球墨铸铁(精)
等温淬火球墨铸铁在高端齿轮上的应用

等温淬火球墨铸铁在高端齿轮上的应用1. 引言1.1 介绍等温淬火球墨铸铁及其特点等温淬火球墨铸铁是一种具有优异性能的铸铁材料,它具有高强度、高韧性和良好的耐磨性等特点。
等温淬火球墨铸铁的制造工艺相对比较复杂,需要经过多道热处理工艺,包括球化退火和等温淬火处理。
这种铸铁材料在高温高压下形成的高强度铸铁基体中分布着球状石墨颗粒,这些球状石墨颗粒可以有效地阻止裂纹的扩展,提高了材料的韧性和抗拉伸强度。
等温淬火球墨铸铁被广泛应用于汽车发动机、船舶、机床和其他需要高强度和高耐磨性的领域。
在高端齿轮制造领域,等温淬火球墨铸铁的应用也越来越广泛,其优异的性能使得其成为高端齿轮制造的理想材料之一。
1.2 高端齿轮的重要性高端齿轮作为机械传动装置中的核心部件,承担着转速传递、扭矩传递和运动方向变换等重要功能。
它连接着机械设备的各个部分,是整个机械系统运转的关键。
高端齿轮的品质直接影响着机械设备的性能和使用寿命,因此在许多关键领域中,对齿轮的要求十分严格。
在航空航天、船舶、高速列车等领域中,高端齿轮承载着高速、大功率的传动任务,要求齿轮具有高强度、高硬度和高耐磨性。
其可靠性和稳定性直接关系着整个系统的安全性和可靠性。
在工程机械、汽车、军工等领域中,高端齿轮则需要具备良好的耐冲击性、耐疲劳性和低噪音等特点。
这些领域的机械设备对齿轮的精密度和可靠性要求非常高,因为任何一处故障都可能导致设备的损坏或者事故的发生。
高端齿轮在各个领域中都扮演着不可替代的重要角色,其质量和性能直接关系着整个机械系统的稳定运作。
采用高品质的材料制造高端齿轮,如等温淬火球墨铸铁,对于提升机械设备的性能和可靠性具有重要意义。
2. 正文2.1 等温淬火球墨铸铁在高端齿轮制造中的具体应用等温淬火球墨铸铁在高端齿轮制造中的具体应用非常广泛。
它可以用于制造各种类型的齿轮,包括直齿轮、斜齿轮、蜗杆等。
由于等温淬火球墨铸铁具有高强度、高韧性和优良的耐磨性,所以在高端齿轮中得到广泛应用。
球墨铸铁金相试样制备中的常见缺陷及其原因分析
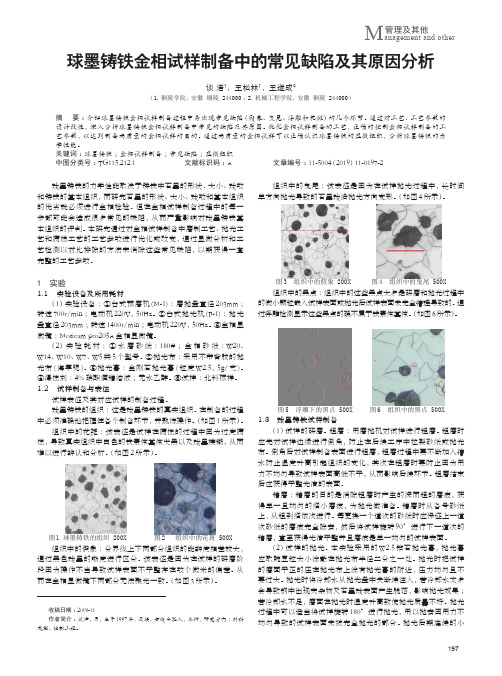
球墨铸铁金相试样制备中的常见缺陷及其原因分析
谈 浩¹,王松林¹,王继成²
(1. 铜陵学院,安徽 铜陵 244000 ;2. 机械工程学院,安徽 铜陵 244000)
摘 要 :介绍球墨铸铁金相试样制备过程中易出现常见缺陷(假象、曳尾、浮雕和花斑)的几个环节。通过对工艺、工艺参数的
收稿日期 :2019-11 作者简介 :谈浩,男,生于 19ห้องสมุดไป่ตู้7 年,汉族,安徽合肥人,本科,研究方向 :材料 成型、控制工程。
组织中的曳尾 :该表征是因为在试样抛光过程中,长时间 单方向抛光导致的石墨球沿抛光方向变形。(如图 4 所示)。
图 3 组织中的假象 200X 图 4 组织中的曳尾 500X 组织中的黑点 :组织中的这些黑点大多是研磨和抛光过程中 的微小颗粒嵌入试样表面或抛光后试样表面未完全清理导致的。通 过浮雕检测显示这些黑点的确不属于铁素体基体。(如图 6 所示)。
2 结果及讨论 2.1 球墨铸铁试样制备中常见的缺陷及应对措施
文献标识码 :A
文章编号 :11-5004(2019)11-0197-2
球墨铸铁的力学性能取决于铸铁中石墨的形状、大小、球数 和铸铁的基本组织,而研究石墨的形状、大小、球数和基本组织 的优劣就必须进行金相检验。但在金相试样制备过程中的每一 步都可能会造成很多常见的缺陷,从而严重影响对球墨铸铁基 本组织的评判。本研究通过对金相试样制备中磨制工艺、抛光工 艺和腐蚀工艺的工艺参数进行优化或改变,通过显微分析和工 艺检测以对比排除的方法来消除这些常见缺陷,以期获得一套 完整的工艺参数。
试样表征及其对应试样的制备过程。 球墨铸铁的组织 :这是球墨铸铁的真实组织。在制备的过程 中必须准确地把握住各个制备环节,并熟练操作。(如图 1 所示)。 组织中的花斑 :该表征是试样在腐蚀的过程中因为过度腐 蚀,导致真实组织中白色的铁素体基体发黑以及球墨模糊,从而 难以进行辨认和分析。(如图 2 所示)。
球墨铸铁正火工艺规范(精)

球墨铸铁正火工艺规范
规范金相组织备注
织均匀性,改善可加工性,提高强度、硬度、耐磨性或口及游离渗碳体珠光体+少量铁素体(牛眼状)
复杂铸件
珠光体+少量铁素体(牛眼状)复杂铸件正火后需要回火
高的综合力学性能,特别是塑性和韧性珠光体+(碎块状或条块状)铁素体+球状石墨
复杂铸件
珠光体+(碎块状或条块状)铁
素体+球状石墨
复杂铸件正火后需要回火
珠光体+(碎块状或条块状)铁素体+球状石墨
铸态如存过量自由渗碳体时,在正火前需经高温石墨化退火 复杂铸件正火后需要回火。
球墨铸铁给水管施工方法胶圈接口精品
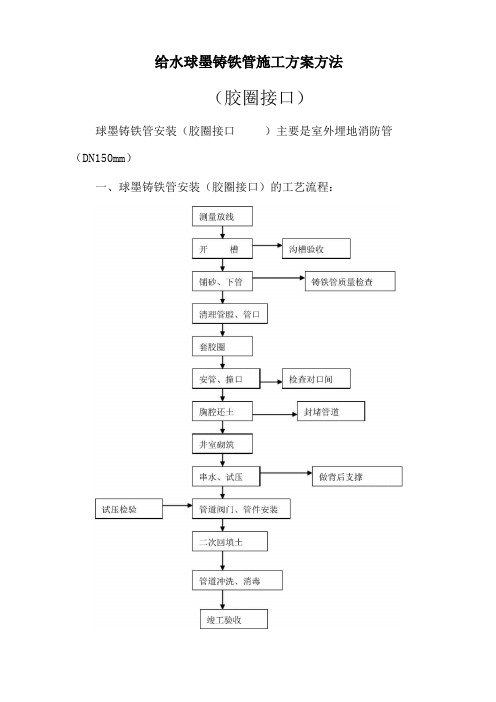
给水球墨铸铁管施工方案方法(胶圈接口)球墨铸铁管安装(胶圈接口)主要是室外埋地消防管(DN150mm)一、球墨铸铁管安装(胶圈接口)的工艺流程:二、沟槽开挖1、沟槽开挖前工作开槽前要认真调查了解地上地下障碍物,以便开槽时采取妥善加固保护措施,根据业主方提供的现况地下管线图和我公司的现场调查,统计出现况地下情况,采取有效措施加以保护。
2、沟槽开挖形式根据设计图中设计管道的规格及埋置深度以及规范要求来确定沟槽开挖的形式。
⑴槽帮坡度的确定:槽深h<3.0米时,槽帮坡度i为1:0.33;⑵管道一侧工作面宽度情况详见下表:⑶沟槽断面形式(见下图)3、开挖方法⑴土方开挖采用机械开挖,槽底预留205由人工清底。
开挖过程中严禁超挖,以防扰动地基,对有地下障碍物(现况管线)的地段由人工开挖,严禁破坏。
⑵沟槽开挖按先深后浅顺序进行,以利排水。
⑶挖槽土方处置,按现场暂存、场外暂存和外弃相结合的原则。
开槽土方凡适宜回填的士选择妥善位置进行堆放,但不得覆盖测量等标注,均暂存于现场用于沟槽回填,回填土施工前合理的土方调配计划。
作好土方平衡,减少土方外运及现场土方调运。
⑷开槽后及时约请有关人员检槽,槽底合格后方可进行下道工序,如遇槽底土基不符设计要求,及时与设计监理单位及地勘部门联系,共同研究基底处理措施,方可进行下道工序。
二、下管在沟槽检底后,经核对管节、管件位置无误后立即下管。
下管时注意承口方向保持与管道安装方向一致。
同时在各接口处掏挖工作坑,工作坑大小以方便管道撞口安装为宜。
三、清理承口清刷承口,铲去所有粘结物,如沙子、泥土和松散土涂层及可能污染水质、划破胶圈的附着物。
四、清理胶圈、上胶圈将胶圈清理干净。
上胶圈时,使胶圈弯成心形或花形放在承口内槽就位,并用手压实,确保各个部位不翘不扭。
胶圈存放注意避沈,不要叠合挤压,长期贮存在盒子里面或用其他东西罩上。
五、清理播口表面插口端是圆角并有一定锥度。
在胶圈内表面和插口外表涂刷润滑剂(洗涤灵),润滑剂均匀刷在承口内已安装好的橡胶圈表面,在插口外表刷润滑剂刷到插口坡口处。
球墨铸铁退火工艺规范(精)

球墨铸铁退火工艺规范
热处理类型热处理目的热处理规范金相组织
备注
去应力低温退火消除或降低
残留应力,
并使其稳定
化
同铸铁原始
组织
球铁根据对工件的组织和性能的要
求,一般均经其它较复杂的热处理,
故不一定要进行此项去应力退火
高温石墨化退火消除自由渗
碳体并降低
硬度,改善
可加工性,
提高塑性和
韧性
1、2-铁素体
+石墨或铁
素体+珠光
体+石墨
3-珠光体+
石墨
1、2-铁素体基体规范3-珠光体基体
规范
低温石墨化退火使共析渗铁
体石墨化与
粒化,从而
降低硬度,
改善可加工
性并提高塑
性和韧性
1-铁素体+
珠光体+石
墨2、3-
铁素体+石
墨
1-铁素体-珠光体基体规范2、3-铁素
体基体规范。
球墨铸铁淬火工艺规范(精)

球墨铸铁淬火工艺规范
热处理规范金相组织备注
回火索氏体+少量铁素体及球状石墨淬火
以前最好先经正火当铸件中存在过量
自由渗碳体时,在淬火前必须进行高温
石墨化退火,以免析出二次网状渗碳
体,这种方式叫“二阶段淬火”。
考虑
到回火脆性,应尽量避免250~300℃范围
内淬火
石墨
石墨
表面层为细针状马氏体+少量残留奥氏体及球状石墨,过渡层为小岛状马氏体+细小铁素体,内部与原始组织相同对铁素体基体的球铁,必须先进行正火,使珠光体量≥70%,有时为了消除淬火应力而在380~410℃温度范围内回火处理
提高强度、硬度和耐磨性,减少淬火变形及裂纹。
它是发挥球铁材料最大潜力的热处理方法下贝氏体+少量马氏体+少量残留奥氏体+
球状石墨
铸态组织需无游离渗碳
石墨化退火。
等温淬火
获得良好的强度和韧性下贝氏体+碎片状铁素体铸态组织需无游离渗碳石墨化退火。
等温淬火。
JBT5439-1991球墨铸铁零件的超声波探伤(精)

4
20%
30%
质量等级 1 2 3 4
表4
缺陷长度 缺陷轴向长度小于或等于缺陷所在截面积 5%的正平方根 缺陷轴向长度小于或等于缺陷所在截面积 10%的正平方根 缺陷轴向长度小于或等于截面积 20%的正平方根 缺陷轴向长度大于或等于截面积 20%的正平方根
10 探伤报告
探伤报告应包括以下内容: a. 委托探伤的单位,探伤报告编号,签发日期; b. 工件的名称、编号、材料牌号、热处理状态、探伤面的表面粗糙度、透声性、工件尺寸草图; c. 超探仪的型号、探头型号、探伤频率、耦合剂、探伤灵敏度; d. 在草图上,标明检测区域。如有因几何形状限制而检测不到的部位也必须在草图上标明; e. 缺陷的类型,尺寸和位置; f. 缺陷等级和探伤结论; g. 探伤人员和审核人员签字。探伤人员的资格证号、等级、姓名和探伤日期。
a 连杆 3ຫໍສະໝຸດ JB/T 5439-1991
b 曲轴
c 高压气缸体和高压气缸头
d 十字头
图4
4
JB/T 5439-1991
7. 2 扫查 7. 2. 1 应对工件整个探测面进行全面连续扫查。相邻两次扫查其相互重叠部分约为探头晶片直径的 15%。 7. 2. 2 扫查时,探头移动速度不得大于 150 mm/s。 7. 2. 3 因工件几何形状限制而扫查不到的区域,应在探伤报告中予以注明。 7. 3 工件透声性的测定
仪器系统的灵敏度余量和分辨力应按照 ZB J04 001 的有关规定进行测试。 5. 3. 1 在工作频率下,纵波直探头的灵敏度余量不得低于 30 dB,横波斜探头的灵敏度余量按附录 A (补充件)A1.2 条的规定。
机械电子工业部 1991-07-22 批准
1992-07-01 实施
球墨铸铁缩孔(精)
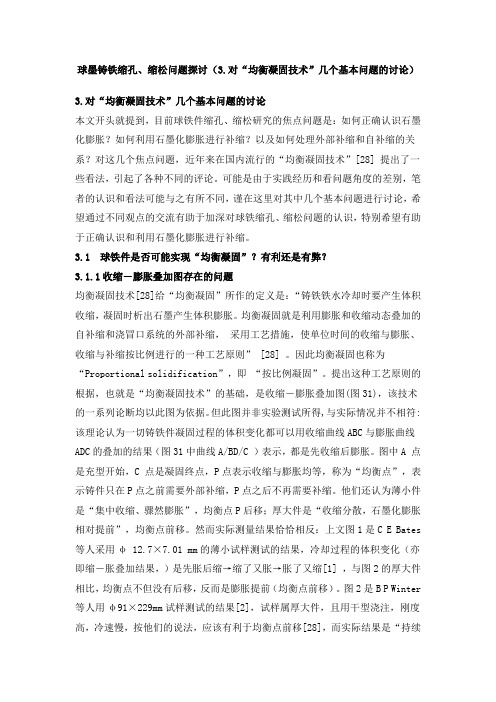
球墨铸铁缩孔、缩松问题探讨(3.对“均衡凝固技术”几个基本问题的讨论)3.对“均衡凝固技术”几个基本问题的讨论本文开头就提到,目前球铁件缩孔、缩松研究的焦点问题是:如何正确认识石墨化膨胀?如何利用石墨化膨胀进行补缩?以及如何处理外部补缩和自补缩的关系?对这几个焦点问题,近年来在国内流行的“均衡凝固技术”[28] 提出了一些看法,引起了各种不同的评论。
可能是由于实践经历和看问题角度的差别,笔者的认识和看法可能与之有所不同,谨在这里对其中几个基本问题进行讨论,希望通过不同观点的交流有助于加深对球铁缩孔、缩松问题的认识,特别希望有助于正确认识和利用石墨化膨胀进行补缩。
3.1 球铁件是否可能实现“均衡凝固”?有利还是有弊?3.1.1收缩-膨胀叠加图存在的问题均衡凝固技术[28]给“均衡凝固”所作的定义是:“铸铁铁水冷却时要产生体积收缩,凝固时析出石墨产生体积膨胀。
均衡凝固就是利用膨胀和收缩动态叠加的自补缩和浇冒口系统的外部补缩,采用工艺措施,使单位时间的收缩与膨胀、收缩与补缩按比例进行的一种工艺原则” [28] 。
因此均衡凝固也称为“Proportional solidification”,即“按比例凝固”。
提出这种工艺原则的根据,也就是“均衡凝固技术”的基础,是收缩-膨胀叠加图(图31),该技术的一系列论断均以此图为依据。
但此图并非实验测试所得,与实际情况并不相符: 该理论认为一切铸铁件凝固过程的体积变化都可以用收缩曲线ABC与膨胀曲线ADC的叠加的结果(图31中曲线A/BD/C )表示,都是先收缩后膨胀。
图中A 点是充型开始,C 点是凝固终点,P点表示收缩与膨胀均等,称为“均衡点”,表示铸件只在P点之前需要外部补缩,P点之后不再需要补缩。
他们还认为薄小件是“集中收缩、骤然膨胀”,均衡点P后移;厚大件是“收缩分散,石墨化膨胀相对提前”,均衡点前移。
然而实际测量结果恰恰相反:上文图1是C E Bates 等人采用φ 12.7×7.01 mm的薄小试样测试的结果,冷却过程的体积变化(亦即缩-胀叠加结果,)是先胀后缩→缩了又胀→胀了又缩[1] ,与图2的厚大件相比,均衡点不但没有后移,反而是膨胀提前(均衡点前移)。
- 1、下载文档前请自行甄别文档内容的完整性,平台不提供额外的编辑、内容补充、找答案等附加服务。
- 2、"仅部分预览"的文档,不可在线预览部分如存在完整性等问题,可反馈申请退款(可完整预览的文档不适用该条件!)。
- 3、如文档侵犯您的权益,请联系客服反馈,我们会尽快为您处理(人工客服工作时间:9:00-18:30)。
球墨铸铁
在河南巩县铁生沟西汉中、晚期的冶铁遗址中出土的铁 ,经过金相检验,具有放射状的球状石墨,球化率相当于现代标准一级水平。
而现代的球墨铸铁则是迟至1947年才在国外研制成功的。
我国古代的铸铁,在一个相当长的时期里含硅量都偏低,也就是说,在约2000年前的西汉时期,我国铁器中的球状石墨,就已由低硅的生铁铸件经柔化退火的方法得到。
这是我国古代铸铁技术的重大成就,也是世界冶金史上的奇迹。
球墨铸铁以其优良的性能,在使用中有时可以代替昂贵的铸钢和锻钢,在机械制造工业中得到广泛应用。
国际冶金行业过去一直认为球墨铸铁是英国人于1947年发明的。
西方某些学者甚至声称,没有现代科技手段,发明球墨铸铁是不可想象的。
1981年,我国球铁专家采用现代科学手段,对出土的513件古汉魏铁器进行研究,通过大量的数据断定汉代我国就出现了球状石墨铸铁。
有关论文在第18届世界科技史大会上宣读,轰动了国际铸造界和科技史界。
国际冶金史专家于1987年对此进行验证后认为:古代中国已经摸索到了用铸铁柔化术制造球墨铸铁的规律,这对世界冶金史作重新分期划代具有重要意义。
1947年英国H. Morrogh发现,在过共晶灰口铸铁中附加铈,使其含量在0.02wt%以上时,石墨呈球状。
1948年美国A. P. Ganganebin等人研究指出,在铸铁中添加镁,随后用硅铁孕育,当残余镁量大于0.04wt%时,得到球状石墨。
从此以后,球墨铸铁开始了大规模工业生产。
球墨铸铁作为新型工程材料的发展速度是令人惊异的。
1949年世界球墨铸铁产量只有5万吨,1960年为53.5万吨,1970年增长到500万吨,1980年为760万吨,1990年达到915万吨。
2000年达到1500万吨。
球墨铸铁的生产发展速度在工业发达国家特别快。
世界球墨铸铁产量的75%是由美国、日本、德国、意大利、英国、法国六国生产的。
我国球墨铸铁生产起步很早,1950年就研制成功并投入生产,至今我国球墨铸铁年产量达230万吨,位于美国、日本之后,居世界第三位。
适合我国国情的稀土镁球化剂的研制成功,铸态球墨铸铁以及奥氏体-贝氏体球墨铸铁等各个领域的生产技术和研究工作均达到了很高的技术水平。
(1)铸态珠光体球墨铸铁曲轴和铸态铁素体球墨铸铁汽车底盘零件分别在我国第二汽车厂、南京汽车厂和第一汽车厂相继投产。
这标志着我国铸态球墨铸铁生产达到了较高水平。
与之相适应的包外脱硫、双联法熔炼、瞬时孕育、孕育块技术以及音频检测和热分析快速分析等技术的采用,则标志着我国大量流水生产汽车铸件的技术水平与国际先进水平的差距正在缩小。
(2)试验研究了大断面(壁厚大于120mm)球墨铸铁的冶金因素以及相应的生产工艺措施。
采用适量的钇基重稀土复合球化剂、强制冷却、顺序凝固、延后孕育,必要时添加微量锑、铋等可防止球墨铸铁件中心部位的石墨畸变和组织疏松等,现已成功地制作了38吨重的大型复杂结构件,17.5吨重的柴油机体、截面为805mm的球墨铸铁轧辊等。
(3)奥氏体-贝氏体球墨铸铁的研究与应用。
20世纪70年代初,几乎同时中国、美国、芬兰3个国家宣布研究成功了具有高强度、高韧性的奥氏体-贝氏体球墨铸铁(国际上统称ADI),这种材质的抗拉强度达1000MPa,因此它广泛应用于齿轮以及各种结构件,与合金钢相比,奥-贝球墨铸铁具有显著的经济效益和社会效益。
(4)球墨铸铁管和水平连续铸造球墨铸铁型材。
我国已相继建成几个球墨铸铁管厂,且近几年还将有几个球墨铸铁管厂建成。
2000年,我国年产离心铸造球墨铸铁管达90万吨。
此外,我国自行研制的水平连续铸造球墨铸铁型材生产线已通过国家鉴定,并已有多家企业投产。
再加上我国引进的一条生产线,至2002年,我国年产球墨铸铁型材的能力达数万吨。
(5)系统地测定了稀土镁球墨铸铁的力学性能及其他性能,为设计人员提供了有关数据。
测定了稀土镁球墨铸铁的比重、导热性、电磁性等物理性能,结合金相标准研究了石墨和基体组织对球墨铸铁性能的影响规律。
系统地测定了铁素体球墨铸铁在常温、低温、静态和动态条件下的各种性能。
此外,还研究了稀土镁球墨铸铁的应力应变性能、小能量多冲抗力和断裂韧性,并开始用于指导生产。
结合球墨铸铁齿轮的应用,还系统地研究了球墨铸铁的弯曲疲劳强度和接触疲劳强度,以及球墨铸铁齿轮的点蚀、剥落机理等。
(6)稀土镁球墨铸铁。
在高强度低合金球墨铸铁方面,除了对铜、钼研究较多外,还对镍、铌等进行了研究。
在利用天然钒钛生铁制作钒钛合金球墨铸铁方面,国内一些单位进行了大量、系统的工作。
中锰球墨铸铁虽然在性能上不够稳定,但多年来的系统研究与生产应用,取得了显著的经济效益。
在耐热球墨铸铁方面,除了中硅球墨铸铁以外,系统研究了Si+Al总量对稀土镁球墨铸铁抗生长能力的影响。
我国研制的RQTAL5Si5耐热铸铁用作耐热炉条的使用寿命是灰铸铁的3倍,是普通耐热铸铁的2倍,并与日本Cr25Ni13Si2耐热钢的使用寿命相当。
高镍奥氏体球墨铸铁方面也取得了进展,它在石油开采机械、化工设备、工业用炉器件上均取得了成功的应用。
在耐酸球墨铸铁方面,我国生产的稀土高硅球墨铸铁比普通高硅铸铁的组织细小、均匀、致密,由此,抗蚀性能提高了10%~90%,并且其机械强度也有显著改善。
(7)稀土在球墨铸铁中的作用。
稀土能使石墨球化。
自从H. Morrogh最先使用铈得到球墨铸铁以来,先后许多人研究了各种稀土元素的球化行为,发现铈是最有效的球化元素,其他元素也均具有程度不等的球化能力。
结合国情,我国对稀土的球化作用进行了大量研制工作,发现稀土元素对常用的球墨铸铁成分
(C3.6~3.8wt%,Si2.0~2.5wt%)来说,很难获得同镁球墨铸铁那样完整均匀的球状石墨;而且,当稀土量过高时,还会出现各种变态形的石墨,白口倾向也增大,但是,如果是高碳过共晶成分
(C>4.0wt%),稀土残留量为0.12~0.15wt%时,可获得良好的球状石墨。
根据我国铁质差、含硫量高(冲天炉熔炼)和出铁温度低的情况,加入稀土是必要的。
球化剂中镁是主导元素,稀土一方面可促进石墨球化;另一方面克服硫以及杂质元素的影响以保证球化也是必须的。
稀土防止干扰元素破坏球化。
研究表明,当干扰元素Pb、Bi、Sb、Te、Ti等总量为0.05wt%时,加入0.01wt%(残余量)的稀土,可以完全中和干扰,并可抑制变态石墨的产生。
我国绝大部分的生铁中含有钛,有的生铁中含钛高达0.2~0.3wt%,但稀土镁球化剂由于能使铁中的稀土残留量达
0.02~0.03wt%,故仍可保证石墨球化良好。
如果在球墨铸铁中加入0.02~0.03wt%Bi,则几乎把球状石墨完全破坏;若随后加入0.01~0.05wt%Ce,则又恢复原来的球化状态,这是由于Bi和Ce形成了稳定的化合物。
稀土的形核作用。
20世纪60年代以后的研究表明,含铈的孕育剂可使铁液在整个保持期中增加球数,使最终的组织中含有更多的石墨球和更小的白口倾向。
经研究还表明,含稀土的孕育剂可改善球墨铸铁的孕育效果并显著提高抗衰退的能力。
加入稀土可使石墨球数增多的原因可归结为:稀土可提供更多的晶核,但它与FeSi孕育相比所提供的晶核成分有所不同;稀土可使原来(存在于铁液中的)不活化的晶核得以长大,结果使铁液中总的晶核数量增多。