焊接板件铣边机设计论文
焊接设备的优化设计论文

焊接设备的优化设计
汇报人:
目录
01 02 03 04 05 06
添加目录项标题 引言
焊接设备的现状 焊接设备的优化设计 焊接设备优化设计的实践应用 焊接设备优化设计的未来展望
01
添加目录项标题
02
引言
焊接设备的重要性
焊接设备在制造业中的地位 焊接设备对产品质量的影响 焊接设备对生产效率的影响 焊接设备对环境的影响
07
结论
研究成果总结
焊接设备优化设计可以降低 能耗
焊接设备优化设计可以提高 生产效率
焊接设备优化设计可以提高 焊接质量
焊接设备优化设计可以改善 工作环境
对未来研究的建议
进一步研究焊接设备的材பைடு நூலகம்选择
提高焊接设备的自动化程度
添加标题
添加标题
优化焊接设备的结构设计
添加标题
添加标题
加强焊接设备的维护和保养
优化设计的必要性
提高生产效率:减少生产时间,提高生产效率 降低成本:减少材料浪费和能源消耗 提高产品质量:减少焊接缺陷和变形 增强市场竞争力:提高产品性能和质量,增强市场竞争力
03
焊接设备的现状
现有焊接设备的种类和特点
焊接设备的种 类:手工电弧 焊、氩弧焊、 二氧化碳气体
保护焊等
焊接设备的特 点:操作简单、 成本低、适用
05
焊接设备优化设计的实践应用
应用场景介绍
汽车制造领域 航空航天领域 造船工业领域 建筑行业领域
实践应用效果评估
焊接设备优化设计的应用领域 实践应用的具体案例 实践应用的效果评估指标 实践应用效果的定量评估
06
焊接设备优化设计的未来展望
工装设计毕业论文终稿 V560铣头铣削加工工艺分析及工装设计

毕业论文(设计)课题名称:V560铣头铣削加工工艺分析及工装设计摘要本论文主要对V560数控机床铣头铣削加工工艺进行分析,通过对选取的两种工艺方案进行分析比较,选取出适合精度与效率要求的工艺。
方案一根据先面后孔、先主要加工表面后次要加工表面和先粗加工后精加工的原则,将电机孔面、导轨面的粗加工放在前面,精加工放在后面,螺纹等次要加工放在最后加工。
这个方案把重要的面放在了前面,把不重要的面放在后面,这样很容易使加工好的面碰损,这将会给实际加工操作中带来严重的影响。
因此方案二对方案一中的工艺路线需要进行部分调整修处理,并阐述方案一中的不足,进行分析从而选取正确的加工工艺程序。
同时由于没有固定的铣床夹具,因而进行了专业的夹具工装设计,以确保产品质量和提高生产率。
关键词:铣头;铣削加工;加工工艺;工装设计ABSTRACTFixture machine is widely used in machinery manufacturing. Fixture fora large number of machine tools used for a large number of mass productionto provide the necessary conditions. Machine Tool tcchnology system is composed of a link, the impact of processing quality is an important factor.The date stick to first surface then aperture 、first primary process the surface then secondary process the surface .Taking the rough machining to the first then taking the finish machining to the second and taking the thread to the last.The adoption of the above scheme due to the common principle ,but a lot of process has some problems .The maximal deficiency of the scheme is take the most important surface to the first and take the minor surface to the last . It may easy clashed the finished surface and have an effect on the practice process operate .In this way ,it can gain a lot of time and raise the productivity .KEYWORDS:Milling head,Mill,Machining technics,Betriebsmittel-Planung目录摘要 (I)ABSTRACT (II)1绪论 (1)2 V560数控铣床铣头零件图纸分析 (2)2.1零件的分析 (2)2.2确定毛坯,画毛坯-零件图 (6)3V560铣床铣头铣加工工艺分析 (8)3.1定位基准的选择 (8)3.2制定工艺路线 (9)3.3选择加工设备及刀、夹、量具 (13)3.4加工工序设计 (14)4夹具的设计 (17)4.1工序220的精铣电机孔面夹具 (17)5结论 (19)谢辞 (20)参考文献 (21)1 绪论机械制造业是制造业的核心,是制造机械产品(如农业机械,动力机械,运输机械,矿山机械等)的工业部门,也是为国民经济各部门提供装备的部门。
铣边机坡口加工定位工装论文

铣边机坡口加工定位工装论文摘要:在铣边机加工中运用该设计加工方案大大提高了产品的加工质量,产品一次加工合格率达98.2%,比以前提高5%,加工废品为零。
与此同时,还降低了筒体钢板的装卡难度,减轻了加工者的劳动强度,提高了筒体坡口生产效率和加工精度,为今后的容器筒体加工提供有力保障。
关键词:铣边机;焊接坡口;加工技术;设计2013年我公司主要承担260台3 m3六容器、35台3 m3(C)容器、120台2.5 m3容器的加工制造。
目前,公司使用新引进的国产铣边机(见图一)进行容器筒体焊接坡口加工,经过我们相关专业人员长期不懈地努力和研究,总结出一套利用铣边机进行筒体焊接坡口加工的实施方案,有效提高了筒体焊接坡口加工质量和效率。
压力容器主要有一个筒体、两个封头等零部件组焊而成。
大容积容器的筒体一般是由长方形钢板压头、卷圆而成,故而需预先加工好焊接坡口就是对钢板毛坯料四边进行加工。
本论文以3 m3六氟化铀容器筒体坡口加工为例进行说明(其他容器筒体坡口加工与其类同)。
一、容器筒体焊接坡口的技术要求压力容器筒体焊接坡口(以下简称“筒体坡口”)形式应按能保证焊接质量填充金属量少、改善劳动强度,便于操作、减少焊接应力和变形、适应探伤要求等原则选用,在实践工作中常用的坡口形式有V 型、U型、双V型、X型等,3 m3六氟化铀容器筒体坡口按图纸规定采用“X型”及“V型”坡口形式,加工技术要求如下图所示:二、铣边机加工焊接坡口的定位装卡方法1.筒体在铣边机上定位需考虑的问题容器筒体在铣边机上的准确定位是铣边机坡口加工关键步骤,直接关系到加工的产品质量。
筒体装卡时应考虑以下几方面的影响因素:(1)要确保筒体直边的加工线与动力机头的横向移动轨迹平行。
(2)要确保筒体待加工边与铣边机底边接触面有足够的伸出量,以防改变动力机头角度时,刀头与铣边机床身发生干涉。
但伸出量不宜过大,负责加工时震动大、噪音大,不利于设备使用,易伤刀片。
多功能机床铣削装置设计论文_学位论文
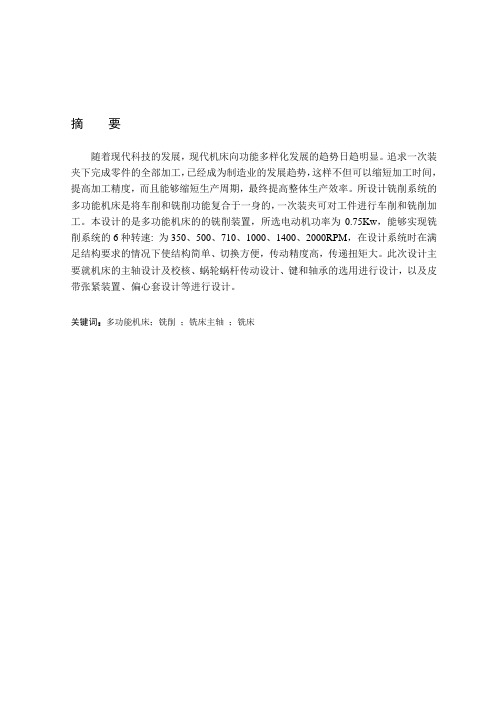
摘要随着现代科技的发展,现代机床向功能多样化发展的趋势日趋明显。
追求一次装夹下完成零件的全部加工,已经成为制造业的发展趋势,这样不但可以缩短加工时间,提高加工精度,而且能够缩短生产周期,最终提高整体生产效率。
所设计铣削系统的多功能机床是将车削和铣削功能复合于一身的,一次装夹可对工件进行车削和铣削加工。
本设计的是多功能机床的的铣削装置,所选电动机功率为0.75Kw,能够实现铣削系统的6种转速: 为350、500、710、1000、1400、2000RPM,在设计系统时在满足结构要求的情况下使结构简单、切换方便,传动精度高,传递扭矩大。
此次设计主要就机床的主轴设计及校核、蜗轮蜗杆传动设计、键和轴承的选用进行设计,以及皮带张紧装置、偏心套设计等进行设计。
关键词:多功能机床;铣削;铣床主轴;铣床ABSTRACTAlong with the modern science and technology development, the modern engine bed are tending to the function diversification development day by day. Pursuing an attire to clamp the whole processing of completing the components has already became the trend of the development of manufacturing industry, which not only may reduce the process period, increase the working accuracy,but also can reduce the production cycle, raise the whole production efficiency finally. A cutter bar end fixes on the main axle, the other end in is revolving in the bearing which locates at the cutter bar place. Designs the milling system's multi-purpose engine beds is bonds the turning and the milling function in a body, an attire clamps may carry on the turning and the milling processing to the work piece. What I design is the milling installment of the multi-purpose engine beds, what I choose on the electric motor power is 0.75KW, it can realize the milling system's 6 kind of rotational speeds: for 350, 500, 710, 1000, 1400, 2000RPM, when designs the system in satisfies the structure request in the situation, at the same time,what we need is that making the structure to be simple, the convenient cut, the high transmission precision, the big transmission torque.This design is mainly on engine bed's main axle design, the examination, the worm gear worm drive design, the key and the bearing selects carries on the design, as well as the belt stretcher, the main axle inner cone hole's design and so on.Key words:multi-purpose engine beds; milling;milling machine main axle ; milling machine目录摘要 (I)A B S T R A C T..........................................................I I 1前言.. (1)2 铣削装置系统的总体设计 (3)2.1 铣削装置的传动方案 (3)2.2 铣削装置的工作原理 (3)3 皮带传动的设计 (5)2.1 带传动整体结构………………………………………………………………… .52.2 皮带的选用....................................................................... . (8)2.3带轮张紧装置与防护罩的设计4 主轴的设计........................................................................... . (9)4.1 概述.................................................................... (9)4.2 主轴的机构设计 (9)5 蜗轮蜗杆传动设计 (11)5.1蜗杆传动设计准则 (11)5.2 蜗杆尺寸与蜗轮尺寸 (11)5.3 蜗轮齿根弯曲强度计算……………………….………………...…………12.6 滚动轴承的选用........................................................................... . (18)7 键的选择.................................................................... ................ . (19)8 偏心轮的设计........................................................................ .......... (20)9结论 (22)参考文献 (23)致谢 (24)1前言1.1 机床行业大背景机床是工作母机,制造机器的机器。
文献综述-铣边机

铣边机一、前言随着机床向高精、高速、高效、数控及多功能方向发展,出现了各种各样的机床,但在加工特定产品的时候仍然需要设计者针对这一产品的加工工艺来进行设计、制造。
因此,设计了这台铣边机。
本铣边机主要是根据用户特定工件,且符合用户要求而研究、设计的一台铣边机。
设计分四个部分来说明。
第一部分是用户提出的要求。
根据用户的具体要求,对所加工的产品有了深刻的认识。
第二部分是加工方案,熟识被加工零件,以及用户所提出的一些具体的要求,就可以制定几种初步的加工方案,来满足用户提出要求的方法,比较几种方案选其最优者。
第四部分确定机床的基本参数。
根据基本参数设计有关部件、及外购件。
在编写毕业设计过程中,得到“大连水产学院”王伟老师和“大连锦运机械设备有限公司”颜庭筠的支持与协助,再此一并致以谢意。
二、设计要求1.1设计名称及数量:1.1.2设备名称:铣边机。
1.1.2数量:1台。
1.1.3主要用途:用于U型槽轴焊接坡口的加工。
1.2 工艺条件和技术要求1.2.1产品数量2.11产品形状及尺寸要求详见附图1.3.1电力:交流380/220V、50Hz.1.3.2压缩空气:压力0.4-0.5Mpa.1.3.3环境温度:0度-60度1.4设备设计、制造原则和执行标准1.4.1.1设备设计、制造原则1.4.1.2保证加工精度和粗糙度要求。
1.4.1.3一次装夹完成加工部位的加工。
1.4.1.4可以使用自制刀具,但应考虑刀具的制造成本和互换性。
1.4.1.5工件的定位、夹紧形式不限,但要考虑工件装夹和工人操作的便利,以及切屑可能对装夹的影响,保证切削和切削精度的实现。
1.4.1.6完善的切屑收集装置,避免切屑的飞溅。
1.4.1.7设备可在标准卧室组合铣床的基础上,本着实用、可靠、经济、适当通用、操作方便的原则,改进、设计、制造。
1.4.2执行标准国家及行业颁有关铣床、液压机、组合机床的相关标准。
1.5 设备要求1.5.1.1主机结构应具有足够的强度和刚性,防止使用过程中的变形。
数控铣床零件加工工艺分析与程序设计毕业论文
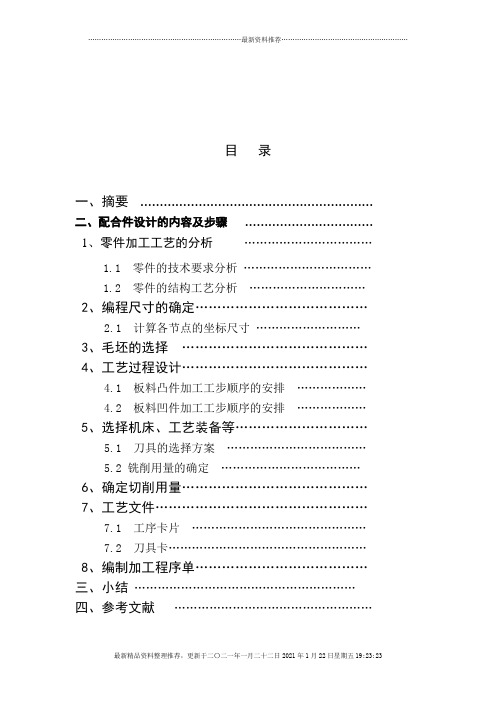
目录一、摘要……………………………………………………二、配合件设计的内容及步骤……………………………1、零件加工工艺的分析……………………………1.1 零件的技术要求分析……………………………1.2 零件的结构工艺分析…………………………2、编程尺寸的确定…………………………………2.1 计算各节点的坐标尺寸………………………3、毛坯的选择……………………………………4、工艺过程设计……………………………………4.1 板料凸件加工工步顺序的安排………………4.2 板料凹件加工工步顺序的安排………………5、选择机床、工艺装备等…………………………5.1 刀具的选择方案………………………………5.2 铣削用量的确定………………………………6、确定切削用量……………………………………7、工艺文件…………………………………………7.1 工序卡片………………………………………7.2 刀具卡……………………………………………8、编制加工程序单…………………………………三、小结…………………………………………………四、参考文献……………………………………………摘要数控机床的出现以及带来的巨大利益,引起世界各国科技界和工业界的普遍重视。
发展数控机床是当前我国机械制造业技术改造的必由之路,是未来工厂自动化的基础。
数控机床的大量使用,需要大批熟练掌握现代数控技术的人员。
数控技术的应用不但给传统制造业带来了革命性的变化,使制造业成为工业化的象征,而且随着数控技术的不断发展和应用领域的扩大,它对国计民生的一些重要行业的发展起着越来越重要的作用。
随着科技的发展,数控技术也在不断的发展更新,现在数控技术也称计算机数控技术,加工软件的更新快,CAD/CAM的应用是一项实践性很强的技术。
如像UG , PRO/E , Cimitron , MasterCAM ,CAXA制造工程师等。
数控技术是技术性极强的工作,尤其在模具领域应用最为广泛,所以这要求从业人员具有很高的机械加工工艺知识,数控编程知识和数控操作技能。
数控论文_铣削盖板类零件的加工
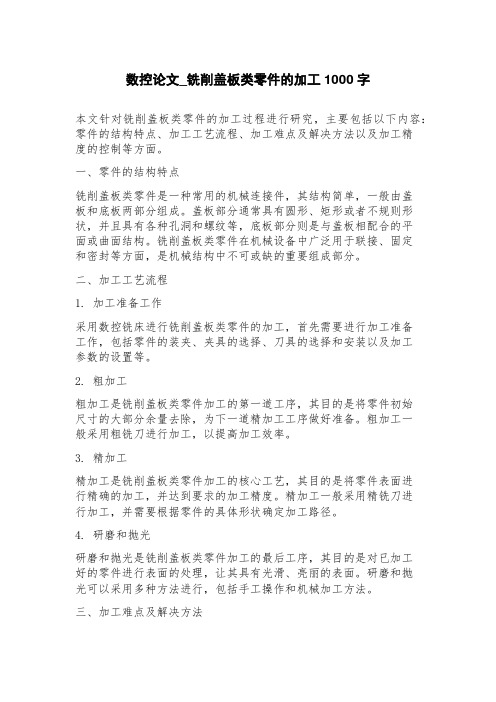
数控论文_铣削盖板类零件的加工1000字本文针对铣削盖板类零件的加工过程进行研究,主要包括以下内容:零件的结构特点、加工工艺流程、加工难点及解决方法以及加工精度的控制等方面。
一、零件的结构特点铣削盖板类零件是一种常用的机械连接件,其结构简单,一般由盖板和底板两部分组成。
盖板部分通常具有圆形、矩形或者不规则形状,并且具有各种孔洞和螺纹等,底板部分则是与盖板相配合的平面或曲面结构。
铣削盖板类零件在机械设备中广泛用于联接、固定和密封等方面,是机械结构中不可或缺的重要组成部分。
二、加工工艺流程1. 加工准备工作采用数控铣床进行铣削盖板类零件的加工,首先需要进行加工准备工作,包括零件的装夹、夹具的选择、刀具的选择和安装以及加工参数的设置等。
2. 粗加工粗加工是铣削盖板类零件加工的第一道工序,其目的是将零件初始尺寸的大部分余量去除,为下一道精加工工序做好准备。
粗加工一般采用粗铣刀进行加工,以提高加工效率。
3. 精加工精加工是铣削盖板类零件加工的核心工艺,其目的是将零件表面进行精确的加工,并达到要求的加工精度。
精加工一般采用精铣刀进行加工,并需要根据零件的具体形状确定加工路径。
4. 研磨和抛光研磨和抛光是铣削盖板类零件加工的最后工序,其目的是对已加工好的零件进行表面的处理,让其具有光滑、亮丽的表面。
研磨和抛光可以采用多种方法进行,包括手工操作和机械加工方法。
三、加工难点及解决方法1. 零件定位和装夹零件定位和装夹是数控铣削加工中的一项关键工艺。
铣削盖板类零件通常具有不规则的形状和较高的加工精度要求,因此其定位和装夹必须非常准确。
解决方法包括采用精密夹具、选用合适的装夹方式以及进行定位精度的检测等。
2. 刀具的选择和安装铣削盖板类零件的加工需要使用不同的刀具进行,刀具的选择和安装必须合理。
刀具的性能和质量决定了加工效率和加工质量的高低,选用合适的刀具和运用正确的安装方法能有效地解决刀具的磨损和断裂等问题。
3. 加工参数的设置加工参数直接影响着零件的加工精度和表面质量。
机床设计论文六篇
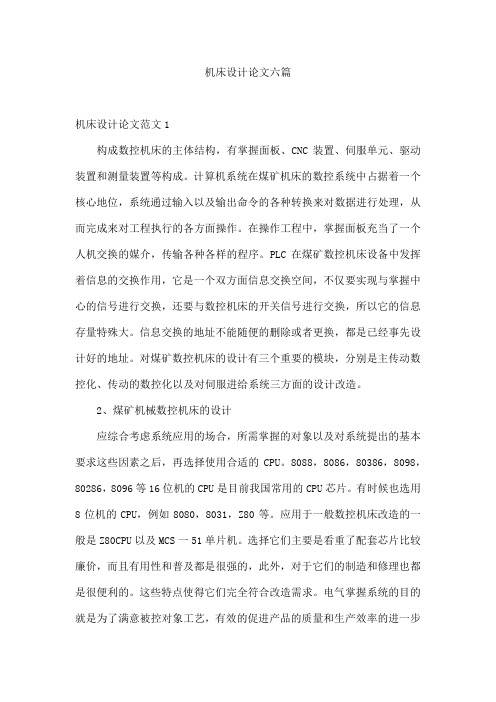
机床设计论文六篇机床设计论文范文1构成数控机床的主体结构,有掌握面板、CNC装置、伺服单元、驱动装置和测量装置等构成。
计算机系统在煤矿机床的数控系统中占据着一个核心地位,系统通过输入以及输出命令的各种转换来对数据进行处理,从而完成来对工程执行的各方面操作。
在操作工程中,掌握面板充当了一个人机交换的媒介,传输各种各样的程序。
PLC在煤矿数控机床设备中发挥着信息的交换作用,它是一个双方面信息交换空间,不仅要实现与掌握中心的信号进行交换,还要与数控机床的开关信号进行交换,所以它的信息存量特殊大。
信息交换的地址不能随便的删除或者更换,都是已经事先设计好的地址。
对煤矿数控机床的设计有三个重要的模块,分别是主传动数控化、传动的数控化以及对伺服进给系统三方面的设计改造。
2、煤矿机械数控机床的设计应综合考虑系统应用的场合,所需掌握的对象以及对系统提出的基本要求这些因素之后,再选择使用合适的CPU。
8088,8086,80386,8098,80286,8096等16位机的CPU是目前我国常用的CPU芯片。
有时候也选用8位机的CPU,例如8080,8031,Z80等。
应用于一般数控机床改造的一般是Z80CPU以及MCS一51单片机。
选择它们主要是看重了配套芯片比较廉价,而且有用性和普及都是很强的,此外,对于它们的制造和修理也都是很便利的。
这些特点使得它们完全符合改造需求。
电气掌握系统的目的就是为了满意被控对象工艺,有效的促进产品的质量和生产效率的进一步提升。
在设计PLC掌握系统的过程中,要根据下列原则进行。
一、坚持完整性原则,也就是说,要确保可以满意工业生产过程和机械设备的需要。
二、经济性原则,就是产品一经设计出可以做到简洁有用。
三、牢靠性原则,就是PLC掌握系统在设计完成后可以稳定牢靠的运行。
四、进展性原则,就是对现在已有的生产工艺进行全面的检查后给将来的进展留出肯定的空间。
通过机床的传动实现不同的工件在不同的速度下运行时的协调。
- 1、下载文档前请自行甄别文档内容的完整性,平台不提供额外的编辑、内容补充、找答案等附加服务。
- 2、"仅部分预览"的文档,不可在线预览部分如存在完整性等问题,可反馈申请退款(可完整预览的文档不适用该条件!)。
- 3、如文档侵犯您的权益,请联系客服反馈,我们会尽快为您处理(人工客服工作时间:9:00-18:30)。
第一章概述1.1 铣削加工的基本知识一、常用铣床概论(一)万能卧式铣床铣床的主轴中心线与工作台面平行。
其工作台有三个方向即垂直横向及纵向都可以移动。
纵向工作台在水平面内还能向左右旋转0—45度的角度。
如选择合理的附件和工具,几乎可以对任何形状的机械零件进行铣削。
(二)立式铣床铣床的主轴中心线与工作台面垂直,有的立铣因为加工需要,主轴还能向左右倾斜一定角度,以便铣削倾斜面。
立式铣床一般用于铣削平面斜面或沟槽,齿轮等零件。
(三)龙门铣床此铣床具有足够的刚度,适用与强力铣削,加工大型零件的平面,沟槽等。
铣床通常有二轴、三轴甚至更多主轴以进行多刀、多工位的铣削加工,生产效率很高。
铣镗加工中心在生产中也获得了广泛应用,他可承担中小型零件的铣削或复杂面的加工。
铣镗加工中心尚可进行铣、钻、绞、镗、纹丝等综合加工,在一次工件装夹中可以自动更换刀具,进行铣、钻、绞、镗、纹丝等多工序操作。
二、铣床加工范围及加工特点(一)铣床加工范围可加工水平面,台阶面,垂直面,齿轮,齿条,各种沟槽(直槽,T型槽,燕尾槽,V型槽)或成形面等。
(二)铣床加工特点加工范围广,适合批量加工,效率高。
铣刀属多齿工具,根据刀具的不同,出现断续切削,刀齿不断切入或切出工件,切削力不断发生变化,产生冲击或振动,影响加工精度和工件表面粗糙度。
铣床加工精度为179—177。
表面粗糙度为Ra6.3-1.6um。
三、铣削加工与铣削工艺(一)铣削加工铣削加工是在铣床上利用铣刀旋转对工件进行切削加工方法。
铣刀是旋转的多刃具。
铣削是多刃加工,且铣刀可使用较大的切削速度,无空回程,故生产效率高。
(二)铣削用量它包括铣削速度,进给量和铣削宽度和深度。
1、切削速度V c切削速度即为铣刀最大直径的线速度:V c=πdn/1000 m/min2、进给量:指刀具在进给运动方向上相对工件的位移量。
有三种方式:(1)每齿进给量f z mm/z(2)每圈进给量f mm/r(3)每分钟进给量mm/min 铣床多用于每分钟进给量γf=f·n=f z·z n mm/min3、背吃刀量也就是切削深度a p,它是沿铣刀轴线方向测量的切削层尺寸。
4、侧吃刀量就是切削宽度a e,它是沿垂直与铣刀轴线上的测量的切削层尺寸。
(三)选择铣削用量的次序首先选择较大的铣削宽度、深度,其次是加大进个量。
最后才是根据刀具耐用度的要求,选择适宜的铣削速度。
(四)铣削方式1、逆铣铣刀的旋转方向与工件进给方向相反的铣削形式称为逆铣。
2、顺铣铣刀旋转方向与工件进给方向相同的铣削方式称顺铣。
3、端铣端铣的铣削方式有对称和不对称铣削两种。
铣削时铣刀的轴线位于工件中心,这种铣削称为对称铣削。
铣刀的轴线偏于工件的一侧时的铣削,称为不对称铣削。
1.2 铣削加工的历史切削加工是用切削工具,把坯料或工件上多余的材料层切去,使工件获得规定的几何形状、尺寸和表面质量的加工方法。
任何切削加工都必须具备三个基本条件:切削工具、工件和切削运动。
切削工具应有刃口,其材质必须比工件坚硬;不同的刀具结构和切削运动形式,构成不同的切削方法。
用刃形和刃数都固定的刀具进行切削的方法有车削、钻削、镗削、铣削、刨削、拉削和锯切等;用刃形和刃数都不固定的磨具或磨料进行切削的方法有磨削、研磨、珩磨和抛光等。
切削加工是机械制造中最主要的加工方法。
虽然毛坯制造精度不断提高,精铸、精锻、挤压、粉末冶金等加工工艺应用日广,但由于切削加工的适应范围广,且能达到很高的精度和很低的表面粗糙度,在机械制造工艺中仍占有重要地位。
切削加工的历史可追溯到原始人创造石劈、骨钻等劳动工具的旧石器时期。
在中国,早在商代中期(公元前13世纪),就已能用研磨的方法加工铜镜;商代晚期(公元前12世纪),曾用青铜钻头在卜骨上钻孔;西汉时期(公元前206~公元23),就已使用杆钻和管钻,用加砂研磨的方法在“金缕玉衣”的4000多块坚硬的玉片上,钻了18000多个直径1~2毫米的孔。
17世纪中叶,中国开始利用畜力代替人力驱动刀具进行切削加工。
如公元1668年,曾在畜力驱动的装置上,用多齿刀具铣削天文仪上直径达2丈(古丈)的大铜环,然后再用磨石进行精加工。
18世纪后半期,英国工业革命开始后,由于蒸汽机和近代机床的发明,切削加工开始用蒸汽机作为动力;到19世纪70年代,切削加工中又开始使用电力。
对金属切削原理的研究始于19世纪50年代,对磨削原理的研究始于19世纪80年代,此后各种新的刀具材料相继出现。
19世纪末出现的高速钢刀具,使刀具许用的切削速度比碳素工具钢和合金工具钢刀具提高两倍以上,达到25米/分左右;1923年出现的硬质合金刀具,使切削速度比高速钢刀具又提高两倍左右;30年代以后出现的金属陶瓷和超硬材料(人造金刚石和立方氮化硼),进一步提高了切削速度和加工精度。
随着机床和刀具的不断发展,切削加工的精度、效率和自动化程度不断提高,应用范围也日益扩大,从而大大促进了现代机械制造业的发展。
金属材料的切削加工有许多分类方法,常见的有按工艺特征、按材料切除率和加工精度、按表面成型方法三种分类方法。
切削加工的工艺特征决定于切削工具的结构,以及切削工具与工件的相对运动形式。
因此按工艺特征,切削加工一般可分为:车削、铣削、钻削、镗削、铰削、刨削、插削、拉削、锯切、磨削、研磨、珩磨、超精加工、抛光、齿轮加工、蜗轮加工、螺纹加工、超精密加工、钳工和刮削等。
1.3 铣削加工现状高速铣削加工(High Speed Milling, HSM)以其巨大的优势,迅速成为现代加工制造领域最重要的加工手段之一,也是衡量一个国家装备制造水平的重要标志。
因为高速切削加工技术已广泛应用于航空航天、汽车、船舶等关系到国计民生的重要领域,也代表着现代切削制造技术的发展趋势。
近几年来,我国对数控机床需求急剧增加,2000年至2005年,我国数控金切机床产量从14053台跃至59639台,年增长率为33.5%。
我国金切机床产值数控化率从1996年的11.6%提高到2005年的47.3%。
这表明我国的数控机床行业有了极大的发展。
另一方面,我国数控机床进口额连年激增,从2001年的24.1亿美圆增至2005年的64.95亿美圆,国有数控机床的市场占有率却呈现出逐年下滑的趋势,尤其是高速、高精度多轴机床,几乎完全依赖进口[1]。
这些数据可以看出我国的机床制造业尤其是高端加工中心落后于发达国家。
因此,国家在“十五”、“十一五”规划中都把以数控机床为核心的装备制造作为重大专项,以期在这方面有所突破。
数控技术是一门集计算机技术、自动控制技术、机械电子技术以及计算机图形处理技术于一体的综合性技术。
其中NC编程是这一技术的灵魂。
NC编程成为各种CAM软件的核心。
因为NC编程直接影响着数控机床的使用效率和加工质量。
所以国内外投入了大量的人力和物力来提高CAD/CAM软件的编程效率,加工效果以及智能化水平。
现代高速切削加工发展概况由于目前绝大部分的机械零件必须经过切削加工实现,切削加工在机械制造中占用十分重要的地位。
经济全球化使制造国际化,因此竞争也越来越激烈。
如何提高效益、降低成本、加快产品开发周期成为每一个面对市场竞争的企业的迫切愿望。
高速切削加工所具有的明显优势,近年来得到广泛应用并迅速发展。
高速铣削加工(High Speed Milling,简称HSM)的概念源于德国切削物理学家C.J .Salomon博士于1931年所提出的著名切削实验及物理引申[2],他认为对应一定的工具材料有一个临界切削速度,达到此温度切削温度最高。
当超过这一临界切削速度,切削温度反而会降低,而大幅度提高机床的生成效率。
高速铣削加工技术作为一门新兴的技术,以其与传统加工相比无可比拟的优点,在加工制造业中得到了越来越广泛的应用,也带来了巨大的经济效益。
我国要实现由制造业大国向制造业强国的跨越,必须有强大的制造装备业及相关产业体系作支撑。
我国目前的高速数控技术也得到了迅速的发展。
但是,我国还缺少高速铣削加工的核心技术,还有许多基础性的研究工作有待开展,这也是我国走向制造业强国的必由之路!第二章方案设计一、方案1:该设计机床的升降运动由顶部的电动机通过联轴器1传到1号减速箱,带动滑动丝杆螺母机构,由滑动丝杆螺母机构带动动力头作升降运动,铣床的进给运动则由底部的电动机经联轴器2传递到2号减速箱,由2号减速箱输出给与之相配合的滑动丝杆螺母机构,从而带动机架部分沿工作台上的导轨面运动,作横向进给。
刀具的旋转运动由动力头提供。
二、方案2:该方案与方案1的不同之处在于升降运动和进给运动都是在钢丝绳的牵引作用下实现的。
三、方案3:该方案与方案1的不同之处在于控制升降运动和进给运动的滑动丝杆螺母机构由滚动丝杆螺母机构代替。
四、方案比较:方案1:该方案的升降运动和进给运动是由滑动丝杆螺母机构实现,而滑动丝杆螺母机构具有降速比大、运动平稳和运动精度高、轴向牵引力大、自锁性能好等优点,但是它的不足之处是它的传动效率不高、刚度较低。
方案2:在该方案中,钢丝绳起了重要的作用,电动机的转动给钢丝绳一个牵引力,通过此力实现机床的升降运动和进给运动。
这个方案的优点在于钢丝绳制造简单、维修方便、成本低、传动效率较高,但是它运动不够平稳且运动精度低,在传动过程中易产生颤动、不能够自锁、降速比不大。
方案3:该方案中采用了滚动丝杆螺母机构,通过该机构来传递运动,以满足机床的要求。
该方案中的滚动丝杆螺母机构具有摩擦损失小,传动效率高、动作灵敏,低速运动时无爬行现象、磨损小,精度保持性好、可消除轴向间隙,轴向刚度高、摩擦系数小等优点,但是它的工艺复杂,生产成本高,不能实现自锁。
综合考虑,最终选取方案1为最终设计方案,通过其Solid Edge绘图如下图2所示。
图1 方案1初步设计工程图五、其工作原理如下:该铣床由三个动力部分组成;分别由三个电动机提供动力来源,即电动机1、电动机2及动力头。
其中:1号电动机通过联轴器带动1号减速箱旋转,从而带动1号丝杆旋转,控制小托板在垂直方向做上下移动,同时使动力头在垂直方向上做上下移动,适合于不同厚度的焊接板件的加工。
其加工行程为560mm;2号电动机通过2号减速箱带动2号丝杆转到,通过螺母机构带动铣边机的大托板(即机架)左右移动,完成行程为3600mm;可以适用于中小焊接板件的铣边。
动力头的功率为5.5kv,转动角度由手轮转动来调节,其转动是通过棘轮调节,达到转动角度为0-90度,能够满足板所有板件的铣边工作。
第三章 机床具体参数设计机床的主要技术参数包括主参数和基本参数,其中基本参数又包括尺寸参数、运动参数、动力参数。
该机床的主参数已经确定,它是加工焊接板件的专用铣床。
其参数如下:一、技术参数如今我以走上了工作的生涯,近段时间对外协这一方面有了一定的了解,其焊接板件在冷作过程中都要经过铣边这一阶段,通过参考厂家铣边的特点以及结合我公司所以工作零件的特点,决定铣边机的工作行程为3600mm ,当今的厂家在生产过程中最看重的是效率问题。