3.控制轧制的基本概念
控制轧制

控制轧制与控制冷却的概念
控制轧制(Controlled rolling) 在热轧过程中,通过对金属加热制度、变形制度和温度
制度的合理控制,使热塑性变形与固态相变相结合,以获得 细小晶粒组织,从而得到较高的综合性能的轧制工艺。
控制冷却(Controlled cooling) 控制轧后钢材的冷却速度达到改善钢材组织和性能的目
淬火
1、定义: 淬火是将钢加热到AC1或 AC3以上温度并保温,
出炉快速冷却,使奥氏体转变成为马氏体的热处理 工艺。
回火
1、定义:回火是把淬火后的钢件,重新加热到A1以 下某一温度,经保温后空冷至室温的热处理工艺。
2、目的:淬火钢件经回火可以减少或消除淬火应力, 稳定组织,提高钢的塑性和韧性,从而使钢的强度、 硬度和塑性、韧性得到适当配合,以满足不同工件 的性能要求。
载荷P压入被测材料表面,保持一定时间后卸除载荷,测出压 痕直径d,求出压痕面积F计算出平均应力值,以此为布氏硬度 值的计量指标,并用符号HB表示。
标注:D/P/T如120HB/10/3000/10,即表示此硬度值120 在D=10mm,P=3000kgf,T=10秒的条件下得到的。
简单标注:200~230HB
工艺性能:是指制造工艺过程中材料适应 加工的性能。如:铸造性、锻造性、焊接 性、切削加工性、热处理工艺性。
金属材料的性能
一、金属材料的机械性能
机械性能— 是指金属材料在外力作用时表现出来的性能。 外力形式:拉伸、压缩、弯曲、剪切、扭转等。 载荷形式:静载荷、冲击载荷、交变载荷等。
指标:强度、刚度、硬度、塑性、韧性和疲劳强度等。
残余压入深度
来表示
为了与习惯上数值越大硬度越高的概念相一 致采用一常数(k)减去(h3-h1)的差值表示硬 度值。为了简便起见又规定每0.002mm压入深度 作为一个硬度单位(即刻度盘上一小格。)
控制轧制与控制冷却培训

控制轧制与控制冷却培训一、轧制的基本原理和过程1. 轧制的概念和分类:介绍了轧制的定义和轧制根据加工方式和加工精度的不同可以分为粗轧和精轧。
2. 轧制的基本原理:介绍了轧制的原理,包括材料变形、变形力和摩擦力。
3. 操作技巧和注意事项:介绍了轧机的操作技巧和相关的注意事项,包括轧机的启动、停止和维护等内容。
二、控制轧制的关键参数1. 温度控制:介绍了轧制过程中温度的控制方法和关键参数。
2. 轧制力和轧制速度:介绍了轧制过程中轧辊的力和速度的控制方法和关键参数。
3. 压下量:介绍了轧制过程中的压下量的控制方法和关键参数。
三、冷却的基本原理和过程1. 冷却的概念和分类:介绍了冷却的定义和冷却方式的分类。
2. 冷却的基本原理:介绍了冷却的原理,包括热量传递和温度控制。
3. 操作技巧和注意事项:介绍了冷却设备的操作技巧和相关的注意事项,包括冷却水的供应和冷却温度的控制等内容。
四、控制冷却的关键参数1. 冷却水温度:介绍了冷却过程中冷却水温度的控制方法和关键参数。
2. 冷却水流量:介绍了冷却过程中冷却水流量的控制方法和关键参数。
3. 冷却时间:介绍了冷却过程中冷却时间的控制方法和关键参数。
五、轧制与冷却的协调控制1. 轧制和冷却的关联性:介绍了轧制和冷却之间的关联性,以及对产品性能和质量的影响。
2. 控制系统的应用:介绍了轧制和冷却中常用的控制系统,包括自动控制系统和人工控制系统等。
3. 故障处理和维护:介绍了轧制和冷却中常见的故障处理方法和设备维护技巧。
以上是本次控制轧制与控制冷却培训的主要内容概要,希望通过此次培训,能够提高操作工人对控制轧制与控制冷却的理解和技能,为公司的生产和产品质量提升贡献力量。
六、安全生产培训1. 轧制和冷却设备的安全操作规程:介绍了轧制和冷却设备的安全操作规程,包括设备启动、停止和紧急情况的处理等内容,以确保操作人员的安全。
2. 安全防护措施:介绍了轧制和冷却设备的安全防护措施,包括安全防护装置的使用和维护,以减少事故发生的可能性。
轧钢车间各工种基本知识问题

1、CP2、CP3、CP4所属设备名称、功能、动作原理、检测原理、润滑制度。
2、了轧制温度、轧制电流、轧制力概念和相互关系、轧机允许最大轧制负荷。
3、轧制变形原理、延伸和宽展关系,掌握H型钢尺寸的控制和基本缺陷的调整。
4、钢温、钢种变化对轧制、成品尺寸的影响,掌握对应的调整方法。
5、换辊、调零步骤,各光电管的作用,掌握测辊缝和轧制线、开口度的方法。
6、自动轧制时的顺控步骤,了解出UF轧件条形对4#台锯切的影响。
7、掌握CP3各种图表的调用、输入、检查和传输。
8、了解我厂原料种类、钢种、米重及各种原料所轧品种。
9、什么叫钢?10、什么叫轧钢,怎样分类?11、什么叫热轧和冷轧?12、什么叫钢的塑性?13、什么叫强度指标、塑性指标、冷弯变形指标?14、怎样实现正常咬入?15、影响轧制压力的因素有哪些?16、什么叫控制轧制?17、什么叫辊跳,它对轧钢有什么影响?18、轧制前要做好哪些准备工作?19、什么叫最小阻力定律?20、什么叫孔型,导卫的基本作用是什么?21、什么叫变形抗力、应力、残余应力?22、什么叫体积不变原理?23、什么叫坐辊?24、什么叫金属的屈服强度?25、何为宽展,有几种形式,举例我厂生产的产品规格各归何种形式宽展?26、改善咬入条件的措施有哪些?27、开轧前轧机要检查哪些项目?28、我厂轧机调零过程及作用是什么?29、我厂轧机为何要使用液压安全接手?30、金属的机械性能指什么?31、断辊的原因及预防措施有哪些?32、轧辊产生裂纹的原因及预防措施有哪些?33、举例说明如何根据成品定尺要求选择原料长度?34、如何确定轧边机宽度和成品UF宽度,为什么?二、原料工基本知识问题1、我厂轧钢生产的工艺流程是什么?2、连铸坯验收标准是什么?3、钢牌号中各符号的代表含义是什么?4、原料的常见缺陷有哪些?它对产品有什么影响?5、原料库管理流程是什么?6、编排轧制计划注意事项有哪些?1、什么叫高炉煤气、焦炉煤气?2、什么是完全燃烧、不完全燃烧?3、什么叫回火、脱火?4、什么叫空气过剩系数?5、什么叫着火温度?6、什么是煤气中毒?7、什么叫爆炸、爆炸极限?8、什么叫氧化、脱碳、过热、过烧?9、什么叫碳素钢、低合金钢?10、步进式加热炉的特点是什么?11、除鳞框有几种规格?轧制不同原料时,除鳞机的进出口导板位置是多少?12、除鳞泵的进水压力最低需多少?出水压力与蓄能器水位一般在多少才能保证正常除鳞?13、简述光电管测长的原理?14、进钢时哪几种长度的钢坯自动定位最靠炉子北侧?步进梁前进与提升的最大行程是多少?步进周期为多少时间?15、步进梁冷却水管的水温正常是多少?16、加热炉冷却水分哪几类,各自的作用是什么?17、步进梁各动梁、各定梁之间的间距有多大?18、各组出炉辊道上光电管的作用是什么?19、简述平焰烧嘴与直焰烧嘴各自的特点?20、加热炉热电偶的分布情况是什么?21、简述加热炉烧嘴及各段的分布?22、主管与八个段的煤气截止阀、流量阀及放散阀的位置是什么?23、简述冷炉点火的步骤?24、造成炉子熄火的原因有哪些?25、什么是空燃比?合理的空燃比对加热有什么好处?26、钢的加热目的、加热要求是什么?27、传热有几种方式?简述钢在炉内的传热过程?28、加热制度包括哪几个方面?29、什么是温度制度?三段式温度制度的特点?30、钢的加热温度主要取决于什么?一般说来温度过高或过低有何影响?31、何为加热速度?在加热速度方面普碳钢与合金钢有何差异?32、钢坯的加热时间指什么?加热时间过长或过短对钢坯有何影响?33、钢坯的加热缺陷有哪些?怎样预防?怎样处理?34、试述几条减少加热不均的方法?35、正常状态下三段式加热炉的炉内气氛如何?36、何为微正压,炉压的大小对炉子有何影响?37、停轧保温制度的内容及作用?38、降低烟气温度的方法是什么?39、换热器的作用是什么?40、CO的浓度与允许工作时间的关系是什么?41、如何进行煤气中毒人员的急救?42、焦炉煤气与高炉煤气的爆炸极限是多少?43、如何处理煤气着火事故?44、如何处理煤气爆炸事故?45、使用氧气呼吸器的注意事项有哪些?46、煤气的基本成分是什么?47、什么是煤气的热值?它对炉子产量有何影响?48、什么叫理论空气量?49、如何提高加热炉的热效率?50、加热炉点火、熄火的主要操作步骤是什么?51、哪些事故影响加热炉熄火?52、什么是按炉送钢制度?53、钢坯表面氧化后由里向外依次氧化物的成分是什么?54、减少钢坯氧化的措施是什么?55、加热炉点火前应作好哪些准备工作?56、加热炉熄火后的操作步骤有哪些?四、行车工基本知识问题1 熟悉本车间天车性能、结构,相关参数及保养方法。
控制轧制和控制冷却的理论及实践概论

1.2 板带产品的力学性能
图2 低碳钢拉伸时的应力-应变曲线
强度指标
比 例 极 限 σP - 应 力 、 应 变 能 保持比例关系时的最大应力
弹 性 极 限 σe - 完 全 卸 载 后 不 出现任何明显残余应变的最 大应力
屈 服 强 度 σS - 有 明 显 上 、 下 屈服点时,用下屈服点对应 的应力表示,无明显屈服点 时,以试样残余应变达到0.2 %时的应力表示,标为σ0.2
2.1 钢材热轧过程中的组织性能变化
再结晶奥氏体的长大过程
图8 Q345钢不同停隔时间的奥氏体组织
晶 粒尺寸,um
200
心 部晶 粒 尺寸
180
边 部晶 粒 尺寸
a 160
f
140
120
e
100
d
80 b
c
60 0
10 20 30 40 50 60
保 温时 间,s
图9 奥氏体晶粒的长大过程
再结晶行为对组织性能的影响
减少游离氮
生产方法 合理选择化学成分
控制轧制 控制冷却
TMCP 热处理 (常化)
热处理 (淬火+回火)
板带轧制过程中的质量性能控制
1.板带产品的质量性能指标 1.1 板带产品的形状、尺寸 1.2 板带产品的力学性能
2.板带轧制过程中的质量性能控制 2.1 钢材热轧过程中的组织性能变化 2.2 板带轧制过程中的组织性能控制 2.3 板带钢生产工艺优化的典型示例分析
0.8
900℃
850℃
800℃
0.6
750℃
700℃
0.4
0.2
0.0
100
101
1பைடு நூலகம்2
控轧控冷总论
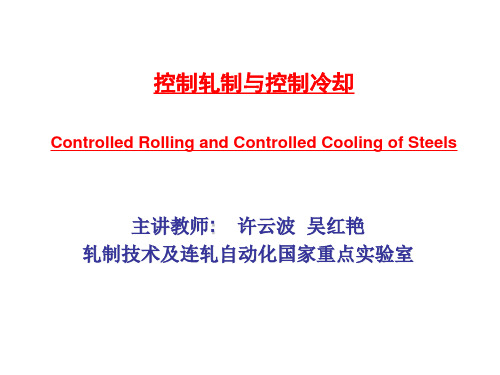
钢的形变热处理
• 钢的形变热处理(TMCP)是指如下工艺过程:控制奥氏体化温度、
变形温度和变形量, 获得理想的奥氏体初始状态; 变形后利用余热控
制冷却, 获得所希望的显微组织, 从而达到控制金属性能的目的。 • 控制轧制和控制冷却技术结合起来,能够进一步提高钢材的强韧性和
获得合理的综合性能,并能够降低合金元素含量和碳含量,节约贵重
艺综合在一起, 成为一个紧密联系的材料体系。
控制轧制的分类 – – – 奥氏体再结晶控制轧制(I 型控制轧制) 奥氏体未再结晶控制轧制(II 型控制轧制) (+)两相区控制轧制
1.1 控制冷却的概念
• 通过控制热轧钢材轧后的冷却条件来控制奥氏体组织状态、控制相变条件、 控制碳化物析出行为、控制相变后钢的组织和性能。 • 现代在线控制冷却工艺的一个重要的金属学特征就是对变形了的未再结晶 奥氏体或再结晶奥氏体进行控制轧制,可根据不同的需要进行不同的组织
控制轧制与控制冷却
Controlled Rolling and Controlled Cooling of Steels
主讲教师: 许云波 吴红艳 轧制技术及连轧自动化国家重点实验室
目
1. 总论
2. 钢的高温变形行为
录
3. 钢的热变形后的相变行为
4. 强韧性能的基本概念及有关理论
5. 钢材的控制轧制理论基础及应用
6. 钢材轧后控制论却技术的基础及应用
7. 钢材的控制轧制和控制冷却技术的结合及应用
1总 论
• 目的: – 了解钢材热加工过程中的形变机理,相变与析出,再结晶行为、强韧化 机制等控制轧制控制冷却工艺的基本原理
– 了解钢材在热加工过程(热轧)的组织演变规律
– 初步具备对不同规律进行定量化或半定量化处理分析的能力 – 在实际生产和科研中应用控制轧制原理 • 金属塑性成型(轧钢): – 定义:金属在外力的作用下,产生塑性变形的过程,它不仅可使金属获 得所必需的尺寸和形状,而且也使之获得所必需的组织和性能。 – 目标:尺寸和外形满足产品标准的公差要求;性能满足产品标准的公差 要求。
钢材的控制轧制和控制冷却
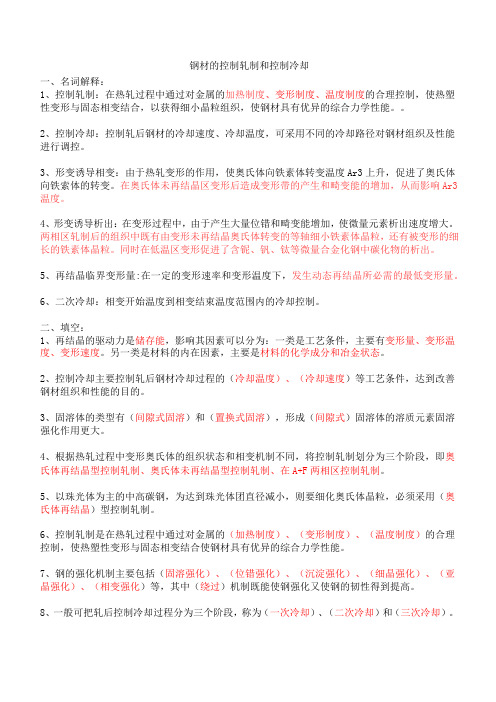
钢材的控制轧制和控制冷却一、名词解释:1、控制轧制:在热轧过程中通过对金属的加热制度、变形制度、温度制度的合理控制,使热塑性变形与固态相变结合,以获得细小晶粒组织,使钢材具有优异的综合力学性能。
2、控制冷却:控制轧后钢材的冷却速度、冷却温度,可采用不同的冷却路径对钢材组织及性能进行调控。
3、形变诱导相变:由于热轧变形的作用,使奥氏体向铁素体转变温度Ar3上升,促进了奥氏体向铁索体的转变。
在奥氏体未再结晶区变形后造成变形带的产生和畸变能的增加,从而影响Ar3温度。
4、形变诱导析出:在变形过程中,由于产生大量位错和畸变能增加,使微量元素析出速度增大。
两相区轧制后的组织中既有由变形未再结晶奥氏体转变的等轴细小铁素体晶粒,还有被变形的细长的铁素体晶粒。
同时在低温区变形促进了含铌、钒、钛等微量合金化钢中碳化物的析出。
5、再结晶临界变形量:在一定的变形速率和变形温度下,发生动态再结晶所必需的最低变形量。
6、二次冷却:相变开始温度到相变结束温度范围内的冷却控制。
二、填空:1、再结晶的驱动力是储存能,影响其因素可以分为:一类是工艺条件,主要有变形量、变形温度、变形速度。
另一类是材料的内在因素,主要是材料的化学成分和冶金状态。
2、控制冷却主要控制轧后钢材冷却过程的(冷却温度)、(冷却速度)等工艺条件,达到改善钢材组织和性能的目的。
3、固溶体的类型有(间隙式固溶)和(置换式固溶),形成(间隙式)固溶体的溶质元素固溶强化作用更大。
4、根据热轧过程中变形奥氏体的组织状态和相变机制不同,将控制轧制划分为三个阶段,即奥氏体再结晶型控制轧制、奥氏体未再结晶型控制轧制、在A+F两相区控制轧制。
5、以珠光体为主的中高碳钢,为达到珠光体团直径减小,则要细化奥氏体晶粒,必须采用(奥氏体再结晶)型控制轧制。
6、控制轧制是在热轧过程中通过对金属的(加热制度)、(变形制度)、(温度制度)的合理控制,使热塑性变形与固态相变结合使钢材具有优异的综合力学性能。
控制轧制
淬 火
1、定义: 定义: 淬火是将钢加热到A 以上温度并保温, 淬火是将钢加热到AC1或 AC3以上温度并保温, 出炉快速冷却, 出炉快速冷却,使奥氏体转变成为马氏体的热处理 工艺。 工艺。
回 火
1、定义:回火是把淬火后的钢件,重新加热到A1以 定义:回火是把淬火后的钢件,重新加热到A 下某一温度,经保温后空冷至室温的热处理工艺。 下某一温度,经保温后空冷至室温的热处理工艺。 2、目的:淬火钢件经回火可以减少或消除淬火应力, 目的:淬火钢件经回火可以减少或消除淬火应力, 稳定组织, 提高钢的塑性和韧性, 从而使钢的强度、 稳定组织 , 提高钢的塑性和韧性 , 从而使钢的强度 、 硬度和塑性、 韧性得到适当配合, 硬度和塑性 、 韧性得到适当配合 , 以满足不同工件 的性能要求。 的性能要求。
洛氏硬度值公式如下: 洛氏硬度值公式如下:
采用金钢石圆锥时k=0.2(用于HRA,HRC) (用于 采用金钢石圆锥时 , ) 用钢球时k=0.26(用于HRB)。 (用于 用钢球时 )。
硬度符号
压头
总载荷 (kgf)
表盘上刻度 颜色
常用硬度值 范围
使用范围
HRA
金钢石圆锥
60
黑 色
70~85
碳化物、硬质合金表 面淬火等
布氏硬度测定主要适用于各种未经淬火的钢、退火、 各种未经淬火的钢、退火、
②洛氏硬度(HR) 洛氏硬度(
基本原理— 基本原理 — 洛氏硬度属压入法洛氏硬度测定时需 要先后施加二次载荷(予载荷P1和主载荷 和主载荷P2) 要先后施加二次载荷 (予载荷 和主载荷 ) 预 加载荷的目的是使压头与试样表面接触良好以保 证测量结果准确。 证测量结果准确。洛氏硬度就是以主载荷引起的 残余压入深度 来表示
控制轧制
线材的控制轧制摘要:结合控制轧制技术的发展,针对线材的轧制工艺,对高速线材的控制轧制系统、控制轧制方式及特点、生产中的技术关键分析,清晰指出了控制轧制在高速线材生产中的重要地位,更加明确了控制轧制的研究方向。
关键字:控制轧制高速线材工艺手段1对控制轧制认识1.1 控制轧制的发展历程油气输送管线钢是控轧控冷技术应用最早和最广泛的领域。
1963年开发了一种屈服强度为352.8 MPa的X52含Nb半镇静钢;20世纪70年代相继开发出寒冷地带油气管线用X60,X65和X70等热轧卷板;80年代后采用控车UJll速冷却工艺相继生产出X80,X100和X120等高性能管线钢。
目前,管线钢的控制轧制和控制冷却技术已发展到一个新的阶段。
热轧过程的计算机控制与热加工物理冶金学相结合,已能对轧制过程中的温度变化、显微组织类型、晶粒尺寸、奥氏体未再结晶区的积累应变、α中残余应变和微合金元素的沉淀动力学等进行有效地控制和准确地预测,为开发具有更佳力学性能的管线钢开辟了广阔的途径。
1.2控制轧制概念及机理控制轧制(Controlled rolling)是在热轧过程中通过对金属加热制度、变形制度和温度制度的合理控制,使热塑性变形与固态相变结合,以获得细小晶粒组织,使钢材具有优异的综合力学性能的轧制新工艺;其机理是:热塑性变形过程中或变形之后的钢组织的再结晶在控制轧制中起决定作用,奥氏体晶粒的细化是控制轧制的基础。
热变形从形变的角度考虑是降低变形抗力和提高钢的塑性变形能力。
从组织控制的角度考虑是:完成钢的奥氏体组织的控制;在一定的奥氏体组织条件下进行形变,通过对形变条件的控制,实现对变形过程中组织的控制为相变做组织准备;控制相变过程,以获得要求的组织和性能。
不同的相变前的奥氏体组织,相变后组织就会不同,性能就不同。
奥氏体化条件不同、形变条件的不同,热变形过程中会出现不同的动态回复过程(动态回复、动态再结晶)、静态回复过程(静态回复、静态再结晶),而不同的回复过程会形成各种热变形条件下钢的组织变化。
控制轧制于控制冷却
1、控制轧制:在热轧过程中,通过对金属加热制度、变形制度和温度制度的合理控制,使热塑性形变与固态相变相结合,以获得细小的晶粒组织,使钢材具有优异的综合力学性能的轧制技术2、控制冷却:通过对控制轧后的钢材的冷却速度来改善钢材的组织性能.3、金属的强化:通过合金化,塑性变形和热处理等手段来提高金属的强度.4、固溶强化:添加溶质元素使固溶体强度提高的方法。
5、韧性:材料在塑性变形和断裂所吸收能量的能力。
6、微合金钢:钢种的合金含量小于0。
1%。
7、IF钢:无间隙原子钢8、不锈钢:具有良好的抗腐蚀性能和抗氧化性的钢.9、变形抗力:在一定条件下材料变形单位面积的抵抗变形的力。
10、在线常化工艺:在热轧无缝钢管中在轧管延伸工序后将钢管按常化热处理要求冷却到某一温度后在进加热炉然后就行减径轧制按照一定的速度冷却到常温。
11、变形温度贝氏体处理化工艺:在钢管轧制过程中不直接加热到马氏体温度一下,而是快速冷却带中温以后再置于静止的空气中冷却、以变形奥氏体转变为贝氏体省去回火工序。
12、高温变形淬火:钢管在稳定的奥氏体区域变形,而且一般温度在再结晶温度以上然后进行淬火,已获得马氏体组织。
13、低温相变淬火:将钢管加热到奥氏体状态,经一段保温冷却到Ac1高于M的某一中间温度进行变形后淬火的工艺。
14、非调质钢:将调质钢的化学成分进行调解并对轧制过程进行控制不进行调制其性能达到调制的水平。
1、控制轧制是指在热轧过程中通过对金属加热制度,温度制度,保险制度的控制而获得细小的晶粒2、控制冷却是控制轧后钢材的冷却速度来改善组织性能。
3、钢材的强化方法有固溶强化,变形强化,沉淀强化,弥散强化,亚晶强化,细晶强化,相变强化.4、影响材料韧性有,化学成分,气体和夹杂物,晶粒细化,形变的影响,形变细化5、动态结晶是晶粒细化提高扩孔性的手段6、控制轧制的目标是为了获得较小的铁素体组织7、加快冷却速度可以获得细小的铁素体晶粒所以不产生奥氏体组织为界限8、贝氏体是结构性能钢有校坏的塑形焊接性能强韧性微合金钢是指钢中的合金元素总量小于0.1%的钢在控制轧制中使用最多的微合金元素有银,钛,钒9、钢通常是指含碳量在0.28-2。
控制轧制与控制冷却要点
我国控轧控冷技术概况
❖ 我国控制控冷起步于60年代初,并取得了 初步成果,例如对含有Cr、Ni、V的超高 强度钢德形变热处理工艺研究,轴承钢轧 后快冷工艺研究等;
❖ 1978年开始对控制控冷进行系统研究; ❖ 武钢、鞍钢、重钢、太钢等钢铁企业采用
控制控冷技术生产高强度、高韧性的造船、 锅炉及压力容器用各种钢材,开发了新钢 种,填补了国内钢材的部分空白。
控制轧制和控制冷却要点
控制轧制和控制冷却概念
❖ 控制冷却(Controlled Cooling):控 制轧制后钢材的冷却速度达到改善钢材组 织和性能的目的。 控制轧制和控制冷却相结合能将热轧钢 材的两种强化效果相加,进一步提高钢材 的强韧性和获得合理的综合力学性能。 目前,控制轧制和控制冷却工艺已应用 到中、高碳钢和合金钢的轧制生产中,取 得了明显的经济效果。
❖ 钢铁冶金学报
控制轧制和控制冷却要点
控制轧制和控制冷却概念
❖ 控制轧制(Controlled Rolling):在热 轧过程中通过对金属加热制度、变形制度和 温度制度的合理控制,使塑性变形与固态相 变结合,以获得细小晶粒组织,使钢材具有 优异的综合力学性能的轧制新工艺。
对低碳钢和低合金钢来说,采用控制轧制 工艺主要通过控制工艺参数,细化变形γ晶 粒,经过γ向α和P的相变,形成细化的α和 较为细小的P球团,从而达到提高钢的强度、 韧性和焊接性能的目的。
❖ 第二篇:控制轧制及控制冷却技术的应用
➢ 控制轧制及控制冷却技术在钢板生产中的应用 ➢ 控制轧制及控制冷却技术在型钢生产中的应用 ➢ 控制轧制及控制冷却技术在钢管生产中的应用
控制轧制和控制冷却要点
教学安排
❖ 教学:本课程2学分,总课时为32学时,每 周2学时,1-16周上课。
- 1、下载文档前请自行甄别文档内容的完整性,平台不提供额外的编辑、内容补充、找答案等附加服务。
- 2、"仅部分预览"的文档,不可在线预览部分如存在完整性等问题,可反馈申请退款(可完整预览的文档不适用该条件!)。
- 3、如文档侵犯您的权益,请联系客服反馈,我们会尽快为您处理(人工客服工作时间:9:00-18:30)。
六十年代后期:美国采用控制轧制工艺生产出 六十年代后期:美国采用控制轧制工艺生产出σs> 422MPa的含 钢板,用来制造大口径输油钢管。日 的含Nb钢板 用来制造大口径输油钢管。 的含 钢板, 本用控制轧制工艺生产出强度高,低温韧性好的钢板, 本用控制轧制工艺生产出强度高,低温韧性好的钢板, 并开发出一系列新的控制轧制工艺, 并开发出一系列新的控制轧制工艺,提出了相应的控 制轧制理论。这期间人们重视奥氏体再结晶行为的研 制轧制理论。 究,开始认识到未再结晶区轧制的重要性。 开始认识到未再结晶区轧制的重要性。 七十年代:完成了控轧三阶段, 、 、 应用逐步 七十年代:完成了控轧三阶段,Nb、V、Ti应用逐步 完善。 完善。
控轧分类 1.奥氏体再结晶区控制轧制(Ⅰ型控制轧制) 奥氏体再结晶区控制轧制( 型控制轧制) 奥氏体再结晶区控制轧制 2.奥氏体未再结晶区控制轧制(Ⅱ型控制轧制) 奥氏体未再结晶区控制轧制( 型控制轧制) 奥氏体未再结晶区控制轧制 3.(r+α)两相区控制轧制 ( )
3.2 控轧工艺特点 一.控制加热温度 控制加热温度 二.控制轧制温 控制轧制温度 三.控制变形程度 控制变形程度 四.控制轧后冷却速度 控制轧后冷却速度 3.3 控轧的效应 一.提高综合性能 提高综合性能 既提高强度,又改善韧性,尤其是钢的 既提高强度,又改善韧性,尤其是钢的Tvs ↓↓ 二.简化工艺 简化工艺 三 . 节省合金元素 控制轧制可充分发挥Nb、 、 等微量合金元素的作用 控制轧制可充分发挥 、V、Ti等微量合金元素的作用 1
六十年代初:英国斯温顿研究所提出,铁素体 六十年代初:英国斯温顿研究所提出,铁素体微组织与性能之间的定量关系。 珠光体钢中显 微组织与性能之间的定量关系。 著名的Petch关系式明确表明了热轧时晶粒细化 关系式明确表明了热轧时晶粒细化 著名的 的重要性。 的重要性。 六十年代中期: 六十年代中期:英国钢铁研究会进行了一系列 研究:降碳改善塑性和焊接性能,利用 、 研究:降碳改善塑性和焊接性能,利用Nb、V 获得高强度, 对奥氏体再结晶的抑制作用以 获得高强度,Nb对奥氏体再结晶的抑制作用以 及细化奥氏体晶粒的各种途径。 及细化奥氏体晶粒的各种途径。
1.再结晶热轧 再结晶热轧
2.板材加速冷却 板材加速冷却 水——钢的最有效的合金化添加剂 钢的最有效的合金化添加剂
1. 控轧工艺分哪几类?控轧实践中最常用的 控轧工艺分哪几类? 是哪种工艺?分别画出示意图。 是哪种工艺?分别画出示意图。 2.Ⅰ型控轧与Ⅱ型控轧相比,哪种工艺轧材 Ⅰ型控轧与Ⅱ型控轧相比, 的性能更好些?为什么? 的性能更好些?为什么? 3.如何理解“水是最有效的合金化添加剂”这 如何理解“ 如何理解 水是最有效的合金化添加剂” 句话 ? 4. 对结构钢的要求有哪些要素 ?
3 控制轧制的基本概述
3.1 控制轧制概念 对结构钢要求的三要素:高强度、高韧性和 对结构钢要求的三要素:高强度、高韧性和良好的焊接性能 过去几十年中对热轧材强化的传统方法是: 过去几十年中对热轧材强化的传统方法是: ①采用合金化 强度↑,韧性↓ 强度和韧性 、 强度和可焊性之间的矛盾 强度 ,韧性 ②采用轧后热处理 增加了工序,增加燃料消耗,增加成本, 增加了工序,增加燃料消耗,增加成本,降低生产率
6
3.4 控制轧制的发展历程 上世纪二十年代: 上世纪二十年代:开始研究温度和变形对显微组织和力学性能 的影响。 的影响。 三、四十年代:荷兰、比利时、瑞典等国一些没有热处理设备 四十年代:荷兰、比利时、 的轧钢厂,为了提高钢的强度和韧性, 的轧钢厂,为了提高钢的强度和韧性,将终轧温度控制在 900℃以下,并给予20~30%的道次压下率,生产出具有良 ℃以下,并给予 的道次压下率, 的道次压下率 好韧性的钢材。这就形成了采用“低温大压下” 好韧性的钢材。这就形成了采用“低温大压下”细化低碳钢 的铁素体晶粒,提高强韧性的“控制轧制”的最初概念。 的铁素体晶粒,提高强韧性的“控制轧制”的最初概念。 五十年代末: 五十年代末:美国和原苏联等国先后开展了钢的形变热处理工 艺与钢材组织和性能关系的理论研究工作。 艺与钢材组织和性能关系的理论研究工作。
定义: 定义: 控制轧制( 控制轧制(Controlled rolling)是在热轧过程中 ) 通过对金属加热制度、 通过对金属加热制度、变形制度和温度制度的合理 控制,使热塑性变形与固态相变结合, 控制,使热塑性变形与固态相变结合,以获得细小 晶粒组织,使钢材具有优异的综合力学性能的轧制 晶粒组织, 新工艺。 新工艺。 控制冷却( 控制冷却(Controlled Cooling)是控制轧后钢材 ) 的冷却速度达到改善钢材组织和性能的目的。 的冷却速度达到改善钢材组织和性能的目的。
钢的成分 % 0.14C+1.3Mn 0.14C+0.034Nb 0.14C+0.08V 0.14C+0.004Nb +0.06V
常规轧制 σs N/mm2 313.9 392.4 421.8 FATT℃ ℃ +10 +50 +40
控制轧制 σs N/mm2 372.7 441.3 451.1 490.3 FATT℃ ℃ -10 -50 -25 -70