抽真空模具的基本设计
IMG阴模真空成型工解析

19
IMG产品主要缺陷介绍
问题:IMG真空成 型后TPO层与PP 发泡层分层
解决方法:降低加热温度;表 皮可能受潮,需要对表皮进行 烘干处理
20
IMG产品主要缺陷介绍
问题:表皮凹坑
解决方法:在阳模贴毛毡减小 模具内的间隙
21
IMG产品主要缺陷介绍
问题:表皮褶皱
解决方法:将褶皱对应位置的 骨架打磨
22
17
IMG工艺介绍
四、模温
在IMG工艺中,模温也是一个重要的参数,如果模温过高则 会造成表皮脱模时变形,如果模温过低则会造成皮纹吸附不清 晰、表皮形状不清晰等缺陷。
18
IMG工艺介绍
五、模内间隙
在IMG+复合的工艺中,模内间隙非常关键,骨架在下模 预装后合模,骨架与模具有细小间隙,如果这个间隙过小,会 造成表皮拉破的缺陷,如果间隙过大则会造成成型褶皱。这个 间隙在模具供应商开发时已经定下,所以骨架的尺寸就至关重 要了。
16
IMG工艺介绍
三、真空度
抽真空是真空成型的必要工序,此道工序的关键参数就是真 空度。
抽真空是靠一个大负压罐完成,负压罐在待机工作时将负压 抽到-0.099MP,然后在抽真空时打开阀门,将模具内腔抽成真 空,要求模具内腔负压力大于-0.085MP。
如果模具内腔真空度过小则说明模具内腔漏气,可能是模具 密封问题或者是表皮加热温度不够,会造成表皮成型不好,皮 纹不清晰等问题。
模具的成本较高和制造周期较长(与传统的凸模成型相比)
模具有一定的寿命,一般为40万模左右(当然,其寿命要远 远高于搪塑,但低于阳模真空成型)
与搪塑模一样,一旦模具损坏(皮纹损伤),修复困难
8
IMG工艺材料介绍
真空吸塑成型原理

真空吸塑成型原理
真空吸塑成型是一种常用于制造塑料制品的加工方法。
该方法利用真空将塑料片或片材软化后吸附在模具表面,经过冷却后形成所需的形状。
该过程的原理是利用模具和真空系统进行加热和冷却。
首先,将塑料片或片材置于预热器中,使其变软。
然后,将变软的塑料片或片材放置于模具上,模具的表面有特定的凹凸形状。
接着,通过气泵将模具上的空气抽出,形成真空环境,使塑料片或片材贴附在模具表面。
当塑料片或片材贴附在模具表面后,开始进行冷却。
通过冷却介质循环流动,使模具表面温度迅速降低,从而使塑料片或片材快速硬化。
在塑料片或片材完全硬化后,可以打开模具,将成型的塑料制品取出。
真空吸塑成型过程中,模具的设计和制造非常重要。
模具的凹凸形状决定了最终产品的形状和尺寸。
同时,模具的材料需要具有良好的导热性能,以便实现快速的冷却。
此外,真空系统的性能也关系到成型效果的好坏,需要确保能够提供足够的真空度和稳定的抽气速度。
总的来说,真空吸塑成型利用模具和真空系统的协作,通过加热软化塑料片或片材,然后利用真空将其吸附在模具表面,最后经过冷却形成所需的形状。
这种成型方法在塑料制品制造中得到广泛应用,具有成本低、加工速度快、适用性广等优点。
抽真空注塑模具设计及应用研究

抽真空注塑模具设计及应用研究随着工业制造的不断发展,注塑技术在塑料制品生产中扮演着重要的角色。
而抽真空注塑模具作为注塑技术的一种改进和发展,已经在许多行业得到了广泛的应用。
本文将从抽真空注塑模具的设计原理、应用研究和发展趋势等方面展开论述,以期为相关领域的研究人员和生产从业者提供一些有益的参考和启发。
一、抽真空注塑模具设计原理抽真空注塑模具是在注塑成型过程中,通过真空泵将模具内的空气抽出,以实现更好的填充性能和产品质量。
在设计抽真空注塑模具时,需要考虑以下几个方面的因素:1. 模具结构设计。
在抽真空注塑模具的设计中,需要考虑模具的整体结构和空腔的设计。
通常采用具有合理排气结构和通道设计的模具,以便在成型过程中将空气有效地排出模具。
2. 真空系统设计。
真空系统包括真空泵、真空管路、真空表和真空阀等组成部分。
在抽真空注塑模具的设计中,需要根据产品的尺寸和注塑成型工艺的要求,选择合适的真空系统,并将其合理地布置在模具上。
3. 匹配注塑机。
抽真空注塑模具通常需要配合具有真空功能的注塑机使用,以确保在注塑成型过程中能够实现真空抽气。
在模具设计过程中,也需要考虑注塑机的类型和参数,以保证模具和注塑机的匹配性。
抽真空注塑模具在塑料制品生产中具有较广泛的应用,主要体现在以下几个方面:1. 提高产品质量。
抽真空注塑模具可以有效地排除模具内的空气,防止产品层析和气泡等质量问题的发生,从而提高产品的表面光洁度和物理性能。
2. 提高生产效率。
抽真空注塑模具在成型过程中可以有效地改善产品的填充性能,减少熔体的挤出压力,缩短注塑周期,提高生产效率。
3. 扩大产品范围。
抽真空注塑模具可以应用于各种不同形状和结构的产品制造,如薄壁、大型、复杂结构的塑料制品,扩大了产品的设计自由度和生产范围。
4. 节约材料和能源。
抽真空注塑模具可以减少产品的缺陷率,提高利用率,从而节约原材料和能源,降低生产成本。
三、抽真空注塑模具的发展趋势1. 多功能化。
注塑机模具模内抽真空装置简版修正

注塑机模具模内抽真空装置1. 背景介绍注塑机模具模内抽真空装置是注塑行业中的一种关键设备,主要用于在注塑过程中从模具中排除空气,提供更好的产品质量。
本文将介绍注塑机模具模内抽真空装置的原理、功能和优势。
2. 原理及工作过程注塑机模具模内抽真空装置的原理是利用真空泵将模具内的空气抽出,从而形成低压环境,使得塑料材料更好地充填模具腔体。
具体的工作过程如下:1. 真空泵启动,开始抽真空操作。
2. 模具内的空气被真空泵吸走,形成低压环境。
3. 塑料材料进入模具腔体,充填更加均匀。
4. 充填完成后,真空泵停止工作,模具腔体恢复正常气压。
5. 产品冷却固化,模具打开,取出成品。
3. 功能及优势注塑机模具模内抽真空装置具有以下功能和优势:3.1 充填效果更好通过抽真空操作,模具内的空气被排除,确保塑料材料能够充填到每一个角落,减少气泡和缺陷的产生,提高产品质量。
3.2 提高生产效率充填效果更好后,产品的成型质量更高,降低了次品率,减少了后续的检验工作,提高了生产效率。
3.3 节省材料通过充填效果的提升,可以减少塑料材料的使用量,降低生产成本。
3.4 扩大适用范围注塑机模具模内抽真空装置适用于各种塑料材料和复杂的产品结构,如薄壁制品、高透明制品等。
使得在生产过程中,更好地满足客户的需求。
4. 应用领域注塑机模具模内抽真空装置广泛应用于各个领域,如:电子电器行业:用于生产方式壳、电视外壳等塑料零件;医疗器械行业:用于生产医疗器械零件;汽车行业:用于生产汽车内饰、外观零件等;家居用品行业:用于生产家具配件、灯具等。
5.注塑机模具模内抽真空装置在注塑行业中扮演着重要的角色,通过抽真空操作,提高了产品的成型质量和生产效率,减少了次品率和材料浪费,扩大了适用范围。
它在电子电器、医疗器械、汽车、家居用品等领域有广泛的应用。
随着技术的不断发展,注塑机模具模内抽真空装置将更加智能化、高效化,推动注塑行业的发展。
冰箱门胆真空吸塑成型模具抽芯机构设计
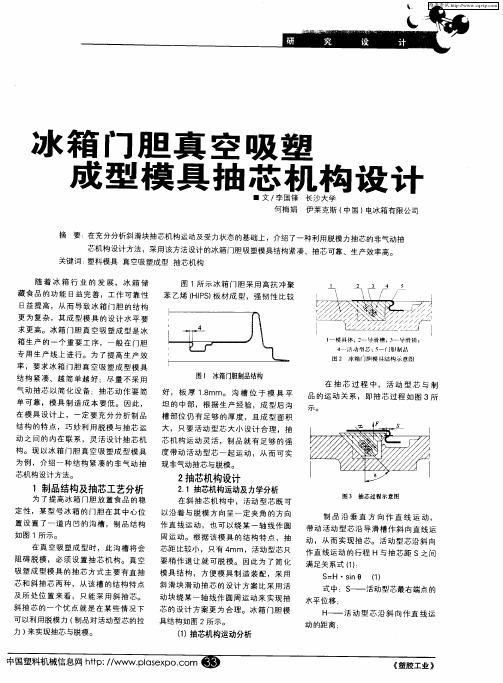
式 中 :S —— 活动型芯最右端点 的
水平位移 :
H —— 活动 型 芯沿 斜 向作直 线 运 动 的距离 :
力 ) 实现抽芯与脱 模。 来
() 1 抽芯机构运动分析
中国塑料机械信息网 ht :/ t /www.ls x o c m p pa e p .o
在 抽 芯 过 程 中 , 活 动 型 芯 与 制 好 , 板 厚 18 .mm。 沟 槽 位 于 模 具 平 品 的 运 动 关 系 , 即 抽 芯 过 程 如 图 3所
示。
坦 的 中部 ,根据 生产 经 验 ,成 型 后沟 槽 部位 仍 有足够 的厚 度 ,且成 型面 积 大 ,只要 活动 型芯 大 小设 计 合理 ,抽 芯机 构运 动 灵活 ,制 品就 有足够 的强
结 构 紧 凑 、 越 简 单 越 好 ;尽 量 不 采 用 图1 冰箱门胆制品结构
图2 冰箱n胴模其结构示意图
气动 抽芯 以简 化设 备 ;抽 芯动 作 要简
单 可 靠 ,模 具 制造 成 本要 低。 因此 , 在模 具 设计 上 ,一 定 要充 分 分析制 品 结构 的特 点 ,巧妙 利 用脱模 与 抽芯 运 动 之间 的 内在 联 系 ,灵 活设 计抽 芯 机 构 。现 以冰 箱 门胆 真空 吸塑成 型模 具 为例 ,介绍 一种 结构 紧 凑 的非 气动抽 芯机构设计 方法。
维普资讯 http://wwLeabharlann
冰 门 胆 真 空 吸 塑 箱 成 型 模 具 抽 芯 机 构 设 计
何 梅娟 伊 莱克斯 ( 中国 ) 电冰 箱有限公 司 介绍 了一种利用脱模力抽芯 的非气动抽 芯机 构设计 方法 ,采用该方法设计 的冰箱 门胆 吸塑模具结构 紧凑 抽芯 可靠 、生产效率 高。 关键词 : 塑料模具 真空 吸塑成型 抽心 机构 - i - i -
汽车内饰件的真空成型工艺详解-精
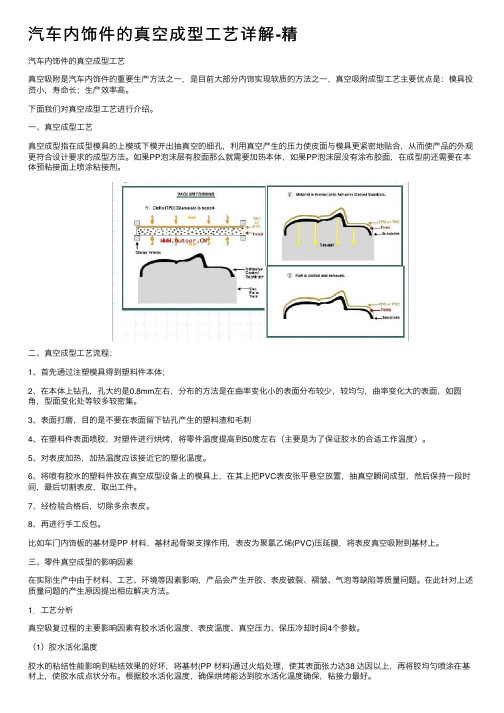
汽车内饰件的真空成型⼯艺详解-精汽车内饰件的真空成型⼯艺真空吸附是汽车内饰件的重要⽣产⽅法之⼀,是⽬前⼤部分内饰实现软质的⽅法之⼀,真空吸附成型⼯艺主要优点是:模具投资⼩,寿命长;⽣产效率⾼。
下⾯我们对真空成型⼯艺进⾏介绍。
⼀、真空成型⼯艺真空成型指在成型模具的上模或下模开出抽真空的细孔,利⽤真空产⽣的压⼒使⽪⾯与模具更紧密地贴合,从⽽使产品的外观更符合设计要求的成型⽅法。
如果PP泡沫层有胶⾯那么就需要加热本体,如果PP泡沫层没有涂布胶⾯,在成型前还需要在本体预粘接⾯上喷涂粘接剂。
⼆、真空成型⼯艺流程:1、⾸先通过注塑模具得到塑料件本体;2、在本体上钻孔,孔⼤约是0.8mm左右,分布的⽅法是在曲率变化⼩的表⾯分布较少,较均匀,曲率变化⼤的表⾯,如圆⾓,型⾯变化处等较多较密集。
3、表⾯打磨,⽬的是不要在表⾯留下钻孔产⽣的塑料渣和⽑刺4、在塑料件表⾯喷胶,对塑件进⾏烘烤,将零件温度提⾼到50度左右(主要是为了保证胶⽔的合适⼯作温度)。
5、对表⽪加热,加热温度应该接近它的塑化温度。
6、将喷有胶⽔的塑料件放在真空成型设备上的模具上,在其上把PVC表⽪张平悬空放置,抽真空瞬间成型,然后保持⼀段时间,最后切割表⽪,取出⼯件。
7、经检验合格后,切除多余表⽪。
8、再进⾏⼿⼯反包。
⽐如车门内饰板的基材是PP 材料,基材起⾻架⽀撑作⽤,表⽪为聚氯⼄烯(PVC)压延膜,将表⽪真空吸附到基材上。
三、零件真空成型的影响因素在实际⽣产中由于材料、⼯艺、环境等因素影响,产品会产⽣开胶、表⽪破裂、褶皱、⽓泡等缺陷等质量问题。
在此针对上述质量问题的产⽣原因提出相应解决⽅法。
1.⼯艺分析真空吸复过程的主要影响因素有胶⽔活化温度、表⽪温度、真空压⼒、保压冷却时间4个参数。
(1)胶⽔活化温度胶⽔的粘结性能影响到粘结效果的好坏,将基材(PP 材料)通过⽕焰处理,使其表⾯张⼒达38 达因以上,再将胶均匀喷涂在基材上,使胶⽔成点状分布。
根据胶⽔活化温度,确保烘烤能达到胶⽔活化温度确保,粘接⼒最好。
真空导入成型 工艺

第三步:增强材料铺设选用增强材料-玻璃纤维,碳纤维,夹心材料…这 要依据制品强度要求来定。选择增强材料对积层工艺来说是很重要的 一步,但对于VIP要多考虑几点。虽然所有织物都可以用,但不同的 材料和织法会影响树脂流速。
VIP工艺的应用领域
1)船艇工业--船体,甲板,方向舵,雷达屏 蔽罩
VIP工艺的应用领域
2)风电能源--叶片,机仓罩 3)体育休闲--头盔,帆板 4)汽车工业--各类车顶,挡风板,车厢 5)建筑领域--建筑物顶部件,建筑模板 6)农业和园艺--粮仓圆盖,农机保护盖
其他问题
1、当然任何一个工艺不可能是十全十美的, 目前来说VIP所需的一次性耗材很大一部分 需要进口,提高材料成本。
2、另外对操作人员的技能要求更高。每一过 程都仔细按步骤做好才能进入下一步的操 作,否则会造成不能逆转的损失。
第六步:配树脂抽真空达到一定要求后,准备树脂。按凝胶 时间配入相应的固化剂,切记不能忘加固化剂,否则很难 弥补。不过一般真空导入树脂含有固化指示剂,可以从颜 色上来判断是否加了固化剂。
第七步:导入树脂把进树脂管路插入配好的树脂桶中,根据 进料顺序依次打开夹子,注意树脂桶的量,及时补充。
第八步:脱模树脂凝胶固化到一定程度后,揭去真空袋材料。 从模具上取出制品并进行后处理。
第四步:真空袋材料铺设先铺上脱模布,接着是导流布,最后是真空袋。 在合上真空袋之前,要仔细考虑树脂和抽真空管路的走向,否则有的 地方树脂会无法浸润到。铺设时要非常小心,以免一些尖锐物刺破真 空袋。
工艺流程
第五步:抽真空铺完这些材料后,夹紧各进树脂管,对整个 体系抽真空,尽量把体系中空气抽空,并检查气密性,这 一步很关键,如有漏点存在,当树脂导入时,空气会进体 入体系,气泡会在漏点向其它地方渗入,甚至于有可能整 个制品报废。
模具抽真空排气设计方案

优点:结构简单,实施方便,效 果显著。
总结词:简单、高效、适用于小 型模具
优缺点
缺点:对于大型模具,需要更多 的时间和能量来抽真空,且可能 需要更高的维护成本。
方案二:间接抽真空法
01
02
背景
在塑料模具、压铸模具等高分子材料成型模具中,残留气体 和挥发物常常会引发许多问题,如气孔、翘曲、变形等,严 重影响产品的质量和生产效率。因此,模具抽真空排气设计 成为了解决这些问题的必要手段。
模具抽真空排气设计的意义
提高产品质量
通过排除模具内部的残留气体和 挥发物,可以减少气孔、翘曲、 变形等问题,从而提高产品的质
THANK YOU
问题三
管道和阀门连接不牢固,导致漏气或真空度不足 。
解决方案三
在连接管道和阀门时,应确保连接处紧固、密封性好, 检查管道和阀门的完好性。
控制:抽真空排气效果的监测和控制方法
01
02
03
方法一
使用压力表监测模具内的 压力变化,判断抽真空排 气效果。
方法二
观察模具表面情况,检查 是否有气孔、气泡等缺陷 ,判断排气效果。
不足
本次研究虽然取得了一定的成果,但在实验过程中发现,该方案对于一些特殊材料的排气效果还有待进一步提高 。
结论二:对未来研究方向的展望
深入研究不同材料对模具抽真空 排气效果的影响,找出更加普遍
适用的解决方案。
进一步优化模具抽真空排气的设 计方案,提高其使用效率和稳定
性。
结合其他先进的制造技术,研究 更加智能化的模具抽真空排气方 案,提高生产效率和产品质量。
- 1、下载文档前请自行甄别文档内容的完整性,平台不提供额外的编辑、内容补充、找答案等附加服务。
- 2、"仅部分预览"的文档,不可在线预览部分如存在完整性等问题,可反馈申请退款(可完整预览的文档不适用该条件!)。
- 3、如文档侵犯您的权益,请联系客服反馈,我们会尽快为您处理(人工客服工作时间:9:00-18:30)。
抽真空模具的基本設計
為了有效地抽真空(92年11月)
用電腦分析模具內塑膠的流動狀況的方法已經趨向普遍化了,但結果未必如分析的那樣,這是為什麼呢?
考慮到原因如下。
即:
1.模腔內的氣壓通常是以一個大氣壓為前提來進行模流分析的。
2.無視塑膠從澆口射出時模腔內產生的高溫氣體。
(無視規則)
不管分析得多好,產生不飽模、熔合線、燒焦等不良,是因為沒有考慮到模腔內的空氣、氣體被壓縮了。
當然,抽掉空氣、氣體就都解決了,這樣的成型不是簡單的。
其中有runner、gate、模溫、塑膠溫度等復雜的因素。
但是,抽去模腔內的空氣和氣體為更好的成型提供了前提,這樣說決不過分。
把空氣、產生的氣體有效地排出模腔,需要怎樣的成型條件呢?絕對不能引起燒焦。
也不能有不飽模。
應該縮小熔合線。
抽真空的方法是把空氣和氣體從模腔內排出的最合適的方法。
真空對利用壓力差把氣體從一個微小間隙的空間抽出來非常有效。
真空度越高,越能從微小的間隙抽出來。
為了能瞬間把空氣排出,必須考慮排氣量的大小。
推薦以下方法作為排出氣體的時機。
1. 完成合模(信號)→排出模腔內的空氣(約0.5sec)
2. 開始射出→抽取產生的氣體(到塑膠到達排氣槽為止)
3. 排除排氣槽內殘留的氣體(約1sec)
以上1、2、3根據定時器來設置。
研究抽真空裝置的性能,同時必須解決的問題是排出氣體的模具構造的設計。
模具的構造千差萬別,但基本的必要的條件有以下4點。
1.把氣體從模具內有效排出的注意點
為了把模腔內殘留的空氣和射出時產生的氣體有效地用真空排出,使用
排氣槽和燒結金屬,下列項目是最合適的模具設計。
1)排氣槽設置在氣體殘留及其周圍處。
若塑膠溢出排氣槽,排氣槽會
因為塑膠的阻塞而無法排出氣體。
2)排氣槽的截面積必須大。
通常成型時,射出時間很短,必須瞬間抽取氣體。
如果截面積小的
話,要快速抽出,其效果就不好了。
3)盡量減小從排氣槽到模具出口的抽取(或排氣)管道內的真空壓力損
失,這樣的管道設計是必要的。
4)不管是排氣槽還是燒結金屬,從模腔內抽取空氣是從極微小的間隙
抽取,必須防止大氣從模具外進入。
為此,根據模具不同,用橡膠
等密封是必要的。
一般很多模具即使沒有密封,密閉度也很高,無的高精度模具,不需要密封,這是實情。
上述4點是成功抽真空的重點,再要說的話,抽真空是即使沒有熟練掌握的技術人員,十分理論的check也可能的一種技術。
即,若即使保持必要的真空度(-600mmHg左右)也無法有效地抽真空,則如下作check。
a). 排氣槽的截面積小嗎?
b). 排出管道內的抵抗大嗎?
c). 排氣槽有氣體阻塞嗎?
再者,若即使排氣槽和管道暢通,也無理想的結果,証明模具正在排出大氣。
此時在模具上裝一個真空計的話,真空計的指針動了就立即能判斷。
2.抽真空模具的標準化提案
最近在成型工廠,抽真空模具的標準化制作越來越多了,因此提案僅供
參考。
但是,這種方法隻適用與中小型成型機,大型成型機要另當別論
了。
1) 在墊腳上安裝抽取口
這種方法減小了管道的壓力損失,加工也容易。
另外,黏稠物也
不容易積留在EP等上了。
2) 因此,墊腳如下圖標準化。
3)排氣槽及吸氣管道的方式
若PL面或模仁的接觸面設排氣槽,吸氣管道通過鑽孔,和墊腳的
空間全部連通。
4)若在壓出pin的間隙及模仁的接觸面裝入排氣槽,抽取空氣時模具
上的注意點。
a)吸氣(或排氣)管道的阻塞小
b)例圖
關於燒結金屬
流動性極好,容易產生毛頭的成型材料和在產品的特質上,要求毛頭的長度在50μ以下的成型,從排氣槽抽取氣體甚,排氣槽有深度的限制,不期待有令人滿意的效果。
另外,在模具的構造上,也有在氣體滯留處不安裝排氣槽的。
這種情況的抽真空多使用燒結金屬,這裡介紹一下市場上出售的商品。
1.東京燒結金屬(株)
圓筒形的燒結金屬是一個有880個直線的孔(直徑為0.2、0.1、0.05、0.03)。
外徑為Φ10、Φ8、Φ6、Φ4、Φ2。
(長為10mm共通)
2.新東工業(株)
10μ以下的細微的連通孔平均地分散在整個模具材料。
與上述燒結金屬的最大的差異是,作為核心的一部分能加工成任意形狀使用。
通氣率為整體25%。
上述2家公司排氣槽的比較
3.燒結金屬在使用上的注意點
不管使用哪一種,因為孔很微小,容易引起黏稠物堵塞。
利用真空抽出氣體可以說是不可欠缺的條件。
就本公司的排氣槽盒的使用方法上來說:
1) GVB-L形
真空抽取時間比通常的要長2~3秒。
2) GVB-A形
開模時,使得壓縮空氣。
特別是使用新東工業的燒結金屬,使用GVB-A形是不可缺少的。