ASME射线评片要点
ASME射线评片要点

各放置一个像质 计。
相似,在底 片上与受检 材料的黑度 公差要得到 满足。
其它
原则上每张底片都 应有像质计的影 像。
双壁单 影
胶片侧
每张底片上都应有像质计的影像
应放置
双壁双 影
在 射线源
每张底片上都应有像质计的影像
侧
一次曝
光 连续排 列的多
根据透 照方式 确定
至少在第一张、中间一张、最后一 张胶片处各放置一个像质计。
表3.5
透照方 式
规定的 放置位
置
像质计的放置原则 像质计放置数量
备注
至少在整圈环缝上
源侧无
整圈环缝 等间隔地放置4个像 法放置像质
质计。
计时,允许
中心 法周 向
长度> 120°的局 部环缝
至少放置3个像质 计,分别位于长度 的两端和中央; 有纵缝相接时在每 条纵缝的远端各放
置一个像质计。
加“F”标记放 置在胶片 侧,但应做 对比试验证 明所达到的 灵敏度,且 应在检测报
不适用
表面余高 或内凸起
Tw
.mm
高 度
mm
Tw
.mm
高 度
mm
Tw
.mm
高 度
mm
Tw
.mm
高度 mm
(对于坡口焊 ≤6.4 1.6 ≤6.4 1.6 ≤6.4 1.6 ≤6.4 1.6
缝,高度是从
其两侧表面所 6.4<
6.4<
6.4<
6.4<
测得的较小 者;对于角焊
Tw≤12.7
3.2
Tw≤12.7 3.2 Tw≤12.7 3.2
1/2″ (21+4mm) 8.2Do (171mm) 10.2Do
ASME射线评片要点
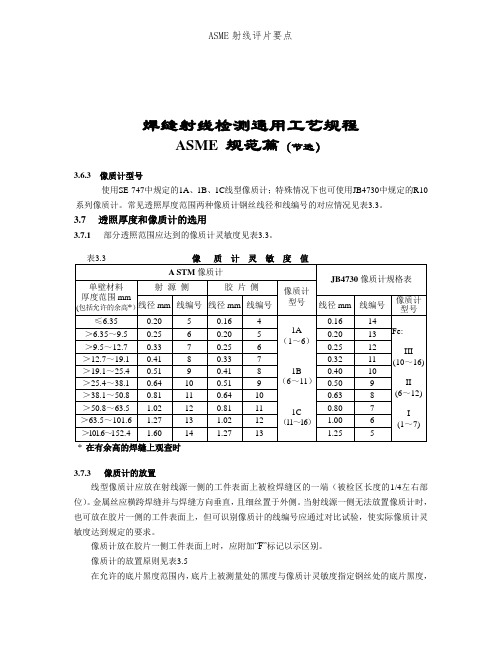
焊缝射线检测通用工艺规程ASME 规范篇(节选)3.6.3像质计型号使用SE-747中规定的1A、1B、1C线型像质计;特殊情况下也可使用JB4730中规定的R10系列像质计。
常见透照厚度范围两种像质计钢丝线径和线编号的对应情况见表3.3。
3.7 透照厚度和像质计的选用3.7.1部分透照范围应达到的像质计灵敏度见表3.3。
3.7.3 像质计的放置线型像质计应放在射线源一侧的工件表面上被检焊缝区的一端(被检区长度的1/4左右部位)。
金属丝应横跨焊缝并与焊缝方向垂直,且细丝置于外侧。
当射线源一侧无法放置像质计时,也可放在胶片一侧的工件表面上,但可识别像质计的线编号应通过对比试验,使实际像质计灵敏度达到规定的要求。
像质计放在胶片一侧工件表面上时,应附加“F”标记以示区别。
像质计的放置原则见表3.5在允许的底片黑度范围内,底片上被测量处的黑度与像质计灵敏度指定钢丝处的底片黑度,bF bd Ug -=当两者黑度变化超过-15%或+30%时,超差区域应放置像质计重新拍片。
由于工件原因造成底片黑度变化较大时(如管子环缝非中心法透照),应在底片有效评定区范围内允许黑度的最大部位和最小部位处各放置一个像质计,以测定不同黑度下的底片灵敏度。
3.7.4 像质计的观察在底片上黑度均匀的部位能够清晰地看到长度不小于10 mm 的连续金属丝影像时,则认为该金属丝是可被识别的。
搭接标记的安放位置见表3.63.9.3几何不清晰度规定几何不清晰度由下式决定:式中: Ug ——几何不清晰度,mm ;d ——焦点尺寸,mm ;b Ug db F m in +=b ——工件厚度,mm ; F ——焦距,mm 。
3.9.4 焦距F 、一次透照长度 L3 和最少透照次数 N 的计算 3.9.4.1 纵缝透照(平板状工件) 最小焦距F min 由下式确定:最少透照次数N min :不设定,所需透照次数按底片黑度进行控制。
在可以实施的情况下,应尽可能采用单壁透照技术。
焊接拍片检测标准

焊接拍片检测标准
焊接拍片检测是一种常用的无损检测方法,用于检测焊接接头的内部缺陷。
以下是一些常见的焊接拍片检测标准:
1. ASME 标准:美国机械工程师协会(ASME)制定了一系列关于焊接检测的标准,其中包括拍片检测标准。
例如,ASME BPVC 第 V 卷包含了关于焊接拍片检测的详细要求。
2. AWS 标准:美国焊接学会(AWS)也制定了一些关于焊接检测的标准,其中包括拍片检测标准。
例如,AWS D1.1 钢结构焊接规范中包含了关于焊接拍片检测的要求。
3. EN 标准:欧洲标准化委员会 (EN)制定了一系列关于焊接检测的标准,其中包括拍片检测标准。
例如,EN 12567 钢焊缝射线检测标准中包含了关于焊接拍片检测的要求。
这些标准通常涵盖了焊接拍片检测的技术要求、检测设备、检测方法、缺陷评定等方面的内容。
具体的标准选择应根据焊接接头的类型、应用领域、法规要求等因素进行确定。
在进行焊接拍片检测时,应按照相关标准的要求进行操作,确保检测
结果的准确性和可靠性。
同时,检测人员应具备相应的资质和经验,以确保检测过程的质量。
ASME标准射线底片评定规则
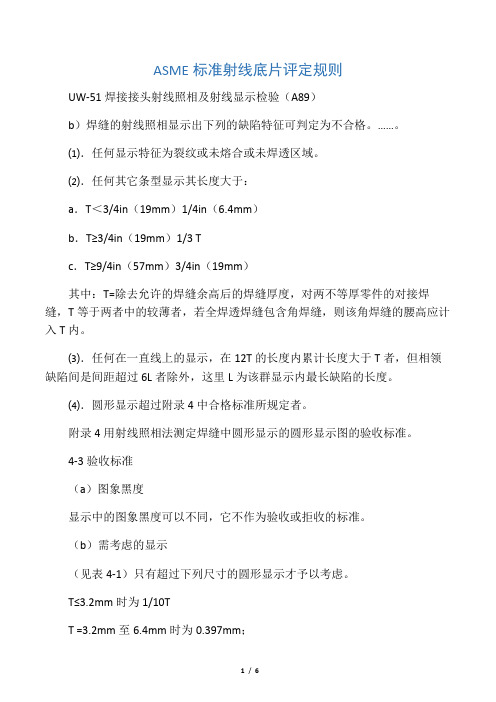
ASME标准射线底片评定规则UW-51焊接接头射线照相及射线显示检验(A89)b)焊缝的射线照相显示出下列的缺陷特征可判定为不合格。
……。
⑴.任何显示特征为裂纹或未熔合或未焊透区域。
⑵.任何其它条型显示其长度大于:a.T<3/4in(19mm)1/4in(6.4mm)b.T≥3/4in(19mm)1/3 Tc.T≥9/4in(57mm)3/4in(19mm)其中:T=除去允许的焊缝余高后的焊缝厚度,对两不等厚零件的对接焊缝,T等于两者中的较薄者,若全焊透焊缝包含角焊缝,则该角焊缝的腰高应计入T内。
⑶.任何在一直线上的显示,在12T的长度内累计长度大于T者,但相领缺陷间是间距超过6L者除外,这里L为该群显示内最长缺陷的长度。
⑷.圆形显示超过附录4中合格标准所规定者。
附录4用射线照相法测定焊缝中圆形显示的圆形显示图的验收标准。
4-3验收标准(a)图象黑度显示中的图象黑度可以不同,它不作为验收或拒收的标准。
(b)需考虑的显示(见表4-1)只有超过下列尺寸的圆形显示才予以考虑。
T≤3.2mm时为1/10TT =3.2mm至6.4mm时为0.397mm;6.4mm<T≤50.8mm时为0.79mm;T >50.8mm时为1.6mm。
(c)圆形显示的最大尺寸(见表4-1)任何显示的最大许可尺寸应为1/4T或3.97mm中的较小者,但与相邻显示相距25.4mm或更远的单个显示例外,它可以等于1/3T或6.4mm中的较小者。
对T大于50.8mm,单个显示的最大许可尺寸应增加到9.5mm。
(d)线性排列圆形显示在长度等于12T内显示各直径的总和小于T时,线性排列圆形显示是合格的。
见图4-1。
各组线性排列圆形显示的长度及各组显示之间的间距应符合图4-2的要求。
P462P1171表4-1厚度Tin小于1/81/83/161/45/163/87/169/165/811/163/4~2超过2mm小于3.23.24.86.47.99.511.112.714.315.917.519.1~50.8超过50.8圆形显示的最大许可尺寸mm 不规则的1/4T1.1941.6001.9812.3112.7693.1753.6073.9623.9623.9623.962单个的1/3T1.0671.6002.1082.6423.1753.7084.2674.7755.8426.359.5250.7871.600注:此表仅作为例子。
ASME射线评片要点
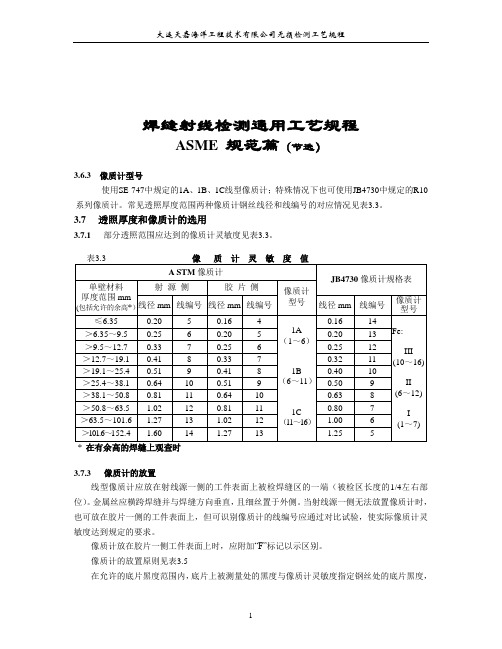
焊缝射线检测通用工艺规程ASME 规范篇(节选)3.6.3像质计型号使用SE-747中规定的1A、1B、1C线型像质计;特殊情况下也可使用JB4730中规定的R10系列像质计。
常见透照厚度范围两种像质计钢丝线径和线编号的对应情况见表3.3。
3.7 透照厚度和像质计的选用3.7.1部分透照范围应达到的像质计灵敏度见表3.3。
3.7.3 像质计的放置线型像质计应放在射线源一侧的工件表面上被检焊缝区的一端(被检区长度的1/4左右部位)。
金属丝应横跨焊缝并与焊缝方向垂直,且细丝置于外侧。
当射线源一侧无法放置像质计时,也可放在胶片一侧的工件表面上,但可识别像质计的线编号应通过对比试验,使实际像质计灵敏度达到规定的要求。
像质计放在胶片一侧工件表面上时,应附加“F”标记以示区别。
像质计的放置原则见表3.5在允许的底片黑度范围内,底片上被测量处的黑度与像质计灵敏度指定钢丝处的底片黑度,bF bd Ug -=当两者黑度变化超过-15%或+30%时,超差区域应放置像质计重新拍片。
由于工件原因造成底片黑度变化较大时(如管子环缝非中心法透照),应在底片有效评定区范围内允许黑度的最大部位和最小部位处各放置一个像质计,以测定不同黑度下的底片灵敏度。
3.7.4 像质计的观察在底片上黑度均匀的部位能够清晰地看到长度不小于10 mm 的连续金属丝影像时,则认为该金属丝是可被识别的。
搭接标记的安放位置见表3.63.9.3几何不清晰度规定几何不清晰度由下式决定:式中: Ug ——几何不清晰度,mm ;d ——焦点尺寸,mm ;b Ug db F m in +=b ——工件厚度,mm ; F ——焦距,mm 。
3.9.4 焦距F 、一次透照长度 L3 和最少透照次数 N 的计算 3.9.4.1 纵缝透照(平板状工件) 最小焦距F min 由下式确定:最少透照次数N min :不设定,所需透照次数按底片黑度进行控制。
在可以实施的情况下,应尽可能采用单壁透照技术。
ASME无损检测中全部和局部两种检测比例的要求
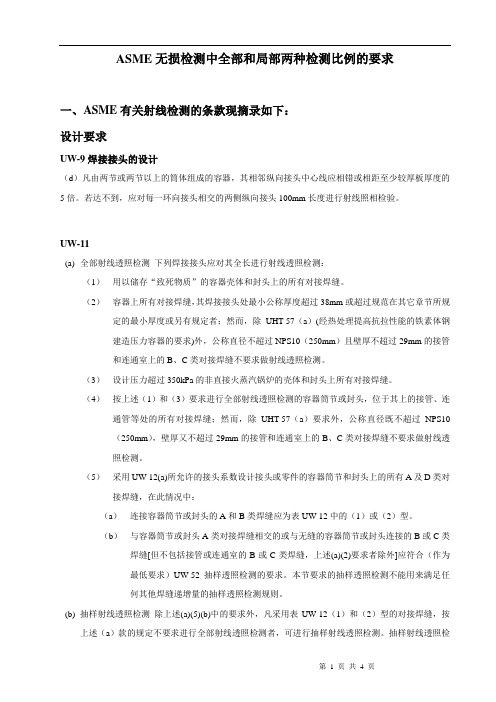
ASME无损检测中全部和局部两种检测比例的要求一、ASME有关射线检测的条款现摘录如下:设计要求UW-9焊接接头的设计(d)凡由两节或两节以上的筒体组成的容器,其相邻纵向接头中心线应相错或相距至少较厚板厚度的5倍。
若达不到,应对每一环向接头相交的两侧纵向接头100mm长度进行射线照相检验。
UW-11(a)全部射线透照检测下列焊接接头应对其全长进行射线透照检测:(1)用以储存“致死物质”的容器壳体和封头上的所有对接焊缝。
(2)容器上所有对接焊缝,其焊接接头处最小公称厚度超过38mm或超过规范在其它章节所规定的最小厚度或另有规定者;然而,除UHT-57(a)(经热处理提高抗拉性能的铁素体钢建造压力容器的要求)外,公称直径不超过NPS10(250mm)且壁厚不超过29mm的接管和连通室上的B、C类对接焊缝不要求做射线透照检测。
(3)设计压力超过350kPa的非直接火蒸汽锅炉的壳体和封头上所有对接焊缝。
(4)按上述(1)和(3)要求进行全部射线透照检测的容器筒节或封头,位于其上的接管、连通管等处的所有对接焊缝;然而,除UHT-57(a)要求外,公称直径既不超过NPS10(250mm),壁厚又不超过29mm的接管和连通室上的B、C类对接焊缝不要求做射线透照检测。
(5)采用UW-12(a)所允许的接头系数设计接头或零件的容器筒节和封头上的所有A及D类对接焊缝,在此情况中:(a)连接容器筒节或封头的A和B类焊缝应为表UW-12中的(1)或(2)型。
(b)与容器筒节或封头A类对接焊缝相交的或与无缝的容器筒节或封头连接的B或C类焊缝[但不包括接管或连通室的B或C类焊缝,上述(a)(2)要求者除外]应符合(作为最低要求)UW-52抽样透照检测的要求。
本节要求的抽样透照检测不能用来满足任何其他焊缝递增量的抽样透照检测规则。
(b)抽样射线透照检测除上述(a)(5)(b)中的要求外,凡采用表UW-12(1)和(2)型的对接焊缝,按上述(a)款的规定不要求进行全部射线透照检测者,可进行抽样射线透照检测。
射线检测评片技巧

射线检测评片技巧评片技巧是放射科技师的重要职责之一,因此需要具备良好的医学知识背景以及丰富的工作经验。
下面将介绍一些常用的射线检测评片技巧:1.仔细观察:评片时应仔细观察片子中的每个细节,包括骨骼结构的完整性、软组织的异常、器官的形态和大小等。
对于不同的放射线检查,要注意观察与该检查相关的特定结构。
2.正确的标记和定位:评片时,对于每一张片子都要正确标记左右、上下、前后,确保能准确的判断疾病的位置和性质。
同时,片子的取向也需要正确,以便医生能够准确判断。
3.对比度的评估:评估片子的对比度是非常重要的,它可以决定影像的清晰度以及对病变的显示情况。
对比度的选择应根据具体病情来决定,过高或过低的对比度都会影响医生的判断。
4.病变的形态学特征:根据病变的形态学特征,可以判断病变的良恶性及其可能的病理类型。
例如,恶性肿瘤通常具有不规则的形状,边界模糊,而良性肿瘤则具有规则的形状,边界清晰。
5.密度和纹理的评估:除了形态学特征外,片子中的密度和纹理也是非常重要的评估指标。
密度的不均匀分布可以提示病灶的存在,而纹理的变化可以反映器官或组织的病变情况。
6.与患者病史的结合:评估片子时,要结合患者的病史以及其他检查结果,以便作出更准确的诊断。
一个病变的诊断不仅依赖于片子本身的表现,还需与其他信息相结合。
7.及时反馈:评片后,要及时向医生提供评估结果。
有时射线检查是为了排除疾病,如果片子未显示明确的异常,可以适当提醒医生对其他病因进行考虑。
8.不断学习和提升:射线检测评片技巧是一个不断学习和提升的过程。
放射科技师应不断学习新的医学知识,了解新的技术和方法,并在实践中不断积累经验,提升自己的评片水平。
总而言之,射线检测评片技巧是放射科技师在工作中不可或缺的一部分。
通过合理的评片技巧,可以为医生提供准确的诊断信息,为患者的治疗和康复提供有力的支持。
放射科技师需要综合运用医学知识、工作经验和专业技能,不断提高自身评片水平,提供更优质的服务。
ASME规范-焊缝RT-评定法则

ASME规范中焊缝RT评定法则一. 透照黑度要求:(1)单片:X射线D≥1.8,γ射线:D≥2.0;(2)多片曝光并叠片观察时,每一张底片的D≥1.3;(3)对(1)或(2)最大黑度D=4.0;(4)当孔型IQI的本体黑度或线型IQI规定线号区的黑度为D时,则被检区任一处的黑度为0.85D~1.3D,否则为不符合要求,在这超差区域应另加一个IQI重新拍片──计算D的变化时,应圆整到0.1。
二.线型IQI选用按下表规定:(1)线形缺陷显示评为不合格的有三种:((a)任何显示特征为裂纹、未焊透、未熔合的;对全焊透焊缝包含角焊缝,则角焊缝的厚度应计入t内。
(c)任何一群成一直线分布的显示,在12 t焊缝长度内显示累计长度> t的,但相邻缺间距> 6L的除外,这L为群显示中最长缺陷显示长度。
当长度<12t的则按比例折算。
(2)圆形缺陷显示(a)不计黑度大小;(b)计作圆形缺陷显示的:(c)间距≥1in.(25mm)时,允许单个显示尺寸为1/3 t或1/4in.(6mm)中的较小者。
若t >2in.(50mm)允许单个圆形显示尺寸为3/8in.(10mm)。
(d)多个圆形显示成线状排列时:在长度为12 t内显示直径d的总和< t时为合格,详见强制性附录4中图4-1。
各组群孔显示成线状排列长度Li及各组相互间距的规定,详见图4-2;在长度12 t内各组群长度之和< t为合格。
(d)密集的和单个的圆形显示对于不同焊缝厚度在图4-3至图4-8中分别给出了典型密集度和尺寸的合格范围,这应结合表4-1给焊缝质量作出正确评定。
(e)对于焊缝厚度t <1/8(3mm)时,在长6in.(150mm)的焊缝内圆形显示数量≤12为合格。
当长度< 6in.(150mm)的焊缝则应按比例折算。
(以上图、表的复印件另附本文后面)(f)密集性显示:(ⅰ)合格的密集性显示长度≤1in.(25mm)或2t中的较小者。
- 1、下载文档前请自行甄别文档内容的完整性,平台不提供额外的编辑、内容补充、找答案等附加服务。
- 2、"仅部分预览"的文档,不可在线预览部分如存在完整性等问题,可反馈申请退款(可完整预览的文档不适用该条件!)。
- 3、如文档侵犯您的权益,请联系客服反馈,我们会尽快为您处理(人工客服工作时间:9:00-18:30)。
焊缝射线检测通用工艺规程
ASME 规篇(节选)
3.6.3像质计型号
使用SE-747中规定的1A、1B、1C线型像质计;特殊情况下也可使用JB4730中规定的R10系列像质计。
常见透照厚度围两种像质计钢丝线径和线编号的对应情况见表3.3。
3.7 透照厚度和像质计的选用
3.7.1部分透照围应达到的像质计灵敏度见表3.3。
3.7.3 像质计的放置
线型像质计应放在射线源一侧的工件表面上被检焊缝区的一端(被检区长度的1/4左右部位)。
金属丝应横跨焊缝并与焊缝方向垂直,且细丝置于外侧。
当射线源一侧无法放置像质计时,也可放在胶片一侧的工件表面上,但可识别像质计的线编号应通过对比试验,使实际像质计灵敏度达到规定的要求。
像质计放在胶片一侧工件表面上时,应附加“F”标记以示区别。
像质计的放置原则见表3.5
在允许的底片黑度围,底片上被测量处的黑度与像质计灵敏度指定钢丝处的底片黑度,当
b
F b
d Ug -=
两者黑度变化超过-15%或+30%时,超差区域应放置像质计重新拍片。
由于工件原因造成底片黑度变化较大时(如管子环缝非中心法透照),应在底片有效评定区围允许黑度的最大部位和最小部位处各放置一个像质计,以测定不同黑度下的底片灵敏度。
3.7.4 像质计的观察
在底片上黑度均匀的部位能够清晰地看到长度不小于10 mm 的连续金属丝影像时,则认为该金属丝是可被识别的。
搭接标记的安放位置见表3.6
3.9.3
几何不清晰度规定
几何不清晰度由下式决定:
式中: Ug ——几何不清晰度,mm ;
d ——焦点尺寸,mm ;
b Ug db F m in +=
b ——工件厚度,mm ; F ——焦距,mm 。
3.9.4 焦距F 、一次透照长度 L3 和最少透照次数 N 的计算 3.9.
4.1 纵缝透照(平板状工件) 最小焦距F min 由下式确定:
最少透照次数N min :不设定,所需透照次数按底片黑度进行控制。
在可以实施的情况下,应尽可能采用单壁透照技术。
为了证实能充分覆盖,应进行足
够次数的曝光 3.9.4.2 环缝透照
a. 小径管(管子外径Do ≤89mm)双壁双影透照 最少透照次数N min :
1. 椭圆成像:N min =每个接头至少要进行二次互成90°的曝光。
2. 垂直成像:N min =每个接头至少要进行三次互成60°或120°的曝光。
b. 双壁双影透照时的最小焦距F min :
不同规格的小径管其透照时的最小焦距应不小于表3.9中的数值。
为便于现场使用,b 可近似看成管子外径Do ,而f (焦点到工件表面的距离)则用b 的倍数
来表示,焦距 F min = f + b 。
(表中b 未包括余高,如精确计算则 b=D O + 双侧余高。
)
表3.10
部分小径管双壁双影透照时的最小f
3.9.
4.3. 除小径管双壁双影外其它环缝透照:
按透照方式可分为以下五种,在满足几何不清晰度要求的情况下其最少透照次数分别为:
1. 环缝单壁外透法:按-15%~+30%控制底片的最大和最小黑度,确定最少透照次数。
2. 环缝透法:
①F=R 中心法(R—半径)透照次数≥1次。
3. 双壁单影法:至少进行三次互成120°的曝光。
3.9.
4.4 底片有效长度
底片有效长度应小于底片实际长度,连续透照时底片两端应各留出≥20mm作为搭接长度。
3.11.
4.1 底片黑度应符合表3.12的要求。
表3.12 底片黑度围
3.12 焊缝缺陷等级评定
长宽比小于或等于3的缺陷定义为圆形缺陷。
它们可以是圆形、椭圆形、锥形或带有尾巴(在测定尺寸时应包括尾巴)等不规则的形状。
缺陷的种类包括气孔、夹渣和夹钨等。
长宽比大于3的缺陷定义为条形缺陷,包括气孔、夹渣和夹钨等。
焊缝缺陷等级评定见表3.13、表3.14、3.15和表3.16。
3.12.1焊缝缺陷评定之一
3.12. 2 焊缝缺陷等级评定之二。