钢的渗碳硬化深度的检测方法
金属表面硬化层的测试

显微硬度计测量金属表面镀层覆层的硬度测试方法显微硬度计测量金属表面镀层覆层的硬度测试方法金属电镀层和覆盖层:电沉积层、自催化镀层、喷涂层以及氧化复膜等。
一般覆盖层厚度比较薄,对覆盖层的硬度要求又大多比较严格,因此覆盖层硬度检测显得十分重要。
检测的几个注意事项:1、试验力的选择:对于覆盖层的硬度检测,一般选用显微硬度试验法或者努氏硬度试验法,不管采用那种试验法,对于试验力的选择尤为关键,如果试验力过大,容易造成压头击穿覆盖层,所得硬度值受基体影响较大;如试验力过小,又容易引入较大误差。
2、试验力的保持时间;通常检测试验控制在10-15s左右,但对于相对较软的覆盖层,可适当延长试验力加载时间。
3、样件的装夹:对于较小工件或者不规则工件,应当采用夹具固定或进行镶嵌制样后进行测试,尽量避免因振动、支撑力不足、表面倾斜等外在因素影响测量数据。
对于需制样的工件,切勿因制样影响覆盖层组织变化,详细请参考金相试样制备,这里不在过多阐述。
4、压痕的打压位置:a、覆盖层切面检测:压痕的角端距离覆盖层的边缘至少为压痕对角线长度的一半。
采用努氏压头时,压痕的长对角线L应当与覆盖层边缘平行。
且软金属覆盖层(金、银、铜等)的厚度不得低于400um,硬覆盖层(硬质合金等)不得低于25um。
采用维氏压头时,两个压头的距离至少为压痕长度的2.5倍以上。
b、覆盖层表面检测:维氏硬度法氏,覆盖层的厚度至少为压痕对角线长度的1.43倍,努氏硬度法时,覆盖层厚度至少为压痕长对角线L的0.33倍。
5、结果的计算:每一试样最少区5点进行测试,取平均值,结果大于100时,取整数。
结果小于100时,保留1位小数,结果小于10时,保留两位小数。
渗氮层、淬硬层、有效硬化层的硬度和厚度测试渗氮层、淬硬层、有效硬化层的硬度和厚度测试一、钢铁零件渗氮(氮化)后的硬度及厚度检测方法:随着工业的发展,渗氮处理被更多的应用到各行各业,对渗氮处理的检测要求也日益提高。
42crmo渗碳 硬度

42crmo渗碳硬度摘要:一、42crmo钢材简介1.42crmo钢材的特性2.42crmo钢材的适用范围二、渗碳处理1.渗碳的定义和目的2.渗碳处理的过程三、42crmo渗碳硬度的影响因素1.渗碳浓度的影响2.保温时间的影响3.冷却方式的影响四、42crmo渗碳硬度的检测方法1.维氏硬度检测法2.布氏硬度检测法3.洛氏硬度检测法五、42crmo渗碳硬度的优化1.选择合适的渗碳浓度2.控制适当的保温时间3.采用适当的冷却方式正文:42crmo钢材是一种高强度、高韧性的合金结构钢,具有良好的综合力学性能、耐磨性和耐疲劳性。
广泛应用于制造高负荷、高扭矩、高弯曲的轴类、齿轮、模具等重要零件。
为了提高42crmo钢材的硬度和耐磨性,常常采用渗碳处理工艺。
渗碳是一种表面强化技术,通过在钢材表面添加碳元素,使其表面硬度提高,从而增加零件的使用寿命。
渗碳处理的过程包括:预热、渗碳、保温、冷却和后处理等步骤。
其中,渗碳浓度、保温时间和冷却方式是影响42crmo渗碳硬度的关键因素。
渗碳浓度对42crmo钢材硬度的影响最为显著。
一般来说,渗碳浓度越高,表面硬度越高,但过高的渗碳浓度会导致心部硬度下降,影响整体性能。
因此,在选择渗碳浓度时,需要根据实际需求进行权衡。
保温时间是影响42crmo渗碳硬度的另一个重要因素。
适当的保温时间可以确保碳原子充分扩散到钢材表面,提高硬度。
然而,过长的保温时间会导致碳原子在钢材内部扩散,降低心部硬度。
因此,在渗碳处理过程中,应根据实际情况控制适当的保温时间。
冷却方式对42crmo渗碳硬度也有一定影响。
快速冷却有助于提高表面硬度,但过快的冷却速度可能导致表层出现裂纹。
因此,选择适当的冷却方式,如油冷、水冷或气冷等,以兼顾硬度和韧性。
为了优化42crmo渗碳硬度,需要选择合适的渗碳浓度、控制适当的保温时间、采用适当的冷却方式。
此外,在生产过程中还需进行严格的检测,以确保42crmo钢材的硬度满足设计要求。
实验十三 渗层的组织观察与检验
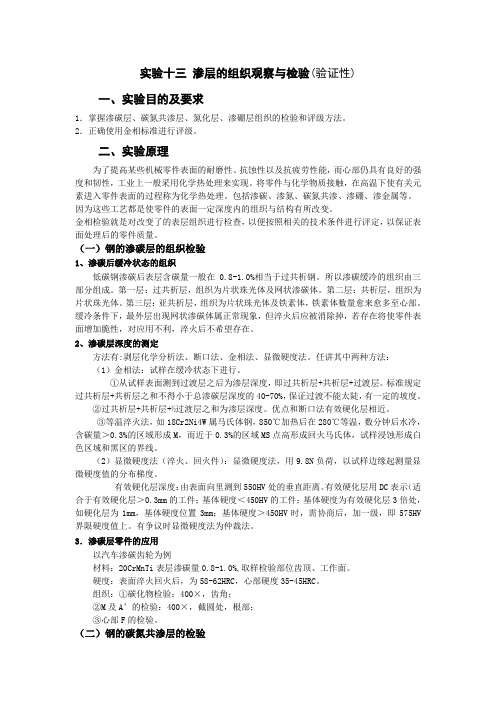
实验十三渗层的组织观察与检验(验证性)一、实验目的及要求1.掌握渗碳层、碳氮共渗层、氮化层、渗硼层组织的检验和评级方法。
2.正确使用金相标准进行评级。
二、实验原理为了提高某些机械零件表面的耐磨性、抗蚀性以及抗疲劳性能,而心部仍具有良好的强度和韧性,工业上一般采用化学热处理来实现。
将零件与化学物质接触,在高温下使有关元素进入零件表面的过程称为化学热处理。
包括渗碳、渗氮、碳氮共渗、渗硼、渗金属等。
因为这些工艺都是使零件的表面一定深度内的组织与结构有所改变。
金相检验就是对改变了的表层组织进行检查,以便按照相关的技术条件进行评定,以保证表面处理后的零件质量。
(一)钢的渗碳层的组织检验1、渗碳后缓冷状态的组织低碳钢渗碳后表层含碳量一般在0.8-1.0%相当于过共析钢。
所以渗碳缓冷的组织由三部分组成。
第一层:过共析层,组织为片状珠光体及网状渗碳体。
第二层:共析层,组织为片状珠光体。
第三层:亚共析层,组织为片状珠光体及铁素体,铁素体数量愈来愈多至心部。
缓冷条件下,最外层出现网状渗碳体属正常现象,但淬火后应被消除掉,若存在将使零件表面增加脆性,对应用不利,淬火后不希望存在。
2、渗碳层深度的测定方法有:剥层化学分析法、断口法、金相法、显微硬度法。
任讲其中两种方法:(1)金相法:试样在缓冷状态下进行。
①从试样表面测到过渡层之后为渗层深度,即过共析层+共析层+过渡层。
标准规定过共析层+共析层之和不得小于总渗碳层深度的40-70%,保证过渡不能太陡,有一定的坡度。
②过共析层+共析层+½过渡层之和为渗层深度。
优点和断口法有效硬化层相近。
③等温淬火法,如18Cr2Ni4W属马氏体钢,850℃加热后在280℃等温,数分钟后水冷,含碳量>0.3%的区域形成M,而近于0.3%的区域MS点高形成回火马氏体,试样浸蚀形成白色区域和黑区的界线。
(2)显微硬度法(淬火、回火件):显微硬度法,用9.8N负荷,以试样边缘起测量显微硬度值的分布梯度。
渗碳层深度检验方法(金相法)
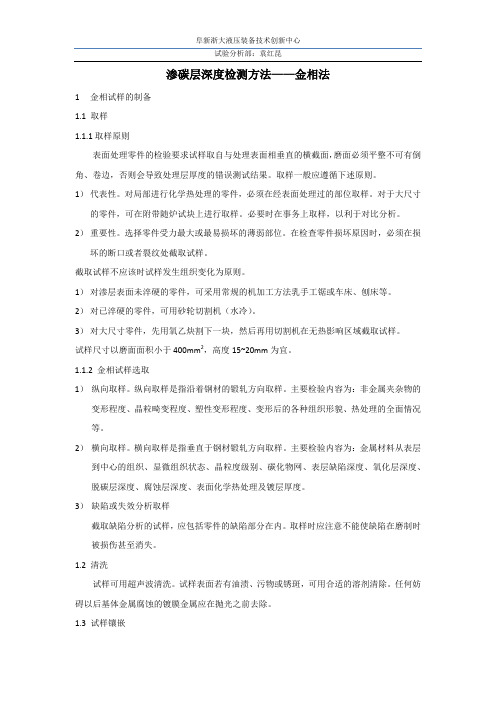
渗碳层深度检测方法——金相法1金相试样的制备1.1 取样1.1.1取样原则表面处理零件的检验要求试样取自与处理表面相垂直的横截面,磨面必须平整不可有倒角、卷边,否则会导致处理层厚度的错误测试结果。
取样一般应遵循下述原则。
1)代表性。
对局部进行化学热处理的零件,必须在经表面处理过的部位取样。
对于大尺寸的零件,可在附带随炉试块上进行取样。
必要时在事务上取样,以利于对比分析。
2)重要性。
选择零件受力最大或最易损坏的薄弱部位。
在检查零件损坏原因时,必须在损坏的断口或者裂纹处截取试样。
截取试样不应该时试样发生组织变化为原则。
1)对渗层表面未淬硬的零件,可采用常规的机加工方法乳手工锯或车床、刨床等。
2)对已淬硬的零件,可用砂轮切割机(水冷)。
3)对大尺寸零件,先用氧乙炔割下一块,然后再用切割机在无热影响区域截取试样。
试样尺寸以磨面面积小于400mm2,高度15~20mm为宜。
1.1.2 金相试样选取1)纵向取样。
纵向取样是指沿着钢材的锻轧方向取样。
主要检验内容为:非金属夹杂物的变形程度、晶粒畸变程度、塑性变形程度、变形后的各种组织形貌、热处理的全面情况等。
2)横向取样。
横向取样是指垂直于钢材锻轧方向取样。
主要检验内容为:金属材料从表层到中心的组织、显微组织状态、晶粒度级别、碳化物网、表层缺陷深度、氧化层深度、脱碳层深度、腐蚀层深度、表面化学热处理及镀层厚度。
3)缺陷或失效分析取样截取缺陷分析的试样,应包括零件的缺陷部分在内。
取样时应注意不能使缺陷在磨制时被损伤甚至消失。
1.2清洗试样可用超声波清洗。
试样表面若有油渍、污物或锈斑,可用合适的溶剂清除。
任何妨碍以后基体金属腐蚀的镀膜金属应在抛光之前去除。
1.3试样镶嵌若试样过于细薄或过软、易碎、或需检验边缘组织、或者为便于在自动磨抛机上研磨试样实验室通常采用可采用热压镶嵌法和浇注镶嵌法较为方便。
所选用先前方法均不得改变试样原始组织。
1.3.1热压镶嵌法将样品磨面朝下放入模中,树脂倒入模中超过样品高度,封紧模子并加热、加压。
渗层厚度的测定
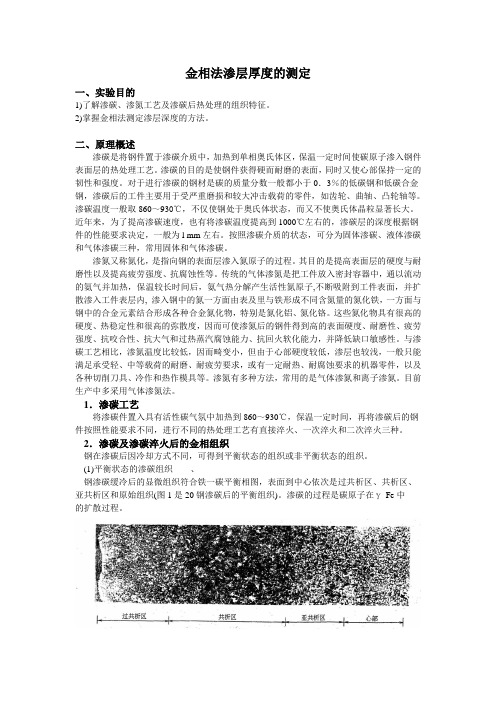
金相法渗层厚度的测定一、实验目的1)了解渗碳、渗氮工艺及渗碳后热处理的组织特征。
2)掌握金相法测定渗层深度的方法。
二、原理概述渗碳是将钢件置于渗碳介质中,加热到单相奥氏体区,保温一定时间使碳原子渗入钢件表面层的热处理工艺。
渗碳的目的是使钢件获得硬而耐磨的表面,同时又使心部保持一定的韧性和强度。
对于进行渗碳的钢材是碳的质量分数一般都小于0.3%的低碳钢和低碳合金钢,渗碳后的工件主要用于受严重磨损和较大冲击载荷的零件,如齿轮、曲轴、凸轮轴等。
渗碳温度一般取860~930℃,不仅使钢处于奥氏体状态,而又不使奥氏体晶粒显著长大。
近年来,为了提高渗碳速度,也有将渗碳温度提高到1000℃左右的,渗碳层的深度根据钢件的性能要求决定,一般为l mm左右。
按照渗碳介质的状态,可分为固体渗碳、液体渗碳和气体渗碳三种,常用固体和气体渗碳。
渗氮又称氮化,是指向钢的表面层渗入氮原子的过程。
其目的是提高表面层的硬度与耐磨性以及提高疲劳强度、抗腐蚀性等。
传统的气体渗氮是把工件放入密封容器中,通以流动的氨气并加热,保温较长时间后,氨气热分解产生活性氮原子,不断吸附到工件表面,并扩散渗入工件表层内, 渗入钢中的氮一方面由表及里与铁形成不同含氮量的氮化铁,一方面与钢中的合金元素结合形成各种合金氮化物,特别是氮化铝、氮化铬。
这些氮化物具有很高的硬度、热稳定性和很高的弥散度,因而可使渗氮后的钢件得到高的表面硬度、耐磨性、疲劳强度、抗咬合性、抗大气和过热蒸汽腐蚀能力、抗回火软化能力,并降低缺口敏感性。
与渗碳工艺相比,渗氮温度比较低,因而畸变小,但由于心部硬度较低,渗层也较浅,一般只能满足承受轻、中等载荷的耐磨、耐疲劳要求,或有一定耐热、耐腐蚀要求的机器零件,以及各种切削刀具、冷作和热作模具等。
渗氮有多种方法,常用的是气体渗氮和离子渗氮。
目前生产中多采用气体渗氮法。
1.渗碳工艺将渗碳件置入具有活性碳气氛中加热到860~930℃,保温一定时间,再将渗碳后的钢件按照性能要求不同,进行不同的热处理工艺有直接淬火、一次淬火和二次淬火三种。
渗碳淬火硬化层深度检测标准

渗碳淬火硬化层深度检测标准渗碳淬火是一种常用的表面处理方法,用于提高金属材料的硬度和耐磨性。
在渗碳淬火过程中,碳原子会渗透到金属表面,并与金属原子结合形成碳化物,从而形成硬化层。
硬化层的深度是评估渗碳淬火质量的重要指标之一。
渗碳淬火硬化层深度的检测标准主要有以下几种方法:1. 金相显微镜观察法:这是一种常用的检测方法,通过金相显微镜观察样品的横截面,可以清晰地看到硬化层的深度。
通常,硬化层的深度应符合相关标准要求。
2. 显微硬度计测量法:显微硬度计是一种常用的硬度测试仪器,可以测量材料的硬度。
通过在硬化层上进行一系列硬度测试,可以确定硬化层的深度。
通常,硬化层的深度应达到一定的数值范围。
3. 金相腐蚀法:金相腐蚀是一种将试样浸泡在特定腐蚀液中,以观察和测量试样表面的腐蚀情况的方法。
通过在硬化层上进行金相腐蚀实验,可以确定硬化层的深度。
通常,硬化层的深度应达到一定的腐蚀程度。
4. 电子显微镜观察法:电子显微镜是一种高分辨率的显微镜,可以观察到非常细小的结构。
通过在硬化层上使用电子显微镜观察,可以清晰地看到硬化层的深度。
通常,硬化层的深度应达到一定的微米级别。
以上是常用的渗碳淬火硬化层深度检测标准方法。
在实际应用中,可以根据具体情况选择合适的检测方法。
同时,还需要注意以下几点:1. 检测设备的准确性和精度:选择合适的检测设备,并确保其准确性和精度。
只有准确的检测结果才能有效评估渗碳淬火的质量。
2. 标准要求的合理性:检测标准应该合理,符合实际应用需求。
标准要求过高或过低都会影响渗碳淬火的质量评估。
3. 检测结果的可靠性:在进行检测时,需要保证样品的代表性和一致性。
只有可靠的检测结果才能准确评估渗碳淬火的质量。
总之,渗碳淬火硬化层深度的检测标准是评估渗碳淬火质量的重要指标之一。
通过选择合适的检测方法,并注意检测设备的准确性和精度,以及标准要求的合理性和检测结果的可靠性,可以有效评估渗碳淬火的质量。
这对于提高金属材料的硬度和耐磨性具有重要意义。
20钢铁材料渗层深度测定及组织检验
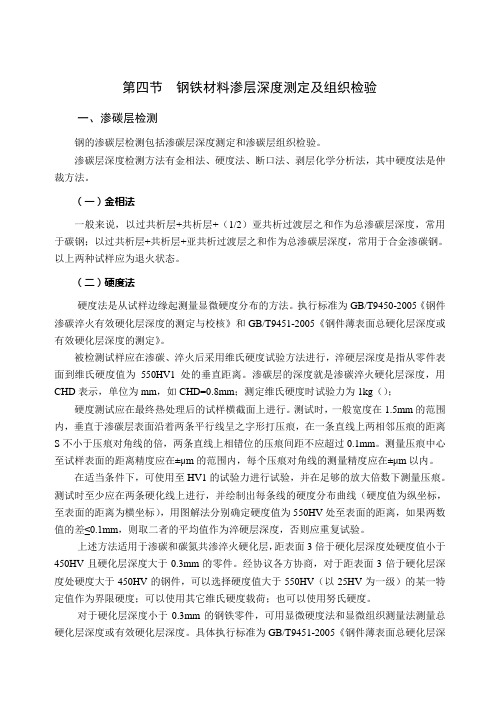
第四节钢铁材料渗层深度测定及组织检验一、渗碳层检测钢的渗碳层检测包括渗碳层深度测定和渗碳层组织检验。
渗碳层深度检测方法有金相法、硬度法、断口法、剥层化学分析法,其中硬度法是仲裁方法。
(一)金相法一般来说,以过共析层+共析层+(1/2)亚共析过渡层之和作为总渗碳层深度,常用于碳钢;以过共析层+共析层+亚共析过渡层之和作为总渗碳层深度,常用于合金渗碳钢。
以上两种试样应为退火状态。
(二)硬度法硬度法是从试样边缘起测量显微硬度分布的方法。
执行标准为GB/T9450-2005《钢件渗碳淬火有效硬化层深度的测定与校核》和GB/T9451-2005《钢件薄表面总硬化层深度或有效硬化层深度的测定》。
被检测试样应在渗碳、淬火后采用维氏硬度试验方法进行,淬硬层深度是指从零件表面到维氏硬度值为550HV1处的垂直距离。
渗碳层的深度就是渗碳淬火硬化层深度,用CHD表示,单位为mm,如CHD=0.8mm;测定维氏硬度时试验力为1kg();硬度测试应在最终热处理后的试样横截面上进行。
测试时,一般宽度在1.5mm的范围内,垂直于渗碳层表面沿着两条平行线呈之字形打压痕,在一条直线上两相邻压痕的距离S不小于压痕对角线的倍,两条直线上相错位的压痕间距不应超过0.1mm。
测量压痕中心至试样表面的距离精度应在±μm的范围内,每个压痕对角线的测量精度应在±μm以内。
在适当条件下,可使用至HV1的试验力进行试验,并在足够的放大倍数下测量压痕。
测试时至少应在两条硬化线上进行,并绘制出每条线的硬度分布曲线(硬度值为纵坐标,至表面的距离为横坐标),用图解法分别确定硬度值为550HV处至表面的距离,如果两数值的差≤0.1mm,则取二者的平均值作为淬硬层深度,否则应重复试验。
上述方法适用于渗碳和碳氮共渗淬火硬化层,距表面3倍于硬化层深度处硬度值小于450HV且硬化层深度大于0.3mm的零件。
经协议各方协商,对于距表面3倍于硬化层深度处硬度大于450HV的钢件,可以选择硬度值大于550HV(以25HV为一级)的某一特定值作为界限硬度;可以使用其它维氏硬度载荷;也可以使用努氏硬度。
渗氮层、淬硬层、有效硬化层的硬度和厚度测试简介

0.05
0.02
0.35
0.15
0.1
0.05
0.4
0.2
0.15
0.05
0.5
0.25
0.2
0.1
0.6
0.3
0.25
0.1
0.65
0.3
0.3
0.1
0.75
0.3
3、总渗氮层深度
b、基体硬度的取点与测定,一般在3倍左右渗氮层深度的距离处测得的硬度值(至少取3点,平均值)做为基体硬度值。
c、对于渗氮层硬度变化很平缓的钢种,(如碳钢、低碳合金钢制件),其渗氮层深度可以从试样表面沿垂直方向测至比基体维氏硬度高30HV处。
d、当渗氮层深度有的特别浅,有的则较深时,检测力可以在0.2KG范围内选择(并注明,如HV0.2)
a、渗氮层脆性级别按维氏硬度压痕边缘碎裂程度分为5级
级别
渗氮层脆性级别说明
1
压痕边角完整无缺
2
压痕一边或一角碎裂
3
压痕二边或二角碎裂
4
压痕三边或三角碎裂
5
压痕四边或四角碎裂
b、渗氮层脆性检验一般采用维氏硬度计,试验力10公斤,试验力的加载必须缓慢(在5-9S内完成),试验力加载完成后必须停留5-10S,然后卸载试验力,特殊情况也可采用5KG或者30KG试验力。
一般零件推荐的化合物层厚度及公差表(单位/mm)
化合物层厚度
上偏差
化合物层厚度
上偏差
0.005
0.003
0.012
0.006
0.008
0.004
- 1、下载文档前请自行甄别文档内容的完整性,平台不提供额外的编辑、内容补充、找答案等附加服务。
- 2、"仅部分预览"的文档,不可在线预览部分如存在完整性等问题,可反馈申请退款(可完整预览的文档不适用该条件!)。
- 3、如文档侵犯您的权益,请联系客服反馈,我们会尽快为您处理(人工客服工作时间:9:00-18:30)。
钢的渗碳硬化深度的检测方法
1.适用范围此规格规定了钢的渗碳淬火或碳氮共渗淬火时的硬化层深度(以下,称硬化
层)的检测方法。
备注:1 此规格出自以下规格
JIS B 0601 表面粗糙度—定义及表示
JIS G 0201 钢铁用语(热处理)
JIS G 0202 钢铁用语(试验)
JIS Z 2244 维氏硬度检测方法
JIS Z 2244 洛氏硬度检测方法
2 与此规格相对应的国际规格如下所示。
ISO 2639: 1982 Steel-Determination and verification of the effective depth of carburized
and hardness case
3 附表是有效硬化层深度的辅助检测方法。
2.用语的定义此规格使用的主要用语的定义,除出自JIS G 0201 及JIS G 0202 之外,还出
自以下几项
(1)有效硬化层深度淬火后,或用不超过200℃的温度进行挥霍的硬化层的表面开始,到
表1所示的界限硬度的位置的距离。
但是,关于非硬化区域的硬度超
出维氏硬度450时,根据双方协议,也可以使用超出维氏硬度550(维
氏硬度25刻度的)界限硬度。
(2)全硬化层深度从硬化层的表面开始,到硬化层与素材的物理性质或是化学性质几乎没有
差异时的位置的距离。
备注:这里所说的物理性质用硬度,化学性质用宏观组织来判定。
(3)硬度推移曲线从硬化层表面开始的,表示垂直距离和硬度之间关系的曲线。
3.测定方法的种类
3.1硬度试验测定方法对试验块的断面通过硬度检测来测定硬化层深度的方法。
3.2宏观组织试验测定方法吧试验块的断面腐蚀后,在低倍率的放大镜下进行观察,测定
硬化层深度的检测方法。
备注:硬化层深度的检测方法,一般使用硬度试验的测定方法,要是简单一点的话,就
用宏观组织试验测定方法。
4.试验品试验品原则上使用产品本身。
但是,不得已时也可以使用与产品同种条件下的同
一钢种的钢材。
5.硬度试验检测方法
5.1 把试验品沿与硬化层垂直的方向切开,把切开面研磨后作为被检测面。
切割或是研磨时,
注意不要对被检测面的硬度造成影响,同时,不要使边部变圆。
5.2 关于被检测面,根据JIS Z 2244 的维氏硬度试验或由双方协定进行洛氏试验力
硬度试验,制作硬度推移曲线,根据此曲线测定有效硬化层或是全硬层
深度。
这时,维氏硬度试验的试验荷重,原则上使用2.9N.但是,如
有必要,也可使用0.98~98.1N的荷重。
5.3 硬度推移曲线的制作,如下所示。
(1)在需要做测定的被检测面,沿与表面相垂直的直线,依次检测硬度,制作硬度推移曲
线。
但是,有必要时,在表面1.5mm的范围内,取2~5个点,在从
各个点开始与表面相垂直的直线上检测硬度,制作一根硬度推移曲
线。
(参照图1)。
图1 硬度测定点的分布
备注: L2-L1, L3-L2, L4-L3,…….在0.1mm以下,从表面开始的累计距离的精度在±25um (2)根据维氏硬度试验制作硬度推移曲线时,测定点的间隔,原则上在0.1mm以下。
但是,表面硬化层很大时,界限硬度旁边区域除外,也可使用0.1mm以上。
(3)维氏硬度试验时,相邻的打点之间的间距,要在打点的对角线长度的2.5倍以上。
(4)使用洛氏试验力硬度检测方法时,根据双方的协商进行。
5.4硬化层深度的判定
(1)根据1根硬度推移曲线,读出硬化层深度。
(2)也可根据双方的协商,制作2条硬度推移曲线,取硬化层深度的平均值。
另外,当两者的差超过0.1mm时,重新测试。
备注:1全硬化层深度难以判定时,根据双方协定,也可以取在大约是硬化层深2倍处测得的素材硬度基础上加30~50HV的点,作为决定全硬化层深度的硬度。
2有必要检测有效硬化层深度时,采用附表所示的方法。
6.宏观组织试验检测方法
6.1 把试验块沿与硬化面垂直的方向切割,研磨后最为被检测面。
切割或是研磨的时候,一定要注意不要对被检测面的组织造成不必要的影响。
被检测面的粗糙度,原则上采用JIS B 0601的1.6umR Y
把被检测面放在约5%的硝酸酒精溶液中,等待合适的时间,使得可以看到明显的变色状态,再把这个腐蚀面放在酒精或水中洗净,用不超过20倍的放大镜确认腐蚀的变色情况。
6.2要求得全硬化层深度时,检测与素材部分变色不同的地方的表面开始的深度。
7.表示
7.1硬化层深度用mm来表示,并保留到小数点之后第1位。
7.2硬化层深度的表示记号,如表2所示。
表2 硬化层深度的表示记号
备注:1△里的数字是JIS Z 2244 表1里硬度记号的数字,□里填入JIS Z 2245表1的刻度。
2.维氏试验荷重为2.9N时,也可以省略不填△。
例1.DC-H0.3-E2.5
(使用5.的维氏硬度试验检测方法,用试验荷重2.9N进行检测,有效硬化层深度2.5mm 时)
例2.DC-H1-T1.1
(使用5.的维氏硬度试验检测方法,用试验荷重9.8N进行检测,全硬化层深度1.1mm 时)
例3.DC-H15N-E1.0
(使用5.的洛氏试验力硬度检测方法,到87HR15N的有效硬化层深度1.0mm时)
例4.DC-M-T2.2
(使用6.的宏观组织检测方法进行测定,全硬化层深度2.2mm时)
3.关于维氏硬度的有效硬化层深度,在相对应的ISO 2639中,用下列所示的标识来表示有效硬化层深度。
“DC(试验荷重*0.102)/界限硬度”
例 DC5/515 (试验荷重49.03N,界限硬度515HV)
但是,当试验荷重9.807N,界限硬度550HV时,只记上”DC”.此表示法适用于双方协商的情况下。
8.报告制作报告时,除了记下测定值以外,最好还要写上以下事项。
(1)钢种或化学成分
(2)试验品(产品或同一钢种的钢材)的区别
(3)热处理条件
(4)检测位置
附表有效硬化层深度的检测
前言:此附表是根据ISO 2639(Steel-Determination and verification of the effective depth of
carburized and hardened case)规定的有效硬化层深度的辅助法制作的
检验方法。
渗碳层的深度事前已经判定过的情况下,根据双方的协定也同样适用。
在垂直断面上,从表面开始的距离d1,d2的地方,测定5个点以上的硬度(参照附表1)d1,d2
分别设定为比要检测的有效硬化层深度小,及大的值,d2 -d1要在
0.3mm以下。
有效硬化层深度,通过下列公式得出:
DC= d1+( d2 -d1)(H1-HS)/(H1-H2)
这里,H3:界限硬度
H1,H2: d1,d2硬度的算术平均(参照附图2)
附图1 硬度检测位置
附图2 有效硬化层深度的计算
维氏
硬度
到表面的距离
D1 D2 DC H1 HS H2。