循环流化床锅炉设计原理
循环流化床锅炉原理
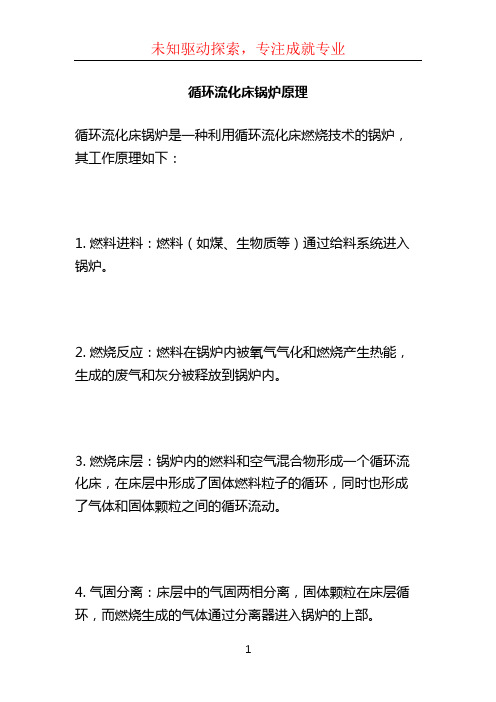
循环流化床锅炉原理
循环流化床锅炉是一种利用循环流化床燃烧技术的锅炉,其工作原理如下:
1. 燃料进料:燃料(如煤、生物质等)通过给料系统进入锅炉。
2. 燃烧反应:燃料在锅炉内被氧气气化和燃烧产生热能,生成的废气和灰分被释放到锅炉内。
3. 燃烧床层:锅炉内的燃料和空气混合物形成一个循环流化床,在床层中形成了固体燃料粒子的循环,同时也形成了气体和固体颗粒之间的循环流动。
4. 气固分离:床层中的气固两相分离,固体颗粒在床层循环,而燃烧生成的气体通过分离器进入锅炉的上部。
5. 固体回流:分离器中的固体颗粒被分离后,一部分被回流到床层继续燃烧,另一部分则通过排渣系统排出锅炉。
6. 热交换:燃烧生成的高温烟气在锅炉的热交换器中与水进行换热,产生蒸汽或热水。
7. 废气处理:通过合适的废气处理系统,对燃烧废气进行脱硫、脱硝和除尘等处理,降低废气对环境的污染。
总体来说,循环流化床锅炉通过循环流化床的形成,实现了燃料和空气的良好混合,提高了燃烧效率;同时通过固体的循环回流,在保持稳定燃烧的同时,降低了燃料的耗损和废渣产生量,提高了锅炉的可持续性和经济性。
循环流化床锅炉的工作原理
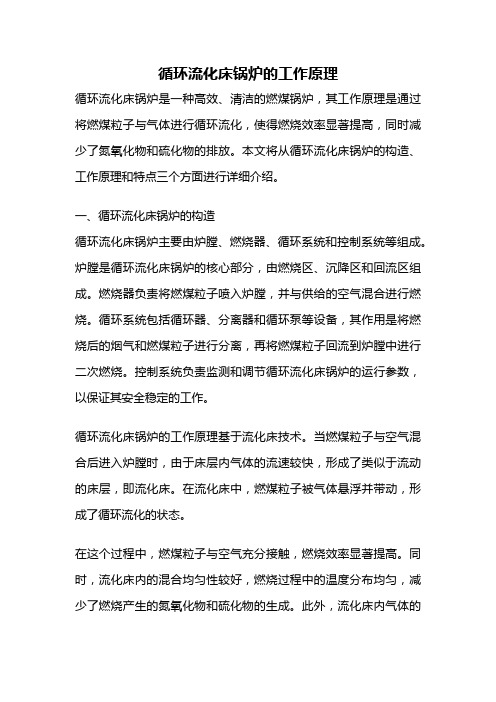
循环流化床锅炉的工作原理循环流化床锅炉是一种高效、清洁的燃煤锅炉,其工作原理是通过将燃煤粒子与气体进行循环流化,使得燃烧效率显著提高,同时减少了氮氧化物和硫化物的排放。
本文将从循环流化床锅炉的构造、工作原理和特点三个方面进行详细介绍。
一、循环流化床锅炉的构造循环流化床锅炉主要由炉膛、燃烧器、循环系统和控制系统等组成。
炉膛是循环流化床锅炉的核心部分,由燃烧区、沉降区和回流区组成。
燃烧器负责将燃煤粒子喷入炉膛,并与供给的空气混合进行燃烧。
循环系统包括循环器、分离器和循环泵等设备,其作用是将燃烧后的烟气和燃煤粒子进行分离,再将燃煤粒子回流到炉膛中进行二次燃烧。
控制系统负责监测和调节循环流化床锅炉的运行参数,以保证其安全稳定的工作。
循环流化床锅炉的工作原理基于流化床技术。
当燃煤粒子与空气混合后进入炉膛时,由于床层内气体的流速较快,形成了类似于流动的床层,即流化床。
在流化床中,燃煤粒子被气体悬浮并带动,形成了循环流化的状态。
在这个过程中,燃煤粒子与空气充分接触,燃烧效率显著提高。
同时,流化床内的混合均匀性较好,燃烧过程中的温度分布均匀,减少了燃烧产生的氮氧化物和硫化物的生成。
此外,流化床内气体的流动还能带走燃烧过程中产生的烟尘,减少了烟尘的排放。
循环流化床锅炉采用循环系统将燃煤粒子回流到炉膛中进行二次燃烧。
在循环器中,燃煤粒子和一部分未燃烧的烟气被分离,未燃烧的烟气经过回流再次参与燃烧,提高了燃烧效率。
经过多次循环后,燃煤粒子中的可燃物质基本被燃烧完全,烟气中的污染物排放得到有效控制。
三、循环流化床锅炉的特点循环流化床锅炉具有以下几个特点:1. 高效节能:循环流化床锅炉采用了循环燃烧技术,燃烧效率高,热效率通常可达到90%以上,节能效果显著。
2. 环保低排放:循环流化床锅炉采用了流化床技术,燃烧过程中的氮氧化物和硫化物排放量较低,符合环保要求。
3. 燃料适应性强:循环流化床锅炉对燃料适应性较强,可燃烧煤炭、生物质、废弃物等多种燃料,灵活性高。
循环流化床锅炉技术
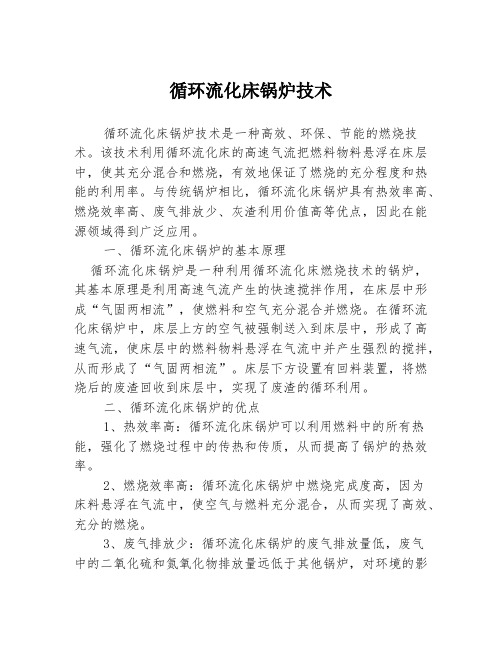
循环流化床锅炉技术循环流化床锅炉技术是一种高效、环保、节能的燃烧技术。
该技术利用循环流化床的高速气流把燃料物料悬浮在床层中,使其充分混合和燃烧,有效地保证了燃烧的充分程度和热能的利用率。
与传统锅炉相比,循环流化床锅炉具有热效率高、燃烧效率高、废气排放少、灰渣利用价值高等优点,因此在能源领域得到广泛应用。
一、循环流化床锅炉的基本原理循环流化床锅炉是一种利用循环流化床燃烧技术的锅炉,其基本原理是利用高速气流产生的快速搅拌作用,在床层中形成“气固两相流”,使燃料和空气充分混合并燃烧。
在循环流化床锅炉中,床层上方的空气被强制送入到床层中,形成了高速气流,使床层中的燃料物料悬浮在气流中并产生强烈的搅拌,从而形成了“气固两相流”。
床层下方设置有回料装置,将燃烧后的废渣回收到床层中,实现了废渣的循环利用。
二、循环流化床锅炉的优点1、热效率高:循环流化床锅炉可以利用燃料中的所有热能,强化了燃烧过程中的传热和传质,从而提高了锅炉的热效率。
2、燃烧效率高:循环流化床锅炉中燃烧完成度高,因为床料悬浮在气流中,使空气与燃料充分混合,从而实现了高效、充分的燃烧。
3、废气排放少:循环流化床锅炉的废气排放量低,废气中的二氧化硫和氮氧化物排放量远低于其他锅炉,对环境的影响小。
4、燃料适应性强:循环流化床锅炉可使用各种燃料,如煤、燃气、油、生物质等,具有一定的燃料适应性。
5、灰渣利用价值高:循环流化床锅炉中的灰渣细化程度高,易于回收利用,在土地改良、水泥生产和道路建设等领域具有广泛的使用价值。
三、循环流化床锅炉的应用领域循环流化床锅炉技术广泛应用于各个领域,如煤炭、石油、天然气、化工、冶金、烟草、食品、纺织等。
在煤炭领域,循环流化床锅炉可用于煤的燃烧,实现高效、低排放、节能的目的。
在化工、冶金、烟草等行业,循环流化床锅炉可用于燃烧废弃物、废气等,实现废物资源化、减少污染的目的。
综上所述,循环流化床锅炉技术是一种高效、环保、节能的燃烧技术,具有热效率高、燃烧效率高、废气排放少、灰渣利用价值高等优点,广泛应用于煤炭、石油、天然气、化工、冶金、烟草、食品、纺织等不同领域。
循环流化床锅炉的构造及工作原理

隔热层分三层砌筑: 密封层 32mm 绝热层 60mm 不大于135mm 耐火层 不大于35mm
布风板的型式
风帽
风帽的作用:是使进入流化 床的空气产生第二次分流并 具有一定的动能,以减少初 始气泡的生成和使底部粗颗 粒产生强烈的扰动,避免粗 颗粒的沉积,减少冷渣含碳 损失。风帽还有产生足够的 压降、均匀布风的作用。
正常燃烧时,在一次风机的作用下,具有一定数量和动 能的空气,经床下启动燃烧器、水冷风室、床上风帽,将床 上物料(煤+炭火+返料灰+石灰石)吹起来,较大的颗粒在 其自身重力作用下向下跌落,与吹起来的粒子发生碰撞、产 生破碎,不断更新粒子的燃烧外表面,使燃烧即快又好。在 上升的火焰和炭火流中,既有分子团的不断形成与扩散,又 有物料的强烈碰撞与返混,使燃烧的炭火流就像金色的喷泉 充满整个炉膛空间。由于流化速度比较高,离开炉膛的烟气 要带走一定数量的灰,经过旋风分离器、上料腿、回料阀、 下料腿,再一次回到床上参加流化、燃烧、传热,顾名思义 ,叫循环流化床锅炉。
回料阀的阻 力:
回料阀空床阻力4000帕-5000帕左右
回料阀的内部工作状 态:
回料器内的两个状态(松 动、流化)
CFB锅炉燃烧过程中的七个状态
• 炉膛浓相区--------紊流状态 • 炉膛稀相区--------高速流化状态 • 旋风分离器--------旋转状态 • 上料腿------------移动状态(不是流动) • 回料器------------鼓泡状态+流化状态 • 下料腿------------流动状态
罗茨风机出力可自动 调节,返料灰多风压自动 加大,返料灰少风压自动 减小。
返料风机采用的运行 方式:
循环流化床锅炉工作原理
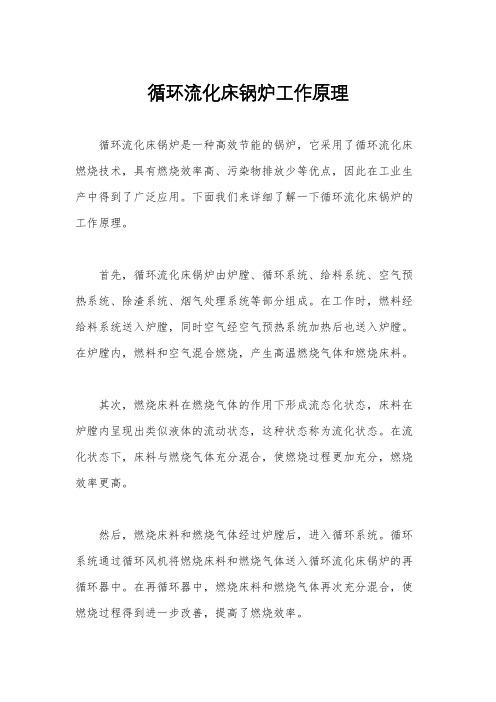
循环流化床锅炉工作原理循环流化床锅炉是一种高效节能的锅炉,它采用了循环流化床燃烧技术,具有燃烧效率高、污染物排放少等优点,因此在工业生产中得到了广泛应用。
下面我们来详细了解一下循环流化床锅炉的工作原理。
首先,循环流化床锅炉由炉膛、循环系统、给料系统、空气预热系统、除渣系统、烟气处理系统等部分组成。
在工作时,燃料经给料系统送入炉膛,同时空气经空气预热系统加热后也送入炉膛。
在炉膛内,燃料和空气混合燃烧,产生高温燃烧气体和燃烧床料。
其次,燃烧床料在燃烧气体的作用下形成流态化状态,床料在炉膛内呈现出类似液体的流动状态,这种状态称为流化状态。
在流化状态下,床料与燃烧气体充分混合,使燃烧过程更加充分,燃烧效率更高。
然后,燃烧床料和燃烧气体经过炉膛后,进入循环系统。
循环系统通过循环风机将燃烧床料和燃烧气体送入循环流化床锅炉的再循环器中。
在再循环器中,燃烧床料和燃烧气体再次充分混合,使燃烧过程得到进一步改善,提高了燃烧效率。
接着,燃烧床料和燃烧气体经过再循环器后,进入烟气处理系统。
烟气处理系统对燃烧床料和燃烧气体进行脱硫、脱硝、除尘等处理,以达到环保排放标准。
通过烟气处理系统处理后的燃烧床料和燃烧气体排放到大气中,对环境影响较小。
最后,循环流化床锅炉通过除渣系统将燃烧床料中的灰渣排出,以保持炉膛内的清洁。
同时,循环流化床锅炉还通过余热回收系统和热力发电系统充分利用燃烧产生的余热,实现能量的最大化利用。
总的来说,循环流化床锅炉通过循环流化床燃烧技术实现了燃烧过程的高效、清洁和节能。
它的工作原理简单清晰,通过循环系统、烟气处理系统等部分的配合,实现了燃烧床料和燃烧气体的充分利用,达到了节能减排的目的。
因此,循环流化床锅炉在工业生产中具有广阔的应用前景。
循环流化床锅炉的原理与设计

循环流化床锅炉中的流化过程
循环流化床锅炉中的流化过程包括以下几个特点
• 炉膛内充满颗粒燃料,气流速度较低 • 燃料颗粒与空气充分混合,燃烧效率高 • 流化床内温度分布均匀,传热效果好
流化过程是指固体颗粒在流体中运动,形成类似流体的状态
• 当气流速度达到一定值时,固体颗粒开始悬浮并相互碰撞 • 这种状态有利于燃料的燃烧和热量的传递
循环流化床锅炉的脱硝技术
• 循环流化床锅炉的脱硝技术包括以下几个方面 • 选择性非催化还原(SNCR)技术:通过向炉内喷射氨水,实现NOx的还原 • 选择性催化还原(SCR)技术:通过设置催化剂层,对烟气进行脱硝处理
循05环流化床锅炉的运行与
维护
循环流化床锅炉的启动与停止操作
• 循环流化床锅炉的启动与停止操作需要遵循以下步骤 • 启动前进行设备检查,确保锅炉各部分正常 • 缓慢启动风机,向炉膛内加入燃料,实现燃料的流化 • 启动过程中注意观察炉膛内的温度和压力变化,确保锅炉稳定 运行 • 停止操作时,先停止燃料供应,然后降低风机转速,最后停止 风机运行
循环流化床锅炉的燃烧室设计
• 循环流化床锅炉的燃烧室设计需要考虑以下几个因素 • 燃烧室的尺寸和形状,以满足燃料燃烧和热量交换的需求 • 燃烧室的温度分布,以保证燃料的充分燃烧和热量的有效传递 • 燃烧室的气流组织,以实现燃料与空气的充分混合和燃烧产物 的排放
循环流化床锅炉的传热元件设计
• 循环流化床锅炉的传热元件设计需要考虑以下几个因素 • 传热元件的材料和结构,以满足锅炉温度和压力的要求 • 传热元件的热交换性能,以提高锅炉的热效率和适应性 • 传热元件的耐腐蚀性能,以延长锅炉的使用寿命
循环流化床锅炉的热交换原理
循环流化床锅炉的热交换原理主要依赖于传热元件
循环流化床锅炉的工作原理
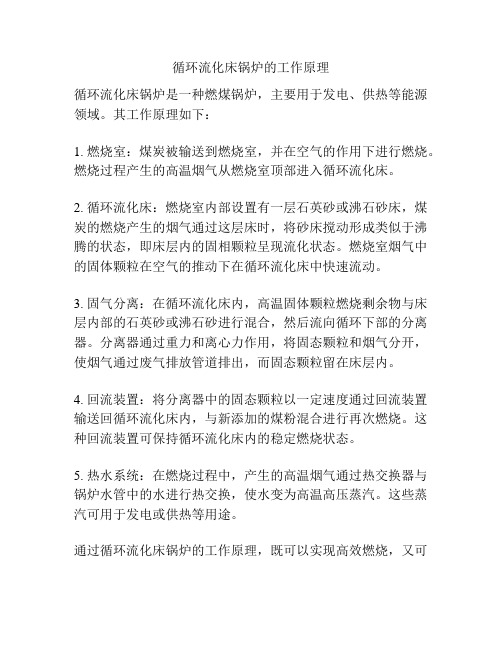
循环流化床锅炉的工作原理
循环流化床锅炉是一种燃煤锅炉,主要用于发电、供热等能源领域。
其工作原理如下:
1. 燃烧室:煤炭被输送到燃烧室,并在空气的作用下进行燃烧。
燃烧过程产生的高温烟气从燃烧室顶部进入循环流化床。
2. 循环流化床:燃烧室内部设置有一层石英砂或沸石砂床,煤炭的燃烧产生的烟气通过这层床时,将砂床搅动形成类似于沸腾的状态,即床层内的固相颗粒呈现流化状态。
燃烧室烟气中的固体颗粒在空气的推动下在循环流化床中快速流动。
3. 固气分离:在循环流化床内,高温固体颗粒燃烧剩余物与床层内部的石英砂或沸石砂进行混合,然后流向循环下部的分离器。
分离器通过重力和离心力作用,将固态颗粒和烟气分开,使烟气通过废气排放管道排出,而固态颗粒留在床层内。
4. 回流装置:将分离器中的固态颗粒以一定速度通过回流装置输送回循环流化床内,与新添加的煤粉混合进行再次燃烧。
这种回流装置可保持循环流化床内的稳定燃烧状态。
5. 热水系统:在燃烧过程中,产生的高温烟气通过热交换器与锅炉水管中的水进行热交换,使水变为高温高压蒸汽。
这些蒸汽可用于发电或供热等用途。
通过循环流化床锅炉的工作原理,既可以实现高效燃烧,又可
以减少污染物的排放,提高能源利用率,具有较好的环保性能和经济性能。
循环流化床锅炉工作原理
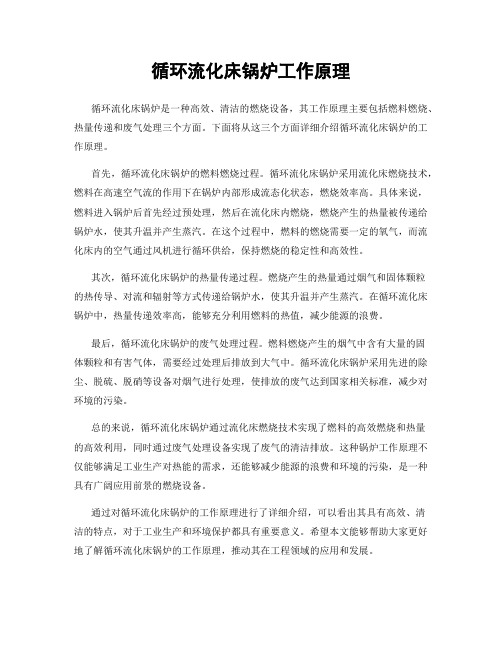
循环流化床锅炉工作原理循环流化床锅炉是一种高效、清洁的燃烧设备,其工作原理主要包括燃料燃烧、热量传递和废气处理三个方面。
下面将从这三个方面详细介绍循环流化床锅炉的工作原理。
首先,循环流化床锅炉的燃料燃烧过程。
循环流化床锅炉采用流化床燃烧技术,燃料在高速空气流的作用下在锅炉内部形成流态化状态,燃烧效率高。
具体来说,燃料进入锅炉后首先经过预处理,然后在流化床内燃烧,燃烧产生的热量被传递给锅炉水,使其升温并产生蒸汽。
在这个过程中,燃料的燃烧需要一定的氧气,而流化床内的空气通过风机进行循环供给,保持燃烧的稳定性和高效性。
其次,循环流化床锅炉的热量传递过程。
燃烧产生的热量通过烟气和固体颗粒的热传导、对流和辐射等方式传递给锅炉水,使其升温并产生蒸汽。
在循环流化床锅炉中,热量传递效率高,能够充分利用燃料的热值,减少能源的浪费。
最后,循环流化床锅炉的废气处理过程。
燃料燃烧产生的烟气中含有大量的固体颗粒和有害气体,需要经过处理后排放到大气中。
循环流化床锅炉采用先进的除尘、脱硫、脱硝等设备对烟气进行处理,使排放的废气达到国家相关标准,减少对环境的污染。
总的来说,循环流化床锅炉通过流化床燃烧技术实现了燃料的高效燃烧和热量的高效利用,同时通过废气处理设备实现了废气的清洁排放。
这种锅炉工作原理不仅能够满足工业生产对热能的需求,还能够减少能源的浪费和环境的污染,是一种具有广阔应用前景的燃烧设备。
通过对循环流化床锅炉的工作原理进行了详细介绍,可以看出其具有高效、清洁的特点,对于工业生产和环境保护都具有重要意义。
希望本文能够帮助大家更好地了解循环流化床锅炉的工作原理,推动其在工程领域的应用和发展。
- 1、下载文档前请自行甄别文档内容的完整性,平台不提供额外的编辑、内容补充、找答案等附加服务。
- 2、"仅部分预览"的文档,不可在线预览部分如存在完整性等问题,可反馈申请退款(可完整预览的文档不适用该条件!)。
- 3、如文档侵犯您的权益,请联系客服反馈,我们会尽快为您处理(人工客服工作时间:9:00-18:30)。
底部设计-1
底部设计-2
循环流化床锅炉一次风比例
Vdaf (%) 一次风比例
贫煤或无烟煤 烟煤或褐煤 烟煤或褐煤
<20 20~40 >40
~65(75) ~60 ~50
布风板
水冷布风板
下炉膛敷设耐火材料
喷嘴
由膜式壁构成的水冷风箱和水冷布风板
风帽1
风帽2
燃烧室高度选择
循环流化床锅炉燃烧室高度
-Lurgi / Alhstrom / EVT / AEE / Alstom -Foster Wheeler -Deutsche Babcock -大量的鼓泡床经验 -带飞灰再燃的鼓泡床 -误区------“鼓泡床拉 拉长”
国内
物料回送部分 给煤 床层 空气 排渣 图 2-10 循环流化床锅炉的构成 料腿 回料阀
分离器对循环流化床锅炉燃烧效率的影响
贫氧区的存在
分离器对飞灰含碳量的影响
40
飞灰含碳量分布 %
30 20 10 0 D (c) 0 50 100 150 200 250 B
贫氧区 二次风 二次风
颗粒直径 m
燃烧中大颗粒失活过程-磨耗
循环流化床锅炉的燃烧效率
燃烧效率
30
典型床温控制在850~900℃
组成部分
循环回路:
尾部烟道:
炉膛 气固分离器 固体粒子回送装置 外部热交换器。
再热器 过热器 省煤器 空气预热器
效率估算
1 q2的计算
石灰石脱硫对烟气量的影响 过量空气系数
表 3.3 炉膛出口过量空气 烟煤、褐煤 1.15~1.20
2 q3的考虑----0 3 q4的计算---灰渣比/灰渣含碳量
发展经历决定了对分离器的理解
高效分离-旋风分离器 简易分离-高效补偿 简易分离-无补偿---带埋管-改进型鼓泡床 简易分离-无补偿-不 带埋管----出力不足 出力不足
烟气 分离器 提升部分 分离部分
物料回送部分 给煤 床层 空气 排渣 图 2-10 循环流化床锅炉的构成 料腿 回料阀
烟气 800~900 ℃
循环流化床 的内外循环
800~900 ℃ 4~6m/s
空气 燃料
石灰石 空气
循环流化床气固两相流性质
物料浓度分布 --贴壁流 形成浓度分布是有条件的 --分离器 --回送装置 --物料来源 浓度分布是有意义的
循环流化床燃烧技术的发展历程
国外
烟气 分离器 提升部分 分离部分
燃烧效率
飞灰含碳量(%)
30 较高温度 较低温度 20
典型床温控制在 850~900℃ 飞灰再循环
10
0 0 2 4 单位热值的可燃基挥发分(%/MJ) 6
循环流化床锅炉的热风温度
目的------降低排烟温度---锅炉效率
表 3.6 循环流化床锅炉的热风温度 给水温度(℃) 104 20~180 20~180 150 100~200 150~250 215 150~250 150~150 240 200~300 200~300 一次风 二次风
7~10m/s
6~9m/s 6~10m/s 6~9m/s 7~13m/s
空气预热器(烟气走管内)
100~250℃
7~12m/s
尾部受热面的传热
循环流化床锅炉的尾部对流受热面热有效系数或空气预热器利用系数 受热面名称 过热器、再热器 过热器、再热器 省煤器 省煤器 所处烟气温度 700~900℃ 500~700℃ 450~600℃ 300~450℃ 烟气速度 有无吹灰 有 0.71~0.82 0.62~0.67 0.60~0.65 0.58~0.63 0.55~0.61 0.75~0.82 0.73~0.80 无 0.70~0.83 0.7~0.80 0.60~0.64 0.58~0.61 0.56~0.59 0.54~0.60 0.72~0.80 0.70~0.78 7.5~12 m/s 0.72~0.84 6~9m/s 7~10m/s 6~9m/s 6~10m/s 6~9m/s 7~13m/s 7~12m/s
循环流化床锅炉设计原理
清华大学 热能工程系 岳光溪 吕俊复 100084 Tel:62781559 62781743
一 循环流化床锅炉设计的一般考虑
炉型选择 预备性计算
锅炉效率计算 脱硫计算及石灰石脱硫热效应和烟气量变化 空气平衡计算 燃料及石灰石计算
整体布置
a-∏形 b-M形 c-倒背锅形 d-半塔形 e-改良∏形 f-紧凑型
1-Up limited 2-Conmmeded curve 2-Lower limited 0 400 800 1200 size di/m 1600 2000
0
0
0
启动床料的要求
100 75 50 25 0 0 1 3 /mm 颗粒粒径 i d 2 4 5
累积份额 W i /%
二 炉膛设计
X(i)
系统对物料i的保存效率为:
hi= 1- [Gout(i)+F(i)] /E(i)*X(i) = hoi+ hi-1
Gout(i)
分离器不同对飞灰粒径分布的影 响 1.6
Pi fa/%m-1
1.2 0.8 0.4 0 0 150 300 450 颗粒粒径 d i /m 600 1# 3# 5# 7# 2# 4# 6#
烟气 800~900℃
气 固 两 相 流 动 过 程
800~900℃ 4~6m/s
空气 燃料
石灰石 空气
循环流化床气固两相流分布特点
分离器对燃烧过程的影响
物料循环对床温的平衡作用-- 低温回灰 中温回灰 高温回灰
床料分析
100-300m;4~6m/s; 外加床料,多采用沙子或外加灰; 少量的细粉燃料; 新添入的和已经失效的脱硫剂; 煤里自身的灰份。
热风温度(℃)
燃料及石灰石粒度要求
80 60 40 20 1 2
accumulated percent %
100
100 80 60 40 20 2
percent
1 3
3
accumulated %
1-Anthracite or lean coal 2-Bituminous 3-Lignite 3 6 9 size di/mm 12 15
循环系统保存效率
F(i)
对于单一粒径颗粒均应有一个平衡关系
E(i)*X(i)
Gin(i) = Gout(i)+ F(i)
hi =1- F(i) /E(i)*X(i)
E(i)*X(i)*(1-hi)= F(i)
以夹带物料流为基, 分离器效率为
Gin(i)
定义排渣效率为: hoi= 1- Gout(i) /E(i)*X(i)
空塔速度—5.0m/s—压力温度修正后 高度---受热面布置/燃烧效率 分离器数量-成双布置 宽度深度比------1.8~2.2
炉 膛 形 状
二次风 燃料 脱硫剂 循环物料 二次风 二次风 二次风
燃料 脱硫剂 循环物料
一次风
一次风
a b 循环床锅炉两种不同的炉膛设计
a-等截面变风速 b-变截面等风速
空气预热器(空气走管内) 250~400℃ 空气预热器(空气走管内) 100~250℃ 空气预热器(烟气走管内) 250~400℃ 空气预热器(烟气走管内) 100~250℃
过热器、再热器的管壁温度计算时,灰污系数取为 0.002m2℃/W。
五 分离器作用的分析
鼓泡流化床或湍流床和气力输送叠加的 燃烧技术 处于鼓泡床和气力输送燃烧之间
分布频率
飞灰及其中碳的形成过程分析
12
烧失量 Cfa/%
8 4 0
d dcoal
Time
Fragmentation Prophase of Attrition Anaphase of Attrition
渣
一电场 二电场 三电场 四电场 样品名称
循环流化床锅炉用的气固分离 器
颗粒尺寸与分离器 l 切割粒径 l 分级分离效率 l 总分离效率 l 粒径分布
对流受热面烟气流速范围
受热面名称
过热器、再热器 过热器、再热器
所处烟气温度
700~900℃ 500~700℃
烟气速度
7.5~12 m/s 6~9m/s
省煤器
省煤器 空气预热器(空气走管内) 空气预热器(空气走管内) 空气预热器(烟气走管内)
450~600℃
300~450℃ 250~400℃ 100~250℃ 250~400℃
分离器作用的一 般认识
对分离效果的认识误区 -燃烧效率 -磨损等 的分析全部归结到分离器
分离器作用的一般理解
同时存在的对分离效果的认识误区 -燃烧效率 -磨损等 的分析全部归结到分离器
循环流化床锅炉燃烧过程的描述
气泡存在的客观性及必要性
颗粒循环的动力
循环流化床锅炉燃烧过程的分析
煤 种 烟 煤 褐 煤 备 注
注:1 适于鼓泡床
锅炉容量 kg/s 9.727 15 14 2 20.83 20 18 2
2 适于循环流化床
36.11 25 24 2
61.11 29 28 2
113.9 34 30 2
186.1 39 37 2
274.2 50 47 2
水冷壁传热
燃烧室受热面传热 l 物料浓度-固体颗粒 l 燃烧室的温度 l 近壁区贴壁下降流 l 粒径 l 受热面的结构尺寸