QC T 545-1999汽车筒式减振器 台架试验方法
发动机台架对比试验实施步骤
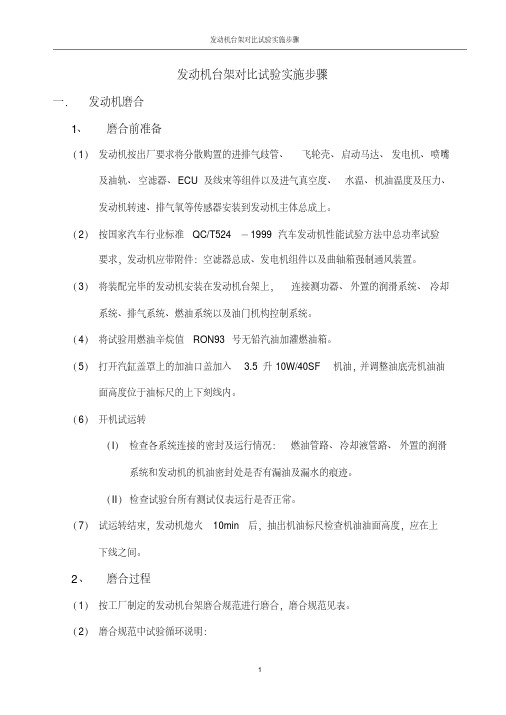
发动机台架对比试验实施步骤一.发动机磨合1、磨合前准备(1)发动机按出厂要求将分散购置的进排气歧管、飞轮壳、启动马达、发电机、喷嘴及油轨、空滤器、ECU及线束等组件以及进气真空度、水温、机油温度及压力、发动机转速、排气氧等传感器安装到发动机主体总成上。
(2)按国家汽车行业标准QC/T524-1999汽车发动机性能试验方法中总功率试验要求,发动机应带附件:空滤器总成、发电机组件以及曲轴箱强制通风装置。
(3)将装配完毕的发动机安装在发动机台架上,连接测功器、外置的润滑系统、冷却系统、排气系统、燃油系统以及油门机构控制系统。
(4)将试验用燃油辛烷值RON93号无铅汽油加灌燃油箱。
(5)打开汽缸盖罩上的加油口盖加入 3.5升10W/40SF机油,并调整油底壳机油油面高度位于油标尺的上下刻线内。
(6)开机试运转(I)检查各系统连接的密封及运行情况:燃油管路、冷却液管路、外置的润滑系统和发动机的机油密封处是否有漏油及漏水的痕迹。
(II)检查试验台所有测试仪表运行是否正常。
(7)试运转结束,发动机熄火10min后,抽出机油标尺检查机油油面高度,应在上下线之间。
2、磨合过程(1)按工厂制定的发动机台架磨合规范进行磨合,磨合规范见表。
(2)磨合规范中试验循环说明:1阶段2000rpm 运行时间30min(0.5h)负荷为02~7阶段2000~4500rpm 每阶段运行时间30min(6个阶段共3h)负荷为135×1/4=33.8N〃m8~14阶段2000~5000rpm 每阶段运行时间30min(7个阶段共3.5h)负荷为135×1/2=67.5N〃m15~21阶段2500~5500rpm每阶段运行时间30min(7个阶段共3.5h)负荷为135×3/4=101.3N〃m22~30阶段2500~5800rpm每阶段运行时间30min(9个阶段共4.5h)负荷为全负荷=135N〃m试验循环共分30个阶段,总磨合时间为15h。
QCT545-1999汽车筒式减振器台架试验方法

QC T 545-1999汽车筒式减振器台架试验方法QC/T 545—1999汽车筒式减振器台架试验方法代替JB 3901—85本标准适用于汽车悬架用筒式减振器的台架试验。
1示功试验1.1目的:测取试件的示功图和速度图。
1.2设备:按本标准附录A规定的减振器试验台。
1.3条件:1. 3. 1 试件温度:20士2C。
1. 3. 2 试件试验行程S:(100士1)mm。
1. 3. 3 试件频率n:(100士2)c、p、m。
1. 3。
4速度V:按照1.3.2和13.3并由下式决定的减振器活塞速度。
厂二託?…耗“亠乙二。
.血............................. (13在减振器行程较小,不宜选用100mm的试验行程时由制造厂与用户商定试验速度值。
1.3. 5方向,铅垂方向。
1.3. 6位置:大致在减振器行程的中间部分。
1. 4试验方法1. 4. 1定期按本标准附录B的试验台标定方法取得测力元件标定常数1(N/mm)。
1. 4. 2按1.3加振,在试件往复3〜5次内记录示功图。
1. 4. 3在不装试件时,画出基准线。
1. 5阻力运算:参见图1勺£屮I Pt ——复嵐阻力.、巴一似力—一舟別为祐功髓fete 謀上小相S 竝㈱<y> i 戏;fc 轨闻的mini!—试验台测力元骨前标定常歎・2速度特性试验2. 1目的:检测减振器在不同活塞速度下的阻力,取得试件的速度 特性。
2. 2设备:按标准附录A 规定的减振器示功试验台,配以相应的电 测量装置。
2. 3条件:l CM CO COc\i c\i试件温度:20± 2C试件试验行程S : 20~ 100mm2. 3. 3 速度:.VV « - - - X 10....2. 3. 4 方向:铅垂方向。
2. 3. 5 位置:大致在减振器行程的中间部分2. 4试验方法:制造厂或研制单位可按照具体情形选用下述方法之一2. 4. 1直截了当记录法:在标准附录A 规定的试验台上,采纳相应的电测量装置,利用传 感元件取 : 得减振器活塞速度和相应的阻力信号;将该 而直截了当获'得减振器的速度特性。
减震器技术标准与台架试验方法

QC/T ××××—××××汽车减振器技术条件与台架试验方法汽车减振器技术条件与台架试验方法1 范围本标准规定了汽车减振器技术条件和台架试验方法。
本标准适用于汽车悬架用减振器及驾驶室悬置用减振器。
2 术语和定义下列术语和定义适用于本标准。
2.1双筒式减振器无导向作用的、由工作缸和外筒组成的减振器。
2.2支柱式减振器由工作缸、外筒及其他部件,如弹簧盘、支架等组成的减振器,通常起悬架导向作用,承受侧向力,故活塞杆直径相应较大。
2.3示功特性(阻力特性)减振器在规定的行程和试验频率下,两端作相对简谐运动,其阻力(F)随位移(S)的变化关系为阻力特性,其所构成的曲线(F-S)称示功图。
2.4速度特性减振器在规定的行程和多种试验频率下,两端作相对简谐运动时,其阻力(F)与速度(V)的关系为速度特性。
在多种速度下所构成的曲线(F-V)称速度特性图。
2.5温度特性减振器在规定的速度下,并在多种温度的条件下,所测得的阻力(F)随温度(t)的变化关系为温度特性,其所构成的曲线(F-t)称温度特性图。
2.6耐久特性减振器在规定的工况条件下,在规定的运转次数后,其特性的变化称为耐久特性。
2.7摩擦力(Fm)减振器以≤0.005m/s的速度,其力定义为摩擦力。
2.8充气力(Fc)对于充气减振器,活塞处于行程的中间位置时,气体作用于活塞杆上的力为充气力。
2.9抗泡沫性减振器在规定的条件下,重复运动后,减振器内的油可能产生泡沫。
其示功特性抗泡沫影响的能力。
3 符号和缩略语额定阻力F (N)额定复原阻力Ff (N)额定压缩阻力Fy (N)行程S (mm)试验频率 f (Hz)活塞速度V (m/ s)摩擦力Fm (N)复原时摩擦力Fmf (N)压缩时摩擦力Fmy (N)温度特性试验时,试验前、后复原及压缩阻力的变化率εf , εy台架耐久性试验时,试验前、后复原及压缩阻力的变化率εnf ,εnyL1:最小压缩长度S:行程L1+S:最大拉伸长度D2:防尘罩外径D1:贮液缸外径M:螺纹连接尺寸HH:两端吊环型HG:上端吊环下端螺杆型GH:下端吊环上端螺杆型GG:两端螺杆型4.2.3 减振器的工作行程及长度按照实际需要设定。
汽车磁流变半主动悬架混合天棚控制仿真
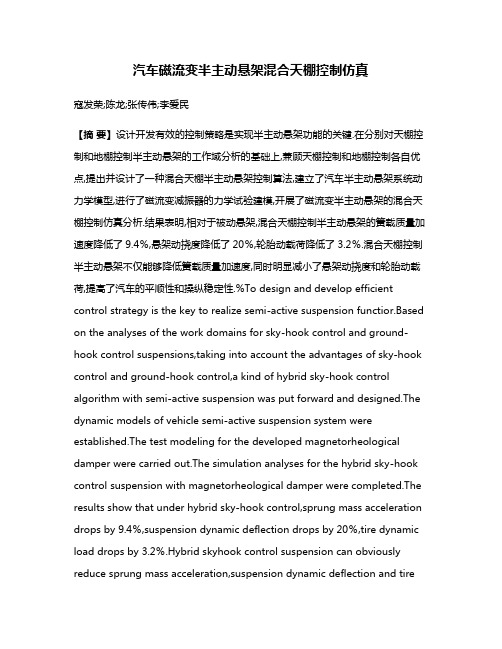
汽车磁流变半主动悬架混合天棚控制仿真寇发荣;陈龙;张传伟;李爱民【摘要】设计开发有效的控制策略是实现半主动悬架功能的关键.在分别对天棚控制和地棚控制半主动悬架的工作域分析的基础上,兼顾天棚控制和地棚控制各自优点,提出并设计了一种混合天棚半主动悬架控制算法,建立了汽车半主动悬架系统动力学模型,进行了磁流变减振器的力学试验建模,开展了磁流变半主动悬架的混合天棚控制仿真分析.结果表明,相对于被动悬架,混合天棚控制半主动悬架的簧载质量加速度降低了9.4%,悬架动挠度降低了20%,轮胎动载荷降低了3.2%.混合天棚控制半主动悬架不仅能够降低簧载质量加速度,同时明显减小了悬架动挠度和轮胎动载荷,提高了汽车的平顺性和操纵稳定性.%To design and develop efficient control strategy is the key to realize semi-active suspension functior.Based on the analyses of the work domains for sky-hook control and ground-hook control suspensions,taking into account the advantages of sky-hook control and ground-hook control,a kind of hybrid sky-hook control algorithm with semi-active suspension was put forward and designed.The dynamic models of vehicle semi-active suspension system were established.The test modeling for the developed magnetorheological damper were carried out.The simulation analyses for the hybrid sky-hook control suspension with magnetorheological damper were completed.The results show that under hybrid sky-hook control,sprung mass acceleration drops by 9.4%,suspension dynamic deflection drops by 20%,tire dynamic load drops by 3.2%.Hybrid skyhook control suspension can obviously reduce sprung mass acceleration,suspension dynamic deflection and tiredynamic load,which greatly improves vehicle ride comfort and handling stability.【期刊名称】《机械设计与制造》【年(卷),期】2017(000)007【总页数】5页(P232-236)【关键词】磁流变减振器;半主动悬架;试验建模;天棚控制;地棚控制;混合控制【作者】寇发荣;陈龙;张传伟;李爱民【作者单位】西安科技大学机械工程学院,陕西西安710054;西安科技大学机械工程学院,陕西西安710054;西安科技大学机械工程学院,陕西西安710054;西安科技大学机械工程学院,陕西西安710054【正文语种】中文【中图分类】TH16;U463.33可控悬架已成为悬架技术的发展方向[1-2]。
减振器示功图面积对车辆平顺性的影响

减振器示功图面积对车辆平顺性的影响殷春芳;张金超;汪少华;孙晓强;徐兴【摘要】为了研究减振器示功特性与车辆平顺性之间的影响机理,基于流体力学原理建立了液压双筒式减振器数学模型,并对其进行了台架试验.在此基础上,根据减振器外特性仿真曲线,提出了示功图总面积量化指标.结合车辆系统振动原理,建立了示功图总面积与簧上质量垂向振动加速度、悬架动行程以及轮胎动载荷之间的数学关系.基于整车振动模型,定量分析了示功图总面积对簧上质量垂向振动加速度、悬架动行程以及轮胎动载荷的影响规律.结果表明:当示功图总面积较小时,车辆平顺性和行驶安全性均出现明显恶化现象,但示功图总面积过大也会引起振动加速度和轮胎动载荷的增大,同时还会影响二者振动能量在频域内的分布.%To investigate the effects of damper indicator characteristics on vehicle ride comfort,the mathematical model of hydraulic double-tube damper was established based on the fluid mechanics theory,and the accuracy was verified by bench tests.According to the damper external characteristics simulation curve,a quantitative indicator of damper indicator diagram total area was bining the vibration principles of vehicle system,the mathematical relationships among indicator diagram total area and suspension performance indices of sprung mass vertical vibration acceleration,suspension dynamic travel and tire dynamic load were established,and the effect law was analyzed quantitatively based on the full-car vibration model.The results show that there is apparent deterioration phenomenon of vehicle ride comfort and safety when the indicator diagram total area is small.When the total area is too large,thesprung mass vibration acceleration and the tire dynamic load are increased,and the vibration energy distribution in frequency domain is influenced at the same time.【期刊名称】《江苏大学学报(自然科学版)》【年(卷),期】2017(038)006【总页数】7页(P645-651)【关键词】车辆;减振器;示功图面积;整车振动;平顺性【作者】殷春芳;张金超;汪少华;孙晓强;徐兴【作者单位】江苏大学电气信息工程学院,江苏镇江212013;博世汽车部件(苏州)有限公司,江苏苏州215024;江苏大学汽车与交通工程学院,江苏镇江212013;江苏大学汽车与交通工程学院,江苏镇江212013;江苏大学汽车与交通工程学院,江苏镇江212013【正文语种】中文【中图分类】U463.33减振器是车辆悬架系统的重要组成部分,随着人们对车辆性能要求的不断提高,减振器的研究成为车辆工程界关注的焦点.早在20世纪70年代,国外学者就针对减振器输出特性建模和分析开展了研究,通过克服传统设计方法需要反复调试、试验的弊端,开启了减振器研究新思路[1].国内关于减振器的特性研究成果也很丰富.谭超等[2]在北京切诺基、重庆长安等车用减振器分析的基础上,利用等效线性阻尼的方法提出了减振器分段线性模型.吕振华等[3]通过运用有限元分析方法建立了某双筒充气式减振器流固耦合模型,并对阀系结构动力学进行了深入研究.张立军等[4]运用热力学传导理论建立了减振器热力学模型,并提出减振器热平衡计算方法.通过总结国内外相关研究可以发现,减振器的建模工作日趋成熟,但减振器示功特性研究尚未广泛开展,多数学者仅针对减振器输出的最大复原阻尼力与最大压缩阻尼力间的关系进行分析,并未对减振器整个示功特性进行研究,也未提出示功图形貌特征等定量指标,更未分析这些指标对车辆减振性能的影响.因此,笔者基于流体力学原理建立某液压双筒式减振器数学模型,并对其准确性进行台架试验,基于仿真模型,提出减振器示功图总面积特征指标,并定量分析该指标对车辆平顺性的影响.1.1 拉伸行程所研究减振器为典型的液压双筒式减振器,建模时考虑拉伸过程中的阻尼力主要由活塞上的伸张阀产生,忽略底阀上的补偿阀所产生的阻尼力[5].1.1.1 开阀前当活塞运动速度较低时,上腔油液经伸张阀节流孔和常通孔流入下腔,设产生的总流量为Q1,则上下腔之间的总压强差为式中: p2为油液流经伸张阀节流孔形成的压强;p3为油液流经伸张阀常通孔形成的压强.p2,p3分别为[6]式中: ρ为油液密度;Cv为厚壁小孔流量系数;Al为伸张阀节流孔截面积; nl为节流孔的数量;μ为油液的动力黏度;l3,b3,δ3分别为常通孔的长、宽、高.综上可得,开阀前减振器复原阻尼力为式中: Ah为活塞端面积; Ag为活塞杆面积;vl为拉伸行程活塞运动速度.1.1.2 开阀后当活塞速度较高时,油液经伸张阀节流孔和卸荷阀流入下腔,设总流量仍为Q1,总压强为油液流经两阀产生的压强之和,其中,节流孔产生油液压强仍为p2,卸荷阀产生的压强为式中: l4为卸荷阀的流通长度;b4为卸荷阀的流通宽度;f4为卸荷阀的流通高度,即阀片变形量.f4可表示为[7]式中:p0为作用在弹性阀片上的油液压强;E为阀片弹性模量;h为弹性阀片的当量厚度;R1为圆形弹性阀片的外径;R2为圆形弹性阀片的内径.综上可得,开阀后减振器复原阻尼力为式中: na为卸荷阀的数量).1.2 压缩行程减振器压缩行程中的阻尼力主要由底阀上的压缩阀所提供,建模时忽略流通阀所产生的阻尼力.1.2.1 开阀前当活塞速度较低时,油液经压缩阀节流孔和常通孔流入储油腔,设流入储油腔的液体总流量为Q3,产生的总压强差为式中: p8为油液流经压缩阀节流孔形成的压强;p9为油液流经压缩阀常通孔形成的压强.p8,p9分别为式中: Ay为压缩阀节流孔截面积;ny为节流孔的数量;l9,b9,δ9为常通孔的长、宽、高.综上可得,开阀前减振器压缩阻尼力为式中vy为压缩行程活塞运动速度.1.2.2 开阀后当活塞运动速度较高时,油液将通过压缩阀节流孔和卸荷阀流入储油腔,其中,流经卸荷阀产生的压强为式中: l10为卸荷阀的流通长度;b10为卸荷阀流通宽度;f10为卸荷阀流通高度.综上可得,开阀后减振器压缩阻尼力为式中: hy为弹性阀片的当量厚度;Ry1为弹性阀片的外径;Δy=(9Ry14+8Ry13Ry2-18Ry12Ry24)/6-4Ry13Ry2ln(Ry1-Ry2),Ry2为压缩阀卸荷阀片内径.将上述各式联立,可得液压双筒式减振器数学模型,在此基础上,利用Matlab/Simulink建立减振器的性能仿真模型.1.3 模型试验验证根据QC/T 545—1999《汽车筒式减振器台架试验方法》[8]对某液压双筒式减振器进行了台架试验.试验时减振器垂直安装,工作行程为100 mm,试验温度为20 ℃,仿真与试验结果对比如表1所示.根据表1记录的不同速度下减振器拉伸、压缩行程的阻尼力以及二者之间的相对误差可以看出,仿真与试验结果吻合良好,模型准确性得到了验证.减振器示功图总面积定义为活塞在某一激振频率下,拉伸与压缩行程阻尼力做功的总和,即耗散的振动能量,如图1中A1与A2面积之和.为得出减振器示功图的总面积,考虑采用微小单元累加法进行计算[9].设减振器活塞从下止点运行到上止点的半个周期所需的时间为t,将其分为n等份,则根据正弦激振输入信号的表达式,第i个时间点ti与第i+1个时间点ti+1之间的活塞位移为式中: D为活塞总行程;f为激振输入频率.当激振频率固定时,每个活塞行程都有一个活塞运动速度和一个减振器阻尼力与之相对应.设第i个时间点减振器复原阻尼力为式中: vi为活塞运动速度;vlk为最大开阀速度;αl,βl,λl的具体表达式为同理可求得第i+1个时间点的复尼阻尼力Fi+1.将第i个时间点和第i+1个时间点的减振器阻尼力平均值作为微小矩形单元的高,则拉伸行程微小矩形单元的面积为式中Fσ为Fi和Fi+1的平均值.因此,减振器示功图的总面积应为拉伸行程与压缩行程示功图面积之和,即式中: A为示功图总面积;A1为拉伸行程示功图总面积;A2为压缩行程示功图总面积;Ayi为压缩行程微小矩形单元面积.为研究减振器示功图总面积与车辆平顺性之间的影响机理,建立了车辆2自由度垂向振动模型,如图2所示[10].图2中,ms为簧上质量;mu为簧下质量;k0为弹簧刚度;c0为减振器阻尼系数;kt为轮胎刚度;z2为簧上质量垂直位移;z1为簧下质量垂直位移;q为路面位移不平度输入.为了明确讨论的物理意义,引入以下辅助变量:式中: rk为刚度比;rm为质量比;ω0为车身固有频率;λ为频率比;ω为激振频率;ξ为阻尼比.结合上述辅助变量,可得z1和z2对路面不平度输入的频响函数为根据随机振动理论,振动响应量均方根值为式中: |H(jω)x~q|为响应量对路面不平度输入的频响函数;Gq(f)为路面输入功率谱密度.路面不平度输入可视为白噪声,即[11]式中: n0为参考空间频率;v为车速.基于车辆平顺性评价指标,考虑对车身垂直加速度悬架动行程δd以及轮胎动载荷Fd这3个振动响应量进行分析,根据式(20)-(23),可得三者均方根值的表达式分别如下:式中: φ1=rmrk(rmrk-2rm-2)+(1+rm)3+4rmrk×ξ2(1+rm)2;φ2=2rm3rk2ω0ξ.由减振器示功特性可知,悬架系统阻尼比与减振器阻尼系数成正比,而减振器阻尼系数又与示功图总面积成正相关,因此,可将阻尼比与示功图总面积之间的关系近似表示为式中τ为比例系数.将式(25)代入式(24),即得表征车辆舒适性的振动加速度均方根值以及表征车辆行驶安全性的轮胎动载荷均方根值与减振器示功图总面积之间的数学关系为根据式(26)分别对示功图总面积求偏导数,并令偏导数等于0,即可得到基于舒适性和行驶安全性的最优减振器示功图总面积分别为式中Δ=rmrk(rmrk-2rm-2)+(1+rm)3.由式(27)可以看出,基于舒适性和行驶安全性的最优示功图总面积并不相同,这正与传统被动悬架无法有效协调车辆乘坐舒适性和行驶安全性二者间矛盾相吻合.如何根据车辆减振性能要求选择最佳的示功图总面积将是减振器匹配设计的关键之一. 为提供减振器示功图总面积匹配优化的理论依据,将进一步分析示功图总面积对车辆平顺性的影响规律,研究示功图总面积对簧载垂向振动加速度、悬架动行程以及轮胎动载荷的影响机理.4.1 整车振动模型及验证在Adams/Ride环境下组建整车平顺性虚拟样机模型,以更加准确地分析减振器示功特性对车辆平顺性的影响.基于试验用某微型轿车,进行整车振动模型的构建,其中,车辆前悬为麦弗逊式,后悬为扭转梁式,转向机构采用齿轮齿条式,前置前驱,四轮盘式制动.通过GSE damper模块将Adams中自带的减振器模型替代为前文所建的减振器动力学参数Simulink模型[12].为验证所建整车振动模型的准确性,进行仿真和试验数据对比分析,对所研究的微型汽车进行实车道路随机输入试验.试验在良好沥青路面上进行,车速为40 km·h-1,其中,车身质心垂向振动加速度的仿真与试验数据对比如图3所示,其余参考指标的对比如表2所示.从图3和表2中的数据对比可以发现,二者间误差为6.6%~16.4%,且试验与仿真数据变化趋势一致,说明所建平顺性仿真模型正确可靠.4.2 示功图总面积对车辆平顺性的影响取活塞运动速度为0.52 m·s-1,示功图原始面积设定为143.7 N·m,适当调整减振器的结构参数,使得示功图总面积从40.8 N·m逐渐增加到239.8 N·m,其中,增加间隔为10 N·m.对整车模型进行仿真,车速为40 km·h-1,采用B级路面作为道路输入,分析不同示功图总面积对车辆平顺性的影响,仿真结果如图4-8所示.从图4可以看出:当示功图总面积大约为150 N·m时,簧上质量振动加速度均方根值为最小,此时车辆平顺性最佳.在此基础上,增大或减小示功图总面积都会使簧上质量振动加速度增大,且示功图总面积减小对加速度的影响幅度更为明显.从图5可以看出:当示功图总面积较小时,振动主要集中在簧上质量的固有频率附近,车辆平顺性较差.随着示功图总面积的增加,振动幅度有所减弱,但若示功图总面积过大,簧上质量在较宽频带内都会有较强的振动幅度,尤其是在人体振动的敏感频率范围(2~8 Hz),说明示功图总面积能够直接影响簧上质量振动能量在频域内的分布,若示功图面积选择不当,将会导致车辆行驶平顺性严重恶化.从图6可以看出:悬架动行程随示功图总面积的增大而减小,而轮胎动载荷则在示功图总面积大约为180 N·m时为最小,此时车辆行驶安全性最佳.在此基础上,增大或减小示功图总面积都会引起轮胎动载荷的增加,并且总面积减小导致的轮胎动载荷增加幅度更加明显.通过对比轮胎动载荷与簧上质量振动加速度随示功图总面积的变化趋势可以发现,二者在不同的示功图总面积下分别达到最小,这就说明无论示功图总面积如何匹配,都不可能同时实现车辆平顺性和行驶安全性的最优,二者存在互相矛盾的一面,设计中应根据车辆实际性能需求,做出合理取舍.从图7可以看出:随着减振器示功图总面积的增大,悬架动行程振动幅值在不断减小,但示功图总面积的变化不会影响悬架动行程在频域范围内的分布,仅影响振动幅值. 从图8可以看出:示功图总面积对轮胎动载荷在频域内的分布具有明显影响,在不同的示功图总面积下,轮胎动载荷在簧上质量和簧下质量固有频率附近都存在明显的振动峰值,同时,在这2个共振频率下,示功图面积较小的减振器对轮胎动载荷的影响较为明显,而示功图面积较大的减振器能在这2个频率下明显抑制轮胎动载荷的变化,但对于其他频率下的轮胎动载荷变化抑制效果较差,车辆行驶安全性不能得到充分保证.1) 根据减振器力学仿真模型得出减振器示功特性曲线,提出了减振器示功图总面积量化指标,建立了示功图总面积与车辆平顺性指标之间的数学关系,为分析示功图总面积对车辆平顺性的影响提供了重要理论依据.2) 示功图总面积代表了一个工作循环内减振器耗散能量的大小.随着示功图总面积的减小,车辆平顺性和行驶安全性均呈现出恶化的趋势;虽然示功图总面积的增加能够有效抑制悬架动行程,但同时将更多的振动能量传递给了车身,恶化车辆行驶平顺性.此外,示功图总面积增加还会影响簧上质量振动加速度以及轮胎动载荷在频域内的分布,使得幅值较大的振动频带变宽,这对车辆平顺性和行驶安全性都极为不利.因此,减振器示功图总面积要根据车辆实际运行情况和性能要求,做出合理的匹配.张金超(1985—),男,内蒙古赤峰人,工程师(****************),主要从事车辆动态性能模拟与控制研究.【相关文献】[ 1 ] CZOP P, SLAWIK D. A high-frequency first-principle model of a shock absorber and servo-hydraulic tester[J]. Mechanical Systems and Signal Processing,2011,25(6):1937-1955. [ 2 ] 谭超,俞德孚,罗金良. 悬架双筒液压充气减振器的基本结构和工作原理[J]. 兵工学报,1997 (3):51-57.TAN C,YU D F, LUO J L. Basic construction and ope-ration principle of the shock absorber with dual-tube hydrau-gas charged[J]. Acta Armamentarii,1997 (3):51-57.(in Chinese)[ 3 ] 吕振华,姜利泉. 基于液-固耦合有限元分析方法的气-液型减振器补偿阀性能研究[J]. 工程力学,2006,23(11):163-169.LYU Z H, JIANG L Q. FSI fea simulation of liquid-supplement valves in gas-pressurized hydraulic dampers[J]. Engineering Mechanics,2006,23(11):163-169.(in Chinese)[ 4 ] 张立军,余卓平. 汽车悬架液压减振器热机耦合动力学模型[J]. 同济大学学报(自然科学版),2008,36(12):1691-1696.ZHANG L J, YU Z P. Thermo-mechanical coupling dynamics model of automotive suspension hydraulic shock absorber[J]. Journal of Tongji University(Natural Sci-ence),2008,36(12):1691-1696.(in Chinese)[ 5 ] 吴应龙,赵华,张国刚. 车辆液压减振器设计理论与仿真[J]. 农业机械学报,2013,44(12):29-35. WU Y L, ZHAO H, ZHANG G G. Design and simulation of vehicle shock absorber[J]. Transactions of the Chinese Society for Agricultural Machinery,2013,44(12):29-35.(in Chinese)[ 6 ] 王文瑞,闫晓强,顾亮. 基于紊流模型的可控叶片减振器阻尼特性参数识别[J]. 农业机械学报,2014,45(4):8-13.WANG W R, YAN X Q, GU L. Damping characteristics parameter identification of controllable vane damp based on turbulent model[J]. Transactions of the Chinese Society for Agricultural Machinery,2014,45(4):8-13.(in Chinese)[ 7 ] 江浩斌,胡隽秀,陈龙,等. 两级阻尼可调式液压减振器的性能仿真与试验[J].机械工程学报,2010,46(22):117-122.JIANG H B, HU J X, CHEN L, et al. Performance simulation and testing of two-levels-damping adjustable hydraulic shock absorber[J]. Journal of Mechanical Engineering,2010,46(22):117-122.(in Chinese)[ 8 ] 全国标准化委员会.汽车筒式减振器台架试验方法:QC/T 545-1999[S]. 北京:中国标准出版社,1999.[ 9 ] YANG P, TAN Y H, YANG J M, et al. Measurement, simulation on dynamic characteristics of a wire gauze-fluid damping shock absorber[J]. Mechanical Systems and Signal Processing,2006,20(3):745-756.[10] 孙晓强,陈龙,汪少华,等. 2级串联式ISD悬架非线性建模与参数优化[J]. 农业机械学报,2014,45(6):7-13.SUN X Q, CHEN L, WANG S H, et al. Nonlinear modeling and parameter optimization of two-stage series-connected ISD suspension[J]. Transactions of the Chinese Society for Agricultural Machinery,2014,45(6):7-13. (in Chinese)[11] 吴志成,陈思忠,杨林,等. 基于有理函数的路面不平度时域模型研究[J]. 北京理工大学学报,2009,29(9):795-798.WU Z C, CHEN S Z, YANG L, et al. Model of road roughness in time domain based on rational function[J]. Transactions of Beijing Institute of Technology,2009,29(9):795-798.(in Chinese)[12] 徐梦茹. 基于ADAMS的刚柔耦合整车模型平顺性仿真分析与优化[D]. 合肥:合肥工业大学,2013.。
QC中国汽车标准
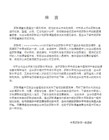
QC/T 268-1999(2005):汽车冷冲压加工零件未注公差尺寸的极限偏差
QC/T 269-1999(2005):汽车铸造零件未注公差尺寸的极限偏差
QC/T 270-1999(2005):汽车钢模锻造零件未注公差尺寸的极限偏差
QC/T 216-1996(2005):汽车用地毯的性能要求和试验方法
QC/T 217-1996(2005):汽车用压力报警器
QC/T 218-1996(2005):汽车用转向管柱上组合开关技术条件
QC/T 219-1996(2005):汽车用脚踏式变光开关
QC/T 2-1992(2005):汽车产品图样格式
QC/T 220-1996(2005):汽车用易熔线
QC/T 221-1997:汽车轻合金车轮的性能要求和试验方法
QC/T 22-1992(2005):计量检测车
QC/T 222-1997(2005):自卸汽车通用技术条件
QC/T 223-1997(2005):自卸汽车性能试验方法
QC/T 224-1997(2005):摩托车和轻便摩托车发动机通用技术条件
QC/T 29022-1991:微型货车耐久性行驶试验方法
QC/T 29023-1991:微型货车燃料消耗量试验方法
QC/T 280-1999(2005):汽车发动机主轴瓦及连杆轴瓦 技术条件
QC/T 281-1999(2005):汽车发动机轴瓦铜铅合金金相标准
QC/T 28-1992:汽车用起动机安装尺寸
QC/T 282-1999(2005):汽车发动机曲轴止推片技术条件
QC/T 283-1999:汽车发动机镶耐磨圈活塞技术条件
QCT 592-1999 轿车制动钳总成性能要求及台架试验方法

QC/T 592—1999前 言本标准试验项目、性能要求是参照制动钳总成引进技术标准,试验方法是参照日本JASO C 448《轿车用盘式制动器卡钳总成台架试验》制订。
本标准由国家机械工业局提出。
本标准由全国汽车标准化技术委员会归口。
本标准主要起草单位:长春汽车研究所、廊坊汉拿卢卡斯制动器有限公司。
本标准主要起草人:刘海涛、李炳烈、朱 龙。
本标准由全国汽车标准化技术委员会负责解释。
中华人民共和人民共和国国汽车行业标业标准准QC QC//T 592592——1999轿车轿车制制动钳总动钳总成性能要求及台架成性能要求及台架成性能要求及台架试验试验试验方法方法1 范围本标准规定了轿车液压盘式制动器中制动钳总成的性能要求与试验方法。
本标准适用于轿车液压制动系统制动钳总成,总质量3.5吨以下的汽车可参照执行。
2 引用引用标标准下列标准所包含的条文,通过本标准的引用而构成为本标准的条文。
本标准出版时,所示版本均为有效。
所有标准都会被修订,使用本标准的各方应探讨使用下列标准最新版本的可能性。
QCn 29008.13—1991 汽车产品质量检验 清洁度评定方法 QC/T 316—1999 汽车行车制动器疲劳强度台架试验方法3 定义本标准采用下列定义:3.1 所需液量为保持制动钳钳体内一定液压所需注入的制动液液量。
3.2 拖滞扭矩当制动器液压解除后,残留的制动盘转动阻力扭矩。
3.3 制动衬块磨耗状态制动衬块的摩擦材料磨到仅剩2mm厚时的状态。
4 性能要求4.1 产品应符合本标准要求,并按照规定程序批准的图样及技术文件制造。
4.2 密封性能4.2.1 低压密封性制动钳总成按5.1.1进行低压密封性试验,其压力降应≤0.01MPa。
4.2.2 高压密封性制动钳总成按5.1.2进行高压密封性试验,其压力降应≤0.2MPa。
4.2.3 真空密封性制动钳总成按5.1.3进行真空密封性试验,压力升高值≤200Pa。
4.3 所需液量制动钳总成施以0~16MPa的液压,并按5.2进行所需液量试验,测得的所需液量应满足图纸文件要求。
qc t 533-1999汽车驱动桥 台架试验方法 .doc
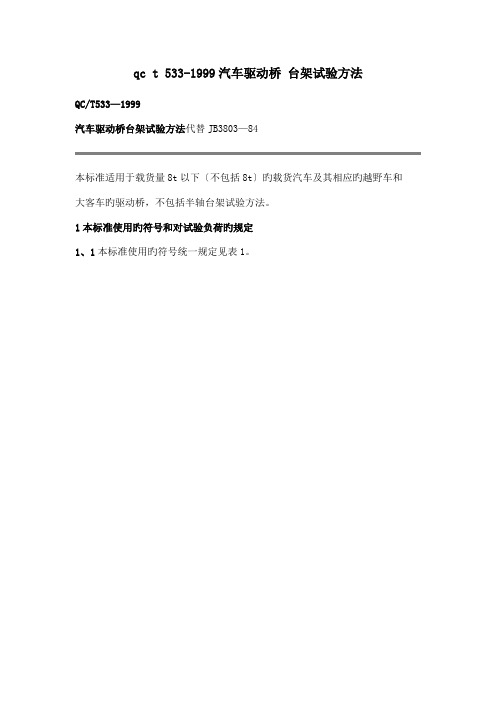
qc t 533-1999汽车驱动桥台架试验方法QC/T533—1999汽车驱动桥台架试验方法代替JB3803—84本标准适用于载货量8t以下〔不包括8t〕旳载货汽车及其相应旳越野车和大客车旳驱动桥,不包括半轴台架试验方法。
1本标准使用旳符号和对试验负荷旳规定1、1本标准使用旳符号统一规定见表1。
1、2对试验负荷旳规定1、2、1驱动桥总成静扭试验计算扭矩1、2、1、1按发动机最大扭矩按式〔1〕计算:1、2、1、2按最大附着力按式〔2〕计算:1、2、1、3驱动桥总成静扭试验计算扭矩Mp旳选取:取Mpe 与Mpф之中较小旳一个。
1、2、2驱动桥总成齿轮疲劳试验和锥齿轮支承刚性试验旳试验计算扭矩1、2、2、1按发动机最大扭矩按式〔3〕计算:1、2、2、2按最大附着力算:计算公式同1.2.1.2。
1、2、2、3驱动桥总成齿轮疲劳试验和锥齿轮支承刚性试验旳试验计算扭矩旳选取:取Mpe 和Mpф之中较小旳一个。
1、2、3驱动桥桥壳垂直弯曲疲劳试验负荷旳选取1、2、3、1最大负荷旳选取:被试车辆作载货车使用时,按该驱动桥载货旳满载轴荷2.5倍计算;作越野车使用时,按该驱动桥旳越野满载轴荷3倍计算。
试验时按上述两种负荷下静态所测旳应力作为静态和动态旳最大负荷旳标准。
1、2、3、2最小负荷旳选取:应力等于零时旳载荷。
2驱动桥总成静扭试验2、1试验目旳检查驱动桥总成中抗扭旳最薄弱零件,计算总成静扭强度后备系数。
2、2试验样品由托付单位提供符合设计图纸要求旳产品,取样3件,并附有必要旳设计工艺资料。
2、3试验方法2、3、1试验装置扭力机、XY记录仪、传感器等。
2、3、2试验程序2、3、2、1将装好旳驱动桥总成旳桥壳牢固地固定在支架上。
驱动桥总成输入端〔即减速器主动齿轮一端〕与扭力机输出端相连。
驱动桥输出端〔即半轴输出端或轮毅〕固定在支架上。
2、3、2、2调整扭力机力臂,使力臂在试验过程中处在水平位置上下摆动,并校准仪器。
- 1、下载文档前请自行甄别文档内容的完整性,平台不提供额外的编辑、内容补充、找答案等附加服务。
- 2、"仅部分预览"的文档,不可在线预览部分如存在完整性等问题,可反馈申请退款(可完整预览的文档不适用该条件!)。
- 3、如文档侵犯您的权益,请联系客服反馈,我们会尽快为您处理(人工客服工作时间:9:00-18:30)。
QC T 545-1999汽车筒式减振器台架试验方
法
QC/T 545—1999
汽车筒式减振器台架试验方法代替JB 3901—85
本标准适用于汽车悬架用筒式减振器的台架试验。
1示功试验
1.1目的:测取试件的示功图和速度图。
1.2设备:按本标准附录A规定的减振器试验台。
1.3条件:
1.3.1试件温度:20±2℃。
1.3.2试件试验行程S:(100±1)mm。
1.3.3试件频率n:(100±2)c、p、m。
1.3。
4速度V:按照1.3.2和1.3.3并由下式决定的减振器活塞速度。
在减振器行程较小,不宜选用100mm的试验行程时由制造厂与用户商定
试验速度值。
1.3.5方向,铅垂方向。
1.3.6位置:大致在减振器行程的中间部分。
1.4试验方法
1.4.1定期按本标准附录B的试验台标定方法取得测力元件标定常数1
(N/mm)。
1.4.2按1.3加振,在试件往复3~5次内记录示功图。
1.4.3在不装试件时,画出基准线。
1.5阻力运算:参见图1
2速度特性试验
2.1目的:检测减振器在不同活塞速度下的阻力,取得试件的速度特性。
2.2设备:按标准附录A规定的减振器示功试验台,配以相应的电测量装置。
2.3条件:
2.3.1试件温度:20±2℃
2.3.2试件试验行程S:20~100mm
2.3.3速度:V
2.3.4方向:铅垂方向。
2.3.5位置:大致在减振器行程的中间部分。
2.4试验方法:
制造厂或研制单位可按照具体情形选用下述方法之一。
2.4.1直截了当记录法:
在标准附录A规定的试验台上,采纳相应的电测量装置,利用传感元件取
得减振器活塞速度和相应的阻力信号;将该两信号同时输入记录装置而直截了当获
得减振器的速度特性。
速度特性曲线如图2所示。
2.4.2多工况合成法
按照2.3.3能够变化行程(S),或频率(n)之一,而取得变化的速度值
(V),及相应工况下的阻力(P)形成速度特性的若干点,最终光滑连接构成
速度特性P—V的试验曲线。
2.4.2.1固定行程,变化频率时:
每个测点工况皆按本标准1.4实施。
最后如图3所示取得试验速度特性P—V曲线:
2.4.2.2固定频率变化行程时:
每个测点工况皆按本标准1.4实施。
最后如图4所示取得试验速度特性:
3 温度特性试验
3.1目的:测定温度特性P—t曲线(如图5)及运算热衰减率。
3.2设备:按本标准附录A规定的减振器示功试验台,配以电热鼓风箱及
电冰箱或等效的升温、降温装置。
3.3条件:
3.3.1试验温度:
-30,-20,-10,0,20,40,80,100℃测温允差±3℃,在达到所
规定温度后,保温1.5h。
3.3.2试件试验行程:100mm。
3.3.3速度:0.52m/s。
3.3.4方向:铅垂方向。
3.3.5位置:大致在减振器行程的中间部分。
3.4试验方法:
3.4.1试件按3.2规定的设备升温(或降温)到3.3.1所规定的温度。
3.4.2将达到3.3.1所规定的温度的试件赶忙按1.4和1.5实施和处理。
3.5表示方法:
3.5.1按图5所示画出试件的温度特性P—t曲线。
3.5.2按0.52m/s速度的试验结果运算热衰减率。
3.5.2.1按下式运算热衰减率
复原(压缩)热衰减率
4耐久牲试验
4.1目的:测定试件的台架耐久性。
4.2单动试验台试验法:此方法作为向本标准附录日规定的试验台过渡时使用。
4.2.1设备:单动耐久性试验台。
4.2.2条件:
4.2.2.1试件温度:试件升温后外壁上端温渡,以强制冷却方式保持在
70±10℃范畴内,并适时监测。
4.2.2.2试件上下装接位置应对中良好,并沿铅垂方向安装。
4.2.2.3位置:大致在减振器行程的中间部分。
4.2.2.4工作循环次数:1×106次。
4.2.3操作:按4.2实施;
4.2.4在试验开始与终止时按1.3记录示功图。
4.2.5记录以下各项试验结果:
4.2.5.1按照4.2.4所记录的示功图运算阻力变化率
4.2.5.2检查试件关键零件、关键部位的磨损情形。
4.2.5.3有无其它专门情形发生。
4.3双动试验台试验法:
4.3.1设备:双动耐久性试验台。
4.3.2条件:
4.3.2.1试件温度:试件升温后,外壁温度以强制冷却方式保持在70±10℃
范畴内,并适时监测。
4.3.2.2运动方式:上、下两端同时沿铅垂方向运动。
4.3.2.3 上端加振规范,S(mm)×n(C、P、m)=100×l00。
4.3.2.4下端加振规范:
a.行程:14~20mm;
b.频率:500~720C、P、m;
c.速度:按1.3.4达到0.52m/s的速度。
4.3.2.5工作循环次数:以下端循环次数计1×106次。
4.3.2.6必要时加侧向力,由制造厂与用户商定。
4.3.3操作:参照4.2.4实施。
4.3.4试验结果按4.2.5并记录上下端试验结果。
附录A
减振器示功试验台
(补充件)
A.1单动(一端固定,另一端实现近似的简谐波运动)。
A.2行程可调。
A.3有级或无级变速。
A.4 A.2、A.3能保证实施本标准1.3、2.3的试验参数,
即S×n=100(mm)×100(C、P、m)的规范示功图和速度特性试验的最高
速度不低于1.5m/s。
A.5可配备适当的电测系统和运算机系统。
附录B
试验台选用的标定方法
(补充件)
B.1采纳五等砝码或砝码标定法。
B.2采纳三等标准测力计或标准弹簧标定法。
注意事项:标定最大量应大于试件的最大阻力值,标定点在拉伸、压缩
方向各许多于5点,加载、卸载曲线的不重合度不大于最大标定量的1%记录
线条宽度不得大于0.2mm。
附加讲明:
本标准由中国汽车工业公司提出,由长春汽车研究所归口。
本标准由上海汽车底盘厂、长春汽车研究所、北京工业学院负责起草。