原理和计算方法。
假设有一台多效蒸发装置,用于处理1000 kg/h的食品浆料,浆料中含有75%的水分。
该多效蒸发装置共有3个蒸发器,设定的蒸发温度为80℃。
第一步,我们先计算浆料中水的质量。
由于浆料含水量为75%,所以浆料中的水质量为1000 kg/h * 75% = 750 kg/h。
第二步,我们需要计算每个蒸发器的蒸汽消耗量。
假设第一个蒸发器的效率为80%,第二个蒸发器的效率为70%,第三个蒸发器的效率为60%。
第一个蒸发器的蒸汽消耗量可以通过以下公式计算:Q1=(1-η1)*m其中,Q1为第一个蒸发器的蒸汽消耗量,η1为第一个蒸发器的效率,m为浆料中水的质量。
Q1 = (1 - 80%) * 750 kg/h = 0.2 * 750 kg/h = 150 kg/h第二个蒸发器的蒸汽消耗量可以通过以下公式计算:Q2=(1-η2)*(m-Q1)其中,Q2为第二个蒸发器的蒸汽消耗量,η2为第二个蒸发器的效率,m为浆料中水的质量,Q1为第一个蒸发器的蒸汽消耗量。
Q2 = (1 - 70%) * (750 kg/h - 150 kg/h) = 0.3 * 600 kg/h =180 kg/h第三个蒸发器的蒸汽消耗量可以通过以下公式计算:Q3=(1-η3)*(m-Q1-Q2)其中,Q3为第三个蒸发器的蒸汽消耗量,η3为第三个蒸发器的效率,m为浆料中水的质量,Q1为第一个蒸发器的蒸汽消耗量,Q2为第二个蒸发器的蒸汽消耗量。
Q3 = (1 - 60%) * (750 kg/h - 150 kg/h - 180 kg/h) = 0.4 *420 kg/h = 168 kg/h第三步,我们需要计算多效蒸发装置的总蒸汽消耗量。
总蒸汽消耗量等于各个蒸发器的蒸汽消耗量之和。
蒸发器工艺计算方法示例

思路:一、先确定工艺流程二、求初始各效蒸发水量 1、初定沸点升为15℃2、各效加热蒸汽和料液沸点之间传热温差为20℃(一般为15-20℃)3、确定最后一效二次蒸汽压强,一般为10KPa ,并对应出温度。
4、推出其它各效和生蒸汽温度及压强。
5、设计换热器位置、加热蒸汽或热水来源,冷凝水温度。
6、列方程组求各效蒸发水量,作为初始值。
三、重新计算各效蒸发水量1、确定苦卤沸点升(实验确定,或参考专利“一种沸石法从海水提取硫酸钾的方法”,可初定为127℃) 根据各效蒸发水量比例,确定其余各效料液沸点升。
44332211升升升升t W t W t W t W === 2、根据各效沸点升、传热温差20℃、以及末效温度,从末效开始推出各效状态和生蒸汽状态。
4.2 方案2:四效逆流,并且增加两个换热器 4.2.1系统示意图4.2.2 求初始各效蒸发水量 4.2.2.1 基础数据1、初定沸点升为15℃2、各效加热蒸汽和料液沸点之间传热温差为20℃(一般为15-20℃)3、确定最后一效二次蒸汽压强,一般为10KPa ,并对应出温度。
4、推出其它各效和生蒸汽温度及压强。
5、设计换热器位置、加热蒸汽或热水来源,冷凝水温度。
6、列方程组求各效蒸发水量,作为初始值。
各效常数表图4.2 蒸发系统示意图(1)富钾卤水:F=218997.81kg/h,t0=25℃。
(2)中间卤水:C p0:3.316kJ/(kg·℃)。
(3)总蒸发水量:108110.03kg/h(4)换热器1冷却水出口温度比进换热器的物料温度130.3℃高20℃,即150℃。
(5)换热器2冷却水出口温度比进换热器的物料温度60.3℃高20℃,即80℃。
4.2.2.2 热量衡算1蒸发水衡算:1效二次汽量+2效二次汽量+3效二次汽量+四效二次汽量=总蒸发水量w1+ w2+ w3+ w4=108110.032 Ⅳ效衡算:四效进汽汽化热+四效进料热量=四效出汽热量+四效出料热量2308.03*w3+3.316*218997.81*25=2578.4*w4+3.316* (218997.81-w4)* 60.33换热器Ⅱ衡算:换热器Ⅱ热水变冷水放出的热量=换热器2物料吸收的热量4.223*w1* (115.3-80) =3.316* (218997.81- w4)* (t2-60.3)4 Ⅲ效衡算:Ⅲ效进汽汽化热+Ⅲ效进料热量=Ⅲ效出汽热量+Ⅲ效出料热量2215.57*w2+3.316 * (218997.81-w4)*t2=2644.19*w3+3.316*(218997.81-w4-w3)* 95.35Ⅱ效衡算:Ⅱ效进汽汽化热+Ⅱ效进料热量=Ⅱ效出汽热量+Ⅱ效出料热量2112.87*w1+3.316*(218997.81-w4-w3)*95.3=2215.57*w2+3.316* (218997.81-w4-w3-w2)* 130.26换热器Ⅰ衡算:换热器Ⅰ热水变冷水放出的热量=换热器1物料吸收的热量4.281*D* (185.3-150)= 3.316* (218997.81-w4-w3-w2)* (t1-130.3)7Ⅰ效衡算:Ⅰ效进汽汽化热+Ⅰ效进料热量=Ⅰ效出汽热量+Ⅰ效出料热量1995.90* D+3.316* (218997.81- w4- w3- w2)* t1=2746.40* w1+3.316* (218997.81- w4- w3- w2-w1)* t1 4.2.2.3 MATLAB运算function q=f(p)q(1)= p(4)+ p(5)+ p(6)+ p(7)-108110.03;q(2)= 2308.03*p(6)+3.316*218997.81*25-(2578.4*p(7)+3.316* (218997.81-p(7))* 60.3);q(3)= 4.223*p(4)* (115.3-80) -(3.316* (218997.81- p(7))* (p(2)-60.3));q(4)= 2215.57*p(5)+3.316 * (218997.81-p(7))*p(2)-(2644.19*p(6)+3.316*(218997.81-p(7)-p(6))* 95.3);q(5)= 2112.87*p(4)+3.316*(218997.81-p(7)-p(6))*95.3-(2215.57*p(5)+3.316* (218997.81-p(7)-p(6)-p(5))* 130.2);q(6)= 4.281*p(3)* (185.3-150)- (3.316* (218997.81-p(7)-p(6)-p(5))* (p(1)-130.3));q(7)= 1995.90* p(3)+3.316* (218997.81- p(7)- p(6)- p(5))* p(1)-(2746.40* p(4)+3.316* (218997.81- p(7)- p(6)- p(5)-p(4))* p(1));运行命令:x=fsolve('f2',[1 2 3 4 5 6 7]',optimset('Display','off')) 计算结果:4.2.3 重新计算各效蒸发水量 4.2.3.1 基础数据1、确定苦卤沸点升(实验确定,或参考专利“一种沸石法从海水提取硫酸钾的方法”,可初定为127℃) 根据各效蒸发水量比例,确定其余各效料液沸点升。
(完全版本)蒸发器热量和面积的计算法则

(完全版本)蒸发器热量和面积的计算法则1. 介绍本文档提供了一种用于计算蒸发器热量和面积的方法,该方法可以帮助用户根据具体需求设计蒸发器,以确保其高效、稳定地运行。
2. 热量计算法则2.1 基本原理蒸发器的热量主要由输入热量、损失热量和有效热量组成。
输入热量是指蒸发器从外界接收的热量,损失热量是指在热量传递过程中产生的热量损失,有效热量是指实际用于蒸发器工作的热量。
2.2 计算公式蒸发器的热量计算公式如下:\[ Q = Q_{\text{输入}} - Q_{\text{损失}} \]\[ Q_{\text{有效}} = Q_{\text{输入}} - Q_{\text{损失}} \]其中:- \( Q \) 表示蒸发器的热量(单位:千瓦时,kWh);- \( Q_{\text{输入}} \) 表示蒸发器的输入热量(单位:千瓦时,kWh);- \( Q_{\text{损失}} \) 表示蒸发器的损失热量(单位:千瓦时,kWh);- \( Q_{\text{有效}} \) 表示蒸发器的有效热量(单位:千瓦时,kWh)。
3. 面积计算法则3.1 基本原理蒸发器的面积主要由传热面积和辅助面积组成。
传热面积是指蒸发器中进行热量传递的面积,辅助面积是指用于支持蒸发器运行的面积。
3.2 计算公式蒸发器的面积计算公式如下:\[ A = A_{\text{传热}} + A_{\text{辅助}} \]其中:- \( A \) 表示蒸发器的总面积(单位:平方米,m²);- \( A_{\text{传热}} \) 表示蒸发器的传热面积(单位:平方米,m²);- \( A_{\text{辅助}} \) 表示蒸发器的辅助面积(单位:平方米,m²)。
4. 应用示例以下是一个简单的应用示例,用于计算一个特定蒸发器的热量和面积。
4.1 假设条件- 输入热量:1000 kWh;- 损失热量:200 kWh;- 传热面积:50 m²;- 辅助面积:10 m²。
蒸发器的设计计算
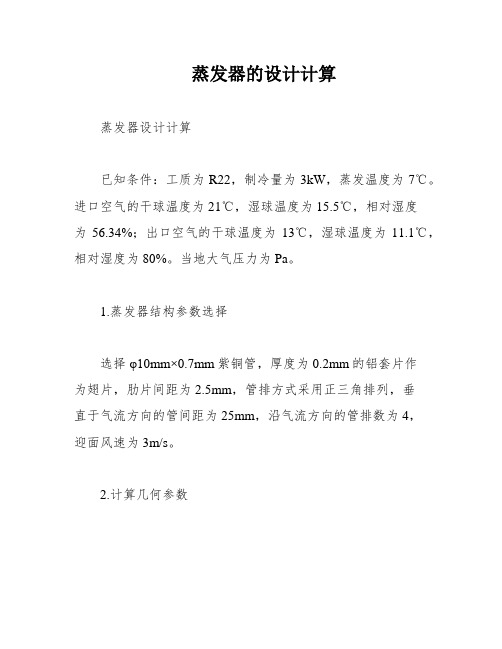
蒸发器的设计计算蒸发器设计计算已知条件:工质为R22,制冷量为3kW,蒸发温度为7℃。
进口空气的干球温度为21℃,湿球温度为15.5℃,相对湿度为56.34%;出口空气的干球温度为13℃,湿球温度为11.1℃,相对湿度为80%。
当地大气压力为Pa。
1.蒸发器结构参数选择选择φ10mm×0.7mm紫铜管,厚度为0.2mm的铝套片作为翅片,肋片间距为2.5mm,管排方式采用正三角排列,垂直于气流方向的管间距为25mm,沿气流方向的管排数为4,迎面风速为3m/s。
2.计算几何参数翅片为平直套片,考虑套片后的管外径为10.4mm,沿气流方向的管间距为21.65mm,沿气流方向套片的长度为86.6mm。
设计结果为每米管长翅片表面积为0.3651m²/m。
每米管长翅片间管子表面积为0.03m²/m。
每米管长总外表面积为0.3951m²/m。
每米管长管内面积为0.027m²/m。
每米管长的外表面积为0.m²/m。
肋化系数为14.63.3.计算空气侧的干表面传热系数1)空气的物性空气的平均温度为17℃。
空气在下17℃时的物性参数为:密度为1.215kg/m³,比热容为1005kJ/(kg·K)。
2)空气侧传热系数根据空气侧传热系数的计算公式,计算得到空气侧的干表面传热系数为12.5W/(m²·K)。
根据给定的数据,蒸发器的尺寸为252.5mm×1mm×10.4mm。
空气在最窄截面处的流速为5.58m/s,干表面传热系数可以用小型制冷装置设计指导式(4-8)计算得到,计算结果为68.2W/m2·K。
在确定空气在蒸发器内的变化过程时,根据进出口温度和焓湿图,可以得到空气的进出口状态点1和点2的参数,连接这两个点并延长与饱和气线相交的点w的参数为hw25kJ/kg。
dw6.6g/kg。
tw8℃。
蒸发器计算

第 2 页
9.5 9.6 9.7
冷水平均流速: 水侧雷诺数: 管外给热系数:
ω = W/Fm= Rew = do· · /μ = ω ρ α o =0.23(λ o/do)Rew0.6Pr1/3(μ /μ w)1.4 = 0
0.000000
m/s
0.000000
W/㎡·K
10. 管程阻力计算: 10.1 阻力沸腾数: KF = 10.2 阻力系数: fTP =11.294(Relo2/KF)-0.159(ρ l/ρ g)-0.693(e/di)0.296(2β /π )0.104 = 10.3 局部阻力降: 流入管口处的当量长度: [le]i = 20di = 流出管口处的当量长度: 10.4 总管长: 10.5 平均密度: 10.6 沿程总阻力: Δ Pt = [le]o = 2[le]i = L = Z(l+[le]i+[le]0) = ρ m= ρ lρ g/[(1-Xm)ρ g+Xmρ l ]= fTP· r2· G L/(ρ m·i) = d Δ tE = Δ Pt/Δ p = #DIV/0! 0.162200 0.324400 5.473200 37.207037 #DIV/0! #DIV/0! m m m kg/m3 Pa ℃ ξ ·Δ X/(Z·g· l· Xm) = ###########
3.
4.
5.
内翅片数: nc = 翅片螺旋角: β = 翅片高度: e= 翅片距: H= 拟取蒸发器管程参数: 管子根数:(管孔数) n= 程 数: Z= 管子有效长度: l= 内表面积: Fin = 壳程参数: 筒体内径: Di = 管间距: s= 对角线上管子数: b= 断路板数量及宽度: w= 纵向折流板厚度: δ= 折流板数: Nb = 平均隔室间距: B= 弓形缺口高度: h= 缺口内管子根数: Nq = 缺口间的管子排数: Nc = 工质在定性温度下的物理性质参数: 定性温度: td = 液体密度: 气体密度: 定压比热: 导热系数: 动力粘度: 普兰德准数: ρ ρ
化工单元操作:蒸发工艺计算

工艺计算
二、加热蒸汽消耗量
D WH '(F W )h1 Fh0 QL H hc
讨论1.加热蒸汽的冷凝水在饱和温度下排出
则H-hc为冷凝潜热
r(kJ/kg)
D WH '(F W )h1 Fh0 QL r
工艺计算
三、蒸发器传热面积计算
由传热速率方程可知,传热面积为:
A Q K tm
(一)蒸发器的热负荷Q 蒸发器的热负荷Q可以根据加热室的热量衡算求得。如果忽略加热室的 热损失,则Q即为加热蒸汽冷凝放出的热量:
Q Dr
工艺计算
三、蒸发器传热面积计算
(二)传热系数K
1.传热系数原则上可按下式计算:
1
蒸发技术 ---蒸发工艺计算
工艺计算
一、水分蒸发量计算
以蒸发器为系统进行溶质的质量衡算(以kg/h为基准) :
Fx0=(F-Wx1
完成液浓度:
x1
Fx0 F W
工艺计算
二、加热蒸汽消耗量
以蒸发器为衡算范围,以kJ/h为单位 对进出蒸发器的热量进行衡算(以 0℃液态为温度与物态基准):
3. 现场测定 对已有的蒸发设备可用实验方法确定其K值,测定方法和换热器传热系数的测定方法相同。
工艺计算
三、蒸发器传热面积计算
(三)平均温度差Δtm
蒸发属两相均有相变的恒温传热过程,故传热的平均温度差(亦称有效温度差)为:
tm T t1
当加热蒸汽选定时,蒸发计算需知道溶液的沸点t1,即可计算传热温度差。
r'
注:T'—操作压力下二次蒸汽的温度,K; r′—操作压力下二次蒸汽的汽化潜热,kJ/kg。
(详尽版)蒸发器的热量和面积计算公式

(详尽版)蒸发器的热量和面积计算公式
1. 引言
本文档旨在提供关于蒸发器热量和面积计算的详细公式和方法。
蒸发器是一种常见的热交换设备,用于将液体转化为气体,通常用
于工业生产中的蒸发过程。
正确计算蒸发器所需的热量和面积对于
设备设计和操作至关重要。
2. 蒸发器热量计算公式
蒸发器的热量计算涉及液体的蒸发过程,其中涉及到以下参数:
- 初始液体温度(T1)
- 终止液体温度(T2)
- 需要蒸发的液体质量(m)
- 液体的蒸发潜热(L)
蒸发器的热量计算公式如下:
Q = m * L
其中,Q表示蒸发器所需的热量。
3. 蒸发器面积计算公式
蒸发器的面积计算涉及到传热过程,其中涉及到以下参数:
- 热传导率(k)
- 温度差(ΔT)
- 热阻(R)
蒸发器的面积计算公式如下:
A = ΔT / (k * R)
其中,A表示蒸发器的面积。
4. 其他考虑因素
蒸发器的热量和面积计算公式提供了基本的计算方法,但在实际应用中,还需要考虑其他因素,如流体流动情况、传热系数、壁面阻力等。
这些因素会对蒸发器的设计和性能产生影响,需要根据具体情况进行综合考虑和调整。
5. 结论
本文档介绍了蒸发器热量和面积计算的详细公式和方法。
在设计和操作蒸发器时,正确计算所需的热量和面积对于设备的正常运行和效率至关重要。
然而,在实际应用中,还需要综合考虑其他因素,以确保蒸发器的性能和稳定性。
以上所述仅为计算公式和基本方法,具体应用时请根据实际情况进行调整和验证。
(完整版)蒸发器的设计计算
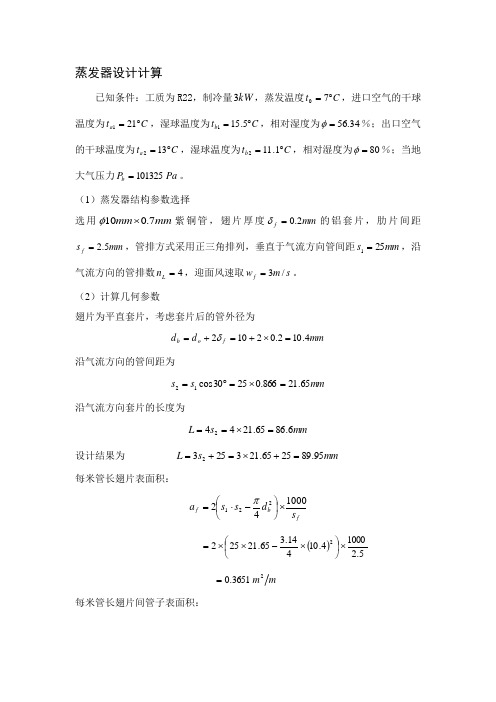
蒸发器设计计算已知条件:工质为R22,制冷量kW 3,蒸发温度C t ︒=70,进口空气的干球温度为C t a ︒=211,湿球温度为C t b ︒=5.151,相对湿度为34.56=φ%;出口空气的干球温度为C t a ︒=132,湿球温度为C t b ︒=1.112,相对湿度为80=φ%;当地大气压力Pa P b 101325=。
(1)蒸发器结构参数选择选用mm mm 7.010⨯φ紫铜管,翅片厚度mm f 2.0=δ的铝套片,肋片间距mm s f 5.2=,管排方式采用正三角排列,垂直于气流方向管间距mm s 251=,沿气流方向的管排数4=L n ,迎面风速取s m w f /3=。
(2)计算几何参数翅片为平直套片,考虑套片后的管外径为mm d d f o b 4.102.02102=⨯+=+=δ沿气流方向的管间距为mm s s 65.21866.02530cos 12=⨯=︒=沿气流方向套片的长度为mm s L 6.8665.21442=⨯==设计结果为 mm s L 95.892565.2132532=+⨯=+= 每米管长翅片表面积:f b f s d s s a 100042221⨯⎪⎭⎫ ⎝⎛-⋅=π ()5.210004.10414.365.212522⨯⎪⎭⎫ ⎝⎛⨯-⨯⨯= m m 23651.0=每米管长翅片间管子表面积:ff f b b s s d a )(δπ-=()5.210002.05.24.1014.3⨯-⨯⨯= m m 203.0=每米管长总外表面积:m m a a a b f of 23951.003.03651.0=+=+=每米管长管内面积:m m d a i i 2027.0)20007.001.0(14.3=⨯-⨯==π每米管长的外表面积:m m d a b b 2003267.00104.014.3=⨯==π肋化系数:63.14027.03951.0===iof a a β每米管长平均直径的表面积:m m d a m m 202983.020086.00104.014.3=⎪⎭⎫ ⎝⎛+⨯==π(3)计算空气侧的干表面传热系数 ①空气的物性 空气的平均温度为C t t t a a f ︒=+=+=1721321221 空气在下C ︒17的物性参数3215.1m kg f =ρ()K kg kJ c pf ⋅=1005704.0=rf Ps m v f 61048.14-⨯=②最窄截面处空气流速()()()()s m s s s s w w f f f d fb 58.52.05.25.24.102525311max =--⨯=--=δ③干表面传热系数干表面传热系数用小型制冷装置设计指导式(4-8)计算15.04.00max 42618.00014.0--⎪⎪⎭⎫⎝⎛⎪⎪⎭⎫⎝⎛+=bo of f a a v d w α15.04.0603267.03951.01048.140104.058.52168.00014.0---⎪⎭⎫ ⎝⎛⎪⎭⎫⎝⎛⨯⨯+=00792.0=()()()km W P c w r pff ⋅=⨯⨯⨯==23232max 402.68704.0100558.5215.100792.0ραα(4)确定空气在蒸发器内的变化过程根据给定的进出口温度由湿空气的焓湿图可得kg g d kg g d kg kJ h kg kJ h 443.7,723.8,924.31,364.432121====。
- 1、下载文档前请自行甄别文档内容的完整性,平台不提供额外的编辑、内容补充、找答案等附加服务。
- 2、"仅部分预览"的文档,不可在线预览部分如存在完整性等问题,可反馈申请退款(可完整预览的文档不适用该条件!)。
- 3、如文档侵犯您的权益,请联系客服反馈,我们会尽快为您处理(人工客服工作时间:9:00-18:30)。
化工原理课程设计说明书设计题目:NaOH水溶液三效并流蒸发装置的设计设计者:班级:化工14组员:谢勋唐洪霆张建雄日期:2016-7-7目录符号说明 (1)一、蒸发装置设计任务书 (3)1.1设计题目 (3)1.2设计任务及操作条件 (3)1.3设计内容 (4)二、前言 (4)2.1概述 (4)2.1.1蒸发及蒸发流程 (4)2.1.2蒸发操作的分类 (5)2.1.3蒸发操作的特点 (5)2.1.4 蒸发设备 (6)三、设计任务 (8)3.1估计各效蒸发量和完成液浓度 (8)3.2估计各效溶液的沸点和总有效传热温差 (8)3.2.1各效由于溶液沸点而引起的温度差损失' (9)3.2.2由于液柱静压力而引起的沸点升高(温度损失) (10)3.2.3由流体阻力引起的温差 (11)3.2.5各效料液的温度和有效总温差 (11)3.3加热蒸汽消耗量和各效蒸发水量的初步计算 (12)3.4估算蒸发器的传热面积 (13)3.5重新分配各效的有效温差 (14)3.6重复上述计算步骤 (15)3.6.1计算各效料液浓度 (15)3.6.2计算各效溶液沸点 (15)3.6.3各效的焓恒算 (16)3.6.4计算蒸发器的传热面积 (18)3.7计算结果列表 (18)四、蒸发器主要工艺尺寸的设计计算 (19)4.1加热管的选择和管数的初步估计 (19)4.2循环管的选择 (20)4.3加热室直径和加热管数目的确定 (21)4.4分离室直径与高度的确定 (22)4.5接管尺寸的确定 (23)4.5.1热蒸汽进口,二次蒸气出口,其中Vs 为流体的体积流量 (23)4.5.2溶液进出口 (24)4.5.3冷凝水出口 (24)五、蒸发装置的辅助设备 (24)5.1气液分离器 (24)5.2.1冷却水量 (25)5.2.2冷凝器直径D (26)5.2.3淋水板的设计 (26)L V符号说明)./(////)./(p 22C m W K kgJ h mh s m g f hkg F hkg D mD md C kg kJ C mb i ︒---------︒--总传热系数,二次蒸汽的焓,高度,重力加速度,校正系数原料液流量,加热蒸汽消耗量,直径,加热管的内径,比热容,管壁厚度,英文字母误差温度损失,对流川热系数,希腊字母质量,单位体积冷却水的蒸汽溶质的质量分率质量流量,蒸发量,分离室的体积,流体得体积流量,蒸发体积强度,-︒-∆︒--------εαCC m W mkg X x hkg Ws hkg W m V sm V s m m U S )./(////)./(233333a//).(//)../(222c P p sm u CT mt Ct m S WC m R kgkJ r R WQ m W q P Pap n n s m kg M mL A e r 压力,流速,温度,管心距,溶液的温度(沸点),传热面积,污垢热阻,气话潜热,雷诺系数总传热速率,热通量,普朗特准数绝对压力,蒸发系统总效数,管数,溶液质量,子周边上的单位时间内通过单位管长度,--︒--︒--︒-----------水流收缩系数管材质的校正系数密度,粘度,导热系数,热利用系数---⋅-︒--ϕφρμλη3/)./(m kg sPa C m W一、蒸发装置设计任务书1.1 设计题目NaOH水溶液蒸发装置的设计1.2 设计任务及操作条件(1)设计任务处理量(): 37083.3 (kg/h)原料液浓度(): 12% 质量分率产品浓度(): 40% 质量分率(2)操作条件加料方式:三效并流加料原料液温度:第一效沸点温度各效蒸发器中溶液的平均密度:ρ1=1014kg/m3,ρ2=1060kg/m3,ρ3=1239kg/m3加热蒸汽压强: 500kPa(绝压),冷凝器压强为 15kPa(绝压)各效蒸发器的总传热系数:K1=1500W/(m2·K),K2=1000W/(m2·K),K3=600W/(m2·K)各效蒸发器中液面的高度: 1.5m各效加热蒸汽的冷凝液均在饱和温度下排出。
假设各效传热面积相等,并忽略热损失。
(3)设备型式中央循环管式蒸发器(4)厂址天津地区(5)工作日:每年300天,每天24小时连续运行。
1.3 设计内容(1)设计方案的简介:对确定的工艺流程及蒸发器型式进行简要论述。
(2)蒸发器的工艺计算:确定蒸发器的传热面积。
(3)蒸发器的主要结构尺寸设计(4)主要辅助设备选型,包括气液分离及蒸气冷凝器等(5)绘制工艺流程图及蒸发器设计条件图(6)设计结果汇总(7)对设计过程的评述和有关问题的讨论二、前言2.1概述2.1.1蒸发及蒸发流程蒸发是采用加热的方法,使含有不挥发性杂质(如盐类)的溶液沸腾,除去其中被汽化单位部分杂质,使溶液得以浓缩的单元操作过程。
蒸发操作广泛用于浓缩各种不挥发性物质的水溶液,是化工、医药、食品等工业中较为常见的单元操作。
化工生产中蒸发主要用于以下几种目的:(1)获得浓缩的溶液产品;(2)将溶液蒸发增浓后,冷却结晶,用以获得固体产品,如烧碱、抗生素、糖等产品;(3)脱除杂质,获得纯净的溶剂或半成品,如海水淡化。
进行蒸发操作的设备叫做蒸发器。
蒸发器内要有足够的加热面积,使溶液受热沸腾。
溶液在蒸发器内因各处密度的差异而形成某种循环流动,被浓缩到规定浓度后排出蒸发器外。
蒸发器内备有足够的分离空间,以除去汽化的蒸汽夹带的雾沫和液滴,或装有适当形式的除沫器以除去液沫,排出的蒸汽如不再利用,应将其在冷凝器中加以冷凝。
蒸发过程中经常采用饱和蒸汽间壁加热的方法,通常把作热源用的蒸汽称做一次蒸汽,从溶液蒸发出来的蒸汽叫做二次蒸汽。
2.1.2蒸发操作的分类按操作的方式可以分为间歇式和连续式,工业上大多数蒸发过程为连续稳定操作的过程。
按二次蒸汽的利用情况可以分为单效蒸发和多效蒸发,若产生的二次蒸汽不加利用,直接经冷凝器冷凝后排出,这种操作称为单效蒸发。
若把二次蒸汽引至另一操作压力较低的蒸发器作为加热蒸气,并把若干个蒸发器串联组合使用,这种操作称为多效蒸发。
多效蒸发中,二次蒸汽的潜热得到了较为充分的利用,提高了加热蒸汽的利用率。
按操作压力可以分为常压、加压或减压蒸发。
真空蒸发有许多优点:(1)在低压下操作,溶液沸点较低,有利于提高蒸发的传热温度差,减小蒸发器的传热面积;(2)可以利用低压蒸气作为加热剂;(3)有利于对热敏性物料的蒸发;(4)操作温度低,热损失较小。
在加压蒸发中,所得到的二次蒸气温度较高,可作为下一效的加热蒸气加以利用。
因此,单效蒸发多为真空蒸发;多效蒸发的前效为加压或常压操作,而后效则在真空下操作。
2.1.3蒸发操作的特点从上述对蒸发过程的简单介绍可知,常见的蒸发时间壁两侧分别为蒸气冷凝和液体沸腾的传热过程,蒸发器也就是一种换热器。
但和一般的传热过程相比,蒸发操作又有如下特点:(1)沸点升高蒸发的溶液中含有不挥发性的溶质,在港台压力下溶液的蒸气压较同温度下纯溶剂的蒸气压低,使溶液的沸点高于纯溶液的沸点,这种现象称为溶液沸点的升高。
在加热蒸气温度一定的情况下,蒸发溶液时的传热温差必定小于加热唇溶剂的纯热温差,而且溶液的浓度越高,这种影响也越显著。
(2)物料的工艺特性蒸发的溶液本身具有某些特性,例如有些物料在浓缩时可能析出晶体,或易于结垢;有些则具有较大的黏度或较强的腐蚀性等。
如何根据物料的特性和工艺要求,选择适宜的蒸发流程和设备是蒸发操作彼此必须要考虑的问题。
(3)节约能源蒸发时汽化的溶剂量较大,需要消耗较大的加热蒸气。
如何充分利用热量,提高加热蒸气的利用率是蒸发操作要考虑的另一个问题。
2.1.4 蒸发设备蒸发设备的作用是使进入蒸发器的原料液被加热,部分气化,得到浓缩的完成液,同时需要排出二次蒸气,并使之与所夹带的液滴和雾沫相分离。
蒸发的主体设备是蒸发器,它主要由加热室和蒸发室组成。
蒸发的辅助设备包括:使液沫进一步分离的除沫器,和使二次蒸气全部冷凝的冷凝器。
减压操作时还需真空装置。
兹分述如下:由于生产要求的不同,蒸发设备有多种不同的结构型式。
对常用的间壁传热式蒸发器,按溶液在蒸发器中的运动情况,大致可分为以下两大类:(1)循环型蒸发器特点:溶液在蒸发器中做循环流动,蒸发器内溶液浓度基本相同,接近于完成液的浓度。
操作稳定。
此类蒸发器主要有a.中央循环管式蒸发器,b.悬筐式蒸发器,c.外热式蒸发器,d.列文式蒸发器,e.强制循环蒸发器。
其中,前四种为自然循环蒸发器。
(2)单程型蒸发器特点:溶液以液膜的形式一次通过加热室,不进行循环。
优点:溶液停留时间短,故特别适用于热敏性物料的蒸发;温度差损失较小,表面传热系数较大。
缺点:设计或操作不当时不易成膜,热流量将明显下降;不适用于易结晶、结垢物料的蒸发。
此类蒸发器主要有a.升膜式蒸发器,b.降膜式蒸发器,c.升—降膜式蒸发器,d.刮板式膜式蒸发器。
本次设计采用的是中央循环管式蒸发器:结构和原理:其下部的加热室由垂直管束组成,中间由一根直径较大的中央循环管。
当管内液体被加热沸腾时,中央循环管内气液混合物的平均密度较大;而其余加热管内气液混合物的平均密度较小。
在密度差的作用下,溶液由中央循环管下降,而由加热管上升,做自然循环流动。
溶液的循环流动提高了沸腾表面传热系数,强化了蒸发过程。
这种蒸发器结构紧凑,制造方便,传热较好,操作可靠等优点,应用十分广泛,有"标准蒸发器"之称。
为使溶液有良好的循环,中央循环管的截面积,一般为其余加热管总截面积的40%~100%;加热管的高度一般为1~2m;加热管径多为25~75mm之间。
但实际上,由于结构上的限制,其循环速度较低(一般在0.4~0.5m/s以下);而且由于溶液在加热管内不断循环,使其组成始终接近完成液的组成,因而溶液的沸点高、有效温度差减小;设备的清洗和检修也不够方便。
三、设计任务3.1估计各效蒸发量和完成液浓度由年处理量267000吨,且每年按照300天计算,每天24小时连续进行,得料液的进料量F 为:37083.3kg/h 用总物料衡算确定总蒸发量W 为:W =F (1-30xx )=37083.3(1-4.012.0)=25958.3kg/h 因并流加料存在自蒸发,且且蒸发中无额外蒸汽引出,可设:W 1:W 2:W 3=1:1.1:1.2 W=W 1+W 2+W 3=3.3W 1W 1=3.33.25958=7866.2kg/h W 2=1.1×7866.2=8652.8kg/h W 3=1.2×7866.2=9439.4kg/h x 1=10W F Fx -=2.7866-3.3708312.03.37083⨯=0.1523 x 2=210W W F Fx --=8.8652-2.7866-3.3708312.03.37083⨯=0.2164 x 3=0.43.2估计各效溶液的沸点和总有效传热温差加热蒸汽压pa 5001K P =(绝压),冷却器的绝压为pa 15’k K P = 假设各效间压力降相等,那么总压力差为:pa 48515-500‘k 1K P P P ==-=∑∆各效间的平均压力差为:pa 7.16134853i K P P ==∑∆=∆ ⨯由各效的压力差可求得各效蒸发室的压力,即:pa 3.338-i 11K P P P =∆=‘pa 6.17621'2K P P P I =∆-=pa 15'k '3K P P ==由各效的二次蒸汽压力,从手册中可查的相应的二次蒸汽的温度和汽化潜能列于下表中: 效数I II III 二次蒸汽压力'i P /kPa338.3176.615二次蒸汽温度'i T /co(即下一效加热蒸汽的温度)137.5 116.6 54二次蒸汽的汽化潜热'i r ,KJ/Kg2150 2218 2366.53.2.1各效由于溶液沸点而引起的温度差损失'∆根据各效二次蒸汽温度(也即相同压力下水的沸点)和各效完成液X ,各效溶液的沸点i t A 分别为:℃6.143084.35.137022.1084.31523.071.2)1523.0(75.15071.275.150022.11523.0142.01x 142.01k 1523.0x 111121211111=+⨯=+==⨯-⨯=-==⨯+=+==y t k t x x y w A 同理可得:℃℃1.80t 7.126t 32==A A则各效由于溶液沸点比水的沸点升高而引起的温度差损失为:℃℃1.2654-1.801.106.116-7.1261.65.137-6.143'33'3'22'2o '11'1==-=∆==-=∆==-=∆T t T t C T t A A A 所以C o '3'2'1'3.421.261.101.6=++=∆+∆+∆=∑∆3.2.2由于液柱静压力而引起的沸点升高(温度损失)由于蒸发器中液柱静压力引起的温度差损失 某些蒸发器在操作时,器内溶液需维持一定的液位,因而蒸发器中溶液内部的压力大于液面的压力,致使溶液内部的沸点较液面处的为高,二者之差即为因液柱静压力引起的温度差损失 根据液柱静力学方程,液层的平均压力为:2'1m ghP P ρ+=,所以Kpa ghP P m 540.34620005.181.911203.33821'11=⨯⨯+=+=ρKpa gh P P m 091.18620005.181.912906.17622'22=⨯⨯+=+=ρKpa gh P P m 742.2520005.181.914601523'33=⨯⨯+=+=ρ对应的饱和温度为:CT opm 4.138'1=CT opm 6.117'2=C T opm 4.63'3=所以C T T opm 9.05.1374.138'1'1''1=-=-=∆C T T o pm 16.1166.117'2'2''2=-=-=∆ C T T o pm 4.9544.63'3'3''3=-=-=∆ 所以C o 3.114.919.0''=++=∑∆''∆3.2.3由流体阻力引起的温差由于管道流体阻力产生的压强降所引起的温度差损失在多效蒸发中末效以前各效的二次蒸汽流到次一效的加热室的过程中由于管道阻力使其压强降低蒸汽的饱和温度也相应降低由此引起的温度差损失即为取经验值C o 1即C o 3211=∆=∆=∆‘’‘’‘’‘’‘所以C o 3=∑∆’‘’ 所以蒸发装置的总温度差损失为:C o''''''6.5633.113.42=++=∑∆+∑∆+∑∆=∑∆3.2.5各效料液的温度和有效总温差由各效二次蒸汽‘i P 及温度差损失’i ∆,即可由下式估算各效料液的温度i t i i i t ∆+=‘T又C o '''1''1'11819.01.6=++=∆+∆+∆=∆ C o '''2''2'221.12111.10=++=∆+∆+∆=∆C o '''3''3'335.3614.91.26=++=∆+∆+∆=∆所以各效料液的温度为C T o 1'115.14585.137t =+=∆+= C T o 2'227.1281.126.116t =+=∆+=C T o 3'335.905.3654t =+=∆+=有效总温差∑∆--=∑∆)(['t K S T T 由手册查的Kpa 绝对压力下饱和蒸汽的温度C T S o 7.151=,汽化潜热为kg J /k 2113r i =,所以C T T K S o '1.416.65-45-7.151t ==∑∆--=∑∆)()( '''∆3.3加热蒸汽消耗量和各效蒸发水量的初步计算第一效的焓衡量式为:()⎥⎦⎤⎢⎣⎡-+='1100,'11111r t t Fc r r D W p η 因沸点进料,故10t t =1W ='1111r r D η1η=0.98-0.7×(1x -0x )=0.98-0.7×(0.1523-0.12) =0.95741W =0.9574×0.215621131D =0.94091D (a )第二效的焓衡量式为:()⎥⎦⎤⎢⎣⎡--+='221,10,'22122)(1r t t c W Fc r r W W W p p η 2η=0.98-0.7×(2x -1x )=0.98-0.7×(0.2164-0.1523) =0.9351 查表得=1,W p c 4.187kj/(kg ·℃)=0p c 3.77kj/(kg ·℃)2W =0.9351()⎥⎦⎤⎢⎣⎡-⨯-⨯+22187.1285.145)187.497.33.37083(2218215011W W =0.87681W +1042.7 (b )第三效的焓衡量式为:()⎥⎦⎤⎢⎣⎡---+='332,2,10,'33233)(21r t t c W c W Fc r r W W W p W p p η3η=0.98-0.7×(3x -2x ) =0.98-0.7×(0.4-0.2164) =0.8515()⎥⎦⎤⎢⎣⎡---⨯+⨯⨯=5.23665.907.128)187.4187.497.33.37083(5.236622188515.02123W W W W=0.59171W +2795.7 (c )1W +2W +3W =25958.3Kg/h (d )联立(a )(b )(c )(d ),解得1D =9523.72kg/h 1W =8960.87kg/h 2W =8899.59kg/h 3W =8097.85kg/h3.4估算蒸发器的传热面积ii i i t K Q S ∆=式中 ---第i 效的传热速率,W 。