钢板火焰切割面质量要求
火焰切割通用检验规范
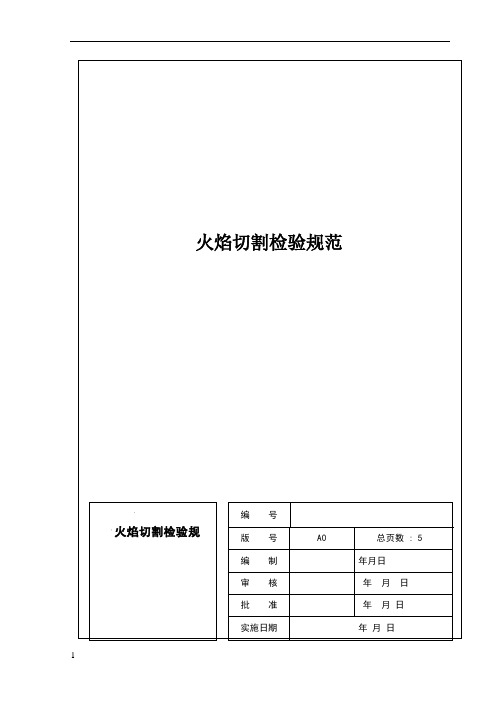
1 目的为规范检验人员对火焰切割零部件的检验,让检验人员在数控火焰切割、半自动切割过程及切割件成品的检验活动有章可依。
同时提升下料件的切割实物割口成型质量,降低切割缺陷的形成几率,提高焊接、装配及整机外观质量。
2 适用范围适用于公司内数控火焰切割、半自动切割过程的检验及切割成品件的检验等。
3 检验及标识工具卡尺、钢尺、卷尺、石笔、记号笔等。
4 外观表面等级定义:产品表面等级根据重要程度,划分为I类面、II类面、III类面,具体定义如下:表面等级定义产品表面等级定义I类面掘进机组装后,表面裸露在人的视线范围内,人体不需要下蹲或站在机组上面能观察到,直接影响掘进机外观的表面。
II类面人体需要下蹲或站在机组上面能观察到的部位。
III类面机组拆解后,在部件上可以观察到的部位。
机器的I类面、II类面、III类面的区分如图 1 所示:图15 热切割质量控制切割过程中,应随时注意观察影响切割质量的因素,保证切割的连续性。
工艺参数对气割的质量影响很大,常见的气割断面缺陷与工艺参数的关系如下所示:气割表面缺陷和原因分析缺陷类型产生原因图示说明切割面粗糙a、切割氧压力过高b、割嘴选用不当c、切割速度太快d、预热火焰能量过大切割面缺口a、切割过程中断,重新起割衔接不好b、钢板表面有厚的氧化皮、铁锈等c、切割机行走不平稳切割面内凹a、切割氧压力过高b、切割速度过快切割面倾斜a、割炬与板面不垂直b、风线歪斜c、切割氧压力低或嘴号偏小切割面上缘呈珠链状a、钢板表面有氧化皮、铁锈b、割嘴到钢板的距离太小,火焰太强切割面上缘熔化a、预热火焰太强b、切割速度太慢c、割嘴离板件太近切割面下缘粘渣A、切割速度太快或太慢b、割嘴号太小c、切割氧压力太低6 切割成品件可接受的范围序号项目分类Ⅰ类面Ⅱ类面Ⅲ类面1δ≤30mm任意100mm长度表面粗糙度<25切角≤3度表面粗糙度≤50切角≤5度表面粗糙度≤50切角≤5度230mm<δ<50mm任意100mm长度表面粗糙度<25切角≤3度表面粗糙度≤50切角≤5度表面粗糙度≤50切角≤5度350mm≤δ≤100mm任意100mm长度表面粗糙度<25切角≤3度表面粗糙度≤50切角≤5度表面粗糙度≤50切角≤5度4δ>100mm任意100mm长度表面粗糙度≤50切角≤3度表面粗糙度≤50切角≤5度表面粗糙度≤50切角≤8度切割边缘的缺陷分级(钢板表面与切割面形成的边线,交汇处平滑过度):边缘的缺陷分级分级评定标准A级深(高)度0.5mm 长度1mm以内凹凸点B级深(高)度~1mm 长度1~2mm以内凹凸点C级深(高)度2mm 长度2mm以上凹凸点切割边缘边线质量允许偏差量:边线的质量允许偏差7 切割过程中的检验检验人员要严格执行“三检制”,监督操作人员执行工艺的正确性,重点要求在巡检过程中,能发现不足及时纠正。
火焰切割相关资料

原因: ① 割嘴与工件之间的高度太大,切割氧压力太高; ② 预热火焰太强。 2.切割断面凹凸不平,即平面度差 (1)切割断面上边缘下方,有凹形缺陷(见图 9-12)现象:在接受切割断面上边缘处有 凹陷,同时上边缘有不同程度的熔化塌边。 原因: ① 切割氧压力太高; ② 割嘴与工件之间的高度太大;割嘴有杂物堵塞,使风线受到干扰变形。 (2)割缝从上向下收缩(见图 9-13)
正常火焰的特征是在其还原区没有自由氧和活性碳,有三个明显的区域,焰芯 有鲜明的轮廓(接近于圆柱形)。焰芯的成分是乙炔和氧气,其末端呈均匀的 圆形和光亮的外壳。外壳由赤热的碳质点组成。焰芯的温度达 1000℃。还原区
处于焰芯之外,与焰芯的明显区别是它的亮度较暗。还原区由乙炔未完全燃烧 的产物——氧化碳和氢组成,还原区的温度可达 3000℃左右。外焰即完全燃烧 区,位于还原区之外,它由二氧化碳和水蒸气、氮气组成,其温度在 1200~250 0℃之间变化。 氧化焰是在氧气过剩的情况下产生的,其焰芯呈圆锥形,长度明显地缩短,轮 廓也不清楚,亮度是暗淡的;同样,还原区和外焰也缩短了,火焰呈紫蓝色, 燃烧时伴有响声,响声大小与氧气的压力有关,氧化焰的温度高于正常焰。如 果使用氧化焰进行切割,将会使切割质量明显地恶化。 还原焰是在乙炔过剩的情况下产生的,其焰芯没有明显的轮廓,其焰芯的末端 有绿色的边缘,按照这绿色的边缘来判断有过剩的乙炔;还原区异常的明亮, 几乎和焰芯混为一体;外焰呈黄色。当乙炔过剩太多时,开始冒黑烟,这是因 为在火焰中乙炔燃烧缺乏必须的氧气造成的。 预热火焰的能量大小与切割速度、切口质量关系相当密切。随着被切工件板厚 的增大和切割速度的加快,火焰的能量也应随之增强,但又不能太强,尤其在 割厚板时,金属燃烧产生的反应热增大,加强了对切割点前沿的预热能力,这 时,过强的预热火焰将使切口上边缘严重熔化塌边。太弱的预热火焰,又会使 钢板得不到足够的能量,逼使减低切割速度,甚至造成切割过程中断。所以说 预热火焰的强弱与切割速度的关系是相互制约的。 一般来说,切割 200mm 以下的钢板使用中性焰可以获得较好的切割质量。在切 割大厚度钢板时应使用还原焰预热切割,因为还原焰的火焰比较长,火焰的长 度应至少是板厚的 1.2 倍以上。 2.切割速度 钢板的切割速度是与钢材在氧气中的燃烧速度相对应的。在实际生产中,应根 据所用割嘴的性能参数、气体种类及纯度、钢板材质及厚度来调整切割速度。 切割速度直接影响到切割过程的稳定性和切割断面质量。如果想人为地调高切 割速度来提高生产效率和用减慢切割速度来最佳地改善切割断面质量,那是办 不到的,只能使切割断面质量变差。过快的切割速度会使切割断面出现凹陷和 挂渣等质量缺陷,严重的有可能造成切割中断;过慢的切割速度会使切口上边 缘熔化塌边、下边缘产生圆角、切割断面下半部分出现水冲状的深沟凹坑等等。 通过观察熔渣从切口喷出的特点,可调整到合适的切割速度。 在正常的火焰切割过程中,切割氧流相对垂直的割炬来说稍微偏后一个角度, 其对应的偏移叫后拖量(见图 9-3)。速度过低时,没有后拖量,工件下面割 口处的火花束向切割方向偏移。如提高割炬的运行速度,火花束就会向相反的 方向偏移,当火花束与切割氧流平行时,就认为该切割速度正常。速度过高时, 火花束明显后偏,见图 9-4。
火焰切割工艺

数控火焰切割工艺气割精度是指被切割完的工作几何尺寸与其图纸尺寸对比的误差关系,切割质量是指工件切割断面的表面粗糙度、切口上边缘的熔化塌边程度、切口下边缘是否有挂渣和割缝宽度的均匀性等。
一、气割前的准备工作被切割金属的表面,应仔细地清除铁锈、尘垢或油污。
被切割件应垫平,以便于散放热量和排除熔渣。
决不能放在水泥地上切割,因为水泥地面遇高温后会崩裂。
切割前的具体要求如下。
①检查工作场地是否符合安全要求,割炬、氧气瓶、乙炔瓶(或乙炔发生器及回火防止器)、橡胶管、压力表等是否正常,将气割设备按操作规程连接好。
②切割前,首先将工件垫平,工件下面留出一定的间隙,以利于氧化铁渣的吹除。
切割时,为了防止操作者被飞溅的氧化铁渣烧伤,必要时可加挡板遮挡。
③将氧气调节到所需的压力。
对于射吸式割炬,应检查割炬是否有射吸能力。
检查的方法是:首先拔下乙炔进气软管并弯折起来,再打开乙炔阀门和预热氧阀门。
这时,将手指放在割炬的乙炔过气管接头上,如果手指感到有抽力并能吸附在乙炔进气管接头上,说明割炬有射吸能力,可以使用;反之,说明割炬不正常,不能使用,应检查修理。
④检查风线,方法是点燃火焰并将预热火焰调整适当。
然后打开切割氧气阀门,观察切割氧流(即风线)的形状,风线应为笔直、清晰的圆柱体并有适当的长度。
这样才能使工件切口表面光滑干净,宽窄一致。
如果风线不规则,应关闭所有的阀门,用通针或其他工具修整割嘴的内表面,使之光滑。
预热火焰的功率应根据板材厚度不同加以调整,火焰性质应采用中性焰。
二、钢板表面预处理钢板从钢铁厂经过一系列的中间环节到达切割车间,在这段时间里,钢板表面难免产生一层氧化皮。
再者,钢板在轧制过程中也产生一层氧化皮附着在钢板表面。
这些氧化皮熔点高,不容易燃烧和熔化,增加了预热时间,降低了切割速度;同时经过加热,氧化皮四处飞溅,极易对割嘴造成堵塞,降低了割嘴的使用寿命。
所以,在切割前,很有必要对钢板表面进行除锈预处理。
常用的方法是抛丸除锈,之后喷漆防锈。
火焰切割技术参数

火焰切割技术参数1.气源选择和压力要求:火焰切割所使用的气源主要是氧气和燃料气(如乙炔、丙烷等)。
氧气用于与燃料气进行燃烧,产生高温火焰。
在使用火焰切割技术时,氧气压力一般为0.5-1.0MPa,燃料气压力根据具体需求来确定。
2.火焰温度:火焰切割是利用火焰的高温来熔化金属进行切割的,因此火焰温度是一个重要的参数。
一般来说,火焰温度可以达到3000℃以上,足以将大部分金属材料进行熔化切割。
3.切割速度:切割速度是指单位时间内切割的长度。
切割速度一般根据材料的厚度和切割质量要求来确定。
一般来说,切割速度较快可以提高生产效率,但对于切割质量要求较高的工件,需要适当降低切割速度以确保切割质量。
4.切割质量和精度:切割质量和精度是衡量火焰切割技术优劣的重要指标。
切割质量主要包括切割面光洁度、垂直度、切口宽度和切口变形等。
切割精度主要包括切割尺寸的偏差和平行度的控制。
要获得较高的切割质量和精度,需要合理调整切割参数和选用合适的切割设备。
5. 切割厚度:火焰切割技术适用于切割较厚的金属板材。
一般来说,在氧燃气切割下,钢板的切割厚度可以达到150mm以上,铸铁等材料的切割厚度也可以达到一定程度。
6.能耗和环境影响:火焰切割技术的能耗主要涉及到氧气和燃料气的消耗。
同时,火焰切割过程中会产生大量的热量和废气,对环境造成一定的影响。
因此,在使用火焰切割技术时,需要注意节约能源和减少环境污染。
总之,火焰切割技术作为一种常用的金属切割方法,具有一系列的技术参数。
使用者需要根据实际需要和工件材料的要求来选择合适的切割参数,以保证切割质量和效率的最佳匹配。
同时,还需要注意安全操作,避免发生事故。
厚度大于50mm的厚钢板一般采用火焰切割
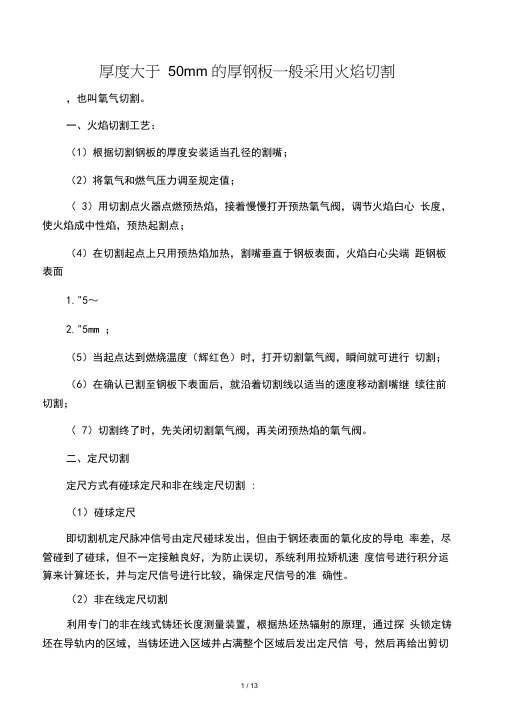
厚度大于50mm 的厚钢板一般采用火焰切割,也叫氧气切割。
一、火焰切割工艺:(1)根据切割钢板的厚度安装适当孔径的割嘴;(2)将氧气和燃气压力调至规定值;(3)用切割点火器点燃预热焰,接着慢慢打开预热氧气阀,调节火焰白心长度,使火焰成中性焰,预热起割点;(4)在切割起点上只用预热焰加热,割嘴垂直于钢板表面,火焰白心尖端距钢板表面1."5~2."5mm ;(5)当起点达到燃烧温度(辉红色)时,打开切割氧气阀,瞬间就可进行切割;(6)在确认已割至钢板下表面后,就沿着切割线以适当的速度移动割嘴继续往前切割;(7)切割终了时,先关闭切割氧气阀,再关闭预热焰的氧气阀。
二、定尺切割定尺方式有碰球定尺和非在线定尺切割:(1)碰球定尺即切割机定尺脉冲信号由定尺碰球发出,但由于钢坯表面的氧化皮的导电率差,尽管碰到了碰球,但不一定接触良好,为防止误切,系统利用拉矫机速度信号进行积分运算来计算坯长,并与定尺信号进行比较,确保定尺信号的准确性。
(2)非在线定尺切割利用专门的非在线式铸坯长度测量装置,根据热坯热辐射的原理,通过探头锁定铸坯在导轨内的区域,当铸坯进入区域并占满整个区域后发出定尺信号,然后再给出剪切命令。
三、氧气切割的基本原理:氧气切割是利用气体火焰的热能将工件切割处预热到燃点后,喷出高速切割氧流,使金属燃烧并放出热量而实现切割的方法。
四、氧气切割过程:⑴预热气割开始时,利用气体火焰(氧乙炔焰或氧丙烷焰)将工件待切割处预热到该种金属材料的燃烧温度——燃点(对于碳钢约为1100~1150℃)。
⑵燃烧喷出高速切割氧流,使已达燃点的金属在氧流中激烈燃烧,生成氧化物。
⑶吹渣金属燃烧生成的氧化物被氧流吹掉,形成切口,使金属分离,完成切割过程。
五、氧气切割的三条件:金属材料要进行氧气切割应满足以下三个条件:1)金属燃烧生成氧化物的熔点应低于金属熔点,且流动性要好。
2)金属的燃点应比熔点低。
3)金属在氧流中燃烧时能放出大量的热量,且金属本身的导热性要低。
火焰切割指导书
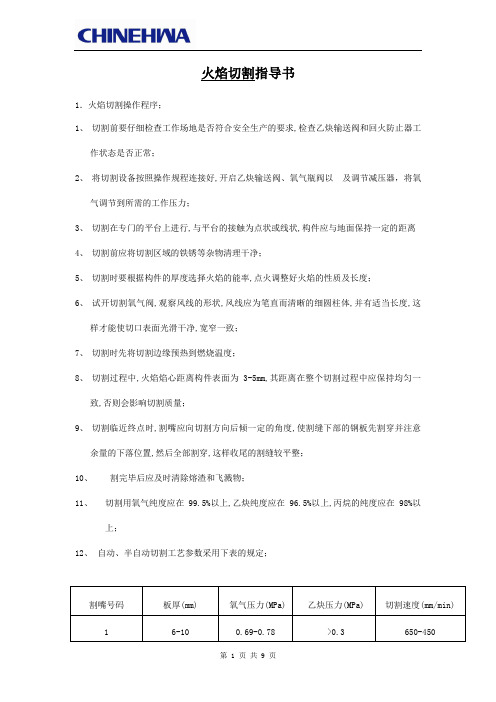
火焰切割指导书1.火焰切割操作程序;1、切割前要仔细检查工作场地是否符合安全生产的要求,检查乙炔输送阀和回火防止器工作状态是否正常;2、将切割设备按照操作规程连接好,开启乙炔输送阀、氧气瓶阀以及调节减压器,将氧气调节到所需的工作压力;3、切割在专门的平台上进行,与平台的接触为点状或线状,构件应与地面保持一定的距离4、切割前应将切割区域的铁锈等杂物清理干净;5、切割时要根据构件的厚度选择火焰的能率,点火调整好火焰的性质及长度;6、试开切割氧气阀,观察风线的形状,风线应为笔直而清晰的细圆柱体,并有适当长度,这样才能使切口表面光滑干净,宽窄一致;7、切割时先将切割边缘预热到燃烧温度;8、切割过程中,火焰焰心距离构件表面为3-5mm,其距离在整个切割过程中应保持均匀一致,否则会影响切割质量;9、切割临近终点时,割嘴应向切割方向后倾一定的角度,使割缝下部的钢板先割穿并注意余量的下落位置,然后全部割穿,这样收尾的割缝较平整;10、割完毕后应及时清除熔渣和飞溅物;11、切割用氧气纯度应在99.5%以上,乙炔纯度应在96.5%以上,丙烷的纯度应在98%以上;12、自动、半自动切割工艺参数采用下表的规定;13、型钢的切割采用锯床或三向自动切割机进行切割;14、承受动力荷载的腹板与翼缘板连接坡口必须用刨边机刨削,其它所有坡口可采用气体切割;15、高屈服强度钢及Q345钢若采用自动切割,根据板厚,切割前预热;16、切割的允许偏差应符合下表的规定;切割的允许偏差(mm)注: t为切割面厚度.17、上边缘熔化程度指切割过程中烧塌状况,表明是否产生塌角及开成间断或连续性的熔滴及熔化条状物;18、零件的切割线与号料线的允许偏差,应符合下列规定:手工切割:: ±1.5mm自动半自动切割: ±1.0mm精密切割: ±0.5mm2一般事项1)2)3)气体切割原则上使用自动切割和定规切割。
切割精度不合标准的,应用砂轮机磨平,必要时焊后再打磨平整。
气割质量要求及缺陷产生和防止措施

气割质量要求及缺陷产生和防止措施(一)气割切口的质量要求气割切口表面应光滑干净,而且粗细纹路要一致,气割的氧化铁渣容易脱落;气割切口缝隙较窄,而且宽窄一致;气割切口的钢板边缘棱角没有熔化等。
具体质量评定标准参见JB3092-82《火焰切割面质量技术要求》。
JB3092-82《火焰切割面质量技术要求》对自动、半自动及手工火焰切割厚度在5~150mm的低碳钢、中碳钢及普通低合金钢的轧制钢材,其切割面质量共分七项评定内容,每项评定内容中,又各分成四个等级,即0级、1级、2级、3级。
(1)切口质量的评定内容及等级划分①表面粗糙度表面粗糙度是指切割面波纹峰与谷之间的距离(了取任意五点的平均值)。
用G表示,切割面波纹高度的分级,详见表4-16的规定。
表4-16 表面粗糙度等级波纹高度(G值)图例≤401≤802≤1603≤320②平面度平面度是指沿切割方向垂直于切割面上的凸凹程度。
按被切割钢板厚度δ的百分比计算,用B表示,其平面度公差详见表417的规定。
表4-17 平面度的公差等级平面度(B值)图例δ<20δ=20~150≤1%δ≤0.5%δ1≤2%δ≤1%δ2≤3%δ≤1.5%δ3≤4%δ≤2.5%δ③上缘熔化程度上缘熔化程度是指气割过程中烧塌情况,表现为是否产生塌角及形成间断或连续性的熔滴及熔化条状物,用S表示。
其等级和熔化程度详见表4-18的规定。
表4-18 上缘熔化程度等级熔化程度(S)及状态说明123基本清角塌边宽度≤0.5上缘有圆角塌边宽≤1上缘有明显圆角塌方宽度≤1.5,边缘有熔融金属上缘有圆角,塌边宽度≤2.5,有连续熔融金属④挂渣挂渣是指切断面的下缘附着铁的氧化物,按其附着多少和剥离难易程度来区分等级,用Z表示,其各等级的状态按表4-19的规定。
表4-19 挂渣状态等级挂渣状态(Z)等级挂渣状态(Z)1挂渣很少,可自动剥离有挂渣,容易清除23有条状挂渣,用铲可清除难清除,留有残迹⑤缺陷的极限间距缺陷的极限间距是指沿切线方向的切割面上,由于振动和间断等原因,出现沟痕,使表面粗糙度突然下降,其沟痕深度为0.32~1.2mm,沟痕宽度不超过5mm者称为缺陷。
切割标准

切割下料标准1.范围:本标准适用于原材料切割下料的加工过程。
适用于以火焰切割及等离子切割作为切割方式的切割下料过程。
2.施工准备:2.1材料要求:2.1.1用于切割下料的钢板应经质量部门检查验收合格,其各项指标满足国家规范的相应规定。
2.1.2钢板在下料前应检查钢板的牌号、厚度和表面质量,如钢材的表面出现蚀点深度超过国标钢板负偏差的部位不准用于产品。
小面积的点蚀在不减薄设计厚度的情况下,可以采用焊补打磨直至合格。
2.1.3在下料时必须核对钢板的牌号、规格和表面质量情况,在确认无疑后才可下料。
2.2施工设备及工具:2.2.1切割下料设备主要包括数控火焰切割机、数控等离子切割机、直条切割机、半自动切割机等。
2.2.2在气割前,先检查整个气割系统的设备和工具全部运转正常,并确保安全的条件下才能运行,而且在气割过程中应注意保持。
2.2.3检测及标识工具分别为:钢尺、卷尺、石笔、记号笔等。
3.切割操作工艺:3.1在进行自动切割时,吊钢板至气割平台上,应调整钢板单边两端头与导轨的距离差在5mm范围内。
在进行半自动切割时,应将导轨放在被切割钢板的平面上,然后将切割机轻放在导轨上。
使有割炬的一侧面向操纵者,根据钢板的厚度选用割嘴,调整切割直度和切割速度。
3.2根据自动切割及半自动切割方式的不同,调整各把割枪的距离,确定后拖量,并考虑割缝补偿;在切割过程中,割枪倾角的大小和方向主要以钢板厚度而定,割嘴倾角与割件厚度的关系及切割余量如下表所示:割嘴倾角与割件厚度的关系钢板切割余量表在进行厚板气割时,割嘴与工件表面保持垂直,待整个断面割穿后移动割嘴,转入正常气割,气割将要到达终点时应略放慢速度,使切口下部完全割断。
3.3根据板厚调整切割参数,切割参数包括割嘴型号、氧气压力、切割速度和预热火焰的能量等,工艺参数的选择主要根据气割机械的类型和可切割的钢板厚度,对未割过的钢板,应试割同类钢板,确定切割参数,同时检查割咀气通畅性。
- 1、下载文档前请自行甄别文档内容的完整性,平台不提供额外的编辑、内容补充、找答案等附加服务。
- 2、"仅部分预览"的文档,不可在线预览部分如存在完整性等问题,可反馈申请退款(可完整预览的文档不适用该条件!)。
- 3、如文档侵犯您的权益,请联系客服反馈,我们会尽快为您处理(人工客服工作时间:9:00-18:30)。
.专业资料分享.
SW ********设备制造有限公司企业标准
Q/SW.J04.01-04 ——————————————————
钢板火焰切割面质量要求
(试行)
2004年8月29日发布 2004年8月31日实施——————————————————————————————*******机电设备制造有限公司批准
钢板火焰切割面质量要求(试行)
1.主要内容与适用范围
本标准规定了钢板、型材火焰切割面质量要求和精度等级以及切割表面加工余量标准。
本标准主要适用于机械自动、半自动火焰切割,板厚4.5~200mm范围。
2.引用标准:
JB/T 10045.3-1999 热切割气割质量和尺寸偏差
S/ZZM0004.2-86 氧割下料质量技术要求
Q/MTZ1015-85 金属焊接结构件通用技术条件
MT/T587-1996 液压支架结构件制造技术条件
3.氧割手工划线宽度不大于0.5mm,交角处圆角半径等于1.0mm。
4.切割表面的质量
4.1.切割表面垂直度(平面度)的偏差(C):指实际切割断面与被切割金属表面的垂线之间的最大偏差,或是沿切割方向垂直于切割面上的凹凸程度。
按表4-1的规定
表4-1 mm
注:对不重要的切割表面,其垂直度应放宽取Ⅳ级精度c≤%4δ。
本公司选用Ⅱ级。
手工切割按Ⅲ级标准要求执行。
4.2.切割表面的粗糙度:指切割表面波纹峰与谷之间的距离。
(取任意5点的平均值,用G表示)。
按表4-2的规定:本公司选用Ⅱ-Ⅲ级
表4-2 mm
注:对不重要的切割表面粗糙度可从宽,作为Ⅳ级对待G<0.35mm。
4.3.切割表面的直线度:是指切割直线时,沿切割方向将起止两端连成的直线同实际切割面之间的间隙。
其公差由板厚δ和长度L决定(用P表示)应符合表4-3的规定。
表4-3 mm
4.4.切割面角度偏差,倒角(坡口)偏差,应符合表4-4的规定。
表4-4 mm
注:1) 表中Ⅰ、Ⅱ级适用于机械切割,Ⅲ级适用于手工切割,
4.5.切割表面上缘熔化程度(S):指切割产生塌角及形成间断或连续性熔滴及熔化条状物的程度。
其等级应符合表4-5的规定。
本公司选用Ⅱ级。
表4-5
4.6.挂渣Z:指切割面的下缘附着铁的氧化物。
其等级按附着多少和剥离难易程度
表区分,应符合表4-6的规定。
本公司选用Ⅱ-Ⅲ级。
表4-6
5.氧割型钢的下料长度偏差按表5-1的规定。
其端面垂直度在公差内。
表5-1 mm
6.板材氧割下料时,如图样或工艺文件上没有要求时,零件尺寸的允许偏差。
应符合表6-1的规定。
表6-1 mm
注:尺寸允差对孔、槽及不通孔深度取“+”值,轴、厚度、长度取“-”值。
7.氧割下料需机械加工的表面,其加工余量见表7-1
表7-1 mm
注:余量的测量是以板件平面为基准面,垂直测量零件的最小边尺寸应增加的数值。
8.说明:
8-1.刀检量:对于板厚小于或等于50mm的零件,可根据零件长度的大小、板厚,在2-4mm范围内选择。
8-2.设计图纸及工艺文件,对氧割件质量标准有规定者,按规定执行,没有要求者,按本标准执行。
附加说明:1.本标准由技术部工艺室提出。
2.本标准起草人:
888888
3.审核:
88888
8。