轴承钢和帘线钢精炼渣系的比较(完成版)分析
第四章 精炼渣系选择

钢中的酸溶铝[Al]S不会还原渣中的(SiO2),这时(SiO2)不会成为供氧源。
钢铁冶金研究所&特殊钢冶金学术方向
各精炼渣系脱硫能力的比较
LF炉精炼过程的脱硫的热力学参数主要有钢水中的溶解氧 含量和渣中的 CaO 活度(即作用浓度)。脱硫的表达式为: (CaO) +[S] = (CaS) + [O]
<0.1 -
♣ 几个主要结构单元的作用浓度
结构单元 作用浓度 A B 山 阳 东北大学 CaO N1 0.1641 0.2348 0.3676 0.3495 SiO2 N2 0.0005 0.0005 0.0002 0.0001 Al2O3 N3 0.0102 0.0097 0.0084 0.0238 MgO N4 0.2162 0.1145 0.0468 0.0598 MgO· Al2O3 N10 - - - 0.0598
钢铁冶金研究所&特殊钢冶金学术方向
精炼渣系选择的实验
小盖 炉盖 发热体 炉管 耐火砖 精炼渣 石墨坩埚 MgO坩埚 钢水
实验渣系及结果
实验号 1# 2# 3# 4# 5# 6# 7# 8# CaO 45~50 54~57 50~60 50~55 45~50 55~60 45~50 50~55 SiO2 20~25 10~15 13~17 10~15 20~25 13~15 20~25 5~10 Al2O3 24~27 24~27 10~15 13~17 13~17 13~17 25~30 25~33 MgO 3~7 3~7 2~6 8~12 8~12 3~8 3~7 5~10 CaF2 0 0 0 5~10 3~8 5~10 0 0 R=(CaO/SiO2) 2 4 4 4.2 2.2 4.5 2 >5 T.O 0.002 0.0013 0.0016 0.0015 0.002 0.0011 0.0015 0.0011
精炼渣系对钢中夹杂物的影响
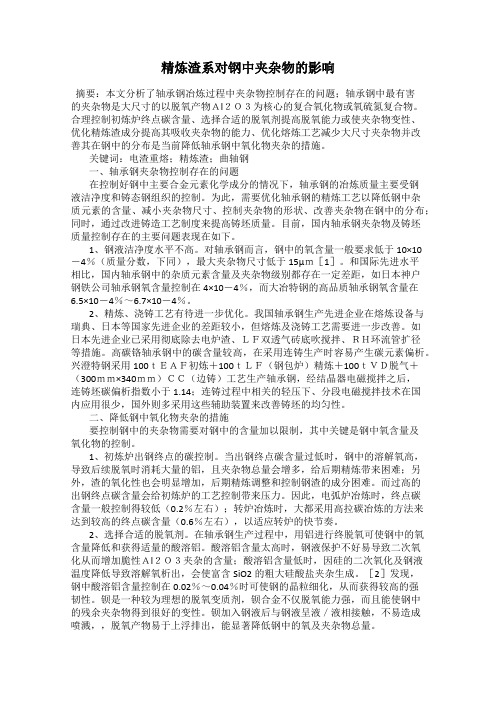
精炼渣系对钢中夹杂物的影响摘要:本文分析了轴承钢冶炼过程中夹杂物控制存在的问题;轴承钢中最有害的夹杂物是大尺寸的以脱氧产物Al2O3为核心的复合氧化物或氧硫氮复合物。
合理控制初炼炉终点碳含量、选择合适的脱氧剂提高脱氧能力或使夹杂物变性、优化精炼渣成分提高其吸收夹杂物的能力、优化熔炼工艺减少大尺寸夹杂物并改善其在钢中的分布是当前降低轴承钢中氧化物夹杂的措施。
关键词:电渣重熔;精炼渣;曲轴钢一、轴承钢夹杂物控制存在的问题在控制好钢中主要合金元素化学成分的情况下,轴承钢的冶炼质量主要受钢液洁净度和铸态钢组织的控制。
为此,需要优化轴承钢的精炼工艺以降低钢中杂质元素的含量、减小夹杂物尺寸、控制夹杂物的形状、改善夹杂物在钢中的分布;同时,通过改进铸造工艺制度来提高铸坯质量。
目前,国内轴承钢夹杂物及铸坯质量控制存在的主要问题表现在如下。
1、钢液洁净度水平不高。
对轴承钢而言,钢中的氧含量一般要求低于10×10-4%(质量分数,下同),最大夹杂物尺寸低于15μm[1]。
和国际先进水平相比,国内轴承钢中的杂质元素含量及夹杂物级别都存在一定差距,如日本神户钢铁公司轴承钢氧含量控制在4×10-4%,而大冶特钢的高品质轴承钢氧含量在6.5×10-4%~6.7×10-4%。
2、精炼、浇铸工艺有待进一步优化。
我国轴承钢生产先进企业在熔炼设备与瑞典、日本等国家先进企业的差距较小,但熔炼及浇铸工艺需要进一步改善。
如日本先进企业已采用彻底除去电炉渣、LF双透气砖底吹搅拌、RH环流管扩径等措施。
高碳铬轴承钢中的碳含量较高,在采用连铸生产时容易产生碳元素偏析。
兴澄特钢采用100tEAF初炼+100tLF(钢包炉)精炼+100tVD脱气+(300mm×340mm)CC(边铸)工艺生产轴承钢,经结晶器电磁搅拌之后,连铸坯碳偏析指数小于1.14;连铸过程中相关的轻压下、分段电磁搅拌技术在国内应用很少,国外则多采用这些辅助装置来改善铸坯的均匀性。
轴承钢牌号、化学成分及标准对比

调研报告容:1、概述〔研究目的与意义〕2、该产品研究国外研究与开展现状(开展过程、现状与开展前景)3、技术、市场分析〔重点介绍〕3.1 国生产现状〔包括主要生产厂家、各厂家生产该产品采用的生产工艺流程、生产设备、关键技术、生产规格、执行标准或技术条件、产品产量和质量状况、现有与潜在用户、市场占有情况等〕〔重点介绍〕3.2市场分析〔包括现有和潜在市场容量、产品规格、售价、利润情况、主要品种、主要目标用户与加工工艺、技术质量要求等〕〔重点介绍〕4、可行性分析莱钢开发生产该产品的必要性和可行性分析〔主要分析莱钢现有装备和工艺条件是否满足、产品利润预测等〕5、其它:特殊要求品种需要介绍一下钢种定义、性能特点、主要用途、用户个性化要求等〕1、概述〔研究目的与意义〕作为合金钢的一种,轴承钢包括高碳铬轴承钢、渗碳轴承钢、高温轴承钢、不锈轴承钢与特殊工况条件下应用的特殊轴承钢。
目前,我国轴承钢总产量已达220万t左右,其中高碳铬轴承钢约占轴承钢总产量的90%以上。
轴承钢是所有合金钢中质量要求最严格、检验项目最多、生产难度最大的钢种之一,主要用于制造滚动轴承。
世界公认轴承钢的生产水平是一个国家冶金水平的标志。
对于一个企业来说,轴承钢的生产水平也是一个企业冶金水平的标志,纵观国际与国的知名特钢生产企业,无一不将轴承钢特别是高标准轴承钢作为其产品调整、开展战略的一个重要目标。
我国的一些知名特钢生产企业如:兴澄特钢、东北特钢、宝钢特钢生产的轴承钢具有品质高〔通过国际知名轴承公司SKF、FAG、Timken认证〕,产量大〔年产量根本维持在30-50万吨的水平〕等特点。
莱钢特钢作为一个老牌特钢生产企业,目前轴承钢生产只能按国标准生产,档次低、品种单一、产量低〔年产量在1万吨左右〕,与国际、国的知名特钢生产企业相比差距明显。
根据现有装备和生产水平,开发高品质轴承钢,并适当扩大产量不仅对于进一步调整、优化企业产品结构,提高莱钢特钢产品的附加值与经济效益,增强市场竞争能力具有重要意义,而且有利于提升企业的知名度。
典型钢种炉外精炼
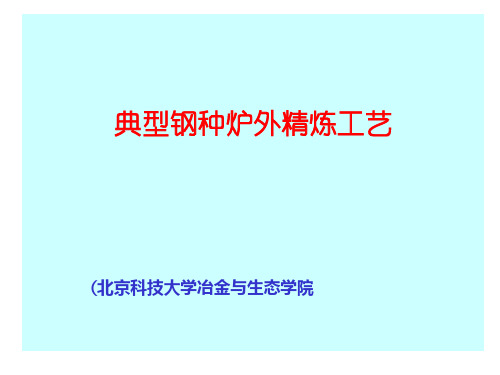
(2)影响钢中铝含量波动的因素。
转炉终点控制:终点碳含量的高低和终点命中
率。
下渣量和终渣的氧化性:不同的炉次,不同的
转炉操作水平差别很大。 6(FeO)+4[Al]=2(Al2O3)+6[Fe] LF炉操作工艺:气氛控制、搅拌剧烈程度、炉 渣流动性、温度高低、精炼时间长短等。
4.连铸容易结瘤,影响连浇。
(1)影响水口结瘤的主要因素之一是钢液中Al2O3夹杂物量的多 少,最大限度去除Al2O3夹杂是最有效的办法,事实也证明大
量的Al镇静钢并不需要用Ca处理。
(2)Ca的加入量主要决定于钢液中Al2O3夹杂物的量,习惯上 用Ca/Al(s), Ca/Al(t), Al(s)/Al(t)来衡量钢液中需要加入的钙量 仅适用在某一特定工况条件下的经验公式,并不十分科学。用 Ca/T[O]可能更为合理一些。
a Al 2O 3 K 2 3 a Al aO
aO a Al 2O 3 /( K a )
3 2 Al
炉渣成分对钢中氧含量的影响
Si脱氧: [Si] + 2[O] = (SiO2)
aSiO2 K Si 2 aSi aO
aO aSiO2 /( K Si aSi )
MnO-Al2O3-SiO2渣系相图
精炼工艺特点:
夹杂物总量要低:夹杂物生成早;容易上浮;容易被顶渣吸 收。采用铝脱氧;高碱度造渣。
D类夹杂物(钙、镁铝酸盐,TiN)几乎没有:极低的钙含量;合 适的镁含量;极低的钛、氮含量;合理的炉渣碱度。 大颗粒夹杂:查明大颗粒夹杂物的性质和类型,分析其来源, 找出去除措施。
(2)高硫易切削非调质钢
CaO-Al2O3-SiO2渣系等硫容量图
2.高洁净度-炉渣吸附Al2O3夹杂物
“钢中之王”——轴承钢生产难点解析
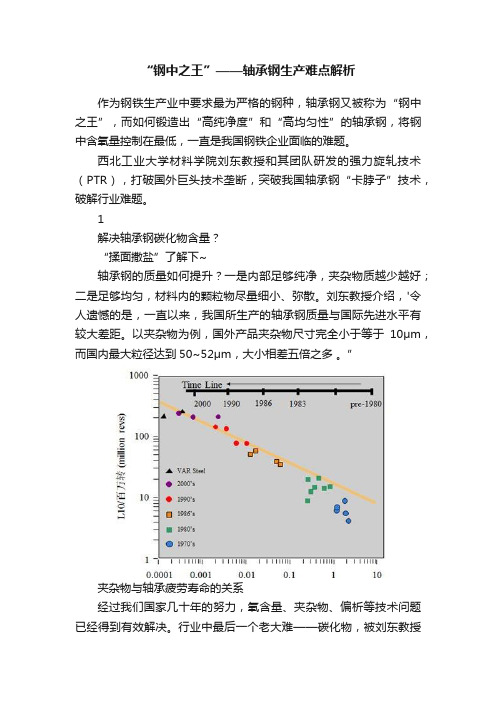
“钢中之王”——轴承钢生产难点解析作为钢铁生产业中要求最为严格的钢种,轴承钢又被称为“钢中之王”,而如何锻造出“高纯净度”和“高均匀性”的轴承钢,将钢中含氧量控制在最低,一直是我国钢铁企业面临的难题。
西北工业大学材料学院刘东教授和其团队研发的强力旋轧技术(PTR),打破国外巨头技术垄断,突破我国轴承钢“卡脖子”技术,破解行业难题。
1解决轴承钢碳化物含量?“揉面撒盐”了解下~轴承钢的质量如何提升?一是内部足够纯净,夹杂物质越少越好;二是足够均匀,材料内的颗粒物尽量细小、弥散。
刘东教授介绍,'令人遗憾的是,一直以来,我国所生产的轴承钢质量与国际先进水平有较大差距。
以夹杂物为例,国外产品夹杂物尺寸完全小于等于10μm,而国内最大粒径达到50~52μm,大小相差五倍之多。
”夹杂物与轴承疲劳寿命的关系经过我们国家几十年的努力,氧含量、夹杂物、偏析等技术问题已经得到有效解决。
行业中最后一个老大难——碳化物,被刘东教授团队攻克。
轴承钢属于高碳钢,其含碳量在所有钢中比较高。
如果碳化物分布不均匀且呈大块状,就会严重影响质量。
刘东教授解释说“就像揉面的时候撒了一把盐,要是面没有揉碎揉匀,那么面里就都是又咸又硬的疙瘩。
”“让盐更细小均匀的分布在面里”就是刘东教授和团队追求的目标。
目前,通过PTR技术改性后的轴承钢已在多个项目中得到运用。
实验室数据显示,运用强力旋轧(PTR)技术,晶粒尺寸由原来的50μm细化至10μm,碳化物尺寸仅为原先的1/10。
首次将100年来,一直徘徊在600~700HV的GCr15轴承钢硬度提高至900HV以上,处于世界顶尖水平。
除此以外,采用该技术后轴承寿命和可靠性得到大幅度提高,平均寿命达到计算寿命的26倍,可靠性达99.9%。
但是,在轴承钢领域,如何缩短与国外技术的差距,我们还有很长的路要走。
2铁姆肯如何提高纯度轴承钢的核心问题是提高纯净度,首先要做的就是控制钢中的氧含量,炼钢中用ppm(每百万分之一)来作为氧含量的单位,一般来说8个ppm的钢就属于好钢,而高端轴承所需要的则是5个ppm的顶级钢。
轴承钢用精炼渣冶金性能分析

过程 中精炼渣 的碱度 和脱硫效果 进行 分析。结果表明 : 在精炼过程 中, C a O含量基本不变 , S i O : 的含量略有减少 , 而A 1 O 含 量稍 有增加 ; 整个精 炼过程 中, 碱度 逐渐升高 , 在精炼结束后 , 终渣碱度维持 在4 . 5 — 5 . O ; 在 吨钢用量 9 . 3 1 k g 合成渣和 2 . 7 9 k g 埋弧渣的条件下 , 精炼渣脱 硫率达 到 8 0 %; C a O — S i O 一 A 1 O , 精炼渣系能够较好地去除钢中游离氧及 氧化物夹杂 , 钢材 的全 氧含量低于 1 2 ×1 0 。 关键词 : 轴承钢 ; 精炼渣 ; 组分 ; 碱度 ; 脱硫率
2 . 1 精炼渣 组成
传统 的轴 承 钢精 炼渣 系 主要是 以 C a O — A 1 0 和 C a O — S i O 一 A 1 : 0 , 的 高 碱 度 精 炼 渣 系 为 主 。 由
C a O — A 1 0 , 二元相 图可知 : 渣 中存在 低熔点 的化合物 1 2 C a O・ 7 A 1 : O n , 可 通过调 节精 炼渣 中 A 1 : O , 含 量 降
轴 承钢 的使 用性 能 。本研究 系统地 讨论精 炼渣 成
高质 量 的轴 承钢要 求 高 的纯 净度 和组 织均 匀 , 即杂质 元素 和非 金属 夹杂 少 , 碳 化 物细小 且分 布均 匀 。精 炼渣 具有 脱氧 、 脱硫 、 去 夹杂 的作 用 , 其 性质 直接影响L F 精 炼过 程 的冶金 效 果 。当碱 性还 原渣 同钢 液 密切 接 触 时 , 钢 液 中实 际 的 氧 、 硫 的数 值 大 于 同渣 平衡 的氧 、 硫 的数值 , 使 钢液 中的 氧 和硫 向 渣 中扩 散 …; 精炼渣中 C a O、 A 1 0 , 等 成 分 能够 与 S i 、 A 1 、 M n 等 的脱 氧 产物 结合 成低 熔 点 的化合 物 , 从 而 降低 脱 氧 产物 的活 度 , 强 化脱 氧 反应 ; 由于精 炼 渣
精炼渣成分控制

化学成分帘线钢要求控制的化学元素较多,表3列出了国内72, 82帘线钢盘条化学成分要求。
表3只是基本标准,各企业内控各不相同,但实际控制水平均要比表3严格的多。
国内钢厂大多在C,Mn,Si,O等成分的控制上一般没有问题,但在S,P,Al等元素的控制上虽然能达到基本标准,但控制水平大多偏低,同国外相比还有一定差距,这也是制约我国帘线钢水平上一个台阶的重要因素。
夹杂物国际上对帘线钢夹杂物要求常用的是意大利的皮拉利标准,要求夹杂物数量<1000个/cm³,尺寸<15 微米,高强度帘线钢要求夹杂物直径小于钢丝直径的2%;允许有纯Al203夹杂物存在,复合夹杂物中A1203含量≤50%,因铝酸钙类夹杂物无可塑性,也不允许存在。
国内对夹杂物要求一般采用评级的方式,要求塑性夹杂A类、C类≤1级,脆性夹杂B类、D类≤0。
5级。
因此,为了保证钢帘线产品质量,盘条金相组织中索氏体含量≥85%,不得有M、B、网状渗碳体等有害组织,表面脱碳层≤0.08 mm。
力学性能方面,72级帘线钢要求抗拉强度(1050士90) MPa,断面收缩率≥35%,82级要求抗拉强度(1150士90)MPa,断面收缩率≥300%。
非金属夹杂物控制造成帘线钢在拉拔或合股过程中断裂的最重要因素之一就是钢中非金属夹杂物 ,特别是硬质、不变形夹杂物 ,如Al2O3 和(Mg、Mn)O ·Al2 O3 ,对高强度帘线钢的影响更为突出 ,因此在生产高强度帘线钢时,采用洁净钢、超洁净钢冶炼技术就显得十分必要。
帘线钢炉外精炼的目的就是合理控制顶渣成分 ,通过钢渣界面反应来最大限度地减少有害夹杂物的影响 ,并对钢中夹杂物的形态、数量和大小进行有效控制是帘线钢生产的关键性环节。
夹杂物目标化学成分帘线钢中的夹杂物主要有两种类型 ,一种是来自于炉渣的 CaO-SiO2-Al2O3系夹杂物 ,另一种是来自于脱氧产物的 SiO2-MnO2-Al2O3系夹杂物。
钢包炉_LF_精炼用渣的功能和配制

Si2Fe 脱氧剂 ,净化钢液
脱氧剂 ,脱硫剂 ,脱硫生成高熔点稀土硫化物几乎不 RE 回硫 ,并能提高粉剂重度
CaC2 脱氧剂 ,其脱氧产物使熔渣前期发泡 SiC 脱氧剂 ,其脱氧产物使熔渣前期发泡
C 脱氧剂 ,其脱氧产物使熔渣前期发泡
Al2O3 ] (s) + 2Π3X[Al ] 生成的铝酸盐夹杂浮出钢液 ,达到 Al2O3 变 性处理的目的 。
精炼渣的脱硫反应受渣中 FeO + MnO 含量的 影响很大 ,它与硫分配常数 K 的关系见图 3[3] ,因 此 ,精炼渣中 MnO 、FeO 要尽量的低 。
配制精炼渣常用的基础渣原料 、脱硫剂 、发泡 剂 、还原剂 、助熔剂及其作用见表 1 。 精炼渣通常有粉剂和颗粒状剂 。粉剂多为机 械混合物 ,使用过程中粉尘大 。颗粒状剂加入钢 包时 ,不会产生粉尘飞扬而污染环境和使物料损 失 。另外 ,颗粒状物料流动性好 ,可以迅速在钢水 表面形成覆盖层 。目前有的连铸生产线 LF 精炼 时间不允许太长 ,为了使精炼渣加入钢包后快速 均匀熔化 ,以缩短精炼时间 ,也常常采用预熔型精 炼渣 ,但成本有所提高 。
1996. 68 2 袁伟霞 ,等. LF 炉埋弧渣的开发及应用研究. 中国金属学会炼
钢学会编. 第九届全国炼钢学术会议论文集 ,1996 ,11 ,423 3 张 鉴. 炉 外 精 炼 的 理 论 与 实 践. 北 京 : 冶 金 工 业 出 版 社 ,
1993. 532 4 金振坚 ,等. 钙合金及其合成渣用于镇静钢的脱氧. 中国稀土
学院冶金系 ,从事铸造 、连铸保护渣 、电渣研究 ,曾获多项 国家和部级奖励及国家发明专利 。
- 1、下载文档前请自行甄别文档内容的完整性,平台不提供额外的编辑、内容补充、找答案等附加服务。
- 2、"仅部分预览"的文档,不可在线预览部分如存在完整性等问题,可反馈申请退款(可完整预览的文档不适用该条件!)。
- 3、如文档侵犯您的权益,请联系客服反馈,我们会尽快为您处理(人工客服工作时间:9:00-18:30)。
轴承钢和帘线钢冶炼精炼渣系研究一、轴承钢1、轴承钢相关背景轴承用钢包括高碳铬轴承钢、渗碳轴承钢、高温轴承钢、不锈轴承钢及特殊工况条件下应用的特种轴承钢等。
其中尤以高碳铬轴承钢生产量为最多。
含C1.O %、Cr 1.5%的高碳铬轴承钢是轴承钢的代表品种。
自本世纪初问世以来,已有近100年的历史,从它诞生至今,化学元素的古最几乎没有变化,但其疲劳寿命却有成倍甚至成几十倍的提高,原因主要就在于近些年冶金工艺的现代化、炉外精炼技术的普遍采用,使得轴承材料的纯净度不断提高。
在合金钢领域内,轴承钢是检验项目最多、质量要求最严、生产难度最大的钢种之一。
衡量轴承钢的冶金质量,一般从三个方面着眼, 是纯净度,即钢中夹杂物的含量;二是碳化物不均匀性;三是钢材的尺寸精度、表向裂纹和脱碳[1]。
2、轴承钢精炼渣处理精炼渣处理钢液是应用最广泛的精炼手段之一,几乎所有的精炼设备工艺都会采用精炼渣处理钢液。
在钢液的精炼过程中,精炼渣一方面吸收上浮的夹杂物从而减少夹杂物总量,另一方面由于精炼渣-钢-夹杂物三者之间的互相影响精炼渣还有夹杂物改质的作用。
根据不同的方法精炼渣有很多种分类,但一般都是依据二元碱度将精炼渣分为高碱度精炼渣和低碱度精炼渣。
在轴承钢的冶炼中,由于对质量的不同需求和初炼钢水状况的不同形成了高碱度渣精炼和低碱度渣精炼两种工艺路线[2]。
2.1、高碱度渣精炼工艺高碱度渣精炼工艺即控制精炼渣中碱度R>4.0,总铁含量≤1.0%。
这种精炼工艺的精炼渣系有很强的脱硫能力,能够生产超低硫系列的轴承钢。
而且具有很高的脱氧能力,能够吸附大量Al 2O 3夹杂物,因此在轴承钢中几乎就没有氧化物夹杂物。
但是精炼渣中Ca0含量高,加上精炼普遍采用铝作为脱氧剂,因此极易被铝还原生成球形夹杂物对轴承钢的质量危害很大。
因此,在采用高碱度精炼渣精炼轴承钢时,要严格控制铝脱氧剂的用量,最大程度地避免球形夹杂物的形成。
(1)日本各轴承钢生产厂家大都采用高碱度渣精炼,其中以山阳特殊制钢公司取得的效果最为瞩目,硫质量分数降到0.002%-0.003%,全氧质量分数达到平均5.4× 10−6,个别炉次甚至达到了3 ×10−6。
山阳公司采用高碱度渣精炼工艺将钢液中的全氧质量分数降到了极低的程度,钢中B 类夹杂物几乎不存在了,但是D 类夹杂物的数量却较多,平均达到了0.9级。
(2)莱钢公司[3]为了降低钢中全氧质量分数,提高GCrI 5钢质量,在LF 精炼过程中采用了碱度4~5的高碱度精炼渣,取得了良好的效果,全氧质量分数由平均11 ×10−6降到7.9×10−6。
应该注意到,高碱度精炼渣虽然在脱硫和降低全氧质量分数上取得了很好的效果,但却增加了钢中的球状不变形夹杂物。
在轴承钢的冶炼中,选择一种适当成分的精炼渣,主要达到三个目的:(1)一定的脱硫能力,使轴承钢中的A 类夹杂物控制在一定范围;(2)吸收Al 2O 3夹杂物的能力,以最大限度地降低氧化物夹杂数量;(3)减少或消除含Ca0的D 类夹杂物。
高碱度精炼渣虽然很好地达到了前两个目的,但却导致了球状夹杂物出现率升高,没能达到第三个目的。
为了获得优良的综合效果,近些年国内的科研院所和高校以及主要的轴承钢生产厂家在精炼渣方面做了大量地研究工作。
2.2低碱度渣精炼工艺低碱度渣精炼工艺是控制渣中碱度R ≥1.2,总铁含量≤1.0%。
这种精炼工艺的精炼渣渣系虽然能够消除含Ca0的D 类球形夹杂物,也能够对Al 2O 3夹杂物有一定的吸附能力。
但是轴承钢中的氧含量是处在一个相对较高的水平,不利于脱硫反应,虽然能改变轴承钢中夹杂物的形态,大幅度提高塑性夹杂物的比例,但是夹杂物的数量并没有因此减少。
(1)大冶钢厂采用低碱度渣一吹氢精炼工艺,取得了良好的效果。
生产实践证实,在这种低碱度渣下精炼,进入钢液中的钙质量分数一般不会超过20×10−6,不足以形成低熔点的球状钙铝酸盐夹杂物[4、5、6]。
(2)本钢采用低碱度的Ca0-Al 2O 3渣系进行顶渣处理,脱硫率达50%-70%,脱氧50%,同时消除了含Ca0的D 类夹杂物[7]。
(3)ASEA-SKF 钢包炉精炼轴承钢时采用中性渣(w(Ca0): w(Al 2O 3):w(SiO 2)=1: 1: 1).它既能有效地吸收夹杂物,又不会侵蚀包壁。
用该渣系精炼的轴承钢,硫质量分数平均在0.020%,钢中不存在G, D 两类夹杂物,B 类夹杂物的数量也很少。
(4)北满特钢先后采用两种(低碱度、高碱度)精炼渣生产,文献[8]分析了两种渣系对轴承钢的氧及夹杂物含量的影响。
研究表明:轴承钢GCr15精炼渣的碱度从2.5提高到5~6,渣中Al 2O 3保持在18%~22%,,高碱度渣脱硫能力比低碱度渣提高30%~50%, 而渣中MgO 低2%~5%, 高碱度渣对钢包的侵蚀速度降低; 改进后渣系冶炼的轴承钢中氧、B 、D 类夹杂物含量明显降低, 硫、A 类夹杂物含量略有下降, 达到SKF 标准。
采用低硅质造渣材料, 进一步降低渣中SiO 2的含量, 提高渣中Al 2O 3的含量, 提高渣的碱度, 降低轴承钢的氧和夹杂物含量。
2.3新型轴承钢精炼渣的研究在精炼渣中加入少量Na 20 ( O 增加到0.3%-0.4%)时,精炼渣的硫容量是原来的3倍多。
由此可见,Na 20能大大提高精炼渣的脱硫能力[9]。
相关文献[10]认为在高碱度炉渣中,Na 20对炉渣的硫容量有十分明显的影响;在低碱度炉渣中,Na 20对炉渣的硫容量影响不大。
由为Na 20在1600 0C 下不稳定,所以其在精炼渣中的影响需要进一步探索研究. 为了提高脱硫效果,同时消除钢中点状不定形夹杂物。
对精炼渣进行改质处理也是优化精炼渣的一种比较可行的手段[11]。
本溪钢铁厂经过对LF 精炼渣的改质处理生产出了的低硫含量的钢。
目前,开发具有低熔化温度、高硫容量的精炼渣成为精炼渣优化的新趋势。
北京科技大学对在精炼渣添加Ba0进行了研究认为:当精炼渣中的Ba0添加量到达50%时,其硫容量为只加入Ca0时的两倍[12]。
另外,无氟精炼渣也是新型精炼渣的一种,由于无氟精炼渣中没有Ca F2,能够减轻侵蚀钢包的包衬和减少对环境的污染,也同样很受欢迎。
3、我国轴承钢生产发现的主要问题是[13]:(1)钢材表面缺陷:材料裂纹、折叠裂纹、麻点(坑)、夹渣、异金属夹杂、表面脱碳、发纹。
(2)钢材低倍缺陷:缩孔(管)残余、翻皮、疏松、气泡、偏析、白点、显微孔隙、内裂。
(3)非金属夹杂物:点状夹杂物、塑性硅酸盐夹杂物。
(4)碳化物不均匀:碳化物带状、液析、网状;退火组织不均匀。
这些缺陷都严重影响轴承的寿命和可靠性。
从对轴承生产企业轴承钢进厂检验和在使用中发现的问题的调查研究情况来看,国产轴承钢缺陷出现频率最高的依次是:材料表面裂纹、缩孔、碳化物液析、碳化物网状、内裂、表面脱碳、碳化物带状、退火组织不合格。
4、通过与国外先进轴承钢生产工艺对比可知,国内外生产工艺的特点如下[14、15]:(1)为提高钢液洁净度和精炼效果,国外电炉采用无渣出钢技术,转炉初炼在钢包中进行真空除渣或炉后扒渣,以降低磷质量分数和防止氧化渣进入精炼炉,而我国轴承钢冶炼大多数只采用电炉偏心底出钢技术;(2)国外轴承钢精炼在采用LF精炼基础上,进行RH真空脱气处理,在提高洁净度的基础上特别注意夹杂物的控制,而国内大多数只有LF+VD精炼,但从脱氮、脱氢效果分析,VD效果远不如RH;(3)国内铸坯断面、连铸机弧半径仍与国外先进企业有一定差距,国外有先进的连铸工艺和完善的精整热处理装备;(4)国外先进轴承钢生产厂家如山阳、神户、大同等公司采用多级电磁搅拌改善铸坯质量;而国内大多数只有结晶器电磁搅拌,只有个别厂家配有末端电磁搅拌;(5)为解决高质量轴承钢的偏析问题,国外采用轻压下、大直径辊强压下和连续锻压等液相高压下技术,而国内采用轻压下很少;(6)国外大量使用转炉流程生产轴承钢,国内则绝大部分轴承钢为电炉流程生产。
综上,虽然我国的轴承钢冶炼水平较过去取得了一些进步,但是与国外高水平轴承钢厂商相比,仍然有着不小的差距。
冶炼水平和装备水平的差距导致了与国际先进水平相比,我国轴承钢产品的实物质量仍然有一定的差距,我国轴承钢纯净度、碳化物均匀性、钢材尺寸精度和表面质量和品种结构上均落后于国外先进水平.二、帘线钢1、帘线钢相关背景帘线钢是轮胎子午线增强骨架的主要用钢,由于公路运输的发展,特别是高速公路的发展,乘用车的高速化,运输车辆的高速、重载和大型化,对配套用钢丝子午胎提出了十分严格的要求,同时由于帘线用盘条(也5~5.5 mm)需拉拔成直径为0.15—0.38 mm的细丝,随后经过高速双捻机合股成绳,整个过程中断丝率小于1次/100 km。
因此对于线材组织及成分的均匀性、纯净度以及综合质量有着极为严格的要求,尤其是对夹杂物的类型和形态。
2、帘线钢的质量要求帘线钢是一种对于强度和性能有着极高要求的优质钢种,在其生产的过程中也有着许多特别的、相对严格的要求,对于拉拔出的非常细的钢丝产品要进行绞合成股,并且在这些过程中几乎不允许出现钢丝断裂的情况。
因此,在生产过程中,对于钢中的化学成分,夹杂物以及连铸坯表面和内在质量都有着如下的要求:(1)化学成分帘线钢对于化学成分的要求必须是均匀的,碳、锰、硅含量波动不能太大,对于硫、磷以及其他微量元素也有着严格的要求,帘线钢化学成分的控制要求.(2)夹杂物控制夹杂物的控制是控制帘线钢产品性能的关键。
在帘线钢的研发中,对于断面出现的夹杂物进行分析,发现引起拉拔断丝的夹杂物主要是以Al2O3为主的高硬度脆性夹杂物。
Al2O3的来源主要分为从钢水中脱氧产生和耐火材料带入两种情况。
第一种情况,可以通过调整炉渣成分,从而有效的调整夹杂物成分使之成为延伸性很高的塑性夹杂物,使之无害化;第二种情况,可以选取最佳的耐火材料来减少其来源,从而降低源于耐火材料夹杂的断丝。
(3)中心偏析帘线钢对于碳的中心偏析有着一定的要求,一般要求碳中心偏析指数<1很多在拉丝和扭转中发生的断裂都是由偏析造成的内部质量和性能不均匀引起。
因此,在帘线钢进行连铸浇铸的过程中,对于钢水成分、温度、二冷参数等指标要采取相应的措施进行严格控制。
(4)表面质量及内部缺陷帘线钢铸坯表面的质量要求有着严格的规定,表面不能够存在针眼、凹坑、结疤、微小夹杂物和裂纹,如有细小裂纹深度应小于0.3 mm。
铸坯内部不能有缩孔。
(5)金相组织及晶粒度钢帘线对于力学性能和冷加工性能有着极高的要求,要想达到这些要求,必须满足整个线材的横截面的显微组织是均匀一致的索氏体组织。
在截面出现不规则的晶粒组织、贝氏体等都会对后续加工产生负面影响。