新型精馏技术及其发展趋势
精馏技术的发展及应用
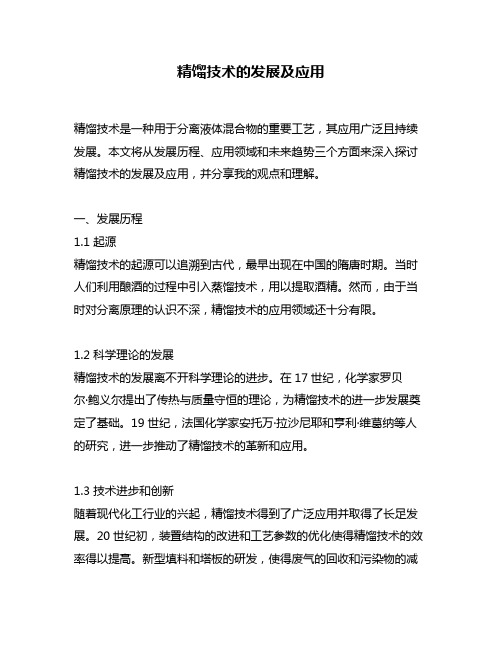
精馏技术的发展及应用精馏技术是一种用于分离液体混合物的重要工艺,其应用广泛且持续发展。
本文将从发展历程、应用领域和未来趋势三个方面来深入探讨精馏技术的发展及应用,并分享我的观点和理解。
一、发展历程1.1 起源精馏技术的起源可以追溯到古代,最早出现在中国的隋唐时期。
当时人们利用酿酒的过程中引入蒸馏技术,用以提取酒精。
然而,由于当时对分离原理的认识不深,精馏技术的应用领域还十分有限。
1.2 科学理论的发展精馏技术的发展离不开科学理论的进步。
在17世纪,化学家罗贝尔·鲍义尔提出了传热与质量守恒的理论,为精馏技术的进一步发展奠定了基础。
19世纪,法国化学家安托万·拉沙尼耶和亨利·维葛纳等人的研究,进一步推动了精馏技术的革新和应用。
1.3 技术进步和创新随着现代化工行业的兴起,精馏技术得到了广泛应用并取得了长足发展。
20世纪初,装置结构的改进和工艺参数的优化使得精馏技术的效率得以提高。
新型填料和塔板的研发,使得废气的回收和污染物的减排成为可能。
二、应用领域2.1 石化行业精馏技术在石化行业中起着举足轻重的作用。
石油精馏是其中的典型应用,通过对原油进行不同温度下的蒸馏,可以将原油中的各种组分分离出来,得到不同用途的产品,如汽油、柴油和润滑油等。
精馏技术还广泛应用于石化工艺中的溶剂回收、尾气净化等方面。
2.2 化学工业精馏技术在化学工业中有着广泛的应用。
有机合成中的溶剂回收、精细化工产品的纯化等都需要利用精馏技术进行分离。
精馏技术也常用于制药工业中,用于提纯药物原料或制备高纯度的药物。
2.3 食品饮料行业在食品饮料行业中,精馏技术的应用也十分广泛。
酒类的蒸馏过程中就离不开精馏技术,从发酵液中提取酒精。
某些食品加工过程中也会利用精馏技术进行分离和提纯,以提高产品的品质和安全性。
三、未来趋势精馏技术在过去几十年中取得了巨大的突破,但仍存在一些挑战和潜力可以进一步发展。
3.1 节能减排当前,环境保护和可持续发展已成为全球关注的焦点。
新型精馏技术介绍
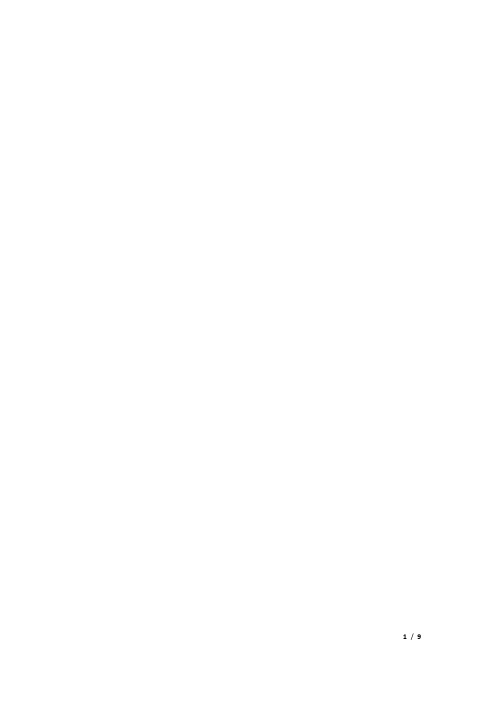
新型精馏技术及其应用摘要介绍了萃取精馏、共沸精馏、反应(催化) 蒸馏、吸附蒸馏、膜蒸馏、惰性气体蒸馏、动态高效规整填料塔精馏和分子蒸馏等新型蒸馏技术的基本原理、特点、研究进展和发展方向关键词萃取精馏共沸精馏反应(催化) 蒸馏吸附蒸馏膜蒸馏惰性气体蒸馏规整填料塔精馏分子蒸馏蒸馏技术作为当代工业应用最广的分离技术,目前已具有相当成熟的工程设计经验与一定的基础理论研究,随着生物技术、中药现代化和环境化工等领域的不断发展和兴起,人们对蒸馏技术提出了很多新的要求(低能耗、无污染等) 。
因此,在产品达到高纯分离的同时又能减低能耗和环境污染就成为蒸馏学科和工程研究开发的主要目标[1 ,2 ] ,并由此开发出以蒸馏理论为基础的许多新型复合传质分离技术,主要有以下几个方面:分子精馏、添加物精馏、耦合精馏和热敏物料精馏。
我尽量大概介绍,并将其中个人觉得比较重点的着重详细介绍。
1分子精馏技术分子蒸馏属于高真空下的单程连续蒸馏技术。
在高真空操作压力下,蒸发面和冷凝面的间距小于或等于被分离物质蒸汽分子平均自由程,由蒸发表面逸出的分子毫无阻碍地奔射并凝集在冷凝表面上。
这样利用不同物质分子平均自由程不同使其在液体表面蒸发速率不同,从而达到分离目的,蒸馏过程如下图所示。
相对于普通的真空蒸馏,分子蒸馏汽液相间不存在相平衡,是一种完全不可逆过程,具有以下特点。
操作压力低(0.1~10Pa);"蒸发面和冷凝面之间的间距小(10~50mm),操作温度远低于沸点;物料受热时间短(0.1-10s)。
因而适用于高分子量、高沸点、热稳定性差的物质蒸馏,特别是高分子有机化合物、热敏性食品、医药产品、塑料等物质的分离、提纯、蒸馏、反应等。
随着合成化学的进展,新的、从来不为人所知的物质的操作愈来愈多,如高分子物质的单体正在不断地构成新的物质,而且新的物质大部分都不稳定,用以往的蒸馏方法多会发生分解或聚合,而使用分子蒸馏就可以加以解决。
1.1理论基础分子平均自由程分子平均自由程是指气体分子在两次连续碰撞之间所走路程的平均值。
精细化工中的高真空连续精馏技术
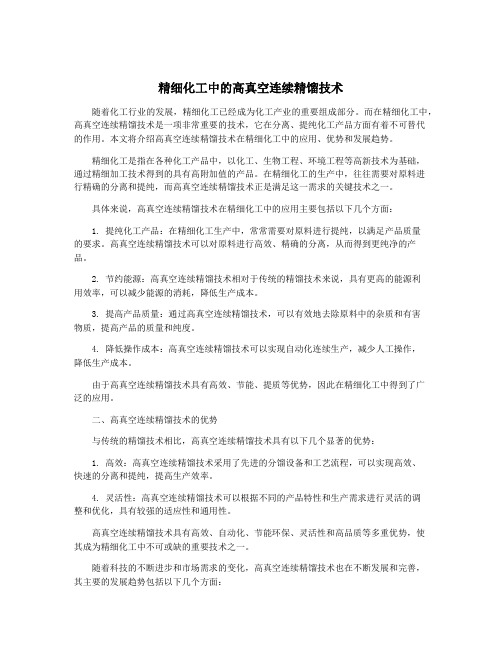
精细化工中的高真空连续精馏技术随着化工行业的发展,精细化工已经成为化工产业的重要组成部分。
而在精细化工中,高真空连续精馏技术是一项非常重要的技术,它在分离、提纯化工产品方面有着不可替代的作用。
本文将介绍高真空连续精馏技术在精细化工中的应用、优势和发展趋势。
精细化工是指在各种化工产品中,以化工、生物工程、环境工程等高新技术为基础,通过精细加工技术得到的具有高附加值的产品。
在精细化工的生产中,往往需要对原料进行精确的分离和提纯,而高真空连续精馏技术正是满足这一需求的关键技术之一。
具体来说,高真空连续精馏技术在精细化工中的应用主要包括以下几个方面:1. 提纯化工产品:在精细化工生产中,常常需要对原料进行提纯,以满足产品质量的要求。
高真空连续精馏技术可以对原料进行高效、精确的分离,从而得到更纯净的产品。
2. 节约能源:高真空连续精馏技术相对于传统的精馏技术来说,具有更高的能源利用效率,可以减少能源的消耗,降低生产成本。
3. 提高产品质量:通过高真空连续精馏技术,可以有效地去除原料中的杂质和有害物质,提高产品的质量和纯度。
4. 降低操作成本:高真空连续精馏技术可以实现自动化连续生产,减少人工操作,降低生产成本。
由于高真空连续精馏技术具有高效、节能、提质等优势,因此在精细化工中得到了广泛的应用。
二、高真空连续精馏技术的优势与传统的精馏技术相比,高真空连续精馏技术具有以下几个显著的优势:1. 高效:高真空连续精馏技术采用了先进的分馏设备和工艺流程,可以实现高效、快速的分离和提纯,提高生产效率。
4. 灵活性:高真空连续精馏技术可以根据不同的产品特性和生产需求进行灵活的调整和优化,具有较强的适应性和通用性。
高真空连续精馏技术具有高效、自动化、节能环保、灵活性和高品质等多重优势,使其成为精细化工中不可或缺的重要技术之一。
随着科技的不断进步和市场需求的变化,高真空连续精馏技术也在不断发展和完善,其主要的发展趋势包括以下几个方面:2. 自动化:随着智能制造技术的发展,高真空连续精馏技术将会更加智能化、自动化,实现智能监控、远程操作等功能。
石油化工中的精馏技术
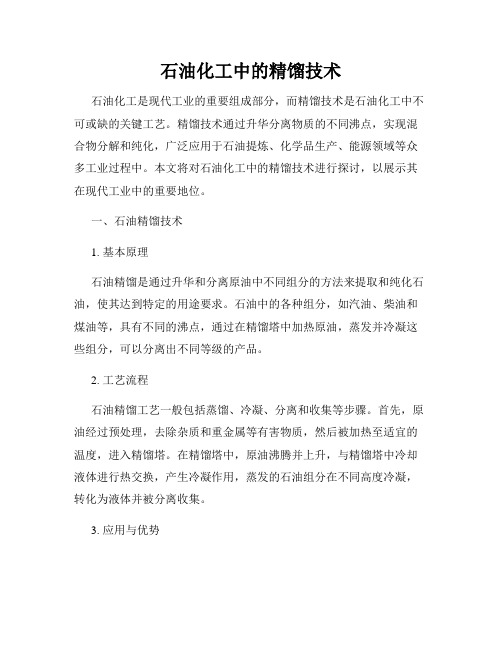
石油化工中的精馏技术石油化工是现代工业的重要组成部分,而精馏技术是石油化工中不可或缺的关键工艺。
精馏技术通过升华分离物质的不同沸点,实现混合物分解和纯化,广泛应用于石油提炼、化学品生产、能源领域等众多工业过程中。
本文将对石油化工中的精馏技术进行探讨,以展示其在现代工业中的重要地位。
一、石油精馏技术1. 基本原理石油精馏是通过升华和分离原油中不同组分的方法来提取和纯化石油,使其达到特定的用途要求。
石油中的各种组分,如汽油、柴油和煤油等,具有不同的沸点,通过在精馏塔中加热原油,蒸发并冷凝这些组分,可以分离出不同等级的产品。
2. 工艺流程石油精馏工艺一般包括蒸馏、冷凝、分离和收集等步骤。
首先,原油经过预处理,去除杂质和重金属等有害物质,然后被加热至适宜的温度,进入精馏塔。
在精馏塔中,原油沸腾并上升,与精馏塔中冷却液体进行热交换,产生冷凝作用,蒸发的石油组分在不同高度冷凝,转化为液体并被分离收集。
3. 应用与优势石油精馏技术在石油炼制过程中具有广泛的应用,可以生产出各种不同等级的燃料,如汽油、柴油、重柴油等。
同时,精馏技术还可以提取石油中的其他重要有机化合物,如石油焦油、溶剂油等,用于化工产品的生产。
其优势在于工艺简单、成本低廉,且具有高效分离和纯化的能力。
二、化工领域中的精馏技术应用1. 化学品生产在化学品的生产过程中,精馏技术被广泛应用于有机物的纯化和分离。
例如,聚合物的制备过程中,需要将不同分子量的聚合物分离出来以获得所需的产品。
此外,化学反应中产生的副产物或杂质也可以通过精馏技术进行纯化,提高产品的质量和纯度。
2. 精细化工精馏技术在精细化工领域中也有重要应用。
许多有机化合物需要经过纯化和分离,以满足特定的工业用途要求。
例如,医药行业中制剂的生产过程中需要对化合物进行纯化,确保产品的纯度和安全性。
精细化工中的精馏技术为化合物的分离纯化提供了有效的工艺手段。
3. 能源领域在能源领域中,精馏技术被广泛应用于燃料的生产和精制过程中。
精细化工中的高真空连续精馏技术
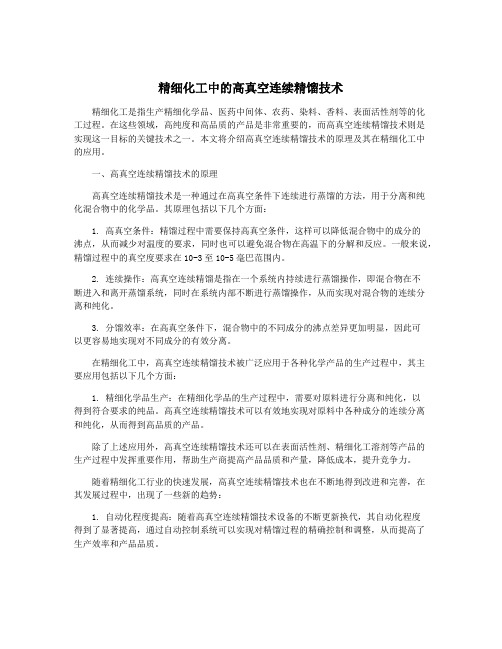
精细化工中的高真空连续精馏技术精细化工是指生产精细化学品、医药中间体、农药、染料、香料、表面活性剂等的化工过程。
在这些领域,高纯度和高品质的产品是非常重要的,而高真空连续精馏技术则是实现这一目标的关键技术之一。
本文将介绍高真空连续精馏技术的原理及其在精细化工中的应用。
一、高真空连续精馏技术的原理高真空连续精馏技术是一种通过在高真空条件下连续进行蒸馏的方法,用于分离和纯化混合物中的化学品。
其原理包括以下几个方面:1. 高真空条件:精馏过程中需要保持高真空条件,这样可以降低混合物中的成分的沸点,从而减少对温度的要求,同时也可以避免混合物在高温下的分解和反应。
一般来说,精馏过程中的真空度要求在10-3至10-5毫巴范围内。
2. 连续操作:高真空连续精馏是指在一个系统内持续进行蒸馏操作,即混合物在不断进入和离开蒸馏系统,同时在系统内部不断进行蒸馏操作,从而实现对混合物的连续分离和纯化。
3. 分馏效率:在高真空条件下,混合物中的不同成分的沸点差异更加明显,因此可以更容易地实现对不同成分的有效分离。
在精细化工中,高真空连续精馏技术被广泛应用于各种化学产品的生产过程中,其主要应用包括以下几个方面:1. 精细化学品生产:在精细化学品的生产过程中,需要对原料进行分离和纯化,以得到符合要求的纯品。
高真空连续精馏技术可以有效地实现对原料中各种成分的连续分离和纯化,从而得到高品质的产品。
除了上述应用外,高真空连续精馏技术还可以在表面活性剂、精细化工溶剂等产品的生产过程中发挥重要作用,帮助生产商提高产品品质和产量,降低成本,提升竞争力。
随着精细化工行业的快速发展,高真空连续精馏技术也在不断地得到改进和完善,在其发展过程中,出现了一些新的趋势:1. 自动化程度提高:随着高真空连续精馏技术设备的不断更新换代,其自动化程度得到了显著提高,通过自动控制系统可以实现对精馏过程的精确控制和调整,从而提高了生产效率和产品品质。
2. 节能环保型:随着人们对环保要求的不断提高,高真空连续精馏技术设备也在朝着节能环保型方向发展,采用了一些新的工艺和材料,降低了能耗和排放,实现了清洁生产。
热泵精馏技术进展介绍

热泵精馏技术进展介绍热泵精馏技术是一种新型的能源利用技术,它是在传统精馏技术的基础上,引入热泵技术,利用热泵对馏分进行加热,从而提高能源利用效率。
热泵精馏技术具有节能、环保、经济等优点,在石油、石化、化工等行业得到了广泛应用。
本文将从热泵精馏技术的基本原理、应用领域、发展现状等方面进行介绍。
一、热泵精馏技术的基本原理热泵精馏技术是将热泵技术应用于传统精馏技术中,其基本原理是利用热泵对馏分进行加热。
热泵是一种能够将低温热量转化为高温热量的装置,它利用制冷剂的循环来完成热量的传递。
热泵精馏技术利用热泵对馏分进行加热,从而提高馏分的温度,使其易于挥发,从而达到提高精馏效率的目的。
热泵精馏技术不仅可以提高能源利用效率,还可以减少环境污染,具有很高的经济效益和社会效益。
二、热泵精馏技术的应用领域热泵精馏技术具有广泛的应用领域,主要包括石油、石化、化工等行业。
在石油行业中,热泵精馏技术可以用于提炼各种石油产品,如汽油、柴油、润滑油等。
在石化行业中,热泵精馏技术可以用于生产各种化工产品,如聚合物、合成纤维等。
在化工行业中,热泵精馏技术可以用于生产各种化工产品,如酸、碱、盐酸等。
三、热泵精馏技术的发展现状热泵精馏技术是一种新型的能源利用技术,近年来得到了快速发展。
在国内,热泵精馏技术已经得到了广泛的应用,各大石油、石化、化工企业都在积极推广和应用这项技术。
同时,国家也在加大对热泵精馏技术的支持力度,制定了相关政策和标准,为热泵精馏技术的发展提供了保障。
在国际上,热泵精馏技术也得到了广泛的应用,各大石油、石化、化工企业都在积极推广和应用这项技术。
四、热泵精馏技术的未来发展热泵精馏技术是一种具有广阔前景的技术,未来的发展前景非常广阔。
随着科技的不断进步和热泵技术的不断改进,热泵精馏技术将会更加成熟和稳定。
同时,随着环保意识的不断提高,热泵精馏技术将会越来越受到重视和关注。
未来,热泵精馏技术将会在各个行业中得到广泛的应用,为推进经济发展和环境保护做出更大的贡献。
超重力精馏技术应用进展
超重力精馏技术应用进展刘 坤山东尚舜化工有限公司Copyright©博看网. All Rights Reserved.44应用技术APPLIED TECHNOLOGY二、超重力精馏原理超重力精馏是一种新型的精馏技术,通过高速旋转产生的离心力来实现超重力场(10~1000g 作用下)的环境,即超重力因子β(ω2r/g )通常可以达到350~450。
在这样的环境下,精馏塔内的气、液两相速度被大幅度提高,其速度可达4~12m/s ,远高于传统塔设备的1.5~1.6m/s ,大大提高了液泛速度。
在转子高速旋转下,超重力塔内的液体被加速甩出,在转子及定子间折流流道中,被逆向行驶的高速旋转汽流剪切撕裂成微图1 超重力精馏装置Copyright ©博看网. All Rights Reserved.45应用技术APPLIED TECHNOLOGY米至纳米级的液膜、液丝和液滴,从而极大地强化了气、液两相间的传热、传质过程,使传质效率比普通塔高出10多倍。
同样产能所需的设备体积也大大缩小(高度缩小8~10倍),同时使用超重力精馏设备分离效果也大为提高(单位体积内的理论塔板数大大提高,传质单元高度仅为1cm左右)。
超重力精馏在设备体积、塔板压降等方面都具有巨大的优势。
三、超重力精馏应用1.工作流程超重力精馏装置见图1。
利用超重力精馏塔作为回收溶剂的主要设备,实现了不同沸点混合液体的分离。
工作时,来自储罐的待分离混合液经在线流量控制进入预热器内,与来自超重力精馏塔的馏分进行换热,既对馏分起到了降温作用,又对原料进行了加热,起到了很好的节能效果。
经过预热的原料通过两路进入超重力精馏塔内,进塔的管道控制阀门通过DSC系统在线调节流量,以达到最佳分离效果。
降温后的馏分分为液相和气相,液相经冷凝器再次冷凝至40℃以下,经检测符合要求的馏分进入成品罐内等待使用,若检测不能满足标准,通过中间罐收集后,将重新进入超重力精馏塔精馏。
精馏技术的发展及应用
精馏技术的发展及应用引言精馏技术是一种通过以不同的沸点将液体混合物分离成纯度较高的组分的方法。
其原理基于不同组分的沸点差异,通过蒸馏和冷凝过程将混合物分离开来。
精馏技术的发展对于化工、制药、石化等工业领域起到了重要的作用。
本文将对精馏技术的发展历程、工艺改进以及应用领域进行探讨。
二级标题1:精馏技术的历史发展精馏技术作为一种传统的分离方法,其发展经历了多个阶段。
以下是精馏技术历史中的几个重要里程碑:三级标题1:早期蒸馏技术•制造酒精始于公元前5000年左右•早期的蒸馏技术主要用于酿酒和提取药物•通过釜炉加热,利用蒸气冷凝分离纯酒精三级标题2:酒精蒸馏的发展•9世纪阿拉伯人发明了现代酒精蒸馏的方法•使用多级塔式蒸馏柱提高蒸馏效率和纯度•酒精蒸馏技术被广泛应用于化妆品、酿造和药物行业二级标题2:精馏工艺的改进随着科学技术的进步和工业需求的增加,精馏工艺也得到了不断的改进。
以下是一些精馏工艺的改进方法:三级标题1:分馏柱的改进•引入反向进料技术,提高馏程效率•使用先进材料和结构设计,提高传热效率和分离效果三级标题2:新型提馏剂的使用•引入分子筛和化学剂等新型提馏剂,提高分离效率和纯度•降低操作温度和能耗,提高生产效率三级标题3:辅助设备的改进•利用先进的传感器和控制系统,实现自动化操作和精确控制•引入节能设备和循环系统,减少原材料和能源的浪费二级标题3:精馏技术的应用领域精馏技术在各个行业中都有广泛的应用。
以下是一些精馏技术的应用领域:三级标题1:石化行业•石油精馏过程中分离不同油品,如汽油、柴油和重油•生产乙烯和丙烯等石化产品中的纯化步骤三级标题2:制药行业•纯化药物原料和中间体,提高产品纯度和质量•分离和回收有机溶剂和溶剂副产品三级标题3:化工行业•生产化工原料和精细化工品的纯化和分离•回收和处理废气、废水和废弃物三级标题4:食品饮料行业•生产纯净水和饮料的处理和提纯•分离酒精和饮料中的其他成分结论精馏技术作为一种重要的分离方法,在工业生产中发挥了重要的作用。
国内的精馏趋势分析现状
国内的精馏趋势分析现状近年来,国内的精馏行业呈现出一系列的发展趋势,这主要受到全球宏观经济环境、国内政策导向以及市场需求等多方面因素的影响。
以下是对国内精馏行业现状的分析,涵盖了市场规模、技术创新、环保趋势以及行业竞争等方面。
市场规模与需求随着我国经济的不断增长和产业结构的升级,精馏行业在过去几年里经历了快速扩张。
石油、化工、医药等行业对精馏产品的需求持续增加,推动了整个行业的发展。
此外,随着新能源、新材料等领域的崛起,对高品质精馏产品的需求也逐渐增加,促使企业不断提升技术水平和产品质量。
技术创新与产业升级在技术创新方面,国内精馏行业正面临由传统制造向智能制造的转变。
自动化、信息化等先进技术的应用,使得生产过程更加智能化和高效化。
同时,新型材料、新工艺的引入提升了产品性能,推动了整个产业向高端化、专业化发展。
环保趋势与可持续发展近年来,环保问题成为社会关注的焦点之一,精馏行业也在不断加强环保意识。
政府颁布的一系列环保法规促使企业加大对污染治理的投入,推动了清洁生产技术的应用。
同时,一些企业开始关注可持续发展,致力于绿色生产、资源循环利用,以适应未来可持续发展的趋势。
行业竞争格局由于市场需求的不断增加,精馏行业的竞争格局也在发生变化。
一方面,一些传统大型企业通过不断升级技术、优化产品结构,保持了在市场中的竞争优势。
另一方面,一些新兴企业通过创新技术、灵活的经营模式,逐渐崭露头角。
同时,国际市场的竞争也对国内精馏企业提出了更高的要求,促使其不断提升竞争力。
未来发展趋势展望在未来,国内精馏行业将继续受到多方面因素的影响,其中包括政策环境、市场需求、技术创新等。
预计随着我国经济结构的进一步升级和绿色制造理念的深入推进,精馏行业将迎来更多的发展机遇。
同时,企业需要加强技术研发,提升产品质量,不断优化生产流程,以适应市场的变化和国际竞争的挑战。
总体而言,国内精馏行业在发展过程中面临着机遇和挑战。
通过持续的技术创新、环保意识的提升以及市场需求的引导,该行业有望实现可持续发展,并在未来取得更大的成就。
新型精馏技术
1 反应精馏反应精馏作为一种新型特殊精馏,因其具有独特的优势而在化学工业中日益受到重视。
由于反应段固体催化剂的选择及装填方式对该工艺起关键作用,故国内外在注重工艺开发的同时,也需要在催化剂及填料上多做研究,以取得更大突破。
目前,反应精馏技术已在多个领域实现了产业化,对某些新领域的开发也取得了一定进展。
随着节能和环保要求日益提高,该技术与先进的计算机模拟软件相结合,在未来几十年将会发挥更大作用,同时会有更好的发展。
1.1 反应精馏技术基本原理反应精馏是在进行反应的同时用精馏方法分离出产物的过程。
其基本原理为;对于可逆反应,当某一产物的挥发度大于反应物时,如果将产物从液相中蒸出,则可破坏原有的平衡,使反应继续向生成物的方向进行,因而可提高单程转化率,在一定程度上变可逆反应为不可逆反应。
1.2 反应精馏技术特点(1) 反应和精馏在同一设备中进行,简化了流程,使设备费和操作费同时下降。
(2) 对于放热反应过程,反应热全部提供为精馏过程所需热量的一部分,节省了能耗。
(3) 对于可逆反应过程中,由于产物的不断分离,可使系统远离平衡状态,增大过程的转化率。
可使最终转化率大大超过平衡转化率,减轻后续分离工序的负荷。
(4) 对于目的产物具有关二次副反应的情形,通过某一反应物的不断分离,从而抑制了副反应,提高了选择性。
(5) 在反应精馏塔内,各反应物的浓度不同于进料浓度。
因此,进料可按反应配比要求,而塔板上造成某种反应物的过量,可使反应后期的反应速度大大提高、同时又达到完全反应;或造成主副反应速率的差异,达到较高的选择性。
这样,对于传统工艺中某些反应物过量从而需要分离回收的情况,能使原料消耗和能量消耗得到较大节省。
(6) 在反应精馏塔内,各组份的浓度分布主要由相对挥发度决定,与进料组成关系不大,因而反应精馏塔可采用低纯度的原料作为进料。
这一特点可使某些系统内循环物流不经分离提纯直接得到利用。
(7) 有时反应物的存在能改变系统各组份的相对挥发度,或绕过其共沸组成,实现沸点相近或具有恒沸组成的混合物之间的完全分离。
- 1、下载文档前请自行甄别文档内容的完整性,平台不提供额外的编辑、内容补充、找答案等附加服务。
- 2、"仅部分预览"的文档,不可在线预览部分如存在完整性等问题,可反馈申请退款(可完整预览的文档不适用该条件!)。
- 3、如文档侵犯您的权益,请联系客服反馈,我们会尽快为您处理(人工客服工作时间:9:00-18:30)。
新型精馏技术及其发展趋【摘要】本文主要介绍反应精馏和隔壁精馏技术,对其原理、优缺点及研究现状进行了综述。
总结了技术中存在的问题并展望其发展前景,结果表明这是两种很有发展前景的精馏技术,在未来会有很好发展。
【关键字】反应精馏;隔壁精馏;发展趋势一、反应精馏(一)、概述反应精馏是蒸馏技术中的一个特殊领域。
目前,反应精馏一方面成为提高分离效率而将反应与精馏相结合的一中分离操作,另一方面则成为提高反应收率而借助于精馏分离手段的一种反应过程。
它有许多优点,可以替代某些传统工艺过程如醚化、加氢、芳烃烷基化等反应,在工业上得到了一定的重视。
但长期以来,对于反应精馏的研究仅限于工艺方面,直到上世纪80年代,反应精馏的基础理论性研究才开始引起研究人员的兴趣和重视。
主要分为三种情况:用精馏促进反应,用反应促进精馏,催化精馏。
1、用精馏促进反应用精馏促进反应,就是通过精馏不断移走反应的生成物,产物离开了反应区,从而破坏了原有的化学平衡,使反应向生成产物的方向移动,以提高反应转化率和收率。
在一定程度上变可逆为不可逆,而且可得到很纯的产物。
但采用这种方法必须具备一定的条件:①生成物的沸点必须高于或低于反应物;②在精馏温度下不会导致副反应等不利影响的增加。
目前在工业上主要应用于酯类(如乙酸乙酯)的生产。
2、用反应促进精馏在待分离的混合物溶液中加入反应夹带剂,使其有选择地与溶液中的某一组分发生快速可逆反应,以加大组分间的挥发度差异,从而能容易地用精馏方法将混合物分离。
通常用于组分的挥发度很接近但化学性质存在差异的混合物。
3、催化精馏催化精馏实质是一种非均相催化反应精馏。
将催化剂填充于精馏塔中,它既起加速反应的催化作用,又作为填料起分离作用,催化精馏具有均相反应精馏的全部优点,既适合于可逆反应,也适合于连串反应。
反应精馏的原理可用下图来表示:(二)、反应精馏技术的优点1、选择性高,由于反应产物一旦生成即移出反应区,对于如连串反应之类的复杂反应,可抑制副反应,提高收率。
2、破坏了可逆反应平衡,增加了反应的选择性和转化率,使反应速度提高,缩短反应时间,从而提高了生产能力。
3、精馏过程可以利用反应热,节省了能量,操作费用低。
4、反应器和精馏塔合成一个设备,节省投资。
5、对某些难分离的物系,可以获得较纯的产品。
6、系统容易控制,常用改变塔的操作压力来改变液体混合物的沸点(即反应温度),从而改变反应速率和产品分布。
(三)、反应精馏技术的缺点1、要求比较苛刻,例如:(1)化学反应必须在液相中进行。
(2)在操作系统压力下,主反应的反应温度和目的产物的泡点温度接近,以使目的产物及时从反应体系中移出。
(3)主反应不能是强吸热反应,否则精馏操作的传热和传质会受到严重影响,会使塔板分离效率减低,甚至使精馏操作无法顺利进行。
(4)主反应时间和精馏时间相比较,主反应时间不能过长,否则精馏塔的分离能力不能得到充分利用。
(5)对于催化蒸馏,要求催化剂具有较长的使用寿命,因为频繁地更换催化剂需要停止反应精馏操作,从而影响到生产效率,同时增加了生产成本。
(6)催化剂的装填结构不仅能使催化反应顺利进行,同时要保证精馏操作也能较好地进行。
(2.对物系有要求所有产物的挥发度大于所有反应物的挥发度;所有反应物的挥发度大于所有产物的挥发度;所有反应物的挥发度介于产物的挥发度之间。
只有这三种情况可以用反应精馏。
(四)、反应精馏的发展趋势及存在问题1.发展历程及趋势有关反应精馏的早期研究始于1921年,反应精馏概念由Backhaus 提出,从20世纪30年代到60年代初,主要对一些特定体系的工艺条件进行探索,并且局限于板式塔中的均相反应精馏。
一直到60年代末,才开始对反应精馏的一般性规律进行研究。
70年代后,开始转向反应精馏的工艺计算,同时也开始对催化精馏进行研究。
20世纪80年代后,反应精馏模拟计算的研究异常活跃,为优化操作和设计装置提供了极为有力的工具,数学模型也由平衡级模型拓展到非平衡级模型进而发展到90年代末的非平衡池模型,可模拟气相和液相在级上的停留时间分布和较准确地描述反应和传质行为,是对非平衡级模型的提高和进一步完善,是非常有前途的反应精馏模型。
国内在这方面的研究起步较晚,据悉,西安交通大学已经对反应精馏和膜分离工艺进行了研究,取得了一定进展。
对于某些已成熟工艺,开发其在新领域的应用也具有重要意义,如将反应精馏用于分离的工艺研究。
目前,反应精馏技术已在多个领域实现了产业化,对某些新领域的开发也取得了一定进展。
随着节能和环保的要求日益提高,反应精馏技术将会发挥更大作用,是解决能源危机和缓解三废污染的有效途径。
结合了先进的计算机模拟工具,相信反应精馏工艺在未来几十年将会有更好的发展。
2.发展中要解决的关键问题(1)反应物种类及反应物和产物的性质对反应精馏的影响。
(2)反应热效应对精馏过程的影响。
(3)非均相催化反应精馏过程的传递规律及其设计方法。
(4)用于精细化工生产的间歇反应精馏的非稳态特性。
二、隔壁精馏(一)、概述隔壁精馏塔简称DWC,DWC是在精馏塔内部设置一个垂直隔板,将精馏塔分为上段,下段,以及由隔板分开的精馏进料段及中间采出段,共四部分。
1、隔壁精馏塔塔的结构特点对于传统的三元混合物分离,若采用简单塔分离序列,至少需要2 个精馏塔才能使其得到有效分离。
而图 1 所示的隔壁塔,利用隔壁将普通精馏塔从中间分割为2 部分,隔壁巧妙的使用实现了两塔的功能及三元混合物的分离。
在隔壁塔中, 进料侧为预分离段,另一端为主塔,混合物A、B、C 在预分离段经初步分离后为A、 B 和B、 C 两组混合物,A、B和B、 C 两股物流进入主塔后,塔上部将A、 B 分离,塔下部将B、 C 分离, 在塔顶得到产物A, 塔底得到产物C,中间组分B 在主塔中部采出。
同时,主塔中又引出液相物流和气相物流分别返回进料侧顶部和底部,为预分离段提供液相回流和初始气相。
这样,只需1 座精馏塔就可得到3 个纯组分,同时还可节省1个蒸馏塔及其附属设备,如再沸器、冷凝器、塔顶回流泵及管道,而且占地面积也相应减少。
一般来说,与传统的两简单塔分离序列相比,隔壁塔的能耗及设备投资均可降低30%左右。
2、隔壁精馏塔的节能原理(1)避免了中间组分的返混效应。
在常规两塔分离序列中,塔 1 提馏段内随着轻组分A 浓度的降低,中间组分 B 的浓度逐渐增加,但在靠近塔釜处,由于重组分C 浓度增加,中间 B 组分浓度在达到最大值后逐渐减小,即组分 B 在该塔中发生返混,这也是该塔分离效率较低的重要原因。
与之相反,在隔壁塔中,经预分离段分离后的A、 B 和B、 C 两组混合物进入主塔后做进一步分离,其中,中间 B 组分在塔中浓度达到最大时采出,这就有效避免了两塔流程中的返混现象。
( 2) 减小进料与进料板上物流组成不同引起的混合问题。
在预分离段顶部和底部B 组分的组成完全和主塔这两股物料进料板上的组成相匹配,符合最佳进料板的要求。
(二)、隔壁精馏技术的优点(1)可得到较高纯的中间产品。
由于隔壁塔所采出的中间产品纯度比单个精馏塔侧线出料达到的纯度要大, 因此,当希望得到高纯度的中间产品时, 可考虑使用隔壁精馏塔。
(2)与传统的两简单塔分离序列相比,隔壁塔的能耗及设备投资均可降低30%左右。
(3)当中间组分为进料中的主要组分, 而轻组分和中间组分的相对挥发度与中间组分和重组分的相对挥发度大小相当时, 采用隔壁塔时节能优势更为明显。
(三)、隔壁精馏技术的缺点(1)由于采用隔壁精馏塔分离三组分混合物是在同一塔设备内完成, 故整个分离过程的压力不能改变。
(2)工艺计算及控制比较复杂。
(3)由于两个精馏塔的控制条件被并到了一个隔壁精馏塔中,塔的控制条件增加了,控制回路增加及机械加工等问题是隔壁精馏无法实现大生产。
(四)、隔壁精馏的发展趋势及存在的问题1.发展历程及趋势1933 年, 因裂解气分离问题, Eric W Luster,提出了隔壁塔概念,并申请了美国专利,但由于其工艺计算及控制的复杂性,直到1985 年, 第一座用于回收精细化学品的隔壁塔才投入工业运转。
目前,大部分运营的隔壁塔为BASF 公司拥有,并由德国Montz 公司提供塔内件,如南非萨索尔公司用于回收合成汽油混合物中 1 - 己烯的隔壁塔即采用了BASF 公司的技术,该塔也是目前世界上最高的一座隔壁塔,其高达107 m, 直径 5 m。
到2006年9月,全世界工业化隔壁塔已发展到近100座。
2.发展趋势隔壁塔技术在多元物系分离中的成功运用,证明了其在降低能耗、减少设备投资方面的巨大潜力。
近年来,研究者们已着眼于将隔壁塔技术应用于特殊精馏体系,如反应精馏、萃取精馏、共沸精馏等新领域,以期最大限度降低能耗。
近年来,国外正在加快隔壁塔的工业化步伐,并取得了令人瞩目的成果。
我国对隔壁塔的研究较少,更缺少实际工业化应用。
加快此项技术的开发和工业化应用步伐,并且拥有独立的知识产权,对降低工业生产的能源消耗,减少CO2 的排放,推动我国石油、化工行业的发展具有重要意义。
3.发展中要解决的关键问题在国内尚未发现隔壁精馏研究机构和应用单位,相关的研究文章也比较少。
我国在石油化工及天然气化工领域的能耗比国外大,占石油化工及天然气化工能耗70 %~80 %的老式精馏操作是有过度耗能之嫌的。
在扩大精馏生产或投资新厂时应考虑应用隔壁精馏。
将隔壁精馏塔工业化,并拥有自己的技术是未来要解决的关键问题。
三、总结综上所述,反应精馏和隔壁精馏都具有各自的优势,加快它们的发展对降低工业生产的能耗,推动我国化工发展有重要意义。
但是要做到这些,还需要加快科技发展和研发,还有很多的工作要做。
相信这两种工艺在将来都会有很好的发展。