航空发动机涡扇叶片及其成形工艺
航空发动机涡轮叶片冷却技术综述

航空发动机涡轮叶片冷却技术一、引言航空发动机自诞生以来,对它的基本发展要求就是推力更大、推重比更高、耗油率更低、质量更轻、耐久性更好和费用更低等。
因此,航空发动机涡轮的发展趋势主要在以下两个方面:其一是不断提高涡轮前温度;其二就是不断增加涡轮气动负荷,采用跨音速涡轮设计方案,减少涡轮级数和叶片排数。
在现有技术条件下,并在保证尺寸小、质量轻的情况下,提高涡轮前温度,是获得大推力和高推重比的主要措施之一。
从理论上讲,涡轮进口温度每提高100℃,航空发动机的推重比能够提高10%左右。
当前,先进航空发动机涡轮前温度已经达到1900K 左右,这远远超过了涡轮叶片所用的高温合金材料的熔点温度。
为了保证涡轮叶片在高温燃气环境下安全可靠地工作,就必须对叶片采取冷却和热防护措施。
对于高温所带来的一系列问题,解决的办法主要有两个:一是提高材料的耐热性,发展高性能耐热合金,制造单晶叶片;二是采用先进的冷却技术,以少量的冷却空气获得更高的降温效果。
其中材料的改善占40%,冷却技术占60%。
对于军用航空发动机,第3代的涡轮进口温度为1680~1750K,涡轮叶片耐温能力主要通过第1代单晶合金或定向合金和气膜冷却技术保证;第4代的涡轮进口温度达到1850~1980K,涡轮叶片耐温能力主要通过第2代单晶合金和对流-冲击-气膜复合冷却技术来保证;未来一代的涡轮进口温度将高达2200K,预计涡轮叶片耐温能力通过第3代单晶合金或陶瓷基复合材料等耐高温材料和包括层板发散冷却在内的更加高效的冷却技术来保证。
二、航空发动机涡轮叶片冷却技术概述涡轮冷却技术研究始于上个世纪40年代,大约在1960年,气冷涡轮首次应用于商业航空发动机上。
经过多年的发展,目前基本上形成了由内部冷却和外部冷却构成的涡轮叶片冷却方案。
1.内部冷却其基本原理是冷气从叶片下部进入叶片内部,通过带肋壁的内流冷却通道,对叶片的内表面实施有效的冷却,一部分冷气通过冲击孔,以冲击冷却的形式对叶片前缘内表面进行冷却,剩下的一部分气体经过叶片尾部的扰流柱,被扰动强化换热以后从尾缘排出。
那些漂亮的航空发动机叶片必须经过这个制造技术的打磨!

那些漂亮的航空发动机叶片必须经过这个制造技术的打磨!航空发动机零件的表面质量是评价产品的一个重要指标。
目前,一些复杂型面航空零件的边缘倒圆、机加叶片零件表面的残留刀纹去除仍未完全摆脱手工抛光方式,除了耗费大量的人力资源,也易造成产品质量不稳定,甚至影响发动机整机性能与寿命。
滚磨光整技术能有效地提高零件表面质量等级,清除毛刺、刀痕等表面缺陷,还能使零件金属表层产生微弱的塑性变形,改善表面残余应力状况。
当前在一些航空发动机零件制造中应用滚磨光整技术,已取得了较好的经济效益与社会效益。
滚磨光整加工滚磨光整加工是将工件、磨块和磨剂按一定混合比装入滚筒中,当滚筒运动时,在工件和磨块间产生强大的挤压力和强制流动力,迫使磨块对工件产生碰撞、滚压、滑擦和刻划,从而实现对工件表面的光整加工。
1滚磨光整加工的类型根据滚筒的运动方式,滚磨光整加工可分为以下几种形式:(1)回转式滚磨:滚筒作单一的回转运动,其转速n 必须小于某固定值,否则工件与磨料将紧贴在滚筒周壁,相互间不产生相对运动而无法实现表面的光整加工。
因此,这种加工方法效率低、质量差,现已逐渐被其他方法所取代。
(2)振动式滚磨:滚筒作三维的空间振动运动,工件和磨料在圆环形容器中沿螺旋轨迹运动,形成复杂的运动轨迹。
这种加工方法对细化表面质量较好,对表面物理机械性能的改善不大,不适用于较大较长的工件。
(3)离心式滚磨:滚筒既自转又公转作行星运动。
这种加工方法可以获得较高的加工质量和加工效率。
(4)主轴回转滚磨:滚筒作回转运动,夹持工件的主轴作逆向回转。
这种加工方法工件有固定的位置,当滚筒与主轴选择合适的相对转速时,便可以获得较好的加工质量和较好的加工效率。
(5)旋转振动式滚磨:滚筒兼具回转运动与空间振动运动方式。
磨料运动轨迹复杂,更易加工一些复杂型面的大型工件。
2滚磨光整的功能特点及适用范围滚磨光整主要有以下特点:(1)操作简单,生产效率高,环境污染小;(2)可实现铸锻件的去飞边、去氧化层和表面清洁处理,也可用于切削加工后零件去毛刺、棱边倒圆和细化表面,降低表面粗糙度值;(3)可适度改善表面应力分布状态;(4)对于内孔、沟槽及凹陷表面的光整加工相对较难,对易变形、易磕碰零件需在光整过程中作防护处理。
航空发动机涡轮叶片精密成型技术分析

航空发动机涡轮叶片精密成型技术分析摘要:航空发动机技术复杂且难以制造。
世界上只有几个国家可以完成航空发动机的设计和制造。
中国不断发展航空发动机的设计和制造,以提高自身的制造水平。
空心涡轮叶片是高性能航空发动机的主要部件之一,制造困难长期以来一直给中国的制造公司带来麻烦。
通过分析空心涡轮叶片的结构特性,分析和解释空心涡轮叶片的精密成型技术。
关键词:空心涡轮叶片;精密成型技术;精密铸造前言空心涡轮叶片是高性能航空发动机的关键组件,由于对精度的要求和制造困难,我们无法批量生产空心涡轮叶片。
为了提高空心涡轮叶片的制造合格率,我们将从叶片精密铸造的“形状控制”和“可控制性”两个方面出发分析空心涡轮叶片的精密铸造工艺,以提高叶片精密铸造的质量。
需要1空心涡轮叶片的精密铸造技术现代飞机发动机正朝着高推进力和低油耗的方向发展。
为了实现这一目标,当今世界上的主流方法是提高航空发动机涡轮的进气温度。
发动机涡轮的当前入口温度已经很高。
随着温度的不断升高,发动机涡轮叶片的温度达到1880℃±50℃,为了解决这个问题,目前的涡轮叶片主要用于复合膜冷却的单晶空心涡轮叶片(称为空心涡轮叶片)。
由于结构的复杂性和材料的特殊性,熔模铸造工艺主要用于制造空心涡轮叶片,但由于精度低,产量低,该工艺存在使空心涡轮叶片具有高性能的问题。
有。
通常,当今的空心涡轮叶片精密铸造的产率约为10%,其中约90%的废叶片的形状和尺寸偏差约为50%,而重结晶缺陷约占25%。
主要原因是铸造缺陷。
为了提高空心涡轮叶片的制造成品率,有必要解决“形状控制”和“铸造控制”两个问题:精密铸造后的尺寸精度和复合材料性能。
空心涡轮叶片的工艺复杂且难以制造:粗略的制造过程如下:首先,使用模芯来完成空心涡轮叶片精密铸造所需的陶瓷芯,并且陶瓷芯是空心的填充零件。
用来。
随后,使用蜡模工艺在芯的外层上制备涡轮叶片蜡模,然后通过烧结注射成型和其他工艺来制造空心涡轮叶片粗糙毛坯。
涡轮叶片气膜孔加工技术及其发展

涡轮叶片气膜孔加工技术及其发展涡轮是中热负荷和机械负荷最大的部件,涡轮叶片的工作环境尤为恶劣,在发动机循环中,它承受着燃烧后的高温高压燃气冲击,其制造技术也被列为现代航空发动机的关键技术。
发动机性能很大程度上取决于涡轮进口温度的高低,它受涡轮叶片材料的限制。
对这些部件进行连续不断的冷却,可以允许它们的工作环境温度超过材料的熔点,这样仍能安全可靠的工作,气膜冷却技术是具有代表性的重要结构改进之一,大大提高了发动机的性能,同时也对气膜孔加工技术提出了更高的要求。
随着制造技术的发展,气膜孔加工新技术也不断出现,在传统的激光打孔(Laser)、电火花高速打孔(EDM)、电化学打孔(ECM)等加工方法的基础上,又发展了激光电火花复合打孔、电解电火花复合打孔等新工艺,去除重熔层技术在磨粒流的基础上,又发展应用了化学研磨技术、电解质- 等离子加工等新技术,为提高涡轮叶片气膜孔加工质量、技术水平和生产效率做出了重要贡献。
气膜冷却技术的发展和应用据统计,涡轮前温度平均每年升高25K,其中约15K是依靠冷却技术的进步取得的。
在过去的三、四十年中,涡轮进口温度提高了大约450K。
其中70%是由于涡轮工作叶片和导向叶片的高效冷却设计取得的,而另外30% 应归于高温合金和铸造加工工艺的改进。
随着航空发动机技术的发展,出现了许多先进的涡轮叶片冷却技术,其发展趋势如图1所示。
提高涡轮进口温度是增大和提高发动机推力与推重比的重要手段。
在材料耐温能力有限的前提下,涡轮叶片冷却技术成为了提高涡轮进口温度、保证涡轮在高温环境下可靠工作的可行且高效的途径。
为此,世界航空发动机设计与制造商研究和开发了大量的涡轮叶片冷却技术,成功地验证和应用了冲击、对流、气膜、复合冷却、铸冷和超冷等叶片技术,并且在提高涡轮进口温度(进而提高涡扇发动机的性能)方面取得了很好的效果。
图2为涡轮叶片及其内部冷却通道的形式图。
气膜孔加工技术气膜冷却技术的主要结构特点是在涡轮叶片前缘、叶身型面等部位设计了大量的气膜孔,孔径一般在0.2~0.8mm,空间角度复杂。
航空发动机精锻叶片数字化数控加工技术
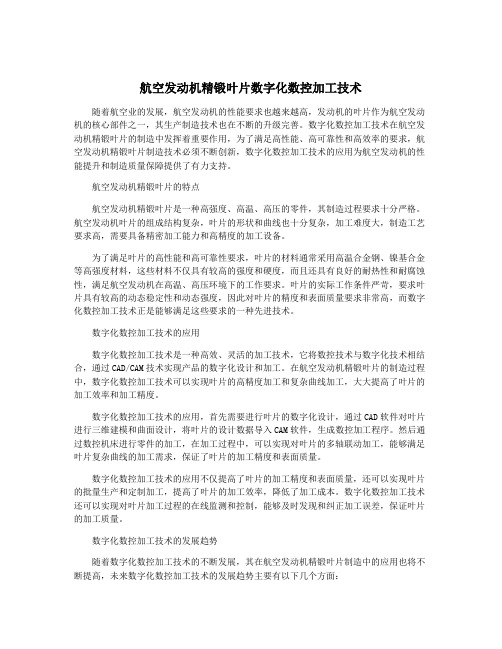
航空发动机精锻叶片数字化数控加工技术随着航空业的发展,航空发动机的性能要求也越来越高,发动机的叶片作为航空发动机的核心部件之一,其生产制造技术也在不断的升级完善。
数字化数控加工技术在航空发动机精锻叶片的制造中发挥着重要作用,为了满足高性能、高可靠性和高效率的要求,航空发动机精锻叶片制造技术必须不断创新,数字化数控加工技术的应用为航空发动机的性能提升和制造质量保障提供了有力支持。
航空发动机精锻叶片的特点航空发动机精锻叶片是一种高强度、高温、高压的零件,其制造过程要求十分严格。
航空发动机叶片的组成结构复杂,叶片的形状和曲线也十分复杂,加工难度大,制造工艺要求高,需要具备精密加工能力和高精度的加工设备。
为了满足叶片的高性能和高可靠性要求,叶片的材料通常采用高温合金钢、镍基合金等高强度材料,这些材料不仅具有较高的强度和硬度,而且还具有良好的耐热性和耐腐蚀性,满足航空发动机在高温、高压环境下的工作要求。
叶片的实际工作条件严苛,要求叶片具有较高的动态稳定性和动态强度,因此对叶片的精度和表面质量要求非常高,而数字化数控加工技术正是能够满足这些要求的一种先进技术。
数字化数控加工技术的应用数字化数控加工技术是一种高效、灵活的加工技术,它将数控技术与数字化技术相结合,通过CAD/CAM技术实现产品的数字化设计和加工。
在航空发动机精锻叶片的制造过程中,数字化数控加工技术可以实现叶片的高精度加工和复杂曲线加工,大大提高了叶片的加工效率和加工精度。
数字化数控加工技术的应用,首先需要进行叶片的数字化设计,通过CAD软件对叶片进行三维建模和曲面设计,将叶片的设计数据导入CAM软件,生成数控加工程序。
然后通过数控机床进行零件的加工,在加工过程中,可以实现对叶片的多轴联动加工,能够满足叶片复杂曲线的加工需求,保证了叶片的加工精度和表面质量。
数字化数控加工技术的应用不仅提高了叶片的加工精度和表面质量,还可以实现叶片的批量生产和定制加工,提高了叶片的加工效率,降低了加工成本。
航空发动机叶片加工工艺探讨

航空发动机叶片加工工艺探讨摘要:在国家飞机装备的制造加工过程中,航空发动机是十分关键的加工部分,其加工质量至关重要。
发动机叶片的制造问题是飞机零部件制造应用领域一道已知的“瓶颈”问题。
由于发动机叶片具有重量轻、壁薄、变异性大等特征,其制造技术一直是研究的重点。
随着科学技术的进步,数字化和自动化机床的引入都极大地改进了叶片制造工艺,在加工的过程中,保障发动机叶片的质量至关重要。
如何高效稳定地制造发动机叶片依然是一个加工难点。
基于此,阐述航空发动机叶片的主要形状与特征,并对航空发动机叶片的加工工艺做出了详尽的分析具有重要意义。
关键词:航空发动机;发动机叶片加工特征;加工工艺探讨;加工检验引言航空发动机是飞行装备加工制造过程中最重要的零件,其叶片也是发动机中数量最多、工艺最复杂的一部分。
在航空发动机的基本构造中,压气机主要由整流叶片组成,数量最多。
正因如此众多性能优异的叶片,航空发动机可以进行多种用途。
航空发动机可以利用叶片的功能对空气进行挤压与扩张,并从中产生动能,从而驱动飞行器正常工作运行。
叶片作为发动机部件中的重要部分,不但数量庞大,而且造型复杂多变。
也正因为叶片加工工艺的复杂性,在叶片加工生产过程中会出现很多影响叶片品质的问题。
作为发动机叶片研究者,保证发动机叶片质量至关重要,这也是发动机叶片加工工艺的难点。
这就要求研究人员必须在实际处理过程中不断结合经验,不断增加人力与财力的投资,以此保证发动机叶片的加工质量。
一、航空发动机叶片加工的主要特征航空发动机开发中所采用的叶片加工技术,和普通发动机批量生产中所采用的叶片加工技术有较大差别[1]。
专业厂家的叶片生产周期一般为十二至十四个月。
而航空发动机开发的叶片加工周期一般为六个月至十二个月。
在飞机发动机研制过程中,叶片的制造批量往往相当小,而且通常是几个或一个的小批量生产。
在航空发动机的研制过程中,叶片技术应该尽量选择国际通用的高效率加工机床,以减少叶片的加工周期,从而降低生产成本。
航空发动机原理图文解析

航空发动机原理--螺桨风扇发动机螺桨风扇发动机是一种介于涡轮风扇发动机和涡轮螺旋桨发动机之间的一种发动机形式,其目标是将前者的高速性能和后者的经济性结合起来,目前正处于研究和实验阶段。
螺桨风扇发动机的结构见图,它由燃气发生器和一副螺桨-风扇(因为实在无法给这个又象螺旋桨又象风扇的东东起个名字,只好叫它螺桨-风扇)组成。
螺桨-风扇由涡轮驱动,无涵道外壳,装有减速器,从这些来看它有一点象螺旋桨;但是它的直径比普通螺旋桨小,叶片数目也多(一般有6~8叶),叶片又薄又宽,而且前缘后掠,这些又有些类似于风扇叶片。
根据涡轮风扇发动机的原理,在飞行速度不变的情况下,涵道比越高,推进效率就越高,因此现代新型不加力涡轮风扇发动机的涵道比越来越大,已经接近了结构所能承受的极限;而去掉了涵道的涡轮螺旋桨发动机尽管效率较高,但由于螺旋桨的速度限制无法应用于M0.8~M0.95的现代高亚音速大型宽体客机,螺桨风扇发动机的概念则应运而生。
由于无涵道外壳,螺桨风扇发动机的涵道比可以很大,以正在研究中的一种发动机为例,在飞行速度为M0.8时,带动的空气量约为内涵空气流量的100倍,相当于涵道比为100,这是涡轮风扇发动机所望尘莫及的,将其应用于飞机上,可将高空巡航耗油率较目前高涵道比轮风扇发动机降低15%左右。
同涡轮螺旋桨发动机相比,螺桨风扇发动机的可用速度又高很多,这是由它们叶片形状不同所决定的。
普通螺旋桨叶片的叶型厚度大以保证强度,弯度大以保证升力系数,从剖面来看,这种叶型实际上就是典型的低速飞机的机翼剖面形状,它在低速情况下效率很高,但一旦接近音速,效率就急剧下降,因此装有涡轮螺旋桨发动机的飞机速度限制在M0.6~M0.65左右;而螺桨-风扇的既宽且薄、前缘尖锐并带有后掠的叶型则类似于超音速机翼的剖面形状,这种叶型的跨音速性能就要好的多,在飞行速度为M0.8时仍有良好的推进效率,是目前新型发动机中最有希望的一种。
当然,螺桨风扇发动机也有其缺点,由于转速较高,产生的振动和噪音也较大,这对舒适性有严格要求的客机来讲是一个难题。
航空发动机叶片材料及制造技术现状

航空发动机叶片资料及制造技术现状在航空发动机中,涡轮叶片由于处于温度最高、应力最复杂、环境最恶劣的部位而被列为第一要点件,并被誉为“王冠上的明珠”。
涡轮叶片的性能水平,特别是承温能力,成为一种型号发动机先进度度的重要标志,在必然意义上,也是一个国家航空工业水平的显然标志【 007】。
航空发动机不断追求高推重比,使得变形高温合金和铸造高温合金难以满足其越来越高的温度及性能要求,因其他国自7O年代以来纷纷开始研制新式高温合金,先后研制了定向凝固高温合金、单晶高温合金等拥有优异高温性能的新资料;单晶高温合金已经发展到了第3代。
8O年代,又开始研制了陶瓷叶片资料,在叶片上开始采用防腐、隔热涂层等技术。
1航空发动机原理简介航空发动机主要分民用和军用两种。
图 1是普惠公司民用涡轮发动机主要构件;图2是军用发动机的工作原理表示图;图 3是飞机涡轮发动机内的温度、气流速度和压力分布;图 4是罗尔斯 -罗伊斯喷气发动机内温度和资料分布;图 5为航空发动机用不同样资料用量的发展变化情况。
图 1普惠公司民用涡轮发动机主要构件图2 EJ200 军用飞机涡轮发动机的工作原理图3商用涡轮发动机内的温度、气流速度和压力分布图4罗尔斯-罗伊斯喷气发动机内温度和资料分布图5航空发动机用不同样资料用量的变化情况1变形高温合金叶片1.1 叶片资料变形高温合金发展有 50多年的历史,国内飞机发动机叶片常用变形高温合金如表 1所示。
高温合金中随着铝、钛和钨、钼含量增加,资料性能连续提高,但热加工性能下降;加入昂贵的合金元素钴此后,能够改进资料的综合性能和提高升温组织的牢固性。
表1国内飞机叶片用高温合金牌号及其工作温度合金牌号合金系统GH4169Cr-Ni GH4033Cr-NiGH4080A Cr-Ni GH4037Cr-Ni GH4049Cr-Ni-Co GH4105Cr-Ni-Co GH4220Cr-Ni-Co 使用温度 /℃特点及应用650 热加工性能好,热变形和模锻叶片成形不困难,叶身变形80%也不开裂。
- 1、下载文档前请自行甄别文档内容的完整性,平台不提供额外的编辑、内容补充、找答案等附加服务。
- 2、"仅部分预览"的文档,不可在线预览部分如存在完整性等问题,可反馈申请退款(可完整预览的文档不适用该条件!)。
- 3、如文档侵犯您的权益,请联系客服反馈,我们会尽快为您处理(人工客服工作时间:9:00-18:30)。
航空发动机涡扇叶片及其成形工艺涡扇发动机具有耗油率低、起飞动力大、噪音低和迎风面积大等特点。
60年代中期,它只应用于客机和轰炸机,当时人们普遍认为,它很难在高速歼击机上应用。
自70年代以来,带加力的高推比涡扇发动机的相继问世,使战斗机的性能提高到了一个新的水平,从而彻底改变了人们对涡扇发动机的偏见。
90年代中期,又为第四代战斗机成功研制了推重比10带加力的涡扇发动机。
与此同时,为满足发展巨型、远程运输机、宽机身客机的需要,国外先进的发动机厂家又研制成功了大推力、低耗油率、大流量比的涡扇发动机。
时至今日,涡扇发动机已是应用数量最多、范围最广和最有发展前景的航空发动机。
风扇叶片是涡扇发动机最具代表性的重要零件,涡扇发动机的性能与它的发展密切相关。
初期的风扇叶片材料为钛合金,具有实心、窄弦、带阻尼凸台结构。
现今,风扇叶片在材料、结构方面已改进许多。
为了增强刚性,防止振动或颤振,提高风扇叶片的气动效率,用宽弦结构代表了窄弦、带阻尼凸台结构;为了减轻重量,用夹芯或空心结构取代了实心结构;为了增大流量比,提高大推力涡扇发动机推进效率,风扇转子直径已增大到了3242mm,风扇叶尖速度已高达457m/s。
而这些材料新、叶身长、叶弦宽、结构复杂的风扇叶片的成形工艺是非常复杂的。
因此,风扇叶片的成形工艺始终是涡扇发动机的关键制造技术之一。
1早期风扇叶片早期风扇叶片为大尺寸实心结构,为防止共振及颤振,它的叶身中部常带有一个阻尼凸台(又称减振凸台)。
所有叶片的凸台连成一环状,既增强了刚性又改变了叶片固有频率,减小了叶根弯曲和扭转应力。
阻尼凸台接合面喷涂有耐磨合金,当叶片振动时,接合面相互摩擦可起阻尼作用。
阻尼凸台一般位于距叶根约整个叶片长度的50%~70%处。
阻尼凸台的存在带来一系列问题,如:由于它的存在及它与叶身连接处的局部加厚,使流道面积减少约2%,使空气流量降低,造成气流压力损失,使压气机效率下降,发动机耗油率增加;增加了叶身重量,使叶片离心力负荷加大;使叶片制造工艺更加复杂。
在有些风扇叶片上,为了增强抗外物撞击损伤能力,叶身上除了阻尼凸台以外,还有较厚的加强筋。
CFM56-3和CFM56-5发动机风扇转子直径约1700mm,风扇叶片长约600mm,由整体钛合金锻件经机械加工而成。
风扇叶片毛坯先镦锻出叶根和阻尼凸台,经预锻成形,再精锻、切边。
叶身成形可用数控铣、数控仿形磨、电解加工和抛光等工艺。
随着叶片批量生产的增加,应尽量采用精锻法生产出钛合金风扇叶片的锻坯,以提高材料的利用率,减少机械加工工作量和提高风扇叶片的使用寿命。
但生产这样大的风扇叶片精锻毛坯,需要使用昂贵的高精度的万吨级机械压力机或螺旋压力机,所需模具的尺寸大、精度也高。
因此,精锻工序的成本很高。
4钛合金宽弦无凸台空心风扇叶片5高韧性环氧复合材料风扇叶片CFM56渦扇發動機的推重比達到5左右2第一代宽弦无凸台风扇叶片针对早期风扇叶片存在的缺点,英国罗*罗公司80年代首先研制成功了面板夹蜂窝芯组成的宽弦无凸台风扇叶片,即第一代宽弦无凸台风扇叶片,并在RB211-535E和V2500等发动机上应用。
叶片弦长比原来增加40%左右,由于刚性增强,因而取消了凸台。
第一代宽弦无凸台风扇叶片具有以下优点:采用宽弦叶片后,转子叶片数量减少了1/3,转子重量一般可减轻10%~30%;蜂窝芯结构还可改善叶片的减振特性;与带阻尼凸台的窄弦风扇叶片相比,叶栅通道面积加大,喘振裕度变宽,级效率提高,寿命增加。
第一代宽弦无凸台风扇叶片制造的主要工序如图1所示。
叶背、叶盆面板用钛合金(Ti-6Al-4V)热轧板材,经精锻或等温锻成形。
化铣除去污染层,并将面板腐蚀成设计要求的气动外形和相应的内腔。
夹芯蜂窝块用钛合金箔板辊压成波纹板,再用电阻焊焊接而成,然后将两面板和夹芯蜂窝块采用活性扩散焊将其焊成整体结构。
叶片的外型面还要在数控铣床上精加工。
经破坏性试验证明,活性扩散连接性能很好,连接处从未开裂。
风扇叶片投入使用前,还经过了严格的投鸟考核试验。
V2500发动机在使用中曾遭受多次巨鸟的撞击事件,发动机仍然安全无恙,这充分证明了这种风扇叶片的结构设计和制造技术是非常成功的。
RB211系列发动机是由罗尔斯罗伊斯(劳斯莱斯)股份有限公司(以下简称罗罗公司)研制生产的高涵道比三转子轴流式涡扇发动机。
于1972年投入使用,发动机的推力为37400-60600磅,并且RB211发动机是世界上最早的三转子发动机。
主要型号有RB211-524和RB211-535分别用于Boeing747-300和Boeing757等飞机。
图1第一代宽弦无凸台风扇叶片的主要制造工序Fig.1Main process for the first generationwide chord lobe_free fan blade3第二代宽弦无凸台风扇叶片用超塑成形/扩散连接组合工艺制成的风扇叶片,即罗.罗公司的第二代宽弦无凸台风扇叶片,它的芯部用建筑物上常用的三角形桁架结构取代了第一代宽弦无凸台风扇叶片的蜂窝芯板。
这种三角形桁架结构不仅轻,而且能参与承力,每片叶片重量比蜂窝芯风扇叶片少15%。
这种风扇叶片已用于A330和波音777飞机的遄达发动机上。
该发动机风扇转子直径为2794mm,风扇叶片速度为457m/s,每个叶片重9kg,气动设计和制造技术均处于当今世界先进水平。
第二代宽弦无凸台风扇叶片采用三层板超塑成形/扩散连接组合成形工艺,其工艺过程见图2。
首先在中间芯板上按一定图形喷涂止焊剂。
其次将芯板与两层面板用氩弧焊焊接缝边(留有进气口),将焊好的三层板放入叶片型面的模具内,连同模具一起放入带有加热系统的压气机内。
当加热至超塑成形/扩散连接温度(钛合金为920℃)时,向模内吹入一定压力的氩气(1.5~2MPa),然后保温、保压,使三层板在各预定部位和周边(无止焊剂部位)进行扩散连接。
连接完成后,再向三层板内吹入一定压力的氩气进行超塑成形,两层面板在超塑状态下进行拉伸和扭曲变形,中间芯板延展变形,形成格形结构。
在向三层板内吹入氩气时,模内氩气应逐渐排出。
板材完全贴模成形后,随炉冷却。
最后取出叶片进行表面化铣,数控加工叶根、叶型边缘,经终检后得到成品。
图2第二代宽弦无凸台风扇叶片的制造工艺过程Fig.2Process of the second generationwide chord lobe_free fan blade美国普惠公司在制造钛合金宽弦无凸台空心风扇叶片时,采用了超塑成形/扩散连接工艺。
其制造过程如图3所示。
叶身由机械加工铣削成带肋的两半片对称的扁平叶身,将两半叶身在平板状态下放入模具内,用扩散连接方法将两半扁平叶身面对面焊成一体,再用超塑成形工艺使叶片成形。
成形过程分成两步:第1步先将叶片毛坯放在一个形状与叶片成品相似的夹具内,并将它放入真空炉内加热至超塑状态,毛坯在重力作用下附在夹具上,使叶片扭度达到要求值的90%;第2步再将叶片放入最终成形模内,向叶片内吹入一定压力的氩气,在超塑状态下,使叶片100%贴模。
最后取出成形的叶片,数控加工叶根。
图3钛合金宽弦无凸台空心风扇叶片的制造工艺过程Fig.3Process of Ti alloy wide chordlobe-free hollow fan blade普惠公司应用这一方法已制造出F119发动机的一级风扇叶片和波音777飞机的PW4084发动机的大型风扇叶片。
其中,PW4084发动机风扇转子直径为2849mm,风扇叶尖速度达387m/s。
美国通用电气公司在GE90发动机上,用高韧性环氧树脂复合材料代替钛合金制成了当今世界上最大的风扇叶片。
该风扇叶高1.1m,弦长0.61m,风扇转子直径3242mm,风扇叶尖速度360~390m/s。
设计和制造这种风扇叶片是冒很大技术风险的。
为提高叶片抗分层性能和抗剪强度,通用电气公司发展了一种称之为大力神8551-7/IM7的增韧环氧/石墨纤维。
在环氧中加入卡芙拉(kevlar)微粒。
用模压成形法制造树脂基复合材料风扇叶片的工艺过程如下:首先用模板法或冲模法截取各个铺层,由于每个铺层尺寸大小不一,可用计算机放样技术来确定它的尺寸。
再将不同铺层以一定顺序装在模具上,按给定工艺参数进行固化。
脱模后对叶片进行加工、去毛刺、修整和钻孔,按顺序在叶片前缘铺上胶膜、丝网和装配完金属保护板后,在一定工艺条件下加热、加压固化。
最后脱模修整后,对叶片表面进行喷砂处理,打底漆,并涂上0.2~0.25mm厚的聚氨酯涂料,待其干燥固化后,即得到带有前缘保护的实心复合材料叶片。
用高韧环氧复合材料制造的风扇叶片比钛合金夹芯结构的风扇叶片轻3184g。
在抗振特别是抗颤振性能方面也优于钛合金,抗鸟击能力和低噪音指标也获得适航当局的合格批准。
装高韧环氧复合材料风扇叶片的GE90发动机已装于波音777飞机,并在1995年投入航线运营使用。
美国F-22“猛禽”战机所使用的F119发动机结构图6金属基复合材料风扇叶片美国普惠公司正在研制连续碳化硅纤维增强的钛基复合材料风扇叶片。
这种用超塑成形/扩散连接工艺制成的重量轻、刚性好、耐撞击破坏强度高的空心风扇叶片可使发动机风扇级再减重约14%。
金属基复合材料风扇叶片的制造过程如下:首先将碳化硅纤维(SCS-6)和钛合金(Ti-6Al-4V)制成钛面板,经X射线、超声波、金相和尺寸检查合格后将它加工成楔形板,再用超塑成形/扩散连接工艺将它制成成形板;然后对成形板进行尺寸和无损检测,以确保金属基复合材料有效连接和成形、内部无缺陷、表面无裂纹、增强纤维无任何变化,并保证蒙皮与芯板的连接缝、扩散连接面的连接质量;最后将检查合格的成形板,按风扇叶片尺寸要求制成叠板组件,用超塑成形/扩散连接工艺成形。
叶片蒙皮厚度从根部到叶尖递减。
蒙皮的制造方法是将单向排列的SCS-6纤维与钛交织成织物(用钛箔控制纤维间隔)按照厚度要求确定蒙皮层数,最后在热等静压罐内扩散结合。