半导体单晶和薄膜制造技术
半导体薄膜
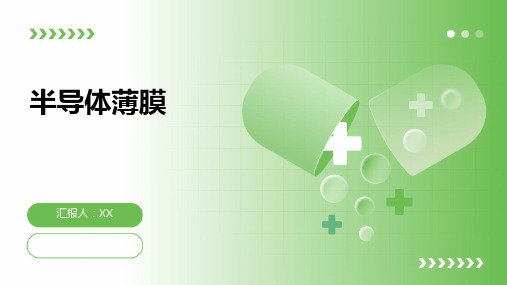
汇报人:XX
目录
• 半导体薄膜概述 • 半导体薄膜制备技术 • 半导体薄膜结构与性能 • 半导体薄膜应用实例 • 半导体薄膜材料发展趋势与挑战
01
半导体薄膜概述
定义与特点
定义
半导体薄膜是一种具有半导体性质的薄膜材料,其厚度通常在纳米至微米级别 。这种材料具有介于导体和绝缘体之间的电导率,因此被称为半导体。
。
缺陷对性能的影响
缺陷对半导体薄膜的性能有重要 影响,如影响载流子浓度、迁移
率、光学透过率等。
电子结构与能带
能带结构
01
半导体薄膜的能带结构决定了其电子状态和电子行为。通常包
括价带、导带和禁带三部分。
载流子类型
02
半导体薄膜中的载流子可以是电子或空穴,这取决于其掺杂类
型和浓度。
载流子浓度和迁移率
03
回收利用
建立完善的回收利用体系,对废旧半导体薄膜进行 回收和再利用,降低资源浪费和环境污染。
THANKS
感谢观看
大面积均匀性控制技术挑战
薄膜沉积技术
如化学气相沉积、物理气相沉积等,需要优化工艺参数,提高薄膜 大面积均匀性。
表面处理技术
如机械抛光、化学抛光等,可以改善基底表面粗糙度,提高薄膜附 着力和均匀性。
薄膜转移技术
如卷对卷技术、激光转移技术等,可以实现大面积薄膜的快速、高效 转移。
提高稳定性及寿命问题探讨
现状
目前,半导体薄膜的制备技术已经非常成熟,包括物理气相沉积、化学气相沉积、溶胶-凝胶法、电化学沉积等 多种方法。同时,半导体薄膜的应用领域也在不断扩展,涉及到电子、光电、生物医学、环境科学等多个领域。
应用领域与前景
应用领域
半导体的生产工艺流程
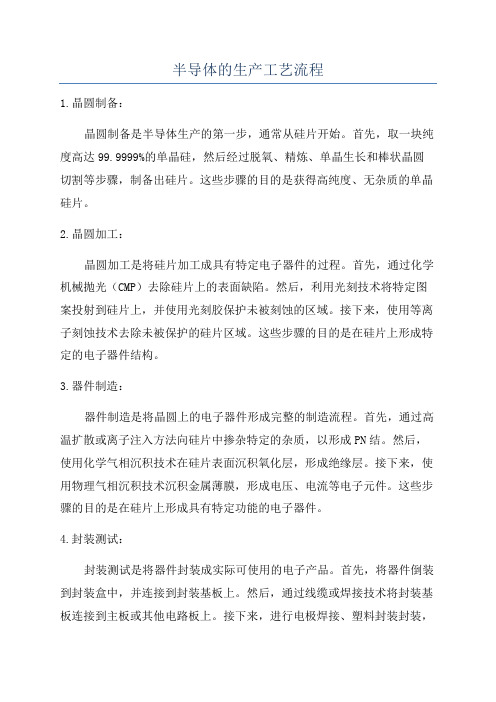
半导体的生产工艺流程1.晶圆制备:晶圆制备是半导体生产的第一步,通常从硅片开始。
首先,取一块纯度高达99.9999%的单晶硅,然后经过脱氧、精炼、单晶生长和棒状晶圆切割等步骤,制备出硅片。
这些步骤的目的是获得高纯度、无杂质的单晶硅片。
2.晶圆加工:晶圆加工是将硅片加工成具有特定电子器件的过程。
首先,通过化学机械抛光(CMP)去除硅片上的表面缺陷。
然后,利用光刻技术将特定图案投射到硅片上,并使用光刻胶保护未被刻蚀的区域。
接下来,使用等离子刻蚀技术去除未被保护的硅片区域。
这些步骤的目的是在硅片上形成特定的电子器件结构。
3.器件制造:器件制造是将晶圆上的电子器件形成完整的制造流程。
首先,通过高温扩散或离子注入方法向硅片中掺杂特定的杂质,以形成PN结。
然后,使用化学气相沉积技术在硅片表面沉积氧化层,形成绝缘层。
接下来,使用物理气相沉积技术沉积金属薄膜,形成电压、电流等电子元件。
这些步骤的目的是在硅片上形成具有特定功能的电子器件。
4.封装测试:封装测试是将器件封装成实际可使用的电子产品。
首先,将器件倒装到封装盒中,并连接到封装基板上。
然后,通过线缆或焊接技术将封装基板连接到主板或其他电路板上。
接下来,进行电极焊接、塑料封装封装,形成具有特定外形尺寸和保护功能的半导体芯片。
最后,对封装好的半导体芯片进行功能性测试和质量检查,以确保其性能和可靠性。
总结起来,半导体的生产工艺流程包括晶圆制备、晶圆加工、器件制造和封装测试几个主要步骤。
这些步骤的有机组合使得我们能够生产出高性能、高效能的半导体器件,广泛应用于电子产品和信息技术领域。
硅基半导体的制备技术

硅基半导体的制备技术硅基半导体是一种重要的材料,在电子行业中有广泛的应用。
它具有优良的电子特性和稳定性,因此被广泛用于集成电路、太阳能电池等领域。
本文将介绍硅基半导体的制备技术,包括单晶硅的生长、掺杂和薄膜沉积等关键步骤。
一、单晶硅的生长单晶硅是硅基半导体的基础材料,其生长过程需要高纯度的硅原料和精密的控制条件。
目前常用的单晶硅生长方法有Czochralski法和区域熔融法。
Czochralski法是一种常用的单晶硅生长方法。
首先,将高纯度的硅原料放入石英坩埚中,加热至高温熔化。
然后,在熔融硅液表面悬挂一根带有小晶种的单晶硅棒,通过旋转和提升下降的方式,逐渐拉出单晶硅棒。
在拉出的过程中,控制温度和拉速,使得硅液逐渐凝固形成单晶硅。
区域熔融法是另一种常用的单晶硅生长方法。
它通过在硅片上制造一定的掺杂区域,然后加热整个硅片,使得掺杂区域熔化。
随后,通过控制温度梯度,使得熔融区域逐渐移动,最终形成单晶硅。
二、掺杂掺杂是指向硅基半导体中引入杂质,以改变其电子特性。
常用的掺杂方法有扩散法和离子注入法。
扩散法是一种常用的掺杂方法。
它通过将硅片放入含有掺杂材料的气氛中,加热至高温,使得掺杂材料扩散到硅片中。
掺杂材料可以是五价元素如磷或三价元素如硼,通过控制温度和时间,可以控制掺杂的浓度和深度。
离子注入法是另一种常用的掺杂方法。
它通过将掺杂材料的离子注入到硅片中,使得掺杂材料与硅原子发生置换。
离子注入法具有高精度和可控性,适用于制备高精度的器件。
三、薄膜沉积薄膜沉积是指在硅基半导体表面沉积一层薄膜,用于制备各种器件结构。
常用的薄膜沉积方法有化学气相沉积(CVD)和物理气相沉积(PVD)。
化学气相沉积是一种常用的薄膜沉积方法。
它通过将气体中的前驱体在高温下分解,生成沉积物质并沉积在硅基半导体表面。
化学气相沉积具有高沉积速率和均匀性好的特点,适用于大面积薄膜的制备。
物理气相沉积是另一种常用的薄膜沉积方法。
它通过将金属或合金材料蒸发或溅射到硅基半导体表面,形成薄膜。
半导体单晶薄膜的制备方法

半导体单晶薄膜的制备方法
制备半导体单晶薄膜的方法主要包括分子束外延技术、化学气相沉积(CVD)技术等。
分子束外延技术(MBE)是将所需要外延的膜料放在喷射炉中,在超高真空条件下使其加热蒸发,并将这些膜料组分的原子或分子按一定的比例喷射到加热的衬底上外延沉积成膜。
这种技术可方便控制组分浓度和杂质浓度,因此可以制出急剧变化杂质浓度和组分的器件。
此外,可以用反射式高能电子衍射(RHEED)原位观察薄膜晶体的生长情况。
化学气相沉积(CVD)技术是以单晶硅为衬底外延生长单晶硅薄膜的同质外延过程,其原理为硅源与氢气发生反应还原出Si。
该技术可以调控外延的元素种类、成分、杂质浓度、位置等,进而制备具有特殊结构或性能的器件。
此外,还可以通过直拉法或区熔法制备单晶硅外延薄膜。
以上内容仅供参考,建议查阅专业半导体书籍或咨询专业人士获取更准确的信息。
揭秘半导体制造全流程

揭秘半导体制造全流程每个半导体产品的制造都需要数百个工艺,整个制造过程大体可分为八个步骤:晶圆加工-氧化-光刻-刻蚀-薄膜沉积-互连-测试-封装。
第一步晶圆加工所有半导体工艺都始于一粒沙子!因为沙子所含的硅是生产晶圆所需要的原材料。
晶圆是将硅(Si)或砷化镓(GaAs)制成的单晶柱体切割形成的圆薄片。
要提取高纯度的硅材料需要用到硅砂,一种二氧化硅含量高达5N(99.999%)的特殊材料,也是制作晶圆的主要原材料。
晶圆加工就是制作获取上述晶圆的过程。
1.铸锭首先需将沙子与碳加热,发生还原反应,得到一氧化碳和硅,并不断重复该过程直至获得超高纯度的电子级硅(EG-Si)。
高纯硅熔化成液体,利用提拉发再凝固成单晶固体形式,称为“锭”,这就是半导体制造的第一步。
需要注意的是:单晶硅锭(硅柱)的制作精度要求很高,其圆整度误差要控制在纳米级。
2.锭切割前一个步骤完成后,需要用金刚石锯切掉铸锭的两端,再将其切割成一定厚度的薄片。
锭薄片直径决定了晶圆的尺寸,更大更薄的晶圆能被分割成更多的可用单元,有助于降低生产成本。
切割硅锭后需在薄片上加入“平坦区”或“凹痕”标记,方便在后续步骤中以其为标准设置加工方向。
3.晶圆表面抛光通过上述切割过程获得的薄片被称为“裸片”,即未经加工的“原料晶圆”。
裸片的表面凹凸不平,无法直接在上面印制电路图形。
因此,需要先通过研磨和化学刻蚀工艺去除表面瑕疵,然后通过抛光形成光洁的表面,再通过清洗去除残留污染物,即可获得表面整洁的成品晶圆。
第二步氧化氧化过程的作用是在晶圆表面形成保护膜。
它可以保护晶圆不受化学杂质影响、避免漏电流进入电路、预防离子植入过程中的扩散以及防止晶圆在刻蚀时滑脱。
氧化过程的第一步是去除杂质和污染物(有机物、金属等杂质及蒸发残留的水分),清洁完成后就可以将晶圆置于800至1200摄氏度的高温环境下,通过氧气或蒸气在晶圆表面的流动形成二氧化硅(即“氧化物”)层。
氧气扩散通过氧化层与硅反应形成不同厚度的氧化层,可以在氧化完成后测量它的厚度。
半导体制造工艺流程简介
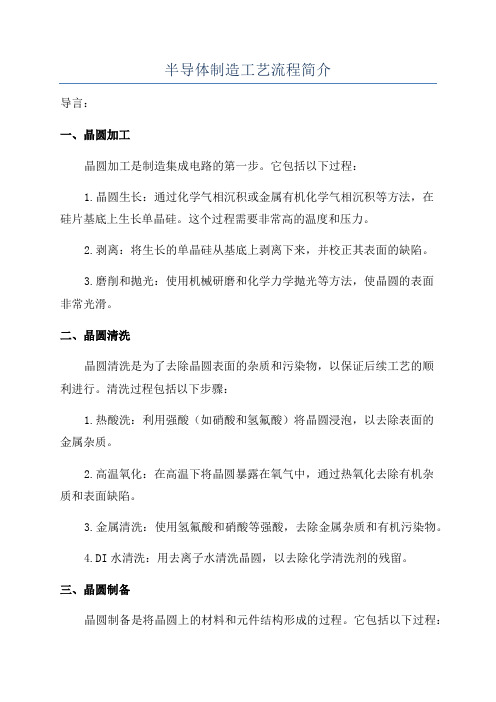
半导体制造工艺流程简介导言:一、晶圆加工晶圆加工是制造集成电路的第一步。
它包括以下过程:1.晶圆生长:通过化学气相沉积或金属有机化学气相沉积等方法,在硅片基底上生长单晶硅。
这个过程需要非常高的温度和压力。
2.剥离:将生长的单晶硅从基底上剥离下来,并校正其表面的缺陷。
3.磨削和抛光:使用机械研磨和化学力学抛光等方法,使晶圆的表面非常光滑。
二、晶圆清洗晶圆清洗是为了去除晶圆表面的杂质和污染物,以保证后续工艺的顺利进行。
清洗过程包括以下步骤:1.热酸洗:利用强酸(如硝酸和氢氟酸)将晶圆浸泡,以去除表面的金属杂质。
2.高温氧化:在高温下将晶圆暴露在氧气中,通过热氧化去除有机杂质和表面缺陷。
3.金属清洗:使用氢氟酸和硝酸等强酸,去除金属杂质和有机污染物。
4.DI水清洗:用去离子水清洗晶圆,以去除化学清洗剂的残留。
三、晶圆制备晶圆制备是将晶圆上的材料和元件结构形成的过程。
它包括以下过程:1.掩膜制作:将光敏材料涂覆在晶圆表面,通过光刻技术进行曝光和显影,形成图案化的光刻胶掩膜。
2.沉积:通过物理气相沉积或化学气相沉积等方法,在晶圆上沉积材料层,如金属、氧化物、硅等。
3.腐蚀:采用湿法或干法腐蚀等技术,去除晶圆上不需要的材料,形成所需的结构。
4.清洗:再次进行一系列清洗步骤,以去除腐蚀产物和掩膜残留物,保证材料层的质量。
四、材料获取材料获取是指在晶圆上制造晶体管、电阻器、电容器等器件结构的过程。
它包括以下步骤:1.掺杂:通过离子注入或扩散等方法,在晶圆上引入有选择性的杂质,以改变材料的导电性或断电性能。
2.退火:通过高温热处理,消除杂质引入过程中的晶格缺陷,并使掺杂的材料达到稳定状态。
3.金属-绝缘体-金属(MIM)沉积:在晶圆上沉积金属、绝缘体和金属三层结构,用于制造电容器。
4.金属-绝缘体(MIS)沉积:在晶圆上沉积金属和绝缘体两层结构,用于制造晶体管的栅极。
五、封装和测试封装是将晶圆上制造的芯片放在封装底座上,并封装成可插入其他设备的集成电路。
半导体八大工艺名称

半导体八大工艺名称1. 硅晶圆制备工艺硅晶圆制备是半导体制造过程的第一步,也是最为关键的一步。
它是指将高纯度的硅材料通过一系列的工艺步骤转化为薄而平整的硅晶圆。
硅晶圆制备工艺主要包括以下几个步骤:(1) 单晶生长单晶生长是将高纯度的硅材料通过熔融和凝固的过程,使其在特定的条件下形成单晶结构。
常用的单晶生长方法包括Czochralski法和区熔法。
(2) 切割切割是将生长好的硅单晶材料切割成薄片的过程。
常用的切割方法是采用金刚石刀片进行切割。
(3) 研磨和抛光研磨和抛光是将切割好的硅片进行表面处理,使其变得平整光滑的过程。
研磨通常使用研磨机进行,而抛光则使用化学机械抛光(CMP)工艺。
(4) 清洗清洗是将研磨和抛光后的硅片进行清洁处理,去除表面的污染物和杂质。
清洗过程通常采用酸洗和溶剂清洗的方法。
2. 光刻工艺光刻工艺是半导体制造中的一项关键工艺,用于将设计好的电路图案转移到硅晶圆上。
光刻工艺主要包括以下几个步骤:(1) 涂覆光刻胶涂覆光刻胶是将光刻胶涂覆在硅晶圆表面的过程。
光刻胶是一种敏感于紫外光的物质,可以通过紫外光的照射来改变其化学性质。
(2) 曝光曝光是将硅晶圆上的光刻胶通过光刻机上的光源进行照射,使其在特定区域发生化学反应。
曝光过程需要使用掩模板来控制光刻胶的曝光区域。
(3) 显影显影是将曝光后的光刻胶进行处理,使其在曝光区域发生溶解或固化的过程。
显影过程通常使用显影液进行。
(4) 清洗清洗是将显影后的硅晶圆进行清洁处理,去除残留的光刻胶和显影液。
3. 离子注入工艺离子注入工艺是将特定的离子注入到硅晶圆中,以改变其电学性质的过程。
离子注入工艺主要包括以下几个步骤:(1) 选择离子种类和能量选择合适的离子种类和能量是离子注入工艺的第一步。
不同的离子种类和能量可以改变硅晶圆的导电性质。
(2) 离子注入离子注入是将选择好的离子通过离子注入机进行注入的过程。
离子注入机通过加速器将离子加速到一定的能量,并将其注入到硅晶圆中。
构成晶圆制造的五大工艺
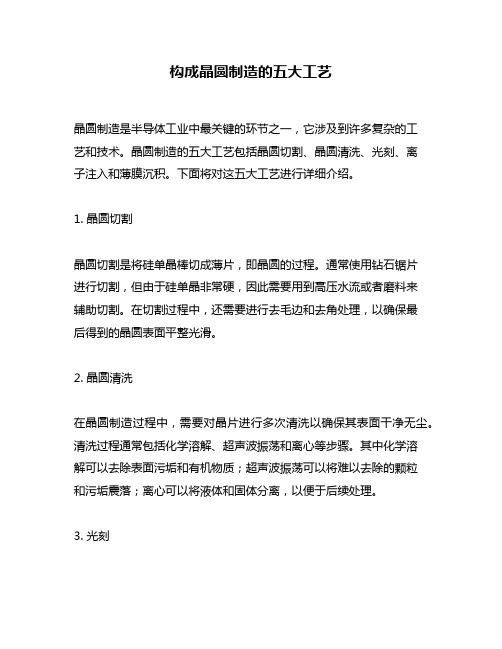
构成晶圆制造的五大工艺晶圆制造是半导体工业中最关键的环节之一,它涉及到许多复杂的工艺和技术。
晶圆制造的五大工艺包括晶圆切割、晶圆清洗、光刻、离子注入和薄膜沉积。
下面将对这五大工艺进行详细介绍。
1. 晶圆切割晶圆切割是将硅单晶棒切成薄片,即晶圆的过程。
通常使用钻石锯片进行切割,但由于硅单晶非常硬,因此需要用到高压水流或者磨料来辅助切割。
在切割过程中,还需要进行去毛边和去角处理,以确保最后得到的晶圆表面平整光滑。
2. 晶圆清洗在晶圆制造过程中,需要对晶片进行多次清洗以确保其表面干净无尘。
清洗过程通常包括化学溶解、超声波振荡和离心等步骤。
其中化学溶解可以去除表面污垢和有机物质;超声波振荡可以将难以去除的颗粒和污垢震落;离心可以将液体和固体分离,以便于后续处理。
3. 光刻光刻是一种利用光敏材料制作图形的技术。
在晶圆制造中,光刻通常用于制作电路图案。
首先,在晶圆上涂覆一层感光胶,然后使用掩模板对感光胶进行曝光,使得只有被曝光的部分会发生化学反应。
最后,使用化学溶解剂将未曝光的感光胶去除,留下所需的电路图案。
4. 离子注入离子注入是一种将材料中的离子注入到另一种材料中的技术。
在晶圆制造中,离子注入通常用于改变硅片的电学性质。
具体来说,通过向硅片中注入不同类型的离子(如磷、硼等),可以改变硅片中自由电子和空穴浓度,从而控制其导电性能。
5. 薄膜沉积薄膜沉积是一种将材料沉积到另一种材料表面上形成薄层的技术。
在晶圆制造中,薄膜沉积通常用于制作金属线路和绝缘层等。
常用的沉积方法包括物理气相沉积、化学气相沉积和溅射等。
其中,物理气相沉积是将固态材料加热到高温后,在真空环境下使其蒸发并在晶片表面形成薄层;化学气相沉积是通过化学反应在晶片表面形成薄层;溅射则是利用离子轰击材料表面将其溅射到晶片表面上。
总之,晶圆制造的五大工艺涵盖了许多复杂的技术和过程。
这些工艺不仅需要精密的设备和仪器,还需要高度专业化的技术人员来操作和控制。
- 1、下载文档前请自行甄别文档内容的完整性,平台不提供额外的编辑、内容补充、找答案等附加服务。
- 2、"仅部分预览"的文档,不可在线预览部分如存在完整性等问题,可反馈申请退款(可完整预览的文档不适用该条件!)。
- 3、如文档侵犯您的权益,请联系客服反馈,我们会尽快为您处理(人工客服工作时间:9:00-18:30)。
区熔法(FZ法)
• 优缺点:
• 可以制备大分解压 化合物半导体单晶
• 避免熔体挥发
• 质量大为提高
4.2 半导体外延制造技术
• 半导体的外延根据向衬底输送原子的方式可分为三种:液相外延、气相外延和真空外延。 MOCVD是一种典型的气相外延,而MBE又是 一种典型的真空外延。由于MOCVD既可以生 长组份突变的异质结,又可以生长组份渐变的 异质结,因此到目前为止,在半导体外延领域, MOCVD技术仍然是外延技术的主流。另外降 低反应室压力可以增加反应剂的流速,易于生 长突变异质结。再有在低压下,反应剂的浓度 可以控制得很低,因此外延生长的速率也可以 控制得很低。正因MOCVD在低压下外延具有 更多的优点,所以目前的MOCVD实际上都是 低压MOCVD,即LP MOCVD。
• 采用从溶液中再结晶原理的外延生长方法称液相 外延;采用从气相中生长单晶原理的称气相外延。 液相外延就是将所需的外延层材料(作为溶质,例 如GaAs),溶于某一溶剂(例如液态镓)成饱和 溶液,然后将衬底浸入此溶液,逐渐降低其温度, 溶质从过饱和溶液中不断析出,在衬底表面结晶 出单晶薄层。汽相外延生长可以用包含所需材料 为组分的某些化合物气体或蒸汽通过分解或还原 等化学反应淀积于衬底上,也可以用所需材料为 源材料,然后通过真空蒸发、溅射等物理过程使 源材料变为气态,再在衬底上凝聚。分子束外延 是一种经过改进的真空蒸发工艺。利用这种方法 可以精确控制射向衬底的蒸气速率,能获得厚度 只有几个原子厚的超薄单晶,并可得到不同材料 不同厚度的互相交叠的多层外延材料。非晶态半 导体虽然没有单晶制备的问题,但制备工艺与上 述方法相似,一般常用的方法是从汽相中生长薄 膜非晶材料。
由于成本和性能的原因,直拉法(CZ)单晶硅材料应用最广。在IC工 业中所用的材料主要是CZ抛光片和外延片。存储器电路通常使用CZ抛光 片,因成本较低。逻辑电路一般使用价格较高的外延片,因其在IC制造 中有更好的适用性并具有消除Latch-up的能力。 单晶硅也称硅单晶,是电子信息材料中最基础性材料,属半导体材料类。 单晶硅已渗透到国民经济和国防科技中各个领域,当今全球超过2000亿 美元的电子通信半导体市场中95%以上的半导体器件及99%以上的集成 电路用硅。
• 砷化镓的外延生长按工艺可分为气相和液相外 延,所得外延层在纯度和晶体完整性方面均优 于体单晶材料。通用的汽相外延工艺为 Ga/AsCl3/H2法,这种方法的变通工艺有 Ga/HCl/AsH3/H2和Ga/AsCl3/N2法。为了改 进Ga/AsCl3/H2体系气相外延层的质量,还研 究出低温和低温低压下的外延生长工艺。液相 外延工艺是用 Ga/GaAs熔池覆盖衬底表面,然 后通过降温以生长外延层,也可采用温度梯度生 长法或施加直流电的电外延法。在器件(特别是 微波器件)的制造方面,汽相外延的应用比液相 外延广泛。液相外延可用来制造异质结(如 GaAs/AlxGa1-xAs),因此它是制造砷化镓双 异质结激光器和太阳电池等的重要手段。
第四章 半导体单晶和薄膜制造技术
4.1 半导体单晶的制造
•
单晶硅圆片按其直径分为6英寸、8英寸、12英寸(300毫米)及18英寸 (450毫米)等。直径越大的圆片,所能刻制的集成电路越多,芯片的成 本也就越低。但大尺寸晶片对材料和技术的要求也越高。单晶硅按晶体 生长方法的不同,分为直拉法(CZ)、区熔法(FZ)和外延法。直拉法、 区熔法生长单晶硅棒材,外延法生长单晶硅薄膜。直拉法生长的单晶硅 主要用于半导体集成电路、二极管、外延片衬底、太阳能电池。目前晶 体直径可控制在Φ3~8英寸。区熔法单晶主要用于高压大功率可控整流器 件领域,广泛用于大功率输变电、电力机车、整流、变频、机电一体化、 节能灯、电视机等系列产品。目前晶体直径可控制在Φ3~6英寸。外延片 主要用于集成电路领域。
常用外延材料及其工艺
砷化镓材料的制备
• 与硅相仿,砷化镓材料也可分为体单晶和外延 材料两类。体单晶可以用作外延的衬底材料, 也可以采用离子注入掺杂工艺直接制造集成电 路(采用高质量、大截面、半绝缘砷化镓单 晶)。重点是液封直拉法(即液封乔赫拉斯基 法,简称LEC法),但水平舟生长法(即水平布 里其曼法)因制出的单晶质量和均匀性较好, 仍然受到一定的重视。液封直拉法的一个新发 展是在高压单晶炉内用热解氮化硼 (PBN)坩埚 和干燥的氧化硼液封剂直接合成和拉制不掺杂、 半绝缘砷化镓单晶。另外,常压下用石英坩埚 和含水氧化硼为液封剂的方法也已试验成功。 不论水平舟生长法或是液封直拉法,晶体的直 径均可达到100~150毫米而与硅单晶相仿。
• 砷化镓外延技术还有分子束外延和金属有机化 合物汽相沉积外延。分子束外延是在超高真空 条件下,使一个或多个热分子束与晶体表面相 作用而生长出外延层的方法。对入射分子或原 子束流施加严格的控制,可以生长出超晶格结 构,例如由交替的GaAs和AlxGa As薄层(厚 度仅10埃)所组成的结构。金属有机化合物汽 相沉积外延是用三甲基镓或三乙基镓与砷烷相 作用而生长外延层。用这种方法也能适当地控 制外延层的浓度、厚度和结构。与分子束外延 相比,金属有机化合物汽相沉积外延设备和工 艺均较简单,但分子束外延层的质量较高。