刀具热处理
t10钢车刀热处理工艺

摘要T10钢车刀是用于车削加工的、具有一个切削部分的刀具。
车刀是切削加工中应用最广的刀具之一。
车刀的工作部分就是产生和处理切屑的部分,包括刀刃、使切屑断碎或卷拢的构造、排屑或容储切屑的空间、切削液的通道等构造要素。
在切削过程中,刀具的切削部分要承受很大的压力、摩擦、冲击和很高的温度。
因此,刀具材料必须具备高硬度、高耐磨性、足够的强度,韧性和抗氧化性,还需具有高的耐热性〔红硬性〕,即在高温下仍能保持足够硬度的性能。
[关键词] 切削耐磨高硬度红硬性技术要求高硬度,高耐磨性是刀具最重要的使用性能之一,假设没有足够的高的硬度是不能进展切削加工的。
否那么,在应力作用下,工具的形状和尺寸都要发生变化而失效。
高耐磨性那么是保证和进步工具寿命的必要性,除了以上要求红硬性及一定的强度和韧性。
在化学成分上,为了使工具钢尤其是刃具钢具有较高的硬度,通常都使其含有较高的的碳〔W〔C〕=0.65%~1.55%〕,以保证淬火后获得高碳马氏体,从而得到高的硬度和切断抗力,这对减少防止工具损坏是有利的。
大量的含碳质量分数又可进步耐磨性,碳素工具钢的理想淬火组织应该是细小的高碳马氏体和均匀细小的碳化物,工具钢在热处理前都应进展球化退火,以使碳化物呈细小的颗粒状且分布均匀。
工作条件及性能要求刃具在切削过程中,刀刃与工件外表金属互相作用,使切削产生变形与断裂,并从工件整体剥离下来。
故刀刃本身承受弯曲、改变、剪切应力和冲击、振动等负载荷作用。
由于切削层金属的变形及刃具与工件、切削的摩擦产生大量的摩擦热,均使刃具温度升高。
切屑速度越快,那么刃具的温度越高,有时刀刃温度可达600℃左右。
失效形式及使用性能刀刃是的失效形式有很多种,磨损是刀具失效的主要原因之一,如崩刃,折断和断裂等等。
〔1〕为了保证刃具的使用寿命,应要求有足够的耐磨性。
高的耐磨性不仅决定于高硬度,同时也取决于钢的组织。
在马氏体基体上分布着弥散的碳化物,尤其是各种合金碳化物能有效地进步刃具钢的耐磨才能。
常用刀具钢材的热处理

常用刀具钢材的热处理的详细资料热处理材料:5160 (弹簧钢)一种很普遍的高端钢材,主要是一种简单的弹簧钢加入铬来增强硬度,具有很好的打磨度。
但其更广为人知的是杰出的坚韧性(象L-6一样)。
通常被用于制造剑类(硬度低于50s RC)和使用强度大的刀具(最高硬度大于60s RC)。
800度油淬,250度回火,保温几分钟,回火250度,保温几分钟意思是,如果你有热处理炉,达到250度时控制在这个温度,过几分钟后即可开炉.用土炉子时估计到250度左右了,把刀夹出迅速插入热煤灰堆几分钟即可完成回火.水冷,弹簧钢空冷有回火脆性,所以要水冷.没有高温计热处理炉,目测火色估温度. 淬火后尺寸没变化,表面会有些轻微脱炭,不过没关系,研磨过后脱炭层就会被磨掉,弹簧钢都应该用油淬,可以达到60度或者再高一点,但是那样子落到地上或者用手掰都会断。
油的冷却速度在工件温度200-300度跟水比肯定是不够,但是可以有效防止开裂。
而且弹簧钢的淬透性很好,如果坚持用弹簧钢做刀,那么还是用油淬比较合适。
52100(GCR15)轴承钢:52100是一种滚轴钢材,只被锻工们使用。
它和5160很近似,(但52100约含有 1% 碳,而5160 约含有0.60%碳),比5160的打磨度好,但不如5160坚韧。
常被用于制造猎刀和其他打磨度要求高而坚韧度要求不似5160那么高的刀具。
轴承钢做刀不错,都能做砍刀了。
回火的时候温度低一点就可以,200多度应该比较合适.GCR15球化退火工艺:加热到790-810度.保温.2-4小时.等温700-720度.保温.1-3小时,随炉冷至500度出炉空冷.淬火温度850.C.油淬.回火温度240.C 保温90-120分钟.硬度HRC59。
还有一种是:52100处理方法淬火(盐浴)650-700度预热8分钟再加热到850-860度保温8-9分钟后油淬回火 160-180度 8小时部分钢号对照表D2=Cr12Mo1V1O1=9CrWMn440C=9Cr18Mo或11Cr17A2= Cr5Mo1VT10=1095420=4Cr1352100=Gcr15D-2(cr12mo1v~cr12mov)D-2 有时被叫作“半不锈钢”,含铬量较高(12%),但不到不锈钢的程度。
刀具的制造工艺
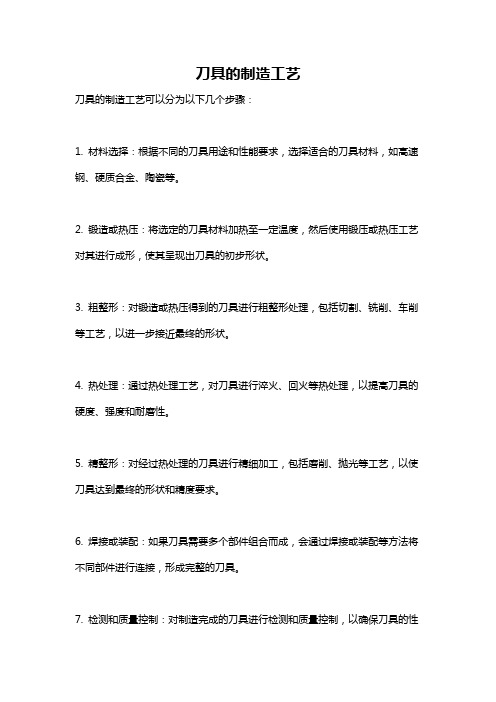
刀具的制造工艺
刀具的制造工艺可以分为以下几个步骤:
1. 材料选择:根据不同的刀具用途和性能要求,选择适合的刀具材料,如高速钢、硬质合金、陶瓷等。
2. 锻造或热压:将选定的刀具材料加热至一定温度,然后使用锻压或热压工艺对其进行成形,使其呈现出刀具的初步形状。
3. 粗整形:对锻造或热压得到的刀具进行粗整形处理,包括切割、铣削、车削等工艺,以进一步接近最终的形状。
4. 热处理:通过热处理工艺,对刀具进行淬火、回火等热处理,以提高刀具的硬度、强度和耐磨性。
5. 精整形:对经过热处理的刀具进行精细加工,包括磨削、抛光等工艺,以使刀具达到最终的形状和精度要求。
6. 焊接或装配:如果刀具需要多个部件组合而成,会通过焊接或装配等方法将不同部件进行连接,形成完整的刀具。
7. 检测和质量控制:对制造完成的刀具进行检测和质量控制,以确保刀具的性
能和质量达到要求。
8. 表面处理:根据需要,对刀具进行表面处理,如镀覆、涂层或涂漆等,以提高刀具的耐腐蚀性和外观质量。
9. 包装和出厂:将制造完成的刀具进行包装,做好标识和记录,最后出厂销售或分发给用户。
高速钢刀具硬度与热处理

立 铣
s 6
>士6mm
6・ 3 5—6 6 6 5—6 . ≤ l 65
6 4 5—6 . 6 67 65 5
W 2M0 C『 9 4VC 8 0
乓 2
1 6 — 11 0 l0 9
表1 高速钢刀具硬度推荐值
( HRC≥ 6 ) 求 外 , 余 产 品 一 律 为 6 3要 其 3~6 HRC, 6 而
对 韧性 未作任 何要 求 。 几 十 年 的 实 践 证 明 , 高 的 硬 度 反 而 使 刀 具 的 过 寿 命 下 降 。 0 代 初 , 国 2 具 行 业 总 工 程 师 会 议 曾 6年 全 1 2
维普资讯
高 速 钢 刀 具 硬 度 与 热 处 理
口
中图分 类号 : G 1 ;G1 T 7 1T 5
赵 步青
口
王金双
文 章 编 号 :01一 9 8 2 0 ) 1 0 0 —0 10 49 (0 2 0 —0 2 ) 2
文献标识码 : C
硬度 是材 料 抵抗 表 面 层 局部 塑性 变形 的能 力 。 到 目前 为 止 , 有 硬 度 这 个 参 数 能 直 接 反 映 材 料 表 唯
Ⅱ
常用高 速钢 刀具硬度推荐值
通 用 高速钢 ( S 淬 火 回火后 的硬度 可 达6 HS ) 3—
盾 , 具 材料从 碳 素工 具钢 、 金工具 钢 、 速钢 、 刀 合 高 硬 质 合 金 发 展 到 当前 的 陶 瓷 、 方 氮 化 硼 等 超 硬 材 料 . 立
刀 具 的 硬 度 越 来 越 高 , 性 却 越 来 越 差 从 某 种 意 义 韧
热处理hrc

热处理hrc热处理是一种常见的金属加工方法,通过加热和冷却的处理,可以改变金属的物理和机械性质,从而使金属更适合特定的应用场合。
其中,HRC是热处理的一种常见指标,下面将对热处理和HRC的相关内容进行介绍。
一、热处理的作用和分类热处理是指对金属进行加热和冷却的工艺,通过加热改变金属的结构,使其达到预定的物理、机械性能和组织状态。
热处理的作用主要有以下几点:1. 改善金属的硬度和韧性;2. 提高金属的强度和耐蚀性;3. 改变金属的内部组织和晶格结构,从而改变材料的宏观性能。
根据热处理的加热和冷却条件,热处理可以分为多种类型,包括淬火、回火、正火、退火等。
其中,淬火是一种常见的热处理方法,通过快速冷却使金属产生马氏体组织,从而提高金属的硬度和强度。
二、HRC的概念和测试方法HRC是硬度的一种表示方法,表示把试样压入一定深度后回弹的程度。
HRC的测试方法主要有两种:Rockwell硬度测试和布氏硬度测试。
Rockwell硬度测试是通过把不同形状的钢球或钻石压入金属表面来测试材料的硬度值。
在测试过程中,将钢球或钻石逐级压入试样表面,通过测量回弹程度来确定材料的硬度值。
Rockwell硬度值通常以HRC表示。
布氏硬度测试则是采用不同形状的金刚石锥尖来对材料进行试验,同样也是根据试样表面上发生的弹性和塑性形变来测量材料的硬度值。
布氏硬度值通常以HB表示。
三、HRC的应用场景由于HRC可以很好地反映出材料的硬度,因此在金属材料的各个加工阶段中都会有所应用。
例如:1. 制造金属零件时,需要选择适当的材料,并对其进行合适的热处理,以满足零件在使用中的要求;2. 在机械加工过程中,需要针对不同材料制造不同的刀具,在刀具设计和生产过程中需要考虑材料的硬度;3. 在车辆、机械和工具的维修过程中,需要对受损部件进行测试,并对其进行相应的修复。
总之,热处理和HRC在金属加工领域中具有广泛的应用和重要的意义。
在实践中,需要根据具体的要求和加工需求选择合适的热处理方法以及测试方法。
高速钢刀具热处理缺陷的原因及预防措施

!% 预防硬度低的措施
( , ) 加强原材料进厂管理。采购运回库房的原材料 要严格入库检验和入库保管,按不同牌号分开存放。对 不同钢厂、不同批次的要做好标记。生产线上的在制品
# !" ! " # " 年 第 # 期$ 热 处 理" 锻 压" 铸 造 ! ! !" # $ % & ’ ! ( ) * + , -. / 0 1 " 2 ( #
要账、物、卡相符,分批存放,防止混料。 ( # ) 严格原材料进厂复验。项目包括:火花鉴别、 化学成分分析、表面脱碳层厚度及碳化物不均匀度评级 等。 图 , 为高速钢原材料碳化物分布照片。试样经淬火 后在 (1$ % 2$$’ 回火 ,3 的情况下观察。图 ,4 为 0 级, 可制造 !0$55 以下的一般刀具。图 ,6 为 1 级,不能制 造高精度的刀具,因为碳化物不均匀度超过 & 级,刀具 易产生崩刃和断裂。
氧与盐浴作用生成金属氧化物: ’01/2 % % . "01’ . - /2’ %! 31/2’ - .’ 水分的作用 ! 工 业 用 氯 化 钡( 31/2’ ,’4’ . ) 本身含有结晶水,空气中含有水分,尤其是梅雨季节, 空气潮湿,更容易引起氧化脱碳反应: +, - 4’ ."+,. - 4’ % / ( 刀具表面) - 4’ ."/. - 4’ % 水与盐浴作用产生金属氧化物的反应: 31/2’ - ’4’ ."31 ( .4) ’ - ’4/2 31 ( .4) ’ " 31. - 4’ . 01/2 - 4’ ."01.4 - 4/2 ’01 ( .4) "01’ . - 4’ . ( ( ) 工业用盐中允许杂质含量的作用 ! 工业用盐技 术条 件 中, 氯 化 钡 的 纯 度 $ $56 , 允 许 杂 质 硫 酸 盐 ( 317.) ) 总含量 8 &9 *6 ;氯化钠的纯度 : $#6 ,允许 杂质硫酸盐( 01’ 7.) ) 总含量!%6 。 这些硫酸盐在高温状态下,直接和刀具表面产生氧 化脱碳反应: +, - 01’ 7.) "+,. - 7.’ - 01’ . ( 铁的氧化) +, - 317.) "+,. - 7.’ - 31. ( 铁的氧化) / ( 刀具表面)- 017.) "/.% - 7.’ - 01’ . ( 脱碳) / ( 刀具表面)- 317.) "/.% - 7.’ - 31. ( 脱碳) ( ) ) 盐浴中氧化铁的作用 ! 盐浴中的氧化铁的含量 来源,像电极氧化铁皮脱落,工作表面生锈,工装卡具 表面氧化生锈,都会增加盐浴中氧化铁的含量,最终使 刀具表面脱碳。氧化铁皮在高温下产生分解反应: ’+,’ .( ")+,. - .’ ( * ) 硝酸盐的作用! 盐浴长期使用,硝酸盐随着工
刀具热处理技术的应用
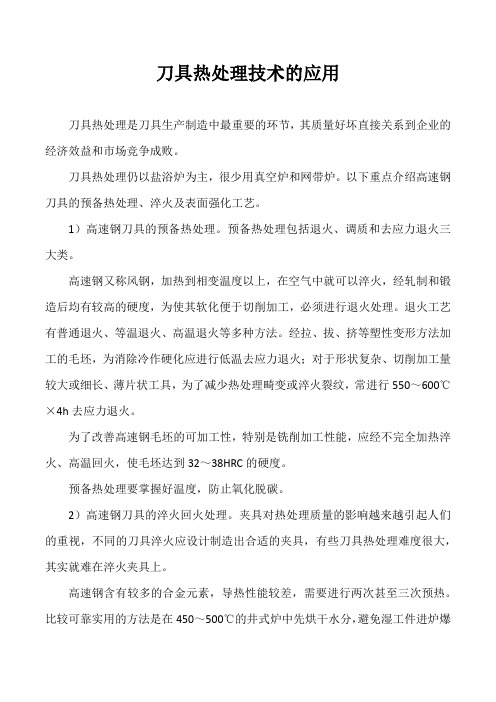
刀具热处理技术的应用刀具热处理是刀具生产制造中最重要的环节,其质量好坏直接关系到企业的经济效益和市场竞争成败。
刀具热处理仍以盐浴炉为主,很少用真空炉和网带炉。
以下重点介绍高速钢刀具的预备热处理、淬火及表面强化工艺。
1)高速钢刀具的预备热处理。
预备热处理包括退火、调质和去应力退火三大类。
高速钢又称风钢,加热到相变温度以上,在空气中就可以淬火,经轧制和锻造后均有较高的硬度,为使其软化便于切削加工,必须进行退火处理。
退火工艺有普通退火、等温退火、高温退火等多种方法。
经拉、拔、挤等塑性变形方法加工的毛坯,为消除冷作硬化应进行低温去应力退火;对于形状复杂、切削加工量较大或细长、薄片状工具,为了减少热处理畸变或淬火裂纹,常进行550~600℃×4h去应力退火。
为了改善高速钢毛坯的可加工性,特别是铣削加工性能,应经不完全加热淬火、高温回火,使毛坯达到32~38HRC的硬度。
预备热处理要掌握好温度,防止氧化脱碳。
2)高速钢刀具的淬火回火处理。
夹具对热处理质量的影响越来越引起人们的重视,不同的刀具淬火应设计制造出合适的夹具,有些刀具热处理难度很大,其实就难在淬火夹具上。
高速钢含有较多的合金元素,导热性能较差,需要进行两次甚至三次预热。
比较可靠实用的方法是在450~500℃的井式炉中先烘干水分,避免湿工件进炉爆炸,飞液溅出伤人。
预热温度一般为850~870℃,预热时间为加热时间的两倍。
盐浴配方(质量分数)为70%BaCl2+30%NaCl。
高速钢刀具高温加热是非常重要又非常难的环节,盐浴成分为100%BaCl2。
从增加碳化物溶入量,提高奥氏体合金化程度的角度考虑,奥氏体化温度越高越好,以便提高钢的耐磨性和热硬性;但从细化晶粒,提高韧性的角度考虑,加热温度不宜太高。
不同牌号有不同的加热温度,同一牌号钢制作不同刀具,加热温度相差也很大,也就是说,制订热处理工艺应该个性化。
不管何种刀具,在制订热处理工艺时,必须了解刀具加工的对象,在满足韧性的前提下,温度高比温度低优越。
高速钢刀具硬度与热处理
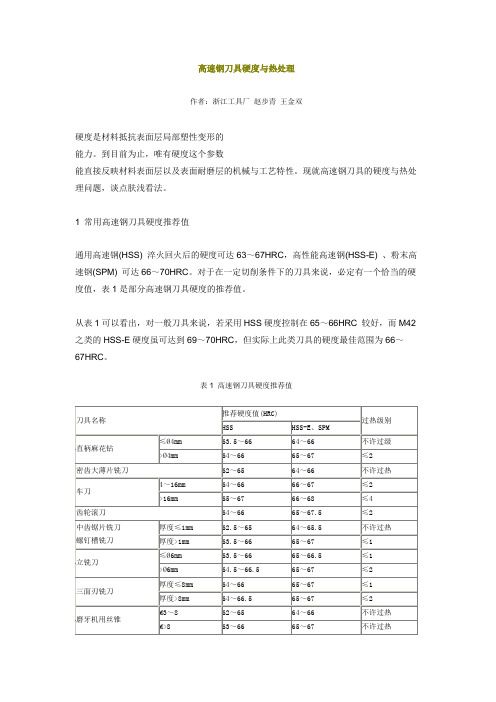
高速钢刀具硬度与热处理作者:浙江工具厂 赵步青 王金双硬度是材料抵抗表面层局部塑性变形的能力。
到目前为止,唯有硬度这个参数能直接反映材料表面层以及表面耐磨层的机械与工艺特性。
现就高速钢刀具的硬度与热处理问题,谈点肤浅看法。
1 常用高速钢刀具硬度推荐值通用高速钢(HSS) 淬火回火后的硬度可达63~67HRC ,高性能高速钢(HSS-E) 、粉末高速钢(SPM) 可达66~70HRC 。
对于在一定切削条件下的刀具来说,必定有一个恰当的硬度值,表1是部分高速钢刀具硬度的推荐值。
从表1可以看出,对一般刀具来说,若采用HSS 硬度控制在65~66HRC 较好,而M42之类的HSS-E 硬度虽可达到69~70HRC ,但实际上此类刀具的硬度最佳范围为66~67HRC 。
表1 高速钢刀具硬度推荐值2 刀具的硬度和韧性的关系硬度和韧性是集中在刀具上一对最为突出的矛盾,刀具材料从碳素工具钢、合金工具钢、高速钢、硬质合金发展到当前的陶瓷、立方氮化硼等超硬材料,刀具的硬度越来越高,韧性却越来越差。
从某种意义上讲,谋求刀具的高韧性比高硬度难得多。
在高速钢刀具产品中,只对硬度作具体规定,用HSS制造的刀具,除钻头、中心钻有下限硬度(HRCP63) 要求外,其余产品一律为63~66HRC,而对韧性未作任何要求。
几十年的实践证明,过高的硬度反而使刀具的寿命下降。
60年代初,全国工具行业总工程师会议曾决定,高速钢刀具硬度超过66.5HRC 不得出厂。
由于当时超硬高速钢和粉末高速钢还未应用,那样的规定对促进刀具业的发展有指导意义。
到了70年代,日本学者提出“对于一般刀具把硬度控制在65~66HRC”的观点。
从全国历年刀具行评结果可知,凡获一等品、优等品的高速钢刀具,其硬度都在65HRC以上,足以说明,低硬度不可能高寿命。
国家规定的硬度下限指标,笔者认为只是合格品的最低水平,如果连合格品标准也达不到,在市场竞争中就没有立足之地。
- 1、下载文档前请自行甄别文档内容的完整性,平台不提供额外的编辑、内容补充、找答案等附加服务。
- 2、"仅部分预览"的文档,不可在线预览部分如存在完整性等问题,可反馈申请退款(可完整预览的文档不适用该条件!)。
- 3、如文档侵犯您的权益,请联系客服反馈,我们会尽快为您处理(人工客服工作时间:9:00-18:30)。
七、高速钢刀具打的变形开裂及防止措施淬火变形是钢淬火必然产生的客观规律。
高速钢刀具在热处理过程中经常遇到变形开裂的问题,尺寸较大、形状较复杂的刀具及细长的刀具尤为突出(前者易开裂,后者易变性)。
现在仅将生产过程中遇到的刀具变形、开裂情况及防止措施,结合典型刀具为例作一些说明。
【高速钢刀具产生变形开裂的原因】高速钢刀具产生变形开裂,主要是受到组织应力和热应力的影响。
1、组织应力的影响刀具在加热和冷却过程中发生各种组织转变,由于钢中各组织的比容不同,因此在相变时发生体积变化。
尤其是高速钢,淬火冷却胡得到高合金度的马氏体组织,马氏体的比容大,使刀具淬火后体积膨胀。
另一方面,由于刀具具有复杂的几何形状,加热和冷却是的组织转变非同时进行,一些尖角的地方容易引起应力集中,导致刀具变形开裂。
影响组织应力大小的因素很多,如加热温度、冷却方法等。
要减小组织应力,主要是在热处理中设法调节马氏体。
奥氏体和贝氏体的相对量,这与淬火方法(油淬分级及等温淬火)直接有关。
2、热应力的影响热应力是刀具在加热和冷却是产生内外温差所引起的。
由于工件表里各种存在温差、造成热胀冷缩的不一致。
高速钢的导热性较差,更加剧热应力的作用。
故对一般易裂易变性的刀具应采用多次预热、多次分级、甚至等温的工艺。
3、原材料碳化物偏析导致变形开裂生产实践中由于碳化物的不均匀性,是工具沿碳化物集中处开裂。
例如铣刀、剃齿刀等刀具的内孔开裂,多数是上述原因所导致的。
4、淬火前刀具内部存在较大的应力在处理过程中易引起变形开裂。
例如薄形锯片铣刀在处理前先消除应力,处理后能减少变形。
5、淬火温度过高使钢材强度大大下降,因此在加热和冷却过程中容易发生变形与开裂。
实践经验证明,凡刀具有过热、过烧现象,则刀具变形就大(如车刀、钻头之类),容易引起开裂(如铣刀、滚刀之类)。
6、冷却过快在热应力和组织应力的复杂作用下,易引起变形开裂。
同样,加热过快也易引起变形开裂。
高速钢具有极好的淬透性,只有在600℃以后缓慢的冷却都不妨碍刀具的硬度和其他切削性能。
例如:我厂在处理组合铣刀时(较大,需加热10~15分钟),由于等温硝盐水份过多,冷却过快,致使组合铣刀全部发生开裂。
7、回火不当所引起的变形开裂大型刀具虽然在淬火过程中不发生开裂,但是回火过程中亦易开裂(参阅高速钢的回火)。
例如:一次,我厂在处理大得指形铣刀时,开裂即在回火炉中发生,因此后来我们规定大型刀具的回火采取低温入炉,缓慢升温。
对于细长刀具(如拉刀),最好作垂直拉状进行回火。
8、水冷处理会使大型复杂的刀具发生开裂我厂曾对剃齿刀淬火进行冰冷处理(-70℃),结果发生开裂;如回火一次后进行冰冷处理,也有开裂。
因此对于剃齿刀来说,冰冷处理只能在二次回火后进行。
9、清洗过早易引起开裂我厂在处理一些成型铣刀及粗直径(φ40以上)拉刀时,由于工件未冷至室温而过早的清洗,结果在刀具的键槽处(如成型铣刀)及中心孔处(如拉刀)发生开裂。
对于较大的刀具应该采用及时回火(淬火后冷至100℃左右立即回火)。
10、刀具加热时放置不合理易引起变形根据我厂实践经验,扎铁丝作垂拉状加热比插架加热好,不易引起变形。
11、其他如设计不合理(多尖角、厚薄悬殊),造成应力集中;表明脱碳;回火不足;重复淬火不经中间退火;材料疏松等均易引起开裂。
下面我们通过一些实例来介绍防止刀具变形开裂的具体方法。
(一)减少锯片铣刀(图2-11)平面弯曲的工艺材料:W18Cr4V规格:φ230×4毫米技术要求:(1)硬度:HRC63~66(2)平面弯曲:不大于0.15毫米处理前加工情况:反复锻造成饼状再行锯开。
碳化物不均匀度≤5级热处理工艺:1、在淬火前先作500~520℃消除内应力处理,保温4~6小时。
2、淬火回火锯片淬火回火工艺见图2-123、工艺说明锯片铣刀热处理主要问题是平面弯曲难以达到技术要求,这里热应力对弯曲变形引起了很大的影响,为此工艺中采取了如下措施:(1)消除处理以前的加工应力,有利于减少淬火弯曲变形。
(2)采用多次预热和多次分级冷却的方法,降低热应力。
特别在800℃左右的短时分级(20秒左右)对减少冷却时刀具内外温差和降低热应力引起了很大作用。
(3)采用较低的淬火温度,以增加淬火钢的强度使有利于减少变形。
(4)回火中用夹具压紧。
回火前先按弯曲方向一致重叠用压板压紧,回火后趁热再行施压(如图2-13所示)。
(5)操作应平稳,用“T”形架垂挂加热和冷却。
锯片铣刀采用上述工艺后,对于减少变形有显著的效果,绝大多数能达到技术要求,少数不合格者,可以用反击法校直进行挽救。
(二)减少组合丝锥螺距伸长的工艺材料:W18Cr4V钢规格:长100~150毫米,直径5~20毫米左右,有锥度。
技术要求:(1)硬度:刃部HRC63~66,柄部HRC30~52(2)变形:偏摆≤0.15毫米(3)螺距伸长:每1000毫米,升长值应小于2毫米处理前加工情况:棒料割断加工,碳化物不均匀度≤3级。
热处理工艺:1、淬火回火组合丝锥淬火回火工艺见图2-14.2、处理采用冰冷处理或稳定化处理。
3、工艺说明组合丝锥是加工圆板牙内螺孔的二类工具,形状如丝锥铰刀(上面有螺纹)。
如按常规处理(不等温),每1000毫米其螺距伸长值要超过2毫米,弯曲变形也大,且切削时有崩齿现象。
同时在使用过程中发现螺距也起了变化。
为此采用贝氏体淬火工艺,时过冷奥氏体部分转变为贝氏体,减少组合丝锥变形的主要矛盾即组织应力,防止体积变形。
为了保证弯曲变形合格,可在等温后进行热校直,弯曲大的,可采用回火后的热校直。
因为等温后残余奥氏体较多,有利于第一次回火后的热校直。
为了保证组合丝锥使用过程中尺寸稳定,采用在四次回火后的稳定化处理,即在370℃左右保温6~8小时,亦可在淬火后进行病理处理(我厂经常用第一种方法)。
最后进行柄部处理:即在900℃左右加热(8~10秒/毫米),而后与200℃硝盐中冷却,使柄部硬度达到HRC30~52.采用上述工艺后,能达到技术要求。
(三)剃齿刀(图2-15)减少内孔开裂及使用中内孔变形的工艺材料:W18Cr4V钢规格:以直径240毫米的剃齿刀为例。
技术要求:硬度HRC63~66成品内孔公差:B级-------8~13微米(生产)A级-------5~8毫米热处理前加工情况:反复锻打后碳化物不均匀度≤4级。
热处理工艺:1、淬火回火剃齿刀淬火回火工艺见图2-16。
2、处理560℃四次回火后稳定化处理:370℃保温6~8小时或560℃二次回火后冷处理(-70℃,4~6小时),然后再回火二次(冰冷处理适用于夏季)。
3、工艺说明剃齿刀早热处理中经常出现三个问题,即键槽涨大、内孔开裂以及使用过程中随着放置时间增长而使内孔涨大。
内孔开裂多数是由于剃齿刀中心处的碳化物不均匀性严重引起的。
因为剃齿刀材料较粗,其中心处的碳化物不均匀性在锻造中难以消除。
内孔涨大是由于热处理后存在的较多残余奥氏体在使用过程中发生了转变所引起的。
以上都是由于组织应力导致变形开裂的原因。
为此在热处理工艺上应采取以下措施:(1)为了防止七内孔开裂,采用稍低的淬火温度,以增加刚才的强度,并且用多次预热、多次分级、最后等温的方法,尽量降低钢材的热应力和组织应力。
等温后冷至150℃左右及时回火也有防止开裂的一个步骤。
(2)回火过程中,采用低温入炉(<500℃)、缓慢升温、回火后缓慢冷却的方法,防止回火过程中可能引起的开裂。
(3)为了防止剃齿刀在热处理过程中发生键槽涨大,我们除了采用上述措施,还在淬火夹具上作了改进(见图2-17),用半圆形架子增加刀具内孔与夹具的接触面,放置剃齿刀时,把键槽放在下面,不使键槽在侧面,以防止加热时被拉长。
(4)为了防止使用过程中发生内孔涨大,在等温处理后采用四次回火(硝盐炉),最后进行稳定化处理。
在夏季二次回火后进行冰冷处理,然后再补充回火二次。
我们知道反复多次回火能减少残余奥氏体;而稳定化处理的目的,却是使在反复回火中不能转变饿极少量的残余奥氏体稳定下来,不让它在工具使用中发生转变,保证精度。
冰冷处理的目的,则是促使残余奥氏体的转变,以提高回火质量。
夏季室温高,工件又难冷至室温,反复回火对残余奥氏体的转变不利,从金相上反映,夏季易出现回火不足的现象。
我厂对剃齿刀内孔变形进行过实验,目前采用的稳定化处理工艺,已经历一年多时间的考验,证明能保持剃齿刀内孔变形达到技术要求。
(四)减少大型刀具开裂的工艺材料:W18cr4v钢规格:一直径220×67毫米组合铣刀为例热处理前加工情况:经锻打后,碳化物不均匀度≤6级技术要求:硬度HRC63~66热处理工艺:第一次预热:500~550℃,120分(箱式炉);第二次预热:800~820℃,12分2次。
加热:1200~1265℃,12分→空冷20秒左右。
第一次分级:580~620℃,10分→空冷1分左右第二次分级:350~400℃,10分。
等温:240~280℃,120~180分缓冷至150℃左右及时回火第一次回火:560℃,60分→260~280℃,120分。
静置空气中缓慢冷却;第二、三、四次回火:560℃,60分3次。
操作要领:(1)预热时间必须充分;(2)高温炉须经脱氧后淬火,防止脱碳;(3)进入高温炉1分钟后在升温,升温应缓慢,采取较小的电流,加热温度应严格控制;(4)工件在预热及加热的入炉和出炉前后,必须在盐浴中上下运动1分钟左右;冷却是亦应在冷却剂中上下运动1~2分钟,使内部温度均匀;(5)等温和分级,硝盐浴内应无水份;(6)第一次回火前的工件温度,应在150℃左右;(7)第一次回火最好在400℃入炉,保温30分钟,然后缓慢升温。
其他几次回火,入炉温度应控制在500℃以下,然后缓慢升温;(8)回火冷却应缓慢,最好放在铁筒中静置空冷;(9)回火结束冷透后才可清洗。
上述工艺采用了二次贝氏体淬火,使大型的组合铣刀能达到技术要求。
一般大型刀具只采用一次贝氏体淬火,即能防止开裂(如剃齿刀)。