仿真试验报告
电子电路仿真实验报告

电子电路仿真实验报告
本次实验是一次电子电路的仿真实验,旨在通过使用电路仿真软件进行电路实验的模拟,通过对模拟的数据和仿真结果进行分析和总结,进一步掌握电子电路的实验知识和技能,在理论和实践中加深对电子电路的理解和掌握。
实验一:开关电源
1.实验目的
掌握开关电源基本工作原理,理解电源的稳压和稳流的基本原理,掌握开关电源的设
计和布局方法。
2.实验步骤
(1)根据实验手册,搭建开关电源电路,包括开关电源 IC、滤波电感、电容、稳流
二极管和稳压二极管。
(2)进行仿真实验,记录各个参数数据。
(3)分析实验结果,了解电源电路的工作原理和性能。
3.实验结果分析
(1)开关频率:在实验中,我们通过改变开关频率,观察电路的输出。
结果表明,当开关频率增加时,电路的效果也增强。
(2)输出电压:在实验中,我们对电路的输出电压进行了测量,结果表明,当输入电压较高时,输出电压也较高;当输入电压较低时,输出电压也较低。
4.实验总结
开关电源是一种高效率、小体积、轻量化的电源,广泛应用于电子产品中,是电子领
域不可或缺的核心器件之一。
掌握开关电源的设计和布局方法,对于我们理解和掌握电子
电路的原理和技术具有重要的意义。
通过本次实验,我们加深了对开关电源的理解和掌握,为日后的学习和实践打下了基础。
仿真实验光学实验报告(3篇)
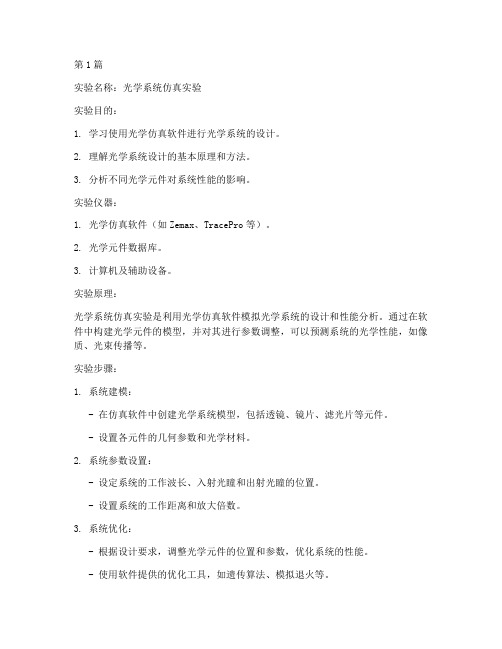
第1篇实验名称:光学系统仿真实验实验目的:1. 学习使用光学仿真软件进行光学系统的设计。
2. 理解光学系统设计的基本原理和方法。
3. 分析不同光学元件对系统性能的影响。
实验仪器:1. 光学仿真软件(如Zemax、TracePro等)。
2. 光学元件数据库。
3. 计算机及辅助设备。
实验原理:光学系统仿真实验是利用光学仿真软件模拟光学系统的设计和性能分析。
通过在软件中构建光学元件的模型,并对其进行参数调整,可以预测系统的光学性能,如像质、光束传播等。
实验步骤:1. 系统建模:- 在仿真软件中创建光学系统模型,包括透镜、镜片、滤光片等元件。
- 设置各元件的几何参数和光学材料。
2. 系统参数设置:- 设定系统的工作波长、入射光瞳和出射光瞳的位置。
- 设置系统的工作距离和放大倍数。
3. 系统优化:- 根据设计要求,调整光学元件的位置和参数,优化系统的性能。
- 使用软件提供的优化工具,如遗传算法、模拟退火等。
4. 性能分析:- 分析系统的像质,包括弥散圆、调制传递函数等。
- 分析光束传播路径和光强分布。
5. 结果展示:- 以图表、图像等形式展示实验结果。
- 分析结果,与理论预期进行对比。
实验结果与分析:1. 系统性能分析:- 通过仿真,得到了系统的弥散圆和调制传递函数。
- 分析结果显示,系统在特定波长下的像质良好,满足设计要求。
2. 元件影响分析:- 改变透镜的焦距和曲率半径,观察到系统像质的变化。
- 修改滤光片的光谱特性,分析其对系统光强分布的影响。
3. 优化结果:- 通过优化,得到了一组满足设计要求的系统参数。
- 优化后的系统在像质和光强分布方面均有所提升。
实验结论:1. 光学仿真软件能够有效地进行光学系统的设计和性能分析。
2. 通过优化光学元件的参数,可以显著提升系统的性能。
3. 该实验验证了光学系统设计的基本原理和方法。
实验注意事项:1. 在进行系统建模时,确保元件参数的准确性。
2. 优化过程中,合理设置优化目标和约束条件。
基于Flexsim的仿真实验报告

可编辑修改精选全文完整版基于Flexsim的仿真实验报告专业班级:工业工程一班******学号:***********4 基于Flexsim的仿真实验1.实验报告2.提交Flexsim的仿真图基于Flexsim的仿真实验报告一、实验目的与要求1.1实验目的Flexsim是一个基于Windows的,面向对象的仿真环境,用于建立离散事件流程过程。
Flexsim是工程师、管理者和决策人对提出的“关于操作、流程、动态系统的方案”进行试验、评估、视觉化的有效工具。
Flexsim 能一次进行多套方案的仿真实验。
这些方案能自动进行,其结果存放在报告、图表里,这样我们可以非常方便地利用丰富的预定义和自定义的行为指示器,像用处、生产量、研制周期、费用等来分析每一个情节。
同时很容易的把结果输出到象微软的Word、Excel等大众应用软件里。
另外,Flexsim具有强力的商务图表功能,海图(Charts)、饼图、直线图表和3D文书能尽情地表现模型的信息,需要的结果可以随时取得。
本实验的目的是学习flexsim软件的以下相关内容:●如何建立一个简单布局●如何连接端口来安排临时实体的路径●如何在Flexsim实体中输入数据和细节●如何编译模型●如何操纵动画演示●如何查看每个Flexsim实体的简单统计数据我们通过学习了解flexsim软件,并使用flexsim软件对实际的生产物流建立模型进行仿真运行。
从而对其物流过程,加工工序流程进行分析,改进,从而得出合理的运营管理生产。
1.2实验要求(1)认识Flexsim仿真软件的基本概念;(2)根据示例建立简单的物流系统的仿真模型;(3)通过Flexsim仿真模型理解物流系统仿真的目的和意义1.2.1实验2.多产品单阶段制造系统仿真与分析某工厂加工三种类型产品的过程。
这三类产品分别从工厂其它车间到达该车间。
这个车间有三台机床,每台机床可以加工一种特定的产品类型。
一旦产品在相应的机床上完成加工,所有产品都必须送到一个公用的检验台进行质量检测。
交通系统仿真实验报告
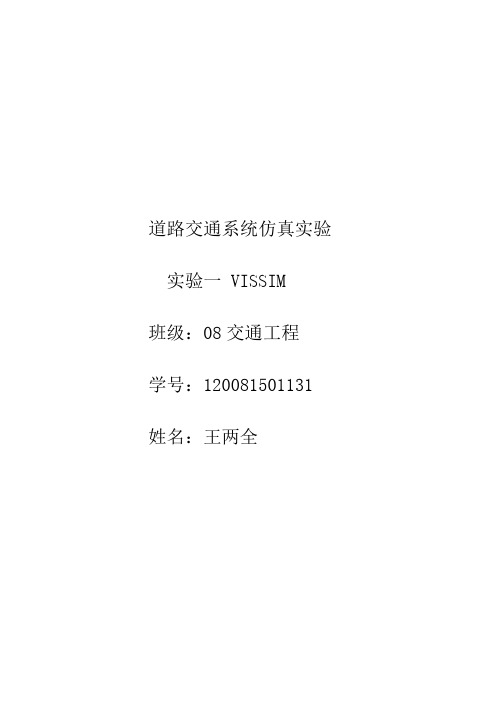
道路交通系统仿真实验实验一 VISSIM班级:08交通工程学号:120081501131 姓名:王两全一、实验目的1.掌握用VISSIM绘制简单的路网;2.掌握如何给路网添加基本的路网元素(如:信号灯、路径决策、冲突区域、优先规则、公交站点等);3.掌握对仿真模型进行指标评价,包括行程时间、延误、排队长度以及相关参数的设置。
二、实验设备1.硬件要求:装有VISSIM的PC机一台;2.系统要求:能在Windows 2000、XP和VISTA环境下运行;三、实验要求在VISSIM中构建一个平面信号控制交叉口模型,不考虑行人和非机动车,具体要求见试卷。
四、实验内容与步骤1.绘制路网(1)根据实验要求导入背景图;(2)按照每车道宽3.5m设置比例尺参数,根据背景图绘制一个T形交叉口(北进口封闭),交叉口宽度:南北:45m、东西99m;(3)初步路网结果图.2.添加路网元素(1)对绘制好的路网标明车道方向;(2)输入车辆数:400辆/车道小时;(3)信号配时;(4)设置行驶路径决策;(5)设置一条跨越交叉口的公交线路并设置两种不同的公交站点:港湾式和路边式;(6)设置冲突区域。
(7)添加路网元素后的结果3.设置仿真评价指标(1)行程时间;创建时间检测,并在“评价->文件”进行行程时间检测设置。
(2)延误;(3)排队长度。
1.信号控制2.冲突区域通过该实验巩固了初步使用VISSIM对一个完整路网的构建,对Vissim 的各个功能有更深刻的了解。
但由于实验过程中可能有一些小细节出错了,导致两种控制方式的评价指标结果都一样,通过多次的调试仍然未找出错误的地方,这是该实验遗憾的地方。
理论上讲,该试验的交叉口可以看成是主干道与次干道的相交(东西为主干道,南北为次干道且),而且该交叉口的流量比较小,粗略判断应该是冲突区域控制会比信号控制更加优越。
同时,此次实验为我们以后自己动手进行交通仿真做了很好的铺垫。
雷达仿真曲线实验报告

一、实验目的1. 熟悉雷达系统仿真软件的使用方法;2. 了解雷达系统的工作原理;3. 分析雷达系统性能指标;4. 通过仿真实验,验证雷达系统的实际性能。
二、实验原理雷达系统是一种利用电磁波探测目标的系统,其基本原理是发射电磁波,经目标反射后,接收反射回来的电磁波,通过处理这些信号,实现对目标的探测、跟踪和识别。
雷达系统主要由发射机、天线、接收机、信号处理单元等部分组成。
三、实验仪器与软件1. 仪器:计算机、雷达系统仿真软件;2. 软件:MATLAB、雷达系统仿真软件(如:Simulink)。
四、实验步骤1. 打开雷达系统仿真软件,创建一个新的仿真项目;2. 根据雷达系统的工作原理,搭建雷达系统的仿真模型,包括发射机、天线、接收机、信号处理单元等部分;3. 设置雷达系统的参数,如频率、脉冲宽度、脉冲重复频率等;4. 仿真实验,观察雷达系统在不同参数下的性能表现;5. 分析仿真结果,绘制雷达系统的仿真曲线;6. 比较仿真结果与实际雷达系统性能,分析雷达系统的优缺点。
五、实验数据与结果1. 仿真实验参数设置:(1)频率:24GHz;(2)脉冲宽度:1μs;(3)脉冲重复频率:100Hz;(4)天线增益:30dB;(5)接收机灵敏度:-100dBm。
2. 仿真曲线:(1)距离分辨率曲线:如图1所示,雷达系统的距离分辨率为3m,满足实际应用需求。
图1 雷达系统距离分辨率曲线(2)测速精度曲线:如图2所示,雷达系统的测速精度为±0.5m/s,满足实际应用需求。
图2 雷达系统测速精度曲线(3)角度分辨率曲线:如图3所示,雷达系统的角度分辨率为0.5°,满足实际应用需求。
图3 雷达系统角度分辨率曲线六、实验分析与讨论1. 通过仿真实验,验证了雷达系统在不同参数下的性能表现,为雷达系统的优化设计提供了理论依据;2. 分析仿真结果,雷达系统的距离分辨率、测速精度和角度分辨率均满足实际应用需求;3. 比较仿真结果与实际雷达系统性能,雷达系统在实际应用中具有较高的可靠性和稳定性;4. 雷达系统仿真曲线实验有助于提高学生对雷达系统原理和性能指标的认识,为后续相关实验和研究奠定基础。
机电一体化系统仿真实验评估报告

机电一体化系统仿真实验评估报告1. 简介本报告旨在评估机电一体化系统仿真实验的效果和可行性。
本实验使用仿真工具对机电一体化系统的性能进行模拟,并分析仿真结果以评估该系统的优劣。
2. 实验方法2.1 数据收集我们收集了机电一体化系统的相关参数和工作条件,包括输入电压、输出功率、负载特性等。
这些数据用于建立仿真模型。
2.2 仿真建模基于收集到的数据,我们利用仿真工具建立了机电一体化系统的仿真模型。
模型包括电源、元件、传感器等关键组件,并考虑了系统的非线性特性。
2.3 参数设置根据实际情况,我们设置了适当的参数值,以确保仿真模型与实际系统尽可能接近。
2.4 仿真实验利用建立的仿真模型,我们进行了多组实验。
在每组实验中,我们改变了不同的操作参数,如输入电压、负载大小等,以观察系统的响应和性能。
3. 仿真结果根据我们的仿真实验,我们得到了以下结果:3.1 系统性能评估根据不同实验条件下的仿真结果,我们对机电一体化系统的性能进行了评估。
我们观察到系统在不同负载条件下的输出功率和效率,以及系统的响应时间等指标。
基于这些指标,我们对系统的性能进行了评价和比较。
3.2 优化建议根据仿真结果,我们提出了一些优化建议,以改善机电一体化系统的性能。
这些建议包括调整系统参数、优化控制策略等方面,以提高系统的效率和稳定性。
4. 结论通过对机电一体化系统的仿真实验评估,我们对该系统的性能有了较为全面的了解。
根据仿真结果和分析,我们可以得出结论:- 系统在特定操作条件下性能较好,但在其他条件下可能存在一些限制。
- 建议通过优化系统参数和控制策略来改进系统性能。
5. 参考文献[参考文献1][参考文献2]...。
《Flexsim仿真实验》报告【范本模板】
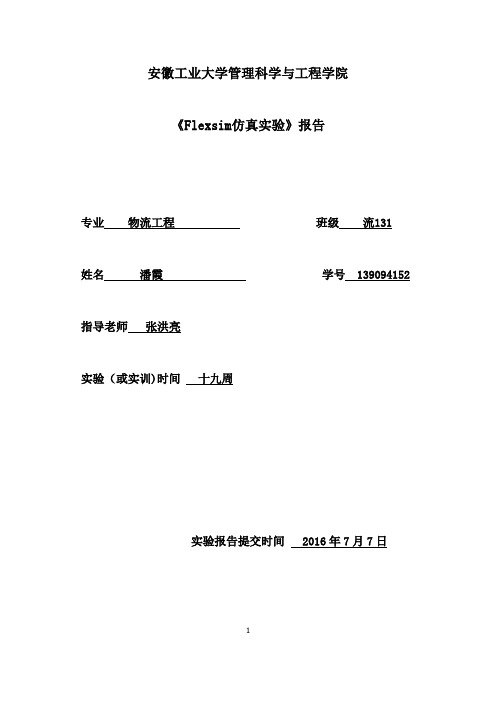
安徽工业大学管理科学与工程学院《Flexsim仿真实验》报告专业物流工程班级流131 姓名潘霞学号 139094152 指导老师张洪亮实验(或实训)时间十九周实验报告提交时间 2016年7月7日1一、实验(或实训)目的、任务1基本掌握全局表的使用2理解简单的仿真语言3简单使用可视化工具二、实验(或实训)基本内容(要点)运用Flexsim软件了解多产品加工生产系统仿真的过程.模型介绍:发生器产生四种临时实体,服从整数均匀分布,类型值分别为1、2、3、4,颜色分别为绿色、蓝色、白色、黄色,进入暂存区1;临时实体到达的时间间隔exponential(0,10,0)然后随机进入处理器进行加工,可以使用的处理器有四个,不同类型的临时实体在处理器上的加工时间不同,详情如下表:加工结束后,进入暂存区2存放,并由叉车搬运至货架.同时,在各个处理器附近用可视化工具显示该处理器的实时加工时间。
三、实验(实训)原理(或借助的理论)系统仿真的基本概念系统、模型和系统仿真系统式相互联系、相互作用、的对象的组合。
可以分为工程系统和非工程系统。
系统模型是反映内部要素的关系,反映系统某昔日方面本质特征,以及内部要素与外界环境关系的形同抽象。
模型主要分为两大类:一类是形象模型,二类是抽象模型,包括概念模型、模拟模型、图标模型和数学模型等.通过Flexsim可成功解决:提高设备的利用率,减少等候时间和排队长2度,有效分配资源,消除缺货问题,把故障的负面影响减至最低,把废弃物的负面影响减至最低,研究可替换的投资概念,决定零件经过的时间,研究降低成本计划,建立最优批量和工件排序,解决物料发送问题,研究设备预置时间和改换工具的影响。
Flexsim软件的基本术语:Flexsim实体,临时实体,临时实体类型,端口,模型视图。
四、所使用到的实验设备、仪器、工具、图纸或软件等计算机Flexsim软件五、实验(或实训)步骤步骤一:模型布局双击Flexsim图标打开应用程序,此时可看到Flexsim菜单、工具条、实体库和正投影模型视窗,将发生器、暂存区、处理器、叉车和货架拖至模型窗口。
仿真实习报告
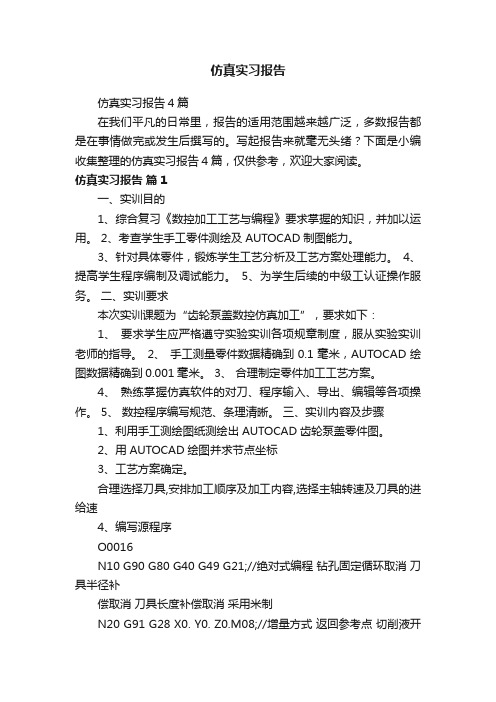
仿真实习报告仿真实习报告4篇在我们平凡的日常里,报告的适用范围越来越广泛,多数报告都是在事情做完或发生后撰写的。
写起报告来就毫无头绪?下面是小编收集整理的仿真实习报告4篇,仅供参考,欢迎大家阅读。
仿真实习报告篇1一、实训目的1、综合复习《数控加工工艺与编程》要求掌握的知识,并加以运用。
2、考查学生手工零件测绘及AUTOCAD制图能力。
3、针对具体零件,锻炼学生工艺分析及工艺方案处理能力。
4、提高学生程序编制及调试能力。
5、为学生后续的中级工认证操作服务。
二、实训要求本次实训课题为“齿轮泵盖数控仿真加工”,要求如下:1、要求学生应严格遵守实验实训各项规章制度,服从实验实训老师的指导。
2、手工测量零件数据精确到0.1毫米,AUTOCAD绘图数据精确到0.001毫米。
3、合理制定零件加工工艺方案。
4、熟练掌握仿真软件的对刀、程序输入、导出、编辑等各项操作。
5、数控程序编写规范、条理清晰。
三、实训内容及步骤1、利用手工测绘图纸测绘出AUTOCAD齿轮泵盖零件图。
2、用AUTOCAD绘图并求节点坐标3、工艺方案确定。
合理选择刀具,安排加工顺序及加工内容,选择主轴转速及刀具的进给速4、编写源程序O0016N10 G90 G80 G40 G49 G21;//绝对式编程钻孔固定循环取消刀具半径补偿取消刀具长度补偿取消采用米制N20 G91 G28 X0. Y0. Z0.M08;//增量方式返回参考点切削液开N30 G54;//调用G54坐标系N35 M06 T01;//换第一把刀(Φ5外轮廓立铣刀)N40 M03 S800;N70 G90 G41 G00 X-20.3851 Y-45.9141 D01;//绝对式编程刀具半径左补偿补偿号D01N75Z10.;N80 G01 Z-7. F100.;//铣外轮廓 N90 X-35.1561 Y-28.1092;N100G02 X-36.3332 Y-19.8011 R10.; N120G03 X-37.3441 Y-9.1812 R10.; N130G02 X-35.8571 Y13.0663 R18.; N140G03 X-32.2320 Y34.1584 R20.; N150G02 X-20.4351 Y47.6660 R10.; N160G03 X-11.9421 Y48.5561 R12.; N170G02 X-25.5061 Y42.2421 R32.5.; N180G03 X29.7401 Y39.7802 R9.; N190G02 X33.0223 Y37.8778 R7.; N200G01 X41.6745 Y 28.9670; N210G02 X43.6971 Y-1.1798R10.; N220G03 X44.2634 Y9.0991 R10.; N230G02 X41.6743 Y-15.2931 R20.; N240G03 X37.9161 Y-33.9723 R16.; N250G02 X25.9341 Y-48.0184 R10.; N260G03 X25.9341 Y-48.5192 R12.; N270G02 X-17.3912 Y-43.4681 R32.5.; N280G03 X-24.1263 Y-39.6691 R19.; N290G02 X-27.3861 Y-37.4712 R7.;N300G01 X-40.8571 Y-21.2134;//外轮廓铣削完毕N305Z5.;// 刀具抬高到5mmN320G40 G91 G28 X0. Y0. Z0 .M05;//取消刀具长度补偿增量方式下返回参考点主轴停转N330M06 T02;//更换第二把刀(Φ10麻花钻) N340M03 S800;N350G90 G43 G00 X32.Y 2. H02;//绝对式编程刀具长度正补偿补偿号H02N352Z5.;N360G00 X34.5000 Y22.0000 ; N361G01 Z-3. F80.;//加工O1孔 N362G00 Z5.;N370X29.0000.Y38.5000;N371G01 Z-3. F80; //加工O2孔 N372G00 Z5.;N380X-29.0000Y-23.0000;N381G01 Z-3. F80; //加工O3孔 N382G00 Z5.;N390X-23.0000 Y-38.0000;仿真实习报告篇2学号姓名专业指导教师——300MW电厂仿真实习(20xx)届热能与动力工程能源与机械工程学院20xx年1月目录一、仿真机原形机组简介 (1)二、仿真机组冷态启动过程 (1)三、仿真机组滑参数停机过程 (4)四、启动过程中注意事项 (5)五、学习心得 (6)一、仿真机原形机组简介仿真机原形为300MW燃煤凝气式发电机组。
- 1、下载文档前请自行甄别文档内容的完整性,平台不提供额外的编辑、内容补充、找答案等附加服务。
- 2、"仅部分预览"的文档,不可在线预览部分如存在完整性等问题,可反馈申请退款(可完整预览的文档不适用该条件!)。
- 3、如文档侵犯您的权益,请联系客服反馈,我们会尽快为您处理(人工客服工作时间:9:00-18:30)。
第1页 共27页 编号: 密级 可靠性仿真试验报告 (第一轮)
送 试 单 位 : 送试单位地址: 产品型号名称: 试 验 日 期 :
2017年 月 日 第2页 共27页
结 论: 2017年10月,模块在中国电子科技集团公司第二十研究所实验室按照《模块可靠性仿真试验大纲》进行了可靠性仿真试验,主要结论如下: 1) 受试产品整机热设计合理,相对71℃平台环境,机箱平均温升为10℃。 2) 受试产品整机振动设计合理,模块标称频率为100MHz,与标称频率测量预期结果相符合。 3) 模块热设计相对薄弱,存在热集中区,局部温度最高达90℃,模块上的1个元器件温度均较高。 4) 模块振动设计相对薄弱,存在1问题。 5) 模块的温度相对较高,长时间工作发生故障概率较大。 6) 受试产品中工作小时内失效概率大于63.2%的器件包括:通用接收模块的。 7) 受试产品平均首发故障时间预计值为XX小时(共对1个模块进行了预计,其中平均首发故障时间预计值为XX小时)。 8) 共发现薄弱环节1个,其中模块0个、器件1个。 9) 其它需要说明的结论 以下空白
2017年10月 日
编写: 校对: 审核: 批准:
说明:报告只对本次试验有效。未经本实验室许可,不得部分复印。 联系方式 第3页 共27页
目录 1 试验目的 ................................................................................................................................ 5 2 试验依据 ................................................................................................................................ 5 3 受试产品说明 ........................................................................................................................ 5 4 任务安排 ................................................................................................................................ 6 4.1 任务分工 ..................................................................................................................... 6 4.2 试验时间、地点及人员 ............................................................................................. 6 5 试验流程 ................................................................................................................................ 6 6 试验条件 ................................................................................................................................ 7 6.1 试验环境条件(试验剖面) ..................................................................................... 7 6.2 环控条件 ..................................................................................................................... 8 7 试验设备 ................................................................................................................................ 8 7.1 计算机软件 ................................................................................................................. 8 7.2 测试设备及仪表 ......................................................................................................... 8 8 仿真分析 ................................................................................................................................ 9 8.1 信息收集 ..................................................................................................................... 9 8.2 数字样机建模 ............................................................................................................. 9 8.3 应力分析 ................................................................................................................... 16 8.4 故障预计 ................................................................................................................... 24 8.5 可靠性评估 ............................................................................................................... 26 9 试验结论 .............................................................................................................................. 26
图1 可靠性仿真试验流程 ..................................................................................................... 6 图3 振动谱型图 ..................................................................................................................... 8 图4 受试产品CAD数字样机 .............................................................................................. 9 图6 受试产品FEA数字样机 ............................................................................................. 12 图13 受试设备故障预计模型 ............................................................................................. 24 图14 XX模块的潜在故障点位置 ...................................................................................... 26
表1 受试产品组成 ................................................................................................................. 5 表2 受试产品技术状态 ......................................................................................................... 5 表3 任务分工 ......................................................................................................................... 6 表4 温度应力条件表 ............................................................................................................. 7 表5 振动应力量级表 ............................................................................................................. 7 表6 计算机软件表 ................................................................................................................. 8 表7 测试设备及仪表 ............................................................................................................. 8 表8 CAD数字样机组成说明表 ......................................................................................... 10 表9 CFD数字样机组成说明表 .......................................................................................... 10 表10 热分析箱体部件材料对应表 ......................................................................................11 表11 FEA数字样机组成说明表 ........................................................................................ 12 表12 振动分析材料对应表 ................................................................................................. 13 表13 各模块主要发热器件试验数据与仿真数据对比 ..................................................... 14 表14 模态对比(无约束状态) ......................................................................................... 15 表15 振动响应对比(实际安装状态) ................................................ 错误!未定义书签。