乳液聚合工艺学_4_乳液聚合工业实施
乳液聚合体系及合成工艺

乳液聚合体系及合成工艺(2007-03-12 14:35:13)转载分类:现代水性涂料一、构成乳液聚合体系的组分乳液聚合体系的主要组分有单体、乳化剂、引发剂和介质,另外根据需要加入其他组分,如助乳化剂、分子量调节剂、pH缓冲剂、抗冻剂、螯合剂、增塑剂、保护胶体、消泡剂等。
1.单体(1)在乳液聚合中单体用量一般控制在40%-50%之间。
(2)乳液的最低成膜温度(MFT)主要决定于乳液聚合物的玻璃化温度(Tg),涂料用聚合物乳液的玻璃化温度,一般在15~25度之间,低于室温。
硬单体(玻璃化温度高的单体)有甲基丙烯酸甲酯(Tg 105)、苯乙烯(Tg 105)丙烯腈(Tg 100)氯乙烯(Tg 75)甲基丙烯酸乙酯(Tg 65)偏二氯乙烯(Tg 52)软单体(玻璃化温度低的单体)有丙烯酸-2-乙基己酯(Tg -85)丙烯酸丁酯(Tg -54)丙烯酸异丁酯(Tg -17)丙烯酸乙酯(Tg -22)丁二烯(Tg -20)氯二丁烯(Tg -45)玻璃化温度适中的单体有醋酸乙烯酯(Tg 29)丙烯酸甲酯(Tg 8)甲基丙烯酸丁酯(Tg 20)(3)线性聚合物进行交联,以生成网状结构聚合物。
有自交联和外交联两种。
二、乳化剂1。
阴离子型、阳离子型、两性和非离子型乳化剂。
2。
乳化剂的选择原则:(1)所选择的乳化剂的HLB值应和所要进行反应的乳液聚合体系相匹配。
(2)所选用的离子型乳化剂的三相点应低于反应温度(3)所选用的非离子型乳化剂的浊点应高于反应温度(4)对离子型乳化剂来说,应选用乳化剂分子的覆盖面积尽可能小;对非离子型乳化剂来说,应选用乳化剂分子的覆盖面积尽可能大(5)应选用临界胶束浓度尽量小的乳化剂(6)应选用增溶度大的乳化剂(7)离子型乳化剂和非离子型乳化剂有协同效应,即两者联合使用比各自单独使用效果都要好。
(8)选择与单体化学结构类似的乳化剂可获得较好的乳化效果(9)亲水性较大和亲水性较大的乳化剂联合使用时乳化效果较好。
聚合反应实施方法
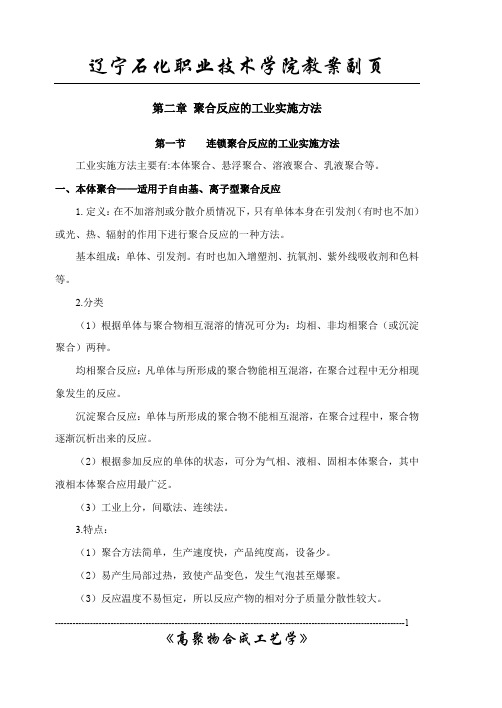
第二章聚合反应的工业实施方法第一节连锁聚合反应的工业实施方法工业实施方法主要有:本体聚合、悬浮聚合、溶液聚合、乳液聚合等。
一、本体聚合——适用于自由基、离子型聚合反应1.定义:在不加溶剂或分散介质情况下,只有单体本身在引发剂(有时也不加)或光、热、辐射的作用下进行聚合反应的一种方法。
基本组成:单体、引发剂。
有时也加入增塑剂、抗氧剂、紫外线吸收剂和色料等。
2.分类(1)根据单体与聚合物相互混溶的情况可分为:均相、非均相聚合(或沉淀聚合)两种。
均相聚合反应:凡单体与所形成的聚合物能相互混溶,在聚合过程中无分相现象发生的反应。
沉淀聚合反应:单体与所形成的聚合物不能相互混溶,在聚合过程中,聚合物逐渐沉析出来的反应。
(2)根据参加反应的单体的状态,可分为气相、液相、固相本体聚合,其中液相本体聚合应用最广泛。
(3)工业上分,间歇法、连续法。
3.特点:(1)聚合方法简单,生产速度快,产品纯度高,设备少。
(2)易产生局部过热,致使产品变色,发生气泡甚至爆聚。
(3)反应温度不易恒定,所以反应产物的相对分子质量分散性较大。
------------------------------------------------------------------------------------------------------------------------1《高聚物合成工艺学》(4)产品容易老化。
4.主要产品:PS树脂、PMMA树脂、PE树脂、PVC树脂等。
5.主要影响因素:(1)单体的聚合热会放出大量的热量,如何排除是生产中的第一个关键问题。
工业生产中:一般采用两段式聚合第一段在较大的聚合釜中进行,控制10%~40%以下转化率;第二段进行薄层(如板状)聚合或以较慢的速度进行。
(2)聚合产物的出料是本体聚合的第二个问题,控制不好不但会影响产品的质量,还会造成生产事故。
解决办法:根据产品特性,选出料方式浇铸脱模制板材或型材,熔融体挤出造粒,粉状出料。
丙烯酸乳液聚合工艺

丙烯酸乳液聚合工艺丙烯酸乳液聚合是一种制备丙烯酸乳液聚合物(通常是聚丙烯酸乳液)的化学过程。
这种聚合过程涉及将丙烯酸单体分散在水中,然后通过引发剂引发聚合反应,最终形成乳液聚合物。
以下是一般的丙烯酸乳液聚合工艺步骤:1. 原材料准备丙烯酸单体:丙烯酸是聚合的基本单体,需要确保其纯度和质量。
分散剂:用于将丙烯酸单体在水中分散。
乳化剂:有助于形成稳定的乳液结构。
引发剂:引发剂引发聚合反应,促使丙烯酸单体形成聚合物。
2. 乳化水相准备:准备含有适当浓度的水溶液。
分散丙烯酸:将丙烯酸单体添加到水相中,并使用分散剂确保丙烯酸均匀分散在水中。
添加乳化剂:添加乳化剂,形成乳液结构。
3. 聚合反应引发剂添加:将引发剂加入乳液中。
聚合反应:引发剂引发丙烯酸单体的聚合反应,生成聚合物颗粒。
反应控制:控制温度、搅拌速度等条件以确保反应进行良好。
4. 终点控制和停止反应终点控制:监测聚合反应的进程,确定聚合物颗粒的大小和分布。
停止反应:在适当的时机停止引发剂的添加,结束聚合反应。
5. 产品调整和稳定化调整pH值:可能需要调整乳液的pH值以获得所需的产品性能。
添加稳定剂:添加稳定剂以提高乳液的稳定性。
6. 过滤和包装过滤:过滤掉未反应的物质和固体颗粒。
包装:将成品乳液聚合物进行包装,以便存储和运输。
7. 质量控制和检验检测颗粒大小和分布:使用仪器或显微镜等工具检测聚合物颗粒的大小和分布。
检验产品性能:对产品进行物理性能和化学性能的检验,确保符合要求。
丙烯酸乳液聚合工艺的具体步骤和条件可能会因制备目的、产品用途和生产规模而有所不同。
在实际生产中,需要根据具体情况进行优化和调整。
乳液聚合合成及生产工艺.

乳液聚合班级:高分0942 姓名:冯会科学号:200910211239乳液聚合(emulsion polymerization)是在乳化剂的作用下并借助于机械搅拌,使单体在水中分散成乳状液,由引发剂引发而进行的聚合反应。
乳液聚合是高分子合成过程中常用的一种合成方法。
乳液聚合体系至少由单体、引发剂、乳化剂和水四个组分构成,一般水与单体的配比(质量)为70/30~40/60,乳化剂为单体的0.2%~0.5%,引发剂为单体的0.1%~0.3%;工业配方中常另加缓冲剂、分子量调节剂和表面张力调节剂等。
所得产物为胶乳,可直接用以处理织物或作涂料和胶粘剂,也可把胶乳破坏,经洗涤、干燥得粉状或针状聚合物。
乳液聚合的发展自由基聚合反应是聚合物生产中应用最为广泛的方法之一,乳液聚合则是由单体和水在乳化剂作用下配制成的乳状液中进行的聚合,体系主要有单体、水、乳化剂和引发剂四种基本组分构成。
乳液聚合技术萌生于上世纪早期,一般公认最早见于文献的是德国Bayer公司的H.Hofmann的一篇关于异戊二烯单体水乳液的聚合专利。
30年代见于工业生产,40年代Harkins定性地阐明了在水中溶解度很低的单体乳液聚合机理。
后来,Smith和Ewart,建立了定量的理论,提出了乳液聚合的三种情况及乳液聚合过程的三个阶段,即乳胶粒生成阶段(阶段I)、乳胶粒长大阶段(阶段II)及乳液聚合完成阶段(阶段III),这一理论被视为乳液聚合的经典理论。
此后乳液聚合成为研究热点。
随着乳液聚合理论的发展,乳液聚合技术也在不断的发展和创新。
关于常规乳液聚合目前研究主要集中在:多组分乳液聚合体系的研究、合成高固含量的乳胶、反应型乳化剂的使用等方面。
另外,在传统乳液聚合工艺的基础上,目前国内外已开发出无皂乳液聚合、细乳液聚合、反相乳液聚合、分散聚合和微乳液聚合等新的聚合工艺。
从本质上来说,这些新的聚合技术与乳液聚合有着共同的特征,即都是分隔体系的聚合反应,有着共同的一些优点。
乳液聚合生产工艺
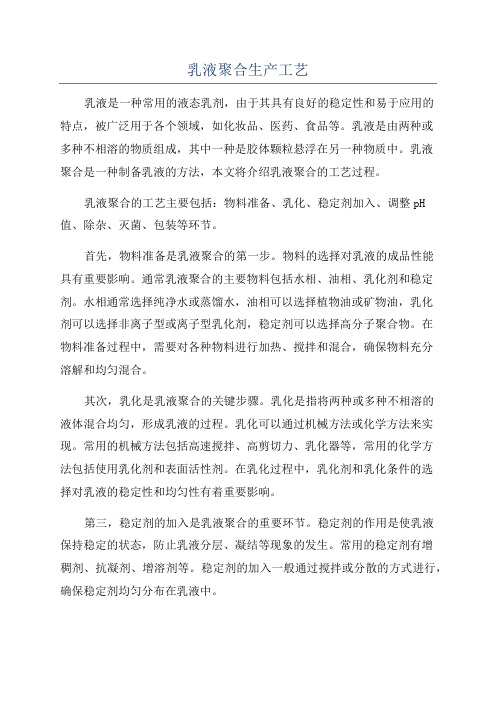
乳液聚合生产工艺乳液是一种常用的液态乳剂,由于其具有良好的稳定性和易于应用的特点,被广泛用于各个领域,如化妆品、医药、食品等。
乳液是由两种或多种不相溶的物质组成,其中一种是胶体颗粒悬浮在另一种物质中。
乳液聚合是一种制备乳液的方法,本文将介绍乳液聚合的工艺过程。
乳液聚合的工艺主要包括:物料准备、乳化、稳定剂加入、调整pH 值、除杂、灭菌、包装等环节。
首先,物料准备是乳液聚合的第一步。
物料的选择对乳液的成品性能具有重要影响。
通常乳液聚合的主要物料包括水相、油相、乳化剂和稳定剂。
水相通常选择纯净水或蒸馏水,油相可以选择植物油或矿物油,乳化剂可以选择非离子型或离子型乳化剂,稳定剂可以选择高分子聚合物。
在物料准备过程中,需要对各种物料进行加热、搅拌和混合,确保物料充分溶解和均匀混合。
其次,乳化是乳液聚合的关键步骤。
乳化是指将两种或多种不相溶的液体混合均匀,形成乳液的过程。
乳化可以通过机械方法或化学方法来实现。
常用的机械方法包括高速搅拌、高剪切力、乳化器等,常用的化学方法包括使用乳化剂和表面活性剂。
在乳化过程中,乳化剂和乳化条件的选择对乳液的稳定性和均匀性有着重要影响。
第三,稳定剂的加入是乳液聚合的重要环节。
稳定剂的作用是使乳液保持稳定的状态,防止乳液分层、凝结等现象的发生。
常用的稳定剂有增稠剂、抗凝剂、增溶剂等。
稳定剂的加入一般通过搅拌或分散的方式进行,确保稳定剂均匀分布在乳液中。
然后,需要调整乳液的pH值。
pH值的调整对乳液的稳定性和成品的质量有着重要影响。
一般来说,乳液的pH值应处于中性或略酸性范围内。
pH值的调整可以通过酸碱中和的方式进行,需要根据具体的产品要求进行调整。
接下来,对乳液进行除杂处理。
除杂的目的是去除乳液中的杂质和残留物,确保乳液的纯度和质量。
除杂的方法有过滤、离心等。
除杂过程中需要注意避免对乳液的物理性能产生影响。
最后,对乳液进行灭菌处理。
灭菌是为了防止乳液中的微生物污染,确保乳液的质量和安全性。
高分子化学第四章乳液聚合

形成保护
增溶作用
单体 液滴 10000A
水相
单体
增溶胶束
乳化剂分子
胶束 40-50A
乳化剂
少量在水相中
单体
大部分形成胶束 部分吸附于单体液滴
小部分增溶胶束内 大部分在单体液滴内
引发剂 大部分在水中
1.聚合场所
水相中?
大量引发剂, 有初级自由 基,但单体 极少。
单体液滴?
引发剂是水溶 性,难以进入
水相中产生自由基,自由基由水相扩散进入胶束,在 胶束中引发增长,形成聚合物乳胶粒的过程。
油溶性单体的主要成核方式。
➢均相成核(homogeneous nucleation)
水相中产生的自由基引发溶于水中的单体进行增长,形 成短链自由基后,在水相中沉淀出来,沉淀粒子从水相 和单体液滴上吸附了乳化剂分子而稳定,接着又扩散入 单体,形成乳胶粒子,这一过程叫均相成核。
连续
转化率 %
>95
99 60
~60 60~90 60~90
一. 乳化剂及乳化作用
乳化剂
亲水基团 疏水基团
C17H35COONa
疏水 亲水
乳化剂种类(type of emulsifier) ➢阴离子型(anionic): 脂肪酸钠(K12,十二烷基硫酸钠),
烷基磺酸钠、松香皂等; ➢阳离子型(cationic): 胺盐、季胺盐;
乳液聚合法生产的聚合物主要品种
主要品种 乳化剂种类
丙烯酸酯类
聚醋酸乙烯 聚氯乙烯
丁苯橡胶 丁腈橡胶 氯丁橡胶
阴离子+非离 子型
非离子型 阴离子+非离
子型 阴离子型 阴离子型 阴离子型
温度 ℃
70~90
乳液聚合生产工艺
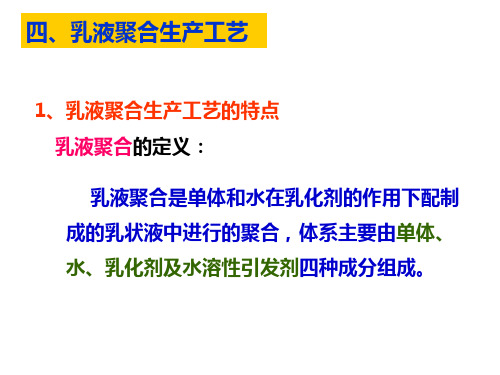
作为O/W型乳化剂
乳化剂的基本特征参数
CMC值:
能够形成胶束的最低浓度称 为临界胶束浓度 。当乳化剂浓 度达到CMC值以后,再增加乳 化剂的浓度只能增加胶束的数量 而不能改变乳液中界面的性质 。 从乳化剂的结构而言,疏
水基团越大,则CMC值越小。
乳化剂浓度变化与乳化剂行为的关系
乳化剂的基本特征参数
当乳化剂浓度在CMC值以
下时,溶液的表面张力与界面张 力均随乳化剂浓度的增大而降低。 而当乳化剂浓度达到CMC值后, 随着乳化剂浓度的增长,其表面
张力和界面张力变化相对很小。
此时,溶液的其他性质,如电导 率、粘度、渗透压等性质随乳化 剂浓度增长的变化规律在CMC
十二烷基硫酸钠水溶液的物理性质变化
值二边也有显著不同。
乳液聚合的影响因素
1、乳化剂的影响(种类和数量) 乳化剂的种类不同,其胶束稳定机理,临界胶束浓度 CMC 、胶束大小及对单体的增容度亦各不相同,从而会 对乳胶粒的稳定性、直径、聚合反应速度和聚合物分子量
产生不同的影响。
乳化剂的浓度对乳液聚合得到的分子量有直接影响,例 如:乳化剂浓度越大,胶束数目越多,链终止的机会小, 链增长的时间长,故此时乳液聚合得到的分子量很大。
• 分散阶段(聚合前段)
• 乳胶粒长大阶段(聚合II段)
• 乳胶粒生成阶段(聚合I段) • 聚合完成阶段(聚合III段)
乳液聚合过程和机理
(1)分散阶段
加入乳化剂,浓度低于CMC时形成真溶液,高于CMC 时形成胶束。
加入单体 按在水中的溶解度以分子 状态溶于水中,更多的溶 解在胶束内形成增溶胶束, 还有的形成小液滴,即单 体液滴。 单体、乳化剂在单体液滴、 水相及胶束间形成动态平 衡。
聚合反应工业实施方法—四大聚合方法及其特点

✓ 如果气态和固态的单体在一定条件下也能聚合的话,按
照定义,应属于本体聚合的一种,可以分别称为气相聚 合和固相聚合。由于所得聚合物将必定和单体产生相分 离,所以气相聚合和固相聚合肯定为非均相聚合
特点几乎都和体系组成的简单有关
✓ 产物纯净
体系中除了因实际需要而加 入少量的助剂如色料、增塑 剂、防老剂、分子量调节剂等 之外,只有单体,产物纯度高
一般聚合液直 接使用
比较纯净,可 能留有少量分
散剂
留有少量乳化 剂和其它助剂
由于介质是水,价格低廉,且生产和应用过程中不存在危险 性和环境污染问题,更适宜直接应用胶乳的场合,如乳胶漆、粘 接剂等
➢ 后处理问题
乳液聚合物的粒径约0.05 ~ 1μm,如需以粒子形态或固体聚 合物使用时乳液要经过与水介质的分离、干燥等工序,使生产成 本提高
➢ 杂质的影响
乳液聚合的产品中残留有乳化剂等杂质难以完全除尽,这将 有损于一些应用性能如防水性、电性能等。
和聚合速率
✓ 应选择聚合物的良溶剂作为反应溶剂,使聚合反应在均相体
系中进行,以尽量消除凝胶效应
✓ 工业上,溶液聚合多用于聚合物溶液直接使用的场合,如涂
料、胶粘剂、浸渍液、合成纤维纺丝液等,因此,还可以根 据应用的需要选择合适的溶剂
2.3 悬浮聚合及其特点
单体以小液滴的形式悬浮 在水介质中,各自独立地 进行聚合
特点
➢ 机理独特
聚合反应分别在各自孤立的乳胶粒中进行,表现出不同的动 力学特征,最重要的是可以在提高聚合速率的同时而不降低产物 的分子量,且可以在较低的温度下聚合
➢ 工艺过程
因以水作为介质,聚合场所在粒径很小的乳胶粒中,乳液的 粘度与聚合物含量及分子量无关,有利于散热、搅拌、管道输送 和连续操作
- 1、下载文档前请自行甄别文档内容的完整性,平台不提供额外的编辑、内容补充、找答案等附加服务。
- 2、"仅部分预览"的文档,不可在线预览部分如存在完整性等问题,可反馈申请退款(可完整预览的文档不适用该条件!)。
- 3、如文档侵犯您的权益,请联系客服反馈,我们会尽快为您处理(人工客服工作时间:9:00-18:30)。
(3)乳化剂 脂肪酸皂:歧化松香酸皂(1:1) 歧化松香酸皂需要经过氢化处理除去不饱和 物质,且低温仍具有良好的乳化效能,不 会产生冻胶。
(4)电解质 一般用量为0.3~0.5份,引发剂为过硫酸钾时 可不加电解质,因其反应后分解为KHSO4, 为电解质。 氧化还原引发剂则需要加入电解质,常用的 有:Na3PO4、K3PO4、KCl、NaCl、Na2SO4 等。
物料进口
(4)反应终点的控制 根据转化率和门尼粘度来加终止剂。 终止剂应加到聚合釜后面连接的小型终止釜 中,常是几个串联,每个釜都有终止剂的 进料口,根据反应需要调整加料的位置。
单体回收过程
胶乳中含有大约40%的未反应单体,需要回收循 环使用。 (1)回收装置与操作条件 丁二烯的回收:40℃,0.02MPa(表压),卧式 压力闪蒸槽;胶乳经闪蒸槽后进入真空卧式闪 蒸槽。 苯乙烯的回收:水蒸气直接加热的蒸馏塔(气提 塔),胶乳塔顶进料,水蒸气塔底进料,苯乙 烯从塔顶出来,塔底流出的胶乳含苯乙烯小于 0.1%。
(8)填充油 常用液态烃,如芳烃或烷烃,有增塑剂的作 用。 配成乳状液之后加入脱除单体后的胶乳中。
(9)引发剂 低温法用氧化还原型引发剂。 氧化剂为有机过氧化物或水溶性过氧化盐,如过 氧化氢、过硫酸钾、异丙苯过氧化氢等,在水 中的溶解度较低。 还原剂在工业上称为活化剂,与氧化剂反应生成 自由基,如硫酸亚铁,常与EDTA配合来控制 亚铁离子的释放速率。同时使用雕白粉来还原 高价的铁离子还原成亚铁离子。
丁苯橡胶乳液聚合所用的电解质常为KCl, 其作用是: (1)降低乳化剂的临界胶束浓度; (2)降低体系的粘度,改善流动性,有利于 传质和传热; (3)起抗冻剂的作用,防止乳液在冷却壁面 上结冰。
(5)分子量调节剂 丁苯乳液聚合常用正十一烷基硫醇或叔十二 烷基硫醇作为链转移剂。 分子量调节剂溶于苯乙烯中,以上其他物质 如电解质、乳化剂、保险粉等一起溶于分 散介质水中。
(2)生产配方
组分 单体 稳定剂 乳化剂 增塑剂 引发剂 PH调节剂 介质 醋酸乙烯酯 聚乙烯醇(1788) OP-10 邻苯二甲酸二丁酯 过硫酸钾 碳酸氢钠 蒸馏水
用量,重量份 100 5.4 1.1 10.9 0.2 0.3 100
注:OP-10为壬基酚聚氧乙烯醚
生产工艺流程 软水计量槽
单 体
预乳化工艺
就是将单体预先进行乳化再加入聚合体系 中的工艺。 预乳化工艺是连续或半连续乳液聚合常用 的单体前处理工艺。 优点: 使乳液体系更加稳定; 不存在生成新乳胶粒的问题; 有利于共聚体系组成均一。
种子乳液聚合
即先制备种子,然后再将制得的种子作为 核加入到聚合体系中,常用于制备核壳功 能乳液。 特点: 可有效控制乳胶粒直径及其分布;
增 塑 剂
调 节 剂
引 发 剂
回流冷凝器
计量槽 聚合釜 隔膜泵
溶解釜 过滤器 过滤器 乳液贮罐
半连续法生产聚醋酸乙烯酯乳液
(3)工艺流程简述
(1)经计量的水、聚乙烯醇投入溶解釜中并送入蒸汽升 温至80℃搅拌4~6h使聚乙烯醇完全溶解; (2)把单体、增塑剂、pH调节剂(10%碳酸氢钠溶液) 和引发剂(10%的过硫酸钾溶液)分别投入计量槽中待 用; (3)溶解釜中的聚乙烯醇溶液经过滤后用隔膜泵送至聚 合釜中,由人孔处加入规定量的OP-10,开动搅拌使其 溶解; (4)从计量槽4向聚合釜送入15份的醋酸乙烯酯,并从 计量槽7向聚合釜送入40%的过硫酸钾溶液,在搅拌下乳 化30min; (5)向聚合物通入水蒸汽使体系升温至60~65℃,此时 聚合反应开始,由于反应放热可使体系升温至80~83 ℃ , 这期间回流冷凝器出现回流;
单体回收需要注意的问题
泡沫:为了防止泡沫进入气体回收系统,在采用卧式 闪蒸槽时必须装设泡沫捕集器,必要时加消泡剂。 凝聚物:为了防止凝聚物堵塞脱除苯乙烯的筛板,可 通过改进塔及塔板的结构、改进塔内表面的处理方法、 改变通入蒸汽的温度与数量以及改善胶乳的稳定性等。 爆聚物:爆聚物是由于丁二烯交联的聚苯乙烯。防止 生成爆聚物的方法是停止生产系统,使用药剂破坏活 性种子,消除已生成的爆聚物,或者将种子生长的抑 制剂(亚硝酸钠、碘、硝酸等)连续不断地加到单体 回收系统或反应系统中。
半连续乳液聚合的优点
可通过加料快慢控制聚合反应速率和放热 速率; 分子量较间歇法偏小,且分布较宽; 乳液聚合体系稳定性高。
连续乳液聚合
各种物料连续不停地加入到反应器中。 与间歇乳液聚合相比具有的特点: 乳胶粒尺寸分布宽; 共聚时聚合物组成不随时间发生变化,但支化 度增大; 聚合体系热量和质量稳定;
(6)待回流减少时,开始向聚合釜通过计量槽4滴加醋酸乙烯 酯,同时通过计量槽7滴加过硫酸钾溶液。通过滴加速度控 制聚合反应温度在78~80 ℃之间,大约8h滴完。单体加完后, 加入全部剩余的过硫酸钾溶液; (7)加完单体和引发剂后通蒸汽升温至90~95 ℃,保温反应 30min; (8)向聚合釜夹套通冷水使体系冷却至50 ℃,通过计量槽分 别加入规定量的PH调节剂碳酸氢钠溶液和增塑剂邻苯二甲 酸二丁酯,然后充分搅拌均匀后出料,过滤后进入乳液贮槽。
半连续乳液聚合
特点: (1)部分组分先投料; (2)剩余部分在一定时间内连续加料,达到 所要求的转化率停止反应。
该法在工业已广泛使用。
半连续乳液聚合的加料方式
按照单体的聚合过程所处的状态分: 饥饿态(加料速率小于反应速率) 充溢态(加料速率大于反应速率) 半饥饿态(先全部一次加入一种或某几种 单体,然后再连续加入另一种或另几种单 体,且滴加速率小于反应消耗速率)
间歇乳液聚合 Batch emulsion polymerization 就是把乳液聚合的各种组成加入反应器中,然 后升温至反应温度,经历阶段1~3之后,达到所 需的转化率停止反应,经降温、过滤得到产品。
主要特点:物料是一次加入反应器
间歇乳液聚合优点
乳胶粒直径分布窄,有利于改善乳液流变 性和成膜性;设备简单,操作方便,生产 灵活,适用于批量少品种多的产品生产。
聚氯乙烯糊树脂生产
聚氯乙烯糊(EPVC)主要用于制造人造革、 壁纸、玩具、汽车内饰等产品。 聚氯乙烯糊生产方法有:间歇乳液聚合法; 半连续乳液聚合法;种子乳液聚合法、微 悬浮聚合法及连续乳液聚合法等。 常用:种子乳液聚合法
氯乙烯种子乳液聚合配方
组分
用量,重量份 配方1 配方2 100 0.07 0.02 150 1 2
单体 引发剂
氯乙烯 过硫酸钾 亚硫酸氢钠
100 0.2 150 1 2 调pH=10~10.5
介质 种子乳液
去离子水 第一代种子 第二代种子
pH调节剂
氢氧化钠
第一代种子:就是用不加种子的乳液聚合法所 制成的乳液。 第二代种子:在第一代种子的基础上继续聚合 所制得的乳液。 用这两种种子制得的乳胶粒直径呈双峰分布, 直径在0.1~2µm之间。可降低增塑剂吸收量, µ 改善树脂的加工性能。
聚氯乙烯糊树脂乳胶粒粒径
生产工艺
软 水
氢 氧 化 钠
引 发 剂
乳 化 剂
氯 乙 烯 种子釜 聚合釜
去后处理 工序
工艺流程简述
包括三个步骤: (1)物料准备与配制 (2)种子的制备 (3)种子乳液聚合
(1)物料准备与配制
十二烷基硫酸钠用软水在50℃下配制并泵 送至计量槽待用; 过硫酸钾用软水在不超过30 ℃下配制并泵 送至计量槽待用; 氢氧化钠用软水常温下配制并泵送至计量 槽待用; 软水及单体泵送至计量槽待用。
干燥: 当前丁苯橡胶工业生产用两种设备进行干 燥: 热风箱式干燥机; 挤压膨胀干燥机。
聚醋酸乙烯酯乳液生产
(1)动力学及工艺特点
聚醋酸乙烯酯乳液聚合不符合Smith-Eward理论,因 单体为水溶性。
稳定乳胶粒采用保护胶为主,乳化剂为辅,聚合反应 速率为保护胶浓度的0.6级反应。
由于最终产品为乳液而不是传统的橡胶产品,因此工 艺与丁苯橡胶不同,不需要进行后处理工艺。
乳液聚合工业实施方法
主要内容
各种乳液聚合工艺 乳液聚合工业生产实例
各种乳液聚合工艺
生产工艺包括: 间歇工艺、半连续工艺、连续工艺、预乳 化工艺、补加乳化剂工艺、种子乳液聚合 工艺等。主要是由于加料方式不同而有所 区别。
工艺不同所得聚合物的质量不同、生产效 率不同、成本不乳液聚合工艺 乳液聚合工业生产实例
聚合物乳液品种
丁苯胶乳 聚醋酸乙烯乳 液 丁腈胶乳 氯丁胶乳 聚苯乙烯及共 聚物胶乳
聚氯乙烯糊树脂 VAE(或EVA) 乳液 (甲基)丙烯酸 酯共聚物乳液
乳液聚合工业生产实例
丁苯橡胶的生产 有溶液丁苯橡胶和乳液丁苯橡胶。 溶液丁苯橡胶 丁二烯和苯乙烯在引发剂丁基锂、溶剂环 己烷以及无规剂四氢呋喃存在下进行溶液 聚合制得的。
转化率%
0
20
40
60
80
90
100
苯乙烯含量%
22.2
22.3
22.5
22.8
23.9
25.3
28.0
(2)聚合反应条件 反应温度 5~7℃; 操作压力(表压)0.25MPa; 反应时间 8~10h; 转化率60%±2%
物料出口
(3)聚合装置 底部进料,上部出料
垂直管式氨蒸发器 1-变速箱;2-电动机; 3-搅拌器;4-夹套; 5-冷却列管;6-人孔
(6)终止剂 二硫代氨基甲酸钠为有效的终止剂,但在单 体回收过程中仍有聚合现象,所以再添加 多硫化钠和亚硝酸钠及多乙烯胺。 多硫化钠可与氧化剂反应;亚硝酸钠可防止 产生菜花状爆聚物。 终止剂用去离子水配制,于反应器后的设备 加入。
(7)防老剂 一般用量为单体量的1.5%; 常用胺类如苯基-β-萘胺、芳基化对苯二胺 等,用于深色制品。一般不溶于水。 防老剂配制成乳液加入已脱除单体的胶乳中, 使之与橡胶混合均匀。