真空精炼炉工艺技术说明VOD设备
炉外精炼工艺设备

炉外精炼工艺设备1、精炼用钢包的内型,其钢水部分的直径与高度比应为0.9~1.1,钢液面以上的自由空间高度应根据不同精炼方法,按下列规定确定:(1)单独用于RH应为400mm~600mm;(2)单独用于LF应为500mm~600mm;(3)用于VD应为800mm~1000mm;(4)用于VOD应为1200mm以上。
2、LF精炼设计应符合下列规定:(1)配备的变压器单位功率应为150(kV·A)/t~200(kV·A)/t,钢水加热速度应达到4℃/min~5℃/min。
(2)电极导电横臂应采用水冷铜钢复合(或铝合金)导电臂。
电极中心圆直径宜小,二次侧短网长度宜短,三相导体应在任意横截面上为等腰或等边三角形布置,三相阻抗不平衡度应小于5%。
(3)电极的升降行程应满足最小处理钢水量的要求,最小处理钢水量宜为公称容量的50%~80%。
(4)包盖应采用管式全水冷钢包盖,钢包盖的结构形式及其与钢包口的配合关系,应能保持钢液面上良好的还原性气氛。
(5)LF应配置机械化加料系统,并应设置6个~20个高位贮存料仓。
料仓容积应保证LF炉工作大于8h所需的量。
3、RH精炼设计应符合下列规定:(1)真空室的设计应根据精炼钢种与钢包尺寸确定真空室的主要参数。
可采用多真空室小车移动方式,真空室可分别移动于处理工位与等待工位,依次轮换工作。
根据布置的需要,也可采用热弯管移动方式。
(2)RH真空室应设在线快速升温装置,并应使处理前真空室内壁表面温度达到1400℃以上。
(3)RH精炼钢包(车)升降宜采用液压机构,正常升降速度不应小于2000mm /min,升降行程应满足处理最小钢水量的要求。
(4)在高海拔地区建RH,应根据当地大气压计算钢水提升高度,确定合理的真空室浸渍管长度。
(5)公称容量不大于200t的RH真空室宜采用分体结构形式。
4、VD、VOD的真空罐设计选型应符合下列规定:(1)VD、VOD的真空罐直径应满足钢包吊放作业时进钩和退钩的要求,其高度除应按钢包高度确定外,还应满足容纳漏钢钢水缓存需要的空间,可在真空罐外设置事故漏钢坑;(2)真空罐罐体与罐盖之间的大法兰密封圈应设置遮护装置;(3)真空罐盖的升降可采用液压或电动方式,罐盖与罐体扣合时,罐盖应处于自由搁放状态;(4)真空罐盖上的设备与管线应合理布置,VOD用氧枪应位于钢包的中心线上,真空料罐的下料管应靠近钢包底吹氩气透气塞位置,测温取样枪应位于钢液面较平静的区域,气封针孔摄像仪与观察孔的位置与角度应保证清晰地观察钢液面距钢包口的距离;(5)当炼钢炉冶炼时间较短时可采用双真空罐形式。
VD真空精炼炉基本工艺操作规程
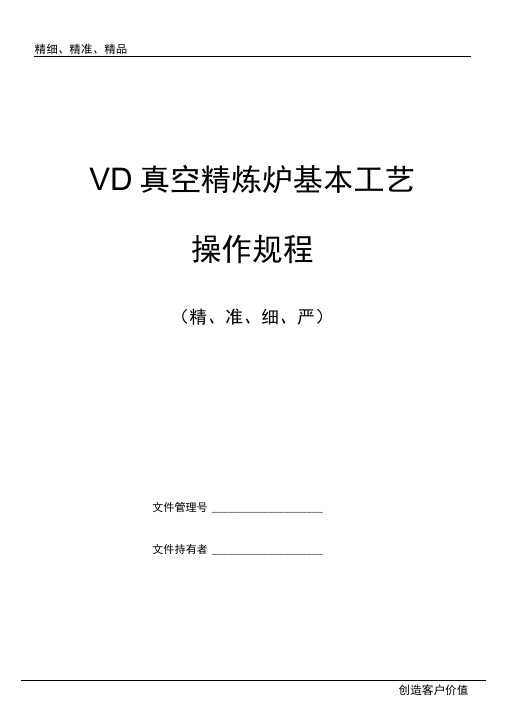
3.1 VD工艺操作原则
3.1.1钢包在真空罐中就位后,打开氩气阀门,将流量调至渣面轻微蠕动时停止,盖好真空罐盖,即可开始 真空处理。
3.1.2抽真空操作按相关操作规程进行。
3.1.3 VD处理过程中,要注意控制和调节吹氩流量。根据监视器观察渣面高度和喷溅情况,调节氩气流量。 在各级泵启动,真空度升高过程中,如产生溢渣和喷溅,应降低氩气流量,必要时可短时间停氩。各级 泵全部启动完毕后,包内渣面趋向稳定时,应逐渐加大氩气流量,以达到良好的脱气效果。VD处理结
精细、精准、精品
VD
(精、准、细、严)
文件管理号
文件持有者
版本:A
更改:0
VD真空炉基本工艺操作规程
编号.
页次:1
1、工艺流程
2、VD设备性能及工艺参数
3、VD操作控制原理
4、相关技术规定
A
版本号
编写
审核
批准
批准日期
实施日期
编号:
VD
页次:2
1
1.1炼钢厂工艺流程图
电弧炉炼钢---炉外精炼(LF、VD)---连铸/钢锭
2
2.1VD设备技术参数
序号
参 数 名 称
单位
数值
附注
1
钢包
钢包额定容量
t
40
钢包自由空间
mm
1100
>850
2
真空罐
罐直径
mm
①4800
外径
罐咼度
mm
52003罐Fra bibliotek车运行速度
m/min
2-12
驱动方式
机械式
变频调速
4
真空系统
抽气能力
AOD和VDVOD炉

AOD和VD/VOD炉AOD即氩氧脱碳精炼炉,是一项用于不锈钢冶炼的专有工艺。
一、AOD氩氧精炼炉设备组成:1、 AOD炉体2、 AOD悬架3、托圈4、 AOD挡渣罩5、 AOD底座6、轴承和轴承座7、倾炉系统驱动机构8 AOD事故倾动驱动机构二、AOD法特点: *采用廉价高碳铬铁大幅度降低原料成本。
*采用二步法炼钢,缩短了冶炼时间,提高了生产本。
*采用AOD法冶炼的不锈钢,质量稳定。
*AOD炉设备简单,基建投资小。
*AOD法操作简单,可靠,并可稳定地实现过程自动控制。
三、目的:主要是冶炼高质量的不锈钢(C<20ppm,S,P<50ppm);使用更廉价的原料(采用高碳铬代低碳铬);备注:使用情况:60-70%的不锈钢产量;我国太钢有国内第一台AOD;四、不锈钢的冶炼方法电炉;电炉或转炉+AOD;电炉或转炉+VOD.五、AOD工艺过程1.炉料:废钢、不锈钢返回料、高碳铬铁、高碳镍铁2.吹炼过程温度及氩氧比的控制3.分不同温度及碳含量控制吹炼氩氧比:O2:Ar=4:1(3:1),C下降为0.2%、T=1680℃;O2:Ar=2:1, C下降为0.1%、T=1700℃;O2:Ar=1:2, C下降为0.02%、T=1730℃;O2:Ar=1:3, C下降为0.01%、T=1750℃;VD/VOD炉基本情况:VD 的功能仅是真空加搅拌,VOD 是Vacuum and stir and injection oxygen;VD主要应用于轴承钢脱氧;VOD 主要用于不锈钢冶炼;一、设备用途:VD型钢包精炼炉可对钢水进行真空脱气处理及真空下合金成分微调及氩气搅拌。
VOD型钢包精炼炉是在真空下吹氧、脱碳、真空除气、真空下合金成分微调,主要用于精炼超低碳不锈钢和电工纯铁等。
二、主要形式:VD/VOD型钢包精炼炉可采用单独工位,也可采用双工位,真空罐为高架式或地坑式布置,也可采用车载式,真空罐盖的移动方式可采取旋开式或车载移开式。
VOD炉精炼不锈钢真空度调节方式的优化

书山有路勤为径,学海无涯苦作舟VOD 炉精炼不锈钢真空度调节方式的优化VOD 炉精炼不锈钢时,钢液入炉时C、Si 含量过高是导致吹氧过程喷溅事故的直接原因。
依据生产实践,提出两种降低喷溅事故产生几率的优化真空度调节方式,即延长2 乘以104Pa 保压时间;3 乘以104Pa 和2 乘以104Pa 两段式保压。
当入炉钢液C≥0.65%、Si≥0.20%时,采用优化后的真空度调节方式,能够有效地预防吹氧过程的喷溅事故,提高VOD 冶炼质量和效率。
VOD(Vacuum Oxygen Decarburization)真空吹氧脱碳工艺,是采用真空设备降低脱碳反应的CO 分压,从而提高脱碳效率的不锈钢炉外精炼工艺,由于在真空条件下很容易将钢液中的碳去除到很低的水平,因此,该精炼方法主要用于超纯、超低碳不锈钢和合金的二次精炼。
VOD 炉精炼不锈钢的核心功能是钢液的脱碳保铬,其精炼过程包括吹氧脱碳和还原脱气2 个阶段。
吹氧脱碳阶段真空度调节对于提高脱碳冶炼质量和效率、避免钢液喷溅等都起着至关重要的作用。
1、吹氧制度中真空度的调节(1)某钢厂VOD 精炼不锈钢的工艺流程为:EAF+LF+VOD(+VHD)或EF+VOD(+VHD)。
当C、Si 含量分别在0.40%~0.65%、0.12%~0.20%范围内,温度T≥1615℃时,是生产中理想的入VOD 吹氧的钢液条件。
此条件下对应的吹氧真空制度见示意(2)理想的VOD 炉吹氧冶炼过程为:开泵抽真空降真空至2 乘以104Par 保压VOD 泵(E5AE4A)开极限真空转VD 泵(E3E2E1)极限真空停泵放气。
此时真空调节的主要功能是促进炉内碳氧反应最大程度的进行,同时抑制Cr 的氧化,从而进一步完成VOD精炼不锈钢的脱碳保铬任务。
经验公式给出当炉内C 含量为0.25%时,真空度2 乘以104Pa 保压结束转成极限抽真空,根据真空吹氧脱碳原理,在真空条件下。
100吨LF精炼炉设备技术说明

100吨LF精炼炉设备技术说明1.1 电炉生产流程及工艺路线根据车间产品大纲,其工艺路线如下: 普通钢、低合金钢: 电炉——LF 炉——模铸/铸件 合金结构钢、优碳钢:电炉——LF 炉——VD ——模铸/铸件 超低碳、超低氮钢类:电炉——VOD ——(LF 炉)——模铸/铸件1.2 电炉工艺技术参数确定1.2.1 平均出钢量及炉壳直径考虑车间产品单重及与现有电炉的合浇工艺,可以设计电炉的平均出钢量为100吨,最大出钢量125吨。
这种情况可以选择公称容量100吨电炉、炉壳直径为6100 mm 、EBT 出钢的电炉。
当新炉体就要出125吨钢水时,可适当垫高(~100 mm )炉门坎并出净炉内钢水即可实现。
1.2.2 电炉冶炼周期与年产钢水量电炉车间的年产钢水量与冶炼周期的关系如下:τN G B A ⨯⨯⨯⨯=6024 ,万t式中:N —电炉车间的炉座数,一座。
G —电炉的平均出钢量,100吨。
B —电炉的年作业天数,对于铸钢行业一般为256~292天,车间作业制度及电炉年作业天数见表2.1。
表2.1 车间作业制度及电炉年作业天数—冶炼周期或出钢周期,以铸锻为主的电炉流程节奏快不起来,电炉冶炼周期也短不了,对于本例设电炉炼钢冶炼周期为120min。
年产钢水量的估算见表2.2。
表2-2 不同产品的年产钢水量注:年作业天数按 274天(年作业率为0.75)。
1.2.3 电炉变压器容量及技术参数1)冶炼周期组成当考虑电炉炼钢冶炼周期120min时,按废钢三次装料设计,补炉、装料(接电极)、出钢等非通电时间25min,使得变压器时间利用率Tu为0.79,通电时间为95min。
非通电时间过长,将延长冶炼周期、生产率降低,增加炉子热损失、降低炉子热效率,也提高吨钢电耗。
2)吨钢电耗采用氧化法,100%废钢,配碳量 1.5%与 3.5%(35kg/t钢)炉渣,在电炉中熔化并加热精炼至出钢温度(1650℃),所需要实际能耗平均为650 kWh/t,考虑到炉门碳-氧枪+炉壁氧枪,吹氧35~40 Nm3/t,与石墨电极氧化等提供的能量,合计160~180 kWh/t。
VODC炉外精炼技术及其冶金效果

VODC炉外精炼技术及其冶金效果
李锡年
【期刊名称】《江西冶金》
【年(卷),期】1999(019)004
【摘要】简述了真空吹氧脱碳转炉(VODC)的设备和经在超低碳不锈钢和普通合金钢的精炼生产中取得了很好的冶金效果,钢中非金属夹杂物减少,氢今是小物3×10^06,氧合量小于6.5×10^-5,不锈钢中铬回收率达98%~99%,精炼后的钢具有十分优越的性能。
VODC精炼工艺成熟,控制容易,适应中小型钢厂和铸钢厂的多钢种、小吨位为表炼生产需要,有着广阔的发展前景。
【总页数】8页(P14-21)
【作者】李锡年
【作者单位】上海大隆铸锻厂
【正文语种】中文
【中图分类】TF769.4
【相关文献】
1.CAS精炼工艺技术与冶金效果研究 [J], 贺道中
2.炉外精炼的应用及冶金效果 [J], 王尚贵;雷跃民
3.炉外精炼技术发展概况和中小转炉配备炉外精炼的意义与可能性 [J], 宋华德
4.我国炉外精炼技术现状及对发展炉外精炼技术的研究 [J], 赵龙飞
5.VODC产品的装备技术 [J], 朱凤新
因版权原因,仅展示原文概要,查看原文内容请购买。
vd、vod炼钢知识简介
脱氢率63%~82%;钢中w[N]由精炼前的0.0026%~
0.0045%降低到0.0018%~0.0032%,脱氮率22%~45
%;真空结束时,w(T[O])由处理前的0.0035%~0.0047
%降低到0.0012%~0.0025%;VD处理前后相比钢中的
夹杂物数量和大小均显著减小,钢液达到了较好的洁净度。
•
VD冶炼效果
• 通过VD精炼,钢中的气体、氧的含量 都降低了很多;夹杂物评级也都明显降低。 这个结果说明,这种精炼方法是有效的。 但是应当指出的是,使用当今系统的炉外 精炼方法得到的钢质量比单独采用VD精炼 要好得多。
上海五钢VD炉处理效果
•
上海五钢1998年建成投产100tVD炉,采用直
流电弧炉—VD真空处理—连铸生产工艺,67Pa
平均达29%,中碳钢的平均真空脱硫率为38%左
右,钢中硫可降到0.010%以下。低碳钢的平均真
空脱硫率为45%左右,钢中硫可降到0.019%以下。
武钢VD炉处理效果
•
武钢一炼钢1998年建成100t双工位的LF和VD各一座。
VD的主要技术参数如下:额定容量100t,真空泵抽气能
力400kg/h;蒸汽压力0.8~0.9MPa;真空罐内径
14~67Pa,与外界大气间形成压力差,钢液就沿
吸管上升到真空室内进行脱气。当钢包和真空室
的相对位置改变时(钢包下降或真空室提升),
脱气后的钢液就会重新返回到钢包内。这样反复
改变钢包和真空室的相对位置(每升降一次处理
钢液的量约为钢包容量的1/6~1/10),就使钢液
分批进入真空室接受处理,直至处理结束为止。
衡阳钢管厂VD炉处理效果
•
衡阳钢管厂于2001年建成投产40tVD炉,真
电炉双联法加VOD法冶炼不锈钢
电炉和精炼炉VOD双联法冶炼不锈钢工艺实践摘要根据我厂品种特点,总结了多年来不锈钢生产的经验,结合现场设备实际特点,摸索出了一套新的生产不锈钢的工艺方法,并在核电泵壳用钢Z3CN20-09M的冶炼中一次性试验成功。
本文主要阐述了Z3CN20-09M 钢的试验过程,并详细总结讨论了这种新工艺同传统VOD生产不锈钢对比的各种优缺点。
关键词不锈钢双联法VOD 工艺实践1.前言我们以前冶炼超低碳不锈钢通常采用两种工艺方法:一种是电炉提供初炼钢水,电炉调整镍钼成分,在精炼炉调整铬、锰、硅,然后倒入另一个精炼包进行VOD操作;另一种是在电炉冶炼初炼钢水时除调整镍钼外,部分调整铬、锰、硅合金,在精炼炉继续调整铬成分,最后倒入另一个精炼包进行VOD操作。
以上两种方法存在工艺烦琐,冶炼时间长等缺点。
在冶炼Z3CN20-09M钢上我们进行了一次重大工艺改进,就是其中一炉初炼钢水全部熔化合金,合兑后简单微调成份即进行VOD操作。
2.炼钢设备我公司新改造的VOD设备,为从原130T VD钢包精炼炉的基础上自行设计改造的。
在原VD 炉的真空盖上配置有拉瓦尔管式水冷氧枪,配有炉气温度显示仪及微氧含量分析仪,为VOD终点碳控制提供保证。
在真空盖上还装有电子视频监视系统,实时观察炉内反应进行状况及喷溅情况。
安装有两个500Kg真空加料仓,可在VOD结束后加造渣材料及脱氧合金。
真空抽气设备为500Kg 蒸汽喷射泵,分为四级,真空度可达到133Pa以下。
提供初练钢水的电弧炉有40TEBT和30T的EAF电弧炉。
3.冶炼工艺要点试验钢种Z3CN20-09M,钢水冶炼量70吨。
成品成份及初炼钢水要求如表1所示:3.1 工艺流程用40T的偏心炉底电炉为VOD精炼炉提供不调整任何合金元素的纯低磷氧化钢水,同时用30T电炉专门熔化合金。
工艺流程如图1所示。
图1 Z3CN20-09M钢试验工艺流程图为了尽量回收渣中的铬,30T电炉的合金直接带渣翻入LF精炼钢包。
VD炉精炼工艺技术介绍
VD炉精炼工艺技术介绍VD炉是一种常用的精炼工艺设备,主要用于对钢水进行去除氧、除杂等操作,从而获得高纯度、低含杂的优质钢材。
下面将对VD炉的工艺技术进行详细介绍。
1.VD炉的工艺流程:VD炉的工艺流程主要包括以下几个步骤:真空抽吸、脱氢、调温、精炼、合金化、钢水倾吐等。
具体流程如下:(1)真空抽吸:通过抽吸系统将炉腔内的气体抽除,建立起一定的真空度,为后续操作创造条件。
(2)脱氢:在真空状态下,通过向钢水中通入氢气,将钢水中的氢气与氧化钢中的氧反应生成水蒸气,从而将氧脱除。
(3)调温:通过加热和冷却系统,在一定的温度范围内对钢水进行调温,以便后续操作的顺利进行。
(4)精炼:在真空状态下,通过向钢水中通入精炼剂(如石灰、铝等),进行脱硫、脱杂等操作,从而得到低含杂、高纯度的钢水。
(5)合金化:根据需要向精炼后的钢水中加入合金元素,以调整其化学成分,提高钢材的性能。
(6)钢水倾吐:精炼和合金化结束后,将得到的优质钢水倾吐到铸型中进行铸造。
2.VD炉的工艺优势:(1)高纯度:由于采用真空精炼技术,能够有效地去除钢水中的气体、杂质等有害元素,提高钢水的纯度和质量。
(2)高效节能:VD炉采用闭式工作,减少了钢水中的挥发损失,具有较高的加热效率和能源利用率。
(3)灵活可控:VD炉可以根据不同的工艺要求进行调整,如调节真空度、精炼时间、合金化元素等,以满足不同类型钢材的生产需求。
(4)环保安全:VD炉在操作过程中采用真空技术,不会产生大量的粉尘、废气等污染物,符合环境保护和安全生产的要求。
3.VD炉的应用领域:VD炉广泛应用于钢铁冶金领域,特别是在高品质、特种钢材的生产中起到重要作用。
它适用于生产高速钢、合金结构钢、工具钢、耐热钢、耐腐蚀钢等。
在钢铁工业中,VD炉已成为一种不可或缺的关键设备。
总之,VD炉是一种重要的精炼工艺设备,通过真空操作和精炼剂的加入,可以高效去除钢水中的氧、气体和杂质等,获得高纯度、低含杂的优质钢材。
炉外精炼工艺与操作
任务4.1LF (V) 法炉外精炼工艺与操作
• 它可以与电弧炉配合, 取代电弧炉的还原期, 也可以与氧气转炉配合, 生产优质合金钢。同时, LF 还是连铸车间, 尤其是合金钢连铸车间不 可缺少的钢液成分、温度控制及生产节奏调整的设备。
• LF (V) 精炼法是钢包炉(Ladle Furnace) +真空(Vacuum) 的炉外精炼 法, 如图4 -3所示, 其是一种集电弧加热、气体搅拌、真空脱气、合成 渣精炼、喷吹精炼粉剂及添加合金元素等功能于一体的精炼法, 也称 多功能LF 法。
• ④检查无误后, 报告精炼炉炉长。 • (2) 精炼工精炼前的检查与准备。 • ①确认电极升降系统正常,三相电极长度能满足精炼需要,特别是
转炉开新炉及回炉钢水;检查电极接头处有无缝隙,如有缝隙,则吊 至电极接长装置并拧紧;检查电极头有无松动,若有松动,则把电极 头打掉;检查备用电极是否接长、数量是否足够。 • ②确认测温、定氧、取样装置工作正常,测温头、定氧头、取样器数 量足够。 • ③检查渣料、合金料、脱氧剂、增碳剂等是否充足,并确认合金成分。
• (12) 造还原渣: 炉渣化好后, 停电测温、取样, 调整吹Ar 强度。往钢包 中加铝粒或铝块, 按0.2 ~0.5 kg/ t 钢分批加入。根据渣样、钢样加石 灰或调渣剂、合金后送电。铝粒要求: wAl >99.0%, 粒度为0.5 ~1.0 mm。
• (13) 精炼时间的控制: 保证精炼时间32 min 以上, 钙处理后必须保证 软吹Ar 时间5 min以上, 钙样必须喂完钙线后软吹氩3 min 才取样。 钙铁线或硅钙线喂线速度控制在3.5 ~4.5 m/ s。
上一页 下一页 返回
任务4.1LF (V) 法炉外精炼工艺与操作
- 1、下载文档前请自行甄别文档内容的完整性,平台不提供额外的编辑、内容补充、找答案等附加服务。
- 2、"仅部分预览"的文档,不可在线预览部分如存在完整性等问题,可反馈申请退款(可完整预览的文档不适用该条件!)。
- 3、如文档侵犯您的权益,请联系客服反馈,我们会尽快为您处理(人工客服工作时间:9:00-18:30)。
真空精炼炉工艺技术说明(VOD设备)
1.1设备的功能、用途和可靠性
VOD型真空精炼设备是目前世界上使用最广泛的炉外精炼设备之一。
它具有设备简单、投资少、成本低、精炼钢种多、质量高、操作方便等诸多优点,因此成为特钢厂必备的精炼手段。
VOD-40t钢包精炼炉具有真空脱气、吹氩搅拌、吹氧脱碳、非真空测温取样等多种功能。
可以精炼轴承钢、合金结构钢、弹簧钢、优质碳素钢、超低碳不锈钢等。
由于它具有极强的真空脱气能力,因此可保证钢种的氢、氧、氮含量达到最低水平,并精确调整钢水成分,使夹杂物充分上浮,而有效提高钢的纯洁度,正因为它精炼的钢种多、质量高,可以为用户更灵活的适应市场竞争的需要,及时精炼出市场需要的钢种,从而增加企业的经济效益。
1.2方案布置
本套VOD-40t钢包精炼炉总体布置初步采用罐体半高架、固定不动,罐盖移动形式。
1.3 设备先进性
VOD-40t钢包精炼炉当不作吹氧操作时,VOD炉可完全实现VD炉操作功能。
冶炼时罐体和真空泵相连,其间通过主截止阀,可实现罐体与真空泵的启闭,并可在钢包吊入罐体之前,先对真空管道进行予抽,这样可以充分利用真空泵,缩短罐体的抽气时间和减少温降,使VOD炉和初炼炉、LF、浇铸相匹配,达到最佳效果。
该设备包括:一个真空罐系统、一个真空罐盖系统,一个罐盖升降及罐盖车系统,吹氧装置,真空加料装置,一套真空泵系统,一套连接罐与真空泵的真空管道系统,液压系统,吹氧系统,吹氩系统,压缩空气系统,冷却水系统,TV
摄像装置,一套电气控制及仪表监测设备系统。
在真空泵的造型和设计,罐盖的设计与密封性,吹氧装置的设计与密封以及全套计算机控制系统等方面,皆按目前世界上最先进的结构进行优化设计,以保证本设备的先进性,合理性,通用性。
设备特点:
(1)、真空罐接受要处理的钢包,吊车将钢包置于真空罐中后,人工连接上氩气管,罐为焊接结构,并设有钢包导向结构,以方便起吊钢包。
具有耐火材料的内衬以防止热应力。
罐底设有防漏装置。
(2)、罐盖升降为液压传动。
(3)、罐盖车行走采用电动机—减速机驱动,变频调速,以保证罐盖车起动行车及停止时平稳运行。
(4)、罐盖采用碟形封头,使罐盖的自重减少,强度增加,同时使罐盖的受力分布更加均匀,罐盖内部设有耐火材料内衬。
(5)、罐盖上装有人工观察窗,可随时观察炉内冶炼状态,实现合金成分调整及非真空状态下的测温取样。
(6)、罐盖与罐体之间,采用单层空心硅橡胶密封圈进行密封。
(7)采用新型专利组合除尘装置,提高除尘效果,对被抽气体进行除尘冷却,一方面保证进入真空泵系统气体的洁净度,又可使被抽气体温度控制在要求的范围之内,保护密封件,防止热失效,使真空泵的抽气效率大为提高。
(8)真空管道设置主截止阀,缩短予抽真空时间。
(9)配备麦氏计定期校验真空测量仪表。
(10)电控系统采用三电一体化设计,对真空泵的控制及炉子其它动作可全部由计算机操作站进行控制。
配置PLC 及工控机操作站作为基础级可连接到
工厂的二级网络上,接受网络系统进行控制操作,由LCD 进行系统监控,用打印机进行报表打印。
1.4 设备工艺流程
1.4.1若是VD工艺时,上工序钢液出钢温度应调整到该钢种浇铸温度上限+70~90℃;若是VOD工艺时,上工位的钢液温度应调整到1600℃左右,[C]和[Si]均有一定控制范围,并除渣。
其工艺流程:行车将盛有钢液的钢包吊入VOD炉真空罐内,人工接通吹氩管,同时进行测温取样。
而后,真空罐盖车从停车工位开到VOD工位,并下降罐盖。
接下来,真空处理、吹氧脱碳,合金微调、吹氩搅拌…待处理结束后,关闭真空主阀→破空→提升罐盖→真空罐盖车开到停车工位→测温取样→停止吹氩→加入保温剂→用行吊将钢包吊运至浇铸工位。
具体作业周期见下表。
1.4.2 VOD工艺可分为四个阶段:钢液准备;吹氧去碳;沸腾去气;还原微调。
每一阶段的精炼任务依各厂家的工艺流程不同而有所差异,但吹氧去碳阶段大体一致,而且是VOD工艺的控制核心。
我公司积累了多年的设计与生产经验,对吹氧终点碳的控制采用多种手段,即不但应用可靠性很强的氧浓差电势参数,而且还参照真空度和废气温度,综合分析,精确完成终点碳定位。
与工艺操作配合,尽量避免过吹和脱碳不足,并通过真空室压力控制,有效防止喷溅,使烙的回收率接近100%。
1.4.3 根据冶炼钢种,整体方案考虑以下工艺流程:
初炼炉→LF精炼→VOD处理→浇注;
该炼钢生产线由初炼炉供应初炼钢水,经过精炼设备对初炼钢水做精炼处理,使其钢水成份、温度满足浇注要求。
VOD炉工艺过程初步设计如下:
(1) 关闭主截止阀,启动真空泵;
(2) 行车将钢包吊入真空罐内,并接通氩气吹氩;
(3) 真空处理工位测温取样,确定钢水的温度及成份,从而确定真空处理制度;
(4) 罐盖车将罐盖运行至VOD工位
(5)落下罐盖;
(6)打开主截止阀,对真空罐内钢包中的钢水进行真空处理;
(7)真空罐内钢包中的钢水进行真空处理完毕,关闭主截止阀及破空;
(8) 提升罐盖,移动罐盖车至停车工位;
(9) 对真空罐内钢包中的钢水测温取样、软吹;用吊车将已真空处理过钢水送到浇注。
以上工序中,钢水处理时间约为60分钟。
VOD设备操作时间表
注:1)上表作业周期时间VOD处理周期~60min,可根据工艺调整作业时间。
其中准备处理阶段时间5min。
2)软吹氩流量:30-80 Nl/min。
3)吹氩时,为防止喷溅可采用流量缓升方式逐渐增加。
1.5 VOD真空精炼炉主要技术参数
说明:
a)设备用水,水质条件按GB10067.1-88《电热设备基本技术条件──通用部分》的有关要求;
具体如下:
PH值:6-8
悬浮性固体:<10mg/L
碱度:<60mg/L
氯离子:平均<60mg/L 最多<220mg/L
硫酸离子:<100mg/L
生铁:<2mg/L
可溶性固体:<300mg/L
可溶性SiO2 <6mg/L
电导率:<500μs/cm
总硬度:(带电体) <10 度( 每度为1 升水中含 10mgCaO)
b)氧枪冷却水≤4德国度(软化水)
c)蒸汽喷射泵冷却水水质为浊环水。