模具设计外文翻译---模具的发展
塑料模具发展中英文对照外文翻译文献

中英文对照外文翻译文献(文档含英文原文和中文翻译)外文:The development of plastic mouldChina's industrial plastic moulds from the start to now, after more than half a century, there has been great development, mold levels have been greatly enhanced. Mould has been at large can produce 48-inchbig-screen color TV Molded Case injection mold, 6.5 kg capacity washing machine full of plastic molds, as well as the overall car bumpers and dashboards, and other plastic mould precision plastic molds, the camera is capable of producing plastic mould , multi-cavity mold small modulus gear and molding mold. --Such as Tianjin and Yantai daysElectrical Co., Ltd Polaris IK Co. manufactured multi-cavity mold VCD and DVD gear, the gear production of such size precision plastic parts, coaxial, beating requirements have reached a similar foreign the level of product, but also the application of the latest gear design software to correct contraction as a result of the molding profile error to the standard involute requirements. Production can only 0.08 mm thickness of atwo-cavity mold and the air Cup difficulty of plastic doors and windows out of high modulus, and so on. Model cavity injection molding manufacturing accuracy of 0.02 to 0.05 mm, surface roughness Ra0.2 μ m, mold quality, and significantly increase life expectancy,non-hardening steel mould life up to 10~ 30 million, hardening steel form up to 50 ~ 10 million times, shorten the delivery time than before, but still higher than abroad,and the gap between a specific data table.Process, the multi-material plastic molding die, efficient multicolor injection mould, inserts exchange structure and core pulling Stripping the innovative design has also made great progress. Gas-assisted injection molding, the use of more mature technologies, such as Qingdao Hisense Co., Ltd., Tianjin factorycommunications and broadcasting companies, such as moldmanufacturers succeeded in 29 ~ 34-inch TV thick-walled shell, as well as some parts on the use of gas-assisted mould technology Some manufacturers also use the C-MOLD gas-assisted software and achieved better results. Prescott, such as Shanghai, such as the newcompany will provide users with gas-assisted molding equipment and technology. Began promoting hot runner mold, and some plants use rate of more than 20 percent, the general heat-thermal hot runner, or device, a small number of units with the world's advanced level of rigorous hot runner-needle device, a small number of units with World advanced level of rigorous needle-hot runner mould. However, the use of hot runner overall rate of less than 10%, with overseas compared to 50 ~ 80%, the gap larger. In the manufacturing technology, CAD / CAM / CAE technology on the level of application of a new level to the enterprise for the production of household appliances representatives have introduced a considerable number of CAD / CAM systems, such as the United States EDS UG Ⅱ, the United States Parametric Technology Pro / Engineer, the United States CV CADS5 company, the British company DOCT5 Deltacam, HZS's CRADE Japan, the company's Cimatron Israel, the United States AC-C-Tech Mold Company and Australia's MPA Mold flow Mold analysis software, and so on. These systems and the introduction of the software, although a lot of money spent, but in our country die industry, and achieving a CAD / CAM integration, and to support CAE technology to forming processes such as molding and cooling, such as computer simulation, and achieved certain The technical and economic benefits, promote and facilitate China's CAD / CAM technology. In recent years, China's own development of the plasticmould CAD / CAM system has achieved significant development, the main guarantor Software Engineering Institute, is the development of CAXA, Huazhong University of Science HSC5.0 development of the system and injection mold CAE software, and so on, these Die of domestic software with the specific circumstances in the application of computer and lower prices, and other characteristics, in order to further universal CAD / CAM technology has created good conditions.In recent years, China has been more extensive use of some new plastic mold steel, such as: P20, 3Cr2Mo, PMS, SM Ⅰ, SM Ⅱ, and the quality of life of mold has a direct significant impact on the overall use of the still less . Plastic Moulds standard model planes, such as standard putter and spring has given more applications, and there have been some of the commercialization of domestic hot runner system components. However, at present China Die level of standardization and commercialization in the general level of below 30 percent and foreign advanced industrial countries has reached 70 percent compared to 80 percent, still a large gap. Table 1, at home and abroad plastic mould technology comparison table? Domestic projects abroad cavity injection model mm0.02 accuracy of 0.005 ~ 0.01 ~ 0.05mm cavity surface roughness Ra0.01 ~ 0.05 μ mRa0.20 μ m non-hardened steel die life 10 to 60 million 10 ~ 30 million hardened steel die life 160 ~ 300 million of 50 ~ 100 million hot runner mould overall utilization rate of more than 80per cent less than 10 per cent level of standardization of 70 ~ 80% less than 30% of medium-sized plastic mould production cycle about a month 2 ~ 4 months in the mold industry in the amount of 30 to 40% 25 to 30% According to the parties concerned forecast, the market's overall vigorous mold is a smooth upward, in the next Die market, the development of plastic mould faster than the other Die, die in the proportion of industry will gradually improve. With the continuous development of the plastics industry, put on the plastic mold growing demands is a normal, and so sophisticated, large-scale, complex, long-life plastic mould development will be higher than the overall pace of development. At the same time, imports in recent years because of the mold, precision, large, complex, long-life die in the majority, therefore, reduce imports, increase Guochanhualu: perspective, in the mold of such high-end market share will gradually increase. The rapid development of theconstruction industry so that the various Profile Extrusion Die, PVC plastic pipe fittings Die Die market become a new economic growth point, the rapid development of highways, car tires also put a higher demand, radial tire Die, Die particularly active pace of development will also be higher than the overall average level of the plastic and wood, plastic and metal to make plastic molds in the automotive, motorcycle industry in the demand for huge household appliances industry in the "10th Five-Year Plan" period have greater development, especially refrigerators,air-conditionersand microwave ovens, and other parts of the great demand for plastic moulds, and electronics and communications products, in addition to audio-video products, such as color televisions, laptop computers and set-top boxes will be given a wider network development, which are Plastic Mold market is the growth point. Second, China's industrial and technological plastic mould the future direction of the major developments will include:1, raising large, sophisticated, complex, long-life mold design and manufacturing standards and proportion. This is due to the molding plastic mould products increasingly large, complex and high-precision requirements, as well as requirements for high productivity and the development of a multi-mode due.2, in the design and manufacture of plastic mould fully promote the use of CAD / CAM / CAE technology. CAD / CAM technology has developed into a relatively mature technology common in recent years CAD / CAM technology hardware and software prices has been reduced to SMEs generally acceptable level of popularity for further create good conditions; based on network CAD / CAM / CAE system integration structure the initial signs of emerging, and it will solve the traditional mixed CAD / CAM system can not meet the actual production process requirements of the division of collaboration; CAD / CAM software will gradually improve intelligence plastic parts and the 3-D mold design andprototyping process 3-D analysis will be in our plastic mould industries play an increasingly important role.3, promote the use of hot runner technology, gas-assisted injection molding technology and high-pressure injection molding technology. Using hot runner mould technology can improve the productivity and quality of parts and plastic parts can be substantial savings of raw materials and energy conservation, extensive application of this technology is a big plastic mould changes. Hot Runner components formulate national standards, and actively produce cheap high-quality components, the development of hot runner mold is the key. Gas-assisted injection molding product quality can be guaranteed under the premise of substantially lower cost. Currently in the automotive and appliance industries gradually promote the use of the Chiang Kai-shek. Gas-assisted injection molding of the ordinary than the traditional injection of more parameters need to identify and control, and its more commonly used in large, complex products, mold design and control more difficult, therefore, the development of gas-assisted molding flow analysis software It seems very important. On the other hand in order to ensure precision plastic parts to continue to study the development of technology and high-pressure injection molding and injection-compression molding mould and die technology is also very important.4, the development of new plastics molding technology and rapid economic mold. To adapt to more variety, less volume of production.5, and improve standardization of plastic mould standard parts usage. China's mold and die level of standard parts standardization still low, the gap between the large and foreign, to a certain extent constraining the development of industries in our country die, die to improve quality and reduce manufacturing costs Die, Die standard parts to vigorously promote the application. To this end, first of all, to formulate a unified national standards, and in strict accordance with the standards of production, secondly it is necessary to gradually scale production, to improve the commercialization of the standard of quality, and reduce costs; again it is necessary to further increase the standard specifications of varieties.6, Die application quality materials and advanced surface treatment technology for improving the quality of life and mold it is necessary.7, research and application of high-speed die measurement technology and reverse engineering. CMM-use 3D scanner or reverse engineering is the realization of plastic moulds CAD / CAM one of the key technologies.Research and Application of diversity, adjustment, cheap detection equipment is to achieve the necessary precondition for reverse engineering.译文:塑料模具的发展我国塑料模工业从起步到现在,历经半个多世纪,有了很大发展,模具水平有了较大提高。
模具设计外文翻译

Four-Cavity Hot-runner Stack Mold for Producing Automotive Inner SillTrim Made from PolypropyleneTo produce the inner sill trim used in an automobile as the transition the carpeting and vehicle frame, a four-cavity hot-runner stack mold was designed. Interconnecting tubes with a sliding fit inate the thermal expansion of the hot-runner systenm ..Depending on the car mold ,there is a left-hand and a right-hand version as well as a long and a short sill.General Mold DesignThe dimensions of the inner sills are 1250 mm*60 mm*2.5 mm, so that the parts are relatively large in area but with comparatively little material content (fig.1). The molded parts weigh 180 and 150 g respectively. Producing these parts by means of a stack mold was the obvious solution, as this doubles the output of the injection molding machine although the claming force requirements remain the same. The name of parts needed to obtain optimum machine utilization resulted in a four-cavity mold with two different cavities for the left-hand and right-hand versions (fig.2 to 5)) . The variation in the lengh of the trim is taken care of by interchangeable mold inserts. To achieve warp-free polypropylene copolymer (hostalon ppr 1042,supplier: Hoechst AG , Germany)required that the flow lengths be limited to approximately 170 mm. Five injection points are needed to along the inside of the trim.The design of the mold provides for simultaneous opening of the two part lines with the aid of two racks (40) and a pinion (36) for each side. As it is essential that no gate marks show on the front of the inside. The mounting attachment and spacers for the carpeting, which require ejector assistance for part release, are also located in this area ,however. Some of the mounting attachment are not at right angles to the part line ,so that hydraulically operated ejectors have been incorporated in hot-runner plates (3) and (5). The cylinders have been specially designed to permit utilization in the immediate vicinity of the hot-runner manifolds at temperatures of about 260 cMold Temperature ControlThree independent circuits have been provide in cach of the mold plates (2) and (3) as well as (5) and (6) for mold temperature control. This permits the temperatures of the outer regions of the 1250 mm long part to be controlled independently of the center region .At a mold width of 1500 mm and with several channels per plate, division into several circuits is also much more favorable with regard to pressure losses, which otherwise would occur.Hot-Rnner DesignA hot-runner system utilizing indirectly heated thermally conductive torpedodes has been selected to distriute melt within the mold.Incorporating the hydraulically operated ejectors in reduce the available space ,thereby forcing a partial reduction of the torpedo diameter.By modifying other design parameters, it was possible to compensate for the resulting change in heat transfer. The chosen injection points require the hot-runner manifold to be 888 mm long. To reduce the ensuing thermal expansion of approx .2 mm total, four indibidual manifold blocks 8 to 11 that are connected to one another by means ofmelt-conbeying pipes 12 to 14 with sliding fits have been provided. The feed pipes 15 divides the central manifold 11 into a right-hand and a left-hand half, each with its own termperature control Eachmaniflod contains four thermally conducting torpecdoes. The left-hand side of manifold block 11 contains only three cartridge heaters, the heating for the feed pipe compensating for any possible heat loss in this area. It is thus possible to vary the temperature at each gate.The melt-conveying pipes of the hot-runner system are fitted with connercially available heater bands with integral thermocouples. The hot-runner system thus contains five heater circuits for the manifold blocks and four heater circuits four the melt-conveying pipes 12 and 13 was not needed. These pipes received adequate heat from the neighboring manifold blocks 8 to 11. No measurable temperature loss occurred .All of the cartridge heaters have the same dimension of 200 mm*16 mm dia. and a heating capacity of 1250w. The watt density in this case lies at 12.5w/cm ,a value guaranteeing long cartridge life even with negligible play in the heater cartridge well. The result is an installed heating capacity of 5000w per manifold or heater circuit power is supplied bia a temperature controller with thyristorcontrol and an output current of 25 A The four controllers for the melt-conveying pipes were chosen to have the same specifications, although an output current of 6 to 10 A would have been adequate. This mesure that if one temperature controller fails, operation of the most important manifold can be ensured by a simple wiring change. The total installed heating capacity thus amounts to 25 kw. The manifolds were designed to have 250w per kg .with this specific heating capacity, balanced heating can be achieved for temperatures of up to approx. 300 c at a mold temperature of 40 c .The warm-up time is approximately 15 minutes, not including the soft start provided bu the controls. The integral soft start limits the supplied power to 50% and thus protects the cartridge heaters.The manifold popes have been produced from hot work steel to ensure that there is no loss in hardness at a possible temperature of 300 c .The sealing lips which slide with the thermal expansion are designed to provide favorable flow characteristics. They have additionally been protected against proven to be leakproof in operation.The threaded section has been produced with a toleranced press fit. The feed pipe 15 is providedwith a decom-pression bushing 16 at the end; this bushing has a stroke of about 5 mm.The length of the feed pipe is such that no dripping material can possibly drop into the parting line of the mold .The melt covers a distance of 940 mm to the farthest gates .The nearest gates are 530 mm away from the decompression bushing. During operation,the hot runner is completely filled with melt. The pressure is thus transmitted almost uniformly up to the individual gates in the stationary melt (or during creep flow ).The holding pressure is therefore also uniformly applied. When the melt is flowing ,however, thereis a pressure drop along the flow path. A moldflow analysis conduted with the objective of providing identical pressure losses in the flowing melt up to each gate yielded different diameters for the runner channels. The primary runner channel has a diameter of 18 mm ,while the vertical secondary runners have a diameter of 6 mm in the center of the mold and one of 8 mm in the outer regions.The torpedoed\s are 110 mm long,17 mm in diameter with an insulating gap of 7.5 mm. At a hot runner manifold temperature of 260 c ,the temperature at the torpedo tip is still at least 235 c. This value is sufficient for polypropylene. Start-up even after a prolonged production inter-ruption does not present any problems. The gate inserts 21 are insulated from the mold plate by a 0.5 mm annular air pocket.A CuCrZr alloy (material no.2.1293) wsa selected for the torpedoes (3) .The torpedoes have been chemically plated with hard nickel 4 to prevent a chemical reaction between the copper and the pp and then subsequently coated with thin ;ayer of chrome to give better adhesive properties.The four hot-runner manifolds 8 to 11 have been provided with central pressure pads 17and 18 which serve to locate the manifolds and transmit the resulting forces into the adjacent mold plates .Four dowel pins in grooves prevent the manifolds from turning. The manifolds are not bolted to the adjacent nozzle plates, but are allowed to float. The distance between the torpedo retainer bushings 20 has been over dimensioned by 0.1 mm in relation to the center frame 4 to ensure that the sustem remains leak-proof even in the eyent of plate deflection or an angular displacement . It was found that, in spite of the size of the mold, the increased thermal expansion of the hot-runner system with respect to the mold frame is sufficient to provide an difficient seal . As a result of the separation into four separate manifolds with axially sliding melt conveying pipes, hermal expansion perpendicular to the mold axis did not have to be taken into account. The torpedoes themselves were shortened by 0.4 mm when cold. As they heat up ,they pxpand into the precalculated insulating ;lates 22 clad with aluminum foil to reduce radiation losses.The total volume of melt in the system is approxi-mately 840; the volume of the four sill trim moldings is 650. The ensures a short residence time for the melt in the manifold system. Changing to a different color for the sill trim does not present any problems during production and can be accomplished quickly.MOLD CONSTRUCTIONMolds for processing of thermosetting molding compounds are generally heated electrically. The heat needed for the crosslinking reaction is drawn from the mold .once in contact with the cavity surface the viscosity of the melt passes through a minimum,i.e. the melt becomes so low in viscosity that it can penetrate into very narrow gaps and produce flash. The molds must thus exhibit very tight fit ,while at the same time providing for adequate venting of the cavity. These largely oppssing requirements are the reason that formation of flast cannot be completely climinated. Molds should be designed to be extremely stiff so that formation of flash are avoided. The use of pressure sensors to determine and monitor the injection pressures, on the basis of which the mechanical properties of the mold are calculated,is recom-mended. The pressure actually required depends on the size an geometry of the molded parts. Material selection is of great importance with regard to the life wcpectancy of the molds, a subject which must already be addressed during the quoting phase what was said in this regard for thermoplastics applies analogously here. Through-hardening steels are to be preferred for the part-forming surfaces and must exhibit a resistance to tempering consistent with the relatively high operating temperatures of stick,e.g. unsaturated polyester resins, steels with >13%chrome content have proven useful, e.g.tool steel no. 1.208, since the thermosetting molding compounds are sometimes modified with abrasive fillers, special attention must be given to the resulting wear. Fillers such as stone flour, mica, glass gibers and the like , for instance ,promote wear. In wear prone regions of the mold such as the gate, for example, metal carbide inserts should be provided. Other wear-prone mold components should gener-ally be designed as easily replace inserts.EJECTION/VENTINGDepending on the geometry of molded part and type of molding compound, different amounts ofdraft for part release must be provided,usually between 1 and 3 .At the time of ejection,theroset parts exhibit very little shrinkage because of the relatively high temperature. As a result, parts are not necessarily retained on the mold cores, but rather may be held in the cavity by a vacuum. To avoid problems during production, measures must be taken to ensure that the parts can always be ejected from the same half of the mold .。
模具毕业设计外文翻译(英文+译文)
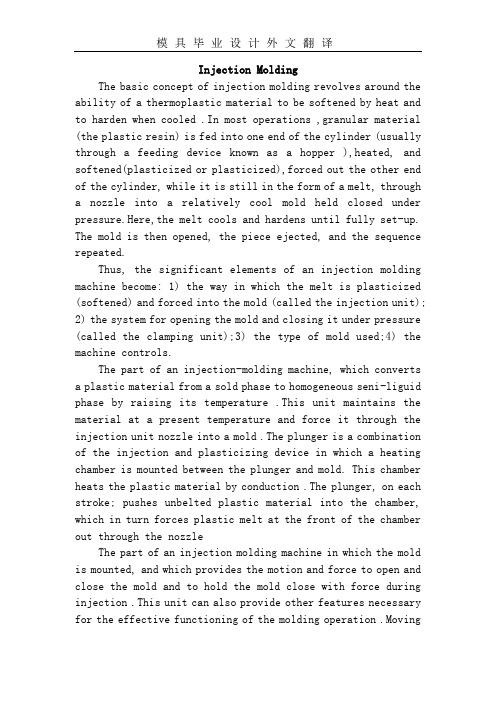
Injection MoldingThe basic concept of injection molding revolves around the ability of a thermoplastic material to be softened by heat and to harden when cooled .In most operations ,granular material (the plastic resin) is fed into one end of the cylinder (usually through a feeding device known as a hopper ),heated, and softened(plasticized or plasticized),forced out the other end of the cylinder, while it is still in the form of a melt, through a nozzle into a relatively cool mold held closed under pressure.Here,the melt cools and hardens until fully set-up. The mold is then opened, the piece ejected, and the sequence repeated.Thus, the significant elements of an injection molding machine become: 1) the way in which the melt is plasticized (softened) and forced into the mold (called the injection unit);2) the system for opening the mold and closing it under pressure (called the clamping unit);3) the type of mold used;4) the machine controls.The part of an injection-molding machine, which converts a plastic material from a sold phase to homogeneous seni-liguid phase by raising its temperature .This unit maintains the material at a present temperature and force it through the injection unit nozzle into a mold .The plunger is a combination of the injection and plasticizing device in which a heating chamber is mounted between the plunger and mold. This chamber heats the plastic material by conduction .The plunger, on each stroke; pushes unbelted plastic material into the chamber, which in turn forces plastic melt at the front of the chamber out through the nozzleThe part of an injection molding machine in which the mold is mounted, and which provides the motion and force to open and close the mold and to hold the mold close with force during injection .This unit can also provide other features necessary for the effective functioning of the molding operation .Movingplate is the member of the clamping unit, which is moved toward a stationary member. the moving section of the mold is bolted to this moving plate .This member usually includes the ejector holes and mold mounting pattern of blot holes or “T” slots .Stationary plate is the fixed member of the clamping unit on which the stationary section of the mold is bolted .This member usually includes a mold-mounting pattern of boles or “T” slots. Tie rods are member of the clamping force actuating mechanism that serve as the tension member of the clamp when it is holding the mold closed. They also serve as a gutted member for the movable plate .Ejector is a provision in the clamping unit that actuates a mechanism within the mold to eject the molded part(s) from the mold .The ejection actuating force may be applied hydraulically or pneumatically by a cylinder(s) attached to the moving plate, or mechanically by the opening stroke of the moving plate.Methods of melting and injecting the plastic differ from one machine to another and are constantly being implored .conventional machines use a cylinder and piston to do both jobs .This method simplifies machine construction but makes control of injection temperatures and pressures an inherently difficult problem .Other machines use a plasticizing extruder to melt the plastic and piston to inject it while some hare been designed to use a screw for both jobs :Nowadays, sixty percent of the machines use a reciprocating screw,35% a plunger (concentrated in the smaller machine size),and 5%a screw pot.Many of the problems connected with in ejection molding arise because the densities of polymers change so markedly with temperature and pressure. thigh temperatures, the density of a polymer is considerably cower than at room temperature, provided the pressure is the same.Therefore,if molds were filled at atmospheric pressure, “shrinkage” would make the molding deviate form the shape of the mold.To compensate for this poor effect, molds are filled at high pressure. The pressure compresses the polymer and allows more materials to flow into the mold, shrinkage is reduced and better quality moldings are produced.Cludes a mold-mounting pattern of bolt holes or “T” slots. Tie rods are members of the clamping force actuating mechanism that serve as the tension members of clamp when it is holding the mold closed. Ejector is a provision in the calming unit that actuates a mechanism within the mold to eject the molded part(s) form the mold. The ejection actuating force may be applied hydraulically or pneumatically by a cylinder(s) attached to the moving plate, or mechanically by the opening stroke of the moving plate.The function of a mold is twofold: imparting the desired shape to the plasticized polymer and cooling the injection molded part. It is basically made up of two sets of components: the cavities and cores and the base in which the cavities and cores are mounted. The mold ,which contains one or more cavities, consists of two basic parts :(1) a stationary molds half one the side where the plastic is injected,(2)Moving half on the closing or ejector side of the machine. The separation between the two mold halves is called the parting line. In some cases the cavity is partly in the stationary and partly in the moving section. The size and weight of the molded parts limit the number of cavities in the mold and also determine the machinery capacity required. The mold components and their functions are as following:(1)Mold Base-Hold cavity (cavities) in fixed, correctposition relative to machine nozzle.(2)Guide Pins-Maintain Proper alignment of entry into moldinterior.(3)Spree Bushing (spree)-Provide means of entry into moldinterior.(4)Runners-Conroy molten plastic from spree to cavities.(5)Gates-Control flow into cavities.(6)Cavity (female) and Force (male)-Control the size,shape and surface of mold article.(7)Water Channels-Control the temperature of mold surfacesto chill plastic to rigid state.(8)Side (actuated by came, gears or hydrauliccylinders)-Form side holes, slots, undercuts and threaded sections.(9)Vent-Allow the escape of trapped air and gas.(10)Ejector Mechanism (pins, blades, stripper plate)-Ejectrigid molded article form cavity or force.(11)Ejector Return Pins-Return ejector pins to retractedposition as mold closes for next cycle.The distance between the outer cavities and the primary spree must not be so long that the molten plastic loses too much heat in the runner to fill the outer cavities properly. The cavities should be so arranged around the primary spree that each receives its full and equal share of the total pressure available, through its own runner system (or the so-called balanced runner system).The requires the shortest possible distance between cavities and primary sprue, equal runner and gate dimension, and uniform culling.注射成型注射成型的基本概念是使热塑性材料在受热时熔融,冷却时硬化,在大部分加工中,粒状材料(即塑料树脂)从料筒的一端(通常通过一个叫做“料斗”的进料装置)送进,受热并熔融(即塑化或增塑),然后当材料还是溶体时,通过一个喷嘴从料筒的另一端挤到一个相对较冷的压和封闭的模子里。
模具设计与制造外文文献及翻译

The mold designing and manufacturingThe mold is the manufacturing industry important craft foundation, in our country, the mold manufacture belongs to the special purpose equipment manufacturing industry. China although very already starts to make the mold and the use mold, but long-term has not formed the industry. Straight stabs 0 centuries 80's later periods, the Chinese mold industry only then drives into the development speedway. Recent years, not only the state-owned mold enterprise had the very big development, the three investments enterprise, the villages and towns (individual) the mold enterprise's development also rapid quietly.Although the Chinese mold industrial development rapid, but compares with the demand, obviously falls short of demand, its main gap concentrates precisely to, large-scale, is complex, the long life mold domain. As a result of in aspect and so on mold precision, life, manufacture cycle and productivity, China and the international average horizontal and the developed country still had a bigger disparity, therefore, needed massively to import the mold every year .The Chinese mold industry must continue to sharpen the productivity, from now on will have emphatically to the profession internal structure adjustment and the state-of-art enhancement. The structure adjustment aspect, mainly is the enterprise structure to the specialized adjustment, the product structure to center the upscale mold development, to the import and export structure improvement, center the upscale automobile cover mold forming analysis and the structure improvement, the multi-purpose compound mold and the compound processing and the laser technology in the mold design manufacture application, the high-speed cutting, the super finishing and polished the technology, the information direction develops .The recent years, the mold profession structure adjustment and the organizational reform step enlarges, mainly displayed in, large-scale, precise, was complex, the long life, center the upscale mold and the mold standard letter development speed is higher than the common mold product; The plastic mold and the compression casting mold proportion increases; Specialized mold factory quantity and its productivity increase; "The three investments" and the private enterprise develops rapidly; The joint stock system transformation step speeds up and so on. Distributes from the area looked,take Zhejiang Delta and Yangtze River delta as central southeast coastal area development quickly to mid-west area, south development quickly to north. At present develops quickest, the mold produces the most centralized province is Guangdong and Zhejiang, places such as Jiangsu, Shanghai, Anhui and Shandong also has a bigger development in recent years.Although our country mold total quantity had at present achieved the suitable scale, the mold level also has the very big enhancement, after but design manufacture horizontal overall rise and fall industry developed country and so on Yu De, America, date, France, Italy many. The current existence question and the disparity mainly display in following several aspects:(1) The total quantity falls short of demandDomestic mold assembling one rate only, about 70%. Low-grade mold, center upscale mold assembling oneself rate only has 50% about.(2) the enterprise organizational structure, the product structure, the technical structure and the import and export structure does not gatherin our country mold production factory to be most is from the labor mold workshop which produces assembles oneself (branch factory), from produces assembles oneself the proportion to reach as high as about 60%, but the overseas mold ultra 70% is the commodity mold. The specialized mold factory mostly is "large and complete", "small and entire" organization form, but overseas mostly is "small but", "is specially small and fine". Domestic large-scale, precise, complex, the long life mold accounts for the total quantity proportion to be insufficient 30%, but overseas in 50% above 2004 years, ratio of the mold import and export is 3.7:1, the import and export balances the after net import volume to amount to 1.32 billion US dollars, is world mold net import quantity biggest country .(3) The mold product level greatly is lower than the international standardThe production cycle actually is higher than the international water broad product level low mainly to display in the mold precision, cavity aspect and so on surface roughness, life and structure.(4) Develops the ability badly, economic efficiency unsatisfactory our country mold enterprise technical personnel proportion lowThe level is lower, also does not take the product development, and is frequent in the passive position in the market. Our country each mold staff average year creation output value approximately, ten thousand US dollars, overseas mold industry developed country mostly 15 to10, 000 US dollars, some reach as high as 25 to10, 000 US dollars, relative is our country quite part of molds enterprises also continues to use the workshop type management with it, truly realizes the enterprise which the modernized enterprise manages fewTo create the above disparity the reason to be very many, the mold long-term has not obtained the value besides the history in as the product which should have, as well as the most state-owned enterprises mechanism cannot adapt the market economy, but also has the following several reasons: .(1) Country to mold industry policy support dynamics also insufficiently Although the country already was clear about has promulgated the mold profession industrial policy, but necessary policy few, carried out dynamics to be weak. At present enjoyed the mold product increment duty enterprise nation 185; the majority enterprise still the tax burden is only overweight. The mold enterprise carries on the technological transformations introduction equipment to have to pay the considerable amount the tax money, affects the technology advancement, moreover privately operated enterprise loan extremely difficult.(2) Talented person serious insufficient, the scientific research development and the technical attack investment too urinemold profession is the technology, the fund, the work crowded industry, along with the time progress and the technical development, grasps the talented person which and skilled utilizes the new technology exceptionally short, the high-quality mold fitter and the enterprise management talent extremely is also anxious. Because the mold enterprise benefit unsatisfactory and takes insufficiently the scientific research development and the technical attack, the scientific research unit and the universities, colleges and institutes eye stares at is creating income, causes the mold profession invests too few in the scientific research development and the technical attack aspect, causes the mold technological development step doe not to be big, progresses does not be quick.(3) The craft equipment level is low, also is not good, the using factor is low. Recent years ,our country engine bed profession progressed quickly, has been able to provide the quite complete precision work equipment, but compared with the overseas equipment, still had a bigger disparity. Although the domestic many enterprises have introduced many overseas advanced equipment, but the overall equipment level low are very more than the overseas many enterprises. As a result of aspect the and so on system and fund reason, introduces the equipment not necessary, the equipment and the appendix not necessary phenomenon are extremely common, the equipment utilization rate low question cannot obtain the comparatively properly solution for a long time .(4) Specialization, standardization, commercialized degree low, the cooperation abilityBecause receives "large and complete" "small and entire" the influence since long ago, mold specialization level low, the specialized labor division is not careful, the commercialized degree is low. At present domestic every year produces mold, commodity mold minister 40% about, other for from produce uses for oneself. Between the molds enterprise cooperates impeded, completes the comparatively large-scale mold complete task with difficulty. Mold standardization level low, mold standard letter use cave rare is low also to the mold quality, the cost has a more tremendous influence, specially has very tremendous influence.(5) To the mold manufacture cycle) the mold material and the mold correlation technology fallThe mold material performance, the quality and the variety question often can affect the mold quality, the life and the cost, the domestically produced molding tool steel and overseas imports the steel products to compare has a bigger disparity. Plastic, plate, equipment energy balance, also direct influence mold level enhancement.At present, our country economy still was at the high speed development phase, on the international economical globalization development tendency is day by day obvious, this has provided the good condition and the opportunity for the our country mold industry high speed development. On the one hand, the domestic mold market will continue high speed to develop, on the other hand, the mold manufacture alsogradually will shift as well as the transnational group to our country carries on the mold purchase trend to our country extremely to be also obvious. Therefore, will take a broad view the future, international, the domestic mold market overall development tendency prospect will favor, estimated the Chinese mold will obtain the high speed development under the good market environment, our country not only can become the mold great nation, moreover certainly gradually will make the powerful nation to the mold the ranks to make great strides forward. "15" period, the Chinese mold industry level not only has the very big enhancement in the quantity and the archery target aspect, moreover the profession structure, the product level, the development innovation ability, enterprise's system and the mechanism as well as the technology advancement aspect also can obtain a bigger development .The mold technology has gathered the machinery, the electron, chemistry, optics, the material, the computer, the precise monitor and the information network and so on many disciplines, is a comprehensive nature multi-disciplinary systems engineering. The mold technology development tendency mainly is the mold product to larger-scale, precise, more complex and a more economical direction develops, the mold product technical content unceasingly enhances, the mold manufacture cycle unceasingly reduces, the mold production faces the information, is not having the chart, is fine, the automated direction develops, the mold enterprise to the technical integration, the equipment excellent, is producing approves the brand, the management information, the management internationalization direction develops. Mold profession in "十15" period needs to solve the key essential technology should be the mold information, the digitized technology and precise, ultra fine, high speed, the highly effective manufacture technology aspect breakthroughAlong with the national economy total quantity and the industry product technology unceasing development, all the various trades and occupations to the mold demand quantity more and more big, the specification more and more is also high.Although mold type many, but its development should be with emphasis both can meet the massive needs, and has the comparatively high-tech content, specially at present domestic still could not be self-sufficient, needs the massive imports the mold and can represent the development direction large-scale, precise, is complex, the longlife mold. Standard letter type, quantity, level and the production of the mold have significant influence to the entire mold profession development. Therefore, some important mold standard letters also must prioritize, moreover its development speed should quickly to the mold development speed, like this be able unceasingly to raise our country mold standardization level, thus improves the mold quality, reduces the mold production cycle, reduces the cost. Because our country mold product holds the bigger price superiority in the international market, therefore regarding the exportation prospect good mold product also should take key develops. According to the above required quantity big, the technical content is high, represents the development direction, the export prospect good principle choice prioritize product, moreover chooses the product to have at present to have the certain technology base, belongs has the condition, has the product which the possibility develops .模具设计与制造模具是制造业的重要工艺基础,在我国模具制造属于专用设备制造业。
模具制造中英文翻译

Modern mold makingI.The stamping die development history and status of technologyIn 1953, the Changchun First Automobile Works in China for the first time established a die shop, the car plant in 1958 began manufacturing automotive panel die. 60 years of the 20th century began producing fine blanking dies. Come a long road of development, China has formed about 300 billion (not including Hong Kong, Macao and Taiwan statistics.) Production capacity of various types of stamping dies. Formed, such as Ningbo and Zhejiang HUANGYAN region "Die village"; Guangdong Corporation and some large rapid rise of township enterprises, K el o n, M id e a, K on ka and other groups have established their own mold manufacturing center; joint ventures and wholly foreign-owned the mold companies now have thousands. With the pace with international standards continues to accelerate, increasing market competition, production and design of the mold has been growing recognition that product quality, cost, and new product development capacities. Mold manufacturing technology to measure a country's manufacturing sector has become an important indicator of the level, and largely determine the survival space. At present, China stamping die, whether in quantity or in quality, technology and other capabilities have made significant progress, but with national needs and the world advanced level, the gap is still great. In the international competition situation, I had the mold industry has rapidly developed, many specialized research centers continue to die set up, mold steel of the structure and made significant achievements, but there is still a big gap. First, imports of high-tech mold most of the large precision molds, mold and exports most of the lower middle and low-tech die, so high-tech high-grade die stamping die market, the overall satisfaction rate is lower than satisfaction rate, which mold development has lagged behind the production of stamping parts, and low-technology market to meet the rate of middle and low die stamping die is higher than the overall market to meet the rate; second is due to the price of the mold is much lower than international market prices, has some competition force, so its prospects in the international market; third in recent years, Hong Kong-and Taiwan-owned, foreign-funded enterprises in China developed rapidly in a large number of these enterprises stamping dies produced for own use no precise statistics, it is not included in the figures being.II. Modern mold manufacturing technology developmentThe development of modern technology should die mold products to meet the "short delivery time", "high precision", "good quality", "low price" request for service. Urgent need to develop to meet this requirement as a number of(1) to comprehensively promote universal DBD / DBM / DBE technologyDie DBD / DBM / DBE technology is the development direction of mold design and manufacturing. With the computer software development and progress, universal DBD / DBM / DBE technology, conditions are ripe, the businesses will increase DBD / DBM technical training and technical service efforts; further expand the scope ofDBE technology. The development of computers and networks are making DBD / DBM / DBE technology trans-regional, cross-enterprise, campus-wide in the industry as possible to promote and achieve re-integration of technical resources to enable virtual manufacturing possible.(2) High-speed millingThe development of foreign high-speed milling process in recent years, significantly improve the processing efficiency, and to get a high surface finish. In addition, the module can also be processed with high hardness, but also with low temperature rise, thermal deformation and so on. High-speed milling technology, automotive, home appliance manufacturing industry in the large cavity mold injected new vitality. It currently has more agile, intelligent, integrated direction.(3) die scanning and digitizing systemHigh-speed scanner provides scanning system and mold from the model or in kind to the processing of the scanned model of the desired number of features required, greatly reducing the manufacturing cycle in the development of mold. Some quick scan system can be quickly installed in existing CNC milling machine and machining center, for fast data acquisition, automatic generation of a variety of CNC machining process, the DBD data in different formats, for mold manufacturing "reverse engineering . "(4) the degree of standardization to improve dieDegree of standardization of the mold is increasing, estimates that the current use of standard mold coverage has reached about 30%. Developed countries is generally about 80%.(5) high-quality materials and advanced surface treatment technologyApplication of high quality steel and the corresponding surface treatment technology to improve the life of the mold it is very necessary. Mold heat treatment and surface treatment can fully mold steel material properties play a key part. Direction of development of mold heat treatment is the use of vacuum heat treatment. In addition to the mold surface should improve the development of advanced technologies such as laser surface treatment.(6) Mold PolishingAutomation, intelligent mold surface quality of mold life, the appearance of quality parts and so have a greater impact of automation and intelligence of the grinding and polishing methods replace the existing manual in order to improve the quality of the mold surface is important trends.(7) die development of automatic processing systemThis is our long-term development goals mold industry. Automatic mold machine processing system should be more than the rational combination; with accompanying plate positioning fixture or positioning; a complete equipment, tool CNC database; a complete CNC flexible synchronization system; a quality monitoringand control system. Of course, as the user to choose the right equipment, if the selection properly, not only can not make money but make the machine work into the bitter situation.III. Modern mold manufacturing technology trendsDie technology is mainly towards the future development trend of information technology, high-speed high-precision production and development. Therefore, the design technology, the development focus is to promote DBD / DBE / DBM technology, and continue to improve efficiency, especially in sheet metal forming process of the computer simulation analysis. Die DBD, DBE technology should be declared human, integration, intelligence and network direction, and improve the mold DBD, DBM system-specific level. To improve the DBD, DBE, DBM technology, establish a complete database and development of the mold expert systems and improve software usability is very important.From the processing technology, the development focused on high-speed processing and precision machining. At present, the development of highly processed high-speed milling, high speed polishing and high-speed electronic processing and rapid tooling technologies. At present, the development of precision machining parts precision mold and the surface roughness of less 1μm Pa ≤ 0.1μm variety of precision machining.IV.the modern mold manufacturing1.CAD/CAE/CAM computer-aided design, simulation, manufacturing integration CAD / CAE / CAM integration, integration technology is the most advanced modern mold making the most reasonable mode of production. Use of computer-aided design, support engineering and manufacturing systems, according to the respective mold parts designed to prepare the NC machining of parts from design to manufacturing process is an inevitable process, which is from CAD / CAE / CAM system carried out, The processing line cable input directly from the processing machine, can be used in the preparation of procedures of processing the system analog functions, will be part tool, tool holder, fixture, platform and tool speed, path, etc. are displayed, to check the program prepared correctness. In short the CAD / CAE / CAM system development and simulation of processing can not fully understand the problems identified, resulting in processing prior to prepare the complete set of processing change work, which for the efficient and accurate processing of the mold has a very important part .2. Advanced equipment in the modern mold making roleThe inevitable trend of modern mold making, machining is possible to replace the manual process, especially now that CNC lathes, multi-axis machine tools, CNC mold engraving machine, EDM machine, CNC precision grinding machines, coordinate measuring machines, scanners and other modern equipment widely used in factories, but most of these devices are basically the application of the procedures used CAD / CAE / CAM system to produce, the operator of work procedures in accordance with the provisions of work piece clamping, with a cutting tool and operation of the machine will be able to automatically complete the processing tasks,and created the ideal mold parts or complete the processing operation for the next part.3. Die materials and surface treatment technologyDue to improper selection and use of materials, resulting in premature failure of the mold, which accounts for more than 45% die failure. Price structure throughout the mold, the materials, the proportion of small, generally 20% to 30%, therefore, the choice of high quality steel and application of surface treatment technology to improve the life of the mold it is very necessary. For tool steel, the ESR technique to be used, such as the use of powder metallurgy high speed steel powders manufactured. Variety of different specifications tool steel, refined products, products of, try to shorten the delivery time is also an important trend.Mold heat treatment of the main trends: the infiltration of a single element to the multi-element penetration, complex permeability (such as TD method) development; by the general spread of the CVD, PVD, PCVD, ion penetration, ion implantation and other direction; addition, the current laser enhanced glow plasma technology and electroplating (plating) and other anti-corrosion technology to strengthen more and more attention.V.reverse engineeringReverse engineering is the first of the parts (the processing of the product) to scan the CAD data generated in multiple formats, and then in the other CAD / CAE / CAM software in the modified design, the technology is the most popular modern mold manufacturing mold manufacturing technology. mold manufacturing company dedicated to development and production of the scanning system, it can be successfully applied to reverse engineering, mold manufacturing, it can not only improve the performance of CNC machine tools, expanding the function of CNC machine tools, CNC machine tools but also improve efficiency., Renscan200, Cyclone high-speed scanner has been Qingdao H a I e r, Jinan Q I n g q i, national mold center and other units started.VI. Summary and OutlookWith the development and progress of computer software, CAD / CAE / CAM technology is getting more mature, and its application in the modern mold will become more widespread. Can be expected in the near future, mold manufacturing to separate from the machine manufacturing industry, and independent national economy to become an indispensable pillar industries, while also further promote the integration of the mold manufacturing technology, intelligence, beneficiary , efficient direction.现代模具制造一.冲压模具发展历史和技术水平状况1953年,长春第一汽车制造厂在中国首次建立了冲模车间,该汽车厂于1958年开始制造汽车覆盖件模具。
模具制造中英文对照外文翻译文献

中英文翻译英文原文:High-speed cutting processing in mold manufactureapplicationAbstractThe current mold application is widespread, also had the very big development with it related die making technology. At present, used the high-speed cutting production mold already to become the die making the general trend. In some mold Manufacturer, the high speed engine bed big area substitution electrical discharge machine, the high-speed cutting production mold already gradually became the die making the general trend. It can improve mold's size, the shape and the surface roughness, reduces even omits the manual sharpening, thus reduces production cost and the reduction manufacturing cycle. This article through to the traditional mold processing craft and the high speed mold processing craft's contrast, elaborated the high-speed cutting processing superiority. In the article also briefly introduced the high-speed cutting processing in the processing craft aspect key technologies.Keywords High-speed cutting Grinding tool Grinding tool processing Process technology1 Introduction1.1 IntroductionAlong with the advance in technology and the industry swift development, the mold already became in the industrial production to use the extremely widespread main craft to equip now. The mold takes the important craft equipment, in Industry sectors and so on consumable, electric appliance electron, automobile, airplane manufacture holds the pivotal status. The manufactured products components rough machining 75%, the precision work 50% and the plastic parts 90% will complete by the mold. At present the Chinese mold market demand has reached 50,000,000,000 Yuan scales, our country die making market potential is huge. The mold is one kind of special-purpose tool, uses in forming () each metal or the nonmetallic material needs the components the shape product, this kind of special-purpose tool general designation mold. The mold is in the industrial production the most foundation equipment, is realizes the few cuttings and the non-cutting essential tool. The mold has widely used in the industrial production each domain, like the automobile, the motorcycle, the domestic electric appliances, the instrument, the measuring appliance, the electron and so on, in them 60%~80% components need the mold to carry on the manufacture; The highly effective production in enormous quantities's, bolt, nut and gasket standard letters and so on plastic also need the mold to produce; The engineering plastics, the powder metallurgy, the rubber, the alloy compression casting, the glass formation and so on need to use the mold to take shape.1.2 High-speed cutting process technologyAs the name suggests, the high-speed cutting, first is the high speed, namely must have the high spindle speed, for instance 12000r/min, 18000r/min, 30000r/min, 40000r/min, even also had a higher rotational speed still in the experiment; On the other hand, should also have the bigger to feed quantity, like 30000mm/min, 40000mm/min, even 60000mm/min; Has is after again the rapid traverse, trades fast the knife, the main axle trade the knife, from the static state arrives its needs rotational speed rise time and so on, only then achieved the above standards to be able to call it high speed.Next is must aim at the different processing object, the different degree of hardness, thedifferent material quality, the different shape to choose the corresponding reasonable parameter, but cannot pursue constantly to be high speed and be high speed, regarding the die space processing, the shape is specially complex, but the cutting tool diameter is also small time, because cutting tool's path is not the simple translation, but is the curve, even has right angle corner time, technological parameter rational especially important, if because wants to maintain the identical feed rate carries on the orthogonal cutting, will not be able to do well will cause as a result of the engine bed moving part's huge inertia the cutting tool will make when the bend angle movement to break suddenly, but the variable motion can, becauseMovements and so on acceleration and deceleration create the thickness of cutting the instantaneous change, but causes the cutter change to enable the work piece surface to have cuts, from this causes the processing drop in quality, therefore, in view of the different processing object, needs the programmers to choose the reasonable cutting tool path, optimized cutting parameter; On the other hand, according to needs to choose the suitable cutting velocity, only then can display the high-speed cutting truly like the strong point.The high-speed cutting (HSC) is an advanced technique of manufacture which for the past ten years rapidly rises. Because the high-speed cutting technology has the cutting efficiency to be high, the processing quality high, can process the hard steel stock and the good efficiency directly, causes profession and so on aviation, mold, automobile, light industry and information production efficiencies and the manufacture quality obviously enhances, and causes the processing craft and the equipment corresponding renewal. Therefore is similar to the numerical control technology is the same, the high-speed cutting and the high speed processing have become in the 21st century a machine-building industry influence profound technological revolution. At present, adapts the HSC request high speed machining center and other high speed numerically-controlled machine tool has assumed the popularization tendency in the developed country, our country recently is also speeding up the development.The high-speed cutting processing is faces for the 21st century a high technology and new technology, it is one kind is different with the traditional processing processing way. Compares with it, the high-speed cutting processing main axle rotational speed high, cuts high for the speed, the cutting quantity is small, but in the unit time material excises the quantity to increase 3 ~ 6 times actually. It take the high efficiency, the high accuracy and the high surface quality as the basic characteristic, in profession and so on in automobile industry, aerospace, mold manufacture and instrument measuring appliance has obtained the increasingly widespread application, and has obtained the significant technology economic efficiency, is the contemporary advanced manufacture technology important constituent.When with traditional way processing mold, often uses the electric spark machining, but the electrode design and makes itself is the technological process which time-consuming takes the trouble. But after uses the high-speed cutting processing, because the narrow and small region processing realization and the high grade superficial result, let the electrode the utilization ratio reduce greatly. Moreover, makes the electrode with the high speed mill also to be possible to make the production efficiency to enhance to a new scale.The major part mold may use the high-speed cutting technology to process, like the forging die, the compression casting mold, cast with the blow molding mold and so on. Hammers the cavity body shallowly, the cutting tool life is long; Compression casting mold size moderate, the productivity is high; Casts with the blow molding mold general size small, quite is economical.2 the high-speed cutting processing mold relative traditionprocesses the mold the superiority2.1 Enhances the productivityIn the high-speed cutting the main axle rotational speed and enters for the speed enhancement, may enhance material removing rate. At the same time, theThe high-speed cutting processing permission use big to feed rate, enhances 5~10 times compared to the convention machining, the unit interval/unit time material excision rate may enhance 3~6 times, the process period may reduce greatly. This may use in processing needs to excise the metal massively the components, specially has the very vital significance regarding the aviation industry.2.2 Improvement processing precishon and surface qualhtyThe high rpeed engine bed must have high performance and so on rigidity and high accuracy, at the same time because cutting force low, the work piece thermal deformation reduces, the cutting tool distorts slightly, the high-speed cutting processing precision Is very high. Depth of cut small, but enters for the speed quickly, the processing surface roughness is very small, cuts when the aluminum alloy may reach Ra0.4 ~ 0.6, when cutting steel stock may reach Ra0.2 ~ 0.4.Compares with the conventional cutting, when high-speed cutting processing the cutting force may reduce 30% at least, this may reduce the processing regarding the processing rigidity bad components to distort, causes some thin wall class fine work piece the machining into possible. Because revolves high speed time the cutting tool cuts the excitation frequency is far away from the craft system's forced oscillation, has guaranteed the good processing condition. Because the cutting force is too small, cut the hot influence to be small, causes the cutting tool, the work piece distortion to be small, maintained the size accuracy, moreover also caused the friction between the cutting tool work piece changes is small, the cutting destruction level thinned, the residual stress was small, has realized the high accuracy, the low roughness processing.2.3 The reduced cutting produces quantity of heatBecause the high-speed cutting processing is the shallow cutting, simultaneously the feed rate is very quick, the knife edge and the work piece contact length and the contact duration were short,reduced the knife edge and the work piece heat conduction, has avoided when the traditional processing met everywhere in the cutting tool and the work piece to have the big calorimetry shortcoming, guaranteed that the cutting tool worked under the temperature not high condition, lengthened cutting tool's service life. As shown in Figure 1, A is time the high-speed cutting processing heat conduction process, B is the traditional processing heat conduction process.Fig.1 high speed processing and traditional processing heat conductionThe high-speed cutting processing process is extremely rapid, 95% above cutting quantity of heat are extremely few, components not because the temperature rise will cause the warp or the inflation distortion. The high-speed cutting is suitable specially for the processing easy thermal deformation components. Is low regarding the processing melting point the metal which, easy to oxidize (for example magnesium), the high-speed cutting has certain significance.2.4 advantageoued in the processing thin wall componentsTime high-speed cutting's cutting force is small, has the high stability, but the high quality processes the thin wall components. Uses as shown in Figure 2 the lamination down milling the processing method, but high-speed cutting wall thickness 0.2mm, wall high 20mm thin wall components. This time, the knife edge and the work piece contact duration was short, has avoided the sidewall distortion.Figure.2 high-speed cutting thin wall components2.5 change the part substitutes certain crafts, like electric spark machining, abrasive machining and so onHigh strength and the high degree of hardness's processing is also a high-speed cutting major characteristic, at present, the high-speed cutting has been possible the work hardness to reach HRC60 the components, therefore, the high-speed cutting can process after the heat treatment hardens the work piece. In the tradition processes in mold's craft, before the precision work, hardens the work piece after the heat treatment to carry on the electric spark machining, may omit in the die making craft with the high-speed cutting processing substitution tradition cutting's processing method the electric spark machining, simplified the processing craft and the cost of investment.the mold's size, the shape and the surface roughness are very important, if after processing the mold cannot meet the requirements the quality precision, needs the massive handworks to rub repairs the work, the handwork rubs repairs can obtain the good surface quality, but it will affect mold's size and the shape precision. Therefore must omit as far as possible in the mold processing rubs manually repairs, improves the mold quality, reduces the production cost and the manufacturing cycle.Figure 3 is the traditional mold processing process: The semifinished materials -> rough machining -> semi-finishing -> heat treatment hardens -> the electric spark machining -> precision work -> to rub manually repairs. Figure 4 is the high speed mold processing process: Hardened semifinished materials -> rough machining -> semi-finishing -> precision work.Figure.3 the traditional mold processes processFigure 4 the high speed mold processes processin Figure 4, in the high speed mold machining process reduced two technological processes,probably reduces the process period 30%~50%. In the traditional processing craft's electric spark machining forms the hardened level easily in the melting processing surface layer, degree of hardness may reach 1000Hv, brings the difficulty for the following machining and the abrasive machining. The electric spark machining also easy to cause the surface layer fatigue cracking and cutting tool's breakage.2.6 Economic efficiency remarkable enhancementSynthesis above all sorts of merits, namely: The comprehensive efficiency will improve, the quality enhances, the working procedure simplifies, the engine bed investment and the cutting tool investment as well as the maintenance cost increase and so on, will use the high-speed cutting craft to cause the synthesis economic efficiency remarkable enhancement.3 high-speed cutting processing craft essential technologyThe high speed engine bed and the high speed cutter are the realization high-speed cutting premise and the basic condition, has the strict request in the high-speed cutting processing to the high speed engine bed performance and the cutting tool material choice.In order to realize the high-speed cutting processing, uses the high flexible high speed numerical control engine bed, the processing center generally, also some use special-purpose high speed mills, drilling machine. At the same time the engine bed has the high speed main axle to be systematic and the high rapid advance or progress gives the system, the high main axle rigidity characteristic, the high accuracy localization function and the high accuracy insert makes up the function, specially the circular arc high accuracy inserts makes up the function.The high-speed cutting cutting tool and ordinary processes the cutting tool the material to have is very greatly different. The main use cutting tool material has the hard alloy, the crystal combination diamond (PCD), the crystal combination cube boron nitride (PCBN) and the ceramics and so on.The high-speed cutting craft technology also is carries on the high-speed cutting processing the key. The cutting method chooses is improper, can make the cutting tool to intensify the attrition, cannot achieve the high speed processing completely the goal. The practice proved, if only then the high speed engine bed and the cutting tool but do not have the good craft technology to make the instruction, the expensive high-speed cutting processing equipment cannot fully play the role. The high-speed cutting processing craft essential technology mainly includes the cutting method and the cutting parameter choice optimization.a. Cutting way choiseIn the high-speed cutting processing, should select the down milling processing as far as possible, because in down milling time, the cutting tool just cut into the thickness of chip which the work piece produces to a big way, afterward reduces gradually. When up milling, the cutting tool just cut into the thickness of chip which the work piece produces to be smallest, afterward the accumulation, increased the cutting tool and the work piece friction like this gradually, has the big calorimetry on the knife edge, therefore produces in the up milling quantity of heat when down milling are more than, the radial force also greatly increases. Meanwhile in the down milling, the knife edge main compression stress, but when the up milling the knife edge tension stress, the stressful condition is bad, reduced cutting tool's service life, the down milling and the up milling the cutting tool cuts into the work piece the process, as shown in Figure 5.Figure.5 the cutting tool cuts into the work piece the process hintb. Maintains constant metal removing rateThe high-speed cutting processing is shallowly suitable for shallowly to cut the depth, the depth of cut should not surpass 0.2/ 0.2mm (ae/Ap), this is for avoids the cutting tool the position deviation, guarantees processes the mold the geometry precision. Maintains constant metal removing rate, guaranteed adds on the work piece the cutting load is constant, by obtains following several good processing effect: (1) may maintain constant cutting load; (2) may maintain the scrap size constant; (3) has the good hot shift; (4) the cutting tool and the work piece maintain at the cold condition; (5) does not need skilled to operate for the quantity and the main axle rotational speed;(6) may lengthen the cutting tool the life; (7) can guarantee the good processing quality and so on.c.choice of the Feeds wayRegarding has opens the mouth die space the region, feeds as far as possible from material outside, by real-time analysis material cutting condition. But regarding does not have the die space enclosed area, selects the screw feed method, cuts into the local region.d. As far as possible reduced cutting tool's commutation rapidlyReduces the cutting tool as far as possible the rapidly commutation, because the zigzag pattern mainly applies in the traditional processing, mainly chooses the return route or the sole way cutting in the high-speed cutting processing. This is because in commutation time the NC engine bed must stop (urgently changing down) immediately then the again execution next step of operation. As a result of engine bed acceleration limitation, but is easy to create the time the waste, stops anxiously or whips then can destroy the surface roughness, also has the possibility because has cut but produces the broach or in the outside undercut. Chooses the sole way cutting pattern to carry on the down milling, does not sever the cutting process and the cutting tool way as far as possible, reduces the cutting tool to cut into as far as possible cuts the number of times, by obtains the relatively stable cutting process.For example, in the cutting mold corner processing, the traditional processing method is usesthe translation (G1), when the cutting tool cuts to the fillet place, the velocity of movement reduces speed, at the same time when enters for the commutation the cutting tool movement is not continuously, can have the massive friction and the quantity of heat in the intermittent process, if processes the aluminum alloy or other light metal alloys, produces the quantity of heat will damage the work piece surface quality.If uses the high-speed cutting processing the method, the use is smaller than the cutting mold corner radius cutting tool, the use high speed engine bed high accuracy circular arc inserts makes up the function (G2, G3) processes the mold corner, the high speed engine bed circular arc inserts makes up the movement is the continuous process, cannot have the cutting tool intermittent motion, thus reduced the cutting tool and the mold contact length and the time, avoids having the massive heat.e In Z direction cutting continual planeThe traditional processing die space's method uses the profile milling, this processing way increased the cutting tool to cut into, to cut the work piece the number of times, has affected the work piece surface quality, has limited the engine bed and the cutting tool formidable function display. In the high-speed cutting processing, often uses the Z direction cutting continual plane. Uses step pitch which is smaller than the convention, thus reduces each tooth cutting elimination quantity, the improvement processing surface's quality, reduced the process period.4 High-speed cutting process technology in die makingapplicationThe high-speed cutting process technology has a series of characteristics and the production benefit aspect's great potential, already becomes country competition research and so on Germany, US and Japan important areas of technology. Now, US, Germany, Japan, France, Switzerland, Italy produce the different specification's each kind of commercialization high speed engine bed already entered the market, applies in the airplane, the automobile and the die making.Along with the high-speed cutting process technology introduction mold industry, has had the very tremendous influence to the traditional mold processing craft, changed the mold processing technical process. Because the mold profile is the very complex free surface generally, and degree of hardness is very high, uses conventional the machining method to satisfy the precision and the shape request with difficulty. The conventional processing method is after the annealing carries on the milling processing, then carries on the heat treatment, the grinding or the electric spark machining, finally the manual polish, polishing, cause the processing cycle to be very long like this. Specially the manual process period, must account for the entire processing cycle to be very big a part. HSC may achieve the accuracy requirement which the mold processes, reduced has even cancelled the manual processing, because and new cutting tool material (for example PCD, PCBN, cermet and so on) the appearance, HSC may the work hardness achieve HRC60, even degree of hardness higher work piece material, after might process hard mold, substitution electric spark machining and abrasive machining.The high speed milling processing has the highly effective high accuracy in the die making as well as may process the high hard material the merit, already obtained the widespread application in the industrially advanced country. The high-speed cutting process technology introduction mold industry, mainly applies in the following several aspects:1) hard mold die space direct processing. After using the high-speed cutting to be possible to process the hard material the characteristic direct processing hard mold die space, improved the quality which and the efficiency the mold processes, may substitute for the electric spark machining.(2) EDM (electric spark) electrode processing. Applied the high-speed cutting technology processing electrode to raise the electric spark machining efficiency to play the very major role. The high-speed cutting electrode improved electrode's surface quality and the precision, reduced the following working process.3) fast sample workpiece manufacture. Uses the high-speed cutting processing efficiencyhigh characteristic, may use in processing the plastic and the aluminum alloy model. After the CAD design produces the 3D full-scale mockup fast, is higher than the fast prototype manufacture efficiency, the quality is good.(4) mold's fast repair. The mold often needs to repair in the use process, lengthens the service life, in the past was mainly completes depending on the electrical finishing, now uses the high speed processing to be possible to complete this work quickly, moreover might use the original NC procedure, did not need to establish.5 ConclusionThe high-speed cutting processing uses the high cutting velocity and the feed rate, the small radial direction and the axial depth of cut, the cutting force is small, the processing surface roughness is very small, cutting tool life enhancement; With the high-speed cutting processing way substitution tradition processing way processing mold, might omit the electric spark machining and rub manually repairs, raised the productivity which the mold processed, reduced the production cost, reduced the processing cycle; When research high-speed cutting processing, must unify closely with the high-speed cutting processing technology, realizes the high efficiency, the high accuracy truly and the redundant reliable goal.The high-speed cutting process technology is the advanced technique of manufacture, has the broad application prospect. Replaces EDM with the high-speed cutting processing (or majority of replaces) speeds up the mold development speed, realizes the craft update major step. The promoted application high-speed cutting process technology applies in the mold manufacturing industry, not only may enhance the machine-finishing large scale the efficiency, the quality, reduces the cost, moreover may lead a series of high technology and new technology industry the development. Therefore, current strengthens the high-speed cutting technology the basic research, establishes the high-speed cutting database, the high-speed cutting safety work standard, enhances the engine bed and tool profession development innovation ability, speeds up the high-speed cutting cutting tool system, the high-speed cutting engine bed system's research development and the industrial production, already was the urgent matter.References[1] A.C. Low, J.W. Kyle, Grinding tool technology recent development, The Mechanical Engineers Association, London, 1986. High-speed cutting and grinding tool manufacture[2] K.L. Johnson, High-speed cutting and grinding tool manufacture, Cambridge University Press, Cambridge, 1985.[3] W.DMay, E.L. Morris, D. Atack, new using of Cutting technology, Applied Physics 30 (1959) 1713–1724.[4] S.C. Hunter, Grinding tool manufacture, Applied Mechanics 28 (1961) 611–617.[5] G. Lodewijks, Dynamics of Belt Systems, Thesis, Delft University of Technology, Delft, 1995.[6] A.N. Gent, High-speed cutting outline, Carl Hanser Verslag, 2001.中文翻译高速切削加工在模具制造中的新应用摘要当前模具应用广泛,与之相关的模具制造技术也有了很大的发展。
模具的历史发展外文文献翻译、中英文翻译、外文翻译
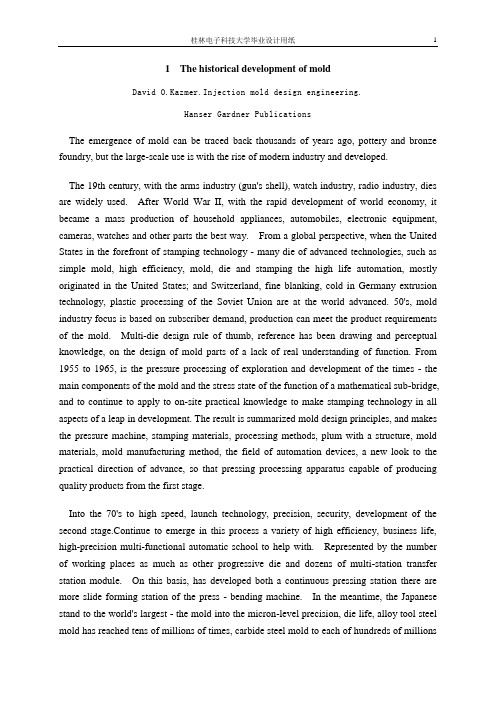
1 The historical development of moldDavid O.Kazmer.Injection mold design engineering.Hanser Gardner PublicationsThe emergence of mold can be traced back thousands of years ago, pottery and bronze foundry, but the large-scale use is with the rise of modern industry and developed.The 19th century, with the arms industry (gun's shell), watch industry, radio industry, dies are widely used. After World War II, with the rapid development of world economy, it became a mass production of household appliances, automobiles, electronic equipment, cameras, watches and other parts the best way. From a global perspective, when the United States in the forefront of stamping technology - many die of advanced technologies, such as simple mold, high efficiency, mold, die and stamping the high life automation, mostly originated in the United States; and Switzerland, fine blanking, cold in Germany extrusion technology, plastic processing of the Soviet Union are at the world advanced. 50's, mold industry focus is based on subscriber demand, production can meet the product requirements of the mold. Multi-die design rule of thumb, reference has been drawing and perceptual knowledge, on the design of mold parts of a lack of real understanding of function. From 1955 to 1965, is the pressure processing of exploration and development of the times - the main components of the mold and the stress state of the function of a mathematical sub-bridge, and to continue to apply to on-site practical knowledge to make stamping technology in all aspects of a leap in development. The result is summarized mold design principles, and makes the pressure machine, stamping materials, processing methods, plum with a structure, mold materials, mold manufacturing method, the field of automation devices, a new look to the practical direction of advance, so that pressing processing apparatus capable of producing quality products from the first stage.Into the 70's to high speed, launch technology, precision, security, development of the second stage.Continue to emerge in this process a variety of high efficiency, business life, high-precision multi-functional automatic school to help with. Represented by the number of working places as much as other progressive die and dozens of multi-station transfer station module. On this basis, has developed both a continuous pressing station there are more slide forming station of the press - bending machine. In the meantime, the Japanese stand to the world's largest - the mold into the micron-level precision, die life, alloy tool steel mold has reached tens of millions of times, carbide steel mold to each of hundreds of millionsof times p minutes for stamping the number of small presses usually 200 to 300, up to 1200 times to 1500 times. In the meantime, in order to meet product updates quickly, with the short duration (such as cars modified, refurbished toys, etc.) need a variety of economic-type mold, such as zinc alloy die down, polyurethane rubber mold, die steel skin, also has been very great development.From the mid-70s so far can be said that computer-aided design, supporting the continuous development of manufacturing technology of the times. With the precision and complexity of mold rising, accelerating the production cycle, the mold industry, the quality of equipment and personnel are required to improve. Rely on common processing equipment, their experience and skills can not meet the needs of mold. Since the 90's, mechanical and electronic technologies in close connection with the development of NC machine tools, such as CNC wire cutting machine, CNC EDM, CNC milling, CNC coordinate grinding machine and so on. The use of computer automatic programming, control CNC machine tools to improve the efficiency in the use and scope. In recent years, has developed a computer to time-sharing by the way a group of direct management and control of CNC machine tools NNC system.With the development of computer technology, computers have gradually into the mold in all areas, including design, manufacturing and management. International Association for the Study of production forecasts to 2000, as a means of links between design and manufacturing drawings will lose its primary role. Automatic Design of die most fundamental point is to establish the mold standard and design standards. To get rid of the people of the past, and practical experience to judge the composition of the design center, we must take past experiences and ways of thinking, for series, numerical value, the number of type-based, as the design criteria to the computer store. Components are dry because of mold constitutes a million other differences, to come up with a can adapt to various parts of the design software almost impossible. But some products do not change the shape of parts, mold structure has certain rules, can be summed up for the automatic design of software. If a Japanese company's CDM system for progressive die design and manufacturing, including the importation of parts of the figure, rough start, strip layout, determine the size and standard templates, assembly drawing and parts, the output NC program (for CNC machining Center and line cutting program), etc., used in 20% of the time by hand, reduce their working hours to 35 hours; from Japan in the early 80s will be three-dimensional cad / cam system for automotive panel die. Currently, the physical parts scanning input, map lines and data input,geometric form, display, graphics, annotations and the data is automatically programmed, resulting in effective control machine tool control system of post-processing documents have reached a high level; computer Simulation (CAE) technology has made some achievements. At high levels, CAD / CAM / CAE integration, that data is integrated, can transmit information directly with each other. Achieve network. Present. Only a few foreign manufacturers ca2 StampingStamping is a kind of plastic forming process in which a part is produced by means of the plastic forming of the material under the action of a die.Stamping is usually carried out under cold state, so it is also called cold stamping. Heat stamping is used only when the blank thickness is greater than 8-100mm. The blank material for stamping is usually in the form sheet or strip, and therefore it is also called sheet metal forming. Some non-metal sheets (such as plywood, mica sheet, asbestos, leather) can also be formed by stamping.Stamping is widely used in various metalworking industry, and it plays a crucial role in the industries for manufacturing automobiles, instruments, military parts and household electrical appliances, etc.The process,equipment and die are the three foundational problems that needed to be studied in stamping.The characteristics of the sheet metal forming are as follows:(1) High material utilization.(2) Capacity to produce thin-walled parts of complex shape.(3) Good interchangeability of stamping parts precision in shape and dimension.(4) Parts with lightweight,high strength and fine rigidity can be obtained.(5) High productivity, easy to operate and to realize mechanization and automatization. The manufacture of the stamping die is costly, and therefore it only fits to mass production. For the manufacture of products in small batch and rich variety, the simple stamping die and the new equipment such as a stamping machining center, are usually adopted to meet he market demands.The materials for sheet metal stamping include mild steel, copper, aluminum, magnesium alloy and high-plasticity alloy steel, etc.Stamping equipment includes plate shear and punching press. The former shears plate into strips with a definite width, which would be pressed later. The later can be used both in shearing and forming.There are various processes of stamping forming with different working patterns and names,but these processes are similar to each other in plastic deformation.There are following conspicuous characteristics in stamping:(1) The force per unit area perpendicular to the blank surface is not large but is enough to cause the material plastic deformation. It is much less than the inner stresses on the plate plane directions.In most cases stamping forming can be treated approximately as that of the plane stress state to simplify vastly the theoretical deformation mechanics analysis and the calculation of the process parameters.(2) Due to the small relative thickness,the anti-instability capability of the blank is weak under compressive stress.As a result,the stamping process is difficult to proceed successfully without using the anti-instability device (such as blank holder).Therefore the variety of the stamping processes dominated by tensile stress are more than those dominated by compressive stress.(3) During stamping forming,the inner stress of the blank is equal to or sometimes less than the yield stress of the material.In this point,the stamping is different from the bulk forming. During stamping forming,the influence of the hydrostatic pressure of the stress state in the deformation zone to the forming limit and the deformation resistance is not so important as to the bulk forming.In some circumstances,such influence may be neglected.Even in the case when this influence should be considered,the treating method is also different from that of bulk forming.(4) In stamping forming,the restrain action of the die to the blank is not severe as in the case of the bulk forming(such as die forging).In bulk forming, the constraint forming is proceeded by the die with exactly the same shape of the part.Whereas in stamping,in most cases,the blank has a certain degree of freedom, only one surface of the blank contacts with the die.In some extra cases, such as the forming of the suspended region of sphere or cone,and curling at the end of tube, neither sides of the blank on the deforming zone contact with the die. The deformation in these regions are caused and controlled the die applying an external force to its adjacent area.Due to the characteristics of stamping deformation and mechanics mentioned above,the stamping technique is different from the bulk metal forming:(1) The importance of the strength and rigidity of the die in stamping forming is less than that in bulk forming because the blank can be formed without applying large pressure unit area on its surface.Instead,the techniques of the simple die and the pneumatic and hydraulic forming are developed.(2) Due to the plane stress or simple strain state in comparison with bulk forming,more research on deformation or force and power parameters has been done, stamping forming canbe performed by more reasonable scientific methods.Based on the real time measurement and analysis on the sheet metal properties and stamping parameters, by means of computer and some modem testing apparatus research on the intellectualized control of stamping process is also in proceeding.(3) It is shown that there is a close relationship between stamping forming and raw material. The research on the properties of the stamping forming,that is,forming ability and shape stability, has become a key point in stamping technology. The research on the properties of the sheet metal stamping not only meets the need of the stamping technology development,but also enhances the manufacturing technique of iron and steel industry, and provides a reliable foundation for increasing sheet metal quality.3 China's mold industry and its development trendDue to historical reasons for the formation of closed, "big and complete" enterprise features, most enterprises in China are equipped with mold workshop, in factory matching status since the late 70s have a mold the concept of industrialization and specialization of production. Mold production industry is small and scattered, cross-industry, capital-intensive, professional, commercial and technical management level are relatively low.According to incomplete statistics, there are now specialized in manufacturing mold, the product supporting mold factory workshop (factory) near 17 000, about 600 000 employees, annual output value reached 20 billion yuan mold. However, the existing capacity of the mold and die industry can only meet the demand of 60%, still can not meet the needs of national economic development. At present, the domestic needs of large, sophisticated, complex and long life of the mold also rely mainly on imports. According to customs statistics, in 1997 630 million U.S. dollars worth of imports mold, not including the import of mold together with the equipment; in 1997 only 78 million U.S. dollars export mold. At present the technological level of China Die & Mould Industry and manufacturing capacity, China's national economy in the weak links and bottlenecks constraining sustainable economic development.3.1 Research on the Structure of industrial products moldIn accordance with the division of China Mould Industry Association, China mold is divided into 10 basic categories, which, stamping die and plastic molding two categoriesaccounted for the main part. Calculated by output, present, China accounts for about 50% die stamping, plastic molding die about 20%, Wire Drawing Die (Tool) about 10% of the world's advanced industrial countries and regions, the proportion of plastic forming die die general of the total output value 40%.Most of our stamping die mold for the simple, single-process mode and meet the molds, precision die, precision multi-position progressive die is also one of the few, die less than 100 million times the average life of the mold reached 100 million times the maximum life of more than accuracy 3 ~ 5um, more than 50 progressive station, and the international life of the die 600 million times the highest average life of the die 50 million times compared to the mid 80s at the international advanced level.China's plastic molding mold design, production technology started relatively late, the overall level of low. Currently a single cavity, a simple mold cavity 70%, and still dominant.A sophisticated multi-cavity mold plastic injection mold, plastic injection mold has been able to multi-color preliminary design and manufacturing. Mould is about 80 million times the average life span is about, the main difference is the large deformation of mold components, excess burr side of a large, poor surface quality, erosion and corrosion serious mold cavity, the mold cavity exhaust poor and vulnerable such as, injection mold 5um accuracy has reached below the highest life expectancy has exceeded 20 million times, the number has more than 100 chamber cavity, reaching the mid 80s to early 90s the international advanced level.3.2 mold Present Status of TechnologyTechnical level of China's mold industry currently uneven, with wide disparities. Generally speaking, with the developed industrial countries, Hong Kong and Taiwan advanced level, there is a large gap.The use of CAD / CAM / CAE / CAPP and other technical design and manufacture molds, both wide application, or technical level, there is a big gap between both. In the application of CAD technology design molds, only about 10% of the mold used in the design of CAD, aside from drawing board still has a long way to go; in the application of CAE design and analysis of mold calculation, it was just started, most of the game is still in trial stages and animation; in the application of CAM technology manufacturing molds, first, the lack of advanced manufacturing equipment, and second, the existing process equipment (including the last 10years the introduction of advanced equipment) or computer standard (IBM PC and compatibles, HP workstations, etc.) different, or because of differences in bytes, processing speed differences, differences in resistance to electromagnetic interference, networking is low, only about 5% of the mold manufacturing equipment of recent work in this task; in the application process planning CAPP technology, basically a blank state, based on the need for a lot of standardization work; in the mold common technology, such as mold rapid prototyping technology, polishing, electroforming technologies, surface treatment technology aspects of CAD / CAM technology in China has just started. Computer-aided technology, software development, is still at low level, the accumulation of knowledge and experience required. Most of our mold factory, mold processing equipment shop old, long in the length of civilian service, accuracy, low efficiency, still use the ordinary forging, turning, milling, planing, drilling, grinding and processing equipment, mold, heat treatment is still in use salt bath, box-type furnace, operating with the experience of workers, poorly equipped, high energy consumption. Renewal of equipment is slow, technological innovation, technological progress is not much intensity. Although in recent years introduced many advanced mold processing equipment, but are too scattered, or not complete, only about 25% utilization, equipment, some of the advanced functions are not given full play.Lack of technology of high-quality mold design, manufacturing technology and skilled workers, especially the lack of knowledge and breadth, knowledge structure, high levels of compound talents. China's mold industry and technical personnel, only 8% of employees 12%, and the technical personnel and skilled workers and lower the overall skill level. Before 1980, practitioners of technical personnel and skilled workers, the aging of knowledge, knowledge structure can not meet the current needs; and staff employed after 80 years, expertise, experience lack of hands-on ability, not ease, do not want to learn technology. In recent years, the brain drain caused by personnel not only decrease the quantity and quality levels, and personnel structure of the emergence of new faults, lean, make mold design, manufacturing difficult to raise the technical level.3.3 mold industry supporting materials, standard parts of present conditionOver the past 10 years, especially the "Eighth Five-Year", the State organization of the ministries have repeatedly Material Research Institute, universities and steel enterprises, research and development of special series of die steel, molds and other mold-specific carbide special tools, auxiliary materials, and some promotion. However, due to the quality is not stable enough, the lack of the necessary test conditions and test data, specifications andvarieties less, large molds and special mold steel and specifications are required for the gap. In the steel supply, settlement amount and sporadic users of mass-produced steel supply and demand contradiction, yet to be effectively addressed. In addition, in recent years have foreign steel mold set up sales outlets in China, but poor channels, technical services support the weak and prices are high, foreign exchange settlement system and other factors, promote the use of much current.Mold supporting materials and special techniques in recent years despite the popularization and application, but failed to mature production technology, most still also in the exploratory stage tests, such as die coating technology, surface treatment technology mold, mold guide lubrication technology Die sensing technology and lubrication technology, mold to stress technology, mold and other anti-fatigue and anti-corrosion technology productivity has not yet fully formed, towards commercialization. Some key, important technologies also lack the protection of intellectual property.China's mold standard parts production, the formation of the early 80s only small-scale production, standardization and standard mold parts using the coverage of about 20%, from the market can be assigned to, is just about 30 varieties, and limited to small and medium size. Standard punch, hot runner components and other supplies just the beginning, mold and parts production and supply channels for poor, poor accuracy and quality.3.4 Die & Mould Industry Structure in Industrial OrganizationChina's mold industry is relatively backward and still could not be called an independent industry. Mold manufacturer in China currently can be divided into four categories: professional mold factory, professional production outside for mold; products factory mold factory or workshop, in order to supply the product works as the main tasks needed to die; die-funded enterprises branch, the organizational model and professional mold factory is similar to small but the main; township mold business, and professional mold factory is similar. Of which the largest number of first-class, mold production accounts for about 70% of total output. China's mold industry, decentralized management system. There are 19 major industry sectors manufacture and use of mold, there is no unified management of the department. Only by China Die & Mould Industry Association, overall planning, focus on research, cross-sectoral, inter-departmental management difficulties are many.Mold is suitable for small and medium enterprises organize production, and our technical transformation investment tilted to large and medium enterprises, small and medium enterprise investment mold can not be guaranteed. Including product factory mold shop, factory, including, after the transformation can not quickly recover its investment, or debt-laden, affecting development.Although most products factory mold shop, factory technical force is strong, good equipment conditions, the production of mold levels higher, but equipment utilization rate.Price has long been China's mold inconsistent with their value, resulting in mold industry "own little economic benefit, social benefit big" phenomenon. "Dry as dry mold mold standard parts, standard parts dry as dry mold with pieces of production. Dry with parts manufactured products than with the mold" of the class of anomalies exist.4 EngineeringEngineering is the discipline, art and profession of acquiring and applying scientific, mathematical, economic, social, and practical knowledge to design and build structures, machines, devices, systems, materials and processes that safely realize solutions to the needs of society.The American Engineers' Council for Professional Development (ECPD, the predecessor of ABET) has defined "engineering" as:The creative application of scientific principles to design or develop structures, machines, apparatus, or manufacturing processes, or works utilizing them singly or in combination; or to construct or operate the same with full cognizance of their design; or to forecast their behavior under specific operating conditions; all as respects an intended function, economics of operation and safety to life and property.One who practices engineering is called an engineer, and those licensed to do so may have more formal designations such as Professional Engineer, Chartered Engineer, Incorporated Engineer, or European Engineer. The broad discipline of engineering encompasses a range of more specialized subdisciplines, each with a more specific emphasis on certain fields of application and particular areas of technology.4.1 Engineering HistoryThe concept of has existed since ancient times as humans devised fundamental inventions such as the pulley, lever, and wheel. Each of these inventions is consistent with the modern definition of engineering, exploiting basic mechanical principles to develop useful tools and objects.The term engineering itself has a much more recent etymology, deriving from the word engineer, which itself dates back to 1325, when an engine’er (literally, one who operates an engine) originally referred to “a constructor of military engines.” In this context, now obsolete, an “engine” referred to a military machine, i.e., a mechanical contraption used in war (for example, a catapult). Notable exceptions of the obsolete usage which have survived to the present day are military engineering corps, e.g., the U.S. Army Corps of Engineers.The word “engine” itself is of even older origin, ultimately deriving from the Latin ingenium (c. 1250), meaning “innate quality, especially mental power, hence a clever invention.”Later, as the design of civilian structures such as bridges and buildings matured as a technical discipline, the term civil engineering entered the lexicon as a way to distinguish between those specializing in the construction of such non-military projects and those involved in the older discipline of military engineering.4.2 Ancient eraThe Pharos of Alexandria, the pyramids in Egypt, the Hanging Gardens of Babylon, the Acropolis and the Parthenon in Greece, the Roman aqueducts, Via Appia and the Colosseum, Teotihuacán and the cities and pyramids of the Mayan, Inca and Aztec Empires, the Great Wall of China, among many others, stand as a testament to the ingenuity and skill of the ancient civil and military engineers.The earliest civil engineer known by name is Imhotep. As one of the officials of the Pharaoh, Djosèr, he probably designed and supervised the construction of the Pyramid ofDjoser (the Step Pyramid) at Saqqara in Egypt around 2630-2611 BC. He may also have been responsible for the first known use of columns in architecture[citation needed].Ancient Greece developed machines in both the civilian and military domains. The Antikythera mechanism, the first known mechanical computer, and the mechanical inventions of Archimedes are examples of early mechanical engineering. Some of Archimedes' inventions as well as the Antikythera mechanism required sophisticated knowledge of differential gearing or epicyclic gearing, two key principles in machine theory that helped design the gear trains of the Industrial revolution, and are still widely used today in diverse fields such as robotics and automotive engineering.Chinese, Greek and Roman armies employed complex military machines and inventions such as artillery which was developed by the Greeks around the 4th century B.C., the trireme, the ballista and the catapult. In the Middle Ages, the Trebuchet was developed.4.3 Renaissance eraThe first electrical engineer is considered to be William Gilbert, with his 1600 publication of De Magnete, who was the originator of the term "electricity".The first steam engine was built in 1698 by mechanical engineer Thomas Savery. The development of this device gave rise to the industrial revolution in the coming decades, allowing for the beginnings of mass production.With the rise of engineering as a profession in the eighteenth century, the term became more narrowly applied to fields in which mathematics and science were applied to these ends. Similarly, in addition to military and civil engineering the fields then known as the mechanic arts became incorporated into engineering.4.4 ModernThe International Space Station represents a modern engineering challenge from many disciplines.Electrical engineering can trace its origins in the experiments of Alessandro Volta in the 1800s, the experiments of Michael Faraday, Georg Ohm and others and the invention of the electric motor in 1872. The work of James Maxwell and Heinrich Hertz in the late 19thcentury gave rise to the field of Electronics. The later inventions of the vacuum tube and the transistor further accelerated the development of electronics to such an extent that electrical and electronics engineers currently outnumber their colleagues of any other Engineering specialty.The inventions of Thomas Savery and the Scottish engineer James Watt gave rise to modern Mechanical Engineering. The development of specialized machines and their maintenance tools during the industrial revolution led to the rapid growth of Mechanical Engineering both in its birthplace Britain and abroad.Chemical Engineering, like its counterpart Mechanical Engineering, developed in the nineteenth century during the Industrial Revolution. Industrial scale manufacturing demanded new materials and new processes and by 1880 the need for large scale production of chemicals was such that a new industry was created, dedicated to the development and large scale manufacturing of chemicals in new industrial plants. The role of the chemical engineer was the design of these chemical plants and processes.Aeronautical Engineering deals with aircraft design while Aerospace Engineering is a more modern term that expands the reach envelope of the discipline by including spacecraft design. Its origins can be traced back to the aviation pioneers around the turn of the century from the 19th century to the 20th although the work of Sir George Cayley has recently been dated as being from the last decade of the 18th century. Early knowledge of aeronautical engineering was largely empirical with some concepts and skills imported from other branches of engineering.The first PhD in engineering (technically, applied science and engineering) awarded in the United States went to Willard Gibbs at Yale University in 1863; it was also the second PhD awarded in science in the U.S.Only a decade after the successful flights by the Wright brothers, the 1920s saw extensive development of aeronautical engineering through development of World War I military aircraft. Meanwhile, research to provide fundamental background science continued by combining theoretical physics with experiments.In 1990, with the rise of computer technology, the first search engine was built by computer engineer Alan Emtage.。
模具设计外文翻译--注射/压缩流体组合模塑的数值模拟

附录二:外文翻译原件及翻译稿Numerical simulation of injection/compression liquid composite moldingPart 1. Mesh generationK.M. Pillai a, C.L. Tucker III, F.R a. Phelan Jr ba Department of Mechanical and Industrial Engineering, University of Illinois,1206 W. Green Street, Urbana, IL61801, USAb Polymer Composites Group, Polymers Division, Building 224, Room B108, National Institute ofStandards and Technology, Gaithersburg, MD20899, USAAccepted 14 June 1999───────────────────────────────────────AbstractThis paper presents a numerical simulation of injection/compression liquid composite molding, where the fiber preform is compressed to a desired degree after an initial charge of resin has been injected into the mold. Due to the possibility of an initial gap at the top of the preform and out-of-plane heterogeneity in the multi-layered fiber preform, a full three-dimensional (3D) flow simulation is essential. We propose an algorithm to generate a suitable 3D finite element mesh, starting from a two-dimensional shell mesh representing the geometry of the mold cavity. Since different layers of the preform have different compressibility, and since properties such as permeability are a strong function of the degree of compression, a simultaneous prediction of preform compression along with the resin flow is necessary for accurate mold filling simulation. The algorithm creates a coarser mechanical mesh to simulate compression of the preform, and a finer flow mesh to simulate the motion of the resin in the preform and gap. Lines connected to the top and bottom plates of the mold, called spines, are used as conduits for the nodes. A method to generate a surface parallel to a given surface, thereby maintaining the thickness of the intermediate space, is used to construct the layers of the preform in the mechanical mesh. The mechanical mesh is further subdivided along the spines to create the flow mesh. Examples of the three-dimensional meshes generated by the algorithm are presented. 1999 Elsevier Science Ltd. All rights reserved.Keywords: Liquid composite molding (LCM); E. Resin transfer molding (RTM)───────────────────────────────────────1. IntroductionLiquid composite molding (LCM) is emerging as an important technology to make net-shape parts of polymer-matrix composites. In any LCM process, a preform of reinforcing fibers is placed in a closed mold, then a liquid polymer resin is injected into the mold to infiltrate the preform. When the mold is full, the polymer is cured by a crosslinking reaction to become a rigid solid. Then the mold is opened to remove the part. LCM processes offer a way to produce high-performance composite parts using a rapid process with low labor requirement.This paper deals with a particular type of LCM process called injection/compression liquid composite molding (I/C-LCM). In I/C-LCM, unlike other types of LCM processes, the mold is only partially closed when resin injection begins. This increases the cross-sectional area availablefor the resin flow, and decreases flow resistance by providing high porosity in the reinforcement. Often, the presence of a gap at the top of the preform further facilitates the flow. After all of the resin has been injected, the mold is slowly closed to its final height, causing additional resin flow and saturating all portions of the preform. The I/CLCM process fills the mold more rapidly, and at a lower pressure than the other LCM processes that use injection alone.Complete filling of the mold with adequate wetting of the fibers is the primary objective of any LCM mold designer; incomplete filling in the mold leads to production of defective parts with dry spots. There are many factors which affect the filling of the mold: permeability of the preform, presence of gaps in the mold to facilitate resin flow, arrangement of inlet and outlet gates, injection rates of resin from different inlet ports, etc. Often it is not possible for the mold designer to visualize and design an adequate system for resin infusion by intuition alone, and mold filling simulations are used to optimize mold performance. The situation in I/C-LCM is more complex than ordinary LCM because of compression of the mold during the filling operation. As a result, numerical simulation of the mold filling process in I/C-LCM becomes all the more important.I/C-LCM fiber preforms frequently comprise layers of different reinforcing materials such as biaxial woven fabrics, stitch-bonded uniaxial fibers, random fibers. Each type of material has a unique behavior as it is compressed in the mold. When such different materials are layered to form the preform, each of them will compress by different amounts as the mold is closed. This behavior is illustrated in Fig. 1, which shows a small piece of a mold. Here the lighter center layer deforms much more than the darker outer layer as the mold is closed.(B) After compression (A) Before compressionFig. 1. Uneven deformation of preform layers under compression.Capturing this deformation behavior during compression is critical to the accuracy of any I/C-LCM process model. Resin flows through the preform at all stages of compression, and the porosity and permeability of the preform are critical in determining the resin flow. The ratio of deformed volume to initial volume determines the porosity of each preform layer, and from this one can determine the layer's permeability, either from a theoretical prediction or a correlation of experimental data. Because of this strong coupling between the state of compression in a preform layer and its permeability, computations for fluid flow and preform compression have to be done simultaneously for mold filling simulations in I/C-LCM.Significant steps have already been taken to computationally model the mold filling in the I/C-LCM process. A computer program called crimson, is capable of isothermal mold fillingsimulation which involves simultaneous fluid flow and preform compression computations in the flow domain. But the initial capacity of crimson is limited to two-dimensional (2D) planar geometries where prediction of preform compression is straightforward. Deformation of the preform is modeled using the incremental linearized theory of elasticity; the mathematics simplifies due to reduction in the number of degrees of freedom (DOF) associated with displacement from the usual three to one along the thickness direction. However parts made by the I/C-LCM process typically have complicated three-dimensional shapes and this reduction of the mathematical complexity is no longer possible. The present paper describes our effort to expand the capability of crimson by enabling it to tackle any arbitrary non-planar three dimensional (3D) mold geometry.Most injection molding simulation programs read for the mold geometry in the form of a shell mesh. Even if it were possible to transmit the full geometrical information about the mold through a 3D mesh, it still is difficult to incorporate all the information of relevance to the process engineer. The latter needs to know the thicknesses of various layers of fiber mats and their corresponding porosities at each time step. As a result, it is very important that elements representing different layers of preform in the 3D finite element mesh fall within separate layered regions. Overlap of an element onto more than one region is not acceptable as the element has to carry the material properties, such as porosity, permeability, of only one fiber mat. Mesh-generators in state-of-the-art commercial software such as PATRAN are not designed to generate such a 3D mesh. Consequently, we decided to create a preprocessor suitable for I/C-LCM mold filling simulation.The objectives of this paper are to introduce basic ideas about modeling mold filling in 3D I/C-LCM parts, and to introduce an algorithm to generate a 3D finite element mesh from a given 2D shell mesh for preform and flow computations. In subsequent papers, we will model finite deformation of preform using the non-linear theory of elasticity, and use this information to model resin flow in an I/C-LCM mold.2. Generating a 3D mesh from the given 2D shell meshOur aim is to develop a preprocessor that can generate 3D finite element meshes for flow computations starting from a 2D shell mesh. We wish to allow the I/C-LCM process engineer to include all relevant information such as thicknesses of the layers of the preform, thickness of the gap, into the mesh.A - open gap everywhere C - just touching / partly compressedD - fully compressed everywhere B - open gap / just touchingFig. 2. A schematic describing the various stages of the compression/injection molding process. The top plate of the mold moves along theclamping vector, while the bottom plate is stationary. Stages A–C arethree possible starting positions of the top plate. Stage D shows the finalconfiguration of the mold when it is fully compressed.Fig.2 describes the three possible starting mold configurations (A-C) for a typical angular part geometry. Case A represents the starting configuration for the open mold injection/compression (I/C) molding, with ample gap between the top plate and preform. Cases B and C occur when the gap is partly or completely eliminated before the start of the injection process. In the former, the preform is completely uncompressed with gaps at a few places. In the latter, the gap is removed at the cost of partial compression of the preform in certain regions. In the present paper, mesh generation for configuration A only will be addressed. Once this mesh is created, cases B and C can be generated by solving for the mechanical compression of the preform.As we shall see in the subsequent papers, six-noded wedge elements and eight-noded brick elements are adequate for modeling both the resin flow and preform compression. Our mesh generation algorithm is designed to generate such elements from the three- and four-noded triangular and quadrilateral elements of the shell mesh.2.1. Mechanical and flow meshesDevelopment of the 3D mesh for flow computations from a given 2D shell mesh, representing the part geometry, is divided into two stages. In the first stage, an intermediate mechanical mesh is created, where the number of layers of elements equals the number of fiber mats in the lay-up, with the thickness of the mats equal to the height of those elements. Such a coarse mesh is adequate to track deformation of the mats during compression of the mold. In the second stage, the mechanical mesh is further subdivided along the thickness direction to create a more refined mesh, called the flow mesh, which is used for flow calculations.3. Basic concepts of mesh generation algorithmWe first introduce two basic ideas that form the backbone of our mesh generation algorithm: spines and parallel surfaces.3.1. Use of spinesOne of the salient features of our mesh generation technique is the use of spines to track the nodes of the 3D mechanical mesh. This is similar to the use of spines in the free boundary problems where they have been used to adapt the computational mesh with time. These spines are lines connecting node points of the top mold surface to their counterparts of the bottom mold surface.4. AlgorithmThe main actions carried out in our mesh generation algorithm are as follows:1. Read data describing the 2D shell mesh. The mesh data is read, along with the information important for process modeling such as direction of clamping, properties of fiber mats, initial gap provided at the top of the preform.2. Construct the upper surface of the final part. The upper surface is generated parallel to the input 2D shell mesh which represents the bottom, immovable surface of the mold. The inputthicknesses between the given and upper surfaces are taken to be the final thickness of the I/C-LCM mold (equal to the desired part thickness).5. Examples and discussionA computer program has been developed to implement the mesh generation algorithm, and tested for its efficacy and robustness. In the following sections, examples of the creation of 3D computational meshes from 2D shell meshes are presented. Since the thicknesses in the I/C-LCM parts are much smaller than their other dimensions, realistic meshes are relatively thin. To highlight important features of the algorithm, the thicknesses of the meshes are scaled up in the following examples. In each example, a gap that is a certain fraction of the total thickness of the uncompressed preform is provided between the upper surface of the preform and the top mold plate.6. Summary and conclusionsIn this paper, we present a methodology to create 3D finite element meshes for modeling mold filling in I/CLCM. We propose the concept of predicting preform compression using the coarse mechanical mesh, and predicting fluid flow using the finer flow mesh. A mesh-generating algorithm, to create the mechanical and flow meshes from a given shell mesh, is presented. This algorithm incorporates information about the position of fiber mat interfaces in a multi-layered preform, which is crucial for accurate modeling of the filling process. A technique to create surfaces parallel to any arbitrary shell mesh surface enables us to represent the interfaces accurately. Further, the use of spines in mesh generation reduces the number of unknowns at each node from three to one. The algorithm is used successfully to create the mechanical and flow meshes from two different shell meshes; its robustness is demonstrated by creating a 3D mesh from a shell mesh for an arbitrary mold shape. The need to refine the shell mesh in the region of a step change in the thickness of the mold is the main limitation of the algorithm. In subsequent papers, we will use the mechanical and flow meshes to simulate preform compression and resin flow during mold filling in I/C-LCM.注射/压缩流体组合模塑的数值模拟第一部分网格生成K.M. Pillai a, C.L. Tucker III, F.R a. Phelan Jr ba伊利诺斯大学机械工业工程系1206 W. Green Street, Urbana, IL61801, USAb国家标准与技术研究所,聚合物部,聚合物合成组Building 224, Room B108,Gaithersburg, MD 20899,USA收稿日期:1999年6月14日───────────────────────────────────────摘要文章介绍了注入模型中的树脂在一次初填充后其纤维预型件被压缩到所需的程度时,注射/压缩流体组合模塑的一种数值模拟。
- 1、下载文档前请自行甄别文档内容的完整性,平台不提供额外的编辑、内容补充、找答案等附加服务。
- 2、"仅部分预览"的文档,不可在线预览部分如存在完整性等问题,可反馈申请退款(可完整预览的文档不适用该条件!)。
- 3、如文档侵犯您的权益,请联系客服反馈,我们会尽快为您处理(人工客服工作时间:9:00-18:30)。
毕业设计论文外文翻译模具的发展1模具在工业生产中的地位模具是大批量生产同形产品的工具,是工业生产的主要工艺装备。
采用模具生产零部件,具有生产效率高、质量好、成本低、节约能源和原材料等一系列优点,用模具生产制件所具备的高精度、高复杂程度、高一致性、高生产率和低消耗,是其他加工制造方法所不能比拟的。
已成为当代工业生产的重要手段和工艺发展方向。
现代经济的基础工业。
现代工业品的发展和技术水平的提高,很大程度上取决于模具工业的发展水平,因此模具工业对国民经济和社会发展将起越来越大的作用。
1989年3月国务院颁布的《关于当前产业政策要点的决定》中,把模具列为机械工业技术改造序列的第一位、生产和基本建设序列的第二位(仅次于大型发电设备及相应的输变电设备),确立模具工业在国民经济中的重要地位。
1997年以来,又相继把模具及其加工技术和设备列入了《当前国家重点鼓励发展的产业、产品和技术目录》和《鼓励外商投资产业目录》。
经国务院批准,从1997年到2000年,对80多家国有专业模具厂实行增值税返还70%的优惠政策,以扶植模具工业的发展。
所有这些,都充分体现了国务院和国家有关部门对发展模具工业的重视和支持。
目前全世界模具年产值约为600亿美元,日、美等工业发达国家的模具工业产值已超过机床工业,从1997年开始,我国模具工业产值也超过了机床工业产值。
据统计,在家电、玩具等轻工行业,近90%的零件是综筷具生产的;在飞机、汽车、农机和无线电行业,这个比例也超过60%。
例如飞机制造业,某型战斗机模具使用量超过三万套,其中主机八千套、发动机二千套、辅机二万套。
从产值看,80年代以来,美、日等工业发达国家模具行业的产值已超过机床行业,并又有继续增长的趋势。
据国际生产技术协会预测,到2000年,产品尽件粗加工的75%、精加工的50%将由模具完成;金属、塑料、陶瓷、橡胶、建材等工业制品大部分将由模具完成,50%以上的金属板材、80%以上的塑料都特通过模具转化成制品。
2模具的历史发展模具的出现可以追溯到几千年前的陶器和青铜器铸造,但其大规模使用却是随着现代工业的掘起而发展起来的。
19世纪,随着军火工业(枪炮的弹壳)、钟表工业、无线电工业的发展,冲模得到广泛使用。
二次大战后,随着世界经济的飞速发展,它又成了大量生产家用电器、汽车、电子仪器、照相机、钟表等零件的最佳方式。
从世界范围看,当时美国的冲压技术走在前列——许多模具先进技术,如简易模具、高效率模具、高寿命模具和冲压自动化技术,大多起源于美国;而瑞士的精冲、德国的冷挤压技术,苏联对塑性加工的研究也处于世界先进行列。
50年代,模具行业工作重点是根据订户的要求,制作能满足产品要求的模具。
模具设计多凭经验,参考已有图纸和感性认识,对所设计模具零件的机能缺乏真切了解。
从1955年到1965年,是压力加工的探索和开发时代——对模具主要零部件的机能和受力状态进行了数学分桥,并把这些知识不断应用于现场实际,使得冲压技术在各方面有飞跃的发展。
其结果是归纳出模具设计原则,并使得压力机械、冲压材料、加工方法、梅具结构、模具材料、模具制造方法、自动化装置等领域面貌一新,并向实用化的方向推进,从而使冲压加工从仪能生产优良产品的第一阶段。
进入70年代向高速化、启动化、精密化、安全化发展的第二阶段。
在这个过程中不断涌现各种高效率、商寿命、高精度助多功能自动校具。
其代表是多达别多个工位的级进模和十几个工位的多工位传递模。
在此基础上又发展出既有连续冲压工位又有多滑块成形工位的压力机—弯曲机。
在此期间,日本站到了世界最前列——其模具加工精度进入了微米级,模具寿命,合金工具钢制造的模具达到了几千万次,硬质合金钢制造的模具达到了几亿次p每分钟冲压次数,小型压力机通常为200至300次,最高为1200次至1500次。
在此期间,为了适应产品更新快、用期短(如汽车改型、玩具翻新等)的需要,各种经济型模具,如锌落合金模具、聚氨酯橡胶模具、钢皮冲模等也得到了很大发展。
从70年代中期至今可以说是计算机辅助设计、辅助制造技术不断发展的时代。
随着模具加工精度与复杂性不断提高,生产周期不断加快,模具业对设备和人员素质的要求也不断提高。
依靠普通加工设备,凭经验和手艺越来越不能满足模具生产的需要。
90年代以来,机械技术和电子技术紧密结合,发展了NC机床,如数控线切割机床、数控电火花机床、数控铣床、数控坐标磨床等。
而采用电子计算机自动编程、控制的CNC机床提高了数控机床的使用效率和范围。
近年来又发展出由一台计算机以分时的方式直接管理和控制一群数控机床的NNC系统。
随着计算机技术的发展,计算机也逐步进入模具生产的各个领域,包括设计、制造、管理等。
国际生产研究协会预测,到2000年,作为设计和制造之间联系手段的图纸将失去其主要作用。
模具自动设计的最根本点是必须确立模具零件标准及设计标准。
要摆脱过去以人的思考判断和实际经验为中心所组成的设计方法,就必须把过去的经验和思考方法,进行系列化、数值化、数式化,作为设计准则储存到计算机中。
因为模具构成元件也干差万别,要搞出一个能适应各种零件的设计软件几乎不可能。
但是有些产品的零件形状变化不大,模具结构有一定的规律,放可总结归纳,为自动设计提供软件。
如日本某公司的CDM系统用于级进模设计与制造,其中包括零件图形输入、毛坯展开、条料排样、确定模板尺寸和标准、绘制装配图和零件图、输出NC程序(为数控加工中心和线切割编程)等,所用时间由手工的20%、工时减少到35小时;从80年代初日本就将三维的CAD/CAM系统用于汽车覆盖件模具。
目前,在实体件的扫描输入,图线和数据输入,几何造形、显示、绘图、标注以及对数据的自动编程,产生效控机床控制系统的后置处理文件等方面已达到较高水平;计算机仿真(CAE)技术也取得了一定成果。
在高层次上,CAD/CAM/CAE集成的,即数据是统一的,可以互相直接传输信息.实现网络化。
目前.国外仅有少数厂家能够做到。
3我国模具工业现状及发展趋势由于历史原因形成的封闭式、“大而全”的企业特征,我国大部分企业均设有模具车间,处于本厂的配套地位,自70年代末才有了模具工业化和生产专业化这个概念。
生产效率不高,经济效益较差。
模具行业的生产小而散乱,跨行业、投资密集,专业化、商品化和技术管理水平都比较低。
据不完全统计,全国现有模具专业生产厂、产品厂配套的模具车间(分厂)近17000家,约60万从业人员,年模具总产值达200亿元人民币。
但是,我国模具工业现有能力只能满足需求量的60%左右,还不能适应国民经济发展的需要。
目前,国内需要的大型、精密、复杂和长寿命的模具还主要依靠进口。
据海关统计,1997年进口模具价值6.3亿美元,这还不包括随设备一起进口的模具;1997年出口模具仅为7800万美元。
目前我国模具工业的技术水平和制造能力,是我国国民经济建设中的薄弱环节和制约经济持续发展的瓶颈。
3.1 模具工业产品结构的现状按照中国模具工业协会的划分,我国模具基本分为10大类,其中,冲压模和塑料成型模两大类占主要部分。
按产值计算,目前我国冲压模占50%左右,塑料成形模约占20%,拉丝模(工具)约占10%,而世界上发达工业国家和地区的塑料成形模比例一般占全部模具产值的40%以上。
我国冲压模大多为简单模、单工序模和符合模等,精冲模,精密多工位级进模还为数不多,模具平均寿命不足100万次,模具最高寿命达到1亿次以上,精度达到3~5um,有50个以上的级进工位,与国际上最高模具寿命6亿次,平均模具寿命5000万次相比,处于80年代中期国际先进水平。
我国的塑料成形模具设计,制作技术起步较晚,整体水平还较低。
目前单型腔,简单型腔的模具达70%以上,仍占主导地位。
一模多腔精密复杂的塑料注射模,多色塑料注射模已经能初步设计和制造。
模具平均寿命约为80万次左右,主要差距是模具零件变形大、溢边毛刺大、表面质量差、模具型腔冲蚀和腐蚀严重、模具排气不畅和型腔易损等,注射模精度已达到5um以下,最高寿命已突破2000万次,型腔数量已超过100腔,达到了80年代中期至90年代初期的国际先进水平。
3.2 模具工业技术结构现状我国模具工业目前技术水平参差不齐,悬殊较大。
从总体上来讲,与发达工业国家及港台地区先进水平相比,还有较大的差距。
在采用CAD/CAM/CAE/CAPP等技术设计与制造模具方面,无论是应用的广泛性,还是技术水平上都存在很大的差距。
在应用CAD技术设计模具方面,仅有约10%的模具在设计中采用了CAD,距抛开绘图板还有漫长的一段路要走;在应用CAE进行模具方案设计和分析计算方面,也才刚刚起步,大多还处于试用和动画游戏阶段;在应用CAM技术制造模具方面,一是缺乏先进适用的制造装备,二是现有的工艺设备(包括近10多年来引进的先进设备)或因计算机制式(IBM微机及其兼容机、HP工作站等)不同,或因字节差异、运算速度差异、抗电磁干扰能力差异等,联网率较低,只有5%左右的模具制造设备近年来才开展这项工作;在应用CAPP技术进行工艺规划方面,基本上处于空白状态,需要进行大量的标准化基础工作;在模具共性工艺技术,如模具快速成型技术、抛光技术、电铸成型技术、表面处理技术等方面的CAD/CAM技术应用在我国才刚起步。
计算机辅助技术的软件开发,尚处于较低水平,需要知识和经验的积累。
我国大部分模具厂、车间的模具加工设备陈旧,在役期长、精度差、效率低,至今仍在使用普通的锻、车、铣、刨、钻、磨设备加工模具,热处理加工仍在使用盐浴、箱式炉,操作凭工人的经验,设备简陋,能耗高。
设备更新速度缓慢,技术改造,技术进步力度不大。
虽然近年来也引进了不少先进的模具加工设备,但过于分散,或不配套,利用率一般仅有25%左右,设备的一些先进功能也未能得到充分发挥。
缺乏技术素质较高的模具设计、制造工艺技术人员和技术工人,尤其缺乏知识面宽、知识结构层次高的复合型人才。
中国模具行业中的技术人员,只占从业人员的8%~12%左右,且技术人员和技术工人的总体技术水平也较低。
1980年以前从业的技术人员和技术工人知识老化,知识结构不能适应现在的需要;而80年代以后从业的人员,专业知识、经验匮乏,动手能力差,不安心,不愿学技术。
近年来人才外流不仅造成人才数量与素质水平下降,而且人才结构也出现了新的断层,青黄不接,使得模具设计、制造的技术水平难以提高。
3.3 模具工业配套材料,标准件结构现状近10多年来,特别是“八五”以来,国家有关部委已多次组织有关材料研究所、大专院校和钢铁企业,研究和开发模具专用系列钢种、模具专用硬质合金及其他模具加工的专用工具、辅助材料等,并有所推广。
但因材料的质量不够稳定,缺乏必要的试验条件和试验数据,规格品种较少,大型模具和特种模具所需的钢材及规格还有缺口。