铝合金铸造副车架开发
汽车底盘生产:乘用车副车架的应用与发展

根据 ( ( 中国齿轮行 业 “ 十二 五”发展规划 纲要》的 权威数 据 , 目前 ,我 国已成为世界第 三大齿轮 制造国 。
海 超 出浦东近 5 亿元 。而 前三 季度 ,这个 差距 被拉 大 。 这也恰 好 是去 年浦 东新 区GDP 超过 滨海 新 区的 数 字 。
以 齿轮 为代表 的基础零 部件是我 国装备制造业 的基础性
性。
图2 奇瑞汽车的后悬架副车架多连杆结构
1 . 控制 臂 2减振 器 3上控 制臂 4后 副车架 前下 . . . 5 下 控制 臂 6 臂 7横 向稳定 杆 . 后 . 纵 .
副车架诞生以后 ,前后悬挂可以先组装 在副车架上 ,构成一个车桥 总成 ,然后再将这 个总成装配到车身上 。悬挂部 件与副车架直接相连 ,相同的振 动通过副车架的缓冲 ,再传 递到车身时 ,振动会大幅度降低 ,从而提升整车的舒适性 。另外由于副车架的刚度比车身 更强 ,通过副车架的连接 ,大大提升 了悬挂连接刚度 ,不仅提升舒适性 ,而且在提升底盘
图1 、图2 为汽车前后悬架总成。
副车架的概念、作用及
原理
简单 地 说 , 副 车 架 是 前 后 车 桥 的骨架重 要组成 部分 。副车 架并
非 完 整 的 车 架 , 只 是 支承 前 后 车
桥 、 悬 架 的 支 架 , 车 桥 、 悬 挂 通 过
图1 凯迪拉克c S T 的前悬模块 ( 框形副车架) 使用
■ 奇 瑞 汽 车 股 份 有 限 公 司/ 宏 薛 友 领 王 田 田 杨 秋 芳 江
l童 ● ,
能
乘用车副车架 应用与发展
汽车的底盘性能无外乎舒适性、操控性两大性能, 而这两大性能又是一对相互制约的
铝副车架调研报告

铝副车架调研报告铝副车架调研报告一、调研背景随着人们对环境保护的重视和对汽车轻量化的追求,铝副车架作为一种新型材料在汽车行业中应用越来越广泛。
为了深入了解铝副车架的发展现状以及其在汽车行业中的应用前景,我们进行了一次调研。
二、调研方法我们采用了问卷调查和实地走访相结合的方式进行了调研。
在问卷调查中,我们向车企、零部件企业以及相关研究机构发放了调查问卷,了解他们对铝副车架的认知、应用情况以及面临的困难和挑战。
同时,我们还走访了几家汽车制造企业和铝副车架生产企业,深入了解他们的研发过程和应用情况。
三、调研结果1.对铝副车架的认知:大多数调研对象对铝副车架具有较高的认知度,认为铝副车架具有轻量化、耐腐蚀、高强度等优点。
2.应用情况:在调研的汽车企业中,约50%的企业已经将铝副车架应用于部分车型中,主要应用于高端车型和新能源汽车;约30%的企业计划将铝副车架在未来3年内应用到更多的车型中;约20%的企业暂时没有应用铝副车架的计划。
3.面临的困难和挑战:调研对象普遍反映,铝副车架的成本相对较高,且加工和焊接技术相对复杂;另外,铝副车架在抗碰撞等安全性能方面仍需进一步改进和优化。
四、调研结论1.铝副车架具有广阔的市场前景,特别是在高端车型和新能源汽车领域有较大的应用潜力。
2.降低成本和提升安全性能是铝副车架应用推广的关键。
未来需要加强研发,降低生产成本,加强技术创新,提高铝副车架的强度和安全性能。
3.政府可以通过出台相关政策,鼓励企业投入研发和生产,推动铝副车架的应用。
综上所述,铝副车架作为一种新型材料在汽车行业中具有广阔的发展前景,但在成本和安全性能方面仍面临一些挑战。
各方应共同努力,推动铝副车架的研发和应用,实现汽车轻量化和环保目标。
其中,政府、车企和零部件企业可以共同合作,加大投入力度,在技术创新和市场推广等方面进行积极探索。
高强度钢板,副车架和铝合金

所谓高强度钢,英文缩写AHSS,指的是屈服强度在500Mpa至1500Mpa的钢具有很好吸能性。
它是钢铁公司应对汽车轻量化的理想方案。
早在1995年,国际钢铁协会、美国钢铁协会等联合提出超前钢车身概念,采用高强度钢材所制造的车身实现更薄、更轻的结构,使车身重量降低,满足轻量化的需求跟钢铁相比,铝最有力的武器是质轻。
普通钢不言自明,即使是高强度钢也比不上。
关键汽车零部件使用高强度钢仅能减少10%的车重,而铝则能减少40%。
跟钢铁相比,铝最有力的武器是质轻。
普通钢不言自明,即使是高强度钢也比不上。
关键汽车零部件使用高强度钢仅能减少10%的车重,而铝则能减少40%。
此外,铝合金在遭遇撞击时的安全系数更高,因为其材质有非常好的吸能作用。
在引擎盖等部分应用铝合金可以减轻撞击对人身造成的二次伤害。
副车架可以看成是前后车桥的骨架,是前后车桥的组成部分。
副车架并非完整的车架,只是支承前后车桥、悬挂的支架,使车桥、悬挂通过它再与"正车架"相连,习惯上称为"副架"。
1.副车架能够带来很好的悬挂连接刚度。
2.能够隔绝路面震动,带来良好的舒适性。
副车架3.把悬挂变成总成部件,提高了悬挂的通用性,降低研发成本。
4.总成部件安装方便,降低了装配成本。
副架的作用是阻隔振动和噪声,减少其直接进入车厢,所以大多出现在豪华的轿车和越野车上,有些汽车还为引擎装上副架。
毫无疑问,若需要一个更“体面”的数值,只能使用“抗拉强度”作为指标。
但对于车辆实际的防护能力而言,屈服强度才是具有更重要意义的指标。
而且“最高强度钢板标号”只是一个极限值,哪怕Body in White(白车身)中只有一个零件使用了这样的钢板,也同样可以堂而皇之的作为“最高强度钢板”的数值出现,但实际意义却几乎可以忽略。
而“抗拉强度”指金属材料在拉断前承受最大应力值(符号:Rm),且在外力碰撞所导致的金属断裂中的首要衡量指标仍是“抗拉强度”。
铝合金低压铸造在汽车底盘应用中的应用
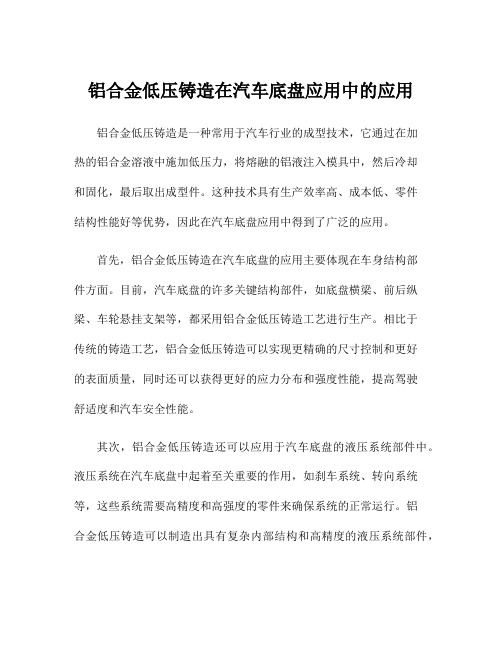
铝合金低压铸造在汽车底盘应用中的应用铝合金低压铸造是一种常用于汽车行业的成型技术,它通过在加热的铝合金溶液中施加低压力,将熔融的铝液注入模具中,然后冷却和固化,最后取出成型件。
这种技术具有生产效率高、成本低、零件结构性能好等优势,因此在汽车底盘应用中得到了广泛的应用。
首先,铝合金低压铸造在汽车底盘的应用主要体现在车身结构部件方面。
目前,汽车底盘的许多关键结构部件,如底盘横梁、前后纵梁、车轮悬挂支架等,都采用铝合金低压铸造工艺进行生产。
相比于传统的铸造工艺,铝合金低压铸造可以实现更精确的尺寸控制和更好的表面质量,同时还可以获得更好的应力分布和强度性能,提高驾驶舒适度和汽车安全性能。
其次,铝合金低压铸造还可以应用于汽车底盘的液压系统部件中。
液压系统在汽车底盘中起着至关重要的作用,如刹车系统、转向系统等,这些系统需要高精度和高强度的零件来确保系统的正常运行。
铝合金低压铸造可以制造出具有复杂内部结构和高精度的液压系统部件,如刹车泵、方向机壳体等,提高零件的性能和可靠性,同时减轻底盘的总重量,提高燃油经济性。
此外,铝合金低压铸造还可以应用于汽车底盘的传动系统部件中。
传动系统在汽车底盘中起着连接发动机和车轮的作用,如变速箱、减速器等,这些部件需要具有高强度、耐磨损和耐腐蚀等性能。
铝合金低压铸造可以制造出具有复杂形状和高强度的传动系统部件,如变速箱壳体、齿轮箱壳体等,提高传动系统的可靠性和性能,并减轻底盘的总重量,提高汽车的操控性和燃油经济性。
此外,铝合金低压铸造还可以应用于汽车底盘的散热系统部件中。
散热系统在汽车底盘中起着散热发动机和其他系统的热量的作用,如散热器、风扇壳体等,这些部件需要具有良好的散热性能和耐腐蚀性能。
铝合金低压铸造可以制造出具有复杂内部结构和高热传导性能的散热系统部件,如散热器壳体、风扇壳体等,提高散热系统的效率和可靠性,并减轻底盘的总重量,提高汽车的燃油经济性。
综上所述,铝合金低压铸造在汽车底盘应用中具有广泛的应用前景。
铝副车架调研报告

铝副车架调研报告铝副车架是一种非常轻量化、坚固耐用的车架材料,在汽车行业中得到了广泛应用。
为了解铝副车架的发展状况和未来发展趋势,我们进行了一系列调研工作。
首先,我们调研了市场上铝副车架的应用情况。
据了解,当前在汽车制造领域,许多车型已经开始采用铝副车架来替代传统的钢铁车架。
这主要是因为铝副车架相比钢铁车架更加轻量化,能够减轻车辆自重,提高燃油经济性和行驶性能。
同时,铝副车架的强度和刚度也非常高,能够有效保护车内乘员的安全。
因此,铝副车架在市场上具有广阔的应用前景。
其次,我们调研了铝副车架的制造工艺和技术水平。
目前,铝副车架主要采用铝合金材料制造,常见的有6xxx系列和7xxx系列铝合金。
制造过程中,需要先进行材料选择和成型设计,然后通过铸造、冷挤压和焊接等工艺进行加工。
随着制造工艺和技术水平的不断提高,铝副车架的制造成本得以降低,生产效率也得到了提升。
最后,我们调研了未来铝副车架的发展趋势。
随着环保意识的不断增强和汽车工业的高度竞争,铝副车架在未来将会有更广泛的应用。
预计在未来几年内,铝副车架在车辆重量减轻、能源消耗降低和碳排放减少等方面将发挥更重要的作用。
同时,随着材料科学和工艺技术的不断进步,铝副车架的强度和刚度将得到进一步提升,以满足不同车型和市场需求。
综上所述,铝副车架作为一种轻量化、坚固耐用的车架材料,其在汽车行业中具有广泛应用的前景。
随着制造工艺和技术水平的提升,以及市场需求的不断增长,铝副车架的发展前景十分乐观。
我们建议相关企业进一步加大研发投入,不断提升铝副车架的制造工艺和技术水平,以满足市场需求,并在未来发展中保持竞争优势。
高压铸造副车架特点

高压铸造副车架特点
高压铸造副车架是一种制造汽车零部件的工艺方法,它具有以下特点。
1. 高强度和耐久性:高压铸造副车架采用高压铸造技术,通过在高压下将液态金属注入模具中,使得副车架具有更高的密度和更均匀的结构。
这使得副车架具有高强度和耐久性,能够承受车辆在行驶过程中的各种力和振动。
2. 轻量化设计:相比传统的副车架制造方法,高压铸造副车架采用了轻量化设计,通过优化结构和减少材料的使用量,使得副车架的重量得到明显的减轻。
这不仅可以提高车辆的燃油经济性,还可以减少对环境的影响。
3. 高精度和一体化:高压铸造副车架采用先进的模具制造技术,能够实现高精度的生产。
通过一体化的设计和制造,可以减少零部件的数量和连接点,提高整体结构的强度和稳定性。
4. 良好的表面质量:高压铸造副车架的表面质量非常好,无需进行额外的表面处理。
这不仅可以减少生产工艺和成本,还可以提高车辆的外观质量和整体品质。
5. 生产效率高:高压铸造副车架采用自动化生产线,具有高度的生产效率和稳定性。
相比传统的副车架制造方法,高压铸造副车架的生产效率可以提高数倍,大大缩短了生产周期,降低了生产成本。
高压铸造副车架具有高强度、耐久性好、轻量化设计、高精度和一体化、良好的表面质量以及高生产效率等特点。
它的出现,不仅提高了汽车的性能和安全性,也促进了汽车工业的发展和进步。
汽车用铝合金副车架成形工艺及应用现状
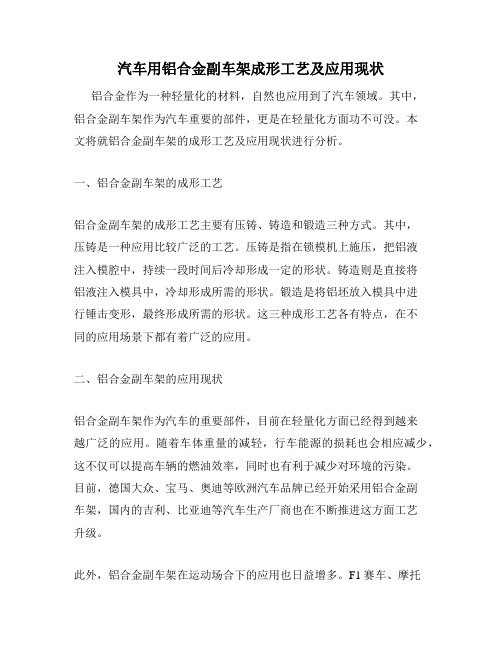
汽车用铝合金副车架成形工艺及应用现状铝合金作为一种轻量化的材料,自然也应用到了汽车领域。
其中,
铝合金副车架作为汽车重要的部件,更是在轻量化方面功不可没。
本
文将就铝合金副车架的成形工艺及应用现状进行分析。
一、铝合金副车架的成形工艺
铝合金副车架的成形工艺主要有压铸、铸造和锻造三种方式。
其中,
压铸是一种应用比较广泛的工艺。
压铸是指在锁模机上施压,把铝液
注入模腔中,持续一段时间后冷却形成一定的形状。
铸造则是直接将
铝液注入模具中,冷却形成所需的形状。
锻造是将铝坯放入模具中进
行锤击变形,最终形成所需的形状。
这三种成形工艺各有特点,在不
同的应用场景下都有着广泛的应用。
二、铝合金副车架的应用现状
铝合金副车架作为汽车的重要部件,目前在轻量化方面已经得到越来
越广泛的应用。
随着车体重量的减轻,行车能源的损耗也会相应减少,这不仅可以提高车辆的燃油效率,同时也有利于减少对环境的污染。
目前,德国大众、宝马、奥迪等欧洲汽车品牌已经开始采用铝合金副
车架,国内的吉利、比亚迪等汽车生产厂商也在不断推进这方面工艺
升级。
此外,铝合金副车架在运动场合下的应用也日益增多。
F1赛车、摩托
车等运动车辆都采用铝合金副车架,这有利于提高运动车辆的速度和灵活性,同时也更加安全。
对于普通消费者而言,铝合金副车架的应用也将使车辆更加安全可靠。
总的来说,铝合金副车架作为汽车轻量化的关键部件,在未来的发展中将越来越广泛地受到重视和应用。
铝合金副车架的成形技术也将不断地进步和完善,更好地满足人们对轻量化汽车的需求。
汽车前副车架轻量化设计

摘要: 对原前副车架结构和材料进行优化设计, 可以达到轻量化的效果。 将前副车架的钢材替换为铝合金材料 ZL114A, 并利
用 CATIA 三维建模软件对前副车架结构进行优化设计。 经优化, 前副车架质量由 17 kg 减少至 11 76 kg, 减重比例达 30 8%, 满
足设计要求。 使用 Nastran 软件对优化后的前副车架进行有限元分析, 结果表明新结构满足各种汽车行驶工况下的强度、 模态以及
刚度性能要求, 因此该轻量化设计方案可行, 在不影响前副车架正常使用的情况下减轻质量。
关键词: 前副车架; 轻量化; 结构优化; 有限元
中图分类号: U463 32
Lightweight Design for Front Subframe
SUN Zhiyuan , CHEN Yongzhong , PENG Hao1 , ZHAO Chaochen1 , LIU Yunbo1 , JI Longhui2 , CAI Cong2 , WU Jinglai1
subframe. After optimization, the weight of front subframe is reduced from 17 kg to 11 76 kg, the weight reduction ratio achieves 30 8%,
which satisfies the design requirement. Nastran software was used to analyze the new structure of frond frame. The results demonstrate that the
有良好的静态特性。
原前副车架如图 1 所示, 若只将前副车架的材料由钢替换
- 1、下载文档前请自行甄别文档内容的完整性,平台不提供额外的编辑、内容补充、找答案等附加服务。
- 2、"仅部分预览"的文档,不可在线预览部分如存在完整性等问题,可反馈申请退款(可完整预览的文档不适用该条件!)。
- 3、如文档侵犯您的权益,请联系客服反馈,我们会尽快为您处理(人工客服工作时间:9:00-18:30)。
挤 压 铸 造 工 艺 液 态 金 属 在 压 力 下 凝 固 结 晶 ,晶 体 组 织 致 密 ,铸 造 毛 坯 力 学 性 能 好 ,且 可 以 进 行 后 期 热处理,进一步提升力学性能指标。
综 合 考 虑 以 上 铸 造 工 艺 的 优 缺 点 ,确 认 采 用 挤 压铸造工艺方式实现副车架的开发。 1.2 材料分析
2 左轮 侧向载荷
-1
-330
-20
3 轮心 垂直载荷
1
4
制动载荷 1
-330
5
向后载荷 1
6 右轮 侧向载荷
1
330
20
7 轮心 垂直载荷
1
8
制动载荷 1
-330
疲 劳 损 伤 计 算 采 用 Palmgren-Miner 线 性 累 积 损
伤计算方法:
∑ ∑ D =
ni Ni
<1
(2)
受垂向和侧向载荷的能力。 通 过 多 次 CAD 修 改 与 强 度 校 核 ,副 车 架 顺 利 通
高 压 铸 造 工 艺 液 态 金 属 在 压 力 下 凝 固 结 晶 ,晶
-58-
体 组 织 致 密 ,铸 造 毛 坯 力 学 性 能 好 。 但 目 前 国 内 高 真 空 压 铸 工 艺 发 展 尚 未 成 熟 ,基 本 均 为 普 通 压 铸 ,而 对 于 副 车 架 等 较 复 杂 结 构 件 来 说 ,容 易 产 生 卷 气 现 象 ,导 致 延 伸 率 较 低 ,且 无 法 进 行 热 处 理 ,力 学 性 能 得不到进一步提升。
架 试 验 各 通 道 单 位 载 荷 的 方 法 [3] ,各 通 道 单 位 载 荷 见
表 1,在此基础上进行多轴疲劳分析预测结构寿命,
目标为 500 个循环。
表 1 载荷谱通道单位载荷
通道
载荷 位置
载荷名称
Fx /kN
Fy /kN
Fz /kN
Mx /N·m
1
向后载荷 1
My /N·m
Mz /N·m
稳定杆、转向机及动力总成悬置上。通过 ADAMS 软 件 将 各 工 况 的 轮 心 受 力 分 解 到 副 车 架 各 安 装 点 ,得 到各安装点的载荷,在此基础上进行强度分析。
整车极限行驶工况: a. 垂 直 冲 击 工 况 ,考 核 实 车 承 受 垂 向 载 荷 的 能力; b. 紧急转弯工况,考核实车同时承受垂向和侧 向载荷的能力; c. 最大加速工况,考核实车同时承受纵向和侧 向载荷的能力; d. 最大制动工况,考核实车同时承受纵向和侧 向载荷的能力; e. 路缘冲击工况,误用工况,考核实车同时承
过 静 强 度 分 析 ,各 工 况 结 构 应 力 小 于 所 选 材 料 力 学 性能指标,图 5 为静强度分析的应力分布图。
主题词:副车架 铝合金 挤压铸造 开发 中图分类号:U463.32 文献标识码:A 文章编号:1000-3703(2015)02-0058-05
Development of Aluminum Alloy Casting Sub-frame
Chen Lei1, Cheng Wenzheng1, Sun Jue2, Wang Shiwei1, Chen Zhigang1, Hou Jie1 (1.China FAW Co., Ltd R&D Center; 2. Suzhou Sanji Foundry Equipment Co., Ltd) 【Abstract】The substitution of traditional steel with aluminum alloy is an effective approach of lightweight design of passenger car chassis structural parts, especially in high-end passenger car. This article introduces the development process of aluminum alloy sub-frame. The development practice shows that, with the application of aluminum alloy and extrusion casting technology, with the aid of rational design of structure and systemic development of technology, the strict requirements on strength and durability of chassis structural component can be satisfied, and the lightweight level of vehicle is improved.
σ=
Mz·y Iz
(1)
根 据 弯 曲 正 应 力 计 算 公 式(1)[1],在 使 用 材 料 相
等 的 情 况 下 ,截 面 惯 性 矩 越 大 ,同 样 弯 矩 下 的 应 力 越
小。而副车架对弯曲方向的高刚度要求决定了必须
选择截面惯性距较大的截面形状,“U”型、“工”字型、
“ 口 ”字 型 为 首 选 ,截 面 惯 性 矩 的 大 小 关 系 为“ 口 ”字
-59-
·中国汽车工程学会悬架技术分会 2014 年度学术年会优秀论文选登·
品结构进行 CAD 详细设计,得到最终产品 CAD 模型
2.7 耐久性分析
如图 4 所示。
在项目开发初期,通过搭建 mule-car 形式采集用
户使用工况的路谱。测试路况涵盖中国各地典型路
况特征,包含高速、城郊结合、一般公路、山区、城市、
Key words:Sub-frame, Aluminum alloy, Extrusion casting, Development
对 于 副 车 架 、控 制 臂 、转 向 节 等 底 盘 重 要 结 构 件 的 轻 量 化 设 计 来 说 ,铝 合 金 材 料 的 选 用 是 大 势 所 趋 。 介 绍 了 铸 铝 工 艺 副 车 架 的 设 计 开 发 过 程 ,对 工 艺 及 材 料 选 择 、结 构 设 计 、工 艺 开 发 、试 验 验 证 等 方 面 进 行 了 阐 述 ,最 终 开 发 出 了 满 足 副 车 架 基 础 功 能 及轻量化要求的产品。
不平整路等。结合整车试验场强化坏路测试载荷
谱 ,通 过 载 荷 谱 关 联 ,获 得 了 与 用 户 使 用 环 境 相 当 的
CAE 耐久分析及台架耐久试验载荷谱。由于副车架
受 力 点 较 多 ,本 文 采 用 系 统 模 型 直 接 在 轮 心 施 加 台
图 4 最终产品 CAD 模型
2.6 静强度分析 副车架主要施力零件装配在副车架的控制臂、
产品结构的拓扑优化模型。
能差,适用于生产结构简单、承载较大部件;
通 过 结 构 设 计 优 化 ,“ T ”型 、“ L ”型 、“ U ”型 、“ 工 ”
铝 镁 系 合 金 ,力 学 性 能 高 ,机 械 加 工 性 能 好 ,但
字型、“口”字型、“十”字型等大多数常见铸件截面结
铸造性能较差;
构,都可以满足强度及刚度要求。
1 铸造工艺及材料确定
1.1 铸造工艺 对 标 国 内 、外 现 有 车 型 铸 铝 工 艺 副 车 架 铸 造 工
艺,主要有重力铸造(含倾转型重力铸造)、高压铸造 (含高真空压力铸造)及挤压铸造等。
重 力 铸 造 工 艺 晶 体 组 织 不 够 致 密 ,且 容 易 产 生 热节缺陷,但可通过后期热处理提升力学性能指标。
平均 10 mm;加强筋壁厚 5~10 mm;拔模斜度 0.5°~2°; 铸造圆角 R2~R3。 2.4 拓扑优化
参考文献[2],采用的优化方法如下。 加 载 条 件 :整 车 极 限 行 驶 工 况(与 后 期 静 强 度 分 析工况相同); 优化目标:工况加权应变能最小; 约束条件:模型质量(体积比); 优 化 控 制 :截 面 形 状 、主 要 铸 造 工 艺 参 数 要 求 、 左右对称等。
按 合 金 元 素 分 类 ,铸 造 铝 合 金 材 料 主 要 分 为 以下 4 类:
铝 硅 系 合 金 ,流 动 性 好 、铸 造 性 能 好 及 气 密 性 好 ,适 用 于 生 产 复 杂 结 构 件 ,通 过 添 加 镁 、铜 等 合 金
汽车技术
·中国汽车工程学会悬架技术分会 2014 年度学术年会优秀论文选登·
型>“U”型>“工”字型。
“ 口 ”字 型 为 空 腔 结 构 ,需 要 通 过 增 加 砂 芯 实 现 ,
铸 造 工 艺 难 度 大 ,且 成 本 高 ,而“ U ”型 和“ 工 ”字 型 截
面铸造工艺实现容易。
综上所述,最终决定选择“U”型截面作为优化设
计方向。
空间 布置包络
拓扑优化
初版产品 CAD
ห้องสมุดไป่ตู้
副车架优化结果如图 3 所示。
图 2 布置空间包络
2.2 截面形状 确 定 副 车 架 的 布 置 空 间 包 络 后 ,需 要 确 定 组 成
2015 年 第 2 期