蒸馏塔的设计-
学习情境四 蒸馏塔的设计与操作
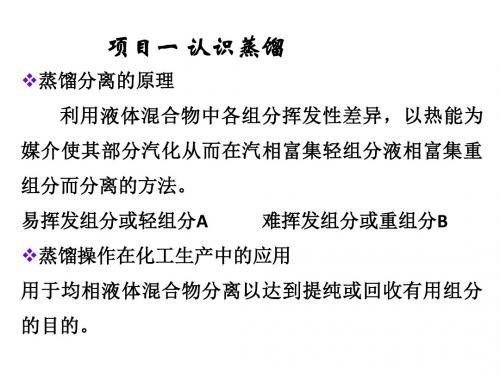
溶液沸腾时,溶液上方的总压应等于各组分分压之和
P pA pB p x p 1 xA
0 P pB xA 0 0 p A pB
0 A A
0 B
泡点方程
poA、 poB 取决于溶液沸腾温度,上式表达一定总压 下液相组成与溶液泡点温度关系。已知溶液的泡点 可由上式计算液相组成;反之,已知溶液组成也可 算出溶液泡点。 纯组分 饱和蒸汽压与温度的关系,用Antoine方程表示:
(二)操作线方程 在连续精馏塔中,因原料液不断从塔的中部加入,致使精馏 段和提馏段具有不同的操作关系。
1.精馏段操作线方程
对精馏段的第 n 十 1 层板以上塔 段及冷凝器作物料衡算,以单 位时间为基准: 总物料衡算: V=L+D 易挥发组分衡算:vyn+1=Lxn+DxD 式中 :V—— 精馏段上升蒸汽的 摩尔流量,kmol/h; L—— 精馏段下降液体的摩尔流 量,kmol/h; yn+1—— 精馏段第 n 十 1 层板上升 蒸汽中易挥发组分的摩尔分数; xn—— 精馏段第 n 层板下降液体 中易挥发组分的摩尔分数。
精馏计算
一、全塔物料衡算
稳定连续操作的精馏塔,以单位时间 为基准,则全塔物料衡算式为: 总物料衡算: F=D+W 易挥发组分衡算: F xF=D xD +W xW 式中: F、D、W——分别为原料、塔顶产品 和塔底产品 的流量,Kmol/h; xF、xD、xW——分别为原料、塔顶产 品和塔底产品中易挥发组分的摩尔分 数。 全塔物料衡算式应用:确定产品流量 及组成。
塔顶轻组分的回收率
DxD 100% : D FxF
W ( 1 x ) W 100% 塔釜难挥发组分的回收率 W : W F (1 xF )
正戊烷-正己烷连续蒸馏塔的设计.doc
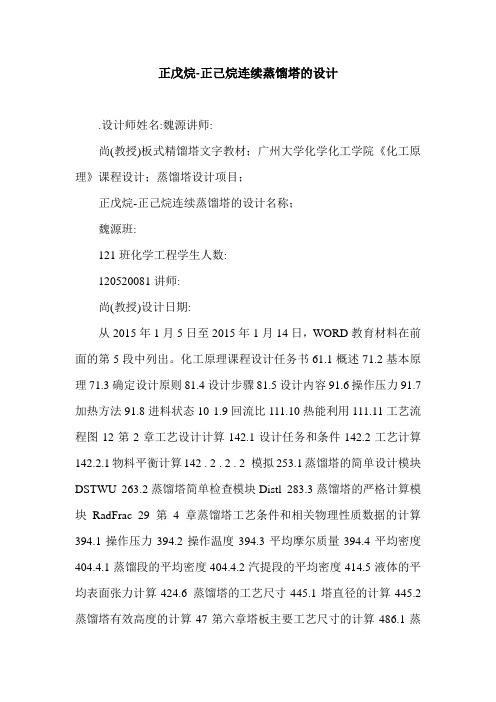
正戊烷-正己烷连续蒸馏塔的设计.设计师姓名:魏源讲师:尚(教授)板式精馏塔文字教材;广州大学化学化工学院《化工原理》课程设计;蒸馏塔设计项目;正戊烷-正己烷连续蒸馏塔的设计名称;魏源班:121班化学工程学生人数:120520081讲师:尚(教授)设计日期:从2015年1月5日至2015年1月14日,WORD教育材料在前面的第5段中列出。
化工原理课程设计任务书61.1概述71.2基本原理71.3确定设计原则81.4设计步骤81.5设计内容91.6操作压力91.7加热方法91.8进料状态10 1.9回流比111.10热能利用111.11工艺流程图12第2章工艺设计计算142.1设计任务和条件142.2工艺计算142.2.1物料平衡计算142 . 2 . 2 . 2 模拟253.1蒸馏塔的简单设计模块DSTWU 263.2蒸馏塔简单检查模块Distl 283.3蒸馏塔的严格计算模块RadFrac 29第4章蒸馏塔工艺条件和相关物理性质数据的计算394.1操作压力394.2操作温度394.3平均摩尔质量394.4平均密度404.4.1蒸馏段的平均密度404.4.2汽提段的平均密度414.5液体的平均表面张力计算424.6 蒸馏塔的工艺尺寸445.1塔直径的计算445.2蒸馏塔有效高度的计算47第六章塔板主要工艺尺寸的计算486.1蒸馏段主要工艺尺寸的计算486.1.1溢流堰486.1.2塔板布置和浮阀数量和布置的计算516 .2蒸馏段主要工艺尺寸的计算536.2.1溢流单元的计算536.2.2塔板布置和浮阀数量和布置54 塔板流体动力学检查577.1精馏段流体动力学检查577.1.1气相压降通过浮阀塔577.1.2浸没塔检查587.1.3雾沫夹带检查597.2精馏段流体动力学检查617.2.1气相压降通过浮阀塔617.2.2浸没塔检查617.2.3夹带检查62第8章塔盘负载性能图638.1精馏段塔盘负载性能图638.1.1夹带线638.1 658.2汽提段塔盘负负荷性能图表668.2.1夹带线668.2.2溢流线678.2.3液体负荷上限线688.2.4泄漏线688.2.5液体负荷下限线69蒸馏段浮阀塔盘工艺设计计算结果汇总表1 71蒸馏段浮阀塔盘工艺设计计算结果汇总表2 72第9章热平衡739.1热平衡739.1塔顶冷凝器冷热平衡739.1.2总塔盘热量结构设计8110.1整体结构8110.1.1基本结构8110.1.2塔的主要尺寸8110.1.3气缸和气缸盖8310.1.4塔的总有效高度-魏源讲师:尚(教授)板式精馏塔文字教材;广州大学化学化工学院《化工原理》课程设计;蒸馏塔设计项目;正戊烷-正己烷连续蒸馏塔的设计名称;魏源班:121班化学工程学生人数:120520081讲师:尚(教授)设计日期:从2015年1月5日至2015年1月14日,WORD教育材料在前面的第5段中列出。
原油常压蒸馏塔工艺设计

原油常压蒸馏塔工艺设计原油常压蒸馏塔工艺设计原油常压蒸馏塔是炼油厂中最基本的设备之一,其主要作用是将原油分离成不同的馏分。
在设计常压蒸馏塔时,需要考虑多个因素,包括原油的物理化学性质、塔的结构和操作参数等。
下面将详细介绍常压蒸馏塔的工艺设计。
一、原油物性分析在设计常压蒸馏塔时,首先需要对原油进行物性分析。
原油的物性包括密度、粘度、沸点范围、蒸汽压等。
这些物性参数对于确定塔的操作参数和分离效果至关重要。
二、塔的结构设计常压蒸馏塔的结构包括塔底、塔体和塔顶三部分。
塔底主要包括进料管、分离器和液位控制器等。
塔体由多个塔板组成,塔板上通常设置有气液分离器和液相收集器。
塔顶包括冷凝器、回流器和出料管等。
在设计塔的结构时,需要考虑原油的物性和塔的操作参数。
例如,对于高沸点的原油,需要增加塔板数目和塔高度,以提高分离效果。
而对于低沸点的原油,则需要减少塔板数目和塔高度,以降低能耗和成本。
三、操作参数设计常压蒸馏塔的操作参数包括进料温度、进料流量、回流比、塔顶温度等。
这些参数对于塔的分离效果和能耗有着重要的影响。
在设计操作参数时,需要考虑原油的物性和塔的结构。
例如,对于高沸点的原油,需要提高进料温度和回流比,以提高分离效果。
而对于低沸点的原油,则需要降低进料温度和回流比,以降低能耗和成本。
四、塔的优化设计在完成初步设计后,需要对塔进行优化设计。
优化设计的目的是提高分离效果和降低能耗和成本。
常用的优化方法包括增加塔板数目、调整操作参数、改变塔的结构等。
总之,常压蒸馏塔的工艺设计需要考虑多个因素,包括原油的物性、塔的结构和操作参数等。
只有在充分考虑这些因素的基础上,才能设计出高效、节能的常压蒸馏塔。
化工原理蒸馏塔课程设计简易步骤

关于课程设计的几点说明1.《化工原理课程设计》是我们学完《化工原理》理论课后,综合应用本门课程和有关先修课程知识,完成以单元操作为主的一次设计实践,是体察工程实际问题复杂性的初次尝试,是综合性和实践性都较强的学习环节。
2.通过课程设计,希望大家:①初步掌握化工单元操作设计的基本方法和程序;②学会查阅文献资料、搜集有关数据、正确选用公式;③培养理论联系实际的正确设计思想,学会综合运用已学过的理论知识去分析和解决工程问题;④培养准确而迅速地进行过程计算及主要设备的工艺设计计算的能力;⑤提高运用工程语言(简洁的文字、清晰的图表、正确的计算)表达设计思想和计算结果的能力。
---------------《化工原理》课程设计说明书设计题目学生姓名指导老师学院专业班级完成时间目录1.设计任务书……………………………………………()2.设计方案的确定与工艺流程的说明…………………()3.全塔物料衡算………………………………………()4.塔板数的确定………………………………………()5.精馏段操作工艺条件及相关物性数据的计算………()6.精馏段的汽液负荷计算………………………………()7.精馏段主要工艺结构尺寸的计算…………………()8.精馏段塔板的流体力学验算…………………………()9.精馏段塔板的汽液负荷性能图………………………()10.精馏段计算结果汇总…………………………………()11.设计评述………………………………………………()12.参考文献………………………………………………()13.附件……………………………………………………()附件1:附图1精馏工艺流程图附件2:附图2弓形降液管参数图附件3:附图2塔板布置图设计任务书一、设计题目:混合液板式精馏塔设计二、原始数据及操作条件:年处理量:万吨料液初温:35℃料液浓度:(苯的质量分率)塔顶产品浓度:96%(苯的质量分率)塔底釜液含甲苯量不低于98%(以质量计)每年实际生产天数300天(每年有两个月检修)精馏塔塔顶压强:4kPa(表压)压力:常压,单板压降不大于0.7kPa假定总板效率为:0.6设备型式:(选择浮阀塔或筛板塔)三、设计内容1、塔的工艺设计1)选择工艺流程和工艺条件:加料状态、塔顶蒸汽冷凝方式、塔釜加热方式等2)精馏工艺计算:物料衡算确定各物料流量和组成。
抽提蒸馏塔与再沸器的平面布置及管道设计
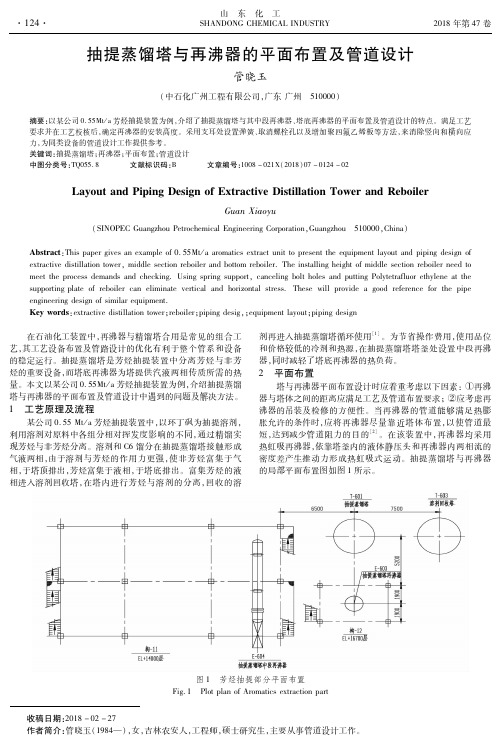
山 东 化 工 收稿日期:2018-02-27作者简介:管晓玉(1984—),女,吉林农安人,工程师,硕士研究生,主要从事管道设计工作。
抽提蒸馏塔与再沸器的平面布置及管道设计管晓玉(中石化广州工程有限公司,广东广州 510000)摘要:以某公司0.55Mt/a芳烃抽提装置为例,介绍了抽提蒸馏塔与其中段再沸器、塔底再沸器的平面布置及管道设计的特点。
满足工艺要求并在工艺校核后,确定再沸器的安装高度。
采用支耳处设置弹簧、取消螺栓孔以及增加聚四氟乙烯板等方法,来消除竖向和横向应力,为同类设备的管道设计工作提供参考。
关键词:抽提蒸馏塔;再沸器;平面布置;管道设计中图分类号:TQ055.8 文献标识码:B 文章编号:1008-021X(2018)07-0124-02LayoutandPipingDesignofExtractiveDistillationTowerandReboilerGuanXiaoyu(SINOPECGuangzhouPetrochemicalEngineeringCorporation,Guangzhou 510000,China)Abstract:Thispapergivesanexampleof0.55Mt/aaromaticsextractunittopresenttheequipmentlayoutandpipingdesignofextractivedistillationtower,middlesectionreboilerandbottomreboiler.Theinstallingheightofmiddlesectionreboilerneedtomeettheprocessdemandsandchecking.Usingspringsupport,cancelingboltholesandputtingPolytetrafluorethyleneatthesupportingplateofreboilercaneliminateverticalandhorizontalstress.Thesewillprovideagoodreferenceforthepipeengineeringdesignofsimilarequipment.Keywords:extractivedistillationtower;reboiler;pipingdesig,;equipmentlayout;pipingdesign 在石油化工装置中,再沸器与精馏塔合用是常见的组合工艺,其工艺设备布置及管路设计的优化有利于整个管系和设备的稳定运行。
蒸馏塔设备规范

塔设备设计、塔设备的结构设计塔设备在石油、化工等生产中,广泛用于精馏、吸收、萃取、气体增湿、离子交换等单元操作中。
虽然所进行的工艺过程(单元操作)各不相同,其结构形式各异但根据塔的内件结构可将塔设备划分为板式塔和填料塔两大类。
不论是板式塔还是填料塔,均由以下几部分组成:塔体由筒体、封头、联接法兰等组成。
内件由塔盘、填料及支承装置组成。
支座一般采用裙式支座。
附件包括人孔、手孔、各种接管、吊柱、操作台、扶梯、保温层等。
(一)板式塔图5-1 板式塔1 板式塔的总体结构及其分类板式塔的结构示意图如图5-1 所示。
板式塔的主体部分由塔体和裙座构成。
塔体和裙痤多采用钢板焊制。
裙座为上端与塔体底封头焊接在一起,下端通过地脚螺栓固定在基础上。
有的塔体需用铸钢制造时,采用以每层塔盘为一段,用法兰联接的形式。
板式塔的内件主要由多层塔盘组成。
各层塔盘的结构相同,由气液接触元件(如浮阀、筛孔、泡罩等)、塔盘板、溢流装置、降液管受液盘以及支承件、紧固件等元件组成。
一般塔盘间距相同。
开有人孔的塔盘间距较大,通常为700mm 。
最底一层塔盘到塔底的距离也比塔盘间距高,因为塔底空间起着贮槽的作用,保证料液有足够的储存,使塔底液体不致流空。
最高一层塔盘和塔项距离也高于塔盘间距,在这一段上往往装有除沫器。
塔盘结构有整块式和分块式两种。
采用形式与塔径大小有关,当直径小于700mm 的板式塔采用整块式塔盘,由于塔体分段,所以塔盘的安装可在塔外进行,塔体不需开设人孔。
当塔的直径大于700mm 时,应采用分块式塔盘,塔体上开设人孔,塔盘的装、拆可以在塔内进行。
按塔盘上气、液两相接触元件结构的不同,板式塔又可分为:泡罩塔、筛板塔、浮阀塔、舌形塔以及各种复合型塔。
目前,国内石油化工生产中使用较多的板式塔为筛板塔和浮阀塔。
1.整块式塔盘结构采用整块式塔盘的塔体是由若干塔节组成,各塔节之间用法兰联接,每个塔节安装一至数块塔盘。
根据塔盘的支承方式,整块式塔盘分为定距管式和重叠式两类。
分离苯—苯乙烯混合液的浮阀塔工艺设计

化工原理课程设计分离苯—苯乙烯混合液的浮阀塔工艺设计课程设计任务书苯-苯乙烯混合液的常压连续蒸馏塔设计一、工艺要求:日处理原料量80吨,一天按20小时工作时计算。
原料液中轻组分含量41%,要求塔顶馏出液中轻组分含量不低于96%,釜液中重组分含量不低于96%(以上均为质量含量)。
二、设计条件1、操作压力:常压2、进料热状况自选3、回流比自选三、塔板类型:浮阀塔设计任务1、精馏塔的物料衡算2、塔板数的确定3、精馏塔的工艺条件及有关数据的计算4、精馏塔的塔体工艺尺寸计算5、塔板主要工艺尺寸的计算6、塔板的流体力学验算7、塔板负荷性能图8、精馏塔接管尺寸计算9、绘制工艺流程图10、对设计过程的评述和有关问题的讨论目录第一部分概述1.1设计目标 (4)1.2设计任务 (4)1.3设计条件 (5)1.4设计内容 (5)1.5工艺流程图 (5)第二部分工艺设计计算一、设计方案的确定 (7)二、精馏塔的物料衡算 (7)2.1原料液及塔顶、塔底产品的摩尔分数 (7)2.2原料液及塔顶、塔底产品的平均摩尔质量和质量分数 (7)2.3物料衡算原料处理量 (7)三、塔板数的确定 (8)N的求取 (9)3.1理论板层数T3.2相对挥发度 (9)3.3进料状态参数 (9)3.4最小回流比 (9)四、精馏塔的工艺条件及有关物性数据的计算 (11)4.1操作压强计算 (11)4.2操作温度计算 (12)4.3平均摩尔质量计算 (12)4.4平均密度计算 (13)4.5液相平均表面张力计算 (14)五、精馏塔的塔体工艺尺寸计算 (15)5.1精馏段塔径的计算....................................... - 14 -5.2精馏塔的有效高度的计算 (17)六、塔板主要工艺尺寸的计算 (17)6.1溢流装置计算 (17)6.2塔板布置 (21)6.3筛孔数n与开孔率 (23)七、筛板的流体力学验算 (24)7.1气体通过干板压降....................................... - 23 -e的验算 (26)7.2雾沫夹带量V7.3液泛验算 (27)八、塔板负荷性能图 (28)8.1漏液线 (28)8.2雾沫夹带线 (29)8.3液相负荷下限线 (29)8.4液相负荷上限线 (30)8.5液泛线 (30)九、接头管设计 (33)9.1接管尺寸 (33)9.2回流管管径 (34)9.3塔底进气管 (34)9.4加料管管径 (34)9.5料液排出管管径 (34)十一、有关问题的讨论 (36)设计一览表 (38)操作方案的说明: (38)总结 (38)参考文献 (39)第一部分概述1.1设计目标分离苯与苯乙烯混合液的浮阀式精馏塔设计1.2设计任务日处理原料量80吨,一天按20小时工作时计算。
化工分离工程的案例教学
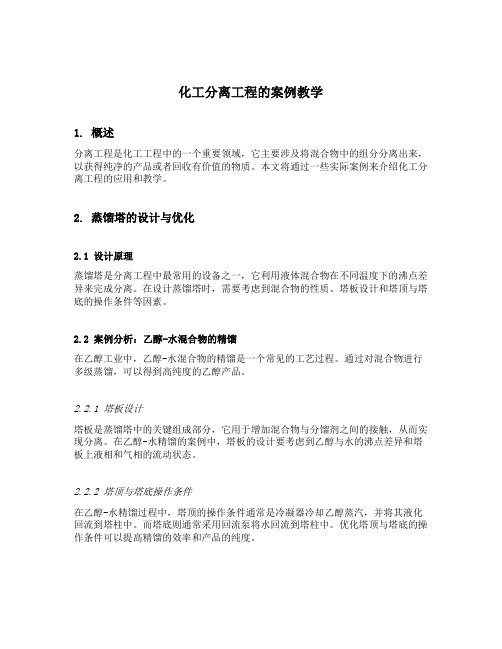
化工分离工程的案例教学1. 概述分离工程是化工工程中的一个重要领域,它主要涉及将混合物中的组分分离出来,以获得纯净的产品或者回收有价值的物质。
本文将通过一些实际案例来介绍化工分离工程的应用和教学。
2. 蒸馏塔的设计与优化2.1 设计原理蒸馏塔是分离工程中最常用的设备之一,它利用液体混合物在不同温度下的沸点差异来完成分离。
在设计蒸馏塔时,需要考虑到混合物的性质、塔板设计和塔顶与塔底的操作条件等因素。
2.2 案例分析:乙醇-水混合物的精馏在乙醇工业中,乙醇-水混合物的精馏是一个常见的工艺过程。
通过对混合物进行多级蒸馏,可以得到高纯度的乙醇产品。
2.2.1 塔板设计塔板是蒸馏塔中的关键组成部分,它用于增加混合物与分馏剂之间的接触,从而实现分离。
在乙醇-水精馏的案例中,塔板的设计要考虑到乙醇与水的沸点差异和塔板上液相和气相的流动状态。
2.2.2 塔顶与塔底操作条件在乙醇-水精馏过程中,塔顶的操作条件通常是冷凝器冷却乙醇蒸汽,并将其液化回流到塔柱中。
而塔底则通常采用回流泵将水回流到塔柱中。
优化塔顶与塔底的操作条件可以提高精馏的效率和产品的纯度。
2.3 优化策略蒸馏塔的设计与优化是一个复杂的过程,需要考虑多个因素。
在乙醇-水混合物精馏的案例中,常用的优化策略包括增加塔板数目、改善传热效果、调整进料位置等。
3. 萃取工艺的应用与优化3.1 工艺原理萃取是一种利用溶剂将混合物中的组分从原料相中分离出来的过程。
它广泛应用于化工工程中,可以用于分离有机物、金属离子等。
在萃取工艺中,选择合适的溶剂和工艺条件是关键。
3.2 案例分析:植物提取物的萃取植物提取物的萃取是化妆品、食品等工业中常见的工艺过程。
通过选择合适的溶剂和优化操作条件,可以提高产率和产品的纯度。
3.2.1 溶剂选择在植物提取物的萃取中,常用的溶剂包括乙醇、乙酸乙酯等。
需要考虑到溶剂的毒性、成本和环境影响等因素。
3.2.2 工艺优化优化植物提取物的萃取工艺可以提高产率和产品的质量。
- 1、下载文档前请自行甄别文档内容的完整性,平台不提供额外的编辑、内容补充、找答案等附加服务。
- 2、"仅部分预览"的文档,不可在线预览部分如存在完整性等问题,可反馈申请退款(可完整预览的文档不适用该条件!)。
- 3、如文档侵犯您的权益,请联系客服反馈,我们会尽快为您处理(人工客服工作时间:9:00-18:30)。
1.二.设计任务及操作条件1.设计任务:生产能力(进料量) : 2万吨/年操作周期: 300*24=7200 h进料组成: 41%塔顶产品组成: >96%塔底产品组成: >1%2.操作条件:操作压力: 4kpa (塔顶表压)进料热状态: 泡点进料单板压降: 不大于0.7kpa3.设备形式: 板式精馏塔,塔顶为全凝器,中间泡点进料,塔底间接蒸汽加热,连续精馏。
4.厂址: 齐齐哈尔市(二)设计内容二)设计内容1.概述:本次设计一筛板设计为例,筛板是在塔板上钻有均布的筛孔,上升气流经筛孔分散,鼓泡通过板上液层,形成气液密切接触的泡沫层.筛板塔的优点是结构简单,制造、维修方便,造价低,相同的条件下生产能力高于浮阀塔,塔板效率接近浮阀塔.他的缺点是操作范围小,小孔径筛板易堵噻不适宜处理粘性大的,脏的和带固体粒子的料液.但设计良好的筛板具有足够的造作弹性,对易引起堵塞的物系可采用大孔径筛板,故近年来我国对筛板的应用日益增多.2.设计流程的说明:精馏装置包括精馏塔,原料预热器,再沸器,冷凝器。
釜液冷却器和产品冷凝器等设备。
热量自塔釜输入,物料在塔内经多次部分汽化与与部分冷凝器进行精馏分离,由冷凝器和冷却器中的冷却介质将余热带走。
在此过程中,热能利用率很低,为此,在确定流程装置时应考虑余热的利用,注意节能。
另外,为保持塔的操作稳定性,流程中除用泵直接送入塔原料外,也可以采用高位槽送料以免受泵操作波动的影响塔顶冷凝装置根据生产状况以决定采用全凝器,以便于准确地控制回流比。
若后继装置使用气态物料,则宜用全分凝器。
总而言之确定流程时要较全面,合理的兼顾设备,操作费用操作控制及安全因素。
连续精馏操作流程图冷凝器再沸器3.操作条件:(1)操作条件精馏操作可在常压,减压和加压下进行,操作压强常取决于冷凝温度。
一般,性物以外,凡通过常压蒸馏不难实现分离要求,并能用江河或循环水将冷凝下来的系统,都应采用常压蒸馏,对热敏性物料或混合液沸点的系统则宜采用减压蒸馏;对常压下的馏出物的冷凝温度过低的系统,需要高塔压或采用深井水,冷冻盐水作为冷却剂;常压下呈现气态的物料必须采用加压蒸馏。
本次设计采用常压蒸馏。
(2)进料液状态的选择进料热状态以进料热状态参数q 表达,即q=每摩尔进料变成饱和蒸汽所需热量/每摩尔进料的汽化潜热有五种进料状态,当q>1时为低于泡点温度的冷凝进料进料;q=1时为泡点下的饱和液体进料;q=0为露点下的饱和蒸汽进料;1>q>0为介于泡点与露点间的汽液混合物进料;q<0为高于露点的过热蒸汽进料。
原则上,在供热量一定情况下,热量应尽可能的由塔底输入,使产生的气相回流在全塔发挥作用,即宜冷进料。
但为使塔的操作稳定,免受季节气温影响,精、提馏段采用相同的塔径以便于制造,则采用饱和液体(泡点)进料,但需增设原料预热器,若工艺要求减少塔釜加热避免釜温过高,料液产生聚合或结焦,则易采用气态进料。
本次设计采用泡点进料。
(3)加热方式蒸馏大多采用间接蒸汽加热,设置再沸器。
有时也采用直接蒸汽,例如蒸馏釜残主要组分是水,切在低浓度下轻组分的相对挥发较大时宜采用直接加热,其优点是可以利用压强较低的加热蒸汽以节省操作费用,并省掉间接加热设备。
但由于直接蒸汽的加入,对釜内溶液起一定稀释作用,在进料条件和产品纯度,轻组分收率一定的前提下,釜液浓度相应降低,故需在提馏段增加塔板以达到生产要求。
本次设计采用间接蒸汽加热。
(4)回流比的选择选择回流比,主要从经济观点出发,力求使设备操作费用之和最低。
一般经验值R=(1.1~2.0) Rmin其中R---操作回流比,Rmin-----最小回流比对特殊物系和与场合,则应根据实际需要选定回流比。
在进行课程设计时,也可以参同类生产的R经验值选定。
必要时选若干个R值,利用吉利兰图求出对应理论板数N,作出N---R曲线或N(R+1)---R曲线,从中找出适宜操作的回流比R。
也可以做出R对精馏塔操作费用的关系线,从中确定适宜回流比R。
本次设计因Rmin较小,故取R=2R。
4.操作方案说明:本设计任务为分离苯—甲苯混合物。
对于二元混合物的分离,应采用连续精馏流程。
设计中采用泡点进料,降原料液通过预热器加热至泡点后送入精馏塔内。
塔顶上升蒸汽采用全凝器冷凝。
冷凝器在泡点下一部分回流到塔内,其余部分经产品冷却器冷却后送入储罐。
该物系属于易分离物系,最小回流比较小,故操作回流比去最小回流比的两倍。
塔釜采用间接蒸汽加热,塔底产品冷却送到储罐。
设计操作流程图(三)本设计中符号说明英文字母:A0筛孔面积,㎡h0降液管底高度,mA a塔板开孔面积,㎡hσ相克服度mA f降液管面积,㎡k筛板的稳定系数A T 塔截面积,㎡L塔内下降液体流量,kmol/hC计算时u max的负荷因数l W溢流堰高度,mC O流量系数L S下降液体流率,m3/sD塔径,m N 理论板数d0 筛孔直径,mm N P实际塔板数E液流收缩系数N T理论塔板数E T 全塔效率n筛孔数e v 雾沫夹带量,kg液/kg气P操作压强,p a或kp aF 进料流量, kmol/h △P压强降,p a或kp aF a气相动能因数q 进料热状态承参数H 板间距,mm R回流比h c 与干板压降相当液柱高度,mS直接蒸汽量,kmol/hh1 进口堰与降液管的水平距离,m t筛孔中心距,mmh l 与气流穿过液层的压降相当液柱高度m u 空塔气速,m/sh f 板上鼓泡层高度,m u0 筛孔气速,m/sh L 板上液曾高度,m u′0降液管底隙处液体流速,m/sh d,与液体流经降液管压降相当液柱高度,mD F进料管直径, mD l回流管直径, mD W 釜液出口管直径, mD T 塔顶蒸汽管直径, m下标:h p 与单板压降相当液层高度,m A易挥发组分B难挥发组分h ow 堰上液层高度,m D馏出液h w 溢流堰长度,m L液相W釜残液流量,kmol/h h小时W C 无效区块度,mi组分序号W d 弓形降液管高度,m m平均w s安定区宽度,m F原料液X液相中易挥发组分摩尔分率min最小Y气相中易挥发组分摩尔分率max最大Z塔的有效高度,m n塔板序号v s塔内上升蒸汽流量,m3/s希腊字母:α相对挥发度,无因次β干筛孔流量系数的修正系数,无因次σ液体表面张力,mN/mδ筛板厚度,mmμ粘度,mP a.sψ液体密度校正系数φ开孔率t时间,sρL液相密度,kg/m3ρV液相密度,kg/m3(五)板数的确定1.苯甲苯属于理想物系,可以采用图解法求理论板层数。
1)由手册查得苯--甲苯物系的气液平衡数据,绘制图。
2)求最小回流比及操作回流比。
采用做图法求最小回流比。
在图中的对角线上,自点e(0.45,0.45)作垂线ef即为进料线(q线),该线与平衡线的交点坐标y q=0.667 ,x q=0.450,故最小回流比为R min=(x D-y q)/(y q-x q)=(0.966-0.667)÷(0.667-0.45)=1.38操作回流比为: R=2R min=2×1.38=2.763)求精馏塔的气,液相负荷L=RD=14.86×2.76=41.01kmol/hV=(R+1)D=(2.76+1)×14.86=55.87kmol/hL1=L+F=41.01+32.37=73.38kmol/hV=V1=55.87kmol/h4)求操作线方程精馏段的操作线方程:y=(L/V)x+(D/V)x D=(41.01/55.87)x+(1 4.86/55.87)0.966=0.734x+0.257提馏段的操作线方程为:y1=(L1/V1)X1+(W/V1)X W=(73.38/55.8 7)X1-(17.51/55.87)×0.012=1.131X1-0.004图解法求求理论板层数:采用图解法求理论层板,如图所示。
求解结果得为:总理论板数层数:N T=12.5(包括再沸器)进料板位置为:N F=62.实际板层数的求取=5/0.52=9.6精馏段实际板层数: N精≈10提馏段实际板层数: N提=7.5/0.52-1=13.42≈14(六)精馏塔的工艺条件及有关物性数据的计算1.操作压力的计算塔顶的操作压力:P D=101.3+4=105.3kp a每层塔板压降:△p=0.7kp a进料压力:P F=105.3+0.7×10=112.3kp a精馏段平均压力:P m=(105.3+112.3)/2=108.8kp a2.平均摩尔质量计算塔顶平均摩尔质量计算:由x D=y1=0.966,查平衡曲线如图所示可知:x1=0.916M VDm=0.966×78.11+(1-0.966)×92.13=78.59kg/kmolM LDm=0.916×78.11+(1-0.916)×92.13=79.29kg/kmol进料板平均摩尔质量的计算:由图解理论板如图所进料板平均摩尔质量计算示得:y F=0.604查平衡曲线如图所示得:x F=0.388 M VFm=0.604×78.11+(1-0.604)×92.13=83.66kg/kmolM LFm=0.388×78.11+(1-0.388)×92.13=86.69kg/kmol精馏段平均摩尔质量的计算:M Vm=(78.59+83.66)/2=81.13kg/kmol M Lm=(79.29+86.69)/2=82.99kg/kmol 3.操作温度得计算依据操作压力,由泡点方程通过试差法计算出泡点温度,其中苯,甲苯的饱和蒸汽压由安托尼方程计算可得:安托尼方程:㏒P*=A-(B/t+C) 【4】其中塔顶操作压力P D=105.3kp a 而进料板压力: P F=112.3kpa泡点方程公式:x A=(P D-p B*)÷(P A*-P B*)【1】设t=83℃而A,B,C由下表中得数据所取:组分A B C苯 6.023 1206.35220.24甲苯6.0781343.94219.58根据上述数据可以算出P A,*,P B*及因此可以求出塔顶温度和进料板温度精馏段平均温度:塔顶温度:t D=83℃进料板温度:t F=98.6℃精馏段平均温度:t m=(83+98.6)/2=90.35℃4.平均密度计算1)气相平均密度计算【3】:由理想状态方程计算公式:ρVm=P m M vm/RT m=(108.8×81.13 )÷[8.314×(90.35+273.15)]=2.92kg/m32)液相平均密度计算:由液相平均密度计算公式得:1/ρLm=∑a i/ρi则塔顶液相平均密度得计算:由t D=83℃,查表知:苯与甲苯的液相密度ρL参数表:温度80 90 100 110 120t℃ρ苯kg/m3 815 803.9792.5780.3768.9ρ甲苯kg/m3 810 800.2790.3780.3770.查的为:ρA=812.7kg/m3ρB=807.9kg/m3ρLDm=1÷[(0.903/812.7)+(1-0.96)/807.9]=812.5kg/m3进料板平均密度得计算:由t F=98.6℃查手册得知:ρA =794.1kg/m3, ρB=791.7kg/m3 进料板液相的质量分率:a A=(0.388×78.11)/[(0.388×78.11)+(1-0.388)92.13]=0.350ρLFm=1÷[(0.35/794.1)+(1-0.35)/791.7]=792.5kg/m3精馏段液相平均密度为:ρLm=(812.5+792.5)/2=802.5kg/m35.液体表面张力计算:液体平均密度表面张力由公式【3】:σLm=∑x iσi塔顶液相平均表面张力得计算:由t D=83℃, 查下表得知:液体表面张力σ温度t℃80 90 100 110 120σ苯, mN/m 21.2720.0618.8517.6616.49σ甲苯,mN/ m 21.6920.5919.9418.4117.31查得:σA =21.24 mN/m σB=21.42 mN/mσLDm=0.966×21.24+0.034)×21.42=21.25 mN/m进料板液相平均表面张力的计算:由t F=98.6℃,查手册得:σA =19.02 mN/mσB=20.03 mN/mσLFm= 0.388×19.02+(1-0.388)×20.03=19.64 mN/m精馏段液相平均表面张力为:σLm=(21.25+19.64)/2=20.45 mN/m 6.液体平均粘度计算:液相平均粘度公式【3】:㏒μLm=∑x i ㏒μi塔顶液相平均粘度得计算:由t D=83℃,查下表得知:液体的粘度μL温度t℃80 90 100 110 120μ苯,mP a.s 0.3080.2790.2550.2330.215μ甲苯,mP a.s 0.3110.2860.2640.2540.228μA =0.302 mP a.s μB=0.306 mP a.s㏒μLDm=0.966㏒(0.302)+0.034㏒(0.306) 解得:μLDm=0.302 mP a.s进料板液相平均粘度的计算:由t F=98.6℃查手册得:μA =0.258mP a.sμB=0.267 mP a.s ㏒μLFm=0.338㏒(0.258)+0.612㏒(0.267)解得:μLFm=0.263 mP a.s精馏段平均粘度的计算:μLm=(0.263+0.302)/2=0.283 mP a.s (七)精馏塔的塔体工艺尺寸计算:1.塔径的计算精馏塔得气,液相体积流率为:V S=VM Vm/3600ρVm=(55.87×81.13)/(3600×2.92)=0.431 m3/sL S=LM Lm/3600ρLm=(41.01×82.99)/(3600×802.5)=0.0012 m3/s由公式:u max=C[(ρL-ρV)/ ρV]1/2式中的由上述计算在图中所查取,图得横坐标为:L h/V h(ρLρV)1/2=[(0.0012×3600)/(0.431×3600)](802.5/2.92)1/2=0.0462取板间距H T=0.40m , 板上液层高度h L=0.06m则: H Th L=0.40-0.06=0.34m-查图可得:C20=0.072C=C20(σL/20)0.2=0.0723u max=0.0723×[(802.5-2.92)/2.92]1/2=1.196 m/s取安全系数为0.7,则空塔气速为:u=0.7u max=0.7×1.196=0.837 m/sD=(4V s/3.14u)1/2=[(4×0.431)/(3.14×0.837)]1/2=0.810 m按标准塔径圆整后为:D=1.0 m 则塔截面积为:A T=(3.14/4)D2=0.785 m2实际空塔气速为:u= V s / A T =0.431/0.785=0.549 m/s2.精馏塔有效高度的计算精馏段的有效高度为:Z 精=(N精-1)H T =(10-1)×0.4=3.6提馏段得有效高度为【1】:Z 提=(N 提-1)H T =(14-1)×0.4=5.2m在进料板上方开一人孔,其高度是0.8 m, 所以精馏塔的有效高度为: Z= Z 精+ Z 提+0.8=3.6+5.2+0.8=9.6 m(八) 塔板主要工艺尺寸的计算1.溢流装置的计算:因为塔径的直径D=1.0 m ,可以选用单溢流弓形降液管,采用凹形受液盘计算如下:a)堰长l w: 由于l w=(0.6~0.8)D(经验确定),取相应系数为0.66则l w=0.66D=0.66×1.0=0.66 m 【2】b)溢流堰高度h w【2】由公式可知:h w=h L-h ow应该选用平直堰上液层高度h ow,而:h ow=(2.84/1000)E(L h/l w)2/3则近似取E=1h ow=(2.84/1000)E(L h/l w)2/3=0.00284×1×[(0.0012×3600)/0.66]2/3=0.010m取板上清液层高度:h L=60 mm,则h w=(0.06-0.010)=0.05mc)弓形降液管宽度W d和截面积A f由公式l w/D=0.66 , 查图可得:A f/A T=0.0722, W d/D=0.124 则:A f=0.0722 A T=0.0722×0.785=0.0567㎡W d=0.124D=0.124×1.0=0.124 md)验算液体在降液管中停留的时间θ=3600 A f H T/L h=(3600×0.05670.04)/(0.0012×3600)=18.9 s由于18.9 s>5 s 所以降液管的设计是合理的。