挤出成型的类型
挤出成型的塑料制品有哪些

挤出成型的塑料制品有哪些挤出成型是一种常用的塑料加工方法,通过将塑料料料加热至熔化状态,然后通过挤压出模具的形状,最终获得所需的塑料制品。
挤出成型能够制造出各种不同形状的塑料制品,下面将介绍一些常见的挤出成型塑料制品。
管材管材是挤出成型最常见的应用之一。
无论是家庭用水管、工业管道还是农业灌溉管道,大部分都是通过挤出成型制造而成。
挤出管材具有良好的尺寸精度、韧性和阻燃性能。
塑料薄膜挤出成型还可用于生产各种塑料薄膜,如聚乙烯薄膜、聚氯乙烯薄膜等。
这些薄膜通常用于包装、保护、覆盖和印刷等领域。
挤出成型薄膜的特点是平整、均匀和透明度高。
塑料板材通过挤出成型可以制造出各种塑料板材,常见的有聚乙烯板、聚氯乙烯板、聚丙烯板等。
塑料板材广泛应用于建筑、装饰、广告牌、冷库墙体等领域,具有重量轻、绝缘性能好、耐腐蚀等特点。
塑料型材挤出成型也可用于生产各种塑料型材,如聚乙烯型材、聚氯乙烯型材等。
这些塑料型材常用于建筑领域,如门窗框、管道连接件等。
塑料型材具有重量轻、成本低、易加工等优点。
工业零部件除了上述应用外,挤出成型还可以制造各种工业零部件。
例如,汽车零部件、电器零部件、家具零部件等,都可以通过挤出成型制造。
这些零部件具有稳定的尺寸、良好的耐用性和耐腐蚀性。
塑料丝挤出成型常用于生产各种塑料丝,如聚乙烯丝、聚氯乙烯丝等。
塑料丝常用于织物、缝纫线、绳索、网格等领域。
挤出成型的塑料丝具有高强度和耐磨性的特点。
综上所述,挤出成型可以制造出众多不同形状的塑料制品,如管材、塑料薄膜、塑料板材、塑料型材、工业零部件和塑料丝等。
该方法具有成本低、生产效率高、制造精度高等优点,因此在塑料制造行业中得到广泛应用。
挤出成型工艺—挤出成型原理(塑料成型加工课件)
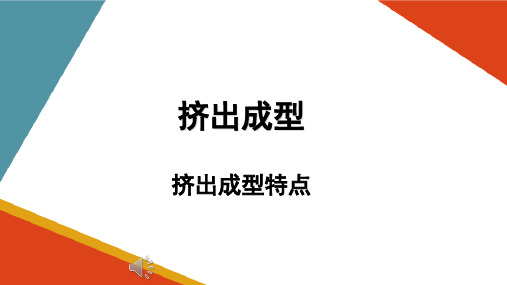
二、挤出成型过程
既有混合过 程,也有成 型过程
树脂原料 加热黏流 塑料熔体
助剂
混合过程
加压 挤出连续体
一定规格的 制品
切割 成型连续体
冷却定型
成型过程
以 管 材 挤 出 原料 成型为例
挤出连续体
熔体
定型连续体
制品
三、挤出成型特点
1. 可以连续化生产,生产效率高。 2. 设备自动化程度高,劳动强度低。 3. 生产操作简单,工艺控制容易。 4. 原料适应性强,适用大多数热塑性树脂和少数热固性 树脂。 5. 可生产的产品广泛,同一台挤出机,只要更换不同的 辅机,就可以生产不同的制品。
挤出成型
挤出成型特点
一、挤出成概述
挤出成型又叫挤出模塑,是利用加热使塑料熔融塑化成 为流动状态,然后在机械力(螺杆或柱塞的挤压)的作用下, 使熔融塑料通过一定形状的口模制成具有恒定截面连续的制 品,适用于绝大部分热塑性树脂和部分热固性树脂。
除了用于挤出造粒、染色、树脂掺和等共混改性,还可用于塑 料薄膜、网材、带包覆层的产品、截面一定、长度连续的管材、板 材、片材、棒材、打包带、单丝和异型材等塑料制品的生产。
料表面接近或达到黏流温度,表面发黏。
要求:输送能力要稍高于熔融段和均化段。
2. 压缩段 (熔融段)
位置:螺杆中部一段。 作用:输送物料,使物料受到热和剪切作用熔 融塑化,并进一步压实和排出气体。 特点:物料逐渐由玻璃态转变为粘流态,在熔 融段末端物料为粘流态。 要求:螺杆结构逐渐紧密,使物料进一步压实。
(3)横流(环流) 由垂直于螺棱方向的分速
度引起的使物料在螺槽内产生翻 转运动。对生产能力没有影响, 但能促进物料的混合和热交换。
(4)漏流 由机筒与螺棱间隙处形成的
挤出机和挤出成型工艺

挤出成型工艺和挤出机1.挤出成型工艺1.1 挤出成型工艺:在挤出机中通过加热、加压而使物料以流动状态持续通过口模(即机头)成型的方式称挤出成型或挤塑。
是塑料重要的成型方式之一。
1.2 挤出成型的特点:①设备本钱低,制造容易,投资少,上马快。
②生产效率高,挤出机的单机产量较高,产率一般在几千克~5吨/小时。
③持续化生产。
能制造任意长度的薄膜、管、片、板、棒、单丝、异型材和塑料与其他材料的复合制品等。
④生产操作简单,工艺控制容易,易于实现自动化。
占地面积小,生产环境清洁,污染少。
⑤能够一机多用。
挤出机也能进行混合、造粒。
1.3 挤出成型可分为两个阶段:第一阶段是使固态塑料变成粘性流体(即塑化),并在加压情形下,使其通过特殊形状的口模,而成为截面与口模形状相仿的持续体。
第二阶段则是用适当的处置方式使挤出的持续体失去塑性状态而变成固体,即取得所需制品。
1.4 挤出成型工艺分类:干法(熔融法)—通过加热使塑料熔融成型①塑化方式湿法(溶剂法)—用溶剂将塑料充分软化成型(CN、CA及纺丝)持续式:螺杆式挤出机,借助螺杆旋转产生的压力和剪切力,使物料充分塑化和均匀混合,通过口模而成型,可进行连续生产。
②加压方式间歇式:柱塞式挤出机,借助柱塞压力,将事先塑化好的物料挤出口模而成型。
仅用于粘度特别大,流动性极差的塑料。
如:PTFE,成型温度下,粘度为1010~1014泊(一般熔融塑料的粘度范围为102~108泊);HUMWPE等。
柱塞可提供很大的压力,但形状不能太复杂,不能加分流梭。
间歇式生产。
2. 挤出设备塑料的挤出,绝大多数都是热塑性塑料,而且又是采用持续操作和干法塑化的。
故在设备方面多用螺杆式挤出机。
螺杆式挤出机有单、双(或多螺杆)之分。
大部份用单螺杆挤出机,只是粉料,RPVC 95%以上都用双螺杆挤出机。
2.1 单螺杆挤出机2.1.1 单螺杆挤出机的组成:由传动系统、加料系统、挤压系统、机头和口模和加热与冷却系统等组成。
第七章 挤出成型
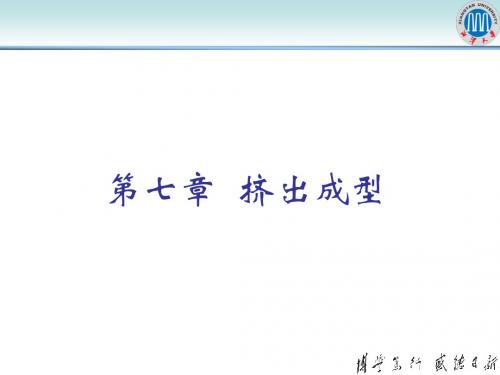
一般 hs=KD
K——常数
(hS为均化段螺槽深度)
取0.02~0.06
⑤螺距(s)螺旋角(¢)
螺距是两个相邻螺纹间的距离,螺旋角是螺旋 线与螺杆中心线垂直面之夹角。螺杆直径一定时, 螺距就决定了螺旋角或螺旋角就决定了螺距, s=πDtg¢.理论和实验证明,30º 的螺旋角最适合于细 粉状塑料;15º 左右适合子方块料;而17º 左右则适合 于球、柱状料。在计量段,根据公式推导,螺旋角 为30º 时产率最高。
螺杆的几种形式
等距不等深螺杆,等深不等距螺杆,不等深不等距螺杆
(2) 螺杆的分段及其作用
按塑料在螺杆上运转的情况可分为加料、熔化(压 缩)和均化(计量)三段,有时就称为三段式螺杆,这 种螺杆就是通用螺杆,或标准螺杆(计量螺杆),螺距 等于D。
① 加料段
加料段是自塑料入口向前延伸一段的距离,其长度 约为4—8D。在这段中,塑料依然是固体状态。 螺杆的主要作用是使塑料受热前移,向熔化段输送 物料,因而螺槽容积可以维持不变,一般做成等距等深 的。螺槽深度(H1),一般为0.1-0.15D,螺距(S)为1一 1.5D。 另外,为使塑料有最好的输送条件,要求减少物料 与螺杆的摩擦而增大物料与料筒的切向摩擦, 为此可采取的方法有:在料筒与塑料接触的表面开 设纵向沟槽;提高螺杆表面光洁度,并在螺杆中心通水 冷却。
橡胶挤出——压出 合成纤维——螺杆挤出纺丝 塑料挤出——主要以热塑性塑料为主
二、挤出成型在聚合物加工中的地位
突出的优点 (1)塑化能力强(一台φ200挤出机产量可达 700kg/ 小时,德国φ500挤出机产量高达20t/小时.) (2)生产效率高(适于大批量生产) (3)材料适应宽(广泛应用于塑料、橡胶、合成纤 维的成型加工,也常用于塑料的着色、混炼、塑化、造 粒及塑料的共混改性等) (4)产品范围大,产品形状多样(能生产管材、棒 材、板材、薄膜、单丝、电线、电缆、异型材,以及中 空制品等截面形状单一的制品) 设备简单,投资少,见效快 近80 %的塑料材料需要挤出成型,挤出设备广泛用 于塑料材料的塑化、熔体输送和泵送加压,从而成为其 他加工方法的基础。
挤出成型类型与工艺流程

主要输送各种流体,以及用作电线套管等。硬聚氯乙烯管易切别、
焊接、钻接、加热可弯曲,因此安装使用非常方便。软聚氯乙烯
管是由聚氯乙烯树脂加入较大量增塑剂和一定量稳定剂,以及其
他助剂,经造粒后挤出成型制成。软聚氯乙烯管材具有优良的化
学稳定性,卓越的电绝缘性和良好的柔软性和着色性,此种管常
用来代替橡胶管,用以输送液体及腐蚀性介质,也用作电缆套管
(1)温度控制 如前所述,生产管材软硬品种不同其加工温 度不同.硬管比软管加工温度高10—20°C。原料状态不同 加工温度也不同,粒料比粉料加工温度高10°C左右。具体 的温度控制应根据具体配方确定。
挤出成型类型和工艺流程
聚氯乙烯管加工温度范围
挤出成型类型和工艺流程
(2)螺杆冷却 由于硬聚氯乙烯熔体粘度大,流动性差,为防 止螺杆因摩擦热过大而升温,引起螺杆粘料分解或使管材内壁 毛糙,必须降低螺杆温度,这样可使物料塑化好,管内表面光 亮,提高管材内外质量。螺杆温度一般控制在80一100 °C之 间,若温度过低反压力增加,产量大大下降,甚至会发生物料 挤不出来而损坏螺杆轴承的事故,因此,螺杆冷却应控制出水 温度不低于70一80 °C。冷却方法是在螺杆内部用通铜管的方 法进行水冷却 。
制
3.1 管材成型工艺
3.1.1 圆 管
塑料管材是塑料挤出成型的主要产品之一。塑料挤出管材就是将 粒状或粉状塑料原料从料斗加入挤出机,物料被加热成熔融的料流, 经螺杆旋转的推力使熔融料通过机头环形通道,形成管状物,经冷 却定型装置对成型的管材进行冷却定型即成为塑料管树。
可供生产管材的塑料原料有:聚乙烯、聚氯乙烯、聚丙烯、ABS、 聚酰胺、聚碳酸酯等。目前国内生产的塑料管材以聚乙烯、聚氯乙 烯、聚丙烯等材料为主。
挤出成型的产品有哪些种类
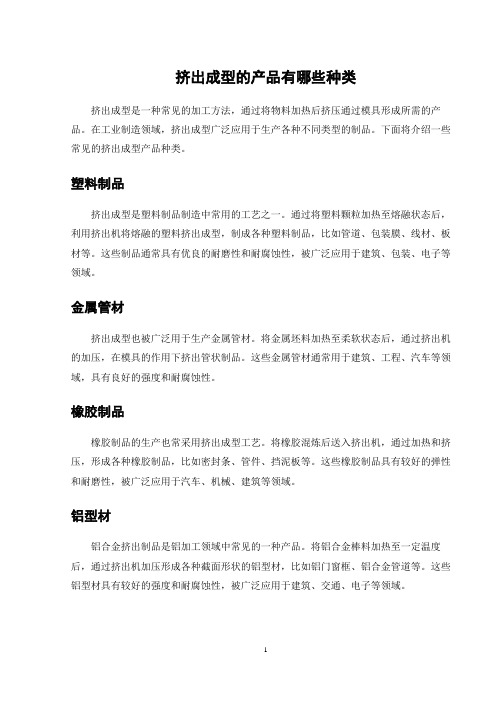
挤出成型的产品有哪些种类挤出成型是一种常见的加工方法,通过将物料加热后挤压通过模具形成所需的产品。
在工业制造领域,挤出成型广泛应用于生产各种不同类型的制品。
下面将介绍一些常见的挤出成型产品种类。
塑料制品挤出成型是塑料制品制造中常用的工艺之一。
通过将塑料颗粒加热至熔融状态后,利用挤出机将熔融的塑料挤出成型,制成各种塑料制品,比如管道、包装膜、线材、板材等。
这些制品通常具有优良的耐磨性和耐腐蚀性,被广泛应用于建筑、包装、电子等领域。
金属管材挤出成型也被广泛用于生产金属管材。
将金属坯料加热至柔软状态后,通过挤出机的加压,在模具的作用下挤出管状制品。
这些金属管材通常用于建筑、工程、汽车等领域,具有良好的强度和耐腐蚀性。
橡胶制品橡胶制品的生产也常采用挤出成型工艺。
将橡胶混炼后送入挤出机,通过加热和挤压,形成各种橡胶制品,比如密封条、管件、挡泥板等。
这些橡胶制品具有较好的弹性和耐磨性,被广泛应用于汽车、机械、建筑等领域。
铝型材铝合金挤出制品是铝加工领域中常见的一种产品。
将铝合金棒料加热至一定温度后,通过挤出机加压形成各种截面形状的铝型材,比如铝门窗框、铝合金管道等。
这些铝型材具有较好的强度和耐腐蚀性,被广泛应用于建筑、交通、电子等领域。
食品制品挤出成型技术在食品工业中也有重要应用。
将食品原料加热后,通过挤出机将其挤出成各种形状的食品制品,比如意面、休闲食品、肉制品等。
这些食品制品形状多样,生产效率高,被广泛用于食品加工生产线。
总的来说,挤出成型是一种灵活多样的加工工艺,可以应用于多种不同材料的制品生产,为各个行业提供高效、精密的生产解决方案。
在未来,随着材料和工艺的不断创新发展,挤出成型技术将在更多领域展现其重要作用。
挤出工艺应用哪些材料成型

挤出工艺应用哪些材料成型挤出工艺是一种常见的制造工艺,广泛应用于塑料、金属、橡胶等材料的加工成型领域。
在挤出工艺中,通过加热和压力将原料推入挤出机的螺杆中,然后经过模具挤压成型,最终得到所需的制品。
挤出工艺不仅具有高效、高速的加工特点,而且可以生产出形状复杂、精度高的制品。
下面将介绍挤出工艺常用的材料及其应用。
塑料材料塑料是挤出工艺中最常用的材料之一,主要包括聚乙烯(PE)、聚丙烯(PP)、聚氯乙烯(PVC)、聚苯乙烯(PS)等。
这些塑料材料具有良好的可塑性和耐腐蚀性,可以满足不同工业领域的需求。
例如,聚乙烯常用于生产管材、薄膜等产品;聚丙烯适用于制作胶带、瓶盖等产品;聚氯乙烯广泛用于制作门窗、管道等制品。
金属材料金属材料在挤出工艺中也有重要的应用,如铝、铜、钢等金属均可以通过挤出工艺进行成型。
金属材料的挤出加工可以提高材料的强度和硬度,同时实现精密成型。
铝挤压制品在汽车、建筑等行业有着广泛的应用,如汽车车身构件、建筑门窗框架等;铜挤压制品常用于电气领域,如电线接线端子等。
橡胶材料挤出工艺也适用于橡胶材料的成型。
橡胶材料具有良好的弹性和密封性,在挤出工艺中可以生产各种密封件、管件等产品。
常见的橡胶材料包括丁晴橡胶、氯丁橡胶、丙烯橡胶等。
丁晴橡胶常用于制作密封圈、O型圈等密封件;氯丁橡胶适用于生产橡胶输送带、橡胶管件等产品。
其他材料除了上述常见的塑料、金属、橡胶材料外,挤出工艺还可以应用于其他材料的成型,如陶瓷、玻璃纤维等。
陶瓷材料通过挤出工艺可以实现复杂形状的成型,广泛用于陶瓷制品制造;玻璃纤维挤出制品在建筑、船舶等领域有着重要的应用,如玻璃钢管道、船体结构件等。
在挤出工艺的应用过程中,不同的材料具有不同的特性和要求,需要选用合适的挤出机、模具和工艺参数来实现高效的生产。
通过合理选择和应用材料,可以满足不同产品的制造需求,推动挤出工艺在各行业的发展和应用。
总的来说,挤出工艺在材料成型中具有重要的地位,通过不断优化工艺和材料选择,可以实现对各类材料的高效成型,满足市场的需求,并促进制造业的发展。
高分子材料成型加工挤出
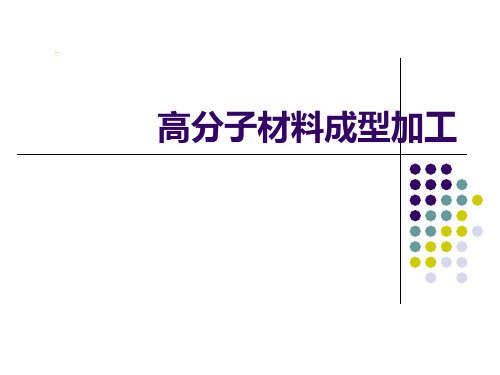
螺杆形式和分段
1-渐变型(等距不等深) 2-渐变型(等深不等距) 3-突变型 4-鱼雷头螺杆 Ⅰ-加料段(固体输送段) Ⅱ-压缩段(熔融段) Ⅲ-计量段(均化段)
加料段 压缩段 计量段
将料斗供给的物料送往压缩段 压缩物料、排除空气
将熔融的物料定量定压送入机头
固态、部分熔融 熔融态 熔融态
螺杆的几何结构参数
工艺示例
以聚丙烯薄膜为例:薄膜厚度10~60μm,挤出温度250~270℃,流 延温度30~40℃,纵向拉伸温度125~145℃、拉伸比4.5~6.0,横向拉 伸温度160~170℃,拉伸比9.0~10.0,热处理温度170~180℃, 陈化处 理2~3天,释放拉伸应力和薄膜表面和起作用的添加剂迁移到表面。
挤出成型设备
螺杆式挤出机:连续成型,用途最多; 柱塞式挤出机:间歇成型,一般不用;
单螺杆式挤出机
螺杆式挤出机 双螺杆式挤出机
多螺杆式挤出机
以单螺杆和双螺杆式挤出机最为常见。
螺杆式挤出机
螺杆式挤出机主要构成
传动装置 加料装置 料筒 螺杆 机头
传动装置
由电机、减速箱、轴承等部分组成 主要作用是带动螺杆转动
感谢阅读
塑化
在挤出机内将固体塑料加热并依靠塑料之间的内摩擦热使其成为 粘流态熔体物料。
固体态聚合 物或混合物
熔融态聚合 物或混合物
成型
在挤出机螺杆的旋转推挤作用之下,通过具有一定形状的口模, 使粘流态的物料成为连续的型材。
1-转动机构;2-止推轴承;3-料斗;4-冷却系统; 5-加热器; 6- 螺杆;7-机筒;8-滤板;9-机头孔型
加热或引发剂
冷却 聚合
(3)物理化学变化兼有:热固性塑料、橡胶
- 1、下载文档前请自行甄别文档内容的完整性,平台不提供额外的编辑、内容补充、找答案等附加服务。
- 2、"仅部分预览"的文档,不可在线预览部分如存在完整性等问题,可反馈申请退款(可完整预览的文档不适用该条件!)。
- 3、如文档侵犯您的权益,请联系客服反馈,我们会尽快为您处理(人工客服工作时间:9:00-18:30)。
一、塑料管材的挤出
管材挤出装置由挤出机、机头口模、定型装置、冷却水槽、牵引及切割或卷取装置等组成,其中挤出机的机头口模和定型装置是管材挤出的关键部件。
(1)机头和口模机头是挤出管材的成型部件,大体上可分直通式、直角式和偏移式三种,其中用得最多的是直通式机头,图8一26所示的是直通式挤管机头,机头包括分流器、分流器支架、管芯、口模和调节螺钉等几个部分。
图8一26管材挤出工艺示意图
1-螺杆 2一机筒 3一多孔板 4一接口套 5一机头体 6一芯棒 7一调节螺钉
8一口模 9一定径套 10一冷却水槽 11一链子 12-塞子 13一牵引装置 14一夹紧装置
15-塑料管子
分流器又称鱼雷头,如图8一27所示。
薪流态塑料经过多孔板而到达分流器,塑料熔体逐渐形成环形,同时料层变薄,有利于塑料的进一步均匀塑化。
分流器与多孔板之间的空腔起着汇集料流的作用。
空腔的距离不宜过小,以防管材挤出不均匀,质量不稳定;距离太大则料流的停留时间太长,易发生塑料分解。
分流器支架的作用是支撑分流器及管芯。
在小型挤出机中,分流器和分流器支架为一个整体。
为支撑分流器,支架上有分料筋,塑料流过时被分料筋分开再汇合,有可能形成熔接痕,因此分料筋要制成流线型。
管芯(型芯)是挤出管材内表面的成型部件,随管子型样不同而有不同的形式,一般为流线型,以便砧流态塑料的流动。
薪流态塑料经过分流器支架后进人管芯与口模之间,管芯经过一定的收缩成为平直的流道。
图8一27分流器与管芯示意图
1一芯棒 2一分流器支架 3一分流器
在管材挤出过程中,机头压缩比表示豁流态塑料被压缩的程度。
机头压缩比是分流器支架出口处流道环形面积与口模及管芯之间的环形截面积之比。
压缩比太小不能保证挤出管材的密实,也不利于消除分料筋所造成的熔接痕;压缩比太大则料流阻力增加。
机头压缩比按塑料性质在3一10的范围内变化。
口模结构如图8一28所示。
口模的平直
部分与管芯的平直部分构成管子的成型部件,
这个部分的长短影响管材的质量。
增加平直部
分的长度,可增大料流阻力,既使管材致密,
又可使料流稳定,能够均匀挤出,消除螺杆旋
转给料流造成的影响,但如果平直部分过长,
则阻力过大,挤出的管材表面粗糙。
口模平直
部分的长度L,一般为内径d;的2-6倍,d,小
时,L,取大值,反之则相反。
管材的内外径应分别等于管芯的外径和
口模的内径,但实际上从口模出来的管材由于
牵引和冷却收缩等因素,其截面会缩小一些;另一方面,在管材离开口模后,压力降低,塑料因弹性恢复而膨胀。
因此挤出管子的收缩及膨胀的大小与塑料性质、离开口模前后的温度、压力及牵引速度等有关,管材最终的尺寸必须通过定径套冷却定型和牵引速度的调节而确定。
二、塑料薄膜的挤出成型
(2)机头和口模吹塑薄膜的主
要设备为单螺杆挤出机,其机头口模
的类型主要有转向式的直角型和水平
向的直通型两大类,结构与挤出管材
的差不多,作用是挤出管状坯料。
直
通型适用于熔体砧度较大和热敏性塑
料,工业上用直角型机头居多,由于
直角型机头有料流转向的问题,模具
设计时须考虑设法不使近于挤出机一
侧的料流速度大于另一侧,以减少薄
膜厚度波动。
为使薄膜的厚度波动在
卷取薄膜辊上得到均匀分布,常采用
直角型旋转机头,如图8一33。
口模
缝隙的宽度和平直部分的长度与薄膜
的厚度有一定的关系,如吹塑0.03一
0. 05mm厚的薄膜所用的模隙宽度为
0.4一0. 8mm,平直部分长度为7一
14mm
(3)吹胀与牵引在机头处有通人压缩空气的气道,通人气体使管坯吹胀成
膜管,调节压缩空气的通人量可以控制膜管的膨胀程度。
衡量管坯被吹胀的程度通常以吹胀比a来表示,吹胀比是管坯吹胀后的膜管直径Dz与挤出机环形口模直径D;的比值,吹胀比的大小表示挤出管坯直径的变化,也表明了黏流态下大分子受到横向拉伸作用力的大小。
常用的吹胀比在2
一6之间。
吹塑是一个连续成型过程,吹胀并冷却的膜管在上升卷绕途中,受到拉伸作用的程度通常以牵伸比R来表示,牵伸比是膜管通过夹辊时的速度v2与口模挤出管坯的速度v1之比。
这样,由于吹胀和牵伸的同时作用,使挤出的管坯在纵横两个方向都发生取向,使吹塑薄膜具有一定的机械强度。
因此,为了得到纵横向强度均等的薄膜,其吹胀比和牵伸比最好是相等的。
不过在实际生产中往往都是用同一环形间隙口模,靠调节不同的牵引速度来控制薄膜的厚度,故吹塑薄膜纵横向机械强度并不相同,一般都是纵向强度大于横向强度。
吹塑薄膜的厚度s与吹胀比和牵伸比的关系可用下式表示:
三、塑料板材挤出
塑料板材的生产常用挤出成型工艺,主要有两种方法,较老的方法是先挤出管子,随即将管子剖开,展平而牵引出板材,此法可用于软板生产。
这种方法除了因为加大管径有困难,从而限制板材的宽度外,还由于板材有内应力,在较高温度下趋向于恢复原来的圆筒形,板材容易翘曲,故目前较少应用。
目前,常用狭缝机头直接挤出板材(硬板或软板)。
挤板工艺也适用于片材和平膜的挤出。
图8一35为狭缝机头的板材挤出生产工艺流程图。
从图中可知,塑料经挤出机从狭缝机头挤出成板坯后,即经过三辊压光机、切边装置、牵引装置、切割装置等,最后得到塑料板材。
如果在压光机之后再装有加热、压波、定型等装置,则可得塑料瓦楞板。
狭缝机头的出料口既宽又薄,塑料熔体由料筒挤人机头,流道由圆形变成狭缝形,这种机头(包括支管型、衣架型、鱼尾型)在料流挤出过程中存在中间流程短、阻力小、流速快,两边流程长、阻力大、流速慢的现象,必须采取措施使熔
体沿口模宽度方向有均匀的速度分布,即能够使熔体在口模宽度方向上以相同的流速挤出,以保证挤出板材的厚度均匀和表面平整。
支管型机头结构见图8一36,这种机头的特点是在机头内有与模唇平行的圆筒形槽(支管),可以贮存一定量的物料,起分配物料作用,并使料流稳定。