有效硬化层深度检测示意图片
硬化层深度测定1
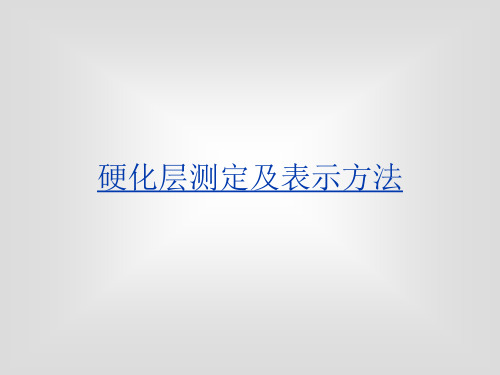
45
49
83
85
64
68
49
54
硬化层深度表示方法
(一).硬化层深度单位以mm表示,小数点第一位以下采四舍五入. (二).硬化层深度的表示符号,如表所示. 测 硬化层深度 微小维克氏硬度 定 方 法 巨观检视 腐蚀试验法
硬 度 试 验 测 定 方 法 洛氏硬度
高调波淬火 有效硬化层深度
火焰淬火 有效硬化层深度 高调波淬火 有效硬化层深度 火焰淬火 有效硬化层深度
氮化层深度及实用氮化层深度的表示方法: 1.1-氮化层深度及实用氮化层深度,单位以mm表示,取至小数点以下第二位. 1.2-氮化层深度较浅时,也可使用µm表示,但须于数字尾端加上单位. 备注: 1.ND:表示氮化层深度.参考(Nitrided case depth) 2.△:表示硬度测试的荷重,其单位为kgf. 3.M :表示金属显微组织(Microstructure). 4.T :表示全氮化层深度(Total Depth). 5.P :表示实用氮化层深度(Practical Depth).
表面硬度HMV(0.5)872 心部硬度HMV(0.3)126 0.1mm 800 0.2mm 846 0.3mm 761 0.4mm 621 0.5mm 400 0.6mm 309 0.7mm 201
硬化层深度表示方法
(一).硬化层深度单位以mm表示,小数点第二位以下采四舍五入. (二).硬化层深度的表示符号,如下表所示.
43.6 53.0 55.9 58.5 62.5 63.6 37.1 46.4 53.7 53.6 61.4 60.9
61.2 68.7 71.4 71.6 73.6 72.3 55.1 64.2 69.9 69.1 62.6 71.1
渗碳淬火组织评级

生产过程中酸洗法进行磨削烧伤的控制,当出现争议时可再用金相组织 法进行最终的判断
30g/L的硝酸水溶液
酸洗法介绍
溶液配比: 配好三种溶液 1、30g/L 的硝酸水溶液 2、50g/L 的盐酸酒精溶液 3、 50g/L 的氢氧化钠水溶液
酸洗法介绍
• 在酸洗前一定要用酒精或洗洁精去处零件表面的 油污和脏物,并用清水冲洗,确保零件表面非常
干净,这个清洗步骤非常重要,零件表面清洗不 干净会引起误判。
• 根据清水冲洗
水溶液
干净
50g/L 的盐酸 25秒 清水冲洗
酒精溶液
干净
吹干
清水冲洗 30秒 50g/L 的氢氧
况确定;常啮合齿轮1-5级,换档齿轮1-4级。
碳化物评级图
钢件渗碳金相检验
抛光态下的内氧化
腐蚀态下的内氧化
钢件渗碳金相检验
• 非马氏体组织:渗碳淬火件表面层中经常出现连续或不连续的 网状或块状黑色组织,主要由于内氧化而贫合金化元素导致形 成屈氏体类组织,一般规定不超过0.02mm.
• 减少非马氏体组织的措施: • 1)尽可能用低碳烃和高纯度气体做制备渗碳气体的原料气; • 2)尽可能选用含Cr、Ti、V、B元素的钢; • 3)从工艺和设备上采取措施,保证炉气不受空气污染; • 4)尽可能采用快速的淬火冷却介质和冷却方式。
钢件渗碳金相检验
钢件渗碳金相检验
钢件渗碳金相检验
• 适用于渗碳淬硬层有效深度大于0.3mm的汽车齿轮。 • 放大倍数:400X • 检验部位: 同芯部硬度 • 铁素体:1-3级
感应淬火硬化层深度的无损测量

除了这些应用信息之外,还记录一般的辅助信息。标准测量值包括测量时间、炉温、样 件的总面积和重点区域、样件平均宽度和高度以及声音/噪音比例,失重和相关图片的对比 度。 其精度可达 0.3 微米。
KLIMATOM 光热测量系统 模拟气候变化下材料的原位表征
弗劳恩霍夫硅酸盐研究所 ISC 的设备研发中心 CeDeD 研发出一款新型测量设备:KLIMATOM。 该设备用于模拟气候变化条件下材料的原位表征。
所有检测统计信息都是在同一个检查过程中通过时分多路传输来采集的。每秒钟可以 进行多达 40 次测量。3MA 系统会计算每个校准目标值的基准值,并通过实时方式显示出来。 检测过程中所涉及到的目标值可能包括多种材料属性,其规格取决于微结构以及残余应力剖 面等。
应用领域: ● 硬度 ● 硬化层深度 ● 残余应力 ● 拉伸试验数据(抗张强度、屈服强度、延伸率等)
感应淬火硬化层深度的无损测量
背景 表面硬化可以提高受动态应力部件的耐磨性以及疲劳强度。这些特性主要是由表面硬
度、硬化深度以及残余应力的深度剖面决定的。硬化层深度是表面硬化处理过程中的一个重 要质量指标。目前只能通过随机检测方法来确保硬化工艺的质量。这种方法不仅会损坏部件, 浪费时间,而且成本也较高。
全面的自动数据评估,最终可以得到材料的硬化深度(DS)(参见图 2)。 这种新式无损检测方法的测量结果与传统有损方法非常接近,并在下列条件下实现最佳
结果: - 被检零件感应淬火; - 零件是锻造的,而不是铸造的; - 最小硬化深度为 1.5mm; - 基础材料与马氏体材料之间有清晰和明显的过渡,而没有如贝氏体材料这样的 中间结构; - 基础材料的微粒大小足以支持 20MHZ 剪切波的良好后向散射。
高温光学测量系统 TOM
谈齿轮渗碳淬火有效硬化层及硬度梯度

浅谈齿轮渗碳淬火有效硬化层及硬度梯度随着机械工业的发展,对齿轮的质量要求日益提高,而齿轮的强度寿命和制造精度与热处理质量有很大关系。
为了检验齿轮材料热处理质量,在1987年以前,我国的齿轮渗碳淬火内在质量检验标准多为终态金相检验标准。
由于检测仪器的精度、分辨率等因素以及检验人员的经验参差不齐,造成检验结果有很大差异和争议。
为了解决金相法内在检验存在的弊端,机械部在1987年借鉴了DIN.ISO等标准中有关内容,修订了我国现行齿轮渗碳淬火内在质量检验标准。
此检验标准中,其金相组织检验标准基本与原标准相似,主要是对渗碳层深度及碳浓度梯度的测定作了较大的修改。
下面就渗碳层深度和碳浓度梯度分别采用金相法与硬度法测定进行简述。
一、渗碳层深度的检测1.1、金相法1.1.1、取本体或与零件材料成分相同,预先热处理状态基本相似的圆试样或齿形试样进行检测。
1.1.2、送检试样热处理状态为平衡状态,即退火状态。
1.1.3、低碳钢渗层深度为:过共析层+共析层+1/2亚共析层。
1.1.4、低碳合金钢渗层深度为:过共析层+共析层+亚共析层。
1.2、硬度法1.2.1、取样方法同金相法取样方法一致。
1.2.2、送检试样状态为淬火+回火状态。
1.2.3、渗碳深度用有效硬化层来表示,其极限硬度根据不同要求进行选择。
1.2.4、有效硬化层深度(DCp):从试样表面测至极限硬度(如HV550)之间垂直距离。
1.3、两种关于渗碳深度检测的方法存在着一定的对应关系,下面用图形来描述。
从图中可看出:DCp(芯部)>DCp(HV500)>DCp(HV550)DCp(HV550)对应渗碳层中碳含量约为0.35~0.38%,此界限处即为金相法中1/2亚共析层处。
DCp(HV500)对应渗碳层中碳含量约为0.31~0.33%,此界限处为金相法中1/2亚共析层处。
DCp(芯部)对应渗碳层中碳含量为基体碳含量,一般为0.17~0.23%,此界限处为金相法中基体组织。
渗氮层、淬硬层、有效硬化层的硬度和厚度测试简介
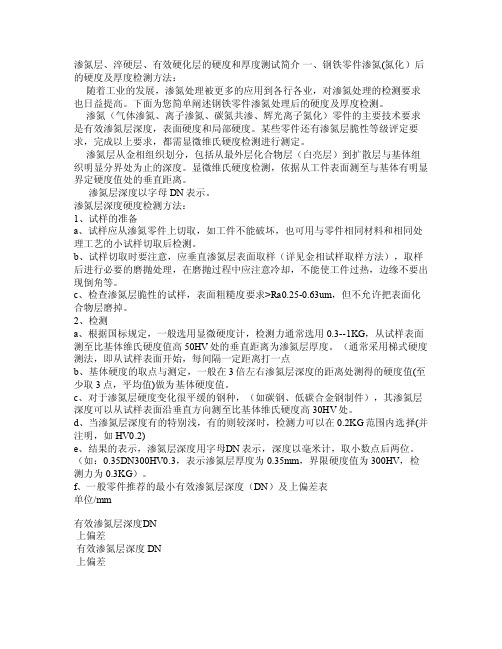
渗氮层、淬硬层、有效硬化层的硬度和厚度测试简介一、钢铁零件渗氮(氮化)后的硬度及厚度检测方法:随着工业的发展,渗氮处理被更多的应用到各行各业,对渗氮处理的检测要求也日益提高。
下面为您简单阐述钢铁零件渗氮处理后的硬度及厚度检测。
渗氮(气体渗氮、离子渗氮、碳氮共渗、辉光离子氮化)零件的主要技术要求是有效渗氮层深度,表面硬度和局部硬度。
某些零件还有渗氮层脆性等级评定要求,完成以上要求,都需显微维氏硬度检测进行测定。
渗氮层从金相组织划分,包括从最外层化合物层(白亮层)到扩散层与基体组织明显分界处为止的深度。
显微维氏硬度检测,依据从工件表面测至与基体有明显界定硬度值处的垂直距离。
渗氮层深度以字母DN表示。
渗氮层深度硬度检测方法:1、试样的准备a、试样应从渗氮零件上切取,如工件不能破坏,也可用与零件相同材料和相同处理工艺的小试样切取后检测。
b、试样切取时要注意,应垂直渗氮层表面取样(详见金相试样取样方法),取样后进行必要的磨抛处理,在磨抛过程中应注意冷却,不能使工件过热,边缘不要出现倒角等。
c、检查渗氮层脆性的试样,表面粗糙度要求>Ra0.25-0.63um,但不允许把表面化合物层磨掉。
2、检测a、根据国标规定,一般选用显微硬度计,检测力通常选用0.3--1KG,从试样表面测至比基体维氏硬度值高50H V处的垂直距离为渗氮层厚度。
(通常采用梯式硬度测法,即从试样表面开始,每间隔一定距离打一点b、基体硬度的取点与测定,一般在3倍左右渗氮层深度的距离处测得的硬度值(至少取3点,平均值)做为基体硬度值。
c、对于渗氮层硬度变化很平缓的钢种,(如碳钢、低碳合金钢制件),其渗氮层深度可以从试样表面沿垂直方向测至比基体维氏硬度高30HV处。
硬化层深度测定
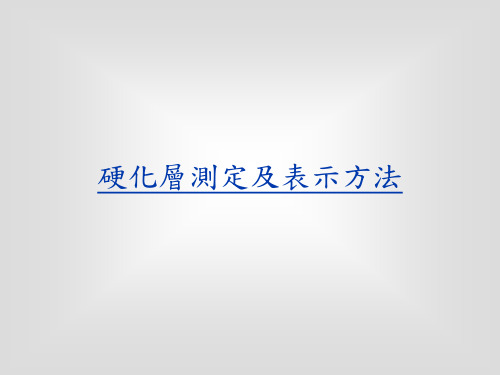
90.0 90.3 87.0
火焰淬火及高週波淬火硬化深度測試
定義:
1.有效硬化層深度: 鋼經火焰淬火及高週波淬火硬化,自硬化層表面到有效硬化層 界限硬度位置的距離稱之.
2.全硬化層深度: 從硬化層的表面到心部位置物理與化學性質的差異,顏色差別 區分之.
3.當有違反衝突到廠內自訂標準,則已客戶要求之合約訂單標準執 行之.或經本廠建議及雙方共同研討且必須經客戶同意之協調內 容,訂為標準合約.
硬化層深度
測定方法 硬度試驗測試法 巨視腐蝕試驗法
有效硬化層深度
DC-H△-E
﹡
全硬化層深度
DC-H△-T
DC-M-T
備註:1.上表△位置必須記入硬度試驗之荷重,其單位為kgf. 2.微小維克氏硬度試驗荷重為0.3kgf時,△位置的記入可省略.
例1.DC-H0.3-E0.8(表示以微小維克氏硬度試驗法測定,試驗荷重為 0.3kgf,有效硬化層深度0.8mm)
1.2-微小維克氏硬ห้องสมุดไป่ตู้試驗測定硬度分佈曲線時,如判定硬化層 深度小於1.5mm以內,則測定間隔原則上小於0.1mm,必要 場合時則可視情況而定.硬化層深度大於1.5mm時,硬度測 定點間格可大於0.1mm以上.
1.3-依微小維克氏硬度試驗,相鄰兩個壓痕中心之間隔必須大 於壓痕對角線長度之2.5倍,且壓痕中心距離試片邊緣也須 有壓痕對角線長度之2.5倍以上.
68
54
硬化層深度表示方法
(一).硬化層深度單位以mm表示,小數點第一位以下採四捨五入. (二).硬化層深度之表示符號,如表所示.
硬化層深度
高週波淬火 有效硬化層深度
火焰淬火 有效硬化層深度
高週波淬火 有效硬化層深度
火焰淬火 有效硬化層深度
钢的渗碳硬化深度的检测方法
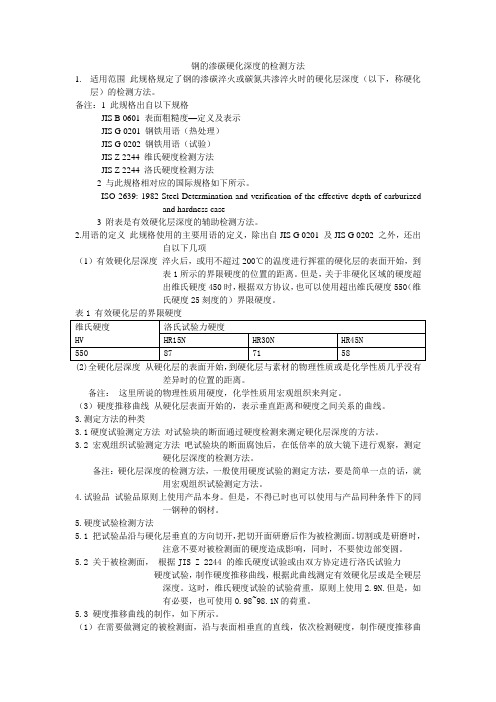
钢的渗碳硬化深度的检测方法1.适用范围此规格规定了钢的渗碳淬火或碳氮共渗淬火时的硬化层深度(以下,称硬化层)的检测方法。
备注:1 此规格出自以下规格JIS B 0601 表面粗糙度—定义及表示JIS G 0201 钢铁用语(热处理)JIS G 0202 钢铁用语(试验)JIS Z 2244 维氏硬度检测方法JIS Z 2244 洛氏硬度检测方法2 与此规格相对应的国际规格如下所示。
ISO 2639: 1982 Steel-Determination and verification of the effective depth of carburizedand hardness case3 附表是有效硬化层深度的辅助检测方法。
2.用语的定义此规格使用的主要用语的定义,除出自JIS G 0201 及JIS G 0202 之外,还出自以下几项(1)有效硬化层深度淬火后,或用不超过200℃的温度进行挥霍的硬化层的表面开始,到表1所示的界限硬度的位置的距离。
但是,关于非硬化区域的硬度超出维氏硬度450时,根据双方协议,也可以使用超出维氏硬度550(维氏硬度25刻度的)界限硬度。
(2)全硬化层深度从硬化层的表面开始,到硬化层与素材的物理性质或是化学性质几乎没有差异时的位置的距离。
备注:这里所说的物理性质用硬度,化学性质用宏观组织来判定。
(3)硬度推移曲线从硬化层表面开始的,表示垂直距离和硬度之间关系的曲线。
3.测定方法的种类3.1硬度试验测定方法对试验块的断面通过硬度检测来测定硬化层深度的方法。
3.2宏观组织试验测定方法吧试验块的断面腐蚀后,在低倍率的放大镜下进行观察,测定硬化层深度的检测方法。
备注:硬化层深度的检测方法,一般使用硬度试验的测定方法,要是简单一点的话,就用宏观组织试验测定方法。
4.试验品试验品原则上使用产品本身。
但是,不得已时也可以使用与产品同种条件下的同一钢种的钢材。
5.硬度试验检测方法5.1 把试验品沿与硬化层垂直的方向切开,把切开面研磨后作为被检测面。
渗氮层、淬硬层、有效硬化层的硬度和厚度测试简介

0.05
0.02
0.35
0.15
0.1
0.05
0.4
0.2
0.15
0.05
0.5
0.25
0.2
0.1
0.6
0.3
0.25
0.1
0.65
0.3
0.3
0.1
0.75
0.3
3、总渗氮层深度
b、基体硬度的取点与测定,一般在3倍左右渗氮层深度的距离处测得的硬度值(至少取3点,平均值)做为基体硬度值。
c、对于渗氮层硬度变化很平缓的钢种,(如碳钢、低碳合金钢制件),其渗氮层深度可以从试样表面沿垂直方向测至比基体维氏硬度高30HV处。
d、当渗氮层深度有的特别浅,有的则较深时,检测力可以在0.2KG范围内选择(并注明,如HV0.2)
a、渗氮层脆性级别按维氏硬度压痕边缘碎裂程度分为5级
级别
渗氮层脆性级别说明
1
压痕边角完整无缺
2
压痕一边或一角碎裂
3
压痕二边或二角碎裂
4
压痕三边或三角碎裂
5
压痕四边或四角碎裂
b、渗氮层脆性检验一般采用维氏硬度计,试验力10公斤,试验力的加载必须缓慢(在5-9S内完成),试验力加载完成后必须停留5-10S,然后卸载试验力,特殊情况也可采用5KG或者30KG试验力。
一般零件推荐的化合物层厚度及公差表(单位/mm)
化合物层厚度
上偏差
化合物层厚度
上偏差
0.005
0.003
0.012
0.006
0.008
0.004