第09章 物料需求计划(MRP)的编制
生产运作管理 第九 章MRP

2)关键
找出上层元件(父项)和下层元件(子项)之间的联 系,这种联系就是按父项的计划发出订货量来计算子项的 总需要量,并保持时间上的一致性。
3)处理过程
① 主生产计划(产品出产计划)
周次 产品A 1 2 3 4 5 6 7 8 10 9 11 15 12
② 产品结构文件
零层
1层
ZC 5 3 ZD 2 4
ZE 3 1
2层 3层
ZE 2 1
4)结构优化
相同的元件出现在不同的层次上,这固然可以清 楚地表是各个不同的生产阶段,但给计算机处理带来 麻烦,为了便于计算机处理,凡是遇到同一元件出现 在不同层次上的情况,取其最低层次号,作为该元件 的底层码。按照改进的产品结构文件,可以从上到下 逐层分解,每一元件只需检索一次,节省了计算机运 行时间。 ZQ
(2)需求数据:是由系统计算得 出的。 C. 总需要量:是由上层元件的计 划发出订货量决定的。 D.净需要量:净需要量=总需要量预计到货量-现有数 。
二 、MRP系统的输出
由于MRP系统的输入内容广泛,因此输出报告的内容涉及范围也几 乎是没有限制的,主要有:
1)零部件投入出产计划
规定每个零件和部件的投入数量、投入时间、出产数量、出产时间。 如果一个零部件由几个车间加工,则要将零部件投入出产计划分解成 “分车间零部件投入出产计划”。
ZD 2 4
ZE 2 1
3)层次
在产品结构文件中,各个元件处于不同的层次,每一 层次表示制造最终产品的一个阶段。通常,最高层为零层,
代表最终产品项,第一层代表组成最终成品的元件,第二 层次代表组成第一层元件的元件,以此类推。
ZQ X 2
ZB 1 2 ZC 2 3 ZD 2 4 ZE 2 1 ZD 2 4
第09章 物料需求计划(MRP)的编制
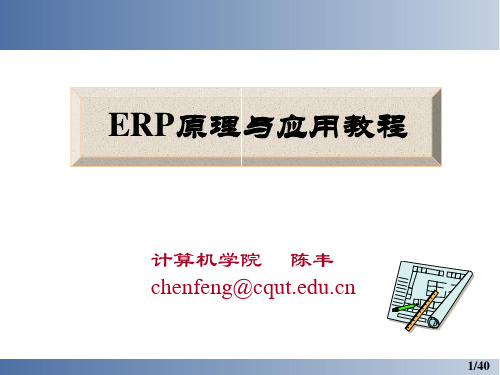
计划接收量和已分配量均为零,求物料B的净需求。
A产品的BOM图见右图
A
(2)
B(1)
B(1)
C(1)
D(1)
30/40
A
直接批量法:完全根据净需求量来 确定计划产出量
安 批 提 现 分 全 低 物 前 有 配 库 阶 料 量
200
60 60 60 60 60 60 140 140 120 120 120 120 120 0 20 20 0 60 0 0 140 140 200 0 0 200 200
1 2 60 0 0 1 C
1 1 120 0 0 2 B
20
200
31/40
4 MRP的编制案例
.11000 ..11100 …11110 ..11200 …12100 .12000 ..12100
方桌(X)
桌面(A) 面板(C) 板材(O) 面框(D) 方木(R) 桌脚(B) 方木(R)
件
件 件 平方米 件 立方米 件 立方米
1
1 1 1 4 0.2 4 0.2
完 全 分 解 表
1 2 3 2 3 1 2
4.1 例1 4.2 例2 4.3 例3 4.4 例4
4.5 例5
32/40
P115 例9.4 MRP的编制简例(当考虑批量规则时) 已知:某物料的毛需求和到货计划见表1,该物料 的已分配量为零,提前期为2周,现分别采用直接批量
法和固定批量法(批量为15)编制MRP。
33/40
批 提 现 分 安 低 物 全 前 有 配 库 阶 料 量 期 量 量 存 码 号
11/40
2.1.2 物料清单
物料需求计划MRP
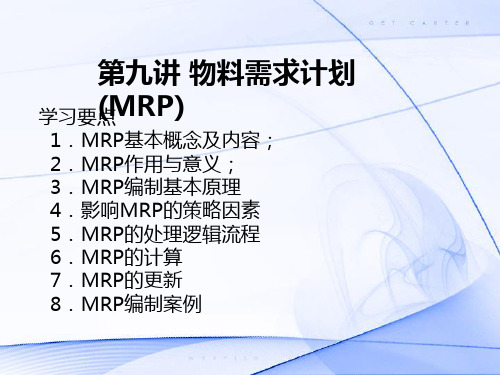
在BOM中,可以得到的信息是:
(1)一个上属项 ( 产品、部件、组件等 ) 是由哪些下属 项 ( 原材料、坯料、零件等 ) 所组成的。同理,也可以说 明某个下属项应用于哪些上属项。上属项为父项,下属项 为子项。 (2)一个上属项对构成它的下属子项的数量要求。 BOM给出了每个子项在其父项中的需要量。
4.库存信息 "已经有什么" (1)物料可用数据 ●现有库存量 ●计划接收量 ●已分配量
(2)编制订单数据 ●制造/采购标识码 ●项目的提前期 ●安全库存 ●批量规则
5.其他
(1) 低位码 所谓低位码是指某个物料在所有产品结构树中所处
的最低层数,因此可以通过零部件所在产品结构树中 的层次来决定它的低位码。
B
2
C
1
D
1
E
MRP数据项
毛需求量 下达订单计划
毛需求量 下达订单计划
毛需求量 下达订单计划
毛需求量 下达订单计划
毛需求量 下达订单计划
1 234
100 100
100 LT=3
200 200 200 200 400 400
567 8 100
LT=4
五、MRP编制案例
【案例2 当独立需求与相关需求同时存在时】
四、MRP更新方法
1.再生法 在使用再生法时,其处理过程包括的内容有:
(1)主生产计划中列出来的每一个最终项目的需求 都要加以分解。 (2)每一个BOM文件都被访问到。 (3)第一个库存状态记录都要经过重新处理。
2.净改变法 净改变式系统的实施可以采用以下两种方式。 (1)较频繁的重排计划(通常每天批处理一次)。 (2)连续地重排计划,即实时处理。
是对主生产计划的各个项目所需的全部制造件和全部采 购件的网络支持计划和时间进度计划。
第9章物料需求计划MRP
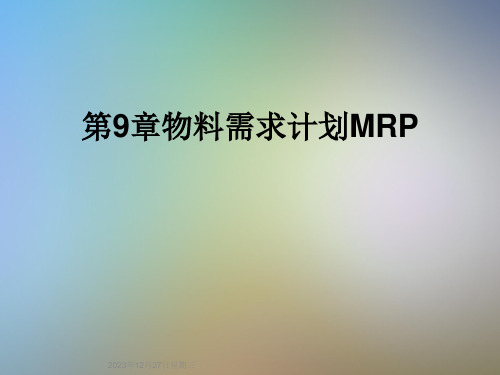
6.MRP系统在总的生产计划中的地位
顾客订货
产品需求预 测
工程设 计
主生产计划
库存存取记录
物料清单
物料需求计划
库存报告
基本报告 生产作业计划 生产指令 采购订单
派生报告 计划完成情况分析报告 急件催派报告 近期重点需要的物料报告
7.一个简单的MRP例子
• 若需要生产100单位产品T,需要零部件 的数量是多少?
假定经济定货批量为50。需求情况如下:
表9-1对某零件的需求
周次
1 2 3 4 5 6 7 8 9 10
需求情况1 20 0 0 20 0 0 0 20 0 0
需求情况2 20 0 40 0 0 0 0 0 0 0
需求情况3 20 0 0 0 0 0 0 0 0 40
2)高库存与低服务水平
传统的订货点方法使得低库存与高服务水平两者不 可兼得。服务水平越高则库存越高,还常常造成零件 积压与短缺共存的局面。
订货点法适合于需求比较稳定和均匀的 物料。然而,在实际生产中,随着市场环境发
生变化,需求常常是不稳定的、不均匀的,在 这种情况下使用订货点法便暴露出一些明显的 缺陷。
1)盲目性
由于需求的不均匀以及对需求的情况不了解,企业不 得不保持一个较大数量的安全库存来应付这种需求。 这样盲目地维持一定量的库存会造成资金积压,造成 浪费。
– 计划调整功能。
3) MRPII阶段(Manufacturing Resource Planning)
MRPII在80年代初开始发展起来,是一种资源协 调系统,代表了一种新的生产管理思想。
• 它把生产活动与财务活动联系起来,将闭环 MRP与企业经营计划联系起来,使企业各个部 门有了一个统一可靠的计划控制工具。它是企 业级的集成系统,它包括整个生产经营活动: 销售、生产、生产作业计划与控制、库存、采 购供应、财务会计、工程管理等。
mrp物料需求计划步骤

mrp物料需求计划步骤一、概述MRP(Material Requirements Planning,物料需求计划)是一种计算工具,可以帮助企业进行物料需求的计划和控制。
它可以根据销售订单、生产计划等信息,自动计算出所需的原材料、零部件等物料,并提供采购、生产等决策支持。
二、步骤1. 建立物料清单(BOM)BOM是指产品的物料清单,包括所有需要用到的原材料、零部件等。
建立BOM是MRP计算的基础,必须准确无误。
BOM应该包括物料编号、名称、数量等信息。
2. 收集需求信息MRP需要收集销售订单、生产计划等信息来进行计算。
销售订单包括客户订购的产品数量和交货时间;生产计划包括要生产的产品数量和交货时间。
3. 计算净需求量净需求量是指需要采购或生产的物料数量。
它由销售订单和生产计划决定,通过减去已有库存量得出。
如果库存不足,则需要采购或生产。
4. 计算批量大小批量大小是指每次采购或生产所需的最小数量。
它由供应商提供的最小订购量、生产设备的最小生产数量等因素决定。
批量大小应该尽可能小,以减少库存和成本。
5. 计算采购或生产计划根据净需求量和批量大小,计算出采购或生产的计划。
如果需要采购,则需要考虑供应商的交货时间、运输时间等因素;如果需要生产,则需要考虑工艺流程、设备利用率等因素。
6. 更新库存信息采购或生产完成后,需要更新库存信息。
如果有多个仓库,则需要分别记录每个仓库的库存情况。
同时,还需要记录每个物料的最大和最小库存量,以便及时补充或清理过多的库存。
7. 监控和调整计划MRP是一个动态的过程,需求信息、供应商情况等都可能发生变化。
因此,需要不断监控和调整计划,以保证物料供应充足、成本最低。
三、注意事项1. MRP计算结果只是一种参考,不是绝对的规定。
实际操作中还需考虑人力资源、设备利用率等因素。
2. MRP计算涉及到大量数据,必须保证数据准确无误。
3. MRP计算应该根据企业实际情况进行调整,不能照搬别人的做法。
MRP物料需求计划编制(doc 9页)
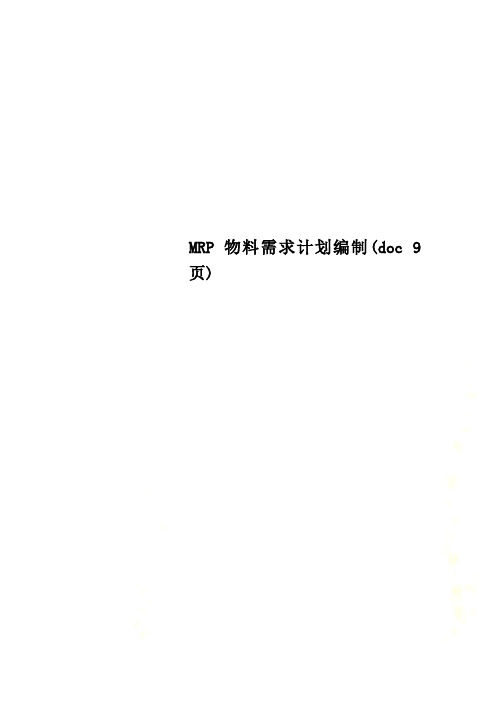
MRP物料需求计划编制(doc 9页)班级:工商091姓名:龚兰萍学号:09064211实验地点:A606实验时间:2012-1-7到1-8专题三:物料需求计划编制一基本知识(1)生产计划类型制造业涉及的相关物料计划一般可以分为三种:划层次,可以说ERP的真正运行是从主生产计划开始的。
III) 物料需求计划(Material Requirement Plan,简称MRP)一种既要保证生产又要控制库存的计划方法,它在产品结构的基础上运用网络计划法原理,根据主生产计划和产品结构中各层次物料的从属和数量关系,以每个物料为计划对象,以(最迟)完工日期为时间基准倒排计划,按提前长短区别各物料(最迟)下达计划时间的先后顺序。
MRP概念公式:A*B-C=DA=主生产计划=要生产什么?B=物料清单=用什么生产?C=库存记录=有什么?D=物料需求计划=还应得到什么?(2)主生产计划MPSMRP基本原理逻辑图MRP处理逻辑的7个关键变量1)总需求(Gross Requirement)(需要多少?)2)计划到货量(Scheduled Receipts,SR)未来某期期末将会取得的量,即一种未来的库存,在交货期末视为可用量。
3)在库量(Projected On-Hand, POH)不考虑计划收货量的情况下:4)净需求(Net Requirement)(还缺多少?)5)计划收货量(Planned Order Receipts, PORC)PORC(订单发出前)◊ SR(订单发出后)◊OH(收货)6)预计可用量(Projected Available Balance, PAB)考虑计划收货量的情况下:7)计划发出订货量(Planned Order Release, POR)(3)批量规则(lot-sizing rules)批量规则表示做MPS或MRP计划时,计算物品的计划下达数量所使用的规则,不同的批量规则表示不同的计划下达量的取值方法,系统可依据批量规则计算需求量。
物料需求计划

物料需求计划物料需求计划(MRP)是一种用于计划生产所需原材料和零部件的方法。
通过物料需求计划,生产企业可以确保在生产过程中有足够的物料供应,从而避免生产线停工和生产延误。
本文将讨论物料需求计划的基本原理和流程,以及如何有效地实施物料需求计划。
物料需求计划的定义和作用物料需求计划是一种基于生产计划和销售订单的方法,用于确定制造企业需要什么类型和数量的原材料和零部件,以及需要何时购买或生产这些物料。
物料需求计划的主要作用包括:•确保生产过程中有足够的物料供应,避免生产线停工•优化库存管理,减少库存积压和库存过多•提高生产计划的准确性和可靠性•减少物料采购和库存管理成本物料需求计划的流程物料需求计划通常包括以下几个步骤:1.制定生产计划和销售预测:根据市场需求和销售预测,制定生产计划,确定需要生产的产品数量和日期。
2.识别物料需求:根据生产计划,确定每种产品所需的原材料和零部件的种类和数量。
3.检查现有库存:检查当前库存,确定哪些物料需要订购或生产。
4.编制需求计划:根据物料清单和生产计划,编制物料需求计划,确定每种物料的采购或生产日期和数量。
5.执行需求计划:根据物料需求计划,及时采购或生产所需的物料。
物料需求计划的实施策略为了有效地实施物料需求计划,企业可以采取以下策略:1.建立完善的物料清单:建立详细的物料清单,明确每种产品所需的原材料和零部件。
2.优化库存管理:根据需求预测和库存水平,优化库存管理,避免库存积压和库存不足。
3.建立供应链合作关系:与供应商建立紧密的合作关系,确保及时供应物料。
4.使用物料需求计划软件:利用物料需求计划软件,自动化物料需求计划的制定和执行过程,提高效率和准确性。
5.持续改进:定期评估物料需求计划的执行效果,根据反馈信息不断改进物料需求计划的流程和策略。
结语物料需求计划是制造企业保持生产运作顺畅和高效的重要工具。
通过合理制定和执行物料需求计划,企业可以实现生产过程的优化和成本的降低,提高竞争力。
第九章+物料需求计划的编制

A LT=1
B(2) LT=2
C(2) LT=3
D(1) LT=1
C(2) LT=3
1.MRP的输入数据项
(2)损耗系数 在生产各个环节中,有各种各样的损 耗,因此在MRP的计算过程中,要考虑 有关损耗系数,如组装废品系数、零件 废品系数、材料利用率等。
1.MRP的输入数据项
① • 组装废品系数 组装废品系数是对部件毛需求量的调整。当一 个零部件在装配它的父项时,能估计到零部件的损 失或毁坏,则考虑组装废品系数,它以百分数表示 ,存放在物料清单中。
1.MRP的输入数据项
• (5)其他因素(输入项)
• (1)低位码(Low Level Code, LLC)
• 定义 • 一个物品只能有一个MRP低位码。 • 当一个物品在多个产品中所处的结构层次不同或即使 处于同一产品结构中但却处于不同产品结构层次时, 则取处在最低层的层级码作为该物品的低位码.即取层 次最低的、数字最大的层级码。
• MPR作用:进行需求资源和可利用能力之间的 进一步平衡。其要解决的是加工中均衡的问题 ,来满足MPS的需求。
• MPS的对象是最终产品,但产品的结构是多层 次的,一个产品可能会包含成百上千种需制造 的零配件与外购材料,而且,所有物料的提前 期(加上时间、准备时间及采购时间等)各不 相同,各零配件的投产顺序也有差别
五、MRP的更新方法
具体处理内容 在这里
• (1)主生产计划中列出来的每一个最终项目的需求都 要加以分解。 • (2)每一个BOM文件都被访问到。 • (3)第一个库存状态记录都要经过重新处理。
•
现行的ERP系统多采用再生法实施MRP
五、MRP的更新方法
• 2.净改变法
• 净改变法(net change MRP ),只对上生产计划中 因改变而受到影响的那些物料清单进行分解处理 • • 采用频繁地甚至连续地进行局部分解的作业方式
- 1、下载文档前请自行甄别文档内容的完整性,平台不提供额外的编辑、内容补充、找答案等附加服务。
- 2、"仅部分预览"的文档,不可在线预览部分如存在完整性等问题,可反馈申请退款(可完整预览的文档不适用该条件!)。
- 3、如文档侵犯您的权益,请联系客服反馈,我们会尽快为您处理(人工客服工作时间:9:00-18:30)。
R 方木
1.0
因此,方木的低阶码为3
16/40
板材
b.作用:
低阶码是MRP的计算顺序。 在MRP运算中,使用低阶码能简化运算—将在BOM表中 多次出现的同一物料“合并”运算,而且使其运算结果更符合
实际、更科学。
17/40
2、损耗系数
在生产各个环节中,有各种各样的损耗,因此在MRP的计
算过程中,要考虑有关损耗系数,包括:组装废品系数、零件废
P112 例9.1 求毛需求及计划投入量
已知MPS为在第8个计划周期时产出100件A产品,其中A产
品的BOM图见下图。
A LT=4 B(1) LT=3
(2)
C(2) LT=2 E(2) LT=1
25/40
D(1) LT=1
某时段下层物料的毛需求是根据 上层物料在该时段的计划投入量 和上下层数量关系计算的
部件A需要5个部件B,则生成5个部件A
则需要25个部件B。
7/40
1 MRP的概念
1.1 物料需求计划的定义 1.2 MRP的计划对象 1.3 MRP回答了制造业的通用公式
8/40
1.3 MRP回答了制造业的通用公式
9/40
2 MRP的工作原理
2.1 MRP的输入数据项 2.1.1 主生产计划 2.1.2 物料清单
时 段
毛需求 计划接收量 预计可用库存 净需求 计划产出量 计划投入量 毛需求 计划接收量 预计可用库存 净需求 计划产出量 计划投入量
当 期
1
5
2 3 4 5 6 7 8
10 20 25 18 7 0 7 10 0 3 3 6 0 6 6 14 10 12 3 15 15 15 6 6 0 6 14 7 8 15 0 0 14 0 14 14
1
.13000
螺钉等(E)
套
1
2.1.3 库存信息
□库存信息保存了每一种物料的有关数据,MRP系统中关于订 什么,订多少,何时发出订货等重要信息,都存贮在库存文件。 □制造/采购标识码(物料主文件中设置) 即一个物料是采购件还是制造件的标识码。采购或制造标 识码通常用一个字母(B或M)表示。当MRP运行时,该码决定 制订采购订单或制造订单计划。
批 提 低 物 安 现 全 前 阶 料 库 有 量 期 码 号 存 量
A
B(1)
C(2) (1) E(2)
D(1)
当 期
时 段
MPS计划产出量 MPS计划投入量 毛需求量 预计可用库存量 净需求 计划产出量 计划投入量 毛需求 计划投入量 毛需求 计划投入量 毛需求 计划投入量
1 2 3 4 5 6 7 8
品系数、材料利用率等。 例:在装配产品A时,估计有10%的玻璃管毁坏,因此,在生产 A所需的玻璃管的毛需求时要增加组装的损耗部分。假设装配 100件A的订单,当考虑其组装废品系数10%时,要有110 (100+100*10%=110)个玻璃管部件的需求。
18/40
2 MRP的工作原理
2.1 MRP的输入数据项 2.1.1 主生产计划 2.1.2 物料清单
1 MRP的概念 2 MRP的工作原理 3 MRP处理过程
4 MRP的编制案例
5 MRP的更新方法 第9章 小结
3/40
1 MRP的概念
1.1 物料需求计划的定义 1.2 MRP的计划对象 1.3 MRP回答了制造业的通用公式
4/40
1.1 物料需求计划的定义
□MRP是一种模拟技术:根据MPS(根据订单结合市场预测制 定出各产品的生产计划,即要生产什么,什么时候生产,生产 多少等内容)、物料清单(产品结构在计算机中的表示)和库 存信息,对每种相关需求物料进行计算,指出何时将会发生物
.11000 ..11100 …11110 ..11200 …12100 .12000 ..12100
方桌(X)
桌面(A) 面板(C) 板材(O) 面框(D) 方木(R) 桌脚(B) 方木(R)
件
件 件 平方米 件 立方米 件 立方米
1
1 1 1 4 0.2 4 0.2
完 全 分 解 表
1 2 3 2 3 1 2
4.0
E 螺钉、 使处于同一产品结构中的但却 套 1.0 胶、 处于不同产品结构层次时,则 油漆
2
11100
C
件1.0
面D 面 R 方木 3 板 件 4.0 m 0.2 框
12100
m3 0.2
11200
12100
取处在最低层的阶码作为该物
料的低阶码,也既取层次最
低、数字最大的阶码。
3
11110
O
2 m
1 1
0 0 0 0 A
200
200
60 60 60 60 60 60 140 140 120 120 120 120 120 0 20 20 0 60 0 0 140 140 200 0 0 200 200
1 2 60 0 0 1 C
1 1 120 0 0 2 B
20
200
31/40
4 MRP的编制案例
4.1 例1 4.2 例2 4.3 例3 4.4 例4
4.5 例5
பைடு நூலகம்
27/40
P113 例9.2 当独立需求与相关需求同时存在时,物料需求的计算
物料A既是产品X的组件又是产品Y的组件,BOM图见下图。所以,A 的需求为相关需求;此外,A作为配件又有独立需求。因此,物料A的 总的毛需求应为其独立需求和相关需求之和。其算例见下表。
提前期=1
批量=1
现有量=0
毛需求的时间即为母件
物料(即上层物料)的 计划投入量的计划时间 ②需求量的确定
1
A B(5)
毛需求
2 25
3
4 50
5
6 70
7
毛需求=母件的计划投入量×子件的用量
23/40
4 MRP的编制案例
4.1 例1 4.2 例2 4.3 例3 4.4 例4
4.5 例5
24/40
7 8 9 10 11 12 13
30 15 40 30 15 30 15 30 15
30
15
0 1
A
毛需求量
45
28/40
4 MRP的编制案例
4.1 例1 4.2 例2 4.3 例3 4.4 例4
4.5 例5
29/40
P113 例9.3 物料净需求的计算(当同一零件分布在同一产品的不
同层次上时,即低阶码的应用)
料短缺,并给出建
议,以满足需求且 避免物料短缺。
5/40
1 MRP的概念
1.1 物料需求计划的定义 1.2 MRP的计划对象 1.3 MRP回答了制造业的通用公式
6/40
1.2 MRP的计划对象
□MRP是基于相关需求的。相关需求的意思是每一个物料的需 求都是由更高层的物料项的需求展开的。例如,桌面、桌脚和方 木等物料都是由方桌需求决定的相关需求物料项目。 □决定需要多少相关需求物料项目是一个 简单的乘法运算过程。即如果生产一个 A B(5)
2.1.3 库存信息 2.1.4 其它因素
2.2 MRP的输出数据项
10/40
2.1.1 主生产计划
□MPS说明一个企业在一个时期内(即计划展望期内)计划生 产的产品名称、数量和日期。
□主生产计划为MRP提供基本的数据,它是MRP运行的驱动力
量,开始编制物料需求计划时,必须首先得到一个有效的主生 产计划。
B (1)
(2) C(1)
B(1) D(1)200
时 段
毛需求 计划接收量 预计可用库存 净需求 计划产出量 计划投入量 毛需求 计划接收量 预计可用库存 净需求 计划产出量 计划投入量 毛需求 计划接收量 预计可用库存 净需求 计划产出量 计划投入量
当 期
1
2 3 4 5 6 7 8
200 0 200 200
已知MPS为在第8个计划周期时产出200件A产品,各物料的
计划接收量和已分配量均为零,求物料B的净需求。
A产品的BOM图见右图
A
(2)
B(1)
B(1)
C(1)
D(1)
30/40
A
直接批量法:完全根据净需求量来 确定计划产出量
安 批 提 现 分 全 低 物 前 有 配 库 阶 料 量 期 量 量 存 码 号
净需求大于0?
YES
毛需求计算
毛需求量的计 算和MPS不同
计划产出量计算 计划投入量计算 预计可用库存计算
NO
完成?
YES
结束
22/40
A
提前期=1 批量=1 现有量=0
段
相关需求物料的毛需求计算 MPS ①需求时间的确定
时
1
2
5
计划产出量 计划投入量
3 5
4
10
5 10
6
14
7 14
MRP B
时 段
11/40
2.1.2 物料清单
□MRP系统要正确计算出相关需求物料需求的时间和数 量,首先要使系统能够知道企业制造的产品所需要用到的 物料。
□物料清单列出构成成品或装配件的所有部件、组件、零
件等的组成、装配关系和数量要求。它是MRP展开的基
础。
12/40
当然,这并不是我们最终所要的BOM(物料清
X Y
在第1,2周期A产品的独立需求均为15件
提 低 物 前 阶 料 期 码 号 4 6 0 0 X Y
A(1)
B(1) (1)
A(1)
C(1) (1)
时 段
计划产出量 计划投入量 计划产出量 计划投入量 相关需求 X->A 相关需求 Y->A 独立需求 A