FPC柔性电路板制造流程.pptx
FPCB工艺制造流程介绍ppt
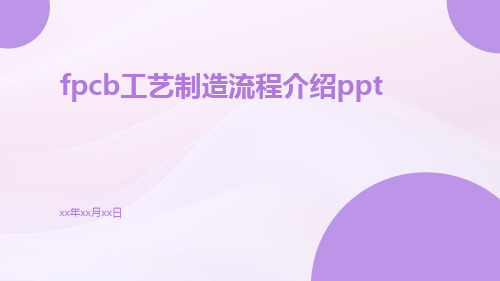
在连接处制作焊盘和标记。
表面处理
对线路图形进行表面处理,以增强其导电性和稳定性。
fpcb制造意义
提高设备的便携性和可靠性
FPCB的轻便、可弯曲、可卷曲等特性使得设备更加便携,同时由于其高度集成和 可靠性,也提高了设备的性能和可靠性。
促进电子设备的多功能化和智能化发展
FPCB的制造工艺和材料多样化,可广泛应用于消费电子、汽车电子、通信设备等 领域,促进电子设备的多功能化和智能化发展。
机遇
技术进步:随着科技的不断发展,FPCB制造工艺也不断 得到改进和提升,为电子设备制造商提供了更多的选择 和机遇。
人力成本上升:由于FPCB制造工艺需要大量的人力资 源,随着人力成本的不断提高,对于FPCB制造企业的 成本控制和盈利能力提出了更高的要求。
新兴产业的发展:随着新能源、5G等新兴产业的发展 ,对于FPCB的需求也不断增加,为FPCB制造工艺带来 了广阔的市场和发展空间。
挑战
环保压力:随着环保意识的不断提高,对于环境污染较 大的FPCB制造工艺也面临着环保方面的压力和挑战, 企业需要不断改进工艺和设备,提高环保水平。
THANKS
谢谢您的观看
资源高效利用
通过提高原材料利用率、减少能源和水资源的消耗等措 施,实现资源的有效利用。
循环经济
采用循环经济模式,实现资源的循环利用和废弃物的再 生利用。
05
总结
fpcb工艺制造的未来趋势
持续高精度化
随着电子设备对于性能和稳定性的需求日益增长,对于高精度、高稳定性的FPCB制造工 艺的需求也将不断增加。
高效化生产管理
精益生产
采用精益生产理念,通过消除浪费、持续改进等手段,提高生 产效率和质量。
FPC的全流程
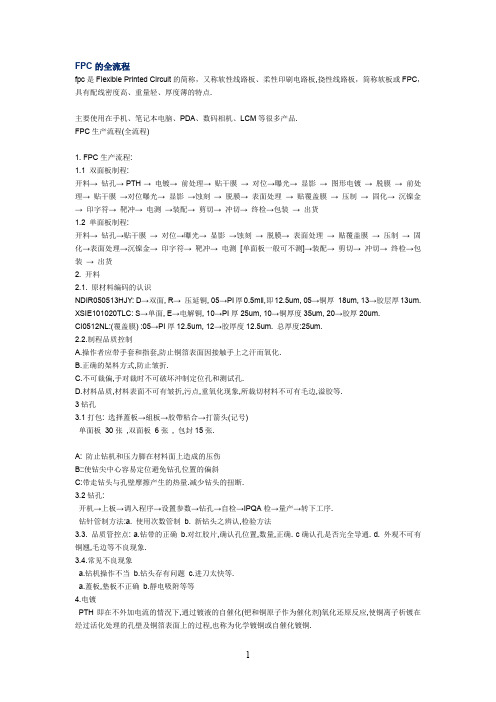
FPC的全流程fpc是Flexible Printed Circuit的简称,又称软性线路板、柔性印刷电路板,挠性线路板,简称软板或FPC,具有配线密度高、重量轻、厚度薄的特点.主要使用在手机、笔记本电脑、PDA、数码相机、LCM等很多产品.FPC生产流程(全流程)1. FPC生产流程:1.1 双面板制程:开料→ 钻孔→ PTH → 电镀→ 前处理→ 贴干膜→ 对位→曝光→ 显影→ 图形电镀→ 脱膜→ 前处理→ 贴干膜→对位曝光→ 显影→蚀刻→ 脱膜→ 表面处理→ 贴覆盖膜→ 压制→ 固化→ 沉镍金→ 印字符→ 靶冲→ 电测→装配→ 剪切→ 冲切→ 终检→包装→ 出货1.2 单面板制程:开料→ 钻孔→贴干膜→ 对位→曝光→ 显影→蚀刻→ 脱膜→ 表面处理→ 贴覆盖膜→ 压制→ 固化→表面处理→沉镍金→ 印字符→ 靶冲→ 电测[单面板一般可不测]→装配→ 剪切→ 冲切→ 终检→包装→ 出货2. 开料2.1. 原材料编码的认识NDIR050513HJY: D→双面, R→ 压延铜, 05→PI厚0.5mil,即12.5um, 05→铜厚18um, 13→胶层厚13um. XSIE101020TLC: S→单面, E→电解铜, 10→PI厚25um, 10→铜厚度35um, 20→胶厚20um.CI0512NL:(覆盖膜) :05→PI厚12.5um, 12→胶厚度12.5um. 总厚度:25um.2.2.制程品质控制A.操作者应带手套和指套,防止铜箔表面因接触手上之汗而氧化.B.正确的架料方式,防止皱折.C.不可裁偏,手对裁时不可破坏沖制定位孔和测试孔.D.材料品质,材料表面不可有皱折,污点,重氧化现象,所裁切材料不可有毛边,溢胶等.3钻孔3.1打包: 选择蓋板→組板→胶帶粘合→打箭头(记号)单面板30张,双面板6张, 包封15张.A: 防止钻机和压力脚在材料面上造成的压伤B::使钻尖中心容易定位避免钻孔位置的偏斜C:带走钻头与孔壁摩擦产生的热量.减少钻头的扭断.3.2钻孔:开机→上板→调入程序→设置参数→钻孔→自检→IPQA检→量产→转下工序.钻针管制方法:a. 使用次数管制b. 新钻头之辨认,检验方法3.3. 品质管控点: a.钻带的正确b.对红胶片,确认孔位置,数量,正确. c确认孔是否完全导通. d. 外观不可有铜翘,毛边等不良现象.3.4.常见不良现象a.钻机操作不当b.钻头存有问题c.进刀太快等.a.蓋板,墊板不正确b.靜电吸附等等4.电镀PTH即在不外加电流的情況下,通过镀液的自催化(钯和铜原子作为催化剂)氧化还原反应,使铜离子析镀在经过活化处理的孔壁及铜箔表面上的过程,也称为化学镀铜或自催化镀铜.碱除油→水洗→微蚀→水洗→水洗→预浸→活化→水洗→水洗→速化→水洗→水洗→化学铜→水洗.:a活化钯吸附沉积不好. b速化槽:速化剂浓度不对. c化学铜:温度过低,使反应不能进行反应速度过慢;槽液成分不对.,粗糙: a化学槽有颗粒,铜粉沉积不均,开过滤机过滤. b板材本身孔壁有毛刺.a化学槽成分不对(NaOH浓度过高).4.4镀铜镀铜即提高孔内镀层均匀性,保证整个版面(孔内及孔口附近的整个镀层)镀层厚度达到一定的要求.a电流密度的选择b电镀面积的大小c镀层厚度要求d电镀时间控制1 贯通性:自检QC全检,以40倍放大镜检查孔壁是否有镀铜完全附着贯通.2 表面品质:铜箔表面不可有烧焦,脱皮,颗粒状,针孔及花斑不良等现象.3 附着性:于板边任一处以3M胶带粘贴后,以垂直向上接起不可有脱落现象.5.线路5.1干膜干膜贴在板材上,经曝光后显影后,使线路基本成型,在此过程中干膜主要起到了影象转移的功能,而且在蚀刻的过程中起到保护线路的作用.5.2干膜主要构成:PE,感光阻剂,PET .其中PE和PET只起到了保护和隔离的作用.感光阻剂包括:连接剂,起始剂,单体,粘着促进剂,色料.5.3作业要求a保持干膜和板面的清洁, b平整度,无气泡和皱折现象.. c附着力达到要求,密合度高.5.4作业品质控制要点,应先用无尘纸粘尘滚轮除去铜箔表面杂质.,压力,转数等参数.,不要直接接触铜箔表面.,以防止产生皱折和附着性不良,然后再去曝光,时间太短会使发生的有机聚合反应未完全,太长则不容易被水解,发生残留导致镀层不良.5.5贴干膜品质确认,不可有皱折,气泡.5.6曝光a作业时要保持底片和板子的清洁.b底片与板子应对准,正确.c不可有气泡,杂质.*进行抽真空目的:提高底片与干膜接触的紧密度减少散光现象.*曝光能量的高低对品质也有影响:1能量低,曝光不足,显像后阻剂太软,色泽灰暗,蚀刻时阻剂破坏或浮起,造成线路的断路.2.能量高,则会造成曝光过度,则线路会缩小或曝光区易洗掉.5.7显影,经过(1.0+/-0.1)%的碳酸钠溶液(即显影液)的处理,将未曝光的干膜洗去而保留经曝光发生聚合反应的干膜,使线路基本成型.a﹑显影液的组成b﹑显影温度. c﹑显影压力. d﹑显影液分布的均匀性.e﹑机台转动的速度.,显影温度,显影速度,喷压.a﹑出料口扳子上不应有水滴,应吹干净.b﹑不可以有未撕的干膜保护膜.c﹑显像应该完整,线路不可锯齿状,弯曲,变细等状况.d﹑显像后裸铜面用刀轻刮不可有干膜脱落,否则会影响时刻品质.e﹑干膜线宽与底片线宽控制在+/-0.05mm以内的误差.f﹑线路复杂的一面朝下放置,以避免膜渣残留,减少水池效应引起的显影不均.g﹑根据碳酸钠的溶度,生产面积和使用时间来及时更新影液,保证最佳的显影效果.h﹑应定期清洗槽内和喷管,喷头中之水垢,防止杂质污染板材和造成显影液分布不均匀性.i﹑防止操作中产生卡板,卡板时应停转动装置,立即停止放板,并拿出板材送至显影台中间,如未完全显影,应进行二次显影.j﹑显影吹干后之板子应有绿胶片隔开,防止干膜粘连而影响到时刻品质.5.8蚀刻脱膜,与没有蚀刻阻剂保护的铜发生氧化还原反应,而将不需要的铜反应掉,露出基材再经过脱膜处理后使线路成形.,双氧水,盐酸,软水5.9蚀刻品质控制要点:, 皱折划伤等,无水滴.,不允收出现蚀刻过度而引起的线路变细,和蚀刻不尽.,杂质,铜皮翘起等不良品质。
《FPC设计基础》PPT课件

19
FPC——焊盘设计
可整理ppt
20
FPC——焊盘设计
可整理ppt
21
FPC——提高翘曲强度和翘曲半径
可整理pቤተ መጻሕፍቲ ባይዱt
22
FPC——提高翘曲强度和翘曲半径
可整理ppt
23
FPC——提高翘曲强度和翘曲半径
可整理ppt
24
FPC——提高翘曲强度和翘曲半径
可整理ppt
25
FPC——提高翘曲强度和翘曲半径
可整理ppt
10
FPC板材——有胶&无胶
可整理ppt
11
FPC板材——保护膜( Coverlayer)
可整理ppt
12
FPC材质——品牌
Rogers; Thin Flex(新扬)---Adhesiveless; Kyocera Chemical(Toshiba Chemical); Microcosm(律胜); Dupont(杜邦)--- Adhesiveless; 台虹; 住友。 建议有弯折要求柔板使用Rogers或Thin Flex,一般的单
压延铜:将电解阴极铜淀熔炼成条状物,经延压成形,由于熔炼之故, 成分较单一且结晶分布均匀。因结晶方向平行于软板,所以适用于 频率高的讯号的传递。压延铜特性比电解铜好。其厚度有1/4OZ、 1/3OZ、1/2OZ、1OZ、2OZ几种.
电解铜:利用电镀原理使铜离子沉积在转动之平滑阴极鼓轮 上,然后将铜箔从阴极滚轮上分离而得到有光面和毛面的铜箔,经 过表面处理后可使用。电解铜箔与阴极鼓接触面非常光滑,但是另 外一面因与镀液接触,在高电流密度作用下会粗糙。此粗糙面经表 面处理后可增加表面接触面积而有 利于提高与保护膜之附着性。 其厚度有1/4OZ、1/3OZ、1/2OZ、1OZ、2OZ几种。
柔性电路板(FPC)工艺介绍

FPC压合工艺介绍1.层压工艺流程:叠层→开模→上料→闭模→预压→成型→冷却→开模→下料→检查→下工序2.叠层操作指示:A.生产前准备好离型膜\钢板\硅胶并用粘尘布或粘尘纸清洁钢板\硅胶\离型膜表面灰尘,杂物等.B.将离型膜尺寸开好(500m*500m),放臵在叠层区备用,且每叠层完一个周期的软板,需备用钢板400块,使生产延续不至于断料.C.叠层操作时,需双手戴手套或5指戴手指套,严禁裸手接触软板.D.叠板时先放钢板硅胶离型膜FPC 离型膜硅胶钢板.一直按此叠10层(特殊要求除外)每一层摆放FPC数量以每1PNL板尺寸大小确定一层可摆FPC的数量是多少(板到硅胶四边的距离需保持7cm以上)摆板时应尽量将FPC摆放于硅胶中央部位,且每块板间距为2cm.每一层里面摆放FPC的厚度要一致(例如:单面板不可与多层板混放)每一开口,每一层摆放FPC的图形要一样,且摆放图形的位臵和顺序大致相同.摆放时应将FPC覆膜面或贴补强面朝上.离型膜要平整覆盖于软板上,不能有折皱和折叠现象.操作完毕,将叠层好的FPC平放在运输带上,送至下工序.3.注意事项:叠层时操作必须戴手套或手指套叠层前检查钢板是否有凹凸不平,硅胶是否有破损\裂痕\蜂眼.离型膜是否粘有垃圾.无以上不良现象的钢板\硅胶\离型膜方能使用于生产叠层时摆放FPC的位臵及图形需一致放离型膜时,必须先确认离型膜正反面.确认方法:1.用油性笔在离型膜一角落划一下,如果笔迹很清楚定为反面,不清晰为正面.2.戴白手套触摸离型膜,有一面很光滑可以逻劲的那一面为正面,反之为反面.4.层压操作指示:A.流程: 生产流程:退膜前处理贴合压合电镀层压流程:钻孔→贴BS膜→过塑→压基材→沉镀Cu→干膜→蚀刻→前处理→贴膜→叠层→压合→检查→下工序生产材料配置:名称规格钢板 550*500mm硅胶 500*500mm离型膜 500*500mm5.工艺说明:A.叠层:在叠层台面上放一块钢板\硅胶\离型膜\软板\离型膜\硅胶\钢板\按此顺序以此类推.叠+层为一个开口B.上料:由两人站在两侧,前后一起抓住叠好的10层(一个开口)的板,轻轻慢慢地抬起放到压合机前每一个开口的边缘,慢慢地推到模板的正中间.不允许只抓一层钢板或只推一块钢板,防止钢板\硅胶\软板\离型膜错位及滑动.叠层结构:钢板 ------------------------------------------硅胶**************************离型膜 ------------------------------------------软板++++++++++++++++++++++++++离型膜 ------------------------------------------硅胶**************************钢板------------------------------------------C.压合:将叠层好的板逐个开口放好后,在机台控制面板上按“闭模”键,模板上开到顶部时,会自动停止并进入预压状态.预压10-15分钟后,须将压力调到所压之型号的工艺参数,详见<压制参数一览表>,此时进入成型压合状态.D.冷却:当成型压合时间到了之后,就将控制面板上的冷却水开关打开,进水管的四个阀门也打开,以及加热开关关闭.将温度降至80℃以下后方可下料.并将冷却水开关及进水开关全部关闭.加热开关打开升温为下次作好准备.E.下料:冷却时间足够后,按开模键.压机开始卸压,模板下降到底部时,戴好厚手套,两个人侧分开站好,分别抬出各个开口的10层板.将钢板\硅胶\离型膜一层层掀开,且把钢板\硅胶摆放齐.废离型膜扔到垃圾桶里.压好的软板用PP膠片隔放好.6.工艺控制:A.压合机在压合之前须检查机器台面是否干净,钢板有无变形,硅胶有无破损,离型膜有无皱折.确认好之后方可生产.B.参数设定:温度时间压力175±10℃传压 30-60min 10-15MP固化温度时间150±10℃ 1-2h7.工艺维护、开关机操作和设备维护A.快压\传压开关机a.合上电源总开关,将开关拨到“ON”位臵.电气柜上电源指示灯亮b. 选择手动操作,按下闭模按钮.油泵电机运转,闭模指示灯亮.柱塞在液压作用下带动热板上开\合模,继而升压.当液压缸内的液压力升至表下限时,油泵开始工作.至最上限时泵止.从而完成闭模动作.B.成型结束后,按下开模按钮,电机运转指示灯亮,既开模.当柱塞下降时,撞到触动行开关时,泵停止.C.加热控制系统温度控制是数字温度调节器来实现自动检测.目板的温度可以在电气柜上的调节气器读出,下排是设定温度,上排是实际温度显示.面板上的“OUT/ON键控制加热温度的启动与停止.D.烘箱\开关机a.设定温度及时间,然后按下“启动”键加热器开始加热.b.待加热到设定温度,带上防高温手套,打开烘箱门,把软板放入烘箱内,将烘箱门关上.c.当设定时间到达时,警报器响.这时只需将“电热”键关上,待温度降到50℃以下,方可将软板取出.d.如需重新工作,只要将“电热”键开启即可.8.检验:A.压不实:即包封膜压不结实,紧密.1.线路导体须有以上的间距.2.导体之间的压不实面积超过线距的20%时作返压处理.3.压不实区域长度超过时作返工处理.B.气泡:即包封与铜箔之间充有空气,形状凸起.1.气泡长度≥10mm时判定为NG2.气泡横跨两导体时判定为NG3.气泡接触处形时判定为NGC.线路扭曲1.线路扭曲,扭折现象不允许D.溢胶:包封膜的胶溢出Cu面1.溢胶面积≤时判定为OK.带孔的焊盘溢胶量≤1/4焊盘面积判定OK.孔边焊盘最小可焊量不小于.E.孔内残胶:不允许孔内有残胶F.折痕\压痕\压伤(压断线,造成线路受损作报废处理)表面伤痕长度L≥20mm,且深度明显,不允许其它轻微的可通过U A I处理.G.可靠性能测试:a.剥离程度测试b.热冲击性能测试。
FPC工艺流程介绍 ppt课件
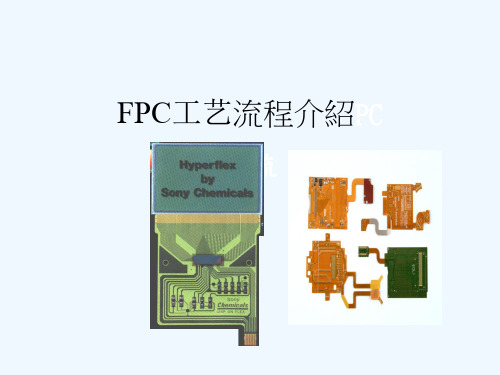
●单面板 P=70~120kg/cm2,T=160~180℃,Time’=5~10S,Time=70~120S
●双面板 P=100~130kg/cm2,T=160~180℃,Time’=5~10S,Time=70~120S
●补强板 P=20~40kg/cm2,T=160~180℃,Time’=5~10S,Time=150~200S
A. B. C. D.
气泡 偏位 溢胶 压痕
FPC工艺流程介绍
丝印感光阻焊可作為軟板外層線路之保護層,具有曝光顯影之特性, 可形成細小結構圖形進行高密度零件組裝。
印刷注意事項
➢ 油墨黏度
➢ 印刷方向(正/反面、前/後方向),依印刷編碼原則區
分正/反面,依印刷對位標示及箭頭標示區分前後方向
➢ 印刷位置度
O O
C
C
R
N
O
n
C
C
O
O
PI結構式
FPC工艺流程介绍
項目
聚銑亞胺 聚酯 聚四氟乙烯
比重
1.42 1.38-1.41 2.15 14.0-24.5 1.1-3.2
拉伸率(%)
70
60-165 100-350
邊緣抗撕裂強度(kg/mm2)
9
17.9-53.6
/
抗拉裂強度(kg/mm2)
SMT。
FPC工艺流程介绍
• 一般均以鋼模(Hard Die)沖軟板外型,其精度較佳,刀 模(Steel Rule Die)一般用於製樣用,或是一般背膠、 PI/PET加強片、等精度要求不高之配件沖型用,亦或 是分條用。當產品長度較長時,鋼模可設計兩段式沖 型,以避免因材料脹縮造成沖偏,此時需採對稱排版, 則僅一套鋼模即可,否則須開兩套鋼模。
fpc生产工艺流程
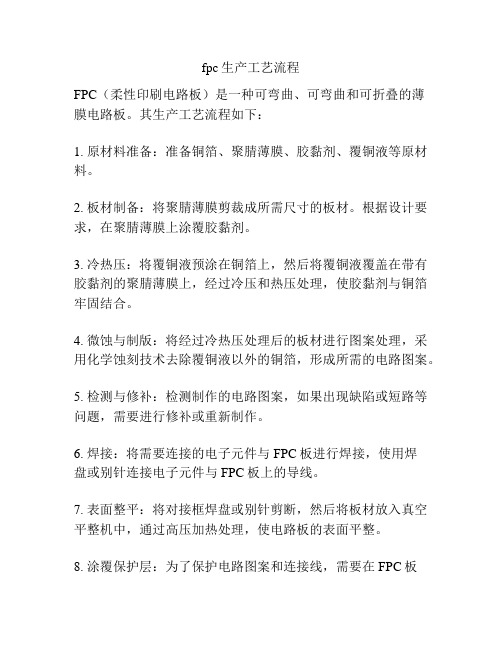
fpc生产工艺流程
FPC(柔性印刷电路板)是一种可弯曲、可弯曲和可折叠的薄
膜电路板。
其生产工艺流程如下:
1. 原材料准备:准备铜箔、聚腈薄膜、胶黏剂、覆铜液等原材料。
2. 板材制备:将聚腈薄膜剪裁成所需尺寸的板材。
根据设计要求,在聚腈薄膜上涂覆胶黏剂。
3. 冷热压:将覆铜液预涂在铜箔上,然后将覆铜液覆盖在带有胶黏剂的聚腈薄膜上,经过冷压和热压处理,使胶黏剂与铜箔牢固结合。
4. 微蚀与制版:将经过冷热压处理后的板材进行图案处理,采用化学蚀刻技术去除覆铜液以外的铜箔,形成所需的电路图案。
5. 检测与修补:检测制作的电路图案,如果出现缺陷或短路等问题,需要进行修补或重新制作。
6. 焊接:将需要连接的电子元件与FPC板进行焊接,使用焊
盘或别针连接电子元件与FPC板上的导线。
7. 表面整平:将对接框焊盘或别针剪断,然后将板材放入真空平整机中,通过高压加热处理,使电路板的表面平整。
8. 涂覆保护层:为了保护电路图案和连接线,需要在FPC板
表面涂覆保护层,防止电路腐蚀、短路和老化。
9. 检测与质量控制:对制作好的FPC板进行严格的检测,包括导通测试、绝缘测试、可靠性测试等,以确保产品质量符合标准要求。
10. 切割与成品加工:根据设计需要,将FPC板切割成所需的大小和形状,然后进行成品加工,如孔洞打孔、焊盘涂锡等。
11. 包装与出货:对成品进行清洁和包装,然后进行验收,最后出货给客户。
以上就是FPC生产工艺流程的大致步骤,每个步骤都需要严格控制和操作,以确保最终产品的质量和可靠性。
不同的制造商可能会在细节上有所不同,但整体流程是相似的。
FPC制造工艺介绍ppt课件

精选2021版课件
16
三、FPC的材料
各种覆盖层的可加工性能比较
类型
厚度 最小孔 最小开 对位精 耐弯 耐焊 材料 加工 (um) 精度 窗 度 曲性 接性 成本 成本
精选2021版课件
13
三、FPC的材料
线路——压延铜箔、电解铜箔、铝蚀刻、溅射铜箔
压延铜箔:纯铜锭经过反复锻压后形成的铜箔,具有良好 的延展性和耐弯曲性能,适宜加工动态FPC。
电解铜箔:经过电解提纯的铜箔,是PCB、静态FPC的理 想材料
铜箔厚度:每平方英寸的重量为1OZ,厚度35.4um;毫 英寸(mil)等于25.4um。常见铜箔厚度0.5oz、1.0oz、 2.0oz,0.5mil、1.0mil、2.0mil。
对位精度 0.05
0.05 0.05
最小加工能力 0.2 0.15 0.5
0.075 0.075
0.3 0.4 0.3
精选2021版课件
21
四、FPC常用的制造工艺流程
常见FPC表面处理方式(单位微英寸)
精选2021版课件
22
四、FPC常用的制造工艺流程
FPC的包装
FPC比较脆弱,尤其是FPC往往有背胶,受到太大压力 挤压时,背胶的胶层会流到FPC表面,因此在包装防护上 需要格外小心。如果像PCB一样要用橡皮筋一扎,或者叠 一叠抽真空包装,是会有大问题的。
常用的的方法,一般是把10~50片FPC叠到一起,用硬纸 板的夹板固定住,再放入干燥剂,密封。硬质板要比FPC 略大。
在装箱时,要使用好的缓冲材料。千万不要为了多装而硬 塞。
《FPC制作流程概述》课件

FPC制作流程的介绍
FPC制作步骤
1
设计
根据需求进行电路图和布局设计。
制图
2
将设计的电路图转化为制图文件。
3
曝光
通过曝光将制图文件转移到感光涂层
蚀刻
4
上。
利用蚀刻液去除未曝光的部分。
材料和设备
材料
使用高温耐受、导电性好的聚 酰亚胺作为FPC的基材。
设备
常用设备包括自动蚀刻机、曝 光机、钻孔机等。
FPC制作的未来发展趋势
灵活性
越来越多的FPC产品会具备 弯曲、折叠等灵活性能。
高密度
FPC制作技术的进步使得电 路板上的线路密度越来越高。
自动化
随着自动化技术的发展, FPC制作的过程将更加高效 和精确。
总结和要点
1 掌握FPC制作流程
了解FPC的制作流程和每个步骤的具体内容。
2 解决常见问题
制造工艺
采用层压、蚀刻、镀铜等工艺 步骤完成FPC的制作。
FPC制作中的常见问题
导பைடு நூலகம்断裂
导线容易因为受力等原因出现断裂现象。
电气性能不稳定
FPC在长时间使用后,电气性能可能会出现不稳定情况。
焊点质量差
焊点接触不良或者溶剂残留可能导致焊点质量差。
解决FPC制作问题的方法
• 通过合理设计来减少导线受力,避免断裂。 • 加强工艺控制,确保FPC制作后的电气性能稳定。 • 严格按照工艺标准进行焊接,避免焊点质量问题。
学会解决FPC制作过程中可能出现的常见问题。
3 关注未来发展
密切关注FPC制作技术的未来发展趋势和新的应用领域。
- 1、下载文档前请自行甄别文档内容的完整性,平台不提供额外的编辑、内容补充、找答案等附加服务。
- 2、"仅部分预览"的文档,不可在线预览部分如存在完整性等问题,可反馈申请退款(可完整预览的文档不适用该条件!)。
- 3、如文档侵犯您的权益,请联系客服反馈,我们会尽快为您处理(人工客服工作时间:9:00-18:30)。
SONY
树脂指标:
含胶量:一般为 45~65%,含量高ε低,击穿电压高,尺寸稳定性差,挥发物 含量高。
流动度:能流动的树脂占树脂总量的百分率,一般为 25~40%,过高易产生缺胶 或贫胶 。
凝胶时间 :一般为 140~190s 挥发物含量:小于等于0.3%,过高层压时易形成气泡; 储存:温度越低越好。
蚀刻反应方程式: Cu +CuCl2 → 2CuCl
2CuCl+H2O2+2HCl→2CuCl2+2H2O l1
蚀刻液温度:40~55℃ h
压力:
蚀刻因子=h/(l2-l1)/2
l2
(over etch under-cut over hang)
剥离药液:1~3%wt NaOH
剥离液温度:40~55℃
所属地域 200强中数 100强中数 50强中数
举
例
中国大陆
5
0
0
超声,深南,大连太平洋,普林,珠海多层
香港
5
4
2
依利,美维,王氏,至卓,Estec
台湾
23
12
8
华通,南亚,楠梓,欣兴,金像,耀文,耀华, 敬鹏
日本
16
14
11
CMK, lbiden, Mektron, 松下,索尼,住友
美国
7
7
4
Viasystems,Multek,IBM,Innovex,M-flex
*喷沙研磨 化学研磨 机械研磨
干膜层压:
SONY
1 、 干膜
聚酯膜 光敏聚合膜 聚乙烯分离层
2 、层压工序
Up roll
D/F
Down roll
Cu
*黏结剂
单体 感光引发剂 增塑层 附着力促进剂 色料
参数设定(参考值):
层压温度(℃) 100~200
压力 (kgf/cm2)
3~5
速度(m/min)
SONY
热压条件:
真空:土耳其袋法、真空框架法、船仓法;
加热方式:油加热、电加热;
压力:用于挤压多层板间空气,并挤压树脂流动填满图形空隙。250~5000PSI
温度 :提供热量促使树脂融化。
温升速率:过快使操作范围变窄,过慢树脂在升温过程中已固化,熔融黏度大,流动
度降低,填充不完全,容易形成间隙,厚薄不均匀。
态黏度,主要由树脂流动曲线决定,曲线可用Haoke Rotiviso锥形或平板黏度计测定。
最低黏度前施加高压较理想,温升过快黏度可达最小,但动态黏度增加较快不利于充
分流动易产生贫胶,过慢树脂逐渐固化,最小黏度偏高,板厚均匀。一般4~8 ℃ /min.
后烘:固化后不可避免地残余了各种应力。后烘可以部分消除板内的残余应力降低板 内的翘曲变形的程度。一般为160 ℃ ,2~4小时。
电镀: 1 、 电镀原理
蚀刻前
蚀刻
SONY
剥离
丝网印刷: 1 、 现像过程
2 、现象相关参数
药液浓度: 0.75%~2%wt Na2CO3 分离点控制:50~70%. 温度:28~32℃ 压力:
SONY
背景资料:
SONY
1、世界PCB制造200强企业在中国大陆设厂,在建的企业:2001.12.25
press press
SUS
TPX FPC TPX
橡胶板 厚纸板
SUS
SONY
压力曲线 温度曲线
时间(分)
*半固化片树脂: A 阶: 在室温下能够完全流动的液态树脂; B 阶: 环氧树脂部分交联于半固化状态,它在加热条件下又 能恢复到液态;
C 阶:树脂全部交联,加热加压软化,但不能再成为液态热压:
SONY
1、热压过程
SUS
盖膜
FPC
蚀刻后 的产品
2 、热压构成材料的作用
TPX FPC TPX Rubber Paper SUS
离形纸 :PTFE离形纸主要作用是便于多层板表面铜箔与分隔板分离,保护分隔板;
缓冲纸:牛皮纸硅橡胶降低传热速率,缩小多层板层与层之间的温差。
3、热压原理及条件设定
107
压制周期:一步法、二步法。
106
一步法适用于低(<18%)流动度半固化片压制; 二步法适用于中(>20%)或高流动度半固化片。 压力变化分预压和高压;
105
104
103 102 80 100 120 140 160 180 200
T(℃)
预压使熔融树脂润湿挤出内层图形间的气体并用树脂填充图形间隙及逐渐提高树脂动
SONY
FPC制造流程
SCSC 王益国 2002年1月25日
前处理:
SONY
1 、 铜箔材料 铜箔
黏结剂 基膜
Cu 类型 Cu 厚度 基膜
2 、前处理
电解(ED) 、压延(RA)等 12、18 (1/2OZ)、35 (1OZ)μm 聚酰亚胺 (PI) 、聚酯(PET)
W3~4μm
机械研磨
D2~2.5μm
曝光:
1 、 曝光过程
SONY
重氮片 底片保护膜
2 、 干膜光阻的感光聚合过程
紫外光照射→引发剂裂解→出现自由基→单体吸收自由基 →形成聚合体 →显影
3 、 曝光相关参数
曝光能量:30~90mj/cm2 mj (milli-joule) 测试工具: 光量计和段位尺 采用透明棕色重氮片
D max 指棕色遮光部分的密度; D min指透光部分的密度; D=-Log T T=It/I; I 入射光强度;It 透射光强度。 一般要求 D max 〉3.5 (0.03%) and D min〈0.17 (70%)
欧洲
2
2
2
AT&S,Aspocomp
新加坡
2
1
0
Gul,Pentex
韩国
1
1
1
三星
共计
61
41
28
背景资料:
SONY
1、世界PCB制造200强企业在中国大陆设厂,在建的企业:2001.12.25
SONY
4、 曝光设备及注意事项
灯管:365~380nm 汞灯,平行光; 曝光机要求平行半角b在2°左右,斜射角a在1.5°以下。 注意事项: 1、底片药膜面务必朝下,使其紧贴干膜抗蚀剂; 2、真空度要好;
Mylar上需有牛顿环出现且不可移动; 导气条及赶气刮刀:导气条置于板边连接底片和排气沟,用赶气 刮刀协助排气。 3、越薄,解像度越好; 4、工作中将底片之线宽放大1~2mil; 5、撕掉P再曝光。
Have Newton roll and not mover
现象: 1 、 现像过程
2 、现象相关参数
药液浓度: 0.75%~2%wt Na2CO3 分离点控制:50~70%. 温度:28~32℃ 压力:
SONY
蚀刻和剥离: 1 、 蚀刻和剥离过程
蚀刻前
蚀刻
SONY
剥离
SONY
2 、蚀刻原理和参数控制