生产现场异常判断及处理
SMT生产现场异常处理流程

责任者
作业者 领班
技术员 领班
根据领班或技术员报告,现场确认处置结果,或对异常的处理作出 主管 进一步的对应或作业指示
根据异常的重要程度,主管对应后向相关者进行联络
主管
1、人身安全按公司危急管理体制路径对应 2、机器设备安全12小时内报告厂长、总经理 3、物品安全关系24H内报告厂长、总经理处置
1、现状把握清楚,召开检讨会议,确定检讨方向 2、追溯关系出荷/在库并按检讨方法处置 3、5W检讨、对策报告提交 4、对策教育并实施
主管
主管/厂长 外部门关系
序号
1 2
3 4 5 6
7 注
处置流程
1 发现
2 对异联络
6 安全
品质 7 事故
SMT生产现场异常处理流程
说明
发现异常,暂停作业,及时报告领班。
1、对异常进行初步判断和处理 2、不能解决的异常应依赖技术员或主管处理 3、对象品的区分隔离和明确标识并特别管理 4、紧急事项(安全/灾难等)依危急管理体制路径对应
生产现场异常判断与处理

生产指标的异常判断
R3数据 产量、超耗推移图 品保统计表 安全检查表
分组讨论
每组提出5个,现存的异常
解决异常的三个重点
1. 找出异常的真正的原因 2. 找出解决问题的重点对策 3. 订出异常解决的行动计划
要做什么(what)? 谁来做(who)? 什么时候完成(when)? 各项行动如何进行(how to)?
39
异常处理
步骤1 步骤2 步骤3 步骤4 步骤5 步骤6 步骤7 步骤8 步骤9
明确的目标、标准 发现异常 分析异常点的产生原因 确定要解决的课题 拟订对策 做出行动计划 执行行动计划 效果确认 标准化
GEC Program
42
知识回顾 Knowledge Review
祝您成功!
评估异常性质的两个步骤
步骤1 解决异常的优先 顺序
❖ 紧急性 ❖ 重要性 ❖ 妥当性
步骤2 区分异常的类别
❖发生型问题 ❖谋求改善型问题 ❖ 潜在型问题
GEC Program
35
如何进行您的工作
以PDCA完成达成目标的程序
P ——计划(plan) D——执行(do) C——检查(check) A——改正再执行(action)
1. 能采取对策者 2. 有因果关系者,归于同一中、小支干內
四. 決定主要原因
4-6項影响問题点的主要原因 在所列出的原因中认为影响較大的划上紅圈,再从划上紅圈的原因中认
为影响更大再劃划上紅圈,一直检讨下去。最后圈选4-6項影响問題點 的主要原因。
五. 加上相關記錄資料
填上製作目的、日期及製作者等資料
显现的异常判断
人:生病、喝酒、精神状态等 机:停机、异响、备件损坏、异味、高
异常工况处置管理规定9.27
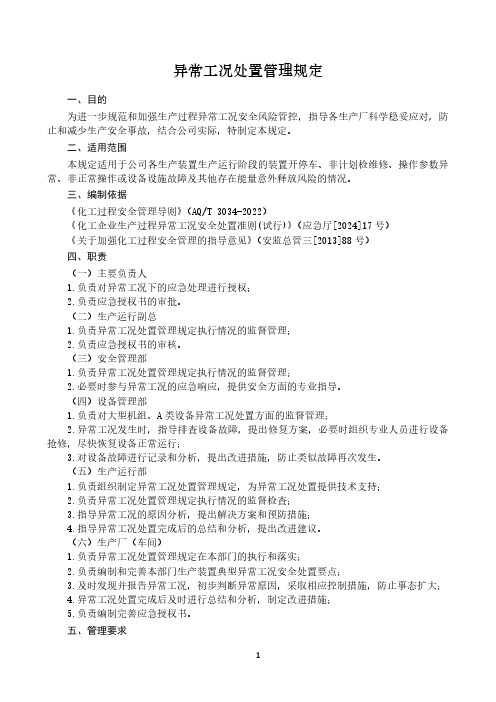
异常工况处置管理规定一、目的为进一步规范和加强生产过程异常工况安全风险管控,指导各生产厂科学稳妥应对,防止和减少生产安全事故,结合公司实际,特制定本规定。
二、适用范围本规定适用于公司各生产装置生产运行阶段的装置开停车、非计划检维修、操作参数异常、非正常操作或设备设施故障及其他存在能量意外释放风险的情况。
三、编制依据《化工过程安全管理导则》(AQ/T 3034-2022)《化工企业生产过程异常工况安全处置准则(试行)》(应急厅[2024]17号)《关于加强化工过程安全管理的指导意见》(安监总管三[2013]88号)四、职责(一)主要负责人1.负责对异常工况下的应急处理进行授权;2.负责应急授权书的审批。
(二)生产运行副总1.负责异常工况处置管理规定执行情况的监督管理;2.负责应急授权书的审核。
(三)安全管理部1.负责异常工况处置管理规定执行情况的监督管理;2.必要时参与异常工况的应急响应,提供安全方面的专业指导。
(四)设备管理部1.负责对大型机组、A类设备异常工况处置方面的监督管理;2.异常工况发生时,指导排查设备故障,提出修复方案,必要时组织专业人员进行设备抢修,尽快恢复设备正常运行;3.对设备故障进行记录和分析,提出改进措施,防止类似故障再次发生。
(五)生产运行部1.负责组织制定异常工况处置管理规定,为异常工况处置提供技术支持;2.负责异常工况处置管理规定执行情况的监督检查;3.指导异常工况的原因分析,提出解决方案和预防措施;4.指导异常工况处置完成后的总结和分析,提出改进建议。
(六)生产厂(车间)1.负责异常工况处置管理规定在本部门的执行和落实;2.负责编制和完善本部门生产装置典型异常工况安全处置要点;3.及时发现并报告异常工况,初步判断异常原因,采取相应控制措施,防止事态扩大;4.异常工况处置完成后及时进行总结和分析,制定改进措施;5.负责编制完善应急授权书。
五、管理要求(一)基本要求1.各公司董事长对异常工况下的应急处理进行授权,明确异常工况边界条件(装置较严重的异常工况,突发的泄漏、火灾爆炸等意外事件),建立完善岗位人员紧急停车、人员撤离等授权机制,制定应急授权书,赋予相关管理人员和基层班组应急处置的权力。
生产现场异常处理流程

生产现场异常处理流程嘿,咱今儿就来说说生产现场异常处理流程这档子事儿!你想想啊,生产现场就好比一个大舞台,各种设备、人员都在上面忙活着呢。
可有时候啊,就会出点小岔子,这就好比一场精彩的表演中突然来了个小意外。
那咋办呢?别急,咱有招儿!一旦发现异常,咱就得像侦探一样,迅速行动起来。
首先得赶紧找到问题出在哪儿呀,不能像个没头苍蝇似的乱撞。
这就好比你丢了东西,得知道大概在哪个范围去找不是?然后呢,得把这个异常的情况详细地记录下来。
这可重要啦,不然回头你都不知道咋跟别人说清楚到底发生了啥。
就跟你给别人讲故事似的,得把细节都讲明白了,人家才能听明白呀。
接着,咱得赶紧分析分析,这异常是咋来的呀。
是设备闹脾气了,还是人员操作失误啦?这就像医生看病,得找到病根儿才能对症下药不是?找到原因了,那咱就得想办法解决啦!该修设备的修设备,该培训人员的培训人员。
可不能拖拖拉拉的,不然这问题就像雪球一样越滚越大,那可就麻烦喽!处理完了,也别着急松口气,还得检查检查,看看这问题是不是真的解决好了。
别弄个表面功夫,过两天又出问题了,那可不行!咱再想想,要是这异常影响了生产进度,那可得赶紧想办法赶回来呀。
就像跑步比赛,摔了一跤也得赶紧爬起来继续跑,可不能就这么放弃了。
还有啊,大家得齐心协力。
这可不是一个人的事儿,是大家共同的事儿。
就像拔河比赛,得大家一起使劲儿才能赢呀。
在这个过程中,可别互相埋怨。
出了问题大家一起解决,埋怨有啥用呢?还不如把那精力放在解决问题上呢。
生产现场异常处理流程,说起来简单,做起来可不容易呢。
但只要咱认真对待,细心处理,就没有解决不了的问题。
咱可不能因为一点小异常就乱了阵脚,要沉着冷静,像个大将军一样指挥若定。
你说是不是这个理儿?咱在生产现场,就得时刻保持警惕,随时准备应对各种异常情况。
只有这样,咱的生产才能顺顺利利的,咱的效益才能越来越好呀!反正我觉得就是这么回事儿,大家都得重视起来,别不当回事儿哟!。
生产现场常见的问题及错误的解决方式

生产现场常见得问题及错误得解决方式企业在其成长过程中,常常会经历各种不同得阶段与遇到不同层面得许多问题点、对于企业来说,发展战略就是成功得坚实基础,但就是企业往往失败在战术方面、所谓得战术失败,指得就是在生产现场得问题点没能得到及时、有效得解决,从而也相应得使问题层出不穷。
这种战术上得失败极有可能导致战略上得失败。
因此,分析企业生产现场所常遇见得各类问题,以及研究企业对问题处理过程中所通常贯用得方式,就是很有现实意义得。
一、常见得问题ﻩ所谓管理,就就是要管理异常得事情,而正常得事情并不需要加以管理。
作为管理干部,本身并不需要参与具体生产得活动,管理者所要做得就就是在生产现场出现问题时,能及时、有效地排除异常得问题。
生产现场得活动就是很复杂得,其中可能包含了很多繁琐得流程、因此,在生产现场将会遇到各方面得很多问题、1、作业流程不顺畅ﻩ每一条生产线中,一般都包含多个流程、因此,生产现场最常见得问题就就是作业流程不顺畅。
作业流程不顺畅得最直接影响就就是致使公司生产产品所需得平均工时增加,从而相应地降低了生产现场得工作效率,甚至导致产品不能按时交货。
当遇到作业流程不顺畅时,最常用得方法就是再增加同样得生产线。
这样一来势必就浪费了不少工时,增加了企业对生产设备得投入,从而严重影响到公司产品生产得成本不断增加与效率不断下降。
ﻫ2、不良品得混入ﻩ如果生产现场不就是井井有条,就会经常发生不良品混入得情况。
所谓不良品得混入,指得就是进料检验过程中出现得漏检,导致一部分不良得原料混入到生产线;或在进料检验过程中已经检验出来,并隔离在仓库,而在领料得过程中又粗心地领出来,混入了生产制造过程中;甚至有可能检验隔离出来得半成品,在进入下一道工序时又粗心地混入其中。
不良品得混入必然会造成重复返工。
重复返工在作业过程中得经常发生,又相应地使产品得品质不断下降。
最后,不合格得产品必将直接导致客户产生抱怨,要求退货,更为严重得就是,客户以后不再愿意与企业合作、产品质量得好坏,直接影响到生产企业得声誉,影响客户对企业得信赖度,最终必将严重损害企业在广大客户心中树立得高大企业形象。
异常处理流程
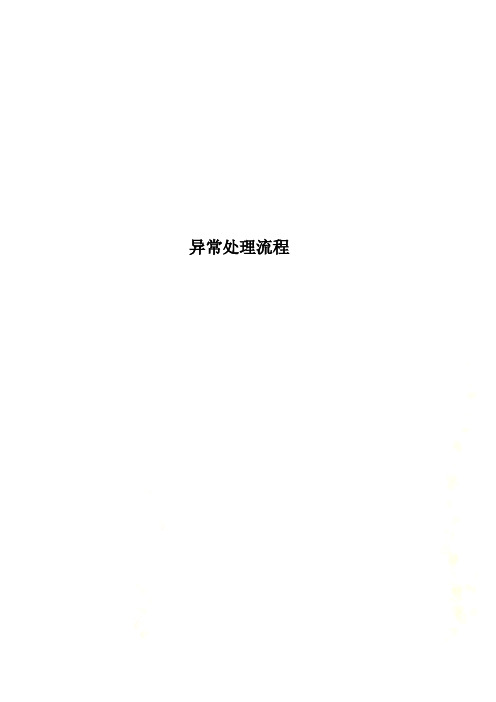
异常处理流程异常处理流程为了更好更快的运行一个流生产,解决生产中出现的异常,降低人力成本,提高生产效率,最终保证客户的正常供货。
拟制此异常处理流程。
一、当生产出现异常,无法继续生产,操作者需要第一时间通知现场工程师,确认是否能够解决,否则由现场工程师根据异常情况,第一时间通知该产品相关部门负责人召集现场。
(计划调度、产品工程师、质量、现场工程师等)二、相关人员必须10分钟之内到达现场,特殊情况由代理人去现场确认,事后交接。
相关人员10分钟到达现场后,30分钟内作出决议。
三、异常处理要求现场30分钟需要确定出来异常产品结果如下1、此批放行;1-1:负责该产品质量工程师确定;1-2:确定下批处理意见,如果需要修模,本批生产结束,由车间调度通知模修,生产计划员提供维修时间段。
2、生产后挑选作业;3、需要维修模具;3-1:生产计划员根据库存状况,提供模修最长修复时间。
3-2:如果提供时间点模修认可,在规定时间内修好,需要第一时间通知车间调度,安排试模。
3-3:如果修模时间点经验判断会超过规定时间,以及第一次试模NG,可能影响生产计划提供的时间点,模修需要通知计划员,并上报上级领导。
3-4:如果模修需要其它部门协助,(产品工程师、模具工程师、计划员等)可以主导相关单位,进行会议检讨,确定维修方案以及进度,各负其责。
以上现场异常处理流程,计划员会以最短时间内作出计划调整,减少工时浪费,责任单位负责主导定出修理方案、完成日期,保证下次正常生产。
备注:1、模修主导会议,需要会议记录形式,发放相关单位确认进度,相互跟踪。
2、针对责任单位,落实不到位,未负其责,追究个人责任,如果影响出货,连带直属主管。
以上,望各单位主管配合,落实到位,认真执行。
会签各部门生产部:车间:产品:质量:模具:设备:。
(精品文档)精益生产_生产现场常见异常处理流程

标题版本01版编码制定制定日期2010.06.1页数异常报警方法:生产过程中出现以下异常状态时 操作工须开启“异常开关”,待解决人员到场后才可关掉“异常开关”。
异常状态人员等待停线出现不能解决或有困难的问题就按照缺陷级别找相关人员来处理。
缺陷级别处理权限处理时间停线班组长全能工机修巡检班组长全能工机修品管班组长批准:审核:制作:会签:1、反复性及无确定性异常须报告上级;2、设备调整、维修时间或中间工序停止作业≥5分钟时,前面所有流水作业工序必须停止作业;3、重复异常升级报告,即当重复性异常发生时,除通知第一责任人到现场外,第一责任之上级也必须到现场。
不影响基本产品功能影响产品功能,但具有更正办法影响产品功能,但没有更正办法丧失产品基本功能或造成人身伤害。
<30分钟<45分钟<30分钟/否否是是一般缺陷轻微缺陷严重缺陷致命缺陷主任工程师主管科长产品堆积设备故障品质异常人员替岗物料过程切换或缺料生产进度缺料:当出现物料不足时,须在10分钟作业量时发出报警信号。
因作业员工报警信号发出延误造成作业中断、堆积时要进行评比教育。
因上工序原因导致缺料不能准时开线生产时,要通知上级,并灵活安排生产。
因过程不稳定因素造成生产量达成不足60%要报告上级并分析原因采取措施调整后续生产进度。
现场停线超出15分钟时班组长须报告上级。
定义特别备注缺陷级别定义详见没有特殊原因在两小时内人员是不予离岗。
距离工休时间30分钟内不予离岗。
确实离岗时,须待替岗人员接替工作后 配戴“离岗证”方可离开。
在生产过程中,物料切换或补料由班组长或全能工完成,确保生产员工作业的均衡,不可中断、堆积。
如胶带机 需要更换胶带时,须在10~20只产品作业量时发出报警信号。
多个岗位均出现堆积:降低线速,增加蜘蛛人。
提高线速,合并工位。
有备用设备:立即更换然后进行报修。
品质异常范围较广,现场常用应急临时对策。
出现如电芯腐蚀、内部短路、PCB烧坏、超声塑焊性能不良等严重、致命不良要立即停止生产,报告上级处理。
13 生产异常控制流程及管理办法

4.相关部门在接到生产异常信息后10分钟内(紧急事件立即处理)赶到生产现场,初步分析。如部门负责人不能到现场应在规定时间内派人到场。
4.1要求异常主导处理责任人在接到信息后30分钟内要求制定出应急措施:
2. 当事部门主管/经理未在规定时间内发出《生产异常联络单》知会PMC部,依《生产管理条例》处理。
六.相关表单
1.《内部联络单》
2.《生产异常联络单》
生产异常控制流程
序号
流程
责任人
相关表单
当班操作员需立即对异常情况做出初步判断,估计其严重性。
2
操作员
当异常无法立即排除且有可能影响到生产进度时,需立即通知车间主管。
3
车间主管
车间主管接到异常汇报时,立即通知厂长。
4
车间三级干部
厂长、车间主管、操作员一起进行现场处理,查找原因、分析对策、若为重大异常,则厂长应立即知会总经理。
生产异常控制管理办法
一.目的
为了把生产中出现的异常状况迅速而有效地处理,使异常影响降到最低程度。
二.适用范围
适用于公司生产车间所发生的生产异常。
三.定义
本办法所指的生产异常是指设备故障、重大品质问题、技术问题、人员不足等影响生产进度,进而会影响到订单交期的突发状况。
四.作业规范
1.当出现生产异常时,现场管理人员立即(10分钟内)报告主管、厂长,车间三级管理人员必需依如下程序进行处理:
5
厂长
内部联络单
由厂长依异常情况发出《内部联络单》通知相关部责任部门协同处理。
6
生产部、相关责任部门
由生产部与相关责任部门一同依据实际情况决定是否停产,并制定出应急处理措施。
- 1、下载文档前请自行甄别文档内容的完整性,平台不提供额外的编辑、内容补充、找答案等附加服务。
- 2、"仅部分预览"的文档,不可在线预览部分如存在完整性等问题,可反馈申请退款(可完整预览的文档不适用该条件!)。
- 3、如文档侵犯您的权益,请联系客服反馈,我们会尽快为您处理(人工客服工作时间:9:00-18:30)。
评估异常性质的两个步骤
步骤1 解决异常的优先 顺序
紧急性 重要性 妥当性
步骤2 区分异常的类别
发生型问题 谋求改善型问题 潜在型问题
GEC Program
35
如何进行您的工作
以PDCA完成达成目标的程序
P ——计划(plan) D——执行(do) C——检查(check) A——改正再执行(action)
为影响更大再劃划上紅圈,一直检讨下去。最后圈选4-6項影响問題點 的主要原因。
五. 加上相關記錄資料
填上製作目的、日期及製作者等資料
特性要因图
分析型与对策型魚骨图
。
环境
作业方法 材料
特 性
机器
作业人員
环境
作业方法 材料
机器
作业人员
問題分析型魚骨图
切記儘可能不要使用上述問題分析型的魚骨圖及問題對策型的魚骨圖,互相對稱使用,因為一 個原因不只一個對策,故若使用上述方法則已被限制使用的方法。故若已找出對策後應分開使 用魚骨圖方為恰當。
例
中要因
大要因 中要因 小要因
中要因
小要因
特 性
中要因
中要因
大要因
小要因
大要因
小要因
制作記錄
特性要因图. 决定大要因 三. 决定中/小要因: 脑力激荡法
1. 能采取对策者 2. 有因果关系者,归于同一中、小支干內
四. 決定主要原因
4-6項影响問题点的主要原因 在所列出的原因中认为影响較大的划上紅圈,再从划上紅圈的原因中认
GEC Program
36
程序化计划的五个步骤:
步骤① 明确了解工作进行的目的及理由 (why)?为什么要做?
步骤② 确定要做哪些事项(what)?
步骤③ 谁来做?明确责任者及协助者 (who)?
步骤④ 什么时候要完成(when)?
步骤⑤ 明确如何进行及进行的顺序步骤
(how to)?
GEC Program
停机分析、设备维修记录、备件更换记 录 料:瓶盖扭拒、瓶盖暴晒、塑膜厚度 法:操作规程、研发标准 环:5s、国家法规、
生产指标的异常判断
R3数据 产量、超耗推移图 品保统计表 安全检查表
分组讨论
每组提出5个,现存的异常
解决异常的三个重点
1. 找出异常的真正的原因 2. 找出解决问题的重点对策 3. 订出异常解决的行动计划
問題 特性
要因
要因
要因
要因
特性要因图
为何要使用特性要因图?
使用图解法显示問題所有可能的原因,容易 发現其根源及重点,寻找对策
优点:
使討论人員,集中討讨论問题之实质內容, 而不是每人的观点或兴趣
易使人了解围绕某問題時所产生的集体智慧 与意見,有助于找到有效的解決方法
特性要因图
大要因
39
异常处理
步骤1 步骤2 步骤3 步骤4 步骤5 步骤6 步骤7 步骤8 步骤9
明确的目标、标准 发现异常 分析异常点的产生原因 确定要解决的课题 拟订对策 做出行动计划 执行行动计划 效果确认 标准化
GEC Program
42
异常判断及处理
-生产现场
生产现场要具备五大要素
人 机 料 法 环
生产重要指标
TQC T-时间、效率 Q-品质 C-成本 A-安全
何谓“异常”
与标准、目标发生偏离,存在差异 发现异常要及时解决
如何判断异常
显现的异常 (通过看、听、触、闻等感 观检查能发现的)
要做什么(what)? 谁来做(who)? 什么时候完成(when)? 各项行动如何进行(how to)?
GEC Program
41
特性要因图
目的:查明原因而不是症狀
何谓特性要因图?
一個問題的特性受到一些要因的影响時,我們
将這些要因加以整理成為有条理的图形,成为
特性要因图
要因
要因
要因
要因
隐藏的异常 (能通过工具、管理方法分 析能发现的)
显现的异常判断
人:生病、喝酒、精神状态等 机:停机、异响、备件损坏、异味、高
温等 料:颜色、规格、破损等 法:安全门、浓水排放、电导率、臭氧 环:温度、湿度、臭氧味道
隐藏的异常判断
人:工资福利、生涯规划、 机:点检表、定期保养维护、停机记录、