船体焊接技术要求
船体合拢通用焊接工艺

多层多道焊的焊接顺序
同一层焊道的焊 接方向要一致, 各层的焊接方向 可以相反,但是 不允许该焊缝的 每一层焊道的接 头(熄弧、燃弧) 是在同一个位置, 要错开至少50mm。
由于大电流电压施焊而导致的气孔; 由于CO2气体保护不到位而产生的气孔;
常见气孔
Porosity
Root piping
常见夹渣产生原因
由于氧化药皮未清理干净; 由于焊道表面杂物,锈等未清理干净;
常见夹渣
现场违章案例分析
焊工上岗不携带焊接辅助工具 ——手工电
焊工要做到“五带”(保温筒、刨锤、铁
常用WPS讲解
UT探伤探头形式
常见裂纹产生原因
由于对焊缝预热未到位而产生的裂纹; 由于焊缝应力未得到有效释放; 由于焊接电流过大; 由于焊缝温度迅速下降; 由于其他缺陷导致的裂纹。
常见裂纹形式
横向裂纹!
纵向裂纹!
常见气孔产生原因
由于焊道水,油,氧化物,渣子等未清理 干净而产生的气孔;
返回
典型单人式退焊法:
3 5OO )
2 5OO )
1 5OO )
( 约 长 ( 约 长 ( 约 长
焊接十字接头的焊缝,必须由双数 焊工对称完成
1
2
1
1
2
2
1
确定焊接顺序的原则
保证钢板和焊接缝一端有自由收缩的可能性。 先焊接对其他焊缝不起刚性拘束的焊缝。 在构架和板接缝焊、横
焊 立向上焊
船体大合拢焊接工艺

船体大合拢焊接工艺1概述船体大合拢焊缝就是各分段或总段在船台上进行合拢后形成的焊缝。
大接缝的质量对船体结构强度起着极其重要的影响。
船体合拢缝焊后,易引起船体变形,反变形的大小根据具体情况确定。
同时焊接时,严格执行焊接工艺确保基准线不偏移,减少大接缝的内应力,防止气孔、咬边、夹渣、未焊透、裂缝等缺陷的产生。
2焊前准备1)焊前彻底清除焊缝坡口边缘30mm范围内的水分、油污、铁锈、切割氧化皮等杂质。
2)大接缝的坡口尺寸符合CB/T3190标准要求;除采用单面衬垫焊外,大合拢焊接坡口一般应在船体结构一侧,以便于碳刨清根工作的进行;定位焊置于另一侧,正面焊缝后碳刨清根时一起刨除。
3)除封闭焊缝外,对接焊缝焊前在接缝的端头安装引、熄弧板,材质应与基材相同。
4)定位焊焊缝长度不小于30mm;影响焊接质量的定位焊,必须清除后重新定位。
5)焊接设备必须完好,能保证焊接规范参数调节灵活,保证焊接过程的稳定,确保焊接质量。
6)焊接的环境温度大于0℃,相对湿度小于90%。
手工电弧焊时风速小于5m/;CO2气体保护焊时风速不大于2m/。
当环境条件不满足要求时,应采取预热、保湿和遮蔽等防护措施。
3焊接方法为提高工效,减少焊弧变形,本船拟采用埋弧自动焊、CO2气体保护焊、CO2陶质衬垫焊、手工电弧焊等焊接方法。
1)大合拢时甲板和双层底的内底板对接缝采用CO2陶质衬垫焊打底,埋弧自动焊盖面的焊接方法。
2)在船体中部,船体底板采用CO2陶质衬垫焊,舷侧外板采用CO2陶质衬垫焊(利用CO2全方位自动焊机)。
3)在船体首部和尾部等线型变化较大部位,采用CO2气体保护焊进行焊接;在密闭和狭小空间不能采用CO2气体保护焊的部位采用手工电弧焊(碱性焊条施焊)。
4大合拢缝的焊接顺序大合拢缝的焊接应先焊总(分)段之间的壳板对接缝,再焊其结构间的对接焊缝,然后焊结构与壳板的角焊缝;先焊立角焊,后焊平角焊;手工焊时对较长的焊缝应采用分中对称分段退焊法;大合拢焊缝装配报检合格后,在24小时内进行焊接。
船体焊接

船体焊接一、总则:1、要求施工者严格按照《焊接规格表》进行施工;2、船体艏艉外板的对接缝(非自动焊拼板部分)应先焊横向焊缝,后焊纵向焊缝;3、在建造过程中,先焊对接焊缝,后焊角焊缝;4、整体建造部分和箱体分段等应从结构的中央向左右和前后逐格对称的进行焊接,由双数焊工对称施焊;5、凡超过1m以上的收缩变形量大的长焊缝,应采用分段退焊法或分中分段退焊进行焊接缝;6、在焊接过程中,先焊收缩变形量大的焊缝,再焊变形量小的焊缝;7、边箱分段、内底分段、甲板分段、艏艉分段分层建造,在合拢口两边应留出200~300mm的外板缝暂不接焊,以利合拢时装配对接,且肋骨、舱壁及平台板等结构靠近合拢口一边的角焊缝也暂不焊接,等合拢缝焊完后再焊;8、靠舷侧的内底边板与纵骨、底外板与纵骨至少要留一条纵骨暂不焊接,避免自由边波浪变形太大,不利于边箱合拢;9、二层底分段艏艉分段大合拢,边箱分段合拢的对接缝要用低氢型(碱性)焊条或用相同级别的711、712的CO2焊丝对称焊接,一次性连续焊完;10、构件、分段、分片等部件各自完工后要自检、互检、报检,把缺陷修补完毕,把合格品送下一道工序组装,没有拿到合格单的部件不能放到下一道工序组装。
二、焊接材料使用范围的规定(一)焊接下列船体结构和部件应采用低氢型焊条(碱性焊条)或相同级别的711、712系列的CO2焊丝。
1、船体环型对接焊缝,中桁材对接缝,合拢口处骨材对接焊缝;2、主机座及其相连接的构件;3、艏柱、艉柱、艉轴管、美人架等;4、桅杆座及腹板、带缆桩、导缆孔、锚机座、链闸及其座板等;5、艉拖沙与外板结构等;6、上下舵杆与法兰,舵杆套管与船体结构之间的连接。
(二)普通钢结构的焊接用酸性E4303焊条焊接或JM-56系列CO2焊丝焊接;(三)埋弧自动拼板,板厚≥8mm,用Ф4.0mm焊丝焊接,板厚5~8mm,用Ф3.2mm焊丝焊接;三、间断焊角接焊缝,局部加强焊的规定1)组合桁材、强横梁、强肋骨的腹板与面板的角焊接缝在肘板区域内应为双面连续焊;2)桁材、肋板、强横梁、强肋骨的端部加强焊长度应不小于腹板的高度,但间断的旁桁材端部可适当减小但要≥300mm;3)纵骨切断处端部的加强焊长度应不小于1个肋距;4)骨材端部削斜时,其加强焊长度不小于削斜长度,在肘板范围内应双面连续焊;5)用肘板连接的肋骨、横梁、扶强材的端部的加强焊,在肘板范围内应双面连续焊;6)各种构件的切口、切角、开孔(如流水孔、透气孔、通焊孔等)的两端应按下述长度进行包角焊;①当板厚>12mm时,包角焊长度≥75mm;②当板厚≤12mm时,包角焊长度≥50mm;7)各种构件对接接头的两侧应有一段对称的角焊缝其长度不小于75mm;四、其他的规定:1)锚机座、链闸、系缆桩底座、桅杆底座等受力部位的甲板与横梁、纵骨等是间断焊缝的应改为双面连续角缝。
(完整版)建造船舶船体焊接工艺
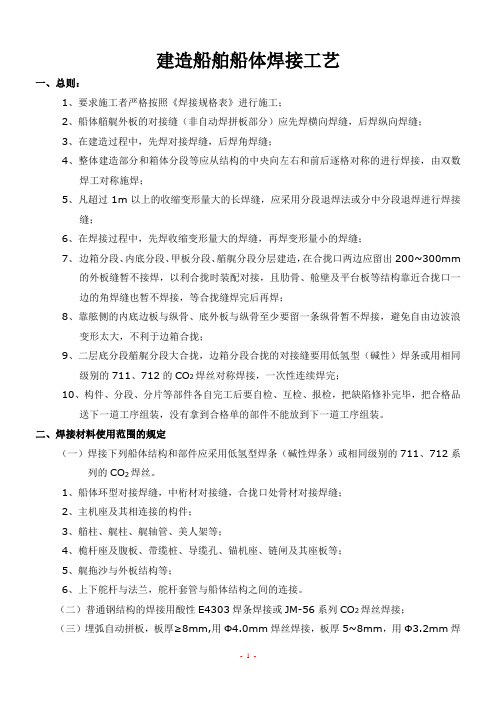
建造船舶船体焊接工艺一、总则:1、要求施工者严格按照《焊接规格表》进行施工;2、船体艏艉外板的对接缝(非自动焊拼板部分)应先焊横向焊缝,后焊纵向焊缝;3、在建造过程中,先焊对接焊缝,后焊角焊缝;4、整体建造部分和箱体分段等应从结构的中央向左右和前后逐格对称的进行焊接,由双数焊工对称施焊;5、凡超过1m以上的收缩变形量大的长焊缝,应采用分段退焊法或分中分段退焊进行焊接缝;6、在焊接过程中,先焊收缩变形量大的焊缝,再焊变形量小的焊缝;7、边箱分段、内底分段、甲板分段、艏艉分段分层建造,在合拢口两边应留出200~300mm的外板缝暂不接焊,以利合拢时装配对接,且肋骨、舱壁及平台板等结构靠近合拢口一边的角焊缝也暂不焊接,等合拢缝焊完后再焊;8、靠舷侧的内底边板与纵骨、底外板与纵骨至少要留一条纵骨暂不焊接,避免自由边波浪变形太大,不利于边箱合拢;9、二层底分段艏艉分段大合拢,边箱分段合拢的对接缝要用低氢型(碱性)焊条或用相同级别的711、712的CO2焊丝对称焊接,一次性连续焊完;10、构件、分段、分片等部件各自完工后要自检、互检、报检,把缺陷修补完毕,把合格品送下一道工序组装,没有拿到合格单的部件不能放到下一道工序组装。
二、焊接材料使用范围的规定(一)焊接下列船体结构和部件应采用低氢型焊条(碱性焊条)或相同级别的711、712系列的CO2焊丝。
1、船体环型对接焊缝,中桁材对接缝,合拢口处骨材对接焊缝;2、主机座及其相连接的构件;3、艏柱、艉柱、艉轴管、美人架等;4、桅杆座及腹板、带缆桩、导缆孔、锚机座、链闸及其座板等;5、艉拖沙与外板结构等;6、上下舵杆与法兰,舵杆套管与船体结构之间的连接。
(二)普通钢结构的焊接用酸性E4303焊条焊接或JM-56系列CO2焊丝焊接;(三)埋弧自动拼板,板厚≥8mm,用Ф4.0mm焊丝焊接,板厚5~8mm,用Ф3.2mm焊丝焊接;三、间断焊角接焊缝,局部加强焊的规定1)组合桁材、强横梁、强肋骨的腹板与面板的角焊接缝在肘板区域内应为双面连续焊;2)桁材、肋板、强横梁、强肋骨的端部加强焊长度应不小于腹板的高度,但间断的旁桁材端部可适当减小但要≥300mm;3)纵骨切断处端部的加强焊长度应不小于1个肋距;4)骨材端部削斜时,其加强焊长度不小于削斜长度,在肘板范围内应双面连续焊;5)用肘板连接的肋骨、横梁、扶强材的端部的加强焊,在肘板范围内应双面连续焊;6)各种构件的切口、切角、开孔(如流水孔、透气孔、通焊孔等)的两端应按下述长度进行包角焊;①当板厚>12mm时,包角焊长度≥75mm;②当板厚≤12mm时,包角焊长度≥50mm;7)各种构件对接接头的两侧应有一段对称的角焊缝其长度不小于75mm;四、其他的规定:1)锚机座、链闸、系缆桩底座、桅杆底座等受力部位的甲板与横梁、纵骨等是间断焊缝的应改为双面连续角缝。
船舶焊接修理技术要求
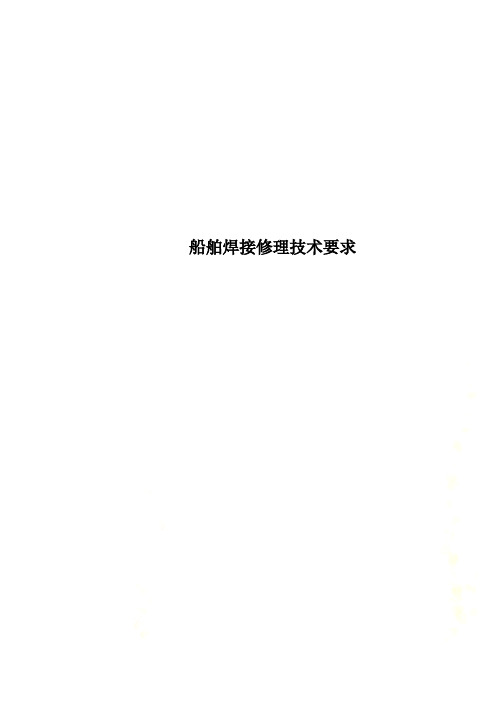
船舶焊接修理技术要求船舶焊接修理技术要求2.1对焊工要求关于影响水密的焊缝、强力构件的对接缝(外板、甲板、内底板、舱壁板等)等位置的焊接,焊工必须配带必要工具。
施焊前应检查施工区域的环境卫生及风力和风向,并采取一定的防预措施,这是保证焊缝质量的前提条件。
1)使用普通焊条(如J422)时,焊工必须带木质焊条盒、钢丝刷、尖嘴榔头等。
2)使用低氢焊条(如J506)时,焊工必须带保温筒(通电使用)、钢丝刷、尖嘴榔头等。
2.2 焊缝表面的修整要求:理论上,焊接后焊缝表面应为非磨削面。
但焊缝表面及周围的焊接飞溅应用工具或尖锤铲除掉。
不论角焊缝或对接焊缝,其表面的不平整度超过3mm 时,应将其打磨至小于3mm止。
焊接坡口的粗糙度应小于1.5mm,当超出要求时,必须打磨光滑。
2.3 船体结构的焊接变形原因及分类产生变形的原因:焊接过程是一种对金属不均匀加热和冷却的过程,在焊接过程中存在着固相向液相的转变,以及液相向固相逆转变,而且是在瞬间发生的;钢材经过焊接加热后,会有金相组织的变化,而且造成残余应力导致变形。
金属结构在焊接时产生的应力和结构变形,其主要原因是焊接时加热不均匀及加热部分的钢性拘束所形成的。
变形的分类:大致可分为纵向收缩变形、横向收缩变形、弯曲变形、扭曲变形和波浪变形五类。
减少结构件的应力集中的措施:A.对接接头,因传力均匀,疲劳强度较高,但易受焊接缺陷的影响。
在承受动载荷的焊件中,要铲除未焊透的焊口,补焊焊根、并将焊缝表面凸起部分刨平。
不同厚度板料对接时,应按1:4的坡度从焊缝削薄,使传力均匀。
另采用斜焊缝对接。
B.搭接接头的正面焊缝,增加与外载力线相平行的角边长度,表面成凹形,使截面变换平缓,且正面焊缝长度不应小于40mm。
侧面焊缝的长度不大于焊脚高度的60倍。
C.承受动载荷的钢结构,其角焊缝除前面所述措施外,还应对一般焊缝表面和棱角用砂轮磨平,将焊接板料的厚度逐渐削薄等。
D.优先选用疲劳强度较好的接头形式,如用对接代替搭接,用T字接头代替角接等。
船体结构焊接程序的基本原则
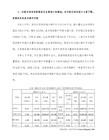
1、船体外板、甲板的对接焊缝,当是错开板缝时,先焊横向焊缝,后焊纵向焊缝;当是平列板逢时,则先焊纵向焊缝,后焊横向焊缝;
2、缝;
3、整体建造船舶或平面分段和立体分段建造时,应从结构的中央向左右和前后逐格对称的进行焊接;
8、肋骨、舱壁等结构靠近总段大接缝一边的角焊缝,以及双层底分段中内底边板与外板尚不角焊缝,一般应在大接缝焊后进行焊接;
9、应力较大的接缝,如总段的大接焊缝,焊接过程不应间断,要求连续完成;
10、分段建造中所产生的焊缝缺陷,应在上船台前修补完毕,不应集中在船台上进行。
4、具有对称中心线的构件,由双数焊工对称进行焊接;
5、手工电弧焊时,凡超过500mm的长焊缝,应采用分段退焊法或分中分段退焊法进行焊接;
6、构件中同时存在单层焊缝和多层焊缝时,先焊接收缩变形较大的多层焊缝,后焊单层焊缝;多层焊时,若条件允许,各层焊缝的焊接方向应相反,焊缝的街头互相错开;
7、分段或总段的外板纵向接缝以及纵向构件与外板的角接焊缝,其两端应留出200~300mm不焊,以利于船台装配时对接;
大型船厂船体焊接原则工艺规范
大型船厂船体焊接原则工艺规范船厂船体焊接是造船过程中的重要环节,其质量直接影响到船舶的安全性和使用寿命。
为了保证船厂船体焊接的质量,制定了一系列的工艺规范和原则。
首先,船厂船体焊接应符合国家相关的法律法规以及行业标准,如《焊接工艺规范》、《焊工技能等级表》等。
同时,还需根据具体船体结构和船舶用途确定船体焊接的工艺参数,包括焊接方法、焊接材料、焊接电流和电压等。
其次,船厂船体焊接需要进行严格的质量控制。
焊工需要经过专业的培训和资质认证,并严格按照规范进行操作。
焊接过程中需要进行焊缝的准备和清理,确保焊接区域的干净和无杂质。
焊接操作需要控制焊接速度、焊接电流和电压等参数,以确保焊缝的质量和强度。
焊接完成后,还需要进行焊缝的无损检测,如X射线检测、超声波检测等,以排除焊接缺陷和隐患。
另外,船厂船体焊接应满足船舶设计和船级社的相关要求。
船体焊接需要符合船舶结构的强度要求,并满足船级社的要求。
例如,焊接工艺应符合船级社的检验和认证要求,焊缝应满足相关的级别和质量标准。
此外,还需要考虑船舶的航行环境和使用条件,确定合适的焊缝类型和焊接方法,以提高焊缝的抗腐蚀性能和使用寿命。
最后,船厂船体焊接还需要进行全过程的质量记录和追溯。
焊接过程中需要做好焊缝的记录,包括焊接材料、焊接参数、焊工资质等。
焊缝的检测和检验结果需要记录,以便后续的质量跟踪和追溯。
总之,大型船厂船体焊接的工艺规范和原则非常重要,它直接关系到船舶的安全性和使用寿命。
船体焊接需要符合国家相关的法律法规和行业标准,严格进行质量控制,满足船舶设计和船级社的要求,并做好全过程的质量记录和追溯。
只有这样,才能确保船体焊接的质量和可靠性。
船体结构焊接要求
船体结构焊接要求1. ⽬的1.1 旨在确保焊接质量满⾜或基本达到各国船级社规范所要求的修船焊接质量标准。
2. 适⽤范围2.1 适⽤各类船舶修理中所⽤的普通结构钢,⾼强度钢的焊接施⼯。
船体结构的焊缝设计在此不作明确规定,原则上均以修理项⽬的具体⼯艺⽂件为准。
3. ⼯艺规程与检验要求3.1 施⼯前应将⼯艺⽂件和检验标准提交相应船级社认可。
⽂件中未提及的均以通⽤⼯艺为准,确保施⼯按规定的要求进⾏。
4. 焊接前的准备构件的坡⼝、装配次序、定位精度及装配间隙应符合⼯艺要求,并应避免强制装配,以减少构件的内应⼒。
若焊接坡⼝或装配间隙过⼤应按规定修正后再施焊。
施焊前焊缝坡⼝区域的铁锈、氧化⽪、油污和杂物等应予以清除,并保持清洁和⼲燥。
涂有车间底漆的钢材,如果车间底漆对焊缝质量有不良影响,则应在焊前将车间底漆清除。
当焊接必须在潮湿、多风或寒冷的露天场所进⾏时,应对焊接作业区域提供适当的遮敝和防护措施。
并保持焊接区域的⼲燥。
将焊条拿到施⼯现场时,最多只能那去半天内所使⽤的数量。
CO2陶瓷衬垫要粘贴牢固、平整且对准坡⼝中⼼,保证坡⼝清洁,随⽤随贴。
5. 焊接⼯艺要点船体重要部位的焊接须由经船级社认可的焊⼯进⾏。
普通结构钢在0℃以下施焊时应使⽤低氢型焊条。
当环境温度低于-5℃时必须按照专门的⼯艺要求采⽤预热或缓冷措施,以防焊件内产⽣冷裂纹和不良组织。
当母材的碳当量(Ceq):Ceq>0.41% 时(Ceq=C+Mn/6+ (Cr+Mo+V)/5+(Ni+Cu)/15),应对焊件进⾏预热;Ceq>0.45% 时,焊后应对焊件进⾏热处理。
所焊结构刚性过⼤、构件板厚较厚或焊段较短时,焊件应进⾏预热。
焊条吸潮过量时,焊接⼯艺性能变差,且产⽣凹坑,应在70—100℃烘⼲30~60min后使⽤。
船体结构的焊缝应按焊接程序进⾏,焊接时尽量使焊接部分⾃由收缩。
对较长的焊缝应尽可能从焊缝中间向两端施焊,对结构复杂的应先焊⽴焊再焊平⾓焊,以减少结构的变形和内应⼒。
第四章 船体结构的焊缝设计
船体结构的焊缝设计<海规>
1.一般要求
1.1 本节规定适用于一般船体结构和构件的焊缝 设计。船体结构的焊接工艺应符合CCS《材料与 焊接规范》的有关规定。 1.2 船体结构的焊缝布置应考虑便于焊工施焊。 施焊时焊缝位置尽可能采用平焊。 1.3 船体各种焊接结构应避免将焊缝布置于应力 集中区域。在结构剖面突变之处应有足够的过渡区 域,尽量避免焊缝过分集中。
2.3 船长大于或等于30m船舶的强力甲板下使用 沸腾钢的焊接,应采用低氢型焊接材料,其焊接 工艺应进行试验并经本社认可。
根据焊条药皮的性质不同,焊条可以分为酸性焊 条和碱性焊条两大类:
药皮中含有多量酸性氧化物(TiO2、SiO2 等)的焊条 称为酸性焊条。药皮中含有多量碱性氧化物(CaO、Na2O 等)的称为碱性焊条。 酸性焊条能交直流两用,焊接工艺性能较好,但焊缝 的力学性能,特别是冲击韧度较差,适用于一般低碳钢和 强度较低的低合金结构钢的焊接,是应用最广的焊条。 碱性焊条脱硫、脱磷能力强,药皮有去氢作用。焊接 接头含氢量很低,故又称为低氢型焊条。 碱性焊条的焊缝具有良好的抗裂性和力学性能,但工 艺性能较差,一般用直流电源施焊,主要用于重要结构 (如锅炉、压力容器和合金结构钢等)的焊接。
1.9 高强度钢角焊缝通常应为双面连续焊缝。 1.10 船体结构主要构件焊接的细节,包括焊缝 型式和尺寸,应清楚地标明在提交审核的图纸上。 自动焊的使用范围应在图纸上注明。
2. 焊接材料 2.1 船体结构所用的焊接材料应符合CCS 《材料与焊接规范》及其修改通报的规定。所 选用焊接材料的级别与船体结构用的钢级相适 应,并符合表4.5的规定。
× × × × × ×
× × × × × × × × × × × × × × ×
船体焊接工艺
二、船体焊接工艺1、概述本工艺对本公司在船舶建造过程中对焊工、焊接材料、焊接工艺认可,焊接程序以及焊接质量等作了规定,本工艺适用于本公司建造的集装箱船、散货船、油船以及其他类型船舶的建造。
2、对焊工的要求2.1凡在本公司建造的船舶上进行电焊的焊工应持有由CCS签发的合格焊工证书。
2.2所持证书应在有效期内。
2.3焊工在船上的允许施工范围应在焊工合格证合格项目的覆盖范围内。
3、焊接材料的选用3.1凡用于船上焊接的所有焊接材料均应符合CCS船级社的要求,并具有焊接材料合格证书;3.2手弧焊焊条牌号有J422、J507,埋弧自动焊。
焊丝牌号为H08A,配用的焊剂HJ431;3.3在下列情况必须采用碱性低氢焊条(例如J507);3.3.1船体大合拢时的环形对接缝和纵桁材的对接缝;3.3.2具有冰区加强的船舶,船体外板端接缝和边接缝;3.3.3吊艇架、系缆桩等承受强大载荷的舾装件及其所有承受高应力的零部件;3.3.4要求具有较大刚度的构件,如艏框架、艉框架等,及其与外板和船体骨架的接缝;3.3.5主机基座及其相连的构件。
4、焊接材料的保管和发放4.1进厂焊接材料应由专职检验人员进行入库检验,对焊接材料的名称、牌号、型号、规格、批号、生产日期、入库日期、有效期、生产厂等,确认后方可入库。
4.2焊材库应满足以下条件4.2.1通风良好,干燥;4.2.2室温不低于5℃,相对于湿度不大于60%;4.2.3设量货架、垫离地面、远离墙壁、采用防潮剂和去湿剂等。
4.2.4对焊条的品种分类堆放,作好标识,以防发错。
5、焊接材料的发放和领用5.1焊条在使用前应经过烘干,烘干的要求如下:5.1.1 70~150℃烘焙一小时,如包装完好,未受潮的酸性焊条,可不必烘焙;5.1.2对于碱性焊条,使用前,必须经350℃烘焙2小时,后降为150℃保温1小时,随烘随用。
5.1.3烘焙时,焊条堆放一般为1~4层,不能太厚,防止焊条受热不均匀和便于潮气的排除。
- 1、下载文档前请自行甄别文档内容的完整性,平台不提供额外的编辑、内容补充、找答案等附加服务。
- 2、"仅部分预览"的文档,不可在线预览部分如存在完整性等问题,可反馈申请退款(可完整预览的文档不适用该条件!)。
- 3、如文档侵犯您的权益,请联系客服反馈,我们会尽快为您处理(人工客服工作时间:9:00-18:30)。
船体焊接工艺
1、手工单面焊双面成形
手工单面焊双面成形是借助开有坡口的接缝处留一定的间隙,并在反面垫衬开有成形槽的铜板,在进行单面手工焊的同时强制反面成形的一种工艺方法。
手工单面焊双面成形一般用于焊缝背面难以进行刨铲焊根和封底焊的接缝,如球缘扁钢对接等,也可用于大接缝中局部甲板、平台及内底板的对接。
采用手工单面焊双面成形工艺时,应采取如下工艺措施:
(1)板厚≥4mm时应沿接缝开出不留根的V形坡口,间隙约4~6mm;
(2)接缝背面平整,焊接前用活络托架或铁楔等将铜垫固定于接缝背面并在焊接过程中保持铜垫与工件的紧贴;
(3)第一层打底焊缝是焊缝反面成形的基础。
焊接时宜采用直径较小的焊条(3~4mm)进行短弧焊接,电弧在间隙中逐渐前移,并使接缝两边边缘熔合良
好。
当一根焊条焊完后,应迅速更换焊条,在弧坑前方约10mm处引弧,逐渐
过渡到弧坑处,以防止焊接接头产生未焊透及焊缝背面成形产生凹陷及焊瘤等
缺陷。
2、立焊向下焊(即“下行焊”)
立焊向下焊是采用专用的立焊向下焊焊条,对垂直位置的焊缝由上向下进行手工电弧焊的一种工艺方法,特加适宜于薄板的垂直焊缝焊接,也可用于船体结构中不重要部位的垂直焊缝和立对接焊缝的打底焊。
采用立焊向下焊工艺时,工作效率高,焊缝美观,焊接变形小。
当进行立焊向下焊时,焊接电流应稍大些,焊条应向下倾斜,使焊条与下垂直面形成35°~85°的夹角。
运条一般不作横向摆动,直拖而下或作微小摆动,以壁免淌渣现象。
当装配间隙较大或需要较大的焊脚尺寸时,也可采用多层焊。
3、船台装焊中单面焊双面成形工艺方法的应用
船体大合拢时的内底板、甲板等对接缝,当采用单面焊双面成形工艺时,可省去仰焊封底焊缝的刨槽和施焊,显著提高生产效率和改善劳动条件。
船体大合拢时甲板、内底板对接采用单面焊双面成形方法的工艺措施如下:
(1)装配时按打底焊采用的不同焊接方法安装板缝。
当采用手工焊打底(陶质衬垫)时板缝开单边V形50°不留根坡口,间隙约4~6mm;当采用CO2气体保护半
自动焊打底(软衬垫)时,板缝开单边V形40°不留根坡口,间隙约7~9mm。
装配时用压板定位,压板间隔约250mm,背面置放衬垫时要使衬垫与板缝紧贴。
(2)当采用手工焊打底时,用直径为3~4mm的J427焊条焊第一层;当采用CO2气体保护半自动焊打底时,用直径为1.2~1.6mm的焊丝焊第一层。
第一层焊接
应注意使背面获得良好的成形。
(3)盖面焊可以根据具体情况分别采用手工焊、CO2气体保护焊或埋弧自动焊。
当采用埋弧自动焊盖面时,打底焊应有足够的厚底,不致使盖面焊时焊穿。
(4)由于船台合拢时工作环境较差,特别要注意接缝的清理。
进行CO2气体保护焊时,要采取有效的防风措施,以保证焊缝质量;
4、加铁粉埋弧自协焊单面焊双面成形
加铁粉埋弧自动焊单面焊双面成形是在接头的背面衬以带成形槽的铜垫,并在间隙和坡口中填放适量的铁粉或合金粉末,用埋弧自动焊从正面施焊,以实现单面焊双面成形的一种新工艺方法生产效率高;同时,能通过在铁粉中掺入合金的办法来调节焊缝金属的化学成份和机械性能;
加铁粉埋弧自协焊单面焊双面成形适用于胎架上分段装配中8-30mm板厚的平对接接头,也可用于平台拼板焊接。
对低碳钢及普通低合金钢都适用。
采用加铁粉埋弧自协焊单面焊双面成形的工艺措施如下:
(1)8~20mm厚的钢板不开坡口,21~30mm厚的钢板开30°不留根V形坡口,间隙均为5(+2、-1)mm。
采用10×80×150的“定位马板”对拼板接头进
行装配,在“马板”两端施定位焊。
“马板”间距约200mm。
焊接过程中边
焊边打去“马板”。
(2)将宽度为35~40mm、厚度为14mm、上面开有成形槽的铜衬垫,用接头背面点焊L形“马”并用铁楔打紧的办法,使其紧贴开接头的背面。
然后在间
隙和坡口内填加符合化学成分要求的铁粉。
对钢板厚度为20mm以下的接头,
铁粉在间隙内填加至距钢板面2mm,用埋弧自动焊方法施焊,通常可以一道
焊成;对钢板厚度为21~30mm的接头,则在坡口内适量填加铁粉,用埋弧
自动焊焊两道;
5、石英砂(或黄砂)衬垫手工电弧焊单面焊双面成形
采用石英砂(或黄砂)衬垫手工电弧焊单面焊双面成形工艺方法时,在对接接头的背面加定位“马板”以固定接头及放置石英砂(或黄砂)衬垫盒。
采用手工电弧焊方法单面焊接,第一道焊缝借接头的适当间隙及背面符合一定化学成分要求的石英砂(或黄砂)衬垫,实现单面焊双面成形。
当手工电弧焊焊完第二道后,以后各道也可采用埋弧自动焊。
石英砂(或黄砂)衬垫焊可以省去仰焊操作,当板厚较厚并由埋弧自动焊进行盖面焊时,生产效率较高。
此工艺方法适用开胎架上分段装配及船台装配中的甲板、平台板、内底板等平对接接缝。
采用石英砂(或黄砂)衬垫焊工艺方法的工艺措施如下:
(1)钢板厚度不超过20mm时,开40°不留根V形坡口,间隙约4~7mm;钢板厚度21~40mm时,开30°不留根V形坡口,间隙约5~8mm。
装配时在
接缝背面加“马板”定位,并安装石英砂(或黄砂)衬垫。
所用的石英砂或
黄砂,除符合规定的化学成和粒度外,尚需经200~300℃温度焙烘1~2小
时。
(2)接头装配后,对砂垫进行整形,然后采用手工电弧焊时行打底焊。
为使背面获得良好的成形需准确地调整焊接叁数。
操作时控制好燃弧点。
同时,要尽
可能缩短更换焊条的时间。
必要时需改进电源设备,达到在起弧的瞬间能产生
一适当时间及强度的电弧脉冲,使收弧时残留在弧坑的缩孔能在重新起弧时得
到充分的重新熔化。
当焊完第二道后,焊缝已有一定厚度,以后各道也可采用
埋弧自动焊。