电液伺服控制系统的应用实例
直驱式容积控制DDVC电液伺服系统及应用液压控制技术在工业

自动化中的应用直驱式容积控制DDVC电液伺服系统及应用液压控制技术在工业自动化中的应用一、前言随着工业自动化的不断发展,液压伺服系统作为一种优秀的动力传递和控制手段,被广泛应用于各种机械设备中。
其中,液压控制技术是实现高精度、高可靠性、大功率控制的关键技术之一。
本文将介绍一种新型的电液伺服系统——直驱式容积控制DDVC电液伺服系统,并探讨其在工业自动化中的应用。
二、直驱式容积控制DDVC电液伺服系统介绍1. 液压伺服系统的优缺点液压伺服系统是一种以液压元件为主要执行元件的动力传递和控制系统。
与机械传动和电传动相比,液压伺服系统具有以下优点:1.传动可靠、功率密度高2.传动平稳、响应快、精度高3.可以长时间连续运行4.可以抵抗恶劣环境的干扰和故障但是,液压伺服系统也有一些缺点:1.系统复杂、维护成本高2.需要较大的动力单元来提供液压能量3.液压元件噪音大、污染环境4.其调节性能受到流量特性和压力特性的限制2. 直驱式容积控制DDVC电液伺服系统的基本原理直驱式容积控制DDVC电液伺服系统是在已有容积式液压传动系统基础上,采用数字控制技术、高效率磁力直驱技术和容积控制技术相结合而成的一种新型的伺服系统。
其基本原理是通过等量液压缸直接驱动负载,纯数字化控制液压泵的输出流量和压力,实现系统的高精度、高效率、低噪音、无油污染和全数字化控制。
3. 直驱式容积控制DDVC电液伺服系统的主要特点直驱式容积控制DDVC电液伺服系统相比传统液压系统,具有如下特点:1.直接驱动负载,转换效率高2.无须传统控制阀和液压元件,系统压降小,无噪音,无油污染3.系统响应快、精度高、调控性能稳定、可靠性高4.可虚拟仿真工艺,大大缩短产品开发周期,提高产品质量和竞争力5.适应范围广,可广泛应用于各种机械设备中,特别是工业自动化领域三、直驱式容积控制DDVC电液伺服系统在工业自动化中的应用直驱式容积控制DDVC电液伺服系统在工业自动化中,可应用于各种液压传动系统,如卷取、输送、成型、调节、挤出等。
电液伺服系统在汽车行业的应用

组员: 组员:
1 电液伺服系统概述
• 电液伺服控制系统是以液压动力作驱
动装置所组成的反馈控制系统。在这 动装置所组成的反馈控制系统。 种系统 能够自动地、 等)能够自动地、快速而准确地复现 输入量的变化规律。 输入量的变化规律。该系统能将输入 的微小电气信号转换为大功率的液压 信号(流量与压力)输出, 信号(流量与压力)输出,因此也是 一个功率放大装置。具有控制精度高, 一个功率放大装置。具有控制精度高, 速度快, 在军事、 速度快,稳定性好等特点 。在军事、航 航天、材料、汽车、 空、航天、材料、汽车、冶金等行业 有广泛的应用。 有广泛的应用。
电控液压助力转向系统工作原理
电控液压助力转向包括液压储油罐、 电控液压助力转向包括液压储油罐、 电动机、 泵、电动机、转向器伺服阀和电子 控制系统等等。 控制系统等等。下图为电控液压助 力转向系统(EHPS)结构 结构。 力转向系统(EHPS)结构。电机控 制器根据所获得的转向盘转角信号 和电动机的转速信号, 和电动机的转速信号,经计算后决 定提供助力大小, 定提供助力大小,以控制电机的转 速,电机驱动齿轮泵向转向器提供 液压油。 液压油。
电控液压助力转向系统结构图
2 电液伺服系统在汽车上的应用
• 电液伺服系统使用闭环控制,可以充分满足被控 电液伺服系统使用闭环控制,
制量实时被系统控制,显著提高了系统控制的准 制量实时被系统控制, 确性和精度。现代汽车行业对汽车的安全性能、 确性和精度。现代汽车行业对汽车的安全性能、 驾驭性能、舒适性能等提出了更高的要求, 驾驭性能、舒适性能等提出了更高的要求,由于 电液伺服控制系统工作可靠、自动化程度高、 电液伺服控制系统工作可靠、自动化程度高、控 制精度高, 制精度高,在汽车行业中电液伺服控制系统受到 充分重视,被广泛应用于汽车控制系统。 充分重视,被广泛应用于汽车控制系统。下面主 要介绍电液伺服系统在汽车防撞系统、 要介绍电液伺服系统在汽车防撞系统、助力转向 系统、 系统、汽车试验系统及主动悬架上的应用
伺服系统在注塑机中的应用

伺服系统在注塑机中的应用注塑机作为一种重要的塑料机械设备,广泛应用于化工、汽车、电子等产业领域。
伺服系统作为一种高精度、高效、低噪音、节能环保的控制系统,在注塑机中得到了广泛应用。
本文将主要探讨伺服系统在注塑机中的应用技术及优势。
一、伺服系统在注塑机中的应用技术伺服系统由伺服驱动器和伺服电机组成,其中伺服电机是一种高度精确的同步电机,具有高性能运动控制能力。
伺服系统具有精密位置、速度、加速度控制能力,能够提供高速、高精度的动力输出。
在注塑模具的开合、注射、压力控制、注塑周期控制等方面,伺服系统起到了至关重要的作用。
1.开合模控制注塑机的开合模控制通常采用伺服电机作为动力源,通过PLC编程实现闭环控制,实现高精度、高稳定性的开合模运动控制。
伺服电机具备快速反馈的能力,能够及时对开合模运动进行控制调节,保证模具运动的精度和稳定性。
2.注射控制注塑机的注射控制是最复杂的控制之一,包括塑料熔融、塑料进料、塑料压缩和塑料注射四个阶段,要求精细控制。
传统注塑机采用伺服电机控制注射进料,电液伺服系统控制塑料的压缩剂注入。
在新型注塑机中,采用了电机直接驱动注射,利用高精度编码器实现精准控制塑料的进料和注射量。
这种控制方式可以提高注塑品质的一致性和稳定性。
3.压力控制注塑过程中的压力控制是保证注塑质量稳定的关键之一,也是注塑机伺服控制的重要应用之一。
传统注塑机的压力控制通常采用“定值控制”或“PID算法控制”,这种控制方式控制效果难以调节,且受到了机械零件间磨损等方面的干扰,注塑精度和质量无法提高。
伺服控制系统采用高精度的传感器,实现闭环控制,精度更高,能够及时反馈注塑压力变化,从而实现稳定的注射行驶和注塑压力控制。
4.注塑周期控制注塑周期控制包括注塑时间、压缩和恢复时间的控制,是注塑品质稳定的重要保障。
传统注塑机通常采用固定周期模式,这种模式无法适应各种注塑产品的需求。
伺服控制系统采用可编程控制器(PLC)实现动态注塑周期,使注射和保压时间动态地调整和优化。
电液位置伺服控制系统实验
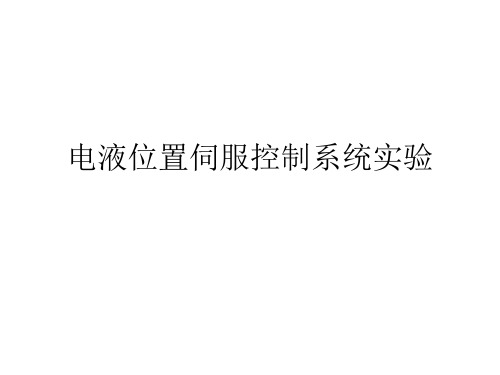
2
s2
2.834 2 0.866 1 2 s s s 1 2 14 .726 14 .726
正常参数时的ωc=2.78, ωh=14.8,Kg=19.1
增大Ki
正常参数
C (s) 4.611 R( s) 1 2 0.866 2 s 14 .726 2 s 14 .726 s 1
斜坡输入1
正弦输入
正弦输入,幅值5,频率1
正弦输入,幅值5,频率2.95
3 液压系统原理
压力传感器2
伺服缸
压力传感器3
平衡阀 电磁换向阀
蓄能器
电液伺服阀 压力传感器1
流量计2
流量计1 精滤器 电磁溢流阀
电机泵组
M
粗滤器 精滤器
4 系统控制原理
数据采集
参考输入
控制器
数模转换
功率放大
伺服阀
伺服缸
K i 73.746 KV 2.834 K d 1 26.022
K d1 h 代入系数得到 K d 1 26 .022 14 .726 h a a 0.12 (b K d 2 ) (b K d 2 ) (0.2 2.861) h h 0.866 2 K d1 a 2 K d 1 a 2 26.022 0.12
mmax 为能量输出单元在线 性范围内的最大值
r0,ml 为输入信号在线性范 围内的最大值
阶跃输入2.5
阶跃输入5
阶跃输入9
阶跃输入12
系统开环传递函数
KV C (s) R(s) 1 2 2 h s 2 s s 1 h h
Ki KV K d1
2)阀控缸微分方程
电液轴控制器(HNC)在伺服缸测试系统中的应用
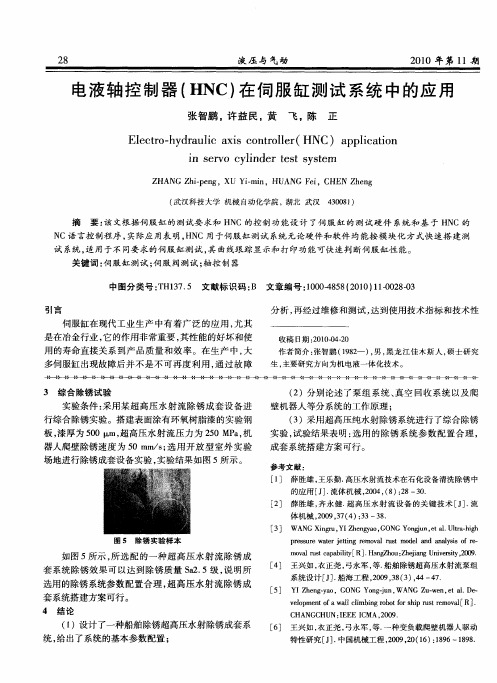
( )设 计 了一 种船舶 除锈 超高压 水射 除锈成套 系 1 统 , 出了系统 的基本参 数配 置 ; 给
[ ] 王兴如 , 6 衣正尧 , 弓永军 , . 等 一种变 负载爬壁机器人驱动 特性研究 [ ] 中国机械工程 ,09 2 (6 :86—19 . J. 2 0 ,0 1 ) 19 88
参考文献 : [ ] 薛胜雄 , 1 王乐 勤. 高压水射 流技术在石化设备清洗 除锈 中 的应用 [ ] 流体机械 ,0 4 ( )2 3 . J. 2 0 ,8 :8— 0 [ ] 薛胜雄 , 2 齐永健 . 高压水 射流设 备 的关 键技 术 [ ] 流 超 J.
体机械 ,0 9 3 ( ) 3 3 . 20 ,7 4 :3— 8 [ ] WA G Xnr , I hnyo G N o g ne a. lah h 3 N ig Y ega ,O GY nj , 1Ut —i u Z u t r g
分析 , 再经过 维修 和测试 , 达到使 用技术 指标 和技术性
收 稿 1期 :0 00 —0 3 2 1 - 2 4
伺 服缸在 现代 工业 生 产 中有 着 广泛 的应 用 , 尤其
是在 冶金行业 , 的作 用非 常重要 , 它 其性 能 的好 坏和使 用 的寿命 直接 关 系到 产 品质 量 和效 率 。在 生 产 中 , 大 多伺服 缸 出现 故障后 并 不 是不 可 再度 利 用 , 过故 障 通
21 0 0年 第 1 1期
液 压 与 气动
2 9
能后仍 可继续使 用 。伺 服缸 测试 系统就 是用来 测试伺 服缸 的技 术特性 , 功能主 要包括 两部分 : 其 一是 对伺服
阀 的性能 进 行 测试 ; 是 对 伺 服 缸 的 特 性 进 行 测 试 。 二
电液控制技术(1)及应用

比例阀技术初步
• 比例阀介于常规开关阀和闭环伺服阀之间已成
为现今液压系统的常用组件,液压工业从比例阀 技术的发展而获益匪浅。
• 看一个例子:
比例阀技术对于液压系统究竟意味着什么
比例阀技术对于液压系统究竟意味着什么
上图说明了信号流程: 输入电信号为电压多数为0至9V由信号放大器成比例地转化为
电流即输出变量如1mV相当于1mA; 比例电磁铁产生一个与输入变量成比例的力或位移输出; 液压阀以这些输出变量力或位移作为输入信号就可成比例地输 出流量或压力; 这些成比例输出的流量或压力输出对于液压执行机构或机器动 作单元而言意味着不仅可进行方向控制而且可进行速度和压力 的无级调控; 同时执行机构运行的加速或减速也实现了无级可调如流量在某 一时间段内的连续性变化等。
如果对于不带位移传感器的直动式比例方向阀,其滞环一 般为5-6%,重复精度2-3%。
比例方向阀-直动式
控制阀芯的结构:
图示,比例阀控制阀芯与普通方向阀 阀芯不同,它的薄刃型节流断面呈三 角形。用这种阀芯形式,可得到一条 渐增式流量特性曲线。
阀芯的三角控制棱边和阀套的控制棱
边,在阀芯移动过程中的任何位置上,
比例泵的恒压、恒流、压力流量复合控制等多种功能控制块 ,可采用组合叠加方式;
控制放大器、电磁铁、和比例阀组成电液一体化结构。
电液比例控制的技术特征
带比例电磁铁的比例阀和比例泵为电气控制提供了良好的接 口无论对于顺序控制的生产机械还是其它可编程的控制/驱动 系统都提供了极大的灵便性。 比例控制设备的技术优势主要在于阀位转换过程是受控的设 定值可无级调节且实现特定控制所需的液压元件较少从而减 少了液压回路的投资费用。 使用比例阀可更快捷更简便和更精确地实现工作循环控制并 满足切换过程的性能要求由于切换过渡过程是受控的避免产 生过高的峰值压力因而延长了机械和液压元器件的使用寿命 。
电液控制-机液伺服系统
四、液压转矩放大器
Hale Waihona Puke 反馈机构为 螺杆、螺母 液压马达轴完全跟 踪阀芯输入转角而 转动。但输出力矩 比输入力矩要大得 多,故称液压转矩 放大器。
电液步进马达
以惯性负载为主时,可分析得
方框图为:
则系统方框图为:
§系统稳定性分析
液压伺服系统的动态分析和设计一般都是以稳定性要求为 中心进行的。
令G(s)为前向通道的传递函数,H(s)为反馈通道的传递函 数,由以上的方框图可得系统的开环传递函数为:
含有一个积分环节,故系统为Ⅰ型系统。
可绘制开环系统伯德图,如下图所示:
对伯德图的分析
幅值穿越频率ωc≈Kv 相位穿越频率ωc=ωg 为了使系统稳定, 必须有足够的相位裕 量和增益裕量。 由图可见,相位裕 度已为正值,为使幅 值裕度为正值,可计 算求得要求: K 2
与全闭环系统相比,半闭环系统的稳定性好得多,但精度较低。
综上所述,由于结构柔度的影响,产生了结构谐振和液压谐 振的耦合,使系统出现了频率低、阻尼比小的综合谐振,综合谐 振频率ωn和综合阻尼比ξn常常成为影响系统稳定性和限制系统频 宽的主要因素,因此提高具有重要意义。 提高ωn 就需要提高结构谐振频率ωs,就要求负载惯量减小 (但已由负载特性决定),结构刚度增大(提高安装固定刚度和 传动机构刚度,尤其是靠近负载处的传动机构的结构刚度)。 增大执行元件到负载的传动比,可提高液压固有频率;提高 液压弹簧刚度的方法也可提高液压固有频率,从而提高综合谐振 频率。
反馈从活塞输出端Xp取出时,构成为半闭环系统,其方框图 为:
此时系统开环传函中含有二阶微分环节,当ωs2和ωn靠得很 近时,会有零极点相消现象,使综合谐振峰值减小,从而改善 系统稳定性,如曲线b所示。 系统闭环传函为:
电液位置伺服控制系统实验
减小Ki
正常参数
Ki减小为40
Ki变小,ωc=1.53<2.78, ωh=14.8不变,Kg=24.5>19.1
增大Kd1
正常参数
Kd1变大为35
Kd1变大,ωc=2.1<2.78, ωh=17.1>14.8 ,Kg=21.8>19.1
减小Kd1
正常参数
Kd1减小为20
Kd1变小,ωc=3.45>2.78, ωh=12.9<14.8 ,Kg=16.8<19.1
2)阀控缸微分方程
负载流量线性化方程 流量连续性方程
忽略阀腔和管道总容积,油液的压缩性影响忽略
液压缸活塞的动力学平衡方程
3)缸输出位移对伺服阀输入电信号的传递函数 或写成:
2 伪微分反馈控制算法
对输出信号C 微分的积分仍是C,这就说明没有必要对C 进行微分
2
微分反馈控制方框图
伪微分反馈控制方框图
增大Kd2
正常参数
Kd2变大为3.3
Kd2变大,ωc=2.78不变, ωh=14.8不变,Kg=20.4>19.1
减小Kd2
正常参数
Kd2减小为0.6
Kd2变小,ωc=2.95基本不变, ωh=14.8不变,Kg=7.51<19.1
斜坡输入1
正弦输入
正弦输入,幅值5,频率1
正弦输入,幅值5,频率2.95
为能量输出单元在线 性范围内的最大值
为输入信号在线性范 围内的最大值
2
系统开环传递函数
代入系数得到
正常参数时的ωc=2.78, ωh=14.8,Kg=19.1
增大Ki
正常参数
Ki变大为120
Ki变大,ωc=4.39>2.78, ωh=14.8不变,Kg=15<19.1
电液伺服系统的原理及应用
电液伺服系统的原理及应用一.电液伺服系统概述电液伺服系统在自动化领域是一类重要的控制设备,被广泛应用于控制精度高、输出功率大的工业控制领域.液体作为动力传输和控制的介质,跟电力相比虽有许多不甚便利之处且价格较贵,但其具有响应速度快、功率质量比值大及抗负载刚度大等特点,因此电液伺服系统在要求控制精度高、输出功率大的控制领域占有独特的优势。
电液伺服控制系统是以液压为动力,采用电气方式实现信号传输和控制的机械量自动控制系统。
按系统被控机械量的不同,它又可以分为电液位置伺服系统、电液速度伺服控制系统和电液力控制系统三种。
我国的电液伺服发展水平目前还处在一个发展阶段,虽然在常规电液伺服控制技术方面,我们有了一定的发展。
但在电液伺服高端产品及应用技术方面,我们距离国外发达国家的技术水平还有着很大差距。
电液伺服技术是集机械、液压和自动控制于一体的综合性技术,要发展国内的电液伺服技术必须要从机械、液压、自动控制和计算机等各技术领域同步推进。
二.电液伺服的组成电液控制系统是电气液压控制系统简称,它由电气控制及液压两部分组成。
在电子-液压混合驱动技术里,能量流是由电子控制,由液压回路传递,充分结合了电子控制和液压传动两者混合驱动技术的优点避免了它们各自的缺陷。
⑴电子驱动技术的特点①高精度、高效率,低能耗、低噪音②高性能动态能量控制③稳定的温度性能④能量再生及反馈电网⑤在循环空闲的时间没有能量损失⑵液压驱动技术的特点①高(力/功)密度②结构紧凑③液压马达(油缸)是大功率且经济的执行元件④在液压系统做压力控制的时候有明显的能量流失液压部分:以液体为传动介质,靠受压液体的压力能来实现运动和能量传递。
基于液压传动原理,系统能够根据机械装备的要求,对位置、速度、加速度、力等被控量按一定的精度进行控制,并且能在有外部干扰的情况下,稳定、准确的工作,实现既定的工艺目的。
(工控网)液压伺服阀是输出量与输入量成一定函数关系,并能快速响应的液压控制阀,是液压伺服系统的重要元件。
电液伺服系统在数控机床中的应用
电液伺服系统在数控机床中的应用伺服系统是一种通过感应和响应外部信号来调整输出的自动控制系统。
电液伺服系统是一种使用电力和液压传动技术的伺服系统,被广泛应用于数控机床中。
本文将探讨电液伺服系统在数控机床中的应用,并介绍其优势和发展趋势。
一、电液伺服系统的工作原理电液伺服系统主要由电液伺服阀、液压伺服缸、传感器、执行器和控制器等组成。
其工作原理是:控制器通过传感器获得外部输入信号,然后将信号传递给电液伺服阀。
电液伺服阀根据接收到的信号来控制油路的开闭,调节液压伺服缸的运动。
液压伺服缸将运动转化为力或位移输出,从而实现对机械装置的精确控制。
二、1. 位置控制:电液伺服系统通过精确的位置控制能够实现数控机床的高精度加工。
通过传感器获得工作台或刀具的位置信号,控制器根据设定值对电液伺服阀进行控制,使得机械装置按照预定的路径和速度进行准确定位。
2. 速度控制:电液伺服系统能够实现数控机床的平稳加速和减速操作。
控制器根据设定值对电液伺服阀进行控制,调节液压伺服缸的运动速度,从而实现对机械加工的平滑速度控制。
3. 力控制:电液伺服系统能够实现数控机床的精确力控制。
通过传感器获取工作台或刀具的力信号,控制器根据设定值对电液伺服阀进行控制,调节液压伺服缸的输出力,确保机械装置对工件施加恰当的力。
4. 自动化操作:电液伺服系统能够实现数控机床的自动化操作。
通过控制器中预设的程序,可以实现自动切换刀具、自动换夹具、自动调整加工参数等功能,提高了数控机床的生产效率和加工质量。
三、电液伺服系统的优势1. 高精度:电液伺服系统具有响应速度快、位置控制精度高的特点,可以满足数控机床对于精密加工的要求。
2. 高可靠性:电液伺服系统由于采用了液压传动技术,具有承受高负载和冲击的能力,能够适应数控机床长时间、高负荷运行的需求。
3. 高适应性:电液伺服系统能够适应不同的加工需求,通过调整控制器中的参数实现不同的运动模式和控制策略。
4. 易于维护:电液伺服系统的设计相对简单,维修和更换零部件相对容易,能够降低机床维护成本和停机时间。
- 1、下载文档前请自行甄别文档内容的完整性,平台不提供额外的编辑、内容补充、找答案等附加服务。
- 2、"仅部分预览"的文档,不可在线预览部分如存在完整性等问题,可反馈申请退款(可完整预览的文档不适用该条件!)。
- 3、如文档侵犯您的权益,请联系客服反馈,我们会尽快为您处理(人工客服工作时间:9:00-18:30)。
第七章 电液伺服控制系统的应用实例 7.1 引例图7-1 阀控油缸闭环控制系统原理图此图为采用电液伺服阀控制的液压缸速度闭环控制系统。
这一系统不仅使液压缸速度能任意调节,而且在外界干扰很大(如负载突变)的工况下,仍能使系统的实际输出速度与设定速度十分接近,即具有很高的控制精度和很快的响应性能。
工作原理如下:在某一稳定状态下,液压缸速度由测速装置测得(齿条1、齿轮2和测速发电机3)并转换为电压。
这一电压与给定电位计4输入的电压信号进行比较。
其差值经积分放大器放大后,以电流输入给电液伺服阀6。
电液伺服阀按输入电流的大小和方向自动地调节其开口量的大小和移动方向,控制输出油液的流量大小和方向。
对应所输入的电流,电液伺服阀的开口量稳定地维持在相应大小,伺服阀的输出流量一定,液压缸速度保持为恒值。
如果由于干扰的存在引起液压缸速度增大,则测速装置的输出电压改变,而使放大器输出电流减小,电液伺服阀开口量相应减小,使液压缸速度降低,直到液压缸恢复原来的速度时,调节过程结束。
按照同样原理,当输入给定信号电压连续变化时,液压缸速度也随之连续地按同样规律变化,即输出自动跟踪输入。
通过分析上述伺服系统的工作原理,可以看出伺服系统的特点如下:(1)反馈系统:把输出量的一部分或全部按一定方式回送到输入端,并和输入信号比较,这就是反馈作用。
在上例中,反馈电压和给定电压是异号的,即反馈信号不断地抵消输入信号,这就是负反馈。
自动控制系统中大多数反馈是负反馈。
(2)靠偏差工作:要使执行元件输出一定的力和速度,伺服阀必须有一定的开口量,因此输入和输出之间必须有偏差信号。
执行元件运动的结果又试图消除这个误差。
但在伺服系统工作的任何时刻都不能完全消除这一偏差,伺服系统正是依靠这一偏差信号进行工作的。
(3)放大系统:执行元件输出的力和功率远远大于输入信号的力和功率。
其输出的能量是液压能源供给的。
7.2 车床液压仿形刀架图7-2 车床液压仿形刀架车削圆锥面时,触销沿样件的圆锥段滑动,使杠杆向上偏摆,从而带动阀芯上移,打开阀口,压力油进入液压缸上腔,推动缸体连同阀体和刀架轴向后退。
阀体后退又逐渐使阀口关小,直至关闭为止。
在溜板不断地做纵向运动的同时,触销在样板的圆锥段上不断抬起,刀架也就不断地作轴向后退运动,两运动的合成就使刀具在工件上车出BC段圆锥面。
从仿形刀架的工作过程可以看出,刀架液压缸是以一定的仿形精度按着触销输入位移信号的变化规律而动作的,所以仿形刀架液压系统是液压伺服系统。
7.3 钢带张力控制系统图7-3 钢带张力控制系统在钢带张力控制液压伺服系统中,热处理炉内的钢带张力由带钢牵引辊组2和带钢加载辊组8来确定。
用直流电机D作牵引,直流电机D作为负载,以造成所需张力。
如果用调节系统中某一部件的位置来控制张力,由于在系统中各部件惯量大,时间滞后大,控制精度低不能满足要求,故在两辊组之间设置一液压伺服张力控制系统来控制精度。
其工作原理是:在转向辊左右两侧下方各设置力传感器,把它作为检测装置,两传感器检测所得到的信号的平均值与给定信号值相比较,当出现偏差信号时,信号经电放大器放大后输入给电液伺服阀。
如果实际张力与给定值相等,则偏差信号为零,电液伺服阀没有输出,液压缸保持不动,浮动辊不动。
当张力增大时,偏差信号使电液伺服阀有一定的开口量,供给一定的流量,使液压缸向上移动,浮动辊上移,使张力减少到一定值。
反之,当张力减少时,产生的偏差信号使电液伺服阀控制液压缸向下移动,浮动辊下移,使张力增大到一定值。
因此该系统是一个恒值力控制系统。
它保证了带钢的张力符合要求,提高了钢材的质量。
7.4 水平连铸电液伺服系统应用实例水平连铸钢拉坯装置的电液伺服系统属于速度伺服系统。
水平连铸拉坯电液速度伺服系统,由电气控制部分和液压伺服驱动装置组成,其系统示意图如图7-5所示。
电气控制部分的主要装置是VC-1型电液速度控制仪。
其中有按拉坯工艺要求发出拉坯动作控制信号的速度指令设定器、功率放大回路、颤振回路和速度反馈回路等。
图7-4 水平连铸电液伺服系统示意图1.速度指令设定器;2.校正装置;3.功率放大器; 4伺服阀; 5.液压马达;6.减速机;7.速度传感器;8.切割小车;9.钢坯; 10.拉辊; 11.辅助轮; 12.结晶器; l3.钢水包水平连铸电液伺服系统的方块图,如图7-5所示。
图7-5 水平连铸电液伺服系统方块图在方块图中各环节的传递函数相应地由下列式子给出。
伺服放大器的传递函数0a0()()I s K v s =(7-1) 电液伺服阀的传递函数sv0()()1K q s sv I s T =+s(7-2) 液压马达的传递函数.m m22h h 1()2()1s D s q s s θζωω=++(7-3) 减速箱的传动比..m ()()s is θθ=(7-4) 直流测速电动机的传递函数f1c.()()V s K s θ=(7-5)衰减器的传递函数f 2H f V K V = (7-6)滤波器的传递函数v f f 2v ()()1K V s V s T s =+ (7-7) 系统开环传递函数为d 2sv sv 2h h (1)()()2(1)1(1)K T s G s H s s T s s T s ζωω+=⎛⎞++++⎜⎟⎝⎠ (7-8)式中 K ——系统开环增益,d a sv c H v m 1K K K K iK K K D =× (7-9)7.5 跑偏控制伺服系统应用实例位置伺服系统是液压伺服系统中最为常见的应用,如电弧炉炼钢电极的位置控制、液压压下装置的位置伺服控制等。
下面简要介绍带材跑偏的位置伺服控制。
钢带卷取是通过卷取机将轧制的钢带卷到卷筒上。
由于受到钢带的张力、厚度、弯曲等因素的影响,钢带会发生跑偏,即轴向对不齐。
跑偏控制的目的是,在钢带卷取过程中使钢带沿轴向对齐,避免跑偏过大造成设备损坏或断带等事故,实现钢带的自动卷齐。
图7-6 跑偏控制示意图图7-7 跑偏控制系统工作原理图系统由光电检测器、伺服放大器、电液伺服阀、液压缸、卷取机等组成,系统框图如图7-8所示。
系统的输入为钢带跑偏位移,系统的输出为卷取机轴向跟踪位移,光电检测器自动检测出钢带与卷取机沿轴向位移的偏差,并将此位移偏差信号转化为电流信号输出,此信号经放大器放大后作为电液伺服阀的差动电流,使伺服液压缸拖动卷取机纠正跑偏,从而实现钢带自动卷齐。
图7-8 系统方框图(1)系统的有关原始参数1)机组最大卷取速度 v =5m/s 。
2)与活塞相连的运动部件质量35000kg 。
3)卷取误差 P ≤±2×10-3m 。
4)钢带卷移动最大距离 s =0.15 m 。
5)最大摩擦力 F f =17500N 。
6)系统剪切频率ω0≥20 rad /s 。
7)卷筒轴向最大速度 v m =2.2×l0-2m/s 。
8)卷筒轴向最大加速度 a m =0.47m/s 2。
(2)光电检测器与放大器的传递函数光电检测器和放大器均可看作比例环节,它们串联在一起为一个比例环节,输入为偏差位移2,输出为差动电流i ,传递函数为:1e 188.6A /m I K X == (7-10)(3)电液伺服阀的传递函数 电液伺服阀的输人为差动电流i ,输出为滑阀位移2,相应的流量为Q 。
从而电液伺服阀以电流l 为输入,以流量Q 为输出的传递函数为:sv sv 2sv 2sv sv ()()2()1Q s K G s s I s ζωω=++ (7-11)其中 K SV ——为电液伺服阀的增益,K SV =l.96×10-3m 3/(s·A);w SV ——为电液伺服阀的固有频率,w SV =157rad/s ;ξSV ——为电液伺服阀的阻尼比, ξSV =0.7。
(4)液压缸的传递函数输入为流量Q ,输出为位移X ,传递函数为p p p 2p 2p p()()2()(1X s K G s s Q s s ζωω==)++ (7-12) 其中 K p ——为液压缸的增益, K p =59.5L/m 2;w SV ——为液压缸的固有频率, w SV =88rad/s ;ξp ——为液压缸的阻尼比, ξp =0.3。
(5)系统的方框图如图7-9所示。
图7-9 带钢卷取跑偏控制系统方框图系统的开环传递函数为:221sv p sv p k 1sv p 222sv sv sv p p p ()()()(2+)(2+K K K G s K G s G s s s s ωω2)ςωωςωω==++ (6-13)7.6 液压压下(即AGC)伺服系统简介轧机液压压下系统是控制大型复杂、负载力很大、扰动因素多、扰动关系复杂、控制精度和响应速度要求很高的设备,采用高精度仪表并由大中型工业控制计算机系统控制的电液伺服系统。
AGC 是厚度自动控制的简称。
液压AGC 采用了液压执行元件(压下缸)的AGC ,国内称液压压下系统。
AGC 是现代板带轧机的关键系统,其功能是不管板厚偏差的各种扰动因素如何变化,都能自动调节压下缸的位置,即轧机的工作辊间隙,从而使出口板厚恒定,保证产品的目标厚度、同板差、异板差达到性能指标要求。
(1)基本控制思想:影响板厚的各种因素集中表现在轧制力和辊缝上。
图7-10,为轧制示意及变形曲线图。
图7-10 轧制示意及变形曲线图H.来料板厚;S0.空载辊缝;P.轧制力;K.轧机的刚度;1.轧机塑性变形抗力曲线;2.轧机弹性变形曲线轧机的弹跳方程为:0/h S p K=+(7-14)式中S0——空载辊缝(mm);P——轧制压力(N);K——轧机的自然刚度(N/mm);h——出口板厚(mm)。
影响轧制力的因素是:来料厚度H的增加使P增大,轧材机械性能的变化和连轧中带材张力波动都将使P发生变化;影响辊缝的因素是:轧辊膨胀使S0减小,轧辊磨损使S0增大,轧辊偏心和油膜轴承的厚度变化会引起5(见下图)的周期变化。
在AGC系统中:h为被控制量,希望h恒定,影响板厚变化的各种因素为扰动量,扰动因素多且变化复杂,因此,AGC系统的基本控制思想是:采用位置闭环控制+扰动补偿控制。
(2)工作原理由于轧制力及其波动值很大,而轧机刚度有限,因此,扰动量中,以轧制力引起的轧机弹跳对出口板厚的影响最大。
采用位置闭环+轧制力主扰动补偿构成的液压AGC,称为力补偿AGC。
图7-11为AGC原理图。
图7-11 AGC 原理图1.伺服放大器;2.伺服阀;3.位移传感器;4.位移传感器二次仪表;5.力传感器(压头);6.力传感器二次仪表;7.补偿系数引入力补偿后,出口板厚:00m (1)0p p p h S C S C S K K K K p ΔΔΔ=+−=+−=+Δ (7-15)式中K m =K /(1-C )——称为轧机的控制刚度,K m 可以通过调整补偿系数C 加以改变:使C =1时,K =∞,意味着轧机控制刚度无穷大,即弹跳变形完全得到补偿,实现了恒辊缝轧制。