电泳常见问题及处理方法
电泳常见问题及解决方法
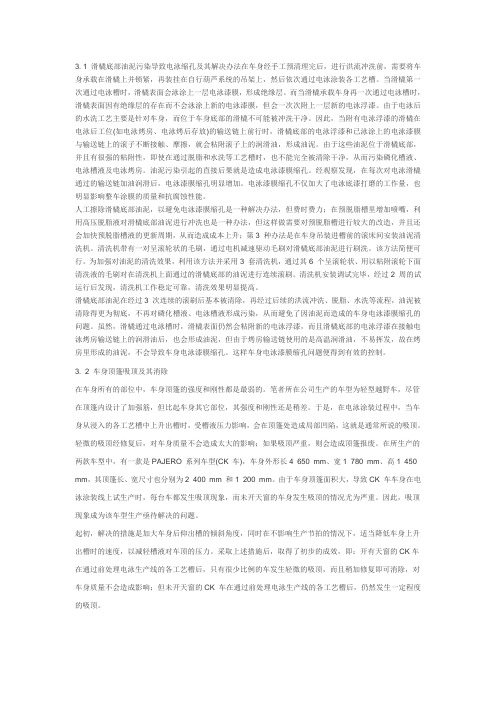
3. 1 滑橇底部油泥污染导致电泳缩孔及其解决办法在车身经手工预清理完后,进行洪流冲洗前,需要将车身承载在滑橇上并锁紧,再装挂在自行葫芦系统的吊架上,然后依次通过电泳涂装各工艺槽。
当滑橇第一次通过电泳槽时,滑橇表面会泳涂上一层电泳漆膜,形成绝缘层。
而当滑橇承载车身再一次通过电泳槽时,滑橇表面因有绝缘层的存在而不会泳涂上新的电泳漆膜,但会一次次附上一层新的电泳浮漆。
由于电泳后的水洗工艺主要是针对车身,而位于车身底部的滑橇不可能被冲洗干净。
因此,当附有电泳浮漆的滑橇在电泳后工位(如电泳烤房、电泳烤后存放)的输送链上前行时,滑橇底部的电泳浮漆和已泳涂上的电泳漆膜与输送链上的滚子不断接触、摩擦,就会粘附滚子上的润滑油,形成油泥。
由于这些油泥位于滑橇底部,并且有很强的粘附性,即使在通过脱脂和水洗等工艺槽时,也不能完全被清除干净,从而污染磷化槽液、电泳槽液及电泳烤房。
油泥污染引起的直接后果就是造成电泳漆膜缩孔。
经观察发现,在每次对电泳滑橇通过的输送链加油润滑后,电泳漆膜缩孔明显增加。
电泳漆膜缩孔不仅加大了电泳底漆打磨的工作量,也明显影响整车涂膜的质量和抗腐蚀性能。
人工擦除滑橇底部油泥,以避免电泳漆膜缩孔是一种解决办法,但费时费力;在预脱脂槽里增加喷嘴,利用高压脱脂液对滑橇底部油泥进行冲洗也是一种办法,但这样做需要对预脱脂槽进行较大的改造,并且还会加快预脱脂槽液的更新周期,从而造成成本上升;第3 种办法是在车身吊装进槽前的滚床间安装油泥清洗机。
清洗机带有一对呈滚轮状的毛刷,通过电机减速驱动毛刷对滑橇底部油泥进行刷洗。
该方法简便可行。
为加强对油泥的清洗效果,利用该方法并采用3 套清洗机,通过其6 个呈滚轮状、用以粘附滚轮下面清洗液的毛刷对在清洗机上面通过的滑橇底部的油泥进行连续滚刷。
清洗机安装调试完毕,经过2 周的试运行后发现,清洗机工作稳定可靠,清洗效果明显提高。
滑橇底部油泥在经过3 次连续的滚刷后基本被清除,再经过后续的洪流冲洗、脱脂、水洗等流程,油泥被清除得更为彻底,不再对磷化槽液、电泳槽液形成污染,从而避免了因油泥而造成的车身电泳漆膜缩孔的问题。
电泳常见问题及解决方法

一、颗粒(1)现象在烘干后的电泳涂膜表面上有手感粗糙的、较硬的粒子,或肉眼可见的细小痱子,往往被涂物的水平面较垂直面严重,这种漆膜病态称为颗粒。
(2)产生原因①CED槽液PH值偏高,碱性物质混入,造成槽液不稳定,树脂析出或凝聚。
②槽内有沉淀“死角”和裸露金属处。
③电泳后清洗液脏、含漆量过高,过滤不良。
④进入的被涂物面及吊具不洁,磷化后水洗不良。
⑤在烘干过程中落上颗粒状污物。
⑥涂装环境脏。
⑦补给涂料或树脂溶解不良,有颗粒。
(3)防治方法①将CED槽液的PH值控制在下限,严禁带入碱性物质,加强过滤,加速槽液的更新。
②消除易沉淀的“死角”和产生沉积涂膜的裸露金属件。
③加强过滤,推荐采用精度为25μm的过滤元件,养活泡沫。
④确保被涂面清洁,不应有磷化沉渣,防止二次污染。
⑤清理烘干室和空气过滤器。
⑥保持涂装环境清洁,检查并消除空气的尘埃源。
⑦确保新补涂料溶解良好,色浆细度在标准范围内。
二、缩孔(陷穴)(1)现象在湿的电泳涂膜上看不见,当烘干后漆膜表面出现火山口状的凹坑,直径通常为~,不露底的称为陷穴、凹洼、露底的称为缩孔,中间有颗粒的称为“鱼眼”。
产生这一弊病的主要原因是电泳湿涂膜中或表面有尘埃,油污与电泳涂料不相溶的粒子,成为陷穴中心,使烘干初期的湿漆膜流展能力不均衡,而产生涂膜缺陷。
(2)产生原因①被涂物前处理脱脂不良或清洗后又落上油污、尘埃。
②槽液中混入油污,漂浮在液面或乳化在槽液中。
③电泳后冲洗液混入油污。
④烘干室内不净,循环风内含油分。
⑤槽液的颜基比失调,颜料含量低的易产生缩孔。
⑥涂装环境脏、空气可能含有油雾、漆雾,含有机硅物质等污染被涂物或湿涂膜。
⑦补给涂料有缩孔或其中树脂溶解不良,中和不好。
(3)防治方法①加强被涂物的脱脂工序,确保磷化膜不被二次污染。
②在槽液循环系统设除油过滤袋,同时查清油污源,严禁油污带入槽中。
③提高后清洗水质,加强过滤。
④保持烘干室和循环热风的清洁。
⑤调整槽液的颜基比,适当加色浆提高颜料含量。
电泳常见问题和解决方法
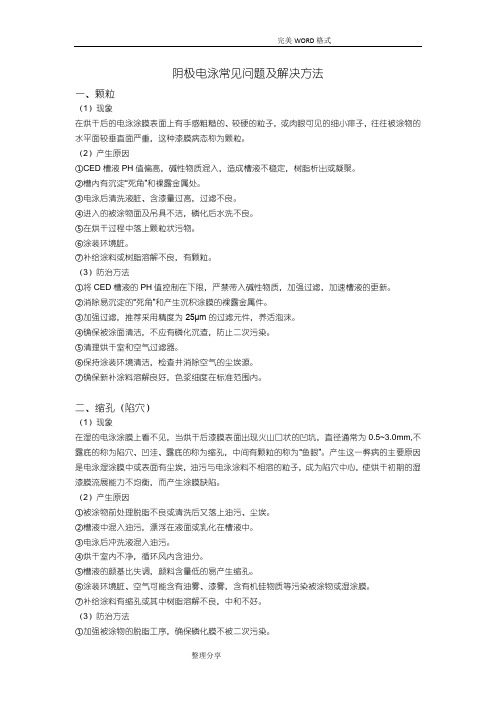
阴极电泳常见问题及解决方法一、颗粒(1)现象在烘干后的电泳涂膜表面上有手感粗糙的、较硬的粒子,或肉眼可见的细小痱子,往往被涂物的水平面较垂直面严重,这种漆膜病态称为颗粒。
(2)产生原因①CED槽液PH值偏高,碱性物质混入,造成槽液不稳定,树脂析出或凝聚。
②槽内有沉淀“死角”和裸露金属处。
③电泳后清洗液脏、含漆量过高,过滤不良。
④进入的被涂物面及吊具不洁,磷化后水洗不良。
⑤在烘干过程中落上颗粒状污物。
⑥涂装环境脏。
⑦补给涂料或树脂溶解不良,有颗粒。
(3)防治方法①将CED槽液的PH值控制在下限,严禁带入碱性物质,加强过滤,加速槽液的更新。
②消除易沉淀的“死角”和产生沉积涂膜的裸露金属件。
③加强过滤,推荐采用精度为25μm的过滤元件,养活泡沫。
④确保被涂面清洁,不应有磷化沉渣,防止二次污染。
⑤清理烘干室和空气过滤器。
⑥保持涂装环境清洁,检查并消除空气的尘埃源。
⑦确保新补涂料溶解良好,色浆细度在标准范围内。
二、缩孔(陷穴)(1)现象在湿的电泳涂膜上看不见,当烘干后漆膜表面出现火山口状的凹坑,直径通常为0.5~3.0mm,不露底的称为陷穴、凹洼、露底的称为缩孔,中间有颗粒的称为“鱼眼”。
产生这一弊病的主要原因是电泳湿涂膜中或表面有尘埃,油污与电泳涂料不相溶的粒子,成为陷穴中心,使烘干初期的湿漆膜流展能力不均衡,而产生涂膜缺陷。
(2)产生原因①被涂物前处理脱脂不良或清洗后又落上油污、尘埃。
②槽液中混入油污,漂浮在液面或乳化在槽液中。
③电泳后冲洗液混入油污。
④烘干室内不净,循环风内含油分。
⑤槽液的颜基比失调,颜料含量低的易产生缩孔。
⑥涂装环境脏、空气可能含有油雾、漆雾,含有机硅物质等污染被涂物或湿涂膜。
⑦补给涂料有缩孔或其中树脂溶解不良,中和不好。
(3)防治方法①加强被涂物的脱脂工序,确保磷化膜不被二次污染。
②在槽液循环系统设除油过滤袋,同时查清油污源,严禁油污带入槽中。
③提高后清洗水质,加强过滤。
④保持烘干室和循环热风的清洁。
电泳常见问题及处理方法
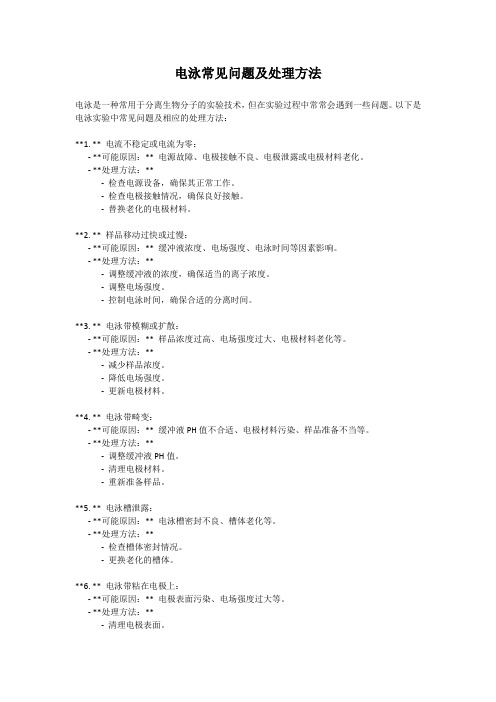
电泳常见问题及处理方法电泳是一种常用于分离生物分子的实验技术,但在实验过程中常常会遇到一些问题。
以下是电泳实验中常见问题及相应的处理方法:**1. ** 电流不稳定或电流为零:- **可能原因:** 电源故障、电极接触不良、电极泄露或电极材料老化。
- **处理方法:**-检查电源设备,确保其正常工作。
-检查电极接触情况,确保良好接触。
-替换老化的电极材料。
**2. ** 样品移动过快或过慢:- **可能原因:** 缓冲液浓度、电场强度、电泳时间等因素影响。
- **处理方法:**-调整缓冲液的浓度,确保适当的离子浓度。
-调整电场强度。
-控制电泳时间,确保合适的分离时间。
**3. ** 电泳带模糊或扩散:- **可能原因:** 样品浓度过高、电场强度过大、电极材料老化等。
- **处理方法:**-减少样品浓度。
-降低电场强度。
-更新电极材料。
**4. ** 电泳带畸变:- **可能原因:** 缓冲液PH值不合适、电极材料污染、样品准备不当等。
- **处理方法:**-调整缓冲液PH值。
-清理电极材料。
-重新准备样品。
**5. ** 电泳槽泄露:- **可能原因:** 电泳槽密封不良、槽体老化等。
- **处理方法:**-检查槽体密封情况。
-更换老化的槽体。
**6. ** 电泳带粘在电极上:- **可能原因:** 电极表面污染、电场强度过大等。
- **处理方法:**-清理电极表面。
-降低电场强度。
**7. ** 电泳结束后凝胶上有色斑:- **可能原因:** 染色不充分、凝胶中存在异物等。
- **处理方法:**-加强染色过程。
-小心操作,避免在凝胶中引入异物。
**8. ** 凝胶破裂:- **可能原因:** 凝胶制备不当、电场强度过大等。
- **处理方法:**-仔细制备凝胶,确保无气泡。
-降低电场强度。
电泳实验中出现问题时,及时采取正确的处理方法是确保实验成功的关键。
通过检查设备、调整实验条件和注意样品制备,可以有效避免或解决电泳过程中的常见问题。
SDS-PAGE电泳常见问题及解决

SDS-PAGE电泳过程中常见问题以及解决方法2Q:SDS-PAGE电泳的基本原理?A:SDS-聚丙烯酰胺凝胶电泳,是在聚丙烯酰胺凝胶系统中引进SDS(十二烷基硫酸钠),SDS会与变性的多肽,并使蛋白带负电荷,由于多肽结合SDS的量几乎总是与多肽的分子量成正比而与其序列无关,因此SDS多肽复合物在丙稀酰胺凝胶电泳中的迁移率只与多肽的大小有关,在达到饱和的状态下,每克多肽可与1.4g去污剂结合。
当分子量在15KD到200KD之间时,蛋白质的迁移率和分子量的对数呈线性关系,符合下式:logMW=K-bX,式中:MW为分子量,X为迁移率,k、b均为常数,若将已知分子量的标准蛋白质的迁移率对分子量对数作图,可获得一条标准曲线,未知蛋白质在相同条件下进行电泳,根据它的电泳迁移率即可在标准曲线上求得分子量。
Q:配胶缓冲液系统对电泳的影响?A:在SDS-PAGE不连续电泳中,制胶缓冲液使用的是Tris-HCL缓冲系统,浓缩胶是pH6.7,分离胶pH8.9;而电泳缓冲液使用的Tris-甘氨酸缓冲系统。
在浓缩胶中,其pH环境呈弱酸性,因此甘氨酸解离很少,其在电场的作用下,泳动效率低;而CL离子却很高,两者之间形成导电性较低的区带,蛋白分子就介于二者之间泳动。
由于导电性与电场强度成反比,这一区带便形成了较高的电压剃度,压着蛋白质分子聚集到一起,浓缩为一狭窄的区带。
当样品进入分离胶后,由于胶中pH的增加,呈碱性,甘氨酸大量解离,泳动速率增加,直接紧随氯离子之后,同时由于分离胶孔径的缩小,在电场的作用下,蛋白分子根据其固有的带电性和分子大小进行分离。
所以,pH对整个反应体系的影响是至关重要的,实验中在排除其他因素之后仍不能很好解决问题的情况,应首要考虑该因素。
Q:样品如何处理?A:根据样品分离目的不同,主要有三种处理方法:还原SDS处理、非还原SDS处理、带有烷基化作用的还原SDS处理。
1、还原SDS处理:在上样buffer中加入SDS和DTT(或Beta巯基乙醇)后,蛋白质构象被解离,电荷被中和,形成SDS与蛋白相结合的分子,在电泳中,只根据分子量来分离。
SDS-PAGE电泳的常见问题解析(FAQ)

活性蛋白整体方案SDS-PAGE电泳的常见问题解析(FAQ)1.关于凝胶的一些问题1.胶的凝结不好,例如有花纹特别是浓度高的胶在冬天温度较低的情况下,在分离胶的下部有波浪样的花纹,凝胶不均匀。
解决方法:加大TEMED和过硫酸胺的量,使其凝结速度加快。
同时洗干净玻璃板,防止有残留的胶干结在玻璃板上。
2.胶不凝,解决方法:温度较低时加大TEMED和过硫酸胺的量,过硫酸胺必须新鲜配制。
如若还是不行重新配制一下缓冲溶液。
3.胶易碎,例如浓度较高的胶在染色和脱色过程以及扫描过程中破裂。
解决方法:首先在上述过程中一定要动作轻缓,其次在室温较高的情况下可以适当减少TEMED和过硫酸胺的量。
4.电泳完后胶上有很多长条纹的杂带,解决方法:建议电泳缓冲液不要回收利用。
配制胶的溶液一定要纯。
2.凝胶时间不对通常胶在30分钟到1小时内凝。
如果凝的太慢,可能是TEMED,AP剂量不够。
如果凝的太快,可能是APS和TEMED用量过多,此时胶太硬易裂,电泳时易烧胶。
3.浓缩胶与分离胶断裂、板间有气泡对电泳的影响前者主要原因是拔梳子用力不均匀或过猛所致;后者是由于在解除制胶的夹子后,板未压紧而致空气进入引起的,一般对电泳结果不会有太大的影响。
4.样品的处理根据样品分离目的不同,主要有三种处理方法:还原SDS处理、非还原SDS处理、带有烷基化作用的还原SDS 处理。
1.还原SDS处理:在上样buffer中加入SDS和DTT(或Beta巯基乙醇)后,形成SDS与蛋白相结合的分子。
2.带有烷基化作用的还原SDS处理:碘乙酸胺的烷基化作用可以很好的保护SH基团,得到较窄的谱带;另碘乙酸胺可捕集过量的DTT,而防止纹理现象的产生。
100uL样品缓冲液中加入10uL20%的碘乙酸胺,并在25℃下保藏30min。
3.非还原SDS处理:生理体液、血清、尿素等样品,一般只用1%SDS沸水中煮3min,未加还原剂,因而蛋白折叠未被破坏,不可作为测定分子量来使用。
电泳过程中常见的问题及解决的方法
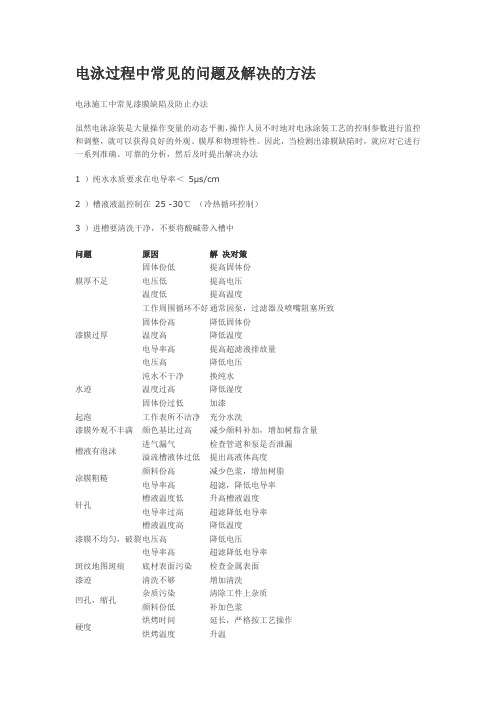
电泳过程中常见的问题及解决的方法电泳施工中常见漆膜缺陷及防止办法虽然电泳涂装是大量操作变量的动态平衡,操作人员不时地对电泳涂装工艺的控制参数进行监控和调整,就可以获得良好的外观、膜厚和物理特性。
因此,当检测出漆膜缺陷时,就应对它进行一系列准确、可靠的分析,然后及时提出解决办法1 )纯水水质要求在电导率<5μs/cm2 )槽液液温控制在25 -30℃(冷热循环控制)3 )进槽要清洗干净,不要将酸碱带入槽中问题原因解决对策膜厚不足固体份低提高固体份电压低提高电压温度低提高温度漆膜过厚工作周围循环不好通常因泵,过滤器及喷嘴阻塞所致固体份高降低固体份温度高降低温度电导率高提高超滤液排放量电压高降低电压水迹沌水不干净换纯水温度过高降低湿度固体份过低加漆起泡工作表所不洁净充分水洗漆膜外观不丰满颜色基比过高减少颜料补加,增加树脂含量槽液有泡沫进气漏气检查管道和泵是否泄漏溢流槽液体过低提出高液体高度涂膜粗糙颜料份高减少色浆,增加树脂电导率高超滤,降低电导率针孔槽液温度低升高槽液温度电导率过高超滤降低电导率漆膜不均匀,破裂槽液温度高降低温度电压高降低电压电导率高超滤降低电导率斑纹地图斑痕底材表面污染检查金属表面漆迹清洗不够增加清洗凹孔,缩孔杂质污染清除工件上杂质颜料份低补加色浆硬度烘烤时间延长,严格按工艺操作烘烤温度升温不够流平加溶剂麻点液温低升温溶剂少加溶剂浓度低加漆条纹表面外观不佳电压升高快溶剂含量低槽液固含量低常见故障及其纠正方法故障产生原因纠正方法桔皮或表面粗糙电压过高降低电压溶液温度高降低温度固体分过高稀释溶液极距太近加大极距烘烤加温太快压缩空气吹干后再烘烤PH 值过高用有机酸调整针孔或麻点固体分过低调整至工艺范围PH 值过低降低溶液酸度清洗水不干净换清洗水溶液电导率太高超滤去掉杂质离子膜厚太薄增加电泳电压或时间电镀表面针孔压缩空气吹干后再烘烤火山口或油点工件上附有油加强除油工序槽液面有油渍防止槽液被油污染颗粒污染加强循环过滤和超滤电压高膜层厚降低电泳电压和时间彩虹膜层太薄增加电泳电压颜色不符膜层太厚或太薄选择合适的工作电压和时间调配涂料时,颜色比例错严格按工艺配方配制电泳漆溶剂太多,渗透能力差,膜层厚薄不均调整溶剂含量,使其符合工艺规范不规则图形前处理不彻底加强前处理工序硬度不够烤烘时间短或温度低严格按工艺规范进行涂装面点状或片状颜色差异零件有针孔或砂眼杜绝不合格工件下槽色料乳化搅拌不匀加强电泳漆搅拌表面有水液用压缩空气吹干水滴未干即烘烤用压缩空气吹干电泳前水洗不彻底加强入槽产零件的清洗。
WB中常见问题和解决方法(学术论文)

1.电泳中常出现的一些现象:●︶条带呈笑脸状原因:凝胶不均匀冷却,中间冷却不好;电泳系统温度偏高。
●︵条带呈皱眉状原因:可能是由于装置不合适,特别可能是凝胶和玻璃挡板底部有气泡,或者两边聚合不完全。
●拖尾原因:样品溶解不好。
●纹理(纵向条纹)原因:样品中含有不溶性颗粒。
●条带偏斜原因:电极不平衡或者加样位置偏斜。
●条带两边扩散原因:加样量过多。
2.Western blot结果中背景较高可能的原因及建议:●膜封闭不够延长封闭的时间;选择更加适合的封闭液。
●一抗稀释度不适宜对抗体进行滴度测试,选择最适宜的抗体稀释度。
●一抗孵育的温度偏高建议4℃结合过夜。
●选择的膜容易产生高背景一般硝酸纤维素膜的背景会比PVDF膜低。
●膜在实验过程中干过实验过程中要注意保持膜的湿润。
●检测时曝光时间过长减少曝光时间。
3.Western blot结果中杂带较多可能的原因及建议:●目的蛋白有多个修饰位点(磷酸化位点、糖基化位点、乙酰化位点等),本身可以呈现多条带。
查阅文献或进行生物信息学分析,获得蛋白序列的修饰位点信息,通过去修饰确定蛋白实际大小。
●目的蛋白有其它剪切本查阅文献或生物信息学分析可能性。
●样本处理过程中目的蛋白发生降解加入蛋白酶抑制剂;样本处理时在冰上操作。
●上样量过高,太敏感适当减少上样量。
●一抗特异性不高重新选择或制备高特异性的抗体。
●一抗不纯纯化抗体●一抗或者二抗浓度偏高降低抗体浓度。
4.Western blot结果中无信号或显示信号弱可能的原因及建议:●检测样本不表达目的蛋白选择表达量高的细胞作为阳性对照,用于确定检测样本是否为阴性。
●检测样本低表达目的蛋白提高上样量,裂解液中注意加入蛋白酶抑制剂。
●转移不完全或过转移可以用丽春红染膜并结合染胶(考马斯亮蓝)后确定条带是否转至膜上或转移过头;适当调整转膜的时间和电流。
●抗体不能识别测试种属的相关蛋白购买抗体前应当认真阅读抗体说明书,确定其是否能够交叉识别测试种属的对应蛋白。
- 1、下载文档前请自行甄别文档内容的完整性,平台不提供额外的编辑、内容补充、找答案等附加服务。
- 2、"仅部分预览"的文档,不可在线预览部分如存在完整性等问题,可反馈申请退款(可完整预览的文档不适用该条件!)。
- 3、如文档侵犯您的权益,请联系客服反馈,我们会尽快为您处理(人工客服工作时间:9:00-18:30)。
电泳常见问题及处理方法1.缩孔这类缺陷在湿的漆膜上看不见,当烘干后漆膜表面出现直径通常为0.5-3.0mm漏底微孔、不漏底的火山口状的凹陷,称为陷穴、凹洼,露底者为缩孔,中间有颗粒但不刮手的称为“鱼眼”。
由于电泳漆湿膜中或表面有尘埃、油渍或与电泳涂料不相容的粒子,成为陷穴中心,因而产生涂膜缺陷。
很多情况下这类缺陷还与被涂物的材质有关,如金属底材上存在微裂纹和微孔等。
原因1:外来油污污染电泳漆膜,油污附着在工件表面,使电泳漆成膜受到影响。
这种原因引起缩孔的几率较大。
解决方法:可检查输送机构、挂具,防止油滴污染漆膜。
从电泳设备制造安装开始就要避免上述物质污染,每一种新零件投入电泳前最好进行相关检验,防止受油、硅油、蜡、脂性碳化物、胶水等污染物对工件,电泳设备及电泳槽液的污染。
原因2:前处理除油不干净,造成润湿性不良,使电泳漆烘干后漆膜有缩孔。
解决方法:加强前处理清洗。
原因3:槽液有油污、异物混入,影响电泳漆膜外观。
解决方法:用吸油纸吸去油污,清除槽液内异物,同时避免异物混入,保持电泳槽液清洁原因4:加漆时有电泳漆没搅拌均匀,使槽液无完全熟化,引起漆膜不良。
解决方法:确保加入的电泳漆搅拌均匀,加强槽液循环,使槽液完全熟化原因5:电泳后水洗中含油分或烘干室内不洁净,循环风含油分,使油分附著在漆膜上面烘干后有缩孔。
解决方法:水洗经常更换,烤箱经常清理.烤箱链轨用油可选用耐高温,不会高温挥发为最佳2.针孔工件上有露底针状小孔,称为针孔,它与缩孔的区别是孔径小,中心无异物,且四周无漆膜堆积凹起。
由漆膜再溶解而引起的针孔,称为再溶解针孔;由电泳过程中产生的气体、湿膜脱泡不良而产生的针孔,称为气体针孔;(1)湿膜针孔:工件未进行烘烤,在空气中凉干,可看到的针孔原因1: 电泳电压过高,电流冲击反应过剧,产生气泡过多,或升压速度过快。
解决方法:适当降低电压,加长软启动时间原因2:溶剂含量偏低。
解决方法:添加溶剂,每次添加不能超过1%原因3:槽液温度过低。
解决方法:控制槽液温度在25—30℃原因4:涂料的PH值过低及溶剂过多,使漆膜抵抗杂质能力变弱。
解决方法:提高涂料的PH至4.3—5.3,并将漆膜厚度控制在必要的范围内。
原因5:槽液杂质离子过高,电解反应剧烈,被涂物表面产生的气体多.解决方法:超滤除去杂质离子(1)烘干后针孔:原因1: 固体份过低解决方法:提高固体份至10%原因1: 溶剂含量过低解决方法:提高溶剂含量至1--2%原因2:混入电泳漆中的杂质(油、润滑脂等)粘附在漆膜上。
解决方法:除去电泳漆中的油脂等杂质3.麻点指电泳漆膜表面上有异物的现象;在烘干后的电泳涂装表面上会有手感粗糙的较硬粒子,或肉眼可见的细小颗粒。
原因1:电泳液中存在较粗大的杂质解决方法:检查电泳槽过滤装置,加强电泳槽液的过滤原因2:车间空气中含有的尘埃等漂浮物飘落到放在滴干区的工件上解决方法:搞好车间环境卫生,防止灰尘漂浮原因3:烤炉内存在灰尘等杂物;解决方法:清洁烤炉原因4:前处理清洗不干净解决方法:加强前处理水洗及除油。
原因5:金属工件表面有颗粒,如毛刺或电镀面起泡.解决方法:工件上挂前,先检查工件表面是否有问题4.橘皮电泳漆膜表面形成像橘皮一样连续的波浪状态。
这种缺陷通常是由于涂料流平性不好而造成,应调整槽液涂料原因1:助溶剂含量低解决方法:补充助溶剂,每次添加不能超过1%原因2:补给原漆时没有充分熟化解决方法:原漆补加前进行充分的搅拌原因3:电泳电压过高,时间过长,使涂膜过厚解决方法:适当降低电泳电压,减短电泳时间原因4:槽液PH高解决方法:加乳酸调整至4.3—5.3,总添加量不能超过1‰原因5:槽液颜基比过低;解决方法:补充颜基比较高的电泳漆原因6:槽液中杂质离子过多,电导率过高;解决方法:超滤处理至350—750us/cm5、颜色不均匀是指涂层烘烤固化后,其颜色的深浅程度不一样,漆膜花脸。
(1)阴阳面原因1:槽液颜基比不合适解决方法:调整颜基比原因2:工件在电泳槽中的位置不当;解决方法:工件应保持在电场中心线与槽两边电极平行且距离相等(2)在同一面上的色泽不一致原因1:槽液中的颜料分散不均匀;解决方法:加强对槽液搅拌循环原因2:固体份含量过低解决方法:补加原料至固体份含量10%原因3:零件形状复杂或上挂方式不对,导致电场被屏蔽;解决方法:改进挂具,安装辅助电极原因4:工件在入电泳槽前氧化,有黑印解决方法:工件进电泳槽前检查底材颜色是否一致原因5:槽液内溶剂含量过低而引起色浆分散不好解决方法:适量补加溶剂,每次添加不能超过1%原因6:溶剂含量过多或电导率过高,引起电泳漆膜不均匀解决方法:超滤处理6.涂膜过薄涂膜过薄指电泳后工件表面漆膜厚度过薄,造成颜色.光泽和遮盖力不理想,质量等级下降。
原因1:电压过低解决方法:升高电压原因2:电泳时间不够解决方法:延长电泳时间原因3:槽液电导率偏低解决方法:减少UF液排放原因4:被涂物通电不良解决方法:清理挂具。
使被涂物通电良好原因5:溶剂含量偏低解决方法:补充溶剂,每次添加不能超过1%原因6:槽液固体份偏低解决方法:提高固体份至10%原因7:PH不当(一般偏低)解决方法:调整PH值至4.3—5.3原因8:槽液温度偏低解决方法:提高槽液温度至25—30℃原因9:极板连接不良或被腐蚀,导电杆连接不良解决方法:检查极板、导电杆电线连接,定期清理极板.导电杆和更新电线7.涂膜过厚工件表面的干漆膜厚度超过工艺规定的要求,但漆膜外观仍很好,则还属于合格品,只是涂料消耗增大,成本提高原因1:槽液中助溶剂含量偏高解决方法:超滤处理原因2:固体份过高解决方法:降低固体份至10%原因3:PH不当解决方法:调整PH4.3—5.3原因4:槽液温度偏高解决方法:降低槽液温度至25—30℃原因5:电压过高解决方法:适当降低电压原因6:电泳时间过长解决方法:适当缩短电泳时间原因9:电导率过高解决方法:超滤处理至350—750us/cm8.工件内表面涂抹过薄(泳透力下降)在正常情况下工件的内腔,夹层结构内表面都能涂上漆,但在生产中有时发现内腔泳涂不上漆或者涂的很薄,这种现象称为泳透力变差原因1:颜基比偏低解决方法:补加色浆提高颜基比原因2:槽液中助溶剂含量过低解决方法:适量补加溶剂,每次添加不能超过1%原因3:电泳电压偏低解决方法:适当提高电压原因4:槽液搅拌不良解决方法:加强搅拌,疏通管道、喷嘴原因5:槽液中杂质离子含量过多解决方法:超滤处理9.气泡(1)气泡产生原因:工件浸入电泳涂料中时,卷入气泡或空气、循环系统原因产生的空气等原因使漆液中含有微小气泡,或工件电极产生气泡过多使漆液流动性差而无法带出原因1:工件浸入电泳涂料中时,卷入气泡或空气解决方法:工件入槽后停留一段时间再通电,使附着在工件上的气泡尽量排尽原因2:工件形状的原因,工件有些位置会藏有空气解决方法:合理设计挂具及调整上挂方式原因3:循环系统原因产生的空气等原因使漆液中含有微小气泡;解决方法:检查循环系统配置是否合理,过滤桶是否有空气,管道是否漏气原因4:电泳槽主副槽液位落差过大,使副槽气泡过多解决方法:电泳槽主副槽液位落差控制在5CM以内(2)气泡产生原因:工件前处理不干净使工件进电泳槽时工件上有油污.水洗槽内有油污,电泳槽内进有油污.吹水空气内有油污或烤箱内有油污;原因1:工件前处理不干净使工件进电泳槽时工件上有油污.解决方法:加强前处理除油,进电泳槽前观查工件上有无油污原因2:水洗槽内有油污解决方法:水洗槽经常换水,发现水洗槽有油污清洗水洗槽原因3:电泳槽内进有油污解决方法:加强过滤或清槽过滤原因4:烤箱内有油污解决方法:保持烤箱内清洁原因5:吹水时空气中有油污解决方法:空压机经常放水,增加油水分离器10.掉漆掉漆的原因一般为涂层结合力不好,或因产品碰撞而导致漆膜从底材脱落的现象(1)湿膜掉漆:原因1:清洗或用气枪吹水时,所用压力太大,对湿膜造成太大的冲击力解决方法:减小清洗或用气枪吹水时压力原因2:工件电泳后,因操作不小心,工件和挂具、其它工件或其它物品碰撞而造成的掉漆解决方法:工件电泳后小心操作,避免碰撞(2)烘干后掉漆原因1:槽液电导率太高,使其丧失附着力解决方法:超滤处理,降低电导率350—750us/cm原因2:烘烤时温度或时间不够,漆膜无完全固化解决方法:提高烘烤温度或加长烘烤时间,根据电泳漆需要控制在130—170℃,时间30min原因3:颜基比过高。
槽液中色浆含量过高,使漆膜附着力变差解决方法:加原漆降低色浆含量原因4:槽液老化,使漆膜失去附着力解决方法:超滤后补充新漆,生产中保持新漆添加速度原因5:前处理清洗不干净,或除油不彻底,使漆膜附着力差解决方法:加强前处理除油和清洗11.堆漆堆漆是指产品烘干前或烘干后工件表面有明显块状漆层(1)湿膜堆漆:产品电泳后,烘干前可见到明显漆块原因1:前处理药水由工件或挂具带入电泳槽,引起槽液结块解决方法:加强前处理水洗。
如前处理药水带入过多已引起槽内有死漆,需清槽和超滤处理原因2:电泳漆或色浆搅拌不均匀就加入电泳槽解决方法:槽液过滤,加强电泳漆和色浆的搅拌原因3:槽液长时间不用老化或槽底有沉淀解决方法:清洗电泳槽,并将槽液过滤后超滤处理,再补充新漆或溶剂(2)烘干后堆漆:原因:工件进入烤箱过急,工件上残留的水珠在100℃以下时没有烘干,经高温烘烤后沸腾,使漆膜爆裂而引起堆积解决方法:加强吹水和预烘烤12.水印水印是指烘烤后的漆膜上有水滴状或流淌的条纹,有水迹的地方与周围涂层在光泽、粗糙度上不一致原因1:水质造成的水印:电泳涂料在涂装生产过程对水质要求较高, 特别是被泳件电泳后需经4次水洗,最后一道需要保持水质干净,稍不注意就会出现电泳固化后表面有水印( 水渍) 。
解决方法:1.保持水洗槽的水质纯度,加强水洗。
2.在最后水洗槽加温40--50度左右。
3.添加脱水剂。
原因2:电导率造成的水印:电泳槽电导率较高时也会产生水印,保持电泳槽液的电导率在正常范围。
解决方法:超滤排水,降低槽液电导率。
原因3:电泳漆膜引起的水印:电泳漆膜较薄时,漆膜流平较差,漆膜表面的水渍不容易流掉,电泳漆膜是由多个带角的分子组成。
分子较少时结构重叠不够紧密,水分会残留在分子间的间隙内不易排出。
解决方法:1.调高电泳液的工作温度(25--30度)。
2.延长电泳时间或增加电压。
3.添加电泳漆,提高固体份至10%。
4.补充溶剂。
原因4:溶剂造成的水印:溶剂添加量过多时,漆膜容易起皱,油性溶剂本身不容易溶入漆中。
解决方法:1.加速搅拌或超滤排掉一部分溶剂。
2.加温(不能超过45度,保温2小时)可以加速漆与溶剂相溶。
3.电泳槽较小时可以改为水性溶剂。
4.油性溶剂在大平面上容易留下凹点现象。