十八种危险工艺检查表
工艺设备安全检查表
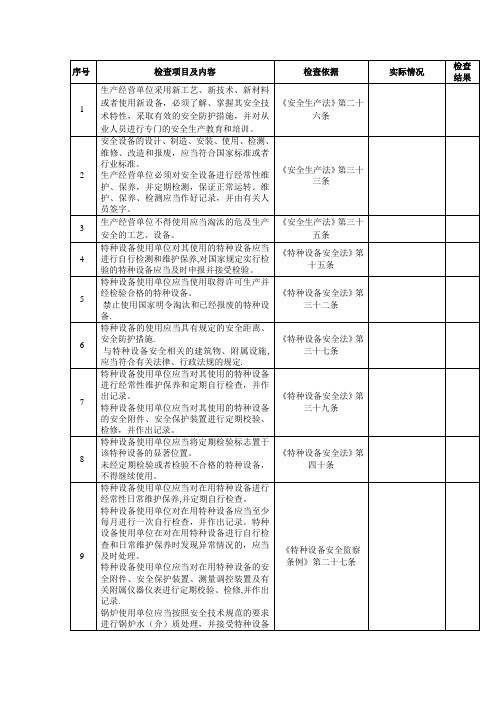
27
设备和管道应根据其内部物料的火灾危险性和操作条件,设置相应的仪表、自动联锁保护系统或紧急停车措施.
《石油化工企业设计防火规范》GB50160-2008第5.1.2条
28
在使用或产生甲类气体或甲、乙A类液体的工艺装置、系统单元和储运设施区内,应按区域控制和重点控制相结合的原则,设置可燃气体报警系统。
5.可燃气体或液体受热膨胀,可能超过设计压力的设备;
6。顶部最高操作压力为0。03~0。1MPa的设备应根据工艺要求设置.
《石油化工企业设计防火规范》GB50160—2008第5。5。1条
31
单个安全阀的开启压力(定压),不应大于设备的设计压力。当一台设备安装多个安全阀时,其中一个安全阀的开启压力(定压)不应大于设备的设计压力;其他安全阀的开启压力可以提高,但不应大于设备设计压力的1.05倍。
7
特种设备使用单位应当对其使用的特种设备进行经常性维护保养和定期自行检查,并作出记录。
特种设备使用单位应当对其使用的特种设备的安全附件、安全保护装置进行定期校验、检修,并作出记录。
《特种设备安全法》第三十九条
8
特种设备使用单位应当将定期检验标志置于该特种设备的显著位置。
未经定期检验或者检验不合格的特种设备,不得继续使用。
序号
检查项目及内容
检查依据
实际情况
检查
结果
1
生产经营单位采用新工艺、新技术、新材料或者使用新设备,必须了解、掌握其安全技术特性,采取有效的安全防护措施,并对从业人员进行专门的安全生产教育和培训。
《安全生产法》第二十六条
2
安全设备的设计、制造、安装、使用、检测、维修、改造和报废,应当符合国家标准或者行业标准。
危化品企业常用安全检查表19张
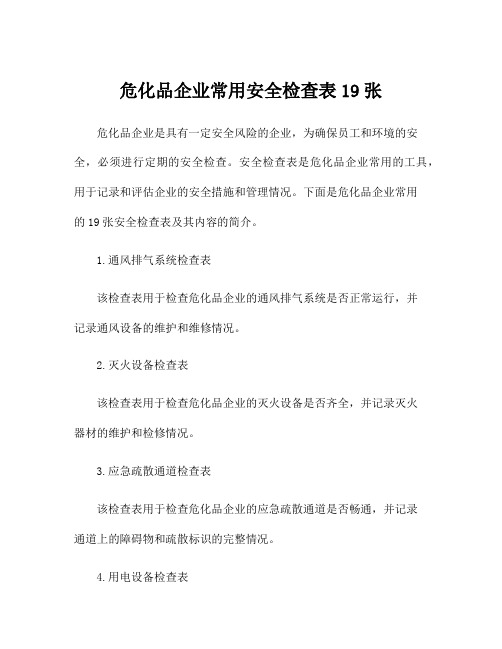
危化品企业常用安全检查表19张危化品企业是具有一定安全风险的企业,为确保员工和环境的安全,必须进行定期的安全检查。
安全检查表是危化品企业常用的工具,用于记录和评估企业的安全措施和管理情况。
下面是危化品企业常用的19张安全检查表及其内容的简介。
1.通风排气系统检查表该检查表用于检查危化品企业的通风排气系统是否正常运行,并记录通风设备的维护和维修情况。
2.灭火设备检查表该检查表用于检查危化品企业的灭火设备是否齐全,并记录灭火器材的维护和检修情况。
3.应急疏散通道检查表该检查表用于检查危化品企业的应急疏散通道是否畅通,并记录通道上的障碍物和疏散标识的完整情况。
4.用电设备检查表该检查表用于检查危化品企业的用电设备是否符合安全要求,并记录设备的维护和维修情况。
5.防雷设施检查表该检查表用于检查危化品企业的防雷设施是否完好,并记录设施的维护和检修情况。
6.安全生产教育培训记录表该检查表用于记录危化品企业员工接受安全生产教育培训的情况,包括培训时间、内容和人员等。
7.危险化学品存储检查表该检查表用于检查危化品企业的危险化学品储存区域是否符合要求,并记录存储区域的安全措施和管理情况。
8.危化品生产操作规程检查表该检查表用于检查危化品企业的生产操作规程是否科学合理,并记录规程的执行和更新情况。
9.事故应急预案检查表该检查表用于检查危化品企业事故应急预案的编制和完善情况,并记录预案的演练和修订情况。
10.安全防护设备检查表该检查表用于检查危化品企业的安全防护设备是否齐全,并记录设备的维护和检修情况。
11.危险废物处理记录表该检查表用于记录危化品企业的危险废物处理情况,包括废物的产生、收集、贮存和处置等。
12.公共卫生管理检查表该检查表用于检查危化品企业的公共卫生管理情况,包括工作区域的清洁和个人卫生等。
13.职业健康监测记录表该检查表用于记录危化品企业员工的职业健康监测情况,包括健康检查的项目和结果等。
14.安全生产资质检查表该检查表用于检查危化品企业的安全生产资质情况,包括许可证、培训证书等的有效性和更新情况。
工艺操作安全检查表

检查人:
7
正常状态或异常状态都有什么样的反应速度,如何预防异常压力、异常反应、混入杂质、流动阻塞、跑冒滴漏,发生了这些情况后,如何采取紧急措施
8
发生异常状况时,有否将反应物质迅速排放的措施
9
有何防止急剧反应和制止急剧反应的措施
10
泵、搅拌器等机械装置发生故障时会产生什么样的危险
11
设备在逐渐或急速堵塞的情况下,生产会出现什么样的危险状态
工艺操作安全检查表
序号
检查内容
检查结果
备注
是(J)
取了何种隔离措施
2
工艺中的各种参数是否接近了危险界限
3
操作中会发生何种不希望的工艺流向或工艺条件以及污染
4
装置内部会发生何种可燃或可爆性混合物
5
对接近闪点的操作,采取何种防范措施
6
对反应或中间产品,在流程中采取了何种安全制度,如果一部分成分不足或者混合比例不同,会产生什么样的结果
3危险化工工艺(18种)安全控制系统检查表

紧急停车系统
同上
1、查设计文件、批准的安全设施设计专篇内容,是否根据工艺要求设计紧急停车系统;
2、紧急停车的自控系统的测量和执行机构设置是否与设计一致;
3、配套的保障供辅:循环、冷冻、仪表风、氮气、供电、伴烧气是否与控制系统匹配;
4、需设置排放时的收集处理,如事故罐(池),及火炬、吸收的适用性。
8
同(一)1
(4)
电流、电压检测及控制
同(一)1
(5)
盐水高位槽温度检测及控制
《关于印发光气及光气化、电解(氯碱)工艺安全控制指导意见的通知》(鲁安监发〔2010〕70号)“电解(氯碱)工艺安全控制指导意见”
同(一)1
(6)
出槽淡碱浓度(总管)集中显示
同(一)1
(7)
可燃气体浓度、有毒气体浓度报警
同(一)1
三、氯化工艺
(一)
重点监控工艺参数
《重点监管的危险化工工艺目录》(2013完整版)
1
氯化反应釜温度和压力;氯化反应釜搅拌速率;反应物料的配比;氯化剂进料流量;冷却系统中冷却介质的温度、压力、流量等;氯气杂质含量(水、氢气、氧气、三氯化氮等);氯化反应尾气组成等。
1、查批准的安全设施设计专篇、设计文件内容,是否设置各参数监测、控制;
1
反应釜温度、压力报警联锁
同上
1、查阅批准的安全设施设计、设计文件与现场设置情况的一致性;
2、查DCS控制系统画面,是否设置相关报警参数显示及联锁调节或切断措施;
3、查报警历史记录曲线,核实参数设置有效性。
2
有毒气体回收及处理系统(自动氨或碱液喷淋装置)
同上
1、查设计文件、批准的安全设施设计专篇的内容与现场设置情况的一致性。
危险工艺安全检查表
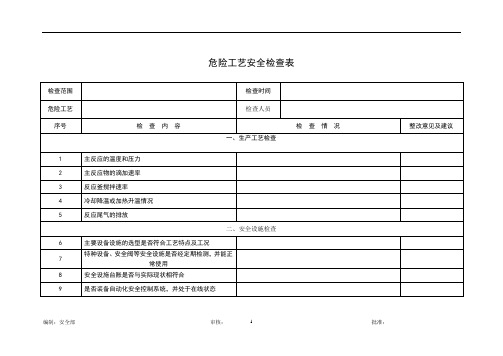
检查范围
检查时间
危险工艺
检查人员
序号
检 查 内 容
检 查 情 况
整改意见及建议
一、生产工艺检查
1
主反应的温度和压力
2
主反应物的滴加速率
3
反应釜搅拌速率
4
冷却降温或加热升温情况
5
反应尾气的排放
二、安全设施检查
6
主要设备设施的选型是否符合工艺特点及工况
7
特种设备、安全阀等安全设施是否经定期检测,并能正常使用
8
安全设施台账是否与实际现状相符合
9
是否装备自动化安全控制系统,并处于在线状态
10
应急处置的装备是否合理,可用
三、安全管理检查
11
对员工是否进行专项的工艺危险性及应急安全教育
12
是否制定有针对性的安全管理制度和操作规程
13
是员工素质是否符合危险工艺从业要求(特种作业证等)
15
是否针对现场处置方案进行过演练,并有记录
生产部:1次/月
危险化学品企业安全检查表
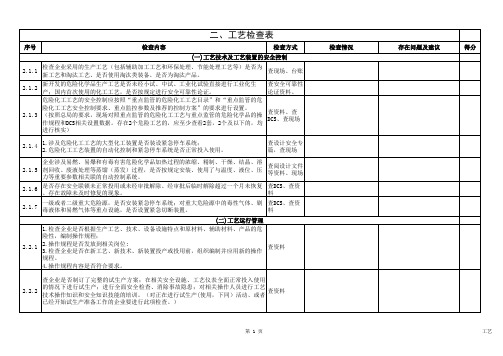
查资料
抽查工艺变更资料:
是否对变更可能导致的风险进行识别评估;
2.2.6 是否根据变更风险识别评估结果制定控制措施;
查变更资料
是否及时将变更内容传达给相关人员,并对相关操作人员进行培训;
变更结束后是否对变更情况进行验收。
(三)现场工艺安全管理
可燃气体、可燃液体设备的安全阀出口连接应符合下列规定:(1)可燃液体设备的安 全阀出口泄放管应接入储罐或其他容器,泵的安全阀出口泄放管宜接至泵的入口管道 2.3.1 、塔或其他容器;(2)可燃气体设备的安全阀出口泄放管应接至火炬系统或其他安全 查现场 泄放设施;(3)泄放后可能立即燃烧的可燃气体或可燃液体应经冷却后接至放空设 施;(4)泄放可能携带液滴的可燃气体应经分液罐后接至火炬系统。
查资料、查 DCS、查现场
进行核实)
2.1.4
1.涉及危险化工工艺的大型化工装置是否装设紧急停车系统; 2.危险化工工艺装置的自动化控制和紧急停车系统是否正常投入使用。
查设计安全专 篇,查现场
2.1.5
企业涉及易燃、易爆和有毒有害危险化学品加热过程的浓缩、精制、干燥、结晶、溶 剂回收、废液处理等蒸馏(蒸发)过程,是否按规定安装、使用了与温度、液位、压 力等重要参数相关联的自动控制系统。
(4)装卸作业完成后充分静置,再进行倒罐作业或向使用装置送料等;
(5)装卸作业前对车辆进行静电接地;
(6)装卸作业前后,对车辆静置10分钟以上消除静电。
2.4.17 易燃易爆介质的装卸场所是否设置独立接地系统。
查现场
第4页
检查情况
存在问题及建议
得分
工艺
序号
检查内容
检查方式
2.4.18
液化烃、液氨、液氯等易燃易爆、有毒有害液化气体的充装是否使用万向管道充装系 统。
重点工艺安全控制检查表
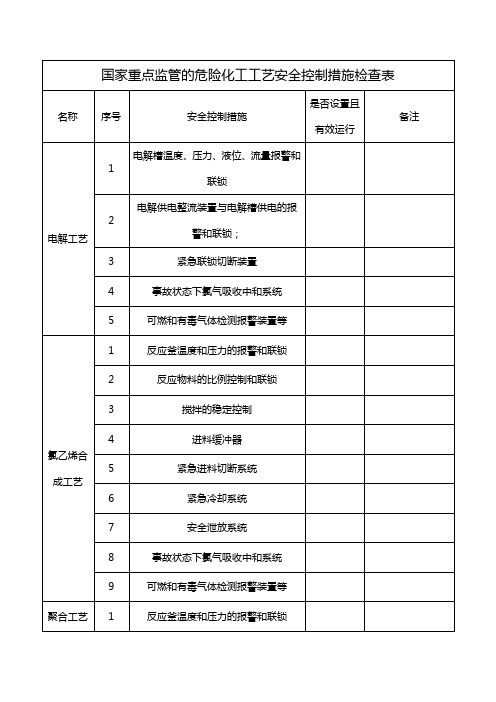
电石生产工艺
1
设置紧急停炉按钮
2
电炉运行平台和电极压放视频监控、输送系统视频监控和启停现场声音报警
3
原料称重和输送系统控制
4
电石炉炉压调节、控制
5
电极升降控制
6
电极压放控制
7
液压泵站控制
8
炉气组分在线检测、报警和联锁
9
可燃和有毒气体检测和声光报警装置
10
设置紧急停车按钮等
反应物料的比例控制和联锁
3
搅拌的稳定控制
4
进料缓冲器
5
紧急进料切断系统
6
紧急冷却系统
7
安全泄放系统
8
事故状态下氯气吸收中和系统
9
可燃和有毒气体检测报警装置等
聚合工艺
1
反应釜温度和压力的报警和联锁
2
紧急冷却系统
紧急切断系统
紧急加入反应终止剂系统
聚合工艺
搅拌的稳定控制和联锁系统
料仓静电消除、可燃气体置换系统,可燃和有毒气体检测报警装置
国家重点监管的危险化工工艺安全控制措施检查表
名称
序号
安全控制措施
是否设置且有效运行
备注
电解工艺
1
电解槽温度、压力、液位、流量报警和联锁
2
电解供电整流装置与电解槽供电的报警和联锁;
3
紧急联锁切断装置
4
氯乙烯合成工艺
1
反应釜温度和压力的报警和联锁
2
检查人员:检查日期:年月日
易燃易爆危险作业-涂装作业-安全检查表
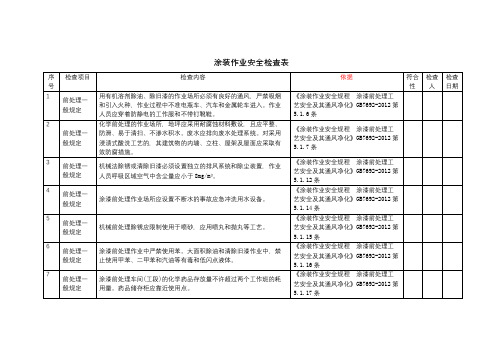
喷漆室通风及灭火
在连续喷漆作业中的大型喷漆室、流平室、供调漆室应设自动灭火系统。
《涂装作业安全规程喷漆室安全技术规定》GB14444-2006第5.9条
40
喷漆室电气
喷漆区和爆炸危险区域2区内不应设置有引起明火、火花的设备和外表超过喷涂涂料自燃点温度的设备。
《涂装作业安全规程喷漆室安全技术规定》GB14444-2006第6.1.5条
《涂装作业安全规程涂漆前处理工艺安全及其通风净化》GB7692-2012第5.2.2条
14
有机溶剂、气相除油前处理
气相除油清洗装置应具有清洗液的温度和液位的自动监控,以及冷凝器冷却水的供水监测装置,其中测温仪的分度值应不大于0.5℃。
《涂装作业安全规程涂漆前处理工艺安全及其通风净化》GB7692-2012第5.2.3条
有机溶剂、气相除油前处理
用可燃性有机溶剂除油时,应先卸下产品或部件上的蓄电池或其他电源装置,其作业场所应设有警示标牌,并配置可燃气体浓度测量仪,定期检测。
《涂装作业安全规程涂漆前处理工艺安全及其通风净化》GB7692-2012第5.2.1条
13
有机溶剂、气相除油前处理
气相除油清洗应在半封闭槽内进行,应有严格的防止清洗液蒸气逸出的措施;槽体内壁衬里材料应用不锈钢、陶瓷、阻燃型不饱和聚酯树脂纤维增强塑料及其他合适的材料。
47
喷漆室结构
干式漆雾去除装置、导流板、分布板、撞击板、均应采用不燃或难燃材料制备,并应方便取出,经常清理。
《涂装作业安全规程喷漆室安全技术规定》GB14444-200所配置的加热器,无论何种类型,均不得布置在室体内。
《涂装作业安全规程喷漆室安全技术规定》GB14444-2006第7.6.2条
30
- 1、下载文档前请自行甄别文档内容的完整性,平台不提供额外的编辑、内容补充、找答案等附加服务。
- 2、"仅部分预览"的文档,不可在线预览部分如存在完整性等问题,可反馈申请退款(可完整预览的文档不适用该条件!)。
- 3、如文档侵犯您的权益,请联系客服反馈,我们会尽快为您处理(人工客服工作时间:9:00-18:30)。
18种危险工艺现场检查表
序号检查内容依据存在问题1、光气及光气化工艺安全控制的基本要求
(1)事故紧急切断阀;安监总管三〔2009〕116号
(2)紧急冷却系统;
(3)反应釜温度、压力报警联锁;
(4)局部排风设施;
(5)有毒气体回收及处理系统;
(6)自动泄压装置;
(7)自动氨或碱液喷淋装置;
(8)光气、氯气、一氧化碳监测及超限报警;(9)双电源供电。
2、电解工艺(氯碱)安全控制的基本要求
(1)电解槽温度、压力、液位、流量报警和联锁;安监总管三〔2009〕116号
(2)电解供电整流装置与电解槽供电的报警和联锁;(3)紧急联锁切断装置;
(4)事故状态下氯气吸收中和系统;
(5)可燃和有毒气体检测报警装置。
3、氯化工艺安全控制的基本要求
(1)反应釜温度和压力的报警和联锁;安监总管三〔2009〕116号
(2)反应物料的比例控制和联锁;(3)搅拌的稳定控制;
(4)进料缓冲器;
(5)紧急进料切断系统;
(6)紧急冷却系统;
(7)安全泄放系统;
(8)事故状态下氯气吸收中和系统;(9)可燃和有毒气体检测报警装置。
4、硝化工艺安全控制的基本要求
(1)反应釜温度的报警和联锁;安监总管三〔2009〕116号
(2)自动进料控制和联锁;
(3)紧急冷却系统;
(4)搅拌的稳定控制和联锁系统;
(5)分离系统温度控制与联锁;
(6)塔釜杂质监控系统;安全泄放系统。
5、合成氨工艺安全控制的基本要求
(1)合成氨装置温度、压力报警和联锁;安监总管三〔2009〕116号
(2)物料比例控制和联锁;
(3)压缩机的温度、入口分离器液位、压力报警联锁;(4)紧急冷却系统;
(5)紧急切断系统;
(6)安全泄放系统;
(7)可燃、有毒气体检测报警装置。
6、裂解(裂化)工艺安全控制的基本要求
安监总管三〔2009〕116号
(1)裂解炉进料压力、流量控制报警与联锁;安监总管三〔2009〕116号
(2)紧急裂解炉温度报警和联锁;
(3)紧急冷却系统;
(4)紧急切断系统;
(5)反应压力与压缩机转速及入口放火炬控制;(6)再生压力的分程控制;
(7)滑阀差压与料位;
(8)温度的超驰控制;
(9)再生温度与外取热器负荷控制;
(10)外取热器汽包和锅炉汽包液位的三冲量控制;(11)锅炉的熄火保护;
(12)机组相关控制;
(13)可燃与有毒气体检测报警装置。
7、氟化工艺安全控制的基本要求
(1)反应釜内温度和压力与反应进料、紧急冷却系统的报
警和联锁;
安监总管三
〔2009〕116号
(2)搅拌的稳定控制系统;
(3)安全泄放系统;
(4)可燃和有毒气体检测报警装置。
8、加氢工艺安全控制的基本要求
(1)温度和压力的报警和联锁;安监总管三〔2009〕116号
(2)反应物料的比例控制和联锁系统;(3)紧急冷却系统;
(4)搅拌的稳定控制系统;
(5)氢气紧急切断系统;
(6)加装安全阀、爆破片等安全设施;(7)循环氢压缩机停机报警和联锁;(8)氢气检测报警装置。
9、重氮化工艺安全控制的基本要求
(1)反应釜温度和压力的报警和联锁;安监总管三〔2009〕116号
(2)反应物料的比例控制和联锁系统;(3)紧急冷却系统;
(4)紧急停车系统;
(5)安全泄放系统;
(6)后处理单元配置温度监测、惰性气体保护的联锁装置。
10、氧化工艺安全控制的基本要求
安监总管三〔2009〕116号
(1)反应釜温度和压力的报警和联锁;安监总管三〔2009〕116号
(2)反应物料的比例控制和联锁及紧急切断动力系统;(3)紧急断料系统;紧急冷却系统;
(4)紧急送入惰性气体的系统;
(5)气相氧含量监测、报警和联锁;
(6)安全泄放系统;
(7)可燃和有毒气体检测报警装置。
11、过氧化工艺安全控制的基本要求
(1)反应釜温度和压力的报警和联锁;安监总管三〔2009〕116号
(2)反应物料的比例控制和联锁及紧急切断动力系统;(3)紧急断料系统;
(4)紧急冷却系统;
(5)紧急送入惰性气体的系统;
(6)气相氧含量监测、报警和联锁;
(7)紧急停车系统;
(8)安全泄放系统;
(9)可燃和有毒气体检测报警装置。
12、胺基化工艺安全控制的基本要求
(1)反应釜温度和压力的报警和联锁;安监总管三〔2009〕116号
(2)反应物料的比例控制和联锁系统;(3)紧急冷却系统;
(4)气相氧含量监控联锁系统;
(5)紧急送入惰性气体的系统;
(6)紧急停车系统;
(7)安全泄放系统;
(8)可燃和有毒气体检测报警装置。
13、磺化工艺安全控制的基本要求
(1)反应釜温度的报警和联锁;安监总管三〔2009〕116号
(2)搅拌的稳定控制和联锁系统;(3)紧急冷却系统;
(4)紧急停车系统;
(5)安全泄放系统;
(6)三氧化硫泄漏监控报警系统。
14、聚合工艺安全控制的基本要求
〔2009〕116号(2)紧急冷却系统;
(3)紧急切断系统;
(4)紧急加入反应终止剂系统;
(5)搅拌的稳定控制和联锁系统;
(6)料仓静电消除、可燃气体置换系统,可燃和有毒气体检测报警装置;
(7)高压聚合反应釜设有防爆墙和泄爆面。
15、烷基化工艺安全控制的基本要求
(1)反应物料的紧急切断系统;安监总管三〔2009〕116号
(2)紧急冷却系统;
(3)安全泄放系统;
(4)可燃和有毒气体检测报警装置。
16、新型煤化工工艺安全控制的基本要求
(1)反应器温度、压力报警与联锁;安监总管三〔2009〕116号
(2)进料介质流量控制与联锁;(3)反应系统紧急切断进料联锁;(4)料位控制回路;
(5)液位控制回路;
(6)H2/CO比例控制与联锁;
(7)NO/O2比例控制与联锁;
(8)外取热器蒸汽热水泵联锁;(9)主风流量联锁;
(10)可燃和有毒气体检测报警装置;(11)紧急冷却系统;
(12)安全泄放系统。
17、电石生产工艺安全控制的基本要求
(1)设置紧急停炉按钮;安监总管三〔2009〕116号
(2)电炉运行平台和电极压放视频监控、输送系统视频监控和启停现场声音报警;
(3)原料称重和输送系统控制;
(4)电石炉炉压调节、控制;
(5)电极升降控制;
(6)电极压放控制;
(7)液压泵站控制;
(8)炉气组分在线检测、报警和联锁;
(9)可燃和有毒气体检测和声光报警装置;设置紧急停车按钮。
18、偶氮化工艺安全控制的基本要求
〔2009〕116号(2)反应物料的比例控制和联锁系统;
(3)紧急冷却系统;
(4)紧急停车系统;
(5)安全泄放系统;
(6)后处理单元配置温度监测、惰性气体保护的联锁装置。