列管式换热器设计方案
列管式换热器设计方案计算过程参考

列管式换热器设计方案计算过程参考
设计换热器的过程一般包括以下几个步骤:确定换热器类型、选择换
热器材质、计算换热面积、计算换热器尺寸、计算流体流量和温度等。
1.确定换热器类型:根据具体的工艺要求、流体性质和换热效率要求,确定使用的换热器类型,如管壳式换热器、管板式换热器、板式换热器等。
2.选择换热器材质:根据流体性质和工艺要求,选择合适的换热器材质,如不锈钢、碳钢、镍及其合金等。
考虑耐腐蚀性、强度和成本等因素。
3.计算换热面积:根据流体的流量、温度和换热传热系数,计算所需
的换热面积。
换热面积的计算可以通过换热器设计软件进行,也可以通过
数学公式计算,例如Q=U*A*(ΔTm)式中的A即为换热面积。
4.计算换热器尺寸:根据换热面积、管子直径和管排布方式,计算换
热器的尺寸,包括换热器的长度、宽度和高度等。
根据需要还可以进行结
构强度校核和模态分析等。
5.计算流体流量和温度:根据工艺要求和热力学计算,确定流体的流
量和温度。
通过质量守恒和能量守恒等原理进行计算,例如根据流体的流
量和温度差,计算冷却液的质量流率和冷却液的温度变化等。
总结起来,设计换热器的过程包括确定换热器类型和材质、计算换热
面积和尺寸,以及计算流体流量和温度等。
根据具体的工艺要求和流体性质,选择合适的设计参数,通过数学计算和换热器设计软件进行计算,最
终得到满足工艺要求的换热器设计方案。
列管式换热器设计

列管式换热器设计列管式换热器是一种常见的换热设备,广泛应用于化工、石油、制药等行业中。
本文将从列管式换热器的设计原理、设计步骤和设计考虑因素三个方面进行详细介绍。
一、设计原理列管式换热器是通过管内的换热流体和管外的换热流体之间的换热传递来实现热量的传递。
它的基本原理是利用换热流体在管内和管外的对流,通过管壁的传导传热作用,使热量从高温流体传递给低温流体。
二、设计步骤1.确定换热器的使用条件:包括换热流体的性质、入口温度、出口温度等。
2.确定换热器的换热面积:根据换热流体的热负荷和传热系数来计算所需的换热面积。
3.选择管子的尺寸和材料:根据换热流体的性质和流量来选择合适的管子尺寸和材料。
4.确定管子的数量和布置方式:根据换热面积和换热流体的流量来确定管子的数量和布置方式,一般采用多行多列的方式。
5.设计管束的尺寸:根据换热面积和管子的数量来确定管束的尺寸,包括管束的直径、长度和布置方式等。
6.计算换热器的传热系数:根据换热面积、流体的性质和传热方式来计算换热器的传热系数。
7.计算换热器的压降:根据流体的流量、管束的阻力和流体的性质来计算换热器的压降。
8.进行换热器的热力学计算:包括换热器的热力学效率、有效传热面积和温差效益等。
三、设计考虑因素1.热负荷:根据换热流体的热负荷来确定换热器的换热面积和管子的数量。
2.材料选择:根据换热流体的性质和工艺要求来选择合适的材料,包括管子的材料和管壳的材料。
3.温度差:根据换热流体的温度差来确定管束的数量和换热器的传热系数。
4.流体压降:根据流体的流量和管束的阻力来计算换热器的压降,并确定合适的管束布置方式和管束的尺寸。
5.清洗和维护:考虑到换热器的清洗和维护,要选择易于清洗和维护的结构设计。
综上所述,列管式换热器的设计是一个复杂的工程,需要考虑多个因素。
设计者需要根据具体的使用条件和要求来确定换热器的换热面积、管子的尺寸和材料、管束的数量和布置方式等。
同时,还需要计算换热器的传热系数、压降和热力学参数等。
化工原理课程设计---列管式换热器的设计
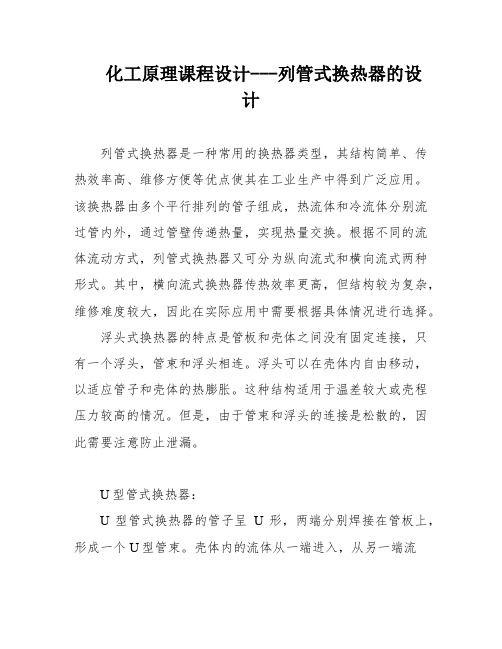
化工原理课程设计---列管式换热器的设计列管式换热器是一种常用的换热器类型,其结构简单、传热效率高、维修方便等优点使其在工业生产中得到广泛应用。
该换热器由多个平行排列的管子组成,热流体和冷流体分别流过管内外,通过管壁传递热量,实现热量交换。
根据不同的流体流动方式,列管式换热器又可分为纵向流式和横向流式两种形式。
其中,横向流式换热器传热效率更高,但结构较为复杂,维修难度较大,因此在实际应用中需要根据具体情况进行选择。
浮头式换热器的特点是管板和壳体之间没有固定连接,只有一个浮头,管束和浮头相连。
浮头可以在壳体内自由移动,以适应管子和壳体的热膨胀。
这种结构适用于温差较大或壳程压力较高的情况。
但是,由于管束和浮头的连接是松散的,因此需要注意防止泄漏。
U型管式换热器:U型管式换热器的管子呈U形,两端分别焊接在管板上,形成一个U型管束。
壳体内的流体从一端进入,从另一端流出,管内的流体也是如此。
这种结构适用于流体腐蚀性较强的情况,因为管子可以很容易地更换。
多管程换热器:多管程换热器是将管束分成多个组,每组管子单独连接到管板上,形成多个管程。
这种结构可以提高传热效率,但也会增加流体阻力。
因此,需要根据具体情况来选择多管程的数量。
总之,列管式换热器是一种广泛应用于化工及酒精生产的换热器。
不同的结构适用于不同的工艺条件,需要根据具体情况来选择合适的换热器。
在使用过程中,需要注意保养和维护,及时清洗和更换损坏的部件,以保证换热器的正常运行。
换热器的一块管板与外壳用法兰连接,另一块管板不与外壳连接,这种结构称为浮头式换热器。
浮头式换热器的优点是管束可以拉出以便清洗,管束的膨胀不受壳体约束,因此在两种介质温差大的情况下,不会因管束与壳体的热膨胀量不同而产生温差应力。
但其缺点是结构复杂,造价高。
填料式换热器的管束一端可以自由膨胀,结构比浮头式简单,造价也较低。
但壳程内介质有外漏的可能,因此不应处理易挥发、易燃、易爆和有毒的介质。
列管式换热器设计方案

列管式换热器设计方案第一节推荐的设计程序一、工艺设计1、作出流程简图。
2、按生产任务计算换热器的换热量Q。
3、选定载热体,求出载热体的流量。
4、确定冷、热流体的流动途径。
5、计算定性温度,确定流体的物性数据(密度、比热、导热系数等)。
6、初算平均传热温度差。
7、按经验或现场数据选取或估算K值,初算出所需传热面积。
8、根据初算的换热面积进行换热器的尺寸初步设计。
包括管径、管长、管子数、管程数、管子排列方式、壳体内径(需进行圆整)等。
9、核算K。
10、校核平均温度差 m T。
11、校核传热量,要求有15-25%的裕度。
12、管程和壳程压力降的计算。
二、机械设计1、壳体直径的决定和壳体壁厚的计算。
2、换热器封头选择。
3、换热器法兰选择。
4、管板尺寸确定。
5、管子拉脱力计算。
6、折流板的选择与计算。
7、温差应力的计算。
8、接管、接管法兰选择及开孔补强等。
9、绘制主要零部件图。
三、编制计算结果汇总表四、绘制换热器装配图五、提出技术要求 六、编写设计说明书第二节 列管式换热器的工艺设计一、换热终温的确定换热终温对换热器的传热效率和传热强度有很大的影响。
在逆流换热时,当流体出口终温与热流体入口初温接近时,热利用率高,但传热强度最小,需要的传热面积最大。
为合理确定介质温度和换热终温,可参考以下数据:1、热端温差(大温差)不小于20℃。
2、冷端温差(小温差)不小于5℃。
3、在冷却器或冷凝器中,冷却剂的初温应高于被冷却流体的凝固点;对于含有不凝气体的冷凝,冷却剂的终温要求低于被冷凝气体的露点以下5℃。
二、平均温差的计算设计时初算平均温差∆t m,均将换热过程先看做逆流过程计算。
1、对于逆流或并流换热过程,其平均温差可按式(2-1)进行计算:2121ln t t t t t m ∆∆∆-∆=∆ (2—1) 式中,1t ∆、2t ∆分别为大端温差与小端温差。
当221t t ∆∆时,可用算术平均值()221t t t m ∆+∆=∆。
列管式换热器的设计(化工原理课程设计)

列管式换热器的设计(化⼯原理课程设计)⽬录§⼀.任务书 (2)1.1.化⼯原理课程设计的重要性1.2.课程设计的基本内容和程序1.3.列管式换热器设计内容1.4.设计任务和操作条件1.5.主要设备结构图1.6.设计进度1.7.设计成绩评分体系§⼆.概述及设计要求 (4)2.1.换热器概述2.2.固定管板式换热器2.3.设计要求§三.设计条件及主要物理参数 (5)3.1.初选换热器的类型3.2.确定物性参数3.3.计算热流量及平均温差3.4.管程安排(流动空间的选择)及流速确定3.5.计算总传热系数3.6.计算传热⾯积§四. ⼯艺设计计算 (9)4.1.管径和管内流速4.2.管程数和传热管数4.3.平均传热温差校正及壳程数4.4.换热管选型汇总4.5.换热管4.6.壳体内径4.7.折流板4.8.接管4.9.壁厚的确定、封头4.10.管板§五.换热器核算 (14)5.1.热量核算5.2.壁温核算5.3.流动阻⼒核算§六. 设计结果汇总 (18)§七. 设计评述 (19)§⼋. ⼯艺流程图 (19)§.九.符号说明 (21)§.⼗.参考资料 (22)§⼀.化⼯原理课程设计任务书1.1.化⼯原理课程设计的重要性化⼯原理课程设计是学⽣学完基础课程以及化⼯原理课程以后,进⼀步学习⼯程设计的基础知识,培养学⽣⼯程设计能⼒的重要教学环节,也是学⽣综合运⽤化⼯原理和相关选修课程的知识,联系⽣产实际,完成以单元操作为主的⼀次⼯程设计的实践。
通过这⼀环节,使学⽣掌握单元操作设计的基本程序和⽅法,熟悉查阅技术资料、国家技术标准,正确选⽤公式和数据,运⽤简洁⽂字和⼯程语⾔正确表述设计思想和结果;并在此过程中使学⽣养成尊重实际问题向实践学习,实事求是的科学态度,逐步树⽴正确的设计思想、经济观点和严谨、认真的⼯作作风,提⾼学⽣综合运⽤所学的知识,独⽴解决实际问题的能⼒。
列管式换热器设计方案和选用
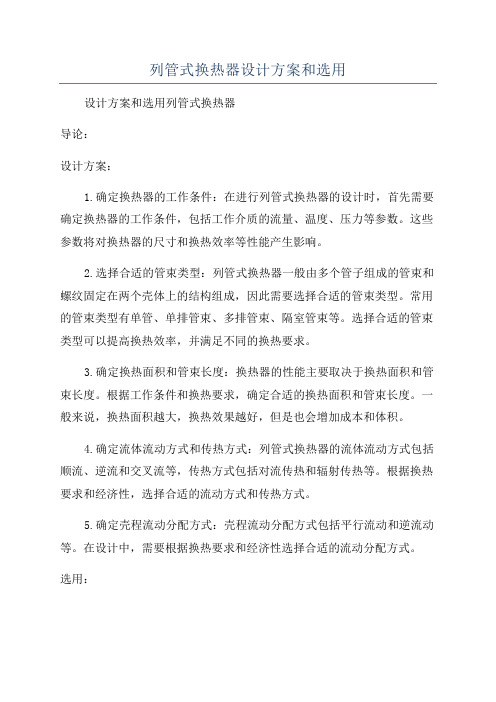
列管式换热器设计方案和选用设计方案和选用列管式换热器导论:设计方案:1.确定换热器的工作条件:在进行列管式换热器的设计时,首先需要确定换热器的工作条件,包括工作介质的流量、温度、压力等参数。
这些参数将对换热器的尺寸和换热效率等性能产生影响。
2.选择合适的管束类型:列管式换热器一般由多个管子组成的管束和螺纹固定在两个壳体上的结构组成,因此需要选择合适的管束类型。
常用的管束类型有单管、单排管束、多排管束、隔室管束等。
选择合适的管束类型可以提高换热效率,并满足不同的换热要求。
3.确定换热面积和管束长度:换热器的性能主要取决于换热面积和管束长度。
根据工作条件和换热要求,确定合适的换热面积和管束长度。
一般来说,换热面积越大,换热效果越好,但是也会增加成本和体积。
4.确定流体流动方式和传热方式:列管式换热器的流体流动方式包括顺流、逆流和交叉流等,传热方式包括对流传热和辐射传热等。
根据换热要求和经济性,选择合适的流动方式和传热方式。
5.确定壳程流动分配方式:壳程流动分配方式包括平行流动和逆流动等。
在设计中,需要根据换热要求和经济性选择合适的流动分配方式。
选用:1.根据工艺要求选择合适的材料:列管式换热器的材料对于其耐用性和可靠性有着重要影响。
根据介质的性质和工艺要求,选择合适的材料,如不锈钢、碳钢、铜等。
2.确定换热器的维护和清洗方式:列管式换热器由于结构复杂,清洗和维护较为困难。
因此,在选用时需要考虑清洗和维护的方便性,选择易于清洗和维护的设计。
3.考虑能量利用率和经济性:在选用列管式换热器时,还需要考虑能量利用率和经济性。
换热器的能量利用率越高,所需热交换面积就越小,经济性就越好。
因此,选择高效能量利用的换热器是非常重要的。
4.参考其他用户的反馈和评价:在选用列管式换热器时,可以参考其他用户对于不同品牌和型号的反馈和评价。
这些反馈和评价可以提供有关换热器性能和可靠性的宝贵信息。
总结:列管式换热器的设计方案和选用需要考虑多个因素,包括工作条件、管束类型、换热面积、管束长度、流体流动方式、传热方式、壳程流动分配方式、材料选择、维护和清洗方式以及能量利用率和经济性等。
果汁中列管式换热器设计
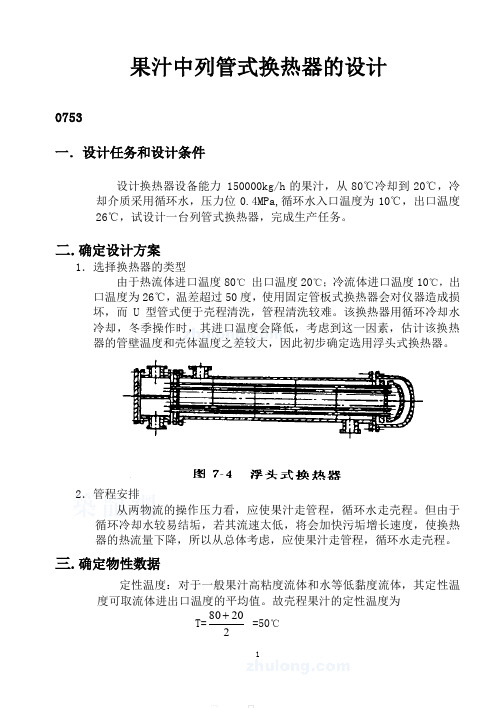
果汁中列管式换热器的设计0753一.设计任务和设计条件设计换热器设备能力 150000kg/h的果汁,从80℃冷却到20℃,冷却介质采用循环水,压力位0.4MPa,循环水入口温度为10℃,出口温度26℃,试设计一台列管式换热器,完成生产任务。
二.确定设计方案1.选择换热器的类型由于热流体进口温度80℃出口温度20℃;冷流体进口温度10℃,出口温度为26℃,温差超过50度,使用固定管板式换热器会对仪器造成损坏,而U型管式便于壳程清洗,管程清洗较难。
该换热器用循环冷却水冷却,冬季操作时,其进口温度会降低,考虑到这一因素,估计该换热器的管壁温度和壳体温度之差较大,因此初步确定选用浮头式换热器。
2.管程安排从两物流的操作压力看,应使果汁走管程,循环水走壳程。
但由于循环冷却水较易结垢,若其流速太低,将会加快污垢增长速度,使换热器的热流量下降,所以从总体考虑,应使果汁走管程,循环水走壳程。
三.确定物性数据定性温度:对于一般果汁高粘度流体和水等低黏度流体,其定性温度可取流体进出口温度的平均值。
故壳程果汁的定性温度为T=22080=50℃管程流体的定性温度为 t=1822610=+℃根据定性温度,分别查取壳程和管程流体的有关物性数据。
对果汁来说,最可靠的无形数据是实测值。
若不具备此条件,则应分别查取混合无辜组分的有关物性数据,然后按照相应的加和方法求出混和气体的物性数据。
果汁在50℃下的有关物性数据如下(来自生产中的实测值):密度 311050mkg =ρ 定压比热容 1p c =3.98kj/kg ℃热导率 1λ=0.61w/m粘度 s mpa .2.11=μ循环水在18℃ 下的物性数据:密度1ρ=998.2㎏/m 3 定压比热容 1p c =4.183kj/kg ℃热导率 1λ=0.5985 w/m ℃粘度 1μ=1.0042×10-3Pas四.估算传热面积1.热流量Q 1=111t c m p ∆=150000×3.98×(80-20)=35820000kj/h =9950kw2.平均传热温差 先按照纯逆流计算,得m t ∆=69.110202680ln )1020()2680(=-----k3.传热面积 由于管程压力较高,故可选取较大的K 值。
列管式换热器设计方案计算过程参考

根据给定的原始条件,确定各股物料的进出口温度,计算换热器所需的传热面积,设计换热器的结构和尺寸,并要求核对换热器压强降是否符合小于30 kPa的要求;各项设计均可参照国家标准或是行业标准来完成;具体项目如下:设计要求:,=0.727Χ10-3Pa.s密度ρ=994kg/m3粘度μ2导热系数λ=62.6Χ10-2 W/m.K 比热容Cpc=4.184 kJ/kg.K苯的物性如下:进口温度:80.1℃出口温度:40℃=1.15Χ10-3Pa.s密度ρ=880kg/m3粘度μ2导热系数λ=14.8Χ10-2 W/m.K 比热容Cpc=1.6 kJ/kg.K苯处理量:1000t/day=41667kg/h=11.57kg/s热负荷:Q=WhCphT2-T1=11.57×1.6×1000×80.1-40=7.4×105W冷却水用量:Wc=Q/c pc t2-t1=7.4×105/4.184×1000×38-30=22.1kg/s4、传热面积的计算;平均温度差确定R和P值查阅化工原理上册203页得出温度校正系数为0.8,适合单壳程换热器,平均温度差为△tm=△t’m×0.9=27.2×0.9=24.5由化工原理上册表4-1估算总传热系数K估计为400W/m²·℃估算所需要的传热面积:S0==75m²5、换热器结构尺寸的确定,包括:1传热管的直径、管长及管子根数;由于苯属于不易结垢的流体,采用常用的管子规格Φ19mm×2mm管内流体流速暂定为0.7m/s所需要的管子数目:,取n为123管长:=12.9m按商品管长系列规格,取管长L=4.5m,选用三管程管子的排列方式及管子与管板的连接方式:管子的排列方式,采用正三角形排列;管子与管板的连接,采用焊接法;2壳体直径;e取1.5d0,即e=28.5mmD i=tn c—1+2e=19×—1+2×28.5=537.0mm,按照标准尺寸进行整圆,壳体直径为600mm;此时长径比为7.5,符合6-10的范围;壳体壁厚的计算[]C ppD i+-=ψσδ2选取设计压力p=0.6MPa,壳体材料为Q235,查的相应的许用应力[]MPa 113=σ;焊接系数65.0=ψ单面焊,腐蚀裕度mm 4C =,所以mm mm 88.274.605.601132900.60==+-⨯⨯⨯=δδ排管方式:横过中心的管子数目:n c ==21.1,取整21根有排管图得出,中心有21根管道时,按照正三角形排列,可排331根,每边各加8根,总共可以排列379根,除去6根拉杆,总共可以排出373,与上述计算相差不大,所以实际管子数目为373根;实际传热面积S 0=N πd o L-0.1=373×3.14×0.019×4.5-0.1=97.9m ²实际传热系数K=W/m ²·K3折流板尺寸和板间距;选取折流板与壳体间的间隙为3.5mm,因此,折流板直径 Dc=600-2Χ3.5=593mm 切去弓形高度 h=0.25D=0.25Χ600=150mm 取折流板间距h o =300mm那么N B =4.5-0.1/0.3=14.6 ,取整得N B =15块实际折流板间距 h=L-0.1/N+1=4500-100/15+1=275mm 拉杆的直径和数量与定距管的选定;选用Φ12mm 钢拉杆,数量6条;定距管采用与换热管相同的管子,即Φ19mm Χ2mm 钢管;温度补偿圈的选用;由于80.1+40/2-30+38/2=26.05<50℃,故需不虑设置温度补偿圈; 4流体进出口接管直径等;苯的进出口管道直径:=0.15m经圆整采用Φ159mm ×10mm 热轧无缝钢管,实际苯的进出口管内流速为=0.867m ²水的进出口管道直径:=0.106m经圆整采用Φ108mm ×5mm 热轧无缝钢管,实际水的进出口管内流速为=2.5m6、管、壳程流体的压力降计算; 管程压降:ΣΔp i =Δp 1+Δp 2F t N s N p管程数N p =3,串联壳程数N s =1,对于Φ19mm Χ2mm 的换热管,结构校正系数为F t =1.5;Re=,取ε=0.2mm,即ε/d i =0.2/14=0.015 查表,得到λ=0.044=5066.6Pa △p 2=3/2=3X880X0.72/2=58.8PaΣΔp i =5066.6×3×1.5+58.8=22849.7Pa <30Kpa,满足条件壳程压降:ΣΔp o =Δp 1’+Δp 2’F s N s ,由于管子排列方式对压强降的校正因子:F=0.5正三角形排列d e ==0.0136mu o =)1(td hD V o s -=)(o c sd n D h V -==0.401m/sRe==7456.5, f o =5×Re -0.228=0.13Δp 1’=Ff o N c N B +122uo ρ=0.5×0.128×21X15+1×994×0.4012/2=1718.5PaΔp 2’=N B 3.5-D h 222ou ρ=15×3.5-2×0.275/0.6×994×0.4012/2=3096.8PaΣΔp i =Δp 1+Δp 2F t N s =1718.5+3096.8×1.15=5537.6Pa <30Kpa 传热系数校正总传热系数由下式计算:计)(1o K =o α1+R so +m o d bd λ+i o si d d R +ii o d d α其中,管内苯的传热系数αi 的计算 αi =0.023iid λR ei 8.03.0Pr =0.023×=570.8W/ m 2.K管间水的传热系数αo 的计算 αo =0.3614.03/155.0Pr Re w d oeoΦλ由于水被加热,取粘度校正系数Φw 14.0=1.05αo =0.36×4147.5 m 2.K取水与苯的污垢热阻均为 1.7197Χ104- m 2.K/W,钢管导热系数λ=51 W/ m.K;故计)(1o K ==2.89×10-3 Ko 计=346 W/m 2.K所以,,一般Ko 计/ Ko 选应在1.15-1.25之间;本设计的换热器可适用7、设计过程的评价及自我体会;。
- 1、下载文档前请自行甄别文档内容的完整性,平台不提供额外的编辑、内容补充、找答案等附加服务。
- 2、"仅部分预览"的文档,不可在线预览部分如存在完整性等问题,可反馈申请退款(可完整预览的文档不适用该条件!)。
- 3、如文档侵犯您的权益,请联系客服反馈,我们会尽快为您处理(人工客服工作时间:9:00-18:30)。
列管式换热器设计方案第一节推荐的设计程序一、工艺设计1、作出流程简图。
2、按生产任务计算换热器的换热量Q。
3、选定载热体,求出载热体的流量。
4、确定冷、热流体的流动途径。
5、计算定性温度,确定流体的物性数据(密度、比热、导热系数等)。
6、初算平均传热温度差。
7、按经验或现场数据选取或估算K值,初算出所需传热面积。
8、根据初算的换热面积进行换热器的尺寸初步设计。
包括管径、管长、管子数、管程数、管子排列方式、壳体内径(需进行圆整)等。
9、核算K。
10、校核平均温度差 m T。
11、校核传热量,要求有15-25%的裕度。
12、管程和壳程压力降的计算。
二、机械设计1、壳体直径的决定和壳体壁厚的计算。
2、换热器封头选择。
3、换热器法兰选择。
4、管板尺寸确定。
5、管子拉脱力计算。
6、折流板的选择与计算。
7、温差应力的计算。
8、接管、接管法兰选择及开孔补强等。
9、绘制主要零部件图。
三、编制计算结果汇总表四、绘制换热器装配图五、提出技术要求 六、编写设计说明书第二节 列管式换热器的工艺设计一、换热终温的确定换热终温对换热器的传热效率和传热强度有很大的影响。
在逆流换热时,当流体出口终温与热流体入口初温接近时,热利用率高,但传热强度最小,需要的传热面积最大。
为合理确定介质温度和换热终温,可参考以下数据:1、热端温差(大温差)不小于20℃。
2、冷端温差(小温差)不小于5℃。
3、在冷却器或冷凝器中,冷却剂的初温应高于被冷却流体的凝固点;对于含有不凝气体的冷凝,冷却剂的终温要求低于被冷凝气体的露点以下5℃。
二、平均温差的计算设计时初算平均温差∆t m,均将换热过程先看做逆流过程计算。
1、对于逆流或并流换热过程,其平均温差可按式(2-1)进行计算:2121ln t t t t t m ∆∆∆-∆=∆ (2—1) 式中,1t ∆、2t ∆分别为大端温差与小端温差。
当221t t ∆∆时,可用算术平均值()221t t t m ∆+∆=∆。
2、对于错流或折流的换热过程,若无相变化,则要进行温差校正,即用公式(2-2)进行计算。
逆t t t m ∆⋅=∆∆ε (2-2) 式中逆t ∆是按逆流计算的平均温差,校正系数t ∆ε可根据换热器不同情况由化工原理教材有关插图查出。
一般要求t ∆ε>0.8,否则应改用多壳程或者将多台换热器串联使用。
三、传热总系数K的确定计算K值的基准面积,习惯上常用管子的外表面积o A 。
当设计对象的基准条件(设备型式、雷诺准数Re 、流体物性等)与某已知K值的生产设备相同或相近时,则可采用已知设备K值的经验数据作为自己设计的K值。
表2-1为常见列管式换热器K值的大致范围。
由表2-1选取大致K值,用式(2-3)进行K值核算。
K=1++++100000αδλαR d d R d d d d m i i i i (2-3) 式中:α-给热系数,W/m 2.℃; R -污垢热阻,m 2.℃/W ; δ-管壁厚度,mm ;λ-管壁导热系数,W/m.℃;下标i、o、m分别表示管内、管外和平均。
当2 i oA A 时近似按平壁计算,即: o m i A A A ≈≈在用式(2-3)计算K值时,污垢热阻o R 、i R 通常采用经验值,常用的污垢热阻大致范围可查《化工原理》相关内容。
式中的给热系数α,在列管式换热器设计中常采用有关的经验值公式计算给热系数α,工程上常用的一些计算α的经验关联式在《化工原理》已作了介绍,设计时从中选用。
四、传热面积A 的确定工程上常将列管式换热器中管束所有管子的外表面积之和视为传热面积,由式(2-4)和式(2-5)进行计算。
A Q0=Kt∆m (2-4) πL nd A o o = (2-5)式中:K - 基于外表面o A 的传热系数,W/m 2.℃ o d -管子外径,m;L -每根管子的有效长度,m;πL nd A o o =n-管子的总数管子的有效长度是指管子的实际长度减去管板、挡板所占据的部分。
管子总数是指圆整后的管子数减去拉杆数。
五、主要工艺尺寸的确定当确定了传热面积o A后,设计工作进入换热器尺寸初步设计阶段,包括以下内容:1、管子的选用。
选用较小直径的管子,可以提高流体的对流给热系数,并使单位体积设备中的传热面积增大,设备较紧凑,单位传热面积的金属耗量少,但制造麻烦,小管子易结垢,不易清洗,可用于较清洁流体。
大管径的管子用于粘性较大或易结垢的流体。
我国列管式换热器常采用无缝钢管,规格为外径×壁厚,常用的换热管的规格:φ19×2,φ25×2.5,φ38×3。
管子的选择要考虑清洗工作的方便及合理使用管材,同时还应考虑管长与管径的配合。
国内管材生产规格,长度一般为:1.5,2,2.5,3,4.5,5,6,7.5,9,12m等。
换热器的换热管长度与壳径之比一般在6-10,对于立式换热器,其比值以4-6为宜。
壳程和壳程压力降,流体在换热器内的压降大小主要决定于系统的运行压力,而系统的运行压力是靠输送设备提供的。
换热器内流体阻力损失(压力降)越大,要求输送设备的功率就越大,能耗就越高。
对于无相变的换热,流体流速越高,换热强度越大,可使换热面积减小,设备紧凑,制作费低,而且有利于抑制污垢的生成,但流速过高,也有不利的一面,压力降增大,泵功率增加,对传热管的冲蚀加剧。
因此,在换热器的设计中有个适宜流速的选取和合理压力降的控制问题。
一般经验,对于液体,在压力降控制在0.01~0.1MPa之间,对于气体,控制在0.001~0.01MPa之间。
表2-2列出了换热器不同操作条件压力下合理压降的经验数据,供设计参考。
2、管子总数n的确定。
对于已定的传热面积,当选定管径和管长后便可求所需管子数n,由式 (2-6)进行计算。
n A d L =0π (2-6) 式中o A -传热面积,m 2;o d -管子外径,m ;L -每根管子的有效长度,m ;计算所得的管子n 进行圆整 3、管程数m 的确定。
根据管子数n 可算出流体在管内的流速u ',由式(2-7)计算。
u'.=v d n si 07852(2-7) 式中 v s -管程流体体积流量,m s 3i d -管子内径, m ;n -管子数。
若流速u '与要求的适宜流速相比甚小时,便需采用多管程,管程数m可按式(2-8)进行计算。
m=u /u '(2-8)式中u '—用管子数n 求出的管内流速,m/s;u -要求的适宜流速,m/s;式(2-8)中的适宜流速u 要根据列管式换热器中常用的流速范围进行选定,参见《化工原理》相关内容,一般要求在湍流下工作(高粘度流体除外),与此相对应的Re 值,对液体为5×103,气体则为104-105。
分程时,应使每程的管子数大致相等,生产中常用的管程数为1、2、4、6、四种。
4、管子的排列方式及管间距的确定。
管子在管板上排列的原则是:管子在整个换热器的截面上均匀分布,排列紧凑,结构设计合理,方便制造并适合流体的特性。
其排列方式通常为等边三角形与正方形两种,也有采用同心圆排列法和组合排列法。
在一些多程的列管式换热器中,一般在程内为正三角形排列,但程与程之间常用正方形排列,这对于隔板的安装是很有利的,此时,整个管板上的排列称为组合排列。
对于多管程的换热器,分程的纵向隔板占据了管板上的一部分面积,实际排管数比理论要少,设计时实际的管数应通过管板布置图而得。
在排列管子时,应先决定好管间距。
决定管间距时应先考虑管板的强度和清理管子外表时所需的方法,其大小还与管子在管板上的固定方式有关。
大量的实践证明,最小管间距的经验值为: 焊接法od a 25.1=最小od a 25.1≥最小胀接法 o d a 25.1≥最小,一般取(1.3~1.5)o d管束最外层管子中心距壳体内表面距离不小于mmd ⎪⎭⎫ ⎝⎛+10210。
5、壳体的计算。
列管式换热器壳体的内径应等于或稍大于(对于浮头式换热器)管板的直径,可由式(2-9)进行计算。
D i =a (b -1)+2L (2-9) 式中D i -壳体内径,mm ;a -管间距,mm ;b -最外层六边形对角线上的管子数;L -最外层管子中心到壳体内壁的距离,一般取L=(1~1.5)o d ,mm ;若对管子分程则D i =f +2Lf 值的确定方法:可查表求取,也可用作图法。
当已知管子数n 和管间距a 后开始按正三角形排列,直至排好n根为止,再统计对角线上的管数。
计算出的壳径D i 要圆整到容器的标准尺寸系列内。
第三节 列管式换热器机械设计在化工企业中列管式换热器的类型很多,如板式,套管式,蜗壳式,列管式。
其中列管式换热器虽在热效率、紧凑性、金属消耗量等方面均不如板式换热器,但它却具有结构坚固、可靠程度高、适应性强、材料范围广等特点,因此成为石油、化工生产中,尤其是高温、高压和大型换热器的主要结构形式。
列管式换热器主要有固定管板式换热器、浮头式换热器、填函式换热器和U 型管式换热器,而其中固定管板式换热器由于结构简单,造价低,因此应用最普遍。
列管式换热器机械设计包括:1、壳体直径的决定和壳体壁厚的计算。
2、换热器封头选择。
3、压力容器法兰选择。
4、管板尺寸确定。
5、管子拉脱力的计算。
6、折流板的选择与计算。
7、温差应力的计算。
8、接管、接管法兰选择及开孔补强等。
9绘制主要零部件图和装配图。
下面分述如下:一、壳体直径的决定和壳体壁厚的计算。
1、已知条件:由工艺设计知管程和壳程介质种类、温度、压力、壳与壁温差、以及换热面积。
2、计算(1)管子数n:列管式换热器常用无缝钢管,规格如下:管子材质的选择依据是介质种类,如果介质无腐蚀,可选碳钢,而介质有腐蚀则选择不绣钢。
管长规格有1500,2000,2500,3000,4500,5000,6000,7500,9000,12000mm。
n=A/(πd m L),其中A—换热面积(m2);L—换热管长度mm;d m—管子的平均直径mm。
由于在列管式换热器中要安装4根或6根拉杆。
所以实际换热管子数为{n-4(6)}根。
(2)管子排列方式,管间距确定。
管子排列方式一般在程内采用正三角形排列,而在程与程之间采用正方形排列。
管间距根据最小管间距选择。
(3)换热器壳体直径的确定壳体直径计算公式:当采用正三角形排列时为D i=a(b-1)+2L式中D i—换热器内径;a—管间距;b—正三角形对角线上的管子数;L—最外层管子的中心到壳壁边缘的距离。
若对管子进行分程则D i=f+2L式中f—壳体同一内直径两端管子中心距mm;D i、L同上。
计算出D i后还要圆整到公称直径系列中。
(4)换热器壳体壁厚的计算计算壁厚为S=PD i/(2[σ]tΦ-P)式中P—设计压力,MPa;当P﹤0.6 MPa时,取P=0.6 MPa;D i—壳体内径,mm;Φ—焊缝系数,根据焊缝情况选取Φ=0.85-1.0;[σ]t—壳体材质在设计温度时的许用应力,MPa。