齿轮加工方案及问题应对方法
常见齿轮加工误差问题分析

常见齿轮加工误差问题分析摘要:齿轮,作为生产制造设备必不可少的基础零件,直接或间接地影响着生产设备的精密度,影响着生产产品的精细度。
为了保障设备与产品的质量得到提升,齿轮自身的精密度与精细度就必须得到提高。
在实际的齿轮生产中,因为机床精度、工装卡具、加工工艺等误差的存在,都会产生齿轮加工误差。
本文就齿轮加工出现的误差问题,做一个简要的分析,并提出一些降低齿轮加工误差的方法。
关键词:齿轮加工;加工;误差引言:当今社会发展迅猛,出现了自控机构、机器人机构、仿生机构、柔性及弹性机构和机电光液广义机构等,而传递与变换运动和力的可动装置中,齿轮是应用最广泛的机械结构。
齿轮传动是机械传动中最重要、应用最为广泛的一种传动机构,大到航天航空装备,小到玩具仪器。
它依靠轮齿齿廓直接接触来传递空间任意两轴间的运动和动力,并具有传递功率范围大、传动效率高、传动比准确、使用寿命长、工作可靠、结构紧凑等优点。
但齿轮传动的制造及安装精度要求高,价格较贵,一般不用于传动距离过大的场合。
对于齿轮的研究采用的方法很多,如弹性力学、动力学、有限元等,但这些方法对齿轮的模型要求高,建模越精确,仿真结果越接近实际,就齿轮啮合而言,实际啮合情况复杂多变,加上加工安装等环节都存在误差,许多数据采集较费时费力,从而使项目周期长,且齿轮的实际啮合情况与理论啮合情况不同,模拟出来的结果不能百分百与实际吻合。
由于齿轮误差的存在,轮齿的某些该接触点无法参与接触,齿轮刚度强度会变差,所以为了更好地研究齿轮,对齿轮误差进行分析是非常有必要的。
1 齿轮传动原理一对齿轮啮合,主动轮通过啮合线接触而将动力、速度、运动等传递给从动轮,两齿轮的传动,严格符合齿廓啮合基本定律即:相互啮合传动的一对齿轮,在任一位置时的传动比,都与其连心线被其啮合齿廓在接触点处的公法线所分成的两线段长成反比。
2 齿轮加工误差产生原因2.1 机床本身精度的误差机床精度的误差包括了几个方面的原因,首先是用来加工齿轮的机床工作台上、下两个的顶尖会有径向跳动的现象产生;其次是两顶尖之间所使用的轴为不相同的工作轴;最后是所使用的加工工作台在分度上有一定的误差。
【齿轮加工的常见问题和解决方法】齿轮怎么加工

【齿轮加工的常见问题和解决方法】齿轮怎么加工齿轮加工的常见问题和解决方法【首席技术支持赖永智;整理校对张艳雷技术指导总工程师张刚、张杰;】【出于对客户的认同及隐私秘密性保密,文中案例所涉及公司名称及油品牌号全部隐去】摘要:齿轮切削工艺分析;配方优缺点分析及相应对策;原材料配比及各自优缺点的分析、关键词:“亿达渤润-线性理论”;齿轮切削油;硫化脂肪酸酯;硫化猪油;硫化烯烃;精制猪油一、市场现状主要就金属加工炼焦煤主要分为切削加工油和塑性加工油(如冲压油、拉伸油、引拔油等),最老其中消耗量最大的是切削油,尤其是齿轮切削相关用油量居多。
目前,国内各大汽车制造厂、发动机配套厂、精密仪表行业大都使用原装进口或外资品牌在国内生产的齿轮切削油,采购成本高,灵活性较差,故而,无论是从市场角度,还是从技术角度来讲,几乎应该攻克齿轮切削油的难关。
二、案例分析在齿轮切削加工之时,多把刀具同时工作,各个民主化的扭矩不同,要求匹配油品必须在加工全阶段都要发挥作用,所以极压抗磨剂的品类越全、比例越高油品的使用效果就越好,刀具磨损快、工件耐磨损暴发差等问题主要发生在加工中后期,此区间是物理润滑向物理润滑过渡的过程,所以要求润滑油中的极压抗磨剂在此区间的释放要快速稳定。
现以我公司在大量的为客户解决的齿轮切削油问题举例说明。
齿轮切削油油样来源:杭州某焦化调和厂,一并提供的还有客户现用的基础油; ---目的是为控管试验测试条件的一致性。
客户工艺及问题以下为方便数据进行定量分析,对以下油样需要进行编号:A:客户原用中其负荷齿轮切削油,配方中主要植物油为:日本硫化猪油**10 + T301 + 美国硫化烯烃**40 + 余量150snB :亿达渤润石化根据客户现有问题改善后的配方为:YD-30155%+T301 10%+YD-1810C 3%+1% 防锈剂+ 精制猪油 5%+余量150sn部分测试结果、截图如下:注:1公斤=9.81N; 在同等实验力的作用下,磨斑越小,其极压抗磨性越好,对工件及设备的侵害越强。
齿轮齿形的加工工艺

铣齿机
用于加工各种类型的齿轮 ,包括直齿、斜齿和人字 齿。
刀具
滚刀
用于切削齿轮的齿槽。
插刀
用于切削直齿和斜齿圆柱齿轮。
铣刀
根据齿轮类型选择不同种类的铣刀。
量具与测量设备
千分尺
用于测量齿轮的尺寸精度和形位公差 。
杠杆表
光学显微镜
用于检测齿轮表面粗糙度和微观缺陷 。
用于测量齿轮的跳动量和齿距偏差。
03 齿轮齿形加工工艺方法
铣齿工艺
总结词
高效加工大型齿轮
详细描述
铣齿工艺是一种通过铣刀在齿轮毛坯上切削,形成齿形的加工方法。它适用于 加工大型齿轮,具有较高的生产效率和加工精度。
插齿工艺
总结词
适合加工直齿圆柱齿轮
详细描述
插齿工艺是利用插齿刀在齿轮毛坯上切削,形成直齿圆柱齿轮齿形的加工方法。 它具有切削速度快、加工精度高的特点,广泛应用于直齿圆柱齿轮的加工。
1.D 磨削工序同样用于提高齿轮的精度和表面光
洁度,而热处理则用于提高齿轮的硬度和抗 疲劳性能。同时,航空齿轮还需要进行一系 列的强度和疲劳试验,以确保其可靠性。
谢谢聆听
切削液的使用与管理
总结词
切削液在齿轮加工中起到冷却、润滑和清洗的作用,对提高加工质量和效率具有重要意 义。
详细描述
切削液的使用和管理需要注意以下几点:首先,要选择合适的切削液品种和浓度,以满 足加工要求;其次,要定期更换切削液,保持切削液的清洁度和浓度;最后,要采用一 些先进的切削液管理技术,如切削液过滤技术、切削液回收利用技术等,提高切削液的
磨削工序同样用于提高 齿轮的精度和表面光洁 度,而热处理则用于提 高齿轮的硬度和抗疲劳 性能。
航空齿轮加工工艺实例
齿轮加工误差产生的原因和消除方法

螺旋线偏差的说明:1、螺旋线偏差的评定范围Lβ除另有规定外,系指在轮齿两端处各减去下面两个数值中较小的一个以后的“齿线长度”,此两个数值为5%的齿宽或等于一个模数的长度。
2、使偏差量增加的偏向齿体外的正偏差,必须计算入误差值。
3、除另有规定外,对于负偏差,其允许值为评定范围Lβ规定的公差的3倍数。
4、螺旋线偏差是在齿轮端面基圆切线方向测量,如果在齿面的法向测量,应将测量值除以cosβb后再与公差值比较。
5、被测齿面的平均螺旋线是设计螺旋线的纵坐标减去一条斜直线的纵坐标后得到的曲线。
这条斜直线使得在评定范围内,实际螺旋线对平均螺旋线偏差的平方和最小。
因此,平均螺旋线的位置和倾斜可以用“最小二乘法”求得。
6、除另有规定外,螺旋线偏差应在沿齿轮圆周均布的不少于三个轮齿的两侧面的齿高中部进行测量。
齿廓(齿形)的说明:1、齿廓偏差在齿轮端平面内且垂直于渐开线齿廓的方向计算,若在齿面的法向测量,应将测量值除以cosβb后再与公差数值进行比较。
2、设计齿廓系指符合设计规定的齿廓,当物其他限定时,是指端面齿廓。
设计齿廓可以设备修正的理论渐开线,包括修缘齿形。
凸齿形等。
3、被测齿面的平均齿廓是设计齿廓线的纵坐标减去一条斜直线的纵坐标后得到的曲线。
这条斜直线使得在齿廓评定范围内,实际齿廓线对平均齿廓线偏差的平方和为最小。
因此,平均齿廓线的位置和倾斜可以用“最小二乘法”求得。
4、齿廓评定范围La系指可用长度L AE中的一部分,除另有规定,其长度等于从E点开始延伸刀有效长度L AE的92%。
对于L AE剩下的8%为靠近齿顶处的L AE与La之差。
在评定齿廓总偏差和齿廓形状偏差时,应遵守下述规则:①、使偏差量增加的偏向齿体外的正偏差,必须计算入误差值。
②、除另有规定外,对于负偏差,其允许值为评定范围La规定的公差的3倍数。
5、有效长度L AE系指可用长度对应于有效齿廓的那部分。
对于齿顶,其有与可用长度同样的限定(A点)。
齿轮加工工艺过程和分析

齿轮的生产过程一.齿轮的主要加工面1.齿轮的主要加工表面有齿面和齿轮基准表面,后者包括带孔齿轮的基准孔、切齿加工时的安装端面,以及用以找正齿坯位置或测量齿厚时用作测量基准的齿顶圆柱面。
2.齿轮的材料和毛坯常用的齿轮材料有15钢、45钢等碳素结构钢;速度高、受力大、精度高的齿轮常用合金结构钢,如20Cr,40Cr,38CrMoAl,20CrMnTiA等。
齿轮的毛坯决定于齿轮的材料、结构形状、尺寸规格、使用条件及生产批量等因素,常用的有棒料、锻造毛坯、铸钢或铸铁毛坯等。
二、直齿圆柱齿轮的主要技术要求,1.齿轮精度和齿侧间隙GBl0095《渐开线圆柱齿轮精度》对齿轮及齿轮副规定了12个精度等级。
其中,1~2级为超精密等级;3—5级为高精度等级;6~8级为中等精度等级;9~12级为低精度等级。
用切齿工艺方法加工、机械中普遍应用的等级为7级。
按照齿轮各项误差的特性及它们对传动性能的主要影响,齿轮的各项公差和极限偏差分为三个公差组(表13—4)。
根据齿轮使用要求不同,各公差组可以选用不同的精度等级。
齿轮副的侧隙是指齿轮副啮合时,两非工作齿面沿法线方向的距离(即法向侧隙),侧隙用以保证齿轮副的正常工作。
加工齿轮时,用齿厚的极限偏差来控制和保证齿轮副侧隙的大小。
2.齿轮基准表面的精度齿轮基准表面的尺寸误差和形状位置误差直接影响齿轮与齿轮副的精度。
因此GBl0095附录中对齿坯公差作了相应规定。
对于精度等级为6~8级的齿轮,带孔齿轮基准孔的尺寸公差和形状公差为IT6-IT7,用作测量基准的齿顶圆直径公差为IT8;基准面的径向和端面圆跳动公差,在11-22μm之间(分度圆直径不大于400mm的中小齿轮)。
3.表面粗糙度齿轮齿面及齿坯基准面的表面粗糙度,对齿轮的寿命、传动中的噪声有一定的影响。
6~8级精度的齿轮,齿面表面粗糙度Ra值一般为0.8—3.2μm,基准孔为0.8—1.6μm,基准轴颈为0.4—1.6μm,基准端面为1.6~3.2μm,齿顶圆柱面为3.2μm。
齿轮加工误差分析及提高加工质量方法
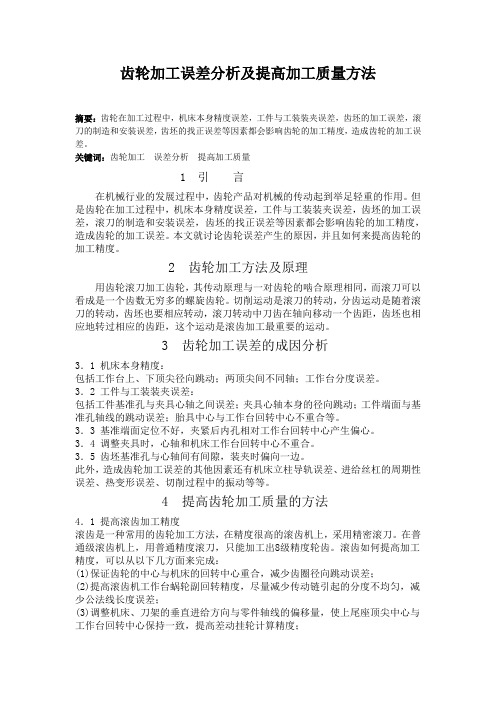
齿轮加工误差分析及提高加工质量方法摘要:齿轮在加工过程中,机床本身精度误差,工件与工装装夹误差,齿坯的加工误差,滚刀的制造和安装误差,齿坯的找正误差等因素都会影响齿轮的加工精度,造成齿轮的加工误差。
关键词:齿轮加工误差分析提高加工质量1 引言在机械行业的发展过程中,齿轮产品对机械的传动起到举足轻重的作用。
但是齿轮在加工过程中,机床本身精度误差,工件与工装装夹误差,齿坯的加工误差,滚刀的制造和安装误差,齿坯的找正误差等因素都会影响齿轮的加工精度,造成齿轮的加工误差。
本文就讨论齿轮误差产生的原因,并且如何来提高齿轮的加工精度。
2 齿轮加工方法及原理用齿轮滚刀加工齿轮,其传动原理与一对齿轮的啮合原理相同,而滚刀可以看成是一个齿数无穷多的螺旋齿轮。
切削运动是滚刀的转动,分齿运动是随着滚刀的转动,齿坯也要相应转动,滚刀转动中刀齿在轴向移动一个齿距,齿坯也相应地转过相应的齿距,这个运动是滚齿加工最重要的运动。
3 齿轮加工误差的成因分析3.1 机床本身精度:包括工作台上、下顶尖径向跳动;两顶尖间不同轴;工作台分度误差。
3.2 工件与工装装夹误差:包括工件基准孔与夹具心轴之间误差;夹具心轴本身的径向跳动;工件端面与基准孔轴线的跳动误差;胎具中心与工作台回转中心不重合等。
3.3 基准端面定位不好,夹紧后内孔相对工作台回转中心产生偏心。
3.4 调整夹具时,心轴和机床工作台回转中心不重合。
3.5 齿坯基准孔与心轴间有间隙,装夹时偏向一边。
此外,造成齿轮加工误差的其他因素还有机床立柱导轨误差、进给丝杠的周期性误差、热变形误差、切削过程中的振动等等。
4 提高齿轮加工质量的方法4.1 提高滚齿加工精度滚齿是一种常用的齿轮加工方法,在精度很高的滚齿机上,采用精密滚刀。
在普通级滚齿机上,用普通精度滚刀,只能加工出8级精度轮齿。
滚齿如何提高加工精度,可以从以下几方面来完成:(1)保证齿轮的中心与机床的回转中心重合,减少齿圈径向跳动误差;(2)提高滚齿机工作台蜗轮副回转精度,尽量减少传动链引起的分度不均匀,减少公法线长度误差;(3)调整机床、刀架的垂直进给方向与零件轴线的偏移量,使上尾座顶尖中心与工作台回转中心保持一致,提高差动挂轮计算精度;(4)滚齿时要控制留磨量,余量不能过大,否则磨齿后齿轮的表面渗碳硬度层会被磨掉,造成硬度下降,降低齿轮的接触疲劳强度。
齿轮加工工艺过程中常见问题及对策探析

齿轮加工工艺过程中常见问题及对策探析【主题:齿轮加工工艺过程中常见问题及对策探析】【引言】在机械制造行业中,齿轮的加工是一个非常重要的环节。
然而,在齿轮加工的过程中,常常会出现一些问题,如尺寸偏差、表面质量不佳以及齿轮传动不稳定等。
这些问题不仅会影响到齿轮的性能和寿命,还会在一定程度上影响到整个机械设备的正常运行。
如何解决这些问题是每一个齿轮加工工艺人员都需要思考和探索的问题。
本文将就齿轮加工工艺过程中常见的问题及对策进行深入分析和探讨。
【正文】1. 尺寸偏差的问题尺寸偏差是齿轮加工中常见的问题之一,它会直接影响到齿轮的配合和传动效果。
尺寸偏差的产生一般是由于加工工艺参数设置不当、加工工艺控制不准确以及设备磨损等原因所致。
为解决这一问题,首先需要优化加工工艺参数的设置,例如合理选择刀具的切削条件、控制切削力的大小以及提高切削液的冷却效果等。
对加工设备进行定期的维护和保养,及时更换磨损的刀具和磨具,也是解决尺寸偏差问题的有效措施。
2. 表面质量不佳的问题在齿轮加工过程中,表面质量不佳是另一个常见的问题。
表面质量不佳会导致齿轮的噪声增加、磨损加剧,甚至影响到齿轮的传动效率。
造成表面质量不佳的原因主要包括切削刀具的磨损、切削速度过高以及加工液的质量不好等。
针对这些问题,首先应定期检查和更换磨损的刀具,保证切削刀具的锋利度和精度。
合理控制切削速度,避免过高的切削速度带来的切削温度过高,从而影响到表面质量。
选择优质的切削液,保证切削液的冷却和润滑效果,也是提高表面质量的关键。
3. 齿轮传动不稳定的问题齿轮的传动不稳定是一种很常见的问题,它表现为齿轮在传动过程中出现噪声、振动甚至传动失效等现象。
齿轮传动不稳定的原因主要包括齿轮参数设计不合理、齿轮加工精度不高以及齿轮配合问题等。
为解决这一问题,首先应优化齿轮的参数设计,确保齿轮的模数、齿宽和齿数等参数满足传动要求。
提高齿轮加工的精度,采用先进的加工设备和工艺,保证齿轮的几何形状和表面质量。
齿轮加工方案及问题应对方法

齿轮加工方案及问题应对方法齿轮是机械传动中常用的零部件,其加工质量直接影响传动系统的效率和稳定性。
本文将探讨齿轮加工过程中的方案选择以及可能出现的问题,并提供相应的问题应对方法,以保证齿轮加工的质量和效率。
一、齿轮加工方案选择在进行齿轮加工前,需要选择适合的加工方案。
根据齿轮的材质、精度要求和批量等因素,可以选择以下几种常见的齿轮加工方案:1. 铣齿加工:铣齿是一种常用的齿轮加工方法,适用于轴齿轮和小模数齿轮的生产。
采用数控铣床进行齿轮加工,可以提高加工效率和加工精度。
2. 齿轮磨削:齿轮磨削是一种高精度的齿轮加工方法,适用于对齿轮要求较高的场合。
磨削可以保证齿轮的精度和表面光洁度,但加工周期相对较长。
3. 齿轮滚削:齿轮滚削是一种高效、高精度的齿轮加工方法。
通过齿轮滚刀与工件的相对滚动,实现齿轮的加工,能够提高齿轮的表面质量和密度。
根据具体的工件要求和设备条件,选择适合的加工方案,可以提高齿轮加工的效率和质量。
二、齿轮加工中可能出现的问题在齿轮加工过程中,可能会出现一些问题,如齿轮加工误差较大、表面质量不理想、加工周期长等。
下面将对可能出现的问题进行分析,并提供相应的解决方法:1. 齿轮加工误差较大:由于加工设备或加工工艺的限制,齿轮加工误差可能会超过规定的范围。
针对这一问题,可以通过提升设备的精度、优化刀具的选择和加工参数的调整来解决。
同时,加强加工过程中的检测和调整,及时发现并修正加工误差,也能有效提高齿轮加工的精度。
2. 表面质量不理想:齿轮的表面质量直接影响其使用寿命和传动效果。
若表面存在瑕疵、粗糙度过大等问题,会导致齿轮传动时产生噪音和振动。
为了解决这一问题,可以合理选择切削液、优化切削参数、加强工件与刀具的冷却等,以提高齿轮的表面质量。
3. 加工周期长:传统齿轮加工方法中,加工周期较长,难以满足大批量生产的需求。
对于这一问题,可以选择更高效的齿轮加工方法,如数控机床加工、自动化生产线等。
- 1、下载文档前请自行甄别文档内容的完整性,平台不提供额外的编辑、内容补充、找答案等附加服务。
- 2、"仅部分预览"的文档,不可在线预览部分如存在完整性等问题,可反馈申请退款(可完整预览的文档不适用该条件!)。
- 3、如文档侵犯您的权益,请联系客服反馈,我们会尽快为您处理(人工客服工作时间:9:00-18:30)。
齿轮加工方案及技术措施齿轮做为常用的机械元件,一向广泛的被运用在机械的传动装置中,小至钟表用齿轮,大至船舶涡轮机用的大型齿轮,都能通过选配齿数组合,获得任意且正确的传动比;它的功率范围大、传动效率高、圆周速度高、传动准确、使用寿命长、结构尺寸小等特点已成为许多机械产品不可缺少的传动部件,也是机器中所占比重最大的传动形式;
现以带有内花键定位的盘状齿轮为例,该齿轮材料为20CrMo Ti,渗碳层1.8-2.2mm,齿面硬度为HRC58-62;
齿轮制造工艺方案,依据不同类型的齿廓形状、齿面硬度结构形式、精度与生产条件来确定;一般来说包括:毛坯准备、齿坯处理、齿坯粗加工、齿轮热处理、齿轮精加工5个阶段,在确定具体加工工艺内容时,着重考虑确定两项精度:
1、是齿轮各部分对中心轴线的形状精度;
2、消除经热处理渗碳淬火后的热变形对齿轮精度的影响;在确定工艺基准时,首先应该选定内花键的大径尺寸为加工工艺基准,这是因为内花键的加工,都是花键拉刀拉制而成的,而拉刀的外径尺寸精度比较高,拉出的花键大径尺寸比较稳定和可靠,完全可以作为齿坯加工的工艺基准,无论是
矩形花键孔或是渐开线花键孔都是一样;实际具体加工工艺为:
●毛坯锻造成形
●热处理正火处理
●粗车1、内孔尺寸一般设计为装配基准,在设定内孔粗车尺寸时一般是按花键拉刀的前导向尺寸确定,比图纸设计尺寸减小0.5-0.6mm,做为热处理后的精磨余量;2、选用拉床定位的端面时应尽量选用大端面,而且要求同内孔一次装夹车成,保证其垂直精度;3、齿坯的其余部分可在粗车加工时留有一定的精车余量;
●拉花键拉内花键用大端面和内孔定位拉制
●精车1、选用内花键的大径尺寸D定位;
2、用车工专用“花键微锥芯轴一次定位加工”在工件调头加工时,可随芯轴一起整体调头加工完成后,再拆卸工件;花键心轴如下图:
车工用微锥花键芯轴,实际上是一个圆柱微锥芯轴,因为在
设计芯轴时,已把花键的键宽和小径尺寸减小了0.5-0.7mm
渐开线花键的齿厚减小0.5使花键芯轴完全靠外径和微锥来定位锁紧齿坯的,这样主要是为了排除多点接触对精度的干涉
●滚齿滚齿的定位仍使用花键大径和大端面为工艺基准齿厚为粗切加工,磨削余量可按下表选择磨削余量:
●倒角齿廓倒角,一般是指齿高的两端和沿齿长的齿顶2×4 5O倒钝;
●热处理按热处理工艺渗碳淬火;
●磨削1、由于齿轮在渗碳淬火的热处理过程中会产生热变形,变形量大小不一,变形位置一般在孔的收缩或涨大和盘
状的翘曲变形;2、为了消除热变形,对齿轮各部加工的影响可按下列方法消除:a、仍以内花键大径为定位基准,上花
键芯轴,对齿轮的外径和大端面一次装夹后,磨光,磨去的,
便是变形量因为这是微量磨削,一般是不会造成尺寸变化的,
这样可以在工艺上保证两个精度,即齿节圆对内花键的同轴度和齿端面对内花键的垂直度;b、在内圆磨床上,将齿轮的大外圆和大端面的跳动同时校正在0.03mm以内,把花键内孔磨成;c、在以内孔和大端面定位磨齿面为成品尺寸;以上三步的做法主要为了保证齿轮各部位对内花键的形位精度,避免由于热处理变形而造成的内花键大径和小径的偏心,而影响装配;
二、滚齿误差产生原因消除方法
在齿轮整个工艺规程中,滚齿是经常产生误差的环节,滚齿经常产生的问题及原因主要有:
齿圈径向圆跳动超差;由于齿坯几何偏心和安装偏心;用顶尖装夹定位时,顶尖与机床中心偏心;通过提高齿坯基准面精度,提高夹具定位面精度,提高调整水平,更换或重新装调顶尖等方式解决;
公法线长度变动超差;由于机床分度蜗杆副制造及安装误差造成运动偏心;机床工作台定心锥形导轨副间隙过大,造成工作台运动中心线不稳定;滚刀主轴系统轴向圆跳动过大或平面轴承咬坏;通过提高分度蜗杆副的制造精度和安装精度,提高工作台锥形导轨副的配合精度,提高滚刀主轴系统轴向精度,更换咬坏的平面轴等方法解决;
齿距偏差超差;滚刀的轴向和径向圆跳动过大;分度蜗杆和分度蜗轮齿距误差;齿坯安装偏心;通过提高滚刀的安装精度,修复或更换分度蜗杆副,消除齿坯安装误差等方法解决;齿顶部变肥,左右齿廓对称;滚刀铲磨时齿形角度小或刃磨产生较大的正前角,使齿形角变小;通过更换滚刀或重磨齿形角及前刃面方法解决;
齿顶部变瘦,左右齿廓对称;滚刀铲磨时齿形角变大或刃磨时产生较大的负前角,使齿形角变大;通过更换滚刀或重磨齿形角及前刀面方法解决;
齿形不对称;滚刀安装对中不好,刀架回转角误差大,滚刀前刀面有导程误差;通过保证滚刀安装精度,提高滚刀刃磨精度,控制前刀面导程误差,微调滚刀回转角方法解决;
齿面出棱;滚刀制造或刃磨时容屑槽等分误差;通过重磨滚刀达到等分要求方法解决;
齿形周期性误差;滚刀安装后,径向或端圆跳动大,机床工作台回转不均匀,分齿交换齿轮安装偏心或齿面有磕碰,刀架滑板松动,齿坯装夹不合理,产生振动;通过控制滚刀的安装精度,检查、调整分度蜗杆副传动精度,重新调整分齿交换齿轮、滑板和齿坯方法解决;
齿向误差超差;垂直进给导轨与工作台轴线平行度误差或歪斜,、下顶针不同轴,下顶针轴线与工作台回转轴线同轴度差;夹具和齿坯的制造、安装、调整精度低;分齿、差动
交换齿轮误差大;齿坯或夹具刚性差,夹紧后变形;通过提
高夹具、齿坯的制造和调整精度,重新计算分齿及差动交换齿轮,修正误差,改进齿还或夹具设计,正确夹紧方法解决;
撕裂;齿坯材质不均匀;齿坯热处理方法不当;滚刀用钝,
不锋利;切削用量选择不当,冷却不良;通过控制齿坯材料
质量,采用正火处理45钢、40cr钢、18CrMnTi,滚刀移位或更换新刀,正确选用切削用量,选用润滑性能良好的切削液,充分冷却方法解决;
啃齿;刀架立柱导轨太松或太紧;油压不稳定;刀架斜轮啮合间隙大;通过调整立柱导轨塞铁松紧,保持油路畅通,油压稳定,刀架斜齿轮若磨损,应更换;
振纹;机床内部某传动环节的间隙过大;工件与刀具的装夹刚性不够;切削用量选用过大;后托架安装后,间隙大;
通过修理或调整机床,提高刀装夹刚性,缩小支承间距离,加大轴径,提高工件刚性,尽量加大支承面,正确选用切削用量,正确安装后托架方法解决;。