生产现场八大浪费PPT课件
合集下载
生产中八大浪费PPT课件
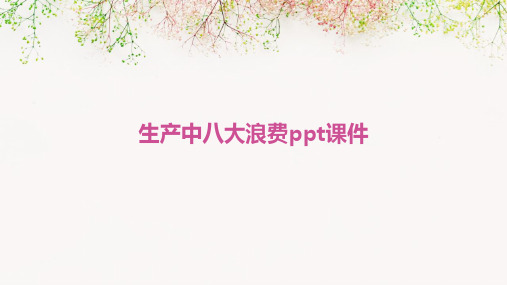
反馈处理
对员工反馈的信息进行及时处理和 跟进,确保问题得到解决和落实。
案例分析法
选择典型案例
经验借鉴
选择生产过程中具有代表性和普遍性 的浪费案例进行分析。
从案例中提炼出可供借鉴的经验和教 训,为减少类似浪费提供参考。
案例剖析
对选定的案例进行深入剖析,了解浪 费的具体情况和原因。
04
减少和消除策略
管理浪费
定义
管理浪费是指企业管理中不必要 的环节、流程或制度所造成的资 源、时间和成本的浪费。
危害
增加管理成本、降低管理效率; 影响企业决策效果和响应速度; 可能导致企业失去市场机会和竞 争优势。
解决方法
优化管理流程和组织结构,减少 不必要的管理环节和制度;实施 信息化和数字化管理手段,提高 管理效率和决策效果;加强员工 培训和管理素质提升,提高员工 对管理要求的认知和执行能力。
设备利用率提高
合理安排生产计划,充分利用设备产能,避免设备闲置和浪费。加强Βιβλιοθήκη 工培训和技能提升员工技能培训
01
针对员工岗位需求,制定个性化的培训计划,提高员工技能水
平和操作效率。
多能工培养
02
鼓励员工学习多种技能,培养多能工,提高员工适应性和灵活
性。
员工激励机制
03
建立合理的激励机制,激发员工积极性和创造力,促进员工持
生产中常见浪费现象
过度生产
生产超出实际需求或计划的产品,导致库存积压和 资金占用。
等待时间
设备或员工在等待下一道工序或资源时产生的空闲 时间。
运输浪费
不必要的物料搬运和运输,以及由此产生的时间和 资源消耗。
生产中常见浪费现象
01
02
对员工反馈的信息进行及时处理和 跟进,确保问题得到解决和落实。
案例分析法
选择典型案例
经验借鉴
选择生产过程中具有代表性和普遍性 的浪费案例进行分析。
从案例中提炼出可供借鉴的经验和教 训,为减少类似浪费提供参考。
案例剖析
对选定的案例进行深入剖析,了解浪 费的具体情况和原因。
04
减少和消除策略
管理浪费
定义
管理浪费是指企业管理中不必要 的环节、流程或制度所造成的资 源、时间和成本的浪费。
危害
增加管理成本、降低管理效率; 影响企业决策效果和响应速度; 可能导致企业失去市场机会和竞 争优势。
解决方法
优化管理流程和组织结构,减少 不必要的管理环节和制度;实施 信息化和数字化管理手段,提高 管理效率和决策效果;加强员工 培训和管理素质提升,提高员工 对管理要求的认知和执行能力。
设备利用率提高
合理安排生产计划,充分利用设备产能,避免设备闲置和浪费。加强Βιβλιοθήκη 工培训和技能提升员工技能培训
01
针对员工岗位需求,制定个性化的培训计划,提高员工技能水
平和操作效率。
多能工培养
02
鼓励员工学习多种技能,培养多能工,提高员工适应性和灵活
性。
员工激励机制
03
建立合理的激励机制,激发员工积极性和创造力,促进员工持
生产中常见浪费现象
过度生产
生产超出实际需求或计划的产品,导致库存积压和 资金占用。
等待时间
设备或员工在等待下一道工序或资源时产生的空闲 时间。
运输浪费
不必要的物料搬运和运输,以及由此产生的时间和 资源消耗。
生产中常见浪费现象
01
02
精益生产八大浪费PPT课件
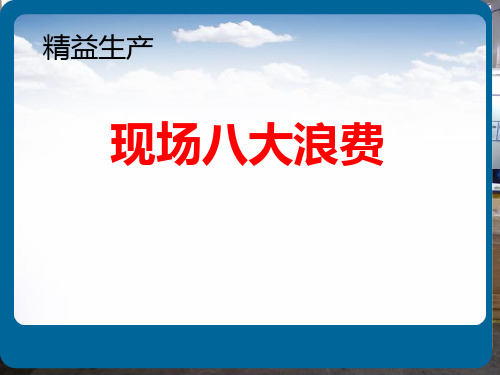
少作业人员,但并非辞退人员,而 是更合理、更有效率地应用人员
20
1.制造过多的浪费
生产的调配方案:
前提:
•窗框班每班借出5人至硬包边班,
6月份金客订单由原先5980台降
由13人生产窗框,标时30pcs/hr
到5500台,公司的生产稼动偏低,近 •前桥线抽调两人至滑道线,12hr
期又决定6月23日~6月30日停产休假, 造成我公司库存品积压过多,生产能
16
浪费的层次
第一层次:过剩生产能力 第二层次:工作进度过度 第三层次: 第四层次:
精益生产
过多人员 过剩设备 过剩物料 过剩厂房
制造过剩
库存过剩
多余仓库 多余库存管理 多余搬运 多余搬运设备
隐藏等待 隐藏等待
17
1.制造过多的浪费
八大浪费
无法保证可卖出的产品做了太多
表现形式:
是浪费的源头
•物流阻塞 •库存、在制品增加 •产品积压造成不良发生 •资金回转率低 •材料、零件过早取得 •影响计划弹性及生产系统的适应能力
表现形式: •自动机器操作中,人员的“闲视”等待
•作业充实度不够的等待 •设备故障、材料不良的等待 •生产安排不当的人员等待 •上下工程间未衍接好造成的工程间的等待
22
2.等待的浪费
八大浪费
原因:
对策:
•生产线布置不当,物流混乱
•采用均衡化生产
9
精益生产的简单系统
竞争力提升
品质提升 合理化成本降低 形象提升
改善 消除浪费 标准化 现场5S
动作改善、作业流程改善、物流改善、设 备模夹治具改善、品质改善、管理改善等
八大浪费、三无工程等
动作标准化、作业流程标准化、操作流程 标准化、包装运输标准化等
20
1.制造过多的浪费
生产的调配方案:
前提:
•窗框班每班借出5人至硬包边班,
6月份金客订单由原先5980台降
由13人生产窗框,标时30pcs/hr
到5500台,公司的生产稼动偏低,近 •前桥线抽调两人至滑道线,12hr
期又决定6月23日~6月30日停产休假, 造成我公司库存品积压过多,生产能
16
浪费的层次
第一层次:过剩生产能力 第二层次:工作进度过度 第三层次: 第四层次:
精益生产
过多人员 过剩设备 过剩物料 过剩厂房
制造过剩
库存过剩
多余仓库 多余库存管理 多余搬运 多余搬运设备
隐藏等待 隐藏等待
17
1.制造过多的浪费
八大浪费
无法保证可卖出的产品做了太多
表现形式:
是浪费的源头
•物流阻塞 •库存、在制品增加 •产品积压造成不良发生 •资金回转率低 •材料、零件过早取得 •影响计划弹性及生产系统的适应能力
表现形式: •自动机器操作中,人员的“闲视”等待
•作业充实度不够的等待 •设备故障、材料不良的等待 •生产安排不当的人员等待 •上下工程间未衍接好造成的工程间的等待
22
2.等待的浪费
八大浪费
原因:
对策:
•生产线布置不当,物流混乱
•采用均衡化生产
9
精益生产的简单系统
竞争力提升
品质提升 合理化成本降低 形象提升
改善 消除浪费 标准化 现场5S
动作改善、作业流程改善、物流改善、设 备模夹治具改善、品质改善、管理改善等
八大浪费、三无工程等
动作标准化、作业流程标准化、操作流程 标准化、包装运输标准化等
《工厂常见的八大浪费及解决办法》PPT课件模板
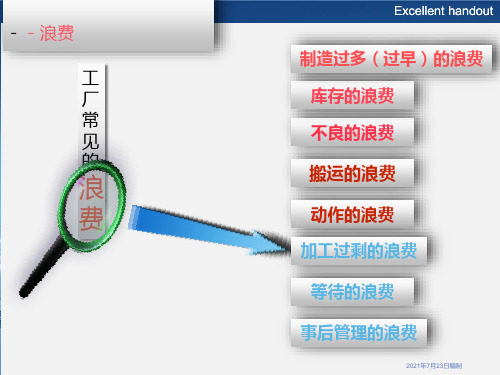
2021年7月23日编制
八大浪费之六 -加工过剩的浪费
Excellent handout
过剩设计
?是指在产品、技术规范、生 产组织、人事安排等等上面给 予的充分安全系数
?查找一下,我们有没有这样 的浪费
2021年7月23日编制
八大浪费之六 -加工过剩的浪费
Excellent handout
外部沟通与内部沟通 结合,理解客户要求
1、固定资产的闲置浪费 2、职能的闲置或重叠的浪费 3、流程复杂低效的浪费 4、人员的闲置浪费 5、信息的闲置浪费
2021年7月23日编制
八大浪费之八 -事后管理的浪费
(四)管理浪费的无序浪费 1、职责不清的无序 2、业务能力低下造成的无序 3、有章不循造成的无序 4、业务流程的无序
Excellent handout
(二)管理协调不利的浪费 1、订单或项目进程未按计划推进,协调无序 2、直接领导安排执行不力,等老板直接安排 3、信息传递或理解不准确,选择性执行或传递
4、没有固化的流程或订单流程的协调不顺畅
2021年7月23日编制
八大浪费之八 -事后管理的浪费
Excellent handout
(三)管理浪费的闲置浪费
2、能否去除所谓的市场产品?
3、加工工艺、物流运输、流程、加
工量及工序安排是否最经济?是否
可以合并或删除?
4、能否放宽公差及品质规格?
5、能否放宽材料利用率?或代替
率?
6、能否实施并线或半自动化或自动
化生产?
7、能否直接缩减或删除不必要的加
工
。。。。。
2021年7月23日编制
八大浪费之七 -等待的浪费
八大浪费之六 -加工过剩的浪费
八大浪费及改善技法(共27张PPT)
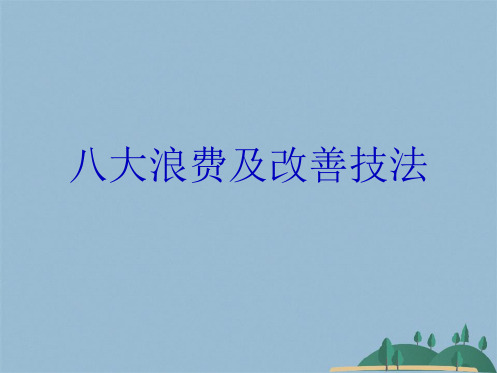
• 调整看板的数量
待机 运输
加工
• 通过作业观察,修改工序安排方法,重新安排作业
• 实现工序同期化,使各个工序直接连接上 (流水生产)
• 区分人工和设备作业,用机械来替代人工作业
(加工时间 加工工时)
• 必须得在实物挂上看板
库存
• 维持适当的看板数量
• 不把同一个产品放在一个场所
工作
• 修改设备布置及操作法,改善标准作业
八大浪费及改善技法
在我们周围的工作区域是否存在这些现象
堆积库存
过量走动
设备故障
过多运输
组织复杂!汇报繁琐!
会议!会议!会议! 2
无附加价值的工作
有附加价值的工作
何谓浪费:
不产生任何附加价值的
动作、方法、行为和计划
顾客不想付钱的所有行为 不能创造出附加价值的所有现 象和其结果 除净作业以外的所有行为都 是浪费
•人员过剩 动作、方法、行为和计划
加强教育培训与动作训练
Байду номын сангаас
定8. 期的•设设备备、模稼夹具动保养过剩
•生产速度快并不代表效率高
•生产浪费大 按物品的移动,详细观察现场。
设备配置不当或设备能力差
•设备余力并非一定是埋没成本
•业务订单预测有误
•生产能力过剩时,应尽量先考虑减
•生产计划与统计错误
少作业人员,但并非辞退人员,而
- 将现场和现物分别当作管理单位和管理对象,并直接观察现实情况,获取信息,从而做出判断
对作业进行反问 - 站在作业当中有浪费因素的观点,详细揭示作业工序
追究功能的必要性 - 进行调查追究其功能是否必要
浪费无处不在 - 假设除本质性功能外,到处都有浪费,揭示浪费因素
待机 运输
加工
• 通过作业观察,修改工序安排方法,重新安排作业
• 实现工序同期化,使各个工序直接连接上 (流水生产)
• 区分人工和设备作业,用机械来替代人工作业
(加工时间 加工工时)
• 必须得在实物挂上看板
库存
• 维持适当的看板数量
• 不把同一个产品放在一个场所
工作
• 修改设备布置及操作法,改善标准作业
八大浪费及改善技法
在我们周围的工作区域是否存在这些现象
堆积库存
过量走动
设备故障
过多运输
组织复杂!汇报繁琐!
会议!会议!会议! 2
无附加价值的工作
有附加价值的工作
何谓浪费:
不产生任何附加价值的
动作、方法、行为和计划
顾客不想付钱的所有行为 不能创造出附加价值的所有现 象和其结果 除净作业以外的所有行为都 是浪费
•人员过剩 动作、方法、行为和计划
加强教育培训与动作训练
Байду номын сангаас
定8. 期的•设设备备、模稼夹具动保养过剩
•生产速度快并不代表效率高
•生产浪费大 按物品的移动,详细观察现场。
设备配置不当或设备能力差
•设备余力并非一定是埋没成本
•业务订单预测有误
•生产能力过剩时,应尽量先考虑减
•生产计划与统计错误
少作业人员,但并非辞退人员,而
- 将现场和现物分别当作管理单位和管理对象,并直接观察现实情况,获取信息,从而做出判断
对作业进行反问 - 站在作业当中有浪费因素的观点,详细揭示作业工序
追究功能的必要性 - 进行调查追究其功能是否必要
浪费无处不在 - 假设除本质性功能外,到处都有浪费,揭示浪费因素
八大浪费概念-PPT课件

四.动作浪费
(二) 浪费的表现:
人(Man)﹕动作无价值﹔劳动强度大﹔寻找﹔ 机(Machine)﹕等待﹔ 料(Material)﹕易损伤 法(Method)﹕程序复杂;
四.动作浪费
动作浪费的12种表现形式
1.两手空闲 2.单手空闲 3.作业时动作突然停止 4.左右手互换 7.移动中变换状态 8.不懂操作技巧 9.作业时动作突然停止 10.伸背
六.搬运浪费
移动浪费消除
卡車
卡車
改善前
改善后
七.等待浪费
(一)定义 是指两个相互依赖的变量不完全同步所造成的空闲时间
七.等待浪费
(二)特点 人等机器
机器等人
人等人 不平衡的操作 对设备故障漠不关心 计划外的停机
七.等待浪费
(三)解决方法
• 生产过程的连续性 – 生产各阶段物流处于不停的运动之中,流程尽可能短; • 生产过程的比例性 – 各生产环节的能力保持符合产品制造数量和质量要求的比例关系; • 生产过程的均衡性 – 保证生产按计划、有节奏的进行,在相同的时间间隔内,生产大致相同数量 递增数量的产品; • 生产过程的准时性 – 在需要的时候,按需要的数量生产所需的产品和零部件; • 生产过程的柔性 – 适应性,加工制造的灵活、可变、可调节性;
八.管理浪费
(三) 浪费的产生:
管理能力﹕素质; 执行力(速度/准度/精度);
技朮层次﹕认知高度﹔把握度﹔(相对)
标准化﹕可行度﹔推广度﹔(点线面) 企业素质﹕整体素质﹔
The End !
注重实操,学以致用
前工序之供给量﹐超过后工序之需求量
多
早
快
二. 过量生产浪费
(二) 后果 直接﹕搬运﹐堆积﹐库存﹐超过终点需求而造成的拆卸﹑报废 等……
企业八大浪费培训ppt课件ppt
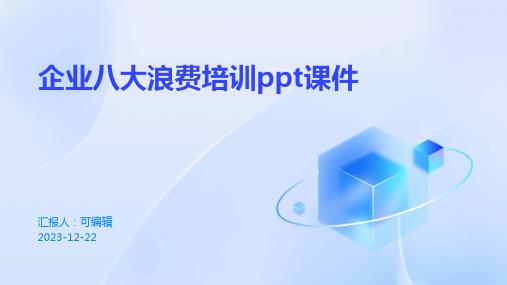
题导致的制程问题。
提高操作员技能水平
定期对操作员进行培训和考核,提高 操作员技能水平,减少操作误差导致 的制程问题。
优化工艺参数设置
根据实际生产情况,不断优化工艺参 数设置,减少制程中的误差和不良品 率。
THANKS
感谢观看
ABCD
预测不准确
企业对市场需求预测不准确,导致库存过多或过 少,影响生产和销售。
生产计划不准确
生产计划不准确,导致生产过剩或不足,进而影 响库存。
解决方案
制定科学合理的库存管理计划
根据企业实际情况和市场预测,制定合理的库存管理计划。
提高预测准确性
通过市场调研和数据分析,提高对市场需求的预测准确性。
提升管理水平,加强信息沟通 ,提高决策效率。
04
搬运的浪费
定义与特点
定义:搬运是指在生产过程中,将原材 料、半成品、成品等在设备、生产线、 仓库等不同地点之间进行移动和传递。
降低生产效率:搬运过程中可能会造成 物品损坏、延误生产进度等问题,影响 生产效率。
增加运输成本:需要使用运输工具和人 力进行搬运,增加了运输成本。
04
市场预测不准确
企业未能准确预测市场需求, 导致生产计划与实际需求存在 偏差,从而产生生产过剩。
生产计划不合理
企业内部生产计划安排不当, 如生产批次过小、批量过大等
,导致生产过剩。
客户需求变化
客户需求变化导致企业生产计 划调整不及时,从而产生生产
过剩。
销售能力不足
企业销售能力不足,无法及时 消化生产出的产品,导致生产
动作的浪费
定义与特点
动作浪费
指在生产过程中由于操作不当、设备故障、流程设计不合理等原因导致的资源 、时间、人力等浪费的现象。
提高操作员技能水平
定期对操作员进行培训和考核,提高 操作员技能水平,减少操作误差导致 的制程问题。
优化工艺参数设置
根据实际生产情况,不断优化工艺参 数设置,减少制程中的误差和不良品 率。
THANKS
感谢观看
ABCD
预测不准确
企业对市场需求预测不准确,导致库存过多或过 少,影响生产和销售。
生产计划不准确
生产计划不准确,导致生产过剩或不足,进而影 响库存。
解决方案
制定科学合理的库存管理计划
根据企业实际情况和市场预测,制定合理的库存管理计划。
提高预测准确性
通过市场调研和数据分析,提高对市场需求的预测准确性。
提升管理水平,加强信息沟通 ,提高决策效率。
04
搬运的浪费
定义与特点
定义:搬运是指在生产过程中,将原材 料、半成品、成品等在设备、生产线、 仓库等不同地点之间进行移动和传递。
降低生产效率:搬运过程中可能会造成 物品损坏、延误生产进度等问题,影响 生产效率。
增加运输成本:需要使用运输工具和人 力进行搬运,增加了运输成本。
04
市场预测不准确
企业未能准确预测市场需求, 导致生产计划与实际需求存在 偏差,从而产生生产过剩。
生产计划不合理
企业内部生产计划安排不当, 如生产批次过小、批量过大等
,导致生产过剩。
客户需求变化
客户需求变化导致企业生产计 划调整不及时,从而产生生产
过剩。
销售能力不足
企业销售能力不足,无法及时 消化生产出的产品,导致生产
动作的浪费
定义与特点
动作浪费
指在生产过程中由于操作不当、设备故障、流程设计不合理等原因导致的资源 、时间、人力等浪费的现象。
八大浪费教材PPT课件
二. 过量生产浪费
过量生产浪费特点
• 货物储备/先做出来 • 设备富余,或设备的产能过大 • 供应及生产各阶段产能不平衡 • 作业员太多 • 产能/投资过大 • 不合格品比例高 • 生产批量大 • 问题被掩盖(计划混乱、不合格事件、设备管理) • 存货管理复杂
二. 过量生产浪费
过量生产浪费
(二) 浪费的表现: 人﹕整理﹐包装﹐搬运﹐无功作业
(三)不良品浪费产生原因
• 过程能力不足 • 过大的变差 • 供应商能力不足 • 操作工控制失误 • 管理层的决策 • 缺乏培训 • 不适当的工具/设备 • 车间布置差/不必要的搬运 • 高的存货水平
一. 不良品浪费
(三)不良品浪费产生原因
供应
制造 使用
来料不良﹕供应商流出不良品﹔物流破坏﹔进料检验﹑投入检查或后工序未发现﹔ 制程不防呆﹔
• 盲目消耗、挥霍 • 没有发挥优势 • 未开发的区域 • 垃圾 • 无价值的剩余物 • 逐渐变弱
用不同的评判标准去判断一个动作、 行为、方法或计划时,所得到的浪费程 度都会不同。
浪费的识别和消除
浪费的种类:
• 过量生产 • 不良品 • 移动 • 加工 • 存货 • 等待 • 动作 • 管理
造成浪费的原因:
三. 过程浪费
过程浪费特点
• 瓶颈 • 缺乏限度样品或明确的客户规范 • 无尽的精致 • 多余的批准手续 • 多余的拷贝/过多的信息
过程浪费的例子
1) 两点间距离宽﹔
始 始 末末
2) 机器行程大; 设备、工具转速慢﹐程序运行时间长
3) 动作的过程(距离﹑阻力﹑复杂程度)
4) 材料强度过剩﹕如螺丝长度,用不必要的耗材(胶水、胶带等)﹔
报告
生产过程中---八大浪费ppt课件
交付周期=∑(CT*批量)
26.04.2020
.
三. 過程浪費
(一) 浪費的定義:
作業的流程過多﹑過長﹑重復﹐或強度過剩 ﹑Over design 等造成的浪費﹐如﹕
直接﹕動作浪費﹔等待﹔材料浪費﹔設備生產力 低﹑折舊成本高……(如例所示)
更甚﹕交付周期增長→資金周轉慢 →損失潛在顧客
26.04.2020
生產過程中,因來料或制程不良,造成的各種 損失, 如:
直接﹕物料報廢、搬運、返工以及后工序的等 待, ……
更甚﹕質量不穩定→客戶抱怨→顧客忠誠↓﹑ 庫存↑ →采購(供應)計划紊亂……
26.04.2020
.
一. 不良品浪費
(二) 浪費的表現:
人(Man)﹕搬運﹐重工﹐維修﹐更換﹐等待 機(Machine)﹕等待或空載 料(Material)﹕報廢﹐退換﹐庫存 法(Method)﹕拆卸﹐分析﹐判斷 環(Environment)﹕存放區﹐搬運﹐維修區
WIP=Work In Process
.
二. 過生產浪費
(三) 浪費的產生:
過量計划(Schedule)﹕信息不准﹔計划錯誤﹔計 划失當﹔信息傳遞不暢﹔制程反應速度慢﹔
例﹕交貨需求5K,5K,5K;計划5.2K,5.2K,5K(4.6K)﹔
前工序過量投入(WIP):工時不平衡﹔Push方式﹔ 看板信息錯誤﹔不是一個流作業﹔工作紀律﹔
不必要但被增加﹔ 可同規格但不同﹔ 未考慮調整/轉換/取放 物料需要翻找﹔
26.04.2020
.
四. 動作浪費
(四) 浪費的消除:
操作不經濟(Handling)﹕按經濟原則設計并標 准化﹔制訂Check list發現并消除﹔ 設計不合理(Design)﹕合理設計﹔變成設計要 素﹔設計驗証與稽核﹔符合人體工效設計﹔
26.04.2020
.
三. 過程浪費
(一) 浪費的定義:
作業的流程過多﹑過長﹑重復﹐或強度過剩 ﹑Over design 等造成的浪費﹐如﹕
直接﹕動作浪費﹔等待﹔材料浪費﹔設備生產力 低﹑折舊成本高……(如例所示)
更甚﹕交付周期增長→資金周轉慢 →損失潛在顧客
26.04.2020
生產過程中,因來料或制程不良,造成的各種 損失, 如:
直接﹕物料報廢、搬運、返工以及后工序的等 待, ……
更甚﹕質量不穩定→客戶抱怨→顧客忠誠↓﹑ 庫存↑ →采購(供應)計划紊亂……
26.04.2020
.
一. 不良品浪費
(二) 浪費的表現:
人(Man)﹕搬運﹐重工﹐維修﹐更換﹐等待 機(Machine)﹕等待或空載 料(Material)﹕報廢﹐退換﹐庫存 法(Method)﹕拆卸﹐分析﹐判斷 環(Environment)﹕存放區﹐搬運﹐維修區
WIP=Work In Process
.
二. 過生產浪費
(三) 浪費的產生:
過量計划(Schedule)﹕信息不准﹔計划錯誤﹔計 划失當﹔信息傳遞不暢﹔制程反應速度慢﹔
例﹕交貨需求5K,5K,5K;計划5.2K,5.2K,5K(4.6K)﹔
前工序過量投入(WIP):工時不平衡﹔Push方式﹔ 看板信息錯誤﹔不是一個流作業﹔工作紀律﹔
不必要但被增加﹔ 可同規格但不同﹔ 未考慮調整/轉換/取放 物料需要翻找﹔
26.04.2020
.
四. 動作浪費
(四) 浪費的消除:
操作不經濟(Handling)﹕按經濟原則設計并標 准化﹔制訂Check list發現并消除﹔ 設計不合理(Design)﹕合理設計﹔變成設計要 素﹔設計驗証與稽核﹔符合人體工效設計﹔
八大浪费培训PPT课件
以成本
降低成
-6/70-
成本节减思想:降低成本
需求 < 供给
通过降低成本来降低销售价格
销售价格
利润 成本
规范 标准 专业 高效
-7/70-
竞争力提升 品质提升 制造成本降低 企业形象提升
改善 消除浪费 标准化
设 改善等
心、
动作改善、作业流程改善、物流改善、 备模夹治具改善、品质改善、管理
八大浪费、三无工程(无责任、无关
-29/70-
3.搬运的浪费
整个冲压过程包括取产品、冲压、 放置产品,其中取产品与摆放产 品占了50%的作业时间,并且这 些动作并不产生价值。
冲压完的产品要先放到周转车 上,再搬运到点焊工位点焊, 这些搬运过程都是浪费,为什 么不把冲压与焊接设备放在一 起呢?
规范 标准 专业 高效
-30/70-
3.搬运的浪费
规范 标准 专业 高效
-35/70-
八大浪费
1.制造过多的浪费 2.等待的浪费 3.搬运的浪费 4.加工的浪费 5.库存的浪费 6.动作的浪费 7.不良的浪费 8.管理的浪费
规范 标准 专业 高效
-36/70-
SUCCESS
THANK YOU
2019/8/1
规范 标准 专业 高效
-37/70-
5.库存的浪费
制
移动
40%
造
所谓的附加值指的是通过加工或组装提 高产品的价值,其余的都是非附加值,就 浪费。
活
附加价值动作
15%
TOYOTA汽车公司
动
非效率的 ‘工作’ 40%
11 /72
定义 95%以上是浪费
规范 标准 专业 高效
-11/70-
降低成
-6/70-
成本节减思想:降低成本
需求 < 供给
通过降低成本来降低销售价格
销售价格
利润 成本
规范 标准 专业 高效
-7/70-
竞争力提升 品质提升 制造成本降低 企业形象提升
改善 消除浪费 标准化
设 改善等
心、
动作改善、作业流程改善、物流改善、 备模夹治具改善、品质改善、管理
八大浪费、三无工程(无责任、无关
-29/70-
3.搬运的浪费
整个冲压过程包括取产品、冲压、 放置产品,其中取产品与摆放产 品占了50%的作业时间,并且这 些动作并不产生价值。
冲压完的产品要先放到周转车 上,再搬运到点焊工位点焊, 这些搬运过程都是浪费,为什 么不把冲压与焊接设备放在一 起呢?
规范 标准 专业 高效
-30/70-
3.搬运的浪费
规范 标准 专业 高效
-35/70-
八大浪费
1.制造过多的浪费 2.等待的浪费 3.搬运的浪费 4.加工的浪费 5.库存的浪费 6.动作的浪费 7.不良的浪费 8.管理的浪费
规范 标准 专业 高效
-36/70-
SUCCESS
THANK YOU
2019/8/1
规范 标准 专业 高效
-37/70-
5.库存的浪费
制
移动
40%
造
所谓的附加值指的是通过加工或组装提 高产品的价值,其余的都是非附加值,就 浪费。
活
附加价值动作
15%
TOYOTA汽车公司
动
非效率的 ‘工作’ 40%
11 /72
定义 95%以上是浪费
规范 标准 专业 高效
-11/70-
现场八大浪费PPT课件
2﹑JIT库存管理---广告牌管理
3﹑控制在库金额。
4﹑定期盘点。 5﹑库存警示方法。
物料最低量标记
2023/10/4
22
2.7 管理浪费
浪费的定义: 由管理造成生产力﹔周期﹔资源利用等浪费.
管理浪费 公司不能获至最大利润而造成 的浪费,是竞争力强弱的表现.
2023/10/4
23
管理存在的问题
1.管理工作的“等﹐靠﹐要” 2.工作规章上的无序 3.协调不力企业丧失凝聚力 4.闲置的人﹑设备未“动”起来 5.最常见应付的现象 6.“低效”的反复发生 7.管理上无真正的有“理”可依
浪费的消除
过量计划(Schedule)﹕计算器信息集成控制﹔准确掌控不良 (报废)率﹔制订宽放标准和计划校正机制﹔缩短交付周期 (CT﹑批量)﹔
前工序过量投入(WIP)﹕生产线平衡; 制订单次传送量标准﹔ 一个流作业﹔作业要求﹔
制造三不 Ü不预测生产 Ü不过量生产 Ü不提早生产
2023/10/4
15
2023/10/4
28
源头的品质
第一次就做对 发生错误时立即停止制程或装配线 员工是自己的检验员,对自己的产出质量负责 员工被授权去做自己的保养工作,直到问题解决
2023/10/4
29
及时生产
➢ 有需求时,生产所需对象且不超额生产 ➢ 典型应用在重复性制造 ➢ 及时生产的理念下:
–批量大小是一 –典型批量:一天生产量的十分之一 –供货商一天送货数次 –效益 –存货投资缩小、前置时间缩短 –公司对需求变动可以更快反应 –质量问题亦可浮现 –JIT暴露隐藏于过量库存和员工中的问题
品质低下,人员不安全) 2.浪费:有能力,但未给予充足的工作量的未饱和状态;
3﹑控制在库金额。
4﹑定期盘点。 5﹑库存警示方法。
物料最低量标记
2023/10/4
22
2.7 管理浪费
浪费的定义: 由管理造成生产力﹔周期﹔资源利用等浪费.
管理浪费 公司不能获至最大利润而造成 的浪费,是竞争力强弱的表现.
2023/10/4
23
管理存在的问题
1.管理工作的“等﹐靠﹐要” 2.工作规章上的无序 3.协调不力企业丧失凝聚力 4.闲置的人﹑设备未“动”起来 5.最常见应付的现象 6.“低效”的反复发生 7.管理上无真正的有“理”可依
浪费的消除
过量计划(Schedule)﹕计算器信息集成控制﹔准确掌控不良 (报废)率﹔制订宽放标准和计划校正机制﹔缩短交付周期 (CT﹑批量)﹔
前工序过量投入(WIP)﹕生产线平衡; 制订单次传送量标准﹔ 一个流作业﹔作业要求﹔
制造三不 Ü不预测生产 Ü不过量生产 Ü不提早生产
2023/10/4
15
2023/10/4
28
源头的品质
第一次就做对 发生错误时立即停止制程或装配线 员工是自己的检验员,对自己的产出质量负责 员工被授权去做自己的保养工作,直到问题解决
2023/10/4
29
及时生产
➢ 有需求时,生产所需对象且不超额生产 ➢ 典型应用在重复性制造 ➢ 及时生产的理念下:
–批量大小是一 –典型批量:一天生产量的十分之一 –供货商一天送货数次 –效益 –存货投资缩小、前置时间缩短 –公司对需求变动可以更快反应 –质量问题亦可浮现 –JIT暴露隐藏于过量库存和员工中的问题
品质低下,人员不安全) 2.浪费:有能力,但未给予充足的工作量的未饱和状态;
- 1、下载文档前请自行甄别文档内容的完整性,平台不提供额外的编辑、内容补充、找答案等附加服务。
- 2、"仅部分预览"的文档,不可在线预览部分如存在完整性等问题,可反馈申请退款(可完整预览的文档不适用该条件!)。
- 3、如文档侵犯您的权益,请联系客服反馈,我们会尽快为您处理(人工客服工作时间:9:00-18:30)。
待
8
管理的浪费
管理本身成为一种专 职的工作发生的浪费
事后管理的浪费
14
1、不良的浪费
工厂内产生不良品,需要进行处置的时间、人力、 物力上的浪费,以及由此产生的相关浪费.
材料的损失; 设备、人员、工时的损失; 额外的处理人员的增加; 影响生产; 降价处理; 出货延误取消定单; 信誉下降……
15
(不良)举例说明
分类
浪费
说明
品 1. 不良品的浪费 不良本身就是浪费
Q
M U D A 质 2. 修正不良的浪费 治标不治本的浪费
的 3. 错误的发生
只有临时对策,不追究根本原因的浪
浪 4. 检验的浪费
费
费 5. 品质管理的浪费 品质管理的事后检查本身就是浪费
S
安 全
灾害与事故的防止
安全的疏忽是对人、对社会最大的 危害,安全第一
不同的经营思想
售价中心型: 以售价为中心,当市场售价降低时,利润随之
减少。 计算公式:利润=售价-成本
市场好时有较高的利润;市场差时利润大幅度降 低; 企业类别:
缺乏改善意识的企业
4
不同的经营思想
利润中心型:
以利润为中心,当市场售价降低时,成本也 必须降低,以便获得的利润(目标利润)不会 减少。
搬运步行的浪费
13
工厂中常见的 8大浪费
NO
制造现场的 浪费
说明
管理部门的浪费
5
库存的浪费
成品、中间品、原材 料的库存浪费
超前储备的浪费带 来大量的管理浪费
M U D A 6
制造过多的 在不必要的时候制造 超前预计市场的结
浪费
不必要的产品
果
人、机械、部件在不
7 等待的浪费 必要时发生的各种等
等待的浪费
能力不平衡造成的各种等待、停滞 流程混乱造成的浪费
M
1. 资料的浪费
资料不用便是浪费
管 2. 会议的浪费
理 3. 管理的浪费
的 4. 通信的浪费
浪 费
5. 工作单的浪费
会议本身的目的不明确就是浪费 管理是浪费,目标、职责不清 信息的目的性不明确就是浪费 工作单的编制填写确认保管就是浪 费
11
5MQS的浪费
7
全面生产系统的浪费
什么是浪费:
✓ 不增加价值的活动,是浪费; ✓ 尽管是增加价值的活动,所用的资源超过了
“绝对最少”的界限,也是浪费。
8
全面生产系统的浪费
生产要素的5MQS: Man(人) Machine(机器) Material(物料) Method(作业方法) Management(管理) Quality(品质) Safety(安全)
计算公式:成本=售价-利润
企业在竞争中立于不败之地;
经营思想:
不断消除浪费; 降低成本; 积极进取;
按照“利润中心型”的 思想经营,企业就可以 在竞争中立于不败之地
5
企业每天都在“烧钱”
以下不良现象或浪费在“烧钱” 仪容不整的工作人员; 好心疼啊!
机器设备放置不合理; 机器设备保养不当; 原材料、在制品、完成品、待修品、不 良品等随意摆放; 通道不明确或被占; 工作场所脏污。
U D A 多余原料 过多螺栓连接,设计不良 焊接过多 多余功能造成的材料浪费
费 5. 不良报废的材料
报废本身就是浪费
设 1. 大型机械的浪费 备 2. 通用机械的浪费 的 3. 传送带的浪费 浪 4. 压缩机的能力过剩 费 5. 故障的浪费
批量生产带来的搬运、停滞的浪费
通用机械功能多数只用一半
只用作传送的皮带是一种浪费
全自动气动装置使压缩机过多投入
机械故障的浪费
10
5MQS的浪费
分类
浪费
说明
作 1. 批量加工的浪费 业 2. 库存的浪费
由于批量生产造成的浪费 库存本身就是浪费
方 3. 搬运的浪费
设备布局的浪费
法 4. 放置(停滞)的浪费 工序过于细分化造成的浪费
M U D A 5
的 浪 费
5. 等待的浪费 6. 不平衡的浪费
17
(加工)举例说明
浪费的产生: 线末100%目使检查 重做或修复或调试区域
6
企业每天都在“烧钱”
如果一个企业每天都在大量的“烧钱”,你指望企业 能获得最大的利润吗?可能有人会说,我赚钱这么 辛苦,还能“烧”钱?可事实上我们大多数企业都 在“烧”钱,只不过不是用火烧,而是企业中存在 大量的浪费,白白地花掉了许多十分辛苦挣来的钱。 否则作完全一样的产品为什么利润差距那么大?如 果不相信的话,我们来看看许多企业的状况:各工 序旁摆放的大量等待加工或已加工的零件、在制品; 仓库中存放可供用2、3个月的料;随时可以买到的 普通包装箱半年前一次采购一大批,然后逐月慢慢 使用;等等,毫无疑问这些会造成场所浪费、租金 损失,流动资金被占用、利息损失、过理储存的报 废、无谓工时的发生、管理成本的增加,这些浪费 现象无异于在“烧”钱。
浪费的产生: 制程不良:作业者不良或损坏;设备﹑夹具/ 治具/工具不防呆;制程不防呆;
浪费的消除: 制程不良:及时指正;培训员工技能;设备 ﹑夹具/治具/工具﹑工艺流程防呆﹔
16
2、加工的浪费
亦称为 “过分加工的浪费”,一是指多余的加工, 另一方面是指过分精确的加工,造成资源的浪 费.
多余的作业时间和辅助设备; 有一些加工程序是可以省略、替代、重组或 合并; 生产用电、气压、油等能源浪费; 加工、管理工时增加; 时间浪费、影响产量完成……
学习目标
认识浪费 不同的经营思想 企业每天都在“烧”钱 全面生产系统(5MQS)的浪费 工厂中常见的8大浪费
2
不同的经营思想
成本中心型: 以计算或实际的成本为中心,加上预先设定
的利润,得出售价。 计算公式: 售价=成本+利润
卖方市场;消极被动; 企业类别:
高新产品 垄断产品 国内的铁路、民航等
3
9
5MQS的浪费
分类
浪费
说明
1. 行走的浪费
人 2. 监视的浪费
的 浪
3. 寻找的浪费
费 4. 动作的浪费
5. 职责不清的浪费
走一步一秒的浪费 CNC操控的无谓监视 找寻物品的时间浪费 不增值的动作浪费 不知自己的职责,人制管理的浪费
M 材 1. 原料的浪费
5 M
料 的 浪
2. 螺栓的浪费 3. 焊接的浪费 4. 功能的浪费
12
工厂中常见的 8大浪费
N 制造现场的
O
浪费
说明
管理部门的浪费
制造不良的浪费,之 低可靠性带来的各
1 不良的浪费 后还有进行检测的浪 种事中、事后的浪
M U D A 费
费
与产品价值核心的功 2 加工的浪费 能不相关的加工与作
作业浪费
业都是浪费
3
动作的浪费
步行、放置、大幅度 的动作
Байду номын сангаас动作的浪费
4 搬运的浪费 物料搬运的浪费