吸塑注塑吹塑比较
注塑材料的成形工艺

加工手段主要有:注塑,挤出,吹塑,吸塑等。
注塑可以加工生产比较复杂形状的产品,比如电视机外壳等。
它是把塑料粒子预先在料管中加热,然后通过螺杆下压,把融化的原料注入到模具,冷却成型后就制成了产品。
挤出就是原料经螺杆的连续推动,使之在料管中(俗称炮筒)加热塑化,然后在定型的模具中挤出,获得所需的形状,比如塑料扣板,水管等。
吹塑和挤出有点相似,只不过它是把压缩空气置于其中来获得形状,比如塑料薄膜,塑料瓶等。
吸塑比较简单,它先把预先制成的塑料片材,经过烘箱焙烤,然后放置在模具中,通过负压使片材与模具密贴而获得形状。
注塑成型原理及注塑过程介绍:注(射模)塑(或称注射成型)是塑料先在注塑机的加热料筒中受热熔融,而后由柱塞或往复式螺杆将熔体推挤到闭合模具的模腔中成型的一种方法。
它不仅可在高生产率下制得高精度,高质量的制品,而且可加工的塑料品种多和用途广,因此注塑是塑料加工中重要成型方法之一。
A注塑机的基本功能:注塑是通过注塑机来实现的。
注塑机的基本功能是:1。
加热塑料,使其达到熔融状态;2。
对熔体施加高压,使其射出而充满模腔。
B注塑过程/设备:热塑性塑料的注塑操作一般是由塑炼。
充模。
压实和冷却等所组成的。
所用设备是由注塑机。
注塑模具及辅助设备(如物料干燥等)组成的。
C注射装置:注射装置在注塑机过程中主要实现塑炼。
计量。
注射和保压补缩等功能。
螺杆式注射装置用得最多,它是将螺杆塑炼和注射用柱塞统一成为一根螺杆而成的。
实质上,应称为同轴往复复杆式注射装置。
它在工作时,料斗内的塑料靠自身的重量落入加热料筒内,通过螺杆的转动,塑料沿螺槽向前移动,这时物料受到加热料筒外部加热器加热,同时内部还有剪切产生的热,温度上升在成为熔融状态。
随着加热料筒前端材料的贮存,这些材料产生的反作用力(背压)将螺杆向后推,利用限位开关限制其后退量,当后退到一定位置时,使螺杆停止转动,由此决定(计量)一次的注射量。
模内的材料冷却后,制品一经取出,就再次合上模具,进入注射工序,这时注射装置的液压缸(注射油缸)向螺杆施力,在高压下螺杆成为射料杆,将其前端的熔体从喷嘴注入模具内。
吹塑、吸塑工艺介绍

吹塑吹塑blow moulding也称中空吹塑,一种发展迅速的塑料加工方法。
热塑性树脂经挤出或注射成型得到的管状塑料型坯,趁热(或加热到软化状态),置于对开模中,闭模后立即在型坯内通入压缩空气,使塑料型坯吹胀而紧贴在模具内壁上,经冷却脱模,即得到各种中空制品。
吹塑薄膜的制造工艺在原理上和中空制品吹塑十分相似,但它不使用模具,从塑料加工技术分类的角度,吹塑薄膜的成型工艺通常列入挤出中。
吹塑工艺在第二次世界大战期间,开始用于生产低密度聚乙烯小瓶。
50年代后期,随着高密度聚乙烯的诞生和吹塑成型机的发展,吹塑技术得到了广泛应用。
中空容器的体积可达数千升,有的生产已采用了计算机控制。
适用于吹塑的塑料有聚乙烯、聚氯乙烯、聚丙烯、聚酯等,所得之中空容器广泛用作工业包装容器。
根据型坯制作方法,吹塑可分为挤出吹塑和注射吹塑,新发展起来的有多层吹塑和拉伸吹塑。
塑料模具常识- 挤出吹塑挤出吹塑是一种制造中空热塑性制件的方法。
广为人制的吹塑对象有瓶、桶、罐、箱以及所有包装食品、饮料、化妆品、药品和日用品的容器。
大的吹塑容器通常用于化工产品、润滑剂和散装材料的包装上。
其他的吹塑制品还有球、波纹管和玩具。
对于汽车制造业,燃料箱、轿车减震器、座椅靠背、中心托架以及扶手和头枕覆盖层均是吹塑的。
对于机械和家具制造业,吹塑零件有外壳、门框架、制架、陶罐或到有一个开放面的箱盒。
聚合物最普通的吹塑挤塑料原料是高密度聚乙烯,大部分牛奶平时有这种聚合物制成的。
其他聚烯烃也常通过吹塑来加工。
根据用途,苯乙烯聚合物、聚氯乙烯、聚酯、聚氨酯、聚碳酸酯和其他热塑性塑料也可以用来吹塑。
最近工程塑料在汽车行业被广泛接受。
材料选择是以机械强度、耐候性、电学性能、光学性能和其他性能为依据的。
工艺3/4的吹塑制品是由挤出吹塑法制造的。
挤出工艺是强迫物料通过一个孔或模具来制造产品。
挤出吹塑工艺由5步组成:1.塑料型胚(中空塑料管的挤出);2.在型胚上将瓣合模具闭合,夹紧模具并切断型胚;3.向模腔的冷壁吹胀型培,调整开口并在冷却期间保持一定的压力,打开模具,写下被吹的零件;5.修整飞边得到成品。
塑料的常用成型方法
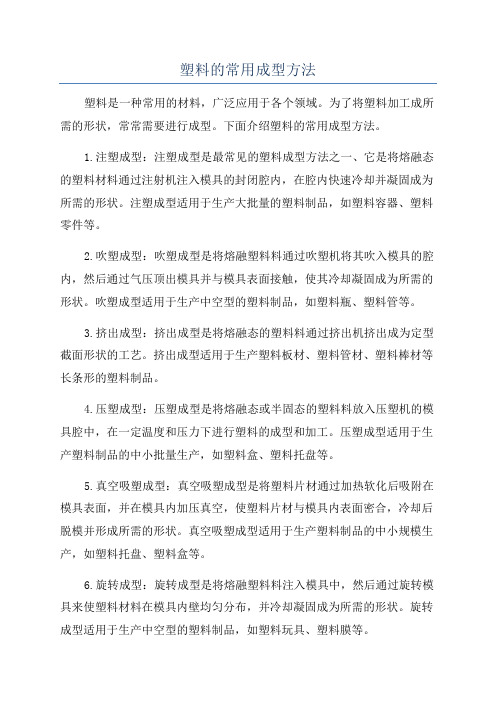
塑料的常用成型方法塑料是一种常用的材料,广泛应用于各个领域。
为了将塑料加工成所需的形状,常常需要进行成型。
下面介绍塑料的常用成型方法。
1.注塑成型:注塑成型是最常见的塑料成型方法之一、它是将熔融态的塑料材料通过注射机注入模具的封闭腔内,在腔内快速冷却并凝固成为所需的形状。
注塑成型适用于生产大批量的塑料制品,如塑料容器、塑料零件等。
2.吹塑成型:吹塑成型是将熔融塑料料通过吹塑机将其吹入模具的腔内,然后通过气压顶出模具并与模具表面接触,使其冷却凝固成为所需的形状。
吹塑成型适用于生产中空型的塑料制品,如塑料瓶、塑料管等。
3.挤出成型:挤出成型是将熔融态的塑料料通过挤出机挤出成为定型截面形状的工艺。
挤出成型适用于生产塑料板材、塑料管材、塑料棒材等长条形的塑料制品。
4.压塑成型:压塑成型是将熔融态或半固态的塑料料放入压塑机的模具腔中,在一定温度和压力下进行塑料的成型和加工。
压塑成型适用于生产塑料制品的中小批量生产,如塑料盒、塑料托盘等。
5.真空吸塑成型:真空吸塑成型是将塑料片材通过加热软化后吸附在模具表面,并在模具内加压真空,使塑料片材与模具内表面密合,冷却后脱模并形成所需的形状。
真空吸塑成型适用于生产塑料制品的中小规模生产,如塑料托盘、塑料盒等。
6.旋转成型:旋转成型是将熔融塑料料注入模具中,然后通过旋转模具来使塑料材料在模具内壁均匀分布,并冷却凝固成为所需的形状。
旋转成型适用于生产中空型的塑料制品,如塑料玩具、塑料膜等。
7.发泡成型:发泡成型是将塑料和发泡剂混合后在一定的压力和温度下进行加工,使混合物膨胀并形成多孔性物体。
发泡成型适用于生产轻质、保温性能较好的塑料制品,如塑料发泡板、塑料发泡箱等。
上述是常见的塑料成型方法,不同的成型方法适用于不同的塑料制品需求。
在实际生产中,需要根据产品的特性、成本、生产效率等因素来选择合适的成型方法。
不同的成型方法也可以结合使用,以满足特殊的要求。
注塑托盘和吹塑托盘异同对比

注塑和吹塑托盘异同对比表一、吹塑托盘的特点:1、我们看到的特点汇总(自己总结):第一:外观方面A、制造工艺所限,都必须是双面托盘;B、制造工艺所限,都是双向进叉;C、中间支撑都是孔径不大的柱状结构,内部及表面清洗不方便;D、承重是通过连续折叠面实现的,而非筋位,限制了表面承重,上架承载力小;第二:制造方面A、需要二次加热成型;B、用料要求高——制品成型时采用多种高强度的HMWHDPE塑料混炼的材料成型;C、因吹塑过程中空气压力是同压力辐射状,所以无法完全控制边角部位加强。
第三:运输方面:A、双面托盘运输费用高,空盘储存占用空间大;B、上架承重力小,无法内置钢管加强。
2、吹塑托盘厂看到的优点(来源于网络):A、塑料吹塑托盘采用高强度高分子量聚乙烯(HMWHDPE)制造,该塑料粘性好、韧性好、耐老化、耐腐蚀、无污染,是最佳的环保产品。
(批注:HMWHDPE 分子量长,价格高)B、安全性能好,产品表面采用特殊防滑花纹设计,安全防滑,并可设置专用的橡胶滑垫,确保托盘堆码中的稳定。
不助燃、不导电、不产生静电、防滑、无毛刺飞边、无其他辅助连接,可确保货物和作业者的安全。
(批注:和普通PE表面无明显区别,化学性能也一样。
)C、环保性能好,制品无毒无味,耐酸碱盐的腐蚀,易于清洗消毒,不腐烂,同时废旧托盘可回收利用,符合环保要求。
外观色彩亮丽,可根据客户的要求选择。
(批注:化学性能与普通PE无异)D、承载能力强。
由于高强度吹塑托盘按受力情况合理地进行了结构设计,并且通过计算机工程分析模拟实际运行状况,使产品承载能力强,均匀分布的承载能力为:静载荷5~6t,动载荷1~2t,架空载荷为0.7~1t。
(批注:表面厚度较薄,无法承受较高压力。
)E、使用寿命长。
制品成型时采用多种高强度的HMWHDPE塑料混炼的材料成型,强度高,抗冲击能力强,并通过多种材料配方确保提高户外使用寿命,一般条件下可用5年以上;恶劣环境下可用2~3年。
塑料加工技术注塑挤出和吹塑
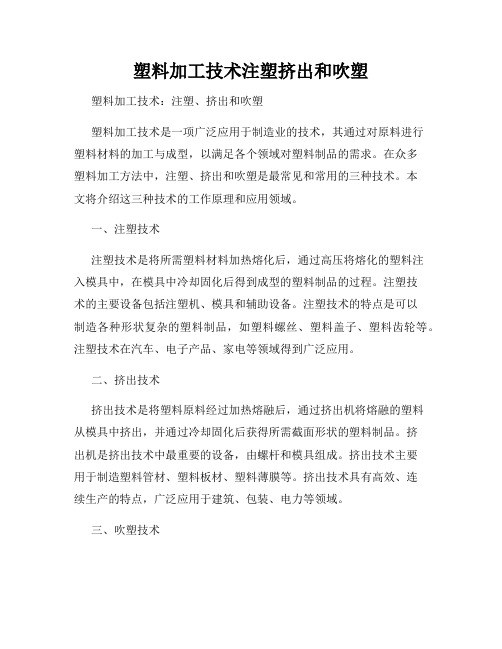
塑料加工技术注塑挤出和吹塑塑料加工技术:注塑、挤出和吹塑塑料加工技术是一项广泛应用于制造业的技术,其通过对原料进行塑料材料的加工与成型,以满足各个领域对塑料制品的需求。
在众多塑料加工方法中,注塑、挤出和吹塑是最常见和常用的三种技术。
本文将介绍这三种技术的工作原理和应用领域。
一、注塑技术注塑技术是将所需塑料材料加热熔化后,通过高压将熔化的塑料注入模具中,在模具中冷却固化后得到成型的塑料制品的过程。
注塑技术的主要设备包括注塑机、模具和辅助设备。
注塑技术的特点是可以制造各种形状复杂的塑料制品,如塑料螺丝、塑料盖子、塑料齿轮等。
注塑技术在汽车、电子产品、家电等领域得到广泛应用。
二、挤出技术挤出技术是将塑料原料经过加热熔融后,通过挤出机将熔融的塑料从模具中挤出,并通过冷却固化后获得所需截面形状的塑料制品。
挤出机是挤出技术中最重要的设备,由螺杆和模具组成。
挤出技术主要用于制造塑料管材、塑料板材、塑料薄膜等。
挤出技术具有高效、连续生产的特点,广泛应用于建筑、包装、电力等领域。
三、吹塑技术吹塑技术是将热塑性塑料预制成中空管状的“坯料”,再将其放入吹塑机的模具内,通过吹气或真空力使其沿模具内表面膨胀,从而获得所需的中空形状的塑料制品。
吹塑技术的主要设备是吹塑机和模具。
吹塑技术通常用于制造塑料瓶、塑料容器、塑料玩具等。
吹塑技术具有成本低、生产效率高、产品质量好的特点,被广泛应用于食品包装、日用品制造等领域。
总结起来,注塑、挤出和吹塑是塑料加工技术中最常见的三种方法。
它们各自具有独特的工作原理和应用领域,为满足不同行业对塑料制品的需求提供了可靠的解决方案。
随着技术不断进步和创新,塑料加工技术将在未来的发展中迎来更加广阔的应用前景。
吸塑工艺和注塑工艺的区别和联系

吸塑工艺和注塑工艺的区别和联系
在现代工业生产中,吸塑工艺和注塑工艺是两种常见的成型工艺,它们在塑料制品加工领域具有重要的应用价值。
尽管二者都是塑料加工技术,但在具体的工艺流程、原理和应用领域上存在一定的区别和联系。
首先,吸塑工艺是一种通过加热和吸力来成型塑料制品的方法。
在吸塑工艺中,先将塑料片材加热软化,然后利用模具或模具系统施加负压,使塑料片材吸附在模具表面,最终冷却固化成型。
而注塑工艺则是在加热熔化的塑料料通过高压射出系统进入模具腔内,在一定压力和温度下冷却凝固成型。
可以看出,吸塑工艺是在模具内部形成真空力来成型,而注塑工艺是通过高压射出来实现成型。
其次,吸塑工艺和注塑工艺在应用领域上也存在一定的区别。
吸塑工艺适用于生产单层或多层塑料膜、薄膜包装、塑料盒、托盘等产品。
而注塑工艺由于其适用性广泛,可以生产各种塑料制品,如零部件、玩具、日用品、汽车零件等。
因此,根据产品的具体要求和形状复杂程度,选择吸塑工艺或注塑工艺有其对应的优势和适用范围。
此外,吸塑工艺和注塑工艺之间也存在一定的联系和互补性。
在一些特定的产品生产过程中,可以采用吸塑和注塑相结合的方式,充分发挥两者的优势。
例如,在生产汽车零部件时,可以先通过注塑工艺生产塑料外壳,再通过吸塑工艺加工成特定形状,既提高了生产效率,又保证了产品的质量和外观。
综上所述,吸塑工艺和注塑工艺在塑料制品加工领域各具特点,区别和联系并存。
在实际生产应用中,根据产品的要求和生产规模选择合适的工艺技术至关重要,同时也可以结合吸塑和注塑等多种工艺手段,以满足不同产品的加工需求,推动塑料制品生产技术的不断创新和发展。
1。
滚塑、吹塑、注塑工艺的区别

滚塑、吹塑、注塑工艺的区别
滚塑成型工艺与传统的吹塑、注塑工艺相比有以下优势:
1、成本优势:滚塑成型工艺中只要求机架的强度足以支承物料、模具及机架自身的重量,以防止物料泄漏的闭模力;并且物料在整个成型过程中,除自然重力的作用外,几乎不受任何外力的作用,从而完全具备了机模加工制造的方便,周期短,成本低的优势。
2、质量优势。
滚塑工艺的产品在整个制作过程中,由于无内应力产生,产品质量和结构更加稳定。
3、灵活多变优势。
滚塑工艺的机模制造方便,价格低廉,故特别适用于新产品开发中的多品种、小批量的生产。
4、个性化设计优势。
滚塑成型工艺中的产品极易变换颜色,并可以做到中空(无缝无焊),在产品表面处理上可以做到花纹、木质、石质及金属的效果,满足现代社会消费者对商品的个性化需求。
采用该工艺生产的产品有:油箱、水箱、机械外壳、挡泥板等。
主要替代对象是金属件及玻璃钢制品。
注塑是一种工艺,是基于比如LIGA的微制造技术开发出来的,当然还有很多其他方法。
而LIGA工艺就是先生产出一个注塑所需要的模型,也就是俗称的"模子",然后将液态塑料灌注在模具中,最后在分离出来,形成最终所需要的产品。
比如一些塑料玩具,产品太多了
滚塑箱是滚塑工艺成型的箱子,它是塑料分子通过喷涂、缠绕的方式在高温下自动融合成型的,分子与分子之间没有任何应力。
注塑箱是浇注的,是挤压成型的,分子与分子间有应力。
滚塑箱相对与注塑箱,抗冲击力更强,更不易变形,更加坚固耐用,有优异的耐腐蚀性能。
滚塑箱适用于应急救援领域,野战领域,化工领域,生活及各种生产领域。
吸塑吸塑加工之吹塑、注塑、吸塑的区别

吸塑吸塑加工之吹塑、注塑、吸塑的区别在日常生活和工业生产中,我们经常听到吹塑、注塑、吸塑这些加工方式。
这些加工方式都属于热加工和塑料成型技术,它们各自有自己的优点和适用范围。
本文主要介绍吹塑、注塑和吸塑三种加工方式的区别。
吹塑吹塑是一种常用于制造塑料容器和瓶子的加工方式。
在吹塑过程中,先准备好预制的管状物,然后在管状物的一端加热软化,接着通过风压将塑料吹成成型的容器。
吹塑适用于制造中小型的塑料容器,如瓶子、桶等。
吹塑的优点在于成本低、生产率高、生产效率高、物料容易处理等。
而缺点是成型尺寸、形状有限,无法制造较复杂的产品。
注塑注塑是一种将加热的塑料材料注入模具,再冷却硬化成为成型产品的加工方法。
注塑过程中,首先将加热的塑料注入到模具中,然后经过短暂的冷却和硬化,即可以获得成型的产品。
注塑适用于生产各种尺寸、形状各异的产品,如手机外壳、汽车零部件、电器外壳等。
注塑的优点在于适用性广泛,可以制造非常复杂的产品,精度高,制品质量好,但缺点在于生产周期长,成本较高。
吸塑吸塑是通过真空把片状塑料材料贴附在塑料模具上,并使其与模具表面紧密贴合,待塑料材料冷却硬化后与模具一起成型的加工方法。
吸塑适用于生产各种中小型的塑料产品,如玩具、名片盒等。
吸塑的优点在于成本较低,手工操作容易,生产效率较高,并且可以生产中小型的塑料制品。
但缺点是成型尺寸、形状受限,无法制造较复杂的产品。
三种加工方法的比较下表列出了三种加工方法在成型效率、成本和适用范围等方面的比较。
吹塑注塑吸塑成型效率高低中等成本低高中等适用范围小型容器复杂零部件中小型产品结论以上是三种热加工技术的区别和优缺点,选择何种加工方式取决于所需要生产的产品,成本,生产周期和适用范围等因素。
注塑适用于生产各种尺寸、形状各异的产品。
吹塑适用于生产中小型的塑料容器,如瓶子、桶等。
吸塑适用于生产中小型的塑料制品,如玩具、名片盒等。
综上所述,吹塑、注塑和吸塑的加工方法都有各自的优劣,生产企业应根据实际需求和预算选择相应的加工方法,以获得最佳效益。
- 1、下载文档前请自行甄别文档内容的完整性,平台不提供额外的编辑、内容补充、找答案等附加服务。
- 2、"仅部分预览"的文档,不可在线预览部分如存在完整性等问题,可反馈申请退款(可完整预览的文档不适用该条件!)。
- 3、如文档侵犯您的权益,请联系客服反馈,我们会尽快为您处理(人工客服工作时间:9:00-18:30)。
吸塑:
一种塑料加工工艺,主要原理是将平展的塑料硬片材加热变软后,采用真空吸附于模具表面,冷却后成型,广泛用于塑料包装、灯饰、广告、装饰等行业。
吸塑包装:采用吸塑工艺生产出塑料制品,并用相应的设备对产品进行封装的总称。
吸塑包装制品包括:泡壳、托盘、吸塑盒,同义词还有:真空罩、泡罩等。
吸塑包装的主要优点是,节省原辅材料、重量轻、运输方便、密封性能好,符合环保绿色包装的要求;能包装任何异形产品,装箱无需另加缓冲材料;被包装产品透明可见,外形美观,便于销售,并适合机械化、自动化包装,便于现代化管理、节省人力、提高效率
吸塑包装设备主要包括:吸塑成型机、冲床、封口机、高频机、折边机。
封装形成的包装产品可分为:插卡、吸卡、双泡壳、半泡壳、对折泡壳、三折泡壳等
注塑,即热塑性塑料注塑成型,这种方法即是将塑料材料熔融,然后将其注入膜腔。
熔融的塑料一旦进入模具中,它就受冷依模腔样成型成一定形状。
所得的形状往往就是最后成品,在安装或作为最终成品使用之前不再需要其他的加工。
许多细部,诸如凸起部、肋、螺纹,都可以在注射模塑一步操作中成型出来。
注射模塑机有两个基本部件:用于熔融和把塑料送入模具的注射装置与合模装置。
和模装置的作用在于:1.使模具在承受住注射压力情况下闭合;2.将制品取出注射装置在塑料注入模具之前将其熔融,然后控制压力和速度将熔体注入模具。
目前采用的注射装置有两种设计:螺杆式预塑化器或双级装置,以及往复式螺杆。
螺杆式预塑化器利用预塑化螺杆(第一级)再将熔融塑料注入注料杆(第二级)。
螺杆预塑化器的优点是熔融物质量恒定,高压和高速,以及精确的注射量控制(利用活塞冲程两端的机械止推装置)。
这些长处是透明、薄壁制品和高生产速率所需要的。
其缺点包括不均匀的停留时间(导致材料降解)、较高的设备费用和维修费用。
最常用的往复式螺杆注射装置不需要柱塞即将塑料熔融并注射。
吹塑:
也称中空吹塑,一种发展迅速的塑料加工方法。
热塑性树脂经挤出或注射成型得到的管状塑料型坯,趁热(或加热到软化状态),置于对开模中,闭模后立即在型坯内通入压缩空气,使塑料型坯吹胀而紧贴在模具内壁上,经冷却脱模,即得到各种中空制品。
吹塑薄膜的制造工艺在原理上和中空制品吹塑十分相似,但它不使用模具,从塑料加工技术分类的角度,吹塑薄膜的成型工艺通常列入挤出中。
吹塑工艺在第二次世界大战期间,开始用于生产低密度聚乙烯小瓶。
50年代后期,随着高密度聚乙烯的诞生和吹塑成型机的发展,吹塑技术得到了广泛应用。
中空容器的体积可达数千升,有的生产已采用了计算机控制。
适用于吹塑的塑料有聚乙烯、聚氯乙烯、聚丙烯、聚酯等,所得之中空容器广泛用作工业包装容器。
根据型坯制作方法,吹塑可分为挤出吹塑和注射吹塑,新发展起来的有多层吹塑和拉伸吹塑。
吸塑工艺流程
• 备料——按施工单上的要求,选择相应的片材,模具。
1) 领取相关模具并清洁润滑
2) 领取相关片材、预检材质、外形尺寸、厚度、重量(数量)
• 模具安装——安装相关模具,吸塑机预加热,同时检查真空泵吸力。
预加热到规定温度后,调试至产品符合施工单要求。
• 吸塑成型生产——将片材安装进吸塑机送料机构,进行正常生产(软化、吸塑、成型),其中加热软化真空吸塑成型3 秒钟,冷却断料12 秒钟,将半成品堆放到指定位置。
按施工单进行半成品质量检验。
• 半成品冲切——安装相应冲切模具并进行调试,合格后半成品进行冲切,边废料放至指定筐内,成品堆放时必须保证产品的清洁无损,按施工单进行成品质量检验。
• 吸塑成品包装——采用纸箱包装,内衬防潮防尘箱袋,按施工单规定每箱数量将合格品装箱。
吸塑的质量要求:试装产品要适合,扣位能扣紧产品,厚度要均衡,表面要光洁通透.
注塑的质量要求:颜色尺寸结构外观字唛要符合完整一致,保持干净,包装防护完好.
吹塑的质量要求:厚度要均衡,重量要统一,颜色要一致,表面要光洁,完整符合.
吸塑:
一种塑料加工工艺,主要原理是将平展的塑料硬片材加热变软后,采用真空吸附于模具表面,冷却后成型,广泛用于塑料包装、灯饰、广告、装饰等行业。
吸塑包装:采用吸塑工艺生产出塑料制品,并用相应的设备对产品进行封装的总称。
吸塑包装制品包括:泡壳、托盘、吸塑盒,同义词还有:真空罩、泡罩等。
吸塑包装的主要优点是,节省原辅材料、重量轻、运输方便、密封性能好,符合环保绿色包装的要求;能包装任何异形产品,装箱无需另加缓冲材料;被包装产品透明可见,外形美观,便于销售,并适合机械化、自动化包装,便于现代化管理、节省人力、提高效率
吸塑包装设备主要包括:吸塑成型机、冲床、封口机、高频机、折边机。
封装形成的包装产品可分为:插卡、吸卡、双泡壳、半泡壳、对折泡壳、三折泡壳等
注塑,即热塑性塑料注塑成型,这种方法即是将塑料材料熔融,然后将其注入膜腔。
熔融的塑料一旦进入模具中,它就受冷依模腔样成型成一定形状。
所得的形状往往就是最后成品,在安装或作为最终成品使用之前不再需要其他的加工。
许多细部,诸如凸起部、肋、螺纹,都可以在注射模塑一步操作中成型出来。
注射模塑机有两个基本部件:用于熔融和把塑料送入模具的注射装置与合模装置。
和模装置的作用在于:1.使模具在承受住注射压力情况下闭合;2.将制品取出注射装置在塑料注入模具之前将其熔融,然后控制压力和速度将熔体注入模具。
目前采用的注射装置有两种设计:螺杆式预塑化器或双级装置,以及往复式螺杆。
螺杆式预塑化器利用预塑化螺杆(第一级)再将熔融塑料注入注料杆(第二级)。
螺杆预塑化器的优点是熔融物质量恒定,高压和高速,以及精确的注射量控制(利用活塞冲程两端的机械止推装置)。
这些长处是透明、薄壁制品和高生产速率所需要的。
其缺点包括不均匀的停留时间(导致材料降解)、较高的设备费用和维修费用。
最常用的往复式螺杆注射装置不需要柱塞即将塑料熔融并注射。
吹塑:
也称中空吹塑,一种发展迅速的塑料加工方法。
热塑性树脂经挤出或注射成型得到的管状塑料型坯,趁热(或加热到软化状态),置于对开模中,闭模后立即在型坯内通入压缩空气,使塑料型坯吹胀而紧贴在模具内壁上,经冷却脱模,即得到各种中空制品。
吹塑薄膜的制造工艺在原理上和中空制品吹塑十分相似,但它不使用模具,从塑料加工技术分类的角度,吹塑薄膜的成型工艺通常列入挤出中。
吹塑工艺在第二次世界大战期间,开始用于生产低密度聚乙烯小瓶。
50年代后期,随着高密度聚乙烯的诞生和吹塑成型机的发展,吹塑技术得到了广泛应用。
中空容器的体积可达数千升,有的生产已采用了计算机控制。
适用于吹塑的塑料有聚乙烯、聚氯乙烯、聚丙烯、聚酯等,所得之中空容器广泛用作工业包装容器。
根据型坯制作方法,吹塑可分为挤出吹塑和注射吹塑,新发展起来的有多层吹塑和拉伸吹塑了。