列管式换热器设计
列管式换热器的设计与计算
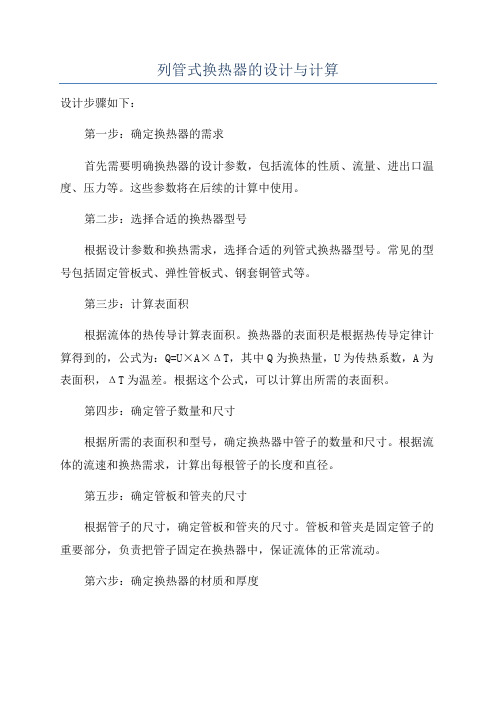
列管式换热器的设计与计算设计步骤如下:第一步:确定换热器的需求首先需要明确换热器的设计参数,包括流体的性质、流量、进出口温度、压力等。
这些参数将在后续的计算中使用。
第二步:选择合适的换热器型号根据设计参数和换热需求,选择合适的列管式换热器型号。
常见的型号包括固定管板式、弹性管板式、钢套铜管式等。
第三步:计算表面积根据流体的热传导计算表面积。
换热器的表面积是根据热传导定律计算得到的,公式为:Q=U×A×ΔT,其中Q为换热量,U为传热系数,A为表面积,ΔT为温差。
根据这个公式,可以计算出所需的表面积。
第四步:确定管子数量和尺寸根据所需的表面积和型号,确定换热器中管子的数量和尺寸。
根据流体的流速和换热需求,计算出每根管子的长度和直径。
第五步:确定管板和管夹的尺寸根据管子的尺寸,确定管板和管夹的尺寸。
管板和管夹是固定管子的重要部分,负责把管子固定在换热器中,保证流体的正常流动。
第六步:确定换热器的材质和厚度根据流体的性质和工作条件,确定换热器的材质和厚度。
常见的材质有不锈钢、碳钢、铜等。
通过计算流体的温度、压力和腐蚀性等参数,选择合适的材质和厚度。
第七步:校核换热器的强度对换热器的强度进行校核。
根据国家相关标准和规范,对换热器的强度进行计算和验证,确保其能够承受工作条件下的压力和温度。
第八步:制定施工方案和图纸根据设计结果,制定换热器的施工方案和详细图纸。
包括换热器的总体布置,管子的连接方式,焊接和安装步骤等。
上述是列管式换热器的设计步骤,下面将介绍列管式换热器的计算方法。
首先,需要计算流体的传热系数。
传热系数的计算包括对流传热系数和管内传热系数两部分。
对于对流传热系数,可以使用已有的经验公式或经验图表进行估算。
对于管内传热系数,可以使用流体的性质和流速等参数进行计算。
其次,根据传热系数和管子的尺寸,计算管子的传热面积。
管子的传热面积可以根据管子的长度和直径进行计算。
然后,根据热传导定律,计算换热器的传热量。
化工原理课程设计 列管式换热器
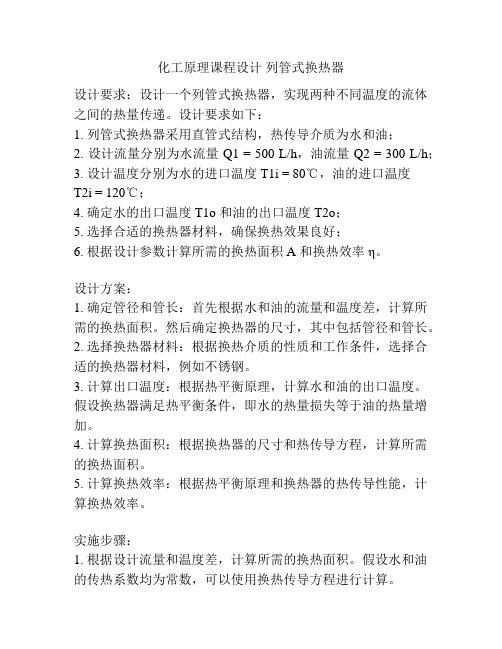
化工原理课程设计列管式换热器设计要求:设计一个列管式换热器,实现两种不同温度的流体之间的热量传递。
设计要求如下:1. 列管式换热器采用直管式结构,热传导介质为水和油;2. 设计流量分别为水流量 Q1 = 500 L/h,油流量 Q2 = 300 L/h;3. 设计温度分别为水的进口温度 T1i = 80℃,油的进口温度T2i = 120℃;4. 确定水的出口温度 T1o 和油的出口温度 T2o;5. 选择合适的换热器材料,确保换热效果良好;6. 根据设计参数计算所需的换热面积 A 和换热效率η。
设计方案:1. 确定管径和管长:首先根据水和油的流量和温度差,计算所需的换热面积。
然后确定换热器的尺寸,其中包括管径和管长。
2. 选择换热器材料:根据换热介质的性质和工作条件,选择合适的换热器材料,例如不锈钢。
3. 计算出口温度:根据热平衡原理,计算水和油的出口温度。
假设换热器满足热平衡条件,即水的热量损失等于油的热量增加。
4. 计算换热面积:根据换热器的尺寸和热传导方程,计算所需的换热面积。
5. 计算换热效率:根据热平衡原理和换热器的热传导性能,计算换热效率。
实施步骤:1. 根据设计流量和温度差,计算所需的换热面积。
假设水和油的传热系数均为常数,可以使用换热传导方程进行计算。
2. 根据所需的换热面积和理论计算值,选择合适的换热器尺寸。
3. 根据所选换热器材料,计算换热器的尺寸和管径。
假设管壁温度近似等于流体温度。
4. 根据热平衡原理,计算出口温度。
假设热平衡条件满足,即水的热量损失等于油的热量增加。
5. 根据所选材料和尺寸,计算换热效率。
假设换热器的热传导系数为常数,使用换热效率计算公式进行计算。
总结:本课程设计主要针对列管式换热器的设计,通过选择合适的换热器材料和计算换热器的尺寸,实现了水和油之间的热量传递。
根据设计要求,通过计算出口温度和换热效率,验证了设计方案的合理性。
设计过程需要考虑多方面的因素,如流体性质、流量和温度差等。
列管式换热器设计

列管式换热器设计列管式换热器是一种常见的换热设备,广泛应用于化工、石油、制药等行业中。
本文将从列管式换热器的设计原理、设计步骤和设计考虑因素三个方面进行详细介绍。
一、设计原理列管式换热器是通过管内的换热流体和管外的换热流体之间的换热传递来实现热量的传递。
它的基本原理是利用换热流体在管内和管外的对流,通过管壁的传导传热作用,使热量从高温流体传递给低温流体。
二、设计步骤1.确定换热器的使用条件:包括换热流体的性质、入口温度、出口温度等。
2.确定换热器的换热面积:根据换热流体的热负荷和传热系数来计算所需的换热面积。
3.选择管子的尺寸和材料:根据换热流体的性质和流量来选择合适的管子尺寸和材料。
4.确定管子的数量和布置方式:根据换热面积和换热流体的流量来确定管子的数量和布置方式,一般采用多行多列的方式。
5.设计管束的尺寸:根据换热面积和管子的数量来确定管束的尺寸,包括管束的直径、长度和布置方式等。
6.计算换热器的传热系数:根据换热面积、流体的性质和传热方式来计算换热器的传热系数。
7.计算换热器的压降:根据流体的流量、管束的阻力和流体的性质来计算换热器的压降。
8.进行换热器的热力学计算:包括换热器的热力学效率、有效传热面积和温差效益等。
三、设计考虑因素1.热负荷:根据换热流体的热负荷来确定换热器的换热面积和管子的数量。
2.材料选择:根据换热流体的性质和工艺要求来选择合适的材料,包括管子的材料和管壳的材料。
3.温度差:根据换热流体的温度差来确定管束的数量和换热器的传热系数。
4.流体压降:根据流体的流量和管束的阻力来计算换热器的压降,并确定合适的管束布置方式和管束的尺寸。
5.清洗和维护:考虑到换热器的清洗和维护,要选择易于清洗和维护的结构设计。
综上所述,列管式换热器的设计是一个复杂的工程,需要考虑多个因素。
设计者需要根据具体的使用条件和要求来确定换热器的换热面积、管子的尺寸和材料、管束的数量和布置方式等。
同时,还需要计算换热器的传热系数、压降和热力学参数等。
化工原理课程设计---列管式换热器的设计
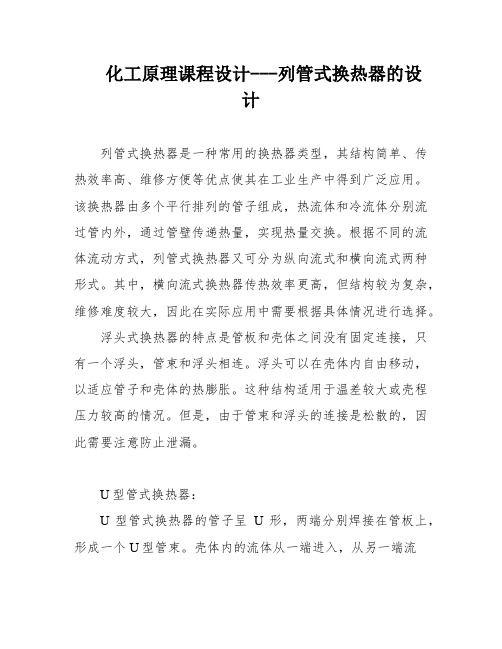
化工原理课程设计---列管式换热器的设计列管式换热器是一种常用的换热器类型,其结构简单、传热效率高、维修方便等优点使其在工业生产中得到广泛应用。
该换热器由多个平行排列的管子组成,热流体和冷流体分别流过管内外,通过管壁传递热量,实现热量交换。
根据不同的流体流动方式,列管式换热器又可分为纵向流式和横向流式两种形式。
其中,横向流式换热器传热效率更高,但结构较为复杂,维修难度较大,因此在实际应用中需要根据具体情况进行选择。
浮头式换热器的特点是管板和壳体之间没有固定连接,只有一个浮头,管束和浮头相连。
浮头可以在壳体内自由移动,以适应管子和壳体的热膨胀。
这种结构适用于温差较大或壳程压力较高的情况。
但是,由于管束和浮头的连接是松散的,因此需要注意防止泄漏。
U型管式换热器:U型管式换热器的管子呈U形,两端分别焊接在管板上,形成一个U型管束。
壳体内的流体从一端进入,从另一端流出,管内的流体也是如此。
这种结构适用于流体腐蚀性较强的情况,因为管子可以很容易地更换。
多管程换热器:多管程换热器是将管束分成多个组,每组管子单独连接到管板上,形成多个管程。
这种结构可以提高传热效率,但也会增加流体阻力。
因此,需要根据具体情况来选择多管程的数量。
总之,列管式换热器是一种广泛应用于化工及酒精生产的换热器。
不同的结构适用于不同的工艺条件,需要根据具体情况来选择合适的换热器。
在使用过程中,需要注意保养和维护,及时清洗和更换损坏的部件,以保证换热器的正常运行。
换热器的一块管板与外壳用法兰连接,另一块管板不与外壳连接,这种结构称为浮头式换热器。
浮头式换热器的优点是管束可以拉出以便清洗,管束的膨胀不受壳体约束,因此在两种介质温差大的情况下,不会因管束与壳体的热膨胀量不同而产生温差应力。
但其缺点是结构复杂,造价高。
填料式换热器的管束一端可以自由膨胀,结构比浮头式简单,造价也较低。
但壳程内介质有外漏的可能,因此不应处理易挥发、易燃、易爆和有毒的介质。
列管式换热器的设计
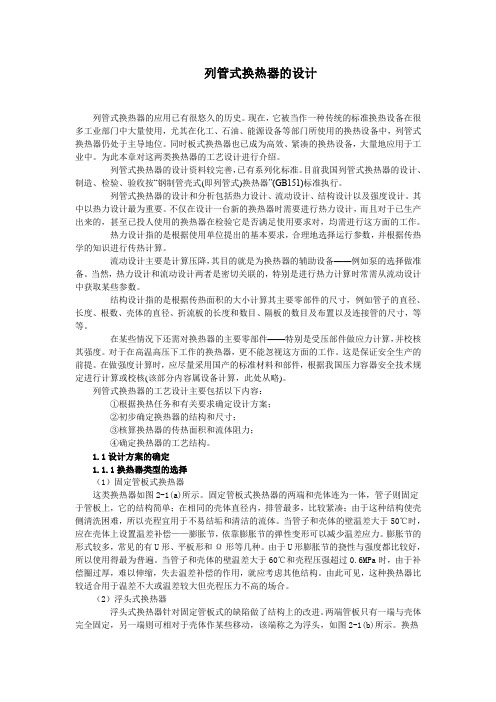
列管式换热器的设计列管式换热器的应用已有很悠久的历史。
现在,它被当作一种传统的标准换热设备在很多工业部门中大量使用,尤其在化工、石油、能源设备等部门所使用的换热设备中,列管式换热器仍处于主导地位。
同时板式换热器也已成为高效、紧凑的换热设备,大量地应用于工业中。
为此本章对这两类换热器的工艺设计进行介绍。
列管式换热器的设计资料较完善,已有系列化标准。
目前我国列管式换热器的设计、制造、检验、验收按“钢制管壳式(即列管式)换热器”(GB151)标准执行。
列管式换热器的设计和分析包括热力设计、流动设计、结构设计以及强度设计。
其中以热力设计最为重要。
不仅在设计一台新的换热器时需要进行热力设计,而且对于已生产出来的,甚至已投人使用的换热器在检验它是否满足使用要求对,均需进行这方面的工作。
热力设计指的是根据使用单位提出的基本要求,合理地选择运行参数,并根据传热学的知识进行传热计算。
流动设计主要是计算压降,其目的就是为换热器的辅助设备——例如泵的选择做准备。
当然,热力设计和流动设计两者是密切关联的,特别是进行热力计算时常需从流动设计中获取某些参数。
结构设计指的是根据传热面积的大小计算其主要零部件的尺寸,例如管子的直径、长度、根数、壳体的直径、折流板的长度和数目、隔板的数目及布置以及连接管的尺寸,等等。
在某些情况下还需对换热器的主要零部件——特别是受压部件做应力计算,并校核其强度。
对于在高温高压下工作的换热器,更不能忽视这方面的工作。
这是保证安全生产的前提。
在做强度计算时,应尽量采用国产的标准材料和部件,根据我国压力容器安全技术规定进行计算或校核(该部分内容属设备计算,此处从略)。
列管式换热器的工艺设计主要包括以下内容:①根据换热任务和有关要求确定设计方案;②初步确定换热器的结构和尺寸;③核算换热器的传热面积和流体阻力;④确定换热器的工艺结构。
1.1设计方案的确定1.1.1换热器类型的选择(1)固定管板式换热器这类换热器如图2-1(a)所示。
列管式换热器结构设计

到焊接的可能性; (b)纵向隔板插入导向槽中; (c)、(d)分别是单双向条形密封,防止间隙短
路,对于需要将管束经常抽出清洗者,采用此结构。
管板与隔板的连接形式 如图 (a)为隔板与管板焊接, (b)是隔板用螺栓联接在焊于管板的角铁上的可
拆结构.
3、分割流板
在壳体上有对称的两个进口及一个出口时,如图中 J型壳体
三、管箱
一、传热管与管板的连接
造成连接处破坏的原因主要有: (1)高温下应力松弛而失效 (2)间隙腐蚀破坏 (3)疲劳破坏 (4)由于热补偿不好引起的破坏
管子与管板的连接形式:强度胀接、强度焊接与 胀焊接混合结构。
应满足以下两个条件: 连接处保证介质无泄漏的充分气密性;承受
介质压力的充分结合力。
②多程管箱,最小流通面积应大于或等于其中一程的管 内流通面积的1/3倍。 ③管箱上各相邻焊缝间距必须大于或等于4s,且应大于 或等于50mm,其中s为管箱壁。
(2)管箱最小长度计算
管箱最小长度计算涉及几何尺寸见图。
A型管箱见图4-35(a),
按流通面积计算
L' g m in
πd
2 i
N
cp
4E
(mm )
(3) Ώ形膨胀节
(4)夹壳膨胀节
2.膨胀节设置必要性判断 通过计算由温差产生轴向力和压力产生轴向力共同作 用,得到: 换热管最大应力、 壳体最大应力及管子拉脱力 当σs>2φ[σ]ts或σt>2[σ]tt时应设置膨胀节 。
3、强度计算 包括: (1)温差引起的轴向力计算 (2)补偿量的计算 (3)膨胀节疲劳寿命计算
列管式换热器的设计(化工原理课程设计)
列管式换热器的设计(化⼯原理课程设计)⽬录§⼀.任务书 (2)1.1.化⼯原理课程设计的重要性1.2.课程设计的基本内容和程序1.3.列管式换热器设计内容1.4.设计任务和操作条件1.5.主要设备结构图1.6.设计进度1.7.设计成绩评分体系§⼆.概述及设计要求 (4)2.1.换热器概述2.2.固定管板式换热器2.3.设计要求§三.设计条件及主要物理参数 (5)3.1.初选换热器的类型3.2.确定物性参数3.3.计算热流量及平均温差3.4.管程安排(流动空间的选择)及流速确定3.5.计算总传热系数3.6.计算传热⾯积§四. ⼯艺设计计算 (9)4.1.管径和管内流速4.2.管程数和传热管数4.3.平均传热温差校正及壳程数4.4.换热管选型汇总4.5.换热管4.6.壳体内径4.7.折流板4.8.接管4.9.壁厚的确定、封头4.10.管板§五.换热器核算 (14)5.1.热量核算5.2.壁温核算5.3.流动阻⼒核算§六. 设计结果汇总 (18)§七. 设计评述 (19)§⼋. ⼯艺流程图 (19)§.九.符号说明 (21)§.⼗.参考资料 (22)§⼀.化⼯原理课程设计任务书1.1.化⼯原理课程设计的重要性化⼯原理课程设计是学⽣学完基础课程以及化⼯原理课程以后,进⼀步学习⼯程设计的基础知识,培养学⽣⼯程设计能⼒的重要教学环节,也是学⽣综合运⽤化⼯原理和相关选修课程的知识,联系⽣产实际,完成以单元操作为主的⼀次⼯程设计的实践。
通过这⼀环节,使学⽣掌握单元操作设计的基本程序和⽅法,熟悉查阅技术资料、国家技术标准,正确选⽤公式和数据,运⽤简洁⽂字和⼯程语⾔正确表述设计思想和结果;并在此过程中使学⽣养成尊重实际问题向实践学习,实事求是的科学态度,逐步树⽴正确的设计思想、经济观点和严谨、认真的⼯作作风,提⾼学⽣综合运⽤所学的知识,独⽴解决实际问题的能⼒。
化工原理课程设计列管式换热器
化工原理课程设计列管式换热器化工原理课程设计是化学工程学科的重要环节,其设计的目的是让学生在理论基础知识的基础上,能够熟练掌握工业化学反应装置和过程的设计方法,并能灵活运用各种装置和工艺条件来实现设备的最优化。
其中列管式换热器是常用于化工生产过程中的一种重要装置,本文将对其进行详细介绍。
一、列管式换热器的结构与原理列管式换热器是通过管壳型构造,由许多纵向的管子构成,管子两侧通过流体工质进行换热。
其主要结构包括壳体、管板、管束、进出口法兰等部分。
换热原理是将热量从高温的流体传给低温的流体,实现两种流体之间的热量交换。
二、列管式换热器的特点和应用列管式换热器具有结构简单、换热效率高、应用范围广、容易清洗维修等特点。
其在化工生产中广泛应用于热回收、冷却、加热等方面,如在石油、化工、冶金、食品、制药、造纸等行业的反应过程中都有重要的应用。
三、列管式换热器的设计方法在设计列管式换热器时,主要需考虑的参数有流体介质、流量、温度、压力等等,其中最核心的是确定热量传递系数与压降。
常用的设计方法有总热传系数法、等效径法、NTU法等。
其中总热传系数法是最常用的方法,其计算的公式为:1/U = 1/hi + Δx/k + Δy/ho其中U为总热传系数,hi、ho分别为热传分界面内的内、外热传系数,k为扩散系数(介质传热系数),Δx、Δy为介质的平均厚度与壁层厚度。
在设计时应根据具体情况选用合适的计算方法。
四、列管式换热器的操作和维护在使用列管式换热器时,应注意清洗维护工作。
由于该装置的结构特殊,应定期进行化学清洗,以避免沉积物和腐蚀物堵塞换热器内壁。
同时还应注意防止介质的过于浓缩,以免产生结晶、沉积、腐蚀等情况。
综上所述,列管式换热器是化工生产中不可缺少的一种装置,其结构特殊、应用范围广泛、换热效率高,并且容易维护操作,是值得研究和推广的一种装置。
在化工原理的课程设计中,学生能够通过对列管式换热器的深入理解和设计方案的完善,培养出创新思维和实际操作能力,为将来化工行业的发展奠定坚实的基础。
列管式换热器的设计与计算
列管式换热器的设计与计算一、需求分析在进行列管式换热器设计与计算之前,首先要明确用户需求。
包括换热介质的种类、流量、进出口温度、压力等参数。
通过对用户需求的分析,可以确定换热器的基本工况。
二、换热面积计算换热面积是列管式换热器设计的重要参数之一、常用的换热面积计算方法有经验公式法、传热负荷法和数值计算法。
其中最常用的方法是经验公式法。
经验公式法是通过已有的实验数据和经验公式来计算换热面积。
常用的经验公式有Dittus-Boelter公式、Sieder-Tate公式和Petukhov公式等。
选择适当的公式并对其进行解析,可以计算出换热器的换热面积。
三、流体参数计算在进行列管式换热器设计与计算之前,需要准确地确定流体的物性参数。
包括流体的热传导系数、粘度、比热容等。
这些参数的计算可以通过查表或者使用流体模拟软件来实现。
四、管道布置管道布置是列管式换热器设计的重要环节。
合理的管道布置可以提高换热效率,减小流体的压降。
通常情况下,采用等分流或者逆流布置方式。
在进行管道布置时,需要考虑管道的长度、中心距、管程数等因素。
五、管壳选型根据用户需求和换热介质的特点,选择合适的管壳材质和型号。
常见的管壳材质有碳钢、不锈钢、铜合金等。
在选择管壳型号时,要考虑流体进出口大小、壳体结构和安装方式等因素。
六、压降计算在进行列管式换热器设计与计算时,需要考虑流体在管内和管外的压降。
通过压降计算可以确定管道的尺寸、长度和流速等参数。
压降计算一般有几种方法,包括经验公式法、流体力学模拟法和试验法等。
七、材料选用在列管式换热器的设计与计算中,材料的选用非常重要。
常见的材料有碳钢、不锈钢、铜合金等。
选择合适的材料,可以确保换热器的使用寿命和性能。
八、换热器结构设计换热器的结构设计包括换热管的排列方式、管道的长度和直径等。
这些参数的选择与具体的应用场景和换热介质有关。
换热器的结构设计要满足换热效率高、压降小和结构紧凑等要求。
总结:列管式换热器的设计与计算涉及多个方面,包括换热面积计算、流体参数计算、管道布置、管壳选型、压降计算、材料选用和换热器结构设计等。
列管式换热器(设计举例)
三、平均传热温差
平均传热温差是换热器的传热推动力。其值不但和流体的进出口温度有关,而且还与换 热器内两种流体的流型有关。对于列管式换热器,常见的流型有三种:并流,逆流,和折流
对于并流和逆流,平均传热温差均可用换热器两端流体温度的对数平均温差表示, 即:
《列管式换热器》
t m t1 t 2 t ln 1 t 2
R
热流体的温降 T1 T2 冷流体的温升 t 2 t1 t t 冷流体的温升 1 2 两流体最初温差 T1 T2
(1—13 a )
P
式中
(1—13 b )
T1、T2 — 热流体进、出口温度, ℃; t1、t 2 — 冷流体进、出口温度, ℃.
《列管式换热器》
第- 称为管心距。管心距的大小主要与传热管和管板的连接方式有 关,此外还要考虑到管板强度和清洗管外表面时所需的空间。 传热管和管板的连接方法有胀接和焊接两种,当采用胀接法时,采用过小的管心距,常 会造成管板变形,而采用焊接法时,管心距过小,也很难保证焊接质量,因此管心距应有一 定的数值范围。一般情况下,胀接时,取管心距 t 1.3~1.5d 0 ;焊接时,取 t 1.25d 0 ( d 0
共 37页
一般要求 t 的值不得低于 0.8,若低于此值,当换热器的操作条件略有变化时, t 的 变化较大,使得操作极不稳定。 t 小于 0.8 的原因在于多管程换热器内出现温度交差或温 度逼近。在这种情况下,应考虑采用多壳程结构的换热器或多台换热器串联来解决。所需的 壳程数或串联的换热器的台数可按下述方法确定: 首先,在坐标纸上作 Q ~ T 和 Q ~ t 线,由热衡算方程知,若两流体的热容量流率不变则
《列管式换热器》
第- 1 -页
- 1、下载文档前请自行甄别文档内容的完整性,平台不提供额外的编辑、内容补充、找答案等附加服务。
- 2、"仅部分预览"的文档,不可在线预览部分如存在完整性等问题,可反馈申请退款(可完整预览的文档不适用该条件!)。
- 3、如文档侵犯您的权益,请联系客服反馈,我们会尽快为您处理(人工客服工作时间:9:00-18:30)。
酒泉职业技术学院毕业设计(论文)2013 级石油化工生产技术专业题目:列管式换热器设计毕业时间: 2015年7月学生姓名:陈泽功刘升衡李侠虎指导教师:王钰班级: 13级石化(3)班2015 年 4月20日酒泉职业技术学院 2013 届各专业毕业论文(设计)成绩评定表答辩小组评价意见及评分成绩:签字(盖章)年月日教学系毕业实践环节指导小组意见签字(盖章)年月日学院毕业实践环节指导委员会审核意见签字(盖章)年月日一、列管式换热器计任务书某生产过程中,需用循环冷却水将有机料液从102℃冷却至40℃。
已知有机料液的流量为2.23×104 kg/h,循环冷却水入口温度为30℃,出口温度为40℃,并要求管程压降与壳程压降均不大于60kPa,试设计一台列管换热器,完成该生产任务。
已知:有机料液在71℃下的有关物性数据如下(来自生产中的实测值)密度定压比热容℃热导率℃粘度循环水在35℃下的物性数据:密度定压比热容K热导率K粘度二、确定设计方案(1)选择换热器的类型(2)两流体温的变化情况:热流体进口温度102℃出口温度40℃;冷流体进口温度30℃,出口温度为40℃,该换热器用循环冷却水冷却,冬季操作时,其进口温度会降低,考虑到这一因素,估计该换热器的管壁温度和壳体温度之差较大,因此初步确定选用浮头式换热器。
(3)管程安排从两物流的操作压力看,应使有机料液走管程,循环冷却水走壳程。
但由于循环冷却水较易结垢,若其流速太低,将会加快污垢增长速度,使换热器的热流量下降,所以从总体考虑,应使循环水走管程,混和气体走壳程。
三、确定物性数据定性温度:对于一般气体和水等低黏度流体,其定性温度可取流体进出口温度的平均值。
故壳程混和气体的定性温度为T= =71℃管程流体的定性温度为t=℃根据定性温度,分别查取壳程和管程流体的有关物性数据。
对有机料液来说,最可靠的无形数据是实测值。
若不具备此条件,则应分别查取混合无辜组分的有关物性数据,然后按照相应的加和方法求出混和气体的物性数据。
有机料液在71℃下的有关物性数据如下(来自生产中的实测值)密度定压比热容℃热导率℃粘度循环水在35℃下的物性数据:密度定压比热容K热导率K粘度四、估算传热面积(一)热流量Q1==22300×4.19×(102-40)=5.79×106kj/h =1609.193kw(二)平均传热温差先按照纯逆流计算,得=(三)传热面积由于壳程气体的压力较高,故可选取较大的K值。
假设K=640W/(㎡k)则估算的传热面积为Ap=(四)冷却水用量m==五、工艺结构尺寸(一)管径和管内流速选用Φ25×2.5较高级冷拔传热管(碳钢),取管内流速u1=1.1m/s。
(二)管程数和传热管数可依据传热管内径和流速确定单程传热管数Ns=按单程管计算,所需的传热管长度为L=按单程管设计,传热管过长,宜采用多管程结构。
根据本设计实际情况,采用非标设计,现取传热管长l=6m,则该换热器的管程数为Np=传热管总根数 Nt=111×2=222(三)传热温差校平均正及壳程数平均温差校正系数:R=P=按单壳程,双管程结构,平均传热温差K由于平均传热温差校正系数大于0.8,同时壳程流体流量较大,故取单壳程合适。
(四)传热管排列和分程方法采用组合排列法,即每程内均按正三角形排列,隔板两侧采用正方形排列。
取管心距t=1.25d0,则 t=1.25×25=31.25≈32㎜隔板中心到离其最.近一排管中心距离:S=t/2+6=32/2+6=22㎜各程相邻管的管心距为44㎜。
管数的分程方法,每程各有传热管222根,其前后管程中隔板设置和介质的流通顺序按(五)壳体内径采用多管程结构,进行壳体内径估算。
取管板利用率η=0.75 ,则壳体内径为:D=1.05t按卷制壳体的进级档,可取D=600mm筒体直径校核计算:壳体的内径应等于或大于(在浮头式换热器中)管板的直径,所以管板直径的计算可以决定壳体的内径,其表达式为:(六)管子按正三角形排列:取e=1.2=1.225=30mm=32 (17-1)+2 30 =572mm 按壳体直径标准系列尺寸进行圆整:=600mm折流挡板采用圆缺形折流挡板,去折流板圆缺高度为壳体内径的25%,则切去的圆缺高度为h=0.25×600=150m,故可取h=150mm 取折流板间距B=0.3D,则 B=0.3×600=180mm,可取B为200mm。
折流板数目折流板圆缺面水平装配。
(七)其他附件拉杆数量与直径选取,本换热器壳体内径为600mm,故其拉杆直径为Ф16拉杆数量8,其中长度5950mm的六根,5500mm的两根。
壳程入口处,应设置防冲挡板。
(八)接管壳程流体进出口接管:取接管内液体流速为u1=10m/s,则接管内径为圆整后可取管内径为30mm。
管程流体进出口接管:取接管内液体流速u2=2.5m/s,则接管内径为圆整后去管内径为140mm六、换热器核算(一)热流量核算1.壳程表面传热系数用克恩法计算,见式【化学工业出版社《化工原理》(第三版)上册】:式(5-72a):当量直径,依式(5-73a)得=壳程流通截面积:壳程流体流速及其雷诺数分别为普朗特数粘度校正2.管内表面传热系数:管程流体流通截面积:管程流体流速:雷诺数:普朗特数:3.污垢热阻和管壁热阻:管外侧污垢热阻管内侧污垢热阻4.传热系数有:碳钢在该条件下的热导率为50w/(m·K)。
所以5.传热面积裕度:计算传热面积Ac:该换热器的实际传热面积为:该换热器的面积裕度为传热面积裕度合适,该换热器能够完成生产任务。
(二)壁温计算因为管壁很薄,而且壁热阻很小,故管壁温度可按式计算。
由于该换热器用循环水冷却,传热管内侧污垢热阻较大,会使传热管壁温升高,降低了壳体和传热管壁温之差。
但在操作初期,污垢热阻较小,壳体和传热管间壁温差可能较大。
计算中,应该按最不利的操作条件考虑,因此,取两侧污垢热阻为零计算传热管壁温。
于是有:式中液体的平均温度和气体的平均温度分别计算为0.4×40+0.6×15=34℃(102+40)/2=71℃4946w/㎡·K1076.5w/㎡·K传热管平均壁温℃壳体壁温,可近似取为壳程流体的平均温度,即T=71℃。
壳体壁温和传热管壁温之差为℃。
该温差较大,故需要设温度补偿装置。
由于换热器壳程压力较大,因此,需选用浮头式换热器较为适宜。
(三)换热器内流体的流动阻力1.管程流体阻力, ,由Re=28528,传热管对粗糙度0.01,查莫狄图:【化学工业出版社《化工原理》(第三版)上册】:图1-27得,流速=1.1m/s,, 所以:管程流体阻力在允许范围之内。
2.壳程阻力:按式计算, , .15流体流经管束的阻力F=0.50.5×0.63×16.4×(29+1)×=4400.9Pa流体流过折流板缺口的阻力, B=0.3m , D=0.6mPa总阻力4400.9+2058.8=6460Pa由于该换热器壳程流体的操作压力较高,所以壳程流体的阻力也比较适宜。
3.换热器主要结构尺寸和计算结果见下表:参数管程壳程流率138260 22300进/出口温度/℃30/40 102/40压力/MPa 0.4 6.9定性温度/℃35 71密度/(kg/m3)994 986 定压比热容/[kj/(kg•K)] 4.174 4.19 粘度/(Pa•s)0.728×0.54×热导率(W/m•K)0.626 0.662 普朗特数 4.85 3.416设备结构参数形式固定管板式壳程数 1壳体内径/㎜600 台数 1管径/㎜Φ25×2.5 管心距/㎜32管长/㎜8000 管子排列正三角形排列管数目/根222 折流板数/个29传热面积/㎡88.225 折流板间距/㎜200管程数 2 材质碳钢主要计算结果管程壳程流速/(m/s) 1.1 0.24 表面传热系数/[W/(㎡•K)] 4946 1076.5 污垢热阻/(㎡•K/W) 3.4394× 1.7197阻力/ MPa 0.035 0.0065热流量/KW 1609.193传热温差/K 28.5传热系数/[W/(㎡•K)] 600裕度/% 34%七、结构设计(一)固定管板及钩圈法兰结构设计:由于换热器的内径已确定,采用标准内径决、定固定管板外径及各结构尺寸。
结构尺寸为:固定管板外径:固定管板外径与壳体内径间隙:取(见《化工单元过程及设备课程设计》(化学工业出版社出版):表4-16);垫片宽度:取固定管板密封面宽度:固定法兰和钩圈的内直径:固定法兰和钩圈的外直径:外头盖内径:螺栓中心圆直径:(二)管箱法兰和管箱侧壳体法兰设计:依工艺条件:管侧压力和壳侧压力中的高值,以及设计温度和公称直径800,按JB4703-92长颈对焊法标准选取。
并确定各结构尺寸,见《化工单元过程及设备课程设计》(化学工业出版社出版):图4-50(a)所示。
(三)管箱结构设计:选用B型封头管箱,因换热器直径较大,且为二管程,其管箱最小长度可不按流道面积计算,只考虑相邻焊缝间距离计算:取管箱长为1300mm,管道分程隔板厚度取14mm,管箱结构如《化工单元过程及设备课程设计》(化学工业出版社出版):图4-50(a)所示。
(四)固定端管板结构设计:依据选定的管箱法兰,管箱侧法兰的结构尺寸,确定固定端管板最大外径为:D=1506mm;结构如《化工单元过程及设备课程设计》(化学工业出版社出版):图4-50(b)所示。
(五)外头盖法兰、外头盖侧法兰设计:依工艺条件,壳侧压力、温度及公称直径;按JB4703-93长颈法兰标准选取并确定尺寸。
(六)外头盖结构设计:外头盖结构如《化工单元过程及设备课程设计》(化学工业出版社出版):图4-51所示。
轴向尺寸由浮动管板、钩圈法兰及钩圈强度计算确定厚度后决定,见《化工单元过程及设备课程设计》(化学工业出版社出版):图4-51。
(七)垫片选择:a.管箱垫片:根据管程操作条件选石棉橡胶垫。
结构尺寸如《化工单元过程及设备课程设计》(化学工业出版社出版):图4-39(b)所示:b.外头盖垫片:根据壳程操作条件选缠绕式垫片,垫片:(JB4705-92)缠绕式垫片。
c.固定垫片:根据管壳程压差,混合气体温度确定垫片为金属包石棉垫,以浮动管板结构确定垫片结构尺寸为1390mm;厚度为3mm;JB4706-92金属包垫片。
(八)鞍座选用及安装位置确定:鞍座选用JB/T4712-92鞍座BI1400-F/S;安装尺寸如《化工单元过程及设备课程设计》(化学工业出版社出版):图4-44所示其中:取:(九)折流板布置:折流板尺寸:外径:;厚度取8mm前端折流板距管板的距离至少为850mm;结构调整为900mm;见《化工单元过程及设备课程设计》(化学工业出版社出版):图4-50(c)后端折流板距固定管板的距离至少为950mm;实际折流板间距B=300mm,计算折流板数为49块。