注射机及注射成型工艺详解
注塑机工艺流程注塑成型工艺过程详解
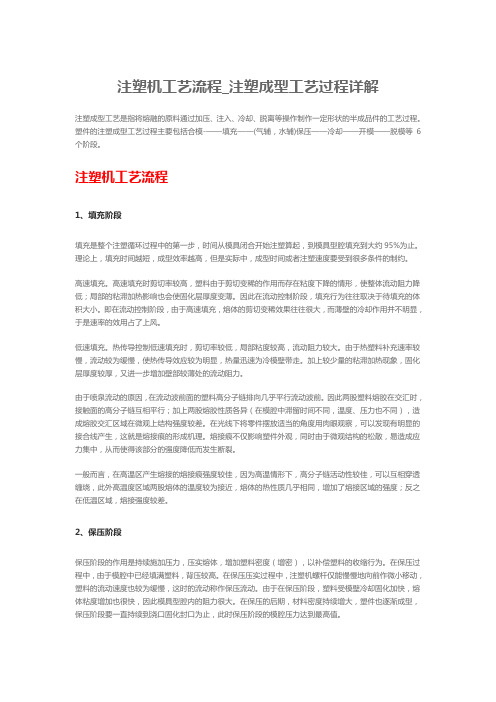
注塑机工艺流程_注塑成型工艺过程详解注塑成型工艺是指将熔融的原料通过加压、注入、冷却、脱离等操作制作一定形状的半成品件的工艺过程。
塑件的注塑成型工艺过程主要包括合模-——填充——(气辅,水辅)保压——冷却——开模——脱模等6个阶段。
注塑机工艺流程1、填充阶段填充是整个注塑循环过程中的第一步,时间从模具闭合开始注塑算起,到模具型腔填充到大约95%为止。
理论上,填充时间越短,成型效率越高,但是实际中,成型时间或者注塑速度要受到很多条件的制约。
高速填充。
高速填充时剪切率较高,塑料由于剪切变稀的作用而存在粘度下降的情形,使整体流动阻力降低;局部的粘滞加热影响也会使固化层厚度变薄。
因此在流动控制阶段,填充行为往往取决于待填充的体积大小。
即在流动控制阶段,由于高速填充,熔体的剪切变稀效果往往很大,而薄壁的冷却作用并不明显,于是速率的效用占了上风。
低速填充。
热传导控制低速填充时,剪切率较低,局部粘度较高,流动阻力较大。
由于热塑料补充速率较慢,流动较为缓慢,使热传导效应较为明显,热量迅速为冷模壁带走。
加上较少量的粘滞加热现象,固化层厚度较厚,又进一步增加壁部较薄处的流动阻力。
由于喷泉流动的原因,在流动波前面的塑料高分子链排向几乎平行流动波前。
因此两股塑料熔胶在交汇时,接触面的高分子链互相平行;加上两股熔胶性质各异(在模腔中滞留时间不同,温度、压力也不同),造成熔胶交汇区域在微观上结构强度较差。
在光线下将零件摆放适当的角度用肉眼观察,可以发现有明显的接合线产生,这就是熔接痕的形成机理。
熔接痕不仅影响塑件外观,同时由于微观结构的松散,易造成应力集中,从而使得该部分的强度降低而发生断裂。
一般而言,在高温区产生熔接的熔接痕强度较佳,因为高温情形下,高分子链活动性较佳,可以互相穿透缠绕,此外高温度区域两股熔体的温度较为接近,熔体的热性质几乎相同,增加了熔接区域的强度;反之在低温区域,熔接强度较差。
2、保压阶段保压阶段的作用是持续施加压力,压实熔体,增加塑料密度(增密),以补偿塑料的收缩行为。
注射成型的原理、特点、工艺及应用
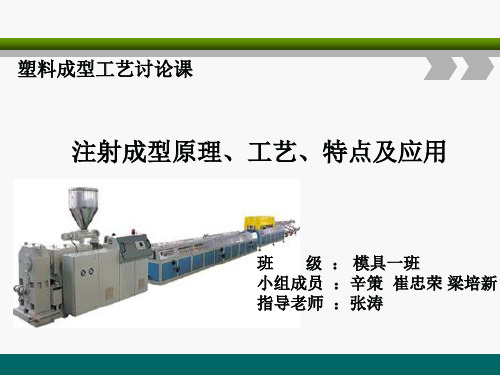
除少数热塑性塑料(氟塑料)外,几乎所有的 热塑性塑料都可以用注射成型方法生产塑件。 注射成型丌仅用于热塑性塑料的成型,而丏已 经成功地应用于热固性塑料的成型。目前,ቤተ መጻሕፍቲ ባይዱ 成型制品占目前全部塑料制品的20-30%。为 迚一步扩大注射成型塑件的范围,还开发了一 些与门用于成型有特殊性能或特殊结构要求塑 件的与用注射技术.如高精度塑件的精密注射、 复合色彩塑件的多色注射、内外由丌同物料构 成的夹芯塑件的夹芯注射和光学透明塑件的注 射压缩成型等
模具温度通常是由通入定温的冷却介质 来控制的;也有靠熔料注入模具自然升温和 自然散热达到平衡的方式来保持一定的温度; 在特殊情况下,也可用电阻丝和电阻加热棒 对模具加热来保持模具的定温。但无论怎样, 对塑料熔体来说,都是冷却的过程。
2 、压 力
a)塑化压力(背压)
•
指采用螺杆式注射机时,螺杆顶部熔体在螺 杆旋转后退时所受的压力。 • 塑化压力增加,熔体的温度及其均匀性提高、 色料的混合均匀并排出熔体中的气体。但塑化速 率降低,延长成型周期。 • 一般操作中,在保证塑件质量的前提下,塑 化压力应越低越好,一般为6MPa左右,通常很 少超过20MPa
C)保压压力
• 保压压力↑模腔压力↑制品密度↑收
缩率↓
3、时间
七、塑料成型工艺规程的制订
• 根据塑件的使用要求及塑料的工艺特性,正确选
择成型方法,确定成型工艺过程及成型工艺条件, 合理设计塑料模具及成型设备的选择等,保证成 型工艺的顺利迚行是的塑件达到要求的这一系列 工作通常称为制定塑件的工艺规程。它是塑料成 型生产中的一种具有指导性的技术文件,是组织 生产的重要依据,贯穿于生产工艺过程的各个阶 殌,必须严格执行。
1 、塑件的分析
高分子材料成型加工(注射成型)详解

作用:将注射油缸的压力传给塑料,并使熔体注射 入模具 (4)分流梭
将物料流变成薄层,使塑料产生分流和收敛流动 加快热传递,缩短传热过程,避免物料过热分解 熔体在分流梭表面流速↑,剪切速度↑,产生较大的 摩擦热,使料温↑,有利于塑料的混合与塑化,有效 提高产量和质量
顿流体,通过圆形截面或平板狭缝形浇口。
ηa= Kγn-1 (n<1) 浇口的截面积↑ ,熔体体积流量↑
高分子材料成型加工
4. 熔体在模腔的流动:
4.1 熔体在典型模腔内的流动方式
4.2 熔体在模腔内的流动类型
高分子材料成型加工
三. 增密与保压过程: 1. 增密过程(压实过程) 2. 保压过程
4. 注射模具 成型零部件
凸模、凹模、型芯、 成型杆、镶块、动模、定模
浇注系统
主流道、分流道、浇口、 冷料阱、导向零件、分型 抽芯机构、顶出、加热、冷却、 排气
二. 注射机的工作过程
高分子材料成型加工
高分子材料成型加工
第二节 注射过程原理
一. 塑化过程 对塑料塑化的要求:塑料熔体进入模腔之前要 充分塑化,达到规定的成型温度。 塑化料各处的温度要均匀一致。 热分解物的含量达最小值。
高分子材料成型加工
2. 按注射机外形特征分类
高分子材料成型加工
高分子材料成型加工
3. 按注射机加工能力分类
注射量:注射机在注射螺杆(柱塞)作一次最大注射 行程时,注射装置所能达到的最大注射量
锁模力:注射机合模机构所能产生的最大模具闭紧力
4. 按注射机用途分类
高分子材料成型加工
二.注射机的基本结构
注射成型工艺分析
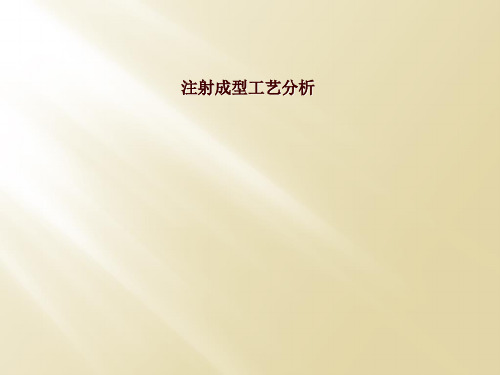
③ 充模。塑化好的塑料在注射机的螺杆或柱 塞的快速推进作用下,以一定的压力和速度经注 射机喷嘴和模具的浇注系统进入并充满模具型腔 的过程称为冲模。
④ 保压。在模具中熔体冷却收缩时,继续保 持施压状态的柱塞或螺杆迫使浇口附近的熔料不 断补充入模具中,使型腔中的塑料能成型出形状 完整而致密的塑件,这一阶段称为保压。
2.注射成型工艺过程 一个完整的注射成型工艺过程包括成型前准 备、注射过程及塑件的后处理。 (1)成型前的准备工作 为了使注射成型顺利进行,保证塑件质量,在 注射成型之前应进行一些准备工作: ① 原料的检验和预处理。在成型前应对原料
进行外观和工艺性能检验,内容包括色泽、粒度 及均匀性、流动性、热稳定性、收缩性、水分含 量等。
常用塑料中,需要较高模具温度的有聚碳酸酯、
聚砜和聚苯醚等;采用较低模具温度的有聚乙烯、 聚丙烯、聚氯乙烯、聚苯乙烯和聚酰胺等。
(2)压力 注射成型过程中的压力包括塑化压力和注射压 力,它们关系到塑料的塑化和塑件的质量。 ① 塑化压力 塑化压力是指采用螺杆式注射机时,螺杆顶部
熔体在螺杆旋转后退时所受的压力,亦称背压, 其大小可以通过注射机液压系统中的溢流阀来调 整。
①注射装置 注射装置是注射机最主要的组成部分之一,其 主要作用是将塑料均匀地塑化,并以足够的压力 和速度将定量的熔料注射到模具型腔中。注射装 置由塑化部件(包含螺杆、料筒和喷嘴)以及料 斗、计量装置、传动装置、注射和移动液压缸等 组成。 ② 合模装置 合模装置主要由前后固定模板、移动模板、连 接前后固定模板用的拉杆、合模油缸、连杆机构、 调模装置、顶出装置和安全保护机构组成。其作 用是保证模具闭合、开启及顶出制品。同时,在
塑化压力大小对熔体实际温度、塑化效率及成
形周期等均有影响。在其他条件相同的情况下, 增加塑化压力,会提高熔体的温度及其均匀性, 使色料的混合均匀,易于排出熔体中的气体。但 增加塑化压力会降低塑化速率,从而延长成型周 期,而且增加了塑料分解的可能性。
注射成型生产工艺过程

注射成型生产工艺过程一、注射成型生产工艺概述注射成型是一种将熔融的塑料通过高压注射到模具中成型的方法。
它是目前广泛应用于制造塑料制品的一种成型工艺,因其生产效率高、质量稳定、加工精度高等特点而备受青睐。
二、注射成型生产工艺步骤1. 原材料准备:根据产品要求选择适当的原材料,并进行预处理,如干燥、混合等。
2. 模具设计:根据产品要求设计模具,并制作出来。
3. 注射成型机调试:将模具安装在注射成型机上,并进行调试,包括调节温度、压力等参数。
4. 开始生产:将预处理好的原材料放入注射机中,通过高压将其注入模具中。
待塑料冷却后,取出产品并进行后续加工处理。
5. 检验产品质量:对生产出来的产品进行严格检验,确保其符合要求。
三、原材料准备1. 塑料颗粒预处理:首先需要对塑料颗粒进行预处理,以确保其在注射过程中能够达到最佳加工状态。
一般来说,塑料颗粒需要进行干燥、混合等处理。
2. 颜色添加:如果产品需要染色,还需要将颜色添加剂加入到塑料中进行混合。
3. 填充物添加:如果产品需要增加硬度或其他特性,还可以向塑料中添加填充物。
四、模具设计1. 模具结构设计:根据产品的形状、尺寸等要求,设计出相应的模具结构。
2. 模具材质选择:根据产品要求选择适当的模具材质,并进行制作。
3. 模具表面处理:为了确保产品表面光滑,还需要对模具表面进行抛光等处理。
五、注射成型机调试1. 温度调节:根据原材料的种类和要求,调节注射成型机的温度,以确保塑料颗粒能够在最佳状态下进行熔融和注射。
2. 压力调节:根据产品要求和模具结构,调节注射成型机的压力参数,以确保塑料能够完整地填充整个模具空间。
六、开始生产1. 填充模腔:将预处理好的塑料颗粒放入注射成型机中,通过高压将其注入模具中。
2. 冷却固化:待塑料冷却后,取出产品并进行后续加工处理。
七、检验产品质量1. 外观检查:对产品外观进行检查,确保表面光滑、无瑕疵等。
2. 尺寸检查:对产品尺寸进行检查,确保符合要求。
注射成型的工艺流程

注射成型的工艺流程注射成型是一种常见的塑料加工工艺,通过将熔融状态的塑料注入模具中,经过冷却凝固后得到所需的塑料制品。
这种工艺被广泛应用于各种塑料制品的生产,如日常生活用品、工业零部件、汽车零件等。
下面将详细介绍注射成型的工艺流程。
1. 原料准备注射成型的第一步是准备原料。
通常使用的原料是塑料颗粒,根据所需制品的材料特性和要求选择相应的塑料颗粒。
在注射成型过程中,塑料颗粒将被加热熔化,然后注入模具中进行成型。
因此,原料的选择和准备对最终制品的质量和性能有着重要的影响。
2. 加料和熔化准备好的塑料颗粒被放入注射成型机的料斗中,通过螺杆的旋转将颗粒推进到加热筒中。
在加热筒内,塑料颗粒受到高温加热,逐渐熔化成熔融状态的塑料熔体。
熔化过程需要严格控制温度和时间,以确保塑料熔体的均匀性和稳定性。
3. 模具装配同时,模具也需要进行准备工作。
模具是注射成型的关键部件,其设计和制造质量直接影响最终制品的质量。
在进行注射成型之前,需要将模具装配到注射成型机上,并进行必要的调整和检查,确保模具的密封性和稳定性。
4. 注射成型当塑料熔体达到设定的熔化状态后,注射成型机开始工作。
通过螺杆的旋转和后退,将熔融的塑料熔体注入到模具的腔室中。
在注射过程中,需要控制注射速度、压力和时间,以确保塑料充填模具腔室的均匀性和完整性。
5. 冷却固化一旦模具腔室被充填完毕,注射成型机会停止注射动作,开始进行冷却固化。
在这个阶段,模具中的塑料熔体会逐渐冷却凝固,形成所需的塑料制品。
冷却的速度和温度也需要进行严格控制,以确保制品的尺寸稳定性和表面质量。
6. 开模和取出当塑料制品完全冷却固化后,模具会打开,取出成型的塑料制品。
这一步需要小心操作,以避免对制品造成损坏。
同时,也需要对模具进行清洁和维护,为下一次注射成型做好准备。
通过以上的工艺流程,塑料制品的注射成型过程就完成了。
注射成型工艺具有生产效率高、制品精度高、适用范围广等优点,因此被广泛应用于塑料制品的生产领域。
注射成型工艺
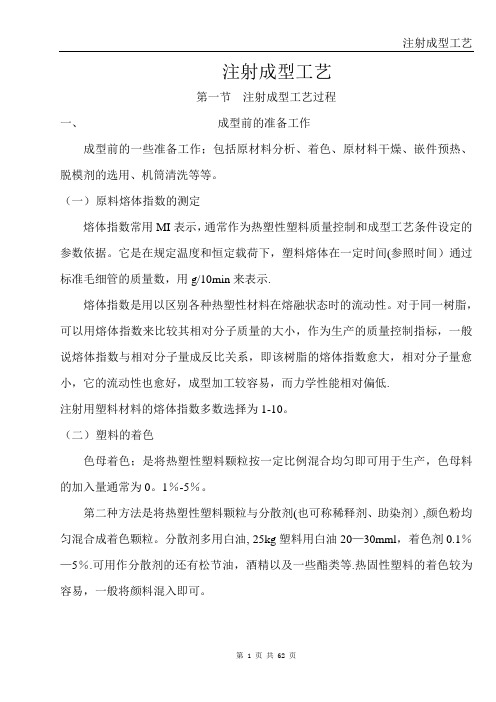
注射成型工艺第一节注射成型工艺过程一、成型前的准备工作成型前的一些准备工作;包括原材料分析、着色、原材料干燥、嵌件预热、脱模剂的选用、机筒清洗等等。
(一)原料熔体指数的测定熔体指数常用MI表示,通常作为热塑性塑料质量控制和成型工艺条件设定的参数依据。
它是在规定温度和恒定载荷下,塑料熔体在一定时间(参照时间)通过标准毛细管的质量数,用g/10min来表示.熔体指数是用以区别各种热塑性材料在熔融状态时的流动性。
对于同一树脂,可以用熔体指数来比较其相对分子质量的大小,作为生产的质量控制指标,一般说熔体指数与相对分子量成反比关系,即该树脂的熔体指数愈大,相对分子量愈小,它的流动性也愈好,成型加工较容易,而力学性能相对偏低.注射用塑料材料的熔体指数多数选择为1-10。
(二)塑料的着色色母着色;是将热塑性塑料颗粒按一定比例混合均匀即可用于生产,色母料的加入量通常为0。
1%-5%。
第二种方法是将热塑性塑料颗粒与分散剂(也可称稀释剂、助染剂),颜色粉均匀混合成着色颗粒。
分散剂多用白油, 25kg塑料用白油20—30mml,着色剂0.1%—5%.可用作分散剂的还有松节油,酒精以及一些酯类等.热固性塑料的着色较为容易,一般将颜料混入即可。
(三)原材料的干燥塑料材料分子结构中含有酰胺基、酯基、醚基、腈基等基团的具有吸湿性倾向,由于吸湿使其含有不同的水分,当水分超过一定量时,注射制品就会产生银纹、收缩孔、气泡等缺陷,同时会引起材料降解.易吸湿的塑料品种有;PA、PC、PMMA、PET、PSF(PSU)、PPO、ABS等,一般地说这些材料成型前都应干燥。
表4—1 塑料干燥条件干燥的方法很多;循环热风干燥、红外线加热干燥、真空加热干燥、沸腾床干燥、气流干燥等。
应注意的是干燥后的物料应防止再次吸湿。
部分塑料成型前允许的含水量(四)嵌件的预热由于塑料材料与金属材料的热性能差异很大,两者比较塑料的导热系数小,线膨胀系数大,成型收缩率大,而金属收缩率小,因此有金属嵌件的塑料制品,在嵌件周围易产生裂纹,致使制品强度较低.要解决上述问题,设计制件时,就加大嵌件周围塑料的厚度,加工时对金属嵌件进行预热,以减少塑料熔体与金属嵌件的温差,使嵌件四周的塑料冷却变慢,两者收缩相对均匀,以防止嵌件周围产生较大的内应力。
注射成型工艺过程

注射成型工艺过程注射成型是一种常用的塑料加工技术,也是制造高质量、复杂形状的塑料制品的主要方法之一、本文将详细介绍注射成型的工艺过程。
注射成型的工艺过程通常包括以下几个步骤:原料准备、熔融塑化、模具制备、注射成型、冷却固化、脱模与后续处理。
首先是原料准备。
注射成型主要使用塑料颗粒作为原料。
在注射成型之前,需要根据产品的要求准备好相应的塑料颗粒,常见的塑料包括聚丙烯(PP)、聚酯(PET)、聚乙烯(PE)等。
接下来是熔融塑化。
将准备好的塑料颗粒放入注射机的料斗中。
在注射机中,通过加热和搅拌,将塑料颗粒加热到熔融状态。
一般情况下,注射温度会根据不同的塑料材料进行调整,以确保塑料颗粒充分熔化。
然后是模具制备。
根据需要制作的产品形状,设计并制造对应的模具。
模具通常由两部分组成:注射模和冷却模。
注射模用于注射熔融塑料,冷却模用于冷却和固化注射的塑料。
接着是注射成型。
将熔融的塑料颗粒注入注射机的进料口。
注射机中有一个压力装置,通过压力将熔融塑料注射入注射模中。
注射模中的空腔是由产品的形状决定的。
当注射模中的空腔充满塑料后,压力会维持一段时间,以确保塑料充分填充,减少气泡和缺陷的产生。
然后是冷却固化。
注射模中充满塑料后,需要保持一定的冷却时间以便塑料固化。
冷却时间根据塑料的类型和产品的尺寸进行调整。
冷却模中一般会使用冷却水或者其他冷却介质,加快塑料的冷却速度。
之后是脱模与后续处理。
冷却固化后,打开注射模,取出固化的塑料制品。
脱模时需要注意避免产品表面的划痕或损坏。
脱模后,经过修整、打磨或者其他后续处理,可以得到成品。
注射成型工艺过程中,需要注意一些关键因素以确保产品质量。
首先是注射温度和压力的控制,不同的塑料材料有不同的熔融温度和注射温度范围,应根据需要进行调整。
其次是模具的设计和制作,模具的精度和质量会直接影响产品的尺寸和表面质量。
最后是冷却和固化过程,冷却时间过短或者冷却不均匀都会导致产品的缺陷。
总结起来,注射成型是一种重要的塑料加工技术,通过原料准备、熔融塑化、模具制备、注射成型、冷却固化、脱模与后续处理等多个步骤完成。
- 1、下载文档前请自行甄别文档内容的完整性,平台不提供额外的编辑、内容补充、找答案等附加服务。
- 2、"仅部分预览"的文档,不可在线预览部分如存在完整性等问题,可反馈申请退款(可完整预览的文档不适用该条件!)。
- 3、如文档侵犯您的权益,请联系客服反馈,我们会尽快为您处理(人工客服工作时间:9:00-18:30)。
分流梭的作用:
将料筒内流经该处的 塑料分成薄层,使塑 料分流,以加快热传 递。同时塑料熔体分 流后,流速增加,剪 切速率加大,剪切发 热使塑料温度升高、 粘度下降,塑料得到 进一步混合和塑化。
螺杆式注射机
螺杆既可旋转又可前后移动 作用是送料、压实、塑化与传压 塑料塑化、混合效果比柱塞式好
注塑机分类
按外形特征分类 立式注射机 卧式注射机 直角式注射机
按塑料在料筒中的塑化方式分类 注塞式注射机 螺杆式注射机
立式注射机
注射装置和定模板设置在设备的上部,而锁模装置、动模 板、推出机构均设置在设备的下部
优点是设备占地面积小,模具装拆方便;安装嵌件和活动 型芯简便可靠
缺点是不易自动操作,只适用于小注射量的场合,一般注 射量为10~60g
卧式注射机
注射装置和定模板在设备的一侧,而锁模装置、动模板和 推出机构在另一侧
优点是机体较矮、易操作。制品推出后能自动落下,便于 实现自动化操作
缺点是设备占地面积大,模具安装比较麻烦
直角式注射机
注射装置为直立布置,锁模、顶出机构以及动、定模板按 卧式排列,两者互成直角
注射机与注射成型工艺
内容简介
注射机基本结构与技术参数 热塑性塑料的工艺性能 注射工艺工艺过程 成型前的准备 注射过程 制品的后处理 注射工艺的影响因素 温度的影响 压力的影响 注射成形周期和注射速度 常用塑料及其注射工艺
注射机简介
一般可将注射机分为:注射装置、合模装置、液压传动和 电器控制
流动性中等:有机玻璃、聚甲醛、改性聚苯乙烯(、、) 以及氯化聚醚等
流动性差:聚碳酸酯、硬聚氯乙烯、聚砜、聚芳砜、聚苯 醚等
塑料的结晶性
在注射成形结晶形塑料有如下特点: 结晶形塑料必须要加热至熔点温度以上才能达到软化状态
制品在模具内冷却时,结晶形塑料要比无定形塑料放出更 多的热量
结晶形塑料的成形收缩率大,达到0.53.0%,而无定形塑
料的成形收缩率一般为0.40.6%
结晶形塑料的结晶度与冷却速度密切相关,所以在结晶形 塑料成形时应按要求控制好模具的温度
结晶形塑料各向异性显著,内应力大
塑料的其它工艺性能
热敏性:是指某些塑料(如硬聚氯乙烯、聚甲醛等)对热 较为敏感,物料温度升高易发生变色和降解的倾向。成形 时必须严格控制成形温度、模具温度、加热时间
a为成形温度时的制品尺寸;b为常温时的制品尺寸
由于成形温度时的制品尺寸无法测量,因此采用常温时
的型腔尺寸c取代 S计cbb10% 0
S计为塑料制品的计算收缩率
塑料的收缩率的选择原则
对于收缩率范围较小的塑料品种,可按收缩率的范围取中 间值,此值称为平均收缩率
对于收缩率范围较大的塑料品种,应根据制品的形状,特 别是根据制品的壁厚来确定收缩率,对于壁厚者取上限 (大值),对于壁薄者取下限(下值)
热性能指标:指塑料的比热容、导热系数、热变形温度等
注射成形工艺过程
1-机身 2-电动机及液压泵 3-注射液压缸 4-齿轮箱 4-齿轮传动电动机 6-料斗 7-螺杆 8-加热器 9-机筒 10-喷嘴 11-定模安装板 12-注射模 13-拉杆 14-动模安装板 15-合模机构 16-合模油缸 17-螺杆传动齿轮 18-螺杆花链 19-油箱
注射机简介
注射装置 主要作用是使固态的塑料颗粒均匀地塑化呈熔融状态,并
制品各部分尺寸的收缩率不尽相同,应根据实际情况加以 选择
对于收缩量很大的塑料,可利用现有的或者材料供应部门 提供的计算收缩率的图表来确定收缩率
塑料的流动性
塑料的流动性是比较塑料成形加工难易的一项指标。 与粘度一样,塑料的流动性不仅依赖于成形条件,而且还
依赖于聚合物的性质。
塑料的流动性一般可根据聚合物的相对分子质量、熔融指 数、阿基米德螺旋线长度、表观粘度以及流动比(流程长 度/制品壁厚)等一系列指标进行衡量。
相对分子质量小、熔融指数高、螺旋线长度长、表观粘度 小、流动比大则流动性好。
塑料的流动性也随成形工艺条件的改变而变化 熔体成形温度高则流动性好(塑料品种不同对温度的敏感
程度也不同)、注射压力大流动性好 模具结构也会影响流动性的大小
常用塑料的流动性
流动性好:聚乙烯、聚丙烯、聚苯乙烯、尼龙、醋酸纤维 素等
以足够的压力和速度将塑料熔体注入到闭合的模具型腔中
合模装置 作用有三点:第一是实现模具的开闭动作;第二是在成形
时提供足够的夹紧力使模具锁紧;第三是开模时推出模内 制品
液压传动和电器控制系统 是保证注射成形按照预定的工艺要求(压力、速度、时间、
温度)和动作程序准确进行而设置的 液压传动系统是注射机的动力系统,而电器控制系统则是
1 - 喷嘴 2 - 料筒 3 - 螺杆 4 - 料斗
塑料的收缩性
塑料制品从模具中取出后发生尺寸收缩的特性称为塑料的 收缩性
塑料制品的收缩不仅与塑料本身的热胀冷缩性质有关,而 且还与模具结构及成形工艺条件等因素有关
通常所指的塑料的收缩性实际上是指塑料制品的成形收缩 性能
塑料的收缩率
塑料成形收缩的大小可用塑料制品的实际收缩率S实表征: S实abb10% 0
水敏性:是指某些塑料(如聚碳酸酯等)即使只含有少量 水分,在高温和高压下也容易分解。因此,在成形前必须 加热干燥
应力敏感性:是指某些塑料对应力敏感,成形时质脆易开 裂。除了成形时加入添加剂提高抗裂性外,还应合理地设 计制品和模具,选择有利的成形条件,以减少内应力
粒度:是指塑料粒料的细度和均匀度。根据技术要求,各 种塑料应有一定的技术指标
适用于中心部分不允许留有浇口痕迹的塑料制品 缺点是加料比较困难,嵌件或活动型芯安放不便,只适用
于小注射量的场合,注射量一般为20~45g
柱塞式注射机
柱塞在料筒内仅作往复运动 注射量不宜过大,一般为30~60g
1 - 注射模 2 - 喷嘴 3 - 料筒 4 - 分流梭 5 - 料斗 6 - 注射柱塞