DS型硫泡沫过滤机
德国欧亚瑟过滤桶评价
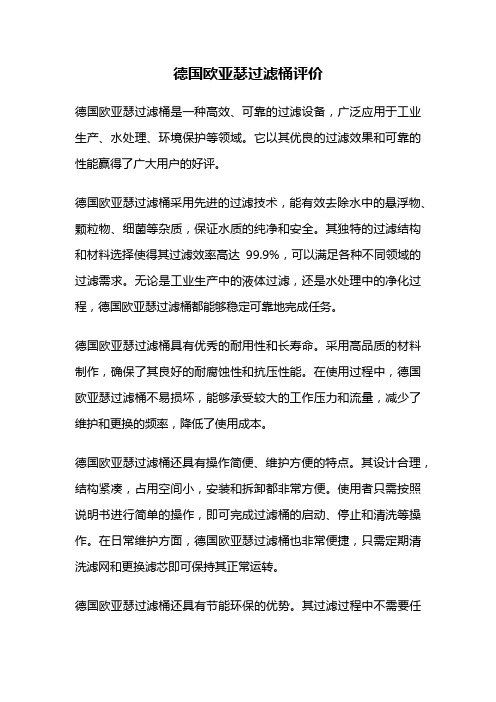
德国欧亚瑟过滤桶评价德国欧亚瑟过滤桶是一种高效、可靠的过滤设备,广泛应用于工业生产、水处理、环境保护等领域。
它以其优良的过滤效果和可靠的性能赢得了广大用户的好评。
德国欧亚瑟过滤桶采用先进的过滤技术,能有效去除水中的悬浮物、颗粒物、细菌等杂质,保证水质的纯净和安全。
其独特的过滤结构和材料选择使得其过滤效率高达99.9%,可以满足各种不同领域的过滤需求。
无论是工业生产中的液体过滤,还是水处理中的净化过程,德国欧亚瑟过滤桶都能够稳定可靠地完成任务。
德国欧亚瑟过滤桶具有优秀的耐用性和长寿命。
采用高品质的材料制作,确保了其良好的耐腐蚀性和抗压性能。
在使用过程中,德国欧亚瑟过滤桶不易损坏,能够承受较大的工作压力和流量,减少了维护和更换的频率,降低了使用成本。
德国欧亚瑟过滤桶还具有操作简便、维护方便的特点。
其设计合理,结构紧凑,占用空间小,安装和拆卸都非常方便。
使用者只需按照说明书进行简单的操作,即可完成过滤桶的启动、停止和清洗等操作。
在日常维护方面,德国欧亚瑟过滤桶也非常便捷,只需定期清洗滤网和更换滤芯即可保持其正常运转。
德国欧亚瑟过滤桶还具有节能环保的优势。
其过滤过程中不需要任何化学药剂,通过物理过滤的方式达到净化水质的目的,避免了化学药剂对环境和人体的危害。
同时,德国欧亚瑟过滤桶采用高效的过滤材料和结构,能够最大限度地降低能耗,减少资源浪费,符合可持续发展的要求。
德国欧亚瑟过滤桶凭借其优良的过滤效果、可靠的性能和方便的操作维护,成为众多用户的首选。
无论在工业生产、水处理还是环境保护等领域,德国欧亚瑟过滤桶都能够满足各种要求,为用户提供可靠的过滤解决方案。
相信随着科技的不断进步和创新,德国欧亚瑟过滤桶将会在未来的发展中更加完善和广泛应用。
DSP型高效雾化喷头在湿法脱硫系统的应用

业有 限公 司 ( 以下 简 称 东 狮 公 司 ) 通 过 多 次 模 拟
试验 , 研 制 开发 了适 应 于湿 法 脱 硫 的 D S P型 系 列
高 效雾 化 喷头 , 并 且 设计 了科 学 合 理 的喷 头 分 布
形式 , 大 大 提高 了脱 硫效 率 , 能有效 防止堵 塔 。
小 氮肥
第4 1卷
第l O期
2 0 1 3年 l O月
1 5
D S P型 高 效 雾 化 喷 头 在 湿 法 脱 硫 系统 的 应 用
王 长 宝
( 长春 东狮 科 贸 实业有 限公 司 吉林 长春 1 3 0 0 3 3 )
0 前 言
近 年来 , 由于产 能大 幅提 高 , 脱 硫 塔塔 径不 得
l 预脱 硫塔 高效雾化喷头
富 液 槽
~ … .
由 4层 喷头 构 成 的空 塔
上 达到 最大 流量 值 , 使 喷 出 的脱 硫 液 达 到 高 效 雾
化 效果 。由于 其具 有 畅通 的通 道 设 计 , 因而 最 大 程 度上 减少 了喷 头 的阻 塞 现 象 。为 防 止 腐蚀 , 喷 头 材质 均 采 用 不 锈钢 , 其 耐腐 性 、 成雾性 、 防堵 性 已被众 多用 户所 认 可 。根 据其 所 喷淋 的介 质流 量
( 收稿 日期 2 0 1 3 . 0 6 - 0 5 )
难 。所 以 , 沉 淀池 内煤泥 沉积 量较 大 , 而捞 出来 后 又无 法 处理 , 造成 煤 泥不 能及 时捞 出来 , 使循 环 水
1 6
小氮肥
第4 1 卷
第l 0期
2 0 1 3年 1 0月
表 2 改造 前 、 后 半 脱液 组分 对 比
焦化厂脱硫硫泡沫处理方案

焦化厂脱硫硫泡沫处理方案英文回答:Sulfur foam treatment is an effective method for desulfurization in coking plants. The main purpose ofsulfur foam treatment is to remove sulfur compounds fromthe flue gas emitted during the coking process. Thisprocess involves the use of a foam generator to produce sulfur foam, which is then injected into the flue gas stream. The sulfur foam reacts with the sulfur compounds in the flue gas, resulting in the formation of solid sulfur particles. These solid particles can then be easily separated from the gas stream using a filtration system.There are several advantages to using sulfur foam treatment for desulfurization in coking plants. Firstly, it is a cost-effective method compared to otherdesulfurization technologies. The foam generator used inthe process is relatively simple and inexpensive to operate. Additionally, the solid sulfur particles produced duringthe process can be recycled and used in other industrial applications, further reducing the overall cost of desulfurization.Furthermore, sulfur foam treatment is environmentally friendly. The solid sulfur particles produced during the process are non-toxic and can be safely disposed of. This eliminates the need for additional waste treatment processes, reducing the overall environmental impact of the desulfurization process.In terms of operational considerations, sulfur foam treatment requires regular maintenance and monitoring to ensure optimal performance. The foam generator andfiltration system need to be properly maintained to prevent any operational issues. Additionally, the sulfur foam injection rate needs to be carefully controlled to ensure efficient sulfur removal from the flue gas stream.Overall, sulfur foam treatment is a viable andeffective solution for desulfurization in coking plants.Its cost-effectiveness, environmental friendliness, andease of operation make it a favorable choice for cokingplant operators.中文回答:脱硫硫泡沫处理是焦化厂脱硫的一种有效方法。
新型脱硫剂的制备及应用

P DS新 型脱 硫 剂 是 一 种 比较 经 济 有 效 的 脱 硫
催化 剂 , 主要 成分 是 双 核酞 菁钴 磺 酸盐 , 可广 泛用 于
含 硫 气体 ( 如半 水煤 气 、 炉 气 、 市煤 气 、 然气 、 焦 城 天 合成 气 、 油半生 气 等 ) 石 和低 粘 度 含硫 液体 ( 如汽 油 、 轻柴 油 、 脑 油 、 石 裂化 油 、 苯 、 粗 丙烯 、 态 烃等 ) 液 的脱
度 。 氨 水 的要 补加 氨 水 , 持浓 度 。 它 生产 工 艺 加 保 其
条 件 要 控 制 在 正 常 范 围 ,尤 其 是 液 气 比和 喷 淋 密
度。
3 5 其 它 应 用 .
初投 量 约 为 3 0 , ×l 即 2—0 —2 收 20 1 0 【 者 简 介 】 妹 文 ( 9 3一)女 , 程 师 , 事 精 细 化 工 新 产 品 的 生 作 王 16 , 工 从
2 2 中和 .
P ( TS O) 放 出 具 有 强 大 氧 化 活 性 的 原 子 态 氧
( , 速 氧化 S 一 出单 质 硫 , 是本 品高 效脱 硫 O) 迅 !析 这
之 原理 , 可 表示 为 : 也 P T( 化 态 ) S 氧 +H — P ( 原 态 ) O TS 还
[ 图分 类 号 】 中 TQ 4 5 56 [ 献 标 识 码 】B 文 [ 章 编 号 】 0 3—5 9 ( 0 2 0 文 10 0 5 2 0 ) 3—0 3 0 4—0 2
1 P DS脱 硫 剂 的 性 质
化 剂 3 0g左 右 , 根据 本 厂脱 硫 液数 量 算 出初 投 催化 剂总量。 将 催 化剂 溶 于碱 液 或氨 水 液 中 ,此 碱 液 为车 间 正 常使 用 的碱 液 。取 贫 硫液 加 溶催 化 剂 ,并 交 替通 人 空气 和 未脱 硫 的煤 气 各 8h 使 其 活化 2 , 4h以上 , 其 间搅 拌 2次 , 其 充分 活化 。 使
脱硫工段硫泡沫处理方案的综述
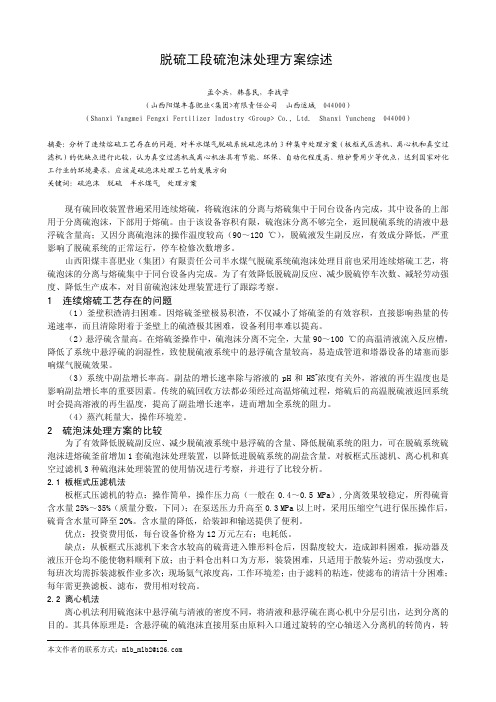
脱硫工段硫泡沫处理方案综述孟令兵,韩喜民,李战学(山西阳煤丰喜肥业<集团>有限责任公司 山西运城 044000)(Shanxi Yangmei Fengxi Fertilizer Industry <Group> Co., Ltd. Shanxi Yuncheng 044000)摘要:分析了连续熔硫工艺存在的问题。
对半水煤气脱硫系统硫泡沫的3种集中处理方案(板框式压滤机、离心机和真空过滤机)的优缺点进行比较,认为真空过滤机或离心机法具有节能、环保、自动化程度高、维护费用少等优点,达到国家对化工行业的环境要求,应该是硫泡沫处理工艺的发展方向关键词:硫泡沫 脱硫 半水煤气 处理方案现有硫回收装置普遍采用连续熔硫,将硫泡沫的分离与熔硫集中于同台设备内完成,其中设备的上部用于分离硫泡沫,下部用于熔硫。
由于该设备容积有限,硫泡沫分离不够完全,返回脱硫系统的清液中悬浮硫含量高;又因分离硫泡沫的操作温度较高(90~120 ℃),脱硫液发生副反应,有效成分降低,严重影响了脱硫系统的正常运行,停车检修次数增多。
山西阳煤丰喜肥业(集团)有限责任公司半水煤气脱硫系统硫泡沫处理目前也采用连续熔硫工艺,将硫泡沫的分离与熔硫集中于同台设备内完成。
为了有效降低脱硫副反应、减少脱硫停车次数、减轻劳动强度、降低生产成本,对目前硫泡沫处理装置进行了跟踪考察。
1 连续熔硫工艺存在的问题(1)釜壁积渣清扫困难。
因熔硫釜壁极易积渣,不仅减小了熔硫釜的有效容积,直接影响热量的传递速率,而且清除附着于釜壁上的硫渣极其困难,设备利用率难以提高。
(2)悬浮硫含量高。
在熔硫釜操作中,硫泡沫分离不完全,大量90~100 ℃的高温清液流入反应槽,降低了系统中悬浮硫的润湿性,致使脱硫液系统中的悬浮硫含量较高,易造成管道和塔器设备的堵塞而影响煤气脱硫效果。
(3)系统中副盐增长率高。
副盐的增长速率除与溶液的pH和HS-浓度有关外,溶液的再生温度也是影响副盐增长率的重要因素。
脱硫过程中硫泡沫处理工艺选择

F e u l& Ch mia r c s e e clPo e ss
Ma .2 l r O1 V l 2 No2 o _ . 4
脱硫 过 程 中硫泡 沫 处理 工 艺选 择
李 国 亮 栾 兆 爱 蒋 秀 香
( 芜钢铁 股份 有 限公 司 焦化厂 ,菜芜 2 10 ) 莱 7 14
2 离 心 机 法 生产 生 硫 工 艺
.
离心机 法利用 硫泡 沫 中悬浮硫 与清 液的密度 不
同 ,将 清液 和悬 浮硫在 离心机 中分层 引 出 ,达 到分 离 的 目的 。具体操 作 :含悬 浮硫 的硫 泡沫 用泵送 入 离心 机的转 筒 内 ,转筒旋 转后 ,由于悬浮硫 的密度 大 ,产 生的 离心力 也大 。离心力 迫使 悬浮硫 迅速 在
收 稿 日期 :2 0 0 — 5 01- 7 1 作 者 简介 :李 国亮 ( 9 3 ) 1 8 ~ ,男 ,工 程 师
( 下转 第 6 3页)
2 1 3月 01 年
第4 2卷 第 2期
燃 料 与 化 工 F e & C e cl rcse ul hmia Poess
6 3
的炭黑 增 多 。通过 减少 装煤 和 平煤 次数 可 以减 少炭
黑 的形 成
黏 度 增 加 ,流 动性 降 低 ,使 之 很 难 与 水 分 离 ,因
此 , 水 分 含 量 增 加 。 当 焦 油 Q 含 量 增 加 时 ,灰 分 I
4 使 用 效 果
熔硫 釜法生 产熟硫 工艺 无论 从工艺 、设备 、运 行 ,还是 环保 、节能 等各方 面都 有很大 的缺点 ,我
厂 已经 将此 工艺 淘汰 ,将离 心机 法与压滤 机法作 对
比 ,见 表 1 。
半水煤气湿法脱硫设备及工艺应用
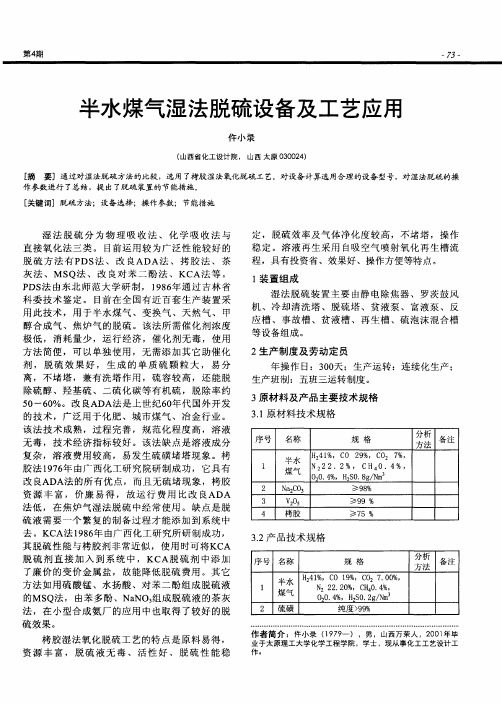
36 计算 .2 .
( )脱硫塔 1 本 工 段 脱硫 负荷 按 全 低 变 流 程 确 定 ,气 体 出 脱硫 清 洗塔 硫化 氢 含量 控 制 在 .g 02 / ,本 塔 以 Nm 此指标 进行 计算 ,选用 填料 塔 。
气量 :3 0 ×2 = 2 0 Nm ( ); 3 0 5 85 0 / 干 h
l.3 6 0 3.9 4O
i l
一 6 . 115 -04 6 .
—9 10 }
} f
1 5 4 4
53 . 4 T3—9 J 6 7
5
硫磺
3 2
13 l
45 4
33 6 3ຫໍສະໝຸດ m 5/ 3 生产流程 . 4
来 自洗 气 塔 的 半水 煤气 H S 量 为04 ~ 08 含 .5 . Nm ,在 t 3 ℃ ,P 0O 4 a <5 .0 MP 工况 下 ,先经 过 湿
用 此 技 术 , 用 于 半 水 煤 气 、变 换 气 、 天然 气 、 甲 醇 合 成 气 、 焦 炉气 的 脱硫 。该法 所 需 催化 剂浓 度 极低 , 消 耗 量 少 , 运 行 经 济 ,催 化 剂 无 毒 , 使 用 方法 简便,可 以单独使用 ,无需添加其它助催化 剂 , 脱 硫 效 果 好 , 生 成 的 单 质 硫 颗 粒 大 , 易 分 离 , 不 堵 塔 , 兼有 洗塔 作 用 ,硫 容较 高 ,还 能 脱 除硫 醇 、羟 基 硫 、 二硫 化 碳 等 有 机 硫 , 脱 除 率 约 5 —6 %。改 良ADA法 是 上世 纪 6 年代 国外 开发 0 0 O 的 技 术 ,广泛 用 于 化 肥 、城 市 煤 气 、冶 金 行 业 。 该法 技 术 成 熟 ,过 程 完 善 ,规 范 化 程 度 高 ,溶 液 无 毒 , 技 术 经 济 指 标 较好 。该 法 缺 点是 溶 液 成 分 复杂 ,溶 液 费 用较 高 , 易发 生 硫 磺 堵 塔 现 象 。栲 胶 法 1 7 年 由广 西 化 工 研 究 院研 制成 功 ,它 具 有 96
PDS脱硫工艺的应用与改造

燃 料 与 化 工 F e &C e cl rc se u l hmia Poess
6l
P 脱 硫 工 艺 的应 用 与 改 造 DS
孙益民 ( 山西 中煤 焦化 九鑫 公 司 ,晋 中 0 10 ) 3 3 7
氨法 一 D P S脱 硫 脱 氰 工 艺是 中冶 焦 耐 设计 的湿 法 氰 化 脱 硫 脱 氰 工 艺 。我 厂 煤 气 处 理 量 为 1 l x0 m / ,2套 5 14 / 3 h x 0m3 h的 P S法脱 硫 装 置并 联 操 作 , D
84 ̄8 8。 . .
究 后 ,将 熟 硫 工 艺 改 为 生硫 工 艺 ,增 加 2台 压 滤 机 ,硫 泡 沫在恒 温 状态 下进 行分 离得 到 硫膏 。 为 防 止 硫 膏 积 累 .从 脱 硫 泵 出 口引 出 1根 D 5 N 0管道 ,在扩 大 部 分增 加 l圈 喷淋 管 ,定 期 喷 洒 ,减少 硫 膏在再 生塔 扩大 部 分积 累 。 改造 后 ,节省 了熔 硫用 蒸 汽 .生 硫 工艺 的清 液
见 S为催 化 剂 ,利用 压 D 缩 空 气使 催化 剂发 生 液相催 化 氧化 反应再 生 .从 而 脱 除煤 气 中的 H S 目前 塔后 H S含 量 在 2 0 / z, 2 0 mg m
以下 。
预
脱
广 _] —L J _
上
14 蒸 氨 系统 改 造 .
原工 艺采 用熔 硫 釜生产 硫磺 ,环 境 恶劣 ,极 易
堵塞 管道 ,造 成脱 硫 系统无 法正 常运 行 。经分 析 研
在 进 预冷 塔 氨气 管路 上 引 出一 分 支 ,新 增加 1 台换 热 器 ,将氨 气冷 凝 为液态 氨 后补 入反 应槽 ,保 证 脱硫 液 中 的浓 度 大 于 8/ gL,此 时 ,最 佳 p H值 为
- 1、下载文档前请自行甄别文档内容的完整性,平台不提供额外的编辑、内容补充、找答案等附加服务。
- 2、"仅部分预览"的文档,不可在线预览部分如存在完整性等问题,可反馈申请退款(可完整预览的文档不适用该条件!)。
- 3、如文档侵犯您的权益,请联系客服反馈,我们会尽快为您处理(人工客服工作时间:9:00-18:30)。
“DS型硫泡沫过滤机+熔硫”技术的使用意义
来源:录入时间:2011-10-9 8:51:00点击:63
在生产中,湿法脱硫绝大多数是以硫泡沫浮选的方式来分离单质S 的。
硫回收是整个脱硫生产中的一个重要环节,近几年来,我们看到的是,无论焦炉煤气还是半水煤气(或水煤气)还是变换气脱硫,硫回收的重要性越来越明显,而且成为脱硫系统运行正常与否的一个关键因素。
因为它不仅影响到脱硫后H2S含量的高低,还直接关系到生产成本,而且由于环保、安全等因素,在操作上也大大增加了压力。
在最初的硫磺回收工艺中,基本采用间歇熔硫,而随着企业规模的不断扩大和高硫煤在企业的广泛使用,间歇熔硫又逐渐被连续熔硫所代替。
但是,近几年来,连续熔硫存在的问题日渐明显,碱耗的增加,副盐含量的升高,废液排放量的增多,腐蚀、堵塞、泡沫浮选不好等均与其有关。
特别是很多焦化厂,因为连续熔硫等因素,其运行可以说是到了举步维坚的程度,影响相当严重。
为此,先过滤再熔硫的技术得到关注,但过滤技术上又有新问题,过滤的效果、操作的难度,处理量上的限制、生产环境的污染、生产成本的高低以及硫泡沫成份的特殊性等,这一系列问题使得我们对过滤机的要求达到了一个更高、更全面的层次。
为此,经过不断开发和研究,开发了DS型硫泡沫专用过滤机,过滤后滤饼进熔硫釜熔硫,滤液回系统。
DS型硫泡沫过滤技术不同于任何以往曾用于硫泡沫过滤中的过滤技术,它结合了脱硫液的粘度、密度、腐蚀性、硫颗粒大小等因素,并满足了企业生产规模大、煤气H2S含量
高、处理量大的问题,又克服了连续熔硫的诸多不利之处,适应了现代化的脱硫生产。
在使用过程中突出了其技术的先进性、实用性和前瞻性。
采用该过滤机过滤后再去熔硫,避免了大量清液进熔硫釜被加热升温再回系统的问题,节约了蒸汽用量,减少了副盐的生成量,降低了碱耗,而增加的只有几千瓦时的电耗。
下面从以上几个方面将该技术与连续熔硫技术作以比较。
1 降低了蒸汽消耗量
一般情况下,再生溢流的硫泡沫液体含量90%左右,那么,采用连续熔硫每生产1吨硫磺,将从熔硫釜回流脱硫液9吨,DS型硫泡沫过滤机过滤后,滤饼含水量30%,也就是每生产1吨硫磺,还要有0.43
吨脱硫液随过滤后的滤饼进入熔硫釜,所以采用DS型硫泡沫过滤机过滤后再熔流比直接连续熔硫,每生成1吨硫磺减少进熔硫釜溶液8.57吨,这些溶液进熔硫釜通常需要从35℃左右被加热到70~90℃后出熔硫釜,那么这部分溶液温度的升高需要的蒸汽量计算如下:
Q液=W液C液(T出-T入)
=8.57×103×4.18×(353-308)
=1612017KJ
由热量衡算式得:
Q汽=Q液+Q损
即:R汽·M汽=Q液+Q液×8%
所以:
M汽=
=
=821kg
式中:
Q液—脱硫液吸收的热量,KJ;
W液—脱硫液的质量,kg;
C液—脱硫液的比热,取水的比热4.18KJ/kg·k
T入、T出—进出熔硫釜脱硫液温度,入口按35℃计,出口温度一般控制在70-90℃,在此按80℃计;
Q汽—蒸汽传给脱硫液的热量;
Q损—传热过程损失的热量,在此按脱硫液吸收热量的8%计;
R汽—蒸汽的冷凝热;KJ/kg,按压力0.45MPa计;
M汽—所需蒸汽的质量,kg。
从计算结果看出,使用DS型硫泡沫过滤机过滤后熔硫将比连续熔硫每吨硫磺节约蒸汽821kg,如此算来,对于一个处理气量为60000Nm3/h 的焦炉煤气脱硫系统,入口H2S按5000mg/Nm3,口控制100mg/Nm3以下,硫回收率85%,则每天节省蒸汽4634kg。
2 减少溶液的温升
采用连续熔硫的厂家,如果不回收回流液是不可能的,因为那样不仅浪费大而又为环保所不容。
如果先冷却再回系统,自然是好,但自然冷却需要较长的时间、设备、场地,溶液量的增加等都是问题,如果采用冷却介质来冷却,那就大大增加了运行成本,而且容易在冷却过程出现析盐、堵塞等现象,所以,特别是一些气量大,煤气H2S含量高的大规模焦化企业,熔硫釜回流液回系统前进行冷却处理的几乎没有,大部分直接回系统。
这样就导致了溶液温度过高,特别是在夏季,给系统的运行带来很大困扰。
还是以气量为60000Nm3/h、煤气H2S为5g/Nm3的焦炉煤气脱硫为例,采用连续熔硫比先用DS型过滤机过滤再熔硫将每天多排出回流液48.4吨。
根据热量平衡关系:
M热·C热·(T2-T)=M冷·C冷(T-T1)
则:T=
=(48.4×103×353+1050×103×308)/(48.4×103+1050×103)
=310K=37℃
T-T1=37-35=2℃
式中:
M热—熔硫釜每天回液量kg;
M冷—系统溶液总量, 1000m3×1050kg/m3=1050×103kg;
C热、C冷—分别是回流液和系统溶液的比热,C热=C冷;
T1—脱硫液的初始温度,k,308k;
T2—熔硫釜回液的温度,k,取353k;
T—混合后脱硫液的温度,k。
由上面的计算看出,连续熔硫较DS过滤机过滤后再熔硫,每天内熔硫釜回流液将导致系统溶液温度升高29℃。
连续不断的回收熔硫液,特别是在夏季,会使系统温度严重超高,对系统的正常运行带来很大影响,甚至难以维持生产。
3 有利于降低副盐生成率
我们知道,温度过高,有利于副盐的生成,特别是温度超过50℃时,Na2S2O3生成率近乎直线上升。
而熔硫釜回流液温度大多在70-90℃之间,虽说釜内溶液中的氧没有再生槽(塔)内那么充足,但硫泡沫及液体从再生槽出来,其中也溶解一定量的氧,在釜内较高的温度下与溶液中的Na2CO3和HS-或单质S生成Na2S2O3的速度是非常快的。
我们曾
专门在一气量为60000Nm3/h,入口H2S5000mg/Nm3的厂家多次分析过Na2S2O3含量,当时硫泡沫取样分析Na2S2O3结果平均为:21.3g/L,而熔硫釜出来的清液中Na2S2O3分析结果平均则是51.4g/L。
其每天回收硫磺5.7吨,采用连续熔硫,每天最少从熔硫釜排出51.3吨清液,而如果先用DS型硫泡沫过滤机过滤再熔硫,则每天少排49吨清液,这49吨脱硫液经熔硫高温再回流,将多产生副盐Na2S2O3:(51.4-21.3)×49/1.05=1405kg,系统溶液总量1000m3,所以,采用DS型过滤机每天内将能使整个系统溶液中Na2S2O3浓度的增长减少1405/1000=1.405g/L。
另外,在大量熔硫釜回流液回至系统时,引起短时间内局部温度过高而副反应加快,副盐生成量大增,在此就不必多论。
4 有利于碱耗的降低
近几年,无论是氮肥待业或焦化行业的脱硫,碱耗高的现象比比皆是,甚至有些厂家高到令人吃惊。
关于副盐的增长引起碱耗的升高及熔硫导致副盐增长,大多数企业生产管理人员都有所了解。
但是采用连续熔硫增加的碱耗到底有多大,几乎很少有人去关心,出现碱耗高的现象,只是一味的从其它方面找原因,最后也是当举功甚微。
在脱硫系统溶液中,Na2S2O3不管是哪种反应而来的,其Na+唯一来源于Na2CO3,所以每生成1molNa2S2O3最终要消耗掉1molNa2CO3,也就是每生成
1kgNa2S2O3,要消耗掉0.67kgNa2CO3象以上(标题3)中所举的气量60000Nm3/h,入口H2S5000mg/Nm3的厂家,每天回收硫磺5.7吨,至少从熔硫釜排出51.3吨清液。
清液中Na2S2O3由21.3升至51.4,每天因
该过滤机在运行中的能耗与其它过滤设备相比节省约90%以上。
而相对于直接连续熔硫其能耗基本上只增加了一项微不足道的电耗。
一般情况下,该过滤机每小时处理硫泡沫的量为0.6-1.2m3/m2·h。
就拿上面提到的企业来说,气量60000Nm3/h,入口H2S5000mg/Nm3,我们可以选择一台DS-15型过滤机,其运行功率仅在9kw,包括清洗时间在内,我们就按每天16h运行时间算,其每天电耗费用:9kw×16×0.76(当地电价)=109元,每天节约费用2000元/天左右。
我们采用“DS型硫泡沫过滤机+熔硫”的技术,目的是将传统的间歇熔硫和连续熔硫相结合,以适应现代化生产的需要,以上将该技术与连续熔硫技术作以比较,其带来的经济效益和环保效益,对这些大规模企业来说并非冰山之一角,从数据上看,令人颇感鄂然,实际上一线生产管理及操作人员应该清楚,我们以上数据还算保守,连续熔硫生产1吨硫磺排出9吨清液也只是在再生槽泡沫溢流十分理想的情况下才能实现,实际上大多数厂家都远大于此数,山东一化肥厂每天生产硫磺2.5砘,每天需要处理的再生槽溢流泡沫量达90m3,所以其引起的蒸汽消耗、碱耗及副盐的生成量也远不止如此。
还有需要说明的是,有些企业采用DS型硫泡沫过滤机过滤后不熔硫,直接外销,因该过滤机过滤后含水量较少,所以企业可根据蒸汽的成本,硫磺的价格及滤饼销售的渠道等因素自身决定。
另外,有些企业,采用了其它过滤技术,自然也无可厚非,但其运行成本、劳动强度、过滤效果、生产环境等问题值得我们去总结、分析,还望业内人士对过滤技术也要经常交流,使其不断提
高,及时推广先进技术与经验,促使硫回收技术不断完善,从而推动脱硫技术的长远发展。