线平衡分析与瓶颈改善
生产线平衡分析与改善(最全面的IE分析-生产线平衡)

2023/12/24
8
二、流水生产线概述
1、 流水生产的基本概念 ● 流水线生产的分类
➢单人单产品式 ➢单产品固定式 ➢多产品固定式 ➢自由流水式 ➢连续传动流水式 ➢ 间歇传动流水式 ➢分组式
设某一产品从原料到成品,需经过A、B、C、D四个工序,其基本标 准工时(秒/个)及相关生产效率、良率、投入机台/人员数分别见表11: 可以求各工序每小时产量为: A工序每小时产量=(3600秒÷6.90)×90%×95%×1=470.87个 B工序每小时产量=(3600秒÷5.1)×80%×99.5%×1=470.87个 C工序每小时产量=(3600秒÷34.40)×100%×99.9%×2=209.09个 D工序每小时产量=(3600秒÷30.40)×100%×99.5%×2=238.8个 。
IE工业工程
-----生产线平衡
主讲:
课 程 内容
生产线平衡 一、生产线平衡的概述 二、流水生产线概述 三、生产线平衡的设计 四、生产线平衡的方法及改善原则 5、案例分析
2023/12/24
2
1.概念
一、生产线平衡的概述
生产线平衡即对生产的全部工序进行平均化,调整作业 负荷,以使各作业的时间尽可能相近的技术手段与方法,它 是生产流程设计及作业标准化中最重要的方法,是通过平衡 生产线使现场真正实施生产同步化,从而达到“一个流”的 理想。
2023/12/24
。
28
四、生产线平衡的改善方法与原则
2、平衡率改善的图示。
2023/12/24
29
四、生产线平衡的改善方法与原则
线平衡分析与瓶颈改善

线平衡分析与瓶颈改善线平衡分析是一种优化生产线的方法,通过对生产线中各个工位的作业时间进行分析,找出生产线的瓶颈,并采取相应的改善措施,以实现整个生产线的平衡,提高生产效率和产能。
线平衡分析的目标是使每个工位的作业时间尽量接近,在不影响产品质量的前提下,提高生产线的整体效率。
一般来说,生产线的效率取决于生产线上最慢工位的作业时间,这个工位被称为瓶颈工位。
首先,进行线平衡分析需要确定生产线上每个工位的作业时间。
这可以通过观察、测量和记录每个工位的作业时间来完成。
作业时间应该包括实际操作时间、等待时间和移动时间。
然后,将这些数据绘制成柱状图或流程图,在图上标出每个工位的作业时间。
接下来,根据作业时间的差异来确定瓶颈工位。
瓶颈工位是指在制造过程中需要最长时间来完成任务的工位。
通过找出瓶颈工位,可以确定生产线的瓶颈所在,并将重点放在如何提高瓶颈工位的效率上。
一旦确定了瓶颈工位,就可以采取一些改善措施来提高其效率。
改善措施可以包括以下几个方面:1.增加资源:增加瓶颈工位的人员和设备资源,以减少瓶颈工位的等待时间和提高其作业效率。
这可能需要增加工人的数量、购置更快速或更高效的设备。
2.优化工艺:重新设计工艺流程,以减少瓶颈工位的作业时间。
这可以通过简化操作步骤、减少不必要的移动和等待时间来实现。
3.平衡工作量:将一些工作从瓶颈工位转移到其他工位,使各个工位的工作负载更均衡。
这可以通过改变工序的顺序、重新安排任务和人员来实现。
4.增加并行工位:在瓶颈工位的前后增加并行工位,以提高生产效率。
这样可以减少瓶颈工位的等待时间和生产周期。
5.增加备用设备:在瓶颈工位周围设置备用设备,以减少设备故障或维修导致的生产中断。
通过以上的改善措施,可以实现生产线的平衡,提高整体效率和产能。
然而,需要注意的是,改善一个瓶颈工位可能会导致其他工位成为新的瓶颈。
因此,线平衡分析应该是一个持续的过程,需要不断监测和改善生产线的各个方面。
瓶颈管理-生产线平衡与瓶颈改善
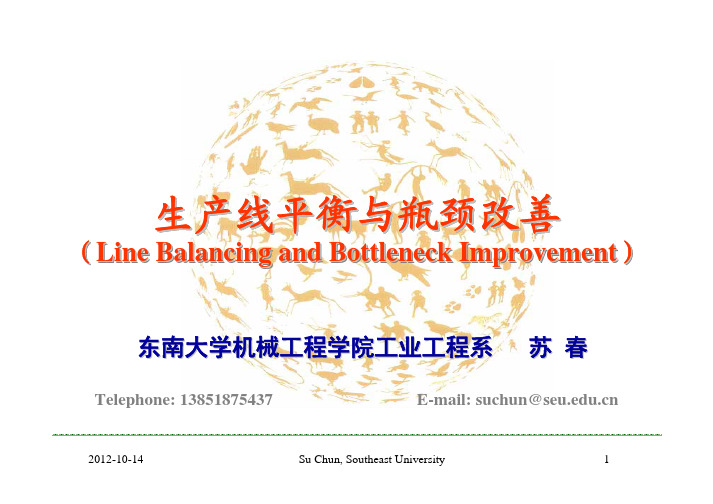
2012-10-14
Su Chun, Southeast University
16
生产线平衡分析的常用术语
1. 生产节拍(cycle time): 节拍表征生产线在规定时间内完成预定产量的能力,即各工 序完成单位产品加工所需的作业时间。
节拍=有效出勤时间/[完成产量 *(1+不良率)]
1.木桶定律: 一个木桶盛水多少,不取决于最高的那块木板,而是取决于 最短的那块木板。
2.木桶定律的三个推论: A. 只有桶壁上所有木板都足够高,木桶才
能盛更多的水。 B. 其它木板中,高出最低木板的部分是没有
意义的,并且高出越多、浪费越大。 C. 提高木桶容量最有效的办法:设法增加最
低木板的高度。
1
提纲
生产线平衡的基本概念 生产线平衡分析的常用术语 生产线平衡分析的基本方法 生产线平衡案例分析
2012-10-14
Su Chun, Southeast University
2
生产线平衡的基本概念
2012-10-14
Su Chun, Southeast University
3
木桶定律
29
生产线平衡分析的基本方法
工序工时改善的基本手段
9 减少动作次数 9 双手操作 9 缩短移动距离 9 简化动作顺序 9 采用辅助工具 9 减少换装时间 9…
2012-10-14
Su Chun, Southeast University
30
生产线平衡分析的基本方法
ECRS法则
符号
名称
说明
E
取消 Eliminate
出料
入料
2012-10-14
生产平衡分析法

生产线平衡分析与瓶颈改善
一,平衡分析用语
节拍时间=有效出勤时间/【生产计划量*(1+不良率)】
二,平衡率
平衡率=生产工序时间总和/(瓶颈工时*人数)
三,平衡改善法则(ECRS法则)
1,取消(ELiminata):取消所有没有必要的工作内容与工作环节。
2,合并(combine):如果不能取消的可以进行分析是否可以“合并”到一个工作环节。
3,重排(Rearrange):“取消”“合并”之后的工作程序还要将它进行整理重新按照合理逻辑进行重排顺序。
4,简化(Simplity):“简化”所有必须的工作环节,对程序的改进除去可以“取消”“合并”之外余下的还可以有必要的简化多余环节。
四,平衡改善法则实施步骤
1,明确改善的目的和对象
2,了解分析生产现状及相关人员工作状态
3,了解生产工艺流程并了解各工序的作业要素,根据工序分析图了解。
五,平衡生产的意义
1,提高作业员及设备工装的工作效率。
2,减少工序的在制品,真正实现“一个流”
3,减少单间产品的工时消耗,降低成本(等同于提高人均产量)
4,在平衡的生产线基础上实现单元生产,提高生产应变能力,对市场变化实现柔性生产系统。
5,通过平衡生产线可以综合应用到程序分析,动作分析,规划分析,搬运分析,时间分析等全部IE手法,提高全员综合素质。
生产线平衡分析改善案例

生产线平衡分析改善案例引言生产线平衡是指在生产过程中,通过合理分配各个工序的工作量,使得各个工序的产能能够实现平衡,从而提高生产效率、降低成本,并确保产品质量。
本文将以一个实际案例为例,介绍生产线平衡分析和改善的具体过程。
案例背景某电子产品制造公司拥有一条生产线,生产一种电子产品,该产品的组装工序分为A、B、C、D四个子工序。
在目前的生产线上,工序A的生产能力远超其他三个工序,导致A工序成为瓶颈工序,无法满足后续工序的需求,从而影响了整个生产线的效率和产量。
因此,公司决定进行生产线平衡分析,并制定改善方案,以提高生产线的平衡度。
生产线平衡分析1. 数据收集首先,需要收集工序A、B、C、D的工作时间数据,包括每个工序的加工时间、准备时间和等待时间。
这些数据将作为分析的基础。
2. 流程图绘制根据数据收集到的各个工序的时间,并结合实际生产情况,可以绘制出生产线的流程图。
流程图可以清晰地展示每个工序的工作时间和流程顺序,有助于进一步分析。
3. 生产线平衡计算根据流程图,可以计算出每个工序的工作时间总和。
然后,根据目标产量,计算出每个工序的标准工作时间,即每个工序应该占用的时间比例。
通过比较实际工作时间和标准工作时间,可以评估生产线的平衡度。
4. 分析结果根据生产线平衡计算的结果,可以看出工序A的工作时间远超其他工序,导致生产线的不平衡。
这也解释了为什么A工序成为瓶颈工序。
改善方案1. 调整工序A的产能由于工序A是瓶颈工序,可以考虑通过增加设备或优化工艺,提高工序A的产能,以满足后续工序的需求。
这可以通过增加工序A的设备数量、提高工段效率或优化工艺流程等手段实现。
2. 优化其他工序除了调整工序A的产能外,还可以进一步优化其他工序的流程,减少每个工序的工作时间。
例如,可以通过流程改进、工艺优化、培训员工等方式,提高其他工序的效率,从而平衡整个生产线。
3. 调整生产计划根据生产线平衡分析的结果,可以对生产计划进行合理调整。
生产线平衡分析与改善最全面的IE分析生产线平衡
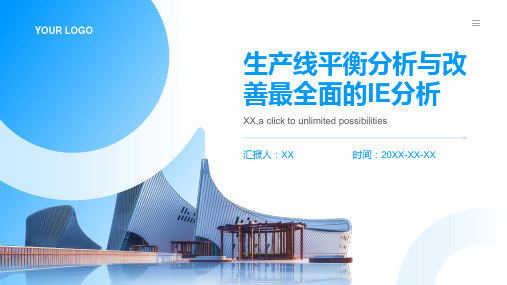
最全面的IE分 析生产线平衡 案例分析
PART 1
单击添加章节标题
P生A产R线T平2衡分析的概念和重要
性
生产线平衡分析的定义
定义:生产线平衡分析是指对生产线上的各个工 序进行平衡,使各工序的工作时间尽可能相近, 从而提高生产效率的过程。
目的:通过对生产线平衡进行分析,可以找出生 产过程中的瓶颈工序,优化生产流程,提高生产 效率,降低生产成本。
跨部门协作:加强各部门之间的沟通与协作,共同推进生产线平衡改善的实施和监控工作。
PIEA分R析T在5生产线平衡改善中的
Hale Waihona Puke 应用IE分析的基本概念和原则
IE分析的定义:工业工程分析, 旨在提高生产效率和降低生产成 本。
IE分析在生产线平衡改善中的应 用:通过分析生产线上的瓶颈、 浪费和不合理之处,提出改善方 案。
注意事项3:考虑人机配合 和作业节拍
注意事项1:分析前要明确 目标和范围
注意事项4:注意设备维护 和保养
PART 4
生产线平衡改善的策略和措施
生产线平衡改善的目标和原则
提高生产效率:通过优化生产线布局和作业分配,降低生产成本,提高产出效率。 降低不良品率:通过平衡生产线上的作业,减少生产过程中的波动和异常,降低不良品率。 提高员工满意度:通过合理分配工作量和减轻员工负担,提高员工的工作积极性和满意度。
生产线平衡分析的工具和技术
作业分析:确定每个作业步骤的时间和顺序,识别瓶颈和浪费。 工艺流程图:可视化生产线流程,找出潜在的改进点。 动作分析:研究工人操作,优化动作,提高效率。 生产计划与调度:合理安排生产计划,确保生产线的平衡。
生产线平衡分析的注意事项
注意事项2:充分了解生产 流程和工艺要求
生产线平衡分析和瓶颈改善课程
生产线平衡分析和瓶颈改善课程生产线平衡分析和瓶颈改善课程介绍生产线平衡分析和瓶颈改善是现代生产管理领域中的重要内容。
在市场竞争日益激烈的背景下,企业需要通过优化生产线,提高生产效率和产品质量,降低成本,从而提高竞争力。
因此,生产线平衡分析和瓶颈改善课程成为企业管理者和生产管理人员必备的培训项目。
课程目标生产线平衡分析和瓶颈改善课程旨在帮助学员理解生产线平衡的概念、原则和方法,并学会如何识别和消除生产线中的瓶颈,以提高生产线的总体效能。
课程将向学员提供相关工具和技术,帮助他们在实际工作中应用所学知识。
课程内容1. 生产线平衡的基本概念- 生产线平衡的定义和重要性- 生产线平衡的目标和原则- 生产线平衡和产能计划的关系2. 生产线平衡方法- 产能评估和需求预测- 工序时间测量和工序分析- 均衡方法和工作站平衡- 循序平衡线和非循序平衡线3. 瓶颈和瓶颈理论- 瓶颈的概念和特征- 瓶颈对生产线的影响- 瓶颈理论的原理和运用4. 瓶颈分析和瓶颈改善- 识别和分析瓶颈- 瓶颈改善的策略和方法- 瓶颈的管理和控制5. 实例分析和案例研究- 生产线平衡分析和瓶颈改善的实际案例- 学员将参与分组讨论和解决实际问题的案例研究课程形式为了更好地帮助学员掌握所学知识和技能,课程将采用多种教学形式和教学方法,包括讲座、案例分析、小组讨论、模拟练习和工厂参观等。
通过这些交流和互动的方式,学员将有机会亲身体验并实践所学内容。
受益人群这门课程适用于企业管理者、生产管理人员和其他对生产线平衡分析和瓶颈改善感兴趣的人士。
无论是在制造业还是在服务行业,都可以从课程中受益。
课程对参与者的角色与职务没有特定要求,只要对生产线平衡和瓶颈改善有兴趣,并且希望在工作中提高效率和竞争力,都可以报名参加。
结语生产线平衡分析和瓶颈改善课程旨在帮助企业实现生产线的优化和升级,从而提高竞争力和市场份额。
通过研究和实践,学员将掌握生产线平衡分析和瓶颈改善的核心概念和方法,并能够灵活应用于实际工作中。
线平衡分析与瓶颈改善
以及工程分析和设计的原理和方法,对该系统所取得的成果进行确定,预测和评价。
•1.2 工业工程的目标:
目标:
工业工程的目标就是设计一个生产系统及该系统的控制方法,使它以最低的成本生产 具有
特定质量水平的某种或几种产品,并且这种生产必须是在保证工人和最终用户的健康和安 全
条件下进行。
线平衡分析与瓶颈改善
2.使用秒表法测量得出的标准工时包含以下几个要素:
•观测时间
•评比因数
•宽放标准
线平衡分析与瓶颈改善
观测时间采集方法:
1. 采取适当的方位,方式及态度进行观测(斜前方2m)事先在纪录表格上记录下要观 测的作业要素及其他必要事项。 2. 多次观测,减少偶然因素的发生。即当所测的数据稳定时纪录的数据。(10times) 3. 不允许随便修改记录的时间值。 4. 去除异常值。 5. 计算平均值,得出观测时间。
•目录:
•1.工业工程概述:
1.1 工业工程的定义 1.2 工业工程的目标 1.3 工业工程的发展史
•2.标准工时基本知识介绍:
2.1 标准工时的定义 2.2 测量标准工时的基本方法
•3.线平衡分析与瓶颈改善:
3.1 线平衡的定义和意义 3.2 生产线平衡的相关概念 3.3 生产线平衡的计算 3.4 生产线平衡的改善原则 3.5 生产线平衡的改善方法
教育
等领域。
线平衡分析与瓶颈改善
•2.标准工时基本知识介绍:
2.1 标准工时的定义
定义:
在正常的操作条件下,熟练工人以标准的作业方法及合理的劳动强度和速度完成符合
质量
要求的某项工作所需作业时间。
利用动作分析、程序分析、操作分析获得最佳的程序和方法,再利用时间研究的基本
生产线平衡分析与改善方案
2019/7/14
5
二、流水生产线概述
1、 流水生产的基本概念
● 流水生产的原理
流水生产是在“分工”和“作业标准化”的原理 上发
展起来的 流水生产方式的诞生 必须依赖加工技术的支撑 流水生产方式的基础是流水生产线
2019/7/14
6
二、流水生产线概述
1、 流水生产的基本概念 ● 流水生产的特点
比较B、C两个工作站,将可发现B工作站的产能为C工作站的 2.69倍,B、C两个工作站将积压大量的半成品。若以传统追求 各工作站提升效率的方式进行管理,B工作站的效率提升,只会 恶化B、C站的半成品积压的浪费,而无助于整体产量的提高 (假设B工作站经训练生产效率达100%,则B工作站每小时产量 将达702.35个,产量为C工作站的3.36倍)。
2019/7/14
14
三、流水生产线平衡的设计方法
3、 单品种流水线平衡方法 ● 案例:生产线平衡分析案例
2019/7/14
15
三、流水生产线平衡的设计方法
3、 单品种流水线平衡方法
● 案例:生产线平衡分析案例
由表一可知A、B、C、D四个工序每小时产量处于不平衡的状态, 整体生产线的产量受限于C工序,每小时只能产出209.09个,其 他的工序的产出高于209.09个,只会堆积在生产线上而造成半成 品库存积压,而D工序更将因为C工序的产量,而形成时间的等 候。
IE工业工程
-----生产线平衡
课 程 内容
生产线平衡 一、生产线平衡的概述 二、流水生产线概述 三、生产线平衡的设计 四、生产线平衡的方法及改善原则 5、案例分析
生产线平衡分析及瓶颈改善
现场案例某企业某条生产线每月的工作天数为22天,正常工作时间每天为8小时,该生产线做A产品有5个工序,第1个工序(装配1)为28秒,第2个工序(装配2)为34秒,第3个工序(测试)为31秒,第4个工序(总装)为40秒,第4个工序(包装)为24秒),现在客户给了18000个/月的A产品订单,该生产线要如何完成任务?因为每天完不成819台的任务,该生产线的组长找人事部招了1个新员工,让这个新员工在生产线上5个工序来回帮忙,哪里做不过来就到哪里帮忙做。
生产部经理不接受生产线组长这种增加人手的做法,要求进行改善,在不增加人工成本的情况下满足客户的订单需求。
运作思路及具体工作第一步:明确改善目的和对象是否因生产量变动(增产或减产)而进行改善;是否为了提高生产率、减少作业人员;改善针对某条生产线、某段工序还是整个流程。
第二步:测量对象各工序的时间秒表法(正常的作业速度,测试20个以上工序时间,取平均值)第三步:衡量生产线平衡情况1、生产线平衡率水准平衡率<85%,水准差,90%>平衡率≥85%,良好;平衡率≥90%,属于优秀2、客户需求节拍:生产线瓶颈工时要小于客户需求节拍A产品平衡率=生产线各工序时间总和/(瓶颈工时*人员数)=(28+34+31+40+24)/(40*5)=78.5%客户需求节拍=有效出勤时间/[生产计划量*(1+不良率)]=22*8*3600/18000=35.2秒注:瓶颈工时40,客户需求节拍35.2s第四步:明确增值和非增值时间增值时间:物料加工、产品组装,质量控制及对产品有利包装。
非增值时间:包括取料距离大于60厘米,弯腰,走动,物料的质量造成的过程返工缺料的等待,停机,工装夹具的维修时间,物料和半成品的运输等。
(非增值时间:指工作中没有能改变产品特性,但目前又是不可获缺的工作,即工序中没有必要或是由于现有设备和工艺无法满足产品质量要求而设置的工作。
)第五步:通过ECRS法则改善平衡在确保人员和物料正常后,采用ECRS法则改善案例中ECRS运用符号名称说明E取消Eliminate总装中,物料放在员工身后的地上,员工弯腰取料浪费3秒时间。
- 1、下载文档前请自行甄别文档内容的完整性,平台不提供额外的编辑、内容补充、找答案等附加服务。
- 2、"仅部分预览"的文档,不可在线预览部分如存在完整性等问题,可反馈申请退款(可完整预览的文档不适用该条件!)。
- 3、如文档侵犯您的权益,请联系客服反馈,我们会尽快为您处理(人工客服工作时间:9:00-18:30)。
正态分布示意图
A wider Training Center
MAG HO 2012 Mayy 2012 9
时间测量方法-秒表法介绍
1.标准工时的计算方法: 标准工时 = 观测时间 x 评比因数 x ( 1 + 宽放标准(%) )
2.使用秒表法测量得出的标准工时包含以下几个要素:
观测时间
评比因数
A wider Training Center
MAG HO 2012 Mayy 2012 13
良 平均 可 欠佳
C1 C2 D E1 E2 F1 F2
6% 3% 0% -15% -10% -16% -22%
良 平均 可 欠佳
评价表
C1 C2 D E1 E2 F1 F2
5% 2% 0% -4% -18% -12% -17%
1.1 工业工程的定义:
定义: 工业工程是对人员、物料、 设备、能源和信息所组成的集成系统,进行设计、改善和 设置的一门学科。 它综合运用数学、物理学、经济、管理、系统工程和社会科学方面的专门知识和技术, 以及工程分析和设计的原理和方法,对该系统所取得的成果进行确定,预测和评价。
1.2 工业工程的目标:
熟练度与努力度评价基准表
熟练系数
超佳 优 良 平均 可 欠佳 A1 A2 B1 B2 C1 C2 D E1 E2 F1 F2 15% 13% 11% 8% 6% 3% 0% -15% -10% -16% -22% 超佳 优 良 平均 可 欠佳
努力系数
A1 A2 B1 B2 C1 C2 D E1 E2 F1 F2 13% 12% 10% 8% 5% 2% 0% -4% -18% -12% -17%
I E Basic Technology 工业工程基本技术 --线平衡分析与瓶颈改善
EPCOS (Zhuhai) Co., Ltd. A Member of TDK-EPC Corporation Magnetics Hongqi, China Dec 12, 2012
MAG HO 2012 Mayy 2012 1
通常不会有所犹豫 3.平均 对工作具有信心 工作速度迟缓 对工作熟悉 能够得心用手 工作成果好 4.良 能够胆任高精度的工作 可以指导他人提高操作熟练程度 非常熟悉 几乎不需要接受指导 完全不犹豫 相当稳定的速度工作 动作相当迅速 5.优 对所担任的工作有高度的适应性 能够正确地工作而不需要检查,核对 工作顺序相当正确 十分有效地使用机器设备 动作很快且正确 动作节奏快 6.超佳 有高度的技术 动作极为迅速,衔接圆滑, 动作犹如机器作业 熟练度最高 工作有节奏性 甚少浪费时间 对工作有兴趣且负责 很乐意接受建议 工作地布臵井然有序 使用适当的工具 5.优 动作很快 工作方法很系统 各个动作都很熟悉 对改进工作很有热心 6.超佳 很卖力地工作,甚至忽视健康 这种工作速度不能持续一整天 3.平均 显得有些保守 虽接受建议但不实施 工作上有良好的安排 自己拟定工作计划 评价表(续) 按良好的工作方法进行工作 4.良
MAG HO 2012 Mayy 2012 2
目录:
1.工业工程概述:
1.1 工业工程的定义
1.2 工业工程的目标
1.3 工业工程的发展史
2.标准工时基本知识介绍:
2.1 标准工时的定义 2.2 测量标准工时的基本方法
3.线平衡分析与瓶颈改善:
3.1 线平衡的定义和意义
3.2 生产线平衡的相关概念
努力的评价
1.欠佳
2.可 勉强接受建议 工作时注意力不太集中 受到生活不正常的影响 工作比较摸索 3.平均 显得有些保守 虽接受建议但不实施 工作上有良好的安排 自己拟定工作计划 按良好的工作方法进行工作 4.良 工作有节奏性 甚少浪费时间 对工作有兴趣且负责 很乐意接受建议
MAG HO 2012 Mayy 2012 14
4. 去除异常值。
5. 计算平均值,得出观测时间。
A wider Training Center
MAG HO 2012 Mayy 2012 11
时间测量记录表
爱普科斯电阻电容(珠海)有限公司
TDK (ZHUHAI) CO., LTD.
STD.Time Checking list/ 标准工时测定记录表
A wider Training Center
MAG HO 2012 Mayy 2012 8
标准时间测量的理论依据
1.标准时间测量的理论依据: 概率论与数理统计
在进行标准工时评估时所采集的数据样本,都服从正态分布。采取的数据越多,标准工 时就越接近客观值。
如取2б 的范围,即确定96%的可靠度,就是所 实现预定的抽样资料中96%以上落入2б 的范围,仅有 4%的误差。
A wider Training Center
MAG HO 2012 Mayy 2012 7
2.2 测量标准工时的基本方法
1.秒表时间研究(秒表法) 定义:秒表时间研究是作业测定技术中的一种常用方法,是在一段时间内运用秒表或电子计 时器对操作者的作业执行情况进行直接、连续地观测,把工作时间和有关工作的其他参数,以及 与标准概念相比较的对执行情况的估价的数据,一起记录下来,并结合组织所制定的宽放政策,来 确定操作者完成某项工作所需要的标准时间的方法。 特点:采用抽样技术进行研究。 测定时间的选择完全是随机的,无任何主观意图的影响,观测结果具有充分的代表 性和可靠性。
标准工时STD.Time(Min)
定额 Quota (Pcs)
对应WI版本 WI Verson A
0.0000 IE manager: Date:
FRM-V6388-A652-02A
A wider Training Center
MAG HO 2012 Mayy 2012 12
评比因数
西屋评价法(Westing house system)
目标: 工业工程的目标就是设计一个生产系统及该系统的控制方法,使它以最低的成本生产具有 特定质量水平的某种或几种产品,并且这种生产必须是在保证工人和最终用户的健康和安全 条件下进行。
A wider Training Center
MAG HO 2012 Mayy 2012 4
1.3 工业工程的发展史:
A wider Training Center
MAG HO 2012 Mayy 2012 5
2.标准工时基本知识介绍: 2.1 标准工时的定义
定义: 在正常的操作条件下,熟练工人以标准的作业方法及合理的劳动强度和速度完成符合质量 要求的某项工作所需作业时间。 利用动作分析、程序分析、操作分析获得最佳的程序和方法,再利用时间研究的基本方 法制定出标准工时。
1776年 亚当.斯密斯(Adam Smith)在《富国论》中提出了劳动分工的概念,是推动工 业化生产的一个重要里程碑。 20世纪初 美国工程师泰勒(F.W.Taylor)发表了经典著作《科学管理的原理》,系统地阐 述了科学管理思想。美国的吉尔布雷斯夫妇(Frank&Gilbreth)从事动作研究并设定了17种动 素(Threbligs)。他们都是最著名的工业工程创始人之一。 1920年 美国成立了美国工业工程师协会(American Society of Industrial Engineer,ASIE,后改为American Institute of Industrial Engineers,AIIE)。 二战以后,工业工程被引入日本并取得了成功,经过消化和改造,开创出丰田生产方式 (Toyota Production System )和全面质量管理(Total Quality Control) 等技术。随着电子 化和自动化的发展,工业工程出现了“人机工程”(又称为工效学 Ergonomics)和“系统工程” 等技术。 20世纪70年代以后至今,工业工程被全面应用于生产,服务,行政,文体,卫生,教育 等领域。
3.3 生产线平衡的计算 3.4 生产线平衡的改善原则
3.5 生产线平衡的改善方法
3.6 生产线平衡的改善步骤
3.7 生产线平衡案例分析
3.8 生产线平衡的其他约束
4.常见八大浪费介绍:
A wider Training Center
MAG HO 2012 Mayy 2012 3
1.工业工程概述:
2. Training materials and trainer
• • • • Prepared by: Reviewed by: Approved by: Final approved by: Huang haifeng Huang haifeng
பைடு நூலகம்
Part-Time Trainer:
A wider Training Center
考核员 Inspector: 生产组 Group : 产品 Product : 工装设备 Device : ),Mass order( ),Former STD( 磁芯 Core : 工序 Process : ),Other(
该表STD通用备注 Producing state remark:New part( , ),Share products:
A wider Training Center
MAG HO 2012 Mayy 2012 6
标准工时的现实意义
标准工时的现实意义: ►一个提高生产效率的重要工具 ►标准工时是企业生产系统的基础数据 ►产能预算,人力及设备需求评估的重要基础数据依据 ►改善的标准 ►生产计划工作的依据 ►评估作业者技术熟练程度和管理水平的标准 ►生产线平衡的数据标准 ►成本核算的基础数据
标准工时汇总 Standard Time Calculation List: 考核时间 评比因数 考核日期 宽放率Allowance Real Time Evaluation Date (Min/pcs) 10% 10% 10% 10% 10% 最新工时 New STD(min): IE engineer: Date: