第二章 蒸发工艺设计计算
蒸发计算书

蒸发和结晶碱工艺计算书
蒸发工序工艺介绍:
浓度约为5%稀碱水经过沉降罐沉降8小时除去大部分钡沉淀和杂质后,再通过预热器预热到85℃后经过滤器过滤,然后进入碱水储罐。
并通过换热器提升温度后进入五效蒸发,进料温度控制在85℃以上.
蒸发过程中首效进蒸汽压力为0.6Mpa、末效真空度为0.08Mpa,碱水经过五效蒸发后浓缩到30%。
30%碱水经过除碳后进入精制罐沉降8小时。
精制后的碱水经过换热器预热后进入双效蒸发器。
双效蒸发采用的是顺流蒸发,进蒸汽压力为0.6Mpa、末效真空度为0.088Mpa,经过蒸发后碱水浓度达60%。
蒸发好的碱水进入制片系统,使用单辊制片机制片后进入自动包装系统,包装入库。
工艺控制指标:
原料:
05碱%:硫化碱≥4.8%;
五效蒸发器:
05碱进蒸发器温度≥85℃、进料量 121.92t/h
生蒸汽压力:0.6 Mpa;
末效真空度:0.08 Mpa;
出料浓度:30%;
双效蒸发器:
30%碱进蒸发器温度≥80℃;进料量22.55t/h
生蒸汽压力:0.6 Mpa;
末效真空度:0.088 Mpa;
出料浓度:60%;
蒸发计算结果
五效蒸发计算结果(以每小时为基准)
双效蒸发计算结果(以每小时为基准)。
蒸发计算
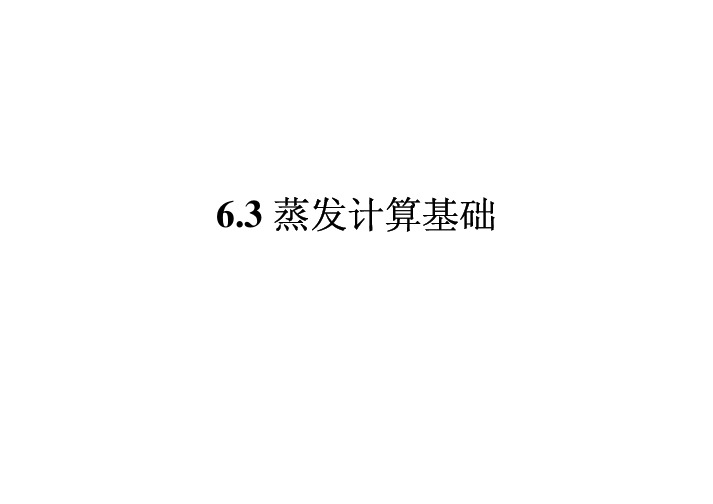
6.3 蒸发计算基础
一、蒸发中的温度差损失•在蒸发操作中,蒸发器加热室一侧是蒸汽冷凝,另一侧为液体沸腾,因此其传热平均温度差应为:
式中:T——加热蒸汽的温度,℃;
t 1——操作条件下溶液的沸点,℃。
1
m
t
T
t−
=
∆
溶液的沸点,不仅受蒸发器内液面压力影响,而且受溶液浓度、液位深度等因素影响。
因此,在计算Δt
时需考虑这些因素。
m
两种不同压力下溶液的沸点差与另一种标准液体在相应压力下的沸点差的比值为常数。
(1)水的关系可以查图表
(2)已知两组数据t A 与t A 0,可求另一t A ’00()A w w A
t K t t t =−+,标准:水
2、液体静压头和加热管内磨擦损失影响:(1)保持一定的液位:(加热管长的1/2-2/3)
(2)动液位→取平均压强―加热管中部p :液面上的压强;L :加热管底部以上液层高;ρ:液体的平均密度。
* 加热管内流速较大时,磨擦损失增大液体平均压强。
/2
m p p p p gL ρ=+∆=+()()p p p t t +∆′′∆−=
3、管道流体阻力产生压降的影响
p C < p 二次蒸汽饱和温度↓
温度差损失十分明显,注意选择加热蒸汽压强!
1′′′∆′′′′′′
∴∆∆∆∆ ℃
=++
三、溶液的浓缩热及焓浓图
NaCl、CaCl2稀释时放热,浓缩时需加热,浓度变大时影响越大。
溶液的焓值由焓浓图查出。
实例:不考虑浓缩热,相同传热面积S下,处理量F与实际的高6%。
蒸发器工艺计算方法示例

思路:一、先确定工艺流程二、求初始各效蒸发水量 1、初定沸点升为15℃2、各效加热蒸汽和料液沸点之间传热温差为20℃(一般为15-20℃)3、确定最后一效二次蒸汽压强,一般为10KPa ,并对应出温度。
4、推出其它各效和生蒸汽温度及压强。
5、设计换热器位置、加热蒸汽或热水来源,冷凝水温度。
6、列方程组求各效蒸发水量,作为初始值。
三、重新计算各效蒸发水量1、确定苦卤沸点升(实验确定,或参考专利“一种沸石法从海水提取硫酸钾的方法”,可初定为127℃) 根据各效蒸发水量比例,确定其余各效料液沸点升。
44332211升升升升t W t W t W t W === 2、根据各效沸点升、传热温差20℃、以及末效温度,从末效开始推出各效状态和生蒸汽状态。
4.2 方案2:四效逆流,并且增加两个换热器 4.2.1系统示意图4.2.2 求初始各效蒸发水量 4.2.2.1 基础数据1、初定沸点升为15℃2、各效加热蒸汽和料液沸点之间传热温差为20℃(一般为15-20℃)3、确定最后一效二次蒸汽压强,一般为10KPa ,并对应出温度。
4、推出其它各效和生蒸汽温度及压强。
5、设计换热器位置、加热蒸汽或热水来源,冷凝水温度。
6、列方程组求各效蒸发水量,作为初始值。
各效常数表图4.2 蒸发系统示意图(1)富钾卤水:F=218997.81kg/h,t0=25℃。
(2)中间卤水:C p0:3.316kJ/(kg·℃)。
(3)总蒸发水量:108110.03kg/h(4)换热器1冷却水出口温度比进换热器的物料温度130.3℃高20℃,即150℃。
(5)换热器2冷却水出口温度比进换热器的物料温度60.3℃高20℃,即80℃。
4.2.2.2 热量衡算1蒸发水衡算:1效二次汽量+2效二次汽量+3效二次汽量+四效二次汽量=总蒸发水量w1+ w2+ w3+ w4=108110.032 Ⅳ效衡算:四效进汽汽化热+四效进料热量=四效出汽热量+四效出料热量2308.03*w3+3.316*218997.81*25=2578.4*w4+3.316* (218997.81-w4)* 60.33换热器Ⅱ衡算:换热器Ⅱ热水变冷水放出的热量=换热器2物料吸收的热量4.223*w1* (115.3-80) =3.316* (218997.81- w4)* (t2-60.3)4 Ⅲ效衡算:Ⅲ效进汽汽化热+Ⅲ效进料热量=Ⅲ效出汽热量+Ⅲ效出料热量2215.57*w2+3.316 * (218997.81-w4)*t2=2644.19*w3+3.316*(218997.81-w4-w3)* 95.35Ⅱ效衡算:Ⅱ效进汽汽化热+Ⅱ效进料热量=Ⅱ效出汽热量+Ⅱ效出料热量2112.87*w1+3.316*(218997.81-w4-w3)*95.3=2215.57*w2+3.316* (218997.81-w4-w3-w2)* 130.26换热器Ⅰ衡算:换热器Ⅰ热水变冷水放出的热量=换热器1物料吸收的热量4.281*D* (185.3-150)= 3.316* (218997.81-w4-w3-w2)* (t1-130.3)7Ⅰ效衡算:Ⅰ效进汽汽化热+Ⅰ效进料热量=Ⅰ效出汽热量+Ⅰ效出料热量1995.90* D+3.316* (218997.81- w4- w3- w2)* t1=2746.40* w1+3.316* (218997.81- w4- w3- w2-w1)* t1 4.2.2.3 MATLAB运算function q=f(p)q(1)= p(4)+ p(5)+ p(6)+ p(7)-108110.03;q(2)= 2308.03*p(6)+3.316*218997.81*25-(2578.4*p(7)+3.316* (218997.81-p(7))* 60.3);q(3)= 4.223*p(4)* (115.3-80) -(3.316* (218997.81- p(7))* (p(2)-60.3));q(4)= 2215.57*p(5)+3.316 * (218997.81-p(7))*p(2)-(2644.19*p(6)+3.316*(218997.81-p(7)-p(6))* 95.3);q(5)= 2112.87*p(4)+3.316*(218997.81-p(7)-p(6))*95.3-(2215.57*p(5)+3.316* (218997.81-p(7)-p(6)-p(5))* 130.2);q(6)= 4.281*p(3)* (185.3-150)- (3.316* (218997.81-p(7)-p(6)-p(5))* (p(1)-130.3));q(7)= 1995.90* p(3)+3.316* (218997.81- p(7)- p(6)- p(5))* p(1)-(2746.40* p(4)+3.316* (218997.81- p(7)- p(6)- p(5)-p(4))* p(1));运行命令:x=fsolve('f2',[1 2 3 4 5 6 7]',optimset('Display','off')) 计算结果:4.2.3 重新计算各效蒸发水量 4.2.3.1 基础数据1、确定苦卤沸点升(实验确定,或参考专利“一种沸石法从海水提取硫酸钾的方法”,可初定为127℃) 根据各效蒸发水量比例,确定其余各效料液沸点升。
蒸发器的设计计算
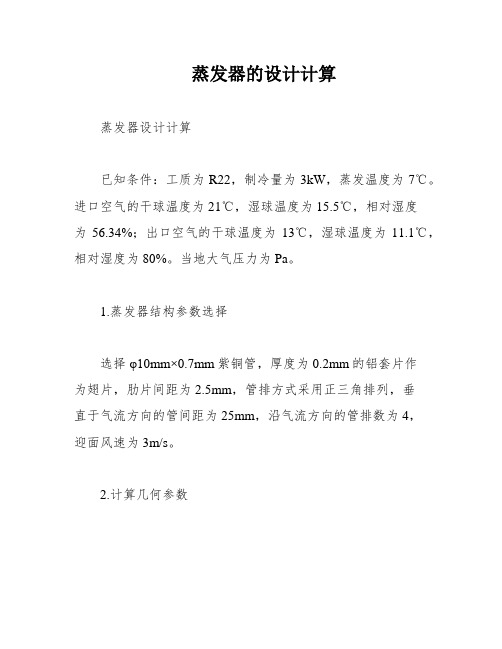
蒸发器的设计计算蒸发器设计计算已知条件:工质为R22,制冷量为3kW,蒸发温度为7℃。
进口空气的干球温度为21℃,湿球温度为15.5℃,相对湿度为56.34%;出口空气的干球温度为13℃,湿球温度为11.1℃,相对湿度为80%。
当地大气压力为Pa。
1.蒸发器结构参数选择选择φ10mm×0.7mm紫铜管,厚度为0.2mm的铝套片作为翅片,肋片间距为2.5mm,管排方式采用正三角排列,垂直于气流方向的管间距为25mm,沿气流方向的管排数为4,迎面风速为3m/s。
2.计算几何参数翅片为平直套片,考虑套片后的管外径为10.4mm,沿气流方向的管间距为21.65mm,沿气流方向套片的长度为86.6mm。
设计结果为每米管长翅片表面积为0.3651m²/m。
每米管长翅片间管子表面积为0.03m²/m。
每米管长总外表面积为0.3951m²/m。
每米管长管内面积为0.027m²/m。
每米管长的外表面积为0.m²/m。
肋化系数为14.63.3.计算空气侧的干表面传热系数1)空气的物性空气的平均温度为17℃。
空气在下17℃时的物性参数为:密度为1.215kg/m³,比热容为1005kJ/(kg·K)。
2)空气侧传热系数根据空气侧传热系数的计算公式,计算得到空气侧的干表面传热系数为12.5W/(m²·K)。
根据给定的数据,蒸发器的尺寸为252.5mm×1mm×10.4mm。
空气在最窄截面处的流速为5.58m/s,干表面传热系数可以用小型制冷装置设计指导式(4-8)计算得到,计算结果为68.2W/m2·K。
在确定空气在蒸发器内的变化过程时,根据进出口温度和焓湿图,可以得到空气的进出口状态点1和点2的参数,连接这两个点并延长与饱和气线相交的点w的参数为hw25kJ/kg。
dw6.6g/kg。
tw8℃。
蒸发浓缩所用设备工艺流程和工艺计算培训教材

温度差损失例题1
对20%NaOH水溶液,求下面各项。 1.查图求101.33kPa压强下该溶液的沸点。 2.分别利用系数校正法和杜林直线法求
50kPa压强下因溶液蒸汽压下降而引起的 温度差损失。( 50kPa下,水的沸点为 81.2℃,气化潜热为2304.5kj/kg)。
蒸发与一般传热的区别
虽然也为传热过程,但蒸发有别于一般传热,表现为 四点:
蒸发与一般传热的区别; 溶液浓度的升高,将导致其物理性质变化—腐蚀性增强,粘度
增大,易结晶结垢,有时产生泡沫,有些溶液有热敏性; 相对于纯溶剂,溶液中含有不挥发性的溶质,其蒸汽压要更
低,在一定操作压强下,沸点比纯溶液要更高。
升膜蒸发器
原料预热至达到或接近沸点,在加热室内膜 状流动(传热效果最好)。
预热原因:使溶液一到达加热管即能产生大 量蒸汽,对溶液上升形成抽吸作用。
适用于:蒸发量大的稀或粘度低的溶液, 有热敏性或易生泡的溶液;但:粘度高, 有晶体析出或结垢情况不适。
降膜蒸发器
适用于:粘度较大、但不是非常大的热 敏性物料;易结晶,结垢溶液不宜。
高 2
计算式: t pm T
gl
pm po 2
上两式:t pm ——液层中部压强下水的沸点; ——液面处的水的沸点,即二次蒸汽温度。
T
温度差损失例题2
在中央循环管式蒸发器内,蒸发25% CaCl2水溶液,已测得二次蒸汽的绝对压 强为40kPa。加热管内液层深度为2.3m, 溶液平均密度为1200 kg/m3 。试求因溶 液液柱静压强引起的温度差损失△’’ , 同时求算出溶液的沸点。
温度差损失例题3
在单效蒸发器中将某种水溶液从10%浓缩 到30%。加热蒸汽为105 ℃的饱和蒸汽, 冷凝器内温度为59℃。液层深度为2m, 溶液平均密度为1080 kg/m3 。已知常压 下溶液因蒸汽压下降而引起的温度差损 失为4 ℃ 。试求:⑴总温度差损失;⑵ 有效温度差;⑶溶液沸点。
矿大北京化工原理蒸发2

解:从附录9分别查出加热蒸汽、二次蒸汽及冷凝水 的有关参数如下。 400 kPa:蒸汽的焓 H=2742.1 kJ /kg,汽化热 r=2138.5 kJ /kg 冷凝水的焓 hw=603.61 kJ /kg,温度T=143.4℃ 50 kPa:蒸汽的焓H’=2644.3 kJ /kg,汽化热 r’=2304.5 kJ /kg,温度T’=81.2℃ (1)考虑浓缩热时 ①加热蒸汽消耗量及单位蒸汽耗量
管外侧:蒸汽 冷凝按膜式 算; 管内侧:沸腾 影响因素多。
3)蒸发器的热负荷
Q
若加热蒸汽的冷凝水在饱和温度下排除,且忽略热 损失,则蒸发器的热负荷为
Q Dr
(5-26)
上面算出的传热面积,应视具体情况选用适当的安 全系数加以校正。
【例3】 在单效蒸发器中每小时将5400 kg、20%NaOH水溶
pdi L
0.31
L 1 v
0.23
(5-30)
s —— 沸腾管材质的校正系数,钢、铜为1,不锈 式中 钢、铬、镍为0.7,磨光表面为0.4;
p ——绝对压强,Pa。
应注意式5-29及式5-30中的 按出口气体的流量计算。
Re L
均按入口的液体流量计算,
N u 0.008 Re L
0.8
PrL
0.8
0.6
w L
0.6
0.38
L di um L c pL L w i 0.008 d i L L L
0.38
Rev
4)降膜蒸发器
降膜蒸发器的操作与整个加热面上是否布满液膜有密切 关系,因此这种蒸发器的传热系数计算式随液体在单位时间 内单位管子周边上流过的质量M而变,即 当
多效蒸发器设计计算
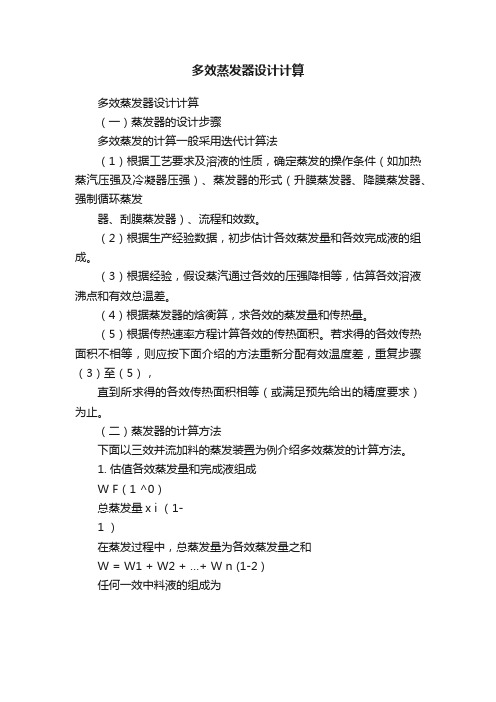
多效蒸发器设计计算
多效蒸发器设计计算
(一)蒸发器的设计步骤
多效蒸发的计算一般采用迭代计算法
(1)根据工艺要求及溶液的性质,确定蒸发的操作条件(如加热蒸汽压强及冷凝器压强)、蒸发器的形式(升膜蒸发器、降膜蒸发器、强制循环蒸发
器、刮膜蒸发器)、流程和效数。
(2)根据生产经验数据,初步估计各效蒸发量和各效完成液的组成。
(3)根据经验,假设蒸汽通过各效的压强降相等,估算各效溶液沸点和有效总温差。
(4)根据蒸发器的焓衡算,求各效的蒸发量和传热量。
(5)根据传热速率方程计算各效的传热面积。
若求得的各效传热面积不相等,则应按下面介绍的方法重新分配有效温度差,重复步骤(3)至(5),
直到所求得的各效传热面积相等(或满足预先给出的精度要求)为止。
(二)蒸发器的计算方法
下面以三效并流加料的蒸发装置为例介绍多效蒸发的计算方法。
1. 估值各效蒸发量和完成液组成
W F(1 ^0)
总蒸发量x i (1-
1 )
在蒸发过程中,总蒸发量为各效蒸发量之和
W = W1 + W2 + …+ W n (1-2 )
任何一效中料液的组成为。
食品工程原理课程设计(食品科学与工程专业)

2010级食品科学与工程专业食品工程原理课程设计授课时间:2012——2013年度第 1 学期题目:双效并流降膜式果汁浓缩装置课程名称:化工原理课程设计专业年级:食品科学与工程2010级学号:1005100110姓名:陈建成绩:指导教师:谢毅2013年7月10日课程设计任务安排表食品科学工程学院班级:2010级食品科学与工程专业食品101班课程名称:化工原理课程设计填写时间:_2013_年_7月_10_日主要符号说明目录第一章前言 (03)第二章蒸发工艺设计计算 (09)2.1蒸发溶液浓度计算 (09)2.2 溶液沸点和有效温度差的确定 (09)2.3加热蒸气消耗量和各效蒸发水量的初步计算 (12)2.4蒸发器传热面积估算 (14)2.5重新分配各效的有效温差 (15)2.6重复上述步骤 (15)2.7再重新分配各效的有效温差 (18)2.8再重复上述步骤 (18)2.9计算结果列表 (21)第三章蒸发器的主要结构尺寸的计算 (21)(1)加热管的选择和加热管数的初步估算 (21)(2)加热室直径及加热管数目的确定 (22)( 3 )分离室直径和高度的确定 (22)( 4 )接管尺寸的确定 (23)第四章. 蒸发装置的辅助设备的选用计算 (25)第五章.双效并流蒸发器结构尺寸确定 (28)第六章. 本次化工设计附图 (30)第七章. 设计总结 (32)第八章.参考文献 (34)第一章前言概述课程设计是本课程教学中综合性和实践性较强的教学环节,是理论联系实际的桥梁,是学习化工设计基本知识的初次尝试。
通过课程设计,要求能够综合运用本课程和前修课程的基本知识进行融会贯通,并在规定的时间内完成指定的化工设计任务,从而得到化工工程设计的初步训练。
本次设计的主要是双效蒸发部分。
1 .蒸发及蒸发流程蒸发是采用加热的方法,使含有不挥发性杂质(如盐类)的溶液沸腾,除去其中被汽化单位部分杂质,使溶液得以浓缩的单元操作过程。
- 1、下载文档前请自行甄别文档内容的完整性,平台不提供额外的编辑、内容补充、找答案等附加服务。
- 2、"仅部分预览"的文档,不可在线预览部分如存在完整性等问题,可反馈申请退款(可完整预览的文档不适用该条件!)。
- 3、如文档侵犯您的权益,请联系客服反馈,我们会尽快为您处理(人工客服工作时间:9:00-18:30)。
化工原理课程设计说明书●班级:●姓名:●组员:●学号:●日期:●指导老师:目录一.概述………………………………………………………………1-1蒸发操作特点……………………………………………………1-2蒸发操作分类……………………………………………………1-3蒸发设备…………………………………………………………1-4蒸发流程示意图…………………………………………………二.蒸发设计计算……………………………………………………2-1完成液浓度和各效水分蒸发量的计算…………………………2-2各效溶液的沸点和总有效温度差估算…………………………2-3加热蒸汽消耗量的计算…………………………………………2-4传热系数的确定…………………………………………………2-5有效温差在各效的分配…………………………………………2-6蒸发器传热面积计算……………………………………………三.蒸发器主要结构尺寸计算………………………………………3-1加热管的选择和管数的初步估计………………………………3-2循环管的选择……………………………………………………3-3加热管的直径以及加热管数目的确定…………………………3-4分离室直径和高度的计算………………………………………3-5接管尺寸的确定…………………………………………………四.蒸发装置的辅助设备……………………………………………4-1气液分离器………………………………………………………4-2蒸汽冷凝器………………………………………………………4-3真空泵的选型……………………………………………………4-4预热器的选型……………………………………………………五.主要设备强度计算及校核………………………………………5-1加热室的强度校核………………………………………………5-2蒸发室的强度校核………………………………………………5-3支座的选择与强度校核…………………………………………六.设计总结…………………………………………………………6-1设计结果汇总表………………………………………………6-2设计评价………………………………………………………6-3心得体会………………………………………………………参考文献………………………………………………………………第一章概述1—1蒸发操作的特点蒸发的目的是是溶剂和溶质分离,但溶液中的含溶质的数量不变,而溶剂气化速率只取决于在传热速率,即蒸发是传热过程。
所以蒸发器也是一种换热器。
然而,和一般传热过程相比,蒸发需要注意以下几点:(1)沸点升高:蒸发的物料是溶有不挥发物质的溶液由拉乌尔定律可知,在相同温度下,其蒸发气压较纯溶剂的低,因此在相同压力下,溶液的沸点就高于纯溶剂的沸点。
故当加热温度一定时,蒸发溶液时的传热温度差就比蒸发纯溶剂的小,并且溶液的浓度越大,这种影响也越显著。
这是蒸发需要考虑的一个问题。
(2)能量的回收与利用:蒸发时汽化的溶剂量是较大的,需要消耗大量的加热蒸汽。
如何充分利用热量,使单位质量的加热蒸汽能除去较多的水分,以及如何提高加热蒸汽的经济程度(例如采用多效蒸发或其他措施),是蒸发要考虑的另一个问题。
(3)物料的工艺恶特性:蒸发的溶液本身常具有某些特性,例如有些物料在浓缩时可能结垢或析出结晶;有些热敏物料在高温下易分解变质;有些则具有较大的粘度或较强的腐蚀性等等。
如何根据物料的这些特性和工艺要求选择适宜的蒸发方法和设备,也是蒸发必须考虑的问题。
1—2蒸发操作分类(1)按操作空格间的压力可分为:常压加压或减压(即真空)蒸发。
对于大多数无特殊要求的溶液,常采用常压加压或减压操作均可。
但对热敏性料液,如抗生素溶液、果汁等的蒸发,为了保证产品的质量,需要在减压下操作。
(2)按二次蒸汽利用的情况可分为单效和多效多效蒸发。
若产生的二次蒸汽不再利用,而直接送冷凝器冷凝除去的蒸发操作,称为单效蒸发。
若将二次蒸汽通到下一压力较低的蒸发器作为加热蒸汽,将多个蒸发器串联,使加热蒸汽在蒸发过过程中得到多次利用的蒸发过程称做多效蒸发。
1—3蒸发设备1.目前常用的间壁传热蒸发器,按溶液在蒸发器中停留的情况,大致可分为循环型和单程型两大类。
(1)循环型蒸发器:中央循环管式蒸发器、悬眶式蒸发器、外热蒸发器、列文式蒸发器。
(2)单程型蒸发器:降膜式蒸发器、升膜式蒸发器、刮板式蒸发器。
2.蒸发辅助设备:除沫器、冷凝器和真空装置。
我们这次设计采用的是三效顺流蒸发法。
顺流法其料液和蒸汽成并流。
优点:各效间有较大的压差,料液能自动从前效进入后效,因而各效间可省去输料泵;前效的操作温度高于后效,料液从前效进入后效呈过热状态,可以产生自蒸发,在各效间不必设预热器;由于辅助设备少,装置紧凑,管路短,因而温度损失;装质的操作简便,工艺条件稳定,设备维修工作减少。
缺点:由于后效的温度低、浓度大,因而料液的粘度增大,降低了传热系数。
因此对于随浓度的增加其粘度增加很大的料液是不宜采取并流的。
亦就是说并流操作只适用于粘度不大的料液。
1—4 蒸发流程示意图第二章 蒸发工艺设计计算1.水分蒸发量和完成液浓度计算总蒸发量: X 0=0.1 X n =0.4 F =5×107320×24=6510㎏/h总蒸发量:nWnW W ii==∑因为并流加热,蒸发中无额外蒸汽引出,可设 2.1:1.1:1::321=W W W W =W 1+W 2+W 3=3.3W 1W 1=1479.5㎏ W 2=1627.5㎏ W 3=1775.5㎏ X 1=001094.125.147965101.06510=-⨯=-W F FX 913.0X 2102=--W W F FX 4.003=-=W F FX X2.各效溶液的沸点和有效总温差可认为各效压力降相等,则总压力差为:∑=⨯+=-=KPaPP P K4819.1018.0400'1各效间平均压力差KPaP 16034813P ===∆∑由各校的压力差可求得各效蒸发室的压力:KPa P P P i 2401604001'1=-=∆-=KPa P P P i 80160240021'2=⨯-=∆-= KPa P P K 81''3-==根据吉辛科法,(引自《化学工程手册》第20页),△‘=0.0162 常∆rT i'(△常表示常压下沸点升高) 解得:△′=△1‘+△1"+△1"′=1.27+1.75+3.1=6.11℃查《化工工艺设计手册》可知:/10131Kg =ρm 3 /10662Kg =ρm 3 /12423Kg =ρm 3由''i Ai i T t -=∆ 得''i i Ai T t +∆= 得1.1391=A t ℃ 5.1182=A t ℃ 4.633=A t ℃(2)由静压引起的△″各效液层的平均压力为:P av =2'gLPav ρ+(取液高为1米, 管长2米)所以,KPa gLP av 6.3462.181.9120.13402P '11av =⨯⨯+=+=ρ同理P av2=186KPa P av3=26.4KPa由《化工原理》可查得对应的饱和蒸汽温度为5.138'1=av P T ℃ 9.117'2=av P T ℃9.61'3=av P T ℃ 所以7.08.1375.138'1'"11=-=-=∆T T av P ℃ 同理可得:=∆"2 1.1℃ 6.1"3=∆℃ ∑=∆4.3"℃(3)由流动阻力引起的温度差损失可取经验值1℃,所以∑=∆3"'℃综上:∑=∆5.12"'℃(4)各效料液的温度和有效总温差: 由各校二次蒸汽压力'i P 及温度差损失i∆,即可由下式估算料液的温度ii i T t ∆+='318.03.5"'1"1'11=++=∆+∆+∆=∆℃ 8.315.14.8"'2"2'22=++=∆+∆+∆=∆℃ Δ3=Δ3′+Δ3"+Δ3′′′=3.1+1.6+1=5.7℃各效料液温度为 t 1=T 1′+∆1=137.8+3=40.8℃ t 2=T 2′+∆2=116.8+1.1=118℃ t 3=T 3′+∆3=60.3+1.6=61.9℃查得400KPa 下饱和蒸汽温度为151.79℃ 气化潜热为2112.9KJ 所以有效总温差为∑Δt =(T s −T k ′)−∑Δ=(151.8−60.3)−12.4=79.1℃3.加热蒸汽消耗量和各效水分蒸发量的初步估算第一效:482.77W 1=η1=(D 1r 1r 1+FC p0t 0−t 1r 1’) 沸点进料t 0=t 1 所以 ηi =0.98−0.7Δx i 代入数据得η1=0.9540W 1=η1D 1r 1r 1‘=0.9520D 1 查《化工原理≫得t 1=140.8℃时 C水=4.287KJ Kg·Kx w <0.2时,查≪传热蒸发与冷凝操作实训≫得C P 0=C 水(1−x w 1)=3.732KJ ㎏·K第二效: W 2=η2=[W 1r 2r 2’+(FC p0−W 1C p w )t 1−t 2r 2‘]=0.9293W 1+250.22η2=0.98−0.7×(0.1913−0.1294)=0.9637 W 2=η2×[W 1r 2r 2′+(Fc P0−W 1C pw )t 1−t 2r 2′]=0.8075W 1+234.38第三效:η3=0.98−0.7△x 3=0.9.8−0.7(0.4−0.1913)=0.8339W 3=η3[W 3r 3r 3′+(F C P0−W 1C P W )t 2−t3r 3′]=0.8339[2213.82354.3W 2+(6510×3.732−4.287W 1)×118−61.92354.3]=0.7839W 2−0.0852W 1+482.77又W 1+W 2+W 3=4882.5联立上面各式解得:W 1=161.5 W 2=1638.9 W 3=1630.1 D 1=1694.94.传热系数K 的确定(此计算K 的方法出自《化工基本过程与设备》) K 1=11α1+∑δλ+1α2取加和项热阻为壁热阻,不计蒸汽一方污垢热阻。
Σδλ=δCR πR+δR λR选38mm×2.5的无缝钢管,λ管=17.4 Σδλ=0.002517.4+0.00052.42=4.89×10−4(㎡·K )∕W冷凝蒸汽对壁的传热系数α1=2.04√r 1ρ12λ13μ1L Δt 14(r 1:加热蒸汽冷凝热;ρ1:液膜平均温度下冷凝液浓度。