石煤提钒流化床焙烧条件优化
石煤提钒钠化焙烧与钙化焙烧工艺研究

第34卷 第2期Vol 134 No 12稀 有 金 属CH I N ESE JOURNAL OF RARE MET ALS2010年3月Mar 12010 收稿日期:2009-09-19;修订日期:2009-10-15 作者简介:别 舒(1983-),女,江苏盐城人,硕士;研究方向:提取冶金及冶金物理化学3通讯联系人(E -mail:zhangyg@tsinghua .edu .cn )石煤提钒钠化焙烧与钙化焙烧工艺研究别 舒1,王兆军1,李清海2,张衍国23(1.北京热华能源科技有限公司,北京100084;2.清华大学热科学与动力工程教育部重点实验室,北京100084)摘要:调研了石煤提钒钠化焙烧和钙化焙烧两种工艺的发展现状。
高硅低钙含量的石煤宜采用钠化焙烧,高钙含量的石煤宜采用钙化焙烧,两种工艺各有所长。
归纳了两种工艺下石煤提钒的最佳焙烧条件,得出最佳焙烧条件分别为:钠化焙烧温度区间800~850,焙烧时间2.0~2.5h,磨矿粒度106~180mm,氯化钠用量为矿石的10%~20%。
钙化焙烧比钠化焙烧要高100℃,温度区间900~950℃,焙烧时间2~3h,磨矿粒度106~180mm,石灰用量为矿石的6%~8%。
两种焙烧都需要充足的氧化氛围,但钠化焙烧时氧气不宜过多。
各最佳焙烧条件之间存在一定耦合关系,在生产实际中,宜针对不同石煤进行特定实验。
最后,总结了石煤提钒的主要焙烧设备,其中流化床炉具有较好的发展前景。
关键词:石煤;钒;焙烧;最佳焙烧条件;流化床doi:10.3969/j .issn .0258-7076.2010.02.023中图分类号:TF841.3 文献标识码:A 文章编号:0258-7076(2010)02-0291-07Rev i ew of Vanad i u m Extracti on fro m Stone Coa l by Roa sti n g Techn i que w ith Sod i u m Chlor i de and Ca lc i u m O x i deBei Shu 1,W ang Zhaojun 1,L i Q inghai 2,Zhang Yanguo23(1.B eijing N o w va Energy Technology Co .,L td .,B eijing 100084,China;2.Key L aboratory for Ther m a l Science and Po w er Engineering of M inistry of Educa tion,Tsinghua U niversity,B eijing 100084,China )Abstract:The devel opment of technol ogy on vanadiu m extracti on fr om st one coal by adding s odiu m chl oride and calciu m oxide wasrevie wed .St one coal with large a mount of silica and l ow in calciu m was suitable f or r oasting with s odiu m chl oride .St one coalwith large a mount of calciu m was suitable for r oasting with calciu m oxide .Both techniques had advantages .The op ti m u m additive dosage,r oast 2ing temperature and r oasting ti m e were concluded .W hen adding s odiu m chl oride,r oasting te mperature of 800~850℃,r oasting ti m e of 2.0~2.5h,granularity of 106~180mm,salt dosage of 10%~20%were f ound t o be the best conditi ons for r oasting .Compared with r oasting with s odiu m chl oride,r oasting te mperature of 900~950℃,r oasting ti m e of 2~3h,granularity of 106~180mm,calci 2u m oxide dosage of 6%~8%were the best conditi ons f or r oasting with calciu m oxide .Both techniques needed sufficient oxidizing at 2mos phere .W hen r oasting with s odiu m chl oride,it was by no means the more oxygen the better .There were coup ling relati onshi p s a 2mong different op ti m u m conditi ons .I n p ractical p r oducti on,s pecial experi m ents should be conducted for different kinds of st one coal .D ifferent r oasting furnaces were su mmarized that circulating fluidized bed (CF B )had more advantages than others .Key words:st one coal;vanadiu m;r oasting;op ti m u m conditi on;circulating fluidized bed 稀有金属元素钒,是一种重要的战略物资,因其具有优良的合金性能和催化作用,被广泛地应用于冶金、化工、机械、电子仪器仪表、汽车、船舶、轻工等国防尖端技术部门[1]。
石煤发电含钒烟灰提钒工艺研究

1 提 钒 原料
提钒 原料 为 循 环 流 化 床 低 温 焙 烧 产 出 的烟 灰 ,
循 环流 化 床 为 D F 0—3 8 / 5 HC 4 .2 2 0一L型 单 汽包 横 置式循 环 炉 。 日处 理 石 煤 钒 矿 约 8 0 t其 含 V 0 0 , 25 为 0.5 , 出 的灰 渣 比为 4 4% 产 5~4 5 8:5~5 。产 出 2 烟灰 平均 含 V 0 为 0 6 % 。烟灰 成分 及 粒 度如 表 , 。5
3 6
湖 南有 色金 属
HU NA N NONFERROU S M ETALS
第2 8卷 第 4期
21 0 2年 8月
石煤发 电含钒 烟灰提钒工艺研究
董 晓伟 牛 磊2 ,
( . 沙有 色冶金设计研究 院有限公 司, 1长 湖南 长沙 4 0 1 ; . 10 1 2 湖南有 色金属研 究院, 湖南 长沙 4 0 1 ) 10 5
V O 产 品 。试验 工艺流 程如 图 1 , 所示 。
酸 , 提钒使 用 , 少 了工 业 硫 酸 购 人 量 和 运 输 量 , 供 减 降低 了提钒 成本 ; 出时部 分 浸 出液 返 回使 用 , 酸 浸 硫
消耗由原料量 的 2 %降低至 1 %; 5 8 烟灰直接浸 出 ,
与咨询工作。
环试 验使 用 烟 灰 10k 。试 验 运 行 4轮后 , 9 g 各项 工
艺参 数基 本稳定 , 其后 四轮 试验 工艺 稳定 运行 , 钒浸
第 4期
烟 灰 硫 酸
董 晓伟 , : 等 石煤 发 电含钒 烟灰 提钒 工 艺研 究
3 7
浸出: 采用 4 m×5 m浸 出槽 , 出剂 为前 5c 5c 浸
石煤提钒实验报告

一、实验目的本实验旨在通过石煤提钒实验,了解石煤提钒的基本原理、工艺流程以及影响因素,掌握石煤提钒实验的操作方法,并分析实验结果,为石煤提钒生产提供理论依据。
二、实验原理石煤提钒实验主要采用酸浸法,通过将石煤中的钒元素溶解于酸溶液中,然后对溶液进行净化、沉钒等操作,最终得到钒产品。
实验原理如下:1. 酸浸法:将石煤与一定浓度的酸溶液混合,在一定温度、压力下进行反应,使石煤中的钒元素溶解于酸溶液中。
2. 净化:通过过滤、吸附等手段,去除溶液中的杂质,提高钒溶液的纯度。
3. 沉钒:在钒溶液中加入适当的沉淀剂,使钒离子生成沉淀,然后通过过滤、洗涤等操作得到钒产品。
三、实验材料与设备1. 实验材料:石煤、硫酸、氢氧化钠、氯化铵、活性炭等。
2. 实验设备:烧杯、玻璃棒、漏斗、滤纸、加热器、搅拌器、电子天平等。
四、实验步骤1. 称取一定量的石煤,用硫酸溶解,制成石煤溶液。
2. 将石煤溶液加热至一定温度,保持一段时间,使钒元素充分溶解。
3. 加入氢氧化钠溶液,调节溶液pH值,使钒离子生成沉淀。
4. 将沉淀过滤、洗涤,得到钒产品。
5. 对实验数据进行记录和分析。
五、实验结果与分析1. 酸浸效果:通过对比不同酸浓度、反应时间等因素对酸浸效果的影响,确定最佳酸浸条件。
2. 净化效果:通过对比不同净化方法、净化时间等因素对净化效果的影响,确定最佳净化条件。
3. 沉钒效果:通过对比不同沉淀剂、沉淀时间等因素对沉钒效果的影响,确定最佳沉钒条件。
4. 钒产品纯度:对得到的钒产品进行化学分析,确定其纯度。
六、实验结论通过本实验,掌握了石煤提钒的基本原理、工艺流程以及影响因素,为石煤提钒生产提供了理论依据。
实验结果表明,在最佳条件下,石煤提钒的酸浸效果、净化效果和沉钒效果均较好,钒产品纯度较高。
七、实验注意事项1. 实验过程中应注意安全,严格遵守实验操作规程。
2. 实验过程中要控制好实验条件,确保实验结果的准确性。
3. 实验结束后,对实验设备进行清洗、保养,以备下次实验使用。
钒的提取工艺研究

石煤湿法提钒新工艺研究摘要:以西南某石煤矿为原料,采用石煤中加入氧化剂和硫酸加热浸出,浸出液经P204萃取后水解沉钒工艺。
研究结果表明,钒总回收率达68%以上,产品V2O5纯度达到国标99级以上。
该方法与传统焙烧法提钒相比,具有无焙烧废气污染,产品质量高,污染少等优点。
介绍了采用脱炭氧化、钠化焙烧、水浸从石煤中提钒的工艺方法。
研究了复合附加剂种类、温度、时间等对石煤焙烧钒转化率的影响:液固比、温度、时间、浸出液钒浓度对浸出的影响及浸出液净化条件等。
研究结果表明,焙烧温度、附加剂、液固比是影响钒转浸率的重要因素。
本研究适宜的工艺条件是:石煤脱炭温度860~(2。
钠化焙烧温度820'(2,焙烧时间4h,附加剂为氯化钠碳酸钠混合。
浸出采用循环富集,液固比为1:1,浸出水温度80℃。
关键词:石煤;湿法浸出;溶剂萃取;水解沉淀;石煤;脱炭;焙烧;水浸;V2O5.。
目前,提钒的工艺有很多种,但为了解决提钒过程“三废”对环境的污染和降低生产成本,研究提出一种清洁型的提钒新工艺,在生产过程中解决石煤提钒过程“三废”的污染问题。
石煤无需焙烧硫酸直接浸出,该法与传统石煤焙烧提钒工艺相比,彻底解决了提钒过程中废气对环境的影响,产品回收率高,可直接得到高品位的V2O5产品等特点。
但高温强氧化条件直接浸出,一般酸耗较高,生产成本较高,特别是在钒产品价格较低时,限制该工艺的生产应用。
降低生产成本是直接酸浸提钒工艺的研究重点,本实验对降低直接浸出酸耗、能耗进行了试验研究。
1原料及试验方法1.1原料石煤原矿为西南某地石煤氧化矿,原矿主要化学成分列于表1。
表1原矿主要组分与含量%1.2试剂、设备及分析方法试验试剂:氧化剂、氯酸钠、硫酸、铁屑、氨水、P204、TBP、磺化煤油。
主要试验设备:PSMCQ180mm×200mm瓷衬球磨机、恒温水浴搅拌器、101—3(A)烘箱、S312恒速搅拌器、SHB—B88型循环水式真空泵、自制孔板式连续萃取器。
石煤提钒实验报告

石煤提钒实验报告实验目的本实验的目的是通过石煤提取钒的方法,了解石煤中钒的含量以及提取过程中的各种因素对钒提取率的影响。
实验原理石煤中的钒以氧化态存在,常见的是V2O5。
石煤中的钒主要通过煅烧氧化、硝酸铵胶凝和浸提等步骤进行提取。
实验步骤1. 取一定量的石煤样品并干燥,然后通过煅烧氧化,使样品中的有机碳得到氧化。
2. 将氧化后的样品加入硝酸铵溶液中形成胶体,然后固化成颗粒。
3. 通过浸提实验,利用稀硫酸或盐酸将胶凝体中的钒溶出,然后进行分离和测定。
实验材料与仪器材料1. 石煤样品2. 硝酸铵溶液3. 稀硫酸溶液或盐酸溶液仪器1. 干燥器2. 昇华炉3. 恒温水浴4. 高速搅拌器5. 离心机6. pH计7. 毛细管8. 新刀实验结果与分析通过实验,我们得到了石煤样品中钒的含量和提取率的数据。
通过对数据进行分析,我们可以得到以下结论:1. 钒的含量在不同石煤样品中存在差异,通常在1%以下。
2. 在石煤样品的氧化过程中,适宜的煅烧温度和时间可以提高钒的氧化率,从而提高提取率。
3. 硝酸铵胶凝体的制备对于提高提取率也起着重要作用。
通过调整胶凝体的pH 值,可以改变钒的溶解度和胶凝体的颗粒大小。
4. 浸提实验中,选择合适的浸提剂和条件对于提取率也有显著影响。
稀硫酸或盐酸溶液的浓度、浸取时间和温度等都需要进行优化。
实验结论通过本次实验,我们了解了石煤提钒的方法和过程,得到了一定的实验数据并进行了分析。
实验结果表明,在合适的条件下,我们可以高效地从石煤中提取钒。
这对于石煤的综合利用和钒的资源化非常重要。
存在问题与建议在本次实验中,我们发现了一些问题,为了进一步提高提取率,有以下建议:1. 石煤样品的选择和处理对于提取率有重要影响,可以进一步优化和改进。
2. 实验过程中一些操作步骤需要更加精确和细致,例如控制煅烧温度和时间、调整胶凝体的pH值等。
3. 浸提实验中,可以尝试不同的浸提剂和操作条件,寻找最佳的提取方案。
钒矿

钒矿化学选矿技术评述我国钒矿资源主要矿物类型及储量钒是我国优势矿产,目前生产的钒一半以上以伴生状态赋存于钒钛磁铁矿中。
钒除了在岩浆结晶作用期以类质同象方式进入钛磁铁矿晶格外,还可在沉积作用过程中以极分散的形式被各种富含有机质的沉积物吸附,形成含钒石煤和含钒黏土矿物等多种矿床。
综合考察报告表明:含钒石煤广泛分布在我国南方数省,储量大,层位稳定、含钒品位高。
石煤中钒(V2O5)总储最1.1797亿t。
为我国钒钦磁铁矿中钒总储量的七倍,超过世界其它国家钒的总储量,是近十多年来积极开发利用的一种新型钒矿资源[1]。
钒钛磁铁矿中的钒,可通过磁选等方式选出富含钒的钛磁铁矿,然后在炼铁的过程中加以回收;回收工艺比较成熟,所以近几年针对钒钛磁铁矿提钒工艺的理论与工艺研究较少。
含钒石煤和含钒黏土矿物的钒,则需要通过更为复杂的选矿工艺,如焙烧法、离子交换法或者酸法加以提炼[2]。
国内作为独立矿床的钒矿主要赋存于细粒黏土矿中,低品位黏土型钒矿由于原矿钒含量较低。
原矿直接进行冶金提钒时存在酸碱等辅助原料消耗大、环境污染严重、提钒成本高等问题。
黏土型钒矿采用浮选-重选-磁选等常规选矿技术,很难使钒矿物得到有效富集。
采用新的选矿工艺技术,提高含钒精矿品位,为冶炼提供高品位提钒原料,使国内低品位含钒黏土矿资源得到充分利用,对低品位含钒黏土矿进行研究开发,具有广阔的应用前景和重要的现实意义。
所以国内外针对黏土钒矿也做了一定的研究工作。
石煤提钒传统工艺石煤是我国储量巨大的低品位钒矿资源,石煤提钒最早采用的工艺为添加氯化钠焙烧-水浸工艺,该工艺污染严重且钒回收率低.近年来,研究人员开发出一些新的石煤提钒工艺。
石煤提钒工艺可分为两类,一类是先焙烧后浸出,一类是不焙烧直接浸出,目前以前者为主[3].核工业北京化工冶金研究院试验研究的“从走马石煤中提钒”工艺流程,采用石煤氧化焙烧一硫酸浸出一固液分离一清液萃取一钱盐沉钒工艺,1987年先后完成小型和台架试验,1988年底完成中间工厂规模试验,在国内首次获得成功,主要技术经济指标达国内提钒工艺先进水平[4]。
复合添加剂对石煤提钒焙烧与浸出工艺研究
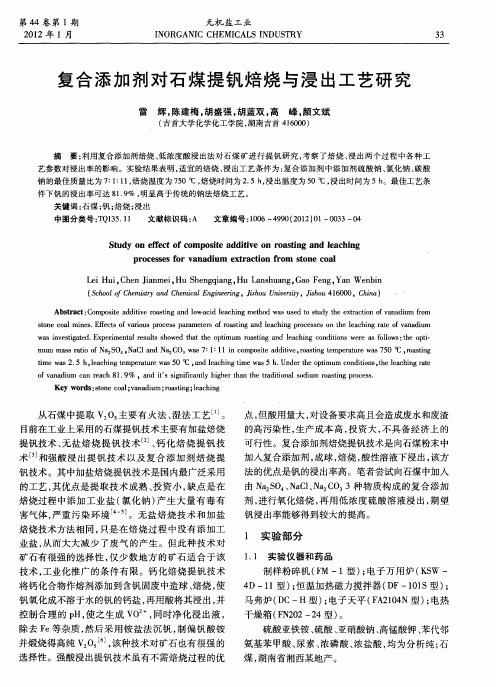
摘
要: 利用复合 添加剂焙烧 、 低浓度酸浸 出法对 石煤 矿进行 提钒研 究 , 考察 了焙烧 、 出两个过程 中各种 工 浸
艺参数 对浸 出率 的影 响。实验结果 表明 , 适宜 的焙 烧 、 出工艺 条件为 : 浸 复合 添加剂 中添加剂硫 酸钠 、 氯化钠 、 酸 碳 钠 的最佳质量 比为 7 1 1 , : : 1 焙烧温度为 7 0o 焙烧 时间为 2 5h 浸 出温度为 5 5 C, . , 0℃ , 出时间为 5h 浸 。最佳工艺条 件下 钒的浸 出率可达 8 .% , 19 明显高于传统 的钠 法焙烧工艺 。
mu ma sr t fNa S , C n a CO3 s7 1 1 n c mp s e a d t e r a t g tmp r tr s 5 ℃ ,o s i g m s a i o 2 O4 Na 1a d N 2 o : : 1 i o o i d i v - o si e e au e wa 0 wa t i n 7 rat n t s2 5 h l a h n mp rt r a 0 ℃ , n a h n mewa . d rt e o t m o dt n ,h a h n t i wa . ,e c i g t me e e au e w s5 a dl c i g t s5 h Un e p i e i h mu c n i o s t e l c i gr e i e a
关键词 : 石煤 ; ; 钒 焙烧 ; 出 浸 中图分类号 :Q 3 . 1 T 15 1 文献标 识码 : A 文章编号 :0 6— 90(02 0 0 3 0 10 4 9 2 1 ) 1— 0 3— 4
S u y o fe to o t d n e c fc mp st d i v n r a t g a d l a h n o i a d t e o o si n e c i g e i n
石煤流态化焙烧—酸浸提钒工艺研究

石煤流态化焙烧—酸浸提钒工艺研究石煤是一种含有丰富钒资源的煤矿石,其主要成分为煤和石灰石。
石煤流态化焙烧—酸浸提钒工艺是利用流态化技术将石煤焙烧成钒酸盐,在酸浸条件下提取钒的一种新型工艺。
本文将从石煤焙烧和酸浸提钒两个方面进行详细研究。
石煤焙烧是指将石煤在一定温度范围内进行高温煅烧的过程。
通过焙烧过程,石煤中的有机物和硫化物会分解为气体和固体产物,同时石煤中的钒和钙会形成固态反应生成钒酸盐。
在焙烧过程中,流态化装置将石煤和石灰石通过流化床的方式进行反应,使得反应更加均匀有效。
此外,流态化技术能够使焙烧反应的温度和时间得到控制,从而提高焙烧效果和产物质量。
石煤焙烧的关键参数是焙烧温度和焙烧时间。
研究表明,焙烧温度在800-1000℃范围内,焙烧时间在1-3小时内,能够获得较好的焙烧效果。
在这一温度范围内,石煤中的有机物和硫化物能够充分分解,而钒和钙能够快速反应生成钒酸盐。
此外,流态化装置的选择和操作也对焙烧效果有一定影响,因此需要进行合理的流态化装置设计和操作参数选择。
焙烧后的石煤产物是一种钒酸盐,其主要成分为钒酸钠和钙钒酸盐。
钒酸钠是一种无机化合物,具有较高的钒含量和稳定性,在后续的酸浸提钒过程中起到重要作用。
而钙钒酸盐则是一种固态反应产物,含有较高的钙含量和较低的钒含量,对后续的钒提取有一定的影响。
因此,石煤焙烧的关键是获得高钒含量的钒酸钠产品。
酸浸提钒是指将焙烧后的石煤产物在酸性条件下进行提取钒的过程。
常用的酸浸剂包括硫酸、盐酸和氯化氢等。
硫酸是一种常见的酸浸剂,具有良好的钒溶解度和选择性。
酸浸提钒的关键参数是浸提温度、酸浸剂浓度和浸提时间。
研究表明,在浸提温度60-80℃范围内,浸提酸浓度1-2mol/L,浸提时间1-2小时内,能够获得较好的钒溶解率和选择性。
酸浸提钒的机理是钒酸盐在酸性条件下与浸提剂发生反应生成溶解态钒离子。
钒酸盐中的钒元素以V(V)价态存在,与酸浸剂中的氢离子发生置换反应生成溶解态三价钒离子或四价钒离子。
- 1、下载文档前请自行甄别文档内容的完整性,平台不提供额外的编辑、内容补充、找答案等附加服务。
- 2、"仅部分预览"的文档,不可在线预览部分如存在完整性等问题,可反馈申请退款(可完整预览的文档不适用该条件!)。
- 3、如文档侵犯您的权益,请联系客服反馈,我们会尽快为您处理(人工客服工作时间:9:00-18:30)。
石煤提钒流化床焙烧条件优化张会丰;曾玺;崔丽杰;许光文【摘要】针对现有石煤焙烧工艺的焙烧效果差、环境污染严重的问题,提出流化床两段石煤焙烧工艺,利用实验室流化床反应器研究了氧化焙烧、复合盐焙烧、添加剂与石煤的混合方式等对石煤流化床焙烧的钒浸出率的影响规律,比较了静态焙烧和流态化焙烧效果的差异,并对CaO的固氯作用进行了考察.结果表明:流态化焙烧缩短了焙烧时间,降低了达到最大钒浸出率所需的反应温度;对比不同的石煤和添加剂的混合方式发现,与简单的物理混合法相比浸渍法不仅能提高钒的浸出率、缩短焙烧时间,而且能降低添加剂的使用量,具有明显的优势.在焙烧过程中加入CaO明显减少了生成气体中的Cl含量,并进一步提高钒的浸出率.综合分析表明,采用浸渍法混合石煤与添加剂时,流化床焙烧的最佳实验条件为:焙烧时间45 min,添加剂用量6%,CaO用量6%,此时的V2O5浸出率达到85.2%.【期刊名称】《煤炭学报》【年(卷),期】2014(039)012【总页数】6页(P2531-2536)【关键词】石煤;流化床;焙烧;钒浸出【作者】张会丰;曾玺;崔丽杰;许光文【作者单位】中国科学院过程工程研究所,北京100190;中国科学院大学化学与化工学院,北京100049;中国科学院过程工程研究所,北京100190;中国科学院大学化学与化工学院,北京100049;中国科学院过程工程研究所,北京100190【正文语种】中文【中图分类】TF841.3钒及其衍生品是重要的战略资源,以其优良的机械性能、合金特性、催化作用等理化性质广泛应用于冶金、国防、电子、化工等领域[1-2]。
目前,我国生产钒制品的主要原料有钒钛磁铁矿和石煤。
其中,石煤中V2O5的总储量高达1.18亿t,是我国钒钛磁铁矿中V2O5储量的6~7倍,超过世界各国V2O5储量的总和[3-4]。
近年来,随着钒制品消耗量不断增大,石煤提钒产量在我国钒行业中的比例快速增加。
因此,从石煤中提钒将是一个非常重要的发展方向,市场前景广阔[5]。
石煤既是一种含碳少、发热量低的劣质无烟煤,又是一种低品味的多金属共生矿。
其主要特点是灰分高、密度和硬度大、热值低、结构致密、着火点高、不易燃烧和难以完全燃烧,且含有多种金属元素。
石煤中的钒多以三价钒为主,主要以类质同象形式取代三价铝赋存于黏土矿物的硅氧四面体结构中,结合紧密且很难被酸或碱浸出。
此外,含钒矿物也常与石煤中的有机碳(含量为10%~20%)共生,嵌布关系复杂,不利于钒的浸出。
目前的石煤提钒工艺可分为两类:火法焙烧-湿法浸出和直接湿法浸出[6-7]。
其中,火法焙烧又分为空白焙烧、钠化焙烧、钙化焙烧、复合添加剂焙烧等方法,而直接湿法浸出包括常压酸浸、氧压酸浸和碱浸等不同方法。
虽然湿法浸出工艺减少了焙烧环节,也可避免烟气污染,但其设备要求很高,浸出过程中要用强酸甚至添加特种助浸剂,故生产成本很高[8],且容易产生大量的含酸废水而引起废水污染。
因此,目前国内的石煤提钒仍然以先火法焙烧再湿法浸出工艺为主。
石煤高温焙烧可以破坏钒矿的物化结构[9],包括脱除石煤中的有机碳、使低价的钒氧化成可溶于水或酸的高价钒氧化物(V2O5)。
在此工艺中,焙烧效果直接影响钒浸出率,进而决定了全流程的钒总回收率[10]。
由此可见,焙烧是影响钒提取率的最关键工艺和环节,对焙烧方式和工艺的研究一直是石煤提钒的工作重点,具有重要意义。
在前述常见的石煤焙烧提钒工艺中,钠化焙烧工艺最为成熟,该工艺具有适应性强、成本低、钒浸出率高等优势[11]。
然而由于传统的钠化焙烧工艺中, NaCl添加量大(一般为石煤的10%~20%),缺乏对大量产生的HCl和Cl2等有毒气体的有效治理手段[12],已经被我国很多地区明令禁止使用。
复合添加剂的研究和使用可以明显降低钠盐用量和焙烧温度[13-14]、缩短焙烧时间,且钒浸出率较高,已成为当前研究的重点和产业化选择的主流技术。
现有的石煤焙烧装置多为平窑、立窑、回转炉、沸腾炉等。
平窑操作简单,但生成能力小、传热、传质效果差、技术落后,属于产业结构调整要求淘汰或限制使用的炉型。
回转窑机械化程度高、生成能力大,但难以对炉内焙烧温度进行有效控制,需要原料脱碳后入炉焙烧。
沸腾炉处理量大、可有效控制炉温,但原料在炉内的停留时间短、颗粒返混严重、钒转浸率较低。
因此,研究处理能力大、炉温可控、钒转浸率较高、污染可控的新型焙烧工艺关系到石煤提钒企业的兴衰[15-16],是石煤提钒利用行业的当务之急。
基于现有焙烧工艺和焙烧装置的弊端,中国科学院过程工程研究所提出了一种新型的流化床两段复合盐法石煤焙烧提钒工艺。
该工艺由流化床预氧化焙烧装置和输送床氧化焙烧装置组成,其工艺流程如图1所示。
破碎后的石煤原料与复合盐充分混合后加入到流化床密相区内预氧化焙烧,初步焙烧后的石煤及生成的气体全部经溢流管进入到输送床内进行深度焙烧,同时在输送床内喷入钙氧化物以控制生成气体中的Cl2,HCl,SO2等有害气体。
输送床出口处的大颗粒原料经过旋风分离器分离后返回预焙烧炉内继续焙烧,焙烧完全后的小颗粒熟料则随生成气体通过旋风出口后被冷却和除尘分离。
焙烧完成后的大颗粒熟料在输送床底部被排出。
由于充分整合了流化床和输送床反应器各自的优势,该工艺充分保证小颗粒原料和大颗粒原料的焙烧时间,同时结合了复合盐污染物排放少和钙氧化物脱硫、固氯的能力,使新工艺具有处理量大、焙烧转浸率高、污染物可控等特点和优势,具有很好的应用前景[17-18]。
模拟图1所示工艺的预焙烧反应器,笔者在实验室小型流化床里系统地研究了石煤焙烧条件,包括添加剂与石煤的混合方式、添加剂用量等对提钒转浸率的影响特性,优化了焙烧工艺条件,并与固定床焙烧工艺进行了对比,对钙氧化物固氯可行性进行了考察,为新型流化床两段石煤焙烧工艺的设计和运行提供基础数据。
1.1 实验原料实验用石煤来自贵州某钒矿,矿石经手选,其元素分析及工业分析结果见表1,石煤灰的XRF结果见表2。
实验用添加剂是由湖北某公司提供的复合盐,其主要成分为NaCl,Na2CO3等。
1.2 流态化焙烧石煤焙烧在实验室流化床反应器中进行,其装置流程如图2所示。
该装置主要包括气体供应系统、流化床反应器、电炉、气体收集与净化系统。
实验前,先将石煤样品与复合盐混合,待实验温度达到设定值后,通入空气并控制气体流量,装置稳定后,将准确称量的20 g石煤样品和复合盐通过料斗加入到流化床底部,焙烧到指定温度后,切断气体,取出反应器并快速冷却至室温。
焙烧生成的气体通入到低温NaOH溶液中,充分吸收排放过程中生成的Cl2和HCl等含氯气体。
1.3 静态焙烧实验用马弗炉来模拟平窑静态焙烧,实验前,将石煤样品与添加剂混合均匀,放入耐火瓷舟中,置入已升温到指定温度的马弗炉中焙烧,焙烧指定时间后,取出瓷舟,迅速冷却,焙烧渣称重,并取样化验焙烧渣中钒含量。
1.4 分析方法称取焙烧后的熟料置于锥形瓶中,加入一定量的氧化剂和一定量的浓硫酸溶液,放入恒温槽中,在一定温度下搅拌数小时,过滤,用硫酸亚铁铵滴定法测定浸出溶液中V2O5的含量,V2O5的浸出率y为式中,m,m0分别为浸出溶液中和石煤矿石中的含钒量,kg。
流化床焙烧后的气体经吸收后,对吸收液体中的氯进行检测。
根据溶液中氯的含量,吸取试样0.5~1.0 mL于250 mL的锥形瓶中,加入50 mL水和5 mL 40%的柠檬酸,放置片刻,准确加入10 mL 0.1 mol/L的硝酸银标准溶液,再加入5 mL的1∶1的硝酸、4 mL 5%的铁铵钒,用0.1 mol/L的硫氰酸铵标准溶液滴定至溶液呈现微红色并且30 s内不褪色为终点,计算溶液中氯的含量。
2.1 流态化焙烧和静态焙烧的比较图3为无添加剂条件下静态/流态化焙烧时间和温度对V2O5浸出率的影响。
由图3(a)可知,在800℃和850℃,钒浸出率随焙烧时间和温度的增加而增加,焙烧4 h后钒的浸出率达到最大值,分别为31.1%和31.9%,继续焙烧,钒浸出率影响不大;而焙烧温度为900℃时,钒浸出率随焙烧时间的增加而下降,且焙烧时间大于3 h后,钒浸出率低于800℃和850℃下的钒浸出率。
用流化床焙烧后,钒的浸出率变化趋势和静态化焙烧有明显的不同。
3个焙烧温度下,钒浸出率均随焙烧时间的延长先升高后下降,在45 min时达到最大值,相同焙烧时间下,焙烧温度为850℃时,焙烧后钒的浸出率最大。
这是因为在无添加剂条件下,焙烧温度越高,钒的氧化程度越高,但过高的温度容易使钒被“玻璃态”物质包裹而难以浸出。
图4为固定床与流化床在不同焙烧温度下最高浸出率的对比,可以看出,达到相似的钒浸出率,流化床焙烧需要的时间明显较短,且过高的焙烧温度不利于钒浸出率的提高。
2.2 复合添加剂对钒浸出率的影响图5为不同焙烧温度下,加入10%添加剂后对钒浸出率变化趋势的影响。
对比图3(b)发现,加入添加剂后,钒浸出率得到大幅提高,且钒浸出率随焙烧时间的变化趋势也有很大的改变。
加入添加剂后,钒的浸出率随焙烧时间的增加迅速提高。
焙烧60 min后达到最大值。
且随着焙烧时间的延长,低温(800℃)的浸出率明显高于高温(850℃)的浸出率,说明添加剂不仅能提高钒的浸出率,且能够降低焙烧温度。
这主要是因为复合添加剂在焙烧中起到了如下的作用:①破坏含钒矿物的晶体结构,使钒从矿物晶体结构束缚态中解离出来,更易被氧化;②与含钒化合物生成NaVO3等可溶性钒酸盐,提高钒的焙烧转化率。
而在高温有氧或有蒸汽情况下,NaCl可以分解产生具有强氧化性的Cl2,可在较低的温度下氧化低价钒,加速低价钒的氧化进程。
2.3 石煤和添加剂的混合方式对焙烧效果的影响考虑到石煤矿孔结构以大孔为主,常用的石煤和添加剂搅拌混合过程中,添加剂成分很难进入孔结构中,势必会影响添加剂与石煤的有效接触面积和焙烧效果。
此外,石煤开采过程中含有一定量的水分(10%~20%),可以考虑利用浸渍的方法将添加剂负载到石煤中,以增加添加剂与石煤的有效接触面积。
图6比较了不同温度下加入10%的添加剂,采用浸渍法处理石煤后对焙烧效果的影响。
低温下,随焙烧时间的延长,钒浸出率迅速增加,在45 min时达到最大值,继续延长焙烧时间,对钒浸出率影响不大;高温下,随焙烧时间的延长,钒浸出率迅速增加,在45 min时候达到最大值,继续延长焙烧时间,钒浸出率迅速下降。
对比低温和高温下钒的浸出效果发现,低温下,钒的浸出率较高。
2.4 添加剂用量对焙烧效果的影响图7为在实验温度为800℃、流化床中的焙烧时间为45 min时,不同混合方式下添加剂用量对钒浸出率的影响。
实验发现,采用机械混合法混合石煤和添加剂,添加剂用量在0~8%范围内增加时,钒浸出率增加迅速;继续增加添加剂的用量,钒浸出率的增幅减少。