电液控制(第6章 电液伺服控制系统)
电液伺服系统
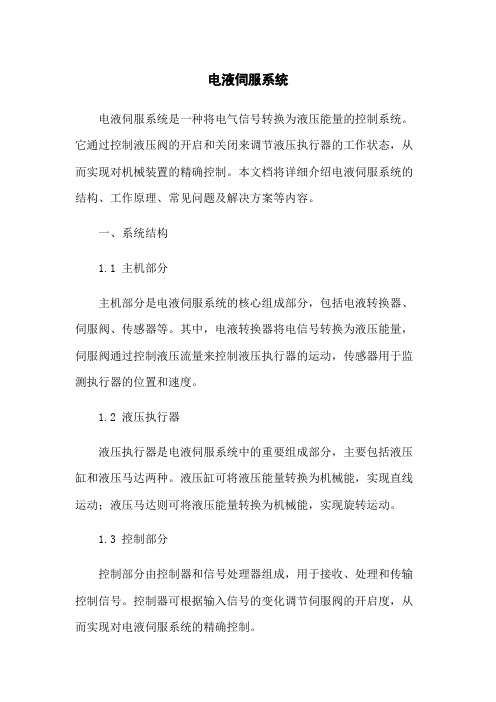
电液伺服系统电液伺服系统是一种将电气信号转换为液压能量的控制系统。
它通过控制液压阀的开启和关闭来调节液压执行器的工作状态,从而实现对机械装置的精确控制。
本文档将详细介绍电液伺服系统的结构、工作原理、常见问题及解决方案等内容。
一、系统结构1.1 主机部分主机部分是电液伺服系统的核心组成部分,包括电液转换器、伺服阀、传感器等。
其中,电液转换器将电信号转换为液压能量,伺服阀通过控制液压流量来控制液压执行器的运动,传感器用于监测执行器的位置和速度。
1.2 液压执行器液压执行器是电液伺服系统中的重要组成部分,主要包括液压缸和液压马达两种。
液压缸可将液压能量转换为机械能,实现直线运动;液压马达则可将液压能量转换为机械能,实现旋转运动。
1.3 控制部分控制部分由控制器和信号处理器组成,用于接收、处理和传输控制信号。
控制器可根据输入信号的变化调节伺服阀的开启度,从而实现对电液伺服系统的精确控制。
二、工作原理2.1 系统工作流程电液伺服系统的工作流程一般包括输入信号采样、信号处理、控制指令、伺服阀控制和液压执行器动作等步骤。
具体流程如下:(1)输入信号采样:传感器将液压执行器的位置和速度等信息转换为电信号,并传输给信号处理器。
(2)信号处理:信号处理器对输入信号进行滤波、放大等处理,将其转换为控制系统可识别的信号。
(3)控制指令:控制器根据输入信号的变化相应的控制指令。
(4)伺服阀控制:控制器根据控制指令调节伺服阀的开启度,控制液压系统的流量大小。
(5)液压执行器动作:伺服阀的控制信号作用于液压执行器,使其按照要求的位置和速度进行运动。
2.2 系统控制策略电液伺服系统可采用位置控制、速度控制和力控制等不同的控制策略。
其中,位置控制可实现对执行器位置的精确控制;速度控制可实现对执行器速度的精确控制;力控制可实现对执行器施加的力或扭矩的精确控制。
三、常见问题及解决方案3.1 液压系统压力不稳定可能原因:(1)供油系统压力不稳定。
电液伺服控制系统

1电液伺服控制系统1.1电液控制系统的发展历史概述液压控制技术的历史最早可以追溯到公元前240年,一位古埃及人发明的液压伺服机构———水钟。
而液压控制技术的快速发展则是在18世纪欧洲工业革命时期,在此期间,许多非常实用的发明涌现出来,多种液压机械装置特别是液压阀得到开发和利用,使液压技术的影响力大增。
18世纪出现了泵、水压机及水压缸等。
19世纪初液压技术取得了一些重大的进展,其中包括采用油作为工作流体及首次用电来驱动方向控制阀等。
第二次世界大战期间及战后,电液技术的发展加快。
出现了两级电液伺服阀、喷嘴挡板元件以及反馈装置等。
20世纪50~60年代则是电液元件和技术发展的高峰期,电液伺服阀控制技术在军事应用中大显身手,特别是在航空航天上的应用。
这些应用最初包括雷达驱动、制导平台驱动及导弹发射架控制等,后来又扩展到导弹的飞行控制、雷达天线的定位、飞机飞行控制系统的增强稳定性、雷达磁控管腔的动态调节以及飞行器的推力矢量控制等。
电液伺服驱动器也被用于空间运载火箭的导航和控制。
电液控制技术在非军事工业上的应用也越来越多,最主要的是机床工业。
在早些时候,数控机床的工作台定位伺服装置中多采用电液系统(通常是液压伺服马达)来代替人工操作,其次是工程机械。
在以后的几十年中,电液控制技术的工业应用又进一步扩展到工业机器人控制、塑料加工、地质和矿藏探测、燃气或蒸汽涡轮控制及可移动设备的自动化等领域。
电液比例控制技术及比例阀在20世纪60年代末70年代初出现。
70年代,随着集成电路的问世及其后微处理器的诞生,基于集成电路的控制电子器件和装置广泛应用于电液控制技术领域。
现代飞机上的操纵系统。
如驼机、助力器、人感系统,发动机与电源系统的恒速与恒频调节,火力系统中的雷达与炮塔的跟踪控制等大都采用了电液伺服控制系统。
飞行器的地面模拟设备,包括飞行模拟台、负载模拟器大功率模拟振动台、大功率材料实验加载等大多采用了电液控制,因此电液伺服控制的发展关系到航空与宇航事业的发展,在其他的国防工业中如机器人也大量使用了电液控制系统。
电液伺服系统详解

电液伺服系统
系统组成:由EH供油系统、电液执行器、保护 系统和试验模块
汽轮机数字电液控制系统
Digital Electro-Hydraulic Control System
EH供油系统 向电液执行器提供符合压力要求和清洁度、酸 度等品质要求的安全、可靠、稳定的液压油。由高压油泵、过 滤器、再生装置、冷油器EH油箱、高压蓄能器、低压蓄能器 等组成。 电液执行器 主汽门和调节汽门的执行调节器。有电液伺服阀 和电磁阀2种控制方式,前者为位置连续调节,后者为开、关2 种状态。 保护系统 “2取1”带电动作OPC电磁阀,“4取2”失电动作电 磁阀,及试验回路。超速保护控制和自动停机遮断,前者用于 超速预警和保护,后者用于事故工况下紧急停机。 试验模块 低润滑油压、低EH油压、推力轴承磨损、低真空 等试验系统。 油路系管路、OPC保护油路或AST停机油路、低压回油油路和无压回 油油路。前3种与电液执行器相连,保护系统的回油经无压回 油油路直接排至主油箱。
EH油系统 运 行
EH油系统概述 随着大容量、高参数汽轮发电机组的发展, 机组调节系统工作介质的额定压力随之升高, 对其工作介质的要求亦越来越高。通常所用 的矿物油自燃点为350℃左右,若在高参数大 容量机组使用,便增加了油泄漏到主蒸汽管 道(>530℃)导致火灾的危险性。为保证机组 的安全经济运行,汽轮机电液调节系统的控 制液普遍采用了磷酸酯抗燃油。
柱塞变量油泵
系统采用进口高压变量柱塞泵,并采用双泵并联工作系统, 当一台泵工作,则另一台泵备用,以提高供油系统的可靠性, 二台泵布置在油箱的下方,以保证正的吸入压头。 由交流马达驱动高压柱塞泵,通过油泵吸入滤网将油箱中的 抗燃油吸入,从油泵出口的油经过压力滤油器通过单向阀流 入和高压蓄能器联接的高压油母管将高压抗燃油送到各执行 机构和危急遮断系统。 泵输出压力可在0-21MPa之间任意设置。本系统允许正常工 作压力设置在11.0~15.0MPa,本系统额定工作压力为 14.5MPa。 油泵启动后,油泵以全流量约85 L/min向系统供油,同时也 给蓄能器充油,当油压到达系统的整定压力14.5MPa时,高 压油推动恒压泵上的控制阀,控制阀操作泵的变量机构,使 泵的输出流量减少,当泵的输出流量和系统用油流量相等时, 泵的变量机构维持在某一位置,当系统需要增加或减少用油 量时,泵会自动改变输出流量,维护系统油压在14.5MPa。 当系统瞬间用油量很大时,蓄能器将参与供油。
伺服控制(电液伺服系统 )课件

(二)系统的闭环刚度特性
闭环惯性环节转折频率的无因次曲线
17
闭环振荡环节固有频率无因次曲线
当h和Kv/h较小时
nc h
18
当h和Kv/h较小时
2 nc 2 h — Kv / h
闭环振荡环节阻尼系数无因次曲线
19
系统频宽主要受h和h的影响 和限制,应适当提高h和 h , 但过大的 h会降低nc,影响响
应速度。
电液位置控制系统闭环频率特性曲线
4)只有在工作频率接近谐振频率h时才有稳定性问题。当工作频率 接近h时,负载压力且也将接近ps了,也就是说压力趋于饱和,Kc变得很
大,阻尼系数比较高。
14
P116页使系统满足一定稳定要求的参数估算
由于以上几点原因,估算时一般可用
Kv
h
3
电液位置伺服系统难于得到较大的幅值稳定裕量Kg,而相位稳定
裕量 易于保证。
6
位置比较用电压比较代替 缸
电液伺服阀 液压能源
样板 给定
xi 位移 ei 比较eg 电伺服 I
传感器
- 放大器
ef
力矩 马达
液压 放大元件
扰动
液压 xp
执行件
位移 传感器1
A 双传感器阀控位置控制系统
7
由计算机图 形代替样板
程序 ei 比较eg
给定
-
ef
电液伺服阀 液压能源
电伺服 i 放大器
力矩 马达
11
将电液伺服阀看成比例环节
Kv
Ke Kd Ka Ksv iDm
TL
K V ce
iD K m
4
s
t
1
e ce
i +
第六章电液调节系统中的主要部件
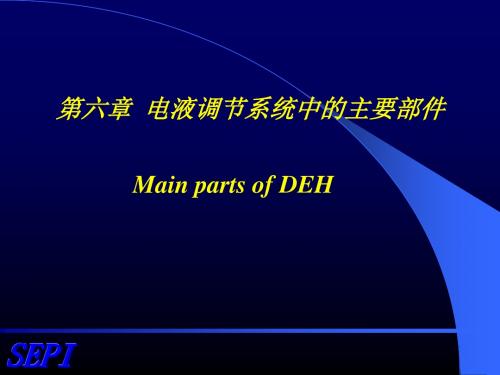
Main parts of DEH
SEPI
电 液 调 节 系 统
电子调节装置 阀位控制装置(电液伺服装置) 配汽机构 调节对象
SEPI
第一节
电子调节装置
Electric control equipment
1、转速测量元件 转速信号转变为直流电压模拟信号后发送给DEH
SEPI
5、功率校正器 PI调节器
6、调节级压力校正器
PI调节器
SEPI
第二节
阀位控制装置
Valve control equipment
1、电液转换器 阀位偏差信号(电信号);转换放大; 液压信号(调节油压);控制油动机 断流式电液转换器 继流式电液转换器 蝶阀型电液转换器
SEPI
2、油动机 调节信号的最后一级放大 双侧进油式油动机 单侧进油式油动机 指标:提升力 油动机时间常数
SEPI
第三节配汽机构源自Executive body
1、传动机构 杠杆式传动机构
凸轮式传动机构
2、调节阀 单阀、双阀 调节阀升程流量特性 调节阀升程提升力特性
SEPI
第四章 跟踪滑阀
Tracking
存在于电调与液调并存的控制方式 中
切换时无扰动
SEPI
转 速 测 量 元 件
磁阻发讯器(永久磁钢、铁芯、线圈)
频率(转速)变送器
SEPI
n
N
S
SEPI
整形
微分
单稳
滤波
SEPI
2、功率测量元件 霍尔定律:半导体薄片置于磁场中,当沿薄片 的一对边通以电流,则另一对边就 会产生电势。
3、功率反调校正元件 转速变化信号落后于功率变化信号
电液伺服系统

蓄能器
❖ 一个气—液式高压蓄压器装在油箱的旁边, 用来维持系统的压力,减小压力波动。此蓄 压器一侧预先充进的氮气压力与另一侧油系 统中的油压相平衡。此蓄压器块上有一个截 止阀,此阀能将蓄压器与系统隔绝,以进行 试验、重新充气或维修。蓄压器氮气一侧有 一个压力表,用以检查充氮压力
蓄能器
EH油系统的运行操作
❖ EH油泵出口滤网前后差压高 报警
❖ 低于9.31 Mpa(g) 汽轮机跳闸 (63/LP) 自动停机
❖ EH油压力回油压力高 回油压力报警 0.21MPa
EH油系统常见故障
❖ 1 系统压力下降,个别调门无法正常开启; ❖ 2 油动机卡涩,调门动作迟缓,有时泄油后不回座; ❖ 3 在开关调门过程中发生某个调门不规则频繁大幅度摆动,
同程度的腐蚀,在滑阀凸肩、喷咀及节流孔处腐蚀尤为严重。
❖ d 电液转换器滑阀两侧压力偏差大: 油中杂质堵塞电液转换器的喷咀;磨 擦、酸性腐蚀造成滑阀的凸肩、滑块与滑座之间磨损,使滑阀相对与滑 座之间的间隙加大,使漏流量增加;酸性油液对喷咀室、通道及节流孔 等的腐蚀,改变了滑阀两侧的压力。
❖ e LVDT线性电压位移转换器故障,电液转换器机械零位不准等
EH油系统 运 行
❖ EH油系统概述 ❖ 随着大容量、高参数汽轮发电机组的发展,
机组调节系统工作介质的额定压力随之升高, 对其工作介质的要求亦越来越高。通常所用 的矿物油自燃点为350℃左右,若在高参数大 容量机组使用,便增加了油泄漏到主蒸汽管 道(>530℃)导致火灾的危险性。为保证机组 的安全经济运行,汽轮机电液调节系统的控 制液普遍采用了磷酸酯抗燃油。
❖ 在机组预启动期间,EH油系统应进行升温、 升压。液压油的正常运行温度是49℃ (38℃~60℃),虽然允许系统可以在21℃ 油温下操作,但不推荐低于21℃油温下运行, 严禁在10℃下运行。因此预启动的第一步是 对油升温。 采用浸入式加热器升温
电液伺服系统原理
电液伺服系统原理
电液伺服系统是一种通过控制液压油流来实现位置、速度和力的精确控制的系统。
它由液压系统、电气系统和机械执行部分组成。
液压系统是电液伺服系统的核心部分,它包括液压泵、液压缸、液压阀和液压油箱。
液压泵通过压力油将液压油推送给液压缸,从而产生力或运动。
液压阀用于控制液压油的流动方向和流量。
液压油箱用于储存液压油,并保持其温度和清洁度。
电气系统通过控制电信号来控制液压系统。
它包括传感器、控制器和执行器。
传感器用于检测被控对象的位置、速度和力,并将其转化为电信号。
控制器接收传感器反馈的电信号,经过计算和处理后,输出控制信号给执行器。
执行器接收控制信号,并控制液压阀的开关状态,从而控制液压系统的运动和力。
机械执行部分将液压系统的力和运动传递给被控对象。
它包括液压缸、阀门、连接杆等元件。
液压缸接收液压油的力,并将其转化为线性运动。
阀门用于控制液压油流的方向和流量。
连接杆将液压缸的运动传递给被控对象,实现位置、速度和力的控制。
总之,电液伺服系统通过控制液压油流来实现位置、速度和力的精确控制。
液压系统、电气系统和机械执行部分相互配合,完成对被控对象的精确控制。
电液伺服控制系统
6-1 怎样区分一个系统是位置、速度或力电-液伺服控制系统。
按系统被控制的物理量的性质来区分,如果是要实现位置控制,当然就是位置电液伺服系统。
6-2 试比较电-液伺服系统与机-液伺服系统的主要优缺点和性能特点。
机液伺服系统的指令给定、反馈和比较都是采用机械构件,优点是简单可靠,价格低廉,环境适应性好,缺点是偏差信号的校正及系统增益的调整不如电气方便,难以实现远距离操作,另外,反馈机构的摩擦和间隙都会对系统的性能产生不利影响。
机液伺服系统一般用于响应速度和控制精度要求不是很高的场合,绝大多数是位置控制系统。
电液伺服系统的信号检测、校正和放大等都较为方便,易于实现远距离操作,易于和响应速度快、抗负载刚度大的液压动力元件实现整合,具有很大的灵活性和广泛的适应性。
特别是电液伺服系统与计算机的结合,可以充分运用计算机快速运算和高效信息处理的能力,可实现一般模拟控制难以完成的复杂控制规律,因而功能更强,适应性更广。
电液伺服系统是液压控制领域的主流系统。
6-3 为什么说电-液伺服系统一般都要加以校正。
当电液位置伺服控制系统的某些性能指标不甚满意时,简单的方法可通过增大系统的开环增益来提高响应速度和控制精度,但提高开环增益受系统稳定性条件的制约,也就是受液压固有频率和阻尼比的限制。
全面改善系统的性能仅仅靠调整开环增益是远远不够的,通过对电液伺服系统进行针对性的校正,往往能够获得更高性能的电液伺服系统,并且不同的校正方法,会得到不同的改善效果。
6-4 怎样才能简化位置电-液伺服控制系统。
当电液伺服阀的频宽与液压固有频率相近时,电液伺服阀的传递函数可用二阶环节来表示;当电液伺服阀的频宽大于液压固有频率(3~5倍)时,电液伺服阀的传递函数可用一阶环节来表示。
又因为电液伺服阀的响应速度较快,与液压动力元件相比,其动态特性可以忽略不计,而把它看成比例环节。
一般的液压位置伺服系统往往都能够简化成以下的这种形式。
()()V2h h h 21K G s H s s s s ζωω=⎛⎫++ ⎪⎝⎭6-5 怎样理解系统刚度高,误差小。
电液伺服控制系统概述
电液伺服控制系统概述摘要:电液伺服控制是液压领域的重要分支。
多年来,许多工业部门和技术领域对高响应、高精度、高功率——重量比和大功率液压控制系统的需要不断扩大,促使液压控制技术迅速发展。
特别是控制理论在液压系统中的应用、计算及电子技术与液压技术的结合,使这门技术不论在原件和系统方面、理论与应用方面都日趋完善和成熟,并形成一门学科。
目前液压技术已经在许多部门得到广泛应用,诸如冶金、机械等工业部门及飞机、船舶部门等。
关键词:电液伺服控制液压执行机构伺服系统又称随机系统或跟踪系统,是一种自动控制系统。
在这种系统中,执行元件能以一定的精度自动地按照输入信号的变化规律动作。
液压伺服系统是以液压为动力的自动控制系统,由液压控制和执行机构所组成。
一、电液控制系统的发展历史液压控制技术的历史最早可以追溯到公元前240年,一位古埃及人发明的液压伺服机构——水钟。
而液压控制技术的快速发展则是在18世纪欧洲工业革命时期,在此期间,许多非常实用的发明涌现出来,多种液压机械装置特别是液压阀得到开发和利用,使液压技术的影响力大增。
18世纪出现了泵、水压机及水压缸等。
19世纪初液压技术取得了一些重大的进展,其中包括采用油作为工作流体及首次用电来驱动方向控制阀等。
第二次世界大战期间及战后,电液技术的发展加快。
出现了两级电液伺服阀、喷嘴挡板元件以及反馈装置等。
20世纪50~60年代则是电液元件和技术发展的高峰期,电液伺服阀控制技术在军事应用中大显身手,特别是在航空航天上的应用。
这些应用最初包括雷达驱动、制导平台驱动及导弹发射架控制等,后来又扩展到导弹的飞行控制、雷达天线的定位、飞机飞行控制系统的增强稳定性、雷达磁控管腔的动态调节以及飞行器的推力矢量控制等。
电液伺服驱动器也被用于空间运载火箭的导航和控制。
电液控制技术在非军事工业上的应用也越来越多,最主要的是机床工业。
在早些时候,数控机床的工作台定位伺服装置中多采用电液系统(通常是液压伺服马达)来代替人工操作,其次是工程机械。
电液伺服系统
电液伺服系统电液伺服系统是一种由电信号处理装置和液压动力机构组成的反馈控制系统。
根据输入信号的形式不同,又可分为模拟伺服系统和数字伺服系统两类。
下面对模拟伺服系统和数字伺服系统作一简单的说明。
模拟伺服系统在模拟伺服系统中,全部信号都是连续的模拟量,如图1所示。
在此系统中,输入信号、反馈信号、偏差信号以及其放大、校正都是连续的模拟量。
电信号可以是直流量,也可以是交流量。
直流量和交流量相互转换可以通过调制器或解调器完成。
模拟伺服系统重复精度高,但分辨能力较低(绝对精度低)。
伺服系统的精度在很大程度上取决于检测装置的精度,而模拟式检测装置的精度一般低于数字式检测装置,所以模拟伺服系统分辨能力低于数字伺服系统。
另外模拟伺服系统中微小信号容易受到噪声和零漂的影响,因此当输入信号接近或小于输入端的噪声和零漂时,就不能进行有效的控制了。
图1 模拟伺服系统方块图数字伺服系统在数字伺服系统中,全部信号或部分信号是离散参量。
因此数字伺服系统又分为数字伺服系统和数字—模拟伺服系统两种。
在全数字伺服系统中,动力元件必须能够接收数字信号,可采用数字阀或电液步进马达。
数字模拟混合式伺服系统如2所示。
数控装置发出的指令脉冲与反馈脉冲相比较后产生数字偏差,经数模转化器把信号变为模拟偏差电压,后面的动力部分不变,仍是模拟元件。
系统输出通过数字检测器(即模数转换器)变为反馈脉冲信号。
图2 数字伺服系统方块图数字伺服系统有很高的绝对精度,受模拟量的噪声和零漂的影响很小。
当要求较高的绝对精度,而不是重复精度时,常采用数字模拟系统。
从经济性可靠性方面来看,简单的伺服系统采用采用模拟型控制为宜。
系统特点及使用场合电液伺服系统综合了电气和液压两方面的优点,具有控制精度高、响应速度快、输出功率大、信号处理灵活、易于实现各种参量的反馈等优点。
因此,在负载质量大又要求响应速度快的场合最为适合,其应用已遍及国民经济的各个领域,比如飞机与船舶舵机的控制、雷达与火炮的控制、机床工作台的位置控制、板带轧机的板厚控制、电炉冶炼的电极位置控制、各种飞机车里的模拟台的控制、发电机转速的控制、材料试验机及其他实验机的压力控制等等。
- 1、下载文档前请自行甄别文档内容的完整性,平台不提供额外的编辑、内容补充、找答案等附加服务。
- 2、"仅部分预览"的文档,不可在线预览部分如存在完整性等问题,可反馈申请退款(可完整预览的文档不适用该条件!)。
- 3、如文档侵犯您的权益,请联系客服反馈,我们会尽快为您处理(人工客服工作时间:9:00-18:30)。
带有加速度和速度反馈的系统方框图 同时具有速度、加速度反馈时,并适当调整前置放 大器增益k1,具有两种反馈的优点。通过位置、速度、加 速度的复合控制可拓宽系统频宽,提高响应快速性,改善 精度。
3、压力反馈和动压反馈校正 压力反馈是电液伺服系统中易于实现的一种方法: 采用压差或压力传感器测取液压缸的负载压降pL,反馈到 伺服阀的输入端,构成压力反馈。
思考: 1、本章的系统校正与“第4章 机液伺服系 统”中的系统校正问题的区别。 2、本章中的“位置、流量、压力反馈” 与“第5章 电液伺服阀”中的“位置、流量、 压力反馈”的区别。
压力反馈产生附加的流量-压力系数,它对系统稳定 性的影响与阀的开口及液压缸泄漏是一样的,可提高和产 生恒定阻尼,液压固有频率也有所提高,并可避免引起效 率和受温度影响等弊病。但会导致开环增益稍有下降,开 环、闭环刚度降低,干扰力误差增加。
压力反馈校正的缺点可采用动压反馈校正的方法弥 补。将压力传感器的放大器换为微分放大器,压力信号经 微分校正装置输出给伺服阀,可构成为动压反馈。微分放 大器的传递函数为: Ts
正环节。 实用简单的校正方法是在前向通道的电子控制 部分加RC校正网络。 对于零型有差系统,为提高系统精度,在前向 通道内可采用积分放大器校正(用运算放大器组成的 积分运算器代替原来的比例放大器),使系统成为Ⅰ 型无差系统。 采用积分校正的速度控制系统模型 与未校正的位置伺服系统模型相似。
四、电液力控制系统
3、位置和速度双闭环的速度系统
同时具有轴向柱塞泵斜盘的位置反馈及速度闭环, 马达的输出转速可得到准确控制。
4、有速度闭环无位置闭环的速度控制系统
去掉轴向柱塞泵斜盘倾角的位置控制回路,只保留 马达速度信号的反馈回路。因液压缸已是一积分环节,具 有积分作用,故不用积分放大器而仅用比例放大器。
电液速度伺服控制系统的设计,有时要加校
电液力(或力矩)控制系统具有精度高、响应快、 功率大、结构紧凑和使用方便等优点,得到越来越广泛 的应用。如材料试验机、车轮刹车装置等。 1、系统组成与工作原理
电液力控制系统一般组成:指令输入装置,伺服放 大器,伺服阀,液压缸,力传感器及受力对象等。 所用的伺服阀可以是压力控制伺服阀或流量控制伺 服阀,前者本身带有压力反馈,其压力增益特性平缓而线 性,可用于开环和闭环压力控制,但制造调试复杂,较少 使用;在系统要求较大流量时,一般采用后者。 在力控制系统中,输出力(负载力)是被调节控制 量,而位置、速度等取决于输出力和受力对象本身的状态。
速度控制的方式有以下四种,可视功率大小而定。 一般在小功率控制中,采用液压伺服阀与液压马达的组 合,大功率时,采用变量泵与液压马达的组合。 1、闭环阀控液压马达速度伺服系统
频响快,效率偏低,多用于中小功率速度控制。
2、开环泵控液压马达速度伺服系统
直接由伺服变量泵控制液压马达,改变泵的斜盘 倾角可控制供给液压马达的流量,以此来调节液压马达 的旋转速度,有轴向柱塞泵斜盘的位置反馈,泵的输出 流量精确。但没有速度闭环,易受负载、油温等变化的 影响,难以得到准确的速度控制。
稳态误差为
3、零漂和死区等引起的稳态误差
静摩擦力矩折算到伺服阀输入端的死区电流为: 电液伺服阀的零漂和死区所引起的位置误差: 设总的零漂和死区电流为Σ△I,则总的静态位置误差为:
(五)电液伺服系统的校正
电液伺服系统固有部分难以保证性能,需加校正,且校 正方便,这也是其优点。 1、串联校正 滞后校正、超前校正、滞后-超前校正等。 2、速度与加速度的反馈校正 位置控制系统的校正方法之一是利用系统输出的速度、 加速度量的补偿方法,需要增设品质优良、价格昂贵的速度、 加速度传感器。 采用速度(加)传感器测取输出(加)速度 信号,反馈到伺服放大器,构成(加)速度负反馈。 速度反馈可增加固有频率,利于提高系统性能,相当于 可增加系统刚度,减小因零漂及负载扰动所引起的位置误差, 但降低了开环增益和阻尼比。 加速度反馈校正可使系统的增益和固有频率不变的情况 下提高阻尼比。
电液控制 ——郭世伟
第6章 电液伺服控制系统
一、电液伺服系统概述
1、电液伺服系统的特点、应用
2、电液伺服系统的组成
3、电液伺服系统的类型
二、电液位置伺服系统
应用最广泛
在电液伺服系统中,除液压执行元件外,指令 输入、检测反馈元件,甚至电液伺服阀都可近似为 比例环节(电液伺服阀作何特性需视系统频宽及伺 服阀频宽而定,在做基本分析时可作为比例环节)。 这样,系统方框图就与机液位置伺服控制系统 相同,系统的开环传递函数可看作比例积分加振荡 环节,对机液位置伺服系统的分析及所得结果,对 于简化后的未加校正的电液位置伺服系统也是适用 的。
电液力控制系统原理图
系统模型的建立。 系统的稳定性分析 的稳定性有很大的影响。 负载刚度对力控制系统
系统的响应速度 由开环增益和惯性环节的 时间常数所决定;穿越频率与负载刚度有关。 系统的稳态精度 未加校正的力控制系统是 零型系统,可提高系统开环增益或采用积分校正变系 统为Ⅰ型系统。 在力控制系统中,负载是经常变化的,需要根 据负载的变化随时调整回路增益和校正装置参数,以 满足系统稳定性和响应速度的要求。
增益裕量大于
20lg Kg 6dB
(三)系统的响应特性分析
对指令输入的闭环频率响应:
对负载力矩的闭环频率响应:
即闭环柔度特性
即闭环刚度特性
(四)系统的稳态误差分析
1、指令输入引起的稳态误差 系统对指令输入的误差传递函数:
稳态误差为
2、负载干扰力矩引起的稳态误差 系统对外负载力矩的误差传递函数:
G fp ( s)
p
Tp s 1
动压反馈校正可提高系统阻尼比,同时可保持频率 和开环增益不变,系统刚度不变,பைடு நூலகம்统的稳态误差特性不 会下降。
带压力反馈系统简化方块图
带压力微分反馈系统简化方块图
压力反馈与压力微分系统的比较
三、电液速度伺服控制系统
输出量为速度,输入及反馈信号也为速度信号。
前面已述,速度回路也可作为一个校 正环节引入位置控制中,以提高系统 的固有频率,改善系统性能。
(一)系统建模
自整角机: 相敏放大器: 伺服放大器: 伺服阀:
阀控液压马达:
齿轮减速箱传动比:
系统开环传函求得为:
(二)系统的稳定性分析
系统稳定性条件为: 简化方框图为:
Kv 2hh
为了保证系统稳定可靠地工作,具有满意的性能指标, 一般要求: 相位裕量
30o
60o ,
进行分析设计