pcb背板制作工艺技术
背板加工工艺

能力
Meadville Group
東莞生益電子有限公司
二.能力:
3.厚度 目前SYE能制作的最大厚度为7mm,特殊控制可以做到 10mm。
4.钻孔及电镀 背板对厚径比的要求相对会高一些,SYE现在的厚径比 可以做到12:1。另外对于压接器件的孔径公差也可以做到 +/-0.05mm。
能力
Meadville Group
THANKS!
Meadville Group
能力 Meadville Group
東莞生益電子有限公司
二.能力:
1.板材 目前对于厚背板我们都建议采用HTG的板材。对于一些 高频的背板还需要采用特殊的高频板材才能实现。SYE在背 板板材上常用的有S1170、EG-150T、N4000-13、Mcl-E-679 等等系列的板材。 2.尺寸 目前SYE能制作的最大尺寸为1080mm*584mm。这个尺寸 主要受制于曝光机的尺寸。
能力
Meadville Group
東莞生益電子有限公司
二.能力:
7.表面处理工艺 过去背板一般都采用HASL的工艺加工,由于Rohs的原 因现在有一些背板转为了其他的表面处理方式,如:ENIG、 OSP、Immersion Tin等工艺。但是不同工艺的尺寸是不一 样的。目前Immersion Tin的尺寸能力为20inch*40inch, OSP的能力为610mm*1016mm,ENIG的能力为18inch*22inch。
能力
Meadville Group
東莞生益電子有限公司
二.能力:
8.特殊工艺 由于背板的复杂性和高性能要求,所以背板上也有用 到许多特殊的工艺。首先由于背板可能会采用一些昂贵的 特殊板材,所以为了节约成本,PCB板厂研究了混压的工艺。 另外,由于板子的频率较高、板厚较厚,所以制板时也可 能需要采用背钻的工艺。
pcb生产工艺流程

pcb生产工艺流程PCB(Printed Circuit Board,印刷电路板)是电子设备中不可缺少的一部分,它用来支持和连接电子设备中的各个组件。
PCB的生产工艺流程包含多个步骤,下面将介绍一个常规的PCB生产工艺流程。
首先,PCB的生产过程通常从原料的准备开始。
原料主要包括聚醯胺薄膜(PI)和铜箔。
聚醯胺薄膜作为PCB的基材,而铜箔则用来制作PCB的导线。
在原料准备完成后,第二个步骤是将聚醯胺薄膜放入机器中进行预处理。
预处理包括去除薄膜表面的油污和尘埃,以确保薄膜表面的光洁度。
接下来,将预处理好的聚醯胺薄膜放入暗室中进行光刻。
光刻是将PCB的设计图案通过光线照射到聚醯胺薄膜上的过程。
此过程需要使用紫外线曝光机和光刻胶。
在光刻胶的帮助下,PCB的设计图案会被转移到聚醯胺薄膜上,形成所需的线路路径和元件位置。
完成光刻后,接下来的步骤是蚀刻。
蚀刻是使用化学物质将未覆盖光刻胶的部分溶解掉,从而形成PCB中的导线和元件位置。
蚀刻通常使用酸性溶液,如硫酸或过氧化氢。
蚀刻完成后,需要去除残留的光刻胶。
这一步骤被称为去胶。
去胶可以使用化学物质或机械方法,如刮刀或喷水的方式进行,以确保PCB表面的光洁度和准确性。
完成去胶后,接下来的步骤是钻孔。
钻孔是为了在PCB上穿孔,以便插入元件。
这一步骤通常使用CNC钻床完成,根据设计图案,钻孔机会自动定位并钻孔。
完成钻孔后,需要进行电镀。
电镀是在PCB表面镀上一层金属,通常是镀铜。
这是为了增强PCB导线的连接性和耐用性。
电镀通常是通过浸泡PCB在含有铜离子的化学溶液中,并通过电流在PCB表面形成铜层。
最后一个步骤是PCB的剪裁和检测。
在这一步骤中,会根据实际需求将PCB切割成所需形状和尺寸。
剪裁通常使用数控机床完成。
之后,会对PCB进行一系列的检测,包括导线的连通性、电气特性、外观质量等。
以上就是一个常规的PCB生产工艺流程。
当然,实际生产中可能还涉及到其他步骤和特殊需求,但总体来说,这些步骤可以覆盖PCB生产的主要过程。
pcb制造工艺流程

pcb制造工艺流程PCB(印刷电路板)是电子产品的重要组成部分,用于支撑和连接电子器件。
PCB制造工艺流程主要包括设计、准备、印刷、成型、焊接和测试等步骤。
首先是设计阶段。
在设计阶段,工程师根据电子产品的需求和要求,使用CAD软件进行电路设计。
设计完成后,可以生成Gerber文件作为后续工艺流程的依据。
接下来是准备阶段。
在准备阶段,工程师需要根据设计需求选择合适的基板材料,并将Gerber文件传输给PCB制造工厂。
工厂会根据Gerber文件进行前期工艺准备,包括图形排版、制作工艺板和蚀刻模板等。
然后是印刷阶段。
在印刷阶段,工厂会将准备好的基板放入自动印刷机中。
印刷机会将焊膏沉积在基板上,形成电路的焊盘和焊丝。
印刷完成后,还需要进行光学检测,确保印刷质量符合要求。
接着是成型阶段。
在成型阶段,工厂会使用切割机将大板切割成多个小板。
切割完成后,还需要进行抛丸处理,去除电路板表面的锡渣和污渍。
然后是焊接阶段。
在焊接阶段,工厂会使用自动焊接设备将电子器件和焊盘连接起来。
焊接设备会通过加热和压力的方式,将电子器件的引脚与焊盘熔接在一起。
焊接完成后,还需要进行视觉检测和电气测试,确保焊接连接质量良好。
最后是测试阶段。
在测试阶段,工厂会进行网络测试和功能测试。
网络测试用于检测电路板的连通性和板间短路情况;功能测试则会检测电子产品的各项功能是否正常。
测试完成后,可以标注电路板的序列号和批次号,并进行包装。
总结来说,PCB制造工艺流程包括设计、准备、印刷、成型、焊接和测试等步骤。
通过这些步骤,工厂能够制造出质量可靠的印刷电路板,满足电子产品的需求。
随着科技的不断进步,PCB制造工艺也在不断改进和创新,以提供更好的性能和更高的可靠性。
PCB板生产工艺和制作流程详解

PCB板生产工艺和制作流程详解1. PCB概述PCB(Printed Circuit Board,印刷电路板)是电子元器件的载体,广泛应用于电子设备中。
它通过将导电层与绝缘层的层状结构、金属化孔穴连接导线、表面元器件垫面等工艺,实现了电子元器件的电气连接与机械支撑功能。
本文将详细介绍PCB板的生产工艺和制作流程。
2. PCB板生产工艺PCB板的生产工艺分为以下几个步骤:2.1 制造电路原型在设计PCB板之前,首先需要制造电路的原型。
一般情况下,原型电路板会使用钻石铣床和刀具来切割电路原型。
这个步骤主要是为了验证电路的设计和功能。
2.2 PCB文件设计在验证电路原型无误后,需要使用PCB设计软件进行电路设计。
PCB文件设计包括布局设计和布线设计,其中布局设计是指在PCB板上确定元器件的安装位置和走线方式,而布线设计就是实际进行导线连接的过程。
2.3 压敏膜的制作在PCB板的制作过程中,需要使用一层压敏膜来进行图案的传递。
压敏膜制作的目的是为了防止电路板在制作过程中出现腐蚀和损坏等问题。
2.4 固化剂涂布在图案传递后,需要在印刷的底内表面上涂布上一层固化剂。
固化剂的作用是为了增加PCB板的强度,提高其抗腐蚀性能。
2.5 稀释、固化和清洗在制作PCB板的过程中,还需要进行稀释、固化和清洗等工艺。
稀释剂的作用是为了使涂布的化学物质更加均匀地分布在PCB板上,固化剂则是通过加热使化学物质形成固体,并加强PCB板的结构稳定性。
2.6 钻孔和插孔在完成上述工艺后,需要进行钻孔和插孔的操作。
钻孔的作用是为了将导线连接到PCB板的不同层,插孔则是为了将元器件插入到PCB板上。
2.7 焊接和涂覆在完成钻孔和插孔后,需要进行焊接和涂覆的操作。
焊接是将元器件和PCB板进行电子连接的过程,而涂覆则是为了保护PCB板免受腐蚀和机械损伤。
2.8 组装和测试最后一步是进行组装和测试。
在组装过程中,需要将元器件按照布局设计的位置进行安装,然后进行电气连接和测试。
PCB板生产工艺和制作流程
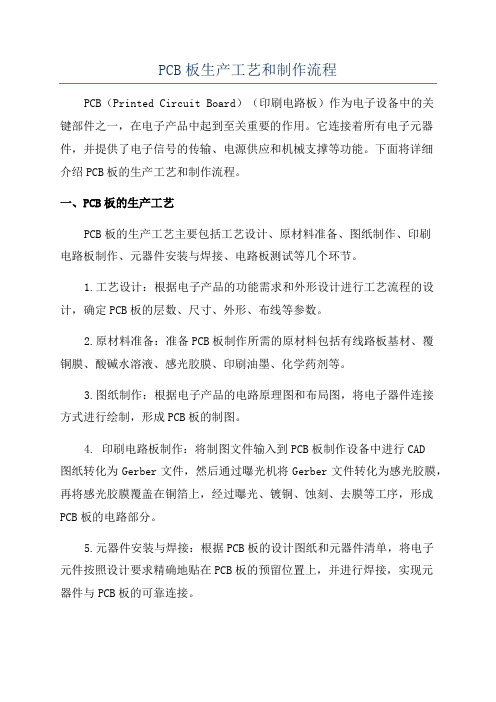
PCB板生产工艺和制作流程PCB(Printed Circuit Board)(印刷电路板)作为电子设备中的关键部件之一,在电子产品中起到至关重要的作用。
它连接着所有电子元器件,并提供了电子信号的传输、电源供应和机械支撑等功能。
下面将详细介绍PCB板的生产工艺和制作流程。
一、PCB板的生产工艺PCB板的生产工艺主要包括工艺设计、原材料准备、图纸制作、印刷电路板制作、元器件安装与焊接、电路板测试等几个环节。
1.工艺设计:根据电子产品的功能需求和外形设计进行工艺流程的设计,确定PCB板的层数、尺寸、外形、布线等参数。
2.原材料准备:准备PCB板制作所需的原材料包括有线路板基材、覆铜膜、酸碱水溶液、感光胶膜、印刷油墨、化学药剂等。
3.图纸制作:根据电子产品的电路原理图和布局图,将电子器件连接方式进行绘制,形成PCB板的制图。
4. 印刷电路板制作:将制图文件输入到PCB板制作设备中进行CAD图纸转化为Gerber文件,然后通过曝光机将Gerber文件转化为感光胶膜,再将感光胶膜覆盖在铜箔上,经过曝光、镀铜、蚀刻、去膜等工序,形成PCB板的电路部分。
5.元器件安装与焊接:根据PCB板的设计图纸和元器件清单,将电子元件按照设计要求精确地贴在PCB板的预留位置上,并进行焊接,实现元器件与PCB板的可靠连接。
6.电路板测试:对已经安装元器件的PCB板进行功能性测试和可靠性检测,确保PCB板的各项电性指标和性能指标符合设计要求。
二、PCB板的制作流程PCB板的制作流程主要包括以下几个步骤:工艺设计、原材料准备、图纸制作、感光及曝光、化学镀铜、蚀刻、电解镀金、钻孔、外层线路图制作、切割成型、表面处理、组装检测等。
1.工艺设计:确定PCB板的层数、尺寸、外形、布线等参数,选择对应的制作工艺。
2.原材料准备:选择适应产品要求的线路板基材、覆铜膜、酸碱水溶液等原材料。
3.图纸制作:根据电子产品的电路原理图和布局图,将电子器件连接方式进行绘制,形成PCB板的制图。
PCB部分工序详解及注意事项
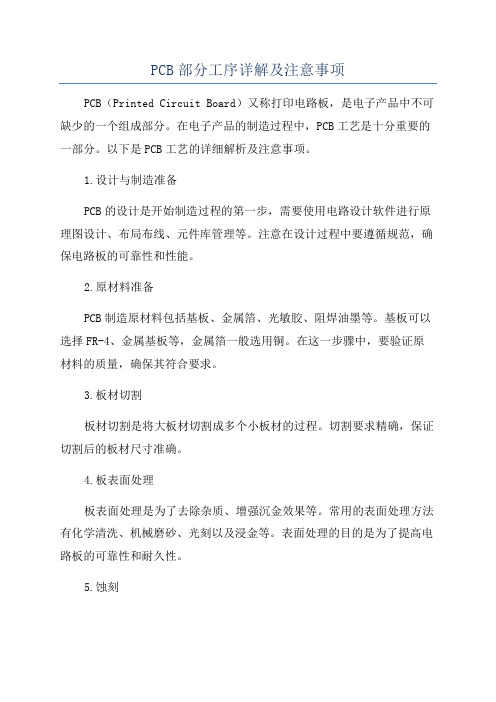
PCB部分工序详解及注意事项PCB(Printed Circuit Board)又称打印电路板,是电子产品中不可缺少的一个组成部分。
在电子产品的制造过程中,PCB工艺是十分重要的一部分。
以下是PCB工艺的详细解析及注意事项。
1.设计与制造准备PCB的设计是开始制造过程的第一步,需要使用电路设计软件进行原理图设计、布局布线、元件库管理等。
注意在设计过程中要遵循规范,确保电路板的可靠性和性能。
2.原材料准备PCB制造原材料包括基板、金属箔、光敏胶、阻焊油墨等。
基板可以选择FR-4、金属基板等,金属箔一般选用铜。
在这一步骤中,要验证原材料的质量,确保其符合要求。
3.板材切割板材切割是将大板材切割成多个小板材的过程。
切割要求精确,保证切割后的板材尺寸准确。
4.板表面处理板表面处理是为了去除杂质、增强沉金效果等。
常用的表面处理方法有化学清洗、机械磨砂、光刻以及浸金等。
表面处理的目的是为了提高电路板的可靠性和耐久性。
5.蚀刻蚀刻是将铜箔蚀刻成制定的线路形状的过程。
常用的蚀刻方法有湿法蚀刻和干法蚀刻。
在蚀刻过程中,要控制好蚀刻剂的浓度和时间,避免过蚀或欠蚀。
6.镀铜镀铜是为了增加线路的导电性能和保护线路不被氧化。
通过电化学方法,在铜箔表面镀一层铜。
在镀铜过程中需要控制好电流密度和镀铜时间,确保铜层的均匀性和厚度。
7.冲孔冲孔是为了在电路板上形成元件引脚的孔洞。
常用的冲孔方法有机械冲孔和激光冲孔。
在冲孔过程中要确保孔径准确,不得损坏板材。
8.焊接焊接是将元件连接到电路板上的过程。
焊接方法有手工焊接和机器焊接。
在焊接过程中,要控制好焊锡的温度和时间,避免焊接不良或短路等问题。
9.包覆胶包覆胶是为了保护电路板上的元件和线路,增强电路板的可靠性和稳定性。
常用的包覆胶有环氧树脂、硅胶等。
包覆胶需要控制好涂胶的厚度和均匀性。
10.后焊接处理后焊接处理包括焊盘复查、割锡、清洁、阻焊油墨涂覆等步骤。
焊盘复查是为了检查焊盘是否连接良好,割锡是为了去除多余的焊锡,清洁是为了去除焊接过程中产生的污垢,阻焊油墨涂覆是为了防止短路和氧化。
pcb制作的基本工艺流程

pcb制作的基本工艺流程PCB制作的基本工艺流程PCB(Printed Circuit Board)即印刷电路板,是电子产品中不可或缺的一部分。
它是一种用于支持和连接电子元件的基板,通过在其表面印刷导电图案来实现电路连接。
PCB制作的基本工艺流程包括设计、制版、印刷、蚀刻、钻孔、插件、焊接和测试等步骤。
1. 设计PCB设计是整个制作过程中最重要的一步。
设计师需要根据电路原理图和元器件布局图,绘制出PCB的布局图和线路图。
在设计过程中,需要考虑电路的稳定性、可靠性、抗干扰性和成本等因素。
设计完成后,需要进行电气规则检查(ERC)和布局规则检查(DRC)等验证,确保设计的正确性和可行性。
2. 制版制版是将设计好的PCB图案转移到铜箔上的过程。
制版通常采用光刻技术,即将PCB图案转移到光刻胶上,再通过曝光和显影等步骤,将图案转移到铜箔上。
制版完成后,需要进行检查和修补,确保图案的完整性和准确性。
3. 印刷印刷是将PCB图案转移到基板上的过程。
印刷通常采用丝网印刷技术,即将PCB图案印刷到基板上,形成导电图案。
印刷完成后,需要进行检查和修补,确保图案的完整性和准确性。
4. 蚀刻蚀刻是将未被印刷的铜箔部分蚀刻掉的过程。
蚀刻通常采用化学蚀刻技术,即将基板浸泡在蚀刻液中,使未被印刷的铜箔部分被蚀刻掉,形成导电通路。
蚀刻完成后,需要进行清洗和检查,确保导电通路的完整性和准确性。
5. 钻孔钻孔是在基板上钻孔,形成插件孔和焊盘孔的过程。
钻孔通常采用机械钻孔技术,即使用钻头在基板上钻孔。
钻孔完成后,需要进行清洗和检查,确保孔的完整性和准确性。
6. 插件插件是将电子元件插入插件孔中的过程。
插件通常采用手工插件技术,即将电子元件手工插入插件孔中。
插件完成后,需要进行检查和修补,确保插件的正确性和稳定性。
7. 焊接焊接是将电子元件与PCB焊接在一起的过程。
焊接通常采用波峰焊接技术,即将PCB浸泡在焊锡池中,使焊锡涂覆在焊盘上,再将电子元件放置在焊盘上,通过加热使焊锡熔化,将电子元件与PCB 焊接在一起。
PCB(印刷电路板)制造过程和工艺详解

PCB(印刷电路板)制造过程和工艺详解pcb(印刷电路板)的原料是玻璃纤维,这种材料我们在日常生活中出处可见,比如防火布、防火毡的核心就是玻璃纤维,玻璃纤维很容易和树脂相结合,我们把结构紧密、强度高的玻纤布浸入树脂中,硬化就得到了隔热绝缘、不易弯曲的pcb基板了--如果把pcb板折断,边缘是发白分层,足以证明材质为树脂玻纤。
光是绝缘板我们不可能传递电信号,于是需要在表面覆铜。
所以我们把pcb板也称之为覆铜基板。
在工厂里,常见覆铜基板的代号是fr-4,这个在各家板卡厂商里面一般没有区别,所以我们可以认为大家都处于同一起跑线上,当然,如果是高频板卡,最好用成本较高的覆铜箔聚四氟乙烯玻璃布层压板。
覆铜工艺很简单,一般可以用压延与电解的办法制造,所谓压延就是将高纯度(>99.98%)的铜用碾压法贴在pcb基板上--因为环氧树脂与铜箔有极好的粘合性,铜箔的附着强度和工作温度较高,可以在260℃的熔锡中浸焊而无起泡。
这个过程颇像擀饺子皮,最薄可以小于1mil(工业单位:密耳,即千分之一英寸,相当于0.0254mm)。
如果饺子皮这么薄的话,下锅肯定漏馅!所谓电解铜这个在初中化学已经学过,cuso4电解液能不断制造一层层的"铜箔",这样容易控制厚度,时间越长铜箔越厚!通常厂里对铜箔的厚度有很严格的要求,一般在0.3mil和3mil之间,有专用的铜箔厚度测试仪检验其品质。
像古老的收音机和业余爱好者用的pcb上覆铜特别厚,比起电脑板卡工厂里品质差了很远。
控制铜箔的薄度主要是基于两个理由:一个是均匀的铜箔可以有非常均匀的电阻温度系数,介电常数低,这样能让信号传输损失更小,这和电容要求不同,电容要求介电常数高,这样才能在有限体积下容纳更高的容量,电阻为什么比电容个头要小,归根结底是介电常数高啊!其次,薄铜箔通过大电流情况下温升较小,这对于散热和元件寿命都是有很大好处的,数字集成电路中铜线宽度最好小于0.3cm也是这个道理。
- 1、下载文档前请自行甄别文档内容的完整性,平台不提供额外的编辑、内容补充、找答案等附加服务。
- 2、"仅部分预览"的文档,不可在线预览部分如存在完整性等问题,可反馈申请退款(可完整预览的文档不适用该条件!)。
- 3、如文档侵犯您的权益,请联系客服反馈,我们会尽快为您处理(人工客服工作时间:9:00-18:30)。
背板制作工艺技术探讨
1.前言
背板(Backplane)是指具有线路和众多排插孔,主要用于承载其它功能性子板和芯片,起到高速信号及大电流传输的一类印制板产品。
背板作为具有专业化性质的一类高端印制板产品,一般具有尺寸大、层数多、厚度大、孔径纵横比高等特点,近年来发展迅速,广泛应用于通讯、航天、医疗设备、军用基站、超级计算机等领域。
背板由于其承载的特殊性能,其设计参数以及需要满足的一些要求与常规印制板产品相比存在巨大差异,技术涉及领域更宽,制作难度较高。
目前,国内能批量生产大尺寸背板的企业屈指可数,大尺寸背板研发及生产技术成为衡量PCB企业技术实力的一个重要指标,背板相关制作技术、检测设备以及专业技术人员的培养是未来背板产业发展的核心。
文章介绍一款整体22层、成品尺寸398 mm×532 mm、背钻孔组数为9组的大尺寸背板产品的关键制作工艺技术。
2.背板制作工艺技术
2.1 产品结构特点
所述印制板为一款大尺寸背板产品,具体结构参数见表1和图1。
图1 大尺寸背板层压结构图
2.2工艺流程设计
根据本款背板产品的结构特点,并结合实际PCB生产制作工艺,确定其生产工艺流程如下。
开料→内层图形→OPE冲孔→内层AOI→棕化→压合→外层钻孔→沉铜→全板电镀→外层图形→图形电镀→背钻孔→外层蚀刻→外层AOI→丝印阻焊→沉镍金→成型→成型后测试→FQC→FQA→包装
2.3工艺制作难点分析及解决方法
2.3.1 镀锡+分段背钻技术
(1)难点描述。
背钻孔是将一个电镀导通后的通孔,使用控深钻孔方法除去一部分孔铜,只保留一部分孔铜而形成的孔,背钻孔的关键作用是在高速信号传输过程中,降低多余孔铜对信号的反射干扰,以保证信号传输的完整性。
目前,背钻孔是成本较低的能够满足高频、高速线路板性能的制作方法。
但实际实施过程中,由于背钻本身的特点及其电路边结构要求等工艺难点,易出现孔内铜丝、堵孔、断钻等品质问题。
使用“前工序→全板电镀→外层图形→图形电镀(镀锡)→蚀刻→背钻→下工序”常规工艺,容易产生孔内披锋、铜丝等问题,如图2所示。
钻孔时,一方面,由于孔壁的电镀铜相对于表面覆铜基材的压延铜结合力稍弱,钻孔时钻断口附近的孔铜容易脱落,造成孔内披锋、铜丝;另一方面,孔内铜厚,一般要求最小厚度≥20 μm,由于铜箔具有较好的延展性,钻孔过程中不容易被切断,易造成孔内披锋问题。
另外,由于L10~L13层铜厚为68.6 μm,其他层铜厚18 μm,板厚4.1 mm,厚度较大,若一次完成背钻,胶渣排泄困难,易发生堵孔,且不利于散热,钻孔时热量集中,容易发生断钻、孔壁不良等问题。
图2 背钻披锋、铜丝不良切片图
(2)改善方案
改用“前工序→全板电镀→外层图形→图形电镀(镀锡)→分段背钻→蚀刻→退锡→飞针检测→下工序”的流程实施背钻,将“背钻”放在“图形电镀”之后,利用锡较铜密度小的特点,提高背钻定位精度和散热;利用蚀刻药水去除孔内铜丝、披锋,并利用高压水洗等水洗段,冲洗干净孔内钻污,防止堵孔。
调整钻针转速50 kr/min,进刀速36 mm/s,退刀速212 mm/s,采用第一次钻要求深镀的10%,第二次钻20%,第三次钻30%,第四次钻40%的“1:2:3:4”分段钻孔技术实施背钻加工。
每次钻完之后都可以更有效的
将钻污排除孔外,避免钻污过量累积产生堵孔现象,并且可以提高内层厚铜钻孔的散热效率,避免热量过大产生的孔内粗糙度过大等不良问题,同时降低断钻率。
图3所示为“1:2:3:4”分段钻孔技术示意图,图4所示为背钻孔合格切片图。
2.3.2 大尺寸背板蚀刻均匀性提升技术
(1)难点描述。
研发过程中,发现背板产品因尺寸较大,上板面容易受到“水池效应(puddling effect)”的影响,蚀刻液在板面上积存不易排走,阻挡了新鲜蚀刻液的补充,导致新鲜的蚀刻液无法直接打在待蚀刻板的板面上,减弱了板面承受的喷射力,造成上板面蚀刻速率低于下板面蚀刻速率的现象. (如图5所示)
图5 “水池效应”示意图
常规蚀刻线喷嘴为圆锥形,喷洒出的药水也为圆锥形,喷淋范围较小,板面局部受喷淋压力过大,而喷嘴之间则容易形成水池效应,导致蚀刻不均;喷嘴的流量及喷射角度受其磨损程度影响大,加上喷嘴容易发生堵塞,导致蚀刻均匀性波动较大;另外,圆锥形喷嘴在蚀刻时,板子的导入边蚀刻效果比后入边蚀刻效果好,因为板子先进入的部分药水尚未堆积,未形成“水池效应”,蚀刻速率较快,后入边进入时,“水池效应”已经形成,蚀刻速率减慢,从而影响整板的蚀刻均匀性。
(2)改善方案
采用“真空蚀刻”方法,如图6所示,在上板面喷淋管之间增加“吸药水”管道,与喷淋头管道交错排列,形成“喷淋蚀刻→吸药水→喷淋蚀刻→吸药水→……”的蚀刻模式,吸药水管道可及时将堆积在板面的药水吸走,为下一个喷淋蚀刻提供新鲜的蚀刻液,防止“水池效应”的形成,大大改善了蚀刻效果。
针对传统喷嘴存在的局限,如图6所示,喷嘴采用扇型设计,扇形喷淋有效增加了药水喷淋的面积,平衡了药水喷淋的压力,同样的喷淋压力下,可使板面受到更均匀的喷淋效果;喷嘴设置与板前进方向呈15°角错开,避免喷嘴间喷射面的交错,减弱板面局部承受的冲击力;另外,为了进一步避免先入边比后入边蚀刻效果好的问题,采用喷管摇摆设计或气动点喷式设计,为药水提供更多的交换效果,达到提升大尺寸背板蚀刻均匀性的目的。
图6 上板面增加吸药水管道示意图(左)及真空蚀刻设备构造图(右)
2.3.3 高厚径比深孔电镀能力提升技术
(1)难点描述
本次制作的背板产品,厚径比为12:1(成品最小孔径0.35 mm,板厚4.1 mm),结构为高频板材与环氧树脂板材混压,含有高频材料、高Tg板材和PP环氧树脂板材。
高频材料含胶量低,在膨松剂作用下,不易软化,采用传统的化学除钻污方法(KMnO4+NaOH)咬蚀,容易产生除钻污不足等问题;而环氧树脂体系,相比高频板材活性较强,化学除钻污药水对它的咬蚀效率快,因而采用传统的(KMnO4+NaOH)化学除钻污方法,极易产生过蚀,从而易造成孔粗糙度过大、灯芯或白化等问题。
采用常规沉铜工艺,由于产品厚径比大,相对于普通产品,孔内容易产生气泡,阻碍了药水的流通,后续容易产生孔无铜、孔铜薄等不良问题(如图7所示)。
针对沉铜次数,及沉铜时震动频率、挂板方式等参数,需要分析探索出一系列配套的调整方案。
对于沉铜后的全板电镀工序,由于板尺寸(398 mm×532 mm)及板厚度(4.1 mm)的限制,我公司采用垂直电镀(龙门线)制作,要求电镀均匀性>90%,采用常规方法,考虑到均匀性极差,难以达到均匀性要求。
图7沉铜不良造成的孔无铜问题切片图
(2)改善方案
采用等离子除钻污方法代替传统的(KMnO4+NaOH)化学除钻污法,等离子体是在高真空条件下利用电能激化气体分子,形成离子或反应性较高的自由基,在进一步电场作用下,与材料表面发生碰撞,进而发生物理、化学反应,除去钻污,并形成一层具有细微凹凸形态的表面结构。
在等离子体化学反应中,起到化学作用的粒子主要是正离子及自由基粒子,对不同材料的作用均匀,所以除钻污效果更好。
经过测试,本产品等离子除钻污参数如表2所示。
沉铜采用隔槽插架,每两块板间距20 mm ~ 24 mm,增加药水的交换空间,避免由于板面积过大,板间距过于紧密而产生的药水流通受阻问题;挂板方向与垂直方向倾斜15°角,在每次板子“入池”时,药水与孔形成一定角度,更容易充实孔内,顺利地将孔内气泡排出,形成良好的药水交换模式;调整震动控制为震25 s停20 s,适当延长震动时间,更有利于深孔内药水的充分交换,并采用多次沉铜,避免一次沉铜产生的深孔漏沉铜,孔内壁空洞、缺口等问题。
全板电镀使用小电流长时间方法制作,为防止上下板均匀性差异,在中途将板上下颠倒180°,倒边制作,提升板面均匀性;类似沉铜原理,合理增加震动频率和震动幅度,便于孔内药水交换。
沉铜、板电具体改善参数见表3。