硅钢片铁芯叠装
发电机定子铁芯叠装工艺介绍
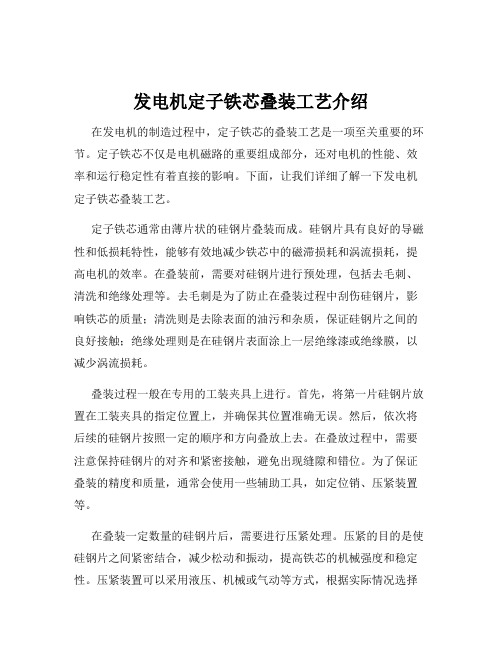
发电机定子铁芯叠装工艺介绍在发电机的制造过程中,定子铁芯的叠装工艺是一项至关重要的环节。
定子铁芯不仅是电机磁路的重要组成部分,还对电机的性能、效率和运行稳定性有着直接的影响。
下面,让我们详细了解一下发电机定子铁芯叠装工艺。
定子铁芯通常由薄片状的硅钢片叠装而成。
硅钢片具有良好的导磁性和低损耗特性,能够有效地减少铁芯中的磁滞损耗和涡流损耗,提高电机的效率。
在叠装前,需要对硅钢片进行预处理,包括去毛刺、清洗和绝缘处理等。
去毛刺是为了防止在叠装过程中刮伤硅钢片,影响铁芯的质量;清洗则是去除表面的油污和杂质,保证硅钢片之间的良好接触;绝缘处理则是在硅钢片表面涂上一层绝缘漆或绝缘膜,以减少涡流损耗。
叠装过程一般在专用的工装夹具上进行。
首先,将第一片硅钢片放置在工装夹具的指定位置上,并确保其位置准确无误。
然后,依次将后续的硅钢片按照一定的顺序和方向叠放上去。
在叠放过程中,需要注意保持硅钢片的对齐和紧密接触,避免出现缝隙和错位。
为了保证叠装的精度和质量,通常会使用一些辅助工具,如定位销、压紧装置等。
在叠装一定数量的硅钢片后,需要进行压紧处理。
压紧的目的是使硅钢片之间紧密结合,减少松动和振动,提高铁芯的机械强度和稳定性。
压紧装置可以采用液压、机械或气动等方式,根据实际情况选择合适的压紧力和压紧方式。
压紧完成后,需要对铁芯进行初步的整形和修整,去除多余的部分,使铁芯的外形尺寸符合设计要求。
接下来是铁芯的焊接或铆接工艺。
焊接可以采用电焊、氩弧焊等方式,将硅钢片之间的连接部位焊接牢固;铆接则是通过铆钉将硅钢片连接在一起。
无论是焊接还是铆接,都需要保证连接的强度和可靠性,同时要避免对铁芯的性能产生不良影响。
完成连接工艺后,需要对定子铁芯进行最后的检查和测试。
检查的内容包括铁芯的尺寸精度、外形平整度、硅钢片之间的连接质量等。
测试则主要包括铁芯的磁性能测试和绝缘性能测试等,以确保铁芯符合设计要求和相关标准。
在整个定子铁芯叠装工艺过程中,质量控制是非常重要的。
定子铁芯为什么采用硅钢片叠压而成

定子铁芯为什么采用硅钢片叠压而成常用的变压器铁芯一般都是用硅钢片制做的.硅钢是一种合硅(硅也称矽)的钢,其含硅量在0.8~4.8%。
由硅钢做变压器的铁芯,是因为硅钢本身是一种导磁能力很强的磁性物质,在通电线圈中,它可以产生较大的磁感应强度,从而可以使变压器的体积缩小.我们知道,实际的变压器总是在交流状态下工作,功率损耗不仅在线圈的电阻上,也产生在交变电流磁化下的铁芯中。
通常把铁芯中的功率损耗叫“铁损”,铁损由两个原因造成,一个是“磁滞损耗”,一个是“涡流损耗”.磁滞损耗是铁芯在磁化过程中,由于存在磁滞现象而产生的铁损,这种损耗的大小与材料的磁滞回线所包围的面积大小成正比。
硅钢的磁滞回线狭小,用它做变压器的铁芯磁滞损耗较小,可使其发热程度大大减小。
既然硅钢有上述优点,为什么不用整块的硅钢做铁芯,还要把它加工成片状呢?这是因为片状铁芯可以减小另外一种铁损——“涡流损耗"。
变压器工作时,线圈中有交变电流,它产生的磁通当然是交变的。
这个变化的磁通在铁芯中产生感应电流。
铁芯中产生的感应电流,在垂直于磁通方向的平面内环流着,所以叫涡流.涡流损耗同样使铁芯发热。
为了减小涡流损耗,变压器的铁芯用彼此绝缘的硅钢片叠成,使涡流在狭长形的回路中,通过较小的截面,以增大涡流通路上的电阻;同时,硅钢中的硅使材料的电阻率增大,也起到减小涡流的作用。
用做变压器的铁芯,一般选用0.35mm厚的冷轧硅钢片,按所需铁芯的尺寸,将它裁成长形片,然后交叠成“日”字形或“口”字形。
从道理上讲,若为减小涡流,硅钢片厚度越薄,拼接的片条越狭窄,效果越好。
这不但减小了涡流损耗,降低了温升,还能节省硅钢片的用料。
但实际上制作硅钢片铁芯时。
并不单从上述的一面有利因素出发,因为那样制作铁芯,要大大增加工时,还减小了铁芯的有效截面。
所以,用硅钢片制作变压器铁芯时,要从具体情况出发,权衡利弊,选择最佳尺寸。
变压器是根据电磁感应的原理制成的。
在在闭合的铁芯柱上面绕有两个绕组,一个原绕组,和一个副绕组.当原绕组假上交流电源电压时。
高压变压器内部结构

高压变压器内部结构
高压变压器的内部结构主要由铁芯、初级绕线组以及次级绕线组组成。
其详细介绍如下:- 铁芯:既是变压器的磁路,又是变压器的机械骨架,一般由0.22-0.5mm厚的硅钢片叠装而成。
叠装前需在硅钢片两面涂上绝缘漆,以起到绝缘效果。
- 绕组:是变压器的电路部分,一般由绝缘铜线或铝线绕制而成。
根据高、低压绕组排列方式的不同,变压器的绕组可分为同心式和交叠式两类。
- 绝缘套管:高、低压绕组引出线从油箱内部引出油箱外时必须经过绝缘套管,使引线与油箱外壳绝缘,同时起到固定引线的作用。
- 油箱及变压器油:将铁芯和绕组的整体称为器身,器身安装在贮满变压器油的油箱中。
油箱则是整个变压器的框架,它将变压器所有的零部件组合成一个整体。
- 保护装置:包括储油柜、吸湿器、气体继电器和安全气道等,主要起到保护油箱的作用。
其中,储油柜安装在油箱顶部,体积一般为油箱体积的8%-10%;吸湿器又称为呼吸器,其作用为吸掉进入油枕的空气中的水分,保证变压器油不被受潮;气体继电器和安全气道可以在变压器内部发生故障时,起到保护油箱不致爆炸的作用。
[重点]定子铁芯为什么采用硅钢片叠压而成
![[重点]定子铁芯为什么采用硅钢片叠压而成](https://img.taocdn.com/s3/m/d47be7acc5da50e2524d7fe5.png)
[重点]定子铁芯为什么釆用硅钢片叠压而成定子铁芯为什么采用硅钢片叠压而成常用的变圧器铁芯一般都是用硅钢片制做的。
硅钢是一种合硅(硅也称矽)的钢,其含硅量在0(8,4(8,。
山硅钢做变压器的铁芯,是因为硅钢本身是一种导磁能力很强的磁性物质,在通电线圈中,它可以产生较大的磁感应强度,从而可以使变圧器的体积缩小。
我们知道,实际的变圧器总是在交流状态下工作,功率损耗不仅在线圈的电阻上,也产生在交变电流磁化下的铁芯中。
通常把铁芯中的功率损耗叫“铁损”,铁损山两个原因造成,一个是“磁滞损耗”,一个是“涡流损耗”。
磁滞损耗是铁芯在磁化过程中,山于存在磁滞现象而产生的铁损,这种损耗的大小与材料的磁滞回线所包W的面积大小成正比。
硅钢的磁滞回线狭小,用它做变压器的铁芯磁滞损耗较小,可使其发热程度大大减小。
既然硅钢有上述优点,为什么不用整块的硅钢做铁芯,还要把它加工成片状呢, 这是因为片状铁芯可以减小另外一种铁损一“涡流损耗”°变压器工作时,线圈中有交变电流,它产生的磁通当然是交变的。
这个变化的磁通在铁芯中产生感应电流。
铁芯中产生的感应电流,在垂直于磁通方向的平面内环流着,所以叫涡流。
涡流损耗同样使铁芯发热。
为了减小涡流损耗,变压器的铁芯用彼此绝缘的硅钢片叠成,使涡流在狭K形的回路中,通过较小的截面,以增大涡流通路上的电阻;同时,硅钢中的硅使材料的电阻率增大,也起到减小涡流的作用。
用做变圧器的铁芯,一般选用0 (35mm )7-的冷轧硅钢片,按所需铁芯的尺寸,将它裁成长形片,然后交叠成“日”字形或“口”字形。
从道理上讲,若为减小涡流,硅钢片片度越薄,拼接的片条越狭窄,效果越好。
这不但减小了涡流损耗,降低了温升,还能节省硅钢片的用料。
但实际上制作硅钢片铁芯时。
并不单从上述的一面有利因素出发,因为那样制作铁芯,要大大增加工时,还减小了铁芯的有效截面。
所以,用硅钢片制作变压器铁芯时,要从具体情况出发,权衡利弊,选择最佳尺寸。
硅钢片叠片铁芯讲义

(3)、叠装系数高。硅钢片表面光滑,平整和厚度均匀,制造铁芯的叠 装系数提高。
(4)、冲片性好。对制造小型、微型电机铁芯,这点更重要。 (5)、表面对绝缘膜的附着性和焊接性良好。 (6)、磁时效 (7)、硅钢片须经退火和酸洗后交货
硅钢片涂有绝缘漆:其目的是限制涡流回路,使涡流只能在一片中流动,这样 涡流回路阻抗较大,限制了涡流的数值。如果片间不绝缘,涡流就会通过相邻的 硅钢片,这样涡流回路的阻抗比单片时小,涡流就会增大,使得涡流产生的损耗 迅速地增大。一般来说,涡流损耗与硅钢片的厚度成正比,如果硅钢片不绝缘, 铁心就相当于一整块铁,或相当于一块厚钢板,这样涡流损耗就会大大地增加。 因此硅钢片表面要涂漆。
3.0~4.5 0.35和0.50
≤0.5
0.50和0.65
0.5~3.2 0.35和0.50
取向硅钢
普通取向硅钢 2.9~3.3 0.20,0.23,
(冷轧变压器钢)
0.27
Issuer: Source:
Function:
高磁感取向硅 2.9~3.3 0.30和0.35 钢
Page ‹#›/1
Date saved: 18. Sep. 08
硅钢片一般随着硅的含量提高而提高,铁损、冲片性、磁感降低、硬度 增高。工作频率越高,产生的涡流损耗越大,选用的硅钢片越薄。
2、按含硅量不同 •低硅片:含硅2.8%以下,它具有一定机械强度,主要用于制造电机俗称电机 硅钢片。 •高硅片:含硅量为2.8%-4.8%,它具有磁性好,但较脆,主要用于制造变压 器铁芯,俗称变压器硅钢片
硅钢片-叠片-铁芯
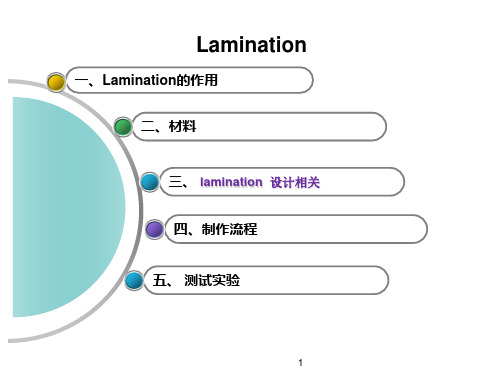
退火的目的是:冷轧带通过再结晶消除冷轧产生的应变和促使晶粒长大, 将钢中的碳脱到0.005%以下(最好在0.003%以下),以保证磁性,硬度和磁实效符合 要求条件。退火时小张力以保证钢带更平整。
二.叠片的材料
5、日本牌号表示方法:
(1)冷轧无取向硅钢带 由公称厚度(扩大100倍的值)+代号A+铁损保证值(将频率50HZ,最大 磁通密度为1.5T时的铁损值扩大100倍后的值)。 如50A470表示厚度为0.5mm,铁损保证值为≤4.7的冷轧无取向硅钢带。
MK70 localization :B 50 A1300 MK70 :JIS 50 A1000 (2)冷轧取向硅钢带 由公称厚度(扩大100倍的值)+代号G:表示普通材料,P:表示高取向 性材料+铁损保证值(将频率50HZ,最大磁通密度为1.7T时的铁损值扩 大100倍后的值)。 如30G130表示厚度为0.3mm,铁损保证值为≤1.3的冷轧取向硅钢带。
• 冷轧:把钢材加热后控制在再结晶温度以下进行轧制加工的工艺称为热轧 (a)晶粒无取向:电机或焊接变压器等 (b)晶粒取向:电源变压器、脉冲变压器和磁放大器等的铁芯,若用冷轧取向带,
性能更佳,用它代替热轧带或低档次冷轧带,可减少变压器电能消耗量45%-50%
冷轧钢
热轧钢
二.叠片的材料
冷轧电工钢带具有表面平整、厚度均匀、叠装系数高、冲片性好等特点, 且比热轧电工钢带磁感高、铁损低。
Lamination
一、Lamination的作用 二、材料 三、 lamination 设计相关 四、制作流程 五、 测试实验
1
一.叠片的作用
1.支撑段绝缘 2.和轴配合为电机提供扭矩 3.引导磁通量通过
[重点]定子铁芯为什么采用硅钢片叠压而成
![[重点]定子铁芯为什么采用硅钢片叠压而成](https://img.taocdn.com/s3/m/ab3ef9ed33687e21ae45a91e.png)
[重点]定子铁芯为什么采用硅钢片叠压而成定子铁芯为什么采用硅钢片叠压而成常用的变压器铁芯一般都是用硅钢片制做的。
硅钢是一种合硅(硅也称矽)的钢,其含硅量在0(8,4(8,。
由硅钢做变压器的铁芯,是因为硅钢本身是一种导磁能力很强的磁性物质,在通电线圈中,它可以产生较大的磁感应强度,从而可以使变压器的体积缩小。
我们知道,实际的变压器总是在交流状态下工作,功率损耗不仅在线圈的电阻上,也产生在交变电流磁化下的铁芯中。
通常把铁芯中的功率损耗叫“铁损”,铁损由两个原因造成,一个是“磁滞损耗”,一个是“涡流损耗”。
磁滞损耗是铁芯在磁化过程中,由于存在磁滞现象而产生的铁损,这种损耗的大小与材料的磁滞回线所包围的面积大小成正比。
硅钢的磁滞回线狭小,用它做变压器的铁芯磁滞损耗较小,可使其发热程度大大减小。
既然硅钢有上述优点,为什么不用整块的硅钢做铁芯,还要把它加工成片状呢, 这是因为片状铁芯可以减小另外一种铁损——“涡流损耗”。
变压器工作时,线圈中有交变电流,它产生的磁通当然是交变的。
这个变化的磁通在铁芯中产生感应电流。
铁芯中产生的感应电流,在垂直于磁通方向的平面内环流着,所以叫涡流。
涡流损耗同样使铁芯发热。
为了减小涡流损耗,变压器的铁芯用彼此绝缘的硅钢片叠成,使涡流在狭长形的回路中,通过较小的截面,以增大涡流通路上的电阻;同时,硅钢中的硅使材料的电阻率增大,也起到减小涡流的作用。
用做变压器的铁芯,一般选用0(35mm厚的冷轧硅钢片,按所需铁芯的尺寸,将它裁成长形片,然后交叠成“日”字形或“口”字形。
从道理上讲,若为减小涡流,硅钢片厚度越薄,拼接的片条越狭窄,效果越好。
这不但减小了涡流损耗,降低了温升,还能节省硅钢片的用料。
但实际上制作硅钢片铁芯时。
并不单从上述的一面有利因素出发,因为那样制作铁芯,要大大增加工时,还减小了铁芯的有效截面。
所以,用硅钢片制作变压器铁芯时,要从具体情况出发,权衡利弊,选择最佳尺寸。
变压器是根据电磁感应的原理制成的.在在闭合的铁芯柱上面绕有两个绕组,一个原绕组,和一个副绕组.当原绕组假上交流电源电压时.原饶组流有交变电流,而建立磁势,在磁势的作用下铁芯中便产生交变主磁通,主磁通在铁芯中同时穿过,{交链]一.二次绕组而闭合由于电磁感应作用分别在一,,二次绕组产生感应电动势, 至于为什么它可以升压,和将压呢..那就需要用楞次定律来解释了.感应电流产生的磁通,总阻碍圆磁通的变化,当原磁通增加时感应电流的产生的磁通与与原磁通相反, 就是说二次绕组所产生的感应磁通与原绕组所产生的主磁通相反,所以二次绕组就出现了低等级的交变电压,,,所以...铁芯是变压器的磁路部分矽钢片电工用硅钢薄板俗称矽钢片或硅钢片。
变压器用硅钢片叠加原因
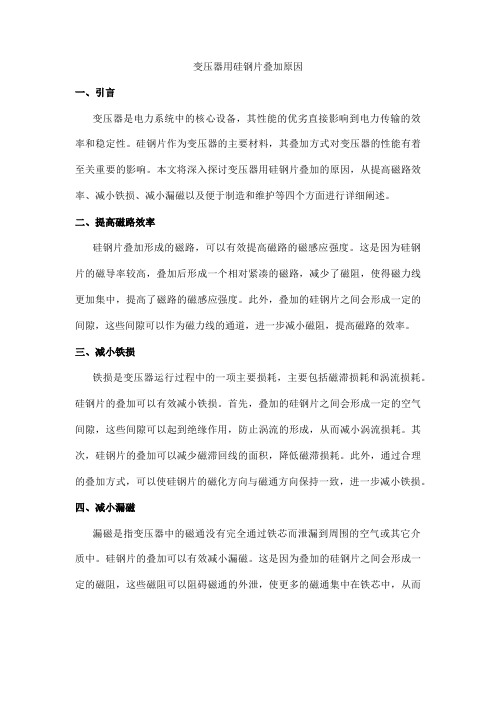
变压器用硅钢片叠加原因一、引言变压器是电力系统中的核心设备,其性能的优劣直接影响到电力传输的效率和稳定性。
硅钢片作为变压器的主要材料,其叠加方式对变压器的性能有着至关重要的影响。
本文将深入探讨变压器用硅钢片叠加的原因,从提高磁路效率、减小铁损、减小漏磁以及便于制造和维护等四个方面进行详细阐述。
二、提高磁路效率硅钢片叠加形成的磁路,可以有效提高磁路的磁感应强度。
这是因为硅钢片的磁导率较高,叠加后形成一个相对紧凑的磁路,减少了磁阻,使得磁力线更加集中,提高了磁路的磁感应强度。
此外,叠加的硅钢片之间会形成一定的间隙,这些间隙可以作为磁力线的通道,进一步减小磁阻,提高磁路的效率。
三、减小铁损铁损是变压器运行过程中的一项主要损耗,主要包括磁滞损耗和涡流损耗。
硅钢片的叠加可以有效减小铁损。
首先,叠加的硅钢片之间会形成一定的空气间隙,这些间隙可以起到绝缘作用,防止涡流的形成,从而减小涡流损耗。
其次,硅钢片的叠加可以减少磁滞回线的面积,降低磁滞损耗。
此外,通过合理的叠加方式,可以使硅钢片的磁化方向与磁通方向保持一致,进一步减小铁损。
四、减小漏磁漏磁是指变压器中的磁通没有完全通过铁芯而泄漏到周围的空气或其它介质中。
硅钢片的叠加可以有效减小漏磁。
这是因为叠加的硅钢片之间会形成一定的磁阻,这些磁阻可以阻碍磁通的外泄,使更多的磁通集中在铁芯中,从而减小漏磁。
此外,通过合理的叠加方式,可以使硅钢片的磁化方向与磁通方向保持一致,进一步减小漏磁。
五、便于制造和维护硅钢片的叠加方式还要考虑到便于制造和维护。
在实际生产中,采用适当的叠加方式可以使硅钢片的排列更加整齐、紧凑,提高生产效率。
同时,合理的叠加方式可以使变压器在运行过程中更加稳定,方便维护和检修。
此外,叠加的硅钢片之间有一定的间隙,这些间隙便于对硅钢片进行散热和防止过热,提高变压器的安全性和稳定性。
六、结论综上所述,变压器用硅钢片叠加的原因主要包括提高磁路效率、减小铁损、减小漏磁以及便于制造和维护等方面。
- 1、下载文档前请自行甄别文档内容的完整性,平台不提供额外的编辑、内容补充、找答案等附加服务。
- 2、"仅部分预览"的文档,不可在线预览部分如存在完整性等问题,可反馈申请退款(可完整预览的文档不适用该条件!)。
- 3、如文档侵犯您的权益,请联系客服反馈,我们会尽快为您处理(人工客服工作时间:9:00-18:30)。
修改记录文件中修改处所属行前面应加上更改标记(I )1本工艺适用于中、小型油浸式配变的硅钢片铁芯叠装工艺,其它类似铁芯的叠装也可参照执行。
2 设备、工模具及量具2.1工装设备:叠装台、翻转台、铁芯小车、刷漆台、行车( 5T)、配套吊具。
2.2工器具:呆扳手、套筒扳手、棘轮扳手、中齿平锉、铁锤、压块、?80木槌、整平铜块、中柱整形槽、尖角整形槽、阶距整块、夹紧槽钢、夹紧螺杆、M12螺母、木板、剪刀、双扣头柔性吊带(1T2M)、卸扣(1T级M14)、铁托盘、吸尘器、干净布块、漆刷、记号笔。
2.3量具:水平尺、游标卡尺(500mm)、高度尺(300mm)、钢直尺(150mm、1m)、钢卷尺(3.5m)。
3 材料准备3.1配套的高低压上、下夹件、拉螺杆、夹紧螺杆、螺母、垫圈、角钢、垫脚。
3.2夹件绝缘、夹紧绝缘、垫脚绝缘、垫脚木块等绝缘。
3.3调配合格的711(聚氨酯绝缘清漆。
4 工艺准备4.1仔细看清图纸、作业指导书及所要叠装铁心的各种材料。
4.2用铁芯小车准备每台铁芯叠装所需的硅钢片片料及夹件、拉螺杆等。
4.3检查所需的各种材料是否有无缺陷,是否干净等。
4.3.1检查硅钢片片料是否合格,包括宽度、长度、波浪度、片尖是否卷曲。
4.3.2检查高低压上下夹件是否符合图纸要求,表面漆是否完整,不合格的不得领用。
4.3.3检查绝缘件是否合格,与图纸要求尺寸是否一致。
4.3.4根据铁芯规格的大小选好槽钢,并在叠装台上均匀放置好槽钢。
4.3.5在叠装台的槽钢上放置检验合格的夹件,须配套使用。
4.3.6在叠装台工作端和两侧铺上木板,准备堆放硅钢片片料。
4.3.7准备并整理好叠装铁芯所用的工装和工具。
5 工艺过程5.1操作流程:5.2 操作过程:图(1)铺台522放夹件及夹件绝缘:5.221按图2所示,在两上下侧槽钢垫脚之间放置夹紧槽钢,在夹紧槽钢上面放置适当规格的铁芯柱夹紧槽钢,并用水平尺校整铁芯柱夹紧槽钢水平一致。
若不水平,可在铁芯柱夹紧槽钢下垫适当厚度的环氧板垫块。
图(2 )夹紧槽钢的放置与校平5.222按图3所示放置低压侧上、下夹件,调整两夹件的间距尺寸符合图纸要求,然后用钢卷尺测量上下夹件的对角线尺寸并进行微调,确保其水平、整齐,且上下夹件的间距和对角线尺寸均一致。
图(3)低压侧夹件放置与校平5.223按图4所示,在低压侧夹件、夹紧垫块上放置相应的夹件绝缘。
然后参照5.222步骤进行再次测量与校核夹件与夹件绝缘的间距与对角线尺寸,确保一致。
图(4)低压侧夹件绝缘的放置5.2.3 叠片523.1校验片料是否合格,并将合格的片料运至木板上。
523.2叠片方式采用 5级全接缝叠法:叠片顺序:中柱T上下轭T旁轭;采用一片一叠(中柱主级片可一次一级叠放)。
5.2.3.2.1按图5所示,根据图纸要求叠放首级中柱片(可适当慢些操作),用150m m钢直尺检查片料四周距离、接缝槽口是否符合要求。
5.2.3.2.2严格按照叠片方式及顺序对首级片进行叠装。
按图6所示,按工艺要求对上下轭片进行插第一片。
5.2.3.2.3首级上、下轭第一片叠好后,参照图7所示及工艺要求放置两侧相应的旁轭片;依次类推,直至首级片叠完为止。
5.2.3.4叠好首级片后,需要对其窗口面、外侧面及四角接缝处进行整理和检查,确保尺寸、片缝的整齐、吻合。
5.2.3.5参照步骤5.2.3.1 ~3、523.4进行叠装下一级片料。
且每叠完一级,均需对接缝、窗口端面、外侧端面进行校直、整平处理。
(参照图8)5.2.3.5.1整理时两人需在对应的两点同时进行,用整平铜块靠在片料端面上,用铁锤轻轻敲打整平铜块。
5.2.3.5.2检查对角线距离是否相等,芯柱与铁轭应垂直。
图(5)首级中柱片的放置处理图(6)首级上下轭片的放置处理5.2.3.6根据图纸尺寸逐级叠放,每叠一级均要做好整理和检查工作。
(如图9)523.7叠完主级后,除了做以上整理和检查工作外,还必须做好以下工作:5.2.3.7.1用水平尺检查上、下铁轭两个端面的垂直度, 检查芯柱两个端面的垂直度,检查边轭两个端面的垂直度每个端面至少检查两处。
523.7.2检查主级厚度,如果与图纸厚度之差为负值,应 在主级上加叠“ 2”的倍数片的主级硅钢片。
5.2.3.7.3检查是否有漏叠或错叠,如有发现应及时纠正。
5.2.3.8继续逐级叠放至全部叠完。
(如 图10)5.2.3.9铁芯全部叠好后,除做以上检查工作外,还必须 用游标卡尺检查总叠厚是否符合图纸要求,检查铁芯各 级层间有无偏移现象。
5.2.3.10如发现有级层偏移,应对偏移的级层进行整理。
5.2.4放绝缘及夹件5.2.4.1在叠好的铁芯上按图纸要求放置相应的高压侧夹 件绝缘、夹紧绝缘和夹紧木块。
5.2.4.2在夹紧木块上放置夹紧槽钢,使其与铁芯下面夹 紧槽钢相对应,然后从下方夹紧槽钢向上安装夹紧螺杆, 并用扳手收紧上端的螺母。
同时放置相应的高压上下夹 件装上,注意配套使用。
(如 图11)5.2.4.3先从下至上安装高低压侧的横拉螺杆,然后再安装高低压侧的竖拉螺杆。
用扳手先将下夹件收紧,再次 将夹紧槽钢收紧,最后将上夹件收紧,整个过程由下向 上逐个夹紧。
(如图12)5.2.4.4在收紧夹件时,须用水平尺测量高、低压下夹件 端面是否水平,再测量高、低压上夹件端面是否水平, 如不在同一水平面上,必须及时调整。
图(12)夹件拉螺杆的收紧处理No. 编号 QEI-31 S11(13作业指导书 Rep. no.替代 A/1图(9)主级片料的叠装处理图(10)铁芯叠装及整压处理 图(11)夹紧槽钢、夹件及绝缘的放置处理Rev. no.版本号B/0 硅钢片铁芯叠装处理Page 页号5/65.245所有夹件都安装紧好后,准备安装垫脚。
5.245.1在垫脚装上按图纸要求选取相应的垫脚绝缘和木垫,然后按图13所示将其安装到垫脚上。
5.245.2按照图纸要求在下夹件上安装垫脚。
然后用卷尺测量垫脚高、低压两侧的距离是否相等,并用水平尺测量两只垫脚是否平行。
最后用扳手先将上端的垫脚螺栓收紧,待器身站立后再将收紧另一端的垫脚螺栓。
图(13)垫脚的安装处理5.2.5铁芯翻转5.2.5.1用行车把铁芯吊到铺有纸板的翻转台上,将吊带及配套吊具固定在铁芯上夹件上。
525.2用行车缓缓将平躺的铁芯拉起,直至铁芯垫脚离开地面,整个铁芯呈竖立状态并静稳下来为止。
(如图14)5.2.5.3翻转铁芯时应及时整理托盘上因翻转造成偏移的纸板,防止翻转时碰伤铁芯夹件和垫脚的表面漆层。
5.2.5.4将铁芯缓慢落至托盘上,收紧低压侧的垫脚螺杆。
5.2.5.5检查铁芯及夹件等是否受损,若有铁芯片尖角卷边现象,应及时修整。
5.2.6铁芯柱绑扎5.2.6.1若铁芯柱和旁铁轭需要绑扎处理,应根据工艺规定,按图15用布带将铁芯柱分上、中、下均匀绑扎三道。
5.2.6.2绑扎要求均匀,拉紧,一致。
5.2.6.3装上接地片,将铁芯清洁干净。
图(15)铁芯柱的绑扎处理5.2.7 刷漆5.2.7.1将铁芯缓慢吊起,移到刷漆区域的台面上。
取下吊带及配套吊具。
5.2.7.2用合格的绝缘清漆在铁芯上进行均匀涂刷(上铁轭不刷)。
下铁轭刷漆必须到位,若有漏刷漆的部位,应及时进行补漆。
(如图16)5.2.7.3按涂漆工艺将没有刷到位的铁芯片补刷到位(不含上铁轭)。
图(16)铁芯的刷漆处理No. 编号QEI-31 S11(13作业指导书Rep. no.替代A/1 Rev. no.版本号B/0 硅钢片铁芯叠装处理Page 页号6/6528.1用500V兆欧表测量,一端接铁芯,一端接夹件或拉螺杆。
(如图17)注意:测量铁芯与夹件的绝缘电阻时,接地片不能搭在铁芯上,否则铁芯与夹件会短接,测量值就显示为零。
528.2铁芯片与夹件之间的绝缘电阻测试值应不小于 2M Q,并将测量值按工艺要求填写在流转卡上。
5.2.9若铁芯受潮,需将铁芯送至烘房内进行干燥。
5.2.10填好铁芯叠装流转卡,将铁芯送检、入库。
5.2.11整理叠装台,打扫工作场地。
图(17)铁芯与夹件的绝缘电阻测试6 外观检查及注意事项6.1叠装前工艺准备一定要充分,严格以“三按”标准要求操作,即按图纸、按作业指导书、按技术要求。
6.2合格的铁芯应整齐摆放在指定地点。
6.3铁芯刷漆应清洁、光滑、均匀、不应有漆流、露底等现象。
6.4夹件表面应无损伤、漆斑、胶迹和灰尘等现象。
6.5铁芯上铁轭不允许有碰伤、缺角、卷边现象。
6.6刷漆时,注意漆不能滴到夹件、垫脚和地面上。
6.7夹紧槽钢应在铁芯完全干燥及绝缘漆固化后才能拆除。
6.8操作过程中应佩戴劳动防护用品。
-可编辑修改-THANKS !!!致力为企业和个人提供合同协议,策划案计划书,学习课件等等打造全网一站式需求欢迎您的下载,资料仅供参考。