粉体自动加料系统的结构设计
自动上料配料系统方案设计

自动配料灌装生产线计量系统方案一、企业现有生产过程情况概述目前企业的生产过程基本为:粉料采用人工称料用行车或叉车人工运料、手工填料的方式,液料采用称重计量,人工泵送料,反应釜一般采用手动变频启动方式、水计量采用就地显示流量计,需要人工看数手动控制开关,从以上看出企业目前基本没有自动计量及传输控制设备。
1、现存问题(1)、人工上料,劳动强度大,速度慢;(2)、液体原料采用桶装称重计量或流量计显示,桶内残留和流量计显示误差,造成计量精度差。
(3)、整个产品生产过程采用人工手动控制,劳动强度大,差错率高,废品率高,致使产品质量控制困难大、生产效率低。
(4)、为了适应产品规模化、高质量生产的需要,系统的布局、控制模式、管理软件系统均需要有重新设计、实施。
2、用户需求分析(1)、产品规模生产要求系统具有更大的产能、更高的稳定性;(2)、降低人工上料劳动强度、提高计量精度;(3)、固体及液体物料均应自动上料、自动计量;(4)、每次生产的不同配方(原料配比)均可在电脑上进行操作;(5)、生产过程实现自动化控制。
二、本方案自动上料配料系统组成生产线配料主要完成水和4中液料的配料混合。
计量罐单独设置,液体原料分开计量加料,现场3排搅拌釜分别为1排3个搅拌罐、2 排3个搅拌罐、3排5个搅拌罐。
1、原料罐四个,分别盛放四种不同的液体原料;水料罐1个,用于暂存水,预留用水量。
现场分别在3排搅拌罐的上部设置5T原料计量罐1台,15T水计量罐1台;2、每个原料罐底部都安装有送料管道(管道口径DN65),分别由自动阀门和手动阀门控制开关,每种液料的自动阀门安装在靠近管道出口位置,由送料泵负责将料通过管道打到计量罐,送料泵两端预留回流管及回流阀(回流管口径与主管道相同),在计量罐进料口处的安装自动阀门,实现物料的快投和慢投料控制;3、液料或水通过管道可直接加进计量罐,计量罐的四个支撑底脚与支撑架基础之间各安装一只称重压力传感器模块,负责计量进入计量罐的物料重量,支撑架基础需做水平调试;4、液体原料计量完毕通过计量罐底部的的自动分流装置,分别自动加到相应的搅拌罐中。
粉料的自动配料设备与运输输送料仓
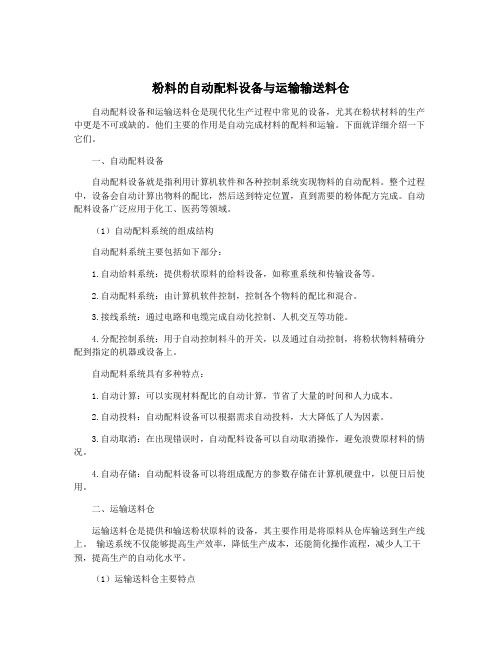
粉料的自动配料设备与运输输送料仓自动配料设备和运输送料仓是现代化生产过程中常见的设备,尤其在粉状材料的生产中更是不可或缺的。
他们主要的作用是自动完成材料的配料和运输。
下面就详细介绍一下它们。
一、自动配料设备自动配料设备就是指利用计算机软件和各种控制系统实现物料的自动配料。
整个过程中,设备会自动计算出物料的配比,然后送到特定位置,直到需要的粉体配方完成。
自动配料设备广泛应用于化工、医药等领域。
(1)自动配料系统的组成结构自动配料系统主要包括如下部分:1.自动给料系统:提供粉状原料的给料设备,如称重系统和传输设备等。
2.自动配料系统:由计算机软件控制,控制各个物料的配比和混合。
3.接线系统:通过电路和电缆完成自动化控制、人机交互等功能。
4.分配控制系统:用于自动控制料斗的开关,以及通过自动控制,将粉状物料精确分配到指定的机器或设备上。
自动配料系统具有多种特点:1.自动计算:可以实现材料配比的自动计算,节省了大量的时间和人力成本。
2.自动投料:自动配料设备可以根据需求自动投料,大大降低了人为因素。
3.自动取消:在出现错误时,自动配料设备可以自动取消操作,避免浪费原材料的情况。
4.自动存储:自动配料设备可以将组成配方的参数存储在计算机硬盘中,以便日后使用。
二、运输送料仓运输送料仓是提供和输送粉状原料的设备,其主要作用是将原料从仓库输送到生产线上。
输送系统不仅能够提高生产效率,降低生产成本,还能简化操作流程,减少人工干预,提高生产的自动化水平。
(1)运输送料仓主要特点运输送料仓具有如下特点:1.输送速度快:送料仓体积大,输送速度快,适用于大批量生产。
2.运输距离长:可实现大范围的物料输送。
3.自动化程度高:自动感知和智能控制设备实现全自动控制,节省人力成本。
4.维护服务好:送料仓采用模块化设计,能够很方便的进行维护和升级。
(2)运输送料仓的应用领域1.化工:化工厂主要生产粉状化工产品,需要大量的物料输送。
粉体配比加料系统设备工艺原理
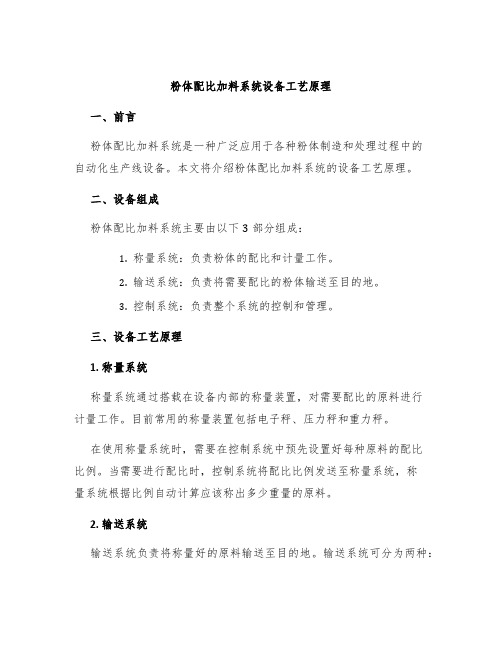
粉体配比加料系统设备工艺原理一、前言粉体配比加料系统是一种广泛应用于各种粉体制造和处理过程中的自动化生产线设备。
本文将介绍粉体配比加料系统的设备工艺原理。
二、设备组成粉体配比加料系统主要由以下3部分组成:1.称量系统:负责粉体的配比和计量工作。
2.输送系统:负责将需要配比的粉体输送至目的地。
3.控制系统:负责整个系统的控制和管理。
三、设备工艺原理1. 称量系统称量系统通过搭载在设备内部的称量装置,对需要配比的原料进行计量工作。
目前常用的称量装置包括电子秤、压力秤和重力秤。
在使用称量系统时,需要在控制系统中预先设置好每种原料的配比比例。
当需要进行配比时,控制系统将配比比例发送至称量系统,称量系统根据比例自动计算应该称出多少重量的原料。
2. 输送系统输送系统负责将称量好的原料输送至目的地。
输送系统可分为两种:1.静压输送系统:利用气泵将压缩空气推动原料向目的地输送。
2.动力推动输送系统:通过电动机驱动输送螺旋或气动活塞等装置,将原料推向目的地。
3. 控制系统控制系统是粉体配比加料系统的大脑,主要负责整个系统的控制和管理。
控制系统可分为两部分:1.电气控制系统:由PLC或其他电气控制器组成,负责控制整个系统的运行。
2.人机界面控制系统:通过触摸屏等人机界面工具,实现对设备的监控和控制。
可以对系统进行调整、监视和记录,实现全方位的控制。
四、优点和应用范围粉体配比加料系统拥有以下几个优点:1.高精度:采用计量装置配比,可以达到非常高的精度要求。
2.高效率:在粉体生产和加工中,可以充分利用自动化特点,提高生产效率。
3.全自动化:可实现无人值守,自动化程度高。
粉体配比加料系统广泛应用于各个领域,如化工、冶金、建筑材料、制药、食品等行业。
在日常生活中,粉体配比加料系统也被广泛应用于喷涂、颜料、塑料、陶瓷等领域。
五、总结本文介绍了粉体配比加料系统的设备工艺原理,以及该系统的组成、工作原理、优点和应用范围等方面的内容。
自动粉体配料系统介绍
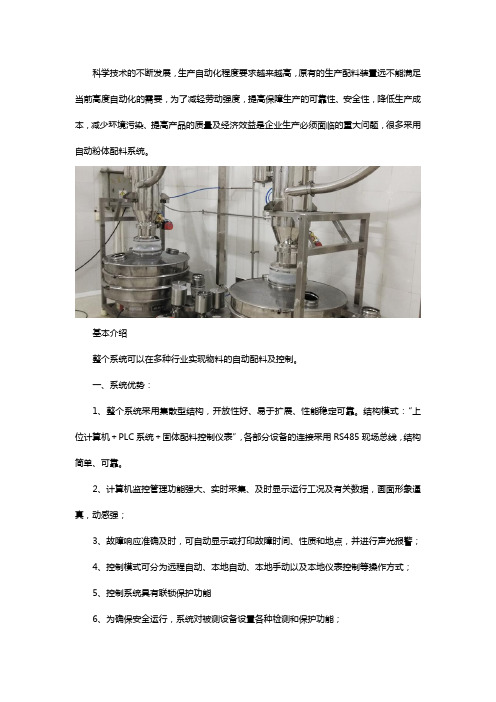
科学技术的不断发展,生产自动化程度要求越来越高,原有的生产配料装置远不能满足当前高度自动化的需要,为了减轻劳动强度,提高保障生产的可靠性、安全性,降低生产成本,减少环境污染、提高产品的质量及经济效益是企业生产必须面临的重大问题,很多采用自动粉体配料系统。
基本介绍整个系统可以在多种行业实现物料的自动配料及控制。
一、系统优势:1、整个系统采用集散型结构,开放性好、易于扩展、性能稳定可靠。
结构模式:“上位计算机+PLC系统+固体配料控制仪表”,各部分设备的连接采用RS485现场总线,结构简单、可靠。
2、计算机监控管理功能强大、实时采集、及时显示运行工况及有关数据,画面形象逼真,动感强;3、故障响应准确及时,可自动显示或打印故障时间、性质和地点,并进行声光报警;4、控制模式可分为远程自动、本地自动、本地手动以及本地仪表控制等操作方式;5、控制系统具有联锁保护功能6、为确保安全运行,系统对被测设备设置各种检测和保护功能;二、本系统人机界面的具体功能有:a.实时数据采集、显示、记录、报警b.设备状态显示、报警c.喂料参数的手动和自动调整d.实时曲线、历史曲线e.系统邦联自诊断功能三、应用:目前这一称重配料控制系统已广泛应用于建材、饲料、化工、冶金、食品等多种行业中。
它集自动控制技术、计量技术、传感器技术、计算机管理技术于一体的机电一体化系统;具有重量值数字显示、过程画面动态显示、配方修改管理、配料速度快、控制精度高等优点,采用上位计算机完全屏上控制系统,具有配料数据自动存储、配料过程清单查询和班、日、月、年报表统计及打印等功能。
系统采用开放的控制方式,兼容性强,开放的数据库,通过以太网可接入厂级局域网,可实现管控一体化。
以上就是相关内容的介绍,希望对大家了解这一问题会有更多的帮助,同时如有这方面的兴趣或需求,可以咨询了解一下官网或直接拨打南京金铂锐工业设备有限公司热线询问。
米粉自动配制机中配料装置的设计与实现

米粉自动配制机中配料装置的设计与实现南方的米粉小吃中有一道工序即向煮熟的米粉中添加各式卤菜、卤水、食用油等配料。
为了提高生产效率,节约劳动成本,针对此道工序,论文详细介绍了米粉自动配制机中配料装置的设计与实现过程,给出了配料装置的机械结构,设计了具体的称量电路,详细阐述了PLC控制过程。
经过样机制作和调试,该配料装置可以将各式配料基本适量、准确地送到碗中,该装置的设计具有一定的实际意义和推广价值。
标签:自动配料PLC控制切料拨动转轴惠斯通电桥0 引言米粉是我国南方大部分地区的主要小吃,一般一碗米粉的制作主要包括烫粉、切菜、配菜、配料等工序。
但是目前,米粉配制的每一道工序都完全由人工操作。
鉴于米粉饮食业广阔的消费市场和自动化技术的发展,以桂林米粉为主要研究对象,提出研究和设计米粉自动配制机,完全代替员工烫粉、切菜、配菜配料等。
论文主要针对米粉自动配制机中的自动配料系统进行研究与设计,该系统可以实现以下功能:第一,可以自动切削各式卤菜,如:牛肉、叉烧、锅烧等;第二,可以自动向碗中添加适量卤菜、卤水、食用油等。
米粉自动配制机的研制将紧密结合实际市场需要,用自动化机器代替人力,提高效率,降低成本。
该技术的研究将填补米粉业,甚至其他有类似工序食品行业的一项空白。
1 供料机械方案设计以桂林米粉为例,供料装置中至少需要两个加料孔,其中一个添加卤水,一个添加食用油;卤菜格子至少4个(分别放置牛肉、叉烧、锅烧等),实现一边切卤菜,一边自动添加适量卤菜到碗中。
自动添加卤菜的方案设计有两种,其一是为螺旋刀片式供料,采用螺旋绞肉,将肉绞入刀片组,其可控制物料的多少,但显然机械结构和控制都较为复杂;其二为切料拨动转轴供料,主要是将切料放在下料工序之前。
考虑到供料的多样性,并且需要准确供应物料重量,螺旋刀片式供料许多零件的制造周期较长,费用较高;只有切料撥动转轴供料体积小巧易于组装,方便控制,并且此模块具有强大的通用性,可以满足各种供料的需要。
自动配料控制系统的设计

0 引言随着计算机技术和自动化技术的发展,自动配料系统的相关技术也日益成熟,并以其计量准确、安全可靠、自动化程度高,广泛应用于化工、矿山、建材、食品、冶金、港口、电力等多种行业。
它既可以自成系统, 独立工作, 也可以接人DCS、FCS系统以下介绍的自动配料技术设计合理、精度高、运行可靠, 可完全替代进口产品。
本设计根据精细化工生产配料系统的功能要求,研究了变频调速技术在生产中的应用,根据原有的控制结构,基于PLC技术,提出了一个改进的系统控制结构,采用此体系结构实现一个自动配料系统,使之具有称重、配比、流量控制、故障检测报警及通讯功能,具有智能化程度高、控制稳定、可靠、操作维修方便等特点,对各种原料能进行精确的计量,保证化工产品准确的成分。
设计在对上述装置分析研究后在自动配料系统中进行相关应用,该系统的总体方案:自动配料控制由一个多输入,多输出,各条配料输送生产线严格协调控制,对料位、流量及时准确地进行监测和调节。
所以,系统由可编程控制器与电子皮带秤组成一个两级计算机控制系统,通过对现场总线连接现场仪器仪表、控制计算机、PLC、变频器等智能程度较高,处理速度快的设备。
1 绪论1.1 配料系统的发展情况目前, 称重配料系统的流程控制大多数由可编程控制器(PLC) 来实现, 上位计算机主要用于配方管理、屏幕人机对话和称重资料的存储打印等工作。
随着微处理器技术的发展, 配料系统中的称量仪表由最初的专用积木式仪表发展为智能化的工业控制终端以及专门的配料控制器。
配料控制器是用来控制一种或多种物料的配制的微电脑系统, 可以完全或部分取代可编程控制器, 实现配料的自动化。
称量仪表的功能也由最初的资料显示发展为具有自诊断、自动零位跟踪、置零去皮、预置点输出、动态称重、数据通信等多项功能。
近年来, 随着现场总线技术的推广, 将传统的配料控制系统改进为基于现场总线的控制系统成为科技进步的必然趋势。
目前, 许多用于配料的称重仪表已经有了Profibus、Modbus 等现场总线接口,使基于现场总线的配料控制系统成为可能, 基于现场总线的配料控制系统正在迅速推广。
自动配料模拟控制系统设计

引言自动配料控制系统是采用PLC控制方式以及新颖的变频调速喂料机构,配合配料控制软件包,实现物料传送、配料控制、配方设计、生产数据管理等功能。
并可以通过网络实现多个配料系统的集合控制。
自动配料控制系统设计步骤:1.主电路设计,并画出接线示意图。
2. 分配I/O地址,列出分配表。
3. 设计系统控制的程序框图。
4. 根据程序框图设计该系统的控制梯形图。
5. 上机调试通过。
6. 利用PLC系统进行模拟运行1自动配料控制系统结构和工作原理1.1自动配料控制系统方案系统启动后,配料装置能自动识别货车到位情况及对货车进行自动配料,当车装满时,配料系统自动关闭。
本设计的突出点是故障检测部分的设计,首先,当某一节传送带发生故障时,该节传送带和其前面的传送带会立即停止,该节之后的传送带会在一定的延时后停止。
其次,当某节传送带上的物体过重时,该节传送带和其前面的传送带会立即停止,并且数码显示电路会显示发生故障的电机的号码,该节之后的传送带会在一定的延时后停止。
1.2 自动配料控制系统基本结构自动配料的模拟面板如图1.1所示,从图中可以看出四节传送带是本次设计的核心电路,PLC编程也是围绕此面板进行的图1.1 自动配料系统图自动配料系统的功能是利用四节传送带为小车自动配料,重物通过传送带进行传输,发生故障时系统自动停机。
自动配料实验面板与PLC接线控制对应关系如表1.1.1所示。
表1.1.1 输入/输出接线列表面板SB1 SB2 S1 SQ1 SQ2 D1PLC I0.0 I0.1 I0.2 I0.4 I0.5 Q0.0面板D2 D3 D4 L1 L2 M1PLC Q0.1 Q0.2 Q0.3 Q0.4 Q0.5 Q0.6面板M2 M3 M4 A B CPLC Q0.7 Q1.0 Q1.1 I0.6 I0.7 I1.0面板 D I1.2 I1.3 I1.4 I1.51. DOP数码显示电路DOP数码显示电路如图1.2所示。
基于PLC的自动配料控制系统设计
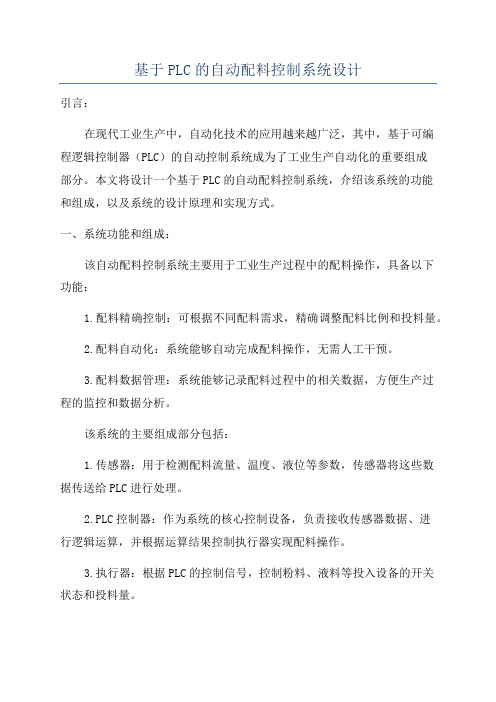
基于PLC的自动配料控制系统设计引言:在现代工业生产中,自动化技术的应用越来越广泛,其中,基于可编程逻辑控制器(PLC)的自动控制系统成为了工业生产自动化的重要组成部分。
本文将设计一个基于PLC的自动配料控制系统,介绍该系统的功能和组成,以及系统的设计原理和实现方式。
一、系统功能和组成:该自动配料控制系统主要用于工业生产过程中的配料操作,具备以下功能:1.配料精确控制:可根据不同配料需求,精确调整配料比例和投料量。
2.配料自动化:系统能够自动完成配料操作,无需人工干预。
3.配料数据管理:系统能够记录配料过程中的相关数据,方便生产过程的监控和数据分析。
该系统的主要组成部分包括:1.传感器:用于检测配料流量、温度、液位等参数,传感器将这些数据传送给PLC进行处理。
2.PLC控制器:作为系统的核心控制设备,负责接收传感器数据、进行逻辑运算,并根据运算结果控制执行器实现配料操作。
3.执行器:根据PLC的控制信号,控制粉料、液料等投入设备的开关状态和投料量。
4.人机界面:提供一个友好的操作界面,供操作员输入配料参数、查看配料数据等。
二、系统设计原理和实现方式:1.传感器的应用:通过给配料过程中的关键参数(如流量、温度、液位)配置相应的传感器,将实时的数据通过模拟量或数字量输入模块传送给PLC进行处理。
2. PLC的控制:PLC使用逻辑运算单元(Ladder Diagram)进行逻辑控制。
根据传感器数据和预设的配料参数,PLC能够判断哪些配料需要进行投料,调整投料设备的开关状态和投料量。
3.执行器的控制:PLC将控制信号发送给执行器,执行器根据信号的状态进行相应的操作,控制粉料、液料等的投入设备。
4.人机界面的设计:采用触摸屏、按钮等电子元件实现人机交互,提供一个用户友好的操作界面,操作员可以输入配料参数、查看配料数据等。
三、系统优势和应用前景:1.提高生产效率:系统能够自动完成配料操作,减少人工操作的时间和精力投入。
- 1、下载文档前请自行甄别文档内容的完整性,平台不提供额外的编辑、内容补充、找答案等附加服务。
- 2、"仅部分预览"的文档,不可在线预览部分如存在完整性等问题,可反馈申请退款(可完整预览的文档不适用该条件!)。
- 3、如文档侵犯您的权益,请联系客服反馈,我们会尽快为您处理(人工客服工作时间:9:00-18:30)。
粉体自动加料系统的结构设计
摘要本文针对粉体在包装过程中出现的偏析和架桥等问题,根据其物理特性和加料工况要求,通过理论分析,计算和结构设计,在现有的设备中进行改进,设计出一种满足使用要求的加料系统。
这种系统主要包括料仓及料斗组件和螺旋输送器,振动料斗的使用使偏析和架桥问题得到解决;螺旋输送器提高了加料精度。
关键词粉体;加料;偏析;架桥
0 引言
工程上将在常态下尺寸比较小,以粉体形式存在的固态颗粒统称为粉体物料,简称粉体。
粉体由于颗粒很小、形状很不规则、堆密度和紧实密度差异比较大,造成其内摩擦系数较大、锥角和吸附力较小,使加料过程变得相对困难[1]。
偏析和架桥是粉体处理过程中通常都会遇到的两个问题,是由于粉体流动不畅造成的。
粉体粒度分布不均匀致使流动时出现偏析,从而导致粒度大的粒子分散于边缘并浮于表层。
自由卸料时,小粒子顺利排出而大粒子之间由于相互支撑,形成球表面一一架桥。
粉体阻塞料斗排出口,导致物料无法正常排出,使粉体的运输和包装产生很大的困难[2]。
本设计以聚丙烯酰胺为例。
聚丙烯酰胺简称PAM,广泛用于水处理及电力、采矿、选煤、石棉制品、石油化工、造纸、纺织、制糖、医药、环保等领域。
1 总体方案设计
所设计的加料系统由2部分组成:1)料仓及料斗组件,用于完成储料、垂直落料和定量计量控制功能;2)螺旋填充器,用于水平输送。
该加料系统是为包装机进行定量加料而设计。
2 料斗组件的设计
料斗组件由料斗体、活化锥、激振器等组成。
料斗的落料方式有自然落料,搅动落料,吹气落料,振动落料等方式。
自然落料适用于流动性好,不容易产生起拱架桥的物料。
而搅动与吹气方式又因为与物料或者空气直接接触,对于密闭空间加料,结构要求很复杂,而且容易产生静电,仅仅适用于开放式落料和不会产生飞扬的物料。
所以本设计选择振动落料。
2.1 料斗体的设计
料斗体为倒置的截圆锥壳形钢结构。
相关资料表明,用料斗处理粉体物料的生产率与排料口直径的关系可用M≈d2.5来表示。
我们并未证实此式可否用于振
动给料,但是排料的快慢与排料口直径有着重要的关系。
料斗的主要参数有进料口直径D、排料口直径d、料斗倾斜角。
(1)根据以往的经验设计,本设计取进料口直径D=500mm,排料口直径d=150mm。
(2)料斗体斜度α。
料斗体斜度α的选择与聚丙烯酰胺和料斗材料的摩擦系数有关。
摩擦系数越大,斗体坡角也越大。
出料口直径确定后,斗体倾斜度越大,料斗高度也越大,在设计时要考虑空间位置的安排。
对于粘性大的物料,通常选择α=60°。
2.2 活化锥
活化锥是一个正圆锥形钢结构,刚性支撑在振动底斗上,与底斗保持一定的环形间隙。
作用是通过物料与其相对运动,产生破拱的效果。
它是振动料斗的重要组成部分。
活化锥主要的参数有底角β、直径d’和足隙d’[3]。
活化锥的底角β底角越大,对物料的水平振动作用越大。
对黏性大的物料活化锥底角选为45°。
活化锥直径d’决定着锥体周边与料斗体间形成的环形面积的大小。
起拱趋势大的物料,活化锥直径应取大值。
本设计中振动料斗还起截流的作用,所以停振后聚丙烯酰胺在环形缝隙之间结拱,使聚丙烯酰胺不能在惯性力的作用下继续流动。
一般活化锥直径按料斗斗体直径大小选取,,本设计取d’=200mm。
活化锥足隙是指活化锥周边对料斗体母线的垂直距离,其大小应满足加料流量的要求。
活化锥足隙越大,给料流量越大。
一般情况下,若要求料斗起闸门作用时,在料斗停止振动时,物料起拱而不再流动。
一般活化锥足隙,这里取h’=75mm。
2.3 料斗振动形式的选择
根据料斗运动形式的不同,可分为直线型、涡旋型、平旋型3种振动形式[4]。
由于平旋型破拱作用比直线型振动强,并且结构比涡旋型简单,应用最为普遍,所以此设计中我们选择平旋型振动形式。
2.4 辅助装置的设计
用人造革、帆布或者橡胶制成波形管,联接并且密封料仓与振动给料斗之间的间隙,使振动给料斗既不影响振动,又不致使物料外溢、灰尘飞扬以及有害气体逸散。
3 螺旋填充器的设计
螺旋加料装置密闭性好、使用外力驱动加料、加料速度快,技术非常成熟、结构简单且价格低廉,能进行准确的速度与位置控制。
螺旋加料器是一种常用的粉体处理设备,从螺旋输送机演变而来,采用管状料槽能实现比输送机更大的充填
率,可用于处理多种类型的粉体[5]。
3.1 螺旋输送器结构尺寸的设计
1)螺旋直径D的确定[6]
螺旋片固定在螺旋轴上面,用轴承支撑,作旋转运动。
根据以往设计,螺旋轴为直径30~35mm,长为1.5~2m的A4钢管或圆钢制成[7]。
螺旋直径的设计方法如下:
假设计量包装秤的设计生产率为每分钟20袋,每袋25kg,则螺旋输送器所要达到的输送能力应为:
一个节距内螺旋轴的体积为(2)
一个节距内螺旋轴所能输送粉体的最大重量为:
螺旋轴每秒的转速为n(r/s),则每秒内螺旋输送器所能输送粉体的重量为:
于是,根据生产效率计算的螺旋输送能力Q应和由螺旋几何尺寸所确定的输送能力相等,即:
式中: k为螺旋输送器的充填系数,对于封闭式螺旋输送器来说取0.45~0.55较为合适;
Q为螺旋输送器输送能力,kg/s ;
为聚丙烯酰胺的容重, kg/mm3;
n为螺旋轴转速, r/s;
d为螺旋轴的直径,mm。
2)螺旋节距的确定[8]
螺旋片是螺旋输送器的主要部分,材料为3~6mm厚的钢带或钢板。
螺旋片分为满面式,带式,月牙式,锯齿式。
螺旋输送器要求连续均匀的供料,满面式主要用来输送干燥的粒状,粉状及有粘附性的物料。
所以本设计中我们采用满面式螺旋片。
螺距t=0.8D。
3)旋转轴转速的确定[9]
螺旋轴的转速应在满足实际生产效率的前提下尽可能的降低,因为螺旋轴转
速过高时,螺旋叶片切线速度过高,进料口的聚丙烯酰胺因叶片的高速抛掷使螺旋输送器内容纳的聚丙烯酰胺减少而影响实际进料速度。
经实验对比,若电机的标定转速为1 500r/min,经过1∶3减速后,螺旋输送器的进料效果较好。
3.2 动力的设计[10]
动力设计的主要内容是确定螺旋轴的输入功率。
功率N0按下式计算:
式中:K1为输送物的阻力系数,与物料性质有关;L为输送机的长度;H为倾斜安置高度。
所需电机功率为:
式中:为传动装置总效率(查机械设计手册);
当时,K2=1.4;当时,K2=1.3;当时,K2=1.2
4 结论
本文介绍了粉体的基本性质,粉体特性及其对加料装置加料性能的影响是设计粉体处理装置的基础。
针对粉体的基本性质,本文在现有设备的基础上,采用振动料斗和螺旋输送器,很好的解决了包装过程中极易出现的架桥和偏析等问题。
参考文献
[1]陆厚根.粉体技术导论[M].上海同济大学出版社,1998.
[2]陶珍东.郑少华粉体工程与设备[M].北京化学工业出版社,2003.
[3]易传云,熊烽,杜润生.轻质微细物料自动加料装置的设计[J].起重运输机械,2002.
[4]张竞寰.振动给料斗[M].北京:水利电力出版社,1989.
[5]张西良.粉粒物料快速高精度自动定量充填机,2003.
[6]谭生禄,冶廷虎.原盐计量包装秤中螺旋输送器的设计计算[J].盐业与化工,2007.
[7]机械工程手册(第十二卷)[M].机械工业出版社出版, 1982.
[8]徐灏.机械设计手册(第一卷)[M].机械工业出版社, 1991.
[9]哈尔滨工业大学理论力学教研室.理论力学[M].高等教育出版社出版,1982.
[10]胡勇克,戴莉莉,皮亚南.螺旋输送器的原理与设计[J].南昌大学学报,2000.。