炉外精炼的工艺技术发展终稿
我国炉外精练技术的发展前景和趋势分析

我国炉外精练技术的发展前景和趋势分析我国炉外精炼技术是冶金行业中一项重要的技术,它是指在冶炼过程中,将粗炼钢液通过炉外装置进行再处理,以提高钢液的质量和温度,减少杂质含量,从而得到更加优质的成品钢材。
随着我国工业化进程的加快和环保意识的提高,炉外精炼技术的发展前景和趋势备受关注。
一、炉外精炼技术的发展历程炉外精炼技术起源于20世纪60年代,当时主要应用于日本、美国等发达国家的钢铁企业。
最早的炉外精炼设备是气吹精炼炼钢炉(LD炉),它利用氧气吹入炉内,通过氧气的化学作用来脱除炼钢过程中产生的杂质和非金属夹杂物,提高成品钢的质量。
而后,随着技术的不断进步和创新,我国也开始引进和发展炉外精炼技术,并在80年代成功开发了自己的炉外精炼装置。
目前,我国的炉外精炼技术已经取得了长足的进步,主要体现在以下几个方面:1. 技术水平不断提升。
我国的炉外精炼技术已经从最初的气吹精炼炼钢炉(LD炉)发展到了RH、VOD、Ladle Furnace等多种不同类型的炉外精炼设备,每一种设备都具有自己的特点和优势,可以满足不同钢种的精炼需求。
2. 炉外精炼技术与自动化技术相结合。
随着我国制造业的智能化升级,炉外精炼技术也在不断引入自动化设备和智能控制系统,以提高生产效率和产品质量。
利用先进的传感技术和控制系统,可以实现对炉外精炼过程的精准监测和控制,确保精炼过程的稳定和可控性。
3. 绿色环保技术的应用。
在炉外精炼过程中,会产生大量的废气和废渣,而这些废气和废渣的排放会对环境造成严重的污染。
在炉外精炼技术的发展中,我国也加大了对绿色环保技术的研发和应用力度,致力于减少废物排放,提高资源利用率。
1. 技术持续创新。
随着科技的不断进步和需求的不断增长,炉外精炼技术将会继续进行技术升级和改造,以适应不同类型钢材的精炼要求。
未来,我国的炉外精炼技术有望实现更高效、更节能、更绿色的发展。
2. 非金属夹杂物的去除技术。
随着精细化钢铁品种的增多,我国的炉外精炼技术将更加注重去除非金属夹杂物的工艺研究和应用,以满足高端产品对钢材质量的严格要求。
炉外精炼的工艺技术发展终稿
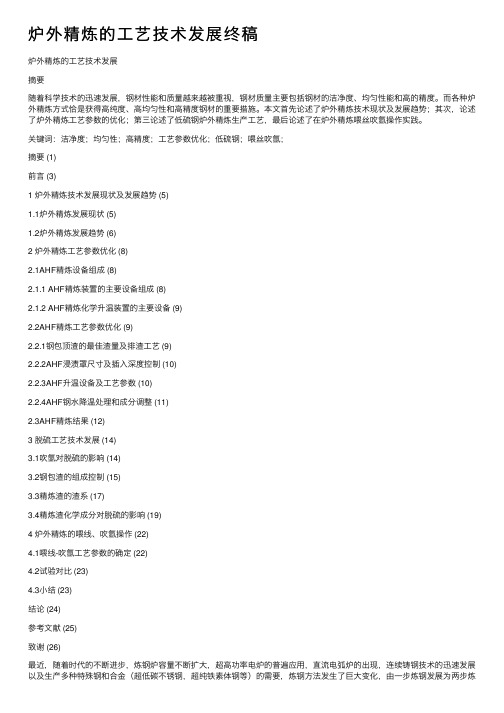
炉外精炼的⼯艺技术发展终稿炉外精炼的⼯艺技术发展摘要随着科学技术的迅速发展,钢材性能和质量越来越被重视,钢材质量主要包括钢材的洁净度、均匀性能和⾼的精度。
⽽各种炉外精炼⽅式恰是获得⾼纯度、⾼均匀性和⾼精度钢材的重要措施。
本⽂⾸先论述了炉外精炼技术现状及发展趋势;其次,论述了炉外精炼⼯艺参数的优化;第三论述了低硫钢炉外精炼⽣产⼯艺,最后论述了在炉外精炼喂丝吹氩操作实践。
关键词:洁净度;均匀性;⾼精度;⼯艺参数优化;低硫钢;喂丝吹氩;摘要 (1)前⾔ (3)1 炉外精炼技术发展现状及发展趋势 (5)1.1炉外精炼发展现状 (5)1.2炉外精炼发展趋势 (6)2 炉外精炼⼯艺参数优化 (8)2.1AHF精炼设备组成 (8)2.1.1 AHF精炼装置的主要设备组成 (8)2.1.2 AHF精炼化学升温装置的主要设备 (9)2.2AHF精炼⼯艺参数优化 (9)2.2.1钢包顶渣的最佳渣量及排渣⼯艺 (9)2.2.2AHF浸渍罩尺⼨及插⼊深度控制 (10)2.2.3AHF升温设备及⼯艺参数 (10)2.2.4AHF钢⽔降温处理和成分调整 (11)2.3AHF精炼结果 (12)3 脱硫⼯艺技术发展 (14)3.1吹氩对脱硫的影响 (14)3.2钢包渣的组成控制 (15)3.3精炼渣的渣系 (17)3.4精炼渣化学成分对脱硫的影响 (19)4 炉外精炼的喂线、吹氩操作 (22)4.1喂线-吹氩⼯艺参数的确定 (22)4.2试验对⽐ (23)4.3⼩结 (23)结论 (24)参考⽂献 (25)致谢 (26)最近,随着时代的不断进步,炼钢炉容量不断扩⼤,超⾼功率电炉的普遍应⽤,直流电弧炉的出现,连续铸钢技术的迅速发展以及⽣产多种特殊钢和合⾦(超低碳不锈钢,超纯铁素体钢等)的需要,炼钢⽅法发⽣了巨⼤变化,由⼀步炼钢发展为两步炼钢,即炉内初炼和炉外精炼。
炉外精炼技术之所以有了较为迅猛的发展,是由于其能够提⾼钢质量和产量,降低成本,改善劳动条件等优点。
精选炉外精炼工艺
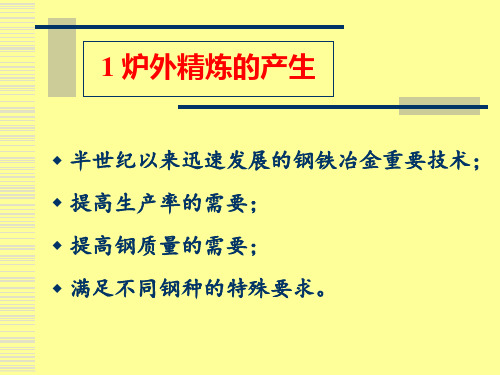
合成渣洗
根据要求将各种渣料配置成满足某种冶金功能 的合成炉渣;
通过在专门的炼渣炉中熔炼,出钢时钢液与炉 渣混合,实现脱硫及脱氧去夹杂功能;
不能去除钢中气体; 必须将原炉渣去除; 同炉渣洗、异炉渣洗。
真空处理
脱气的主要方法 提高真空度可将钢中C、H、O降低;
日本真空技术,真空度到1 torr; C<10ppm,H<1ppm,O<5ppm
3.3 VD/VOD 炉
VD 的功能仅是真空加搅拌, VOD 是Vacuum and stir and injection
oxygen; VD主要应用于轴承钢脱氧; VOD 主要用于不锈钢冶炼;
V D / VOD
VD工艺
以轴承钢冶炼为例
轴承钢最重要的性能指标是疲劳寿命。
影响轴承钢寿命的重要指标是钢中氧含量,钢 中[O]控制在10ppm为好。
3.5 CAS、CAS-OB精炼工 艺
工艺优点: • 钢液升温和精确控制钢水温度 • 促进夹杂物上浮,提高钢水纯净度 • 精确控制钢液成分,实现窄成分控制 • 均匀钢水成分和温度 • 与喂线配合,可进行夹杂物的变性处理 • 冶炼节奏快,适合转炉的冶炼节奏。
CAS和CAS-OB
O2
CAS-OB的冶炼效果
加热;升温速度5-6℃/min; 钢液成分:吹氧前后变化不大; 钢水洁净度:[O]基本不变,可降低
[N]含量。
3.6 喷粉工艺
效果最好投资及使用成本最低也是最不好掌握的 技术;可脱硫、脱磷、合金化、夹杂变性;
工艺参数: 喷枪插入深度;h=H(钢液深)-hc(喷入深); 喷吹压力:大于钢液、炉渣及大气压; 喷吹时间:喷粉设备及钢液容纳粉剂的能力; 供料速度:设备能力及钢液化学反应速度; 载气能力与粉气比。
炉外精炼工艺技术
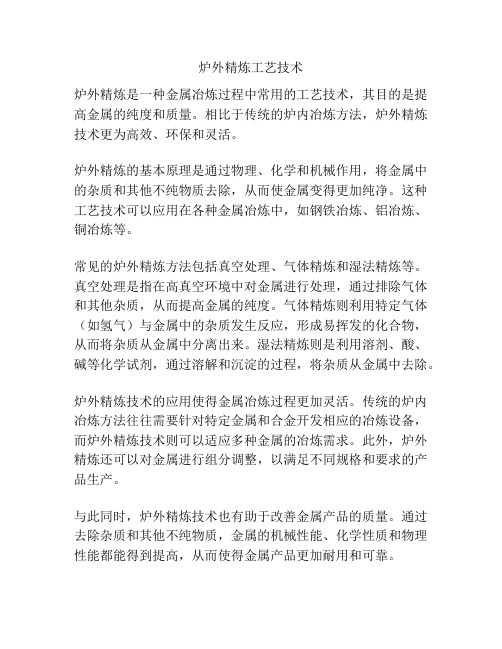
炉外精炼工艺技术炉外精炼是一种金属冶炼过程中常用的工艺技术,其目的是提高金属的纯度和质量。
相比于传统的炉内冶炼方法,炉外精炼技术更为高效、环保和灵活。
炉外精炼的基本原理是通过物理、化学和机械作用,将金属中的杂质和其他不纯物质去除,从而使金属变得更加纯净。
这种工艺技术可以应用在各种金属冶炼中,如钢铁冶炼、铝冶炼、铜冶炼等。
常见的炉外精炼方法包括真空处理、气体精炼和湿法精炼等。
真空处理是指在高真空环境中对金属进行处理,通过排除气体和其他杂质,从而提高金属的纯度。
气体精炼则利用特定气体(如氢气)与金属中的杂质发生反应,形成易挥发的化合物,从而将杂质从金属中分离出来。
湿法精炼则是利用溶剂、酸、碱等化学试剂,通过溶解和沉淀的过程,将杂质从金属中去除。
炉外精炼技术的应用使得金属冶炼过程更加灵活。
传统的炉内冶炼方法往往需要针对特定金属和合金开发相应的冶炼设备,而炉外精炼技术则可以适应多种金属的冶炼需求。
此外,炉外精炼还可以对金属进行组分调整,以满足不同规格和要求的产品生产。
与此同时,炉外精炼技术也有助于改善金属产品的质量。
通过去除杂质和其他不纯物质,金属的机械性能、化学性质和物理性能都能得到提高,从而使得金属产品更加耐用和可靠。
除了提高金属产品的质量外,炉外精炼技术还可以减少环境污染。
传统的炉内冶炼方法往往会产生大量的废气、废水和废渣,对环境造成严重的污染。
而炉外精炼技术则通过控制冶炼过程中的气体、液体和固体排放,使得废气减少、废水得到处理和回收、废渣变废为宝,从而实现了资源的循环利用和环境保护。
总之,炉外精炼工艺技术是一种高效、环保和灵活的金属冶炼方法。
它通过利用物理、化学和机械作用,对金属中的杂质和其他不纯物质进行去除,从而提高金属的纯度和质量。
这种技术的应用不仅可以改善金属产品的质量,还可以减少环境污染,实现资源的循环利用。
炉外精炼工艺技术是金属冶炼领域中的一项重要技术手段,它能够在金属冶炼过程中去除杂质和不纯物质,提高金属的纯度和质量。
炉外精炼的工艺设计

炉外精炼的工艺设计炉外精炼是一种对金属合金进行深度精炼的工艺,在金属冶炼过程中起到非常重要的作用。
炉外精炼技术可以通过减小金属杂质含量、提高合金成分均匀性、调整合金中的内应力和改善合金物理性能等多个方面对合金进行改善和调整。
本文将详细介绍炉外精炼的工艺设计。
1.炉外精炼工艺选择-操作方式:炉外精炼可以采用化学或物理方式进行,例如溶剂抽取、真空除气、电渣重熔等。
根据合金材料和工艺要求选择最合适的精炼方式。
-精炼介质:选择合适的精炼介质,例如惰性气体、真空、溶剂等,根据材料特性和成分要求进行选择。
-精炼设备:根据工艺要求选择合适的设备,例如真空炉、溶剂萃取设备、电渣炉等。
2.炉外精炼的关键参数控制-温度:精确控制精炼温度,根据不同的材料和要求进行调整,确保炉外精炼的效果。
-压力:根据材料的气体溶解度和精炼介质的选择,调整精炼过程中的压力,确保溶质向介质中迁移。
-时间:根据精炼过程的要求,确定精炼的时间,在一段时间内实现对杂质去除、合金调整和分相等的目标。
-速度:根据炉外精炼的工艺要求,确定精炼过程中的速度,例如溶质迁移速度、溶剂流动速度等。
3.炉外精炼的工艺步骤-准备工作:包括材料的预处理、精炼设备的准备、精炼介质的选择等。
-进料:将需要精炼的材料进料到精炼设备中,并根据要求确定进料方式和进料量。
-精炼操作:根据工艺要求进行精炼操作,例如加热、真空抽取、溶剂萃取等。
-过程监测:通过监测精炼过程中的温度、压力、溶质浓度等参数,控制精炼过程的效果,并及时调整工艺参数。
-精炼结束:根据工艺要求,判断精炼过程是否达到预期目标,如果达到预期目标,则结束精炼过程。
-产品处理:对精炼后的产品进行处理,例如冷却、干燥、分析检测等。
4.炉外精炼的优点和应用炉外精炼技术具有以下优点:-可以有效地去除金属杂质,改善合金的纯度和均匀性。
-可以调整合金的成分和物理性能,满足不同的应用要求。
-可以减小合金中的内应力,提高材料的延展性和抗拉强度。
转炉炼钢炉外精炼与连铸工艺
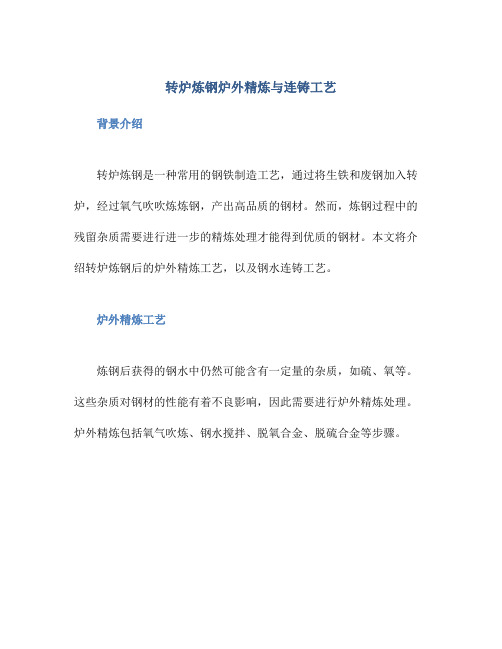
转炉炼钢炉外精炼与连铸工艺背景介绍转炉炼钢是一种常用的钢铁制造工艺,通过将生铁和废钢加入转炉,经过氧气吹吹炼炼钢,产出高品质的钢材。
然而,炼钢过程中的残留杂质需要进行进一步的精炼处理才能得到优质的钢材。
本文将介绍转炉炼钢后的炉外精炼工艺,以及钢水连铸工艺。
炉外精炼工艺炼钢后获得的钢水中仍然可能含有一定量的杂质,如硫、氧等。
这些杂质对钢材的性能有着不良影响,因此需要进行炉外精炼处理。
炉外精炼包括氧气吹炼、钢水搅拌、脱氧合金、脱硫合金等步骤。
氧气吹炼是炼钢后必不可少的处理步骤之一。
通过将氧气通入钢水中,可以氧化钢水中的杂质,提高钢水的纯度。
同时,氧气吹炼还可以促进钢水的温度均匀性,减少气泡等缺陷。
钢水搅拌钢水搅拌是通过机械手等设备对炉外的钢水进行搅拌,促使钢水中的气泡和杂质向上浮动,有助于去除杂质并提高钢水的均匀性。
脱氧合金脱氧合金是指向钢水中添加具有强还原性的合金元素,如硅、铝等。
这些合金元素可以与钢水中氧化铁等氧化物结合,减少钢水中氧的含量,提高钢水的纯度。
脱硫合金是指向钢水中添加具有高硫亲和性的合金元素,如镁、钙等。
这些合金元素可以与钢水中的硫结合,从而降低钢水中的硫含量,提高钢材的质量。
钢水连铸工艺钢水连铸是钢材生产中的一项重要工艺,通过将炉外精炼处理后的钢水连续铸造成坯料、板材等形状的半成品。
钢水连铸可以有效提高生产效率,减少钢材的能耗和生产成本。
连铸机连铸机是实现钢水连铸的设备,通常由结晶器、浇铸机、冷却装置等组成。
在连铸机中,经过炉外精炼处理的钢水被连续铸造成各种形状的半成品,如板材、方坯等。
在连铸过程中,钢水经过结晶器冷却凝固,逐渐形成坯料,然后通过浇铸机进行切割成指定长度的板材。
冷却装置可以控制板材的温度和结晶组织,保证最终产品的质量。
连铸优势钢水连铸具有生产周期短、成品质量高、生产过程环保等优势。
同时,连铸还可以减少人工操作,提高生产效率,是现代钢铁制造中不可或缺的工艺。
结语通过炉外精炼和钢水连铸工艺,钢铁制造厂可以生产出高品质、高效率的钢材产品,满足市场需求。
我国炉外精练技术的发展前景和趋势分析

我国炉外精练技术的发展前景和趋势分析1. 引言1.1 炉外精练技术的定义炉外精练技术是指在炉外对金属进行精细加工和提纯的一种技术。
通过使用高温加热和物理、化学等方法,将金属原料中的杂质和不纯物质去除,从而使金属的质量和纯度得到提高。
这种技术可以有效地提高金属材料的性能和品质,满足不同需求下金属材料的要求。
炉外精练技术的功能主要包括提高金属的纯度、改善金属的微观组织结构、调整金属的化学成分以及控制金属的晶粒粒度。
通过这些技术手段,金属材料的力学性能、耐热性、耐腐蚀性等方面都可以得到显著提升。
炉外精练技术在金属制造和加工领域中具有重要的应用价值,可以广泛应用于钢铁、有色金属等材料的生产过程中。
这项技术的发展,对我国的工业生产、科研以及经济建设都具有重要意义,有助于提高我国金属材料生产的质量和技术水平,推动相关产业的升级和发展。
1.2 炉外精练技术的重要性炉外精练技术是钢铁生产中至关重要的一环,其重要性主要体现在以下几个方面:1. 提高钢铁质量:炉外精练技术能够有效降低钢水中的杂质含量,使钢水质量更加纯净,从而提高最终产出的钢铁质量。
优质的钢铁产品更受市场青睐,能够提升企业的竞争力。
2. 提高生产效率:通过炉外精练技术的应用,可以实现钢水的快速净化和调控,提高炉台利用率,减少生产过程中的能耗和时间浪费,进而提高生产效率和降低生产成本。
3. 保护环境:炉外精练技术可以有效控制和减少废气废渣的排放,从而减少对环境的污染,符合环境保护和可持续发展的要求。
4. 提升技术水平:研究和应用炉外精练技术可以促进钢铁生产技术的创新和提高,推动整个行业向更加先进、高效的方向发展,并增强我国在钢铁生产领域的国际竞争力。
炉外精练技术的重要性不可忽视,它不仅关乎钢铁企业的发展和竞争力,还对环境保护和钢铁行业的可持续发展具有重要意义。
进一步推动炉外精练技术的研究和应用具有重要意义。
1.3 研究炉外精练技术的意义研究炉外精练技术的意义在于探索先进的金属材料加工技术,提高金属材料的品质和性能。
浅谈炉外精炼技术的应用和发展
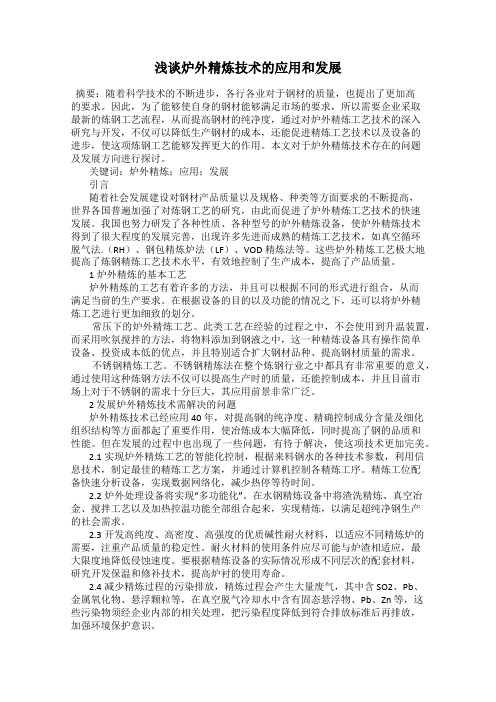
浅谈炉外精炼技术的应用和发展摘要:随着科学技术的不断进步,各行各业对于钢材的质量,也提出了更加高的要求。
因此,为了能够使自身的钢材能够满足市场的要求,所以需要企业采取最新的炼钢工艺流程,从而提高钢材的纯净度,通过对炉外精炼工艺技术的深入研究与开发,不仅可以降低生产钢材的成本,还能促进精炼工艺技术以及设备的进步,使这项炼钢工艺能够发挥更大的作用。
本文对于炉外精炼技术存在的问题及发展方向进行探讨。
关键词:炉外精炼;应用;发展引言随着社会发展建设对钢材产品质量以及规格、种类等方面要求的不断提高,世界各国普遍加强了对炼钢工艺的研究,由此而促进了炉外精炼工艺技术的快速发展。
我国也努力研发了各种性质、各种型号的炉外精炼设备,使炉外精炼技术得到了很大程度的发展完善,出现许多先进而成熟的精炼工艺技术,如真空循环脱气法.(RH)、钢包精炼炉法(LF)、VOD精炼法等。
这些炉外精炼工艺极大地提高了炼钢精炼工艺技术水平,有效地控制了生产成本,提高了产品质量。
1炉外精炼的基本工艺炉外精炼的工艺有着许多的方法,并且可以根据不同的形式进行组合,从而满足当前的生产要求。
在根据设备的目的以及功能的情况之下,还可以将炉外精炼工艺进行更加细致的划分。
常压下的炉外精炼工艺。
此类工艺在经验的过程之中,不会使用到升温装置,而采用吹氛搅拌的方法,将物料添加到钢液之中,这一种精炼设备具有操作简单设备、投资成本低的优点,并且特别适合扩大钢材品种、提高钢材质量的需求。
不锈钢精炼工艺。
不锈钢精炼法在整个炼钢行业之中都具有非常重要的意义,通过使用这种炼钢方法不仅可以提高生产时的质量,还能控制成本,并且目前市场上对于不锈钢的需求十分巨大,其应用前景非常广泛。
2 发展炉外精炼技术需解决的问题炉外精炼技术已经应用 40 年,对提高钢的纯净度、精确控制成分含量及细化组织结构等方面都起了重要作用,使冶炼成本大幅降低,同时提高了钢的品质和性能。
但在发展的过程中也出现了一些问题,有待于解决,使这项技术更加完美。
- 1、下载文档前请自行甄别文档内容的完整性,平台不提供额外的编辑、内容补充、找答案等附加服务。
- 2、"仅部分预览"的文档,不可在线预览部分如存在完整性等问题,可反馈申请退款(可完整预览的文档不适用该条件!)。
- 3、如文档侵犯您的权益,请联系客服反馈,我们会尽快为您处理(人工客服工作时间:9:00-18:30)。
炉外精炼的工艺技术发展终稿(总28页)本页仅作为文档页封面,使用时可以删除This document is for reference only-rar21year.March炉外精炼的工艺技术发展摘要随着科学技术的迅速发展,钢材性能和质量越来越被重视,钢材质量主要包括钢材的洁净度、均匀性能和高的精度。
而各种炉外精炼方式恰是获得高纯度、高均匀性和高精度钢材的重要措施。
本文首先论述了炉外精炼技术现状及发展趋势;其次,论述了炉外精炼工艺参数的优化;第三论述了低硫钢炉外精炼生产工艺,最后论述了在炉外精炼喂丝吹氩操作实践。
关键词:洁净度;均匀性;高精度;工艺参数优化;低硫钢;喂丝吹氩;目录摘要 .......................................................................................................... 错误!未定义书签。
前言 .......................................................................................................... 错误!未定义书签。
1 炉外精炼技术发展现状及发展趋势 .................................................... 错误!未定义书签。
炉外精炼发展现状 ............................................................................ 错误!未定义书签。
炉外精炼发展趋势 ............................................................................ 错误!未定义书签。
2 炉外精炼工艺参数优化 ........................................................................ 错误!未定义书签。
AHF精炼设备组成............................................................................ 错误!未定义书签。
AHF精炼装置的主要设备组成................................................ 错误!未定义书签。
AHF精炼化学升温装置的主要设备........................................ 错误!未定义书签。
AHF精炼工艺参数优化.................................................................... 错误!未定义书签。
钢包顶渣的最佳渣量及排渣工艺 ........................................ 错误!未定义书签。
AHF浸渍罩尺寸及插入深度控制 ........................................ 错误!未定义书签。
AHF升温设备及工艺参数 .................................................... 错误!未定义书签。
AHF钢水降温处理和成分调整 ............................................ 错误!未定义书签。
AHF精炼结果 ................................................................................. 错误!未定义书签。
3 脱硫工艺技术发展 ................................................................................ 错误!未定义书签。
吹氩对脱硫的影响 ............................................................................ 错误!未定义书签。
钢包渣的组成控制 ............................................................................ 错误!未定义书签。
精炼渣的渣系 .................................................................................... 错误!未定义书签。
精炼渣化学成分对脱硫的影响 ........................................................ 错误!未定义书签。
4 炉外精炼的喂线、吹氩操作 ................................................................. 错误!未定义书签。
喂线-吹氩工艺参数的确定............................................................... 错误!未定义书签。
试验对比 ............................................................................................ 错误!未定义书签。
小结 .................................................................................................... 错误!未定义书签。
结论 .......................................................................................................... 错误!未定义书签。
参考文献 ................................................................................................. 错误!未定义书签。
致谢 .................................................................................................... 错误!未定义书签。
前言最近,随着时代的不断进步,炼钢炉容量不断扩大,超高功率电炉的普遍应用,直流电弧炉的出现,连续铸钢技术的迅速发展以及生产多种特殊钢和合金(超低碳不锈钢,超纯铁素体钢等)的需要,炼钢方法发生了巨大变化,由一步炼钢发展为两步炼钢,即炉内初炼和炉外精炼。
炉外精炼技术之所以有了较为迅猛的发展,是由于其能够提高钢质量和产量,降低成本,改善劳动条件等优点。
目前,全世界已有炉外精炼设备30余种,1100余台,我国拥有不同精炼设备40~50台。
为了增强在国内和国外市场上的竞争力,发展新的工艺是有必要的。
这些工艺必须是经济的。
目前,典型的炼钢炉是一个废钢熔化装置,在炼低合金钢的情况下,在炉中脱碳和脱磷以及升温到符合出钢要求,其全部精炼过程都是在钢包中进行的,进而提高了炼钢设备的生产能力。
通过炉外精炼技术可冶炼出具有高质量特性的钢种满足实际需要,具体要求如下:①精确控制成分以保证力学性能的稳定。
②减少钢中硫、磷含量以改善冲击性能、抗层状拉裂性能、热脆性,并能减少中心偏析和防止连铸坯的表面缺陷。
③减少钢中氧、氢、氮含量以减少超声波探伤缺陷、条状裂纹等,并且能改善钢材的制管性能。
④使用先进技术精炼钢液以满足对钢质量的各种特殊需要。
例如,控制硫化物夹杂形态以防止轻质裂纹。
⑤控制夹杂物的形状以改善钢的深冲性能和钢的加工性能。
⑥脱碳到极低程度,以提高钢的深冲性能、电磁性能和耐腐蚀性能。
⑦防止钢水的二次氧化和重新吸气,以免炉外精炼的效果前功尽弃。
炉外精炼的产生和发展与国民经济的需要和科学技术的发展水平是分不开的。
在很早以前,人们就产生了利用真空去除钢中气体的想法,如1860年英国贝赛迈尔就曾有过罐内钢桶去气的设想,1884年英国艾特肯也曾提出过提升法(类似DH法);1932年捷克人科贝尔曾提出并实现了带盖钢桶去气法。
但由于当时真空技术的发展水平低下,还制造不出抽气能力很大的真空泵,以上方法因规模太小并未很快地应用于生产。
二次世界大战后,随着真空技术的发展和大型蒸汽喷射泵的研制成功,为钢液的大规模真空处理提供了条件。
此后,大型生产性真空脱气设备相继被研究成功,并在发展中不断完善,增加了搅拌、加热、吹氧等装置,从而单纯的真空脱气设备转变成为成为灵活多样的各种炉外真空精炼设备。
在炉外精炼发展过程中,人们发现不仅靠真空可以降低钢中的气体,采用惰性气体降低有害气体的分压,也可以达到同样目的,由此发展了不同形式的非真空精炼法。
各种炉外精炼方法的工艺各异,其共同特点:有一个理想的精炼气氛条件,通常用真空、惰性气体和还原性气氛;搅动钢水,可采用电磁力搅拌,惰性气体搅拌或机械搅拌的方法;为补偿精炼过程的钢水温度损失,而采用加热设施,有电弧加热、等离子加热或增加钢水化学热等。
1 炉外精炼技术发展现状及发展趋势炉外精炼发展现状近年来,国外炉外精炼设备发展很快,主要为炉外精炼设备逐年增长。
目前,国外炉外精炼设备的总数已超过1000座.随着对超低碳钢和超低硫磷钢的需要量越来越大,RH、 RH-0B 、RH-PB真空精炼设备将继续增加,现代化的转炉炼钢车间都采用这种精炼方法。
AOD、VOD等主要用于精炼不锈钢的炉外精炼设备,其生产能力已完全可以满足生产不锈钢的需要。
从美国和加拿大发展情况来看,一是LF炉发展很快,在具有三种电弧加热功能的精炼炉中占有绝对优势;另一个是钢包精炼站发展很快。
在炉外精炼设备发展中,连铸发展和要求钢水清洁度起了决定作用。
由于美国和加拿大连铸比仍较低,其炉外精炼设备发展就占很大比重,而投资较少的LF炉相应也占了较大比重。
从有关数据表明,不同种类的炉外精炼设备的发展是不同的,其中,发展速度最快的是LF、RH。
1985年宝钢投产后,引进的RH、CAS、KIP正常投入生产,在线作业对提高产品质量,开发高水平的品种等方面起到了良好的示范作用。
80年代后期,国产喂线机与包芯线喂线技术已在许多钢厂广泛使用。