三氯氢硅合成的探讨
试说明三氯氢硅的合成原理

试说明三氯氢硅的合成原理
三氯氢硅的合成原理如下:
1. 制备原料:将硅粉和氯化氢进行反应,制备出三氯化硅。
Si + 3HCl →SiCl3 + H2
2. 氯化氢和硅源反应:将三氯化硅和氢气进行反应,在高温下制备出三氯氢硅。
SiCl3 + H2 →H3SiCl
3. 精制和稳定化处理:三氯氢硅经过精制和稳定化处理后,即可成为工业上所使用的三氯氢硅。
三氯氢硅的合成原理,主要就是通过氯化氢和硅源的反应,制备出三氯化硅,再经过氢气还原后得到三氯氢硅。
整个反应过程需要在高温下进行,并需要精制和稳定化处理,以保证制备出的三氯氢硅的纯度和质量。
SiHCl3合成041114

三氯氢硅合成)的合成,是生产多晶硅的重要环节之一。
包括液氯汽三氯氢硅(SiHCl3合成等工序。
辅助设施有湿法除尘釜液回收装置(6级精化、HCl合成、SiHCl3合成炉,的工作效能直接影响馏塔)、硅粉洗涤回收装置。
其核心设备SiHCl3整个合成车间的经济指标,应作重点了解。
本章按工序顺序介绍所用原材料的性质和制备原理及工艺。
(一)液氯汽化1.氯气的性质氯气分子量为71,熔点-101.6℃,沸点-34.6℃,常温常压下呈黄绿色气体,气体密度3.21克/升。
氯气在空气中不燃烧,但有助燃性。
在日光下与易燃气体混合时会发生燃烧甚至爆炸。
氯气对空气的相对密度为2.45,比空气重,泄漏的氯气常常滞留在地面。
液氯/氯气为剧毒物质,氯气在空气中的最大允许浓度为1mg/m3。
其职业性接触毒物危害程度等级为Ⅱ级,属高度危害,能严重刺激皮肤、眼睛、粘膜;高浓度时,有窒息作用;可引起喉肌痉挛、粘膜肿胀、恶心、呕吐、焦虑和急性呼吸道疾病,如咳嗽、咯血、胸痛、呼吸困难、支气管炎、肺水肿、肺炎等;氯气还能刺激鼻、口、喉,随浓度升高引起咳嗽直至引发喉肌痉挛而导致死亡。
人吸入氯气最低致死浓度为LCLo:2530mg/m3/30min或500ppm/5min。
与氢气的反应氯气与氢气的反应异常激烈,在光照或加热情况下二者迅速反应合成HCl,并放出大量的热(Q):H2+Cl2=2HCl+Q氢气和氯气在稳定燃烧时,会发出苍白色火焰。
但在较低温度和无光照情况下,二者的反应速度缓慢。
因此,当氢气和氯气发生混合后应注意降温、避光和卸压,并送入大量的氮气稀释,产生的尾气通入碱洗设备处理。
与水的反应氯气与水反应的产物是盐酸和次氯酸: Cl 2+H 2O =HCl+HClO氯气与水的反应是可逆反应,当水中H +含量偏高时,可认为氯气解溶解于水中,加热会逸出。
次氯酸是强氧化剂和杀菌剂。
自来水厂的杀菌工序就是向水中通入少量氯气,生成次氯酸进行杀菌和除臭。
三氯氢硅合成原理

三氯氢硅合成原理三氯氢硅合成系统包括:1,硅粉加料装置,2,三氯氢硅合成炉,3,旋风干法除尘,4,过滤装置,5,STC湿法除尘,6,合成气分离回收(CDI)等工序。
硅粉加料装置完成向合成炉连续定量地供应硅粉;三氯氢硅合成炉是生产三氯氢硅的关键设备;旋风干法除尘、过滤装置与STC湿法除尘是回收硅粉和除去合成气的硅尘,CDI是将合成气进行分离回收,它们都是不可或缺的设备。
合成三氯氢硅的原料是硅粉与HCL气体。
3.1. 原料工业硅简介工业硅的外观为深灰色与生铁颜色接近,也称硅铁。
工业硅的块密度约2.0×103kg/m3,硬度为7,纯度一般为95%~99%,其中的主要杂质为Fe、Al、Ca。
工业硅的制备一般采用冶炼法,在冶炼炉中用还原剂将SiO2还原成单质硅(冶金硅)。
通常用的还原剂有碳、镁、铝等。
用镁或铝还原SiO2,如果还原剂的纯度较高得到的单质硅纯度可达3~4个“9”。
不过,由于纯度较高的镁、铝价格高,会增加工业硅的生产成本,因此,目前国内的生产厂家都采用在电炉中用焦炭还原SiO2来制取单质硅(冶金硅),即把碳电极插入由焦炭(或木炭)和石英石组成的炉料中,温度控制在1600℃~1800℃还原出硅,反应式如下:石英砂(硅石)与炭在电弧炉里还原成硅(MG-Si)反应是在电弧炉(见图二)里的相邻电极之间发生的,该处温度超过2000℃,释放出来的SiO 和CO流到上部较冷区域(小于1500℃),形成所必要的SiC。
还原后的单质硅是以液态从反应炉中流进硅液煲,在这一过程中如Fe、Al、Ca、B、P、Cu等杂质也会以不同化合态进入液态的单质硅中,为了保证产品符合要求(一般控制在99%以上),硅液需要经过进一步处理去除其中的杂质。
处理方法是利用杂质的化合态(氯化物或氧化物、硅酸盐等)在液体状态时会逐步离析到液体表面的规律,通过除去表层硅液来达到去除杂质的目的。
因此,工业硅厂大都采用在硅液保温槽中通入Cl2或O2,促使大部分Fe、Al、Ca等杂质生成氯化盐或硅酸盐等物质,定期清除表层。
三氯氢硅合成的热力学

( . Fa u t f M e a l g c l n e g g n e i g,Ku m i g Un v r iy o i n e a d Te h o o y,Ku mi g 6 0 9 1 c ly o t l ur ia d En r y En i e rn a n n i e st fSce c n c n l g n n 5 0 3,Ch n ia
三 氯 氢 硅 合 成 的 热 力 学
彭如 振 俞 小花 , 刚 , 云 , 谢 姚
(.昆 明理 工 大 学 冶金 与 能源 工 程 学 院 , 1 昆明 609 ;.云 南 冶金 集 团股 份 有 限公 司技 术 中心 , 5 032 昆明 603) 50 1
摘 要 : 用 Icsg 应 at e软 件 研 究 三 氯 氢 硅 合 成 的 复 杂 化 学 反 应 , 制 了 体 系 中存 在 的 8个 化 学 反 应 的 a 绘
a d HC1S lrr t r ic se . Th e u t h w h ta Iwe e e a u e ,a hg e r s u e n /i moa a i we ed s u s d o e r s lss o t a o rtmp r t r s i h rp e s r s
ห้องสมุดไป่ตู้
mod a i o t r a t a .Digr ms o o he eghtc mia e ton n t ss s e v r us t mpe a yn m c s fwa e f c s ge a a f f r t i he c lr aci s i hi y t m e s e r— t e we e p ote . W h n t e c i e c e q lb i m ,t e a i ns p be we n g s p s o ur r l t d e he r a ton r a h d e uii r u he r lto hi t e a ha ec mpo ii ns sto
三氯氢硅合成原理

三氯氢硅合成原理三氯氢硅合成系统包括:1,硅粉加料装置,2,三氯氢硅合成炉,3,旋风干法除尘,4,过滤装置,5,stc湿法除尘,6,合成气分离回收(cdi)等工序。
硅粉加料装置完成向合成炉连续定量地供应硅粉;三氯氢硅合成炉是生产三氯氢硅的关键设备;旋风干法除尘、过滤装置与stc湿法除尘是回收硅粉和除去合成气的硅尘,cdi是将合成气进行分离回收,它们都是不可或缺的设备。
制备三氯氢硅的原料就是硅粉与hcl气体。
3.1.原料工业硅概述工业硅的外观为深灰色与生铁颜色接近,也称硅铁。
工业硅的块密度约2.0×103kg/m3,硬度为7,纯度一般为95%~99%,其中的主要杂质为fe、al、ca。
工业硅的制取通常使用炼钢法,在冶炼炉中用还原剂将sio2转换成单质硅(冶金硅)。
通常用的还原剂存有碳、镁、铝等。
用镁或铝还原成sio2,如果还原剂的纯度较低获得的单质硅纯度仅约3~4个“9”。
不过,由于纯度较低的镁、铝价格低,可以减少工业硅的生产成本,因此,目前国内的生产厂家都使用在电炉中用焦炭还原成sio2去制备单质硅(冶金硅),即为把碳电极填入由焦炭(或木炭)和石英石共同组成的炉料中,温度控制在1600℃~1800℃还原成出来硅,反应式如下:石英砂(硅石)与炭在电弧炉里还原成硅(mg-si)反应就是在电弧炉(见到图二)里的相连电极之间出现的,该处温度少于2000℃,转化成的sio和co流进上部较冷区域(大于1500℃),构成所必要的sic。
还原后的单质硅是以液态从反应炉中流进硅液煲,在这一过程中如fe、al、ca、b、p、cu等杂质也会以不同化合态进入液态的单质硅中,为了保证产品符合要求(一般控制在99%以上),硅液需要经过进一步处理去除其中的杂质。
处理方法是利用杂质的化合态(氯化物或氧化物、硅酸盐等)在液体状态时会逐步离析到液体表面的规律,通过除去表层硅液来达到去除杂质的目的。
因此,工业硅厂大都采用在硅液保温槽中通入cl2或o2,促使大部分fe、al、ca等杂质生成氯化盐或硅酸盐等物质,定期清除表层。
低压合成法制备三氯氢硅工艺概述
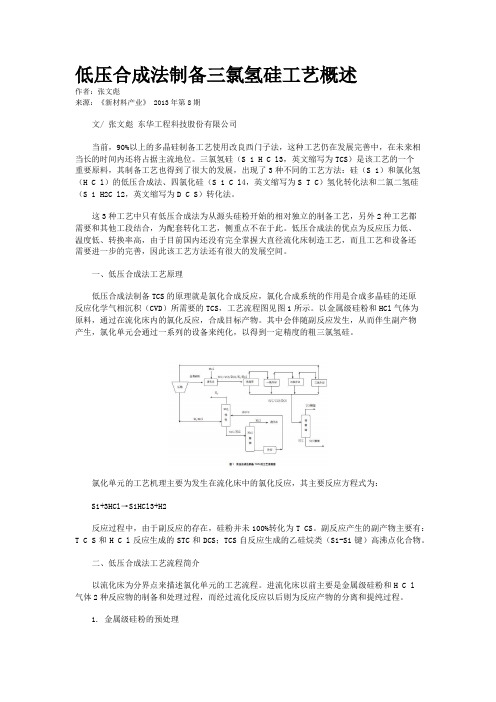
低压合成法制备三氯氢硅工艺概述作者:张文彪来源:《新材料产业》 2013年第8期文/ 张文彪东华工程科技股份有限公司当前,90%以上的多晶硅制备工艺使用改良西门子法,这种工艺仍在发展完善中,在未来相当长的时间内还将占据主流地位。
三氯氢硅(S i H C l3,英文缩写为TCS)是该工艺的一个重要原料,其制备工艺也得到了很大的发展,出现了3种不同的工艺方法:硅(S i)和氯化氢(H C l)的低压合成法、四氯化硅(S i C l4,英文缩写为S T C)氢化转化法和二氯二氢硅(S i H2C l2,英文缩写为D C S)转化法。
这3种工艺中只有低压合成法为从源头硅粉开始的相对独立的制备工艺,另外2种工艺都需要和其他工段结合,为配套转化工艺,侧重点不在于此。
低压合成法的优点为反应压力低、温度低、转换率高,由于目前国内还没有完全掌握大直径流化床制造工艺,而且工艺和设备还需要进一步的完善,因此该工艺方法还有很大的发展空间。
一、低压合成法工艺原理低压合成法制备TCS的原理就是氯化合成反应,氯化合成系统的作用是合成多晶硅的还原反应化学气相沉积(CVD)所需要的TCS,工艺流程图见图1所示。
以金属级硅粉和HCl气体为原料,通过在流化床内的氯化反应,合成目标产物。
其中会伴随副反应发生,从而伴生副产物产生,氯化单元会通过一系列的设备来纯化,以得到一定精度的粗三氯氢硅。
氯化单元的工艺机理主要为发生在流化床中的氯化反应,其主要反应方程式为:Si+3HCl→SiHCl3+H2反应过程中,由于副反应的存在,硅粉并未100%转化为T CS。
副反应产生的副产物主要有:T C S和H C l反应生成的STC和DCS;TCS自反应生成的乙硅烷类(Si-Si键)高沸点化合物。
二、低压合成法工艺流程简介以流化床为分界点来描述氯化单元的工艺流程。
进流化床以前主要是金属级硅粉和H C l气体2种反应物的制备和处理过程,而经过流化反应以后则为反应产物的分离和提纯过程。
三氯氢硅合成工艺简述
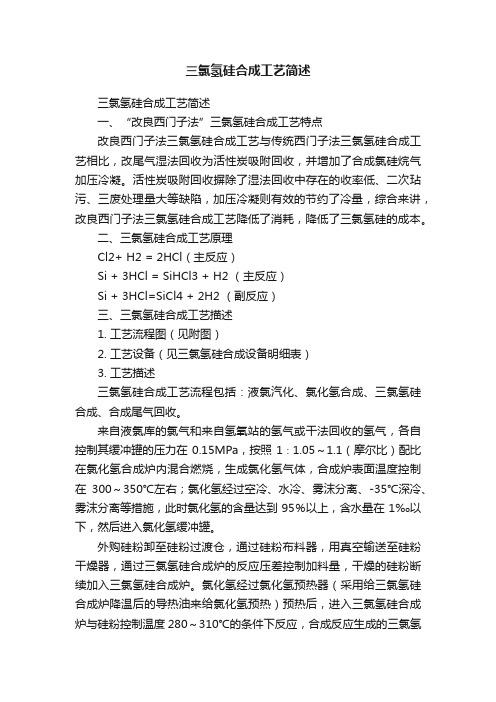
三氯氢硅合成工艺简述三氯氢硅合成工艺简述一、“改良西门子法”三氯氢硅合成工艺特点改良西门子法三氯氢硅合成工艺与传统西门子法三氯氢硅合成工艺相比,改尾气湿法回收为活性炭吸附回收,并增加了合成氯硅烷气加压冷凝。
活性炭吸附回收摒除了湿法回收中存在的收率低、二次玷污、三废处理量大等缺陷,加压冷凝则有效的节约了冷量,综合来讲,改良西门子法三氯氢硅合成工艺降低了消耗,降低了三氯氢硅的成本。
二、三氯氢硅合成工艺原理Cl2+ H2 = 2HCl(主反应)Si + 3HCl = SiHCl3 + H2 (主反应)Si + 3HCl=SiCl4 + 2H2 (副反应)三、三氯氢硅合成工艺描述1. 工艺流程图(见附图)2. 工艺设备(见三氯氢硅合成设备明细表)3. 工艺描述三氯氢硅合成工艺流程包括:液氯汽化、氯化氢合成、三氯氢硅合成、合成尾气回收。
来自液氯库的氯气和来自氢氧站的氢气或干法回收的氢气,各自控制其缓冲罐的压力在0.15MPa,按照1∶1.05~1.1(摩尔比)配比在氯化氢合成炉内混合燃烧,生成氯化氢气体,合成炉表面温度控制在300~350℃左右;氯化氢经过空冷、水冷、雾沫分离、-35℃深冷、雾沫分离等措施,此时氯化氢的含量达到95%以上,含水量在1‰以下,然后进入氯化氢缓冲罐。
外购硅粉卸至硅粉过渡仓,通过硅粉布料器,用真空输送至硅粉干燥器,通过三氯氢硅合成炉的反应压差控制加料量,干燥的硅粉断续加入三氯氢硅合成炉。
氯化氢经过氯化氢预热器(采用给三氯氢硅合成炉降温后的导热油来给氯化氢预热)预热后,进入三氯氢硅合成炉与硅粉控制温度280~310℃的条件下反应,合成反应生成的三氯氢硅、四氯化硅、氢气与未完全反应的氯化氢混合气体经漩涡分离器、袋式过滤器,除去粉尘(进废碴淋洗塔)和高氯硅烷,经沉积器、压缩前水冷、压缩前-5℃冷、压缩前-35℃深冷,冷凝下来的氯硅烷通过压缩前合成产品计量罐进入压缩前合成产品贮罐;未冷凝的气体经过活塞压缩机加压,再经过压缩后水冷、压缩后-5℃冷,冷凝下来的氯硅烷通过压缩后合成产品计量罐进入压缩后合成产品贮罐;少量的未凝气体三氯氢硅、四氯化硅和不凝气体氢气、氯化氢,通过管道进入三氯氢硅合成尾气回收系统。
多晶硅工艺-三氯氢硅

多晶硅工艺-三氯氢硅首先是原料制备,多晶硅生产过程中需要使用高纯度的多晶硅原料,一般采用金属硅、硅冶炼废料等制备。
这些原料需要经过破碎、磨粉等步骤,得到粒度合适的原料粉末。
氯硅烷气相法是多晶硅制备的核心步骤。
在该工艺中,三氯氢硅是最常用的反应物之一、其化学式为SiHCl3、氯硅烷气相法是通过将三氯氢硅及氧化剂(如氢氧化钠)加热反应,得到硅及氯化氢气体。
反应过程可用化学反应方程式表示如下:SiHCl3+2NaOH->SiO2+2NaCl+2H2O反应中,三氯氢硅与氢氧化钠反应生成二氧化硅、氯化钠和水。
这一步骤中的反应条件和控制对于多晶硅质量的提高非常关键,需要控制反应温度、催化剂的使用量、气体流量等参数。
多晶硅生长是接下来的重要步骤。
通过将氯硅烷气和氢气混合,进入炉中进行化学气相沉积(Chemical Vapor Deposition, CVD)或者物理气相沉积(Physical Vapor Deposition, PVD)的方式,让硅原子沉积在衬底上,逐渐生长成大型的多晶硅晶体。
多晶硅生长过程中,需要控制温度、气氛、沉积速度等参数,以保证多晶硅晶体的质量和纯度,同时还需要控制晶体的取向和尺寸。
多晶硅生长完成后,还需要进行多晶硅切割。
切割过程中,使用钻石线锯或者钻石盘等工具,将多晶硅晶体切割成适合太阳能电池制造的大小和形状。
切割过程需要注意防止晶体的破损和浪费。
最后,将切割后的多晶硅晶体用于太阳能电池的制造。
太阳能电池制造过程中,将多晶硅片片安装、清洗、镀膜等步骤,最终制造成太阳能电池。
总结一下,多晶硅工艺中的三氯氢硅起着重要的作用,用于多晶硅的原料制备和气相生长。
三氯氢硅在氯硅烷气相法中被加热与氧化剂反应,得到硅原料。
多晶硅生长过程中,需要控制多个参数以保证多晶硅质量,切割后可用于太阳能电池的制造。
多晶硅是太阳能电池制造中的关键材料,多晶硅工艺中的三氯氢硅是其生产过程中的重要一环。
深入了解三氯氢硅的工艺流程和相关知识,能够更好地掌握多晶硅工艺并提高产品质量。
- 1、下载文档前请自行甄别文档内容的完整性,平台不提供额外的编辑、内容补充、找答案等附加服务。
- 2、"仅部分预览"的文档,不可在线预览部分如存在完整性等问题,可反馈申请退款(可完整预览的文档不适用该条件!)。
- 3、如文档侵犯您的权益,请联系客服反馈,我们会尽快为您处理(人工客服工作时间:9:00-18:30)。
3反 应温度 I 1 对S C 合成的 H3 影响
从S C 合成的反应原理可知, i I H , 硅粉和H I C反应是很复杂的, 生成S C, 还产生 S IS 21 除了 i I H 外, ' 4 i C2 C , H 等各种抓硅烷等副产物。 iC, S I H 合成反 应是放热反应, 反应温度对 S C, iI H 合成的影响较大。 温度过低, 则反应缓慢;温度过高 ( 大于 40 ) 5' ,则反应产品中 S C 含量降 C 'I H3 低, i。 Sl c 含量增 ‘2 从分子结构 加11 [ , 也可看出, ii S 。 c 具有高度的对称性,硅原子与抓原子是以 共价键结合。生产时反应温度高达 6 0 0 ℃以上, 也不会引 起热分解。 iC, S I H 的分子结构是不 对称的, 硅原子与氢原子 近于离子键,不稳定11 由 iC [2 于S I [ H, 的热稳定性较差,在 40 0℃开始分解, 5℃剧烈分解,因此在生产过程中选择适当的反应温度。并将反应 50
水后,使H I C 中水含量控制在0 % 后,再进沸腾炉进行反应,这样才能保证冷凝料中S C, . 以内 1 i I H 含量在 8% 5 左右1 H I ' C水含量对S C, 1 . i I H 收率的影响见图21 1 1 .
圈2 C含水率对S C, H I i I H 收率的影晌
A7 液中S C 含t -彼 ? iIi H,
( 反应条件 硅粉 2-0 0 公斤)
Q - 系H I 1 0 C 流盘为 1米21 情况下作的曲 0 、 时的 线其余依次类推
( 奴 )1 率 .1。 =访 告 吸恢
。 1 2 3 4 5 . , 8 ,
放出的热及时的传出,以保证炉内反应温度稳定,是9
应温度, 在生产中进行过多次试验,试验结论认为: 温度控制在 2030 较合适。 8-2℃ 试验过程中, 反应放 出的热通过温水、热导油或低压蒸汽带走.在实际生产过程中,通过调节温水水套出水阀, 控制沸腾炉 冷却水套进水调节阀,使沸腾炉恒温在 2030 8-2℃之间[ 3 1沸腾炉内的反 应温度与合成产物中S C 含量 i I H 3
等 个 面 ' I 成的 进行了 讨. 响 几 方 对S C 合 形 H, 探
关 词 三氢 合 叭 探 键 组硅 良
I 概述
目 外生产多晶 前,国内 硅最广、 最主要的 方法是西门子法,西门子法生产多晶硅是以 S C 为原料, i I H , 所以 S C, i I H 合成的产率和 S C, i I H 质量对多晶 硅产I、 质量和成本有着直接的 影响。 至此,S C, i I H 的合成 在国内外多晶硅生产厂家中被引起了广泛的关注, 各生 厂家对 S C 的合 产 i l 成进行了 方面的 H, 多 研究, 并
4 氧和水份对S C3 i i H 合成的影响
三氛氮硅合成的探讨—
汤传斌
SC%f ) i , t H ( 加
90 肋 叩 6D 加 胡 加 即 10
尸 } 厂二... ̄ 一 厂 一} 盯 「 } 一一 盯一 厂一 「下 一 厂下 巨二
} I 一 I
} 一
{
} }
} 一
Hale Waihona Puke 「  ̄, 一 .  ̄第八届全国 铅锌冶金生产技术 及产品 应用学术年会论文集
三氯氢硅合成的探讨
北京有色冶金设计研究总院 汤传斌
摘 要 本 阐 了 i1 成 原 , 从 应 度 原 中 暇 水 、 粉 层 度 叙 氢 f 硅 较 文 述 SC 合 的 理 并 反 沮 、 料 含 和 份 硅 料 高 及 化 流 、 粉 度 H3
剩余料在1k 以 冷 0 下, 凝液中S C 含量有所增加。 此, g ih H 因 在整个反 应过程中 维持一定的 料层高 . 硅粉
度非常重要。
三氛氢硅合成的探讨—
汤传斌
根据以 上情况可以 看出, 上述规格的 沸腾合成炉的 料层高 度维持在 1 2 硅粉量比 01 叱 较合适。 如料
}
一 }
,,, ̄
} 一 I
 ̄
一 }
队
I 一
}
 ̄、卜 、、 、
} 一
}
 ̄、、挂
I 一
I
}
}
S4 t i% ) C( 0 t 「二 10 厂二 即 厂一 30 厂一 40 「 一一 幼 60 、 、、 厂, 钧 卜不 即 厂一 的阴 厂一
圈1反应温度与 合成产物中S C, } i l 的关系 H 含t 游离氧及水份, 对反应极为有害,因为 SO键比 SC 键更为稳定,反应产物极易发生氧化或水解, i - iI - 使 S C, iI H 的产率降低.水解产生的 硅胶会堵塞管道,使操作发生困 游离氧或水份还能在硅表面上逐 难. 渐形成一层致密的 氧化膜。 如果硅粉和H I C含水I愈大,则产物中S C 含里愈 'l H3 低。当H I C 中含水量为
7 结语
本文仅从反应温度、 硅粉、 C 中 H I 氧和水份含量、 硅粉料层高度及H I C 流量、 硅粉粒度等几个方面对
S C 合成的 进行了 i1 H3 影响 探讨。 实, S C 合成过 其 在 '1 H3 程中, S C 合成的 还有 应压力、 化 对 '1 H3 影响 反 催
剂、反应活化剂、 反应炉的 类型及气体分布板的 类型等因素m m。因此, 在今后的 生产过程中 应加强这些 方面的 研究, 对提高S C 合成的 '1 H3 产率和S C 的 i I 质量非常有益。 H,
0 % 则S C 含 于8 ; C 中 . 时, I 卜 量小 0 当H I 含水为0 1 时, u l 1 H % .% 则S- , 0 I 含量9% C 0 左右m 在实际生 I A 。 产
过程中,硅粉通过干燥后,使硅粉中水含量控制在 0 5 . %以内;H I 0 C 通过水冷器、深冷器、雾沫分离器除
取得了不少成果。
2 H 1 S C3 i 合成的反应原理
在S C, i I H 合成沸腾炉内, 一定配比的硅粉和H I C主要进行如下的反应: S 3 C=iC, , 03 km l i H l H 1H+ 9 4J o' + S + 2 / l ) 同时, 还伴随下列一些副反应: S 4 C S l2 2 4. km l i H I i4 H+ 0 2 o' + = C+ 2 3 J l / ) S 2C S C( 川 i,I iH 1 H 2 + = 微量)
同 我 通 过图34 可以 现, C流 增 反 温 升高的 相 缩 产 时, 们 ,还 发 随H I 量的 加, 应 度 时间 应 短, 物中S C i1 H3
的含量略有增加, 所以 增加 H I C 流量对提高 S C3 I l H 合成的产率有益, 但是 H I C 流量过大, 进入合成尾气 中H I C 量增大, 造成H I 大量浪费 C的 和尾气处理系统的负担, 甚至还有可能 造成对环境的污染。
层过高,不但没有好处,反而要求过高的 H I C 压力,同时也会造成合成炉中 硅粉易被气流带出 等缺点, 给生产带来困难。 如料层过低,虽然可提高一些 S C 的含量, i 1 H 3 但是反应温度不易控制.另外,不同规 _ 格的沸腾合成炉,其反应所需的最恰当的料层高度也有所不同。 但是,在实际生产过程中,由于加料自 动化问题仍未解决,加料方式仍是间隙加料,在整个反应过 程中,无法维持一定的料层高 所以 S C3 度, 对 i 1 H 合成的产率影响非常大。 至此, 在今后的生产中,加强 自 动加料装置的研究很有必要。
参考文献 ( 略)
70
一 。 . )侧 盟 喊
咖 50 40c 洲
你4 l 业”“攀峥 io r o 1
犷
Id 朋口翔 派t 甸e 。 i
中 .
.4 .业。S 杯口 刀 4 4
冲.
一书 1 U M ! H 箫
日 的幼 以
0 ? 8
9 1 反 问 树 ) 断 ( 0
图3 反应温度随 硅粉层高度 ( 用反应时间 表示) 和速度的变化
1 反时 (时 0 应 问小 )
图4 H I ( S C, i 含f随H I C 线速度及硅粉层高度 用反应时间 表示)的变化
6 硅粉粒度对S C 合成的 [3 il H3 影响11 1 [
粒度大小及粒度分布范围对产物质量、传热、传质等有极大的影响。根据生产实践,硅粉粒度一般 要求在 8 -0 020目范围内就可以使用。
BH I -C 中水盆f
5 硅粉料 度及H I 对S C 合成的 D3 层高 C流量 ' 1 H3 影响 1 [ 1
料层高度及 C 流量是影响产物质量及合成效果的重要因素。 H I 某厂曾 经在 ( 5x60 D 050 沸腾炉内 1 加入 2k 硅粉进行试验, 0g 试验结果如图3 41 . 。从图3 看出,随着硅粉料层高度降 合成炉内 1 ' 可以 低, 剩余硅 粉量到 89g以 合成炉中、下部 -k 后, - 温差增大,随后温度急剧下降。从图 4 看出,随着料层高度降低,