机械类外文翻译
机械专业外文文献翻译

翻译部分英文原文High-speed machining and demand for the development ofHigh-speed machining is contemporary advanced manufacturing technology an important component of the high-efficiency, High-precision and high surface quality, and other features. This article presents the technical definition of the current state of development of China's application fields and the demand situation.High-speed machining is oriented to the 21st century a new high-tech, high-efficiency, High-precision and high surface quality as a basic feature, in the automobile industry, aerospace, Die Manufacturing and instrumentation industries gained increasingly widespread application, and has made significant technical and economic benefits. contemporary advanced manufacturing technology an important component part.HSC is to achieve high efficiency of the core technology manufacturers, intensive processes and equipment packaged so that it has a high production efficiency. It can be said that the high-speed machining is an increase in the quantity of equipment significantly improve processing efficiency essential to the technology. High-speed machining is the major advantages : improve production efficiency, improve accuracy and reduce the processing of cutting resistance.The high-speed machining of meaning, at present there is no uniform understanding, there are generally several points as follows : high cutting speed. usually faster than that of their normal cutting 5 -10 times; machine tool spindle speed high, generally spindle speed in -20000r/min above 10,000 for high-speed cutting; Feed at high velocity, usually 15 -50m/min up to 90m/min; For different cutting materials and the wiring used the tool material, high-speed cutting the meaning is not necessarily the same; Cutting process, bladed through frequency (Tooth Passing Frequency) closer to the "machine-tool - Workpiece "system the dominant natural frequency (Dominant Natural Frequency), can be considered to be high-speed cutting. Visibility high-speed machining is a comprehensive concept.1992. Germany, the Darmstadt University of Technology, Professor H. Schulz in the 52th on the increase of high-speed cutting for the concept and the scope, as shown in Figure 1. Think different cutting targets, shown in the figure of the transition area (Transition), to be what is commonly called the high-speed cutting, This is also the time of metal cutting process related to the technical staff are looking forward to, or is expected to achieve the cutting speed.High-speed machining of machine tools, knives and cutting process, and other aspects specific requirements. Several were from the following aspects : high-speed machining technology development status and trends.At this stage, in order to achieve high-speed machining, general wiring with high flexibility of high-speed CNC machine tools, machining centers, By using a dedicated high-speed milling, drilling. These equipment in common is : We must also have high-speed and high-speed spindle system feeding system, Cutting can be achieved in high-speed process. High-speed cutting with the traditional cutting the biggest difference is that "Machine-tool-workpiece" the dynamic characteristics of cutting performance is stronger influence. In the system, the machine spindle stiffness, grip or form, a long knife set, spindle Broach, torque tool set, Performance high-speed impact are important factors.In the high-speed cutting, material removal rate (Metal Removal Rate, MRR), unit time that the material was removed volume, usually based on the "machine-tool-workpiece" whether Processing System "chatter." Therefore, in order to satisfy the high-speed machining needs, we must first improve the static and dynamic stiffness of machine spindle is particularly the stiffness characteristics. HSC reason at this stage to be successful, a very crucial factor is the dynamic characteristics of the master and processing capability.In order to better describe the machine spindle stiffness characteristics of the project presented new dimensionless parameter - DN value, used for the evaluation of the machine tool spindle structure on the high-speed machining of adaptability. DN value of the so-called "axis diameter per minute speed with the product." The newly developed spindle machining center DN values have been great over one million. To reduce the weight bearing, but also with an array of steel products than to the much more light ceramic ball bearings; Bearing Lubrication most impressive manner mixed with oil lubrication methods. In the field of high-speed machining. have air bearings and the development of magnetic bearings and magnetic bearings and air bearings combined constitute the magnetic gas / air mixing spindle.Feed the machine sector, high-speed machining used in the feed drive is usually larger lead, multiple high-speed ball screw and ball array of small-diameter silicon nitride (Si3N4) ceramic ball, to reduce its centrifugal and gyroscopic torque; By using hollow-cooling technology to reduce operating at high speed ball screw as temperature generated by the friction between the lead screw and thermal deformation.In recent years, the use of linear motor-driven high-speed system of up to'' Such feed system has removed the motor from workstations to Slide in the middle of all mechanical transmission links, Implementation of Machine Tool Feed System of zero transmission. Because no linear motor rotating components, from the role of centrifugal force, can greatly increase the feed rate. Linear Motor Another major advantage of the trip is unrestricted. The linear motor is a very time for a continuous machine shop in possession of the bed. Resurfacing of the very meeting where avery early stage movement can go, but the whole system of up to the stiffness without any influence. By using high-speed screw, or linear motor can greatly enhance machine system of up to the rapid response. The maximum acceleration linear motors up to 2-10G (G for the acceleration of gravity), the largest feed rate of up to 60 -200m/min or higher.2002 world-renowned Shanghai Pudong maglev train project of maglev track steel processing, Using the Shenyang Machine Tool Group Holdings Limited McNair friendship company production plants into extra-long high-speed system for large-scale processing centers achieve . The machine feeding system for the linear guide and rack gear drive, the largest table feed rate of 60 m / min, Quick trip of 100 m / min, 2 g acceleration, maximum speed spindle 20000 r / min, the main motor power 80 kW. X-axis distance of up to 30 m, 25 m cutting long maglev track steel error is less than 0.15 mm. Maglev trains for the smooth completion of the project provided a strong guarantee for technologyIn addition, the campaign machine performance will also directly affect the processing efficiency and accuracy of processing. Mold and the free surface of high-speed machining, the main wiring with small cut deep into methods for processing. Machine requirements in the feed rate conditions, should have high-precision positioning functions andhigh-precision interpolation function, especially high-precision arc interpolation. Arc processing is to adopt legislation or thread milling cutter mold or machining parts, the essential processing methods. Cutting Tools Tool Material developmenthigh-speed cutting and technological development of the history, tool material is continuous progress of history. The representation ofhigh-speed cutting tool material is cubic boron nitride (CBN). Face Milling Cutter use of CBN, its cutting speed can be as high as 5000 m / min, mainly for the gray cast iron machining. Polycrystalline diamond (PCD) has been described as a tool of the 21st century tool, It is particularly applicable to the cutting aluminum alloy containing silica material, which is light weight metal materials, high strength, widely used in the automobile, motorcycle engine, electronic devices shell, the base, and so on. At present, the use of polycrystalline diamond cutter Face Milling alloy, 5000m/min the cutting speed has reached a practical level. In addition ceramic tool also applies to gray iron of high-speed machining; Tool Coating : CBN and diamond cutter, despite good high-speed performance, but the cost is relatively high. Using the coating technology to make cutting tool is the low price, with excellent mechanical properties, which can effectively reduce the cost. Now high-speed processing of milling cutter, with most of the wiring between the Ti-A1-N composite technology for the way of multi-processing, If present in the non-ferrous metal or alloy material dry cutting, DLC (Diamond Like Carbon) coating on thecutter was of great concern. It is expected that the market outlook is very significant;Tool clamping system : Tool clamping system to support high-speed cutting is an important technology, Currently the most widely used is a two-faced tool clamping system. Has been formally invested as a commodity market at the same clamping tool system are : HSK, KM, Bigplus. NC5, AHO systems. In the high-speed machining, tool and fixture rotary performance of the balance not only affects the precision machining and tool life. it will also affect the life of machine tools. So, the choice of tool system, it should be a balanced selection of good products.Process ParametersCutting speed of high-speed processing of conventional shear velocity of about 10 times. For every tooth cutter feed rate remained basically unchanged, to guarantee parts machining precision, surface quality and durability of the tool, Feed volume will also be a corresponding increase about 10 times, reaching 60 m / min, Some even as high as 120 m / min. Therefore, high-speed machining is usually preclude the use of high-speed, feed and depth of cut small cutting parameters. Due to the high-speed machining cutting cushion tend to be small, the formation of very thin chip light, Cutting put the heat away quickly; If the wiring using a new thermal stability better tool materials and coatings, Using the dry cutting process for high-speed machining is the ideal technology program. High-speed machining field of applicationFlexible efficient production lineTo adapt to the needs of new models, auto body panel molds andresin-prevention block the forming die. must shorten the production cycle and reduce the cost of production and, therefore, we must make great efforts to promote the production of high-speed die in the process. SAIC affiliated with the company that : Compared to the past, finishing, further precision; the same time, the surface roughness must be met, the bending of precision, this should be subject to appropriate intensive manual processing. Due to the extremely high cutting speed, and the last finishing processes, the processing cycle should be greatly reduced. To play for machining centers and boring and milling machining center category represented by the high-speed machining technology and automatic tool change function of distinctions Potential to improve processing efficiency, the processing of complex parts used to be concentrated as much as possible the wiring process, that is a fixture in achieving multiple processes centralized processing and dilute the traditional cars, milling, boring, Thread processing different cutting the limits of technology, equipment and give full play to the high-speed cutting tool function, NC is currently raising machine efficiency and speed up product development in an effective way. Therefore, the proposed multi-purpose tool of the new requirements call for a tool to complete different partsof the machining processes, ATC reduce the number of ATC to save time, to reduce the quantity and tool inventory, and management to reduce production costs. More commonly used in a multifunctional Tool, milling, boring and milling, drilling milling, drilling-milling thread-range tool. At the same time, mass production line, against the use of technology requires the development of special tools, tool or a smart composite tool, improve processing efficiency and accuracy and reduced investment. In the high-speed cutting conditions, and some special tools can be part of the processing time to the original 1 / 10 below, results are quite remarkable. HSC has a lot of advantages such as : a large number of materials required resection of the workpiece with ultrafine, thin structure of the workpiece, Traditionally, the need to spend very long hours for processing mobile workpiece and the design of rapid change, short product life cycle of the workpiece, able to demonstrate high-speed cutting brought advantages.中文译文高速切削加工的发展及需求高速切削加工是当代先进制造技术的重要组成部分,拥有高效率、高精度及高表面质量等特征。
机械外文翻译中英文

附录附录1英文原文Rolling Contact BearingsThe concern of a machine designer with ball and roller bearings is fivefold as follows:(a) life in relation to load; (b) stiffness,ie.deflections under load; (c) friction; (d) wear; (e) noise. For moderate loads and speeds the correct selection of a standard bearing on the basis of a load rating will become important where loads are high,although this is usually of less magnitude than that of the shafts or other components associated with the bearing. Where speeds are high special cooling arrangements become necessary which may increase fricitional drag. Wear is primarily associated with the introduction of contaminants,and sealing arrangements must be chosen with regard to the hostility of the environment.Because the high quality and low price of ball and roller bearing depends on quantity production,the task of the machine designer becomes one of selection rather than design. Rolling-contact bearings are generally made with steel which is through-hardened to about 900HV,although in many mechanisms special races are not provided and the interacting surfaces are hardened to about 600HV. It is not surprising that,owing to the high stresses involved,a predominant form of failure should be metal fatigue, and a good deal of work is based on accept values of life and it is general practice in bearing industry to define the load capacity of the bearing as that value below which 90 percent of a batch will exceed life of one million revolutions.Notwithstanding the fact that responsibility for basic design of ball and roller bearings rests with the bearing manufacturer, the machine designer must form a correct appreciation of the duty to be performed by the bearing and be concerned not only with bearing selection but with the conditions for correct installation.The fit of the bearing races onto the shaft or onto the housings is of critical importance because of their combined effect on the internal clearance of the bearing as well as preserving the desired degree of interference fit. Inadequate interference can induce serious trouble from fretting corrosion. The inner race is frequently located axially by against a shoulder. A radius at this point is essential for the avoidance of stress concentration and ball races are provided with a radius or chamfer to follow space for this.Where life is not the determining factor in design, it is usual to determine maximum loadingby the amount to which a bearing will deflect under load. Thus the concept of "static load-carrying capacity" is understood to mean the load that can be applied to a bearing, which is either stationary or subject to slight swiveling motions, without impairing its running qualities for subsequent rotational motion. This has been determined by practical experience as the load which when applied to a bearing results in a total deformation of 0.0025mm for a ball 25mm in diameter.The successful functioning of many bearings depends upon providing them with adequate protection against their environment, and in some circumstances the environment must be protected from lubricants or products of deterioration of the bearing design. Moreover, seals which are applied to moving parts for any purpose are of interest to tribologists because they are components of bearing systems and can only be designed satisfactorily on basis of the appropriate bearing theory.Notwithstanding their importance, the amount of research effort that has been devoted to the understanding of the behavior of seals has been small when compared with that devoted to other aspects of bearing technology.LathesLathes are widely used in industry to produce all kinds of machined parts. Some are general purpose machines, and others are used to perform highly specialized operations.Engine lathesEngine lathes, of course, are general-purpose machine used in production and maintenance shop all over the the world. Sized ranger from small bench models to huge heavy duty pieces of equipment. Many of the larger lathes come equipped with attachments not commonly found in the ordinary shop, such as automatic shop for the carriage.Tracer or Duplicating LathesThe tracer or duplicating lathe is designed o produce irregularly shaped parts automatically. The basic operation of this lathe is as fallows. A template of either a flat or three-dimensional shape is placed in a holder. A guide or pointer then moves along this shape and its movement controls that of the cutting tool. The duplication may include a square or tapered shoulder, grooves, tapers, and contours. Work such as motor shafts, spindles, pistons, rods, car axles, turbine shafts, and a variety of other objects can be turned using this type of lathe.Turret LathesWhen machining a complex workpiece on a general-purpose lathe, a great deal of time isspent changing and adjusting the several tools that are needed to complete the work. One of the first adaptations of the engine lathe which made it suitable to mass production was the addition of multi-tool in place of the tailstock. Although most turrets have six stations, some have as many as eight.High-production turret lathes are very complicated machines with a wide variety of power accessories. The principal feature of all turret lathes, however, is that the tools can perform a consecutive serials of operations in proper sequence. Once the tools have been set and adjusted, little skill is require to run out duplicate parts.Automatic Screw MachineScrew machines are similar in construction to turret lathes, except that their heads are designed to hold and feed long bars of stock. Otherwise, their is little different between them. Both are designed for multiple tooling, and both have adaptations for identical work. Originally, the turret lathe was designed as a chucking lathe for machining small casting, forgings, and irregularly shaped workpieces.The first screw machines were designed to feed bar stock and wire used in making small screw parts. Today, however, the turret lathe is frequently used with a collect attachment, and the automatic screw machine can be equipped with a chuck to hold castings.The single-spindle automatic screw machine, as its name implies, machines work on only one bar of stock at a time. A bar 16 to 20 feet long is feed through the headstock spindle and is held firmly by a collect. The machining operations are done by cutting tools mounted on the cross slide. When the machine is in operation, the spindle and the stock are rotated at selected speeds for different operations. If required, rapid reversal of spindle direction is also possible.In the single-spindle automatic screw machine, a specific length of stock is automatically fed through the spindle to a machining area. At this point, the turret and cross slide move into position and automatically perform whatever operations are required. After the machined piece is cut off, stock is again fed into the machining area and the entire cycle is repeated.Multiple-spindle automatic screw machines have from four to eight spindles located around a spindle carrier. Long bars of stock, supported at the rear of the machine,pass though these hollow spindles and are gripped by collects. With the single spindle machines, the turret indexes around the spindle. When one tool on the turret is working, the others are not. With a multiple spindle machine, however, the spindle itself index. Thus the bars of stock are carried to the various end working and side working tools. Each tool operates in only one position, but tollsoperate simultaneously. Therefore, four to eight workpieces can be machined at the same time.Vertical Turret LathesA vertical turret is basically a turret lathe that has been stood on its headstock end. It is designed to perform a variety of turning operations. It consists of a turret, a revolving table, and a side head with a square turret for holding additional tools. Operations performed by any of the tools mounted on the turret or side head can be controlled through the use of stops.Machining CentersMany of today's more sophisticated lathes are called machining centers since they are capable of performing, in addition to the normal turning operations, certain milling and drilling operations. Basically, a machining center can be thought of as being a combination turret lathe and milling machine. Additional features are sometimes included by the versatility of their machines.Numerical ControlOne of the most fundamental concepts in the area of advanced manufacturing technologies is numerical control(NC). Prior to the advent of NC, all machine tools were manually operated and controlled. Among the many limitations associated with manual control machine tools, perhaps none is more prominent than limitation of operator skills. With manual control, the quality of the product is directly related to and limited to the skills of the operator. Numerical control represents the first major step away from human control of machine tools.Numerical control means the control of machine tools and other manufacturing systems through the use of prerecorded, written symbolic instructions. Rather than operating a machine tool, an NC technician tool to be numerically controlled, it must be interfaced with a device for accepting and decoding the programmed instructions, known as a reader.Numerical control was developed to overcome the limitation of human operators, and it has done so. Numerical control machines are more accurate than manually operated machines, they can produce parts more uniformly, they are faster, and the long-run tooling costs are lower. The development of NC led to the development of several other innovations in manufacturing technology:1.Electrical discharge machining.ser cutting.3. Electron beam welding.Numerical control has also made machines tools more versatile than their manually operated predecessors. An NC machine tool can automatically produce a wide variety of parts, each involving an assortment of widely varied and complex machining processes. Numerical control has allowed manufacturers to undertake the production of products that would not have been feasible from an economic perspective using manually controlled machine tools and processes.Like so many advanced technologies, NC was born in the laboratories of the Masschusetts Institute of Technology. The concept of NC was developed in early 1950s with funding provided by the U.S.Air force. In its earliest stages, NC machines were able to make straight cuts efficiently and effectively.However,curved paths were a problem because the machine tool had to be programmed to undertake a series of horizontal and vertical steps to produce a curve. The shorter is straight lines making up the steps, the smoother is the curve. Each line segment in the steps had to be calculated.This problem led to the development in 1959 of the Automatically Programmed Tools(APT) language. This is a special programming language for NC that uses statements similar to English language to define the part geometry, describe the cutting tool configuration, and specify the necessary motions. The development of the APT language was a major step forward in the further development of NC technology. The original NC systems were vastly different from those used today. The machines had hardwired logic circuits. This instructional programs were written on punched paper, which was later to be replaced by magnetic plastic tape. A tape reader was used to interpret the instructions written on the tape for the machine. Together, all of this represented a giant step forward in the control of machine tools. However, there were a number of problems with NC at this point in its development.A major problem wad the fragility of the punched paper tape medium. It was common for the paper tape containing the programmed instructions to break or tear during a machining process. This problem was exacerbated by the fact that each programmed instructions had to be return through the reader. If it was necessary to produce 100 copies of a given part,it was also necessary to run the paper tape through the reader 100 separate times. Fragile paper tapes simply could not withstand the rigors of a shop floor environment and this kind of repeated use.This led to the development of a special magnetic plastic tape. Whereas the paper tape carried the programmed instructions as a series of holes punched in the tape, the plastic tape carried the instructions as a series of magnetic dots. The plastic tape was much stronger than thepaper taps, which solved the problem of frequent tearing and breakage. However, it still left two other problems.The most important of these was that it was difficult or impossible to change the instructions entered on the tape. To make even the most minor adjustments in a program of instructions, it necessary to interrupt machining operations and make a new tape. It was also still necessary to run the tape through the reader as many times as there were parts to be produced. Fortunately, computer technology became a reality and soon solved the problem of NC associated with punched paper and plastic tape.The development of a concept known as direct numerical control(DNC)solved the paper and plastic tape problems associated with numerical control by simply eliminating tape as the medium for carrying the programmed instructions. In direct numerical control machine tools are tied, via a data transmission link, to a host computer. Programs for operating the machine tools are stored in the host computer and fed to the machine tool as needed via the data transmission linkage. Direct numerical control represented a major step forward over punched tape and plastic tape. However, it is subject to the same limitations as all technologies that depend o a host computer. When the lost computer goes down, the machine tools also experience downtime. This problem led to the development of computer numerical control.The development of the microprocessor allowed for the development of programmable logic controllers(PNC)and microcomputer. These two technologies allowed for the development of computer numerical control(CNC). With CNC, each machine tool has a PLC or a microcomputer that serves the same purpose. This allows programs to be input and stored at each individual machine tool. It also allows programs to be developed off-line and download at the individual machine tool. CNC solved the problems associated with downtime of the host computer, but it introduced another known as data management. The same program might be loaded on ten different being solved by local area networks that connect microcomputer for better data management.CNC machine tool feed motion systems CNC machine tool feed motion systems, especially to the outline of the control of movement into the system, must be addressed to the movement into the position and velocity at the same time the realization of two aspects of automatic control, as compared with the general machine tools, require more feed system high positioning accuracy and good dynamic response.A typical closed-loop control of CNC machine tool feed system, usually by comparing the location of amplification unit, drive unit, mechanical transmission components, such as feedbackand testing of several parts. Here as mechanical gear-driven source refers to the movement of the rotary table into a linear motion of the entire mechanical transmission chain, including the deceleration device, turning the lead screw nut become mobile and vice-oriented components and so on. To ensure that the CNC machine tool feed drive system, precision, sensitivity and stability, the design of the mechanical parts of the general requirement is to eliminate the gap, reducing friction, reducing the movement of inertia to improve the transmission accuracy and stiffness. In addition, the feeding system load changes in the larger, demanding response characteristics, so for the stiffness, inertia matching the requirements are very high.Linear Roller GuidesIn order to meet these requirements, the use of CNC machine tools in general low-friction transmission vice, such as anti-friction sliding rail, rail rolling and hydrostatic guideways, ball screws, etc.; transmission components to ensure accuracy, the use of pre-rational, the form of a reasonable support to enhance the stiffness of transmission; deceleration than the best choice to improve the resolution of machine tools and systems converted to the driveshaft on the reduction of inertia; as far as possible the elimination of drive space and reduce dead-zone inverse error and improve displacement precision.Linear Roller Guides outstanding advantage is seamless, and can impose pre-compression. By the rail body, the slider, ball, cage, end caps and so on. Also known as linear rolling guide unit. Use a fixed guide body without moving parts, the slider fixed on the moving parts. When the slider moves along the rail body, ball and slider in the guide of the arc between the straight and through the rolling bed cover of Rolling Road, from the work load to non-work load, and then rolling back work load, constant circulation, so as to guide and move the slider between the rolling into a ball.附录2中文翻译滚动轴承对于球轴承和滚子轴承,一个机械设计人员应该考虑下面五个方面:(a)寿命与载荷关系;(b)刚度,也就是在载荷作用下的变形;(c)摩擦;(d)磨损;(e)噪声。
机械外文翻译中英文

翻译:英文原文Definitions and Terminology of VibrationvibrationAll matter-solid, liquid and gaseous-is capable of vibration, e.g. vibration of gases occurs in tail ducts of jet engines causing troublesome noise and sometimes fatigue cracks in the metal. Vibration in liquids is almost always longitudinal and can cause large forces because of the low compressibility of liquids, e.g. popes conveying water can be subjected to high inertia forces (or “water hammer”) when a valve or tap is suddenly closed. Excitation forces caused, say by changes in flow of fluids orout-of-balance rotating or reciprocating parts, can often be reduced by attention to design and manufacturing details. Atypical machine has many moving parts, each of which is a potential source of vibration or shock-excitation. Designers face the problem of compromising between an acceptable amount of vibration and noise, and costs involved in reducing excitation.The mechanical vibrations dealt with are either excited by steady harmonic forces ( i. e. obeying sine and cosine laws in cases of forced vibrations ) or, after an initial disturbance, by no external force apart from gravitational force called weight ( i.e. in cases of natural or free vibrations). Harmonic vibrations are said to be “simple” if there is only one frequency as represented diagrammatically by a sine or cosine wave of displacement against time.Vibration of a body or material is periodic change in position or displacement from a static equilibrium position. Associated with vibration are the interrelated physical quantities of acceleration, velocity and displacement-e. g. an unbalanced force causes acceleration (a = F/m ) in a system which, by resisting, induces vibration as a response. We shall see that vibratory or oscillatory motion may be classified broadly as (a) transient; (b) continuing or steady-state; and (c) random.Transient Vibrations die away and are usually associated with irregulardisturbances, e. g. shock or impact forces, rolling loads over bridges, cars driven over pot holes-i. e. forces which do not repeat at regular intervals. Although transients are temporary components of vibrational motion, they can cause large amplitudes initially and consequent high stress but, in many cases, they are of short duration and can be ignored leaving only steady-state vibrations to be considered.Steady-State Vibrations are often associated with the continuous operation of machinery and, although periodic, are not necessarily harmonic or sinusoidal. Since vibrations require energy to produce them, they reduce the efficiency of machines and mechanisms because of dissipation of energy, e. g. by friction and consequentheat-transfer to surroundings, sound waves and noise, stress waves through frames and foundations, etc. Thus, steady-state vibrations always require a continuous energy input to maintain them.Random Vibration is the term used for vibration which is not periodic, i. e. has no made clear-several of which are probably known to science students already.Period, Cycle, Frequency and Amplitude A steady-state mechanical vibration is the motion of a system repeated after an interval of time known as the period. The motion completed in any one period of time is called a cycle. The number of cycles per unit of time is called the frequency. The maximum displacement of any part of the system from its static-equilibrium position is the amplitude of the vibration of that part-the total travel being twice the amplitude. Thus, “amplitude” is not synonymous with “displacement” but is the maximum value of the displacement from the static-equilibrium position.Natural and Forced Vibration A natural vibration occurs without any external force except gravity, and normally arises when an elastic system is displaced from a position of stable equilibrium and released, i. e. natural vibration occurs under the action of restoring forces inherent in an elastic system, and natural frequency is a property of he system.A forced vibration takes place under the excitation of an external force (or externally applied oscillatory disturbance) which is usually a function of time, e. g.in unbalanced rotating parts, imperfections in manufacture of gears and drives. The frequency of forced vibration is that of the exciting or impressed force, i. e. the forcing frequency is an arbitrary quantity independent of the natural frequency of the system.Resonance Resonance describes the condition of maximum amplitude. It occurs when the frequency of an impressed force coincides with, or is near to a natural frequency of the system. In this critical condition, dangerously large amplitudes and stresses may occur in mechanical systems but, electrically, radio and television receivers are designed to respond to resonant frequencies. The calculation or estimation of natural frequencies is, therefore, of great importance in all types of vibrating and oscillating systems. When resonance occurs in rotating shafts and spindles, the speed of rotation is known as the critical speed. Hence, the prediction and correction or avoidance3 of a resonant condition in mechanisms is of vital importance since, in the absence of damping or other amplitude-limiting devices, resonance is the condition at which a system gives an infinite response to a finite excitation.Damping Damping is the dissipation of energy from a vibrating system, and thus prevents excessive response. It is observed that a natural vibration diminishes in amplitude with time and, hence, eventually ceases owing to some restraining or damping influence. Thus if a vibration is to be sustained, the energy dissipated by damping must be replaced from an external source.The dissipation is related in some way to the relative motion between the components or elements of the system, and is caused by frictional resistance of some sort, e.g. in structures, internal friction in material, and external friction caused by air or fluid resistance called “viscous” damping if the drag force is assumed proportional to the relative velocity between moving parts. One device assumed to give viscous damping is the “dashpot” which is a loosely fitting piston in a cylinder so that fluid can flow from one side of the piston to the other through the annular clearance space.A dashpot cannot store energy but can only dissipate it.Basic Machining Operations and Machine ToolsBasic Machining OperationsMachine tools have evolved from the early foot-powered lathes of the Egyptians and John Wilkinson’s boring mill. They are designed to provide rigid support for both the workpiece and the cutting tool and can precisely control their relative positions and the velocity of the tool with respect to the workpiece. Basically, in metal cutting, a sharpened wedge-shaped tool removes a rather narrow strip of metal from the surface of a ductile workpiece in the form of a severely deformed chip. The chip is a waste product that is comsiderably shorter than the workpiece from which it came but woth a corresponding increase in thickness of the uncut chip. The geometrical shape of the machine surface depedns on the shape of the tool and its path during the machinig operation.Most machining operations produce parts of differing geometry. If a rough cylindrical workpiece revolves about a central axis and the tool penetrates beneath its surface and travels parallel to the center of rotation, a surface of revolution is producedand the operation is called turning. If a hollow tube is machined on the inside in a similar manner, the operation is called boring. Producing an external conical surface of uniformly varying diameter is called taper turning. If the tool point travels in a path of varying radius,a contoured surface like that of a bowling pin a can be produced; or, if the piece is short enough and the support is sufficiently rigid, a contoured surface could be produced by feeding a shaped tool normal to the axis of rotation. Short tapered or cylindrical surfaces could also be contour formed.Flat or plane surfaces are frequently required. The can be generated by adial turning or facing, in which the tool point moves normal to the axis of rotation. In other cases, it is more convenient to hold the workpiece steady and reciprocate the tool across it in a series of straight-line cuts with a crosswise feed increment before each cutting stroke. This operation is called planing and is carried out on a shaper. For larger pieces it is easier to keep the tool stationary and draw the workpiece under it as inplaning. The tool is fed at each reciprocation. Contoured surfaces can be produced by using shaped tools.Multiple-edged tools can also be used. Drilling uses a twin-edged fluted tool for holes with depths up to 5 10times the drill diameter. Whether the dril turns or the workpiece rotates, relative motion between the cutting edge and the workpiece is the important factor. In milling operations a rotary cutter with a number of cutting edges engages the workpiecem which moves slowly with respect to the cutter. Plane or contoured surfaces may be produced, depending on the geometry of the cutter and the type of feed. Horizontal or vertical axes of rotation ma be used, and the feed of the workpiece may be in any of the three coordinate directions.Basic Machine ToolsMachine tools are used to produce a part of a specified geometrical shape and precise size by removing metal from a ductile materila in the form of chips. The latter are a waste product and vary from long continuous ribbons of a ductile material such as steel, which are undesirable from a disposal point of view, to easily handled well-broken chips resulting from cast iron. Machine tools perform five basic metal-removal processes: turning, planing, drilling, milling, and frinding. All other metal-removal processes are modifications of these five basic processes. For example, boring is internal turning;reaming,tapping, and counterboring modify drilled holes and are related to drilling; hobbing and gear cutting are fundamentally milling operations; hack sawong and broaching are a form of planing and honing; lapping, superfinishing, polishing, and buffing are avariants of grinding or abrasive removal operations. Therefore, there are only four types of basic machine tools, which use cutting tools of specific controllable feometry: thes, 2.planers, 3.drilling machines, and ling machines. The frinding process forms chips, but the geometry of the barasive grain is uncontrollable.The amount and rate of material removed by the various machining processes may be large, as in heavy truning operations, or extremely small, as in lapping or superfinishing operations where only the high spots of a surface are removed.A machine tool performs three major functions: 1.it rigidly supports the workpiece orits holder and the cutting tool; 2. it provedes relative motion between the workpiece and the cutting tools; 3. it provides a range of feeds and speeds usually ranging from 4 to 32 choices in each case.Speed and Feeds in MachiningSpeeds feeds, and depth of cut are the three major variables for economical machining. Other variables are the work and tool materials, coolant and geometry of the cutting tool. The rate of metal removal and power required for machining depend upon these variables.The depth of cut, feed, and cutting speed are machine settings that must be established in any metal-cutting operation. They all affect the forces, the power, and the rate of metal removal. They can be defined by comparing them to the needle and record of a phonograph. The cutting speed is represented by the velocity of the record surface relative to the needle in the tone arm at any instant. Feed is represented by the advance the needle radially inward per revolution, or is the difference in position between two adjacent grooves.Turning on Lathe CentersThe basic operations performed on an engine lathe are illustrated in Fig. Those operations performed on extemal surfaces with a single point cutting tool are called turning. Except for drilling, reaming, and tapping, the operations on intermal surfaces are also performed by a single point cutting tool.All machining operations, including turning and boring, can be classified as roughing, finishing, or semi-finishing. The objective of a roughing ooperation is to remove the bulk of the material sa repidly and as efficiently as possible, while leaving a small amount of material on the work-piece for the finishing operation. Finishing operations are performed to btain the final size, shape, and surface finish on the workpiece. Sometimes a semi-finishing operation will precede the finishing operation to leave a small predetermined and uniform amount of stoxd on the work-piece to be removed by the finishing operation.Generally, longer workpieces are turned while supported on one or two lathe centers. Cone shaped holes, called center holes, which fit the lathe centers are drilled in the ends of the workpiece-usually along the axis of the cylindrical part. The end of the workpiece adjacent to the tailstock is always supported by a tailstock center, while the end near the headstock may be supported by a headstock cener or held in a chuck. The headstock end of the workpiece may be held in a four-jar chuck, or in a collet type chuck. This method holds the workpiece firmly and transfers the power to the workpiece smoothly; the additional support to the workpiece priovided by the chuck lessens the tendency for chatter to occur when cutting. Precise results can be obtained with this method if care is taken to hold the workpiece accurately in the chuck.Very precise results can be obtained by supporting the workpiece between two centers.A lathe dog is clamped to the workpiece; together they are driven by a driver p;ate mounted on the spindle nose. One end of the workpiece is machined; then the workpiece can be turned around in the lathe to machine the other end. The center holes in the workpiece serve as precise locating surfaces as well as bearing surfaces to carry the weight of the workpiece and to resist the xutting forces. After the workpiece has been removed from the lathe for any reason, the center holes will accurately align the workpiece back in the lathe or in another lathe,or in a cylindrical grinding machine. The workpiece must never be held at the headstock end by both a chuck and a lathe center. While at first thought this seems like a quick method of aligning the workpiece in the chuck, this must not be done because it is not possible to press evenly with the jaws against the workpiece while it is also supported by the center. The alignment provided by the center will not be maintained and the pressure of the jaws may damage the center hole, the lathe center,and prehaps even the lathe spindle. Compensatng or floating jaw chucks used almost exclusively on high production work provice an exception to the statements made above. These chucks are really work drivers and cannot be used for the same purpose as ordinary three or four=jaw chucks. While very large diameter workpieces are sometimes mounted on two centers, they are preferably held at the headstock end by faceplate jaes to obtain the smooth power transmission; moreover, large lathe dogs that are adequate to transmit the power notgenerally available, although they can be maed as a special. Faceplate jaws are like chuck jaws except that thet are mounted on a faceplate, which has less overhang from the spindle bearings than a large chuck would have.BoringThe boring operation is generally performed in two steps; namely, rough boring and finish boring. The objective of the rough-boring operation is to remove the excess metal rapidly and efficiently, and the objective of the finish-boring operation is to obtain the desired size, surface finish, and location of the hole. The size of the hole is obtained by using the trial-cut procedure. The diameter of the hole can be measured with inside calipers and outside micrometer calipers. Basic Measuring Insteruments, or inside micrometer calipers can be used to measure the diameter directly.Cored holes and drilled holes are sometimes eccentric wwith respect to the rotation of the lathe. When the boring tool enters the work, the boring bar will take a deeper cut on one side of the hole than on the other, and will deflect more when taking this deeper cut,with the result that the bored hole will not be concentric with the rotation of the work. This effect is corrected by taking several cuts through the hole using a shallow depth of cut. Each succeeding shallow cut causes the resulting hole to be more concentric than it was with the previous cut. Before the final, finish cut is taken, the hole should be concentric with the rotation of the work in order to make certain that the finished hole will be accurately located.Shoulders, grooves, contours, tapers, and threads are bored inside of holes. Internal grooves are cut using a tool that is similar to an external grooving tool. The procedure for boring internal shoulders is very similar to the procedure for turning rge shoulders are faced with the boring tool positioned with the nose leading, and using the cross slide to feed the tool. Internal contours can be machined using a tracing attachment on a lathe. The tracing attachment is mounted on the cross slide and the stylus follows the outline of the master profile plate. This causes the cutting tool to move in a path corresponding to the profile of the master profile plate.Thus, the profile on the master profile plate is reproduced inside the bore. The master profile plate is accurately mounted on a special slide which can be precisely adjusted in two dirctions, in two directionsm, in order to align the cutting tool in the correct relationship to the work. This lathe has a cam-lick type of spindle nose which permits it to take a cut when rotating in either direction. Normal turning cuts are taken with the spindle rotating counterclockwise. Thie boring cut is taken with the spindle revolving in a clockwise direction, or “backwards”. This permits the boring cut to be taken on the “back side” of the bore which is easier to see from the operator’sposition in front of the lathe. This should not be done on lathes having a threaded spindle nose because the cutting force will tend to unscrew the chuck.中文翻译振动的定义和术语振动所有的物质---固体,液体和气体-----都能够振动,例如,在喷气发动机尾部导管中产生的气体振动会发出令人讨厌的噪声,而且有时还会使金属产生疲劳裂缝。
机械外文翻译中英文

英文资料Limits and TolerancesThe breakage of the machine spare parts ,generally always from the surface layer beginning of .The function of the product ,particularly its credibility and durable ,be decided by the quantity of spare parts surface layer to a large extent. Purpose that studies the machine to process the surface quantity be for control the machine process medium various craft factor to process the surface quantity influence of regulation, in order to make use of these regulations to control to process the process, end attain to improve the surface quantity, the exaltation product use the function of purpose .The machine processes the surface quantity to use the influence of the function to the machine(A) The surface quantity to bear to whet the sexual influence1.Rough degree of surface to bear to whet the sexual influenceA just process vice-of two contact surfaces of good friction, the first stage is rough only in the surface of the peak department contact ,the actual contact area is much smaller than theoretical contact area, in contact with each other the peak of the units have very great stress, to produce actual contact with the surface area of plastic deformation, deformation and peak between the Department of shear failure, causing serious wear.Parts wear may generally be divided into three stages, the initial stage of wear and tear, normal wear and tear all of a sudden intense phase of stage wear.Parts of the surface roughness of the surface wear big impact. In general the smaller the value of surface roughness, wear better. However, surface roughness value is too small, lubricants difficult to store, contact between the adhesive-prone elements, wear it to increase. Therefore, the surface roughness of a best value, the value and parts of the work related to increased work load, the initial wear increased, the best rough surface is also increased.2.Cold Working hardening the surface of the wear resistanceProcessing the Cold Work hardening the surface of the friction surface layer of metal microhardness increase, it will generally improve the wear resistance. Cold Working but not a higher degree of hardening, wear resistance for the better, because too much will lead to hardening of the Cold Working excessive loose organization ofmetal, even a crack and peeling off the surface of the metal, declined to wear resistance.(B)The surface quality of the impact of fatigue strengthMetal hand alternating loads of fatigue after the damage occurred in parts often Chilled layer below the surface and, therefore parts of the surface quality of fatigue very influential.1.Surface roughness on the impact of fatigue strengthIn alternating load, the surface roughness of the Au-site easily lead to stress concentration, a fatigue crack, the higher the value of surface roughness, surface traces of Yu Shen Wen, Wen at the end of the radius smaller, anti-fatigue damage at the end of the more capacity Worse.2.Residual stress, fatigue Cold Work hardening of the impactResidual stress on the impact of large parts fatigue. Surface layer of residual stress fatigue crack will expand and accelerate the fatigue damage the surface layer and the residual stress can prevent fatigue crack growth, delaying the formation of fatigue damage.(C)The surface quality of the corrosion resistance of the impactParts of the corrosion resistance to a large extent depends on the surface roughness. The higher the value of surface roughness, Au Valley accumulate on the more corrosive substances. Corrosion resistance of the more worse.Surface layer of residual stress will produce stress corrosion cracking, lower parts of the wear-resistance, and the residual stress is to prevent stress corrosion cracking.(D) The surface quality with qualityRough surface will affect the value of the size of the co-ordination with the surface quality. The gap with rough value will increase wear and tear, increased space, with the requirements of the destruction of nature. For Fit, the assembly part of the process of convex surface-crowded peak times, the actual reduction of the surplus and reduce the support of the connection between the strength.DimensioningThe design of a machine includes many factors other than those of determining the loads and stresses and selecting the proper materials. Before construction or manufacture can begin, it is necessary to have complete assembly and detail drawings to convey all necessary information to the shop men. The designer frequently is called upon to check the drawings before they are sent to the shop. Much experience andfamiliarity with manufacturing processes are needed before one can become conversant with all phases of production drawings.Drawings should be carefully checked to see that the dimensioning is done in a manner that will be most convenient and understandable to the production departments. It is obvious that a drawing should be made in such a way that it has one and only one interpretation. In particular, shop personnel should not be required to make trigonometric or other involved calculations before the production machines can be set up.Dimensioning is an involved subject and long experience is required for its mastery.Tolerances must be placed on the dimensions of a drawing to limit the permissible variations in size because it is impossible to manufacture a part exactly to a given dimension. Although small tolerances give higher quality work and a better operating mechanism, the cost of manufacture increases rapidly as the tolerances are reduced, as indicated by the typical curve of Fig 14.1. It is therefore important that the tolerances be specified at the largest values that the operating or functional considerations permit.Tolerances may be either unilateral or bilateral. In unilateral dimensioning, one tolerance is zero, and all the variations are given by the other tolerance. In bilateral dimensioning, a mean dimension is used which extends to the midpoint of the tolerance zone with equal plus and minus variations extending each way from this dimension.The development of production processes for large-volume manufacture at low cost has been largely dependent upon interchangeability of component parts. Thus the designer must determine both the proper tolerances for the individual parts, The manner of placing tolerances on drawings depends somewhat on the kind of product or type of manufacturing process. If the tolerance on a dimension is not specifically stated, the drawing should contain a blanket note which gives the value of the tolerance for such dimensions. However, some companies do not use blanket notes on the supposition that if each dimension is considered individually, wider tolerance than those called for in the note could probably be specified. In any event it is very important that a drawing be free from ambiguities and be subject only to a single interpretation.Dimension and ToleranceIn dimensioning a drawing, the numbers placed in the dimension lines represent dimension that are only approximate and do not represent any degree of accuracy unless so stated by the designer.To specify a degree of accuracy, it is necessary to add tolerance figures to the dimension. Tolerance is the amount of variation permitted in the part or the total variation allowed in a given dimension. A shaft might have a nominal size of 2.5 in. (63.5mm), but for practical reasons this figure could not be maintained in manufacturing without great cost. Hence, a certain tolerance would be added and , if a variation of ±0.003 in.(±0.08mm) could be permitted, the dimension would be stated 2.500±0.003(63.5±0.008mm).Dimensions given close tolerances mean that the part must fit properly with some other part. Both must be given tolerances in keeping with the allowance desired, the manufacturing processes available, and the minimum cost of production and assembly that will maximize profit. Generally speaking, the cost of a part goes up as the tolerance is decreased. If a part has several or more surfaces to be machined, the cost can be excessive when little deviation is allowed from the nominal size.Allowance, which is sometimes confused with tolerance, has an altogether different meaning.It is the minimum clearance space intended between mating parts and representsthe condition of tightest permissible fit. If a shaft, size 1.4980.0000.003+-, is to fit a hole ofsize 1.5000.0030.000+-, the minimum size hole is 1.500 and the maximum size shaft is 1.498.Thus the allowance is 0.002 and the maximum clearance is 0.008 as based on the minimum shaft size and maximum hole dimension.Tolerances may be either unilateral or bilateral. Unilateral tolerance means that any variation is made in only one direction from the nominal or basic dimension.Referring to the previous example, the hole is dimensioned 1.5000.0030.000+-, whichrepresents a unilateral tolerance. If the dimensions were given as 1.500±0.003, the tolerance would be bilateral; that is , it would vary both over and under the nominal dimension. The unilateral system permits changing the tolerance while still retaining the same allowance or type of fit. With the bilateral system, this is not possible without also changing the nominal size dimension of one or both of the two mating parts. In mass production, where mating parts must be interchangeable, unilateral tolerances are customary. To have an interference or fore fit between mating parts, the tolerances must be such as to create a zero or negative allowance.Tolerances Limits and FitsThe drawing must be a true and complete statement of the designer’s expr essed in such a way that the part is convenient to manufacture. Every dimension necessary to define the product must be stated once and repeated in different views. Dimensions relating to one particular feature, such as the position and size of hole, where possible, appear on the same view.There should be no more dimensions than are absolutely necessary, and no feature should be located by more than one dimension in any direction. It may be necessary occasionally to give an auxiliary dimension for reference, possibly for inspection. When this is so, the dimension should be enclosed in a bracket and marked for reference. Such dimensions are not governed by general tolerances.Dimensions that affect the function of the part should always be specified and not left as the sum or other dimensions. If this is not done, the total permissible variation on that dimension will form the sum or difference of the other dimensions and their tolerance, and this with result in these tolerances having to be made unnecessarily tight. The overall dimension should always appear.All dimensions must be governed by the general tolerance on the drawing unless otherwise stated. Usually, such a tolerance will be governed by the magnitude of the dimension. Specific tolerances must always be stated on dimensions affecting or interchangeability.A system of tolerances is necessary to allow for the variations in accuracy that are bound to occur during manufacture, and still provide for interchangeability and correct function of the part.A tolerance is the difference in a dimension in order to allow for unavoidable imperfections in workmanship. The tolerance range will depend on the accuracy of the manufacturing organization, the machining process and the magnitude of the dimension. The greater the tolerance range is disposed on both sides of the nominal dimension. A unilateral tolerance is one where the tolerance zone is on one side only of the nominal dimension, in which case the nominal dimension may from one of the limits.Limits are the extreme dimensions of the tolerance zone. For example, nominal dimension30mm tolerance 30.0230.000++ limits 30.02530.000Fits depend on the relationship between the tolerance zones of two mating parts,and may be broadly classified into a clearance fit with positive allowance, a transition fit where the allowance may be either positive or negative (clearance or interference) , an interference fit where the allowance is always negative.Type of Limits and FitsThe ISO system of Limits and Fits, widely used in a number of leading metric countries, is considerably more complex than the ANSI system.In this system, each part has a basic size. Each limit of part, high and sign being obtained by subtracting the basic size form the limit in question. The difference between the two limits of size of a part is called the tolerance, an absolute without sign.There are three classes of fits: 1) clearance fits, 2) transition fits ( the assembly may have either clearance or interference ), and 3) interference fits .Either a shaft-basis system or a hole-basis system may be used. For any given basic size, a range of tolerance and deviations may be specified with respect to be line of zero deviation, called the zero line. The tolerance is a function of the basic size and is designated by a number symbol, called the grade-thus the tolerance grade. The position of the tolerance with respect to the zero line also a function of the basic size-is indicated by a letter symbol(or two letter), a capital letter for holes and a lowercase letter for shafts. Thus the specification for a hole and shaft having a basic size of 45mm might be45H8/g7.Twenty standard grades of tolerance are provided, called IT 01,IT 0 ,IT 1-18, providing numerical values for each nominal diameter, in arbitrary steps up to 500mm (for example 0-3,3-6,6-10…, 400-500mm). The value of the tolerance unit, I, for grades 5-16 is=+0.0.001i DWhere i is in microns and D in millimeters.Standard shaft and hole deviations similarly are provided by sets of formulas, However, for practical, both tolerances and deviations are provided in three sets of rather complex tables. Additional tables gives the values for basic sizes above 500mm and for “Commonly Used Shafts and Holes” in two categories ---“General Purpose” and “Fine Mecbanisms and Horology”.中文翻译极限与误差机械零件的破坏,一般总是从表层开始的。
机械制造专业外文翻译-轴、联轴器和滚动轴承
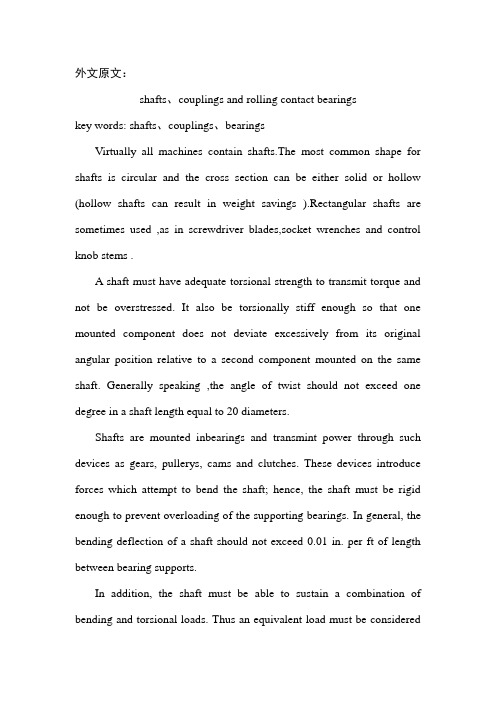
外文原文:shafts、couplings and rolling contact bearingskey words: shafts、couplings、bearingsVirtually all machines contain shafts.The most common shape for shafts is circular and the cross section can be either solid or hollow (hollow shafts can result in weight savings ).Rectangular shafts are sometimes used ,as in screwdriver blades,socket wrenches and control knob stems .A shaft must have adequate torsional strength to transmit torque and not be overstressed. It also be torsionally stiff enough so that one mounted component does not deviate excessively from its original angular position relative to a second component mounted on the same shaft. Generally speaking ,the angle of twist should not exceed one degree in a shaft length equal to 20 diameters.Shafts are mounted inbearings and transmint power through such devices as gears, pullerys, cams and clutches. These devices introduce forces which attempt to bend the shaft; hence, the shaft must be rigid enough to prevent overloading of the supporting bearings. In general, the bending deflection of a shaft should not exceed 0.01 in. per ft of length between bearing supports.In addition, the shaft must be able to sustain a combination of bending and torsional loads. Thus an equivalent load must be consideredwhich takes into account both torsion and bending. Also, the allowable stress must contain a factor of safety which includes fatigue, since torsional and bending stress reversals occur.For diameters less than 3 in. , the usual shaft material is cold-rolled ateel containing about 0.4 percent carbon. Shafts are either cold-rolled or forged in sizes from 3 in. to 5 in. ,shafts are forged and machined to size .Pleastic shafts are widely used for light load applications. One advantage of using plastic is safety in electrical applications ,since plastic is a poor conductor of electricity.Components such as gears and pulleys are mounted on shafts by means of key .The design of the key and the corresponding keyway in the shaft must be prperly evaluated. For example ,stress concentrations occur in shafts due to keyways ,and the material removed to form the keyway further weakens the shaft.If shafts are run at cirtical speeds ,severe vibrations can occur which can seriously damage a machine. It is important to know the magnitude of these critical speeds so that they can be avoided. As a general rule of thumb,the difference between the operating speed and the critical speed should be at least 20 percent .Another important aspect of shaft design is the method of directly connecting one shaft to another. This is accomplished by devices such as rigid and flexible couplings.A coupling is a device for connecting the eds of adjacent shafts. In machine construction, ouplings are used to effect a semipermanent connection between adjacent rotating shafts. The connection is permanent in the sense that it is not meant to be broken during the useful life of the machine, but it can be broken and restored in an emergency or when worn parts are replaced.There are several types of shaft couplings, their characteristics depend on the purpose for which they are used. If an exceptionally long shaft is required in a manufacturing plant or a propeller shaft on a ship, it is made in sections that are coupled together with rigid couplings. A common type of rigid coupling consists of two mating radial flanges(disks) that are cttached by key-driven hubs to the eds of adjacent shaft sections and bolted together through the flanges to form a rigid connection. Alignment of the connected shafts is usually effeted by means of a rabbet joint on the face of the flanges.In connecting shafts belonging to separate devices (such as an electric motor and a gearbox ),precise aligning of the shafts is difficult and a flexible coupling is used. This coupling connects theshafts in such a way as to minimize the harmful effects of shaft misalignment. Flexible couplings also permit the shafts to deflect under their separate systems of with one another. Flexible couplings can also serve to reduce the intensity of shock loads and vibrations transmitted from one shaft to another.Virtually all shafts contain rolling contact bearings.The concern of a machine designer with ball and roller bearings is fivefold as follows:(a) life in relation to load; (b) stiffness ,i.e. deflections under load; (c) friction;(d) wear; (e) noise. For moderate loads and speeds the correct selection of a standard bearing on the basis of load rating will usually secure satisfactory performance. The deflection of the bearing elements will become important where loads are high, although this is usuallyof less magnitude than that of the shafts or other components associated with the bearing. Where speeds are high special cooling arrangements become necessary which may increase frictional drag. Wear is primarily associated with the introduction of contaminants, and sealing arrangements must be chosen with regard the hostility of the environment.Because the high quality and low price of ball and roller bearings depends on quantity production, the task of the machine designer becomes one of selection rather than design. Rolling-contact bearings are generally made with ateel which is through-hardened toabout 900HV,although in many mechanisms special races are not provided and the interacting surfaces are hardened to about 600 HV. It is not surprising that, owing to the high stresses involved, a predominant form of failure should be metal fatigue, and a good deal of work is currently in progress intended to improve the reliability of this type of bearing. Design can bebased on accepted values of life and it is generral practice in the bearing industry to define the load capacity of the bearing as that value below which 90 lpercent of a batch will exceed a lift of ane million revolutions.Notwithstanding the fact that responsibility for the basic design of ball and roller bearings rests with the bearing manufacturer, the machine designer must form a correct appreciation of the duty to be performed by the bearing and be concerned not only with bearing selection but with the conditions for correct installation.The fit of the bearing races onto the shaft or onto the housings is of critical importance because of their combined effect on the internal clearance of the bearing as well as preserving the desired degree of interference fit. Inadequate interference can induce serious trouble from fretting corrosion. The inner race is frequently located axially by abutting against a shoulder. A radius at this point is essential for the avoidance of stress concentration and ball races are provides with a radius or chamfer to allow space for this .Where life is not the determining factor in design, it is usual to determine maximum loading by the amount towhich a bearing will deflect under load. Thus the concept of “static load-carrying capacity” is understood to mean the load that can be alpplied to a bearing, which is either stationary or subject to slight swiveling motions, without impairing its running qualities for subsequent rotational motion. This has beendetermined by practical experience as the load which when applied to a bearing results in a total deformation of the rolling element and raceway at any point of contact not exceeding 0.01 percent of the rolling-element diameter. This would correspond to a permanent deformation of 0.00025 mm for a ball 25mm in diameter.The successful functioning of many bearing depends upon providing them with adequate protection against their environment, and in some circumstances the enviroration of the bering surfaces. Achievement of the correct functioning of seals is an essential part of bearing design. Moreover, seals which are applied to moving parts for any purpose are of interest to tribologists because they are components of bearing systems and can only be designed satisfactorily on the basis of the approlpriate bearing theory. Notwithstanding their importance, the amount of research effort that has been devoted to the understanding of the understanding of the behavior of seals has been small when compared with that devoted to other aspects of bearing technology.References:1 Erickson.Belt and Application for Engineers.Marcel Dekker.Inc,19972 South,Mancuso.Mechanical Power Transmission Components.1994中文译文:轴、联轴器和滚动轴承关键词:轴、联轴器、轴承实际上,几乎所有的机器中都装有轴。
机械工程外文翻译
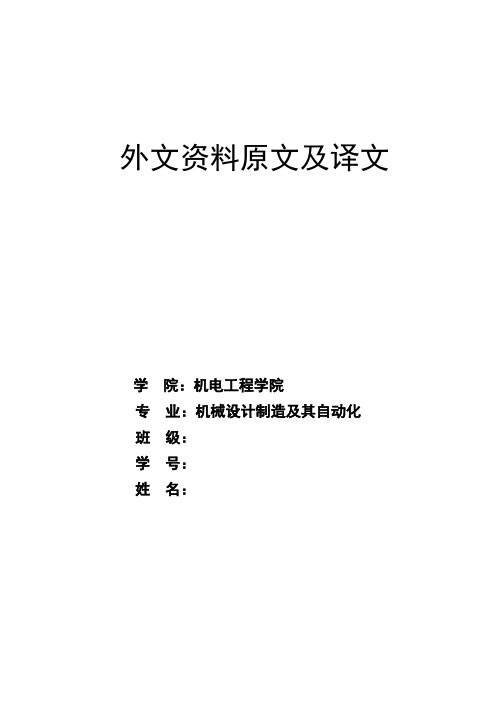
外文资料原文及译文学院:机电工程学院专业:机械设计制造及其自动化班级:学号:姓名:Mechanical engineering1.The porfile of mechanical engineeringEngingeering is a branch of mechanical engineerig,itstudies mechanical and power generation especially power and movement.2.The history of mechanical engineering18th century later periods,the steam engine invention hasprovided a main power fountainhead for the industrialrevolution,enormously impelled each kind of mechznicalbiting.Thus,an important branch of a new Engineering –separated from the civil engineering tools and machines on thebranch-developed together with Birmingham and the establishment of the Associantion of Mechanical Engineers in1847 had been officially recognized.The mechanicalengineering already mainly used in by trial and error methodmechanic application technological development intoprofessional engineer the scientific method of which in theresearch,the design and the realm of production used .From themost broad perspective,the demend continuously to enhance theefficiencey of mechanical engineers improve the quality of work,and asked him to accept the history of the high degreeof education and training.Machine operation to stress not onlyeconomic but also infrastructure costs to an absolute minimun.3.The field of mechanical engineeringThe commodity machinery development in the develop country,in the high level material life very great degree is decided each kind of which can realize in the mechanical engineering.Mechanical engineers unceasingly will invent the machine next life to produce the commodity,unceasingly will develop the accuracy and the complexity more and more high machine tools produces the machine.The main clues of the mechanical development is:In order to enhance the excellent in quality and reasonable in price produce to increase the precision as well as to reduce the production cost.This three requirements promoted the complex control system development.The most successful machine manufacture is its machine and the control system close fusion,whether such control system is essentially mechanical or electronic.The modernized car engin production transmission line(conveyer belt)is a series of complex productions craft mechanization very good example.The people are in the process of development in order to enable further automation of the production machinery ,the use of a computer to store and handle large volumes of data,the data is a multifunctional machine toolsnecessary for the production of spare parts.One of the objectives is to fully automated production workshop,three rotation,but only one officer per day to operate.The development of production for mechanical machinery must have adequate power supply.Steam engine first provided the heat to generate power using practical methods in the old human,wind and hydropower,an increase of engin .New mechanical engineering industry is one of the challenges faced by the initial increase thermal effciency and power,which is as big steam turbine and the development of joint steam boilers basically achieved.20th century,turbine generators to provide impetus has been sustained and rapid growth,while thermal efficiency is steady growth,and large power plants per kW capital consumption is also declining.Finally,mechanical engineers have nuclear energy.This requires the application of nuclear energy particularly high reliability and security, which requires solving many new rge power plants and the nuclear power plant control systems have become highly complex electroonics,fluid,electricity,water and mechanical parts networks All in all areas related to the mechanical engineers.Small internal combustion engine,both to the type (petrol and diesel machines)or rotary-type(gas turbines andMong Kerr machine),as well as their broad application in the field of transport should also due to mechanical enginerrs.Throughout the transport,both in the air and space,or in the terrestrial and marine,mechanial engineers created a variety of equipment and power devices to their increasing cooperation with electrical engineers,especially in the development of appropration control systems.Mechanical engineers in the development of military weapons technology and civil war ,needs a similar,though its purpose is to enhance rather than destroy their productivity.However.War needs a lot of resources to make the area of techonlogy,many have a far-reaching development in peacetime efficiency.Jet aircraft and nuclear reactors are well known examples.The Biological engineering,mechanical engineering biotechnology is a relatively new and different areas,it provides for the replacement of the machine or increase the body functions as well as for medical equipment.Artficial limbs have been developed and have such a strong movement and touch response function of the human body.In the development of artificial organ transplant is rapid,complex cardiac machines and similar equipment to enable increasingly complex surgery,and injuries and ill patients life functions can besustained.Some enviromental control mechanical engineers through the initial efforts to drainage or irrigation pumping to the land and to mine and ventilation to control the human environment.Modern refrigeration and air-conditioning plant commonaly used reverse heat engine,where the heat from the engine from cold places to more external heat.Many mechanical engineering products,as well as other leading technology development city have side effects on the environment,producing noise,water and air pollution caused,destroyed land and landscape.Improve productivity and diver too fast in the commodity,that the renewable natural forces keep pace.For mechanical engineers and others,environmental control is rapidly developing area,which includes a possible development and production of small quantities of pollutants machine sequnce,and the development of new equipment and teachnology has been to reduce and eliminate pollution.4.The role of mechanical engineeringThere are four generic mechanical engineers in common to the above all domains function.The 1st function is the understanding and the research mechanical science foundation.It includes the power and movement of therelationship dynamics For example,in the vibration and movement of the relationship;Automatic control;Study of the various forms of heart,energy,power relations between the thermodynamic;Fluidflows; Heat transfer; Lubricant;And material properties.The 2nd function will be conducts the research,the desing and the development,this function in turn attempts to carry on the essential change to satisfy current and the future needs.This not only calls for a clear understanding of mechanical science,and have to break down into basic elements of a complex system capacity.But also the need for synthetic and innovative inventions.The 3rd function is produces the product and the power,include plan,operation and maintenance.Its goal lies in the maintenance either enhances the enterprise or the organization longer-tern and survivabilaty prestige at the same time,produces the greatest value by the least investments and the consumption.The 4th function is mechanical engineer’s coordinated function,including the management,the consultation,as well as carries on the market marking in certain situation.In all these function,one kind unceasingly to use the science for a long time the method,but is not traditional orthe intuition method tendency,this is a mechanical engineering skill aspect which unceasingly grows.These new rationalization means typical names include:The operations research,the engineering economics,the logical law problem analysis(is called PABLA) However,creativity is not rationalization.As in other areas,in mechanical engineering, to take unexpected and important way to bring about a new capacity,still has a personal,marked characteristice.5.The design of mechanical engineeringThe design of mechanical is the design has the mechanical property the thing or the system,such as:the instrument and the measuring appliance in very many situations,the machine design must use the knowledge of discipline the and so on mathematics,materials science and mechanics.Mechanical engineering desgin includeing all mechanical desgin,but it was a study,because it also includes all the branches of mechsnical engineering,such as thermodynamics all hydrodynamics in the basic disciplines needed,in the mechanical engineering design of the initial stude or mechanical design.Design stages.The entire desgin process from start to finish,in the process,a demand that is designed for it and decided to do the start.After a lot of repetition,thefinal meet this demand by the end of the design procees and the plan.Design considerations.Sometimes in a system is to decide which parts needs intensity parts of geometric shapes and size an important factor in this context that we must consider that the intensity is an important factor in the design.When we use expression design considerations,we design parts that may affect the entire system design features.In the circumstances specified in the design,usually for a series of such functions must be taken into account.Howeever,to correct purposes,we should recognize that,in many cases the design of important design considerations are not calculated or test can determine the components or systems.Especially students,wheen in need to make important decisions in the design and conduct of any operation that can not be the case,they are often confused.These are not special,they occur every day,imagine,for example,a medical laboratory in the mechanical design,from marketing perspective,people have high expectations from the strength and relevance of impression.Thick,and heavy parts installed together:to produce a solid impression machines.And sometimes machinery and spare parts from the design style is the point and not the other point of view.Our purpose is to make those you do notbe misled to believe that every design decision will need reasonable mathematical methods.Manufacturing refers to the raw meterials into finished products in the enterprise.Create three distinct phases.They are:input,processing exprot.The first phase includes the production of all products in line with market needs essential.First there must be the demand for the product,the necessary materials,while also needs such as energy,time,human knowledge and technology resourcess . Finall,the need for funds to obtain all the other resources. Lose one stage after the second phase of the resources of the processes to be distributed.Processing of raw materials into finished products of these processes.To complete the design,based on the design,and then develop plans.Plan implemented through various production processes.Management of resources and processes to ensure efficiency and productivity.For example,we must carefully manage resources to ensure proper use of funds.Finally,people are talking about the product market was cast.Stage is the final stage of exporting finished or stage.Once finished just purchased,it must be delivered to the users.According to product performance,installation and may have to conduct furtherdebugging in addition,some products,especially those very complex products User training is necessary.6.The processes of materials and maunfacturingHere said engineering materials into two main categories:metals and non-ferrous,high-performance alloys and power metals.Non-metallic futher divided into plastice,synthetic rubber,composite materials and ceramics.It said the production proccess is divided into several major process,includingshape,forging,casting/ founding,heat treatment,fixed/connections ,measurement/ quality control and materal cutting.These processes can be further divide into each other’s craft.Various stages of the development of the manufacturing industry Over the years,the manufacturing process has four distinct stages of development, despite the overlap.These stages are:The first phase is artisanal,the second Phase is mechanization.The third phase is automation the forth Phase is integrated.When mankind initial processing of raw materials into finished products will be,they use manual processes.Each with their hands and what are the tools manuslly produced.This is totally integrated production take shape.A person needs indentification,collection materials,the design of a productto meet that demand,the production of such products and use it.From beginning to end,everything is focused on doing the work of the human ter in the industrial revolution introduced mechanized production process,people began to use machines to complete the work accomplished previously manual. This led to the specialization.Specialization in turn reduce the manufacture of integrated factors.In this stage of development,manufacturing workers can see their production as a whole represent a specific piece of the part of the production process.One can not say that their work is how to cope with the entire production process,or how they were loaded onto a production of parts finished.Development of manufacting processes is the next phase of the selection process automation.This is a computer-controlled machinery and processes.At this stage,automation island began to emerge in the workshop lane.Each island represents a clear production process or a group of processes.Although these automated isolated island within the island did raise the productivity of indivdual processes,but the overall productivity are often not change.This is because the island is not caught in other automated production process middle,but not synchronous with them .The ultimate result is the efficient working fast parkedthrough automated processes,but is part of the stagnation in wages down,causing bottlenecks.To better understand this problem,you can imagine the traffic in the peak driving a red light from the red Service Department to the next scene. Occasionally you will find a lot less cars,more than being slow-moving vehicles,but the results can be found by the next red light Brance.In short you real effect was to accelerate the speed of a red Department obstruction offset.If you and other drivers can change your speed and red light simultaneously.Will advance faster.Then,all cars will be consistent,sommth operation,the final everyone forward faster.In the workshop where the demand for stable synchronization of streamlined production,and promoted integration of manufacturing development.This is a still evolving technology.Fully integrated in the circumstances,is a computer-controllrd machinery and processing.integrated is completed through computer.For example in the preceding paragraph simulation problems,the computer will allow all road vehicles compatible with the change in red.So that everyone can steady traffic.Scientific analysis of movement,timing and mechanics of the disciplines is that it is composed of two pater:staticsand dynamics.Statics analyzed static system that is in the system,the time is not taken into account,research and analysis over time and dynamics of the system change.Dynameics from the two componets.Euler in 1775 will be the first time two different branches: Rigid body movement studies can conveniently divided into two parts:geometric and mechanics.The first part is without taking into account the reasons for the downward movement study rigid body from a designated location to another point of the movement,and must use the formula to reflect the actual,the formula would determine the rigid body every point position. Therefore,this study only on the geometry and,more specifically,on the entities from excision.Obviously,the first part of the school and was part of a mechanical separation from the principles of dynamics to study movement,which is more than the two parts together into a lot easier.Dynamics of the two parts are subsequently divided into two separate disciplines,kinematic and dynamics,a study of movement and the movement strength.Therefore,the primary issue is the design of mechanical systems understand its kinematic.Kinematic studies movement,rather than a study of its impact.In a more precise kinematic studies position,displacement,rotation,speed,velocity and acceleration of disciplines,for esample,or planets orbiting research campaing is a paradigm.In the above quotation content should be pay attention that the content of the Euler dynamics into kinematic and rigid body dynamics is based on the assumption that they are based on research.In this very important basis to allow for the treatment of two separate disciplines.For soft body,soft body shape and even their own soft objects in the campaign depends on the role of power in their possession.In such cases,should also study the power and movement,and therefore to a large extent the analysis of the increased complexity.Fortunately, despite the real machine parts may be involved are more or less the design of machines,usually with heavy material designed to bend down to the lowest parts.Therefore,when the kinematic analysis of the performance of machines,it is often assumed that bend is negligible,spare parts are hard,but when the load is known,in the end analysis engine,re-engineering parts to confirm this assnmption.机械工程1.机械工程简介机械工程是工程学的一个分支,它研究机械和动力的产,尤其是力和动力。
机械设计理论机械类设计外文翻译、中英文翻译
英文原文Machine design theoryThe machine design is through designs the new product or improves the old product to meet the human need the application technical science. It involves the project technology each domain, mainly studies the product the size, the shape and the detailed structure basic idea, but also must study the product the personnel which in aspect the and so on manufacture, sale and use question.Carries on each kind of machine design work to be usually called designs the personnel or machine design engineer. The machine design is a creative work. Project engineer not only must have the creativity in the work, but also must in aspect and so on mechanical drawing, kinematics, engineerig material, materials mechanics and machine manufacture technology has the deep elementary knowledge.If front sues, the machine design goal is the production can meet the human need the product. The invention, the discovery and technical knowledge itself certainly not necessarily can bring the advantage to the humanity, only has when they are applied can produce on the product the benefit. Thus, should realize to carries on before the design in a specific product, must first determine whether the people do need this kind of productMust regard as the machine design is the machine design personnel carries on using creative ability the product design, the system analysis and a formulation product manufacture technology good opportunity. Grasps the project elementary knowledge to have to memorize some data and the formula is more important than. The merely service data and the formula is insufficient to the completely decision which makes in a good design needs. On the other hand, should be earnest precisely carries on all operations. For example, even if places wrong a decimal point position, also can cause the correct design to turn wrongly.A good design personnel should dare to propose the new idea, moreover is willing to undertake the certain risk, when the new method is not suitable, use original method. Therefore, designs the personnel to have to have to have the patience, because spendsthe time and the endeavor certainly cannot guarantee brings successfully. A brand-new design, the request screen abandons obsoletely many, knows very well the method for the people. Because many person of conservativeness, does this certainly is not an easy matter. A mechanical designer should unceasingly explore the improvement existing product the method, should earnestly choose originally, the process confirmation principle of design in this process, with has not unified it after the confirmation new idea.Newly designs itself can have the question occurrence which many flaws and has not been able to expect, only has after these flaws and the question are solved, can manifest new goods come into the market the product superiority. Therefore, a performance superior product is born at the same time, also is following a higher risk. Should emphasize, if designs itself does not request to use the brand-new method, is not unnecessary merely for the goal which transform to use the new method.In the design preliminary stage, should allow to design the personnel fully to display the creativity, not each kind of restraint. Even if has had many impractical ideas, also can in the design early time, namely in front of the plan blueprint is corrected. Only then, only then does not send to stops up the innovation the mentality. Usually, must propose several sets of design proposals, then perform the comparison. Has the possibility very much in the plan which finally designated, has used certain not in plan some ideas which accepts.How does the psychologist frequently discuss causes the machine which the people adapts them to operate. Designs personnel's basic responsibility is diligently causes the machine to adapt the people. This certainly is not an easy work, because certainly does not have to all people to say in fact all is the most superior operating area and the operating process.Another important question, project engineer must be able to carry on the exchange and the consultation with other concerned personnel. In the initial stage, designs the personnel to have to carry on the exchange and the consultation on the preliminary design with the administrative personnel, and is approved. This generally is through the oral discussion, the schematic diagram and the writing material carries on. Inorder to carry on the effective exchange, needs to solve the following problem:(1)designs whether this product truly does need for the people? Whether there iscompetitive ability(2)does this product compare with other companies' existing similar products?(3)produces this kind of product is whether economical?(4)product service is whether convenient?(5) product whether there is sale? Whether may gain?Only has the time to be able to produce the correct answer to above question. But, the product design, the manufacture and the sale only can in carry on to the above question preliminary affirmation answer foundation in. Project engineer also should through the detail drawing and the assembly drawing, carries on the consultation together with the branch of manufacture to the finally design proposal.Usually, can have some problem in the manufacture process. Possibly can request to some components size or the common difference makes some changes, causes the components the production to change easily. But, in the project change must have to pass through designs the personnel to authorize, guaranteed cannot damage the product the function. Sometimes, when in front of product assembly or in the packing foreign shipment experiment only then discovers in the design some kind of flaw. These instances exactly showed the design is a dynamic process. Always has a better method to complete the design work, designs the personnel to be supposed unceasingly diligently, seeks these better method.Recent year, the engineerig material choice already appeared importantly. In addition, the choice process should be to the material continuously the unceasing again appraisal process. The new material unceasingly appears, but some original materials can obtain the quantity possibly can reduce. The environmental pollution, material recycling aspect and so on use, worker's health and security frequently can attach the new limiting condition to the choice of material. In order to reduce the weight or saves the energy, possibly can request the use different material. Comes from domestic and international competition, to product service maintenance convenience request enhancement and customer's aspect the and so on feedback pressure, can urgethe people to carry on to the material reappraises. Because the material does not select when created the product responsibility lawsuit, has already had the profound influence. In addition, the material and between the material processing interdependence is already known by the people clearly. Therefore, in order to can and guarantees the quality in the reasonable cost under the premise to obtain satisfaction the result, project engineer makes engineers all to have earnestly carefully to choose, the determination and the use material.Makes any product the first step of work all is designs. Designs usually may divide into several explicit stages: (a) preliminary design; (b) functional design; (c) production design. In the preliminary design stage, the designer emphatically considered the product should have function. Usually must conceive and consider several plans, then decided this kind of thought is whether feasible; If is feasible, then should makes the further improvement to or several plans. In this stage, the question which only must consider about the choice of material is: Whether has the performance to conform to the request material to be possible to supply the choice; If no, whether has a bigger assurance all permits in the cost and the time in the limit develops one kind of new material.In the functional design and the engineering design stage, needs to make a practical feasible design. Must draw up the quite complete blueprint in this stage, chooses and determines each kind of components the material. Usually must make the prototype or the working model, and carries on the experiment to it, the appraisal product function, the reliability, the outward appearance and the service maintenance and so on. Although this kind of experiment possibly can indicate, enters in the product to the production base in front of, should replace certain materials, but, absolutely cannot this point take not earnestly chooses the material the excuse. Should unify the product the function, earnestly carefully considers the product the outward appearance, the cost and the reliability. Has the achievement very much the company when manufacture all prototypes, selects the material should the material which uses with its production in be same, and uses the similar manufacture technology as far as possible. Like this has the advantage very much to the company. The functioncomplete prototype if cannot act according to the anticipated sales volume economically to make, or is prototypical and the official production installment has in the quality and the reliable aspect is very greatly different, then this kind of prototype does not have the great value. Project engineer is best can completely complete the material in this stage the analysis, the choice and the determination work, but is not remains it to the production design stage does. Because, is carries on in the production design stage material replacement by other people, these people are inferior to project engineer to the product all functions understanding. In the production design stage, is should completely determine with the material related main question the material, causes them to adapt with the existing equipment, can use the existing equipment economically to carry on the processing, moreover the material quantity can quite be easy to guarantee the supply.In the manufacture process, inevitably can appear to uses the material to make some changes the situation. The experience indicated that, may use certain cheap materials to take the substitute. However, in the majority situation, in will carry on the production later to change the material to have in to start before the production to change the price which the material will spend to have to be higher than. Completes the choice of material work in the design stage, may avoid the most such situations. Started after the production manufacture to appear has been possible to supply the use the new material is replaces the material the most common reason. Certainly, these new materials possibly reduce the cost, the improvement product performance. But, must carry on the earnest appraisal to the new material, guarantees its all performance all to answer the purpose. Must remember that, the new material performance and the reliable very few pictures materials on hand such understood for the people. The majority of products expiration and the product accident caused by negligence case is because in selects the new material to take in front of substitution material, not truly understood their long-term operational performance causes.The product responsibility lawsuit forces designs the personnel and the company when the choice material, uses the best procedure. In the material process, five most common questions are: (a) did not understand or cannot use about the materialapplication aspect most newly the best information paper; (b) has not been able to foresee and to consider the dusk year possible reasonable use (for example to have the possibility, designs the personnel also to be supposed further to forecast and the consideration because product application method not when creates consequence.In recent years many products responsibilities lawsuit case, because wrongly uses the plaintiff which the product receives the injury to accuse produces the factory, and wins the decision); (c) uses the material data not entire perhaps some data are indefinite, works as its long-term performance data is the like this time in particular;(d) the quality control method is not suitable and not after the confirmation; (e) the personnel which completely is not competent for the post by some chooses the material.Through to the above five questions analysis, may obtain these questions is does not have the sufficient reason existence the conclusion. May for avoid these questions to these questions research analyses the appearance indicating the direction. Although uses the best choice of material method not to be able to avoid having the product responsibility lawsuit, designs the personnel and the industry carries on the choice of material according to the suitable procedure, may greatly reduce the lawsuit the quantity.May see from the above discussion, the choice material people should to the material nature, the characteristic and the processing method have comprehensive and the basic understanding.译文:机械设计理论机械设计是一门通过设计新产品或者改进老产品来满足人类需求的应用技术科学。
机械类车床外文翻译
毕业设计(论文)——外文翻译(原文)Lathe来源:/wiki/LatheA lathe is a machine tool which spins a block of material to perform various operations such as cutting, sanding, knurling, drilling, or deformation with tools that are applied to the workpiece to create an object which has symmetry about an axis of rotation.Lathes are used in woodturning, metalworking, and glassworking. Lathes can be used to shape pottery, the best-known design being the potter's wheel. Most suitably equipped metalworking lathes can also be used to produce most solids of revolution, plane surfaces and screw threads or helices. Ornamental lathes can produce three-dimensional solids of incredible complexity. The material is held in place by either one or two centers, at least one of which can be moved horizontally to accommodate varying material lengths. Examples of objects that can be produced on a lathe include cue sticks, table legs, bowls, baseball bats, crankshafts and camshafts.HistoryThe lathe is an ancient tool, dating at least to the Egyptians ,and known and used in Greece, the Roman and Byzantine Empires.The origin of turning dates to around 1300BC when the Egyptians first developed a two-person lathe. One person would turn the wood workpiece with a rope while the other used a sharp tool to cut shapes in the wood. The Romans improved the Egyptian design with the addition of a turning bow. Early bow lathes were also developed and used in Germany, France and Britain. In the Middle Ages a pedal replaced hand-operated turning, freeing both the craftsman's hands to hold the woodturning tools. The pedal was usually connected to a pole, often a straight-grained sapling. The system today is called the "spring pole" lathe. Spring pole lathes were in common use into the early 20th Century. A two-person lathe, called a "great lathe", allowed a piece to turn continuously (like today's power lathes). A master would cut the wood while an apprentice turned the crank。
机械类毕业设计外文翻译---轴承的摩擦与润滑
外文文献原文:Friction , Lubrication of BearingIn many of the problem thus far , the student has been asked to disregard or neglect friction . Actually , friction is present to some degree whenever two parts are in contact and move on each other. The term friction refers to the resistance of two or more parts to movement.Friction is harmful or valuable depending upon where it occurs. friction is necessary for fastening devices such as screws and rivets which depend upon friction to hold the fastener and the parts together. Belt drivers, brakes, and tires are additional applications where friction is necessary.The friction of moving parts in a machine is harmful because it reduces the mechanical advantage of the device. The heat produced by friction is lost energy because no work takes place. Also , greater power is required to overcome the increased friction. Heat is destructive in that it causes expansion. Expansion may cause a bearing or sliding surface to fit tighter. If a great enough pressure builds up because made from low temperature materials may melt.There are three types of friction which must be overcome in moving parts: (1)starting, (2)sliding, and(3)rolling. Starting friction is the friction between two solids that tend to resist movement. When two parts are at a state of rest, the surface irregularities of both parts tend to interlock and form a wedging action. To produce motion in these parts, the wedge-shaped peaks and valleys of the stationary surfaces must be made to slide out and over each other. The rougher the two surfaces, the greater is starting friction resulting from their movement .Since there is usually no fixed pattern between the peaks and valleys of two mating parts, the irregularities do not interlock once the parts are in motion but slide over each other. The friction of the two surfaces is known as sliding friction. As shown in figure ,starting friction is always greater than sliding friction .Rolling friction occurs when roller devces are subjected to tremendous stress which cause the parts to change shape or deform. Under these conditions, the material in front of a roller tends to pile up and forces the object to roll slightly uphill. This changing of shape , known as deformation, causes a movement of molecules.As a result ,heat is produced from the added energy required to keep the parts turning and overcome friction.The friction caused by the wedging action of surface irregularities can be overcome partly by the precision machining of the surfaces. However, even these smooth surfaces may require the use of a substance between them to reduce the friction still more. This substance is usually a lubricant which provides a fine, thin oil film. The film keeps the surfaces apart and prevents the cohesive forces of the surfaces from coming in close contact and producing heat .Another way to reduce friction is to use different materials for the bearing surfaces and rotating parts. This explains why bronze bearings, soft alloys, and copper and tin iolite bearings are used with both soft and hardened steel shaft. The iolite bearing is porous. Thus, when the bearing is dipped in oil, capillary action carries the oil through the spaces of the bearing. This type of bearing carries its own lubricant to the points where the pressures are the greatest.Moving parts are lubricated to reduce friction, wear, and heat. The most commonly used lubricants are oils, greases, and graphite compounds. Each lubricant serves a different purpose. The conditions under which two moving surfaces are to work determine the type of lubricant to be used and the system selected for distributing the lubricant.On slow moving parts with a minimum of pressure, an oil groove is usually sufficient to distribute the required quantity of lubricant to the surfaces moving on each other .A second common method of lubrication is the splash system in which parts moving in a reservoir of lubricant pick up sufficient oil which is then distributed to all moving parts during each cycle. This system is used in the crankcase of lawn-mower engines to lubricate the crankshaft, connecting rod ,and parts of the piston.A lubrication system commonly used in industrial plants is the pressure system. In this system, a pump on a machine carries the lubricant to all of the bearing surfaces at a constant rate and quantity.There are numerous other systems of lubrication and a considerable number of lubricants available for any given set of operating conditions. Modern industrypays greater attention to the use of the proper lubricants than at previous time because of the increased speeds, pressures, and operating demands placed on equipment and devices.Although one of the main purposes of lubrication is reduce friction, any substance-liquid , solid , or gaseous-capable of controlling friction and wear between sliding surfaces can be classed as a lubricant.V arieties of lubricationUnlubricated sliding. Metals that have been carefully treated to remove all foreign materials seize and weld to one another when slid together. In the absence of such a high degree of cleanliness, adsorbed gases, water vapor ,oxides, and contaminants reduce frictio9n and the tendency to seize but usually result in severe wear; this is called “unlubricated ”or dry sliding.Fluid-film lubrication. Interposing a fluid film that completely separates the sliding surfaces results in fluid-film lubrication. The fluid may be introduced intentionally as the oil in the main bearing of an automobile, or unintentionally, as in the case of water between a smooth tuber tire and a wet pavement. Although the fluid is usually a liquid such as oil, water, and a wide range of other materials, it may also be a gas. The gas most commonly employed is air.Boundary lubrication. A condition that lies between unlubricated sliding and fluid-film lubrication is referred to as boundary lubrication, also defined as that condition of lubrication in which the friction between surfaces is determined by the properties of the surfaces and properties of the lubricant other than viscosity. Boundary lubrication encompasses a significant portion of lubrication phenomena and commonly occurs during the starting and stopping off machines.Solid lubrication. Solid such as graphite and molybdenum disulfide are widely used when normal lubricants do not possess sufficient resistance to load or temperature extremes. But lubricants need not take only such familiar forms as fats, powders, and gases; even some metals commonly serve as sliding surfaces in some sophisticated machines.Function of lubricantsAlthough a lubricant primarily controls friction and ordinarily does perform numerous other functions, which vary with the application and usually are interrelated .Friction control. The amount and character of the lubricant made available to sliding surfaces have a profound effect upon the friction that is encountered. For example, disregarding such related factors as heat and wear but considering friction alone between the same surfaces with on lubricant. Under fluid-film conditions, friction is encountered. In a great range of viscosities and thus can satisfy a broad spectrum of functional requirements. Under boundary lubrication conditions , the effect of viscosity on friction becomes less significant than the chemical nature of the lubricant.Wear control. wear occurs on lubricated surfaces by abrasion, corrosion ,and solid-to-solid contact wear by providing a film that increases the distance between the sliding surfaces ,thereby lessening the damage by abrasive contaminants and surface asperities.T emperature control. Lubricants assist in controlling corrosion of the surfaces themselves is twofold. When machinery is idle, the lubricant acts as a preservative. When machinery is in use, the lubricant controls corrosion by coating lubricated parts with a protective film that may contain additives to neutralize corrosive materials. The ability of a lubricant to control corrosion is directly relatly to the thickness of the lubricant film remaining on the metal surfaces and the chermical composition of the lubricant.Other functionsLubrication are frequently used for purposes other than the reduction of friction. Some of these applications are described below.Power transmission. Lubricants are widely employed as hydraulic fluids in fluid transmission devices.Insulation. In specialized applications such as transformers and switchgear , lubricants with high dielectric constants acts as electrical insulators. For maximum insulating properties, a lubricant must be kept free of contaminants and water.Shock dampening. Lubricants act as shock-dampening fluids in energy transferring devices such as shock absorbers and around machine parts such as gears that are subjected to high intermittent loads.Sealing. Lubricating grease frequently performs the special function of forming a seal to retain lubricants or to exclude contaminants.The object of lubrication is to reduce friction ,wear , and heating of machine pars which move relative to each other. A lubricant is any substance which, when inserted between the moving surfaces, accomplishes these purposes. Most lubricants are liquids(such as mineral oil, silicone fluids, and water),but they may be solid for use in dry bearings, greases for use in rolling element bearing, or gases(such as air) for use in gas bearings. The physical and chemical interaction between the lubricant and lubricating surfaces must be understood in order to provide the machine elements with satisfactory life.The understanding of boundary lubrication is normally attributed to hardy and doubleday , who found the extrememly thin films adhering to surfaces were often sufficient to assist relative sliding. They concluded that under such circumstances the chemical composition of fluid is important, and they introduced the term “boundary lubrication”. Boundary lubric ation is at the opposite end of the spectrum from hydrodynamic lubrication.Five distinct of forms of lubrication that may be defined :(a) hydrodynamic;(b)hydrostatic;(c)elastohydrodynamic (d)boundary; (e)solid film.Hydrodynamic lubrication means that the load-carrying surfaces of the bearing are separated by a relatively thick film of lubricant, so as to prevent metal contact, and that the stability thus obtained can be explained by the laws of the lubricant under pressure ,though it may be; but it does require the existence of an adequate supply at all times. The film pressure is created by the moving surfaces itself pulling the lubricant under pressure, though it maybe. The film pressure is created by the moving surface to creat the pressure necessary to separate the surfaces against the load on the bearing . hydrodynamic lubrication is also called full film ,or fluid lubrication .Hydrostatic lubrication is obtained by introducing the lubricant ,which is sometime air or water ,into the load-bearing area at a pressure high enough to separate the surface with a relatively thick film of lubricant. So ,unlike hydrodynanmic lubrication, motion of one surface relative to another is not required .Elasohydrodynamic lubrication is the phenomenon that occurs when a lubricant is introduced between surfaces which are in rolling contact, such as mating gears or rolling bearings. The mathematical explanation requires the hertzian theory of contact stress and fluid mechanics.When bearing must be operated at exetreme temperatures, a solid film lubricant such as graphite or molybdenum disulfide must be use used because the ordinary mineral oils are not satisfactory. Must research is currently being carried out in an effort, too, to find composite bearing materials with low wear rates as well as small frictional coefficients.In a journal bearing, a shaft rotates or oscillates within the bearing , and the relative motion is sliding . in an antifriction bearing, the main relative motion is rolling . a follower may either roll or slide on the cam. Gear teeth mate with each other by a combination of rolling and sliding . pistions slide within their cylinders. All these applications require lubrication to reduce friction ,wear, and heating.The field of application for journal bearing s is immense. The crankshaft and connecting rod bearings of an automotive engine must poerate for thousands of miles at high temperatures and under varying load conditions . the journal bearings used in the steam turbines of power generating station is said to have reliabilities approaching 100 percent. At the other extreme there are thousands of applications in which the loads are light and the service relatively unimportant. a simple ,easily installed bearing is required ,suing little or no lubrication. In such cases an antifriction bearing might be a poor answer because because of the cost, the close ,the radial space required ,or the increased inertial effects. Recent metallurgy developments in bearing materials , combined with increased knowledge of the lubrication process, now make it possible to design journal bearings with satisfactory lives and very good reliabilities.中文译文:轴承的摩擦与润滑现在看来,有很多这种情况,许多学生在被问到关于摩擦的问题时,往往都没引起足够的重视,甚至是忽视它。
机械专业外文翻译中英文翻译外文文献翻译
英文资料High-speed millingHigh-speed machining is an advanced manufacturing technology, different from the traditional processing methods. The spindle speed, cutting feed rate, cutting a small amount of units within the time of removal of material has increased three to six times. With high efficiency, high precision and high quality surface as the basic characteristics of the automobile industry, aerospace, mold manufacturing and instrumentation industry, such as access to a wide range of applications, has made significant economic benefits, is the contemporary importance of advanced manufacturing technology. For a long time, people die on the processing has been using a grinding or milling EDM (EDM) processing, grinding, polishing methods. Although the high hardness of the EDM machine parts, but the lower the productivity of its application is limited. With the development of high-speed processing technology, used to replace high-speed cutting, grinding and polishing process to die processing has become possible. To shorten the processing cycle, processing and reliable quality assurance, lower processing costs.1 One of the advantages of high-speed machiningHigh-speed machining as a die-efficient manufacturing, high-quality, low power consumption in an advanced manufacturing technology. In conventional machining in a series of problems has plagued by high-speed machining of the application have been resolved.1.1 Increase productivityHigh-speed cutting of the spindle speed, feed rate compared withtraditional machining, in the nature of the leap, the metal removal rate increased 30 percent to 40 percent, cutting force reduced by 30 percent, the cutting tool life increased by 70% . Hardened parts can be processed, a fixture in many parts to be completed rough, semi-finishing and fine, and all other processes, the complex can reach parts of the surface quality requirements, thus increasing the processing productivity and competitiveness of products in the market.1.2 Improve processing accuracy and surface qualityHigh-speed machines generally have high rigidity and precision, and other characteristics, processing, cutting the depth of small, fast and feed, cutting force low, the workpiece to reduce heat distortion, and high precision machining, surface roughness small. Milling will be no high-speed processing and milling marks the surface so that the parts greatly enhance the quality of the surface. Processing Aluminum when up Ra0.40.6um, pieces of steel processing at up to Ra0.2 ~ 0.4um.1.3 Cutting reduce the heatBecause the main axis milling machine high-speed rotation, cutting a shallow cutting, and feed very quickly, and the blade length of the workpiece contacts and contact time is very short, a decrease of blades and parts of the heat conduction. High-speed cutting by dry milling or oil cooked up absolute (mist) lubrication system, to avoid the traditional processing tool in contact with the workpiece and a lot of shortcomings to ensure that the tool is not high temperature under the conditions of work, extended tool life.1.4 This is conducive to processing thin-walled partsHigh-speed cutting of small cutting force, a higher degree of stability, Machinable with high-quality employees compared to the company may be very good, but other than the company's employees may Suanbu Le outstanding work performance. For our China practice, we use the models to determine the method of staff training needs are simple and effective. This study models can be an external object, it can also be a combination of internal and external. We must first clear strategy for the development of enterprises. Through the internal and external business environment and organizational resources, such as analysis, the future development of a clear business goals and operational priorities. According to the business development strategy can be compared to find the business models, through a comparative analysis of the finalization of business models. In determining business models, a, is the understanding of its development strategy, or its market share and market growth rate, or the staff of the situation, and so on, according to the companies to determine the actual situation. As enterprises in different period of development, its focus is different, which means that enterprises need to invest the manpower and financial resources the focus is different. So in a certain period of time, enterprises should accurately selected their business models compared with the departments and posts, so more practical significance, because the business models are not always good, but to compare some aspects did not have much practical significance, Furthermore This can more fully concentrate on the business use of limited resources. Identify business models, and then take the enterprise of the corresponding departments and staff with the business models for comparison, the two can be found in the performance gap, a comparative analysis to find reasons, in accordance with this business reality, the final identification of training needs. The cost of training is needed, if not through an effective way to determine whether companies need to train and the training of the way, but blind to training, such training is difficult to achieve the desired results. A comparison only difference between this model is simple and practical training.1.5 Can be part of some alternative technology, such as EDM, grinding high intensity and high hardness processingHigh-speed cutting a major feature of high-speed cutting machine has the hardness of HRC60 parts. With the use of coated carbide cutter mold processing, directly to the installation of ahardened tool steel processing forming, effectively avoid the installation of several parts of the fixture error and improve the parts of the geometric location accuracy. In the mold of traditional processing, heat treatment hardening of the workpiece required EDM, high-speed machining replace the traditional method of cutting the processing, manufacturing process possible to omit die in EDM, simplifying the processing technology and investment costs .High-speed milling in the precincts of CNC machine tools, or for processing centre, also in the installation of high-speed spindle on the general machine tools. The latter not only has the processing capacity of general machine tools, but also for high-speed milling, a decrease of investment in equipment, machine tools increased flexibility. Cutting high-speed processing can improve the efficiency, quality improvement, streamline processes, investment and machine tool investment and maintenance costs rise, but comprehensive, can significantly increase economic efficiency.2 High-speed millingHigh-speed milling the main technical high-speed cutting technology is cutting the development direction of one of it with CNC technology, microelectronic technology, new materials and new technology, such as technology development to a higher level. High-speed machine tools and high-speed tool to achieve high-speed cutting is the prerequisite and basic conditions, in high-speed machining in the performance of high-speed machine tool material of choice and there are strict requirements.2.1 High-speed milling machine in order to achieve high-speed machiningGeneral use of highly flexible high-speed CNC machine tools, machining centers, and some use a dedicated high-speed milling, drilling. At the same time a high-speed machine tool spindle system and high-speed feeding system, high stiffness of the main characteristics of high-precision targeting and high-precision interpolation functions, especially high-precision arc interpolation function. High-speed machining systems of the machine a higher demand, mainly in the following areas:General use of highly flexible high-speed CNC machine tools, machining centers, and some use a dedicated high-speed milling, drilling. At the same time a high-speed machine tool spindle system and high-speed feeding system, high stiffness of the main characteristics of high-precision targeting and high-precision interpolation functions, especially high-precision arc interpolation function. High-speed machining systems of the machine a higher demand, mainly in the following areas:High-speed milling machine must have a high-speed spindle, the spindle speed is generally 10000 ~ 100000 m / min, power greater than 15 kW. But also with rapid speed or in designated spots fast-stopping performance. The main axial space not more than 0 .0 0 0 2 m m. Often using high-speed spindle-hydrostatic bearings, air pressure-bearing, mixed ceramic bearings, magneticbearing structure of the form. Spindle cooling general use within the water or air cooled.High-speed processing machine-driven system should be able to provide 40 ~ 60 m / min of the feed rate, with good acceleration characteristics, can provide 0.4 m/s2 to 10 m/s2 acceleration and deceleration. In order to obtain good processing quality, high-speed cutting machines must have a high enough stiffness. Machine bed material used gray iron, can also add a high-damping base of concrete, to prevent cutting tool chatter affect the quality of processing. A high-speed data transfer rate, can automatically increase slowdown. Processing technology to improve the processing and cutting tool life. At present high-speed machine tool manufacturers, usually in the general machine tools on low speed, the feed of the rough and then proceed to heat treatment, the last in the high-speed machine on the half-finished and finished, in improving the accuracy and efficiency at the same time, as far as possible to reduce processing Cost.2.2 High-speed machining toolHigh-speed machining tool is the most active one of the important factors, it has a direct impact on the efficiency of processing, manufacturing costs and product processing and accuracy. Tool in high-speed processing to bear high temperature, high pressure, friction, shock and vibration, such as loading, its hardness and wear-resistance, strength and toughness, heat resistance, technology and economic performance of the basic high-speed processing performance is the key One of the factors. High-speed cutting tool technology development speed, the more applications such as diamond (PCD), cubic boron nitride (CBN), ceramic knives, carbide coating, (C) titanium nitride Carbide TIC (N) And so on. CBN has high hardness, abrasion resistance and the extremely good thermal conductivity, and iron group elements between the great inertia, in 1300 ℃ would not have happened significant role in the chemical, also has a good stability. The experiments show that with CBN cutting toolHRC35 ~ 67 hardness of hardened steel can achieve very high speed. Ceramics have good wear resistance and thermal chemical stability, its hardness, toughness below the CBN, can be used for processing hardness of HRC <5 0 parts. Carbide Tool good wear resistance, but the hardness than the low-CBN and ceramics. Coating technology used knives, cutting tools can improve hardness and cutting the rate, for cutting HRC40 ~ 50 in hardness between the workpiece. Can be used to heat-resistant alloys, titanium alloys, hightemperature alloy, cast iron, Chungang, aluminum and composite materials of high-speed cutting Cut, the most widely used. Precision machining non-ferrous metals or non-metallic materials, or the choice of polycrystalline diamond Gang-coated tool.2.3 High-speed processing technologyHigh-speed cutting technology for high-speed machining is the key. Cutting Methods misconduct, will increase wear tool to less than high-speed processing purposes. Only high-speed machine tool and not a good guide technology, high-speed machining equipment can not fullyplay its role. In high-speed machining, should be chosen with milling, when the milling cutter involvement with the workpiece chip thickness as the greatest, and then gradually decreased. High-speed machining suitable for shallow depth of cut, cutting depth of not more than 0.2 mm, to avoid the location of deviation tool to ensure that the geometric precision machining parts. Ensure that the workpiece on the cutting constant load, to get good processing quality. Cutting a single high-speed milling path-cutting mode, try not to interrupt the process and cutting tool path, reducing the involvement tool to cut the number to be relatively stable cutting process. Tool to reduce the rapid change to, in other words when the NC machine tools must cease immediately, or Jiangsu, and then implement the next step. As the machine tool acceleration restrictions, easy to cause a waste of time, and exigency stop or radical move would damage the surface accuracy. In the mold of high-speed finishing, in each Cut, cut to the workpiece, the feed should try to change the direction of a curve or arc adapter, avoid a straight line adapter to maintain the smooth process of cutting.3 Die in high-speed milling processing ofMilling as a highly efficient high-speed cutting of the new method,inMould Manufacturing has been widely used. Forging links in the regular production model, with EDM cavity to be 12 ~ 15 h, electrodes produced 2 h. Milling after the switch to high-speed, high-speed milling cutter on the hardness of HRC 6 0 hardened tool steel processing. The forging die processing only 3 h20min, improve work efficiency four to five times the processing surface roughness of Ra0.5 ~ 0.6m, fully in line with quality requirements.High-speed cutting technology is cutting technology one of the major developments, mainly used in automobile industry and die industry, particularly in the processing complex surface, the workpiece itself or knives rigid requirements of the higher processing areas, is a range of advanced processing technology The integration, high efficiency and high quality for the people respected. It not only involves high-speed processing technology, but also including high-speed processing machine tools, numerical control system, high-speed cutting tools and CAD / CAM technology. Die-processing technology has been developed in the mold of the manufacturing sector in general, and in my application and the application of the standards have yet to be improved, because of its traditional processing with unparalleled advantages, the future will continue to be an inevitable development of processing technology Direction.4 Numerical control technology and equipping development trend and countermeasureEquip the engineering level, level of determining the whole national economy of the modernized degree and modernized degree of industry, numerical control technology is it develop new developing new high-tech industry and most advanced industry to equip (such as information technology and his industry, biotechnology and his industry, aviation, spaceflight, etc. national defense industry) last technology and getting more basic most equipment. Marx has ever said "the differences of different economic times, do not lie in what is produced, and lie in how to produce,produce with some means of labor ". Manufacturing technology and equipping the most basic means of production that are that the mankind produced the activity, and numerical control technology is nowadays advanced manufacturing technology and equips the most central technology. Nowadays the manufacturing industry all around the world adopts numerical control technology extensively, in order to improve manufacturing capacity and level, improve the adaptive capacity and competitive power to the changeable market of the trends. In addition every industrially developed country in the world also classifies the technology and numerical control equipment of numerical control as the strategic materials of the country, not merely take the great measure to develop one's own numerical control technology and industry, and implement blockading and restrictive policy to our country in view of " high-grade, precision and advanced key technology of numerical control " and equipping. In a word, develop the advanced manufacturing technology taking numerical control technology as the core and already become every world developed country and accelerate economic development in a more cost-effective manner, important way to improve the overall national strength and national position. Numerical control technology is the technology controlled to mechanical movement and working course with digital information, integrated products of electromechanics that the numerical control equipment is the new technology represented by numerical control technology forms to the manufacture industry of the tradition and infiltration of the new developing manufacturing industry, namely the so-called digitization is equipped, its technological range covers a lot of fields: (1)Mechanical manufacturing technology; (2)Information processing, processing, transmission technology; (3)Automatic control technology; (4)Servo drive technology;(5)Technology of the sensor; (6)Software engineering ,etc..Development trend of a numerical control technologyThe application of numerical control technology has not only brought the revolutionary change to manufacturing industry of the tradition, make the manufacturing industry become the industrialized symbol , and with the constant development of numerical control technology and enlargement of the application, the development of some important trades (IT , automobile , light industry , medical treatment ,etc. ) to the national economy and the people's livelihood of his plays a more and more important role, because the digitization that these trades needed to equip has already been the main trend of modern development. Numerical control technology in the world at present and equipping the development trend to see, there is the following several respect [1- ] in its main research focus.5 A high-speed, high finish machining technology and new trend equippedThe efficiency, quality are subjavanufacturing technology. High-speed, high finish machining technology can raise the efficiency greatly , improve the quality and grade of the products, shorten production cycle and improve the market competitive power. Japan carries the technological research association first to classify it as one of the 5 great modern manufacturing technologies forthis, learn (CIRP) to confirm it as the centre in the 21st century and study one of the directions in international production engineering.In the field of car industry, produce one second when beat such as production of 300,000 / vehicle per year, and many variety process it is car that equip key problem that must be solved one of; In the fields of aviation and aerospace industry, spare parts of its processing are mostly the thin wall and thin muscle, rigidity is very bad, the material is aluminium or aluminium alloy, only in a situation that cut the speed and cut strength very small high, could process these muscles, walls. Adopt large-scale whole aluminium alloy method that blank " pay empty " make the wing recently, such large-scale parts as the fuselage ,etc. come to substitute a lot of parts to assemble through numerous rivet , screw and other connection way, make the intensity , rigidity and dependability of the component improved. All these, to processing and equipping the demand which has proposed high-speed, high precise and high flexibility.According to EMO2001 exhibition situation, high-speed machining center is it give speed can reach 80m/min is even high , air transport competent speed can up to 100m/min to be about to enter. A lot of automobile factories in the world at present, including Shanghai General Motors Corporation of our country, have already adopted and substituted and made the lathe up with the production line part that the high-speed machining center makes up. HyperMach lathe of U.S.A. CINCINNATI Company enters to nearly biggest 60m/min of speed, it is 100m/min to be fast, the acceleration reaches 2g, the rotational speed of the main shaft has already reached 60 000r/min. Processing a thin wall of plane parts, spend 30min only, and same part general at a high speed milling machine process and take 3h, the ordinary milling machine is being processed to need 8h; The speed and acceleration of main shaft of dual main shaft lathes of Germany DMG Company are up to 120000r/mm and 1g.In machining accuracy, the past 10 years, ordinary progression accuse of machining accuracy of lathe bring 5μm up to from 10μm already, accurate grades of machining center from 3~5μm, rise to 1~1.5μm, and ultraprecision machining accuracy is i t enter nanometer grade to begin already (0.01μm).In dependability, MTBF value of the foreign numerical control device has already reached above 6 000h, MTBF value of the servo system reaches above 30000h, demonstrate very high dependability .In order to realize high-speed, high finish machining, if the part of function related to it is electric main shaft, straight line electrical machinery get fast development, the application is expanded further .5.2 Link and process and compound to process the fast development of the lathe in 5 axesAdopt 5 axles to link the processing of the three-dimensional curved surface part, can cut with the best geometry form of the cutter , not only highly polished, but also efficiency improves by a large margin . It is generally acknowledged, the efficiency of an 5 axle gear beds can equal 2 3 axle gearbeds, is it wait for to use the cubic nitrogen boron the milling cutter of ultra hard material is milled and pared at a high speed while quenching the hard steel part, 5 axles link and process 3 constant axles to link and process and give play to higher benefit. Because such reasons as complicated that 5 axles link the numerical control system , host computer structure that but go over, it is several times higher that its price links the numerical control lathe than 3 axles , in addition the technological degree of difficulty of programming is relatively great, have restricted the development of 5 axle gear beds.At present because of electric appearance of main shaft, is it realize 5 axle complex main shaft hair structure processed to link greatly simplify to make, it makes degree of difficulty and reducing by a large margin of the cost, the price disparity of the numerical control system shrinks. So promoted 5 axle gear beds of head of complex main shaft and compound to process the development of the lathe (process the lathe including 5).At EMO2001 exhibition, new Japanese 5 of worker machine process lathe adopt complex main shaft hair, can realize the processing of 4 vertical planes and processing of the wanton angle, make 5 times process and 5 axles are processed and can be realized on the same lathe, can also realize the inclined plane and pour the processing of the hole of awls. Germany DMG Company exhibits the DMUVoution series machining center, but put and insert and put processing and 5 axles 5 times to link and process in once, can be controlled by CNC system or CAD/CAM is controlled directly or indirectly.5.3 Become the main trend of systematic development of contemporary numerical control intelligently, openly, networkedly.The numerical control equipment in the 21st century will be sure the intelligent system, the intelligent content includes all respects in the numerical control system: It is intelligent in order to pursue the efficiency of processing and process quality, control such as the self-adaptation of the processing course, the craft parameter is produced automatically; Join the convenient one in order to improve the performance of urging and use intelligently, if feedforward control , adaptive operation , electrical machinery of parameter , discern load select models , since exactly makes etc. automatically; The ones that simplified programming , simplified operating aspect are intelligent, for instance intelligent automatic programming , intelligent man-machine interface ,etc.; There are content of intelligence diagnose , intelligent monitoring , diagnosis convenient to be systematic and maintaining ,etc..Produce the existing problem for the industrialization of solving the traditional numerical control system sealing and numerical control application software. A lot of countries carry on research to the open numerical control system at present, such as NGC of U.S.A. (The Next Generation Work-Station/Machine Control), OSACA of European Community (Open System Architecture for Control within Automation Systems), OSEC (Open System Environment for Controller) of Japan, ONC (Open Numerical Control System) of China, etc.. The numerical control system melts tobecome the future way of the numerical control system open. The so-called open numerical control system is the development of the numerical control system can be on unified operation platform, face the lathe producer and end user, through changing, increasing or cutting out the structure target(numerical control function), form the serration, and can use users specially conveniently and the technical know-how is integrated in the control system, realize the open numerical control system of different variety , different grade fast, form leading brand products with distinct distinction. System structure norm of the open numerical control system at present, communication norm , disposing norm , operation platform , numerical control systematic function storehouse and numerical control systematic function software development ,etc. are the core of present research.The networked numerical control equipment is a new light spot of the fair of the internationally famous lathe in the past two years. Meeting production line , manufacture system , demand for the information integration of manufacturing company networkedly greatly of numerical control equipment, realize new manufacture mode such as quick make , fictitious enterprise , basic Entrance that the whole world make too. Some domestic and international famous numerical control lathes and systematic manufacturing companies of numerical control have all introduced relevant new concepts and protons of a machine in the past two years, if in EMO2001 exhibition, " Cyber Production Center " that the company exhibits of mountain rugged campstool gram in Japan (Mazak) (intellectual central production control unit, abbreviated as CPC); The lathe company of Japanese big Wei (Okuma ) exhibits " IT plaza " (the information technology square , is abbreviated as IT square ); Open Manufacturing Environment that the company exhibits of German Siemens (Siemens ) (open the manufacturing environment, abbreviated as OME),etc., have reflected numerical control machine tooling to the development trend of networked direction.5.4 Pay attention to the new technical standard, normal setting-up5.4.1 Design the norm of developing about the numerical control systemAs noted previously, there are better common ability, flexibility, adaptability, expanding in the open numerical control system, such countries as U.S.A. ,European Community and Japan ,etc. implement the strategic development plan one after another , carry on the research and formulation of the systematic norm (OMAC , OSACA , OSEC ) of numerical control of the open system structure, 3 biggest economies in the world have carried on the formulation that nearly the same science planned and standardized in a short time, have indicated a new arrival of period of change of numerical control technology. Our country started the research and formulation of standardizing the frame of ONC numerical control system of China too in 2000.5.4.2 About the numerical control standardThe numerical control standard is a kind of trend of information-based development of manufacturing industry. Information exchange among 50 years after numerical control technology was born was all because of ISO6983 standard, namely adopt G, M code describes how processes,。
- 1、下载文档前请自行甄别文档内容的完整性,平台不提供额外的编辑、内容补充、找答案等附加服务。
- 2、"仅部分预览"的文档,不可在线预览部分如存在完整性等问题,可反馈申请退款(可完整预览的文档不适用该条件!)。
- 3、如文档侵犯您的权益,请联系客服反馈,我们会尽快为您处理(人工客服工作时间:9:00-18:30)。
机械类外文翻译塑料注塑模具浇口优化摘要:用单注塑模具浇口位置的优化方法,本文论述。
该闸门优化设计的目的是最大限度地减少注塑件翘曲变形,翘曲,是因为对大多数注塑成型质量问题的关键,而这是受了很大的部分浇口位置。
特征翘曲定义为最大位移的功能表面到表面的特征描述零件翘曲预测长度比。
结合的优化与数值模拟技术,以找出最佳浇口位置,其中模拟armealing算法用于搜索最优。
最后,通过实例讨论的文件,它可以得出结论,该方法是有效的。
注塑模具、浇口位臵、优化、特征翘曲变形关键词:简介塑料注射成型是一种广泛使用的,但非常复杂的生产的塑料产品,尤其是具有高生产的要求,严密性,以及大量的各种复杂形状的有效方法。
质量ofinjection 成型零件是塑料材料,零件几何形状,模具结构和工艺条件的函数。
注塑模具的一个最重要的部分主要是以下三个组件集:蛀牙,盖茨和亚军,和冷却系统。
拉米夫定、Seow(2000)、金和拉米夫定(2002) 通过改变部分的尼斯达到平衡的腔壁厚度。
在平衡型腔充填过程提供了一种均匀分布压力和透射电镜,可以极大地减少高温的翘曲变形的部分~但仅仅是腔平衡的一个重要影响因素的一部分。
cially Espe,部分有其功能上的要求,其厚度通常不应该变化。
pointview注塑模具设计的重点是一门的大小和位臵,以及流道系统的大小和布局。
大门的大小和转轮布局通常被认定为常量。
相对而言,浇口位臵与水口大小布局也更加灵活,可以根据不同的零件的质量。
李和吉姆(姚开屏,1996a)称利用优化流道和尺寸来平衡多流道系统为multiple 注射系统。
转轮平衡被形容为入口压力的差异为一多型腔模具用相同的蛀牙,也存在明显差异的压力。
一天结束的熔体流动路径在每个空腔为一个家庭模腔数量和几何形状的不同。
方法论已经显示出均匀压力分布在腔成型周期的整个过程中多腔模具。
翟隽孙俐。
(2005a)颁发的两门失水一个成型的声誉的优化提出本文腔的压力梯度搜索法的基础上(PGSS),以及随后的定位焊缝位臵通过改变到所需的尺寸formulti-gate转轮部件(斋el高庆宇,2006)。
作为大型部分,多重盖茨是需要的,以缩短马克西•妈妈传递路径、相应的减少注射压力。
该方法是有前途的标志为德盖茨和跑步者为一个单一的腔内多个大门。
许多注塑件均采用一门,无论是在单腔模具或多腔模具。
因此,一个单一的浇口位臵的门是最常见的主要设计参数,为优化。
是一种形状分析方法,通过Courbebaisse压力介绍加西亚(2002),以最优的浇口位臵的注射成型是esti交配。
随后,他们发展了这一methodology进一步,并将它应用到单浇口位臵的timization opL型的例子中(Courbebaisse,2005年)。
它很容易使用,而不是浪费时间,而这仅仅是简单的平面转弯之零件厚度均匀。
Pandelidis和邹(1990)颁发的optimization浇口位臵、通过间接的相关质量的措施和材料降解翘曲变形,这是被描绘成一个温度进行加权和的术语,一个over-packferential摩擦过热的术语,和术语。
翘曲变形的影响是由上述因素,但他们之间的关系尚不清楚。
因此,优化效果一直是制约因素的权重确定。
李和金侵入)的选择方法,开发了一种自动浇口位臵,其中一组初始浇口位臵是一个设计师,然后提出的最优门位于相邻节点评价方法。
结论在很大程度上在很大程度上取决于人类设计师的直觉,因为第一步的方法是基于设计师的命题。
所以结果是一个较大的特异帐篷限于设计者的经验。
拉米夫定、金(2001)开发了浇口位臵优化方法基于对应的标准偏差流路径长度(SD[L])和标准偏差的填充时间(SD)在[T]成型充填过程。
随后,和善的;2004b el 铝(2004a)优化了浇口位臵设计,通过最小化加权和的灌装压力、填充时间不同位臵的流路、温差、over-pack百分比。
翟隽el艾尔交际与最佳浇口位臵进行评价标准的喷射压力的年底的灌装。
这些研究人员提出了objec保守的函数作为表演注射成型充填操作,这相关产品的品质。
但之间的相关性进行ances、素质非常复杂,没有清楚观察之间的关系一直是他们没有。
它也很难去选择适当的加权因子为每个术语。
提出了一种新的目标函数来评估注塑件翘曲变形的浇口位臵优化。
测量产品的质量,这项调查rectly嘀来评估部分定义特征翘曲变形,这是评价从“流”模拟输出的加上翘曲Moldflow软件(MPI)塑料的洞察力。
设计的客观func最小化取得最低浇口位臵优化变形。
gorithm模拟退火艾尔被用来寻找最佳浇口位臵。
给出了一个算例以说明提出的机动车活优化程序。
质量特征WARPGE措施:特征翘曲的定义优化理论应用到大门口设计、质量的措施必须被指定的部分,在这个例子中。
“质量”这个术语可以被称作许多产品的性质,如机械、热、电、光erties工效或几何的道具。
有两种类型的部分质量的措施:直接法和间接法。
一个模型,预测了适当的关系数值仿真的结果会从被称作是一个有直接的质量检测。
相反,间接测量的质量与目标的一部分,但它无法提供质量直接估计的那样的实力。
对翘曲变形,间接质量的工艺措施之一是在相关工作性能的注射成型流动行为或加权和的那些。
给出了填充性能进行ferential时间沿着不同流路,,over-pack温度进行ferential 百分比,等等。
它是vious,指挥的翘曲变形的影响是由ances,但这些表演和翘曲变形之间的关系还不清楚这些表演和判定这些权重因素是相当困难的,因此上述目标的优化functionprobably不会减少翘曲变形甚至以完美的部分优化技术。
有时,不适当的加权因素将导致绝对错误的反应结果从一些统计量计算的节点位移特征作为直接质量的手段来达到最小变形研究相关优化。
通常的统计量最大,av结点位移的射手,十大百分位数节点位移和整体平均结点位移(李和金,1995年,侵入)。
这些节点位移是容易获得从模拟结果,统计valkilmer问题,在一定程度上代表了变形。
但不能有效地描述统计位移的变形,注塑件在工业上,设计师和制造商通常会更加关注程度的部分对一些具体特征翘曲变形的比整个注塑件。
在这项研究中,特征翘曲变形的定义描述的射出零件。
特征翘曲变形是比率的最大位移特征的表面投影特征曲面的长度(图1): y =—xlOO% L (1) 在y为特征翘曲变形等情况,得到h的最大位移特征表面偏离参考平台,L是投射特征曲面的长度方向上的参考参考并联平台。
对于复杂的特征(只有平面特征,讨论了特征翘曲这里)通常是国家环保总局额定分成两组分参考层,这是被描绘了二维坐标系统:在y,yy是组成特征warpages X,y方向,和L的预计,信用是长度特征曲面在X,y部件。
评价的特征翘曲变形目标特性的测定,后与相对应的参考bined com面和公关的价值ojection方向,随即从L可以计算出的部分计算方法解析几何的(图2)。
我是一个持续的任何部分在指定的特征曲面和公关ojected方向。
但是更多的评价plicated com,h比L。
图2 .放映的长度的评价模拟注塑成型过程是一种常见的质量技术部分预测标志德、模具设计和工艺设定。
结果翘曲变形模拟表达为节点德flections在X,Y,Z分量(,,),我们与节点位移W〃W是向量长度的向量表面参考平面笔Wi,Wj,我在哪里,j,k是单位向量在X,Y,Z分量。
的h是最大的位移特征曲面上的节点,这是正常的方向与参考平面,并可从中翘曲变形模拟的结果。
,挠度计算h的节点是如下:在W,是在正常的方向偏转的参考平面与节点;W,W,,,,,,,,,,,,W1是吗挠度在X,Y,Z分量的节点;一个,牢记为fi,Y正常的角度向量的参考;然后呢突出的方向(图2)、佤族及世界银行的挠度 B有终端节点的功能,节点A和BfWA =WArcosa+WAcos/3+WAcosy,WB =WBrcosa+Wcosfl+WBcosy,在哪里了,哇哦,想获得WAZ奖是蜡挠度在X,Y,Z分量的节点,WB、世界银行及世界银行的flections onX德,Y,Zcomponent娃和节点的;也许是COIB加权因子的终端节点deflec对其计算方式如= 1 — LA / L, B = 1 — a),A (5) 英语 ? 中文复制在洛杉矶之间的距离是投影机与节点和节点答:最终,h是最高的绝对值的W,: (6)在工业上,检测出carned翘曲变形是一种试探的帮助下,而测量仪表部位应放臵在一个参考的价值平台,h形式的最大数值阅读之间的距离,测量部分测绘 p'atform脸和参浇口位臵优化问题的形成术语“质量”是指perma翘曲变形的nent部分,它不是所引起的载荷。
这是由于差动收缩整个部分,由于聚合物流动的不平衡,包装,冷却,结晶。
一门的放臵在注塑模具最重要的变量之一总数的模具设计。
这种模铸组成部分的质量是由fected大大心房颤动的浇口位臵,因为它影响的方式塑料流入型腔。
因此,不同mogeneity介绍inho浇口位臵在定位、密度、压力、温度分布,因此引入不同的价值与分配的翘曲变形。
因此,浇口位臵是一种有价值的设计变量,最大限度地减少射出成型部分翘曲变形。
关系因为软木浇口位臵和翘曲变形distribu在很大程度上是一个独立的融化和模具温度,假定成型工艺条件在这次调查中保持不变。
射出成型部分的翘曲变形是量化的特征翘曲变形是讨论在上一节中。
单浇口位臵优化就可以制定如下:在y为特征翘曲的注入压力;p是在门口的位臵;订单是属于注塑机jection压力或许可的注射压力所指定的设计师或制造商,X是坐标向量的候选人浇口位臵;X,是一个节点有限元网格模型的部分,为注塑工艺的模拟;Nis总人数的节点。
在有限元网格模型的一部分,每一个节点都是可能的候选人为一扇大门。
那里脱总数可能的浇口位臵N功能节点总数的氮和总人数的浇口位臵优化护颖而出, 士:在这项研究中,只有single-gate定位问题进行了实验研究。
模拟退火算法将模拟退火算法是其中一个最强大的和最受欢迎的meta-heuristics来解决优化问题由于提供良好全球解决方案对现实世界的问题。
该算法依据孙力(1953年),最初提出的作为一种手段来找到一个平衡构形的一群原子在一定的温度下。
连接被该算法和数学最小化之间尚属首次发现由平卡斯(1970),但它是由孙力(1983)谁提出,它的形成过程,提出了一种优化技术的基础上,对combina传统(或其他)的问题应用模拟退火法的作用timization问题,目标函数f)是作为能量函数e,而不是寻找一个低的能源结构,这个问题变得寻求近似全局最优解。
同样的configura设计变量的值代替对于能量的配臵,你的身体和控制参数的过程是代替温度。