联轴器材质及表面处理
常见机械材料特性及表面处理

常见机械材料特性及表面处理1、钢铁类1. 1、碳素钢。
(1)根据含碳量分低碳钢:含碳量<0.25%中碳钢:含碳量0.25%~0.6%高碳钢:含碳量>0.6%(2)按含有害杂质S、P含量分普通碳素钢:含S、P分别低于0.035%~0.050%和0.035%~0.045%优质碳素钢:含S、P分别低于0.035%高级优质碳素钢:含S、P分别低于0.020%~0.030%和0.025%~0.030% (3)按用途分碳素结构钢:主要用于构件和机器零件。
碳素工具钢:主要用于刀具、工具量具、模具。
1.2、钢的牌号。
(1)普通碳素结构钢。
屈服点拼音字头Q、屈服极限值(单位MPa)质量等级符号、脱氧方法符号四部分组成。
质量等级四级A、B、C、D表示。
脱氧方法以F、b、Z、TZ分别表示沸腾钢、半镇静钢、镇静钢、特殊镇静钢、例,Q235AF表示屈服极限235MPa、质量等级A、沸腾钢。
(2)优质碳素结构钢。
用两位数字表示含碳量为万分之几。
如45钢,指含碳量为0.45%45Mn,指锰的含量较高,0.7%~1.2%(3)铸造碳钢牌号ZG、屈服极限、横线、抗拉极限表示例ZG200—400表示屈服强度≥200Mpa, 抗拉极限≥400Mpa的铸造碳钢。
(4)碳素工具钢。
含碳量0.65%~1.35%T+数字如T8,含碳量为0.8%。
T8A,指高级优质碳素工具钢(5)合金结构钢两位数字+合金元素符号+数字如:12GrNi3钢,指含碳量0.12%,含Gr小于1.5%,平均含Ni 3%(6)合金工具钢含碳量大于等于1%时不注;小于1%时以千分之几表示。
如9GrSi表示碳量0.9%,含Gr、Si均小于1.5%(7)滚动轴承钢G+Gr+数字例GGr13表示含Gr小于1.30%,1.3、常见钢材性能1.3.1 45号钢(优质碳素结构钢)(价格:7元/KG)常见图纸标示:45#,S45C 含碳量:0.45% ;密度:7.85g/cm3 抗拉强度: ≥600 (MPa)屈服强度: ≥355 (MPa)是机械设计中使用最多的金属材料,常用于:支撑件、普通轴、导向件、定位件、连接件曲轴、传动轴、齿轮、蜗杆、键、销等。
机床主轴材料和表面处理
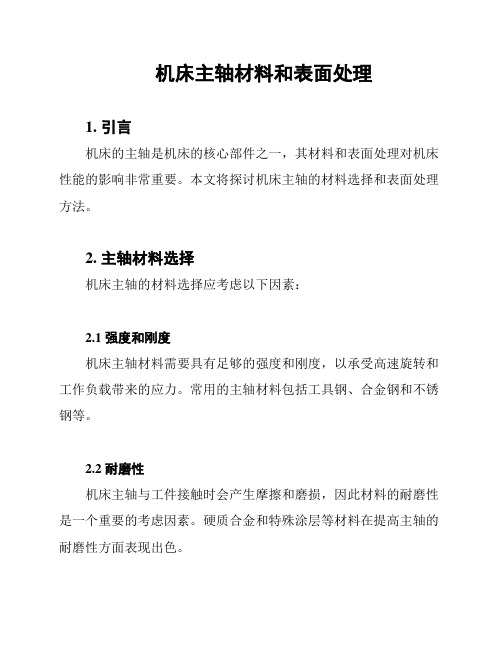
机床主轴材料和表面处理1. 引言机床的主轴是机床的核心部件之一,其材料和表面处理对机床性能的影响非常重要。
本文将探讨机床主轴的材料选择和表面处理方法。
2. 主轴材料选择机床主轴的材料选择应考虑以下因素:2.1 强度和刚度机床主轴材料需要具有足够的强度和刚度,以承受高速旋转和工作负载带来的应力。
常用的主轴材料包括工具钢、合金钢和不锈钢等。
2.2 耐磨性机床主轴与工件接触时会产生摩擦和磨损,因此材料的耐磨性是一个重要的考虑因素。
硬质合金和特殊涂层等材料在提高主轴的耐磨性方面表现出色。
2.3 导热性机床主轴在高速运转时,会产生大量的热量。
材料的导热性能影响着热量的传导和分散,因此材料应具有良好的导热性能,以保持主轴的温度稳定。
高温合金是一种常用的导热性能较好的材料。
3. 主轴表面处理主轴表面处理主要是为了提高其表面质量和耐磨性,并减小与工件的摩擦。
常见的主轴表面处理方法包括以下几种:3.1 硬化主轴经过热处理或化学处理,使其表面形成一层硬化层。
硬化层可以提高主轴的硬度和耐磨性,从而延长主轴的使用寿命。
3.2 镀铬将主轴表面浸泡在铬盐溶液中,可以在主轴表面形成一层铬镀层。
铬镀层具有优异的耐磨性和耐腐蚀性,可以有效地保护主轴表面。
3.3 涂层在主轴表面涂覆一层特殊涂层,如金属陶瓷涂层或陶瓷涂层等,可以提高主轴的耐磨性和摩擦性能。
4. 结论机床主轴的选择和表面处理对机床性能至关重要。
在选择材料时需要考虑强度、耐磨性和导热性等因素,而表面处理则可以通过硬化、镀铬或涂层等方法来提高主轴的表面质量和耐磨性。
正确的选择和处理可以提高机床主轴的使用寿命和工作效率。
以上是关于机床主轴材料和表面处理的简要介绍,希望对您有所帮助。
膜片联轴器标准范文

膜片联轴器标准范文一、膜片联轴器的设计标准:1.结构设计:膜片联轴器应采用对称结构,各膜片长度和宽度应一致,各膜片的刚度和质量应相近,确保联轴器在工作过程中不产生偏心力。
2.耐用性设计:膜片联轴器应具有较高的耐用性,能够承受较大的扭矩和振动,确保传动系统的稳定运行。
3.安全设计:膜片联轴器应具有一定的安全性能,能够在传动系统发生故障时自动断开,避免进一步损坏机械设备和人身安全。
4.尺寸设计:膜片联轴器的尺寸应根据实际传动力矩和转速进行设计,确保联轴器能够满足传动系统的工作要求。
二、膜片联轴器的制造标准:1.材料选择:膜片联轴器的制造材料应选择高强度、耐磨损、抗腐蚀的材料,如优质钢材、合金钢等。
2.制造工艺:膜片联轴器的制造过程中应采用先进的加工工艺和设备,保证联轴器的精度和质量。
3.表面处理:膜片联轴器的表面应进行防锈处理,如镀锌、喷涂等,以增加联轴器的耐腐蚀性和美观度。
4.检测要求:膜片联轴器的制造过程中应进行严格的质量控制和检测,确保联轴器的尺寸和质量符合设计要求。
三、膜片联轴器的安装标准:1.安装位置:膜片联轴器的安装位置应保证与传动系统的输入轴和输出轴对齐,并且联轴器的连接端面平行度应控制在一定范围内。
2.装配要求:膜片联轴器的装配过程中应保持正确的顺序和方法,避免损坏联轴器的膜片和其他零部件。
3.螺栓紧固:膜片联轴器的连接螺栓应均匀紧固,不得出现松动和变形现象,确保联轴器的连接牢固和稳定。
4.润滑要求:膜片联轴器的润滑油脂应根据工作条件选择合适的润滑剂,并定期进行检查和更换。
四、膜片联轴器的使用标准:1.正确使用:膜片联轴器在使用过程中应严格按照设计要求和安装规范进行操作,避免超载和过速等情况发生。
2.维护保养:膜片联轴器应定期进行维护和保养,包括清洁、润滑和检查等工作,以确保联轴器的正常运行和寿命。
3.故障处理:膜片联轴器在使用过程中如出现故障或异常情况,应及时停机检修,排除故障,以避免进一步损坏设备和人身安全。
联轴器上的膜片的制作工艺

联轴器上的膜片的制作工艺一、前言联轴器上的膜片是联轴器中非常重要的一个组成部分,它是用来传递扭矩和减震的。
在制作膜片时需要注意很多细节,因此本文将详细介绍联轴器上的膜片的制作工艺。
二、材料准备1. 板材:一般采用不锈钢板或弹簧钢板,厚度一般在0.2-0.5mm之间。
2. 制模材料:采用高强度钢材或铸铁。
3. 油漆:防锈油漆和表面涂装油漆。
4. 其他辅助材料:包括螺丝、垫片、弹簧等。
三、制作流程1. 制作模具首先需要根据设计图纸制作出模具。
模具应该采用高强度钢材或铸铁,并且要保证精度和平整度。
制作完成后需要进行检查和测试,确保其符合设计要求。
2. 制作膜片将选好的板材放入模具中,并按照设计要求进行冲剪成形。
在冲剪过程中需要注意板材的厚度和尺寸,保证其符合设计要求。
同时还需要注意冲剪过程中的刀模和压模的磨损情况,及时更换或修整。
3. 焊接将冲剪好的膜片进行拼接,并进行焊接。
在焊接过程中需要注意焊缝的质量和强度,以及避免产生变形和裂纹等问题。
焊接完成后需要进行检查和测试,确保其符合设计要求。
4. 表面处理将焊接好的膜片进行表面处理。
首先需要进行除锈处理,然后再进行防锈涂装。
最后再进行表面涂装油漆。
5. 装配将制作好的膜片与其他零部件进行组装,并按照设计要求进行调整和校准。
在装配过程中需要注意零部件之间的配合精度和密封性。
四、质量控制1. 板材:必须选择优质材料,并且要按照规定厚度和尺寸加工。
2. 制模:必须保证模具的精度和平整度,并且要经过检查和测试。
3. 冲剪:必须按照设计要求进行冲剪成形,并且要注意刀模和压模的磨损情况。
4. 焊接:必须保证焊缝的质量和强度,并且要避免产生变形和裂纹等问题。
5. 表面处理:必须进行除锈处理和防锈涂装,以及表面涂装油漆。
6. 装配:必须按照设计要求进行组装,并且注意零部件之间的配合精度和密封性。
五、结语联轴器上的膜片是联轴器中非常重要的一个组成部分,其制作工艺需要注意很多细节。
弹性柱销联轴器的加工工艺

弹性柱销联轴器的加工工艺
弹性柱销联轴器是一种常见的机械传动连接方式,它通过柱销将两个轴连接在一起,并通过弹性元件提供一定的柔性,以吸收轴上的振动和冲击力。
下面将介绍弹性柱销联轴器的加工工艺。
1. 原材料准备:弹性柱销联轴器通常由高强度合金钢、不锈钢等材料制成。
进行加工前,需要准备好符合要求的原材料,选材时要考虑到强度、硬度和耐磨性等因素。
2. 打圆:首先需要将原材料进行车床车削,使其成为圆柱形。
这个过程旨在形成一根直径适中的棒材,以便进行下一步的加工。
3. 键槽加工:根据设计要求,在两个轴的连接部位,使用铣床或刨床等设备开槽。
这些槽将用于安装弹性柱销,以确保其稳定性和可靠性。
4. 弹性柱销加工:弹性柱销是连接两根轴的关键部件,它需要经过多道工序进行加工。
首先,可以使用车床对其两端进行磨平,以提高其工作平整度。
然后,在车床上逐步加工出所需的直径和长度。
最后,使用铣床或刨床等设备对弹性柱销进行槽口加工,以提高其弯曲和扭转的柔性。
5. 表面处理:为了提高联轴器的使用寿命和性能,还需要对其表面进行处理。
例如,可以进行钝化处理以提高耐腐蚀性,或进行硬化处理以提高强度和耐磨性。
6. 总装:在加工完成后,将弹性柱销、轴和其他部件进行总装。
在总装过程中,需要严格检查每个部件是否符合要求,并确保其连接紧固。
综上所述,弹性柱销联轴器的加工工艺包括原材料准备、打圆、键槽加工、弹性柱销加工、表面处理和总装等环节。
通过这些工艺步骤,可以制造出具有高强度、高耐磨性和良好柔性的弹性柱销联轴器,以满足各种机械传动的要求。
轴类零件的材料与热处理

轴类零件的材料与热处理一般轴类零件常用中碳钢,如45钢,经正火、调质及部分表面淬火等热处理,得到所要求的强度、韧性和硬度。
对中等精度而转速较高的轴类零件,一般选用合金钢(如40Cr等),经过调质和表面淬火处理,使其具有较高的综合力学性能。
对在高转速、重载荷等条件下工作的轴类零件,可选用20CrMnTi、20Mn2B、20Cr等低碳合金钢,经渗碳淬火处理后,具有很高的表面硬度,心部则获得较高的强度和韧性。
对高精度和高转速的轴,可选用38CrMoAl 钢,其热处理变形较小,经调质和表面渗氮处理,达到很高的心部强度和表面硬度,从而获得优良的耐磨性和耐疲劳性。
附:钢的淬火与回火是热处理工艺中很重要的、应用非常广泛的工序。
淬火能显著提高·钢的强度和硬度。
如果再配以不同温度的回火,即可消除(或减轻)淬火内应力,又能得到强度、硬度和韧性的配合,满足不同的要求。
所以,淬火和回火是密不可分的两道热处理工艺。
车床主轴加工工艺过程分析⑴ 主轴毛坯的制造方法锻件,还可获得较高的抗拉、抗弯和抗扭强度。
⑵ 主轴的材料和热处理45钢,普通机床主轴的常用材料,淬透性比合金钢差,淬火后变形较大,加工后尺寸稳定性也较差,要求较高的主轴则采用合金钢材料为宜。
①毛坯热处理采用正火,消除锻造应力,细化晶粒,并使金属组织均匀。
②预备热处理粗加工之后半精加工之前,安排调质处理,提高其综合力学性能③最终热处理主轴的某些重要表面需经高频淬火。
最终热处理一般安排在半精加工之后,精加工之前,局部淬火产生的变形在最终精加工时得以纠正。
加工阶段的划分①粗加工阶段用大的切削用量切除大部分余量,及时发现锻件裂纹等缺陷。
②半精加工阶段为精加工作好准备③精加工阶段把各表面都加工到图样规定的要求。
粗加工、半精加工、精加工阶段的划分大体以热处理为界。
工序顺序的安排毛坯制造——正火——车端面钻中心孔——粗车——调质——半精车表面淬火——粗、精磨外圆——粗、精磨圆锥面——磨锥孔。
联轴器上的膜片的制作工艺
联轴器上的膜片的制作工艺一、膜片的定义与作用膜片是一种薄而柔韧的材料,常用于联轴器等机械装置中,用于传递和调节扭矩、吸收振动和冲击等。
它的作用是连接两个轴,保证传动系统的正常运转。
二、常见膜片的材料选择不同的工况和使用要求决定了膜片材料的选择。
常见的膜片材料包括以下几种:1.金属膜片:如不锈钢、铜合金等,具有较高的强度和耐磨性,适用于较大扭矩和较高速度的传动系统。
2.弹性体膜片:如橡胶、聚氨酯等,具有良好的弹性和耐磨性,适用于较小扭矩和较低速度的传动系统。
3.复合材料膜片:如碳纤维增强树脂等,结合了金属和弹性体的优点,具有较高的强度和耐磨性,适用于较为复杂的工况。
三、膜片的制作工艺膜片的制作工艺主要包括以下几个步骤:1. 材料准备根据设计要求和使用环境选择合适的膜片材料,并对材料进行切割和加工,以获得所需的形状和尺寸。
2. 压制模具设计与制造根据膜片的形状和尺寸,设计和制造相应的压制模具。
模具通常由金属材料制成,具有膜片所需的凸凹形状。
3. 材料热处理对金属膜片进行热处理,以提高其硬度和强度,并调整其结构和性能。
这一步骤可以通过淬火、回火等工艺完成。
4. 材料压制将准备好的材料放入压制模具中,施加适当的温度和压力,使其与模具表面接触,并获得所需的膜片形状。
5. 表面处理对膜片的表面进行处理,以提高其耐磨性和耐腐蚀性。
常见的表面处理方法包括镀铬、镀镍、喷涂等。
6. 成品检验对制作好的膜片进行检验,包括外观质量、尺寸精度、硬度、强度等方面的测试,以确保其符合设计和使用要求。
四、膜片的应用与发展趋势膜片广泛应用于各种机械装置中,如汽车传动系统、风力发电机组、工业泵等。
随着科技的进步和工艺的改进,膜片的制作工艺也在不断发展。
未来的趋势可能包括以下几个方面:1.材料的创新:新型材料的研发和应用,如纳米材料、高分子复合材料等,可以提高膜片的性能和使用寿命。
2.制造工艺的自动化:采用先进的制造设备和自动化技术,可以提高膜片的制作效率和品质稳定性。
联轴器的加工工艺
联轴器的加工工艺联轴器是一种用于连接两个轴传输能量的装置。
它由两个部分组成:套筒和弹簧。
加工联轴器的工艺包括以下几个步骤:1. 材料选择:联轴器通常由金属材料制成,如钢、铸铁等。
材料选择应考虑到联轴器的使用环境和传动功率等因素。
2. 设计制图:根据联轴器的使用需求和机械设计原理,进行设计制图。
包括确定联轴器外形尺寸、孔径等参数。
3. 材料切削:首先,根据设计制图的要求,将原材料切割成相应的尺寸。
可以使用剪切机、钢丝锯等工具进行切割。
4. 材料加工:将切割好的材料进行加工。
这包括车削、铣削、钻孔等工艺。
通过车床、铣床、钻床等机床进行相应加工操作。
根据不同类型的联轴器,可以进行内孔加工、外形加工、键槽加工等。
5. 弹簧加工:联轴器的弹簧通常使用弹簧钢制成。
首先,选择合适的弹簧钢材料,并根据设计要求进行弹簧卷制。
然后,使用卷簧机对弹簧进行成形和弯曲。
6. 组装:在联轴器的加工过程中,套筒和弹簧分别加工完成后,进行组装。
将弹簧放入套筒中,根据设计要求进行弹簧的压装或焊接。
组装时需要保证套筒和弹簧的配合度和工作性能。
7. 表面处理:联轴器的表面处理可以选用镀锌、喷涂等方式,以提高联轴器的耐腐蚀性和美观度。
8. 检验和质量控制:加工完成后,对联轴器进行检验。
例如,使用测量仪器对外观尺寸、孔径等进行测量和检验。
同时,还需进行弹簧的弹性试验和套筒的轴向承载力试验等性能检查。
9. 热处理:根据需要,可以对联轴器进行热处理。
热处理可以提高联轴器的强度、硬度和耐磨性等性能。
常用的热处理方法有淬火、回火等。
10. 包装运输:加工完成的联轴器需要进行包装和标识,并进行寄送或储存。
综上所述,联轴器的加工工艺包括:材料选择、设计制图、材料切削、材料加工、弹簧加工、组装、表面处理、检验和质量控制、热处理和包装运输等步骤。
每个步骤都需要合理安排和操作,以确保联轴器的质量和性能。
万向联轴器材质技术要求
万向联轴器材质技术要求作为连接传动装置的重要部件之一,万向联轴器扮演着不可或缺的角色。
其材质的选择对其使用寿命、运行效率、耐用性等方面的影响至关重要。
因此,下面就介绍一下万向联轴器材质技术要求。
一、选材原则。
(1)可靠性:选材时要考虑联轴器一旦出现故障将会对生产带来的负面影响,因此需要选用高可靠性材料。
(2)机械性能:联轴器要有足够的强度和硬度,同时还需要具备一定的韧性,这样才能在高压、高速、高温等恶劣环境下保持稳定运行。
(3)耐磨性:联轴器工作时要承受较大的摩擦力,因此耐磨性是一个关键因素之一。
(4)耐腐蚀性:特别是在潮湿、酸碱等腐蚀性环境下,需要选用耐腐蚀性能好的材料。
(5)加工工艺:联轴器通常需要进行加工、锻造或铸造等工艺,因此选材时需要考虑其加工性能。
二、常用材质。
(1)铸钢材料:铸钢材料具有优良的机械性能,并且耐磨、耐腐蚀性好。
常用的有ZG25、ZG35、ZG45等。
(2)铸铁材料:铸铁材料具有良好的耐磨性和振动吸收性能,常用的有QT400、QT500、QT600等。
(3)不锈钢材料:不锈钢材料耐腐蚀性好,并且具备较高的强度和硬度,常用的有304、316、317等。
(4)铝合金材料:铝合金材料重量轻、强度高,但不耐磨,常用的有LY12、LF21等。
三、应注意的问题。
(1)选择材料时需根据具体使用环境和需求进行合理的匹配,以确保联轴器的可靠性和稳定性。
(2)不同材质在生产加工和使用时有不同的特点和应用范围,需要选择合适的材料。
(3)不同材质之间的性能也有区别,在选择时需了解其特点和优劣。
总的来说,万向联轴器材质的选择需要经过科学的分析和合理的匹配,以确保其性能满足需求。
同时,在使用过程中还需要注意保养和维护,延长其使用寿命和保障生产效率。
联轴器介绍与应用
联轴器介绍与应用一.联轴器介绍联轴器是用来联接不同机构中的两根轴(主动轴和从动轴)使之共同旋转以传递扭矩的机械零件。
在高速重载的动力传动中,有些联轴器还有缓冲、减振和提高轴系动态性能的作用。
联轴器由两半部分组成,分别与主动轴和从动轴联接。
一般动力机大都借助于联轴器与工作机相联接。
二.联轴器分类1.滑块联轴器介绍十字滑块联轴器又名金属滑块联轴器,其滑块呈圆环形,用钢或耐磨合金制成,适用于转速较低,传递转矩较大的传动。
滑块联轴器简介十字滑块联轴器由两个在端面上开有凹槽的半联轴器和一个两面带有凸牙的中间盘组成。
因凸牙可在凹槽中滑动,故可补偿安装及运转时两轴间的相对位移。
这种联轴器零件的材料可用45钢,工作表面需要进行热处理,以提高其硬度;要求较低时也可用Q275钢,不进行热处理。
为了减少摩擦及磨损,使用时应从中间盘的油孔中注油进行润滑。
因为半联轴器与中间盘组成移动副,不能发生相对转动,故主动轴与从动轴的角速度应相等。
但在两轴间有相对位移的情况下工作时,中间盘就会产生很大的离心力,从而增大动载荷及磨损。
因此选用时应注意其工作转速不得大于规定值。
这种联轴器一般用于转速n<250r/min,轴的刚度较大,且无剧烈冲击处。
利用中间滑块在其两侧半联轴器端面的相应径向槽内滑动,以实现两半联轴器联接。
该联轴器噪声大,效率低,磨损快,一般尽量不选用,只有转速很低的场合,本标准所规定的滑块联轴器,适用于油泵装置或其它传递扭矩较小的场合,具有一定补偿两轴相对偏移量,减震和缓冲性能;其工作温度为-20~70°C。
传递公称扭矩为16~500N.m。
●许用补偿量:轴向△ x=1~2mm ,径向△ y ≤ 0.2mm ,角向△α≤ 40 ′。
滑块联轴器定义与构成滑块联轴器又名金属十字滑块联轴器,其滑块呈圆环形,用钢或耐磨合金制成,适用于十字滑块联轴器的具体尺寸与技术参数转速较低,传递转矩较大的传动。
十字滑块联轴器由两个在端面上开有凹槽的半联轴器和一个两面带有凸牙的中间盘组成。
- 1、下载文档前请自行甄别文档内容的完整性,平台不提供额外的编辑、内容补充、找答案等附加服务。
- 2、"仅部分预览"的文档,不可在线预览部分如存在完整性等问题,可反馈申请退款(可完整预览的文档不适用该条件!)。
- 3、如文档侵犯您的权益,请联系客服反馈,我们会尽快为您处理(人工客服工作时间:9:00-18:30)。
联轴器材质及表面处理
联轴器是一种常用的机械传动装置,用于连接两个旋转轴,并传递扭矩和旋转运动。
联轴器的材质选择和表面处理对其性能和使用寿命有着重要的影响。
1. 材质选择:
联轴器的材质应根据具体工作条件和要求来选择,常见的材质有以下几种:
- 钢:常见的钢材有碳钢、合金钢等,具有较高的强度和刚性,适用于一般工况下的联轴器。
- 铸铁:铸铁具有良好的耐磨性和防腐性能,适用于一些特殊环境下的联轴器,如化工、食品等行业。
- 不锈钢:不锈钢具有良好的耐腐蚀性能,适用于湿润、腐蚀性较强的环境中的联轴器。
2. 表面处理:
联轴器的表面处理可以提高其耐磨性、抗腐蚀性和耐久性,常见的表面处理方法有以下几种:
- 热处理:通过加热和冷却的方式改变材料的组织结构,提高其硬度和强度。
- 镀锌:在联轴器表面镀上一层锌,形成锌层保护材料不被氧化和腐蚀。
- 涂装:在联轴器表面涂上一层防腐漆或涂料,能够起到防止腐蚀和磨损的作用。
- 氮化处理:将联轴器加热至高温,使其与氮气反应生成氮化物层,提高联轴器的硬度和耐磨性。
需要根据具体的工况和要求选择适合的联轴器材质和表面处理方法。
对于特殊环境下的联轴器,如高温、腐蚀等情况,可以采用特殊材质和表面处理方式来增强其性能和耐久性。