铝合金门窗生产流程
铝合金门窗生产工艺流程
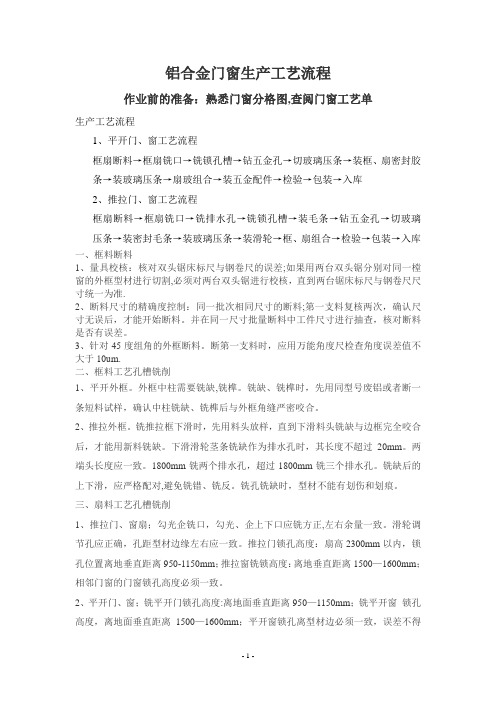
铝合金门窗生产工艺流程作业前的准备:熟悉门窗分格图,查阅门窗工艺单生产工艺流程1、平开门、窗工艺流程框扇断料→框扇铣口→铣锁孔槽→钻五金孔→切玻璃压条→装框、扇密封胶条→装玻璃压条→扇玻组合→装五金配件→检验→包装→入库2、推拉门、窗工艺流程框扇断料→框扇铣口→铣排水孔→铣锁孔槽→装毛条→钻五金孔→切玻璃压条→装密封毛条→装玻璃压条→装滑轮→框、扇组合→检验→包装→入库一、框料断料1、量具校核:核对双头锯床标尺与钢卷尺的误差;如果用两台双头锯分别对同一樘窗的外框型材进行切割,必须对两台双头锯进行校核,直到两台锯床标尺与钢卷尺尺寸统一为准.2、断料尺寸的精确度控制:同一批次相同尺寸的断料;第一支料复核两次,确认尺寸无误后,才能开始断料。
并在同一尺寸批量断料中工件尺寸进行抽查,核对断料是否有误差。
3、针对45度组角的外框断料。
断第一支料时,应用万能角度尺检查角度误差值不大于10um.二、框料工艺孔槽铣削1、平开外框。
外框中柱需要铣缺,铣榫。
铣缺、铣榫时,先用同型号废铝或者断一条短料试样,确认中柱铣缺、铣榫后与外框角缝严密咬合。
2、推拉外框。
铣推拉框下滑时,先用料头放样,直到下滑料头铣缺与边框完全咬合后,才能用新料铣缺。
下滑滑轮茎条铣缺作为排水孔时,其长度不超过20mm。
两端头长度应一致。
1800mm铣两个排水孔,超过1800mm铣三个排水孔。
铣缺后的上下滑,应严格配对,避免铣错、铣反。
铣孔铣缺时,型材不能有划伤和划痕。
三、扇料工艺孔槽铣削1、推拉门、窗扇;勾光企铣口,勾光、企上下口应铣方正,左右余量一致。
滑轮调节孔应正确,孔距型材边缘左右应一致。
推拉门锁孔高度:扇高2300mm以内,锁孔位置离地垂直距离950-1150mm;推拉窗铣锁高度:离地垂直距离1500—1600mm;相邻门窗的门窗锁孔高度必须一致。
2、平开门、窗;铣平开门锁孔高度:离地面垂直距离950—1150mm;铣平开窗锁孔高度,离地面垂直距离1500—1600mm;平开窗锁孔离型材边必须一致,误差不得超过1mm。
铝合金门窗制作流程

铝合金门窗制作流程铝合金门窗制作流程是一个复杂的过程,需要经过多个步骤才能完成。
下面将介绍一个大致的制作流程,以便了解铝合金门窗的制作过程。
1. 设计和测量:首先,根据客户的需求和要求,设计师需要绘制门窗的设计图纸。
这个过程通常需要考虑门窗的尺寸、形状、样式和它们的功能等因素。
然后,工作人员需要到现场进行测量,确保门窗的尺寸精确无误。
2. 剪裁铝型材:根据设计图纸的要求,工人需要根据尺寸和形状要求,将铝型材进行剪裁。
这个步骤通常使用切割机和锯床进行操作,确保铝型材的准确度和精度。
3. 加工和钻孔:接下来,铝型材需要进一步加工和钻孔。
这个步骤通常使用铣床、钻床和冲床等设备进行。
加工和钻孔旨在为门窗的安装和组装提供必要的通孔和配件。
4. 焊接和组装:在铝型材加工完成后,工人将进行焊接和组装。
这个步骤通常需要使用焊接机和组装工具,将铝型材按照设计图纸的要求进行焊接和组装。
焊接是连接铝型材的主要方法,确保门窗的稳固性和耐用性。
5. 表面处理:铝型材的表面通常需要进行处理,以增加其美观性和耐用性。
表面处理通常包括喷涂、阳极氧化和电泳涂装等。
这些方法可以让铝合金门窗具有不同的颜色、纹理和耐用性特点。
6. 玻璃安装和调试:门窗的玻璃安装通常是最后一个步骤。
根据门窗的设计,工人需要将玻璃安装到门窗框架中,并进行调试和测试,确保门窗的开启和关闭顺畅,并且玻璃能够正常使用。
7. 清洁和包装:最后,门窗需要进行清洁和包装。
工人会清洁门窗的表面,确保没有灰尘和污垢。
然后,门窗将进行包装,以确保在运输和安装过程中不被损坏。
综上所述,铝合金门窗的制作流程经过多个步骤,包括设计和测量、剪裁铝型材、加工和钻孔、焊接和组装、表面处理、玻璃安装和调试,以及清洁和包装。
这个过程需要专业的技术和设备,以确保门窗的质量和性能,同时也需要注重细节和精确度。
(完整)铝合金门窗生产作业指导书要点

铝合金门窗生产作业指导书目的:为规范生产工艺标准、完善工序衔接管理,员工统一掌握生产岗位专业技能知识,产品在工序生产过程中能熟知的标准要求,强化自检合格率、质量意识的全面提升,达到规范化、标准化作业的要求,制定本作业指导书.范围:适用于车间每道工序的生产管理及检验。
工艺标准流程铝合金门窗加工工艺流程,依次对锯切下料工序、机加工(铣、冲、钻)工序、组装(接中挺、装五金件、胶条、组角、成框)等工序进行制定。
1。
型材锯切下料工序检验铝合金型材锯切下料工序是铝合金窗生产的重要工序,是关键质量控制点,应保证锯切下料后的杆件质量处于受控状态.所以铝型材经切割机锯切下料后,必须对锯切加工后的杆件严格进行检验,并使尺寸误差控制在允许范围内。
1)检验项目及质量要求a. 下料后型材长度(L)≤2000mm时,尺寸允许偏差为±0.3mm;>2000mm时,尺寸允许偏差为±0。
5mm;b.角度允许偏差为±10′;c。
切割断面毛刺高度<0。
1mm;d。
型材切割面切屑无粘连、无漏屑;e.型材外观不得有碰、拉、划伤痕(不包括由模具造成的型材挤压痕);注:上述项目的质量要求是根据成品窗的外形尺寸标准,要确保成品窗的质量,在下料工序提出的尺寸偏差内控标准。
2)检验器具钢卷尺、万能角度尺、卡尺、深度尺。
3)检验方法a。
下料长度。
用钢卷尺紧贴型材表面与长度方向平行,一端定位从另一端读出测量数据.b。
垂直度和角度。
用万能角度尺测量,测量时把万能尺的一边靠紧型材的一面,调整万能角度尺另一边至被测角度,最后使用微调调棘轮,即可测出角度数值;c. 使用深度尺测量毛刺长度;d. 目测切屑无无粘连在加工面上现象。
锯切下料工序检验记录格式见表2.机加工(铣、冲、钻)工序检验机加工工序是指对锯切后的型材杆件,按照加工工艺和生产图纸的要求,利用机械加工设备或专用设备对型材杆件进行的铣、冲、钻加工。
铣排水槽:1)质量要求a. 排水槽的尺寸和位置应符合图纸要求;b。
铝合金门窗的制作教学设计

铝合金门窗的制作教学设计一、引言铝合金门窗是现代建筑中常见的一种建材产品,具有轻质、耐久、防腐蚀和美观等优势,因而在建筑行业中得到广泛应用。
本文将针对铝合金门窗的制作过程进行详细的教学设计,帮助读者了解门窗的制作流程和要点。
二、材料准备制作铝合金门窗所需的主要材料有:1. 铝合金型材:根据门窗的设计和尺寸要求选择相应的型材。
2. 五金配件:包括门窗的开合装置、密封条、玻璃等配件。
3. 玻璃:根据门窗的设计要求选择合适的玻璃。
三、工具准备为了进行铝合金门窗的制作,需要准备以下基本工具:1. 锯床:用于切割铝合金型材。
2. 钻机:用于在铝合金型材上钻孔。
3. 手动铣床:用于加工铝合金型材的槽口和连接槽。
4. 气动铆枪:用于固定铝合金门窗的五金配件。
四、制作步骤1. 设计制作图纸:根据门窗的尺寸和形状要求,绘制门窗的制作图纸。
2. 切割铝合金型材:根据图纸上的尺寸,使用锯床切割铝合金型材,注意保持切割的精度和平整度。
3. 加工型材槽口:使用手动铣床在铝合金型材上加工槽口,以便安装门窗的五金配件。
4. 钻孔:根据图纸上的标注,在铝合金型材上钻孔,确保钻孔位置准确。
5. 安装五金配件:使用气动铆枪将门窗的五金配件安装到铝合金型材上,确保稳固和牢固。
6. 安装玻璃:将预先准备好的玻璃安装到门窗上,使用密封条或胶水固定好玻璃。
7. 调整和检验:对制作好的铝合金门窗进行调整和检验,确保其开合顺畅,无漏风、漏水等问题。
五、安全注意事项在制作铝合金门窗的过程中,需要遵守以下安全注意事项:1. 戴上适当的防护眼镜和手套,以防切割铝合金型材时产生的飞溅物伤害眼睛和手部。
2. 使用锯床、钻机和铣床时,必须稳固工作台和工作材料,确保工作安全。
3. 使用气动铆枪时,要注意操作规范,避免误伤自己或他人。
六、总结通过本文的教学设计,我们了解了制作铝合金门窗的基本步骤和要点。
制作门窗需要根据设计图纸进行材料准备、工具准备和制作过程的具体操作。
铝合金门窗工艺流程图
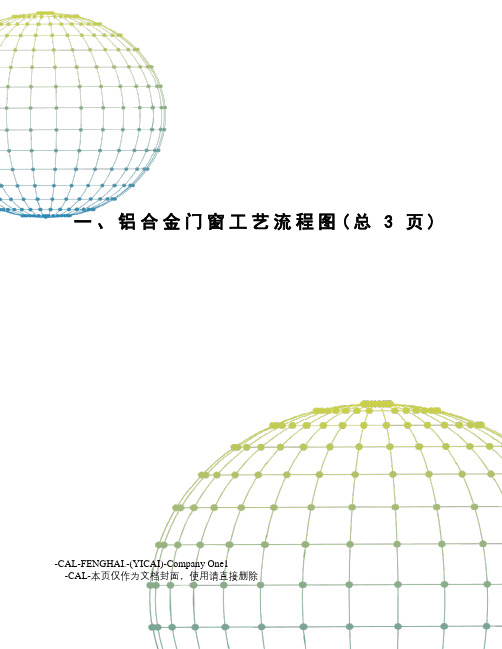
一、铝合金门窗工艺流程图(总3页) -CAL-FENGHAI.-(YICAI)-Company One1-CAL-本页仅作为文档封面,使用请直接删除一、铝合金门窗工艺流程图0 [4 g6 p ^* ~* _放样→ 下料→ 机加工→ 组件拼装→ 安装二、制作:# I4 B! s0 Z" Q8 h4 M0 Y* Z$ J8 Z1 放样在加工前应根据施工图进行翻样,校核施工土建尺寸,并据以制作各节点部位样板,用样板,用样板在杆件需要加工的部分划线放样作为加工依据。
2 下料* u7 ~, ]+~ |+ U7 I下料前应进行校正调直,下料应使用双头切割机。
3 机加工铝合金门窗要对杆件进行孔、槽、豁、榫的加工后才能安装,孔:孔位允许偏差± 0.5mm ,孔距允许偏± 0.5mm ,累计误差不大于± 0.1mm9 {% x: v# j9 i4 j2 F6 w" v槽:定位尺寸± 0.5mm 。
# }( R5 \+ c4 n; B) Y6 c/ ^7 w& Q槽尺寸± 0.5mm 。
豁尺寸± 0.5mm 。
榫尺寸± 0.5mm 。
孔的加工方法可采取钻孔,也可以冲孔。
槽、豁、榫加工可采取铣加工成型,也可以采取冲切成型,杆件在加工过程中,堆放时每层应用抱有软塑料套的垫条隔断,不得使杆件直接接触,以免损坏镀膜表面,垫条间不大于 1m 。
! 8 K3 G3 U6 @& u0 E6 w8 }7 y上下要对齐,以免影响杆件变形。
4 组件拼装组件,杆间连接,按设计分别采用铆接,螺栓等,连接应牢固,各连接缝隙应进行可靠的密封处理。
6 H9 l4 S; N C. K组件框允许偏差见表:表: Untitled-19 c# J5 u: z1 Y0 m拼装好的框件应垂直堆放,下面用有套的垫木垫好,不准随便在地面堆放。
三、产品的保护: O _) v# |" O# j, R3 S已加工、拼装完毕的门窗框半成品、成品在运输前应全部用塑料纸或胶带纸包扎完毕,以免表面擦伤。
门窗生产流程与质量控制

门窗生产流程与质量控制一、引言门窗是建造物中不可或者缺的部份,它们不仅要具备美观的外观,还要具备良好的质量和可靠的性能。
为了确保门窗的生产过程能够顺利进行,并且产品质量符合要求,需要建立一套科学的生产流程和质量控制措施。
本文将详细介绍门窗的生产流程和质量控制标准。
二、门窗生产流程1. 原材料采购与检验门窗的生产过程首先需要采购所需的原材料,如铝型材、玻璃、五金配件等。
在采购过程中,应选择合格的供应商,并对所采购的原材料进行严格的检验,确保其符合相关标准和要求。
2. 材料切割与加工在门窗生产的初期阶段,需要对原材料进行切割和加工。
铝型材需要根据设计要求进行切割,并进行必要的加工,如打孔、开槽等。
玻璃也需要进行切割和加工,以满足门窗的尺寸和形状要求。
3. 组装与焊接组装是门窗生产过程中的关键步骤。
根据设计图纸,将切割好的铝型材和玻璃进行组装,使用专用的五金配件将它们连接在一起。
对于铝合金门窗,还需要进行焊接工艺,确保连接坚固。
4. 表面处理与喷涂组装完成后,门窗需要进行表面处理和喷涂。
表面处理可以包括阳极氧化、电泳涂装等,以增加门窗的耐腐蚀性和美观度。
然后,使用喷涂设备对门窗进行喷涂,保护表面,并使其具备所需的颜色和质感。
5. 装配与调试经过表面处理和喷涂后,门窗需要进行装配和调试。
安装五金配件、密封条等,并确保门窗的开启、关闭、密封性等功能正常。
同时,还需要进行质量检查,确保门窗的质量符合要求。
6. 包装与发货最后一步是门窗的包装和发货。
根据客户要求,对门窗进行适当的包装,以保护其在运输过程中不受损坏。
然后,安排发货,并确保门窗按时送达客户手中。
三、门窗质量控制1. 原材料质量控制在门窗生产过程中,原材料的质量直接影响着最终产品的质量。
因此,需要建立严格的原材料质量控制标准。
对于每批采购的原材料,应进行抽样检验,检查其外观、尺寸、化学成份等指标是否符合要求。
2. 生产过程控制在门窗的生产过程中,需要进行严格的生产过程控制,确保每一个环节的质量符合要求。
铝合金门窗的生产工艺
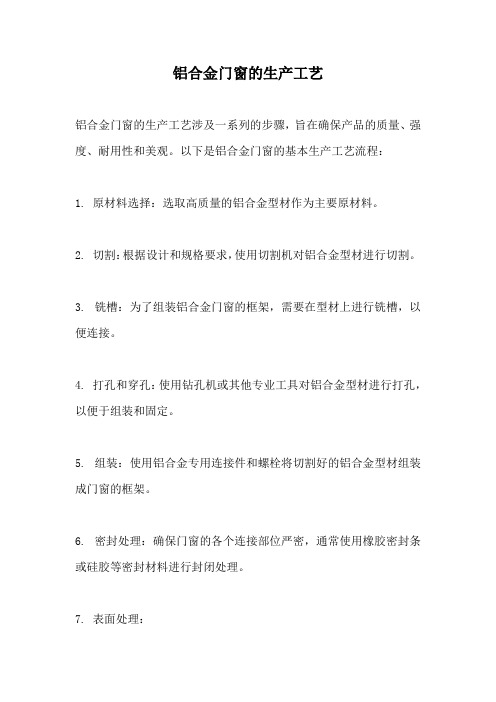
铝合金门窗的生产工艺铝合金门窗的生产工艺涉及一系列的步骤,旨在确保产品的质量、强度、耐用性和美观。
以下是铝合金门窗的基本生产工艺流程:1. 原材料选择:选取高质量的铝合金型材作为主要原材料。
2. 切割:根据设计和规格要求,使用切割机对铝合金型材进行切割。
3. 铣槽:为了组装铝合金门窗的框架,需要在型材上进行铣槽,以便连接。
4. 打孔和穿孔:使用钻孔机或其他专业工具对铝合金型材进行打孔,以便于组装和固定。
5. 组装:使用铝合金专用连接件和螺栓将切割好的铝合金型材组装成门窗的框架。
6. 密封处理:确保门窗的各个连接部位严密,通常使用橡胶密封条或硅胶等密封材料进行封闭处理。
7. 表面处理:阳极氧化:形成一个厚度一致的氧化膜,提高铝材的耐腐蚀性并赋予其美观的颜色。
电泳涂装:使铝材表面具有光滑的保护膜,增强耐腐蚀性。
粉末喷涂:铝材经过阳极氧化后,采用静电粉末喷涂工艺,增强抗紫外线和耐腐蚀性能,且颜色选择多样。
木纹转移打印:使铝材表面呈现出木材的纹理和颜色,增强装饰性。
8. 安装五金配件:如门锁、把手、铰链等。
9. 玻璃安装:选取适当的玻璃,如双层隔音玻璃、钢化玻璃或低辐射玻璃,按照门窗框架的尺寸进行切割后,使用玻璃胶或其他固定方式安装在门窗框内。
10. 质检:对完成的铝合金门窗进行严格的质量检查,确保没有任何瑕疵,满足客户的要求。
11. 包装与运输:将合格的铝合金门窗进行包装,确保在运输过程中不会受到损伤。
整个生产工艺中,需要注意的是,铝合金门窗的设计、制造和安装必须满足国家和地方的相关标准和规定。
这些规定通常与门窗的强度、密封性、隔音性、防火性和安全性等有关。
铝合金门窗制作的工艺流程详解
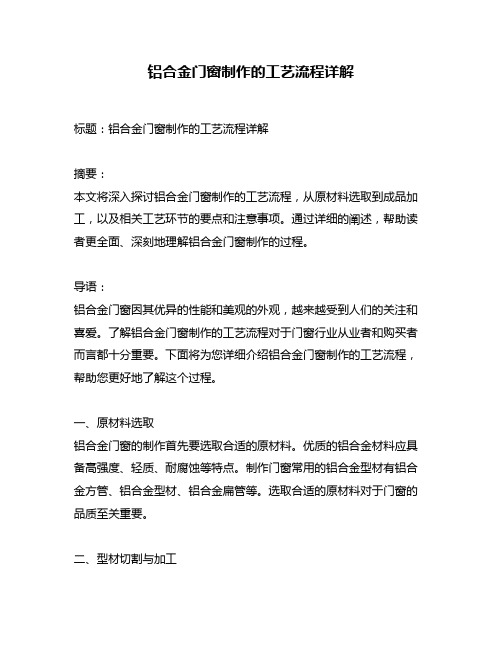
铝合金门窗制作的工艺流程详解标题:铝合金门窗制作的工艺流程详解摘要:本文将深入探讨铝合金门窗制作的工艺流程,从原材料选取到成品加工,以及相关工艺环节的要点和注意事项。
通过详细的阐述,帮助读者更全面、深刻地理解铝合金门窗制作的过程。
导语:铝合金门窗因其优异的性能和美观的外观,越来越受到人们的关注和喜爱。
了解铝合金门窗制作的工艺流程对于门窗行业从业者和购买者而言都十分重要。
下面将为您详细介绍铝合金门窗制作的工艺流程,帮助您更好地了解这个过程。
一、原材料选取铝合金门窗的制作首先要选取合适的原材料。
优质的铝合金材料应具备高强度、轻质、耐腐蚀等特点。
制作门窗常用的铝合金型材有铝合金方管、铝合金型材、铝合金扁管等。
选取合适的原材料对于门窗的品质至关重要。
二、型材切割与加工选取好的铝合金型材后,需要进行切割与加工。
常见的加工方式有数控切割、锯切和剪切等。
根据门窗的尺寸和设计要求,将铝合金型材切割成不同的长度和形状。
此阶段要注意切割精度和保持型材的表面光洁度。
三、型材型制型材型制是铝合金门窗制作的关键步骤之一。
通过将型材放入专用模具中,运用压力和热力使型材变形,得到所需的门窗形状。
型制过程中需要注意加热温度和模具的调节,以保证型材的质量和门窗的准确性。
四、角连接角连接是铝合金门窗制作中重要的组装环节。
通过角连接件将各个型材连接在一起,形成门窗的框架结构。
角连接的质量和稳固性直接关系到门窗的使用寿命和安全性。
在角连接过程中,要严格按照设计要求和标准进行操作,并进行必要的调直、调平和调直角。
五、表面处理铝合金门窗制作完成后,需要进行表面处理,以增加门窗的美观性和耐久性。
常见的表面处理方式有阳极氧化、电泳涂装和粉末涂装等。
这些处理方法都能增加门窗的耐腐蚀性和表面硬度,同时赋予门窗不同的颜色和质感。
六、玻璃安装门窗的最后一个环节是玻璃的安装。
选用合适的密封胶和真空进口玻璃,将玻璃嵌入到门窗的框架中。
玻璃安装的质量关系到门窗的隔音、保温和安全性能。
- 1、下载文档前请自行甄别文档内容的完整性,平台不提供额外的编辑、内容补充、找答案等附加服务。
- 2、"仅部分预览"的文档,不可在线预览部分如存在完整性等问题,可反馈申请退款(可完整预览的文档不适用该条件!)。
- 3、如文档侵犯您的权益,请联系客服反馈,我们会尽快为您处理(人工客服工作时间:9:00-18:30)。
铝门窗生产工艺流程图标“*”为关键工序(一)、下料(关键工序)A、工序流程:*为关键工序B、操作方法1、领料后仔细确认下料加工单和优化单材料与实物一致。
2、确认下料方式(900或450或异型)3、确认型材放置方向是否正确。
4、根据不同的型材选择不同的工装卡具。
5、根据不同的型材调整锯片的进给速度和冷却剂的喷射量。
6、450下料时应仔细测量料高,如果安装模具要经锯床水平台面与料的最高点做料高,不许单独测量原材料的料高(测料高采用游标卡尺,至少3点,以平均值为准)。
7、下料时必须严格执行首检制,确认无误后方可成批下料(由工艺员、质检员、班长认可并做好首检记录),并且在下料过程中要进行抽检。
8、主操手和副操手应互检,每次调整尺寸或角度,副操手应复合尺寸和角度,防止批量尺寸或角度出现错误,9、角码要根据不同的型材试装后,方可成批下料,样窗及私人窗,如果没有订购角码,可自行配制,应以间隙不大于0.2为准。
工程用角码一定按设计要求提角码料切割。
10、工件的数量应以生产部下发的下料单或班长经书面形式提供的数量为准,确保数量无误(生产部或班长签字为准)。
11、尺寸:框料0——+0.5;扇料-0.5——0.。
12、下完料后要及时清除腔内的铝屑(用压缩空气吹,但是要注意安全),要按照不同的规格,标明尺寸/数量,分类码放整齐,不同规格不能混放,转到下道工序时要办好交接记录(填好工艺卡片)。
13、合格下料转到下道工序后,下料任务单由下料工签字后交组长保存,以便查阅。
14、需交接班时,应有记录,并作好交接手续。
由于交接不当而出现的问题由交接双方负同责。
15、检查方法:检查首件记录、现场抽查、按照批量3%抽查且不少于5根。
C、质量控制点:1、型材下料后的长度L±0.52、角度偏差-10′D、检验标准:下料长度L±0.5,角度偏差-10′,型材不得夹伤和变形,切口平整,不准缺角或留有断E、基本要求:1、人员要求:经过机械设备操作规程的培训,考核合格,熟悉本职工作的所有程序。
2、使用设备:双头切割锯单头切割锯角码切割锯设备必须处于完好状态。
3、车间环境要求:地面干净,操作平台上无铝屑,车间温度控制在10度以上。
4、技术要求:严格依照制定的技术文件操作。
5、操作方法:严格依据工艺流程、设备操作规程以及生产操作流程。
6、检验器具:角度尺(0-3200)、盒尺(0-7.5m)、游标卡尺(0-150mm)(二)、加工:A、工序流程B、操作方法:a、领半成品料领下料成品料时要按工艺流程卡点清数量,抽查质量。
如果发现质量、数量问题,应及时申报处理。
不许不合格品流入本工序。
检查合格后,在工艺流程卡上签字。
各工序主操手应认真领会加工工艺,先确定工艺流程然后再加工。
b、画线1、批量的画线,应制作标准对应的模具。
2、画线应用铅笔(2B),需用其它锐器画线时应注意不能划伤型材的装饰面。
3、画线时,线条应细清。
4、卡尺画线时,线条不应过长,够用就行。
5、按工艺流程逐项加工,避免认错线。
6、安装工艺孔和连接件工艺孔交叉存在同一料时,先划连接件工艺孔,再划安装工艺孔(注意两种工艺孔的内外径尺寸)。
7、严格执行首检制度,首检合格后方可批量画线,同时在画线过程中要抽检。
c、框料工艺孔、连接孔钻铣(使用设备:钻铣床)1、钻头的选择:根据需要加工尺寸及偏差要求,选择合适的钻头。
2、注意型材加工的深度和要穿透的层数。
3、批量定位钻孔过程中,要不断检查孔位是否偏差过大,并采用有效措施避免。
4、画线钻孔,严格执行首检制,要做到定位准确,如画线不清,要核对后再加工钻孔。
5、扩孔:注意深度,不要因扩大而造成材料的报废,要磨好钻头保证沉头钉孔位或阶梯孔光滑、美观。
6、钻孔时要根据不同的材料调整台钻的转速(铁300-500:铝800-1200)。
7、加工过程中要注意保护型材,如避免型材划伤、变形。
8、严格执行首检制度。
d、中挺料端面铣削(使用设备:端面铣床)1、进行正常的加工前,检查工作台挡板与工件加工切面保持至90°,按加工要求和参数,调整锯片和基准挡板至要求位置。
2、加工等长重力力矩较大时,应在加工工件悬空一端放置托轮架对工件进行托举,托举面的高度须保持与工作台面在同一平面上。
3、工件进行正常加工时应将工件紧靠工作台和基准挡板,进行试加工,工件检验合格后,方进行批量加工。
4、工件进行正常加工时,铣削进给时应保持匀速均衡的手推力度,使铣削量由零状态逐渐到正常状态,避免撞击造成工件和刀具的损坏。
5、批量工件正常加工时,应定时定量抽检,工件取放应保持合理的频率和力度,避免磕碰现象的发生。
6、工件加工完成后,应清点,贴上相应的标签并码放整齐,工序总检后交接转至下一道工序。
7、严格执行首检制度。
e、扇料槽口、执手孔的冲铣(使用设备:高精度仿形铣、冲床)1、按工艺要求选择合适的设备和模具。
2、熟练工运行操作,如遇特殊情况,需要新手操作时,熟练工应先对设备调试定位,并实验操作,确认无误后方可让新手工作。
3、无论是铣条形孔、圆孔、都应按划线指示或工孔要求,做到外形美观,尺寸准确。
4、严格按照图纸提供的数量加工。
5、严格执行首检制度。
f、料件加工完后1、加工完后的型材用压缩空气把型材腔内的铝屑吹干净。
2、填写工艺流程卡片,记明型号、数量等并签字,转到下道工序。
C、检验标准:各种偏差标准见工艺卡D、基本要求:1、人员要求:经过机械设备操作规程的培训,考核合格,熟悉本职工作的所有程序。
2、使用设备:端面铣床高精度仿形铣钻铣床冲床。
设备必须处于完好状态。
3、车间环境要求:地面干净,操作平台上无铝屑,车间温度控制在10度以上。
4、技术要求:严格依照制定的技术文件操作。
5、操作方法:严格依据工艺流程、设备操作规程以及生产操作流程。
6、检验器具:角度尺(0-3200)、盒尺(0-7.5m)、游标卡尺(0-150mm)(三)、组装A、工序流程:*为关键工序 B、操作方法 a 、领半成品料检查机加工序的成品料数量、质量,合格后在工艺流程卡上签字,严禁不合格品流入本工序。
b、框料、扇料组角1、根据所需的不同规格和用途的半成品料分类码放。
2、确认胶条的安装方法,先穿后组的必须是先穿后组。
3、确认开启扇的部位,截取合适长度的胶条。
4、450料穿完胶条,截面应与型材截面角度一致。
5、所有胶条、毛条不能过长或过短,应与自然平坦时的长度为准,不能拉伸或压缩。
6、批量生产时,拼缝处应均涂组角胶,角码应先装在比较短的料上,组角前要在角部的腔内注入少量的组角胶。
7、组装时,应注意检查所需材料是否已加工完闭,且符合设计要求,并分清开启扇的位置,左右方向,分格尺寸,并注意应装数量。
8、批量组装时应定人定料,以防出错。
9、严格执行首检制度。
c、框料、扇料挤角(关键工序)1、调试组角机,并制作样角,确认无误(a、松紧度;b、有无起包现象)。
2、组角时注意饰面的平整度,阶差不大于0.15.3、完毕后应马上清理余胶,并调整平整度。
4、按照不同规格尺寸码放整齐。
5、严格执行首检制度。
d、铝合金窗组装1、挑选所用的中挺和对应的框。
2、成批量的组装也根据分格尺寸,做对应的模具。
多组组装时,应统一模具尺寸。
3、组装完的框应按图纸要求注明工程名称、楼号、楼层和窗号。
4、组装的整个过程,负责人应对其质量进行监督、检查并负责任。
5、外开窗组装时应注意胶条是否已穿完整。
6、严格执行首检制度。
e、安装五金件1、拆分五金件,留下车间安装部分,剩余点好数量,保管好,发往工地或退库。
2、传动杆的尺寸应准确无误,避免影响五金件的使用性能。
3、应紧固的部分必须紧固牢靠,防止搬运过程中的丢失。
4、自检质量,按照同种规格,分类码放整齐。
5、严格执行首检制度。
f、包装1、根据所包产品,半成品的宽度,切割对应尺寸的胶带,防止浪费和影响美观,包装前应对产品、半成品进行自检、互检,合格后应报车间质检人员检查,合格后发合格证,并且对成品、半成品要有明确标识。
2、粘贴保护胶带应做到表面平整、无气泡、断面整洁。
C、质量控制点:饰面的平整度:阶差不大于0.15.D、检验标准:E、基本要求1、人员要求:经过机械设备操作规程的培训,考核合格,熟悉本职工作的所有程序。
2、使用设备:撞角机设备处于完好状态。
3、车间环境要求:地面干净,操作平台上无铝屑,车间温度控制在10度以上。
4、技术要求:严格依照本司制定的技术文件操作。
5、操作方法:严格依据工艺流程、设备操作规程以及生产操作流程。
6、检验器具:角度尺(0-3200)、盒尺(0-7.5m)、游标卡尺(0-150mm)。
铝门窗生产工艺流程图标“*”为关键工序(一)、下料(关键工序)A、工序流程:*为关键工序B、操作方法1、领料后仔细确认下料加工单和优化单材料与实物一致。
2、确认下料方式(900或450或异型)3、确认型材放置方向是否正确。
4、根据不同的型材选择不同的工装卡具。
5、根据不同的型材调整锯片的进给速度和冷却剂的喷射量。
6、450下料时应仔细测量料高,如果安装模具要经锯床水平台面与料的最高点做料高,不许单独测量原材料的料高(测料高采用游标卡尺,至少3点,以平均值为准)。
7、下料时必须严格执行首检制,确认无误后方可成批下料(由工艺员、质检员、班长认可并做好首检记录),并且在下料过程中要进行抽检。
8、主操手和副操手应互检,每次调整尺寸或角度,副操手应复合尺寸和角度,防止批量尺寸或角度出现错误,9、角码要根据不同的型材试装后,方可成批下料,样窗及私人窗,如果没有订购角码,可自行配制,应以间隙不大于0.2为准。
工程用角码一定按设计要求提角码料切割。
10、工件的数量应以生产部下发的下料单或班长经书面形式提供的数量为准,确保数量无误(生产部或班长签字为准)。
11、尺寸:框料0——+0.5;扇料-0.5——0.。
12、下完料后要及时清除腔内的铝屑(用压缩空气吹,但是要注意安全),要按照不同的规格,标明尺寸/数量,分类码放整齐,不同规格不能混放,转到下道工序时要办好交接记录(填好工艺卡片)。
13、合格下料转到下道工序后,下料任务单由下料工签字后交组长保存,以便查阅。
14、需交接班时,应有记录,并作好交接手续。
由于交接不当而出现的问题由交接双方负同责。
15、检查方法:检查首件记录、现场抽查、按照批量3%抽查且不少于5根。
C、质量控制点:1、型材下料后的长度L±0.52、角度偏差-10′D、检验标准:下料长度L±0.5,角度偏差-10′,型材不得夹伤和变形,切口平整,不准缺角或留有断E、基本要求:1、人员要求:经过机械设备操作规程的培训,考核合格,熟悉本职工作的所有程序。
2、使用设备:双头切割锯单头切割锯角码切割锯设备必须处于完好状态。
3、车间环境要求:地面干净,操作平台上无铝屑,车间温度控制在10度以上。